英文版IE知识培训
精选英文版IE知识培训

Maximum range: 5th to 95th percentile (adjustable design)
2002/9/26
15
Assembly Line Balancing
Equalize workload among the assemblies. Identify the bottleneck operation. Establish the speed of the assembly line. Determine the number of work stations. Determine the labor cost of assembly. Establish the percent workload of each
- eg. Change adjustments of the chair for those sit for a long time.
10. Maintain a comfortable environment
- eg. Consider the quantity and quality of light at the workstation.
Examples
Design aims
Examples of Design examples: measurements to
consider:
Users that the design should accommodate:
Easy reach
Shelving
Arm length, shoulder height
2002/9/26
2
Objectives
IE培训内容课件

4.分析一搬步骤
IE 教育
现象分析
原因分析
改善案导出
成果计算
1.稼动分析(运转分析) 1)工程单位构成表 2)W/S观测表 3)W/S观测统计 4)W/S分析表2.作业分析 —所有要素作业的时间分析表3.编程分析 —现况的Line Layout作成4.工程分析 —部品加工分析 --部品供给方式5.执行分析 —现在管理指数 (回收率\人时当生产量)
1. 作业分析概论2. 联合作业分析—连续观测法
第五章 作业分析
IE 教育
5.作业分析
1 作业分类(按精密度)
□ 对作业详细分解,发现平时感觉不到的很小的Loss □ 定量的了解事实,掌握现在的方法-□ 改善要素作业□ 改善作业所必需的JIG(夹具),加工条件,部品精密度等
Line
作业说明
作 业
主作业
主体作业
附属作
NO
日期 :
观测者
非作业
作业余量
管理余量
疲劳余量
个人余量
无作业
组装 部品的组装
焊接 人工焊接
固定 螺母,螺栓的固定
连接 连接电线,捆
--> -->-->-->-->
利用5W 1H的改善想法
4 改善原则的应用
5 要素作业分析表
IE 教育
5.作业分析
IE 教育
5.作业分析
二 要素作业的分析方法----连续观测法
观测记录和整理方法
观测时应先起动秒表开始
应连续观测作业的重复
读取的时间记录到观测用纸的摾奂茡栏中.
观测结束后整理时在表中记录 各要素作业的时间
>
工程
单位作业
>
IE基础知识培训内部培训
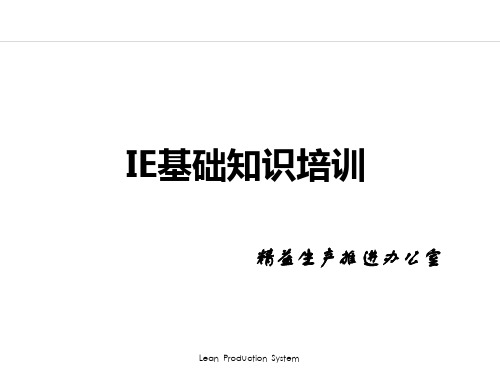
减少零件的件数 使位置的决定单纯化 自动化,加工方式
规格的统一 传票的统一 作业标准的订定
收集配送时间定时化
有盖车、无盖车、家畜 车、冷冻车 设备及模等的专业化 职务的专门化(装配、 搬运、检查……)
10
◇以人为中心的意识:人起主导作用;人参与的积极性,成员的创造
性;
任何事情;归根揭底都是通过人来最终实现的,人是根本 ,人是资本,人是成本; 要想使事情完成的更成功,就要减少 人的失误,而人的失误是由人的变异性造成的,这种变异性 有两种,即随机变异和系统变异,从而失误也分为随机失误 和系统失误两种。
作业测定 决定时间标准
制定工作标准
2024/1/13
训练操作工人
Lean Production System
程序分析 操作分析 动作分析
工艺程序图 流程程序图 布置与经路分析
人机操作分析 联合作业分析 双手操作分析
动作要素分析 动作经济原则
运用上述分析技术,实现 工作方法、程序、环境、 条件的最佳化,为制定工 作标准打下基础,也为时 间研究作好准备。
2024/1/13
Lean Production System
效果 作业的排除 作业的简化
制程,步骤的变更 (结合) (交换)
作业的简化
合理化
21
5WHY
WHYWHY为什么-为什么分析;也被称作5个为什么分析,它是用来识别和说明因 果关系链,它的根源会引起恰当地定义问题;
不断提问为什么前一个事件会发生,直到回答没有好的理由或直到一个新的故障模 式被发现时才停止提问。解释根本原因以防止问题重演。文件中所有带有“为什么” 的语句都会定义真正的根源通常需要至少5个“为什么”,但5个why不是说一定就是 5个,可能是1个,也可能是10个都没有抓到根源。
精选IE基础知识培训课件

经济分析
工艺改进
成本降低
生产流程
现有各系统
设施改进
产品标准化
信息系统
质量控制
系统组织
库存计划
安全系统
员工业绩
工作方法
员工培训
卫生系统
制定评价指标及规程
创新激励(管理创新体制创新技术创新)
……
……
……
……
7、IE在我国的发展状况
我国工业工程产生的社会背景与美日等国家有相当大的历史落差 80年代初,引进、学习、模仿国外的工业工程经验 1989年,中国机械工程学会工业工程分会成立并举办第一次全国工业工程学术会议;至今已举办八次全国会议。联络了1000多名工业工程学者 和专家,3000多个企业应用工业工程成绩斐然 国内实施工业工程的成功案例 长春一汽变速箱厂降低流动资金70%,提高劳动生产率0%二汽车桥厂转向节生产线产量提高29.8%,废品率下降68%,设备故障率下降84%上海大众一线劳动生产率接近德国同行水平科龙冰箱供应系统一次性降低流动资金3000万元邯钢1994~1996年38个IE项目累计创利1.66亿元
人员
是否遵守作业标准?
工作技能足够吗、全面吗?
工作干劲高不高?
作业条件、作业环境如何?
材料
材料品质状况如何?
材料库存数量是否合适?
材料存放、搬运方式好不好?
材料成本如何,能否更便宜?
方法
作业标准内容是否合适?
作业前后的准备工作是否经济高效?
前后工序的衔接好吗?
作业安全性如何?
使用问题检查表,
逐条对照找出问
题点。
4.查找问题的方法
运用统计数据、报告分析,找出问题点。
5.查找问题的方法
精选IE基础和IE手法培训lrj

1.研究雙手的動作,以求其互相平衡.2.顯現出伸手找尋,以及笨拙而無效的動作.3.發現工具、物料、設備等不合適的位置.4.改善工作布置.5.協助操作技術的訓練.
雙手法的運用
意義:利用抽樣原理,以推測人或物之作業真象,以利進行分析改善.應用範圍:1.辦公室人員工作時間所占之百分率.2.機器設備之維修百分率或停機百分率.3.現場操作人員從事有生產性工作之百分率.4.決定標準工時之寬放時間百分率.5.用以決定工作之標準工時.6.商店顧客類別或消費金額或光顧時刻次數等之分配比例資料.7.其他可應用抽樣調查以收集資料的場合.
提高生產力和效益降低成本保證質量和安全獲取多方面的綜合效益.
IE的目標 :
以前 ………… 管理者 (傳統式)現在 ………… 現場人員未來 ………… 全體人員 (豐田式)
IE的責任 :
1.工業心理 : 訓練、人體工學.2.作業研究:方法研究、產品評價、作業衡量、組織學.3.計劃及控製:要徑分析、作業研究、品質管製.4.物料搬運:自動運輸、包裝.
2. 動 改 法
1.兩手同時開始及完成動作.2.除休息時間外,兩手不應同時空開.3.兩臂之動作應反向同時對稱.4.盡可能以最低級動作工作.5.物體之“動量”盡可能利用之.6.連續曲線運動較方向突變直線運動為佳.7.彈道式運動較快.
動 作 經 濟 原 則
8.動作宜輕松有節奏.9.工具物料應置於固定處所.10.工具物料應裝置應依工作順序排列並置於近處.11.利用重力喂料,愈近愈佳.12.利用重力墜送.13.適當之照明.
3. 流 程 法
加工:給原料、材料、零件、製品形狀,性質變化的過程.運搬:給原料、材料、零件、製品位置變化的過程.貯藏:依照計劃貯藏原料,材料及零件.滯留:表示原料、材料、零件、製品違反計劃滯留的狀態.數量檢查:測出原料、材料、零件、製品量,或者個數,把結果跟基準作比較,以測知差異的結果.品質檢查:試驗原料、材料、零件、製品的品質特性,把其結果跟基準比較,藉此判斷製品單位合格與否,或者個品優良與否的過程.
IE七大手法培训

*持续的进步是企业及个人长久生存的根基.
*改善就是进步的原动力,没有改善就没有进步.—学如逆水行舟,不进则退.
*改善是永无止境的,必须长久持续去进行 IE的主要范围?
* 工程分析*价值分析(V.A)*动作研究*工作标准 *时间研究*时间标准*工厂布置*运搬设计 为甚么要有改善(IE)七大手法? *以不教而战,谓之杀. *徒然要求改善而不讲求方法、技巧,于事无补. *给人一条鱼吃,不如教他捕鱼的技术. *要求捕更多的鱼,首先必须讲求捕鱼技术的传授与使用. *改善七大手法(IE 7 TOOLS)就是协助我们改善我们工作的技术..
泰勒以鐵鍬研究與吉爾布雷斯對砌牆動作的研
究等事例,發現了科學的管理方法:
不依賴直覺,而以扎實的資料作根據;
以科學方法分析,提高生產性.
IE简介
IE的ቤተ መጻሕፍቲ ባይዱ的?
应用科学及社会学的知识,以合理化、舒适化的途径来改善我们工作的质量及效率以达到提高生产力增进 公司之利润进而使公司能长期的生存发展下去,个人的前途也有寄托之所在.因此,简单地说,IE的目的就 是充分利用工厂的人力、设备、材料,以最经济有效的工作方法,使企业独得最大的效益.
三.分析:應用最合适的技術,嚴格而有系統的分析已記錄的事實.
分析時依動作的优先順序進行. A.准備動作,做動作前的動作都是准備動作. B.做的動作,程序中對工作目的最有价值,最有貢獻的動作. C.拿開動作,做的動作后之放下,移開清理動作.
IE七大手法 —流程法(4)
四.建立:在分析中所獲得的意見,發展成為最使用.經濟而有效的新方法.
IE七大手法 —防错法(3)
5.应用原理 1>. 断根原理: 将会造成错误的原因从根本上排除掉,使绝不发生错误. 2>. 保险原理: 采用二个以上的动作必需共同或依序执行才能完成工作. 3>. 自动原理: 以各种光学、电学、力学、机构学、化学等原理来限制某些动作的执行 或不执行,以避免错误之发生.目前这些自动开关非常普遍,非常简易的“自动化”之应 用. 4>. 相符原理: 藉用检核是否相符合的动作,来防止错误的发生. 5>. 顺序原理: 避免工作之顺序或流程前后倒置,可依编号顺序排列,可以减少或避免错 误的发生. 6>. 隔离原理: 藉分隔不同区域的方式,来达到保护某些地区,使不能造成危险或错误的 现象发生.隔离原理亦称保护原理. 7>. 复制原理: 同一件工作,如需做二次以上,最好采用“复制”方式来达成,省时又不 错误. 8>. 层别原理: 为避免将不同工作做错,而设法加以区别出来.
IE基础知识教程--Bobby

Prepared by:郭凤坡 Date: 2011.02.18
目 录 IE基础知识识记 一,IE基础知识识记
定义,特点, 定义,特点,作用
二,IE活动的展开方式 IE活动的展开方式 IE相关知识体系 三,IE相关知识体系 IE七大手法 四,IE七大手法 IE七种浪费 五,IE七种浪费 六,写在后面
浪费: 浪费:附加在商品上的 无价值的人类劳动。 无价值的人类劳动。
对生产制程无益的 单元操作。 单元操作。
等待(停滞)的浪费 等待(停滞)的浪费: 生产线品种切换。 每天工作量变动大,当工作量变小时,无事可做。 常因机器设备缺料而停工待料。 常因前工序延误,导致下工序无事可做。 机器设备时常发生故障。 生产线不平衡。 存在劳逸不匀现象。 生产计划异常,切换频繁。 搬运的浪费: 搬运的浪费: 搬运是一种不产生附加价值的劳动,搬运的损失分 为放置,堆积,移动,整列等动作浪费。物品移动所需 要的空间浪费。包括:时间的耗费;人力,工具的占用; 搬运的物损等。
步骤: 步骤: 1.课题的选择 课题的选择 2.现状的把握 现状的把握 3.发现重点并分析 发现重点并分析 4.实施改善 实施改善 5.确认效果 确认效果 6.水平推广并标准化 水平推广并标准化
重点
a.专案目标确定 专案目标确定 b. Cell切割 切割 c.借助管理工具 借助管理工具 d.修正,纠偏 修正, 修正 e.数据,效果图等 数据, 数据 f.执行力度 执行力度
IE的特点 的特点
1.IE是以工程技术为基础,配合科学管理的技巧来发现 问题/解决问题/预防问题; 2.IE最终目的是经由管理的运作,使企业能获得最大 的利益,故与成本或经济效 益有关,包括制度、作 业方法、机器、工具、流程均应予掌握并加以改善; 3.IE是一门应用科学,其操作理论均要能符合实际的 需要,是故IE专案参与人员均应具备身体力行的能 力,而使理论与实务相得益彰 理论与实务相得益彰,保证改善效果; 理论与实务相得益彰 4.IE是运用重点管理的技巧,在所面临的问题上做重 点突破。
IE培训教材1

IE培训教材1一.IE(Industrial Engineering)工業工程如何將人力,材料,資金,機器,廠房有效組合,達到效率高,品質穩定,交期準,浪費少,成本低的目的,彌補管理及工程技術脫節,在這里就需要IE.1.IE是以工程技術為基礎,配合科學管理的技巧來預防問題,發現問題,解決問題.2.美國對IE協會(AIIE) IE定義:IE是在工學之中以設計,改善設定來綜合人﹑材料﹑設備等系統的綜合,應用數學﹑自然科學﹑社會科學等知識來明示﹑預測﹑評價該系統,以求得到更高生產力的專門技術.IE在日本也稱為(生產技術)或者(管理工學).二.IE的工作職責1.生產方法改善1)排除〝浪費﹑勉強﹑不均衡〞的生產方法或者流程,生產方法的簡化或者省略.2)更新生產裝備与生產工具﹑工廠布置﹑物料搬運等,如:a.要紧生產設備的布置符合工藝要求,使手工操作盡量減少工人的行走距離,還要符合安全生產与節約生產面積的要求;b.工作地上的各类物品都應有適當的固定的存放點,通常應放在看得見﹑夠得著的地方,符合工人操作順序便於工人使用与拿放;c.工具﹑用具應盡量布置在工人正常的與最大的工作區域內,使工人能以最短的距離,最少的時間与最小的體力消耗進行操作;d.物品放置高度,工作椅与工作臺的高度都要適合操作工人身軀的特點,使工人操作時或者拿放物品的時候盡量不彎腰,不蹬腳,不轉身,使工人避免不安定的作業姿態.2. 流程作業改善1) 產品生產作業流程上改善,要紧用四個動作來表示(加工﹑搬運﹑檢驗﹑停滯) 如:2) 產品排程流程改善;3. 動作研究 就是說對於一個作業者使用兩眼﹑兩手﹑兩腳﹑的動作加以細分,並進行分析研究,把〝不必要〞的動作〝去除〞,把〝必要〞的動作變為〝有效率〞,人不易〝疲勞〞的最經濟性動作.如:4.工時研究在時間上對這個作業進行研究,進而改善作業与標準工時制訂,如:一道工序用第一种方法來做要10秒,而用第二种方法來做只要8秒,那從工時來研究就用第二种方法.5.量產﹑試產導入就是工程課所研制出來的新機种,導入試產﹑量產的時候 ,誰來解決一些工藝﹑結構及怎麼來操作的一些問題,也能够說是IE 工程師現場技術指導工作.6. (工藝性) 品質不良改善(自動流水線) 改善前: 改善后:如:組合上﹑下蓋.當組合好上﹑下蓋后,發現縫大或者變形等不良現象,這种不良就是工藝性不良,這就要IE對這個結構工藝進行分析,是作業者組裝方法不對,設計不良,還是里面有電子元件或者其它膠柱頂住等.7.安全作業改善要紧改善機器設備﹑電氣設備﹑勞動條件,預防与消除工傷事故,中毒与職業病等安全作業;包含安全的工廠,安全的管理,安全的機器,安全的工作行為.三.現階段在公司的要紧工作範圍1.作來流程的制作與分析.作業流程:從投入零件原材料到產品入庫出貨的一個產品工作流程,它有固定的格式,用來作為生產線排程依據.要紧方法是: a.以產品材料﹑零件﹑產品复雜度來分析与制作作業流程;b.以作業者﹑設備﹑工具等來分析与制作作業流程;c.用〝加工(操作)〞﹑〝搬運〞﹑〝檢查〞﹑〝停滯〞四大動作對作業流程進行細分.2.制訂標準工時與時間研究.1) 標準時間a.標準工時定義:在特定的工作環境下,熟練操作者用規定作業方法(標準作業方法)与設備以正常速度完成規定的一個單位工作量(工序)所需時間.b.標準工時作用:○1.作業方法比較選擇; ○2.工廠布置的依據; ○3.計算工廠產能;○4.決定人工成本; ○5.作為人員增減依據; ○6.流水線生產平衡評估;○7.生產計劃基礎; ○8.效率分析的基礎.c.標準時間制訂:標準工時=正常時間+寬放時間或者=正常時間*(1+寬放率)寬放率=(寬放時間/作業時間)*100%d.標準時間計算:正常時間:實際所測N次時間平均數,通常用馬表測定實際時間,計算方法:1〝分〞=0.01分=0.6秒寬放率通常為實際所測總時間的18%~22%2).時間研究按所測時間對作業方法進行改善,如把作業工序合並﹑分割﹑重排﹑簡化等.3.編寫作業指導書(動作分析)1).經過了動作分析,工藝性分析,作業者的操作程度等用文字的方式將準備工作﹑操作方法﹑注意事項﹑工程規格詳細描述出來的一种技術性文件,它具有作業者操作的指導性﹑技術資料的储存性﹑作為操作方法改進的依據性,還具有判斷對錯的權威性;2).編寫作業指導書的要紧依據是動作分析与作業分析,以人為中心根據工廠現有的設備﹑工具﹑及產品的复雜度對怎樣才能用最簡單的方法,最能提高工作效率的方式來偏寫作業指導書.3).作業指導書要紧內容:準備工作﹑操作方法﹑注意事項﹑工程產品規格﹑簡單操作圖示﹑所用材料﹑工具﹑設備等.4.所耗工時﹑人力及成本分析1).要紧是從標準工時上來分析所耗工時﹑人力及計算出它的定額產能,並比較實際產能﹑工時﹑人力來發現問題与提高生產效率的一种方式;2).工作內容:在工時﹑人力上進行分析,如8秒可做好的方法就不用10秒才做好的方法,1人可做的工序就不用二人來做等;並且評估分析所耗總工時﹑總人力与總產能与成本.5.試產﹑量產現場指導工作1).因為流程是IE排的,作業指導書是IE寫的,標準工時表也是IE按在制樣時實際所測出來,那麼試產﹑量產的時候當然要IE來具體指導工作,到底該怎麼來做;2).工作內容:要紧包含指導操作方法﹑提出重點注意事項﹑排生產流程的改善﹑記錄﹑解決生產線出現的問題,根據實際情況對作業改善,觀察操作者作業方法是否準確等.6.量產導入生產線平衡分析1).定義:指工程流動間或者工序流動間時間差距最小,流動順暢,減少因時間差所造成等待或者滯留現象;使生產線流動順暢達到最佳狀態的一种分析.2).目的:物流快速﹑減少生產周期﹑減少或者消除物料或者半成品周轉場所,消除工作〝瓶頸〞,提高作業效率,穩定產品品質,提升工作士氣,改善作業秩序.3).平衡分析的步驟:a.準備流程圖b.準備工時表c. 測算工序實際作業時間DM (Decimal Minute)並記錄,1DM=0.01分=0.6秒d.清點各工序﹑作業人數並記錄,1人的實質時間/人數=每人分配時間;e.計算不平衡損失不平衡損失=(最高的DM*合計人數)-各工序時間的合計f. 計算生產平衡率(有兩方法):第1种:生產平衡率=各工序實質時間/(最高的DM*合計人數)*100%第2种:(最大值-最小值)/平均值*100%g.計算平衡損失率;平衡損失率=1-生產平衡率h.假如是自動流水生產線,則應計算生產線節拍來分析工序時間是否超出節拍,節拍=實際工作時間/實際生產量i.計算定額產能:[一天八小時工作時間(秒)]*人數/(最高DM*0.6秒)=平均每人每天產能4).生產線平衡改善方法:假如平衡損失率高,實際產能與定額產能相差遠,生產線工序實測時間超過節拍時間等該怎樣來改善.通常有兩种情況:a.耗時最長工序(工序瓶頸)的作業時間的改善;○1.作業分割:將此作業的一部分工作分割到工時較短的工序來作業;○2.利用与改善工具﹑治具;○3.提高作業者本身技能及操作方法.○4.調換較熟練作業者;○5.增加作業者(最后考慮這個方法);○6.簡化复雜動作.b.工序時間短的作業時間之改善;○1.取消這個工序分到其它作來工序上;○2.合並兩道時間都較短的工序;○3.重排作業流程与動作;5).對生產線平衡改善注意事項:a.盡量不用增人的方法;b.對材料﹑零部件﹑設計方法進行分析是否可縮短工時;c.對生產線補進的新手,防止因生產線不平衡而對新手造成過大的工作壓力,注意操作技術培訓与工作安排.7.有關工藝性不良的產品分析:提出相關對策与對策實施,如:NPA3000502K PCBA板短芯線容易斷,線材印字脫落,線材印字模糊,端子下陷等這些工藝不良就是IE所要分析的工作,它要紧應用的方法:1).5W 1H即Why(為什麼) What(什麼原因) Where(在什麼地方出現) When(什麼時候最高)Who(由誰來做) How(該怎樣處理)2)4MMachine(設備) Man(人) Method(方法) Material(材料)通常流程:把握現狀原因分析改善對策對策實施效果確認﹑鞏固8.制作樣品參與工程在制作客戶樣品時候,IE參與制作樣品的工作,要紧目的是熟悉產品結構复雜度与考慮假如大量生產的話,生產線該怎樣來做,在此之間,標準工時,作業流程,作業指導書,生產品質重點及注意事項等資料要擬寫出來.四.IE的工作目的与信念1.IE的工作目的:廣議地說就是將工廠投入的人力﹑物料﹑設備以達到效率高,品質穩定,交期準,浪費少,成本低的目的,簡單地說就是使生產線達到最佳的平衡狀態來提高生產效率,降低不良率的目的.2.IE的工作信念:減少浪費.1).浪費要紧包含:不良改正的浪費,制造過多的浪費,加工過剩的浪費,搬運的浪費,庫存量過多的浪費,等待的浪費,動作浪費等.動作的浪費又包含:兩手空閑的浪費,單手空閑的浪費,作業動作停止浪費,作業動作太大的浪費,拿的動作交替的浪費,步行的浪費,轉身角度太大的浪費,重复動作的浪費,不熟悉作業技巧的浪費等.2).減少浪費對策﹑方法a.將物品進行整理﹑整頓並標識清晰來創造看得見浪費現場;b.一定要按標準作業指導書,其它設備操作規程及圖示來作業;c.應用動作分析(前面已講到)与動作經濟原則,所謂動作經濟原則就是使操作者在操作的時候感到輕鬆自然与動作距離剛好,兩手可同時使用等.五.IE常用手法:1.流程分析法;2.動作分析法;3.動作經濟原則;4.工時研究法;5.工作抽查法;6.人機配置法;7.工作簡化法.通過IE的七個手法,對怎樣來生產產品而達到最佳狀態,當然IE的工作是不斷地改進与整頓,以上有的沒詳細說明這里不再解釋.六.通過以上對IE的工作職責,工作內容等的介紹已初步熟悉IE,那麼怎樣來配合IE展開工作呢?第一.IE的工作目的与所有工廠人員目的一致,應相互熟悉,互相協助;第二.IE的工作與工廠其他部門的工作相輔相成,做到〝你建議我,我建議你〞的方式;第三.各人有各人的責任,IE也一樣,敬請大家須按標準作業指導書,作業流程及所示圖紙來作業;第四.任何有關IE所負責的機种出現了工藝性問題,請先以文件的方式會知或者口頭告知IE,如IE不解決或者解決不了或者沒有任何簽复的情況下再會知到你的經理或者IE課長,當然能够同以知會到你的經理或者IE課長;第五.假如IE在作業流程上安排不當或者根本沒法作業的情況且IE不在現場時,請及時通知IE進行調整与指導作業,包含作業指導書部分;第六.假如生產線很不平衡,出現了嚴重堆積及等待加工的情況,且IE不在現場時務必叫IE進行處理以免影響產能;第七.記住IE的職責:IE有責任去進行生產方式改善,流程作業改善,作業方法改善,進行量產﹑試產的導入,作業時間研究,工藝性不良的改善与安全作業的改善等.。
- 1、下载文档前请自行甄别文档内容的完整性,平台不提供额外的编辑、内容补充、找答案等附加服务。
- 2、"仅部分预览"的文档,不可在线预览部分如存在完整性等问题,可反馈申请退款(可完整预览的文档不适用该条件!)。
- 3、如文档侵犯您的权益,请联系客服反馈,我们会尽快为您处理(人工客服工作时间:9:00-18:30)。
n eg. Clicking is easier than memorizing commands.
12. Reduce stress
- eg. Design task to fit people.
2002/9/26
SMT Training for Productivity
11
Anthropometry
Definition
Measurement of the human body and its biomechanical characteristics.
Biomechanical refers to the mechanical (machine-like) capabilities of the human skeleton-muscular systems.
2002/9/26
SMT Training for Productivity
4
Twelve Principles of Ergonomics
1. Work in neutral postures
n eg. Wrist rests for keyboard and mouse.
2. Reduce excessive forces
10. Maintain a comfortable environment
- eg. Consider the quantity and quality of light at the workstation.
2002/9/26
SMT Training for Productivity
10
Ergonomics Principles
- eg. Boxes with handholds for carrying.
2002/9/26
SMT Training for Productivity
5
Ergonomics Principles
3. Keep everything in easy reach
- eg. Keep materials within the “reach envelope” of the arm.
Industrial Engineering : Work Design
Prepared by Ken Leung
2002/9/26
Hale Waihona Puke SMT Training for Productivity
1
Work Design
Methods Improvement
Ergonomics Assembly line balancing Principles of motion economy Various type of charts
2002/9/26
SMT Training for Productivity
9
Ergonomics Principles
9. Move, exercise, and stretch
- eg. Change adjustments of the chair for those sit for a long time.
2002/9/26
SMT Training for Productivity
7
Ergonomics Principles
5. Reduce excessive motions
n eg. Use power screwdriver.
6. Minimize static load
- eg. Use a pencil grip.
2002/9/26
SMT Training for Productivity
3
Objectives
To enhance the work effectiveness and efficiency.
Increased convenience of use Reduced errors Increased productivity
To enhance human values.
Improved safety Reduced fatigue and stress Increased comfort Greater user acceptance Increased job satisfaction Improved quality of life
2002/9/26
SMT Training for Productivity
6
Ergonomics Principles
4. Work at proper heights
- eg. Heavy work should be performed lower than elbow height; precision work should be higher.
Work measurement
Time study Activity sampling
2002/9/26
SMT Training for Productivity
2
Ergonomics
Definition
Apply information about human behavior, abilities, limitations, and other characteristics to the design of tools, machines, system, tasks, jobs, and environments for productive, safe, comfortable, and effective human use.
Measures our sizes and how we move and move easily.
2002/9/26
SMT Training for Productivity
8
Ergonomics Principles
7. Minimize pressure points
n eg. Provide padding for hand grips.
8. Provide clearance
- eg. Provide visual access (carton delivery).