MAX6320PUK38DW-T中文资料
XPM6320(20W移动电源IC)规格书
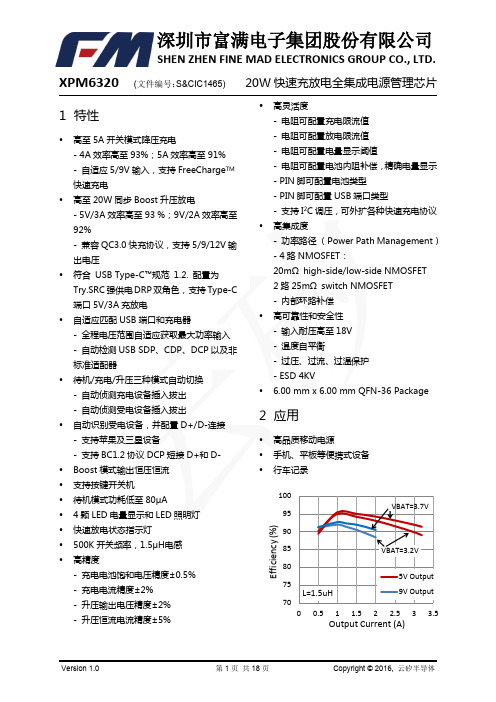
WLED VBAT SW BOOT
FC
LED1
LED2
LED3
LED4 VIN DP DM DP DM
USB-B
USB-A DP DM
XPM6320
VSYS NTC KEY ISET OLIM AGND VCC VOUT TCG
USB-C VBUS CC1 CC2 RBATS RBATC VBATS MODE CC1 CC2
深圳市富满电子集团股份有限公司
SHEN ZHEN FINE MAD ELECTRONICS GROUP CO., LTD.
XPM6320
6.5 电气特性
(文件编号: S&CIC1465)
20W 快速充放电全集成电源管理芯片
没有特别注明情况下,以下参数为
,
μΗ 条件下测得。
Parameters
静态电流 Quiescent Currents 待机模式电流 充电模式静态电流 升压模式静态电流 充电系统 Battery Charger VIN 工作电压范围 电池充电饱和电压 电池回充电压阈值 电池回充迟滞电压 电池过压阈值 恒流充电范围
名称 FC NTC ISET OLIM WLED VBUS VIN KEY VOUT VSYS SW NC BOOT VCC VBAT VBATS TCG CC1/CC2 MODE DM/DP LED1~4 RBATC RBATS AGND PGND
描述 升压放电模式工作时,快速放电状态指示 电池温度检测 设置充电电流 设置输出电流 LED 照明灯驱动端口 USB Type-C 接口 VBUS 引脚 输入电源端口 开机使能按键 输出电源端口 系统输出电压 DC-DC 电感接入端 High-side 功率管驱动电源 系统内部电源 电池电压检测端口 电池类型选择端口,悬空 4.2V,接地 4.35V USB Type-C 接口 VBUS 开关管控制端口 USB Type-C 接口 CC 引脚 悬空配置为双 USB-A 接口,接地配置为 USB-A+Type-C 接口 USB 的 D-/D+接入端口,用于 USB 自动识别与快充检测 4 颗 LED 灯驱动端口,用于电池电量显示 电池内阻补偿端口 设置电池电量显示阈值 系统模拟地 系统功率地
PC-6320

PC-6320 8位模入模出接口卡技术说明书1. 概述:PC-6320 模入接口卡适用于具有ISA 总线的PC系列微机,具有很好的兼容性,CPU从目前广泛使用的64位处理器直到早期的16位处理器均可适用,操作系统可选用经典的MS-DOS,目前流行的 Windows 系列,高稳定性的Unix 等多种操作系统以及专业数据采集分析系统 LabVIEW 等软件环境。
在硬件的安装上也非常简单,使用时只需将接口卡插入机内任何一个ISA总线插槽中,信号电缆从机箱外部直接接入。
PC-6320模入模出接口卡可广泛应用于工业过程控制系统以及实验室数据采集系统。
本卡安装使用方便,程序编制简单。
其模入模出信号均由卡前端的26 线扁平带缆插头与外部信号源及设备连接。
对于模出部分,用户可根据控制对象的需要选择电压或电流输出方式以及不同的量程。
2. 主要技术参数:2.1 模入部分:2.1.1 输入通道数:单端8路2.1.2 输入信号范围:0V~5V2.1.3 A/D转换分辨率:8位2.1.4 A/D转换速度:116μS (一次转换时间)2.1.5 系统综合误差:≤0.4% F.S2.2 模出部分:2.2.1 输出通道数:2路 (互相独立,可同时或分别输出)2.2.2 输出范围:电压方式:0~5V、-2.5V~+2.5V电流方式:0~10mA、4~20mA2.2.3 D/A转换器件:DAC08322.2.4 D/A转换分辨率:8位2.2.5 D/A转换综合建立时间:≤5μS2.2.6 D/A转换综合误差:电压方式:≤0.4% F.S电流方式:≤1% F.S2.3电源功耗:+5V(±10%)≤250mA+12V(±10%)≤150mA-12V(±10%)≤60mA2.4 使用环境要求:工作温度:10℃~40℃相对湿度: 40%~80%存贮温度:-55℃~+85℃2.5 外型尺寸:长×高= 140mm×106mm (5.5 英寸×4.2英寸)3. 工作原理:PC-6320模入模出接口卡主要由模数转换电路、数模转换电路、接口控制逻辑电路及电源电路构成。
MAX6368PKA23-T中文资料
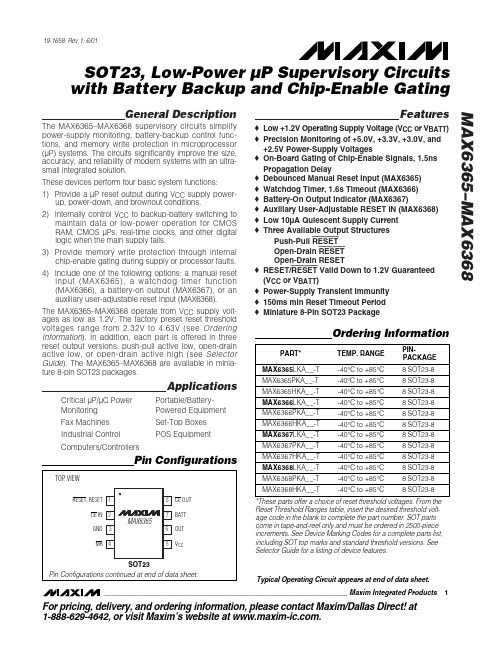
MAX6365–MAX6368
SOT23, Low-Power µP Supervisory Circuits with Battery Backup and Chip-Enable Gating
ABSOLUTE MAXIMUM RATINGS
Terminal Voltages (with respect to GND)
SOT23 Pin Configurations continued at end of data sheet.
Typical Operating Circuit appears at end of data sheet.
________________________________________________________________ Maxim Integrated Products 1
Pin Configurations
TOP VIEW
RESET, RESET 1 CE IN 2 GND 3 MR 4
MAX6365
8 CE OUT 7 BATT 6 OUT 5 VCC
Features
o Low +1.2V Operating Supply Voltage (VCC or VBATT) o Precision Monitoring of +5.0V, +3.3V, +3.0V, and
VCC, BATT, OUT.......................................................-0.3V to +6V RESET (open drain), RESET (open drain) ................-0.3V to +6V BATT ON, RESET (push-pull), RESET IN,
MAX6373KA+T中文资料

General DescriptionThe MAX6369–MAX6374 are pin-selectable watchdog timers that supervise microprocessor (µP) activity and signal when a system is operating improperly. During normal operation, the microprocessor should repeated-ly toggle the watchdog input (WDI) before the selected watchdog timeout period elapses to demonstrate that the system is processing code properly. If the µP does not provide a valid watchdog input transition before the timeout period expires, the supervisor asserts a watch-dog (WDO ) output to signal that the system is not exe-cuting the desired instructions within the expected time frame. The watchdog output pulse can be used to reset the µP or interrupt the system to warn of processing errors.The MAX6369–MAX6374 are flexible watchdog timer supervisors that can increase system reliability through notification of code execution errors. The family offers several pin-selectable watchdog timing options to match a wide range of system timing applications:•Watchdog startup delay: provides an initial delay before the watchdog timer is started.•Watchdog timeout period: normal operating watch-dog timeout period after the initial startup delay.•Watchdog output/timing options: open drain (100ms)or push-pull (1ms).The MAX6369–MAX6374 operate over a +2.5V to +5.5V supply range and are available in miniature 8-pin SOT23 packages.________________________ApplicationsEmbedded Control Systems Industrial ControllersCritical µP and Microcontroller (µC) Monitoring AutomotiveTelecommunications NetworkingFeatures♦Precision Watchdog Timer for Critical µP Applications ♦Pin-Selectable Watchdog Timeout Periods ♦Pin-Selectable Watchdog Startup Delay Periods ♦Ability to Change Watchdog Timing Characteristics Without Power Cycling ♦Open-Drain or Push-Pull Pulsed Active-Low Watchdog Output ♦Watchdog Timer Disable Feature ♦+2.5V to +5.5V Operating Voltage ♦8µA Low Supply Current♦No External Components Required ♦Miniature 8-Pin SOT23 PackageMAX6369–MAX6374Pin-Selectable Watchdog Timers19-1676; Rev 3; 11/05Ordering InformationPin Configuration appears at end of data sheet.Note:All devices are available in tape-and-reel only. Required order increment is 2,500 pieces.Devices are available in both leaded and lead-free packaging.Specify lead-free by replacing “-T” with “+T” when ordering.Selector GuideFor pricing, delivery, and ordering information,please contact Maxim/Dallas Direct!at1-888-629-4642, or visit Maxim’s website at .M A X 6369–M A X 6374Pin-Selectable Watchdog Timers 2_______________________________________________________________________________________ABSOLUTE MAXIMUM RATINGSELECTRICAL CHARACTERISTICS(V CC = +2.5V to +5.5V, SET_ = V CC or GND, T A = -40°C to +85°C, unless otherwise noted. Typical values are at T A = +25°C andStresses beyond those listed under “Absolute Maximum Ratings” may cause permanent damage to the device. These are stress ratings only, and functional operation of the device at these or any other conditions beyond those indicated in the operational sections of the specifications is not implied. Exposure to absolute maximum rating conditions for extended periods may affect device reliability.Terminal Voltage (with respect to GND)V CC .....................................................................-0.3V to +6V WDI.....................................................................-0.3V to +6V WDO (Open Drain: MAX6369/71/73).................-0.3V to +6V WDO (Push-Pull: MAX6370/72/74 .......-0.3V to (V CC + 0.3V)SET0, SET1, SET2................................-0.3V to (V CC + 0.3V)Maximum Current, Any Pin (input/output)...........................20mAContinuous Power Dissipation (T A = +70°C)SOT23-8 (derate 8.75mW/°C above +70°C)...............700mW Operating Temperature Range ...........................-40°C to +85°C Storage Temperature Range.............................-65°C to +150°C Junction Temperature......................................................+150°C Lead Temperature (soldering, 10s).................................+300°C V CC Rise or Fall Rate......................................................0.05V/µsMAX6369–MAX6374Pin-Selectable Watchdog Timers_______________________________________________________________________________________3ELECTRICAL CHARACTERISTICS (continued)M A X 6369–M A X 6374Pin-Selectable Watchdog Timers 4_______________________________________________________________________________________461081214-4010-15356085SUPPLY CURRENT vs. TEMPERATURETEMPERATURE (°C)S U P P L Y C U R R E N T (µA )Typical Operating Characteristics(Circuit of Figure 1, T A = +25°C, unless otherwise noted .)0.9970.9990.9981.0011.0001.0021.003-4010-15356085WATCHDOG TIMEOUT PERIODvs. TEMPERATUREM A X 6369/74-02TEMPERATURE (°C)N O R M A L I Z E D W A T C H D O G T I M E O U T P E R I O DELECTRICAL CHARACTERISTICS (continued)Note 2:Guaranteed by design.Note 3:In this setting the watchdog timer is inactive and startup delay ends when WDI sees its first level transition. See SelectingDevice Timing for more information.Note 4:After power-up, or a setting change, there is an internal setup time during which WDI is ignored.MAX6369–MAX6374Pin-Selectable Watchdog Timers_______________________________________________________________________________________5Pin DescriptionDetailed DescriptionThe MAX6369–MAX6374 are flexible watchdog circuits for monitoring µP activity. During normal operation, the internal timer is cleared each time the µP toggles the WDI with a valid logic transition (low to high or high to low) within the selected timeout period (t WD ). The WDO remains high as long as the input is strobed within the selected timeout period. If the input is not strobed before the timeout period expires, the watchdog output is asserted low for the watchdog output pulse width (t WDO ). The device type and the state of the three logic control pins (SET0, SET1, and SET2) determine watch-dog timing characteristics. The three basic timing varia-tions for the watchdog startup delay and the normalTable 1 for the timeout characteristics for all devices in the family):•Watchdog Startup Delay:Provides an initial delay before the watchdog timer is started.Allows time for the µP system to power up and initial-ize before assuming responsibility for normal watch-dog timer updates.Includes several fixed or pin-selectable startup delay options from 200µs to 60s, and an option to wait for the first watchdog input transition before starting the watchdog timer.M A X 6369–M A X 6374Pin-Selectable Watchdog Timers 6_______________________________________________________________________________________•Watchdog Timeout Period:Normal operating watchdog timeout period after the initial startup delay.A watchdog output pulse is asserted if a valid watch-dog input transition is not received before the timeout period elapses.Eight pin-selectable timeout period options for each device, from 30µs to 60s.Pin-selectable watchdog timer disable feature.•Watchdog Output/Timing Options:Open drain, active low with 100ms minimum watch-dog output pulse (MAX6369/MAX6371/MAX6373).Push-pull, active low with 1ms minimum watchdog output pulse (MAX6370/MAX6372/MAX6374).Each device has a watchdog startup delay that is initi-ated when the supervisor is first powered or after the user modifies any of the logic control set inputs. The watchdog timer does not begin to count down until theFigure 1. Functional Diagramcompletion of the startup delay period, and no watch-dog output pulses are asserted during the startup delay. When the startup delay expires, the watchdog begins counting its normal watchdog timeout period and waiting for WDI transitions. The startup delay allows time for the µP system to power up and fully ini-tialize before assuming responsibility for the normal watchdog timer updates. Startup delay periods vary between the different devices and may be altered by the logic control set pins. To ensure that the system generates no undesired watchdog outputs, the routine watchdog input transitions should begin before the selected minimum startup delay period has expired. The normal watchdog timeout period countdown is initi-ated when the startup delay is complete. If a valid logic transition is not recognized at WDI before the watchdog timeout period has expired, the supervisor asserts a watchdog output. Watchdog timeout periods vary between the different devices and may be altered by the logic control set pins. To ensure that the system generates no undesired watchdog outputs, the watch-dog input transitions should occur before the selected minimum watchdog timeout period has expired.The startup delay and the watchdog timeout period are determined by the states of the SET0, SET1, and SET2 pins, and by the particular device within the family. For the MAX6369 and MAX6370, the startup delay is equal to the watchdog timeout period. The startup and watchdog timeout periods are pin selectable from 1ms to 60s (minimum).For the MAX6371 and MAX6372, the startup delay is fixed at 60s and the watchdog timeout period is pin selectable from 1ms to 60s (minimum).The MAX6373/MAX6374 provide two timing variations for the startup delay and normal watchdog timeout. Five of the pin-selectable modes provide startup delays from 200µs to 60s minimum, and watchdog timeout delays from 3ms to 10s minimum. Two of the selectable modes do not initiate the watchdog timer until the device receives its first valid watchdog input transition (there is no fixed period by which the first input must be received). These two extended startup delay modesare useful for applications requiring more than 60s for system initialization.All the MAX6369–MAX6374 devices may be disabledwith the proper logic control pin setting (Table 1).Applications InformationInput Signal Considerations Watchdog timing is measured from the last WDI risingor falling edge associated with a pulse of at least 100nsin width. WDI transitions are ignored when WDO is asserted, and during the startup delay period (Figure2). Watchdog input transitions are also ignored for asetup period, t SETUP, of up to 300µs after power-up ora setting change (Figure 3).Selecting Device TimingSET2, SET1, and SET0 program the startup delay and watchdog timeout periods (Table 1). Timeout settingscan be hard wired, or they can be controlled with logicgates and modified during operation. To ensure smooth transitions, the system should strobe WDI immediately before the timing settings are changed. This minimizesthe risk of initializing a setting change too late in thetimer countdown period and generating undesired watchdog outputs. After changing the timing settings,two outcomes are possible based on WDO. If the change is made while WDO is asserted, the previous setting is allowed to finish, the characteristics of thenew setting are assumed, and the new startup phase is entered after a 300µs setup time (t SETUP) elapses. Ifthe change is made while WDO is not asserted, thenew setting is initiated immediately, and the new start-up phase is entered after the 300µs setup time elapses.MAX6369–MAX6374Pin-Selectable Watchdog Timers_______________________________________________________________________________________7 Figure 3. Setting Change TimingM A X 6369–M A X 6374Pin-Selectable Watchdog TimersSelecting 011 (SET2 = 0, SET1 = 1, SET0 = 1) disables the watchdog timer function on all devices in the family.Operation can be reenabled without powering down by changing the set inputs to the new desired setting. The device assumes the new selected timing characteris-tics and enter the startup phase after the 300µs setup time elapses (Figure 3).The MAX6373/MAX6374 offer a first-edge feature. In first-edge mode (settings 101 or 110, Table 1), the internal timer does not control the startup delay period.Instead, startup terminates when WDI sees a transition.If changing to first-edge mode while the device is oper-ating, disable mode must be entered first. It is then safe to select first-edge mode. Entering disable mode first ensures the output is unasserted when selecting first-edge mode and removes the danger of WDI being masked out.OutputThe MAX6369/MAX6371/MAX6373 have an active-low,open-drain output that provides a watchdog output pulse of 100ms. This output structure sinks current when WDO is asserted. Connect a pullup resistor from WDO to any supply voltage up to +5.5V.Select a resistor value large enough to register a logic low (see Ele ctrical Characte ristics ), and small enoughto register a logic high while supplying all input current and leakage paths connected to the WDO line. A 10k Ωpullup is sufficient in most applications. The MAX6370/MAX6372/MAX6374 have push-pull outputs that pro-vide an active-low watchdog output pulse of 1ms.When WDO deasserts, timing begins again at the beginning of the watchdog timeout period (Figure 2).Usage in Noisy EnvironmentsIf using the watchdog timer in an electrically noisy envi-ronment, a bypass capacitor of 0.1µF should be con-nected between V CC and GND as close to the device as possible, and no further away than 0.2 inches.________________Watchdog SoftwareConsiderationsTo help the watchdog timer monitor software execution more closely, set and reset the watchdog input at differ-ent points in the program, rather than pulsing the watch-dog input high-low-high or low-high-low. This technique avoids a stuck loop, in which the watchdog timer would continue to be reset inside the loop, keeping the watch-dog from timing out. Figure 4 shows an example of a flow diagram where the I/O driving the watchdog input is set high at the beginning of the program, set low at the end of every subroutine or loop, then set high again when the program returns to the beginning. If the pro-gram should hang in any subroutine, the problem would be quickly corrected, since the I/O is continually set low and the watchdog timer is allowed to time out, causing WDO to pulse.Figure 4. Watchdog Flow DiagramChip InformationTRANSISTOR COUNT: 1500PROCESS: BiCMOSPin ConfigurationMaxim cannot assume re sponsibility for use of any circuitry othe r than circuitry e ntire ly e mbodie d in a Maxim product. No circuit pate nt lice nse s are implied. Maxim reserves the right to change the circuitry and specifications without notice at any time.8_____________________Maxim Integrated Products, 120 San Gabriel Drive, Sunnyvale, CA 94086 408-737-7600©2005 Maxim Integrated ProductsPrinted USAis a registered trademark of Maxim Integrated Products, Inc.。
Chroma 63200 系列可编程直流电子负载说明书

Key Features:Power Rating:2600W,5200W,6500W,10400W,14500W, 15600WVoltage range: 1-80V/ 2.5-500VCurrent range: Up to 1000ACC, CR, CVMaster/Slave paralleling control mode, allow synchronous load control under static and dynamic loading modeDynamic loading: Up to 20KHzOnly need 1V to draw rated currentProgrammable slew rate, up to 41A/uS Measurement: Voltage / CurrentPower/ ResistanceLarge LED/LCD displayExternal loading waveform simulationShort circuit simulation and shortcircuit current measurementFull protection: OPreverse protectionVersatile remote controllerGPIB& RS-232C; RS-485 interfaceSurge load capabilityBattery discharge timerand therefore can test if the battery charger has correct charging current corresponding to its own out-put, or more precisely, the battery voltage. If the UUT is battery, the electronic load is able to simulate the behavior of the device that uses the battery. For most of the electronic and electrical devices, their power consumption patterns are more likely constant power devices.Consequently, CP mode simulation will be essential for a battery discharge load.2. LOW VOLTAGE OPERATING CHARACTERISTICSdirectly.1000A at only 1V input.3. MEASUREMENTSChroma 63200 series are built in the15-bits precision A/D converter, thus can achieve 0.05%F .S., 0.1%F .S. and 0.3%F .S. accuracy for voltage,current and power measurement respectively. And they can be shown simultaneously on three big LED displays for user's convenience. In additional to standard measurements, they also provide voltage and current monitor outputs, which are useful when user needs to monitor the voltage and current waveform via scope.4. DYNAMIC LOADING AND CONTROLparameters of the 63200 load modules. The programmable slew rate makes the simulation of transient load change demanded by the require-ment of real life application possible. The internal waveform generator of 63200 is capable of producing maximum slew rate at 25A/uS (63208),and dynamic cycling up to 20KHz. Its dedicated remote load senses and controls circuit guarantee the minimum waveform distortion during continuous load changes.5. MASTER / SLAVE PARALLEL CONTROLWhen higher power is required,it is common to parallel two elec-tronic loads together to draw higher current. 63200 series high power loads have smart Master / Slave control mode. When the loads are set to Master / Slave mode, users can program the load-ing (CC mode only) on master unit. The loading current values ofthe slave units will be calculated and downloaded by master unit automatically. In short, unlike the traditional design, users may consider several load units that work under Master / Slave mode as a single load unit. It simplifies the user operation dramatically.SIMULATIONThe CC and CR mode loading simula-tion is helpful to test whether the output voltage of the UUT remains stable or regulated under different loading cur-rent or resistance conditions. For bat-tery chargers, CV mode may help tochange the output voltage of a charger 1. APPLICATION SPECIFIC LOAD SIMULATIONChroma electronic loads 63200 series provide constant current, constant resistance, constant voltage and constant power modes for various application requirements.V I V I V I VIConstant current Constant resistance Constant voltage Constant power8. SURGE LOAD CAPABILITYChroma’s 63200 Series D C Loads provide a unique surge load simulation capability which allows users to overdrive the loads up to 2.7 times their rated power for short periods. This feature is ideal when the average power require by the UUT is low compared to short-term peak power demands. Plasma Display Panel (PDPs) testing is one typical applica-tion, others include battery 3C discharge, breaker & fuse over rating (300% to 1000%) tests, car engine startup simu-lation and DC motor startup simulation.The amount of surge loading available using the 63200 loads is related to the initial loading conditions. Figures 1 and 2 show the relationship of initial state (Load_Low under D ynamic mode) and the maximum acceptable overdrive power. Under this operation, the load will display an Over Power Protection Alarm (OPP) and will disable the load cur-rent if the user violates the maximum surge load capability showed in the figures.Note 1 :The Initial state under Static Mode should last at least 1 second. Note 2 :This surge load capability will be regulated by the temperature de-rat-ing characteristics. (Refer to Note 1 in Specifications)Note 3 :Examples below assume the use of the Model 63201 load with a con-tinuous rating of 2600W/300A/1-80VDC9. TIMER FUNCTION FOR BATTERY DISCHARGE TESTINGThe 63200 Loads include unique timing & measurement function allowing for precision time settings and measure-ments in the range of 1s to 99999s. This feature allows users to set a final voltage & timeout value for battery dis-charge testing and similar applications.For Example, Figure 3 below shows that the 63200’s internal timer can be initiated automatically when the battery voltage falls below a preset value. The timer will continue countinguntil the second preset voltage value is reached.Example 1: STATIC LOADINGThe Model 63201 can be overdriven to approximately 5200W (200% of its rated con-tinuous power rating) for 6.0 ms seconds when the starting power is 650W (25% of its rated power). This is represented by DOT on the blue curve in Figure 1.Example 2: DYNAMIC LOADINGThe Model 63201 is capable of a zero – to- 6500W (250%) pulse at a duty cycle of 5%. This is represented by the DOT on the purple curve in Figure 2.7. SHORT CIRCUIT SIMULATION63200 series electronic loads can also simulate short circuit condition. Owing to this capability, it can short DC power source or any power sup-plies that have built in current limit function, and measure their short circuit currents. So that users can verify if the UUT current limit is functional.APPLICATIONSof testing all sorts of DC output power supplies directly or via rectifier, they can also be used to test the AC output power supplies.CC & CR ModeA/ D Power supplyD/ D ConverterBattery chargerUPS/AVR4. SYSTEM INTEGRATIONChroma 63200 series electronic loads provide GPIB, RS-232C and RS-485 PC controllable interfaces. The external waveform simulation and voltage / current monitoring capability make Chroma 63200 family ideal for automatic system integration.Discharge by CR modeDischarge by CP mode1. Power Switch2. LED Display:Voltage read back.3. LED Display:Current/ ohm read back.4. LED Display:Power read back.5. LCD Display:For setting and editing.6. Rotary knob:T o adjust the loading and parameter setting.7. Numeric key:For data setting.8. Function key:T o select load mode, control mode, and define thereading specification.9. System key:For system config and data store, recall.10. Load terminal11. Voltage sense terminal12. RS-485 connector13. GPIB connector14. RS-232C connector15. Voltage monitor output:Analog output which indicates the voltage waveform.16. Current monitor output:Analog output which indicates the current waveform.17. External V reference:External programming voltage input.246351Model: 63203, 63204PANEL DESCRIPTIONModel 63208 / 63209 / 63210Model 63206 / 63207Model 63203 / 63204Model63201 / 63202Model 63205SPECIFICATIONSSPECIFICATIONSSe riesAll specifications are subject to change without notice.Note*1: The power rating specifications at ambient temperature=25. And see the diagram below for power derating. (Derate power by 1.53perfrom 25to 40)Note*2: The Vin is greater than min. operating voltage of each model.Note*3: The Vin is greater than 7V of each model.Note*4: Setting error will be 1% for R<0.005Ωat CRL range.SPECIFICATIONSV-I Curve:Model 63201/ 63203/ 63205/ 63206/ 63207/ 63208/ 63209Low Voltage Operating:Low Voltage & V-I Curve Operating Characteristics (Typical) of 63200 SeriesNote: All specifications are measured at load input terminals. (Ambient temperature of +25)Distributed by:Worldwide Distribution and Service Network63200-200607-PDFCHINACHROMA ELECTRONICS (SHENZHEN) CO., LTD.8F , No.4, Nanyou Tian An Industrial Estate, Shenzhen,China PC: 518054T el: +86-755-2664-4598Fax: +86-755-2641-9620EUROPECHROMA ATE EUROPE B.V.Max Planckstraat 4, 6716 BE Ede, The Netherlands T el: +31-318-648282Fax: +31-318-648288U.S.A.CHROMA ATE INC. (U.S.A.)7 Chrysler Irvine, CA 92618T el: +1-949-421-0355Fax: +1-949-421-0353T oll Free: +1-800-478-2026CHROMA ATE INC.HEADQUARTERS66, Hwa-Y a 1st Rd., Hwa-Y a T echnology Park, Kuei-Shan Hsiang, Taoyuan Hsien 333,TaiwanT el: +886-3-327-9999 Fax: +886-3-327-8898E-mail:*****************.twDeveloped and Manufactured by :63207 : DC Electronic Load 10.4KW/ 300A/ 80V 63208 : DC Electronic Load 15.6KW/ 600A/ 80V 63209 : DC Electronic Load 15.6KW/ 1000A/ 80V 63210 : DC Electronic Load 14.5KW/ 150A/ 500V A600009 : GPIB Cable (200 cm)A600010 : GPIB Cable (60 cm)A632001 :Remote Controller63201 : DC Electronic Load 2.6KW/ 300A/ 80V 63202 : DC Electronic Load 2.6KW/ 50A/ 500V 63203 : DC Electronic Load 5.2KW/ 600A/ 80V 63204 : DC Electronic Load 5.2KW/ 100A/ 500V 63205 : DC Electronic Load 6.5KW/ 180A/ 80V 63206 : DC Electronic Load 10.4KW/ 600A/ 80VA632001ORDERING INFORMATION15A 30A 45A 60A 75A 90A 105A 120A 135A 150A15A30A 45A60A 75A 90A 105A 120A 135A 150A。
DS-KH6320-WTDE1 网络室内站点说明书

1. Insert 2 expansion tubes into the wall. 2. Fix the wall moun�ng plate to the junc�on box with 2 screws. 3. Hook the indoor sta�on to the wall moun�ng plate �ghtly by inser�ng the plate hooks into the slots on the rear panel of the indoor sta�on, during which the lock catch will be locked automa�cally.
Make sure all related equipments are power-off during the installa�on.
Check the product specifica�on for the installa�on environment.
Wall Moun�ng with junc�on Box
2 Terminal and Wiring
There are 10 pins in the terminal on the rear panel of the indoor sta�on: 2 GND pin, 2 alarm input pins, 4 relay output pins and 2 RS-485 pins.
4 Getting Started
Activate Indoor Station
You are required to activate the device first by setting a strong password before you can use the device.
TC6320中文资料

Supertex Inc. does not recommend the use of its products in life support applications and will not knowingly sell its products for use in such applications unless it receives an adequate "products liability indemnification insurance agreement." Supertex does not assume responsibility for use of devices described and limits its liability to the replacement of devices determined to be defective due to workmanship. No responsibility is assumed for possible omissions or inaccuracies. Circuitry and specifications are subject to change without notice. For the latest product specifications, refer to the Supertex website: . For complete liability information on all Supertex products, refer to the most current databook or to the Legal/Disclaimer page on the Supertex website.Initial ReleaseN- and P-Channel Enhancement-Mode MOSFET PairFeaturesIntegrated gate-source resistor Integrated gate-source zener diode Low threshold Low on-resistance Independent N- and P-channels Electrically isolated N- and P-channels Low input capacitance Fast switching speeds Free from secondary breakdowns Low input and output leakageApplicationHigh voltage pulsers Amplifiers Buffers Piezoelectric transducer drivers General purpose line drivers Logic level interfacesAbsolute Maximum Ratings*Drain-to-Source Voltage BV DSS Drain-to-Gate VoltageBV DGSOperating and Storage Temperature -55°C to +150°CSoldering Temperature*300°C*Distance of 1.6mm from case for 10 seconds.General DescriptionThe Supertex TC6320TG consists of a high voltage lowthreshold N-channel and P-channel MOSFET in an SO-8 package. Both MOSFETs have integrated gate-source resistors and gate-source zener diode clamps which are desired for high voltage pulser applications. TC6320TG, a complementary high-speed, high voltage, gate-clamped N- and P-channel MOSFET pair in a single SO-8 package. The TC6320TG offers 200V breakdown voltage, 2.0A output peak current and low input capacitance. The 2.0A output current capability will minimize rise and fall times. The low input capacitance will minimize propagation delay times and also rise and fall times. The MOSFETs have integrated gate-source resistors and gate-source zener diode clamps that are desired for high voltage pulser applications saving board space and improving performance. It is specifically designed for applications in medical ultrasound transmitters and non-destructive evaluation in materials flaw detection, but it can also be used as an efficient buffer.Package OptionS1G1S2G2D2D2D1D1SO-8 Package (top view)N-ChannelP-Channel 12345678Supertex, Inc. January 21, 20032BV DSS / BV DGS R DS(ON) (max) Order Number / Package N-Channel P-Channel N-Channel P-Channel SO-8 200V -200V 7.0Ω 8.0Ω TC6320TGN-Channel Electrical Characteristics (at T A =25°C unless otherwise specified)Symbol ParameterMin Typ Max Units ConditionsBV DSS Drain-to-SourceBreakdown Voltage200 V V GS =0V, I D =2mA V GS(th) Gate Threshold Voltage1.02.0 V V GS =V DS , I D =1mA ∆V GS(th) Change in V GS(th) with Temperature -4.5 mV/°C V GS =V DS , I D =1mA R GS Gate-Source Shunt Resistor10 50 K Ω I GS=100µA ∆R GSChange in R GS with Temperature TBD %/°C I GS =100µA Vz GS Gate-Source Zener Voltage13.2 25 V I GS =2mA ∆Vz GS Change in Vz GS with Temperature TBD mV/°C I GS =2mA 10 µA V GS =0V, V DS =Max Rating I DSS Zero Gate Voltage Drain Current 1.0 mA V GS =0V, V DS =0.8 MaxRating, T A =125°C1.0 V GS =4.5V, V DS =25V I D(ON)On-State Drain Current2.0 A V GS =10V, V DS =25V 8.0 V GS =4.5V, I D =150mA R DS(ON) Static Drain-to-SourceON-State Resistance7.0 Ω V GS =10V, I D =1.0A ∆R DS(ON) Change in R DS(ON) with Temperature 1.0 %/°C V GS =4.5V, I D =150mA G FS Forward Transconductance 400 mmho V DS =25V, I D =200mA C ISS Input Capacitance 110 C OSS Common Source Output Capacitance 60C RSS Reverse Transfer Capacitance 23 pF V GS =0V, V DS =25Vf=1MHz t d(ON) Turn-ON Delay Time 10 t r Rise Time 15 t d(OFF) Turn-Off Delay Time 20t f Fall Time 15 nsV DD =25V,I D =1.0A R GEN =25 Ω V SD Diode Forward Voltage Drop 1.8 V V GS =0V, I SD =0.5A t rr Reverse Recovery Time300 ns V GS =0V, I SD =0.5ANotes:1) All DC parameters 100% tested at 25°C unless otherwise stated. (Pulsed test: 300µs pulse at 2% duty cycle.) 2) All AC parameters sample tested.OUTPUT10V0V0VV DDt d(OFF)InputOutputt r t f t d(ON)t (ON)t (OFF)10%90%90%10%90%10%P-Channel Electrical Characteristics (at T A =25°C unless otherwise specified)Symbol ParameterMin Typ Max Units ConditionsBV DSS Drain-to-SourceBreakdown Voltage-200 V V GS =0V, I D =-2mA V GS(th) Gate Threshold Voltage-1.0 -2.4 V V GS =V DS , I D =-1mA ∆V GS(th) Change in V GS(th) with Temperature 4.5 mV/°CV GS =V DS , I D =-1mA R GS Gate-Source Shunt Resistor10 50 K Ω I GS =-100µA ∆R GSChange in R GS with Temperature TBD %/°C I GS =-100µA Vz GS Gate-Source Zener Voltage13.2 25 V I GS =-2mA ∆V GS(th) Change in Vz GS with Temperature TBD mV/°C I GS =-2mA -10 µA V GS =0V, V DS =Max Rating I DSS Zero Gate Voltage Drain Current -1.0 mA V GS =0V, V DS =0.8 MaxRating, T A =125°C-1.0 V GS =-4.5V, V DS =-25V I D(ON)On-State Drain Current-2.0 A V GS =-10V, V DS =-25V 10 V GS =-4.5V, I D =-150mA R DS(ON) Static Drain-to-SourceON-State Resistance8.0 Ω V GS =-10V, I D =-1.0A ∆R DS(ON) Change in R DS(ON) with Temperature 1.0 %/°C V GS =-10V, I D =-200mA G FS Forward Transconductance 400 mmho V DS =-25V, I D =-200mA C ISS Input Capacitance 200 C OSS Common Source Output Capacitance 55C RSS Reverse Transfer Capacitance 30 pF V GS =0V, V DS =-25Vf=1MHz t d(ON) Turn-ON Delay Time 10 t r Rise Time 15 t d(OFF) Turn-Off Delay Time 20t f Fall Time 15 nsV DD =-25V,I D =-1.0A R GEN =25 Ω V SD Diode Forward Voltage Drop -1.8 V V GS =0V, I SD =-0.5A t rr Reverse Recovery Time300 ns V GS =0V, I SD =-0.5ANotes:1) All DC parameters 100% tested at 25°C unless otherwise stated. (Pulsed test: 300µs pulse at 2% duty cycle.) 2) All AC parameters sample tested.P-Channel Switching Waveforms and Test CircuitDD0V -10V0V V DDt d(OFF)InputOutputt rt ft d(ON)t (ON)t (OFF)90%10%90%10%10%90%1/22/03。
北京公达电子 TP UP-AT微型面板式打印机 说明书
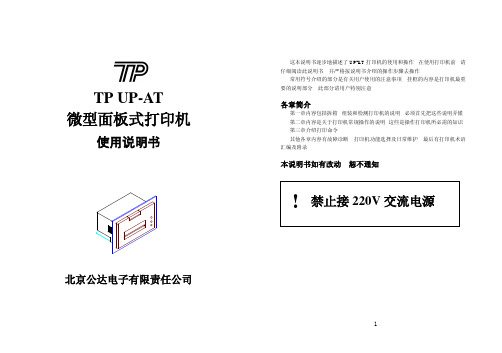
l 再次按下 SEL 键 指示灯显示绿色 重新进入在线工作方式
注意 打印机处于离线工作方式时 打印机不再接受来自主机的数据
19
2) 打印过程中实现暂停 在打印过程中按一下 SEL 键 打印机在完成前一行字符的打
印后 会暂停打印进入离线方式 再次按一下 SEL 键 打印机继 续打印 3 进入 HEX-DUMP 方式
图七
10
11
将新色带盒的右端轻轻放在机头右端轮轴上 注意此时左端稍微抬起 不要放下
图八 检查色带盒的右端如果未落到底 请用手指按住色带盒上的旋钮 按箭头方 向稍微转动 直到色带盒的右端落到底后再放下色带盒的左端 请检查色带是否拉直 如未拉直 或色带还露在色带盒的外面 可转动色带 盒上的旋钮 直到色带拉入色带盒内并拉直为止 当没有纸在机头里时 更换色 带更加容易 5. 推回机头并锁紧 6. 关上前盖
电源极性一定不要接错
!
电源电压一定要在容许范围之内
否则会给打印机造成永久性损坏
安装色带
色带盒在打印机出厂时已经装好 但经过一段时间使用后 需要更换色带盒 请按下列步骤装配色带盒 1. 确认打印机已同电源断开 2. 按下前盖锁扣, 打开前盖 3. 向下按右上角弹出按钮 弹出机头
图六 4. 用手抬起色带盒左端 窄的一端 然后再抬起色带盒的右端 取下色带盒
╲ 请按上面步骤更换色带
12
安装纸卷
安装纸卷的一般过程如下 1. 按下前盖锁扣, 打开前盖 2. 向下按右上角弹出按钮 弹出机头 3. 用手轻轻扳动机头板下端 向上向外抬起机头板
图九 4. 取出纸轴 5. 将新纸卷套在纸轴上后 按图十所示安装方向, 将纸轴装入打印机的
- 1、下载文档前请自行甄别文档内容的完整性,平台不提供额外的编辑、内容补充、找答案等附加服务。
- 2、"仅部分预览"的文档,不可在线预览部分如存在完整性等问题,可反馈申请退款(可完整预览的文档不适用该条件!)。
- 3、如文档侵犯您的权益,请联系客服反馈,我们会尽快为您处理(人工客服工作时间:9:00-18:30)。
___________________________________________________________________Selector Guide________________General DescriptionThe MAX6316–MAX6322 family of microprocessor (µP)supervisory circuits monitors power supplies and microprocessor activity in digital systems. It offers sev-eral combinations of push/pull, open-drain, and bidirec-tional (such as Motorola 68HC11) reset outputs, along with watchdog and manual reset features. The Selector Guide below lists the specific functions available from each device. These devices are specifically designed to ignore fast negative transients on V CC . Resets are guaranteed valid for V CC down to 1V.These devices are available in 26 factory-trimmed reset threshold voltages (from 2.5V to 5V, in 100mV incre-ments), featuring four minimum power-on reset timeout periods (from 1ms to 1.12s), and four watchdog timeout periods (from 6.3ms to 25.6s). Thirteen standard ver-sions are available with an order increment requirement of 2500 pieces (see Standard Versions table); contact the factory for availability of other versions, which have an order increment requirement of 10,000 pieces.The MAX6316–MAX6322 are offered in a miniature 5-pin SOT23 package.________________________ApplicationsPortable Computers Computers ControllersIntelligent InstrumentsPortable/Battery-Powered Equipment Embedded Control Systems____________________________Features♦Small 5-Pin SOT23 Package♦Available in 26 Reset Threshold Voltages2.5V to 5V, in 100mV Increments ♦Four Reset Timeout Periods1ms, 20ms, 140ms, or 1.12s (min)♦Four Watchdog Timeout Periods6.3ms, 102ms, 1.6s, or 25.6s (typ) ♦Four Reset Output StagesActive-High, Push/Pull Active-Low, Push/Pull Active-Low, Open-Drain Active-Low, Bidirectional♦Guaranteed Reset Valid to V CC = 1V♦Immune to Short Negative V CC Transients ♦Low Cost♦No External ComponentsMAX6316–MAX63225-Pin µP Supervisory Circuits withWatchdog and Manual Reset________________________________________________________________Maxim Integrated Products 119-0496; Rev 7; 11/07_______________Ordering InformationOrdering Information continued at end of data sheet.*The MAX6318/MAX6319/MAX6321/MAX6322 feature two types of reset output on each device.Typical Operating Circuit and Pin Configurations appear at end of data sheet.For pricing, delivery, and ordering information, please contact Maxim Direct at 1-888-629-4642,or visit Maxim’s website at .Specify lead-free by replacing “-T” with “+T” when ordering.ELECTRICAL CHARACTERISTICS(V CC = 2.5V to 5.5V, T A = -40°C to +125°C, unless otherwise noted. Typical values are at T A = +25°C.) (Note 1)M A X 6316–M A X 63225-Pin µP Supervisory Circuits with Watchdog and Manual Reset 2_______________________________________________________________________________________ABSOLUTE MAXIMUM RATINGSStresses beyond those listed under “Absolute Maximum Ratings” may cause permanent damage to the device. These are stress ratings only, and functional operation of the device at these or any other conditions beyond those indicated in the operational sections of the specifications is not implied. Exposure to absolute maximum rating conditions for extended periods may affect device reliability.Voltage (with respect to GND)V CC ......................................................................-0.3V to +6V RESET (MAX6320/MAX6321/MAX6322 only)...... -0.3V to +6V All Other Pins.........................................-0.3V to (V CC + 0.3V)Input/Output Current, All Pins.............................................20mAContinuous Power Dissipation (T A = +70°C)SOT23-5 (derate 7.1mW/°C above +70°C)...............571mW Operating Temperature Range..........................-40°C to +125°C Junction Temperature......................................................+150°C Storage Temperature Range..............................-65°C to +160°C Lead Temperature (soldering, 10s).................................+300°CTH available in 100mV increments from 2.5V to 5V (see Table 1 at end of data sheet).Note 3:Guaranteed by design.MAX6316–MAX63225-Pin µP Supervisory Circuits withWatchdog and Manual Reset_______________________________________________________________________________________3Note 5:Measured from RESET V OL to (0.8 x V CC ), R LOAD = ∞.Note 6:WDI is internally serviced within the watchdog period if WDI is left unconnected.Note 7:The WDI input current is specified as the average input current when the WDI input is driven high or low. The WDI input is designed for a three-stated-output device with a 10µA maximum leakage current and capable of driving a maximum capac-itive load of 200pF. The three-state device must be able to source and sink at least 200µA when active.ELECTRICAL CHARACTERISTICS (continued)M A X 6316–M A X 63225-Pin µP Supervisory Circuits with Watchdog and Manual Reset 4_________________________________________________________________________________________________________________________________Typical Operating Characteristics(T A = +25°C, unless otherwise noted.)021*********-4020-20406080100MAX6316/MAX6317/MAX6318/MAX6320/MAX6321SUPPLY CURRENT vs. TEMPERATURETEMPERATURE (°C)S U P P L Y C U R R E N T (μA )302010504090807060100-40-20020406080100V CC FALLING TO RESET PROPAGATIONDELAY vs. TEMPERATURETEMPERATURE (°C)R E S E T P R O P A G A T I O N D E L A Y (μs )140180160240220200300280260320-40020-20406080100MAX6316/MAX6317/MAX6319/MAX6320/MAX6322MANUAL RESET TO RESETPROPAGATION DELAY vs. TEMPERATURETEMPERATURE (°C)P R O P A G A T I O N D E L A Y (n s )0.950.980.970.961.000.991.041.031.021.011.05-40-2020406080100NORMALIZED RESET TIMEOUT PERIOD vs. TEMPERATUREM A X 6316t o c 04TEMPERATURE (°C)N O R M A L I Z E D R E S E T T I M E O U T P E R I O D0.950.980.970.961.000.991.041.031.021.011.05-40-2020406080100MAX6316/MAX6317/MAX6318/MAX6320/MAX6321NORMALIZED WATCHDOG TIMEOUTPERIOD vs. TEMPERATUREM A X 6316t o c 05TEMPERATURE (°C)N O R M A L I Z E D W A T C H D O G T I M E O U T P E R I O D800101001000MAXIMUM V CC TRANSIENT DURATION vs. RESET THRESHOLD OVERDRIVE2010RESET THRESHOLD OVERDRIVE (mV) V RST - V CCT RA N S I E N T D U R A T I O N (μs )3050604070200ns/divMAX6316M/6318MH/6319MHBIDIRECTIONALPULLUP CHARACTERISTICSMAX6316–MAX63225-Pin µP Supervisory Circuits withWatchdog and Manual Reset_______________________________________________________________________________________5______________________________________________________________Pin DescriptionM A X 6316–M A X 63225-Pin µP Supervisory Circuits with Watchdog and Manual Reset 6______________________________________________________________________________________________________Detailed DescriptionA microprocessor’s (µP) reset input starts or restarts the µP in a known state. The reset output of the MAX6316–MAX6322 µP supervisory circuits interfaces with the reset input of the µP, preventing code-execution errors during power-up, power-down, and brownout condi-tions (see the Typical Operating Circuit ). The MAX6316/MAX6317/MAX6318/MAX6320/MAX6321 are also capa-ble of asserting a reset should the µP become stuck in an infinite loop.Reset OutputThe MAX6316L/MAX6318LH/MAX6319LH feature an active-low reset output, while the MAX6317H/MAX6318_H/MAX6319_H/MAX6321HP/MAX6322HP feature an active-high reset output. RESET is guaran-teed to be a logic low and RESET is guaranteed to be a logic high for V CC down to 1V.The MAX6316–MAX6322 assert reset when V CC is below the reset threshold (V RST ), when MR is pulled low (MAX6316_/MAX6317H/MAX6319_H/MAX6320P/MAX6322HP only), or if the WDI pin is not serviced withinthe watchdog timeout period (t WD ). Reset remains assert-ed for the specified reset active timeout period (t RP ) after V CC rises above the reset threshold, after MR transitions low to high, or after the watchdog timer asserts the reset (MAX6316_/MAX6317H/MAX6318_H/MAX6320P/MAX6321HP). After the reset active timeout period (t RP )expires, the reset output deasserts, and the watchdog timer restarts from zero (Figure 2).Figure 1. Functional DiagramFigure 2. Reset Timing DiagramMAX6316–MAX63225-Pin µP Supervisory Circuits withWatchdog and Manual Reset_______________________________________________________________________________________7Bidirectional R E S E T OutputThe MAX6316M/MAX6318MH/MAX6319MH are designed to interface with µPs that have bidirectional reset pins,such as the Motorola 68HC11. Like an open-drain output,these devices allow the µP or other devices to pull the bidirectional reset (RESET ) low and assert a reset condi-tion. However, unlike a standard open-drain output, it includes the commonly specified 4.7k Ωpullup resistor with a P-channel active pullup in parallel.This configuration allows the MAX6316M/MAX6318MH/MAX6319MH to solve a problem associated with µPs that have bidirectional reset pins in systems where sev-eral devices connect to RESET (F igure 3). These µPs can often determine if a reset was asserted by an exter-nal device (i.e., the supervisor IC) or by the µP itself (due to a watchdog fault, clock error, or other source),and then jump to a vector appropriate for the source of the reset. However, if the µP does assert reset, it does not retain the information, but must determine the cause after the reset has occurred.The following procedure describes how this is done in the Motorola 68HC11. In all cases of reset, the µP pulls RESET low for about four external-clock cycles. It then releases RESET , waits for two external-clock cycles,then checks RESET ’s state. If RESET is still low, the µP concludes that the source of the reset was external and, when RESET eventually reaches the high state, it jumps to the normal reset vector. In this case, stored-state information is erased and processing begins fromscratch. If, on the other hand, RESET is high after a delay of two external-clock cycles, the processor knows that it caused the reset itself and can jump to a different vector and use stored-state information to determine what caused the reset.A problem occurs with faster µPs; two external-clock cycles are only 500ns at 4MHz. When there are several devices on the reset line, and only a passive pullup resis-tor is used, the input capacitance and stray capacitance can prevent RESET from reaching the logic high state (0.8✕V CC ) in the time allowed. If this happens, all resets will be interpreted as external. The µP output stage is guaran-teed to sink 1.6mA, so the rise time can not be reduced considerably by decreasing the 4.7k Ωinternal pullup resistance. See Bidirectional Pullup Characteristics in the Typical Operating Characteristics .The MAX6316M/MAX6318MH/MAX6319MH overcome this problem with an active pullup FET in parallel with the 4.7k Ωresistor (F igures 4 and 5). The pullup transistor holds RESET high until the µP reset I/O or the supervisory circuit itself forces the line low. Once RESET goes below V PTH , a comparator sets the transition edge flip-flop, indi-cating that the next transition for RESET will be low to high. When RESET is released, the 4.7k Ωresistor pulls RESET up toward V CC . Once RESET rises above V PTH but is below (0.85 x V CC ), the active P-channel pullup turns on. Once RESET rises above (0.85 x V CC ) or the 2µs one-shot times out, the active pullup turns off. The parallel combination of the 4.7k Ωpullup and theFigure 3. MAX6316M/MAX6318MH/MAX6319MH Supports Additional Devices on the Reset BusM A X 6316–M A X 63225-Pin µP Supervisory Circuits with Watchdog and Manual Reset 8_______________________________________________________________________________________Figure 4. MAX6316/MAX6318MH/MAX6319MH Bidirectional Reset Output Functional DiagramMAX6316–MAX63225-Pin µP Supervisory Circuits withWatchdog and Manual Reset_______________________________________________________________________________________9P-channel transistor on-resistance quickly charges stray capacitance on the reset line, allowing RESET to transition from low to high within the required two elec-tronic-clock cycles, even with several devices on the reset line. This process occurs regardless of whether the reset was caused by V CC dipping below the reset threshold, the watchdog timing out, MR being asserted,or the µP or other device asserting RESET . The parts do not require an external pullup. To minimize supply cur-rent consumption, the internal 4.7k Ωpullup resistor dis-connects from the supply whenever the MAX6316M/MAX6318MH/MAX6319MH assert reset.Open-Drain R E S E T OutputThe MAX6320P/MAX6321HP/MAX6322HP have an active-low, open-drain reset output. This output struc-ture will sink current when RESET is asserted. Connect a pullup resistor from RESET to any supply voltage up to 6V (Figure 6). Select a resistor value large enough toregister a logic low (see Electrical Characteristics ), and small enough to register a logic high while supplying all input current and leakage paths connected to the RESET line. A 10k Ωpullup is sufficient in most applications.Manual-Reset InputThe MAX6316_/MAX6317H/MAX6319_H/MAX6320P/MAX6322HP feature a manual reset input. A logic low on MR asserts a reset. After MR transitions low to high, reset remains asserted for the duration of the reset timeout peri-od (t RP ). The MR input is connected to V CC through an internal 52k Ωpullup resistor and therefore can be left unconnected when not in use. MR can be driven with TTL-logic levels in 5V systems, with CMOS-logic levels in 3V systems, or with open-drain or open-collector output devices. A normally-open momentary switch from MR to ground can also be used; it requires no external debouncing circuitry. MR is designed to reject fast, negative-going transients (typically 100ns pulses). A 0.1µF capacitor from MR to ground provides additional noise immunity.The MR input pin is equipped with internal ESD-protection circuitry that may become forward biased. Should MR be driven by voltages higher than V CC , excessive current would be drawn, which would damage the part. F or example, assume that MR is driven by a +5V supply other than V CC . If V CC drops lower than +4.7V, MR ’s absolute maximum rating is violated [-0.3V to (V CC + 0.3V)], and undesirable current flows through the ESD structure from MR to V CC . To avoid this, use the same supply for MR as the supply monitored by V CC . This guarantees that the voltage at MR will never exceed V CC .Watchdog InputThe MAX6316_/MAX6317H/MAX6318_H/MAX6320P/MAX6321HP feature a watchdog circuit that monitors the µP’s activity. If the µP does not toggle the watchdog input (WDI) within the watchdog timeout period (t WD ),reset asserts. The internal watchdog timer is cleared by reset or by a transition at WDI (which can detect pulses as short as 50ns). The watchdog timer remains cleared while reset is asserted. Once reset is released, the timer begins counting again (Figure 7).The WDI input is designed for a three-stated output device with a 10µA maximum leakage current and the capability of driving a maximum capacitive load of 200pF.The three-state device must be able to source and sink at least 200µA when active. Disable the watchdog function by leaving WDI unconnected or by three-stating the driver connected to WDI. When the watchdog timer is left open circuited, the timer is cleared internally at intervals equal to 7/8 of the watchdog period.Figure 6. MAX6320P/MAX6321HP/MAX6322HP Open-Drain RESET Output Allows Use with Multiple SuppliesFigure 5. Bidirectional RESET Timing DiagramM A X 6316–M A X 63225-Pin µP Supervisory Circuits with Watchdog and Manual Reset 10______________________________________________________________________________________Applications InformationWatchdog Input CurrentThe WDI input is internally driven through a buffer and series resistor from the watchdog counter. For minimum watchdog input current (minimum overall power con-sumption), leave WDI low for the majority of the watch-dog timeout period. When high, WDI can draw as much as 160µA. Pulsing WDI high at a low duty cycle will reduce the effect of the large input current. When WDI is left unconnected, the watchdog timer is serviced within the watchdog timeout period by a low-high-low pulse from the counter chain.Negative-Going V CC TransientsThese supervisors are immune to short-duration, nega-tive-going V CC transients (glitches), which usually do not require the entire system to shut down. Typically,200ns large-amplitude pulses (from ground to V CC ) on the supply will not cause a reset. Lower amplitude puls-es result in greater immunity. Typically, a V CC transient that goes 100mV under the reset threshold and lasts less than 4µs will not trigger a reset. An optional 0.1µF bypass capacitor mounted close to V CC provides addi-tional transient immunity.Ensuring Valid Reset OutputsDown to V CC = 0The MAX6316_/MAX6317H/MAX6318_H/MAX6319_H/MAX6321HP/MAX6322HP are guaranteed to operate properly down to V CC = 1V. In applications that require valid reset levels down to V CC = 0, a pulldown resistor to active-low outputs (push/pull and bidirectional only,F igure 8) and a pullup resistor to active-high outputs(push/pull only, Figure 9) will ensure that the reset line is valid while the reset output can no longer sink orsource current. This scheme does not work with the open-drain outputs of the MAX6320/MAX6321/MAX6322.The resistor value used is not critical, but it must be large enough not to load the reset output when V CC is above the reset threshold. F or most applications,100k Ωis adequate.Watchdog Software Considerations(MAX6316/MAX6317/MAX6318/MAX6320/MAX6321)One way to help the watchdog timer monitor software execution more closely is to set and reset the watchdog input at different points in the program, rather than pulsing the watchdog input high-low-high or low-high-low. This technique avoids a stuck loop, in which the watchdog timer would continue to be reset inside the loop, keeping the watchdog from timing out.Figure 7. Watchdog Timing RelationshipFigure 9. Ensuring RESET Valid to V CC = 0 on Active-High Push/Pull OutputsFigure 8. Ensuring RESET Valid to V CC = 0 on Active-Low Push/Pull and Bidirectional OutputsMAX6316–MAX6322Watchdog and Manual Reset______________________________________________________________________________________11F igure 10 shows an example of a flow diagram where the I/O driving the watchdog input is set high at the beginning of the program, set low at the end of every subroutine or loop, then set high again when the pro-gram returns to the beginning. If the program should hang in any subroutine, the problem would be quickly corrected, since the I/O is continually set low and the watchdog timer is allowed to time out, causing a reset or interrupt to be issued. As described in the Watchdog Input Current section, this scheme results in higher time average WDI current than does leaving WDI low for the majority of the timeout period and periodically pulsing it low-high-low.Figure 10. Watchdog Flow Diagram__________________Pin ConfigurationsTypical Operating CircuitTable 2. Standard VersionsTable 1. Factory-Trimmed Reset ThresholdsM A X 6316–M A X 6322Watchdog and Manual ResetTable 3. Reset/Watchdog Timeout PeriodsMAX6316–MAX6322Watchdog and Manual Reset______________________________________________________________________________________13__Ordering Information (continued)a watchdog feature (see Selector Guide) are factory-trimmed to one of four watchdog timeout periods. Insert the letter corre-sponding to the desired watchdog timeout period (W, X, Y, or Z from Table 3) into the blank following the reset timeout suffix.TRANSISTOR COUNT: 191SUBSTRATE IS INTERNALLY CONNECTED TO V+Chip Informationdard versions only. The required order increment for nonstandard versions is 10,000 pieces. Contact factory for availability.M A X 6316–M A X 6322Watchdog and Manual Reset 14______________________________________________________________________________________Package Information(The package drawing(s) in this data sheet may not reflect the most current specifications. For the latest package outline information,go to /packages .)M axim cannot assume responsibility for use of any circuitry other than circuitry entirely embodied in a M axim product. No circuit patent licenses are implied. Maxim reserves the right to change the circuitry and specifications without notice at any time.Maxim Integrated Products, 120 San Gabriel Drive, Sunnyvale, CA 94086 408-737-7600 ____________________15©2007 Maxim Integrated Productsis a registered trademark of Maxim Integrated Products, Inc.MAX6316–MAX6322 Watchdog and Manual ResetRevision History。