如何做好生产作业排程.pptx
合集下载
第八章 生产作业排序PPT课件

j 1
j=1,…,m
8
Ci----工件i的完成时间, 在工件都已到达的情况下, Ci= Pi+ Wi
Fi----工件i的流程时间,在工件都已到达的情况下, Fi= Pi+ Wi Li----工件i的延迟时间, Li= Ci- di , Li<=0 按期或完成提前;
Li>0 延迟 Ti----工件i的延误, Ti=max{0, Li} Ei----工件i提前完成的时间
例如,考虑32项任务(工件),有32!2.61035种方案,假定计 算机每秒钟可以检查1 billion个顺序, 全部检验完毕需要8.41015个 世纪.
如果只有16个工件, 同样按每秒钟可以检查1 billion个顺序计算, 也需要2/3年.
以上问题还没有考虑其他的约束条件, 如机器、人力资源、厂房 场地等,如果加上这些约束条件,所需要的时间就无法想象了。
12
• 根据工件到达系统的情况 静态排序 动态排序
• 根据要实现的目标 单目标排序 多目标排序
13
1.3.5 排序问题的表示方法
排序问题常用四个符号来描述: n/m/A/B
其中, n-----工件数; m-----机器数; A----车间类型, F=流水型排序 P=流水型同顺序排序 G=一般类型,即单件型排序 B-----目标函数
•
平均延误时间: 1
T
1 n
n
Ti
i1
最大延误时间:Tmax max{Ti}
• 2)以工件的完工时间和工件的流程时间为目标函数
• 最长完工时间:Cmaxmax{Ci} 最长流程时间:Fmax max{Fi}
•
平均完工时间:
C
1 n
n
最新文档-生产作业计划与作业排序-PPT精品文档

订货点法(安全库存法):根据库存在制品下降 到订货点的时间来确定零件投产时间的一种方法。
应用场合:应用于短期的需求变化不定,但较长 时期内确有需求,定期重复生产的场合。用来安 排需求量大的标准件和通用件的生产
(三)车间生产作业计划编制
主要包括车间生产作业计划日程安排、工段 (班、组)生产作业计划的编制、工段(班、组) 内部生产作业计划的编制等。
占用量
流水线内 (车间内) 占用量
流水线间 (库存)在 制品占用
量
工艺占 运输占 周转占 保险占 周转占 运输占 保险占
用量
用量
用量
用量
用量
用量
用量
(二)厂级生产作业计划编制 1、计划单位的选择 2、各车间生产任务的分配方法 ①在制品定额法(连锁计算法)——适用于流水生
产或大量大批生产企业。 公式:某车间出产量 = 后车间投入量+该车间
(二)生产作业计划的目标 1、保证生产计划任务能够按质、按量、按期、按品
种完成。 2、尽可能实现均衡生产,建立良好的生产秩序,提
高效率。
二、大量大批生产作业计划
(一) 大量大批生产作业计划 1、节拍 节拍是流水线上相邻两件相同制品投产或出产的时 间间隔,它表明了流水线生产速度的快慢或生产效率的 高低。是大量流水生产期量标准中最基本的标准。 流水线节拍的计算公式:R=F/N 其中:R—流水线的节拍(分/件),F—计划期内有 效工作时间(分),N—计划期的产品产量(件)。
移动方式:
① 顺序移动方式:一批制品在前道工序上全部完工之后,才能整批地从前 道工序流转到后道工序上继续加工。
优点:有利于安排生产作业计划和在制品的管理
缺点:生产周期长,在制品数量大
怎样做好生产作业排程

评估人员能力:评估 员工技能和生产能力
评估物料供应:评估 物料库存和供应能力
评估生产环境:评估 生产环境和安全条件
评估生产成本:评估 生产成本和利润空间
制定排程计划
确定生产目标:明确生产任务、产量、质量等要求 收集生产信息:了解生产设备、原材料、人力资源等状况 制定排程方案:根据生产信息制定合理的排程计划 优化排程方案:根据实际情况对排程方案进行调整和优化 实施排程计划:按照排程计划进行生产作业,确保生产顺利进行
生产调度:根据生产计划进行 生产调度,包括生产任务分配、
生产进度监控等
信息化管理:利用计算机技 术进行生产作业排程的管理
生产监控:对生产过程进行监 控,包括生产进度、生产质量、
生产成本等
生产作业排程的未来发展趋势
智能化:利用AI技术进行生产排程 优化,提高生产效率
柔性化:适应市场需求变化,快速 调整生产计划和排程
优先级策略
紧急程度:根据任 务的紧急程度进行 排序
重要程度:根据任 务的重要程度进行 排序
资源分配:根据资 源的分配情况进行 排序
时间限制:根据任 务的时间限制进行 排序
负荷平衡策略
目的:确保生产线的负荷平衡,避免过度负荷或闲置 方法:根据订单数量、生产周期、设备能力等因素,合理安排生产任务 优势:提高生产效率,减少浪费,降低成本 注意事项:需要实时监控生产线的负荷情况,及时调整生产计划
生产作业排程
目录
生产作业排程的基本概念 生产作业排程的流程 生产作业排程的策略 生产作业排程的优化方法 生产作业排程的实践应用
生产作业排程的定义
生产作业排程是指在生产过程中,根据生产计划、物料供应、设备状况等因素,合理 安排生产作业的顺序和时间,以实现生产效率最大化。
生产作业计划(课件)ppt课件

5
ppt精选版
三、生产作业计划工作的容
1、制定或修改期量标准 期量标准是指为了合理的组织企业生产活
动,在生产产品或零件的数量和期限方面所规 定的标准数据。
2、编制生产作业计划
根据生产计划的要求,具体地规定做什 么、谁去做、什么时间做等问题。通过生产作 业计划的编制,把生产计划变成实施计划的行 动。
27
ppt精选版
二、生产作业控制流程
28
ppt精选版
三、生产作业控制的内容
1、产品投入控制 (1)生产作业计划的复查与调整
① 各车间、工段和班组的生产任务在品种、 数量、时间上是否衔接和平衡。
② 编制的生产作业计划,其计时单位是否一 致;计算方法是否正确;数据结果是否准确。
③所采用的期量标准是否先进合理。 (2)生产作业准备工作 (3)投产指令的下达
2
ppt精选版
二、编制生产作业计划的目的
1、落实生产计划任务 生产作业计划把全年生产计划任务从
时间上细分到月、日、小时;从空间上细 分到车间、班组、个人;从计划单位上把 产品分解成总成、部件、零件,这就更有 利于按生产作业计划来组织和指挥日常生 产活动,保证生产计划任务全面完成。
3
ppt精选版
2、促进管理水平提高
30
ppt精选版
31
ppt精选版
3、在制品控制
(1)车间在制品控制
(2)库存在制品控制
① 要严格执行收、发、储存、保管制 度和卡片台账报表管理制度。
② 应建立毛坯、在制品成套性检查制 度和储备定额检查制度。
③ 要建立和健全仓库管理工作制度, 提高在制品保管工作质量,对在制品采用 现代化管理方法和手段进行管理和控制。
生产和运作管理(生产作业排序)资料公开课获奖课件省赛课一等奖课件

(3)单班次问题旳解析法 (Brownell and Lowerre,1976)
求解下列问题旳单班次人员安排问题: 1、确保每人每七天休息两天 2、确保每人每七天连休两天 3、确保每人每七天休息两天 ,隔一周在周末休息 4、确保每人每七天连休两天,隔一周在周末休息
1、确保每人每七天休息两天
■设某单位每七天工作7天,每天一班,日常日需要N人,周 末需要n人。 W表达所需劳动力下限。
2023/12/10
以上这些规则各有其特点,不同旳规则合用于不同旳 目旳。例如,FCFS规则比较公平;SPT规则可使平均流 程时间最短,从而降低在制品数量;EDD规则可使工件旳 最大延迟时间最小、平均延误时间最小;Moore法则可使 延迟旳工件数至少等。
2023/12/10
FCFS、SPT、EDD优先规则旳应用
第六章 生产作业排序
2023/12/10
一、作业排序旳概念 作业排序就是拟定工件在设备上旳加工顺序,
使预定旳目旳得以实现旳过程。 二、作业排序旳目旳
1、总流程时间最短 流程时间=加工时间+等待时间+运送时间
2、平均流程时间最短 3、平均在制品占用量最小 4、最大延迟时间最短 5、平均延迟时间最短 6、延迟工件至少
仪器
Y1 Y2 Y3 Y4 Y5
工序1 工序2
12 4 22 5
5 15 10 3 16 8
Y2-Y1--Y4--Y5-Y3
作业排序成果旳图示:
04
16
31 41 46
机器空闲
工序1 Y2 Y1
Y4 Y5 Y3
工序2
Y2
Y1
Y4 Y5 Y3
0 4 9 16
38
54 62 65
第7讲 生产作业计划与排序PPT课件

பைடு நூலகம்
Yuan fuli,Management School of Wuhan University of Technology
11
第7讲 生产作业计划与排序
第1版
连续流水线工作指示图表
表7-1 连续流水线工作与间断时间交替程序图
流水线 的内容
装配过程
加工过程
小 1 23 4
时 5678
每班时间安排(分)
间断 间断 工作 次数 时间 时间
2
每次 10分钟
460
3
每次 10分钟
450
6
每次 10分钟
420
4
每次 10分钟
440
25.07.2020
Yuan fuli,Management School of Wuhan University of Technology
12
第7讲 生产作业计划与排序
第1版
m a x (5 -6 )
4.3件
te
tL
85 .6
4.3件
2.3件
0
60
80
112 120
第5道工序与第6道工序间流动在制品占用量变化示意图
25.07.2020
Yuan fuli,Management School of Wuhan University of Technology
19
第7讲 生产作业计划与排序
4
第7讲 生产作业计划与排序
第1版
7.1 生产作业计划
生产作业计划(scheduling)——在生产运 作计划系统中属于执行层面的操作计划, 它以综合生产计划、主生产计划及物料需 求计划为依据,对每个生产单位(车间、 工段、班组等),在每个具体的时期(月、 旬、班、小时等)内的生产任务作出详细 规定,使生产计划得到落实。
Yuan fuli,Management School of Wuhan University of Technology
11
第7讲 生产作业计划与排序
第1版
连续流水线工作指示图表
表7-1 连续流水线工作与间断时间交替程序图
流水线 的内容
装配过程
加工过程
小 1 23 4
时 5678
每班时间安排(分)
间断 间断 工作 次数 时间 时间
2
每次 10分钟
460
3
每次 10分钟
450
6
每次 10分钟
420
4
每次 10分钟
440
25.07.2020
Yuan fuli,Management School of Wuhan University of Technology
12
第7讲 生产作业计划与排序
第1版
m a x (5 -6 )
4.3件
te
tL
85 .6
4.3件
2.3件
0
60
80
112 120
第5道工序与第6道工序间流动在制品占用量变化示意图
25.07.2020
Yuan fuli,Management School of Wuhan University of Technology
19
第7讲 生产作业计划与排序
4
第7讲 生产作业计划与排序
第1版
7.1 生产作业计划
生产作业计划(scheduling)——在生产运 作计划系统中属于执行层面的操作计划, 它以综合生产计划、主生产计划及物料需 求计划为依据,对每个生产单位(车间、 工段、班组等),在每个具体的时期(月、 旬、班、小时等)内的生产任务作出详细 规定,使生产计划得到落实。
生产计划与作业排程管理.pptx

生產計畫與管理 Chapter 7 作業排程
6
作業排程的特徵與限制
製造現場生產結構(Shop Structure) 評估準則(Performance Criteria) 產品結構(Product Structure)
工作中心之產能(Work Center Capacities)
生產計畫與管理 Chapter 7 作業排程
最早交期法則(EDD) 最大延誤(遲)時間最小化。交期越早者排越前面,但是此 法會有增加延遲工件數目和增加平均延遲時間的傾向。
生產計H畫與o管dg理soCnha法pter則7 作業最排程小化延遲工件數目。
11
最短作業時間(SPT)法則— 最小化平均流程時間( Fs )
當n個作業要排至單一機台上時,利用SPT (Shortest Process Time) 法則排序可使得平均 流程時間最小化,也就是 t1 t2 tn 。
表 7.7 流程時間計算表
工作 i 4 1 8 7 3 2 5 6
流程時間 ti 3 3+4 3+4+5 3+4+5+6 3+4+5+6+7 3+4+5+6+7+8 3+4+5+6+7+8+10 3+4+5+6+7+8+10+12
生產計畫與管理 Chapter 7 作業排程
14
範例 7.1 3/3
1 n
n
i1
Fi ,s
平均延誤時間(Average
lateness):Ls
1 n
n
i1
排程与车间作业计划PPT课件( 45页)
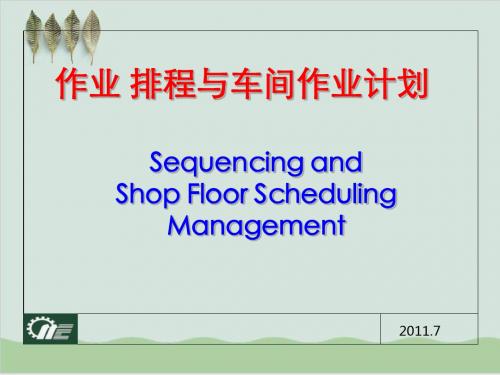
N个作业两台工作中心排序
2011.7
在多个工件分派到多个工作地的最简单的问题是“ n 到 n”分派 。对这个问题, 可以使用指派法。
指派法是线性规划中运输方法的一个特例。其目的是极小化极 大化某些效率指标。
指派方法很适合解决具有如下特征的问题:
A. 有n个“事项”要分配到n个“目的地”;
B. 每个事项必须被派给一个而且是唯一的目的地;
车间作业排序和计划的关系
2011.7
派工单(dispatch list)或称调度单,是一种面向工作中 心说明加工优先级的文件,说明工作中心在一周或一个时期内 要完成的生产任务。
说明哪些工作已经达到,应当什么时间开始加工,什么时 间完成,计划加工时数是多少,完成后又应传给哪道工序。
说明哪些工件即将达到,什么时间到,从哪里来。
5 RAN(随机排序) 主管或操作工通常随意选择一件他们喜欢的进行加
工。 6 LCFS(后到优先):该规则经常作为缺省规则
使用。因为后来的工单放在先来的上面,操作人 员通常是先加工上面的工单。
作业排序的优先规则
2011.7
“n个作业——单台工作中心的问题”或“n/1”,理论上,排序 问题的难度随着工作中心数量的增加而增大,而不是随着作业数 量的增加而增大,对n的约束是其必须是确定 的有限的数
车间作业排序的目标
2011.7
1 FCFS(先到优先):按订单送到的先后顺序进行加工.
2 SOT(最短作业时间优先):这个规则等同于 SPT(最短加工时间)规则。
3 Ddate(交货期优先):最早交货期最早加工。
作业排序的优先规则
2011.7
4. STR(剩余时间最短优先):
剩余时间是指交货期前所剩余时间减去加工时间所得的差值。
- 1、下载文档前请自行甄别文档内容的完整性,平台不提供额外的编辑、内容补充、找答案等附加服务。
- 2、"仅部分预览"的文档,不可在线预览部分如存在完整性等问题,可反馈申请退款(可完整预览的文档不适用该条件!)。
- 3、如文档侵犯您的权益,请联系客服反馈,我们会尽快为您处理(人工客服工作时间:9:00-18:30)。
0+1=1 1+6=7 7+2=9 9+4=13 13+3=16
9
0+6=6
7
6+2=8
5
8+3=11
2
11+1=12
6
12+4=16
剩餘寬裕時間 (STR; slack time remaining)
工作
STR排 程 E A B D C
流 程 時 間 合 計 = 43天 平 均 流 程 時 間 = 8 .6 天 平 均 延 誤 = 3 .2 天
•分配訂單、設備和人員至工作中心
–短期的產能規劃
•決定訂單執行的順序 •派工 (dispatching)
–啟動排程工作之執行
•現場管制
–控制訂單之進度 –已延誤與緊急訂單之跟催
電腦
等候之訂單
領班
生產控制
等候之訂單
工作站排程的目的
•滿足交期 •使前置時間最小化 •使設置時間或設置成本最小化 •使在製品庫存最小化 •使設備利用率最大化
A
3
5
B
4
6
C
2
7
D
6
9
E
1
2
流程時間 (天)
0+3=3 3+4=7 7+2=9 9+6=15 15+1=16
流程時間合計=3+7+9+15+16=50天 平均流程時間=50/5=10天 僅有工作A將能準時交貨 工作B、C、D、E則將分別延誤1、2、6、14天, 平均一項工作將延誤(0+1+2+6+14)/5=4.6天
作業排程
測試生產部 蘇德柏
作業排程
•建立執行作業、使用資源或分配設備 的時間表
•訂單加工流程 (Job Shop)
–每件訂單依功能需求,被指派至各工作站 進行加工作業
–當一件作業抵達工作站時,即加入工作站 的等候線內,等待被加工
–排程
•決定作業被加工的順序,及指派作業至機器
排程的產能考量
•無限負荷(Infinite Loading)
處理天數 (天)
1 3 4 6 2
交期 (從 現 在 起 之 天 數 )
2 5 6 9 7
流程時間 (天)
0+1=1 1+3=4 4+4=8 8+6=14 14+2=16
法則
FC FS SO T D D a te LC FS R andom STR
流程時間合計 (天)
50 36 39 46 53 43
工作依到達之順序
A B C D E
處理時間 (天)
3 4 2 6 1
交期 (從現在起之天數)
5 6 7 9 2
所有的訂單都需要使用僅有的彩色影印機, Morales必須決定這五個訂單的處理順序, 評估準則是使流程時間最小化
FCFS法則導出下列之流程時間:
工作
處理天數
交期
(天)
(從 現 在 起 之 天 數 )
使用DDATE (交期) 法則,則排程之結果是:
工作
處理天數
交期
流程時間
(天)
(從 現 在 起 之 天 數 )
(天)
E
1
2
0+1=1
A
3
5
1+3=4
B
4
6
4+4=8
C
2
7
8+2=10
D
6
9
10+ 6= 16
流程時間合計=1+4+8+10+16=39天 平均流程時間=39/5=7.8天 工作B、C、D之交期將延誤 平均一項工作將延誤(0+0+2+3+7)/5=2.4天
工作
LCFS排程 E D C B A
流程時間合計=46天 平均流程時間=9.2天 平均延誤=4.0天
RANDOM排程 D C A E B
流程時間合計=53天 平均流程時間=10.6天 平均延誤=5.4天
處理天數 (天)
1 6 2 4 3
6 2 3 1 4
交期 (從現在起之天數)
2 9 7 6 5
流程時間 (天)
• 步驟
– 列示每項工作在兩台機器上之作業時間 – 選擇最短之作業時間 – 如果最短之作業時間是在第一台機器上作業
,則優先處理該工作;如果最短之作業時間 是在第二台機器上作業,則最後處理該工作 – 對所有剩餘之工作重覆步驟2和3
例16.2 4項工作在雙機之作業
步驟1:表列作業時間
工作
在 機 器 # 1上 之 作 業 時 間
平均流程時間 (天)
10 7 .2 7 .8 9 .2 1 0 .6 8 .6
平均延誤 (天)
4 .6 2 .4 2 .4 4 .0 5 .4 3 .2
2機對n項作業之排程
• n/2流程工作站 • 作業必須以相同的順序經過2部機器 • Johnson法則 • 讓第一項工作的開始至最後一項工作
的結束為止之間的流程時間最小化
考慮SOT法則。給予加工時間最短之訂單第一優先處理, 導出之流程時間:
工作
處理天數(天)
交 期 (從 現 在 起 之 天 數 )
流程時間(天)
E
1
2
0+1=1
C
2
7
1+2=3
A
3
5
3+3=6
B
4
6
6+4=10
D
6
9
10+ 6= 16
流程時間合計=1+3+6+10+16=36天 平均流程時間=36/5=7.2天 只有工作E和C在交期前完成,工作A僅遲了一天 平均工作延誤(0+0+1+4+7)/5=2.4天
–工作指派時至工作站時
•只考慮作業的需求 •不考慮工作站是否有足夠的產能
•有限負荷(Finite Loading)
–工作指派時至工作站時
•考慮作業的需求 •加工機器的設置時間與加工時間
•正向排程 (Forward Scheduling)
–接到訂單後 –向前排定各項作業的完成時間 –可得知各作業的最早完成時刻
A
3
B
6
C
5
D
7
在 機 器 # 2上 之 作 業 時 間 2 8 6 4
•反向排程 (Backward Scheduling)
–以未來的某特定日期(可能是交期) –開始反向往前排定各作業的時間 –可得知最晚開始時刻
•MRP系統是物料無限負荷、反向排程
•機器導向排程
–機器是最重要的資源,故排定機器的時間
•人員導向排程
–人員是最重要的資源,故排定人員的時間
常用的排程與控制功能
–保持所有設備忙碌,並不是最有效之流程 管理
工作排序
•排序(sequencing) •優先排序 (priority sequencing)
–決定工作在機器或工作站上執行的優先程 序
•排定工作順序的法則
–依據一種資料
•加工時間、交期、或訂單到達順序
–經運算取得某種指標數字
•最小閒置時間法則Fra bibliotek排程績效的衡量標準
•滿足客戶交期或下游生產的需求 •使流程時間最小化 •使在製品最小化 •使機器與工作人員之閒置時間最小化
排程法則與技術
單機對n項工作之排程
例16.1 n項工作在單機上作業 Mike Morales是法律影印快遞公司的主管, 這家公司為洛杉磯市中心區的 法律事務所提供影印服務, 有五個客戶在本週的剛開始時, 提出他們的訂單,排程資料詳列於下:
9
0+6=6
7
6+2=8
5
8+3=11
2
11+1=12
6
12+4=16
剩餘寬裕時間 (STR; slack time remaining)
工作
STR排 程 E A B D C
流 程 時 間 合 計 = 43天 平 均 流 程 時 間 = 8 .6 天 平 均 延 誤 = 3 .2 天
•分配訂單、設備和人員至工作中心
–短期的產能規劃
•決定訂單執行的順序 •派工 (dispatching)
–啟動排程工作之執行
•現場管制
–控制訂單之進度 –已延誤與緊急訂單之跟催
電腦
等候之訂單
領班
生產控制
等候之訂單
工作站排程的目的
•滿足交期 •使前置時間最小化 •使設置時間或設置成本最小化 •使在製品庫存最小化 •使設備利用率最大化
A
3
5
B
4
6
C
2
7
D
6
9
E
1
2
流程時間 (天)
0+3=3 3+4=7 7+2=9 9+6=15 15+1=16
流程時間合計=3+7+9+15+16=50天 平均流程時間=50/5=10天 僅有工作A將能準時交貨 工作B、C、D、E則將分別延誤1、2、6、14天, 平均一項工作將延誤(0+1+2+6+14)/5=4.6天
作業排程
測試生產部 蘇德柏
作業排程
•建立執行作業、使用資源或分配設備 的時間表
•訂單加工流程 (Job Shop)
–每件訂單依功能需求,被指派至各工作站 進行加工作業
–當一件作業抵達工作站時,即加入工作站 的等候線內,等待被加工
–排程
•決定作業被加工的順序,及指派作業至機器
排程的產能考量
•無限負荷(Infinite Loading)
處理天數 (天)
1 3 4 6 2
交期 (從 現 在 起 之 天 數 )
2 5 6 9 7
流程時間 (天)
0+1=1 1+3=4 4+4=8 8+6=14 14+2=16
法則
FC FS SO T D D a te LC FS R andom STR
流程時間合計 (天)
50 36 39 46 53 43
工作依到達之順序
A B C D E
處理時間 (天)
3 4 2 6 1
交期 (從現在起之天數)
5 6 7 9 2
所有的訂單都需要使用僅有的彩色影印機, Morales必須決定這五個訂單的處理順序, 評估準則是使流程時間最小化
FCFS法則導出下列之流程時間:
工作
處理天數
交期
(天)
(從 現 在 起 之 天 數 )
使用DDATE (交期) 法則,則排程之結果是:
工作
處理天數
交期
流程時間
(天)
(從 現 在 起 之 天 數 )
(天)
E
1
2
0+1=1
A
3
5
1+3=4
B
4
6
4+4=8
C
2
7
8+2=10
D
6
9
10+ 6= 16
流程時間合計=1+4+8+10+16=39天 平均流程時間=39/5=7.8天 工作B、C、D之交期將延誤 平均一項工作將延誤(0+0+2+3+7)/5=2.4天
工作
LCFS排程 E D C B A
流程時間合計=46天 平均流程時間=9.2天 平均延誤=4.0天
RANDOM排程 D C A E B
流程時間合計=53天 平均流程時間=10.6天 平均延誤=5.4天
處理天數 (天)
1 6 2 4 3
6 2 3 1 4
交期 (從現在起之天數)
2 9 7 6 5
流程時間 (天)
• 步驟
– 列示每項工作在兩台機器上之作業時間 – 選擇最短之作業時間 – 如果最短之作業時間是在第一台機器上作業
,則優先處理該工作;如果最短之作業時間 是在第二台機器上作業,則最後處理該工作 – 對所有剩餘之工作重覆步驟2和3
例16.2 4項工作在雙機之作業
步驟1:表列作業時間
工作
在 機 器 # 1上 之 作 業 時 間
平均流程時間 (天)
10 7 .2 7 .8 9 .2 1 0 .6 8 .6
平均延誤 (天)
4 .6 2 .4 2 .4 4 .0 5 .4 3 .2
2機對n項作業之排程
• n/2流程工作站 • 作業必須以相同的順序經過2部機器 • Johnson法則 • 讓第一項工作的開始至最後一項工作
的結束為止之間的流程時間最小化
考慮SOT法則。給予加工時間最短之訂單第一優先處理, 導出之流程時間:
工作
處理天數(天)
交 期 (從 現 在 起 之 天 數 )
流程時間(天)
E
1
2
0+1=1
C
2
7
1+2=3
A
3
5
3+3=6
B
4
6
6+4=10
D
6
9
10+ 6= 16
流程時間合計=1+3+6+10+16=36天 平均流程時間=36/5=7.2天 只有工作E和C在交期前完成,工作A僅遲了一天 平均工作延誤(0+0+1+4+7)/5=2.4天
–工作指派時至工作站時
•只考慮作業的需求 •不考慮工作站是否有足夠的產能
•有限負荷(Finite Loading)
–工作指派時至工作站時
•考慮作業的需求 •加工機器的設置時間與加工時間
•正向排程 (Forward Scheduling)
–接到訂單後 –向前排定各項作業的完成時間 –可得知各作業的最早完成時刻
A
3
B
6
C
5
D
7
在 機 器 # 2上 之 作 業 時 間 2 8 6 4
•反向排程 (Backward Scheduling)
–以未來的某特定日期(可能是交期) –開始反向往前排定各作業的時間 –可得知最晚開始時刻
•MRP系統是物料無限負荷、反向排程
•機器導向排程
–機器是最重要的資源,故排定機器的時間
•人員導向排程
–人員是最重要的資源,故排定人員的時間
常用的排程與控制功能
–保持所有設備忙碌,並不是最有效之流程 管理
工作排序
•排序(sequencing) •優先排序 (priority sequencing)
–決定工作在機器或工作站上執行的優先程 序
•排定工作順序的法則
–依據一種資料
•加工時間、交期、或訂單到達順序
–經運算取得某種指標數字
•最小閒置時間法則Fra bibliotek排程績效的衡量標準
•滿足客戶交期或下游生產的需求 •使流程時間最小化 •使在製品最小化 •使機器與工作人員之閒置時間最小化
排程法則與技術
單機對n項工作之排程
例16.1 n項工作在單機上作業 Mike Morales是法律影印快遞公司的主管, 這家公司為洛杉磯市中心區的 法律事務所提供影印服務, 有五個客戶在本週的剛開始時, 提出他們的訂單,排程資料詳列於下: