电炉炼钢
电炉炼钢
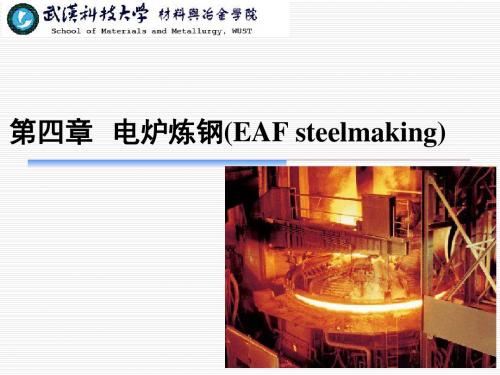
22
4.4.5 还原
还原期的主要任务
脱氧至要求(wO为0.003-0.008%); 脱硫至一定值; 调整钢液成分,进行合金化; 调整钢液温度。
其中:脱氧是核心,温度是条件,造渣是保证。
1/30/2019/19:58:21
23
还原操作
电炉常用综合脱氧法,其还原操作以脱氧为核心。 当钢液的温度、磷和碳含量符合要求,扒渣量超 过95%; 加Fe-Mn、Fe-Si块等预脱氧(沉淀脱氧); 加石灰、萤石、火砖块,造稀薄渣; 还原,加碳粉、Fe-Si粉等脱氧(扩散脱氧), 分3~5批,7~10min/批; 搅拌,取样、测温; 调整成分,加Al或Ca-Si块等终脱氧(沉淀脱 氧); 出钢
1/30/2019/19:58:21
17
4.4.2 装料
目前,广泛采用炉顶料篮装料,每炉钢的炉料分 1~3次加入。 装料的好坏影响炉衬寿命、冶炼时间、电耗、电 极消耗以及合金元素的烧损等。因此要求合理装 料,这主要取决于炉料在料筐中的布料合理与否。 现场布料(装料)经验:下致密、上疏松、中间 高、四周低、炉门口无大料,穿井快、不搭桥, 提前助熔效果好。
1/30/2019/19:58:21
24
4.4.6 出钢
传统电炉冶炼工艺,钢液经氧化、还原后, 当化学成分合格,温度符合要求,钢液脱 氧良好,炉渣碱度与流动性合适时即可出 钢。 因出钢过程的钢-渣接触可进一步脱氧与 脱硫,故要求采取“大口、深冲、钢-渣 混合”的出钢方式。
1/30/2019/19:58:21
1/30/2019/19:58:21
18
电 炉 装 料
4.4.3 熔化
电炉炼钢

炉料熔化过程及供电
装料完毕即可通电熔化。炉料熔化过程图, 基本可分为四个阶段(期),即点弧、穿井、主 熔化及熔末升温。
点(起)弧期
从送电起弧至电极端部下降到深度为d电极为点 弧期。 此期电流不稳定,电弧在炉顶附近燃烧辐射,二 次电压越高,电弧越长,对炉顶辐射越厉害,并且热 量损失也越多。 为保护炉顶,在炉上部布一些轻薄料,以便让电 极快速进入料中,减少电弧对炉顶的辐射。 供电上采用较低电压、较低电流。
近些年,我国电炉流程的发展虽然受到重视, 但发展电炉短流程应慎重一些,可以适当发展, 不可盲目。因为在当前条件下,我国不具备电 能和废钢方面的优势,即不具备成本优势。在 江阴兴澄钢铁有限公司,已建成我国第一条四 位一体的特殊钢短流程生产线,工艺流程 为:100t直流电弧炉冶炼-LF、VD精炼-R=12m 大方坯连铸-热送全连轧,全套全新设备从德国 引进,能够开发生产合金结构钢、弹簧钢、齿 轮钢、易切削钢、轴承钢、高压锅炉管坯钢等 品种,将成为全国优质钢、特殊钢装备水平领 先、能力超百万吨的企业
2)双渣氧化法
又称氧化法,它的特点是冶炼过程有正常的氧 化期,能脱碳、脱磷,去气、夹杂,对炉料也无特殊要
求;还有还原期,可以冶炼高质量钢。
目前,几乎所有的钢种都可以用氧化法冶炼, 以下主要介绍氧化法冶炼工艺。
冶炼工艺
传统氧化法冶炼工艺是电炉炼钢法的基础。 其操作过程分为:补炉、装料、熔化、 氧化、还原与出钢六个阶段。因主要由熔化、氧 化、还原期组成,俗称老三期。 一、补炉 1)影响炉衬寿命的“三要素” • 炉衬的种类、性质和质量; • 高温电弧辐射和熔渣的化学浸蚀; • 吹氧操作与渣、钢等机械冲刷以及装料的冲击。
脱磷反应与脱磷条件:
脱磷反应:
2[P]+5(FeO)+4(CaO)=(4CaO· P2O5)+5 [Fe], △ H<0 分析:反应是在渣-钢界面上进行,是放 热反应。
电炉炼钢原理及工艺
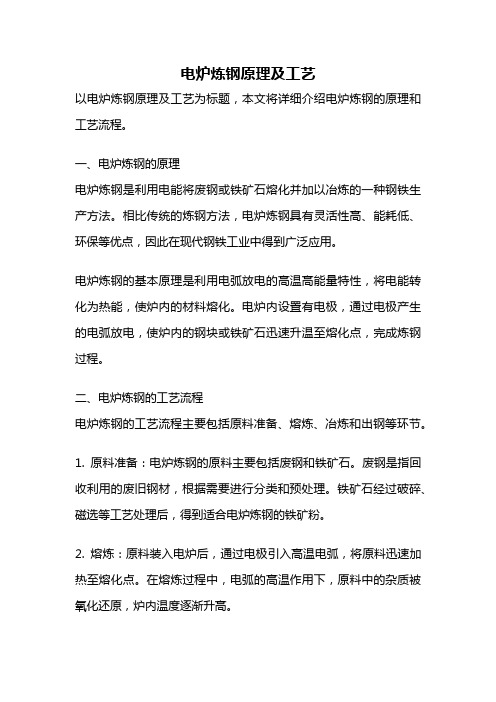
电炉炼钢原理及工艺以电炉炼钢原理及工艺为标题,本文将详细介绍电炉炼钢的原理和工艺流程。
一、电炉炼钢的原理电炉炼钢是利用电能将废钢或铁矿石熔化并加以冶炼的一种钢铁生产方法。
相比传统的炼钢方法,电炉炼钢具有灵活性高、能耗低、环保等优点,因此在现代钢铁工业中得到广泛应用。
电炉炼钢的基本原理是利用电弧放电的高温高能量特性,将电能转化为热能,使炉内的材料熔化。
电炉内设置有电极,通过电极产生的电弧放电,使炉内的钢块或铁矿石迅速升温至熔化点,完成炼钢过程。
二、电炉炼钢的工艺流程电炉炼钢的工艺流程主要包括原料准备、熔炼、冶炼和出钢等环节。
1. 原料准备:电炉炼钢的原料主要包括废钢和铁矿石。
废钢是指回收利用的废旧钢材,根据需要进行分类和预处理。
铁矿石经过破碎、磁选等工艺处理后,得到适合电炉炼钢的铁矿粉。
2. 熔炼:原料装入电炉后,通过电极引入高温电弧,将原料迅速加热至熔化点。
在熔炼过程中,电弧的高温作用下,原料中的杂质被氧化还原,炉内温度逐渐升高。
3. 冶炼:炉内温度达到要求后,加入适量的脱氧剂和合金元素,调整炉内成分,提高钢的质量。
同时,通过喷吹氧气等方式进行氧化剂的供给,控制冶炼过程中的氧化还原反应,进一步净化钢液。
4. 出钢:冶炼结束后,通过倒炉或倾炉等方式将炼好的钢液从电炉中倾出,进一步加工成所需的钢材。
出钢后,需要进行连铸、轧制等工艺,最终得到成品钢材。
三、电炉炼钢的特点和优势1. 灵活性高:电炉炼钢可灵活调整炉内温度和成分,适应不同的钢种和质量要求,具有较强的适应性和灵活性。
2. 能耗低:电炉炼钢相比传统炼钢方法,能耗更低。
电能可以高效转化为热能,提高能源利用效率,减少能源浪费。
3. 环保:电炉炼钢过程中没有燃料燃烧产生的废气和废渣,减少了对环境的污染。
另外,电炉炼钢可以使用废钢作为原料,有效促进了废钢的回收利用,减少了资源浪费。
4. 生产效率高:电炉炼钢的工艺流程简单,生产周期短,可以实现快速连续生产,提高生产效率。
电炉炼钢流程

电炉炼钢流程电炉炼钢是一种利用电能作为热源,通过电弧加热炉料,将废钢和铁合金等原料炼制成优质钢材的冶炼方法。
电炉炼钢流程通常包括预处理、炉料装入、炉前准备、炉内冶炼和炉后处理等环节。
下面将详细介绍电炉炼钢的流程及各个环节的操作步骤。
1. 预处理。
在进行电炉炼钢之前,首先需要对原料进行预处理。
这包括对废钢进行分类、清理和切割,对铁合金进行筛分和称重等工作。
同时,还需要对电炉进行检查和维护,确保电炉设备处于良好状态。
2. 炉料装入。
在炉料装入环节,操作人员需要按照炉料配比要求,将预处理好的废钢和铁合金装入电炉中。
同时,还需要加入适量的石灰、氧化铁等炼钢助剂,以调整炉料成分和保证冶炼质量。
3. 炉前准备。
在炉前准备阶段,操作人员需要对电炉进行预热,提高炉温至冶炼温度。
同时,还需要对电炉进行真空抽气或气体通风,以确保炉内气氛符合冶炼要求。
4. 炉内冶炼。
炉内冶炼是电炉炼钢的核心环节,操作人员需要根据工艺要求,通过电弧加热炉料,使其迅速熔化。
在冶炼过程中,还需要根据炉料状况进行合理的搅拌和氧化处理,以保证炼钢过程的顺利进行。
5. 炉后处理。
炉后处理是指在炼钢结束后,对冶炼产物进行处理和整理的环节。
这包括对炉渣进行清理和处理,对炼钢温度进行控制,以及对炼钢成品进行取样和检验等工作。
总结。
通过以上流程的介绍,我们可以看到,电炉炼钢是一个复杂的工艺过程,需要操作人员严格按照流程要求进行操作,以确保炼钢质量和生产效率。
同时,还需要对电炉设备进行定期维护和检查,以保证设备的正常运行和安全生产。
希望本文的介绍能够帮助大家更好地了解电炉炼钢的流程和操作要点,为相关行业的生产和管理工作提供参考和指导。
电炉炼钢工艺流程
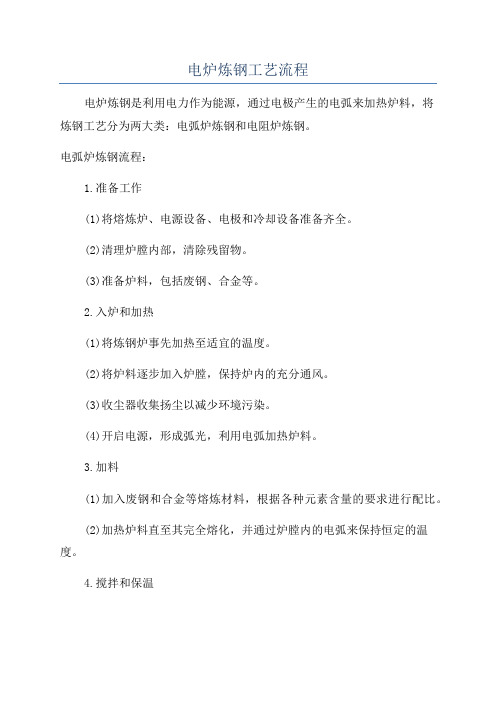
电炉炼钢工艺流程电炉炼钢是利用电力作为能源,通过电极产生的电弧来加热炉料,将炼钢工艺分为两大类:电弧炉炼钢和电阻炉炼钢。
电弧炉炼钢流程:1.准备工作(1)将熔炼炉、电源设备、电极和冷却设备准备齐全。
(2)清理炉膛内部,清除残留物。
(3)准备炉料,包括废钢、合金等。
2.入炉和加热(1)将炼钢炉事先加热至适宜的温度。
(2)将炉料逐步加入炉膛,保持炉内的充分通风。
(3)收尘器收集扬尘以减少环境污染。
(4)开启电源,形成弧光,利用电弧加热炉料。
3.加料(1)加入废钢和合金等熔炼材料,根据各种元素含量的要求进行配比。
(2)加热炉料直至其完全熔化,并通过炉膛内的电弧来保持恒定的温度。
4.搅拌和保温(1)通过搅拌装置(机械手、气枪等)对炉内炉料进行搅拌,以保证均匀加热。
(2)在最佳温度下保温,以提高合金和炉料的反应速度。
5.放钢和渣(1)根据钢种要求,加入脱氧剂和合金稀释剂。
(2)按照配方要求加入炉渣,帮助除去杂质和渣夹。
6.合金调整和测温(1)根据测温结果,调整冶炼条件,确保达到合适的温度。
(2)根据钢种需要,加入适量的合金元素,保证合金成分符合技术要求。
7.出钢(1)开启出钢口,将炼好的钢液顺利倾出。
(2)根据需要对炼钢炉进行钢包保温、修补等工作。
(3)将倾出的钢液进行调节和再加工,以满足用户要求。
(4)进行钢液的凝固和结晶,得到成品钢。
电阻炉炼钢流程:电阻炉是通过电流通过炉体自身的电阻产生热能,实现炉料加热熔化。
1.准备工作(1)检查电阻炉的各项设备和电源的正常运行。
(2)清理炉内和炉外的杂质和残留物。
(3)准备好炉料,包括废钢、矿石等。
2.入炉和加热(1)将炼钢炉预先加热至适宜的温度。
(2)逐步加入炉料,保持通风和顺畅的炉内气流。
(3)开启电源,使电流通过炉体,产生热能。
3.加料和熔化(1)加入炉料,实现其完全熔化。
(2)通过控制电流和炉内温度,保持炉料的恒定熔化状态。
4.炉内观察和保温(1)观察炉内炉料的状况,保持熔化状态的均匀性。
电炉炼钢原理及工艺
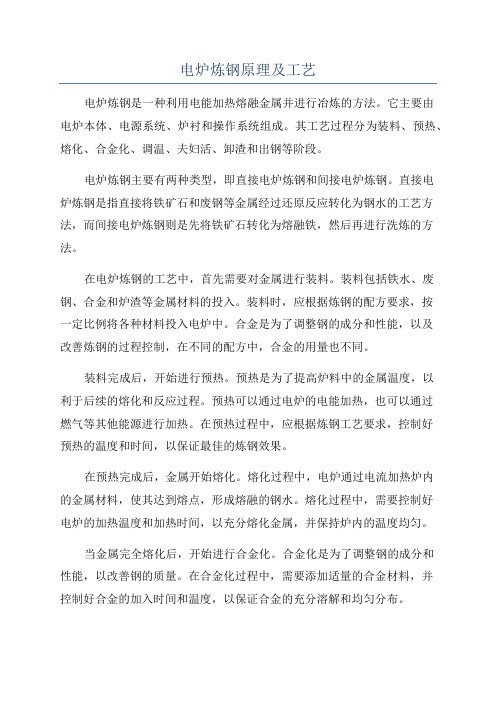
电炉炼钢原理及工艺电炉炼钢是一种利用电能加热熔融金属并进行冶炼的方法。
它主要由电炉本体、电源系统、炉衬和操作系统组成。
其工艺过程分为装料、预热、熔化、合金化、调温、夫妇活、卸渣和出钢等阶段。
电炉炼钢主要有两种类型,即直接电炉炼钢和间接电炉炼钢。
直接电炉炼钢是指直接将铁矿石和废钢等金属经过还原反应转化为钢水的工艺方法,而间接电炉炼钢则是先将铁矿石转化为熔融铁,然后再进行洗炼的方法。
在电炉炼钢的工艺中,首先需要对金属进行装料。
装料包括铁水、废钢、合金和炉渣等金属材料的投入。
装料时,应根据炼钢的配方要求,按一定比例将各种材料投入电炉中。
合金是为了调整钢的成分和性能,以及改善炼钢的过程控制,在不同的配方中,合金的用量也不同。
装料完成后,开始进行预热。
预热是为了提高炉料中的金属温度,以利于后续的熔化和反应过程。
预热可以通过电炉的电能加热,也可以通过燃气等其他能源进行加热。
在预热过程中,应根据炼钢工艺要求,控制好预热的温度和时间,以保证最佳的炼钢效果。
在预热完成后,金属开始熔化。
熔化过程中,电炉通过电流加热炉内的金属材料,使其达到熔点,形成熔融的钢水。
熔化过程中,需要控制好电炉的加热温度和加热时间,以充分熔化金属,并保持炉内的温度均匀。
当金属完全熔化后,开始进行合金化。
合金化是为了调整钢的成分和性能,以改善钢的质量。
在合金化过程中,需要添加适量的合金材料,并控制好合金的加入时间和温度,以保证合金的充分溶解和均匀分布。
合金化完成后,开始进行调温。
调温是为了得到合适的熔融铁水温度和钢水温度,以满足后续冶炼工艺的需求。
调温可以通过调节电炉的加热功率和炉内的温度控制装置来实现。
调温完成后,进行夫妇活。
夫妇活是为了提高钢水的纯净度和均匀性,以去除炉渣和杂质。
夫妇活可以通过在炉内注入草酸、石灰和氮气等化学物质,或者进行吹炼和搅拌来实现。
夫妇活完成后,开始卸渣。
卸渣是指将炉渣从熔融金属中移除的过程。
卸渣可以通过倾炉或者顶炉的方式来进行。
电炉炼钢对废钢的要求

电炉炼钢是利用电力作为能源的一种炼钢方法,对于废钢的要求通常包括以下几个方面:
1.废钢质量:废钢应具备一定的质量标准,例如需要符合特定的化学成分、含碳量、硫、
磷等元素的限制。
这是为了确保最终炼钢过程中所得到的钢材质量符合规定的技术要求。
2.温度:废钢在投入电炉前应达到适宜的温度范围。
过低的温度可能导致炉内温度下降,
影响炉内反应的进行和炼钢工艺的正常运行。
3.清洁度:废钢表面不应有过多的污染物,如泥土、油脂、涂料等,以避免对炉内设备和
操作产生不利影响。
清洁的废钢也有助于提高炼钢过程中的炉效和钢材质量。
4.尺寸:废钢应符合一定的尺寸要求,以便在电炉中更好地进行搅拌和熔化。
通常,废钢
块的尺寸要适中,不宜过大或过小。
这些要求会根据具体的电炉炼钢工艺和使用的废钢种类而有所不同。
在实际生产中,通常会制定详细的废钢品质标准,以确保废钢能够满足电炉炼钢的要求,并最大限度地提高炼钢效率和产品质量。
第八章 电炉炼钢

⑶电抗器 它串联在变压器的高压侧。其作用是使电路中感抗增加,以达 到稳定电弧和限制短路电流的目的。 ⑷变压器
它是电弧炉的主要电器设备。
⑸短网:是指从变压器低压侧的引出线至电极这一段线路。 ⑹电极:是将变压器输入的电流引入熔炼室的导体。
电炉炼钢技术发展重点
纯净钢(Clean steel),是指对钢中O、S、P、H、N等杂质元素的控 制以及对非金属夹杂物数量和形态的要求。近年来,又增加了对残余 元素的要求。随着连铸技术和炉外处理技术的发展,钢材纯净度显著 提高,提高纯净度可大大改善钢的加工和使用性能。
炉料密实
做到大、中、小料块合理搭配,保证有较大的堆密度,减少装料
次数,缩短冶炼时间,降低电耗。对于10~100 t的电弧炉,通常把重
量小于10kg的料块叫小料;10~50kg的叫中料;大于50kg而小于炉 料总重的1/50的叫大料。搭配时大块料约占总装入量的40%,中料45%、
小料15%。
•布料原则为;下致密、上疏松;中间高、四周低、炉门口无大料, 保证穿井快、不搭桥。 •现代电炉装料方式有料斗(或称为料篮、料罐、料筐)顶装料和皮带 料两种方式。 装
布料合理
目的:使炉料能最大限度地吸收电弧热,减少对炉衬的辐射和合金元 的挥发。 一般布料顺序是: 素
先在炉底均匀铺一层石灰,石灰量约为料重的1%~2%、以保护炉底和提前 造渣。 石灰上面装小料,重量约为小料总量的一半,也起保护炉底的作用。 小料上的电弧高温区装大料和难熔料,以加速其熔化。 大料间空隙填充小料,靠近炉墙及大料上面装入全部中料,最上面则装其 余小料。 镍、铬等铁合金不应装在电极下方;钨铁、钼铁等不易氧化而且难熔,可 放在高温区,但不宜放在电极下面; 增碳用焦炭或碎电极块应装在石灰上面或底层小料上面。以控制碳的回收 率; 最后在电极下面放一些碎焦以便起弧。
- 1、下载文档前请自行甄别文档内容的完整性,平台不提供额外的编辑、内容补充、找答案等附加服务。
- 2、"仅部分预览"的文档,不可在线预览部分如存在完整性等问题,可反馈申请退款(可完整预览的文档不适用该条件!)。
- 3、如文档侵犯您的权益,请联系客服反馈,我们会尽快为您处理(人工客服工作时间:9:00-18:30)。
然后炉盖同吊架以及支柱一起开向出钢槽一边。
炉身开出式装料:装料,电极升高,炉盖抬起, 炉身沿轨道向炉门方向开出。
电炉炉身开出式装料情况
炉盖旋转式炼钢电 弧炉的装料情况
1-电弧炉平台;2-出钢槽;3-炉盖;4-石墨电极; 5-装料筐;6-炉体;7-倾斜摇架
八 水冷炉壁及水冷炉盖
目前,在大容量电炉和超高功率电弧炉上大都采用水冷
大部分采用采用预制整块的流钢槽砖砌成,使用寿命
较长,且拆装也方便。在保证出钢顺利的前提下,流 钢槽长度应尽可能短些,以减少出钢时产生的二次氧
化。
四 电极密封圈
为使电极在炼钢过程中能自由升降,电极孔直径
-般要比电极直径大40~50mm,炉内的高温气体就
不断地从电极孔缝隙中逸出,而空气则不断地从炉门 缝隙中吸入,这样不但使热损失增加,不利于维护炉 内还原性气氛,而且还使电极受高温炉气的冲刷而氧 化烧损严重,电极直径变细,易于析断。因此,必须
量必须很低,致使酸性电弧炉冶炼不能广泛使用,
炼钢电弧炉通常都采用碱性法冶炼,因此本章只讨 论碱性电弧炉的冶炼工艺 。
碱性电弧炉炼钢的特点 电弧炉主要是利用电极与炉料间放电产生电弧发出 的热量来炼钢。其优点为:热效率比较高,废气带走的 热量相对较少,其热效率可达65%以上;温度高,电 弧区温度高达3000℃以上,可快速熔化各种炉料,并
使用电极密封圈,以减少缝隙,防止炉气外逸,同时
也可冷却炉顶,延长炉顶寿命。
五 电极夹持器
电极夹持器有两个作用,-是向电极导电,二
是将电极固定,并在需要松放电极时能方便灵活
地松开。电极夹持器在高温下工作,并受到大电
流通过时产生的电阻热的作用,故要求夹持器应 能牢固地夹住电极,不能因电极的自重而松动或 滑动;接触表面要光滑,与电极之间不能因接触 不良而起弧;要有足够的机械强度,能耐高温、
第四章 电炉炼钢
电炉炼钢,主要是指电弧炉炼钢,是国内外生
产特殊钢的主要方法。目前,世界上95%以上的电
炉钢是由电弧炉生产的,还有少量是由感应炉、电 渣炉等生产的。根据炉衬材料化学性质不同,电弧 炉炼钢有酸性和碱性之分。采用碱性耐火村料做炉 衬,炼钢时造碱性炉渣,这种炉子称为碱性电弧炉。
以酸性耐火村料做炉衬,炼钢时造酸性炉渣,这种
碱度和氧化性等有关;而在吹氧时C氧化10%~
30%、Fe氧化2%~3%。
率,但在我国由于受原料来源的限制,用得不多。
氧化法:一般以废钢为原料,冶炼过程中用矿石或氧 气来氧化炉料中的杂质,同时通过氧化沸腾过程去除钢
水中大部分气体。此法不能回收废钢中的大部分合金元
素,但它是电炉冶炼的基本方法,在我国应用最为广泛。
氧化法电弧炉炼钢工艺的特点是冶炼过程有正 常的氧化期,能脱碳、脱磷,去气、夹杂,对炉料 也无特殊要求;还有还原期,可以冶炼高质量钢。 目前,几乎所有的钢种都可以用氧化法冶炼,以
下主要介绍氧化法冶炼工艺。
§4.3 电炉冶炼工艺
传统氧化法冶炼工艺是电炉炼钢法的基础。 其操作过程分为:补炉、装料、熔化、氧化、 还原与出钢六个阶段。因主要由熔化、氧化、还 原期组成,俗称老三期。
一、补炉 1)影响炉衬寿命的“三要素”
• 炉衬的种类、性质和质量; • 高温电弧辐射和熔渣的化学浸蚀; • 吹氧操作与渣、钢等机械冲刷以及装料的冲击。
炉子称为酸性电弧炉。
酸性电弧炉冶炼和碱性电弧炉冶炼相比有较多
的优越性,如钢中的气体含量较低,钢材的纵向与 横向机械性能相近,即各向异性较小。在酸性电弧 炉中由于酸性渣的电阻较大、因此电弧较短,热效 率高。此外,酸性炉衬的寿命高于碱性炉衬,这些
都是酸性电弧炉的优越性。但酸性电炉冶炼对炉料
要求甚严,由于炼钢时造酸性炉渣,因而对钢液基 本不具备脱硫及脱磷能力,要求炉料中的磷、硫含
熔末升温 期
电弧暴露 → 全熔
保护 炉壁
低电压、 大电流
水冷+ 泡沫渣
2)及时吹氧与元素氧化
熔化期吹氧助熔,初期以切割为主,当炉料
基本熔化形成熔池时,则以向钢液中吹氧为主。 吹氧是利用元素氧化热加速炉料熔化。当固 体料发红(~900℃)开始吹氧最为合适,吹氧过 早浪费氧气,过迟延长熔化时间。 一般情况下,熔化期钢中的Si、Al、Ti、V等 几乎全部氧化,Mn、P氧化40%~50%,这与渣的
二、装料
目前,广泛采用炉顶料罐(或叫料篮、料 筐)装料,每炉钢的炉料分1~3次加入。装料的 好坏影响炉衬寿命、冶炼时间、电耗、电极消耗 以及合金元素的烧损等。因此,要求合理装料, 这主要取决于炉料在料罐中的布料合理与否。 现场布料(装料)经验:下致密、上疏松、 中间高、四周低、炉门口无大料,穿井快、不搭 桥,熔化快、效率高。
•
•
• •
3)补炉方法
补炉方法分为人工投补和机械喷补,根据选用材料 的混合方式不同,又分为干补和湿补两种。 目前,在大型电炉上多采用机械喷补,机械喷补设 备有炉门喷补机、炉内旋转补炉机,机械喷补补炉速度 快、效果好。 补炉的原则是:高温、快补、薄补。
4)补炉材料
机械喷补材料主要用镁砂、白云石或两者的混合物, 并掺入磷酸盐或硅酸盐等粘结剂。
§4.2 电炉冶炼原材料及操作方法
一 原材料
1 金属料:废钢、生铁(铁水)、铁合金
2 造渣剂:(石灰、萤石、铁矿石 3 氧化剂:氧气、铁矿石、氧化铁皮
4 增碳剂:电极块、焦炭粉、生铁
二 操作方法 (P125~126)
碱性电弧炉的工艺操作可分为两种:氧化法和不氧化法。 不氧化法(也称为返回冶炼法):用较好的合金废钢 作原料,废钢成分与冶炼钢种的成分基本相近似,冶炼 过程中只造还原渣,可回收大部分合金元素和提高生产
电炉冶炼与炉外精炼及连铸相结合形成的基本炼钢流 程,不但提高了钢的质量,还降低了上产成本。
但是,电弧炉也还存在一些不足之处,如由于电
弧的离解作用,使空气和水蒸气离解出大量氢和氮,
在还原期易被钢水吸收,因此,电炉钢若不经特殊处 理,其氢、氮含量一般比转炉钢高;由于电弧是点热
源,炉内温度分布不均匀,熔池平静时,各部位的钢
使钢水加热到大于1600℃;同时温度容易调整和控制,
可满足冶炼不同钢种的要求;炉内气氛可以控制,既可 造成氧化性气氛,又可造成还原性气氛,因此,具有很
强的去除钢中有害杂质磷、硫的能力,同时还有很强的
脱氧能力,故钢中非金属夹杂物含量相对较低,合金元 素收得率也相对较高,钢的成分容易控制,适于冶炼各
种合金钢及优质钢;可用100%的废钢进行熔炼。
三、熔化期
传统冶炼工艺的熔化期占整个冶炼时间的 50%~70%,电耗占70%~80%。因此熔化期的长短影 响生产率和电耗,熔化期的操作影响氧化期、还原 期的顺利与否。 (1)熔化期的主要任务 • 将块状的固体炉料快速熔化,并加热到氧化温度;
• 提前造渣,早期去磷,减少钢液吸气与挥发。 (2)熔化期的操作 合理供电,及时吹氧,提前造渣。
炉壁及水冷炉盖,效果都非常好。它能最大限度地用水冷件
取代耐火材料,水冷件用得多,耐火材料费用节约就愈多。 为了安全,水冷件仅用于那些在熔融、精炼和出钢时不与钢
水接触的部位。
自20世纪90年代中期以来,我国由于进行产业结构的优 化与调整,淘汰了大量落后的小电炉(1994年我国小电炉有 1403座,2000年仅有179座),一批现代电炉迅速投产、达产、 超产,我国电炉炼钢工作者在消化引进国外先进技术的基础 上自主创新,在开发具有中国特色的现代电炉炼钢技术方面 取得了长足的进步,电炉水冷件也得到了很好的应用。
水温度相差较大,尤其大炉子更为突出。
§4.1 电弧炉及其主要设备
炉体是电炉的最主要装置,用来熔化
炉料和进行各种冶金反应。电弧炉的炉体
由金属构件和耐火材料砌成的炉衬两部分
组成、炉体的金属构件又包括炉壳、炉门、
出钢槽(现代电炉多数已无出钢槽而采用
偏心炉底出钢)、炉顶圈和电极密封圈等
组成。
炼钢电弧炉的基本结构
在工业发达国家,由于废钢量较大,电炉炼钢已
从20世纪中的主要生产特殊钢过渡到生产全钢种,甚
至以生产普通碳素钢为主。在最近一、二十年间,随 着二次精炼技术的下断发展和完善,电炉冶炼由原来 的三期演变成仅作为熔化设备,并与二次精炼和连铸 技术配套形成自动化水平高、功率高、能耗低的专业
化生产系统,从而增强了电炉生产工艺的竞争能力。
• 熔末升温期
电弧开始暴露给炉壁至炉料全部熔化为熔末 升温期。 此阶段因炉壁暴露,尤其是炉壁热点区的暴 露受到电弧的强烈辐射。 应注意保护炉壁,即提前造好泡沫渣进行埋 弧操作,否则应采取低电压、大电流供电。 各阶段熔化与供电情况见下表。 典型的供电曲线如下图。
炉料熔化过程与操作
熔化过程 点弧期 穿井期 主熔化期 电极位置 送电 → d极 d极→ 炉底 炉底 → 电弧 暴露 必要 条件 保护 炉顶 保护 炉底 快速 熔化 办 较低电压 较低电流 较大电压 较大电流 最高电压 最大电流 法 炉顶布 轻废钢 石灰垫底
2)补炉部位
炉衬各部位的工作条件不同,损坏情况也不一 样。炉衬损坏的主要部位如下: 炉壁渣线 受到高温电弧的辐射,渣、钢的化 学侵蚀与机械冲刷,以及吹氧操作等损坏严重; 渣线热点区 尤其2#热点区还受到电弧功率大、 偏弧等影响侵蚀严重,该点的损坏程度常常成为 换炉的依据; 出钢口附近 因受渣钢的冲刷也极易减薄; 炉门两侧 常受急冷急热的作用、流渣的冲刷 及操作与工具的碰撞等损坏也比较严重。
的1/200,通常厚度约回12~30mm,炉身做成圆筒
形可减少散热面积及热损失。
典型的炉壳及炉底结构形状如图所示
。
(a)平底形;(b)截锥形;(c)球形
1-圆筒形炉身;2-炉壳底;3-加强筋
二 炉门
炉门包括炉门盖、炉门框、炉门坎和炉门升降机构
等部分。对炉门的要求是:结构严密,升降简便灵活,