自动化铆接
工业自动化中的自动化铆接技术
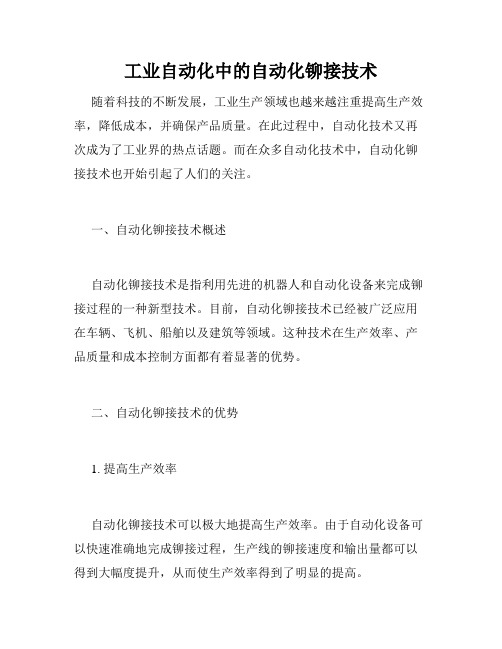
工业自动化中的自动化铆接技术随着科技的不断发展,工业生产领域也越来越注重提高生产效率,降低成本,并确保产品质量。
在此过程中,自动化技术又再次成为了工业界的热点话题。
而在众多自动化技术中,自动化铆接技术也开始引起了人们的关注。
一、自动化铆接技术概述自动化铆接技术是指利用先进的机器人和自动化设备来完成铆接过程的一种新型技术。
目前,自动化铆接技术已经被广泛应用在车辆、飞机、船舶以及建筑等领域。
这种技术在生产效率、产品质量和成本控制方面都有着显著的优势。
二、自动化铆接技术的优势1. 提高生产效率自动化铆接技术可以极大地提高生产效率。
由于自动化设备可以快速准确地完成铆接过程,生产线的铆接速度和输出量都可以得到大幅度提升,从而使生产效率得到了明显的提高。
2. 保证产品质量传统的手工铆接技术存在人为因素干扰的风险,而自动化铆接技术可以快速准确地完成铆接过程,从而消除了铆接中的人为误差。
此外,自动化铆接技术可以更加精确地控制铆接力度和接合密度,从而提高了产品质量并减少了因不良铆接引起的问题。
3. 降低生产成本传统的手工铆接需要大量的人工劳动,耗时且劳动力成本高。
而自动化铆接技术可以减少人工投入,从而降低人工成本,同时自动化设备的占地面积也相对较小,从而减少了工厂的租金和人员维护成本。
三、自动化铆接技术的应用1. 车辆制造自动化铆接技术在车辆制造领域得到了广泛应用。
在汽车生产领域,自动化铆接技术被用来完成车身和车门的铆接过程,从而提高了车辆的生产效率和产品质量。
2. 船舶制造在船舶制造领域,自动化铆接技术也得到了广泛的应用。
自动化铆接技术可以更好地应对铆接大型船体的问题,并且还可以提高船舶的强度和耐用性。
3. 飞机制造在航空领域,自动化铆接技术也是一个必不可少的环节。
传统的手工铆接技术不仅效率低下,而且难以保证铆接质量,容易引起事故。
自动化铆接技术可以减少人为因素的干扰,从而极大地减少了事故的发生概率,并且可以提高飞机的结构强度和耐用性。
铆钉铆接机械的加工效率与生产成本分析
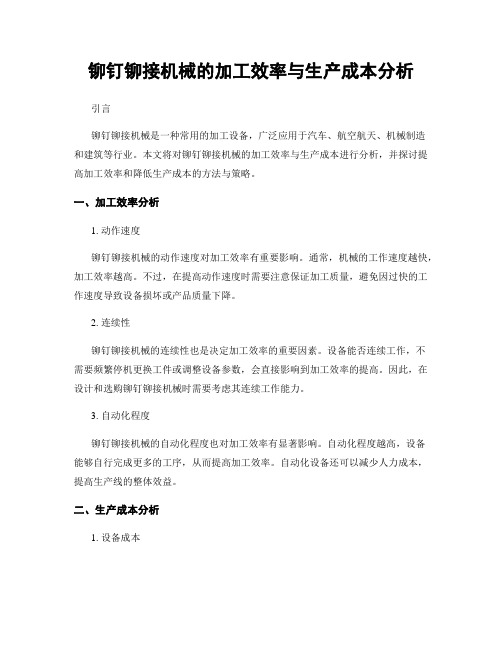
铆钉铆接机械的加工效率与生产成本分析引言铆钉铆接机械是一种常用的加工设备,广泛应用于汽车、航空航天、机械制造和建筑等行业。
本文将对铆钉铆接机械的加工效率与生产成本进行分析,并探讨提高加工效率和降低生产成本的方法与策略。
一、加工效率分析1. 动作速度铆钉铆接机械的动作速度对加工效率有重要影响。
通常,机械的工作速度越快,加工效率越高。
不过,在提高动作速度时需要注意保证加工质量,避免因过快的工作速度导致设备损坏或产品质量下降。
2. 连续性铆钉铆接机械的连续性也是决定加工效率的重要因素。
设备能否连续工作,不需要频繁停机更换工件或调整设备参数,会直接影响到加工效率的提高。
因此,在设计和选购铆钉铆接机械时需要考虑其连续工作能力。
3. 自动化程度铆钉铆接机械的自动化程度也对加工效率有显著影响。
自动化程度越高,设备能够自行完成更多的工序,从而提高加工效率。
自动化设备还可以减少人力成本,提高生产线的整体效益。
二、生产成本分析1. 设备成本铆钉铆接机械的价格因品牌、型号和技术各异而有所差异。
在选择设备时,需要综合考虑设备的性能和价格,选择性价比较高的设备。
此外,还需要考虑设备的维护成本和使用寿命,以减少后续维修和更换设备的成本。
2. 劳动力成本劳动力成本是生产成本的重要组成部分。
在铆钉铆接机械的操作过程中,需要工人进行设备的操作和监控。
为了降低劳动力成本,可以提供员工培训,提高操作技能,并灵活安排工作时间以提高工作效率。
3. 能耗成本铆钉铆接机械在工作过程中会消耗大量的能源。
合理使用能源、采用节能措施是降低生产能耗成本的关键。
例如,选择高效能耗低的设备,优化设备运行参数,以减少能源浪费。
4. 生产线布局铆钉铆接机械的生产线布局对于提高生产效率和降低生产成本至关重要。
合理规划设备的摆放位置,减少物流距离,缩短生产周期。
此外,采用自动化输送带和机器人等智能系统,能够进一步提高生产线的效率和降低生产成本。
三、提高加工效率和降低生产成本的方法与策略1. 技术更新及时采用先进的铆钉铆接机械,利用新技术提高设备的操作效率和生产能力。
铆工领域的新技术和趋势分析
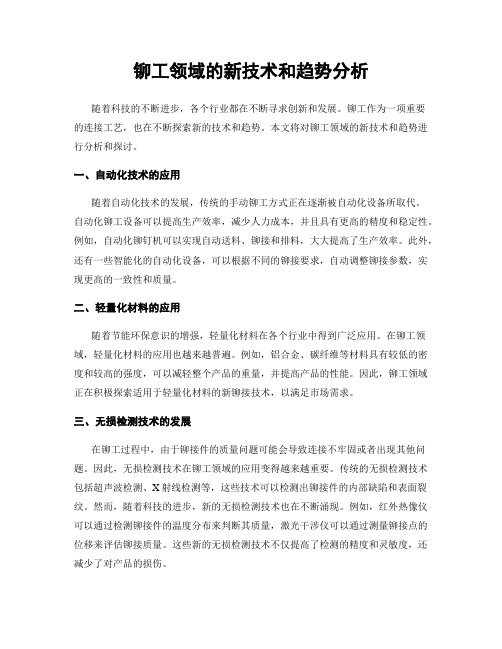
铆工领域的新技术和趋势分析随着科技的不断进步,各个行业都在不断寻求创新和发展。
铆工作为一项重要的连接工艺,也在不断探索新的技术和趋势。
本文将对铆工领域的新技术和趋势进行分析和探讨。
一、自动化技术的应用随着自动化技术的发展,传统的手动铆工方式正在逐渐被自动化设备所取代。
自动化铆工设备可以提高生产效率,减少人力成本,并且具有更高的精度和稳定性。
例如,自动化铆钉机可以实现自动送料、铆接和排料,大大提高了生产效率。
此外,还有一些智能化的自动化设备,可以根据不同的铆接要求,自动调整铆接参数,实现更高的一致性和质量。
二、轻量化材料的应用随着节能环保意识的增强,轻量化材料在各个行业中得到广泛应用。
在铆工领域,轻量化材料的应用也越来越普遍。
例如,铝合金、碳纤维等材料具有较低的密度和较高的强度,可以减轻整个产品的重量,并提高产品的性能。
因此,铆工领域正在积极探索适用于轻量化材料的新铆接技术,以满足市场需求。
三、无损检测技术的发展在铆工过程中,由于铆接件的质量问题可能会导致连接不牢固或者出现其他问题。
因此,无损检测技术在铆工领域的应用变得越来越重要。
传统的无损检测技术包括超声波检测、X射线检测等,这些技术可以检测出铆接件的内部缺陷和表面裂纹。
然而,随着科技的进步,新的无损检测技术也在不断涌现。
例如,红外热像仪可以通过检测铆接件的温度分布来判断其质量,激光干涉仪可以通过测量铆接点的位移来评估铆接质量。
这些新的无损检测技术不仅提高了检测的精度和灵敏度,还减少了对产品的损伤。
四、数字化技术的应用随着数字化技术的飞速发展,铆工领域也开始应用数字化技术来提高生产效率和质量。
例如,数字化设计软件可以帮助工程师更加准确地设计铆接结构,减少设计错误和重复工作。
数字化仿真软件可以模拟铆接过程,评估不同参数对铆接质量的影响,从而优化铆接方案。
此外,数字化技术还可以实现铆接过程的实时监控和数据采集,为质量控制和过程改进提供依据。
综上所述,铆工领域的新技术和趋势主要包括自动化技术的应用、轻量化材料的应用、无损检测技术的发展和数字化技术的应用。
铆钉铆接机械的先进传感技术与智能控制研究
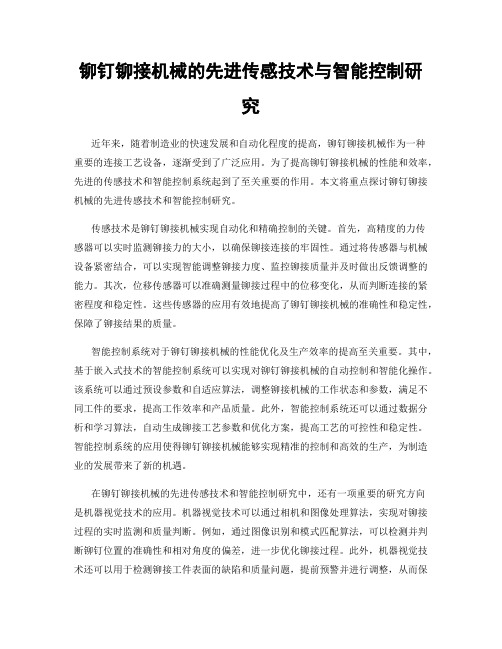
铆钉铆接机械的先进传感技术与智能控制研究近年来,随着制造业的快速发展和自动化程度的提高,铆钉铆接机械作为一种重要的连接工艺设备,逐渐受到了广泛应用。
为了提高铆钉铆接机械的性能和效率,先进的传感技术和智能控制系统起到了至关重要的作用。
本文将重点探讨铆钉铆接机械的先进传感技术和智能控制研究。
传感技术是铆钉铆接机械实现自动化和精确控制的关键。
首先,高精度的力传感器可以实时监测铆接力的大小,以确保铆接连接的牢固性。
通过将传感器与机械设备紧密结合,可以实现智能调整铆接力度、监控铆接质量并及时做出反馈调整的能力。
其次,位移传感器可以准确测量铆接过程中的位移变化,从而判断连接的紧密程度和稳定性。
这些传感器的应用有效地提高了铆钉铆接机械的准确性和稳定性,保障了铆接结果的质量。
智能控制系统对于铆钉铆接机械的性能优化及生产效率的提高至关重要。
其中,基于嵌入式技术的智能控制系统可以实现对铆钉铆接机械的自动控制和智能化操作。
该系统可以通过预设参数和自适应算法,调整铆接机械的工作状态和参数,满足不同工件的要求,提高工作效率和产品质量。
此外,智能控制系统还可以通过数据分析和学习算法,自动生成铆接工艺参数和优化方案,提高工艺的可控性和稳定性。
智能控制系统的应用使得铆钉铆接机械能够实现精准的控制和高效的生产,为制造业的发展带来了新的机遇。
在铆钉铆接机械的先进传感技术和智能控制研究中,还有一项重要的研究方向是机器视觉技术的应用。
机器视觉技术可以通过相机和图像处理算法,实现对铆接过程的实时监测和质量判断。
例如,通过图像识别和模式匹配算法,可以检测并判断铆钉位置的准确性和相对角度的偏差,进一步优化铆接过程。
此外,机器视觉技术还可以用于检测铆接工件表面的缺陷和质量问题,提前预警并进行调整,从而保证产品质量。
因此,机器视觉技术的应用可以进一步完善铆钉铆接机械的传感和控制系统,提高铆接工艺的可靠性和稳定性。
此外,在铆钉铆接机械的先进传感技术与智能控制研究中,值得关注的是无线传感技术和云计算技术的应用。
电动铆钉枪的工作原理及应用领域探析

电动铆钉枪的工作原理及应用领域探析电动铆钉枪作为一种现代化的工具,在各个领域有着广泛的应用。
它能够快速、高效地完成铆接任务,大大提高了生产效率和质量。
本文将对电动铆钉枪的工作原理和应用领域进行深入探析,以便更好地了解这一工具的运作机制和使用范围。
首先,我们来了解电动铆钉枪的工作原理。
电动铆钉枪是利用电动机驱动,通过连续打击和压力,将铆钉牢固地固定在工件上。
其工作原理主要包括以下几个步骤:1. 供电:将电动铆钉枪插入电源,接通电源开关,使电动机得到电能供应。
2. 转动电动机:当电流通过电动机的线圈时,产生磁场,使电动机的转子旋转。
转子上的曲轴带动铆钉枪的动力头进行往复运动。
3. 挤出铆钉:当电动铆钉枪的动力头接触到工件上的铆钉时,通过往复运动的压力,将铆钉挤出铆接工件的一侧。
在运动过程中,铆钉头在被压迫的情况下扩展并形成垫圈。
4. 使铆钉固定:在铆钉挤出并形成垫圈后,电动铆钉枪的动力头继续施加压力,使铆钉牢固地固定在工件上。
电动铆钉枪的工作原理简单而高效,操作方便。
它本质上是一种自动化工具,能够完成大量铆接任务,提高生产效率,减少人工劳动成本。
接下来,让我们来了解电动铆钉枪在各个领域的应用。
1. 汽车制造业:电动铆钉枪在汽车制造过程中起到重要作用。
它能够快速、准确地完成汽车骨架或车身零部件的铆接任务,提高生产效率和产品质量。
电动铆钉枪广泛地应用于车身制造、底盘组装、车门和车窗安装等环节。
2. 电子设备制造业:在电子设备制造过程中,电动铆钉枪被用来固定电路板和零部件。
它可以快速完成铆接任务,确保电路板和零部件之间的稳固连接,提高电子设备的可靠性和稳定性。
3. 航空航天工业:在航空航天工业中,电动铆钉枪被广泛用于飞机和航天器的制造和维护。
它能够完成飞机结构的铆接任务,保证飞机的安全性和可靠性。
电动铆钉枪可以快速完成对薄壁铝合金和复合材料的铆接任务,确保飞机的结构强度和轻量化。
4. 家具制造业:在家具制造过程中,电动铆钉枪被用来固定家具的零部件,如床架、椅背、桌脚等。
铆工技术的发展趋势与前景展望
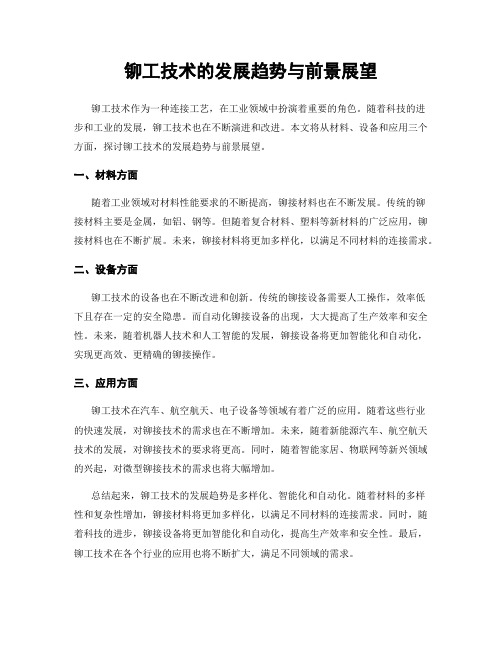
铆工技术的发展趋势与前景展望铆工技术作为一种连接工艺,在工业领域中扮演着重要的角色。
随着科技的进步和工业的发展,铆工技术也在不断演进和改进。
本文将从材料、设备和应用三个方面,探讨铆工技术的发展趋势与前景展望。
一、材料方面随着工业领域对材料性能要求的不断提高,铆接材料也在不断发展。
传统的铆接材料主要是金属,如铝、钢等。
但随着复合材料、塑料等新材料的广泛应用,铆接材料也在不断扩展。
未来,铆接材料将更加多样化,以满足不同材料的连接需求。
二、设备方面铆工技术的设备也在不断改进和创新。
传统的铆接设备需要人工操作,效率低下且存在一定的安全隐患。
而自动化铆接设备的出现,大大提高了生产效率和安全性。
未来,随着机器人技术和人工智能的发展,铆接设备将更加智能化和自动化,实现更高效、更精确的铆接操作。
三、应用方面铆工技术在汽车、航空航天、电子设备等领域有着广泛的应用。
随着这些行业的快速发展,对铆接技术的需求也在不断增加。
未来,随着新能源汽车、航空航天技术的发展,对铆接技术的要求将更高。
同时,随着智能家居、物联网等新兴领域的兴起,对微型铆接技术的需求也将大幅增加。
总结起来,铆工技术的发展趋势是多样化、智能化和自动化。
随着材料的多样性和复杂性增加,铆接材料将更加多样化,以满足不同材料的连接需求。
同时,随着科技的进步,铆接设备将更加智能化和自动化,提高生产效率和安全性。
最后,铆工技术在各个行业的应用也将不断扩大,满足不同领域的需求。
展望未来,铆工技术将继续发展壮大,成为工业领域中不可或缺的连接技术。
随着科技的进步和工业的发展,铆工技术将不断创新和改进,为各个行业提供更高效、更可靠的连接解决方案。
同时,铆工技术的发展也将推动相关产业链的发展,带动经济增长和就业机会的增加。
总之,铆工技术的发展前景广阔,将在材料、设备和应用方面不断创新和进步。
我们有理由相信,铆工技术将在未来的工业领域中发挥更加重要的作用,为工业发展和社会进步做出贡献。
自动铆接机的原理

上海途博技术研究中心
上海途博技术研究中心 /technology 自动铆接机的原理,自动铆接机是采用冷碾铆接的原理,利用铆杆对铆钉局部加压,并绕中心连续摆动直到铆钉成形的铆接设备。
该设备采用电动与气动、液压相结合的原理,完成各种所需形式的铆接。
铆接机逐渐取代了锤铆、冲压等落后工艺,成为体现企业加工能力、提高产品加工质量、提高生产效率的新型设备。
源通铆接机设备结构紧凑、运行平稳、性能稳定、成本低、效率高。
铆接工件时无冲击,铆后工件无弯曲、鼓肚、墩粗等不良变形。
自动铆接机加工质量高,铆接表面光滑平整。
设备无振动、低噪音、低功耗,操作安全简单。
可安装于大型自动生产线中,易于实现自动化。
可铆接材料:各种碳钢、铜、铝、金、银等金属材料,可塑性玻璃、塑料、陶瓷等非金属材料适用行业:铆接设备可应用于机械、电子、五金等各个行业,特别适用于各种机械零部件加工、五金制品、汽车摩托车配件、高低压电气、电动工具、仪器仪表等行业。
特殊加工:铆接机除正常的立铆外,还可实现倒铆、勾铆、弯铆、对铆、卧铆等各种形式的铆接。
另外还可实现多头铆接、多点铆接与悬臂铆接。
铆接知识点总结大全
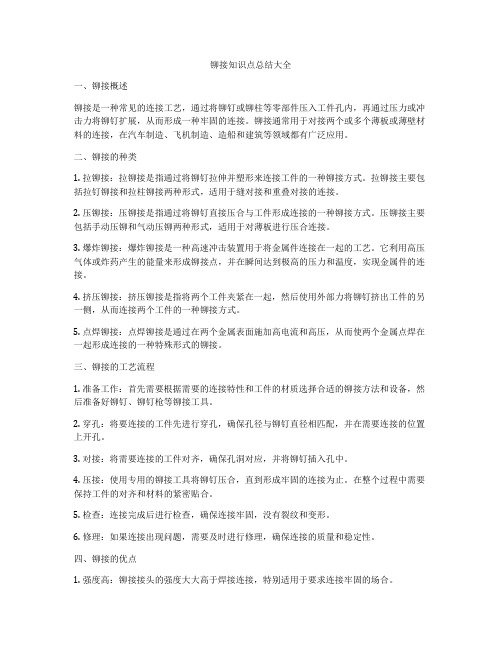
铆接知识点总结大全一、铆接概述铆接是一种常见的连接工艺,通过将铆钉或铆柱等零部件压入工件孔内,再通过压力或冲击力将铆钉扩展,从而形成一种牢固的连接。
铆接通常用于对接两个或多个薄板或薄壁材料的连接,在汽车制造、飞机制造、造船和建筑等领域都有广泛应用。
二、铆接的种类1. 拉铆接:拉铆接是指通过将铆钉拉伸并塑形来连接工件的一种铆接方式。
拉铆接主要包括拉钉铆接和拉柱铆接两种形式,适用于缝对接和重叠对接的连接。
2. 压铆接:压铆接是指通过将铆钉直接压合与工件形成连接的一种铆接方式。
压铆接主要包括手动压铆和气动压铆两种形式,适用于对薄板进行压合连接。
3. 爆炸铆接:爆炸铆接是一种高速冲击装置用于将金属件连接在一起的工艺。
它利用高压气体或炸药产生的能量来形成铆接点,并在瞬间达到极高的压力和温度,实现金属件的连接。
4. 挤压铆接:挤压铆接是指将两个工件夹紧在一起,然后使用外部力将铆钉挤出工件的另一侧,从而连接两个工件的一种铆接方式。
5. 点焊铆接:点焊铆接是通过在两个金属表面施加高电流和高压,从而使两个金属点焊在一起形成连接的一种特殊形式的铆接。
三、铆接的工艺流程1. 准备工作:首先需要根据需要的连接特性和工件的材质选择合适的铆接方法和设备,然后准备好铆钉、铆钉枪等铆接工具。
2. 穿孔:将要连接的工件先进行穿孔,确保孔径与铆钉直径相匹配,并在需要连接的位置上开孔。
3. 对接:将需要连接的工件对齐,确保孔洞对应,并将铆钉插入孔中。
4. 压接:使用专用的铆接工具将铆钉压合,直到形成牢固的连接为止。
在整个过程中需要保持工件的对齐和材料的紧密贴合。
5. 检查:连接完成后进行检查,确保连接牢固,没有裂纹和变形。
6. 修理:如果连接出现问题,需要及时进行修理,确保连接的质量和稳定性。
四、铆接的优点1. 强度高:铆接接头的强度大大高于焊接连接,特别适用于要求连接牢固的场合。
2. 耐腐蚀:由于铆接不涉及加热过程,因此接头处不会出现氧化、软化等问题,具有很好的耐腐蚀性。
- 1、下载文档前请自行甄别文档内容的完整性,平台不提供额外的编辑、内容补充、找答案等附加服务。
- 2、"仅部分预览"的文档,不可在线预览部分如存在完整性等问题,可反馈申请退款(可完整预览的文档不适用该条件!)。
- 3、如文档侵犯您的权益,请联系客服反馈,我们会尽快为您处理(人工客服工作时间:9:00-18:30)。
自动化铆接
1.自动化铆接技术的发展与运用
1.1自动化铆接技术的发展
自动钻铆技术从70年代起就在国外普遍采用,其发展一直未曾间断。
国外目前生产中的军、民用飞机的自动钻铆率分别达到了17%和75%以上,大量采用无头铆钉干涉配合技术,新型紧固件包括无头和冠头铆钉、钛环槽钉、高锁螺栓、锥形螺栓以及各种单面抽钉等,80%的铆接和100%的不可卸传剪螺栓连接均采用干涉配合,而且孔壁还要进行强化。
波音民机的壁板机铆系统已达60%~75%,麦道军机也已达17.5%,但是真正的全自动钻铆还需要解决工件定位和校平问题。
近年来,铆接正向着机器人和包含机器人视觉系统、大型龙门式机器人、专用柔性工艺装备、全自动钻铆机和坐标测量机组成的柔性自动化装配系统发展。
如B767、B777采用了翼梁自动装配系统,提高效率14倍,费用降低90%,废品率降低50%。
进一步的改进可使钻铆工具能够到达以前难以达到的部位。
随着高性能飞机对铆接质量和可靠性要求的不断提高,一般的手工钻孔,铆接已越来越不能满足要求。
采用自动化铆接技术不仅能提高装配效率,降低成本,改善劳动条件,而且能保证装配质量。
1.2自动化铆接技术的应用
自动化铆接铆接适合于钢板。
不锈钢板。
铝板及非金属夹层的连
接。
用无铆钉连接的典型零件有:车顶窗、保险杠、排气管、油箱、制动器罩壳、车门、仪表框架、发动机支架、发动机罩壳、车尾盖板、冷却器、座椅、摇窗机、消声器、冰箱门、洗衣机壳体、风机壳体、复印机机座、计算机壳体、牙医机外壳等等。
目前,自动钻铆技术已经在世界上所有的大飞机制造公司得到广泛运。
以美国格鲁门NGCAD公司为例,在波音757尾段机身48段双曲度壁板壁板均采用了自动钻铆技术,占了整个装配铆接工作量的85%。
1.3自动化铆接技术的特点
1.连接点牢固可靠。
2.没有原料消耗和不需要辅助材料。
3.超越了金属材质局限和厚度局限。
4.可以形成圆点和巨型点连接。
5.连接区域没有热应力。
6.不会损伤工件表面的保护层。
7.不需要预先或事后处理,允许有夹层和多层连接。
8.工作环境好,没有灰尘毒烟排放,没有噪音。
9.操作简单、消耗低、维修费少。
但是真正的全自动铆接还需要解决工件定位和校平的问题。
近年来,铆接正向大型自动化装配系统发展。
2.自动化铆接技术的机理
自动钻铆技术是指在装配过程中自动完成装配件的定位,夹紧,钻孔,涂胶,送钉,铆接等工作。
自动钻铆机是利用冲压机设备和专用连接模具通过一个瞬间强高压加工过程,依据板件本身材料的冷挤压变形,形成一个具有一定抗拉和抗剪强度的无应力集中内部镶嵌圆点,即可将不同材质不同厚度的两层或多层板件连接起来。
自动化铆接对板件表面无任何要求,连接点处板件表面原有的镀层、漆层不受损伤。
连接过程自动化程度高,可单点或多点同时连接,能进行无损伤连接强度检测及全过程自动监控,生产效率高。
无铆钉连接技术是一种逐步取代传统落后连接工艺的新型连接方法。
图1.1自动化铆接过程
3.自动化铆接工艺流程
3.1系统工作流程
1.根据任务的要求,做好工作准备,首先开机后对系统进行自检,包括检查机器人的工作模式和通讯连接设备,各传感器的连接检查,末端执行器和电主轴复位检查,各输油输气管道检查以及机器人工作空间安全检查,判断系统是否一切正常,不正常则排除故障,然后再返回自检模式下重新检测待一切正常后,进行下一步工作。
2.结合工装重构信息,机器人自身状态,机器人转站定位信息以及外环境状态,对整个系统工作参数进行配置。
3.机器人定位到原站进行复位,在控制系统中导入测试程序,然后将机器人系统定位到测试区域进行试加工,并在加工完成后,检查加工质量,如不满足质量要求,则根据质量检测结果,修正加工参数,如满足质量要求,进行下一步。
4.导入离线加工程序,对程序进行预处理,如:词法,语法,超程,译码等工作,并在工件上打点测试代码运行。
5.正式运行程序,对加工定位点进行精度补偿,根据精度补偿后的定位点坐标进行机器人定位。
6.机器人调整到位后,末端执行器开始执行加工任务,包括加工,进给,制孔,钻孔,工位切换,铆接,涂胶,润滑,排屑等操作。
7.在线检查加工质量。
图1.2自动钻铆过程
3.2自动钻铆工艺装备
自动铆接机的GEMCOR公司研制的8坐标,9坐标和压铆力的全自动钻铆机,钻铆速度达到每分钟12-14个铆钉,压力达到23t。
自动钻铆机需与相应的托架系统配套,才能发挥自动钻铆技术的优势。
托架系统主要用来进行装配件的定位和夹持,加大尺寸及复杂的架构,尤其是大型飞机机身和机翼壁板,双曲度壁板的自动钻铆,需要配备全自动托架系统以实现工件的自动定位和调平。
外形较平直的中小尺寸的壁板,翼肋等结构大多配置手动,半自动托架系统。
目前用于钻铆的机器人有三种类型,即柔性轨道机器人,自主爬行机器人和工业机械臂,其中最为常见的是工业机械臂。
常见的工业机械臂上安装一个末端执行器和视觉定位系统,就可以在空间进行打孔;自主爬行机器人是指在一些大型工件上自主爬行或者可以在飞机表面爬行到一定位置吸附,经定位系统定位后,操作末端执行器进行打孔;柔性机器人由机器人,视觉定位系统,执行末端组成。
4.铆接质量检测
精密检测与测量技术是自动化铆接的核心之一。
检测的方法主要有手工检测,离线检测和在线检测。
手工检测利用塞规,极限量规,比较样板等标准测量具;离线检测利用三坐标测量机,视觉系统等;在线检测利用先进的传感器和检测技术,与系统高度集成化,可有效提高加工精度。
钻铆质量的检测主要包括:制孔法向,钻孔深度,各层材料厚度,制孔厚度,孔径,孔间接,孔排距等信息。
ONCE(One sided cell end effect)系统的鼻头装置中,利用三个激光传感器组成集成法向传感器,可对壁板法向进行测量反馈和实时法向找正;可选配标准孔探测器,利用标准两点式球头直接贴合产品,可进行孔径,孔度轮廓,钻孔深度反馈,夹层厚度轮廓反馈等检测,孔径精度可以达到+-0.03mm,钻孔深度精度可以达到+-0.02mm,可以检测0-90度的孔度轮廓。
德国宝捷的自动钻铆系统中,先通过网络,温度和负载的精度补偿提高机器人空间定位精度,再通过安装在末端执行器上的激光传感器加上机器人第三轴的摆动,用来测量临时铆钉,孔和边缘等几何特征,测量结果也用于坐标转换,以补偿实际产品的位置和方向。
洛克希德-马丁公司用大型龙门式钻铆系统对F-35飞机复合材料
机翼壁板的钻铆。
该系统它使用激光跟踪仪进行定位,配合电磁马达和压力脚进行精密钻孔,满足F-35的气动和耐久性的要求。
瑞典隆德大学研究的机器人钻铆系统,应用激光跟踪仪与执行器上手持式探针结合,进行孔的精确定位。
80年代中期后,这种以工作站为基础的CAD/CAM系统发展很快,其功能达到甚至超过小型机CAD/CAM系统。
可以预见,这种系统将成为CAD/CAM系统的主流。
这种系统的制造厂商只提供硬件和系统软件,而应用软件则由其它专门开发软件的公司研制和销售。
近年来在我国市场上销售这类产品的公司有IBM公司、HP公司、SUN公司、DEC、公司、SGI公司等,产品的种类很多,各有特点。
由于微型计算机的性能和价格比的提高,目前以PC386486为主机的CAD/CAM系统不断增加。
该系统的特点是容量小,处理速度慢,但价格十分便宜,应用软件丰富,便于学习和维护。
另外还可以进入网络系统共享资源,并可以替代工作站完成一部分CAD/CAM作业,很适合中、小型企业和刚开始应用CAD/CAM技术的单位。
我国在CAD/CAM技术方面的研究开始于70年代中期,当时主要是研究开发二维绘图软件,并利用绘图机输出二维图形。
主要研究单位是高等学校。
航空和造船工业是应用CAD/CAM技术较早的部门。
80年代初,有些大型企业和设计院成套引进CAD/CAM系统(主要是Turnkey System)在此基础上进行开发和应用,取得了一定的成果。
随着改革开放和发展商品经济的需要,在80年代中后期,我国的CAD/CAM技术有了较大的发展,而且CAD/CAM 技术的优点被越来越多的人所注意。
进入90年代后,各工业部门普遍提出了开发CAD/CAM技术的计划,主要表现在以下几个方面:部分单位已较好地应用CAD/CAM技术,提高设计质量,取得了经济效益;CAD/CAM
技术的理论和软件开发进行了大量的研究,并取得了成果(如清华大
学、浙江大学、西北工业大学、北京航空航天大学、中科院计算所等)。
进入90年代后,国家科委、各工业部门都十分重视CAD/CAM技术的发展,并有计划、有步骤地在全国各地CAD/CAM培训基地,对有关人员CAD/CAM技术方面的培训,以提高有关人员CAD/CAM素质。
与此同时,有些工业部门还对所属单位提出应用CAD/CAM技术的具体要求。