齿轮类零件加工工艺分析及夹具方案
直齿圆柱齿轮工艺及夹具设计

直齿圆柱齿轮工艺及夹具设计对于直齿圆柱齿轮的工艺设计,首先需要进行齿轮的结构设计,确定齿轮的模数、齿数、压力角等参数。
然后,根据齿轮的类型和尺寸,选择合适的加工工艺。
一般情况下,直齿圆柱齿轮的加工工艺包括车削、铣削和磨削等过程。
下面,我将分别介绍这些工艺的具体步骤。
1.车削加工:车削是直齿圆柱齿轮加工的主要方法之一、车削加工需要使用齿轮车削机,通过将刀具沿齿轮的螺旋线进行切削来加工齿轮齿面。
车削加工的关键是确定好刀具的进给量和切削速度,以保证齿轮齿面的质量和精度。
2.铣削加工:铣削是直齿圆柱齿轮加工的另一种常用方法。
铣削加工需要使用齿轮铣床,通过将刀具沿齿轮的齿廓进行切削来加工齿轮齿面。
铣削加工通常采用刀具分多次切削的方式,以提高加工效率和保证齿轮齿面的质量。
3.磨削加工:磨削是直齿圆柱齿轮加工的最后一道工序。
磨削加工需要使用齿轮磨床,通过将砂轮沿齿轮的齿廓进行磨削来加工齿轮齿面。
磨削加工可以大大提高齿轮的精度和光洁度,达到高精密要求。
除了工艺设计,夹具设计也是直齿圆柱齿轮加工中不可忽视的一环。
夹具的设计应根据齿轮的类型和尺寸来确定,以确保齿轮在加工过程中的稳定性和精度。
常见的齿轮夹具包括顶夹具、侧夹具和中心夹具等。
在夹具设计过程中,需要考虑夹紧力、夹紧方式、夹紧面形状等因素,以提高夹具的稳定性和工作效率。
综上所述,直齿圆柱齿轮的工艺及夹具设计对于保证齿轮加工质量和提高生产效率至关重要。
在工艺设计中,需要选择合适的加工工艺,并控制好加工参数,以确保齿轮的精度和光洁度。
在夹具设计中,需要根据齿轮的类型和尺寸,设计合理的夹具结构和夹紧方式,以提高夹具的稳定性和工作效率。
机械工艺夹具毕业设计77齿轮架零件的机械加工工说明书

毕业设计设计题目:齿轮架零件的机械加工工艺规程及专用夹具设计机械设计及自动化专业学生姓名:起讫日期:指导老师:目录一设计目的及要求 (1)二设计任务 (1)三对零件工作图的分析 (2)四选择毛坯 (3)五确定表面加工方案 (4)六选择定位基准 (6)七拟订加工工艺路线 (6)八确定加工余量 (8)九选择工艺装备 (9)十夹具设计要求 (11)十一夹紧力的计算 (11)十二夹具零件的选择 (12)十三选择切削用量及切削力 (14)十四确定工时定额 (15)十五小结 (15)十六参考书 (17)一设计目的及要求1、目的:机械制造技术基础是以机械制造工艺技术设备为主要内容的技术科学,是机械类专业的一门主要课程,具有很强的实践性。
因此在完成了理论教学和实践教学后,还需要对学生进行机械零件加工工艺设计的实际训练,使学生通过工艺设计获得综合运用所学过的全部相关课程(如机械制造技术基础,互换性及技术测量,金属学与热处理学)进行零件工艺及结构设计的基本能力,能根据被加工零件的技术要求,运用夹具设计的基本原理和方法,学会拟订夹具设计方案,完成夹具结构设计,初步具备设计出高效、省力、经济合理并能保证加工质量的专用夹具的能力,培养学生熟悉并运用有关手册、标准、图表等技术资料的能力,进一步培养学生识图、制图、运算和编写技术文件等基本技能。
2、要求:○1掌握编制机械加工工艺规程的方法,能正确解决中等复杂程度零件在加工中的工艺问题。
○2根据已学的知识,提高结构设计的能力,通过设计夹具的训练,根据被加工零件要求,设计出能保证加工技术要求,经济、高效的工艺装备。
○3认真复习设计有关的知识,并查阅有关的资料,手册让学生会使用与机械加工工艺和工装设计有关的手册及图纸资料。
二设计任务:设计题目:设计齿轮架零件的机械加工工艺规程及专用夹具设计。
生产纲领:一般为500-5000件(中批)具体设计工作内容:1、抄绘,分析零件的工作图,图幅为A3。
齿轮类零件加工工艺分析及夹具设计
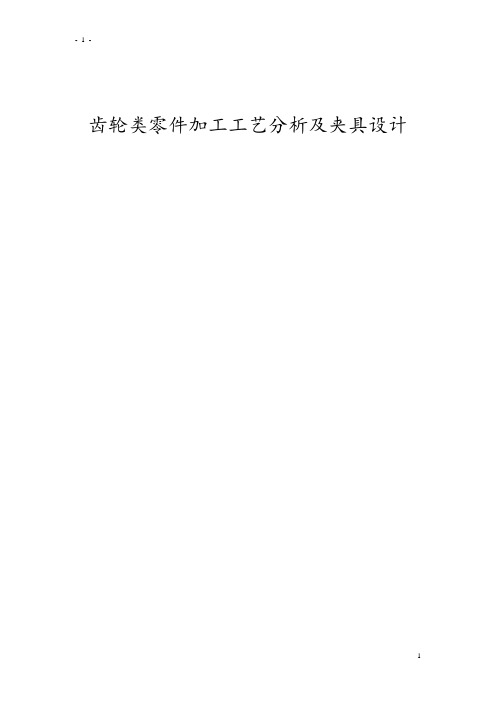
齿轮类零件加工工艺分析及夹具设计目录摘要 (4)第一章齿轮类零件加工工艺规程编制概述 (5)1.1工艺编制的总体步骤 (5)第二章对齿轮类零件的加工工艺编制及分析 (6)2.1分析齿轮类零件的技术要求 (6)2.2明确毛坯尺寸 (8)2.3拟定工艺路线 (8)2.4设计工序内容 (10)2.5填写工艺文件 (10)第三章对齿轮类零件加工工艺进行合理性分析 (11)第四章夹具设计的要求 (11)4.1 了解夹具设计的总体要求 (11)第五章夹具设计的特点 (12)5.1确定夹具的类型 (12)5.2钻模的主要类型 (12)第六章工件夹紧计算及选择 (13)6.1工件的夹紧 (13)6.2 夹紧力的选择 (13)6.3夹紧力的计算及精度分析 (14)第七章夹具的结构分析及设计 (16)7.1夹具的夹紧和定位 (16)7.2夹具的导向 (17)第八章夹具的总体分析 (17)第九章致谢 (18)摘要齿轮类零件是典型零件之一,它在机械主要用于传动,齿轮类零件主要有齿轮.齿轮轴,涡轮涡杆,在机械领域运用很广泛。
按传动形式分圆柱类齿轮、锥齿轮、齿条等。
按齿形状分:齿轮、齿、字齿等。
按制作方法分:铸造齿轮、烧结齿轮、轧制齿轮等。
我以齿轮加工工艺编制分析齿轮的加工要求,在生产实际中阐述齿轮的工艺过程,及工艺的合理性。
夹具在机械加工中有举足轻重的作用,好的夹具才是保障零件加工的方法。
我从夹具的分析、设计、计算、使用方面概述夹具的用途。
按专业化程度可分为通用夹具、专用夹具、可调夹具、组合夹具、成组夹具、标准夹具、随行夹具、组合机床夹具等。
我这次设计的是盖板式钻夹具。
这是一种专用夹具,专为一工件的一道工序而设计的夹具。
关键词:齿轮、夹具、工艺、设计1.1工艺编制的总体步骤1.分析零件的结构和技术要求(1)分析图样资料①加工工艺表面的尺寸精度和形状精度②各加工表面之间以及加工表面和不加工表面之间的位置精度③加工表面的粗糙度及表面的其他要求④热处理及其他要求(2)零件的结构工艺分析。
齿轮齿条零件机械加工工艺规程及专用夹具设计
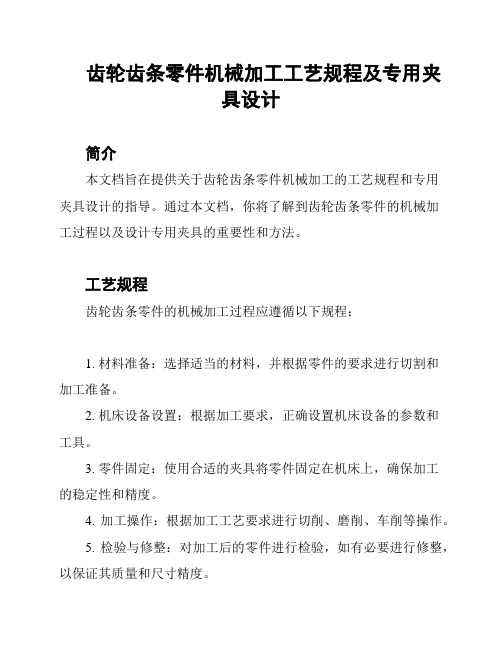
齿轮齿条零件机械加工工艺规程及专用夹具设计简介本文档旨在提供关于齿轮齿条零件机械加工的工艺规程和专用夹具设计的指导。
通过本文档,你将了解到齿轮齿条零件的机械加工过程以及设计专用夹具的重要性和方法。
工艺规程齿轮齿条零件的机械加工过程应遵循以下规程:1. 材料准备:选择适当的材料,并根据零件的要求进行切割和加工准备。
2. 机床设备设置:根据加工要求,正确设置机床设备的参数和工具。
3. 零件固定:使用合适的夹具将零件固定在机床上,确保加工的稳定性和精度。
4. 加工操作:根据加工工艺要求进行切削、磨削、车削等操作。
5. 检验与修整:对加工后的零件进行检验,如有必要进行修整,以保证其质量和尺寸精度。
6. 表面处理:根据需要,对零件进行表面处理,如镀铬、镀锌等。
专用夹具设计设计合适的专用夹具是确保齿轮齿条零件机械加工过程的关键。
下面是一些设计专用夹具的重要原则和方法:1. 夹具类型选择:根据零件的形状和加工要求,选择合适的夹具类型,如平面夹具、圆形夹具等。
2. 夹具定位:确保夹具能够准确地定位零件,以保证加工的精度和一致性。
3. 夹具固定:夹具的固定方式应牢固可靠,能够承受加工过程中的力和振动。
4. 夹具材料选择:选择适当的夹具材料,具有足够的强度和耐磨性,同时尽量避免对零件表面的损伤。
5. 夹具调试与测试:在使用之前,对夹具进行调试和测试,确保夹具的性能和可靠性。
总结本文档介绍了齿轮齿条零件机械加工的工艺规程和专用夹具设计的重要性。
通过遵循正确的工艺规程和合理设计专用夹具,可以提高加工效率和质量,确保零件的尺寸精度和稳定性。
齿轮泵泵体加工工艺与专用夹具设计

Φ18孔和2×Φ12孔。
底面为基准的加工面,主要加工左端面和2×G1/4的中心线和左端面为基右端面,2个小侧面。
零件的生产类型一般是根据工件或者产品的每年的零件的年生产纲领计算公式如下:(1)机床夹具的复杂程度和零件的加工质量。
定位基准可分为粗基准、精基准和辅助基准。
3.1粗基准的选择生产类型零件生产纲领/(件/年)重型零件中型零件轻型零件单件生产小批生产中批生产大批生产大量生产<55~100100~300300~1000>1000<1010~200200~500500~5000>5000<100100~500500~50005000~50000>50000表1生产纲领和生产类型图2泵体零件图图1齿轮泵实体图泵盖销泵体纸垫泵盖填料螺塞螺钉齿轮齿轮①我们通常用某个加工余量比较均匀一点的和十分要紧的表面零件的粗基准。
②那些我们暂时不用加工的表面,我们的粗基面选用当中精度要求较高的表面。
③一般选光滑、干净、平整面作粗基准面,不能有飞边、刮痕、缺口、裂痕等特别明显的缺陷。
④如果我们用毛坯表面做粗基准时,通常最好就用一次,因为毛坯表面是比较粗糙的,这样导致了定位误差比较大,会影响零件的加工精度的。
⑤以工件比较容易装夹为原则,夹紧机构尽量简单,操作尽量方便。
3.2精基准的选择“互为基准,反复加工”原则;③加工工艺过程如表5专用夹具设计5.1夹具体的设计夹具体是夹具的基础部件。
所需要的各种装置,重要。
夹具体设计时应满足以下要求:①应该有足够大的刚度和强度。
②稳定加工尺寸。
③便于排屑。
④夹具通常来说是单件生产的,图3泵体零件毛坯简图5.3铣床夹具的总体设计该夹具主要是确定定位:底面是采用两个支承板,限定了三个自由度,Y 和Z 方向的旋转,X 方向的移动,右面ϕ32mm 圆柱端面用一个支承钉限定一个Y 方向的移动自由度,顶面用V 型块限定Z 方向的移动和X 方向的旋转自由度,这样就限定了六个自由度,满足了六点定位原理,工件在夹具中合理定位;再就是夹紧,选择两个侧面面作为夹紧面,采用铰链机构,螺钉和压板夹紧,可人为的调紧调松,用V 形块压板夹紧顶端圆弧部分,选择辅助支撑用来减少加工时工件的震动,确保夹紧机构夹紧可靠。
屈文平:齿轮零件的机械加工工艺过程及及进行滚齿加工用的夹具设计

齿轮零件的机械加工工艺过程及进行滚齿加工用的夹具设计第一部份齿轮零件的机械加工工艺过程1、定位基准的选择在零件的加工过程中,合理的选择定位基准对保证零件的尺寸精度和位置度有着决定性的作用。
根据工件加工要求确定工件应限制的自由度数后,某一方向自由度的限制往往会有几个定位基准可选择,则提出了如何正确选择定位基准的问题。
定位基准有粗基准和精基准之分。
1.1. 粗基准的选择原则:(1)尽量选择不要求加工的表面作为粗基准.这样可使加工表面与不加工表面之间的位置误差量最小,同时还可以在一次装夹中加工出更多的表面。
(2)若零件的所有表面都要加工,应选择加工余量和公差最小的表面作为粗基准.这样可保证作为粗基准的表面在加工时,余量均匀。
(3)选择光洁、平整、面积足够大、装夹稳定的表面作为粗基准。
(4)粗基准一般只在第一到工序中用,以后应避免重复使用。
1.2.精基准的选择原则:基准重合的选择原则。
尽可能的用设计基准作为定位基准,这样可避免因定位基准与设计基准不重合而引起的定位误差,以保证加工表面与设计基准间的位置精度。
基准同一原则.一尽可能多的表面加工都用同一个定位基准,这样有利于保证各加工面之间的位置精度。
选择面积大、精度较高、安装稳定的表面作为精基准,而且所选的基准使夹具结构简单,装夹和加工方便。
综合上面的粗基准和精基准的选择原则,为使基准同一和基准重合,齿轮加工时常选内孔和端面作为精基准加工外圆和齿轮,用作精基准的端面和内孔要在一次装夹中加工出来以保证两者之间的垂直度,但是在加工大型齿轮时可用外圆作找正基准,但此时应保证内孔与外圆同轴。
所以加工本设计齿轮用齿轮外圆和端面作为粗基准,用内孔和端面作为精基准。
2.、装夹方法在加工齿轮时在滚齿机上一般用心轴装夹,滚齿心轴夹具3.、加工工艺问题(1)、基准修正齿形表面淬火后,内孔会受到影响而变形:一般的孔直径会缩小0.01-0.05mm,因此淬火后应安排精基准修正工序.修正的方法有推孔和磨孔,也可以用镗孔。
齿轮零件的机械加工工艺过程及进行滚齿加工用的夹具设计方案

重庆大学网络教育学院毕业设计<论文)题目齿轮零件的机械加工工艺过程及进行滚齿加工用的夹具设计学生所在校外学习中心重庆学习中心批次层次专业092机械设计制造及自动化学号学生指导教师起止日期20180909-201810242018年10月齿轮零件的机械加工工艺过程及进行滚齿加工用的夹具设计摘要齿轮作为机械设备中的传动、控速、换向、变向的必要构件和设备,其设计和加工制作工艺决定着整个机械行业的发展进度。
机床夹具是在金属切削过程中,用以准确的确定工件位置,并将其牢固的夹紧,以接受加工的工艺装备。
为了保证工件的加工质量,提高加工效率,减轻工人的劳动强度,充分发挥和扩大机床的工艺性能。
因此,本次我们针对齿轮零件的机械加工工艺和流程提出了该设计理念。
本文针对齿轮在切机床上的加工工艺要求和具体流程,从定基、装夹、加工到设备的选用,均有深入研究。
其次,针对滚齿加工时使用的夹具和滚齿液压波形胀紧夹具设计采用的夹紧原理,通过不断实践深入分析,并对生产模型进行模拟。
并配合CAD、Pro/Engineer等辅助设计软件来实现整个设计过程。
完成了齿轮机械加工工艺的全部过程分析和与其配套的机床夹具研究,包括定基、加工、设备的选用分析和原理分析等,本文设计的齿轮生产方式,基本可以满足工程需要,本文使用的设计方法,也可为同类夹具的设计提供参考。
关键词:齿轮;加工工艺;夹紧原理;夹具设计目录1 绪论41.1本课题研究的背景和意义41.2国内外相关研究情况51.3本课题研究的相关情况61.4本课题的研究方法62 齿轮零件的机械加工工艺72.1定位基准的选择72.1.1粗基准的选择原则72.1.2精基准的选额原则82.1.3辅助基准的应用102.2装夹方法102.2.1压板、螺丝、V 型架、垫块组合102.2.2 采用502胶水粘合112.2.3 磁性吸盘吸附122.3加工工艺问题162.3.1基准修正162.3.2齿轮加工方案162.3.3热处理的安排182.3.4制定工艺路线192.3.5选择加工设备及刀具202.3.6加工工序设计253 滚齿加工用的夹具设计273.1夹紧原理简介273.2夹具设计284 滚齿液压波形胀紧夹具设计314.1夹紧原理简介314.2夹具设计321 绪论1.1本课题研究的背景和意义机械工程是以有关的自然科学和技术科学为理论基础,结合在生产实践中积累的技术经验,研究和解决在开发设计、制造、安装、运用和修理各种机械中的理论和实际问题的一门应用学科。
齿形轴零件机械加工工艺过程及加工用夹具设计
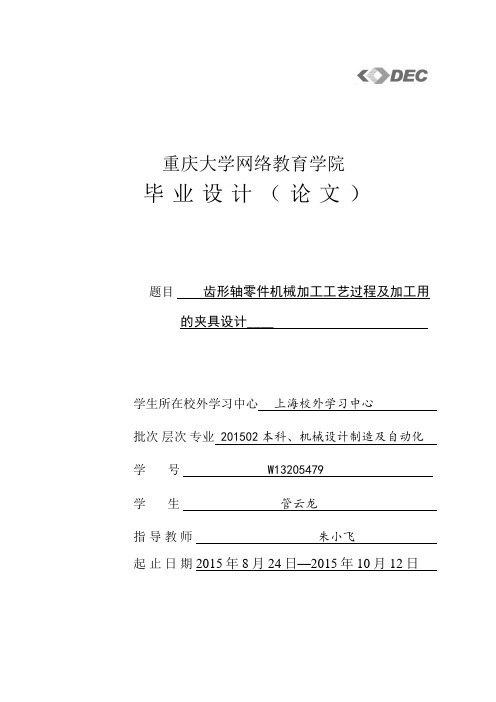
重庆大学网络教育学院毕业设计(论文)题目齿形轴零件机械加工工艺过程及加工用的夹具设计____学生所在校外学习中心上海校外学习中心批次层次专业201502本科、机械设计制造及自动化学号W13205479学生管云龙指导教师朱小飞起止日期 2015年8月24日—2015年10月12日摘要齿轮轴零件的主要作用是支撑回转零件、实现回转运动并传递转矩和动力。
齿轮轴具备传动效率高、结构紧凑和使用寿命长等一系列优点,是通用机械特别是工程机械传动中的重要零件之一。
齿轮轴加工材料、热处理方式、机械加工工艺过程的优化,将对提高齿轮轴的加工质量及寿命有着重要借鉴意义。
本文对某设备中“齿轮轴”零件进行了机械制造工艺规程设计和加工用的夹具设计。
对于工艺规程设计和夹具设计制订了两套不同的方案,从中甄选出最佳方案。
本设计首先分析了齿轮轴零件的作用和加工工艺性,然后进行工艺规程设计,最后是加工用夹具设计。
齿轮轴零件的机械综合性能要求较高,一般选择锻件作为毛坯。
合理安排工艺路线,划分加工阶段对保证零件加工质量至关重要。
使用夹具可以缩短辅助时间,提高劳动生产率,保证加工精度,稳定加工质量,降低对工人的技术要求,扩大机床工艺范围。
本文对所设计的专用夹具进行了精度校核和定位误差分析,对夹具的设计质量也进行了评估。
关键词:齿轮轴;工艺分析;工艺规程设计;夹具设计目录摘要 (2)1 设计背景及目的 (4)2生产纲领及生产类型的确定 (4)3 零件的分析 (5)4 选择毛坯 (5)5 工艺规程设计 (6)5.1 定位基准选择 (6)5.2 零件的加工方法的选择 (6)5.3 定制工艺路线 (6)5.4 确定机械加工的余量及毛坯尺寸,设计毛坯-零件综合图 (7)6 工序设计 (9)6.1 选择加工设备工艺装备 (9)6.2 工序尺寸的确定及计算 (10)6.3 选择切削用量,确定时间定额 (11)7 滚齿用夹具设计 (13)7.1 拟定滚齿夹具的结构方案 (13)7.2 确定刀具的导向方式或对刀装置 (14)7.3 夹具精度的计算 (14)7.4 夹具总图(图4) (15)7.5 夹具零件图(图5、图6) (16)8 课题小结 (17)1 设计背景及目的在我们学完了大学的全部基础课程、技术课程及全部专业课程之后进行的。
- 1、下载文档前请自行甄别文档内容的完整性,平台不提供额外的编辑、内容补充、找答案等附加服务。
- 2、"仅部分预览"的文档,不可在线预览部分如存在完整性等问题,可反馈申请退款(可完整预览的文档不适用该条件!)。
- 3、如文档侵犯您的权益,请联系客服反馈,我们会尽快为您处理(人工客服工作时间:9:00-18:30)。
齿轮类零件加工工艺分析及夹具设计学校:襄阳职业技术学院系院:汽车工程学院班级:机械设计与制造1002姓名:曾凯指导老师:黄贞贞目录摘要 (4)第一章齿轮类零件加工工艺规程编制概述 (5)1.1工艺编制的总体步骤 (5)第二章对齿轮类零件的加工工艺编制及分析 (6)2.1分析齿轮类零件的技术要求 (6)2.2明确毛坯尺寸 (8)2.3拟定工艺路线 (8)2.4设计工序内容 (10)2.5填写工艺文件 (10)第三章对齿轮类零件加工工艺进行合理性分析 (11)第四章夹具设计的要求 (11)4.1 了解夹具设计的总体要求 (11)第五章夹具设计的特点 (12)5.1确定夹具的类型 (12)5.2钻模的主要类型 (12)第六章工件夹紧计算及选择 (13)6.1工件的夹紧 (13)6.2 夹紧力的选择 (13)6.3夹紧力的计算及精度分析 (14)第七章夹具的结构分析及设计 (16)7.1夹具的夹紧和定位 (16)7.2夹具的导向 (17)第八章夹具的总体分析 (17)第九章致谢 (18)摘要齿轮类零件是典型零件之一,它在机械主要用于传动,齿轮类零件主要有齿轮.齿轮轴,涡轮涡杆,在机械领域运用很广泛。
按传动形式分圆柱类齿轮、锥齿轮、齿条等。
按齿形状分:齿轮、齿、字齿等。
按制作方法分:铸造齿轮、烧结齿轮、轧制齿轮等。
我以齿轮加工工艺编制分析齿轮的加工要求,在生产实际中阐述齿轮的工艺过程,及工艺的合理性。
夹具在机械加工中有举足轻重的作用,好的夹具才是保障零件加工的方法。
我从夹具的分析、设计、计算、使用方面概述夹具的用途。
按专业化程度可分为通用夹具、专用夹具、可调夹具、组合夹具、成组夹具、标准夹具、随行夹具、组合机床夹具等。
我这次设计的是盖板式钻夹具。
这是一种专用夹具,专为一工件的一道工序而设计的夹具。
关键词:齿轮、夹具、工艺、设计1.1工艺编制的总体步骤1.分析零件的结构和技术要求(1)分析图样资料①加工工艺表面的尺寸精度和形状精度②各加工表面之间以及加工表面和不加工表面之间的位置精度③加工表面的粗糙度及表面的其他要求④热处理及其他要求(2)零件的结构工艺分析。
零件的结构工艺是指所设计的零件在满足性能的要求下,制造的经济性和可行性,包括整个工艺过程,有毛坯制作、切削加工、装配及维修等工艺。
2.明确毛坯的状况(1)零件的材料及热处理,零件应根据不同工作条件和使用要求选不同的材料和热处理方式,以获得一定的强度、韧性及耐磨性。
(2)毛坯的形状和尺寸的确定(3)毛坯的选用3.拟定工艺路线(1)确定加工方案(2)划分加工工段(3)选择定位基准(4)加工顺序4.设计工序内容(1)确定余量,工序尺寸及其公差(2)选择设备及工装5.填写工艺卡完成以上工作后,按要求填写工序卡片2.齿轮类零件加工工艺编制及分析2.1分析齿轮类零件的结构特点和技术要求齿轮加工的过程由若干个工序组成,为了获得符合精度要求的齿轮,齿形加工是整个加工的关键。
以直齿圆柱齿轮工艺为例。
如下图:齿轮的加工方法很多,按加工中有无切削,可分为有切削和无切削加工两大类。
其中无切削加工有:热轧齿轮、冷轧齿轮、精煅等新工艺。
切削加工有:成形法、展成法。
(1)齿轮类零件的结构特点和技术要求①圆柱齿轮的结构特点,按加工角度分圆柱齿轮分,为轮体和齿圈两部分分,按轮齿的分布形式分直齿、斜齿、人字齿等等。
②圆柱齿轮的精度要求根据齿轮的使用要求,对齿轮传动油以下几方面的要求:A.运动精度,传动比恒定,要求齿轮在转一圈时,转角误差不超过一定的范围。
B.工作平稳性,要求齿轮运动平稳,冲击,振动和噪声小C.载荷分布均匀性,为了不致因载荷分布不均匀使接触应力过大,引起齿面早起磨损,要求齿面接触要均匀,并保证一定的接触面积和接触位置。
D.合理的齿侧间隙,要求齿轮在传动时,要有一定的齿侧间隙。
(2)分析结构和技术要求。
如图示,运动精度为7级,主要是公法线变动公差为Fw为0.0 036mm,径向公差为0.08mm,传动平稳性等级为6级,表面粗糙的为Ra1.6μm,端面与轴线有垂直度要求,齿轮表面需淬火,齿部硬度为52-54HRC.2.2明确毛坯尺寸(1)齿轮的材料与毛坯根据齿轮的工作条件和失效形式,制造齿轮的齿轮有锻钢、铸钢,铸铁,特殊情况时有有色金属和非金属材料。
(2)齿轮的毛坯形式主要有棒料,锻件和铸件(3)齿轮的热处理,齿轮粗加工前常安排预热处理,其目的是改善加工性能。
本零件可运用正火,正火可以消除内应力,提高强度和韧性,改善加工性能,齿轮毛坯正火一般在粗加工之前。
正火处理后的硬度为160—220HBW。
2.3拟定加工工艺路线根据齿轮材质和热处理要求,齿轮结构和尺寸大小,精度要求,生产批量和车间设备条件而定,一般工艺路线如下:毛坯制造→毛坯热处理→齿坯加工→齿形加工→齿圈热处理→齿轮定位表面热处理→齿圈的精整加工(1)确定加工方案A.齿坯加工:齿形加工中,主要保证基准孔的尺寸精度,位置精度,基准端面相对于基准孔的位置精度。
齿形的公差及表面粗糙度如下表:B.齿形加工:齿形加工一般采用滚齿,插齿,对于8级以下可以直接加工,6—7齿轮采用剃→垳齿,该齿轮采用滚齿,该齿轮的精加工采用剃→垳齿(2)划分加工阶段齿轮的加工工艺阶段可分为:毛坯制造,毛坯热处理,齿坯加工,齿形加工,齿端加工,齿面热处理,齿轮定位表面精加工,齿形精加工。
(3)选择定位基准A.以内孔和端面定位:确定齿轮中心和轴向位置,并采用面向端面的夹紧方式。
使设计基准,装配基准,测量基准重合,又使齿形加工等工序统一。
B,以外圆和端面定位:工件和夹具心轴间隙大时,采用千分表找正中心的方法;从另一端夹紧,也可以找正。
(4)加工顺序安排:工艺路线:毛坯制造→正火→齿轮毛坯粗,精车→滚齿→齿圈淬火→齿轮定位表面内锥孔磨削→垳齿2.4设计工序内容A.确定工序尺寸,粗车各端面,外圆,内孔按图样加工尺寸每部留1.5mm余量;精加工,内锥孔磨削和垳齿加工到图样规定尺寸,满足其技术要求。
B.选择设备工装,C6132,CA6140,滚齿机齿轮加工夹具,心轴,节圆专用夹具2.5填写工艺文件(如下表)3对齿轮类零件加工工艺进行合理性及加工成本进行分析A.严格安照了典型零件加工的工艺过程进行工艺编制,条例清晰,五大步骤,路线明确B.遵循了基准重合,基准统一原则,在2.3(3)选择定位基准时,以内孔和端面定位,这种方式可使定位基准、设计基准、装配基准、测量基准重合,又能够使齿形加工等工序基准统一。
提高了定位精度。
C.严格按照了先粗后精、先主后次的加工工序安排。
D.科学有序的安排工艺,合理的安排了工时,运用普通机床,减少了成本。
4夹具设计的要求1)夹具应满足零件加工工序的精度要求。
特别对于精加工工序,应适当提高夹具的精度,以保证工件的尺寸公差和形状位置公差等。
2)夹具应达到加工生产率的要求。
特别对于大批量生产中使用的夹具,应设法缩短加工的基本时间和辅助时间。
3)夹具的操作要方便、安全。
按不同的加工方法,可设置必要的防护装置、挡屑板以及各种安全器具。
4)能保证夹具一定的使用寿命和较低的夹具制造成本。
夹具元件的材料选用将直接影响夹具的使用寿命。
因此,定位元件以及主要元件宜采用力学性能较好的材料。
在大批量生产中。
宜采用气压、液压等高效夹紧装置;而小批量生产,则宜采用较简单的夹具结构。
5)要适当提高夹具元件的通用化和标准程度。
选用标准化元件,特别应选用商品化的标准元件,以缩短夹具制造周期,从而降低夹具成本。
6)必须具有良好的结构工艺性,以便夹具的制造、使用和维修。
以上要求有时是互相矛盾的,故应在全面考虑的基础上,处理好主要矛盾,使之达到较好的效果。
5夹具设计的特点5.1确定夹具的类型按使用范围,夹具可分为通用夹具和专用夹具两类。
通用夹具适用于各种不同尺寸的零件加工,如导尺、分度盘等。
这类夹具是作为附件与机床一起配套供应的。
专用夹具是专门为某一工件在某一工序进行加工而设计的夹具,如在铣床上加工弯曲零件必须采用相应的夹具5.2钻模的主要类型钻床专用夹具一般通称为“钻模”。
可按钻模有无夹具体,以及夹具体是否可动,而分为下面几类:A.固定式钻模这种钻模在使用时,是被固定在钻床工作台。
用于在立轴式钻床上加工较大的单孔或在摇臂钻床上加工平行孔系。
这种加工方式的钻孔精度比较高。
B.回转式钻模回转式钻模主要用于加工同一圆周面上的平行孔系,或分布在圆周上的径向孔。
C.翻转式钻模主要用于加工小型工件不同表面上的孔。
使用翻转式钻模可减少工件装夹的次数,提高工件上各孔之间的位置精度6.工件夹紧计算及选择6.1 工件的夹紧6.1.1夹紧基本原理理论夹紧的目的是保证工件在夹具中的定位,不致因工时受切削力,重力或伴生离心力,惯性力,热应力等的作用产生移动或振动。
夹紧装置是夹具完成夹紧作用的一个重要的而不可以缺少的组成部分,除非工件在加工过程中所受到的各种力不会使它离开定位时所需确定的位置,才可以设有夹紧装置。
设计夹紧装置时,应满足下述主要要求:[2]A.夹紧装置在对工件夹紧时,不应破坏工件的定位,为此,必须正确选择夹紧力的方向及着力点。
B.夹紧力的大小应该可靠,适当,要保证工件在夹紧后的变形和受压表面的损伤不致超出允许的范围。
C.夹紧装置结构简单合理,夹紧动作要迅速,操作方便省力,安全。
D.夹紧力或夹紧行程在一定范围内可进行调整和补偿6.2夹紧力的选择A.夹紧力方向在保证安装的真确可靠,减少工件的变形,定位方便和在可以减少所需夹紧力的大小的前提下,夹具的夹紧方向和工件重力方向和切削方向相同。
B.夹紧力的作用点夹紧力的作用点是指夹紧元件与工件相接触的一小块面积。
现在夹紧力的方案已定。
考虑夹具的结构尺寸特征可以确定夹紧力的作用点个数为2个。
考虑夹紧力作用点的一般要求:①夹紧力的作用点应能保持工件定位稳定,而不至引起工件发生位移和偏转;②夹紧力的作用点,应使被夹紧的夹紧变形尽可能的小些;③夹紧力的作用点应尽可能靠近加工表面,以提高定位稳定性。
6.3夹紧力的计算及精度分析夹紧力的大小重要取决于切削P和重力G,重力是可认为不变的,而切削力在切削的过程中是变化的。
影响切削力的大小因素很多,如工件质量的不均匀,加工质量的不均匀,刀具磨损以及切削用量的变化等等。
工件的加工误差:造成表面位置的加工误差包括下列四方面:1)△A——夹具位置误差,即定位元件相对机床的切削成形运动的位置误差。
△A1——定位元件定位面对夹具体基面的误差;△A2——夹具的安装连接误差。
2)△D——定位误差,即由定位引起的工序基准的位置误差。
3)△T——刀具相对夹具的位置误差,即对刀导向误差。
4)△G——与加工过程中一些因素有关的加工误差。
包括机床误差、刀具误差以及工艺系统的受力变形(如夹紧误差)、热变形、磨损等因素造成的加工误差。