APQP程序
APQP程序

1、目的
提前策划产品和过程质量控制,有效预防缺陷,减少变差和浪费,及时、高效、优质地提供满足顾客要求的产品。
2、适用范围
适用于新产品(包括产品变更)的过程设计和开发过程控制。
过程负责:研发部
3、术语和定义
质量策划:致力于制定质量目标并规定必要运行过程和相关资源以实现质量目标。
特殊特性:可能影响产品的安全性或法规的符合性、配合、功能、性能或其后续过程的产品特性或生产过程参数。
APQP:产品质量先期策划与控制计划PPAP:生产件批准程序
PFMEA:过程潜在失效模式及后果分析SPC:统计过程控制
MSA :测量系统分析CFT: 横向职能小组
4、工作程序。
APQP产品先期质量策划和控制计划五大阶段实施过程

〇
变质、组合或分解
移动物体使改变位置的活动
检查或化验物体在数量上或质量 □ 上是否合乎标准
下一活动不能连续进行所发生的
D
停留与等待
有计划有目的的储存 ▽
两种活动同时发生
产品先期质量策划 APQP
产品设计和开发
Product Design and Development
计划 计划批准
样品和试制
试生产
PROCESS STEP
PROCESS HANDLE
INSPECTION DELAY
STORE
V
.005
.01
.01 .33
.008
TIME (hours)
NV
144
DISTMAONVCEEDTRANQSUFEARNCTorrIeTctYioOnverprodMuTacttli.oYMnvmMPto. tioEn SWaitO ing FInvenW toryPrAocesSsingTE
国际 标准 ISO - 9000
确定 国际 要求
顾客 要求 Q S- 90 00 生 产 件 批 核 程 序 (PPAP) 公司 特殊要 求
确定 顾客 要求
客户 参考手 册
质量手册
笫 1阶 确定 方法及 职责
- APQP - FME A
程序文件
笫 2阶
- MSA
确定 谁, 什么, 何时 - SPC
工作指导书
-
周转时间
-
开发时间
-
服务
-
保修期
产品先期质量策划 APQP
计划和确定阶段
Plan and Define Program
计划 计划批准
样品和试制
APQP流程图及详解

2、工装包括注塑模具、治夹具、检具;新设备包含各种成型机器、加工设备等; 3、技术部做成《模具制作明细表》、《治夹具、检具制作表》及《新设备需求清单》等;
《设计信息检查清单》
《采购技术条件》
《模具制作明细表》 《治夹具、检具制作表》
进
行开发并申请采购。
1、针对材料清单,技术部主导与物供部一起确认材料分包商,编写《初选分包商名录》;
2、选择的分包商,必须具备程序文件规定的资格; 3、针对新材料的供应商可能需要在产品试产后,经确认合格才可以确认。
《初选分包商名录》
1、技术部负责编写新产品生产的《初始过程流程图》; 2、《初始过程流程图》要求能够明确表达出产品生产的整个工作流程与加工工艺。
开 发 计 划
技 术 部
A P Q P
计 划 的 编 写
技 术 部
产 品
书
责 任
部
技 术
1、当《产品开发建议书》完成后,营销部应根据相关程序,召集各部相关人员对新产品
进行项目可行性研究;
相关部门 2、可行性研究主要对以下几点进行研讨:1)市场分析;2)生产工艺;3)产量与产能;
4)模具、工装与设备;5)场地与设施;6)时间节点;7)财务经济;8)市场风险
APQP 工作流程图
第一阶段:确定目标及计划
项目前期准备工作
APQP计划编写
产品建议书 可行性研究
合同评审 项目开发立项 ★新产品开发计划
产
初
初
选
始
初 始 零
品
分ห้องสมุดไป่ตู้
过
件
责
APQP流程

源于第二阶段的输 出
Input
生产平衡分析
生产平衡分析表
车间平面图编 特性矩阵图编
车间平面布置图
车间平面布置图检 查表
特性矩征阵图
PFMEA分析
PFMEA
5
6
Process
5
6
Output
项目小组 工程部
Owner
评审
PFMEA检查表
工程部
项目小组对过程流程图各工序的工时进行估算,并确定各工序人员数量,计算平均 工时,加上一定的宽放率后计算出生产效率及班产量。
工程图样及工程规范设计/编制后项目小组应组织评审,评审结果应进行记录。
Activity
产品设计开发部门负责产品可制造性和装配设计的确认。应从设计、概念、功能等 对制造变差敏感度,制造和/或装配过程,尺寸公差,性能要求,部件数,过程调整,材料 搬运等方面进行确认。
项目小组应确保制定样件控制计划并对其进行检查,以便对样件制造过程中的尺寸 测量和材料与功能试验进行准确详尽的描述。
新产品开发申请/
审批
成立跨功能小组 编制APQP计划
产品开发小组成员 新产品APQP开发计
Owner
研发中心主管 工程部主管
研发中 心主管根据 新产品开发 设计Input 信息确定新 产品开发来 源。
Activity
研发中心主管组织进行新产品制造可行性分析,并将分析结果填入《新产品制造可 行性分析报告》中。
项目小组应在第二阶段的产品质量先期策划结束时对第二阶段的工作执行情况进行总 结,并通过其表明已满足所有的策划要求和/或关注的问题均已写入文件中,并列入解 决的目标中来体现管理者的支持。
制造过 程设计输入 的评审工作 由项目小组 进行。
APQP 程序

6.2.2.8可靠性和质量目标
ENG与QA确定并完成生产该产品所需测试的可靠性项目
及确定总体质量目标﹑各工序的质量控制目标.
6.2.2.9初始材料清单
ENG确定生产该产品的所需原材料﹑辅料等清单
(包括早期分供方名单)
6.2.2.10初始流程图
ENG确定需要制作样板的工艺流程方案(包括初始材料清单)
6.2.3.5工程图样
ENG充分研究/理解/评审工程图样,以协助确定产品的特殊特性,
并反映到样件控制计划.
6.2.3.6工程规范
ENG在评定规范或补充的规范的基础上,对样件控制计划中(如
有关检测项目)的合理性进行评审.
6.2.3.7材料规范
ENG和QA确定生产该产品所需的合理的材料质量要求.
6.2.3.8图样和规范的更改
ENG对该中如有图样和规范更改,应及时传达及执行.包括对
客户的更改.并以书面文件通知有关部门,并注明推行时间.
6.2.3.9新设备﹑工具和设施
ENG确定该产品生产时是否需增加新设备﹑工具和设施,若需
要,对它进行具体规定﹑并按APQP手册A-3《新设备﹑工装
和试验装备检查清单》进行评估.
6.2.3.10特殊产品和过程特性
6.2.1概念提出/策划
6.2.1.1成立策划小组
根据产品的性质,对某一类产品(必要时可以为某单一产品)
成立策划小组,小组成员为经理/主管或工程师级别人员.
6.2.1.2小组的责任
制订及完成产品质量先期策划进度和表中规定的相关事项.
6.2.1.3各代表的作用
根据产品特性确定小组每位成员作用.
6.2.1.4确定客户需要
APQP控制程序

APQP控制程序制定项目开发计划工程部根据业务部提供的资料,成立多功能小组,制定项目开发计划。
计划包括项目开发周期、开发流程、各阶段的任务和责任分工等内容。
5.2设计与开发5.2.1设计评审多功能小组按照项目开发计划,进行设计评审。
评审内容包括图纸规范、特殊特性、制造工艺可行性等方面。
评审结果将作为后续工作的基础。
5.2.2制定检验规范和测量方案___根据设计评审结果,制定检验规范和测量方案。
同时,制定MSA分析计划和初始过程能力分析计划。
5.2.3试制制造部负责试制产品。
试制过程中,需对制造工艺进行可行性评估和工模设计方案进行评估。
同时,制造部还需提出设备采购申请。
5.3验证5.3.1验证样品评审多功能小组对试制的产品进行验证样品评审。
评审结果将作为后续工作的基础。
5.3.2MSA和初始过程能力分析的实施___根据制定的MSA分析计划和初始过程能力分析计划,进行MSA和初始过程能力分析的实施和确认。
5.4生产准备5.4.1设备采购和加工/气密检测夹具设计工程部负责设备采购和加工/气密检测夹具的设计。
同时,制定相关作业指导书和加工工艺的编制。
5.4.2人员培训工程部负责人员培训,确保生产准备工作的顺利进行。
5.5生产运作生产运作阶段,各部门需按照工作计划和责任分工,确保产品的顺利生产。
同时,___需进行测量和检验,确保产品质量符合要求。
6.0文件控制本程序由工程部制定并负责文件的修订和控制。
修订时,需经过制订审核和核准。
同时,需对文件进行版本控制和变更记录。
5.2.1 项目启动后,工程部将按照《模治具制造管理程序》的要求,负责完成相关模具的生产制作工作。
5.2.2 品质部将根据项目进度要求,及时完成量具和测试夹具的制作或购买。
5.2.3 样品试制和确认阶段,工程部将根据项目进度要求制作样品,并依据《样品制作及模具试用作业指导书》完成新样品相关的检测确认。
5.3 过程的设计和开发阶段,为了保证开发出一个有效的制造系统,必须进行过程设计和开发。
APQP管理程序PPT课件
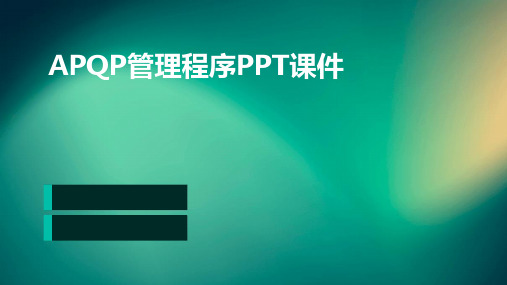
contents
目录
• APQP概述 • APQP管理程序的核心要素 • APQP管理程序的实施步骤 • APQP管理程序的效益与挑战 • APQP管理程序的应用案例
01 APQP概述
APQP的定义与重要性
定义
APQP(Advanced Product Quality Planning)是一种先进的产品质量策 划方法,旨在确保产品在设计和开发 阶段就达到高质量标准。
跟踪项目进度,确保项 目按计划进行,及时调
整计划以应对变化。
评估项目风险
识别项目潜在的风险, 制定应对措施,降低风
险对项目的影响。
设计与开发
01
02
03
04
需求分析
明确产品或过程的需求,分析 用户期望和竞争对手表现。
设计概念
根据需求分析,提出设计概念 ,确定产品的主要特性和功能
。
设计评估
对设计进行评估和优化,确保 设计满足要求,提高产品的可
供应商改进
与供应商合作,提高供应商的 质量和交货能力,降低采购成
本。
制造与装配
工艺流程设计
根据产品设计,制定制造工艺流程,确保生 产过程的顺畅。
制造与装配
按照工艺流程进行制造与装配,确保产品质 量和生产效率。
生产准备
准备生产所需的设备、工具、材料等资源, 确保生产线的正常运行。
生产监控与改进
监控生产过程的质量和效率,及时调整工艺 参数,提高生产线的性能。
竞争力。
案例三
总结词
机械制造行业是传统制造业的重要组成 部分,APQP管理程序的应用能够帮助机 械制造企业提高产品质量和生产效率, 降低生产成本。
VS
APQP程序

公司組成APQP小組準備產品實現策劃,其內容包括特殊特性的界定,FMEA的開發與評審,控制計劃的開發與評審等.
5.1.11此階段完成後由APQP小組共同擬訂出整個<<APQP推行計劃表>>,以利後續各階段之推行。
5.2第二階段:產品設計和開發
5.2.1工程部依據相關客戶資訊和本公司產品設計或開發過程,製作<,設計失效模式及後果分析>>,並針對其進行評估,製作<<設計FMEA檢查表>>.
5.2.5 PIE課相關人員依據產品製造或生產等具體現狀,於<<原型控制計劃>>中提出保證產品製造、生產、檢驗等相關過程之要求,以便將任何關注問題、變異及成本等影響傳達於客戶。並針對控制計劃內容或要求部分作出相應之評估或記錄,製作<<控制計劃檢查表>>
5.2.6 PIE相關人員依據圖面或要求進行樣品製作,在製作前必須對產品之製作加以評估,如有新設備、工裝和試驗設施等要求,必須提前提出新設備工裝設施,並即時加以備查、跟蹤,製作<<新設備工裝和試驗設備檢查表>>。PIE相關人員並針對產品圖面之製造或生產等要求規劃<<特殊特性符號表>>及產品和過程特殊特性。且由品保部負責提供<<量具試驗設備要求一覽表>>。
▲5.1.8在設計開發策劃階段,應參考先期產品品質策劃和控制計劃的手冊,進行開發,同時使用Delphi AQE/SQE推荐的表格或流程圖來報告APQP狀態,特定的SPDP包括了先期產品策劃的主要工作,其具體詳細資料見Delphi特殊要求.
▲5.1.9顧客指定的特殊特性
當客戶有指定特殊特性標識符號時,公司統一按客戶指定的特殊特性標識符號用於控制計劃/圖紙/FMEA文件中,若客戶對特殊特性符號沒有任何要求,則公司依實際運作貫用的符號標注特殊特性.
- 1、下载文档前请自行甄别文档内容的完整性,平台不提供额外的编辑、内容补充、找答案等附加服务。
- 2、"仅部分预览"的文档,不可在线预览部分如存在完整性等问题,可反馈申请退款(可完整预览的文档不适用该条件!)。
- 3、如文档侵犯您的权益,请联系客服反馈,我们会尽快为您处理(人工客服工作时间:9:00-18:30)。
客户服务部:客户签订试制协议
财务管理部:产品报价表
项目小组组长组织各个成员:APQP权责表
技术开发部:产品目标、特殊特性明细表
质量保证部:质量目标、量具/试验设备要求
生产制造部:初始材料/外协/外购件清单、产能分析、初始过程流程图
行政办公室:培训计划
7.4.6初始过程能力研究按《过程能力研究规定》执行。
7.4.7小批试生产的产品由生产制造部办理入库手续,小组组长提交顾客进行小批量认可,必要时由项目小组组长委派相关人员前往顾客处协商具体事宜。
7.4.8在过程和产品确认后,由生产制造部对设施、设备和过程策划的有效性(工厂的布局,材料流转的合理性、场地空间的增值使用、总体的工作规划和是否适当的考虑到:适当的自动化、人机工程与人的因素、操作者与生产线的平衡等)评价按“设施、设备和过程策划有效性检查清单”进行评价。必要时在清单中提出整改措施,规定负责人,并由小组组长进行跟踪验证。
7.3.3.8完成上述工作后由项目小组组长就里程碑C/D进行检查,完成“里程碑C/D检查表”。
7.4产品和过程确认阶段
7.4.1项目小组按首次样品的生产结果进行改进,当适合时,按实际情况增加所需内容
7.4.2本阶段项目小组在组长的组织下完成下列工作:
技术图纸/工程规范的认可
生产制造部:分承包方确定
技术开发部:作业指导书/检验指导书更新(有更改时)
制定部门
编号
主题
先期产品质量规划程序(APQP)
项次
1
本程序确定产品开发全过程的各个步骤,促进与所涉及的每个职能部门的联系,保证开发进程;今早发现所需更改,确保产品使顾客满意。
本程序适用于本公司所有新产品开发和顾客工程更改后须按本程序规定重新送样的产品
3.1《过程能力研究规定》
3.2《文件和资料控制程序》
技术开发部:D/PFMEA更新(有更改时)
质量保证部:产品/过程质量体系评审清单
7.4.3完成上述工作后由项目小组组长就里程碑E进行检查,完成“里程碑E检查表”,在检查的结果符合后,项目小组继续完成下列事项:
质量保证部:测量系统分析计划/测量系统分析
制订部门
主题
先期产品质量规划程序(APQP)
项次
技术开发部:过程能力研究计划
附录02.1.18“里程碑G检查表”
附录02.1.19“质量策划有效性检查表”
附录02.1.20“批量生产大检查清单”
附录02.1.21“批量生产的重新认可检查清单”
附录02.1.22“设施、设备和过程策划有效性检查清单“
OTC:工装样件
PVS:小批生产件
SOP:批量生产件
5.1项目小组负责产品先期策划,包括现有质量体系和顾客要求的差距分析;制定开发目标及跟踪,如成品率、工序能力、循环时间、开发进度、开发成本等;编制APQP实施计划并负责检查实施情况。
5.2项目小组组长应充分代表公司的行动,保证公司的利益,组长协调个部门在项目开发全过程中任务的分配和质量、进度的控制。在管理者支持和足够资源配备的条件下,对项目的成败负主要责任。
附录02.1.1“项目策划权责表”
附录02.1.2“小组可行性承诺”
附录02.1.3“新设备、工装和试验装置检查清单”
附录02.1.4“产品/过程质量审核检查单”
附录02.1.5“场地平面布置图检查清单”
附录02.1.6“过程流程图检查清单”
附录02.1.7“过程FMEA检查清单”
附录02.1.8“控制计划检查清单”
生产制造部:新设备、工装和设施要求
小组组长组织各个成员:新产品开发费用预算
项目小组:小组可行性承诺
7.2.8在完成上述事项后由项目小组组长就里程碑B进行检查,完成“里程碑B检查表”。
7.3生产过程的策划和验证阶段
7.3.1在本阶段项目在项目组长的组织下完成下述工作:
技术开发部:产品图样、工程及材料规范转换及评审
技术开发部:试生产控制计划
生产制造部:试生产计划
技术开发部:试生产
技术开发部:初始过程能力研究
生产制造部:设备能力研究
项目小组组长/客户服务部:生产件确认和小批量认可
技术开发部:包装评估
7.4.4完成上述工作后由项目小组组长就里程碑F进行检查,完成“里程碑F检查表”。
7.4.5测量系统分析按《测量系统分析工作程序》执行。
7.6持续改进
7.6.1产品正式投产后技术开发部负责工序能力研究、工艺技术改进及相关技术资料的更改
7.6.2技术开发部负责当发生顾客工程规范更改时的产品图及相关标准的更改。7.6.3客户服务部负责顾客及内部质量问题的分析处理。
7.6.4重大改进项目按《持续改进控制程序》进行。
7.7项目策划形成的文件和资料按《文件和资料控制程序》进行控制。
7.3.3.3生产制造部门办理样件入库手续,客户服务部提交顾客,技术开发部跟踪样件试装过程。
7.3.3.4项目小组组长根据顾客反馈意见决定是否进行再提交。
7.3.3.5过程潜在失效模式及后果分析和控制计划的编制按最新版本的《FMEA潜在的失效模式及后果分析》、《产品质量先期策划及控制计划》手册进行。
7.3.3.6产品图、过程流程图、工艺规程、原材料验收标准等技术文件的编写要求、格式更改见《文件和资料控制程序》。
7.3.3.7在过程、设施、设备和工装策划过程中,采用相应的错误预防技术,防错的采用由技术开发部提出,填写“防错采用审批表”,经小组审批后实施,对已经实施的防错技术由技术开发部将其归纳成“防错采用一览表”。
完成上述事项后由项目小组组长及里程碑G进行检查,完成“里程碑G检查表”
7.5.2在此期间出现任何工程规范更改及生产过程的变动等,由项目小组重新提交,直至认可。
7.5.3在生产件获得批准后,如果顾客要求进行两日试生产,则由生产制造部组长实施。
7.5.4批量生产获得通过后,由客户服务部与客户签订供货合同。
3.3《FEMA应用规定》
3.4《持续改进控制程序》
3.5《测量系统分析工作程序》
3.6《特殊特性管理规定》
3.7VDA4.3《批量投产前的质量保证》
3.8《产品质量先期策划及控制计划》参考手册
APQP:产品质量先期策划
FMEA:潜在的失效模式及后果分析
PFMEA:过程潜在的失效模式及后果分析
R&R:测量系统的重复性和再现性
7.4.9在量产后三个月,由过程审核及质量小组活动进行评价。
7.5生产阶段
7.5.1项目小组根据顾客对试生产确认的结果进行修改,完善以下内容:
生产控制计划/控制计划检查清单
技术文件更新
过程流程图的更新
PFMEA更新
工艺规程更新
工艺装备明细表
生产作业指导书
检验和试验作业指导书
原材料工艺定额
质量策划实施有效性检查/质量策划有效性检查表
技术开发部、生产制造部:工装设计/制造/新设备、工装和实验、装置检查清单
技术开发部、质量保证部:检具设计及顾客认定
技术开发部:控制计划(样件)
质量保证部:OTS实验大纲
生产制造部:样件制作
技术开发部:作业指导书
质量保证部:检验指导书
生产制造部:样品试制计划
生产制造部:样件检验和试验
技术开发部、客户服务部:样件认可
5.3项目小组成员在组长的领导下,互相配合,共同完成项目开发任务。在工作中与本部门经理广泛交流意见并统一认识,以代表本部职能。
5.4项目小组负责产品开发费用预算和开发过程成本监控。
5.5行政办公室负责安全性培训和与开发项目有关的技术培训。
5.6项目小组及各部门的具体职责在成立项目小组时明确。
5.7在项目策划的各个里程碑点由项目小组组长组织小组成员进行检查。
周转时间
开发时间
服务和竞争对手比较
项目小组在《产品建议书》和优劣势分析的基础就如何解决问题由谁去实施和实现的可行性共同完成《产品责任书》。
7.2.5项目小组应采用同步技术,加快开发进程,确保进度符合顾客要求,编制APQP实施计划,经项目小组组长批准后发布,使计划在受控状态下实施。
7.2.6在项目确定后由项目小组组长就里程碑A进行检查,完成“里程碑A检查表”。
附录02.1.9“防错采用审批表”
附录02.1.10“防错采用一览表”
附录02.1.11“产品建议书”
附录02.1.12“产品责任书”
附录02.1.13“里程碑A检查表”
附录02.1.14“里程碑B检查表”
附录02.1.15“里程碑C/D检查表”
附录02.1.16“里程碑E检查表”
附录02.1.17“里程碑F检查表”
7.2.2.1总经理任命小组组长
7.2.2.2项目小组成员应来自以下部门:技术开发部、生产制造部、行政办公室、质量保证部、客户服务部,必要时,可有分承包方或顾客代表参加。
7.2.3项目小组组长召开项目小组全体成员会议,安排新产品开发任务。
7.2.4项目小组根据客户服务部与顾客联系索取的技术资料,标准和样件、图纸等相关信息,识别顾客要求,由项目小组组长组织人员完成《产品建议书》,同时为保证公司具有长期的竞争能力,项目小组采用多方认证的方法就一下各个方面进行优势/劣势分析。
项次
A.对于停产6个月相应订单的生产
B.对于由于过程失控造成的重大质量事故或在正常工艺下连续3个月不良品率上升。
7.5.6.2批量生产的重新认可,由技术开发部负责组织技术部、质保部、生产部按《批量生产重新认可清单》所需内容进行审核,完全符合后,填写《批量生产重新认可清单》,方可生产。
7.5.7整个项目策划完成后由项目小组组长组织人员对本次过程开发的经验数据和结果进行总结,并加以分析和汇总成可供以后进行过程策划参考的文件。