通孔回流问题点
通孔回流工艺 -回复

通孔回流工艺-回复什么是通孔回流工艺,该工艺如何应用于电子制造业?通孔回流工艺是电子制造业中的一项关键工艺,用于将表面组装贴片元件(SMD)焊接至电路板上。
该工艺通过在数秒或数分钟内加热电路板,使焊料熔化,并与电路板上的焊盘实现连接。
通孔回流工艺的应用旨在确保焊接的贴片元件与焊盘之间的可靠连接,从而保证电路板的功能和可靠性。
通孔回流工艺通常包括以下步骤:1. 打磨和去污:在回流工艺之前,首先需要对电路板进行打磨和去污。
这是为了去除表面的氧化物和污垢,以便确保焊接表面的良好接触。
2. 贴片:在电路板上放置SMD元件,这些元件通常是芯片型、二极管型或电感型的元器件。
在这个阶段,工作人员需要按照设计图纸进行放置,确保元件准确无误地安装在焊盘上。
3. 贴片传送:经过贴片后,电路板需要经过贴片传送工作台。
这个工作台使用机器手臂或传送带,将贴片元件以准确的速度和位置传送至回流炉的入口。
4. 回流焊接:在回流炉中,电路板通过预先设置的温度曲线进行加热。
温度曲线是根据焊接材料和元件所需温度而设计的。
加热的过程中,焊料会熔化,与焊盘进行连接。
通过精确控制温度和时间,可以确保焊接的可靠性和质量。
5. 冷却:焊接完成后,电路板会经过一个冷却过程,以确保焊接处的固化。
冷却通常在温度下降的环境中进行,这个过程可以逐渐降低焊接处的温度,使其固化并达到最佳性能。
通孔回流工艺在电子制造业中的应用非常广泛。
随着电子产品尺寸越来越小,组装更密集,传统的手工焊接方法已无法满足需求。
通孔回流工艺的应用可以提供以下优势:1. 高精度:通孔回流工艺使用机械定位和自动控制,能够实现高度准确的焊接位置和排列。
相比手工焊接,通孔回流工艺可以大幅提高焊接的精度和一致性。
2. 高效率:通孔回流工艺可以通过自动化设备实现高速焊接。
相比手工焊接,通孔回流工艺可以提高生产效率,节约时间和成本。
3. 低能耗:通孔回流工艺使用的加热方式通常是通过热风或红外辐射,相比传统的水暖炉等加热方式,能耗更低。
通孔回流工艺

穿孔回流焊是一项国际电子组装应用中新兴的技术。
当在PCB的同一面上既有贴装元件,又有少量插座等插装元件时,一般我们会采取先贴片过回流炉,然后再手工插装过波峰焊的方式。
但是,如果采取穿孔回流焊技术,则只需在贴片完成后,进回流炉前,将插件元件插装好,一起过回流炉就可以了。
通过这项比较,就可以看出穿孔回流焊相对于传统工艺的优越性。
首先是减少了工序,省去了波峰焊这道工序,在费用上自然可以节省不少。
同时也减少了所需工作人员,在效率上也得到了提高。
其次是回流焊相对于波峰焊,生产桥接的可能性要小得多,这样就提高了一次通过率。
穿孔回流焊技术相对传统工艺在经济性、先进性上都有很大的优势。
所以,穿孔回流焊技术是电子组装中的一项革新,必然会得到广泛的应用。
但如果要应用穿孔回流焊技术,也需要对器件、PCB设计、网板设计等方面提出一些不同于传统工艺的要求。
a)元件:穿孔元件要求能承受回流炉的回流温度的标准,最小为230度,65秒。
这一过程包括在孔的上面涂覆焊膏(将在回流焊过程中进入孔中)。
为使这一过程可行,元件体应距板面0.5毫米,所选元件的引脚长度应和板厚相当,有一个正方形或U形截面,(较之长方形为好)。
b)计算孔尺寸完成孔的尺寸应在直径上比引脚的最大测量尺寸大0.255毫米(0.010英寸),通常用引脚的截面对角,而不包括保持特征。
钻孔的尺寸比之完成孔再大0.15毫米(0.006英寸),这是电镀补偿,这样算得的孔就是可接受的最小尺寸。
c)计算丝网:(焊膏量)第一部分计算是找出焊接所需的焊膏量,孔的体积减去引脚的体积再加上焊角的体积。
(需要什么样的焊接圆角)。
所需焊接体积乘以2就是所需焊膏量,因为焊膏中金属含量为50%体积(以ALPHA 的UP78焊膏为例)。
丝印过程中将焊膏通过网孔印在PCB上,由于压力一般能将焊膏压进孔中0.8毫米(当刮刀与网板成45度角时)。
我们计算进入孔中焊膏的体积,从所需焊膏量中减去它就得到在网孔中留下的焊膏的体积。
通孔回流工艺解析经典版
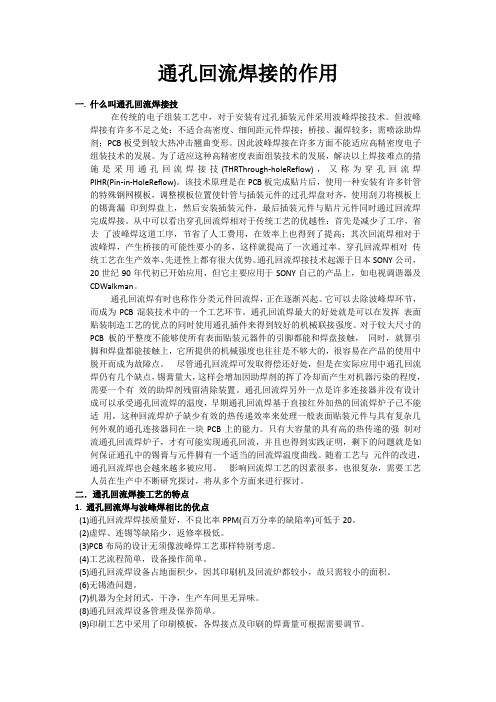
通孔回流焊接的作用一.什么叫通孔回流焊接技在传统的电子组装工艺中,对于安装有过孔插装元件采用波峰焊接技术。
但波峰焊接有许多不足之处:不适合高密度、细间距元件焊接;桥接、漏焊较多;需喷涂助焊剂;PCB板受到较大热冲击翘曲变形。
因此波峰焊接在许多方面不能适应高精密度电子组装技术的发展。
为了适应这种高精密度表面组装技术的发展,解决以上焊接难点的措施是采用通孔回流焊接技(THRThrough-holeReflow),又称为穿孔回流焊PIHR(Pin-in-HoleReflow)。
该技术原理是在PCB板完成贴片后,使用一种安装有许多针管的特殊钢网模板,调整模板位置使针管与插装元件的过孔焊盘对齐,使用刮刀将模板上的锡膏漏印到焊盘上,然后安装插装元件,最后插装元件与贴片元件同时通过回流焊完成焊接。
从中可以看出穿孔回流焊相对于传统工艺的优越性:首先是减少了工序,省去了波峰焊这道工序,节省了人工费用,在效率上也得到了提高;其次回流焊相对于波峰焊,产生桥接的可能性要小的多,这样就提高了一次通过率。
穿孔回流焊相对传统工艺在生产效率、先进性上都有很大优势。
通孔回流焊接技术起源于日本SONY公司,20世纪90年代初已开始应用,但它主要应用于SONY自己的产品上,如电视调谐器及CDWalkman。
通孔回流焊有时也称作分类元件回流焊,正在逐渐兴起。
它可以去除波峰焊环节,而成为PCB混装技术中的一个工艺环节。
通孔回流焊最大的好处就是可以在发挥表面贴装制造工艺的优点的同时使用通孔插件来得到较好的机械联接强度。
对于较大尺寸的PCB板的平整度不能够使所有表面贴装元器件的引脚都能和焊盘接触,同时,就算引脚和焊盘都能接触上,它所提供的机械强度也往往是不够大的,很容易在产品的使用中脱开而成为故障点。
尽管通孔回流焊可发取得偿还好处,但是在实际应用中通孔回流焊仍有几个缺点,锡膏量大,这样会增加因助焊剂的挥了冷却而产生对机器污染的程度,需要一个有效的助焊剂残留清除装置。
通孔回流焊接的工艺技术

通孔回流焊接的工艺技术如图2,可实现在单一步骤中同时对通孔元件和表面贴装元件(SMC/SMD)进行回流焊。
相对传统工艺,在经济性、先进性上都有很大的优势。
所以,通孔回流工艺是电子组装中的一项革新,必然会得到广泛的应用。
二通孔回流焊接工艺与传统工艺相比具有以下优势:1、首先是减少了工序,省去了波峰焊这道工序,多种操作被简化成一种综合的工艺过程;2、需要的设备、材料和人员较少;3、可降低生产成本和缩短生产周期;4、可降低因波峰焊而造成的高缺陷率,达到回流焊的高直通率。
;5、可省去了一个或一个以上的热处理步骤,从而改善PCB可焊性和电子元件的可靠性,等等。
尽管用通孔回焊可得到良好的工艺效果,但还是存在一些工艺问题。
1、在通孔回焊过程中锡膏的用量比较大,由于助焊剂挥发物质的沉积会增加对机器的污染,因而回流炉具有有效的助焊剂管理系统是很重要的;2、对THT元件质量要求高,要求THT元件能经受再流焊炉的热冲击,例如线圈、连接器、屏蔽等。
有铅焊接时要求元件体耐温235℃,无铅要求260℃以上。
许多THT元件尤其是连接器无法承受回流焊温度;电位器、铝电解电容、国产的连接器、国产塑封器件等不适合回流焊工艺。
3、由于要同时兼顾到THT元件和SND元件,使工艺难度增加。
本文重点是确定对通孔回流工艺质量有明显影响的各种因素,然后将这些因素划分为材料、设计或与工艺相关的因素,揭示在实施通孔回流工艺之前必须清楚了解的关键问题。
1. 通孔回流焊焊点形态要求2. 获得理想焊点的锡膏体积计算3. 锡膏沉积方法4. 设计和材料问题5. 贴装问题6. 回流温度曲线的设定下面将逐项予以详细描述。
1、通孔回流焊焊点形态要求:首先,应该确定PIHR焊点的质量标准,建议参照业界普遍认同的焊点质量标准IPC-A-610D,根据分类(1、2或3类)定出目视检查的最低可接受条件。
企业可在此标准基础上,进行修改以适应其工艺水平。
通孔回流理想焊点模型是一个完全填充的电镀通孔(Plated Through Hole,PTH),在PCB的顶面和底面带有焊接圆角(如图3)。
通孔回流焊工艺要求

通孔回流焊工艺要求
通孔回流焊工艺是一种常用的电子制造工艺,用于将电子元件与PCB(印制电路板)连接。
在实施通孔回流焊工艺时,需要满足以下要求:
1. 温度曲线控制:通孔回流焊工艺要求在焊接过程中,加热和冷却速度要控制在合适的范围内,以避免对电子元件产生过大的热应力。
通常会采用预热、焊接和冷却三个阶段的温度曲线控制。
2. 焊接温度:焊接温度是通孔回流焊工艺中的一个重要参数。
一般情况下,焊接温度应根据PCB和电子元件的性质,选择适当的温度范围,以确保焊接质量和元件的安全性。
3. 焊接时间:焊接时间也是通孔回流焊工艺中需要控制的重要参数。
焊接时间过长可能导致焊接质量下降,焊接时间过短则可能无法达到良好的焊接效果。
一般情况下,会根据焊接温度和焊接表面积来确定焊接时间。
4. 焊接气氛:通孔回流焊工艺要求在焊接过程中,提供适当的气氛,以防止元件与焊接面的氧化和蒸发。
常见的焊接气氛包括氮气、氢气和惰性气体等。
5. 焊接通道设计:通孔回流焊工艺中的通道设计要合理,以确保热量能够均匀地传递到焊接区域,并且能够有效地移除焊接过程中产生的气体和挥发物。
总结而言,通孔回流焊工艺的要求主要包括温度曲线控制、焊接温度和时间的控制、焊接气氛和通道设计等。
通过合理的工艺参数设置,可以确保焊接质量和电子元件的安全性。
通孔回流焊工艺要求

通孔回流焊工艺要求通孔回流焊是一种常见的表面贴装技术,在电子制造行业中广泛使用。
它通过将电子元件焊接到PCB板上进行连接,以实现电子设备的正常运行。
下面是通孔回流焊工艺的要求和相关参考内容。
1. 焊接温度控制:在通孔回流焊过程中,焊接温度是一个非常重要的参数。
焊接温度过高会导致元件损坏,焊接温度过低会导致焊接不良。
因此,对于不同类型的元件,应根据供应商提供的数据和规范来确定适当的焊接温度范围。
2. 焊接时间控制:除了焊接温度外,焊接时间也是影响焊接质量的重要因素。
焊接时间过长可能会导致焊接点过热,焊接时间过短可能会导致焊接不充分。
通常,焊接时间应根据焊接温度和元件类型进行调整,以确保焊接质量。
3. 焊接剂的选择:焊接剂在通孔回流焊工艺中起到重要的作用。
它可以帮助提高焊接质量,并防止氧化。
在选择焊接剂时,应根据焊接材料和工艺要求选择适合的类型和规格的焊接剂。
4. 焊接机器设备的选取:通孔回流焊需要使用专门的焊接设备,如回流焊炉。
在选购设备时,应考虑焊接速度、温度控制的精度、设备的稳定性等因素。
并且,设备的使用和维护也是确保焊接质量的关键。
5. PCB设计的要求:良好的PCB设计对于焊接质量的保证至关重要。
在PCB设计中,应考虑元件的布局、焊盘的大小和间距等因素,以便实现良好的焊接质量。
6. 焊接操作的执行:良好的焊接操作是保证焊接质量的重要保证。
操作人员应熟悉焊接工艺要求,并采取正确的焊接操作,包括元件的放置和固定、焊接温度和时间的控制、焊接剂的喷洒等。
7. 焊后检测的要求:焊接后的检测对于发现焊接缺陷和及时修复非常重要。
可以借助透光检查、高倍显微镜检查、飞针测试等方法来进行焊后检测。
8. 质量管理的要求:通孔回流焊工艺要求严格的质量管理,包括过程记录、检验记录、不良品管理等。
操作人员应按照质量管理程序要求进行操作,并确保焊接质量符合相关标准和规范。
综上所述,通孔回流焊工艺的要求包括焊接温度控制、焊接时间控制、焊接剂的选择、焊接机器设备的选取、PCB设计的要求、焊接操作的执行、焊后检测的要求和质量管理的要求。
通孔回流焊孔的尺寸与焊接柱大小的关系

通孔回流焊孔的尺寸与焊接柱大小的关系焊接是一种常用的连接工艺,而焊孔则是焊接过程中的一个关键因素。
焊孔的尺寸与焊接柱的大小有着密切的关系,本文将探讨二者之间的关系。
焊孔的尺寸是指焊接前所需的孔洞尺寸,通常包括直径和深度两个方面。
焊孔的尺寸对于焊接质量具有重要影响,若焊孔尺寸过小,会导致焊接材料填充不足,影响焊接强度;而若焊孔尺寸过大,则会产生过多的焊接材料,增加了焊接成本,并可能引起焊接缺陷。
焊接柱的大小则是指焊接后形成的焊接部分。
焊接柱的大小与焊孔的尺寸密切相关,一般情况下,焊孔尺寸越大,焊接柱的大小也会相应增加。
这是因为焊接时,填充到焊孔中的焊接材料会通过熔化和凝固的过程形成焊接柱,而焊孔尺寸的增大会使得焊接材料的填充量增加,从而形成更大的焊接柱。
然而,焊孔尺寸与焊接柱大小之间并非简单的线性关系。
焊接过程中,除了焊孔尺寸外,还有许多其他因素会影响焊接柱的大小。
例如,焊接电流、焊接时间、焊接速度等都会对焊接柱的形成产生影响。
因此,在实际焊接过程中,需要根据具体情况综合考虑多个因素,确定合适的焊孔尺寸,以达到所需的焊接柱大小。
在焊接工程中,焊孔尺寸通常会根据焊接材料的厚度和焊接强度要求来确定。
一般来说,焊孔的直径一般为焊接材料厚度的1.5倍至2.5倍,深度为焊接材料厚度的0.5倍至1倍。
当焊接材料的厚度较小时,焊孔尺寸可以适当减小,以减少焊接材料的浪费;而当焊接材料的厚度较大时,焊孔尺寸则需要适当增大,以确保焊接强度的要求。
除了焊孔尺寸外,焊接柱的大小还受到焊接方法的影响。
不同的焊接方法对焊接柱的形成有着不同的要求。
例如,对于电弧焊接来说,焊接柱的大小会受到焊接电流和电弧长度的影响;而对于激光焊接来说,焊接柱的大小则会受到激光功率和焊接速度的影响。
因此,在选择焊接方法时,需要考虑到焊接柱大小的要求,并进行合理的调整。
焊孔尺寸与焊接柱大小之间存在着密切的关系。
在实际焊接过程中,需要根据焊接材料的厚度、焊接强度要求以及所采用的焊接方法等因素综合考虑,确定合适的焊孔尺寸,以获得所需的焊接柱大小。
通孔焊接工艺缺陷分析及处1

1.合理的设计焊盘;
2.阻焊膜未经过良好的处理。阻焊膜的吸附是产生锡球的一个必要条件;
2.通孔铜层至少25μm以避免和防止板内所含的水汽的影响;
3.焊锡膏中助焊剂使用量太大;
3.采用合适的锡膏涂刷,减少锡膏内混入的其他气体量;
4.PCB板没有经过预热过程或预热温度不够,助焊剂未能有效挥发;
1、使用专业刷锡设备、通孔刷锡/回流治具;
2.过孔设计不合理,影响了焊点热容的损失;
2、PCB板过孔的设计不能影响到焊点的热容损失;
连锡
1.线路分布太密,引脚太近或不规律;(一定搭配的焊盘与引脚焊点在一定条件下能承载的锡膏量是一定的,处理不当多余的部分都可能造成桥连现象);
1、合理设计焊盘,避免过多采用密集布线;
2.回流温度不均匀;
2、改善回流槽结构;
3.PCB没有经过预热过程或预热温度不够及助焊剂活性不够;
3、增加预热区,适当提高焊接预热温度,同时可以考虑在一定范围内提高焊接温度以提高焊锡合金流动性;
4.锡膏印刷桥连或是偏移等;
4、调整刷锡通孔治具位置与PCB板原件脚位置对准或调小刷锡锡膏流量;
锡珠/锡球
针对这些问题,我们也多次反复实验及参考了其它相关的资料,总结得出以下问题及改善方案:
不良现象
描述
改善措施
焊点不湿润
1.焊接温度不够或不均匀,预热温度偏低或是助焊剂活性不够,使得助焊剂未能有效去除焊盘以及引脚表面氧化膜;在此,我们在做实验的同时完全没有预热的这一作业步骤。
1、增加预热区域;
2.焊接温度不够。常用无铅焊锡合金的熔点升高且润湿性大为下降,需要更高的焊接温度来保证焊接质量;(已改善);
4.适当提高预热的温度;