轴承压装机压装力的计算
轴承压装力计算软件

计算数据F--压入力(N)F=P fmax πd f L f μ584.1509设计数据d f --结合直径(mm)34.9000设计数据L f --结合长度(mm)9.3980选择数据μ--结合面摩擦系数0.1300计算数据P fmax --结合面承受的最大单位压力(N/mm 2)13.7000设计数据δmax --最大过盈量(mm)0.0127选择参数E a --包容件材料弹性模量(N/mm2)230000.0000选择数据E i --包容件材料弹性模量(N/mm2)230000.0000计算数据C a --系数C a =[(d a 2+d f 2)/(d a 2-d f 2)]+V a 1.3516计算数据C i --系数C i =[(d f 2+d i 2)/(d f 2-d i 2)]-V i4.7576设计数据d a --包容件外径(mm)70.0000设计数据d i --被包容件内径,实心轴为0(mm)28.5750选择参数V a --包容件泊松系数0.3100选择参数V i --被包容件泊松系数0.3100计算数据F end ----最终压装力(N)1927.698058-22 材料摩擦系数村料摩擦因数μ(无润滑)摩擦因数μ(有润滑)钢一钢0.07~0.160.05~0.13钢—铸钢0.110.07钢一结构钢0.10.08钢一优质结构0.110.07钢—青铜0.15~0.200.03~0.06钢—铸铁0.12~0.150.05~0.10铸铁—铸铁0.15~0.250.05~0.10表58-23,常用材料的弹性模量,泊松比和线胀系数加热碳钢、低合金钢、合金结构钢200~2350.30~0.3111灰铸铁(HT150、HT200)70~800.24~0.2511灰铸铁(HT250、HT300)105~1300.24~0.2610可锻铸铁90~1000.2510非合金球墨铸铁160~1800.28~0.2910青铜850.3517黄铜800.36~0.3718铝合金690.32~0.3621镁铝合金400.25~0.3025.5注:在选用压力机规格时应是计算压力P的3~3.5倍材料弹性模量E/(KN/mm 2)泊松比v 线胀系数-6/℃使用资料压装时的主要要求为: 1)压装时不得损伤零 2)压入时应平稳,被压入件应准确到位。
轴承设计的计算公式

一、滚动轴承承载能力的一般说明滚动轴承的承载能力与轴承类型和尺寸有关。
相同外形尺寸下,滚子轴承的承载能力约为球轴承的1.5~3倍。
向心类轴承主要用于承受径向载荷,推力类轴承主要用于承受轴向载荷。
角接触轴承同时承受径向载荷和轴向载荷的联合作用,其轴向承载能力的大小随接触角α的增大而增大。
二、滚动轴承的寿命计算轴承的寿命与载荷间的关系可表示为下列公式:或式中:──基本额定寿命(106转);──基本额定寿命(小时h);C──基本额定动载荷,由轴承类型、尺寸查表获得;P──当量动载荷(N),根据所受径向力、轴向力合成计算;──温度系数,由表1查得;n──轴承工作转速(r/min);──寿命指数(球轴承,滚子轴承)。
三、温度系数f t当滚动轴承工作温度高于120℃时,需引入温度系数(表1)表1 温度系数四、当量动载荷当滚动轴承同时承受径向载荷和轴向载荷时,当量载荷的基本计算公式为式中:P——当量动载荷,N;——径向载荷,N;——轴向载荷,N;X——径向动载荷系数;Y——轴向动载荷系数;——负荷系数五、载荷系数f p当轴承承受有冲击载荷时,当量动载荷计算时,引入载荷系数(表2)表2 冲击载荷系数f p六、动载荷系数X、Y表3 深沟球轴承的系数X、Y表4 角接触球轴承的系数X、Y表5 其它向心轴承的系数X、Y表6 推力轴承的系数X、Y七、成对轴承所受轴向力计算公式:角接触球轴承:圆锥滚子轴承:式中e为判断系数,可由表4查出;Y应取表5中的数值。
●正排列:若则若则●反排列:若则若则八、成对轴承当量动载荷根据基本公式:式中:P——当量动载荷,N;——径向载荷,N;——轴向载荷,N;X——径向动载荷系数;Y——轴向动载荷系数;——负荷系数。
九、修正额定寿命计算对于要求不同的可靠度、特殊的轴承性能以及运转条件不属于正常情况下的轴承寿命计算时,可采用修正额定寿命计算公式:式中:──特殊的轴承性能、运转条件以及不同可靠度要求下的修正额定寿命(106转);a1──可靠度的寿命修正系数;a2──特殊的轴承性能寿命修正系数;a3──运转条件的寿命修正系数。
压入力计算

8 计算与校核[21]8.1过盈配合装配压入力的计算在立式轴承压装机邀标文件的技术要求中明确指出锥轴承外圈与轴承孔配合为过渡配合,故采用过盈配合装配压入力的计算方法。
方法如下:过盈配合装配压入力的计算方法μπf f f L d p P max =其中:P —压入力,Nm ax f p —结合表面承受的最大单位压力,2/mm N f d —结合直径,mm f L —结合长度,mm μ—摩擦系数结合表面最大单位压力计算公式:)(maxmax iia a f f E C E C d p +=δ其中:m ax δ —最大过盈量,mma C 、i C —系数;a E 、i E —包容件和被包容件的材料弹性模量,2/mm N系数a C 、i C 计算方法如下:ν+-+=2222f a f a a d d d d Cν--+=2222if if i dd d d Ca d 、i d 分别为包容件外径和被包容件内径(实心轴i d =0),mmν—泊松系数压装机所需的压力一般为压入力的3~3.5倍表8.1常用材料的摩擦系数表摩擦系数μ材料无润滑有润滑钢-钢0.07~0.16 0.05~0.13钢-铸钢0.11 0.07钢-结构钢0.10 0.08钢-优质结构钢0.11 0.07钢-青铜0.15~0.20 0.03~0.06钢-铸铁0.12~0.15 0.05~0.10铸铁-铸铁0.15~0.25 0.05~0.10表8.2常用材料弹性模量、泊松系数材料弹性模量E 泊松系数ν碳钢196~216 0.24~0.28 低合金钢、合金结构钢186~206 0.25~0.30灰铸铁78.5~157 0.23~0.27 铜及其合金72.6~128 0.31~0.42铝合金70 0.33轴承为标准件,采用轴承钢GCr15;压头的材料选用高级优质碳素工具钢T10A,其密度是7.85g/cm3,特点是容易锻造、加工性能良好、价格便宜,能够承受冲击、硬度高,应用于不受剧烈冲击的高硬度耐磨工具,如车刀、刨刀、冲头、丝锥、钻头、手锯条。
轴承计算方法
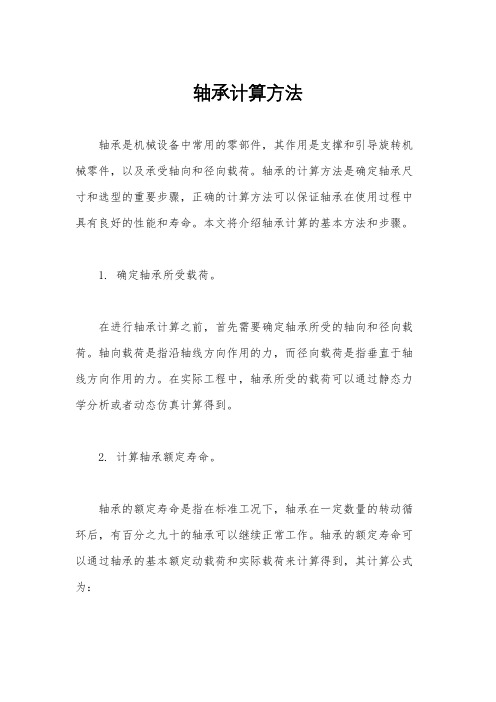
轴承计算方法轴承是机械设备中常用的零部件,其作用是支撑和引导旋转机械零件,以及承受轴向和径向载荷。
轴承的计算方法是确定轴承尺寸和选型的重要步骤,正确的计算方法可以保证轴承在使用过程中具有良好的性能和寿命。
本文将介绍轴承计算的基本方法和步骤。
1. 确定轴承所受载荷。
在进行轴承计算之前,首先需要确定轴承所受的轴向和径向载荷。
轴向载荷是指沿轴线方向作用的力,而径向载荷是指垂直于轴线方向作用的力。
在实际工程中,轴承所受的载荷可以通过静态力学分析或者动态仿真计算得到。
2. 计算轴承额定寿命。
轴承的额定寿命是指在标准工况下,轴承在一定数量的转动循环后,有百分之九十的轴承可以继续正常工作。
轴承的额定寿命可以通过轴承的基本额定动载荷和实际载荷来计算得到,其计算公式为:L10 = (C / P)^3 10^6。
其中,L10为额定寿命(单位,转),C为基本额定动载荷(单位,N),P为实际载荷(单位,N)。
3. 确定轴承尺寸和选型。
在确定轴承所受载荷和额定寿命之后,可以根据轴承的静载荷和动载荷来选择合适的轴承尺寸和型号。
通常情况下,轴承的静载荷要大于或等于实际静载荷,动载荷要大于或等于实际动载荷,以确保轴承在工作过程中具有足够的承载能力和寿命。
4. 考虑轴承安装和润滑。
除了轴承的基本计算之外,还需要考虑轴承的安装和润滑。
轴承的安装质量直接影响轴承的使用寿命和性能,因此需要按照标准的安装工艺进行安装。
同时,轴承在工作过程中需要进行润滑,以减小摩擦和磨损,延长轴承的使用寿命。
5. 结语。
轴承计算是确定轴承尺寸和选型的重要步骤,正确的计算方法可以保证轴承在使用过程中具有良好的性能和寿命。
通过确定轴承所受载荷、计算轴承的额定寿命、确定轴承尺寸和选型,以及考虑轴承的安装和润滑等步骤,可以有效地进行轴承计算,并选择合适的轴承以满足实际工程需求。
在实际工程中,轴承的计算方法需要结合具体的工程要求和条件进行综合考虑,以确保轴承在工作过程中具有良好的性能和可靠性。
(整理)轴承压装力计算公式
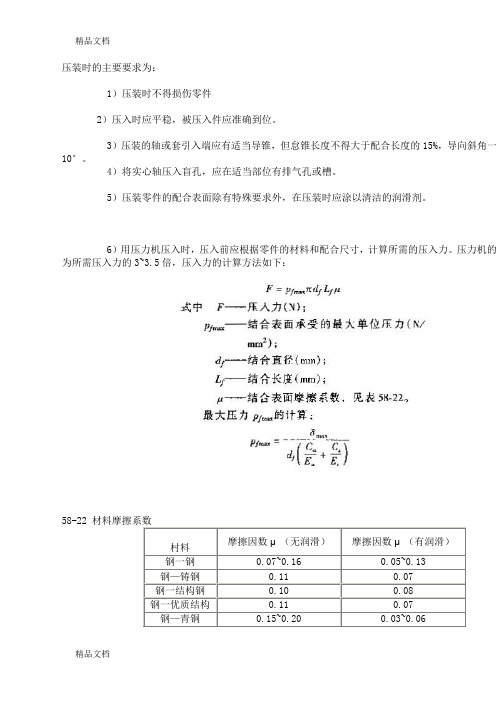
压装时的主要要求为:
1)压装时不得损伤零件
2)压入时应平稳,被压入件应准确到位。
3)压装的轴或套引入端应有适当导锥,但怠锥长度不得大于配合长度的15%,导向斜角一10°。
4)将实心轴压入盲孔,应在适当部位有排气孔或槽。
5)压装零件的配合表面除有特殊要求外,在压装时应涂以清洁的润滑剂。
6)用压力机压入时,压入前应根据零件的材料和配合尺寸,计算所需的压入力。
压力机的为所需压入力的3~3.5倍,压入力的计算方法如下:
58-22
钢—铸铁0.12~0.15 0.05~0.10
铸铁—铸铁0.15~0.25 0.05~0.10
表58-23,常用材料的弹性模量,线胀系数。
立式轴承压装机简介

立式轴承压装机简介
一、立式轴承压装机的定义
电机转子轴承压装机是轴承的典型加工设备。
控制系统触摸采用按键操作加控制按钮方式,操作控制系统和按钮分别安装在操作面板及前操作盒上。
压装机的逻辑控制部份、控制元件及伺服驱动单元等都安装在机床架体内部。
二、立式轴承压装机功能结构
1、液压压床以2-20MPA的液体压力为动力源,外接三相AC380V 50HZ或三相AC220 60HZ交流电源.
2、以液体作为介质来传递能量,采用先进的子母缸液压回路,油温低,空行程速度均在150MM/秒以上, 工进速度30 MM/秒以下,
3、采用整体焊接的坚固开式结构,可使机身保持足够的的钢性,同时拥有最方便的操作空间,
4、分手动和半自动两种控制方式,手动可将压装上模停在任意行程范围内,配有紧急回升按钮,也可加装红外线护手装置.
5、压装行程一般通过计时器,压力开关,位置感应器,或客户本身的模具进行控制
6、压装主轴的回升高度,可通过计时器,或位置感应器任意行程范围内调整.
7、压力、行程、保压时间、闭合高度客户均可自行调整,方便操作;
三、立式轴承压装机的优点
1、采用增速液压缸,工作时先快后慢,噪音低,高效益,低能耗。
2、滑块采用上下电子感应器限位,寿命长,操作简单。
3、设有压力保护、限位、半自动、手动控制功能。
4、也可依客户需求安装红外线护手装置
四、立式轴承压装机的用途
用于轴类零件和轴套类零件的压装,也可以完成压印,套形等动作。
压制不很严格的粉末、塑料制品,用途:汽车减震器装配、精密轴承、轴套、汽车零部件、水泵、涡轮增压器,、变速箱、齿轮、汽车底盘零件、后桥,副车架衬套等的压装
(枣庄力邦机械有限公司整理)。
轴承轴向载荷计算公式

轴承轴向载荷计算公式
轴承是一种用于支撑机械旋转部件的重要元件。
在实际应用中,轴承通常承受着来自旋转部件的各种载荷,其中包括轴向载荷。
轴向载荷是指垂直于轴心线方向的力或压力,其作用方向与轴的轴向相同或相反。
轴向载荷的计算对于正确选择合适的轴承和确保轴承工作正常非常重要。
以下是常用的轴向载荷计算公式:
1. 线性轴承的轴向载荷计算公式:
轴向载荷 = 1/2 * (F1 + F2)
其中,F1和F2分别为轴承所受外力的大小,取正负号表示方向。
2. 圆柱滚子轴承的轴向载荷计算公式:
轴向载荷 = (F1 + F2) / 2
其中,F1和F2分别为轴承所受外力的大小,取正负号表示方向。
3. 锥形滚子轴承的轴向载荷计算公式:
轴向载荷= (F1 + F2) / 2 * cosα
其中,F1和F2分别为轴承所受外力的大小,取正负号表示方向;α为锥面与轴线的夹角。
4. 推力球轴承的轴向载荷计算公式:
轴向载荷 = F
其中,F为轴承所受外力的大小,取正负号表示方向。
需要注意的是,在实际应用中,轴向载荷不仅仅是由外力引起的,还可能由于转子离心力、温度变化等因素而产生。
因此,需要综合考虑这些因素对轴向载荷的影响,进行准确的计算。
在进行轴向载荷计算时,还需要考虑其他一些因素,如轴承的额定载荷、轴承的径向载荷等。
同时,还要根据具体的工况条件和设计要求,选择合适的轴承类型和规格。
轴向载荷的计算是轴承设计中非常重要的一部分。
通过合理计算和选择,可以确保轴承工作正常,并提高设备的安全性和可靠性。
机械设计--轴承计算

),常温下工作,径向载荷Fr=10KN,轴向载荷Fa=3KN,求轴承的寿命为多少?
∵ Fa / C0r = 3000 / 36300 = 0.083 ∴ e = 0.28 ∵Fa / Fr = 3000 / 10000 = 0.3 >e = 0.28 ∴ X = 0.56 Y = 1.55
轴承2 被压紧 Fa2 = Fd1+Fae = 1720N 轴承1 被放松 Fa1 = Fd2 = 2720 N
Fae
Fr2
Fr1
P1 P2
∴轴承1寿命低。
Fa1 / Fr1 = 2720 / 4000 = 0.59<e = 0.68
X1 = 1 Y1 = 0 P1 f P ( X 1Fr1 Y1Fa1 ) =1×4000 = 4000N
Lh
10
6
(
60n
ft C ) P
10 6 (48400 60 200 12300
)3
5077 .38
h
某轴中间受径向载荷 Fr 4430 N 作用,两端选用深沟球轴承6210(
Cr 27KN ),轴转速n=1800r/min,载荷基本稳定( f p 1.1
),常温下工作,求轴承的寿命为多少?
Fa/Fre XY 10
Fa/Fr>e XY 0.41 0.87
∵ Fa1 / Fr1 = 1474 / 400 = 3.685> e = 0.68 ∴ X1 = 0.41 Y1 = 0.87 ∵Fa2 / Fr2 = 1224 / 1800 = 0.68 = e = 0.68 ∴ X2 = 1 Y2 = 0
- 1、下载文档前请自行甄别文档内容的完整性,平台不提供额外的编辑、内容补充、找答案等附加服务。
- 2、"仅部分预览"的文档,不可在线预览部分如存在完整性等问题,可反馈申请退款(可完整预览的文档不适用该条件!)。
- 3、如文档侵犯您的权益,请联系客服反馈,我们会尽快为您处理(人工客服工作时间:9:00-18:30)。
轴承压装机压装力的计算
摘要介绍了与传统设计不同的轮轴冷压装计算方法,设计员可节省查阅资料时间,应用新型的计算公式,能快速获得准确工艺参数,并量化轮轴设计尺寸。
本文的车辆轮轴注油冷压装工艺属国内首例。
此方法对机械制造工业价值巨大。
关键词轮轴冷压装轮轴注油冷压装计算公式工艺工装修复技术
一、前言
本文论述的内容,适用于铁路机车车辆、工程机械和机床制造。
该技术的特点是:在轮轴冷压装设计中,既节省了查阅设计手册和行业标准所用的大量时间,又能快速获得准确工艺参数和设计量化值。
工艺简单、加工方便、能有效避免轮轴配合面被擦伤,与传统的轮轴冷压装工艺设计相比,这是专业技术领域中的新思路。
二、工艺参数计算
在设计轮轴冷压装产品时,如何根据配合直径来求得合理的过盈量及冷压装吨位,这是专业工艺人员极为关注的技术难题。
作者通过长期试验论证,运用数学原理推导出了下列理论计算公式,技术难题迎刃而解,现简介如下。
-4-4 δ=7×10D+0.06 (1) δ=7.6×10D+0.09 (2) 12
δ=0.5(δ+δ) (3) δ=δ-0.02 (4) 31243
δ=δ+0.01 (5) δ=δ,δ (6) 5345
P=(3.11D+66)+6 (7) P=4.88D+101 (8) 12
P=P,P (9) 12
δ—粗算轮轴配合过盈量下限值mm;δ—粗算轮轴配合过盈量上限值mm;δ—粗算轮轴配123合过盈量平均值mm;δ—精算轮轴配合过盈量下限值mm;δ—精算轮轴配合过盈量上限值45
mm;δ—轮轴配合过盈量精确值mm;D—轮轴配合直径mm;P—轮轴冷压装吨位下限值kN;1
P—轮轴冷压装吨位上限值kN;P—轮轴冷压装吨位精确值kN。
2
三、计算应用实例
计算图1所示的车辆轮轴采用冷压装工艺时,所需配合过盈量及压装吨位。
解:(1)计算过盈量
-4-4 δ=7×10D+0.06=7×10×182+0.06=0.19(mm) 1
-4-4 δ=7.6×10D+0.09 =7.6×10×182+0.09=0.23(mm) 2
δ=0.5(δ+δ)=0.5(0.19+0.23)=0.21(mm) 312
δ=δ-0.02=0.21-0.02=0.19(mm) 43
δ=δ+0.01=0.21+0.01=0.22(mm) 53
δ=δ,δ =0.19~0.22(mm) 45
(2)计算冷压装吨位
P=(3.11D+66+6=(3.11×182+66)+6=683(kN) 1
P=4.88D+101=4.88×182+101=989(kN) 2
P=P,P=683,989(kN) 12
以上计算出来的δ值和P值,即为所求车辆轮轴冷压装时,所需的配合过盈量和冷压装吨位。
根据δ值,即可量化出车轴配合座部位的精确尺寸和车轮配合孔部位的精确尺寸。
四、轮轴机械加工
轮孔的配合表面是通过镗削加工来实现的,其表面粗糙度可按Ra3.2控制;轴座的配合表面是通过磨削加工来实现的,其表面粗糙度可按Ra1.6控制。
为了保证轮轴配合面不被擦伤,轮孔两端应有R3,5mm的过渡圆弧,轴座的压装始端,应有10,13mm圆锥引入段。
五、工艺与操作
1.清洁度、过盈量、轴长中心
轮轴冷压装之前,轮孔和轴座必须用汽油刷洗干净,用量缸表和千分尺分别测量轮孔和轴座的配合直径,并以此确定二者的配合过盈量。
若轮轴配合组件是由一轴两轮组成的轮对,则确定轴长中心是轮轴冷压装配前的重要因素。
具体方法是:用划规分别以有一定加工精度的轴两端或适当的对称轴肩作基准,以相同半径分别向轴长中心方向划线,若两线重合,该点即是轴长中心,若两线不重合,则折中线即是轴长中心。
图2中的A、B部位即是对称轴肩,时,纵向中心线即是轴长中心。
2.冷压装
轮轴冷压装之前,应把导向套分别安装在轴两端,在导向套外表面和轴座配合表面均匀涂抹纯净的植物油(禁用桐油)之后,把轮分别套装在轴两端的导套上。
用起重设备把轮轴组件水平吊起,在油压机的移动小车支架上稳放,用框式水平仪测量轴水平。
准备工作就绪后,把轴端保护套安装在轴的受力一端,待压装,见图3所示。
导向套在轮轴配合冷压装中的作用是:引导轮、轴对中,避免配合面被擦伤。
制造导向套时,应使其与轮、轴均为间隙配合,Q235A钢和工业尼龙为常用材料。
轴端保护套的作用是:避免轴端面直接受力造成塑性变形,这种作用在轴端有螺纹时,尤为重要。
轮轴冷压装时,应使压入力作用在轴端,使用轴长中心样板尺进行同步测量,这样可保证轮内侧端面与轴长中心之间的距离不超限。
一端压装完工后,把轮轴组件在油压机的移动小车支架上旋转180?,在受力轴端装好保护套,施行另一端轮轴冷压装,此时可用专用测尺按设计要求检测两轮内侧面之间的距离。
压装过程不允许中途停机。
3.压力曲线
轮轴冷压装的压力曲线,是通过油压机上的自动记录仪绘制的,它是衡量轮轴冷压装质量的重要指标,轮轴过盈配合冷压装的压力参数也由此得出。
冷压装时,压力曲线应均匀平稳上升,曲线中部不允许存在陡吨(压力曲线不平滑)、降吨(压
力曲线朝数值减小的方向变化)等缺陷,合格的压力曲线见图4所示。
压力曲线理论长度可按如下公式计算。
S=(L+A-K-r)i S—压力曲线理论长度;L—轮毂长度;A—伸出轮毂孔外端之轴座长度;K—轮座前端锥形长度;r—压力指示器传达系数,即指示器圆筒行程比鞲鞴冲程缩短系数,可根据压力指示器构造决定。
4.修复技术
对不符合冷压装技术标准的轮轴过盈配合组件,应及时退轮检查配合面是否被擦伤,并进行修复。
未能及时退轮的轮轴过盈配合组件,其放置时间不允许超过
12小时。
对达到压装力要求的轮轴过盈配合组件,允许原轮在原轴上重新压装一次;对压装力不足的轮轴过盈配合组件,不允许原轮在原轴上重新压装,原因是:退轮后,轮轴配合表面看起来粗糙度无变化,实际已经朝粗糙度上升的方向变化了,在这种情况下,若进行重新压装,容易出现假吨(记录仪上显示的压装力数值,比实际压装力数值大)。
对压装力超限的轮轴过盈配合组件,必须重新修磨轮轴配合表面,并进行严格测量及过盈量选配后,才能重新进行压装。
六、车辆轮轴注油冷压装工艺
1.简介
车辆轮轴过盈配合注油冷压装与普通轮轴过盈配合冷压装在结构上的不同点是:前者的轮孔中部有一个环形油槽与轮毂件上的注油孔相通,见图5所示。
图中各件号代表的含义为:1.车轴;2.车轮;3.高压注油管;4.注油扩压设备。
压装过程中,在轮轴配合面之间注入高压油,以使轮孔产生微量扩大,所需轴向压力可随之减小。
此方法既能保护轮轴配合面不被擦伤,又能方便的微调轮对内侧距。
2.工艺
轮轴过盈配合注油冷压装与普通轮轴过盈配合冷压装在工艺上的不同点,分别体现在轮轴配合部位加工、轮轴配合过盈量、向轮轴配合面之间注入高压油。
其余方面二者相同。
(1)轮轴配合部位加工
车轮的配合孔在加工时,应制成有0.02,0.03mm正锥的配合孔。
加工车轮配合孔的注油孔时,应使其轴向中心线与轮孔轴向中心线夹45?角。
车轴的轮座在加工时,不允许有任何锥度,应确保轮座的圆柱配合面光滑及轴向平行。
(2)注油冷压装
进行轮轴注油冷压装时,注入高压油之前的压入力应逐渐上升;从过油槽起,向轮轴配合面之间注入高压油,此时的压入力开始下降。
注油压装过程中,允许注油压力在100,165MPa
范围内波动,此阶段的压入力应小于未注油时的数值。
压装终止时的压入力须在200kN以下。
调整超限轮对内侧距的方法是:向轮轴配合面之间注入高压油,用铜棒按所需的轴向力方向振动轮,直至符合设计标准。
3.实例资料
图6所示的车辆轮轴注油冷压装曲线,是为台湾客户制造的DQJ2型桥检车轮对资料,进行轮轴注油冷压装时,所用设备为国产压装机和从日本进口的高压油泵。
应用此项新工艺,为台湾客户制造出了优质产品。
据国内有关专家通报,此项成功的车辆轮轴注油冷压装工艺,在我国大陆尚属首例。
DQJ2型轮对尺寸与国产铁路货车8G转向架上使用的轮对尺寸相似。
七、结语
本文论述的轮轴冷压装计算与工艺,经历了长期的生产实践和验证,节省设计时间、工艺过程简化、数据准、成本低、可靠性强,均是此项新技术的突出优点。
大陆和台湾岛的车辆运行可靠性,充分证明了此项技术是轮轴冷压装领域的新途径。