NO reduction in 0.03–0.2 MW oxy-fuel combustor
SAE J17112010
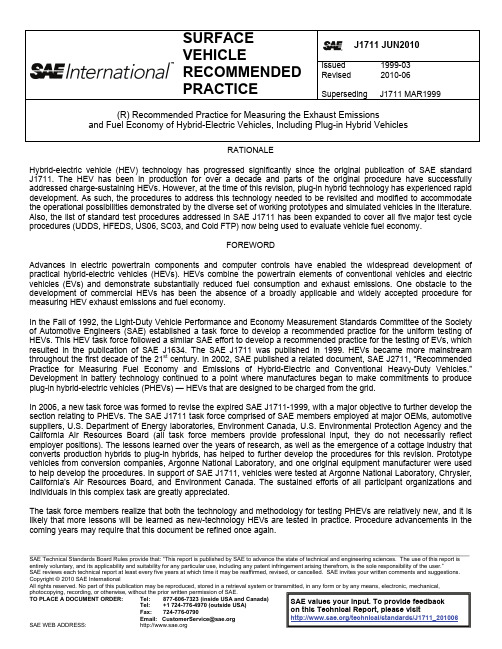
entirely voluntary, and its applicability and suitability for any particular use, including any patent infringement arising therefrom, is the sole responsibility of the user.”
SAE reviews each technical report at least every five years at which time it may be reaffes your written comments and suggestions.
SURFACE VEHICLE RECOMMENDED PRACTICE
J1711 JUN2010
Issued Revised
1999-03 2010-06
Superseding J1711 MAR1999
(R) Recommended Practice for Measuring the Exhaust Emissions and Fuel Economy of Hybrid-Electric Vehicles, Including Plug-in Hybrid Vehicles
Copyright © 2010 SAE International
All rights reserved. No part of this publication may be reproduced, stored in a retrieval system or transmitted, in any form or by any means, electronic, mechanical,
Oxy-fuel combustion of solid fuels
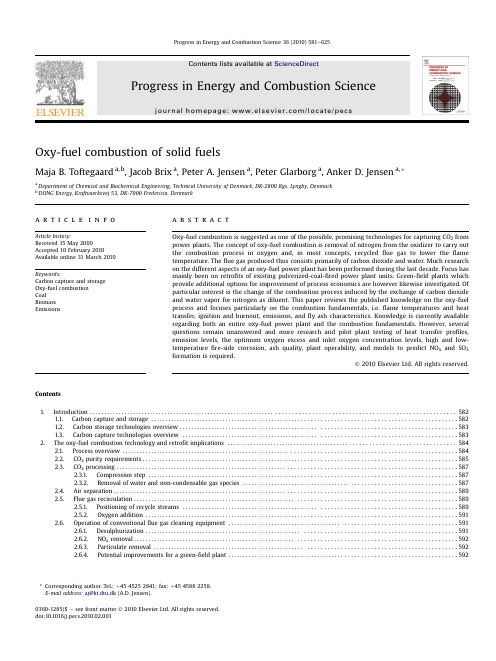
Oxy-fuel combustion of solid fuelsMaja B.Toftegaard a ,b ,Jacob Brix a ,Peter A.Jensen a ,Peter Glarborg a ,Anker D.Jensen a ,*a Department of Chemical and Biochemical Engineering,Technical University of Denmark,DK-2800Kgs.Lyngby,Denmark bDONG Energy,Kraftvaerksvej 53,DK-7000Fredericia,Denmarka r t i c l e i n f oArticle history:Received 15May 2009Accepted 10February 2010Available online 31March 2010Keywords:Carbon capture and storage Oxy-fuel combustion Coal Biomass Emissionsa b s t r a c tOxy-fuel combustion is suggested as one of the possible,promising technologies for capturing CO 2from power plants.The concept of oxy-fuel combustion is removal of nitrogen from the oxidizer to carry out the combustion process in oxygen and,in most concepts,recycled flue gas to lower the flame temperature.The flue gas produced thus consists primarily of carbon dioxide and water.Much research on the different aspects of an oxy-fuel power plant has been performed during the last decade.Focus has mainly been on retro fits of existing pulverized-coal-fired power plant units.Green-field plants which provide additional options for improvement of process economics are however likewise investigated.Of particular interest is the change of the combustion process induced by the exchange of carbon dioxide and water vapor for nitrogen as diluent.This paper reviews the published knowledge on the oxy-fuel process and focuses particularly on the combustion fundamentals,i.e.flame temperatures and heat transfer,ignition and burnout,emissions,and fly ash characteristics.Knowledge is currently available regarding both an entire oxy-fuel power plant and the combustion fundamentals.However,several questions remain unanswered and more research and pilot plant testing of heat transfer pro files,emission levels,the optimum oxygen excess and inlet oxygen concentration levels,high and low-temperature fire-side corrosion,ash quality,plant operability,and models to predict NO x and SO 3formation is required.Ó2010Elsevier Ltd.All rights reserved.Contents 1.Introduction ......................................................................................................................5821.1.Carbon capture and storage ...................................................................................................5821.2.Carbon storage technologies overview .........................................................................................5831.3.Carbon capture technologies overview ........................................................................................5832.The oxy-fuel combustion technology and retrofit implications ..........................................................................5842.1.Process overview ............................................................................................................5842.2.CO 2purity requirements ......................................................................................................5852.3.CO 2processing .. (587)pression step ....................................................................................................5872.3.2.Removal of water and non-condensable gas species (587)2.4.Air separation ...............................................................................................................5892.5.Flue gas recirculation .. (589)2.5.1.Positioning of recycle streams ........................................................................................5892.5.2.Oxygen addition .. (591)2.6.Operation of conventional flue gas cleaning equipment (591)2.6.1.Desulphurization ....................................................................................................5912.6.2.NO x removal ........................................................................................................5922.6.3.Particulate removal .................................................................................................5922.6.4.Potential improvements for a green-field plant .. (592)*Corresponding author.Tel.:þ4545252841;fax:þ4545882258.E-mail address:aj@kt.dtu.dk (A.D.Jensen).Contents lists available at ScienceDirectProgress in Energy and Combustion Sciencejournal homepage:w ww.el/locate/pecs0360-1285/$e see front matter Ó2010Elsevier Ltd.All rights reserved.doi:10.1016/j.pecs.2010.02.001Progress in Energy and Combustion Science 36(2010)581e 6252.7.Boiler and steam cycle (593)2.7.1.Burner operation and flame stabilization (593)2.7.2.Heat uptake (593)2.7.3.Oxygen excess (594)2.7.4.Fire-side corrosion (594)2.7.5.Aspects regarding green-field plants (594)2.8.Summary (594)3.Oxy-fuel combustion fundamentals (595)3.1.Research groups and experimental facilities (595)3.2.Heat and mass transfer effects (595)3.2.1.Flame and gas phase temperatures (595)3.2.2.Radiative and convective heat transfer (598)3.3.The combustion process (600)3.3.1.Devolatilization and ignition (600)3.3.2.Volatile and char burnout (601)3.4.Gaseous pollutants emissions (604)3.4.1.NO x (604)3.4.2.SO x (612)3.4.3.Trace elements (615)3.5.Ash and deposition chemistry (615)3.5.1.Particle formation mechanisms (615)3.5.2.The effects of gas composition on particle formation (615)3.5.3.Ash quality (617)3.5.4.Depositions,slagging,and fouling (618)3.6.Oxy-fuel combustion of biomass (618)3.6.1.The combustion process (618)3.6.2.Emissions (619)3.6.3.Ash and corrosion (619)3.7.Summary (620)4.Conclusions (621)Acknowledgements (622)References (622)1.IntroductionThe world,and especially the developing countries such as China and India,is facing an increasing growth in the demand for electrical power[1,2].New power plants are thus being constructed at a considerable rate in order to keep up with this demand[1e3]. The majority of the recently constructed and planned power plants, on a world-wide basis,are coal-fired[1,2].Coal is a cheaper and more abundant resource than other fossil fuels such as oil and natural gas while at the same time being a very reliable fuel for power production[4,5].In the developed countries an increasing part of the energy consumption is being produced from renewable sources of energy; wind,biomass,solar,hydro power,etc.[1].The main purpose of the shift from a fossil fuel based production to renewable energy is to decrease the emission of greenhouse gases.Especially the emission of CO2from the combustion of fossil fuels has gained great focus in recent years in connection with the discussions of global warming. Since the beginning of the industrialization in the late part of the 18th century the amount of CO2in the atmosphere has increased sharply from about280to380ppm[6],see Fig.1.Table1lists the current and projected CO2emissions,in Gton carbon per year,from power generation(both electricity and heat) [1].Both the emissions and the coal share of the emissions are seen to increase toward2030for the world as a whole.Even though the CO2emissions are seen to increase within Europe the percentage increase is much less pronounced than for the rest of the world and the coal share of the emissions is expected to decrease.Despite the fact that the ultimate goal for most countries is to phase out all fossil fuels in heat and power production as well as in the transport sector, the share of renewable energy sources increases only slowly and the world will depend on fossil fuels for many years to come.A rapid move away from fossil fuels could result in great conflicts concerning water and land use between biomass for energy production,food production,and forestation[7]as well as in serious disruption to the global economy[8].The latter is mainly caused by the long lifetime of the energy supply infrastructure.In the transitional period, technologies are sought which will enable the continuous usage of fossil fuels but at the same time eliminate the emission of CO2.1.1.Carbon capture and storageSince power plants constitute large point sources of CO2 emission the main focus is related to their operation.Currently,YearCO2(ppm),N2O(ppb)CH4(ppb)Fig.1.Development in the concentrations of important long-lived greenhouse gases in the atmosphere over the last2000years.The increases in concentrations since about year1750are attributed to human activities in the industrial era.Data taken from[6].M.B.Toftegaard et al./Progress in Energy and Combustion Science36(2010)581e625 582several possible technologies are being investigated which will enable the so called Carbon Capture and Storage (CCS)from power plants [5,8e 14].Both researchers in universities and other research institutions,most manufacturers of boilers and other power plant related equipment,and many power companies are S will act as a complimentary technology to the ongoing work related to increasing fuel ef ficiency and the change toward fuels with lower fossil carbon content,e.g.natural gas and/or biomass.As indicated by the term CCS,the elimination of CO 2emissions include two consecutive operations:1.Capture of CO 2from the power plant flue gas2.Storage of the CO 2(incl.transport to storage site)The estimated cost of separation,capture,and compression of CO 2(point 1)from power plants or other point sources accounts for around 75%of the total cost of a geologic sequestration process [11,15e 17].1.2.Carbon storage technologies overviewThe disposal technology should ensure a complete elimination of the CO 2from the earth's carbon cycle in order to stabilize the CO 2concentration in the atmosphere.Two types of disposal are de fined:sequestration (permanent disposal)or storage (disposal for a signi ficant time period)[7].These terms are often inter-changed in the sense that time periods of more than the order of 10,000years are considered permanent.Possible storage methods suggested include injection in e.g.depleted oil and gas reservoirs,coal beds,deep saline aquifers,etc.[7,11,17e 24].The estimated storage potential for the suggested options is given in Table 2.When CO 2is injected below the caprock in oil and gas reservoirs as well as deep saline aquifers it is first trapped by static and hydrodynamic mechanisms.Secondary trapping mechanisms begin operating over time and act to immobilize the CO 2in the reservoir,thereby signi ficantly limiting the risk of leakage [7,15,24e 26].This type of storage is considered secure even in the initial injection phase where the secondary trapping mechanisms contribute only minimally [7].The large storage potential in deep aquifers without structural traps is only obtainable if the traps are not required for secure storage during the initial phases [19].Even without this storage volume the remaining sites offer storage capability for potentially the next many hundred of years [19,22],see more below.According to Table 2the estimated retention time in the underground storage sites is 105e 106years.The retention time for storage incombination with enhanced oil recovery (EOR)differs between authors and ranges from only 10s of years [20,19]to permanent disposal [7].Because of the limited retention times and the great risks of explosive release of CO 2back into the atmosphere and/or an alteration of the ocean chemistry in the near vicinity of the disposal sites [7]ocean disposal is regarded a less attractive storage solution.A comparison of the estimated CO 2emissions from power production,Table 1,and the estimated storage capacities in EOR and saline aquifers,Table 2,yields between 75and 6000years of storage on a world-wide basis (2.5Gton C/year stored).This calculation is based on the fact that due to small size and remote location of many utility plants only a limited fraction of these emissions can be captured and stored cost-effectively.Baes et al.[18]estimate this fraction to be around 50%.CCS is generally not anticipated as a permanent solution to the elimination of anthro-pogenic CO 2emissions from electricity and heat generation.The lower limit of 75years of storage capacity should thus be suf ficient in order for the industry to change almost entirely toward renew-able sources of energy.1.3.Carbon capture technologies overviewThe identi fied technologies for carbon capture can be divided into four main categories [5,11,12,23,27e 30],described brie fly below.Fig.2shows the main operations concerned with the post-,pre-,and oxy-fuel combustion technologies.Post-combustion capture:CO 2is separated from the flue gas of conventional pulverized-coal-fired power plants.The separation is typically performed via chemical absorption with monoethanol-amine (MEA)or a sterically hindered amine (KS-1)[23,31e 35].Amine absorption is a proven technology in the process industry [23,34,36,37].The demonstrated scale of operation is,however,signi ficantly smaller than the typical size of power plants [34]and serious penalties to the plant ef ficiency exist at the current state of development [5,8,12,16,34,38e 43].The anticipated drop in the net ef ficiency of the power plant is about 10e 14%points [41,34].Some current research projects investigate the possibility ofdevelopingTable 1Estimated CO 2emissions from power generation (Gton C/year).The numbers inTable 2Estimated storage capacities and retention times for CO 2in different types of sinksFig.2.Possible,overall plant con figurations for the three main categories of carbon capture technologies.Adopted from [10].M.B.Toftegaard et al./Progress in Energy and Combustion Science 36(2010)581e 625583more efficient absorbents[35].More on the technology can be seen in[5,8,13,29,44e47].The chilled ammonia process in which an aqueous solution of ammonia constitutes the absorbent has shown promising reduc-tions in energy consumption in laboratory studies,up to50%, compared to the MEA process[42].The process benefits from low operating temperatures and precipitation of ammonium bicar-bonate(NH4HCO3)yielding a higher CO2loading of the absorbent.Retrofit to existing plants for both process types is considered relatively simple since the capture unit can be added downstream of the boiler andflue gas cleaning systems without any significant changes to the original plant[8,45].There are,however,strict requirements for removal of SO2and NO2from theflue gas prior to the CO2capture since these components react irreversibly with the absorbent leading to its degradation.Pre-combustion capture:Also termed fuel decarbonisation.The process is typically suggested to be used in connection with Inte-grated Gasification Combined Cycle(IGCC)power plants where it is termed IGCC e CCS.Coal gasification is applied to obtain a gas (syngas)containing CO,CO2,and H2.The CO is transformed into CO2 by the water-gas shift reaction and can then be separated from the remaining hydrogen containing gas before this is combusted in a gas turbine.Alternatively,H2can be separated from the syngas and the CO combusted in an O2/CO2atmosphere[48].Some techno-economic calculations[11,30,36,49,50]show that IGCC has promising process economics and plant efficiency characteristics. However,high capital costs are associated with plant construction and IGCC plants are generally much more complicated systems than suspension-fired boilers[51,37].Only few electricity producing IGCC units exist[29,50,52e54],none of which are equipped with CCS.As a consequence of the few plants and limited operating experience along with the highly integrated nature of the plants compared to the more matured,conventional pulverized-coal-fired power plants,the demonstrated availability for IGCC is significantly less (80e85%versus w96%,respectively)[5,30,37,50,52,55].IGCC e CCS is not a viable option for retrofit of existing pf plants[30,51,56,57].Oxy-fuel combustion:By eliminating molecular nitrogen from the combustion medium theflue gas will consist mainly of CO2and water.The plant configuration typically suggested involvesflue gas recirculation to the burners to control theflame temperature to within the acceptable limits of the boiler materials.Implementa-tion of the oxy-fuel combustion technology in existing pulverized-coal-fired power plants will induce a larger change of the plant configuration when comparing to the post-combustion absorption processes mentioned above.This is mainly due to the fact that the combustion chemistry is altered by substituting recycledflue gas (mainly CO2and water)for nitrogen in the oxidizer.Several of the earlier techno-economic assessment studies indicate that oxy-fuel combustion should be the most energy and cost efficient of the carbon capture technologies[9,16,38,58e63].This conclusion is mainly based on assumptions of greater boiler efficiency caused by a smallerflue gas volume and the reduced need forflue gas cleaning,i.e.deNO x and desulphurization,including the derived decrease in capital and operating costs.It is suggested that SO x and NO x can be stored along with CO2in the geospheric sinks [8,12,64,65].Typically,no experimental validation of these assumptions has been performed.Whether co-storage of SO x and NO x is politically acceptable is,however,questionable.The main disadvantage of the oxy-fuel combustion technology is the need for almost pure oxygen.The available large-scale technology for air separation is based on cryogenic distillation which will impose a very large energy penalty on the plant[65]. The expected efficiency drop is about7e11percent points,or about 15e30%of the generated electricity(net power output),depending on the initial plant efficiency[5,8,12,16,27,29,43,58,59,66e69].Emerging technologies:Technologies such as membrane sepa-ration,chemical looping combustion,carbonation e calcination cycles,enzyme-based systems,ionic liquids,mineralization,etc. impose the possibility to drastically reduce the cost of electricity and the energy penalty concerned with carbon capture from power plants.The papers by Eide et al.[70],Abu-Khader[28],Hossain and de Lasa[71],and Figueroa et al.[14]provide broad overviews of these technologies and their current state of development.The choice of technology will depend on several factors.First and foremost the economy and the expected development in plant efficiency is of importance.The maturity,expected availability, operatingflexibility,retrofit or green-plant built,local circum-stances,utilities preferences,etc.will likewise have to be taken into account.No general acceptance of superiority of one of the presented technologies over the others exists.Several techno-economic studies also indicate that with the current knowledge on the technologies no significant difference in cost within the limits of precision of the applied cost estimates can be determined between amine absorption capture,coal-based IGCC type capture,and oxy-fuel combustion capture[5,8,22,57,66,67,72].Because of the large changes induced in the power plant by the implementation of oxy-fuel combustion,more research is needed to fully clarify the impacts of the introduction of this technology.Many laboratory scale investigations of the technology have been per-formed within the last two decades and it is generally accepted that it is possible to burn coal and natural gas in an O2/CO2atmosphere.On the other hand,it is likewise recognized that much work still remains in obtaining sufficient insight into the effects on e.g.emissions, residual products such asfly ash,flue gas cleaning,heat transfer,etc.In2005,Wall and coworkers[4]published a literature review on the oxy-fuel combustion technology.The work was updated in the broader CCS review by Wall[5]in2007.The reviews focused mainly on combustion fundamentals,overviews of research groups and their experimental facilities,techno-economic assessments of the technology,and research needs.The amount of literature on the oxy-fuel technology has increased drastically over the latter years and significant new information is thus now available.The objective of the present review has been to summarize the current knowledge status on the oxy-fuel combustion technology.The current review has two focuses.(1)The possible advantages and challenges associated with retrofitting of existing pulverized-coal-fired power plants to the oxy-fuel combustion technology as well as considerations regarding green-field plants.(2)The reported results from labora-tory-and semi-technical scale experiments regarding the combustion process fundamentals,including theflue gas compo-sition and residual products.2.The oxy-fuel combustion technology and retrofit implications2.1.Process overviewIn open literature,oxy-fuel combustion with recirculation offlue gas was proposed almost simultaneously by Horn and Steinberg [58]and Abraham et al.[60]in the early eighties.Abraham et al. proposed the process as a possible mean to produce large amounts of CO2for Enhanced Oil Recovery(EOR)whereas Horn and Stein-berg had in mind the reduction of environmental impacts from the use of fossil fuels in energy generation.As such,the technology received renewed interest in the mid-90s in connection with the re-emerging discussions of global warming caused by increased CO2levels in the atmosphere[12].Oxy-combustion can in principle be applied to any type of fuel utilized for thermal power production.The research interests haveM.B.Toftegaard et al./Progress in Energy and Combustion Science36(2010)581e625 584mainly been focused on coal and natural gas since these are the most abundant fuels.For these speci fic fuels the technology is typically termed oxy-coal and oxy-natural gas combustion,respectively.Application of CCS through oxy-combustion of biomass or blends of coal and biomass will result in a possible mean of extracting CO 2from the atmosphere and thereby possibly inverting the presumed anthropogenic caused changes to the climate [11,23,30].As indicated in Section 1.3a shift from conventional air-firing to oxy-fuel combustion in a power plant will induce multiple changes to the plant con figuration.Fig.3provides a sketch of a coal-fired oxy-fuel plant with indications of the major process steps and the necessary energy inputs and low-temperature-heat outputs new to the plant when retro fitting an existing coal-fired unit.The sketch covers the original state-of-the-art plant with boiler,coal mills,and flue gas cleaning equipment.The final processing of the CO 2stream,i.e.the removal of water and the non-condensible gases like O 2,N 2,Ar,etc.to meet the requirements regarding purity of the CO 2stream,as well as the air separation unit (ASU)and the compres-sion step for the CO 2stream before it is transported to the storage site are new to the plant.The discussion in the coming sections is based on the assumption that an underground geological forma-tion,a saline aquifer,is used as storage site.The type of storage will have an impact on the oxy-fuel process,especially the flue gas puri fication units,through the quality criteria for the CO 2stream.Table 3provides the results of our calculation on the approxi-mate daily flows in and out of a 500MW e oxy-fuel combustion power plant.The calculations are based on a state-of-the-art electrical ef ficiency of 46%of the conventional plant (supercritical steam parameters,LHV basis)[49]with a 10percent point decrease due to oxy-fuel operation.The used reference coal is a high-volatile bituminous coal from Colombia see Table 4for its properties.The oxygen is assumed to have a purity of 100%,in order to simplify the calculations.The combustion is performed in a mixture of 30%O 2in CO 2with an oxygen excess of 10%,corresponding to an oxygenconcentration of 3%in the dry recycle stream.The recycle ratio for the dry flue gas is 0.75.As a preliminary assumption,the condenser will remove 100%of the water in the flue gas.The CO 2capture ef ficiency is w 92%.The remainder of CO 2is vented to the atmo-sphere together with the non-condensable gas species in the exhaust gas from the CO 2cleaning unit.Generally,between 90and 95%capture ef ficiency is expected for oxy-fuel plants [30].The survey of the implications of retro fitting for oxy-fuel combustion in the next sections will be starting at the point of delivery of the sequestration-ready CO 2.The discussion will proceed with the auxiliary units new to the plant and end up with the original parts of the power plant.In order to limit the survey,the discussions,when relevant,will refer to plants utilizing bitu-minous and/or sub-bituminous coals.Speci fic aspects regarding lignite fired plants are excluded.2.2.CO 2purity requirementsThe exact requirements to the quality of the CO 2stream for different storage scenarios are not yet fully clari fied [30,73e 75].Fig.3.Possible con figuration of an oxy-fuel power plant.ASU:Air Separation Unit,SCR:Selective Catalytic Reduction reactor (deNOx),ESP:Electrostatic Precipitator,FGD:Flue Gas Desulphurization.Energy inputs and low-temperature-heat outputs new to the plant in case of a retro fit are indicated.Table 3Approximate mass streams in a 500MW e oxy-fuel combustion power plant with an electric ef ficiency of 36%on a net heating value (LHV)basis.StreamMass Flow (ton/day)Oxygen in 9700Coal in4400Waste water (from condenser)2000Exhaust gas1100CO 2for sequestration 10,300N 2from ASU31,800Table 4Properties for El Cerrejon bituminous coal (Colombian).LHV,as received (MJ/kg)27.09Moisture,as received (wt%) 5.0Proximate analysis (wt%,dry)Ash 10.1Volatile36.7Fixed carbon (by difference)53.2Ultimate analysis (wt%,daf)C 80.70H 5.41N 1.69S0.73O (by difference)11.47Ash composition (wt%,dry)Al 10.89Ca 1.58Fe 5.05K 1.78Mg 1.39Na 0.59P 0.08Si 26.73Ti0.53O (by difference)51.37M.B.Toftegaard et al./Progress in Energy and Combustion Science 36(2010)581e 625585However,Table 5provides a number of suggestions for purity requirements found in the literature.Some authors lay down different criteria for different storage sites [76,78],the differences mainly being associated with the content of water,oxygen and SO 2.Lee and Miller [77]comment on the individual limits with respect to e.g.the minimum miscibility pressure (CO 2,hydrocarbons,and N 2),the risk of corrosion (O 2,water),as well as materials (temperature),operations (glycol),and safety (H 2S).Anheden [76]likewise identi fies the aspects which should be taken into account when determining the individual limits.These aspects come down to operational issues,storage integrity,environmental aspects during the full lifetime of the capture and storage chain,health and safety aspects,legal aspects,and economic considerations.The authors state that the require-ments arising from exposure limits in case of leakage to air put the strictest restrictions to the process and are,at the same time,the easiest to quantify.The exact requirements will most probably be determined for each individual case of capture and storage.Jordal and coworkers [10,74]considered the optimum speci fi-cations with respect to technical and economical considerations.Not surprisingly,the optima differed.For economic reasons,the preferable option is to co-store as many of the impurities;SO x ,NO x ,non-condensable gas species,and water,as possible.This will reduce the plant investment and operating costs of the process.The disadvantage could be the requirement for more expensive mate-rials in pressors and pipelines to withstand the potentially severely corrosive environment.There is,however,an economic optimum for the non-condensables (N 2,O 2,NO,CO,H 2,CH 4,Ar,etc.)since co-storage of these species will increase energy and reservoir size requirements as well as capital and operating expenses in the transport chain with an amount proportional to their concentrations [24,73,74].At the same time the non-condensible gas species will entail an energy and capital penalty when removed from the CO 2stream [73,74].Technically,there are two general issues which should be considered.First,the purity requirements for transport and storage with respect to corrosion and the risk of structural changes within the storage formations caused by impurities in the CO 2stream.Secondly,the limitations to the present best available technology for flue gas cleaning,i.e.particle removal,water condensation,dehydration,SO x removal and removal of non-condensible gas species,and how to minimize the loss of CO 2to the atmosphere during the puri fication process.It is obvious that the technical considerations will set both the lower and upper limits to the purity requirements.SO 2receives the largest amount of interest with respect to the effect of contaminants on the structure of storage formations.A typical assumption regards the possibility of co-storing the SO 2together with the CO 2because of very similar physical and chemical properties at supercritical conditions [10,58,65,67,75,79].However,even small amounts of SO 2may cause problems due to the risk of calcium sulphate formation and thus a decreasing porosity of the reservoir rock [26,75,79,80].Oxygen could likewise lead to the formation of precipitations [74].On the other hand,if the concerns regarding SO 2in the storage formations prove to be insigni ficant there would obviously be a possible economic bene fit from combined capture and storage of CO 2and SO 2[80].The current state of flue gas cleaning on modern power plants involves w 85%removal of NO x ,w 98%removal of SO 2,and w 99.8%removal of particulates [68,30].The fact that only a finite percentage of the SO 2is removed with the current best available technology elucidates the importance of identifying the correct purity demands through e.g.field tests since these may have a signi ficant impact on the plant con figuration,operating conditions and operating costs [43,64].Besides the chemical effects of impurities in the CO 2on the reservoir rock,CO 2itself has the potential to alter the mechanical properties of the rock [26,17].Especially calcite (CaCO 3)precipitation which can cement the reservoir around the injection well and render further injection impossible should be taken into consideration.With respect to transportation the greatest concern involves the water content in the CO 2stream [27,64,73,75].In the presence of water,CO 2can cause so called sweet corrosion [26,17].Water vapor and CO 2in the presence of liquid water can likewise form solid ice-like crystals known as hydrates [64,73,79,80].Concurrent pres-ence of both water and SO 2(incl.H 2S)in the CO 2stream will increase the risk of sulfuric acid corrosion.If the flue gas is dehydrated to a dew point 5 C below the temperature required for transport conditions,the sulphur dioxide will behave almost as carbon dioxide in the supercritical state and the two gases should not cause any corrosion problems [26,79,80].Others report no risk of corrosion at a dew point of less than À60 C [66].A requirement for a very low water content in the CO 2is thus present.This can most likely not be achieved by condensation alone and drying by e.g.absorption in a recyclable dehydrant (triethylene glycol)in combination with the last compression step,see Section 2.3,will be necessary [43,65,74,79].Some researchers believe that all the limiting factors regarding purity of the CO 2stream arise from compression and trans-portation requirements [67,73,74].In this respect,the demand of dryness is crucial.Table 5Suggested CO 2quality speci fications from different sources.ParameterModest quality,aquifer storage High quality,on-shore storage U.S.Speci fications Saline formation Anheden et al.[76]Lee and Miller [77]Fout [78]Pressure110bar 110bar e150bar Temperature 50 C 50 C <50 C eCO 2>96vol%>96vol%>95%Not limited b H 2O <500ppm <50ppm <480ppmv 150ppmv N 2,Ar <4vol%a e<4%Not limited b O 2<4vol%a<100ppm <10ppm <100ppmv SO 2<200mg/Nm 3<50mg/Nm 3e<3vol%H 2S e e <10e 200ppm <1.3vol%NO x e e e Uncertain NH 3e e e Not limited CO e e e Not limited CH 4e e e <0.8vol%HC's e e <5%<5vol%H 2e e eUncertain Glycole e <0.04ppmvea Sum of N 2,O 2,and Ar should be <4vol%.bNo limit but the impacts on compression power and equipment cost need to be considered.M.B.Toftegaard et al./Progress in Energy and Combustion Science 36(2010)581e 625586。
气体再燃低NOx燃烧中NO与NH反应研究
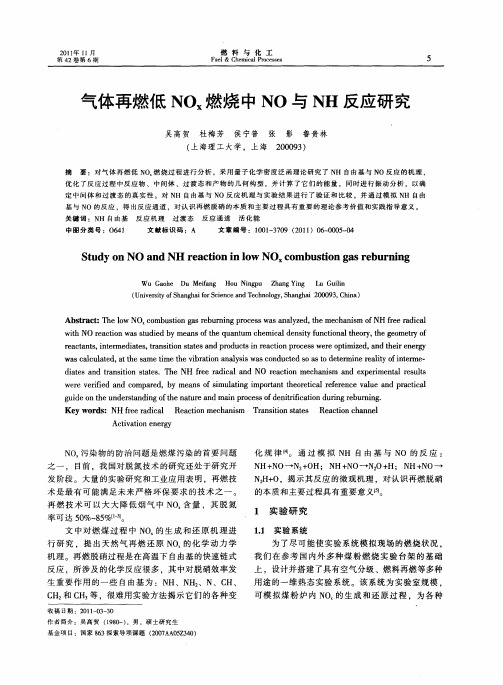
N2 O,揭示 其 反应 的微 观机 理 ,对认 识再 燃 脱硝 H+
的本质 和 主要过 程具 有重 要意 义[ 5 1 。
再 燃 技 术 可 以大 大 降 低 烟 气 中 N 量 ,其 脱 氮 O含
再通 人模 拟高 炉煤气 。待 反应 充分后 ,关 闭三通 阀
图 1 气体 再 燃 试 验 系 统 示 意 图
通 向大气 的开关 ,开 通连 接烟 气分析 仪 的开关 ,进
12 实验 煤种 .
行数 据采 样 。关 闭气 体 阀 门 ,改变 实验 条件 ,准 备
测量 下一 工况 。
实 验 中选 取 了大 同烟煤 ( 、龙 口褐 煤 ( 、 1) 2) 神 府 混煤 ( 3)和晋 城 无 烟煤 ( 4)为 主燃 煤 种 进
ra tn s itr dae ,rn i o tts n rd cs nra t npo esw r p i z d a dter n ry e ca t,neme its t st nsae dp o u t ci rc s e eo t a i a i e o mie , n ie eg h wa ac ltd a esmet evb aina ay i wa o d ce Oa eemierai f ne e sc luae , t h a met irt n lss s n u td S st d tr n e t o tr - t i h o c o l y i m dae n rn i o tts h itsa d t st n sae .T e NH re rdc la d NO ra t n me h ns a d e p r na e ut a i fe a ia n e ci c a im n x ei o me tlrs l s
富氧

Twenty-Seventh Symposium(International)on Combustion/The Combustion Institute,1998/pp.1411–1418 DOMINANT CHEMISTRY AND PHYSICAL FACTORS AFFECTING NO FORMATION AND CONTROL IN OXY-FUEL BURNINGC.J.SUNG and WDepartment of Mechanical and Aerospace EngineeringPrinceton UniversityPrinceton,NJ08544,USANO formation in oxygen-enriched counterflow methane diffusionflames has been computationally stud-ied with detailed chemistry and transport properties.Particular interests are the identification of the dom-inant chemistry in the production of NO and the investigation of the sensitivity of NO production due to effects of air infiltration,fuel contamination,flame radiation,and aerodynamic straining when applying oxy-fuel combustion as a control technique for NO emissions.It is shown that oxygen displacement sig-nificantly modifies the diffusionflame structure from the familiar one obtained with air as the oxidizer, with thermal NO gradually replacing Fenimore NO as the dominant production pathway with increasing oxygen enrichment.Based on GRI-Mech2.11,the net production of NO through the Fenimore mechanism is shown to be negative in oxygen-enriched combustion such that simulation of NO formation in oxy-fuel combustion by considering thermal mechanism alone will yield an overprediction of NO emissions.Im-portant reactions leading to NO formation and destruction are also identified and compared under various levels of oxygen enrichment.It is further demonstrated that NO emission is very sensitive to the extent of air leakage and that it is advantageous to apply oxy-fuel control with even more than0.6%nitrogen contamination of methane,provided that there is no severe air infiltration in the oxidizer stream.For the nonadiabatic oxygen-enriched combustion with radiative heat loss,the net production through Fenimore mechanism is negative over a wide range of strain rate,while NO emissions decrease with increasing strain rate.The study suggests that because NO formation can be substantially reduced with increasing strain rate and because oxy-fuel combustion is more resistant to stretch-induced extinction,the strategy to min-imize effects of air infiltration and fuel contamination is to operate the burner at high turbulence intensities and,thereby,correspondingly high local strain rates.IntroductionA viable control technology for NO x emissions [1,2]is oxy-fuel combustion,which involves the burning of fuel with pure oxygen.Since the com-bustion temperature associated with such intense burning must be necessarily high,successful opera-tion of oxy-fuel burners requires minimum amount of nitrogen contamination either in the fuel stream due to impurities in the fuel supply or in the oxygen stream due to furnace leaks and the failure to main-tain a positive pressure in the combustor and feeding streams[1,3].However,the tolerable levels of con-tamination,as measured against NO x formation from the burning of fuel with air,have not been compre-hensively studied but are needed for the specifica-tions of the purity of oxygen and fuel supplies and for burner design in terms of sealing and positive pressure criteria.For example,it has been shown[3] that,with a0.4%nitrogen contamination of the fuel, the extent of NO emission is still much lower than that produced from a fuel-air burner.It is therefore of interest to explore whether higher levels of con-tamination can be tolerated.Thus,the motivating objective of the present study is to identify the dom-inant chemistry in oxy-fuel combustion and through it provide useful input on the threshold contamina-tion levels.In addition to contamination,there are two aux-iliary physical factors that must also be considered. Thefirst is the influence of the strain rate experi-enced by theflame because it controls the residence time within the reaction zone and consequently the extent of NO x formation.In particular,it is of inter-est to explore possible benefits of high-strain-rate, high-turbulence-intensity operations because of the associated reduction in theflame temperature.The second factor is the influence of radiative loss,which could be substantial for the highflame temperatures in oxy-fuel combustion.Because radiative heat loss and NO x kinetics are both highly nonlinear pro-cesses,it is not clear a priori the extent of influence of radiative loss on NO x formation.The study was conducted computationally through the response of laminar counterflow methane-oxy-gen diffusionflames with various levels of nitrogen addition to the fuel and the oxidizer streams.The computational aspects will be specified in the next14111412NO x FORMATION AND CONTROLsection,which will be followed by presentation anddiscussion of the results.Computational SpecificationsThe mathematical model and the governing equa-tions of the adiabatic,counterflow non-premixed sys-tem employed here follow that of Smooke et al.[4],with the assumption of potentialflow in cylindricalcoordinates.The strain rate j is chosen as the singleparameter to characterize the strainedflow and isdefined as the negative of the axial velocity gradientahead of the thermal mixing layer on the oxidizerside.The inverse of the strain rate represents theglobal characteristic time of theflame.The governing equations and boundary conditionsconstitute a two-point boundary value problem.They are discretized into a system of algebraic equa-tions and solved numerically by modified Newton’smethod used in the one-dimensional premixedflamecode developed by Kee et al.[5].For nonadiabatic situations,radiative heat losswith the optically thin assumption was accounted forCH4,CO2,H2O,and CO.The Planck mean absorp-tion coefficients for the radiating species are givenas a function of temperature in Refs.[6]and[7].Calculations were performed for1atmosphere pres-sure and300K upstream temperature.The reactionmechanism used for methane combustion was takenfrom GRI-Mech 2.11,which is essentially GRI-Mech1.2plus the relevant nitrogen chemistry[8],and was specifically developed and optimized fornatural gas(CH4,C2H6)combustion.A crucial computational requirement is the gen-eration of extinction turning points in an efficientmanner.To accomplish this,we adopted the two-point temperature-controlling method of Nishiokaet al.[9].The main advantage with this approach isthe substantial reduction in CPU time due to theincreased computational stability and the conven-ience of gridding.Results and DiscussionFlame Structure and Dominant ChemistryTo identify the dominant chemistry for differentlevels of oxygen addition,we consider contributionsto the total NO formation from the following fourNO formation mechanisms according to Nishioka etal.[10]:(1)thermal NO(Zeldovich mechanism),(2)prompt NO(Fenimore mechanism),(3)N2O→NO mechanism,and(4)NO2→NO mechanism.Spe-cifically,the thermal NO is separately calculated byusing the methane oxidation kinetics(essentiallyGRI-Mech1.2)plus the Zeldovich mechanism:NםO⇔NםNO(R1)2NםO⇔NOםO(R2)2NםOH⇔NOםH(R3) Contribution of NO formation due to the N2O→NO mechanism is evaluated from the full mecha-nism calculation(GRI-Mech2.11)based on the fol-lowing three reaction steps:N OםO⇔2NO(R4)2N OםH⇔NHםNO(R5)2N OםCO⇔NCOםNO(R6) 2NO formation through the NO2→NO mechanism is determined in a similar manner by considering the following four reactions:NOםOH⇔HOםNO(R7)22NOםM⇔NOםOםM(R8)2NOםO⇔NOםO(R9)22NOםH⇔NOםOH(R10)2Consequently,NO formation from the Fenimore mechanism is determined by subtracting contribu-tions from these three mechanisms(thermal,N2O →NO,and NO2→NO)from the net production. Figure1plots the net emission index of NO and the individual contributions through the four differ-ent mechanisms at various levels of oxygen enrich-ment,characterized by the oxygen mole fraction,␣סO2/(N2םO2),for a given jס100sמ1,which is a representative strain rate for hydrocarbon-air dif-fusionflames under vigorous burning.The blowup plot clarifies the effects of small oxygen addition. The definition of the emission index of NO,EI NO, is that of Takeno and Nishioka[11]:LW x dxNO NOΎEIסNO LמW x dxCH CHΎ44where W k is the molecular weight of species k,x k the molar production rate of species k,and L the separation distance between fuel and oxidizer boundaries.Wefirst note from Fig.1that NO production through the N2O→NO and NO2→NO mecha-nisms is relatively insignificant,a result which holds for all situations studied in the present investigation. As such,our following discussion will only be con-cerned with NO formation through the thermal and Fenimore mechanisms.In accordance with Ref.[10],for air-fuel combus-tion with moderate straining(e.g.,jס100sמ1)suf-ficiently away from the state of extinction,which cor-responds to an extinction strain rate of j extϳ600/s in the present calculations,the major source of NONO FORMATION/CONTROL IN OXY-FUEL BURNING1413F emission index of NO and the individual contribution through four different mechanisms of NO formation at various levels of oxygen enrichment.The blowup plot demonstrates the effects of small ox-ygenaddition.F ig.2.Spatially resolved profiles of temperature and molar production rate of NO through various mechanisms for three representatives of oxygen enrichment:air-fuel combustion,70%oxygen in oxidizer,and99%oxygen in oxidizer.The arrows denote the corresponding location of the stagnation surface.production is prompt NO.However,the tempera-ture-sensitive thermal NO gradually becomes the dominant production pathway with increasing oxy-gen enrichment(beyond25%oxygen)and hence in-creasingflame temperature.Furthermore,it is seen that the net NO production through the Fenimore mechanism becomes negative when oxygen addition exceeds29%and,therefore,assumes a beneficial role in NO reduction.As a corollary,this interesting result also implies that simulation of NO production in oxygen-enriched combustion by considering the thermal mechanism alone could result in overpred-ictions of the net NO emission.Figure2shows the spatially resolved profiles of temperature and molar production rate of NO through the thermal and Fenimore mechanisms for three representative oxygen enrichments,namely, air-fuel combustion,70%oxygen in oxidizer,which is around the maximum EI NO,and oxygen-fuel with about1%air infiltration(99%oxygen in oxidizer). The arrows denote the corresponding locations of the stagnation surface.It isfirst seen that,with increasing oxygen enrich-ment,not only the maximumflame temperature, T max,increases but theflame structure also becomes broader.This broaderflame structure implies a longer local residence time favorable for NO for-mation,despite the same characteristic global resi-dence time due to thefixed strain rate.Results also show that,for all cases studied,NO formation and destruction primarily occurs on the oxidizer side of the stagnation surface where theflame is situated. Furthermore,with increasing oxygen addition and hence increasingflame temperature and thickness, the main reaction zone of NO production,which is basically confined within the high-temperature re-gion,shifts toward the stagnation surface due to the1414NO x FORMATION ANDCONTROLF ig.3.Maximumflame temperature T max and emission index of NO EI NO as functions of the oxygen enrichment and air infiltration for adiabatic and nonadiabatic methane diffusionflames,with jס100sמ1and massflux of fuel kept constant.approximate stoichiometric requirement for the fuel and air gradients at theflame.It is also seen that while air-fuel combustion has only one dominant,positive production peak of NO through the Fenimore mechanism,oxygen-enriched combustion exhibits dual peaks of positive NO for-mation,which are respectively dominated by the Fenimore mechanism situated on the relatively fuel-rich side and the thermal mechanism situated on the relatively fuel-lean side.For all cases of oxygen en-richment,the Fenimore mechanism also serves as the major pathway for NO destruction.Further-more,while the thermal mechanism(R1–R3)solely plays the role of NO production in air-fuel combus-tion,מR1(the reverse reaction of R1)is responsible for part of the NO destruction in oxygen-enriched combustion because the NO concentration becomes larger and hence comparable to those of the impor-tant radicals.The important reaction steps leading to the for-mation and destruction of NO have been identified and are compared for the same three different levels of oxygen enrichment as those of Fig.3.For air-fuel combustion,the major NO destruction is through the Fenimore mechanism and is mainly contributed byHCCOםNO→HCNOםCO(R11)CHםNO→HםHCNO(R12)2CHםNO→HCNםO(R13)CHםNO→HCNםH O(R14)32The importance of R11as well as the associated NO →HCN recycle mechanism in methane-air diffu-sionflames,leading to the negative production of NO,has also been addressed in Ref.[10].It is noted that R13and R14are the reburn reactions of the form CHםNO→HCNםH O,i iמ1iס1and3,respectively In addition,the corresponding positive production is mainly viaםR3,the forward reaction of R3,andHNOםH→HםNO(R15)2Another important reaction accounting for the pro-duction and destruction of NO,in the relatively fuel-rich and fuel-lean sides of the major NO production, respectively,isHםNOםM⇔HNOםM(R16) For oxygen-enriched combustion,in addition to R11–R14,the major NO destruction is contributed byמR1andCHםNO→NםHCO(R17)CםNO→COםN(R18) In contrast to air-fuel combustion,NO production is now mainly contributed by the following three rank-ordered reactions:םR3,מR16,and R15.For the case of70%oxygen,the additional NO production near the oxidizer side becomes comparable with that via the Fenimore mechanism,which is mainly con-tributed by the thermal mechanism,םR3andםR1, as well as the NO2→NO mechanism,םR10.With further increasing oxygen concentration,say beyond 90%oxygen,the positive NO production closer to the stagnation surface is again larger than that near the oxidizer side.Effects of Air InfiltrationHaving identified the dominant chemistry in the production of NO,we now assess in sequence the influences of air infiltration,fuel contamination,flame radiation,andflame stretch on NO production in oxy-fuel combustion.For adiabatic methane flames,Fig.3shows the maximumflame tempera-ture T max and EI NO as functions of the oxygen en-richment and air infiltration,with jס100sמ1and the massflux of fuel kept constant.It is seen that T max monotonically increases with increasing oxygen addition and hence decreasing air leakage.EI NO,on the other hand,increases until about75%oxygen enrichment.Above75%oxygen,the reduction of ni-trogen in the combustion air outweighs the increase inflame temperature,resulting in a net decrease in the amount of NO emitted.It is also noted that with small addition of oxygen,up to30%,T max increases rapidly while the increase in EI NO is relatively gen-tle.This further implies that within this range of ox-ygen enrichment,the temperature-sensitive Zeldov-ich mechanism is not the dominant mode leading to NO formation.Recognizing that the initial increase in NO withNO FORMATION/CONTROL IN OXY-FUEL BURNING1415F emission index of NO and the individual contribution of NO formation through thermal and Feni-more mechanisms as a function of the percent nitrogen in methane for oxygen-fuel combustion,with jס100sמ1 and massflux of fuel kept constant.increasing oxygen enrichment is due to the increas-ing temperature,while its subsequent decrease isdue to availability of nitrogen,it is of interest to notethat the oxygen concentration at which EI NO peaks,␣ס0.75,approximately corresponds to the state determined by assuming all N2is converted to NOand all CH4is converted to CO2and H2O;this stoi-chiometry-based transition␣is0.6when all CH4is assumed to be converted to CO and H2O.Further-more,if hydrogen were used as the fuel and com-plete conversions of N2and H2were assumed,the required␣is0.60.This compares quite well with an additional,detailed chemistry calculation for oxy-hy-drogen combustion,not reported here due to space limitation,showing that EI NO maximizes near0.65 oxygen enrichment.This result then implies that at the maximum EI NO,the formation of NO ceases to be rate sensitive and is largely determined by frozen stoichiometry.Perhaps the most useful insight gained here is thatNO emission is very sensitive to the amount of airinfiltration.It is seen that,with small air leakage inthe oxidizer stream,say1%,the corresponding EI NOisfive times of that emitted from regular air-fuelcombustion.As such,in order to apply oxy-fuel con-trol as compared to the air-fuel combustion,air in-filtration has to be kept below0.2%in oxidizer,asshown in Fig.3.Effects of Fuel ContaminationFigure4plots the various EI NO as a function ofthe nitrogen mole fraction in the methane-nitrogenmixture,with jס100sמ1and massflux of fuel keptconstant.Symbols denote the corresponding valuesfor the burning of air with pure methane.Becausethe small amount of nitrogen contamination has nosignificant effect on theflame-temperature reduc-tion(less than2K within the range of interest),the controlling mechanism and reactions leading to NO production and destruction are similar to those of pure methane with oxygen enrichment,with the Fenimore mechanism asserting a beneficial effect on the overall formation.It is also of interest to note that NO formation increases nearly linearly with in-creasing nitrogen in methane.Furthermore,the re-sults show that,compared to air-fuel combustion,it is advantageous to apply NO control using oxygen-fuel burning even up to0.6%nitrogen contamina-tion in methane with jס100sמ1,if there is no air infiltration in the oxidizer stream.Effects of Flame RadiationAlthough it is not unreasonable to speculate that because of the highflame temperatures associated with oxy-fuel combustion,radiative loss would be significant and its presence could substantially lower theflame temperature and thereby the extent of NO formation,Fig.3shows for jס100sמ1that this is not the case.In contrary,flame radiation does not lead to significant changes in allflame responses, with reductions in T max,peak CO,and EI NO from the corresponding adiabatic conditions being about 0.6%,2%,and9%,respectively.This small reduction in theflame temperature,which leads to the corre-spondingly small reductions in other quantities,is caused by two factors.In the relatively low oxygen enrichment regime,theflame temperature is not high,and radiative loss is therefore not large.In the relatively high oxygen enrichment regime,the“ca-pacitor”effect of product dissociation is in operation in that the potential reduction in theflame tem-perature due to radiative loss is compensated to a large extent by the simultaneous reduction in prod-uct dissociation.In other words,the temperature of a highly dissociatedflame is not sensitive to system perturbations.Furthermore,as a corollary to this re-sult,we note that although soot formation and ra-diation were not included in the present calculations, their effects on theflame temperature and hence the associated NO formation are not expected to signifi-cantly affect the conclusions drawn herein. Effects of Strain RateFigure5plots the variousflame-response prop-erties versus the strain rate,allowing for radiative heat loss,for0.21and0.99oxygen concentrations. It is seen that there exists a complex isola behavior for the air case,with dual turning points and two-staged extinction occurring at the low strain rate re-gime,and a single extinction point at the high strain rate regime.Such an isola response wasfirst re-ported in Ref.[12]and is caused by the following mechanism.Extinction at the high-strain-rate re-gime is well established[13]in that it is brought1416NO x FORMATION ANDCONTROLF ig parison of maximum flame temperature and emission index of NO with strain-rate variations for nona-diabatic methane-air and methane-oxygen-enriched (99%oxygen in oxidizer)diffusionflames.F ig parison of the net emission index of NO and the individual contribution through thermal and Fenimore mechanisms as a function of strain rate,for nonadiabatic methane-air and methane-oxygen-enriched (99%oxygen in oxidizer)diffusion flames.about by the reduced residence time due to the re-duced flame thickness with increasing strain rate.Extinction in the low-strain-rate regime is caused by the increased heat loss and hence reduced flame temperature due to the increased flame thickness with reduced strain rate.These low-strain-rate flames have been observed only under the very spe-cial situations of microgravity [14,15]and are there-fore probably not of practical terrestrial relevance.Focusing now on the high-strain-rate regime for the 0.99oxygen case,we note that although the flame temperature remains minimally affected by the strain rate,again due to the capacitor effect ofproduct dissociation,NO formation is now substan-tially reduced with increasing strain rate and hence reduced residence time for formation.For example,by increasing the strain rate from 100to 1000,5000,and 7000s מ1,EI NO is correspondingly reduced,from 3.06ן10מ3to 3.57ן10מ4,4.92ן10מ5,and 3.42ן10מ5g/g.These reductions and hence results are significant and lead to the following sug-gestion to minimize the effects of nitrogen contam-ination in oxy-fuel combustion.Specifically,because the combustion intensity of these oxy-fuels is ex-tremely high and thereby resistant to stretch-in-duced extinction,and because NO is proportionately reduced with increasing strain rate,the strategy is to operate the burner at high turbulence intensities and thereby correspondingly high local strain rates.We shall return to this possibility in the next section.Figure 6compares the emission indexes of NO as functions of strain rate for the nonadiabatic flames.Here we first note that for the adiabatic methane-air diffusion flames,Ref.[10]has shown that while thermal NO is the major source of NO production for small strain rates,its contribution rapidly de-creases with increasing straining.On the other hand,the Fenimore production first increases and then de-creases gradually [10]and is the dominant mecha-nism of NO production at higher strain rates.For the nonadiabatic methane-air diffusion flames,how-ever,Fig.6shows that thermal NO now also exhibits a nonmonotonic behavior in that,with increasing strain rate,it first increases and then decreases.The initial increase is due to the reduced radiative heat loss as the flame becomes thinner and the flame tem-perature becomes higher.Furthermore,the Feni-more mechanism is now always the dominant path-way for NO production,except for excessively low strain rates around 10s מ1,at which NO production through thermal mechanism becomes comparable with that of Fenimore mechanism.For the nonadiabatic,99%oxygen-enriched flames,Fig.6demonstrates that thermal mechanism is the main source of NO production,whereas the Fenimore mechanism is the major pathway for NO destruction,except for exceedingly small strain rates (j Ͻ1.5s מ1).NO Reduction under High Strain RatesRecognizing the potential benefit of operation un-der high strain rates,as discussed earlier,it behooves us to re-assess the effects of air infiltration and fuel contamination under such situations.Figure 7shows the calculated EI NO for the radiative flames with strain rates of 100,2000,and 5000s מ1as functions of air infiltration and fuel contamination.In the fig-ure,we have also marked off the NO emission levels for methane-air flames with strain rates of 100and 551s מ1,with the latter being the extinction strain rate.The operation strain-rate range of methane-airNO FORMATION/CONTROL IN OXY-FUEL BURNING1417F ig.7.Emission index of NO as functions of the air infiltration and fuel contamination for nonadiabatic meth-ane diffusionflames,with jס100,2000,and5000sמ1 and massflux of fuel kept constant for the corresponding strain rate.The representing operation range for the reg-ular air-fuel burning is bounded between jס100and j ext ס551sמ1.burning can be considered to be bounded by thesetwo paring to the relatively strong air-fuelflames,jס100sמ1,the tolerable level of airleakage for oxy-fuel burning can now be up to5%for jס2000sמ1and much more than10%with j ס5000sמ1.Furthermore,Fig.7shows that with increasing strain rate,the tolerable level for fuel con-tamination can be much higher than1%.Therefore,it is advantageous to operate oxy-fuel burning underhigh strain rates in order to minimize the effects ofnitrogen contamination.It is important to emphasizethat operation under such high-strain-rate situationsis entirely reasonable and realizable because theflame is far from the state of extinction for suchstrongly burning oxy-fuelflames.Concluding RemarksIn the present study,we have computationally in-vestigated the sensitivity of NO formation in oxy-fuelcombustion due to the effects of air infiltration,fuelcontamination,flame radiation,and strain rate,al-lowing for detailed chemistry and transport includ-ingflame radiation.In addition,recognizing that thediffusionflame structure is strongly influenced byreactant composition,flame temperature,and aero-dynamic straining and that there exists a strong cou-pling between primary and pollutant species chem-istry,the controlling pathways and mechanism leading to NO formation were systematically iden-tified at various conditions.Specifically,we have found that the major source of NO production is prompt NO with air-fuel com-bustion.Temperature-sensitive thermal NO gradu-ally becomes the dominant production pathway with increasing oxygen enrichment.Over a wide range of strain rate,for the oxygen-enriched combustion,the net production through Fenimore mechanism is negative,whereas the net production via thermal mechanism is larger than the total NO emissions. This suggests that simulation of NO production in oxygen-enriched combustion by considering the thermal mechanism alone will lead to a significant overprediction of the net emissions of NO.In terms of the effects of air infiltration,NO emis-sions are found to be very sensitive to the amount of air leakage.With small air leakage in the oxidizer stream,the corresponding NO emissions can be much larger than that emitted in the regular air-fuel combustion,under the same straining condition. Therefore,it is imperative to prevent the entering of atmospheric nitrogen into the combustion system when applying oxygen-fuel controls.Regarding the effects of fuel contamination,under the same straining condition,oxy-fuel combustion yields smaller NO emissions even with0.6%contam-ination of nitrogen in methane,if there is no signifi-cant air leakage.While the degree of fuel contami-nation depends on the source of supply,relatively speaking,the effects of fuel contamination on NO emissions is less severe than that of air infiltration. Radiative heat loss does not seem to significantly affect theflame temperature because of the capac-itor effect due to product dissociation for such strongly burningflames.It can,however,causeflame extinction at very small strain rates that are not of interest for practical situations.Perhaps the most practically significant result from the present study is the recognition that while the flame temperature may not be substantially reduced with increasing strain rate for high oxygen concen-tration situations,the residence time is reduced and hence can lead to significant reduction in NO for-mation.This has led us to propose that a viable strat-egy to minimize the effects of air infiltration and fuel contamination is to operate the oxy-fuel burner at high turbulence intensities and,thereby,corre-spondingly high local strain rates,because of the as-sociated high combustion intensity that is resistant to stretch-induced extinction.Finally,we caution that application of the present results to the practical situations of turbulentflames in burners should recognize the facts that the pres-ent study is most relevant to the laminarflamelet regime of turbulentflames,that the simulation was conducted with certain assumptions such as the specific chemical mechanism adopted and radiative transfer being optically thin,and that a controlled。
350MW_燃煤锅炉在富氧下掺烧生物质气的数值模拟

Modeling and Simulation 建模与仿真, 2023, 12(5), 4294-4304 Published Online September 2023 in Hans. https:///journal/mos https:///10.12677/mos.2023.125392350MW 燃煤锅炉在富氧下掺烧生物质气的数值模拟曹广懿德,陈 帅*,胡 超上海工程技术大学机械与汽车工程学院,上海收稿日期:2023年6月29日;录用日期:2023年8月28日;发布日期:2023年9月4日摘要为了研究火力燃煤锅炉的碳减排与低氮燃烧技术,本文通过数值模拟方法研究了不同O 2/CO 2体积分数比的富氧条件下四角切圆锅炉内生物质气与煤粉混燃情况。
结果表明:当O 2浓度高于29%时,炉膛整体速度梯度提高,有利于煤粉的充分混合燃烧,从而改善了煤粉的燃烧特性;随着O 2/CO 2体积分数比的增加,炉膛内温度整体是提高的,有利于提高炉膛内的换热性能;随着O 2/CO 2体积分数比的增加,炉膛内整体的CO 2浓度逐渐提高,炉膛出口的CO 2浓度是70%~77%,有利于CO 2的捕集,同时,炉膛内NOx 的浓度也逐渐提高,主要原因是炉膛内的温度随着O 2浓度的增加而上升,由此热力型NOx 的产生量更大。
关键词富氧燃烧,生物质气,掺烧比,数值模拟Numerical Simulation of Biomass Gas Blending in 350MW Coal-Fired Boiler under Oxygen EnrichmentGuangyide Cao, Shuai Chen *, Chao HuSchool of Mechanical and Automotive Engineering, Shanghai University of Engineering Science, ShanghaiReceived: Jun. 29th , 2023; accepted: Aug. 28th , 2023; published: Sep. 4th , 2023AbstractIn order to study the carbon reduction and low-NOx combustion technology of thermal coal-fired boiler, this paper investigates the mixing and combustion of biomass gas and pulverized coal in a*通讯作者。
2010-26-EU-欧盟新排放指令

DIRECTIVESCOMMISSION DIRECTIVE 2010/26/EUof 31 March 2010amending Directive 97/68/EC of the European Parliament and of the Council on the approximation of the laws of the Member States relating to measures against the emission of gaseous and particulate pollutants from internal combustion engines to be installed in non-road mobile machinery(Text with EEA relevance)THE EUROPEAN COMMISSION, Having regard to the Treaty on the Functioning of the European Union,Having regard to Directive 97/68/EC of 16 December 1997 of the European Parliament and of the Council on the approxi mation of the laws of the Member States relating to measures against the emission of gaseous and particulate pollutants from internal combustion engines to be installed in non-road mobile machinery ( 1 ), and in particular Articles 14 and 14a thereof, Whereas:(1) Article 14a of Directive 97/68/EC sets out the criteria and the procedure for extending the period referred to in Article 9a(7) of that Directive. Studies carried out in accordance with Article 14a of Directive 97/68/EC show that there are substantial technical difficulties to comply with stage II requirements for professional use, multi- positional, hand-held mobile machinery in which engines of classes SH:2 and SH:3 are installed. It is therefore necessary to extend the period referred to in Article 9a(7) until 31 July 2013. (2) Since the amendment of Directive 97/68/EC in 2004, technical progress has been made in the design of diesel engines with a view to make them compliant with the exhaust emission limits for stages IIIB and IV. Electronically controlled engines, largely replacing me- chanically controlled fuel injection and control systems, have been developed. Therefore, the current general type- approval requirements in Annex I to Directive 97/68/EC should be adapted accordingly and general type-approval requirements for stages IIIB and IV should be introduced. (3) Annex II to Directive 97/68/EC specifies the technical details of the information documents that need to be submitted by the manufacturer to the type-approval authority with the application for engine type-approval. The details specified regarding the additional anti- pollution devices are generic and should be adapted to the specific after-treatment systems that need to be used to ensure that engines comply with exhaust emission limit stages IIIB and IV. More detailed information on the after-treatment devices installed on the engines should be submitted to enable type-approval authorities to assess the engine’s capability to comply with stages IIIB and IV.(4) Annex III to Directive 97/68/EC sets out the methodtesting the engines and determining their level of emissions of gaseous and particulate pollutants. The type-approval testing procedure of engines to demon strate compliance with the exhaust emission limits of stage IIIB and IV should ensure that the simultaneous compliance with the gaseous (carbon monoxide, hydro carbons, oxides of nitrogen) and the particulate emission limits is demonstrated. The non-road steady cycle (NRSC) and non-road transient cycle (NRTC) should be adapted accordingly. (5) Point 1.3.2 of Annex III to Directive 97/68/EC foreseesthe modification of the symbols (section 2.18 of Annex I), the test sequence (Annex III) and calculation equations (Appendix III to Annex III), prior to the introduction of the cold/hot composite test sequence. The type approval procedure to demonstrate compliance with the exhaust emission limits of stage IIIB and IV requires the intro duction of a detailed description of the cold start cycle. (6) Section 3.7.1 of Annex III to Directive 97/68/EC sets out the test cycle for the different equipment specifications. The test cycle under point 3.7.1.1 (specification A) needs to be adapted to clarify which engine speed needs to be used in the type approval calculation method. It is also necessary to adapt the reference to the updated version of the international testing standard ISO 8178-4:2007.( 1 ) OJ L 59, 27.2.1998, p. 1.(7) Section 4.5 of Annex III to Directive 97/68/EC outlines the emissions test run. This section needs to be adapted to take account of the cold start cycle. (8) Appendix 3 of Annex III to Directive 97/68/EC sets out the criteria for the data evaluation and calculation of the gaseous emissions and the particulate emissions, for both the NRSC test and the NRTC test set out in Annex III. The type approval of engines in accordance with stage IIIB and IV requires the adaptation of the calculation method for the NRTC test. (9) Annex XIII to Directive 97/68/EC sets out the provisions for engines placed on the market under a ‘flexible scheme’. To ensure a smooth implementation of stage IIIB, an increased use of this flexibility scheme may be needed. Therefore, the adaptation to technical progress to enable the introduction of stage IIIB compliant engines needs to be accompanied by measures to avoid that the use of the flexibility scheme may be hampered by notifi cation requirements which are no longer adapted to the introduction of such engines. The measures should aim at simplifying the notification requirements and the reporting obligations, and at making them more focused and tailored to the need for market surveillance authorities to respond to the increased use of the flexi bility scheme that will result from the introduction of stage IIIB. (10) Since Directive 97/68/EC provides for the type-approval of stage IIIB engines (category L) as from 1 January 2010 it is necessary to provide for the possibility to grant type approval from that date. (11) For reasons of legal certainty this Directive should enter into force as a matter of urgency. (12) The measures provided for in this Directive are in accordance with the opinion of the Committee estab lished in Article 15(1) of Directive 97/68/EC, HAS ADOPTED THIS DIRECTIVE: Article 1 Amendments to Directive 97/68/EC Directive 97/68/EC is amended as follows: 1. in Article 9a(7), the following subparagraph is added: ‘Notwithstanding the first subparagraph, an extension of the derogation period is granted until 31 July 2013, within the category of top handle machines, for professional use, multi- positional, hand-held hedge trimmers and top handle tree service chainsaws in which engines of classes SH:2 and SH:3 are installed.’;2. Annex I is amended in accordance with Annex I to this Directive;3. Annex II is amended in accordance with Annex II to this Directive;4. Annex III is amended in accordance with Annex III to this Directive;5. Annex V is amended in accordance to Annex IV to this Directive;6. Annex XIII is amended in accordance with Annex V to this Directive.Article 2Transitional provisionWith effect from the day following the publication of this Directive in the Official Journal, Member States may grant type-approval in respect of electronically controlled engines which comply with the requirements laid down in Annexes I, II, III, V and XIII to Directive 97/68/EC, as amended by this Directive.Article 3Transposition1. Member States shall bring into force the laws, regulations and administrative provisions necessary to comply with the Directive within 12 months after the publication of the Directive. They shall forthwith communicate to the Commission the text of those provisions.They shall apply those provisions from 31 March 2011.When Member States adopt those provisions, they shall contain a reference to this Directive or be accompanied by such a reference on the occasion of their official publication. Member States shall determine how such reference is to be made.2. Member States shall communicate to the Commission the text of the main provisions of national law which they adopt in the field covered by this Directive.Article 4Entry into forceThis Directive shall enter into force on the day following its publication in the Official Journal of the European Union .Article 5AddresseesThis Directive is addressed to the Member States. Done at Brussels, 31 March 2010. For the Commission The President José Manuel BARROSOANNEX IThe following section 8 is added to Annex I to Directive 97/68/EC:IIIBIVSTAGESANDFOR‘8. TYPEAPPROVALREQUIREMENTS8.1. This section shall apply to the type-approval of electronically controlled engines, which uses electronic control todetermine both the quantity and timing of injecting fuel (hereafter “engine”). This section shall apply irrespective of the technology applied to such engines to comply with the emission limit values set out in sections 4.1.2.5 and 4.1.2.6 of this Annex.8.2. DefinitionsFor the purpose of this section, the following definitions shall apply:8.2.1. “emission control strategy” means a combination of an emission control system with one base emission controlstrategy and with one set of auxiliary emission control strategies, incorporated into the overall design of an engine or non-road mobile machinery into which the engine is installed.8.2.2. “reagent” means any consumable or non-recoverable medium required and used for the effective operation of theexhaust after-treatment system.8.3. Generalrequirements8.3.1. Requirements for base emission control strategy8.3.1.1. The base emission control strategy, activated throughout the speed and torque operating range of the engine,shall be designed as to enable the engine to comply with the provisions of this Directive8.3.1.2. Any base emission control strategy that can distinguish engine operation between a standardised type approvaltest and other operating conditions and subsequently reduce the level of emission control when not operating under conditions substantially included in the type approval procedure is prohibited.8.3.2. Requirements for auxiliary emission control strategy8.3.2.1. An auxiliary emission control strategy may be used by an engine or a non-road mobile machine, provided thatthe auxiliary emission control strategy, when activated, modifies the base emission control strategy in response toa specific set of ambient and/or operating conditions but does not permanently reduce the effectiveness of theemission control system:(a) where the auxiliary emission control strategy is activated during the type approval test, sections 8.3.2.2 and8.3.2.3 shall not apply;(b) where the auxiliary emission control strategy is not activated during the type approval test, it must bedemonstrated that the auxiliary emission control strategy is active only for as long as required for thepurposes identified in section 8.3.2.3.8.3.2.2. The control conditions applicable to this section are all of the following:(a) an altitude not exceeding 1 000 metres (or equivalent atmospheric pressure of 90 kPa);(b) an ambient temperature within the range 275 K to 303 K (2 °C to 30 °C);(c) the engine coolant temperature above 343 K (70 °C).Where the auxiliary emission control strategy is activated when the engine is operating within the control conditions set out in points (a), (b) and (c), the strategy shall only be activated exceptionally.8.3.2.3. An auxiliary emission control strategy may be activated in particular for the following purposes:(a) by onboard signals, for protecting the engine (including air-handling device protection) and/or non-roadmobile machine into which the engine is installed from damage;(b) for operational safety and strategies;(c) for prevention of excessive emissions, during cold start or warming-up, during shut-down;(d) if used to trade-off the control of one regulated pollutant under specific ambient or operating conditions, formaintaining control of all other regulated pollutants, within the emission limit values that are appropriate forthe engine concerned. The purpose is to compensate for naturally occurring phenomena in a manner thatprovides acceptable control of all emission constituents.8.3.2.4. The manufacturer shall demonstrate to the technical service at the time of the type-approval test that theoperation of any auxiliary emission strategy complies with the provisions of section 8.3.2. The demonstration shall consist of an evaluation of the documentation referred to in section 8.3.3.8.3.2.5. Any operation of an auxiliary emission control strategy not compliant with section 8.3.2 is prohibited.8.3.3. Documentation requirements8.3.3.1. The manufacturer shall provide an information folder accompanying the application for type-approval at thetime of submission to the technical service, which ensures access to any element of design and emission control strategy and the means by which the auxiliary strategy directly or indirectly controls the output variables. The information folder shall be made available in two parts:(a) the documentation package, annexed to the application for type-approval, shall include a full overview of theemission control strategy. Evidence shall be provided that all outputs permitted by a matrix, obtained fromthe range of control of the individual unit inputs, have been identified. This evidence shall be attached to theinformation folder as referred to in Annex II;(b) the additional material, presented to the technical service but not annexed to the application for type-approval, shall include all the modified parameters by any auxiliary emission control strategy and theboundary conditions under which this strategy operates and in particular:(i) a description of the control logic and of timing strategies and switch points, during all modes ofoperation for the fuel and other essential systems, resulting in effective emissions control (such asexhaust gas recirculation system (EGR) or reagent dosing);(ii) a justification for the use of any auxiliary emission control strategy applied to the engine, accompanied by material and test data, demonstrating the effect on exhaust emissions. This justification may be basedon test data, sound engineering analysis, or a combination of both;(iii) a detailed description of algorithms or sensors (where applicable) used for identifying, analysing, or diagnosing incorrect operation of the NO x control system;(iv) the tolerance used to satisfy the requirements in section 8.4.7.2, regardless of the used means.8.3.3.2. The additional material referred to in point (b) of section 8.3.3.1 shall be treated as strictly confidential. It shallbe made available to the type-approval authority on request. The type-approval authority shall treat this material as confidential.ofoperationNO x control measures8.4. Requirementstoensurecorrect8.4.1. The manufacturer shall provide information that fully describes the functional operational characteristics of theNO x control measures using the documents set out in section 2 of Appendix 1 to Annex II and in section 2 of Appendix 3 to Annex II.8.4.2. If the emission control system requires a reagent, the characteristics of that reagent, including the type of reagent,information on concentration when the reagent is in solution, operational temperature conditions and reference to international standards for composition and quality must be specified by the manufacturer, in section 2.2.1.13 of Appendix 1 and in section 2.2.1.13 of Appendix 3 to Annex II.8.4.3. The engine emission control strategy shall be operational under all environmental conditions regularly pertainingin the territory of the Community, especially at low ambient temperatures.8.4.4. The manufacturer shall demonstrate that the emission of ammonia during the applicable emission test cycle ofthe type approval procedure, when a reagent is used, does not exceed a mean value of 25 ppm.8.4.5. If separate reagent containers are installed on or connected to a non-road mobile machine, means for taking asample of the reagent inside the containers must be included. The sampling point must be easily accessible without requiring the use of any specialised tool or device.8.4.6. Use and maintenance requirements8.4.6.1. The type approval shall be made conditional, in accordance with Article 4(3), upon providing to each operator ofnon-road mobile machinery written instructions comprising the following:(a) detailed warnings, explaining possible malfunctions generated by incorrect operation, use or maintenance ofthe installed engine, accompanied by respective rectification measures;(b) detailed warnings on the incorrect use of the machine resulting in possible malfunctions of the engine,accompanied by respective rectification measures;(c) information on the correct use of the reagent, accompanied by an instruction on refilling the reagentbetween normal maintenance intervals;(d) a clear warning, that the type-approval certificate, issued for the type of engine concerned, is valid only whenall of the following conditions are met:(i) the engine is operated, used and maintained in accordance with the instructions provided;(ii) prompt action has been taken for rectifying incorrect operation, use or maintenance in accordance with the rectification measures indicated by the warnings referred to in point (a) and (b);(iii) no deliberate misuse of the engine has taken place, in particular deactivating or not maintaining an EGR or reagent dosing system.The instructions shall be written in a clear and non-technical manner using the same language as is used in the operator’s manual on non-road mobile machinery or engine.8.4.7. Reagent control (where applicable)8.4.7.1. The type approval shall be made conditional, in accordance with the provisions of section 3 of Article 4, uponproviding indicators or other appropriate means, according to the configuration of the non-road mobile machinery, informing the operator on:(a) the amount of reagent remaining in the reagent storage container and by an additional specific signal, whenthe remaining reagent is less than 10 % of the full container’s capacity;(b) when the reagent container becomes empty, or almost empty;(c) when the reagent in the storage tank does not comply with the characteristics declared and recorded insection 2.2.1.13 of Appendix 1 and section 2.2.1.13 of Appendix 3 to Annex II, according to the installedmeans of assessment.(d) when the dosing activity of the reagent is interrupted, in cases other than those executed by the engine ECUor the dosing controller, reacting to engine operating conditions where the dosing is not required, providedthat these operating conditions are made available to the type approval authority.8.4.7.2. By the choice of the manufacturer the requirements of reagent compliance with the declared characteristics andthe associated NO x emission tolerance shall be satisfied by one of the following means:(a) direct means, such as the use of a reagent quality sensor.(b) indirect means, such as the use of a NO x sensor in the exhaust to evaluate reagent effectiveness.(c) any other means, provided that its efficacy is at least equal to the one resulting by the use of the means ofpoints (a) or (b) and the main requirements of this section are maintained.’ANNEX IIAnnex II to Directive 97/68/EC is amended as follows:1. Section 2 of Appendix 1 is replaced by the following:POLLUTIONAIRAGAINSTTAKEN‘2. MEASURESyes/no(*)............................................................................................................gases:recyclingcrankcase2.1. Deviceforcoverednotbyheading)ifanother(ifanti-pollutiondevices2.2. Additionalandany,(*)yes/noconverter:2.2.1. Catalytic.......................................................................................................................................................................................2.2.1.1. Make(s):........................................................................................................................................................................................2.2.1.2. Type(s):converterselements................................................................................................................andcatalytic2.2.1.3. Numberofconverter(s):...............................................................................................thecatalyticofandvolume2.2.1.4. Dimensions-........................................................................................................................................................action:ofcatalytic2.2.1.5. Typeprecious........................................................................................................................................metals:of2.2.1.6. Totalchargeconcentration:...........................................................................................................................................................2.2.1.7. Relative.....................................................................................................................................material):and2.2.1.8. Substrate(structure...............................................................................................................................................................................2.2.1.9. Celldensity:2.2.1.10. Type of casing for the catalytic converter(s): .................................................................................................................2.2.1.11. Location of the catalytic converter(s) (place(s) and maximum/minimum distance(s) from engine): ............2.2.1.12. Normal operating range (K): ................................................................................................................................................2.2.1.13. Consumable reagent (where appropriate): .......................................................................................................................2.2.1.13.1. Type and concentration of reagent needed for catalytic action: .............................................................................2.2.1.13.2. Normal operational temperature range of reagent: ......................................................................................................2.2.1.13.3. International standard (where appropriate): ....................................................................................................................2.2.1.14. NO x sensor: yes/no (*)(*)yes/nosensor:2.2.2. Oxygen.......................................................................................................................................................................................2.2.2.1. Make(s):............................................................................................................................................................................................2.2.2.2. Type:.....................................................................................................................................................................................2.2.2.3. Location:(*)yes/noinjection:2.2.3. Airetc.):.........................................................................................................................................pump,2.2.3.1. Type(pulseair,air(*)yes/no2.2.4. EGR:etc.):pressure,........................................................................2.2.4.1. Characteristicspressure/low(cooled/uncooled,high(*)yes/no2.2.5. Particulatetrap:particulate.........................................................................................................thetrap:capacityof2.2.5.1. Dimensionsandparticulatetrap:.........................................................................................................................theandof2.2.5.2. Typedesignengine):..................................................................fromdistance(s)2.2.5.3. Locationand(place(s)maximum/minimumdescriptionand/ordrawing:regeneration,............................................................................ofor2.2.5.4. Methodsystempressure(kPa)and..................................................................................range:2.2.5.5. Normal(K)operatingtemperature(*)yes/nosystems:2.2.6. Otheroperation:...................................................................................................................................................and2.2.6.1. Description___________(*) Strike out what does not apply.’2. Section 2 of Appendix 3 is replaced by the following:POLLUTIONAGAINSTAIRTAKEN‘2. MEASURESyes/no(*)............................................................................................................gases:crankcase2.1. Deviceforrecyclingcoverednotbyheading)ifanotherany,anti-pollutiondevices(ifand2.2. Additional(*)yes/noconverter:2.2.1. Catalytic.......................................................................................................................................................................................2.2.1.1. Make(s):........................................................................................................................................................................................2.2.1.2. Type(s):and................................................................................................................converterselementscatalyticof2.2.1.3. Numberconverter(s):...............................................................................................thecatalyticofandvolume2.2.1.4. Dimensions-........................................................................................................................................................action:ofcatalytic2.2.1.5. Typeprecious........................................................................................................................................metals:of2.2.1.6. Totalchargeconcentration:...........................................................................................................................................................2.2.1.7. Relative.....................................................................................................................................material):and2.2.1.8. Substrate(structure...............................................................................................................................................................................2.2.1.9. Celldensity:2.2.1.10. Type of casing for the catalytic converter(s): .................................................................................................................2.2.1.11. Location of the catalytic converter(s) (place(s) and maximum/minimum distance(s) from engine): ............2.2.1.12. Normal operating range (K) .................................................................................................................................................2.2.1.13. Consumable reagent (where appropriate): .......................................................................................................................2.2.1.13.1. Type and concentration of reagent needed for catalytic action: .............................................................................2.2.1.13.2. Normal operational temperature range of reagent: ......................................................................................................2.2.1.13.3. International standard (where appropriate): ....................................................................................................................2.2.1.14. NO x sensor: yes/no (*)yes/no(*)sensor:2.2.2. Oxygen.......................................................................................................................................................................................2.2.2.1. Make(s):............................................................................................................................................................................................2.2.2.2. Type:.....................................................................................................................................................................................2.2.2.3. Location:(*)yes/noinjection:2.2.3. Airetc.):.........................................................................................................................................pump,2.2.3.1. Type(pulseair,air(*)yes/no2.2.4. EGR:etc.):pressure,........................................................................2.2.4.1. Characteristicspressure/low(cooled/uncooled,high(*)yes/no2.2.5. Particulatetrap:particulate.........................................................................................................thetrap:capacityof2.2.5.1. Dimensionsandparticulatetrap:.........................................................................................................................theandof2.2.5.2. Typedesignengine):..................................................................fromdistance(s)2.2.5.3. Locationand(place(s)maximum/minimumdescriptionand/ordrawing:regeneration,............................................................................ofor2.2.5.4. Methodsystempressure(kPa)and..................................................................................range:2.2.5.5. Normal(K)operatingtemperature(*)yes/nosystems:2.2.6. Otheroperation:...................................................................................................................................................and2.2.6.1. Description___________(*) Strike out what does not apply.’。
全氧烧嘴-速焰英国

R
a
E-mail:solution@ Tel:021-58814569 Fax:021-51685084
p
idflamechin a
694
Industrial Burners Handbook
21.1 INTRODUCTION
R
21.2.1.1 High Flame Temperature and Heat Transfer High adiabatic flame temperature and high heat release rate and transfer are the main benefits for which traditional applications of oxy-fuel burners were developed. Welding with an oxy-acetylene flame, flame polishing of glass surfaces, and oxygen cutting of steel plates are some of examples of applications that take advantage of these oxy-fuel flame characteristics. 21.2.1.2 Fuel Savings The use of oxygen in a heating process eliminates the nitrogen introduced with combustion air from the process and hence eliminates the energy required to heat the nitrogen from inlet temperature to outlet temperature. For high-temperature processes (>2200°F or 1200°C) with no heat recovery, fuel savings when using oxygen can exceed 50%. As heat recovery is employed with the air combustion system, the savings achievable when switching to oxy-fuel combustion are reduced. A simple heat and mass balance on the furnace under each operating condition can provide accurate
高含量氮掺杂碳纳米管的合成及NO电氧化
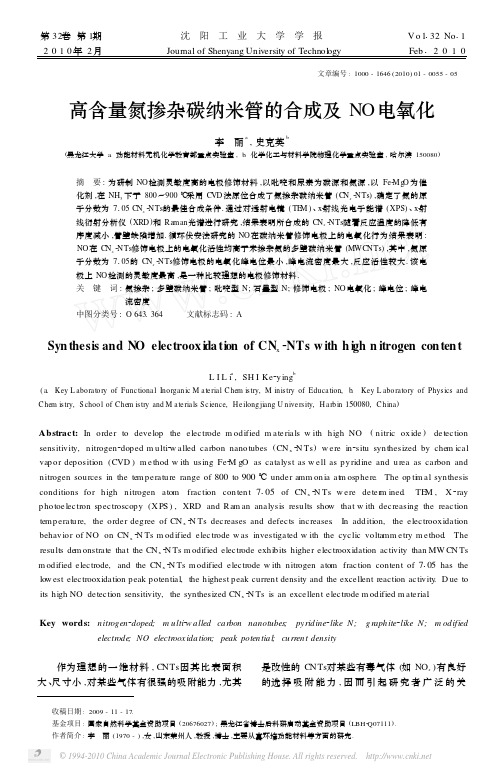
Abstract: In o rde r to develop the elec trode m od ified m a te rials w ith h igh NO ( n itric ox ide ) de tection sensitiv ity, n itrogen2dop ed m u lti2w alled ca rbon nano tubes ( CN x 2N Ts) w ere in2situ syn thesized by chem ical vap o r dep osition (CVD ) m e thod w ith using Fe2M gO as cata lyst as w e ll as p y rid ine and u rea as ca rbon and n itrogen sou rces in the tem p era tu re range of 800 to 900 ℃ under amm on ia atm osp he re. The op tim al syn thesis cond itions fo r h igh n itrogen atom frac tion con ten t 7105 of CN x 2N Ts w ere dete rm ined. TEM , X 2ray p ho toe lectron sp ectroscop y (X PS ) , XRD and R am an analysis resu lts show that w ith decreasing the reaction tem p eratu re, the o rder deg ree of CN x 2N Ts decreases and defects increases. In add ition, the e lectroox idation behav io r of NO on CN x 2N Ts m od ified elec trode w as investiga ted w ith the cyc lic vo ltamm e try m ethod. The resu lts dem onstrate that the CNx 2N Ts m odified electrode exhibits higher electrooxidation activity than MW CN Ts m odified electrode, and the CNx 2N Ts m odified electrode w ith nitrogen atom fraction content of 7105 has the low est electrooxidation peak potential, the highest peak current density and the excellent reaction activity. D ue to its high NO detection sensitivity, the synthesized CNx 2N Ts is an excellent electrode m odified m aterial.
- 1、下载文档前请自行甄别文档内容的完整性,平台不提供额外的编辑、内容补充、找答案等附加服务。
- 2、"仅部分预览"的文档,不可在线预览部分如存在完整性等问题,可反馈申请退款(可完整预览的文档不适用该条件!)。
- 3、如文档侵犯您的权益,请联系客服反馈,我们会尽快为您处理(人工客服工作时间:9:00-18:30)。
NO reduction in 0.03–0.2MW oxy-fuel combustorusing flue gas recirculation technologyHo Keun Kim a ,Yongmo Kima,*,Sang Min Lee b ,Kook Young AhnbaDepartment of Mechanical Engineering,Hanyang University,17,Haengdang-Dong,Seongdong-Ku,Seoul 133-792,Republic of KoreabEco-Machinery Engineering Department,Korea Institute of Machinery and Materials,Jang-Dong 171,Yusung-Ku,Taejon 305-660,Republic of KoreaAbstractIn the present study,the NO emission characteristics have been experimentally investigated for the oxy-fuel combustors using flue gas recirculation (FGR)technology.In order to find the optimal inlet arrange-ment and operating conditions of the FGR oxy-fuel combustor,the flame stability tests have been carried out for various oxy-fuel combustor.The oxy-fuel combustor with two separate oxidizer nozzles yields the most stable flames in a wide range of CO 2ratios.The NO emission characteristics are also experimentally analyzed for the various operating conditions of 0.03and 0.2MW FGR oxy-fuel combustors.Based on experimental results,the detailed discussions have been made for the effects of CO 2ratio,FGR ratio,and oxygen flow-rate ratio on the NO emission.When the 0.03MW oxy-fuel combustor is operated at the 40%FGR ratio,the NO emission level is below 30ppm and the reduction ratio of NO emission is approximately 93%.In the 0.2MW FGR oxy-fuel combustors operated at the 40%FGR ratio,the NO emission level is below 150ppm and the reduction ratio of NO emission is approximately 85%.Experimen-tal results clearly indicate that the present FGR technology is quite effective for reducing the NO emission in the oxy-fuel combustor.Ó2006The Combustion Institute.Published by Elsevier Inc.All rights reserved.Keywords:Oxy-fuel combustor;Oxygen-enhanced combustion;FGR (flue gas recirculation);NO emission1.IntroductionCombustors using pure oxygen are conven-tionally called ‘‘oxy-fuel’’combustors.Due to the high cost of oxygen in the early days of air sep-aration technologies,the oxy-fuel combustor were originally developed only for special high-flame-temperature applications in which air-fuel com-bustors were not applicable.However,since air separation technologies have been improved andthe cost of oxygen has been reduced,oxy-fuel combustors can be used for a wide range of indus-trial furnaces such as those for glass-making,alu-minum,iron,and steel production.The inherent advantages of oxy-fuel combustion include its high combustion efficiency,low volume of exhaust gas,low fuel consumption,high melting capacity,and low NO x emission.It achieves the high com-bustion efficiency by eliminating the need to heat the nitrogen in air.In the oxy-fuel combustion,the volume of exhaust gas significantly decreases and the zero NO x emission can be achieved theo-retically.It has been widely recognized that oxy-fuel combustion is one of the most effective ways1540-7489/$-see front matter Ó2006The Combustion Institute.Published by Elsevier Inc.All rights reserved.doi:10.1016/j.proci.2006.08.083*Corresponding author.Fax:+82222970339.E-mail address:ymkim@hanyang.ac.kr (Y.Kim).Proceedings of the Combustion Institute 31(2007)3377–3384/locate/prociProceedings of theCombustion Instituteto capture CO 2from exhaust gas as well as to comply with the CO 2regulations internationally agreed on by the 1997Kyoto Protocol [1–4].Even though oxy-fuel combustion technology provides these advantages,it is impossible to com-pletely eliminate nitrogen in the process,and thus NO x emission control is needed.Both inherent nitrogen in oxygen and/or fuel,and air infiltration through furnace gaps are mainly responsible for the NO x formation in oxy-fuel combustion.Fig-ure 1shows the equilibrium NO emission versus nitrogen percentage in an oxidizer [16].The NO emission dramatically increases up to 30%by ele-vating the nitrogen-in-oxidizer percentage.This is especially evident when the nitrogen-in-oxidizer percentage is less than 10%.The NO emission level reaches a peak value when the nitrogen per-centage in the oxidizer reaches approximately 30%,and the corresponding NO emission level is higher than that at 80%of CH 4-air combustion conditions.Therefore,in the design and applica-tion of oxy-fuel combustor,the reduction of NO x emission is the most important requirement.To achieve this in air-fuel combustion,various methods such as flue gas recirculation (FGR)and staged combustion have been developed and applied [17].However,there is scant experimental data for applying these methods to oxy-fuel com-bustion.Thus,more comprehensive research efforts including trial and error testing,combus-tion measurements and analysis are needed for improved designs of oxy-fuel combustors.Dita-ranto et al.[5–7]showed oxy-fuel combustion increases thermal efficiency and NO x emission is sensitive to air leaks into the combustion cham-ber.Tan et al.[8]indicated that oxygen-enhanced combustion techniques with FGR offer excellent potential for CO 2emission abatement,reduction of NO x emissions and improvement of plant effi-ciency in conventional boilers.According to Baukal and Gebhart [9],thermal radiation increases dramatically by enriching oxy-gen in the oxidizer as well as by increasing the fir-ing rate.They also found that the oxygen enhancement increases the flame temperature to nearly 3000K and the NO x formation for the oxy-gen-enhanced combustion is mainly controlled by the thermal mechanism.In a semi-industrial oxy-fuel combustor,Hedley et al.[10,11]measured the detailed profiles for temperature and species concentration including NO x ,and compared mea-surements with predictions.The OXYFLAME project [12–14]in IFRF provided useful in-flame data collected in an oxy-fuel combustor with thermal input of 0.8to 1.0-MW,which include the profiles of axial veloc-ity,temperature,species concentrations,total radiance and total radiative fluxes at the furnace wall.In their study,the effects of nitrogen concen-tration and momentum injection strength on the NO x emission level were also experimentally analyzed.However,these previous studies on oxy-fuel combustion were conducted under limited condi-tions.Moreover,the reduction of NO emission using FGR technology in oxy-fuel combustion has yet to be fully explored.The main motivation for this present study was to experimentally inves-tigate the NO emission characteristics of the oxy-fuel combustor using FGR technology.In the present study,the NO emission charac-teristics have been experimentally investigated for the oxy-fuel combustors using flue gas recircula-tion (FGR)technology.The flue gas is fed by an ejector instead of the FGR fan.To simulate the NO emission characteristics of industrial oxy-fuel furnaces,nitrogen was supplied by three percent-ages of the total oxygen flow rate.In order to find the optimal inlet arrangement and operating con-ditions of the oxy-fuel combustor utilizing FGR technology,the flame stability characteristics are performed for the oxy-fuel combustors.The oxy-fuel combustor with two separate oxidizer nozzles yields the most stable flames in a wide range of CO 2ratios.The NO emission levels are also mea-sured for the various operating conditions of 0.03and 0.2MW FGR oxy-fuel combustors.The detailed discussions have been made for the effects of CO 2ratio,FGR ratio,and oxygen flow-rate ratio on the NO emission and combustion characteristics.2.Experimental setupFigure 2shows the inlet nozzle arrangement and configuration for various oxy-fuel combus-tors.These combustors have been designed to ver-ify the feasibility of FGR technology.In the oxy-fuel combustor A ,a central fuel nozzle is aligned with an annular oxidizer nozzle.The oxy-fuel combustor B has a wall between a central fuel nozzle and an annular oxidizer nozzle.OntheFig.1.Effect of nitrogen-in-oxidizer percentage on NO emission.3378H.K.Kim et al./Proceedings of the Combustion Institute 31(2007)3377–3384other hand,the oxy-fuel combustors C and D con-sist of a central fuel nozzle and four quadrilateral oxidizer nozzles far away from the fuel nozzle.Among these four oxy-fuel combustors,the com-bustor A has the nearest distance between a cen-tral fuel nozzle and an oxidizer nozzle,followed by combustor B ,combustor C ,and combustor D .Unlike these four oxy-fuel combustors described above,the oxy-fuel combustor E has two separate oxidizer nozzles.In the oxy-fuel combustor E ,a central fuel nozzle is aligned with the first oxidizer nozzle which is surrounded by the second oxidizer nozzle.Detailed dimension and flow rate conditions are listed in Table 1.Here,the designed oxidizer flow rate is considered to be the total flow rate (7.229Nm 3/h)mixed with the oxygen flow rate (1.863Nm 3/h)and the oxi-dizer flow rate (5.366Nm 3/h)of the 200%FGR ratio at the overall equivalence ratio,0.98.In the case of the oxy-fuel combustor E ,the designed oxidizer flow rate is also 7.229Nm 3/h.The flow rate of the first oxidizer nozzle might be adjusted from zero to 1.863Nm 3/h and the flow rate of the second oxidizer nozzle could be controlled from zero to 7.229Nm 3/h of oxidizer flow rate,at the overall equivalence ratio,0.98.Since the measurements for all combustors using the FGR system are expensive and time con-suming,the flame stability experiments for vari-ous oxy-fuel combustors are conducted by varying the ratio for CO 2gas instead of flue gas.The 100%CO 2ratio is defined as the total flow rate of supplied fuel and oxygen.In the case of the oxy-fuel combustor E ,the flame stability test is performed for the oxygen flow-rate ratio (a =30%,50%,and 70%)of the first oxidizer noz-zle by increasing the CO 2ratio to the second oxi-dizer nozzle.Here,the oxygen flow rate ratio of the first oxidizer nozzle is identical to the oxygen flow rate supplied to the first oxidizer nozzle which is separated from the total oxygen flow rate.The remaining oxygen is supplied to the second oxidizer nozzle.In this study,the oxygen flow-rate ratio,a is defined as the oxygen flow-rate fraction of the first oxidizer nozzle over the total oxygen flow rate.Figure 3a shows the experimental apparatus for the various oxy-fuel combustors.The experi-mental apparatus consists of the combustor,com-bustion chamber,analyzer and flow controlling system.A chemically pure grade (>99.9%)meth-ane is used as a fuel,and pure oxygen andpureFig.2.Inlet arrangement and configuration for various oxy-fuel combustors.Table 1Dimension and flow rate conditions for the various types of oxy-fuel combustors Combustor Flow Flowrate [Nm 3/h]Inside diameter [mm]Outside diameter [mm]Distance from center [mm]Width [mm]Height [mm]Velocity [m/s]A Fuel 0.82 2.740oxidizer 7.22961320B Fuel 0.82 2.740oxidizer 7.2291317.420C Fuel 0.82 2.740oxidizer 7.229202.51020DFuel 0.82 2.740Oxidizer 7.229402.51020Fuel 0.82 2.740E1-Stage 1.86368.4202-Stage7.2291216.620Fig. 3.Schematics for experimental apparatus and 0.03MW FGR oxy-fuel combustion system.H.K.Kim et al./Proceedings of the Combustion Institute 31(2007)3377–33843379CO 2are used to meet the given oxidizer condition.A cylindrical quartz tube is utilized to visualize the oxy-fuel flame and combustion processes.The diameter and length of this cylindrical quartz tube are 300mm and 1200mm,respectively,and its exhaust diameter 50mm.A gas analyzer (HORI-BA,VA-3000)using a water-cooled sampling probe is installed to measure the emission levels for CO,CO 2,O 2,and NO.Figure 3b shows the schematic of the 0.03MW FGR oxy-fuel combustor.The 0.03MW FGR oxy-fuel combustor has been designed as the oxy-fuel combustor E .The oxygen flow-rate ratio (a )of the designed FGR oxy-fuel combustor is 30%,and the flow rate of the second oxidizer noz-zle is 24.567Nm 3/h which is mixed with 70%oxy-gen (4.803Nm 3/h)and the flow rate (19.764Nm 3/h)of the 200%FGR ratio at the overall equiva-lence ratio,0.98.In order to simulate the NO emission characteristics of the industrial oxy-fuel furnaces,nitrogen with three percentages of total oxygen flow rate is mixed with the oxidizer of the second oxidizer nozzle.Measurement for NO emission is then performed for the various CO 2ratios supplied to the second oxidizer nozzle at a =10%,20%,30%,and 40%,respectively.Final-ly,NO emission is measured by gradually increas-ing FGR ratios delivered to the second oxidizer nozzle at the FGR system.Detailed dimension and flow rate conditions of the 0.03MW FGR oxy-fuel combustor are given in Table 2.Figures 3c and d shows a schematic of the FGR system and the ejector used.In this ejector,the flue gas flow is driven by the oxygen expansion process in the converging nozzle.Since the oxygen pressure is very high,the flue gas is properly fed by this ejector system without the FGR fan.In FGR systems,the flow rate of the flue gas is cal-culated by the following equation based on the measured temperatures at inlet and outlet as indi-cated in Fig.3d.m f ¼m o C po ðT m ÀT o ÞC pf ðT f ÀT m Þð1ÞThe schematic configuration of the 0.2MW FGR oxy-fuel combustor is shown in Fig.4a.The inlet oxidizer arrangement of the 0.2MW FGR oxy-fu-el combustor is identical to one of the 0.03MW FGR oxy-fuel combustor which is designed to supply oxidizer through two oxidizer nozzles [18].The overall equivalence ratio is 0.98,and detailed information about the dimension and flow rate conditions are listed in Table 2.The furnace sche-matic arrangement of the 0.2MW FGR oxy-fuel combustor is illustrated in Fig.4b.In this furnace,the six cooling air tubes are mounted by diameter 600mm to control in-furnace temperature.Their diameter and thickness are 77mm and 3mm,respectively.The flow rate of air supplied by a blower is about 800kg/h.This flow rate is sup-plied to maintain a stationary in-furnace tempera-ture of 1020°C at axial direction 3000mm signed in Fig.4b.The diameter and length of the furnace are 700and 3100mm,respectively.The furnace wall is made of the insulator material,and the diameter of the exhaust duct is 300mm.Industrial natural gas and pure CO 2are used,and pure oxy-gen is supplied by evaporating the liquid oxygen.Table 2Dimension and flow rate conditions of the 0.03-0.2MW FGR oxy-fuel combustor Combustor capacityFlow Flowrate (Nm 3/h)Inside diameter [mm]Outside diameter [mm]Velocity [m/s]Fuel 3.02 4.21600.03MW1Stage 2.058 6.217.4452Stage 24.5679.417.440Fuel 2211.5600.2MW1-Stage 14.9971821452Stage178.97254740Fig.4.Schematics for 0.2MW FGR oxy-fuel combus-tor and furnace.3380H.K.Kim et al./Proceedings of the Combustion Institute 31(2007)3377–3384In case of the 0.2MW FGR oxy-fuel combus-tor,NO emission is measured for the various CO 2ratios at a =30%as well as for the various FGR ratios at the FGR system.To simulate the NO emission process encountered in the industrial oxy-fuel furnaces,three percent nitrogen of the total oxygen flow rate is also injected to the sec-ond oxidizer nozzle.3.Results and discussionThe present experimental study has been focused on the NO emission characteristics of the FGR oxy-fuel combustors.Before we get into this main subject,the flame stability tests are per-formed to find the optimal inlet arrangement and operating conditions of five oxy-fuel combustor (A ,B ,C ,D ,and E )utilizing FGR technology.In case of the oxy-fuel combustor E with two sepa-rate oxidizer nozzles,CO 2gas is supplied through the second oxidizer nozzle and measurements are made for three different oxygen flow-rate ratio (a =30%,50%,and 70%).In other four oxy-fuel combustors (A ,B ,C ,and D ),O 2and CO 2gas are supplied to single oxidizer nozzle.Figure 5shows the flame images for various oxy-fuel combustors at 20%CO 2ratio.The oxy-fuel combustor A yields the shortest flame length,followed by combustor E and combustor B .Unlike the other types (A ,B ,and E )of combus-tors,the oxy-fuel combustors C and D produce the much longer flame length and they also yield a turbulent non-premixed lifted flame.These dis-tinctly different flame characteristics of combustor C and D are mainly tied with the much longer dis-tance between a central fuel nozzle and oxidizer nozzles which leads to the much lower turbulent intensity and the relatively poor turbulent mixing process in the flame pared to the oxy-fuel combustor C ,the oxidizer nozzle of the oxy-fuel combustor D ,is located further away from the fuel nozzle.Therefore,the oxy-fuel combustor D yields the much lower turbulent intensity and the much lower turbulent flame speed aroundthe flame stabilization region.Consequently,the turbulent nonpremixed lifted flame for combustor D is stabilized at the much further downstream region.The luminosity of oxy-fuel combustor C and D is considerably reduced because of the increased premixedness in the upstream-unburned zone of the turbulent nonpremixed lifted flames [15].Figure 6presents the experimental results of flame stability for various oxy-fuel combustors.This graph displays the region where the stable flame exists over a wide operating range of CO 2ratios.In case of the oxy-fuel combustor E ,the stable flames are formed even at the 200%CO 2ratio for three oxygen flow-rate ratios (30%,50%,and 70%).This flame stability characteristics of the combustor E results from the flame anchor-ing effects of the first oxidizer nozzle which sup-plies pure oxygen for enhanced turbulent mixing and stable combustion with the aligned central fuel jet.In contrast,the oxy-fuel combustor A yields a stable flame up to the 120%CO 2ratio,and the flame stability of the oxy-fuel combustors B ,C ,and D is achieved roughly up to the 110%,44%,and 22%CO 2ratios,respectively.These flame stability characteristics of the oxy-fuel com-bustors are closely related to the distance between a central fuel nozzle and oxidizer nozzles which substantially influences the turbulent intensity in the flame zone.As mentioned above,the much longer distance between a central fuel nozzle and oxidizer nozzles results in the much lower turbu-lent intensity and the much lower turbulent flame speed around the flame stabilization region.Among these four oxy-fuel combustors (A ,B ,C ,and D ),the combustor A has the widest stability zone due to the nearest distance between a central fuel nozzle and an oxidizer nozzle,followed by combustor B ,combustor C ,and combustor D .Therefore,these experimental results suggest that the oxy-fuel combustor E can provide the best flame stability characteristics among the oxy-fuel combustors with the FGRsystem.Fig.5.Flame images for various oxy-fuel combustors at CO 2ratio =20%.Fig. 6.Stable flame zones for various oxy-fuel combustors.H.K.Kim et al./Proceedings of the Combustion Institute 31(2007)3377–33843381Next,the NO emission and combustion char-acteristics of the 0.03MW FGR oxy-fuel combus-tor have been experimentally investigated at the wide range of the oxygen flow-rate ratios (a )and CO 2ratios.Figure 7a shows the flame images for various CO 2ratios at a =30%.By increasing the CO 2ratio,the flame length is noticeably reduced due to the increased turbulent intensity corresponding to the elevated velocity at the sec-ond oxidizer nozzle.It can be also seen that,because of increased dilution effects of CO 2gas,luminosity is decreased with increasing CO 2ratios.Figure 7b displays the flame image at four oxygen flow-rate ratios (a =10%,20%,30%,and 40%)with the 0%CO 2ratio.By increasing the oxygen flow-rate ratio (a ),the flame length is also reduced due to the increased turbulent intensity corresponding to the elevated velocity at the first oxidizer nozzle.The flame images indicate that the flame length is more sensitively changed with the oxygen flow-rate ratio at the first oxidizer nozzle.Figure 8shows the NO emission characteristic for various CO 2ratios at four oxygen flow-rate ratios (a =10%,20%,30%,and 40%).These results indicate that,at 0%CO 2ratio,the lower oxygen flow-rate ratio yields the higher NO emis-sion level.By increasing the oxygen flow-rate ratio from 10%to 40%,the NO emission level at 0%CO 2ratio is decreased from 740to 450ppm.Inthis 0.03MW FGR oxy-fuel combustor,the NO emission characteristic is mainly influenced by the residence time,the flame-zone volume,and the nonequilibrium chemistry associated with tur-bulence-chemistry interaction.In this 0.03MW FGR oxy-fuel combustor,the lower oxygen flow-rate ratio is corresponding to the lower velocity at the first oxidizer nozzle and the lower turbulent intensity in the flame zone.Thus,by decreasing the oxygen flow-rate ratio,the resident time and the flame-zone volume is increased and the flame tem-perature approaches to the equilibrium flame tem-perature due to the much smaller departure from the chemical equilibrium condition.Therefore,the lower oxygen flow-rate ratio produces the much higher NO emission.By increasing the CO 2ratio,the NO emission level at four oxygen flow-rate ratios is drastically reduced due to increased dilution effects.At the 20%CO 2ratio,the NO emission levels at four oxygen flow-rate ratios are below 100ppm.The NO emission level at CO 2ratios between 20%and 60%is gradually reduced.The NO emission levels at the 40%CO 2ratio are below 20ppm and the nearly invariant NO emission level (below 10ppm)is reached at the ratios higher than 60%CO 2.In case of the 0.03MW oxy-fuel combustor installed in the FGR system,the NO emission characteristics have been also experimentally investigated for various FGR ratios at the 30%oxygen flow-rate ratio.Figure 9shows NO emis-sion level versus FGR ratio in the 0.03MW FGR oxy-fuel combustor.Here,the NO emission level is based on dry exhaust with 3%O 2.By increasing the FGR ratio,the NO emission level is drastically reduced due to the increased dilution effect.At the 0%FGR ratio,NO emission is about 530ppm,and it is reduced rapidly below roughly 80ppm when the FGR ratio is increased up to 20%.In the FGR ratio between 20%and 60%,the NO emission level gradually decreases.At the 40%FGR ratio,the NO emission levelisFig.7.Flame images for increasing CO 2ratios at a =30%and for a =10%,20%,30%,and 40%at CO 2ratio =0%.Fig.8.NO emission versus CO 2ratio for the 0.03MW FGR oxy-fuel combustor.3382H.K.Kim et al./Proceedings of the Combustion Institute 31(2007)3377–3384below 30ppm and the reduction ratio of NO emission is approximately 93%.These results clearly indicate that this FGR technology is effec-tive for reducing the NO emission in the oxy-fuel combustor.The experimental results using CO 2gas are also displayed in Fig.9.Experimental results using CO 2and FGR are nearly identical.Thus,it is expected that CO 2gas could be proper-ly utilized instead of flue gas for the development of the FGR oxy-fuel combustor.Finally,the present study has investigated the NO emission characteristics of the 0.2MW FGR oxy-fuel combustor.Measurements are carried out for various CO 2ratios and various FGR ratios at the 30%oxygen flow-rate ratio.Figure 10shows NO emission level versus CO 2ratio and FGR ratio in the 0.2MW FGR oxy-fuel com-bustor.Without FGR (0%CO 2ratio),the NO emission level is nearly 1000ppm.This implies that NO emission in oxy-fuel combustion could be quite sensitive to the nitrogen fraction in fuel or oxygen,and to the infiltration process of air to the furnace.The NO emission level is drastical-ly decreased with increasing the CO 2ratio because of the increased dilution effects.At the 40%CO 2ratio,the NO emission level is below 200ppmand the reduction ratio of NO emission is about 83%.In case of the 0.2MW FGR oxy-fuel combus-tor installed in the FGR system,experimental results shown in Fig.10also indicate that the NO emission level is substantially reduced with increasing the FGR ratio.This is due to increased dilution effects.At the 40%FGR ratio,the NO emission level is below 150ppm and the reduction ratio of NO emission is approximately 85%.By increasing the FGR ratio up to 60%,the NO emis-sion level is approaching to 100ppm.These exper-imental results suggest that the reduction of NO emission in the FGR oxy-fuel combustor could be quite effective at FGR ratios higher than 40%.However,it is necessary to note that the too high FGR ratio is counterproductive in terms of energy efficiency.4.ConclusionIn the present study,the NO emission charac-teristics have been experimentally investigated for the oxy-fuel combustors using flue gas recircula-tion (FGR)technology.Measurements are made for the various operating conditions of 0.03and 0.2MW FGR oxy-fuel combustors.Based on experimental results,the following conclusions can be drawn:(1)The oxy-fuel combustor A yields the shortestflame length,followed by combustor E and combustor B .Unlike the other types (A ,B ,and E )of combustors,the oxy-fuel combus-tors C and D produce the much longer flame length and they also yield a turbulent non-premixed lifted flame.These distinctly differ-ent flame characteristics of combustor C and D are mainly tied with the much longer dis-tance between a central fuel nozzle and oxi-dizer nozzles which leads to the much lower turbulent intensity and the relatively poor tur-bulent mixing process in the flame zone.(2)In case of the oxy-fuel combustor E ,the sta-ble flames are formed even at the 200%CO 2ratio for three oxygen flow-rate ratios (30%,50%,and 70%).This flame stability character-istics of the combustor E results from the flame anchoring effects of the first oxidizer nozzle which supplies pure oxygen for enhanced turbulent mixing and stable com-bustion with the aligned central fuel jet.In contrast,the oxy-fuel combustor A yields a stable flame up to the 120%CO 2ratio,and the flame stability of the oxy-fuel combustors B ,C ,and D is achieved roughly up to the 110%,44%,and 22%CO 2ratios,respectively.(3)By increasing the CO 2ratio and the oxygenflow-rate ratio in the 0.03MW FGR oxy-fuel combustor,the flame length isnoticeablyFig.10.NO emission versus FGR ratio and CO 2ratio for the 0.2MW FGR oxy-fuel combustor at a =30%.Fig.9.NO emission versus FGR ratio and CO 2ratio for the 0.03MW FGR oxy-fuel combustor at a =30%.H.K.Kim et al./Proceedings of the Combustion Institute 31(2007)3377–33843383reduced due to the increased turbulent inten-sity corresponding to the elevated velocity at the second oxidizer nozzle and at thefirst oxi-dizer nozzle.Theflame images indicate that theflame length is more sensitively changed with the oxygenflow-rate ratio at thefirst oxi-dizer nozzle.In terms of the NO emission characteristics,at0%CO2ratio,the lower oxygenflow-rate ratio yields the higher NO emission level mainly due to the longer resi-dent time,the largerflame-zone,and the much smaller departure from the chemical equilibrium condition.(4)When the0.03MW FGR oxy-fuel combustoris operated at the40%FGR ratio,the NO emission level is below30ppm and the reduc-tion ratio of NO emission is approximately 93%.Since experimental results using CO2 and FGR are nearly identical,it is expected that CO2gas could be properly utilized instead offlue gas for the development of the FGR oxy-fuel combustor.(5)In case of the0.2MW FGR oxy-fuel com-bustor installed in the FGR system,the NO emission level is substantially reduced with increasing the FGR ratio due to the increased dilution effects.At the40%FGR ratio,the NO emission level is below 150ppm and the reduction ratio of NO emission is approximately85%.By increas-ing the FGR ratio up to60%,the NO emis-sion level is approaching to100ppm.These experimental results suggest that the reduc-tion of NO emission in the FGR oxy-fuel combustor could be quite effective at FGR ratios higher than40%.AcknowledgmentThis research was supported by a grant(AE2-101-1-0-1)from Carbon Dioxide Reduction& Sequestration Research Center,one of the21st Century Frontier Programs funded by the Ministry of Science and Technology of Korean government.References[1]J.T.Brown,Ceram.Eng.Sci.Proc.12(1991)594–609.[2]C.E.Baukal,Industrial Burners Handbook,CRCPress,2004.[3]C.E.Baukal,Oxygen-Enriched Combustion,CRCPress,1998.[4]T.K.Dankert,G.B.Tuson,Eng.Sci.Proc.17(2)(1996)47–54.[5]M.Ditaranto,J.C.Sautet,J.M.Samaniego,Exp.Fluids30(2001)253–261.[6]J.C.Sautet,M.Ditaranto,J.M.Samaniego,O.Charon,m.Heat Mass Transfer26(1999) 647–656.[7]J.C.Sautet,L.Salentey,M.Ditaranto,m.Heat Mass Transfer28(2001)277–287.[8]Y.Tan,M.A.Douglas,K.V.Thambimuthu,Fuel18(8)(2002)979–1091.[9]C.E.Baukal,B.Gebhart,Int.J.Heat Mass Transfer40(1997)2539–2547.[10]J.T.Hedley,M.Pourkashanian, A.Williams,Combust.Sci.Technol.108(1995)311–322. [11]A.Brink,M.Hupa,F.Breussin,llemant,R.Weber,J.Propul.Power16(2000)609–614. [12]llemant,F.Breussin,R.Weber,T.Ekman,J.Dugue,J.M.Samaniego,O.Charon,A.J.Van Den, J.Van Der,W.Fujisaki,T.Imanari,T.Nakamura, K.Iino,J.Inst.Energy73(2000)169–182.[13]llemant,J.Dugue,R.Weber,Analysis of theexperimental data collected during the oxyflame-1 and oxyflame-2experiments,IFRF Doc F85/y/4 Part1,1997.[14]U.Bollettini,F.Breussin,llemant,R.Weber,Mathematical modeling of oxy-natural gasflames, IFRF Doc F85/y/6,1997.[15]W.M.Pitts,bust.Inst.22(1988)809–816.[16]R.J.Kee,F.M.Rupley,ler,Sandia NationalLaboratories Report SAND89-8009,1990.[17]M.Flamme,Energy Convers.Manage.42(2001)1919–1935.[18]R.Weber,bust.Inst.26(1996)3343–3354.3384H.K.Kim et al./Proceedings of the Combustion Institute31(2007)3377–3384。