质量工具--8D分析共41页文档
质量管理体系的文件控制

质量管理体系有关的文件控制资料【最新资料,WORD文档,可编辑修改】1、目的对与组织质量管理体系有关的文件进行控制,确保各相关场所使用文件为有效版本。
2、范围适用于与质量管理体系有关的文件控制。
3、职责3.1 总经理负责批准发布质量保证手册。
3.2 管理者代表负责审核质量保证手册。
3.3 各部门负责相关文件的编制、使用和保管。
3.4 质管部负责组织对现有体系文件的定期评审。
3.5 各部门资料员负责本部门与质量管理体系有关的文件的收集、整理和归档等。
4、程序4.1 文件分类及保管4.1.1 质量保证手册(包含了所有过程控制的程序文件),由质管部备案保存。
4.1.2 公司级管理性文件,如各种行政管理制度、部分外来的管理性文件,包括与质量管理体系有关的政策,法规文件等,由综合管理部保存。
4.2 文件的编写、审核、批准、发放文件发布前应得到批准,以确保文件是适宜的:4.2.1 质量保证手册由质管部负责组织编写,由管理者代表审核,上报总经理批准发布,由质管部负责登记、发放;4.2.2 各部门工作手册由各部门经理组织编写、汇总,由管理者代表审核,报总经理批准,质管部负责登记、发放;4.2.3 应确保文件使用的各场所都应得到相关文件的适用版本。
文件的发放、回收要填写《文件发放、回收记录》。
4.3 文件的受控状况文件分为“受控”和“非受控”两大类,凡与质量体系运行紧密相关的文件应为受控,由各主管部门按规定执行。
4.4 文件的更改4.4.1 质量保证手册由质管部组织更改,填写《文件更改申请》,经管理者代表审核,上报总经理批准后更改,由质管部发放。
质管部应保留文件更改内容的记录。
4.4.2 其他文件的更改由各相应主管部门填写《文件更改申请》,经原审批部门审批,再由各相应部门指定人员进行更改、发放、处理。
如果指定其他部门审批时,该部门应获得审批所需依据的有关背景资料。
4.4.3 所有被更改的原文件必须由相应主管部门收回,以确保有效文件的唯一性。
8D基本知识介绍
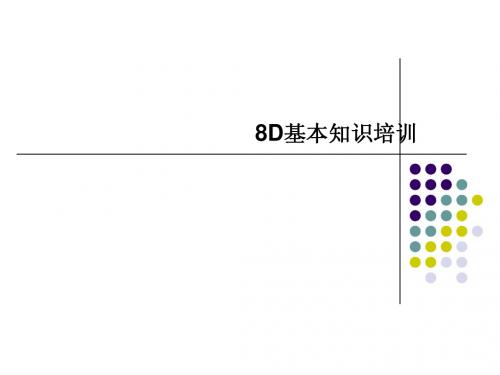
2、8D的流程: 8D的流程: 的流程 D0:问题提出(准备) D0:问题提出(准备) 问题提出 D1: D1:小组成立 D2: D2:问题描述 D3: D3:实施并验证临时措施 D4:确定并验证根本原因 D4: D5: D5:选择和验证永久纠正措 施 D6: D6:实施永久纠正措施 D7: D7:预防再发生 D8: D8:小组祝贺
定团队的负责人 • 选定团队负责人
主要活动内容
团队负责人要做的工作有确保队员、预算、工程及设计变更、 推进日程等相关决定内容的管理及采取措施
选拔团队成员
• 与问题解决相关的人员选拔
成员的能力与否 N Y 设定问题解决目标 确定各推进项目领导及工作计划 把握现象 • 认识团队的目标
• 设定问题解决日程及领域
临时(封锁) 措施 确认 临时(封锁) 树立措施计划 N 隔离问题的影响 Y 分析措施结果 N 除去问题的影响 Y 持续的事后管理 分析根本原因
主要活动内容
• 本措施是为了不让再发生原因已知道的问题点 • 分工对措施的日程计划及作用
• 其问题点的影响是否与内外部客户隔离 ?
• 根据数据的效果确认
• 一直实施到根本对策树立执行为止
机(因 1) 因2 因2 料(因 1) 因2 因2 因3 法(因 1)
人(因 1) 因2
问题的果
因2 因4 因3
环(因 1)
五个为什么方法 五个为什么是发掘现场原因的最有效的方法之一,就是持 续问“为什么?”直到找到问题的原因为止。
根由 Root Cause
为什麽? 为什麽? 为什麽? 为什麽?
真正原因
常见性错误: 常见性错误:
所选择的完成8D过程的小组成员没有技术知识。 只有一两个人实施该过程
8D资料培训讲义(41页)

两者区别:
–纠正措施是针对已出现的不合格,是为 了防止再发生。
–预防措施是针对潜在的不合格,是为了 防止发生。
2020/10/21
5
解决问题的方法
例:XX公司生产产品长度短,其措施如下 1、对不合格产品进行返工,再冲一次,请
问此措施是什么措施? 纠正
2、对冲压模具的定位靠山进行固定,并每 日点检确认,请问是什么措施? 纠正措施
性差,而PPG的油漆在通用已得到认可,兄弟公司使用性能稳定
30%
2.使用杜邦油漆素材表面需要打磨处理,涂装后一次合格格率低(只有30%~50%的合格率),而使用PPG的
油漆素材不需打磨处理,产品合格率可达到90%以上
40%
3.組織內的變更管理流程不严谨
ห้องสมุดไป่ตู้20%
4.人員培訓不到位/現場管理欠缺
10%
D5/D6-永久性的纠正措施/验证Permanent Corrective Action/Validation
从2008.3.26 开始
报告人 Author:
时间Date:
赵艳/张仕荣 2008.3.24
2020/10/21
9
5 Why’S Root Cause 例1
例如,焊接到膜盒上的一根毛细管发生了泄漏:
– 为什么会泄漏?
• 焊接密封不好。
– 为什么焊接的密封不好?
• 在毛細管內有沉积物。
– 为什么在毛細管內有沉积物?
–注1:返工或降级可作为纠正的示例 –注2:纠正可连同纠正措施一起实施。
–糾正措施:为消除已发现的不合格或其 他不期望情况的原因所采取的措施
–注1:一个不合格可以有若干个原因。
2020/10/21
完整8D报告模板
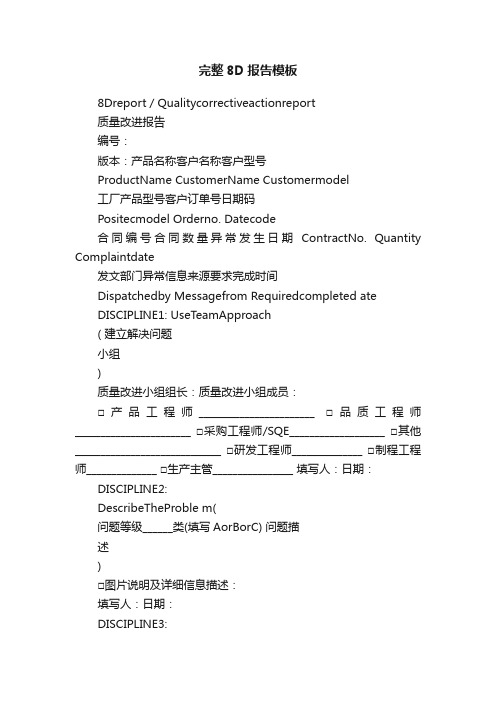
完整8D报告模板8Dreport/Qualitycorrectiveactionreport质量改进报告编号:版本:产品名称客户名称客户型号ProductName CustomerName Customermodel工厂产品型号客户订单号日期码Positecmodel Orderno. Datecode合同编号合同数量异常发生日期ContractNo. Quantity Complaintdate发文部门异常信息来源要求完成时间Dispatchedby Messagefrom Requiredcompleted ateDISCIPLINE1: UseT eamApproach( 建立解决问题小组)质量改进小组组长:质量改进小组成员:□产品工程师_______________________ □品质工程师_______________________ □采购工程师/SQE___________________ □其他_____________________________ □研发工程师______________ □制程工程师______________ □生产主管________________ 填写人:日期:DISCIPLINE2:DescribeTheProble m(问题等级______类(填写AorBorC) 问题描述)□图片说明及详细信息描述:填写人:日期:DISCIPLINE3:ImplementAndVerifyContainmentAction (□返工/补充加工(QE/PE) 执行暂时对策)□质量问题通知供应商(SQE或采购) □生产计划调整(QE)□(在线/在途/库存)零部件库存处理(PE) □通知客户/QA(公司QA 或工厂QE)□国外产品处理(项目主管or品质经理) □其它相应措施说明:日期:管理部门:品质部第1页;共4页保存期限:三年【中PTA-0807-04-04】8Dreport/Qualitycorrectiveactionreport质量改进报告编号:版本:DISCIPLINE4: DefineandVerifyRootCause( 找出问题的真正原因)原因分析(责任部门填写)□设计缺陷/Designdefects □规格、标准缺陷 /criteriondefects□工装设备缺陷/Equipmentdefects □检查判定缺陷(误判、错判)/Wrongverdict □制程及作业上缺陷(含料件)/Partsorassemblingdefects□模具、夹具缺陷/Fixturedefects □其他/Others具体说明/Describedindetail:□失效模式再现验证说明□改进失效验证说明附原因分析报告《》(插入附件,空白表单在下面连接内)填写人:日期:DISCIPLINE5:ChooseandVerifyPermanentCorrectiveAct ion( 选择永久对策)相应措施进度及说明:具体内容责任人计划完成时间样品采购样品确认工程样机装配实验申请实验结果判断工装申请小批验证□ECR:(连接到文管中心下文件)□修模单:(连接到文管中心下文件)□其它填写人:日期:DISCIPLINE6: ImplementPermanentCorrectiveAction( 执行及验证永久对策)□品质标准(品质人员提供,需明确清晰):□正向模式验证:□反向失效模式验证:实际完成情况确认人实际完成时间样品采购样品确认工程样机装配实验申请实验结果判断工装申请小批验证(工程人员提供正/反验证需包含详细数据,如实验申请号,验证结果等.)(品质)填写人:日期:(工程)填写日期:人:DISCIPLINE7: PreventRecurrence&Standardization( 防止再发生措施及标准化)第2页;共4页管理部门:品质部保存期限:三年【中PTA-0807-04-04】8Dreport/Qualitycorrectiveactionreport质量改进报告编号:版本:产品工程师PE:□ECN□BOM□PQC检指/培训□IQC检指/培训制程工程师:□总装工艺卡/装配人员培训品质工程师QE:□FQC检指/培训采购部SQE:□供应商培训□供应商检指□供应商检具□供应商工艺□供应商库存处理其它填写人:日期:DISCIPLINE8:CongratulateOurTeam( 批量验证/团队激励) 改善情况的追踪:□ECN□BOM□供应商培训□供应商检指□供应商检具□供应商工艺□供应商库存处理□IQC检指/检验结果□PQC检指/检验结果□FQC检指/检验结果□总装工艺卡□试验/检验考核结果经办/draftedby: 部门审核/checkedby:填写人:品质经理审核:日期:批准/Approvedby:一、QC培训记录二、QC检指记录三、供应商方面培训、检(插入相关支持文件)指、检具、工艺、协议记录四、工艺文件备注:1.对异常问题或改进状态的描述要尽量有图片说明或详细的信息记录。
8D问题解决方法 共135页

13.07.2019
45
永久措施的過程想法
xx
x
process
Y
xx
我们修改了x(原因)来期望可以将y做好。 所以对x,y都要有一些衡量,才能确认效果好不好
13.07.2019
46
D7:防止问题再度发生
• 防止问题再度发生:着手进行管理制度, 操作系统,作业实务,及作业程序等项之修 改,以防同一问题及类似问题之再度发生。
5
面对问题不可以各自
面对问题应群策群力,
为政,自我本位主义
相互提携、互相帮助
否Hale Waihona Puke 将无法有效解决问题 如此才能彻底解决问题
13.07.2019
6
何谓8D
• 此一方式须透过“问题分析报告”。
• 此一方式可为从统计制程管制作业,应如 何走向品质实际提升之间,提供一项具体 的连系。
应用SPC
8D方法
提升制程能力
13.07.2019
37
5-WHY CASE3
•焊接到膜盒上的一根毛细管发生了泄漏:
–为什么样会泄漏?
•焊接密封不好。
–为什么焊接的密封不好?
•在毛细管内有沉积物。
–为什么在毛细管内有沉积物?
•清洗管子时没有清洗掉。
–为什么清洗不掉?
•使用的洗涤剂效果不好。
–为什么洗涤剂效果不好?
•洗涤剂的配方对毛细管内的这种沉积物无效
问题层次是否降低
问题是否消除
34
识别根本原因的方法
TOYOTA 5-WHY
WHY 问题
WHY
WHY
WHY
WHY
中间原因 中间原因 中间原因 根本原因
13.07.2019
8D报告模板_6

其他
3.供应商内部流出原因(或汽车厂家处未识别出)的初步分析
不合格零件应当在何处被发现?
N
在制造工序中
在制造后(如最终检验)
出货前/汽车厂家入库时
没有被发现的原因
对不良产生原因初步判断/流出原因的分析:
D3-第三步骤:执行临时对策
4.临时对策–立即的
组织相关人员针对此问题开现场分析会。
考虑事项
防止再发生对策报告书―8D
编号:
D1-第一步骤:建立解决问题小组
组长:
组员:
D2-第二步骤: 描述问题
减振器在新车交验过程中损坏:弹簧弹出,减震器失效。
1 问题详情
受影响的数量(或追溯)
2. 向类似零件的展开
该问题在其他零件上发生过吗?
考慮事項
Y
N
备注/ 結果
其他车型零件
同一不良现象覆盖的所有车型。
D8-第八步骤: 团队激励。
处置
OK数
NG数
在制品
中间在库品(半成品)
仓库存品
服务备件
其他
首批交付合格部品如何特殊标识/标记 ?
标牌
D4-第四步骤: 找出问题真正原因
5最终分析
时间
原因
责任部门
生产管理部
生产管理部
D5-第五步骤: 选择永久对策
6.永久対策
措施
负责人
部门
实施时间
D6-第六步骤:执行及验证永久对策
7. 对策确认
Y
N
Y
N
D7-第七步骤: 防止再发。
8.跟踪措施
考慮事项
Yes/No
实施时间
实施部门
工序作业/检查指导书
8D-报告写法

問題
緊急處理
為什麼機器會超載?
過去
為什麼軸承會潤滑不足?
為什麼潤滑幫浦會失靈?
why真因
why
真因
why
真因
一次因 (近因)
治標對策 (暫時)
改善行動 防呆設計
為什麼潤滑幫浦的 輪軸會耗損?
why
真因
真因
第18页,共80页。
n 次因
Page of 110 (遠因)
治本對策 (永久)
5 Why & 關連圖
• 問1:為什麼機器停了? • 答1:因為機器超載, 保 險絲燒斷了
• 問2:為什麼機器會超載? • 答2: 因為軸承的潤滑 不足
第14页,共80页。
Page of 110
5 Why 範例: 為何停機
• 問1:為什麼機器停了? • 答1:因為機器超載, 保
險絲燒斷了
• 問2:為什麼機器會超載? • 答2: 因為軸承的潤滑
工作 不專心
材料問題
TRAY
設計不良
人員疏失
平面度 良率不佳
職前訓練 不足
BUY OFF檢 查動作不確實
設備問題
模具異常
產品定位 不良
機台操作
不熟悉 Page of 110
第20页,共80页。
磨損
PDCA 的介紹
第21页,共80页。
何謂管理?
ACTION PLAN CHECK DO
QUALITY CONSCIOUSNESS
第35页,共80页。
Page of 110
Sigma Rule
99-100% 90-98% 60-75%
-s
+s
-2s
+2s
PQE培训教材-8D报告

PQE培训教材-8D报告1. 什么是8D报告8D报告是一种问题解决方法,它可以帮助团队追溯和解决问题的根本原因,并制定有效的纠正和预防措施。
它是以8个步骤命名的,每个步骤都有具体的任务和工具,以确保问题得到彻底解决。
以下是8D报告的八个步骤:1.D1:建立问题解决团队2.D2:描述问题3.D3:立即暂时解决问题4.D4:根本原因分析5.D5:制定纠正措施6.D6:实施纠正措施7.D7:验证纠正措施8.D8:预防措施跟踪2. D1:建立问题解决团队在D1阶段,我们需要确定一个问题解决团队,这个团队由不同领域和专业的人员组成,以确保问题得到全面的解决。
团队应包括以下成员:•项目经理:负责整个问题解决过程的组织和协调。
•质量工程师:负责分析和解决质量问题。
•制造工程师:负责分析和解决制造过程中的问题。
•供应链代表:负责协调和解决供应商相关的问题。
•设计工程师:负责分析和解决设计问题。
•生产经理:负责分析和解决生产过程中的问题。
•客户代表:负责与客户沟通并解决与客户相关的问题。
建立问题解决团队后,团队成员需要明确各自的角色和职责,并制定一个工作计划,以确保问题得到及时解决。
3. D2:描述问题在D2阶段,团队成员需要准确地描述问题,并确保问题被充分理解。
问题描述应包括以下内容:•问题发生的具体时间和地点。
•问题的具体表现或症状。
•问题影响的范围。
•对问题的初步评估以及可能的原因。
描述问题时,团队成员应尽量客观和详细,以确保问题不会被误解或忽视。
4. D3:立即暂时解决问题在D3阶段,团队成员需要立即采取措施解决问题的紧急影响。
这些措施是暂时的,旨在缓解问题的影响,但不一定解决问题的根本原因。
暂时解决问题的措施可能包括以下内容:•停机或减少生产。
•调整生产工艺。
•加强质量检查。
•与供应商联系并请求紧急支持。
在采取暂时解决措施后,团队应监控问题,并确保措施的有效性。
5. D4:根本原因分析在D4阶段,团队成员需要进行根本原因分析,以确定问题的根本原因。