表4 触头法磁化电流值
磁化方法

1. 轴向通电法(1) 轴向通电法是将工件夹于探伤机的两磁化夹头之间,使电流从被检工件上直接流过,在工件的表面和内部产生一个闭合的周向磁场,用于检查与磁场方向垂直、与电流方向平行的纵向缺陷。
如右图所示,是最常用的磁化方法之一。
图3-12 轴向通电法图3-13 夹钳通电法将磁化电流沿工件轴向通过的磁化方法称为轴向通电法,简称通电法;电流垂直于工件轴向通过的方法,称为直角通电法;若工件不便于夹持在探伤机两夹头之间时,可采用夹钳通电法,如图3-14所示,此法不适用大电流磁化。
(2) 轴向通电法和触头法产生打火烧伤的原因是:①工件与两磁化夹头接触部位有铁锈、氧化皮及脏物;②磁化电流过大;③夹持压力不足;④在磁化夹头通电时夹持或松开工件。
(3) 预防打火烧伤的措施是:①清除掉与电极接触部位的铁锈、油漆和非导电覆盖层;②必要时应在电极上安装接触垫,如铅垫或铜编织垫,应当注意,铅蒸汽是有害的,使用时应注意通风,铜编织物仅适用于冶金上允许的场合;③磁化电流应在夹持压力足够时接通;④必须在磁化电流断电时夹持或松开工件;⑤用合适的磁化电流磁化。
(4) 轴向通电法的优点、缺点和适用范围轴向通电法的优点:①无论简单或复杂工件,一次或数次通电都能方便地磁化;②在整个电流通路的周围产生周向磁场,磁场基本上都集中在工件的表面和近表面;③两端通电,即可对工件全长进行磁化,所需电流值与长度无关;④ 磁化规范容易计算;⑤ 工件端头无磁极,不会产生退磁场;⑥ 用大电流可在短时间内进行大面积磁化;⑦ 工艺方法简单,检测效率高;⑧ 有较高的检测灵敏度。
轴向通电法的缺点:① 接触不良会产生电弧烧伤工件;② 不能检测空心工件内表面的不连续性;③ 夹持细长工件时,容易使工件变形。
轴向通电法适用于:承压设备实心和空心工件的焊缝、机加工件、轴类、管子、铸钢件和锻钢件的磁粉检测。
2.中心导体法(1) 中心导体法是将导体穿入空心工件的孔中,并置于孔的中心,电流从导体上通过,形成周向磁场。
磁化规范
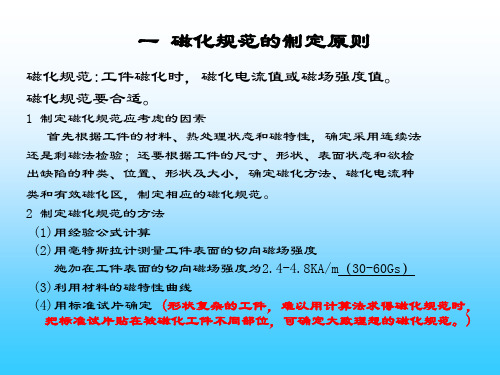
T<19 T≥19 注: I──磁化电流A;
[例]:有一板材对接焊缝,板厚=20mm,采用 触头间距固定为150mm的仪器来检查,需要 多大磁化电流? 解: ∵L=150mm,T=20mm ∴I=(4-5)L=(600-750)A
五 线圈法磁化规范
1. 用连续法检验的线圈法磁化规范
(1)低填充因数线圈——线圈横截面积与被检工件横截面积之比≥10倍时
代入公式得:L/D=L/Deff=600/60=10
将上述工件放入直径为200mm,绕5匝的线圈中,求所需磁 化电流值? 解:Y=π ×1002/π ×502=4 代入中填充系数线圈公式3-10中
10 Y Y 2 IN ( IN ) h ( IN )1 0.75( NI ) h 0.25( NI )l 8 8
三 偏置芯棒法磁化规范
当采用中心导体法磁化时,若工件直径大、设备 的功率不能满足时,可采用偏置芯棒法磁化。应依 次将芯棒紧靠工件内壁(必要时对与工件接触部位 的芯棒进行绝缘)停放在不同位置,以检测整个圆 周,在工件圆周方向表面的有效磁化区为芯棒直径d 的4倍,并应有不小于10%的磁化重叠区。磁化电流 仍按上述表中的公式计算,只是工件直径D要按芯棒 直径加两倍工件壁厚之和计算
[例]有一钢管,规格为φ 180×17×1000,用偏置芯棒法 检验管内、外壁的纵向缺陷,应采用多大的磁化电流?若采用直 径为25mm的芯棒时,需移动几次才能完成全部表面的检验? 解:当芯棒直径D=25mm时, I=(8~15)×(25+2×17)=(472~885)A 又因为检测范围为:4D=4×25=100(mm) 钢管外壁周长为:L=π φ =3.14×180≈570(mm) 考虑到检测区10%的重叠,所以完成全部表面的检验需移动 芯棒次数为:取整数N=7 L 570 N 6.3 4 D1 10% 100 0.9 答:当芯棒直径为25mm时,用偏置芯棒法全面检验钢管需472~ 855A磁化电流,钢管应移动7次。
作业指引——磁粉检测(MT)

文件名称 磁粉检测(MT)作业指引 发布时间磁粉检测(MT)作业指引编制人: 日期:审核人: 日期:批准人: 日期:修订记录日期修订状态修改内容修改人审核人批准人文件名称 磁粉检测(MT)作业指引 发布时间1.质量控制流程图文件名称 磁粉检测(MT)作业指引 发布时间2.检验人员2.1.检验人员必须持有中国船级社(CCS)颁发的资格证书,并在有效期范围内;应按有关规程的规定经过严格培训和考核,并持有相应考核组织颁发的等级资格证书。
2.2.检验人员的视力应每年检查一次,校正视力不低于1.0,无色盲和色弱。
3.检测方法及要求3.1.检验前,焊缝及其附近的母材表面应进行清理,去除表面的油污、焊接飞溅物、松散的铁锈和氧化皮、厚度较大的各种覆盖层(漆层、保温层等);去除放置在表面的各种器具和物品。
3.2.被捡部位在检验中应至少按下述顺序经历了三个检验步骤:a)用磁粉探伤设备进行过必要的磁化;b)在被磁化的区域内用干法施加过干燥的磁粉,或者用湿法施加过磁悬液(即用磁粉或磁膏同载液配制而成的混合液体);c)对施加过磁粉或磁悬液的部位进行磁痕的观察、分析和评定。
3.3.在一般情况下应尽可能采用连续法进行检验。
3.4.焊缝上的每一个检验部位应至少在相互垂直或近于垂直的两个方向上分别得到磁化(有足够依据说明不会产生横向缺陷的情况除外)。
可采用的磁化方式有以下三种:a)纵向磁化加横向磁化——在垂直于焊缝走向和平行于焊缝走向的两个方向上分别进行磁化,先后次序不论。
b)交叉式磁化——在与焊缝走向大致上成+45°和—45°的方向上分别进行磁化,先后次序不论。
c)旋转磁场或摆动磁场磁化——用能在360°或90°平面范围内自动而又连续改变磁场方向的磁场进行磁化。
3.5.一般应在使用适合局部磁化以磁轭法为主。
3.6.用磁轭法磁化焊缝时,每次被磁化的长度范围,最小50mm,最大200mm。
3.7.用湿法施加磁悬液时,施加到被检表面的磁悬液应尽可能均匀分布,并利用载液的流动特性带动磁粉流动。
磁粉检测知识点总结

磁粉检测原理铁磁性材料和工件被磁化后,由于不连续性的存在,使工件表面和近表面的磁感应线发生局部畸变而产生漏磁场,吸附施加在工件表面的磁粉,形成在合适光照下目视可见的磁痕,从而显示出不连续性的位置、形状、大小和严重程度。
磁粉检测的基础是不连续性处漏磁场与磁粉的磁性相互作用。
磁粉检测是靠漏磁场吸附磁粉形成磁痕显示缺陷的。
磁痕显示程度不仅与缺陷性质、磁化方法、磁化规范、磁粉施加方式、工件表面状态和照明条件等有关,还与磁粉本身的性能如磁特性、粒度、形状、流动性、密度和识别度有关。
磁粉的性能1、磁特性:高磁导率、低矫顽力、低剩磁 2、粒度 3、形状4、流动性 5、密度 6、识别度衡量磁粉性能最根本的办法还是通过综合性能(系统灵敏度)试验的结果确定。
磁粉检测适用范围1适用于检测铁磁性材料工件表面和近表面尺寸很小、间隙极窄和目视难以看出的缺陷。
2适用于检测马氏体不锈钢和沉淀硬化不锈钢材料,但不适用于检测奥氏体不锈钢材料和用奥氏体不锈钢焊条焊接的焊接接头,也不适用于检测铜、铝、镁、钛合金等非磁性材料。
3适用于检测工件表面和近表面的裂纹、白点、发纹、折叠、疏松、冷隔、气孔和夹杂等缺陷,但不适用于检测工件表面浅而宽的划伤、针孔状缺陷、埋藏较深的内部缺陷和延伸方向与磁力线方向夹角小于20°的缺陷; 4适用于检测未加工的铁磁性原材料和加工的半成品、成品件及在役与使用过的工件及特种设备。
5适用于检测管材、棒材、板材、型材和锻钢件、铸钢件及焊接件。
磁粉检测的优点:1可检测出铁磁材料表面或近表面的缺陷 2能直观显示缺陷位置、大小、形状和严重程度3具有很高的检测灵敏度 ,可检测微米级宽度的缺陷 4单个工件检测速度快,工艺简单,成本低廉,污染少 5.采用合适的磁化方法,几乎可以检测到工件的各个部位,基本上不受工件大小和形状的限 6.缺陷检测重复性好7.可检测受腐蚀的表面局限性:1.只能适用于检测铁磁性材料,不适用于检测奥氏体不锈钢及其他非铁磁性材料22.只适合检测工件的表面和近表面缺陷 3.检测时的灵敏度与磁化方向有很大关系,若缺陷方向与磁化方向近似平行或缺陷与工件表面夹角小于20°,缺陷就难以发现。
MT探伤方法与应用

MT探伤方法与应用1 磁粉探伤方法分类及选择磁粉探伤方法的分类:1.1.1 按施加磁粉的载体分两种:干法(荧光、非荧光)、湿法(荧光、非荧光)。
1.1.2 按施加磁粉的时机分两种:连续法、剩磁法。
1.1.3 按磁化方法分六种:轴向通电法、触头法、线圈法、磁轭法、中心导体法、交叉磁轭法。
磁粉探伤方法的一般选择原则:1.2.1 连续法和剩磁法都可进行探伤时,优先选择连续法。
1.2.2 对于湿法和干法,优先选择湿法。
,优先选用要根据工件的形状、尺寸、探伤操作的困难程度进行。
2 磁粉探伤方法具体介绍连续法:2.1.1 概念:在磁化的同时,施加磁粉或磁悬液。
2.1.2 适用范围:①形状复杂的工件;②剩磁Br (或矫顽力Hc)较低的工件;③检测灵敏度要求较高的工件;④表面覆盖层无法除掉(涂层厚度均匀不超过0.05mm)的工件。
;②磁化过程中施加磁悬液,磁化时间1S-3S;③磁化停止前完成施加操作并形成磁痕,时间至少1S;④至少反复磁化两次。
(2)具有最高的检测灵敏度。
(3)可用于多向磁化。
(4)交流磁化不受断电相位的影响。
(5)能发现近表面缺陷。
(6)可用于湿法和干法检验。
(1)效率低。
(2)易产生非相关显示。
(3)目视可达性差。
剩磁法:2.2.1 概念:停止磁化后,施加磁粉或磁悬液。
2.2.2 适用范围:①矫顽力Hc在1000A/m以上,并保持剩磁Br在以上的工件,一般如经过热处理的高碳钢和合金结构钢(淬火、回火、渗碳、渗氮、局部正火);低碳钢、处于退火状态或热变形后的钢材都不能采用剩磁法;②成批的中小型零件进行磁粉检测时;③因工件几何形状限制连续法难以检验的部位。
;②磁化后检验完成前,任何磁性物体不得接触被检工件;③磁化时间一般控制在;④浇磁悬液2 – 3遍,或浸入磁悬液中10—20S,保证充分润湿;⑤交流磁化时,必须配备断电相位控制器。
(1)效率高。
(2)具有足够的检测灵敏度。
(3)缺陷显示重复性好,可靠性高。
磁粉检测工艺规程
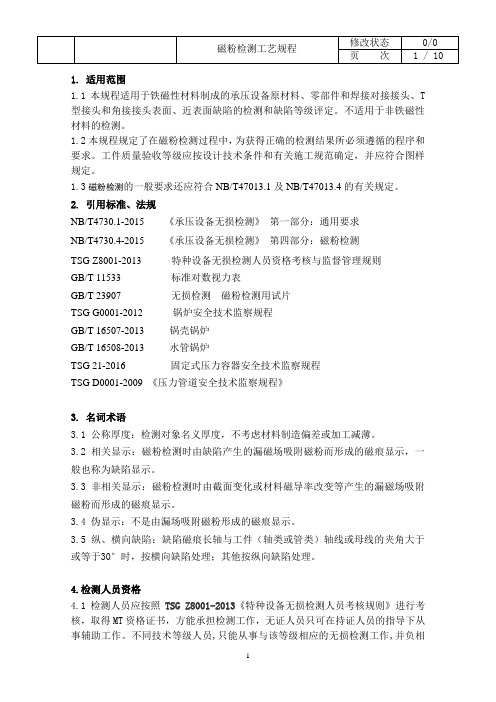
1. 适用范围1.1本规程适用于铁磁性材料制成的承压设备原材料、零部件和焊接对接接头、T 型接头和角接接头表面、近表面缺陷的检测和缺陷等级评定。
不适用于非铁磁性材料的检测。
1.2本规程规定了在磁粉检测过程中,为获得正确的检测结果所必须遵循的程序和要求。
工件质量验收等级应按设计技术条件和有关施工规范确定,并应符合图样规定。
1.3磁粉检测的一般要求还应符合NB/T47013.1及NB/T47013.4的有关规定。
2. 引用标准、法规NB/T4730.1-2015 《承压设备无损检测》第一部分:通用要求NB/T4730.4-2015 《承压设备无损检测》第四部分:磁粉检测TSG Z8001-2013 特种设备无损检测人员资格考核与监督管理规则GB/T 11533 标准对数视力表GB/T 23907 无损检测磁粉检测用试片TSG G0001-2012 锅炉安全技术监察规程GB/T 16507-2013 锅壳锅炉GB/T 16508-2013 水管锅炉TSG 21-2016 固定式压力容器安全技术监察规程TSG D0001-2009《压力管道安全技术监察规程》3.名词术语3.1 公称厚度:检测对象名义厚度,不考虑材料制造偏差或加工减薄。
3.2 相关显示:磁粉检测时由缺陷产生的漏磁场吸附磁粉而形成的磁痕显示,一般也称为缺陷显示。
3.3 非相关显示:磁粉检测时由截面变化或材料磁导率改变等产生的漏磁场吸附磁粉而形成的磁痕显示。
3.4 伪显示:不是由漏场吸附磁粉形成的磁痕显示。
3.5 纵、横向缺陷:缺陷磁痕长轴与工件(轴类或管类)轴线或母线的夹角大于或等于30°时,按横向缺陷处理;其他按纵向缺陷处理。
4.检测人员资格4.1检测人员应按照TSG Z8001-2013《特种设备无损检测人员考核规则》进行考核,取得MT资格证书,方能承担检测工作,无证人员只可在持证人员的指导下从事辅助工作。
不同技术等级人员,只能从事与该等级相应的无损检测工作,并负相应的技术责任。
典型焊接接头磁粉检测技术教案
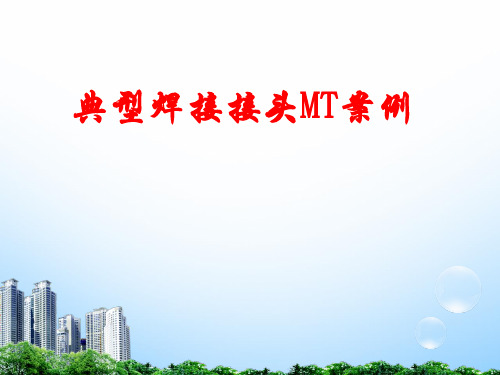
工 序
工序名称
操作要求及主要工艺参数
1 预清理
采用砂轮打磨等方式,清除焊缝及边缘处飞溅焊渣,并 保证被检区域光滑。
采用磁轭法磁化, 先磁轭平行焊缝磁化,磁轭间距为
2
磁 化
磁化顺序与 磁化次数
100mm。两次之间重叠10mm,对整条焊缝磁化完成后, 再用磁轭垂直焊缝磁化,磁轭间距200mm,每次磁化 焊缝的有效长度100mm,两次之间重叠10mm,依次完 成整条焊缝磁化。
请按照NB/T47013.4-2015,Ⅰ级合格,编写磁 粉检测操作指导书。
可选用的设备有:CEE-1000型磁轭探伤仪、 CXE-2000型旋转磁场探伤仪、CJX-1000型交流磁 粉探伤仪、CYD-3000移动式磁粉探伤机、CEW3000型整流磁粉探伤仪及磁粉、载液和其他相关 器材。
图14 液化石油气储罐
触头法的电极应控制在75mm~200mm之间。但 触头连线间距应L≥75mm,两次磁化间的两触头 间距b≤L/2。触头法磁化电流值I按NB/T47013.4 表4计算,触头法检测平板对接焊缝如图4和5所 示;检测T型焊缝如图6所示;检测管板焊缝如图 7所示;检测角焊缝如图8所示。
表4 触头法磁化电流值
灵敏度校核
所有磁化方式其磁化规范最终以A1:30/100试片确定, 放置在焊缝热影响区灵敏度最弱处。
磁悬液要求 3 及施加方式
磁悬液配好后,应采用梨形沉淀管测定磁悬液浓度,保 证浓度在要求范围内。正式检测前,应在被检表面进行 水断实验,合格后再进行检测。喷洒时自高而低,自上 而下分进行磁化。
检验时机 检验在磁痕形成后立即进行。
术
工 艺 参
磁悬液沉淀 浓度
0.10.4mL/100m
磁粉检测(MT-Ⅱ)知识点总结

精心整理磁粉检测(MT-Ⅱ)知识点总结磁粉检测原理铁磁性材料和工件被磁化后,由于不连续性的存在,使工件表面和近表面的磁感应线发生局部畸变而产生漏磁场,吸附施加在工件表面的磁粉,形成在合适光照下目视可见的磁痕,从而显示出不连续性的位置、形状、大小和严重程度。
磁粉检测的基础是不连续性处漏磁场与磁粉的磁性相互作用。
6局限性:1.只能适用于检测铁磁性材料,不适用于检测奥氏体不锈钢及其他非铁磁性材料22.只适合检测工件的表面和近表面缺陷3.检测时的灵敏度与磁化方向有很大关系,若缺陷方向与磁化方向近似平行或缺陷与工件表面夹角小于20°,缺陷就难以发现。
4.受几何形状影响,易产生非相关显示5.若工件表面有覆盖层,将对磁粉检测有不良影响,在通电法和触头发磁化时,易产生打火烧伤6.部分磁化后具有较大剩磁的工件需进行退磁处理磁粉检测的七个程序:(1)预处理;(2)磁化;(3)施加磁粉或磁悬液;(4)磁痕的观察与记录:(5)缺陷评级;(6)退磁;(7)后处理。
磁力线具有以下特性:1)磁感应线是具有方向性的闭合曲线。
在磁体内,磁感应线是由S极到N极;在磁体外,磁感应线是由N极出发,穿过空气进入S极的闭合曲线。
2)磁感应线互不相交。
3)磁感应线可描述磁场的大小和方向。
4)磁感应线沿磁阻最小路径通过磁场强度H=I/(2πr)在SI单位制中,磁场强度的单位是安(培)/米(A/m)奥(斯特)Oe;磁感应强度又称为磁通密度。
在SI单位制中,磁感应强度的单位是特(斯拉)(T)=104高斯(Gs)μμo=α,用Br(1)(2)通电圆柱导体的磁场磁场方向:与电流方向有关,用右手定则确定。
磁场大小:安培环路定律计算通电长导体导体表面的磁场强度为:H=I/2πR导体外r处(r>R)的磁场强度:H=I/2πr导体内部r处(r<R)磁场强度:H=Ir/2πR2用交流电和直流电磁化同一钢棒时,其共同点是:1)在钢棒中心处,磁场强度为零;2)在钢捧表面,磁场强度达到最大;3)离开钢棒表面,磁场强度随r的增大而下降。
- 1、下载文档前请自行甄别文档内容的完整性,平台不提供额外的编辑、内容补充、找答案等附加服务。
- 2、"仅部分预览"的文档,不可在线预览部分如存在完整性等问题,可反馈申请退款(可完整预览的文档不适用该条件!)。
- 3、如文档侵犯您的权益,请联系客服反馈,我们会尽快为您处理(人工客服工作时间:9:00-18:30)。
表4 触头法磁化电流值 工件厚度T ,mm 电流值I ,A
T <19 (3.5~4.5)倍触头间距
T ≥19
(4~5)倍触头间距
3.8.5 磁轭法
3.8.5.1 磁轭的磁极间距应控制在75mm ~200mm 之间,检测的有效区域为两极连线两侧各50mm 的范围内,磁化区域每次应有不少于15mm 的重叠。
3.8.5.2 采用磁轭法磁化工件时,其磁化电流应根据标准试片实测结果来选择;如果采用固定式磁轭磁化工件时,应根据标准试片实测结果来校验灵敏度是否满足要求。
3.8.6 线圈法
线圈法产生的磁场平行于线圈的轴线。
线圈法的有效磁化区是从线圈端部向外延伸到150mm 的范围内。
超过150mm 以外区域,磁化强度应采用标准试片确定。
3.8.6.1 低充填因数线圈法。
当线圈的横截面积大于或等于被检工件横截面积的10倍时,使用下述公式: 偏心放置时,线圈的磁化电流按式(1)计算(误差为10%):
………………………………………(1) 正中放置时,线圈的磁化电流按式(2)计算(误差为10%):
……………………………………(2) 以上各式中:
I ——施加在线圈上的磁化电流,A ;
N ——线圈匝数;
L ——工件长度,mm ;
D ——工件直径或横截面上最大尺寸,mm ;
R ——线圈半径,mm 。
3.8.6.2 高充填因数线圈法。
用固定线圈或电缆缠绕进行检测,若此时线圈的截面积小于或等于2倍工件截面积(包括中空部分),磁化时,可按式(3)计算磁化电流(误差10%):
(3)
式中各符号意义同式(1)。
3.8.6.3 中充填因数线圈法。
当线圈大于2倍而小于10倍被检工件截面积时,
()()()()8/]210[-+-=Y NI Y NI NI l h (4)
式中:
(NI )h ——式(3)高充填因数线圈计算的NI 值。
(NI )l ——式(1)或式(2)低充填因数线圈计算的NI 值。
Y ——线圈的横截面积与工件横截面积之比。
3.8.6.4 上述公式不适用于长径比(L /D )小于2的工件。
对于长径比(L /D )小于2的工件,若要使用线圈法时,可利用磁极加长块来提高长径比的有效值或采用标准试片)
/(45000D L N I =]
5)/(6[1690-=D L N R I ]2)/[(35000+=D L N I
实测来决定电流值。
对于长径比(L/D)大于等于15的工件,公式中(L/D)取15。
3.8.6.5 当被检工件太长时,应进行分段磁化,且应有一定的重叠区。
重叠区应不小于分段检测长度的10%。
检测时,磁化电流应根据标准试片实测结果来确定。
3.8.6.6 计算空心工件时,此时工件直径D应由有效直径D eff代替。
对于圆筒形工件:
D eff=[(D o)2-(D i)2]1/2 (5)
式中:
D o——圆筒外直径,mm;
D i——圆筒内直径,mm。
对于非圆筒形工件:
Deff=
πAh
At-
2 (6)
式中:
A t——零件总的横截面积,mm2;
A h——零件中空部分的横截面积,mm2。