Cross-coupled controller design for triaxial motion systems based on second-order contour error
Robust control of robot manipulators
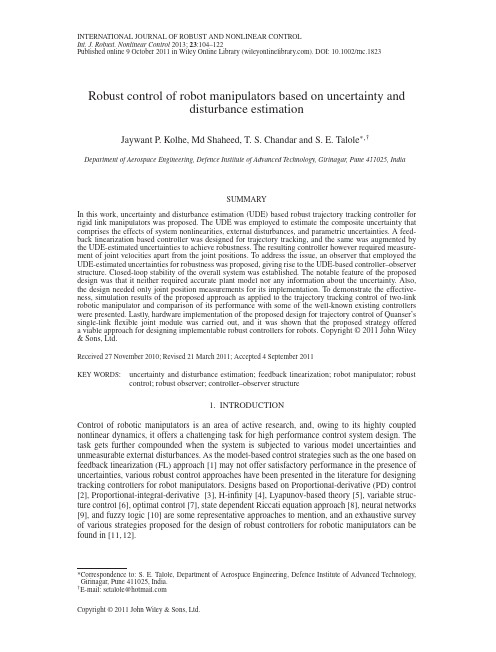
INTERNATIONAL JOURNAL OF ROBUST AND NONLINEAR CONTROLInt.J.Robust.Nonlinear Control2013;23:104–122Published online9October2011in Wiley Online Library().DOI:10.1002/rnc.1823Robust control of robot manipulators based on uncertainty anddisturbance estimationJaywant P.Kolhe,Md Shaheed,T.S.Chandar and S.E.Talole*,†Department of Aerospace Engineering,Defence Institute of Advanced Technology,Girinagar,Pune411025,IndiaSUMMARYIn this work,uncertainty and disturbance estimation(UDE)based robust trajectory tracking controller for rigid link manipulators was proposed.The UDE was employed to estimate the composite uncertainty that comprises the effects of system nonlinearities,external disturbances,and parametric uncertainties.A feed-back linearization based controller was designed for trajectory tracking,and the same was augmented by the UDE-estimated uncertainties to achieve robustness.The resulting controller however required measure-ment of joint velocities apart from the joint positions.To address the issue,an observer that employed the UDE-estimated uncertainties for robustness was proposed,giving rise to the UDE-based controller–observer structure.Closed-loop stability of the overall system was established.The notable feature of the proposed design was that it neither required accurate plant model nor any information about the uncertainty.Also, the design needed only joint position measurements for its implementation.To demonstrate the effective-ness,simulation results of the proposed approach as applied to the trajectory tracking control of two-link robotic manipulator and comparison of its performance with some of the well-known existing controllers were stly,hardware implementation of the proposed design for trajectory control of Quanser’s single-linkflexible joint module was carried out,and it was shown that the proposed strategy offered a viable approach for designing implementable robust controllers for robots.Copyright©2011John Wiley &Sons,Ltd.Received27November2010;Revised21March2011;Accepted4September2011KEY WORDS:uncertainty and disturbance estimation;feedback linearization;robot manipulator;robust control;robust observer;controller–observer structure1.INTRODUCTIONControl of robotic manipulators is an area of active research,and,owing to its highly coupled nonlinear dynamics,it offers a challenging task for high performance control system design.The task gets further compounded when the system is subjected to various model uncertainties and unmeasurable external disturbances.As the model-based control strategies such as the one based on feedback linearization(FL)approach[1]may not offer satisfactory performance in the presence of uncertainties,various robust control approaches have been presented in the literature for designing tracking controllers for robot manipulators.Designs based on Proportional-derivative(PD)control [2],Proportional-integral-derivative[3],H-infinity[4],Lyapunov-based theory[5],variable struc-ture control[6],optimal control[7],state dependent Riccati equation approach[8],neural networks [9],and fuzzy logic[10]are some representative approaches to mention,and an exhaustive survey of various strategies proposed for the design of robust controllers for robotic manipulators can be found in[11,12].*Correspondence to:S.E.Talole,Department of Aerospace Engineering,Defence Institute of Advanced Technology, Girinagar,Pune411025,India.†E-mail:setalole@ROBUST CONTROL OF ROBOT MANIPULATORS BASED ON UDE105 In many of the robust control formulations presented in the literature,there exists certain issues that need attention.Firstly,in the number of the proposed controllers,knowledge of some charac-teristic of uncertainty is assumed.To cite a few examples,in[13],the uncertainty is assumed to be bounded by higher-order polynomials in system states.In[14],the uncertainty is assumed to be bounded by a known continuous function.Similarly,in[15],afinite-time robust control formula-tion is presented wherein the knowledge of uncertainty bound is needed.Also,as is well known, the formulations based on sliding mode control(SMC)and Lyapunov-based approaches in general require a priori knowledge of bounds of uncertainty.As the uncertainties are generally unknown or poorly known,not having accurate information on the characteristics of the uncertainty results into degraded performance.For example,when the knowledge of bound on uncertainties is not available,the use of highly conservative bound results in excessive control effort,and use of lower bounds may result in degradation of performance or even in instability.Secondly,most of the con-trollers proposed for robotic manipulators need the measurement of joint positions and velocities. Whereas position can be accurately measured by good precision encoders,velocity measurement is often an issue because of measurement noise[16].Apart from this,the cost and weight of an additional sensor can also be a deterrent.One approach to address the issue is to obtain the estimate of velocity from position measurement through approximate differentiation.However,the resulting estimate may not be satisfactory.A better alternative is to obtain the velocity states by designing an appropriate observer[17].However,observers designed based on an assumed system model may suffer from robustness when the model uncertainties show up.Also,as the separation principle is not,in general,valid in nonlinear systems,the closed-loop stability of the controller–observer sys-tem remains an stly,an important consideration in designing controllers in robotic system is that it should be simple from real-time implementation point of view.In this paper,an uncertainty and disturbance estimation(UDE)[18]based robust trajectory track-ing controller is proposed for rigid link manipulators.An FL-based controller is formulated by considering the system nonlinearities,uncertainties,and external disturbances as a composite uncer-tainty.The FL controller is then augmented by the UDE-estimated uncertainty[19]to achieve robustness.As the resulting controller requires joint velocities apart from the joint positions,a robust observer is proposed to provide estimate of the joint velocities.The observer design too employs the UDE-estimated uncertainty to achieve robustness,thus giving rise to the UDE-based controller–observer structure.Closed-loop stability of the controller–observer structure is estab-lished.The significant feature of the proposed approach is that it does not need any information about the uncertainties.Also,the design does not require accurate plant model and needs mea-surement of only link positions for its implementation.Effectiveness of the proposed approach is demonstrated through simulations with significant uncertainties in the system model.Next,numer-ical simulation results are presented by comparing the performance of the proposed approach with some well-known existing designs to highlight the performance benefits of the proposed design. Finally,hardware implementation of the proposed controller for trajectory tracking of Quanser’s single-linkflexible joint module is carried out,and the related results are presented.The remaining paper is organized as follows.In Section2,a mathematical model and FL-based controller design for the two-link robot manipulator is presented.An overview of the UDE approach and its application for robustification of the FL control is the subject of Section3.In Section4,the UDE-based controller–observer structure is presented whereas closed-loop stability of the overall system is presented in Section5.In section6,simulation results of the application of the proposed strategy are given.The results on comparative study of the proposed design with some well-known existing control strategies are the subject of Section7.In Section8,the results of the experimen-tal validation of the proposed design as applied to Quanser’s rigid linkflexible joint module are presented,and lastly,Section9concludes this work.2.STATEMENT OF THE PROBLEM2.1.Dynamics of robot manipulatorThe dynamics of a two-link rigid robot manipulator,shown in Figure1,can be obtained via the Euler–Lagrangian formalism as[20]106J.P.KOLHE ETAL.Figure 1.Two link planar robot manipulator.M.Â/R ÂC C.Â,P Â/C K.Â/D (1)where ÂD ŒÂ1Â2 T is the vector of joint positions,P ÂD ŒP Â1P Â2 T is the vector of joint velocities,M.Â/is the inertia matrix,C.Â,P Â/is the centripetal and Coriolis torque matrix,K.Â/represents the gravitational torques,and D Œ 1 2 T represents the input torque vector.For the two-link robotic manipulator,the various matrices appearing in Equation (1)can be obtained as M.Â/D "m 1l 21C m 2.l 21C l 22C 2l 1l 2cos Â2/m 2.l 22C l 1l 2cos Â2/m 2.l 22C l 1l 2cos Â2/m 2l 22#C.Â,P Â/D " m 2l 1l 2sin Â2P Â2.2P Â1C P Â2/m 2l 1l 2P Â21sin Â2#K.Â/D ".m 1C m 2/gl 1sin Â1C m 2gl 2sin .Â1C Â2/m 2gl 2sin .Â1C Â2/#(2)where l 1and l 2are the lengths of the links whereas m 1and m 2are the masses as shown in Figure 1.The quantity,g ,is the gravitational acceleration.The control objective is to design a robust con-troller using only joint position feedback such that the manipulator joint position vector,Â.t/,tracks the desired joint position Â?.t/as per the specifications imposed.2.2.Feedback linearization based controlThe FL [1,21]is one of the most prominent approaches in nonlinear control systems design.One of the advantages offered by the FL approach is that it provides a systematic framework for designing controllers for nonlinear systems.The inverse dynamics or computed torque methods in robotics are essentially the FL controllers.The basic idea underlying the FL is to seek a nonlinear state-coordinate transformation and nonlinear feedback control law under which the system exhibits linear closed-loop relationship.Once the system is linearized,any standard linear technique can be employed for designing the control law to achieve desired performance.To this end,the design consists typically of two steps:firstly,constructing a nonlinear control law as an inner-loop control and then designing a second stage or outer-loop control to obtain the desired closed-loop perfor-mance.In this work,the FL approach is employed for designing the tracking controller for robot manipulator.Consider the dynamics given by Equation (1).As the inertia matrix of the two-link robot manipulator is non-singular in the whole state-space,the dynamics can be rewritten asR ÂD M.Â/ 1C.Â,P Â/ M.Â/ 1K.Â/C M.Â/ 1 (3)For the system of (3),nonlinear coordinate transformation is not required,and the control,which achieves FL with the link positions as outputs can be obtained as [1]D C.Â,P Â/C K.Â/C M.Â/ (4)ROBUST CONTROL OF ROBOT MANIPULATORS BASED ON UDE107 where DŒ 1 2 T is the outer-loop control.Substituting the FL control(4)in Equation(3)results into a linear and decoupled input–output relationship asRÂD (5) Now,defining the outer-loop control, ,asi D RÂ?i C k i2.PÂ?i PÂi/C k i1.Â?i Âi/,i D1,2(6) where the starred quantities represent the reference trajectories of the corresponding link positions. Applying Equation(6)to Equation(5)results into the tracking error dynamics asR e ic C k i2P e ic C k i1e ic D0(7)where e ic.t/DÂ?i .t/ Âi.t/is the position tracking error of the i-th link.The controller gains,k ij,are the design parameters and are needed to be chosen such that desired tracking performance is achieved.As is well known,the FL control requires exact cancellation of the nonlinearities.It offers asymptotic tracking of the reference trajectory only when the models are known exactly,and the fed back states are measured without any error.In reality,these conditions are hard to meet,and so the FL control law may not offer satisfactory performance.Because modeling uncertainties are almost always present,there is a need to robustify the FL-based controller.Another important con-sideration in FL-based control law is its implementation.The controller requires knowledge of link velocities apart from the link positions.In view of the reasons stated earlier,it is necessary to address the issue of requirement of link velocities as well.3.UNCERTAINTY AND DISTURBANCE ESTIMATION BASED CONTROLLEROne approach for designing robust control for uncertain systems is to estimate the effect of uncer-tainties and disturbances acting on the system and compensate it by augmenting the controller designed for nominal system.Techniques like disturbance observer[22],unknown input observer [23],and perturbation observer[24]have been in place for quite sometime to estimate the effects of uncertainties and disturbances.Application of these techniques for estimating disturbance in robotic manipulators has also appeared[25,26].A time delay control(TDC)is one such well-known strat-egy used for estimation of system uncertainties[27].In TDC,a function representing the effect of uncertainties and external disturbances is estimated directly using information in the recent past,and then a control is designed using this estimate in such a way to cancel out the effect of the unknown dynamics and external disturbances.Application of TDC in robotics has also been reported in the literature[28,29].Following the line of TDC and addressing some issues associated with it,a novel UDE technique is proposed in[18].Since then,application of UDE in various contexts has appeared in the literature.An application of the UDE in robustifying a feedback linearizing control law for a robot having jointflexibility is presented in[30]wherein the effect of jointflexibility is treated as a disturbance.An application of UDE in overcoming the issues of requirement of knowledge of uncertainty bound and chattering in SMC can be found in[31].In[32]and[33],the UDE-based robust control designs for uncertain linear and nonlinear systems with state delays are presented, and the authors have shown that the designs offer excellent tracking and disturbance rejection per-formance.In[19],an application of the UDE in robustification of the input-output linearization (IOL)controller is presented,wherein the UDE-estimated uncertainties are used in robustifying an IOL controller.The robustification is achieved by estimating the uncertainties and external unmea-surable disturbances using the UDE and compensating the same by augmenting the IOL controller designed for nominal system.In this work,the UDE approach presented in[19]is used and extended for state estimation for designing of robust controller for robotic manipulators.3.1.FL+UDE controllerConsider the dynamics given by Equation(3).Because exact system model is rarely known in prac-tice,it becomes necessary to account for the modeling errors and inaccuracies.To this end,in the108J.P.KOLHE ET AL.present work,the inertia matrix,M.Â/is taken as uncertain with M.Â/D M o C M.Â/where M o is a chosen constant diagonal matrix and M.Â/is its associated uncertainty.Further,the matrices C.Â,PÂ/and K.Â/are assumed to be completely unknown.In view of the considered uncertainty in M../,the dynamics of Equation(3)can be rewritten asRÂDŒ M.Â/ 1C.Â,PÂ/ M.Â/ 1K.Â/C.M.Â/ 1 M 1o / C M 1oC d0(8)where d0may represent the effect of external disturbances,if any.Because C../and K../are assumed as completely unknown,they form a part of the total uncertainty d that needs to be estimated,and to this end,the total uncertainty d is defined asd D M.Â/ 1C.Â,PÂ/ M.Â/ 1K.Â/C.M.Â/ 1 M 1o/ C d0(9) In view of Equation(9),the dynamics of Equation(8)takes the formRÂD d C M 1o(10) where d DŒd1d2 T.With M o diagonal,it is straightforward to verify that the dynamics of Equation (10)is decoupled.In view of this,the dynamics for the i-th link can be written asRÂiD d i C b i i i I(11)where b i i are the diagonal elements of M 1o .To address the issue of the uncertainty,the FL controltakes the form asi D1b i i.u d i C i/I(12)where u d i is that part of the control,which cancels the effect of uncertainties.We designate the controller of Equation(12)as FL+UDE controller.Substituting Equation(12)in Equation(11) leads toRÂiD u d i C i C d i(13) From where one getsd i D RÂi u d i i(14) In view of Equation(14)and following the procedure given in[18,19],the estimate of d i is obtained asO diD G if.s/.RÂi u d i i/(15) where O d i is an estimate of d i,and G if.s/is afirst-order low passfilter with a time constant of if.G if.s/D11C if sI i D1,2(16)Selecting u d i D O d i and using Equation(15),one getsu d i D G if.s/.RÂi u d i i/(17) Now,solving for u d i leads tou d i D O d i DG if.s/1 G if.s/.RÂi i/(18)Substitution of Equations(6)and(18)in Equation(12)gives the FL+UDE controller.The time domain form of the resulting controller isi D1b i iÄ1ifPÂiC i C1ifZi dt(19)ROBUST CONTROL OF ROBOT MANIPULATORS BASED ON UDE109 Clearly,under the assumption of O d i d i,application of the control(19)to the dynamics of(10) results into the same error dynamics as given by Equation(7),thus eliminating the effect of uncer-tainties and therefore robustifying the FL controller.The robustified FL control(12)has been designated as the FL+UDE controller.Whereas the controller achieves the objective of robustifi-cation of the FL control,the implementation of the same requires measurement of joint positions as well as velocities as is obvious from Equation(19).The estimation of velocities are obtained by UDE-based observer as presented in the next section.4.UNCERTAINTY AND DISTURBANCE ESTIMATION BASEDCONTROLLER–OBSERVER STRUCTUREThe FL+UDE controller(12)or alternatively(19)requires link velocity measurement apart from the link positions for its implementation.As a solution to this problem,a design of UDE-based robust observer is proposed in this section.4.1.Uncertainty and disturbance estimation based observerAs is obvious from Equation(11),the dynamics are decoupled,and hence observer design for i-th link only is presented.To this end,defining x i1DÂi and x i2D PÂi,the dynamics of Equation(11) can be rewritten in a phase variable state-space model form asP x i1D x i2P x i2D b i i i C d iy i D x i1(20) Defining the state vector as x ip DŒx i1x i2 T DŒÂi PÂi T,the system of(20)can be written asP x ip D A ip x p C B ip i C B id d iy ip D C ip x ip(21)whereA ip D Ä0100I B ip DÄb i iI B id DÄ1I C ip DŒ10It may be noted that a conventional Luenberger observer will not be able to provide accurate state estimation for the plant of Equation(21),owing to the presence of the uncertainty.In view of this,a Luenberger-like observer of the following form is proposed asP O xipD A ip O x ip C B ip i C B id O d i C L i.y ip O y ip/O y ip D C ip O x ip(22) where L i DŒˇi1ˇi2 T is the observer gain vector.The observer however requires estimate of the uncertainty,that is,O d i.Because the uncertainty is the same as present in Equation(11),the UDE-estimated uncertainty is used in the observer(22)too,giving rise to the UDE-based controller–observer structure.It may be noted that the proposed observer does not need an accurate plant model and is robust.Noting that O x ip DŒO x i1O x i2 T DŒOÂi P OÂi T,the FL+UDE control of(12)with i of Equation(6)and u d i of Equation(18),both evaluated using the UDE observer estimated states given by Equation(22),the issue of requirement of link velocity measurement is addressed.5.CLOSED-LOOP STABILITYThe FL+UDE control(12)using i of Equation(6)evaluated using the observer estimated states and using u d i D O d i can be written asi D1b i ihRÂ?iC k i1.Â?i OÂi/C k i2.PÂ?i P OÂi/ O d ii(23)110J.P.KOLHE ET AL.Denoting the reference state vector R i DŒÂ?i PÂ?iT and defining the state feedback gain vector,K ipas K ip DŒm i1m i2 with the elements as m i1D k i1b ii ,m i2D k i2b ii,the controller(23)is rewritten asi D K ip O x ip C K ip R i1b i iO diC1b i iRÂ?i(24)It is straightforward to show that the dynamics of reference state vector,R i,can be written asP RiD A ip R i C B id RÂ?i(25) Defining the state tracking error,e ic D R i x ip and using Equations(21),(24),and(25),and carrying out some simplifications lead to the following state tracking error dynamicsP e ic D.A ip B ip K ip/e ic .B ip K ip/e io B id Q d i(26) where Q d i D d i O d i is the uncertainty estimation error,and e io D x ip O x ip is the observer state estimation error vector.Next,the observer error dynamics can be obtained by subtracting Equation(22)from Equation(21)asP e io D.A ip L i C ip/e io C B id Q d i(27) Lastly,the uncertainty estimation error dynamics is obtained.From Equations(14)and(15),the estimate of the uncertainty,d i,is given asO diD G if.s/d i(28) From Equation(28),one hasd i DO diG if.s/(29)With the uncertainty estimation error defined as Q d i D d i O d i and using Equation(16)and carrying out some simplifications giveP Q d i D1ifQ diC P d i(30)Combining Equations(26),(27),and(30)yields the following error dynamics for the controller–observer combination2 64P e icP e ioP Q d375D264.A ip B ip K ip/ .B ip K ip/ B id0.A ip L i C ip/B id00 1if375264e ice ioQ di375C2641375P di(31)From Equation(31),the system matrix being in a block triangular form,it can be easily verified that the eigenvalues of the system matrix are given byj sI .A ip B ip K ip/jj sI .A ip L i C ip/jj s .1if/j D0(32)Noting that the pair.A ip,B ip/is controllable,and the pair.A ip,C ip/is observable,the controller gain,K ip,and the observer gain,L i,can be chosen appropriately along with if>0to ensure sta-bility for the error dynamics.As the error dynamics is driven by P d i,it is obvious that,for bounded j P d i j,bounded input-bounded output stability is assured.Finally,if the rate of change of uncertainty is negligible,that is,if P d i 0,then the error dynamics is asymptotically stable.As has been stated,the error dynamics(31)is asymptotically stable if P d i 0.However, asymptotic stability for the error dynamics can always be assured if some higher derivative ofROBUST CONTROL OF ROBOT MANIPULATORS BASED ON UDE111 the uncertainty is equal to zero.For example,if P d i¤0but some higher derivative of d i is zero, then the asymptotic stability of the error dynamics can be guaranteed by choosing an appropriate higher-orderfilter[19]in place of the one chosen in Equation(16).As stated in Section3.1,the u d i is that part of control,which cancels the effect of uncertain-ties.It is important to address the issue of existence of such a control.Although a detailed study on the existence of u d i is not attempted here,some comments can be offered.The control u d i is derived under the assumption that some derivative of d i is negligibly small,that is,any d i that can be approximated by functions of the type a o C a1t C a2t2C...where a i,i D1,2,:::are unknown constants.The control,u d i,does not exist for systems in which d i,P d i and so on are discontinuous. For systems where the derivatives of d i arefinite and small,instead of asymptotic stability,one may get uniform ultimate boundedness.This facilitates the design of u d i in many practical situa-tions.Now some comments on the choice of thefilter time constant are in order.From Equations (29)–(30),it can be observed that the choice of thefilter time constant, if,affects the uncertainty estimation error accuracy,that is,the uncertainty estimation error,Q d i,is proportional to if imply-ing that smaller value of thefilter constant leads to a smaller estimation error.It can also be noted that estimation does not depend on the magnitude of the uncertainty as such,but does depend on its rate of change.Further,one can note that thefilter time constant acts as the time constant of the uncertainty estimation error dynamics,meaning that smaller value of thefilter constant leads to faster uncertainty estimation convergence.From control efforts’point of view,the magnitude of the control increases with1= if as is evident from Equation(19).Thus,the choice of thefilter con-stant is a tradeoff between estimation accuracy and its rate of convergence on the one hand,and the control efforts on the other hand.6.SIMULATIONS AND RESULTSIn this section,numerical simulation results using the FL+UDE controller of(12)with i of Equation(6)and u d i of Equation(18),both evaluated using the UDE observer estimated states given by Equation(22)are presented.The link parameters used in the simulations,as taken from [34],are given in Table I.In simulations,the tracking specification for each link is considered in terms of the desired settling time and damping ratio as given in Table I.Consequently,the controller gains k i1and k i2required in Equation(6)are chosen to satisfy these specifications.The observer gains,ˇij’s are obtained by placing the observer poles at 300for both the links.The initial condi-tions for the observer as well as for the plant variables are taken as zero.In simulations,uncertainty is introduced by considering m1and m2uncertain by 50%of their respective nominal values. Further,a load disturbance torque of 30%of maximum input torques is considered.The desiredposition trajectory is taken asÂ?1D30sin.t/deg andÂ?2D 30sin.t/deg.The values of b i iare taken as inverse of the diagonal elements of the inertia matrix given in Equation(2)with cosine term approximated to unity.Actuator saturation limits of 1max D˙50N-m and 2max D˙10N-m have been considered in the simulations.With these data,simulations are carried out,and the results are presented in Figure2.In Figures2(a)–(b),the reference,estimated and actual joint positions are plotted,and it can be seen that the observer estimates the states accurately.Also,from time historyTable I.Simulation parameters.Parameter Definition Valuem1Mass of link12kgm2Mass of link21kgl1Length of link12ml2Length of link21mg Gravitational acceleration9.8m/s2t s1,t s2Desired settling times0.5s1, 2Damping ratios11f, 2f Filter time constants0.05s112J.P.KOLHE ETAL.−30−20−100102030−30−20−1001020300246810−40−202040600246810−200204060(a)(b)(c)(e)(f)(g)(h)(d)Figure 2.Performance of UDE-based controller.ROBUST CONTROL OF ROBOT MANIPULATORS BASED ON UDE113 of reference trajectory,it can be seen that the UDE-based controller–observer offered a highly sat-isfactory tracking performance despite the significant model uncertainty.The reference,estimated and actual link velocities are given in Figures2(c)–(d),and one can observe that the estimation is quite satisfactory.The time histories of the actual and estimated uncertainties for both the links are given in Figures2(g)–(h)from where it can be observed that the UDE estimator has estimated the uncertainty quite accurately.The time histories of the input torques are shown in Figures2(e)–(f).PARISON WITH EXISTING DESIGNSSimulations are carried out to compare the performance of the proposed design with some well-known existing controllers.The controllers considered for comparison purpose are:(1)gravity compensated PD control;(2)FL-based control;(3)FL controller with Lyapunov-based outer-loop design;and(4)controller based on SMC theory.A brief of the controllers are as follows:Design-1:Proportional-derivative control with gravity compensation.A gravity-compensated PD controller[1]of the following formD K p.Â? Â/C K d.PÂ? PÂ/C N K.Â/(33) where K P>,K D>0are the diagonal gain matrices,and N K.Â/is the nominal gravity matrix.It has been shown that the simple PD controller with gravity compensation offers robustness for set-point control of robot manipulators[12].For simulations,gains K P and K D are chosen to satisfy the desired settling time and damping ratio given in Table I.The design is referred to as Design-1. Design-2:Feedback linearization based control.An FL[1]-based controller without robustification is considered as Design-2for comparison.The control law isD N C C N K C N M (34) where N M,N C,and N K are the nominal values for the respective matrices,which are obtained from Equation(2)by using the parameters given in Table I.The outer-loop control, ,is chosen asD RÂ?C K P.Â? Â/C K D.PÂ? PÂ/(35) wherein K P and K D are the diagonal gain matrices chosen in similar manner as carried out in Design-1.Design-3:Lyapunov-based control.FL control with Lyapunov-based outer-loop design given in[1]is used as Design-3in this ing Lyapunov’s second method,the control law designed for two-link robot manipulator takes the formD N C C N K C N M (36) with the outer-loop design given byD RÂ?C K P.Â? Â/C K D.PÂ? PÂ/C W(37)where W DŒW1W2 T withW i D 8<:D i B T i P i e ij B TiP i e i jif j B TiP i e i j> iD i B T i P i e iif j B TiP i e i j< i,i D1,2(38)The P i is a unique symmetric positive definite matrix satisfying the Lyapunov equationA T i P i C P i A i C I D0(39)。
基于曲线插补的多轴联动交叉耦合控制方法

基于曲线插补的多轴联动交叉耦合控制方法赵国勇;赵玉刚【摘要】针对高精度轮廓跟踪需要,将曲线插补和交叉耦合控制器结合起来进行研究。
在每个采样周期根据各轴反馈的实际刀具位置与插补缓冲区中存储的一定数量的插补点,研究了一种"三点圆弧法"轮廓误差计算模型,并研究了轮廓误差补偿修正量计算及分配方法。
在数控试验台上跟踪一段三次非均匀有理B样条轮廓曲线,对比试验表明,所提出的基于曲线插补的轮廓误差交叉耦合控制方法能够有效减小轮廓误差,获得更高轮廓精度。
%Aiming at the tracking demand of high precision contour,the cross-coupled controller integrated with curve interpolation was studied.According to the real cutter positions from each axis feedback and the interpolation dots stored in the interpolation buffer in every sampling period,a "three-point arc approach" contour error computing model was developed.Moreover,the contour error compensated correction quantity computation and distribution approach was put forward.A cubic Non-Uniform Rational B-Spline Curve(NURBS)profile curve on the numerial control experiment table was tracked.The experiment results showed that the developed contour error cross-coupled control approach based on curve interpolation could effectively reduce contour error and obtain satisfactory contour precision.【期刊名称】《计算机集成制造系统》【年(卷),期】2011(017)009【总页数】5页(P1968-1972)【关键词】曲线插补;交叉耦合控制;轮廓误差;补偿修正量;机床【作者】赵国勇;赵玉刚【作者单位】山东理工大学精密制造与特种加工省级重点实验室,山东淄博255049;山东理工大学精密制造与特种加工省级重点实验室,山东淄博255049【正文语种】中文【中图分类】TH13数控机床轮廓精度的提高与机床各进给轴的动态特性是否匹配密切相关。
DesignElements

Subsystem
Many-to-Many Mapping
7
Identifying Design Classes
An analysis class maps directly to a design class if:
It is a simple class It represents a single logical abstraction
Boundary classes placed in separate packages
11
Boundary classes packaged with functionally related classes
Packaging Tips: Functionally Related Classes
15
A
X
A
B
Upper Layer
X
Lower Layer
B
X
C
X = Coupling violation
Example: Registration Package
MainStudentForm 1 0..1 <<boundary>> RegisterForCoursesForm 1 1 <<control>> RegistrationController MainRegistrarForm 1 0..1 <<boundary>> CloseRegistrationForm
3
Identify Design Elements Overview
Supplementary Specifications
基于CANopen协议的转台双电机同步控制

基于CANopen协议的转台双电机同步控制钱俊璋;马文礼;林梦云【摘要】After a brief introduction of the CANopen protocol,this paper describes the design of a dual-motor synchronization control system based on CANopen protocol.CANopen-based servo control is implemented successfully on the elevation axis of the test turntable.Cross-coupled control algorithm is adopted.The tracking curve is y =sin (0.1 t) in the experiment,and the tracking accuracies reach 0.2980" and 0.2813" respectively for single-motor control and dual-motor control.The experiment results show that this system has quick response,high reliability and good synchronization and can meet design requirements.%对CANopen协议进行了简单介绍,设计了一套基于CANopen协议的双电机同步控制系统.并在实验转台的俯仰轴上成功实现了基于CANopen的伺服控制.控制算法采用交叉耦合的控制.实验跟踪曲线为y=sin(0.1t),单电机控制和双电机控制的跟踪精度分别为0.298 0"和0.281 3".结果表明,系统响应迅速,可靠性高,同步性好,满足设计要求.【期刊名称】《电气自动化》【年(卷),期】2017(039)006【总页数】3页(P17-18,50)【关键词】双电机;CANopen协议;交叉耦合控制;转台;同步性【作者】钱俊璋;马文礼;林梦云【作者单位】中国科学院光电技术研究所,四川成都610209;中国科学院大学,北京100049;中国科学院光电技术研究所,四川成都610209;中国科学院光电技术研究所,四川成都610209;中国科学院大学,北京100049【正文语种】中文【中图分类】TM3410 引言引言单电机直接驱动的控制方式广泛应用在光电经纬仪和大型望远镜中[1-3]。
半导体专业名词解释
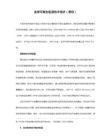
Cd cadmium
AWS advanced wet station
Manufacturing and Science
Sb antimony
===B===
B billion; boron
Ba barium
BARC bottom antireflective coating
BASE Boston Area Semiconductor Education (Council)
ACF anisotropic conductive film
ACI after-clean inspection
ACP anisotropic conductive paste
ACT alternative control techniques; actual cycle time
Al aluminum
ALD atomic layer deposition
ALE atomic layer epitaxy; application logic element
ALS advanced light source; advanced low-power Schottky
===A===
A/D analog to digital
AA atomic absorption
AAS atomic absorption spectroscopy
ABC activity-based costing
ABM activity-based management
AC alternating current; activated carbon
基于FPGA的交叉耦合控制器的设计与实现
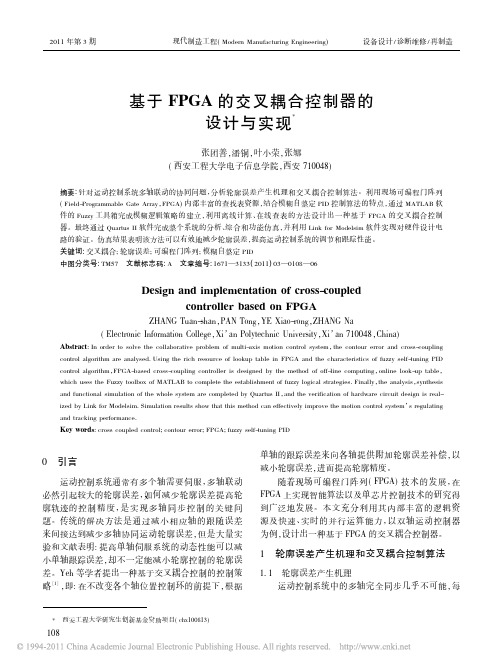
2011年第3期现代制造工程(Modern Manufacturing Engineering)设备设计/诊断维修/再制造基于FPGA的交叉耦合控制器的设计与实现*张团善,潘铜,叶小荣,张娜(西安工程大学电子信息学院,西安710048)摘要:针对运动控制系统多轴联动的协同问题,分析轮廓误差产生机理和交叉耦合控制算法。
利用现场可编程门阵列(Field-Programmable Gate Array,FPGA)内部丰富的查找表资源,结合模糊自整定PID控制算法的特点,通过MATLAB软件的Fuzzy工具箱完成模糊逻辑策略的建立,利用离线计算、在线查表的方法设计出一种基于FPGA的交叉耦合控制器。
最终通过Quartus II软件完成整个系统的分析、综合和功能仿真,并利用Link for Modelsim软件实现对硬件设计电路的验证。
仿真结果表明该方法可以有效地减少轮廓误差,提高运动控制系统的调节和跟踪性能。
关键词:交叉耦合;轮廓误差;可编程门阵列;模糊自整定PID中图分类号:TM57文献标志码:A文章编号:1671—3133(2011)03—0108—06Design and implementation of cross-coupledcontroller based on FPGAZHANG Tuan-shan,PAN Tong,YE Xiao-rong,ZHANG Na(Electronic Information College,Xi’an Polytechnic University,Xi’an710048,China) Abstract:In order to solve the collaborative problem of multi-axis motion control system,the contour error and cross-coupling control algorithm are analysed.Using the rich resource of lookup table in FPGA and the characteristics of fuzzy self-tuning PID control algorithm,FPGA-based cross-coupling controller is designed by the method of off-line computing,online look-up table,which uses the Fuzzy toolbox of MATLAB to complete the establishment of fuzzy logical strategies.Finally,the analysis,synthesis and functional simulation of the whole system are completed by Quartus II,and the verification of hardware circuit design is real-ized by Link for Modelsim.Simulation results show that this method can effectively improve the motion control system’s regulating and tracking performance.Key words:cross coupled control;contour error;FPGA;fuzzy self-tuning PID0引言运动控制系统通常有多个轴需要伺服,多轴联动必然引起较大的轮廓误差,如何减少轮廓误差提高轮廓轨迹的控制精度,是实现多轴同步控制的关键问题。
孵化

GPC control design for a Temperature and Humidity Prototype using ICD Analysis.J. Licéaga-Castro©, C. Ramírez-España©, E. Licéaga-Castro§AbstractIn this paper the design of a multivariable control system for an air conditioning process is presented. The controller design is based on the classical Generalized Predictive Control (GPC)scheme, while the resulting stability, robustness and performance properties are analysed in the context of Individual Channel Design (ICD). The design specifications in this work are those established by the Mexican Government Metrology Office (Centro Nacional de Metrología, México); it indicates that the temperature and humidity values must be kept within certain ranges. The designed control system has been tested using the Gunt Hamburg ET605 Recirculating Air Conditioning Trainer. Real time results are included in order to show the excellent performance of the control design.1 IntroductionAir conditioning systems are mainly installed in offices and houses. In general the design specifications for these processes in terms of accuracy, time response and noise rejections are not very demanding, so that traditional PI controllers have satisfactory performance. Nonetheless, there are applications where the specifications are rather demanding, as it is the case of industrial metrology laboratories, which require very tight control of temperature, humidity and sometimes flow and pressure. Under these circumstances the performance of PI controllers is not satisfactory anymore. A characteristic of these kind of processes is their very slow dynamics, which normally would require high gain controllers and schemes for dealing with control saturation. An alternative to such schemes is the Generalised Predictive Control (GPC) introducedin [1, 2]. The original GPC scheme has been modified in order to improve its robustness robustness and has also been applied to multiva-.© Departament of Mecatronics of the Instituto Tecnológico yde Estudios Superiores de Monterrey-Campus Estado deMéxico. email: jliceaga@itesm.mx, ciref@itesm.mx§ SEPI-ESIME Ticoman Intituto Politecnico Nacional. email: eliceagac@ riable systems [3,4]. Successful applications of the GPC to thermal processes have been reported in [3, 5, 6, 7, 8, 9]. There are two key features an industrial control design must satisfy in order to succeed in the production arena: simplicity and transparency. Indeed, a industrial controller should be easy to implement with the lowest possible computational effort; as for transparency,it should be easy to understand, operate and manipulate by the engineers responsible of its operation. A frame work of analysis which solves the problem of transparency is the Individual Channel Analysis and Design (ICD) [10, 11]. A key concept of ICD is the Multivariable Structure Function, which allows the analysis of the dynamical structure and coupling of a multivariable system using classical tools: Bode and Nyquist plots. Through ICD it is possible to determine if customer specifications can be met and the price in terms of control complexity or sophistication. In this work it is shown, through ICD techniques, that the air conditioning multivariable control problem of a standard metrology laboratory can be solved successfully via a diagonal GPC controller. The control problem is stated as the regulation of a 2u2 MIMO control where the output variables are the temperature and the humidity. The input variables are the voltages applied to the heater and the humidifier drivers. It is required that the temperature should be 20, s0.3o C within an hour or s0.5o C within 12 hours of operation and relative humidity 45 %, s 5 % within 4 hours of operation. The Gunt Hamburg ET605 Recirculating Air Conditioning Trainer [14] was used as a bank-bench for the test of the control scheme proposed. The paper is organized as follows. In Section 2 the MIMO models for the four possible operating regimens are presented. In Section 3 the dynamical of the system is analyzed, that is, coupling quantification, open loop stability and structural robustness (the number of right hand plane zeros (RHPZ) and the number of right hand plane poles (RHPP)) via the Multivariable Structure Function. In Section 4 a brief summaryof the classical GPC is described. In Section 5 the controller design and a reformulation of theProceedings of the 2006 IEEEInternational Conference on Control ApplicationsMunich, Germany, October 4-6, 2006WeC07.4controllers to comply with the ICD structure, as well as stability, robustness and performance analysis is presented. In Section 6, typical real time responses are presented. That section is followed by the Conclusions.2 MIMO process modelIn this work a control system design for the GuntHamburg ET605 Recirculating Air Conditioning Trainer build by Gunt is presented. The ET605 system can operate in four possible regimes: Heating-ON and humidifier-ON, Heating-ON and humidifier-OFF, Heating-OFF and humidifier-ON, Heating-OFF and humidifier-OFF. The 2u 2discrete matrix transfer functions for these operating regimes were estimated according to the Strej method. The results obtained are:1. Heating-ON and Humidifier-ON: on on on 12Y(z)G (z)U(z)[g (z),g (z)]U(z)(1)2. Heating-ON and Humidifier-OFF:(z)(z)]U g ,(z)[g (z) U (z)G (z)Y off on 21on_off (2)3. Heating-OFF and Humidifier-ON:(z)(z)]U g ,(z)[g (z) U (z)G (z)Y on f of 21off_on (3)4. Heating-OFF and Humidifier-OFF:(z)(z)]U g ,(z)[g (z) U (z)G (z)Y off off 21off (4)The input and output vectors are defined as T volts 2volts 1](z)u ,(z)u [(z)U a ndT Humidity 2%Celsius 1](z)y ,(z)[y (z)Y r espectively.The columns of the transfer matrices of equations 1 to 4 are:»»»»¼º««««¬ª »¼º«¬ª 0.459091.41281z -z 0.01490-0.01930z -0.486601.45212z -z 0.008480.01079z (z)g (z)g (z)g 2on 21on 11on 1»»»»¼º««««¬ª »¼º«¬ª 0.25381.2039z -z 0.01544-0.02426z -0.532641.50015z -z 0.008790.01084z (z)g (z)g (z)g 2off21off11off 1»»»»¼º««««¬ª »¼º«¬ª 0.921531.91993z -z 0.04683-0.04771z 0.863641.86025z -z 0.00079150.0008311z (z)g (z)g (z)g 2on 22on 12on2»»»»¼º««««¬ª »¼º«¬ª 0.242521.13298z -z 0.011240.11362z 0.819181.81422z -z 0.001120.00119z (z)g (z)g (z)g 2off22off12off 2The individual transfer function for heater and humidifier in ON and OFF conditions are denoted as:on ij g and off ij g , i = 1,2, j = 1, 2. The discrete transfer functions include the ZOH (zero order holds) with a sampling period of 1 minute.3 System AnalysisIn this section the dynamical structure of the air conditioning system ET605 is analyzed in terms of its multivariable structure function (MSF) [10,12]. It is possible to define two MSF’s for a 2×2 system. Each one of these functions is related to the two possible input-output pairings. ICD is based on the resulting MSF, as a matter of fact, the dynamical structure, coupling and control design is dictated by the frequency response of the corresponding MSF. A series of design examples varying from the coupled to strongly coupled non-minimum phase plants have been reported in [12]. As follows the analysis and design procedures reported in [10] are applied to the air conditioning system ET605. By pairing input-i to output-i (i =1, 2) the MSF obtained isz g z g z g z g z 22112112J , [8, 9,10]. Every operating condition defined by equations 1-4 has associated a MSF Ȗ(z). The above analysis also shows that if the pairing input-i to output-j with i z j (i = 1, 2 and j = 1, 2) is considered, then the magnitude of the resultingMSFz g z g z g z g z b 21122211J , is very large, it is as a matter of fact the inverse of the magnitude of Ȗ(z) corresponding to the previous pairing Figure (1). Thus, the coupling resulting with this input -output channel definition is very high. In this case it is obvious that the ET605 process was designed to operate according to the input-i to ouput-i(i = 1, 2) pairing. Designs with the i z j ( i = 1, 2 and j = 1, 2) pairing will render unrealistic control systems. On the other hand, there are four MIMO models -one for each regimen-. This situation normally requires the implementation of anadaptive controller or a scheduling strategy inorder toFigure 1. Nyquist Diagrams of Ȗ(z) for the 4 regimens.coupe with the variations of the process dynamics along the four regimens. Nonetheless, the analysis of the four Ȗ(z) functions reveals that the change of regime does not impose changes in the dynamical structure of the process. This fact is shown in [10, 11, 12]. Indeed, Figure 1 shows that the system is always minimun-phase and almost decoupled, due to the low gain of Ȗ(z) at the cross over frequencies [10, 11, 12]. In addition the system is stable. Thus, it is concluded that there exist a fixed linear diagonal robust controller for the operational regimes defined by equations 1-4. From figure 1 it is clear that the coupling is higher during the ON-ON regime. The model corresponding to this operating condition is used in order to design a fix controller for the four regimes. Due to the dynamical characteristics of the models the design based on the ON-ON model will satisfy the design requirements of the other three operational conditions [13]. In the following section the GPC strategy is summarized and recasted in the ICD context.4 Generalized Predictive Con- trolLet the SISO CARIMA model't q C t u q B t y qA [1111 (5)wherena na q a q a q A 1111,nb nb q b q b bq B 1101,11 'q ,and t u and t y the input and output signalsrespectively. Assuming11 q C ,'t [represents an integrated white noise or a randomwalk, which is a mo del well accepted for disturbances,[5]. Let the cost function>@¦21221{,N N j j t w j t y E N N J >@¦ ' 212}1N j j t u j O (6)where:w(t) is a reference signal, N 1is the minimum costing horizon (it is a common practice to set N 1=0), N 2is the maximum costing horizon; and O O j is the control signal weighting factor. The control law which minimizes the cost function (6) with the restriction (5) and a control horizon N 2equal to 1 is given by:f w -Tg 1)-u(t =u(t)(7)where T N 21y(t)]F ;y(t);F y(t);[F f 2 . F j is thesolution of the Diophantine equation 1 = E j+1ǻA +q -(j+1)F j+1 with initial solution 1 = E 1ǻA + q -1F 1,with g -T is the first column of (G T G + ȜI)-1G T where:»»»»»¼º«««««¬ª 032101011100000g g g g g g g G n n n (8) B E G j j ,>@TN G G G G 2,,,21 , and>@2,,2,1N t w t w t w w T a vectorcontaining the reference signal with w t w N t w t w t w 221 .The reader is referred to [1] and [2] for further details of the basic GPC.5 Controller Design and Robustness AnalysisAs follows the control law (7) is reformulated according to the ICD analysis. Under this framework the selection of the weighting factor Ȝ,in equation (6) is a clear and transparent process, in terms of robustness and performance requirements. It is well known that Ȝ has a gain effect on the controller and is normally designed via try and error but, thanks to the reformulation of the control law, its design can be done via simple Bode analysis. Let the control law of eq (7):f g w g t u q T__11 (9)thus, (1-q -1)u(t) = (g 1+g 2+…+g 10)w-(g 1F 1+g 2F 2+ … + g 10F 10) y(t), which can be rewritten as (1-q -1)u(t) = W i w _ Fl i y(t). Where W i = (g 1+g 2+…+g 10) and Fl i = (g 1F 1+g 2F 2+…+g 10F 10);with i = 1 for controller based on g 11(z) and i =2 for controller based on g 22(z). Therefore,t e q t u 111(10)wheret y Fl w W t e i i (11) Thus, the block diagram of the reformulatedcontroller is shown in Figure 2.Figure 2. Reformulated GPC controller.Thus, the ICD channels, [10], for the MIMO control system are given by:j i j i h g K C j ii i i z ¸¸¹·¨¨©§,2,1,2,1,1__J (12) where:2,1,1_i g K Fl g K Fl h ii i i iii i (13) 2,1,1_i z zFl K ii (14) From the solution of the Diophantine equation and the matrix transfer function of equation 1, with N 2=10, Ȝ1= 1:4 and Ȝ2= 20. Moreover, Fl i (z) has the form2,1,2120 i za a z a z Fl ii i i (15) The conditions for robustness and performance for a 2x2 MIMO control system with a MIMO diagonal controller are described in [10, 11]. Nevertheless, this conditions have to be modified in order to include the feedback filters Fl i (z) of equation 15. These conditions are summarized in table 1.StructuralRobustness k 1g 11 and k 2g 22 with appropriate gain andphase margins Ȗh 1 and Ȗh 2 now here nearthe point ( 1 ,0 ) .Stability Robustness C 1 and C 2 with appropriate gain and phase margin .Performance Adequate Bode properties of the closedloop transfer functions of C 1and C 2(including gain W iof figure 2 ) .Table 1. Conditions for Robustness and Performance.The controller must satisfy the design requirements for the four operating regimes. The gain and phase margins of _k i g ii , for all regimens, are within 39.3 dB´s and 70o for i 1, respectively; and 19.9 dB´s and 56.9o for i = 2, respectively. Also, Figures 3 and 4 show the Nyquist diagrams of Ȗh 2and Ȗh 1, for all regimens. From this figures it is possible to see minimum differences between them, as expected from the analysis of section 3, and all of them are nowhere near the point (1,0). Therefore, conditions for structural robustness are satisfied. Figures 5 and 6 show the open loop Bode diagrams of channel 1 and Channel 2 (12) for all regimens. The phase and gain margins of these diagrams are within 51.5o and 19.2 dB´s for channel 1, and 47.1o and 20.6 dB´s for channel 2. Thus, both channels are robust. Finally, the closed loop Bode diagrams of Channel 1 and 2, including gain W i , are shown in figures 7 and 8. For both cases is appreciable an adequate behaviour at low frequency and a roll-off of -20 dB.s, therefore, performance conditions are accomplish.Figure 3. Nyquist Diagram for Ȗh 1.Figure 4.Nyquist Diagram for Ȗh 2.6 Real time responsesThe real time responses of the control system are shown in figure 9. In Figure 9.a the output responses of the temperature and humidity are shown. These responses include the rejection to step perturbations in humidity and temperature. These perturbations where introduced at sampling time t=60 and removed at t=180. This figure shows that the responses comply with the requirements of design described in Section 1. Also, from figure 9.b, it is possible to see that the effort of the control signals are within the limits of saturation (0 ĺ 10 Volts) of the heater andhumidifier.Figure 5. Bode diagram for channel 1 openloop.Figure 6. Bode diagram for channel 2 openloop.7 ConclusionsUsing ICD analysis it was possible to design a diagonal multivariable GPC controller for the Gunt Hamburg Air Conditioning Trainer ET605. The control system here presented satisfies robustness conditions and the requirements of design for typical metrology labs. The GPCalgorithm was selected due to its effectiveness dealing with systems dominated by very slow dynamics. It is shown by the ICD analysis that the system is practically decoupled at its four operational regimes over the required band-widths. Therefore a diagonal controller satisfies the robustness and performance for the four operational regimes. Also due to the fact that there are no structural differences among the matrix transfer functions of the process representing its four regimes, as depicted by Multivariable Structure Function, it was possible to implement a fixed multivariable controller for all regimes. This controller was designed based on the model which presents the highest coupling. Additionally, thanks to a reformulation of the GPC controller and the use of the single channels, a clear and transparent way for the selection of the weighting factor Ȝof the GPC controller was found.Figure 7.Bode diagram for channel 1 closedloop.Figure 8.Bode diagram for channel 2 closedloop.Figure 9. Real time responses. References[1] Clarke D.W., Mohtadi C., Tuffs P.S.Generalized Predictive Control, Part 1 theBasic Algorithm and Part 2 Extensions andInterpretations. Automatica, 1987,Vol 23, No.2 pp 137-160.[2] Clarke D.W. and Mohtadi C. Properties ofGeneralized Predictive Control. Automatica,1989,vol. 25, No. 6, pp 859-875.[3] Chi-Ming Chow, Kusnetsov A., Clarke D.Application of multivariable generalizedpredictive control to the simulink model of apaper machine, pp 1675-1681.[4] Jöel Bordeneuve and Cyril Vaucoret; RobustMultivariable Predictive Control. IEEEControl Systems Magazine, April 2001,pp.54-65.[5] Rossiter J.A. Model Based Predictive Control.A practical approach. CRC Press, 2003.ISBN: 0-9493-1291-4.[6] Petrault Christine, Mehdi Driss, TrigeassouJean-Claude. C.G.P.C.: An Application to anAir Conditioning System. Proceedings of theAmerican Control Conference, June 1997,pp.1951-1952.[7] Clarke David W. Application of GeneralizedPredictive Control to Industrial Processes.IEEE Control Systems Magazine, April 1988,pp.49-55.[8] Kouvaritakis B., Rossiter J.A., Gossner J.R.Improved algorithm for multivariable stablegeneralized predictive control. IEE Proc.Control theory appl. Vol. 144, No. 4, July1997, pp 309-312.[9] Dumur D., Boucher P., Murphy K.M., DéquéF. Comfort Control in Residential Housingusing Predictive Controllers. Proceedings ofthe IEEE International Conference on ControlApplications, October 1997, pp 265-270. [10] O.Reilly, J. and Leithead, W.E.;Multivariable control by Individual ChannelDesign. International Journal of Control,1991, Vol. 54, No. 1, pp1-46.[11] Leithead, W.E. and O.Reilly, J.; Performanceissues in the individual channel design of 2-input 2-output systems. International Journalof Control, 1991, Vol. 54, No. 1, pp47-82. [12] Liceaga E., Liceaga J., Ugalde C.; Beyondthe existence of diagonal controllers: Fromthe relative gain array to the MultivariableStructure Function. Proceedings of the 44thIEEE, CDC ECC-05. Seville,Spain, December 2005.[13] Leithead, W.E. and O.Reilly, J. UncertainSISO systems with fixed stable minimumphase con-rollers: Relationship of closed loopsystems to plant RHP poles and Zeros.International Journal of control, 1991, Vol.53, pp 771-798.[14] Instruction Manual. G.U.N.T. GerätebauGmbH PO. Box 1125 D-22881 BarsbütelGermany.。
通信工程专业英语词汇
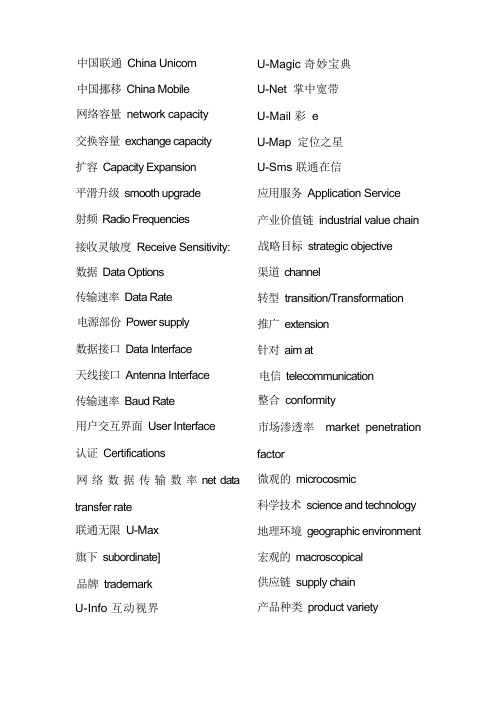
中国联通China Unicom中国挪移China Mobile网络容量network capacity交换容量exchange capacity扩容Capacity Expansion平滑升级smooth upgrade射频Radio Frequencies接收灵敏度Receive Sensitivity: 数据Data Options传输速率Data Rate电源部份Power supply数据接口Data Interface天线接口Antenna Interface传输速率Baud Rate用户交互界面User Interface认证Certifications网络数据传输数率net data transfer rate联通无限U-Max旗下subordinate]品牌trademarkU-Info 互动视界U-Magic 奇妙宝典U-Net 掌中宽带U-Mail 彩eU-Map 定位之星U-Sms 联通在信应用服务Application Service产业价值链industrial value chain 战略目标strategic objective渠道channel转型transition/Transformation推广extension针对aim at电信telecommunication整合conformity市场渗透率market penetration factor微观的microcosmic科学技术science and technology 地理环境geographic environment 宏观的macroscopical供应链supply chain产品种类product variety价格水平price level销售方式modes of sale客户client敏感sensitivity营业场所business ground or office投诉complaintelecom operators 电信运营商指标index第二手资料secondary source data 第一手材料the first-hand material/first-hand data分销商distributor管理者administrative supervisor 增值value increment副总经理deputy general manager 交通枢纽traffic hub渤海Bohai Sea华北平原North China Plain人力资源human resources奖惩rewards and punishment长江三角洲the Yangtze Delta 珠江三角洲Pearl River Delta经济圈economic circle经济一体化economic integration 地形terrain地貌topographic feature海岸线coast line造纸paper making胶片film化工chemical industry]矿产minerals可支配收入disposable income良性循环virtuous circles生产总值total output value人均国内生产总值per capita GDP消费性支出nonproductive expenditure衣、食、住、行basic life necessities of clothing, food, shelter and weans of travel产业结构industrial structure结构优化optimum structure改革开放reform and opening翻两番quadruple可持续发展sustainable development城市化urbanizationActuator 执行器A:Amplifier 放大器A:Attendance 员工考勤A:Attenuation 衰减AA:Antenna amplifier 开线放大器AA:Architectural Acoustics 建造声学AC:Analogue Controller 摹拟控制器ACD:Automatic Call Distribution 自动分配话务ACS:Access Control System 出入控制系统AD:Addressable Detector 地址探测器ADM:Add/Drop Multiplexer 分插复用器ADPCM:Adaptive Differential ulse Code Modulation 自适应差分脉冲编码调制AF:Acoustic Feedback 声反馈AFR:Amplitude /Frequency Response 幅频响应AGC:Automati Gain Control 自动增益控制AHU:Air Handling Unit 空气处理机组A-I:Auto-iris 自动光圈AIS:Alarm Indication Signal 告警指示信号AITS:Acknowledged Information Transfer Service 确认操作ALC:Automati Level Control 自动平衡控制ALS:Alarm Seconds 告警秒ALU:Analogue Lines Unit 摹拟用户线单元AM:Administration Module 管理模块AN:Access Network 接入网ANSI:American National Standards Institute 美国国家标准学会APS:Automatic Protection Switching 自动保护倒换ASC:Automati Slope Control 自动斜率控制ATH:Analogue Trunk Unit 摹拟中继单元ATM:Asynchrous Transfer Mode 异步传送方式AU- PPJE:AU Pointer Positive Justification 管理单元正指针调整AU:Administration Unit 管理单元AU-AIS:Administrative Unit Alarm Indication SignalAU 告警指示信号AUG:Administration Unit Group 管理单元组AU-LOP:Loss of Administrative Unit Pointer AU 指针丢失AU-NPJE:AU Pointer Negative Justification 管理单元负指针调整AUP:Administration Unit Pointer 管理单元指针AVCD:Auchio &Video Control Device 音像控制装置AWG:American Wire Gauge 美国线缆规格BA:Bridge Amplifier 桥接放大器BAC:Building Automation & Control net 建造物自动化和控制网络BAM:Background Administration Module 后管理模块BBER:Background Block Error Ratio 背景块误码比BCC:B-channel Connect ControlB 通路连接控制BD:Building DistributorBEF:Buiding Entrance Facilities 建造物入口设施BFOC:Bayonet Fibre Optic Connector 大口式光纤连接器BGN:Background Noise 背景噪声BGS: Background Sound 背景音响BIP-N:Bit Interleaved Parity N code 比特间插奇偶校验N 位码B-ISDN:Brand band ISDN 宽带综合业务数字网B-ISDN:Broad band -Integrated Services Digital Network 宽带综合业务数字网BMC:Burst Mode Controller 突发模式控制器BMS:Building Management System 智能建造管理系统BRI:Basic Rate ISDN 基本速率的综合业务数字网BS:Base Station 基站BSC:Base Station Controller 基站控制器BUL:Back up lighting 备用照明C/S: Client/Server 客户机/服务器C:Combines 混合器C:Container 容器CA:Call Accounting 电话自动计费系统CATV:Cable Television 有线电视CC:Call Control 呼叫控制CC:Coax cable 同轴电缆CCD:Charge coupled devices 电荷耦合器件CCF:Cluster Contril Function 簇控制功能CD:Campus Distributor 建筑群配线架CD:Combination detector 感温,感烟复合探测器CDCA:Continuous Dynamic Channel Assign 连续的动态信道分配CDDI:Copper Distributed Data 合同缆分布式数据接口CDES:Carbon dioxide extinguisbing system 二氧化碳系统CDMA:Code Division Multiplex Access 码分多址CF:Core Function 核心功能CFM:Compounded Frequency Modulation 压扩调频繁CIS:Call Information System 呼叫信息系统CISPR:Internation Special Conmittee On Radio Interference 国际无线电干扰专门委员会CLNP:Connectionless Network Protocol 无连接模式网络层协议CLP:Cell Loss Priority 信元丢失优先权CM:Communication Module 通信模块CM:Configuration Management 配置管理CM:Cross-connect Matrix 交叉连接矩阵CMI:Coded Mark Inversion 传号反转码CMISE:Common Management Information Service 公用管理信息协议服务单元CPE:Convergence protocol entity 会聚协议实体CR/E:card reader /Encoder (Ticket reader )卡读写器/编码器CRC:Cyclic Redundancy Check 循环冗佘校验CRT:Cathode Ray Tabe 显示器,监视器,阴极射线管CS: Convergence service 会聚服务CS:Cableron Spectrum 旧纳档块化技术CS:Ceiling Screen 挡烟垂壁CS:Convergence Sublayer 合聚子层CSC:Combined Speaker Cabinet 组合音响CSCW:Computer collaborative work 协同工作CSES:Continuiussupported 计算机支持的SeverelyErrored Second 连续严重误码秒CSF:Cell Site Function 单基站功能控制CTB:Composite Triple Beat 复合三价差拍CTD:Cable Thermal Detector 缆式线型感温探测器CTNR:carrier to noise ratio 载波比CW:Control Word 控制字D:Directional 指向性D:Distortion 失真度D:Distributive 分布式DA:Distribution Amplifier 分配的大器DBA:Database Administrator 数据库管理者DBCSN:Database Control System Nucleus 数据库控制系统核心DBOS:Database Organizing System 数据库组织系统DBSS:Database Security System 数据库安全系统DC:Door Contacts 大门传感器DCC:Digital Communication Channel 数字通信通路DCN:Data Communication Network 数据通信网DCP-I:Distributed Control Panel -Intelligent 智能型分散控制器DCS:Distributed Control System 集散型控制系统DDN:Digital Data Network 数字数据网DDS:Direct Dignital Controller 直接数字控制器DDW:Data Describing Word 数据描述字DECT:Digital Enhanced Cordless Telecommunication增强数字无绳通讯DFB:Distributed Feedback 分布反馈DID:Direct Inward Dialing 直接中继方式,呼入直拨到分机用户DLC:Data Link Control Layer 数据链路层DLI:DECT Line Interface DODI:Direct Outward Dialing One 一次拨号音DPH:DECT PhoneDRC:Directional Response Cahracteristics 指向性响应DS:Direct Sound 直正声DSP:Digital signal Processing 数字信号处理DSS:Deiision Support System 决策支持系统DTMF:Dual Tone Multi-Frequency 双音多频DTS:Dual -Technology Sensor 双鉴传感器DWDM:Dense Wave-length Division Multiplexing 密集波分复用DXC:Digital Cross-Connect 数字交叉连接E:Emergency lighting 照明设备E:Equalizer 均衡器E:Expander 扩展器EA-DFB:Electricity Absorb-Distributed Feedback 电吸收分布反馈ECC:Embedded Control Channel 嵌入或者控制通道EDFA:Erbium-Doped FiberAmplifier 掺饵光纤放大器EDI:Electronic Data Interexchange 电子数据交换EIC:Electrical Impedance Characteristics 电阻抗特性EMC :Electro Magnetic Compatibiloty 电磁兼容性EMI:Electro Magnetic Interference 电磁干扰EMS:Electromagnetic Sensitibility 电磁敏感性EN:Equivalent Noise 等效噪声EP:Emergency Power 应急电源ES:Emergency Sooket 应急插座ES:Evacuation Sigvial 疏散照明ESA:Error SecondA 误码秒类型AESB:ErrorSecondB 误码秒类型BESD:Electrostatic Discharge 静电放电ESR:Errored Second Ratio 误码秒比率ETDM:Electrical Time Division Multiplexing 电时分复用ETSI:European Telecommunication Standards Institute 欧洲电信标准协会F:Filter 滤波器FAB:Fire Alarm Bell 火警警铃FACU:Fire Alarm Contrlol Unit 火灾自动报警控制装置FC:Failure Count 失效次数FC:Frequency Converter 频率变换器FCC:Fire Alarm System 火灾报警系统FCS:Field Control System 现场总线FCU:Favn Coil Unit 风机盘管FD:Fire Door 防火门FD:Flame Detector 火焰探测器FD:Floor DistributorFD:Frequency Dirsder 分频器FDD:Frequency Division Dual 频分双工FDDI :Fiberdistributed Data Interface 光纤缆分布式数据接口。
- 1、下载文档前请自行甄别文档内容的完整性,平台不提供额外的编辑、内容补充、找答案等附加服务。
- 2、"仅部分预览"的文档,不可在线预览部分如存在完整性等问题,可反馈申请退款(可完整预览的文档不适用该条件!)。
- 3、如文档侵犯您的权益,请联系客服反馈,我们会尽快为您处理(人工客服工作时间:9:00-18:30)。
proposed by Koren and Lo [4,5] to deal with this problem, and it has become one of the most popular approaches in contouring control. The CCC scheme includes two essential parts. One is to estimate the contour error in a real-time manner, and the other is to compensate each axis along the direction of the estimated contour error vector by applying a control law. Contour error, defined as the deviation of the actual position from the desired contour path, is difficult to be calculated exactly for free-form contour-following tasks. Conway et al. [6] proposed an iterative algorithm to estimate the foot point of the actual position on the desired contour, and subsequently evaluated the contour error by the definition. However, this method is time-consuming and unaffordable for general microprocessors. Thus, many studies calculated the approximate contour error rather than the actual one. Linear and circular approximations are usually adopted for
1 Introduction
In a CNC machine, nonlinearities and unmatched axial dynamics often result in contour error, which is the most fundamental factor that determines the final product quality. Traditionally, feedback and feedforward controllers [1–3] are designed for each axis independently to reduce the tracking errors. However, the good tracking performance of each individual axis does not mean that the desired contouring accuracy can be achieved in a multiaxis motion system. To complete a contour-following task with satisfactory contouring performance, a nature way is to design a controller based on the contour error directly. The CCC scheme with variable gains and symmetric control structure was
ZHAO Huan1, ZHU LiMin2* & DING Han1
1
State Key Laboratory of Digital Manufacturing Equipment and Technology, Huazhong University of Science and Technology, Wuhan 430074, China; 2 State Key Laboratory of Mechanical System and Vibration, Shanghai Jiao Tong University, Shanghai 200240, China Received December 22, 2014; accepted March 9, 2015; published online May 22, 2015
SCIENCE CHINA
Technological Sciences
• Article •
July 2015 Vol.58 No.7: 1209–1217 doi: 10.1007/s11431-015-5835-y
Craxial motion systems based on second-order contour error estimation
1210
Zhao H, et al.
Sci China Tech Sci
July (2015) Vol.58 No.7
arbitrary planar contours. For the linear approximation, the contour error is defined as the shortest distance from the actual position to the tangential line or velocity vector at the desired position [7,8], or to the piecewise straight lines which are defined by adjacent reference position commands [9–11]. For the circular approximation [5,12,13], the desired contour is locally approximated by the circle of curvature at the command position, and the contour error is defined as the shortest distance from the actual position to the circle. These approximation methods suffer from two main drawbacks: (1) They only apply to planar curved paths; and (2) they provide satisfactory accuracy only when the path curvature and the tracking error are relatively small. With regard to spatial arbitrary contours, Yeh and Hsu [14] proposed a linear contour approximation method, which defined the vector from the actual position to the nearest point on the line that passes through the reference position tangentially as the contour error vector. However, like those in the planar cases, this linear method may lead to significant estimation errors in high speed tracking of paths with large curvatures. By using the second-order Taylor approximant of the point-to-curve distance function, Zhu et al. [15] proposed an approach for calculating contour errors of arbitrary curves in real time. Compared with the existing methods, this method can provide more accurate contour error estimation even when the curvature of the contour is large. Once the contour error vector is obtained, the variable gains of the multiaxis CCC structure can be readily determined. Then, by employing a specific control law to implement the CCC, the compensated control efforts are injected to the position or velocity loops of all the axes. Based on the traditional velocity loop-based CCC [5,16], Chin and Lin [17] proposed a modified CCC structure with an additional pre-compensated controller. Tarng et al. [18] proposed a cross-coupled fuzzy feedrate control scheme, and applied a genetic based learning algorithm to optimize the controller gains. Yeh and Hsu [19] proposed an integrated controller, which combines zero phase error tracking controller (ZPETC) and CCC controller. Cheng and Lee [8] implemented a tangential-contouring controller to improve the contour-following accuracy. Su and Cheng [20] developed an integrated motion control scheme that consists of a modified CCC controller and a fuzzy-logic based feedrate regulator. Yan et al. [21] combined a self-tuning adaptive control strategy with the cross-coupled controller to imTable 1 Comparison of CCC schemes for contouring applications Applications Biaxial systems Triaxial systems Contour error estimation Linear Quadratic Linear Quadratic