摩擦与磨损
摩擦与磨损

表面摩擦与磨损一、摩擦与磨损的定义摩擦的定义是:两个相互接触的物体在外力的作用下发生相对运动或者相对运动趋势时,在切相面见间产生切向的运动阻力,这一阻力又称为摩擦力。
磨损的定义是:任一工作表面的物质,由于表面相对运动而不断损失的现象。
据估计消耗在摩擦过程中的能量约占世界工业能耗的30%。
在机器工作过程中,磨损会造成零件的表面形状和尺寸缓慢而连续损坏,使得机器的工作性能与可靠性逐渐降低,甚至可能导致零件的突然破坏。
人类很早就开始对摩擦现象进行研究,取得了大量的成果,特别是近几十年来已在一些机器或零件的设计中考虑了磨损寿命问题。
在零件的结构设计、材料选用、加工制造、表面强化处理、润滑剂的选用、操作与维修等方面采取措施,可以有效地解决零件的摩擦磨损问题,提高机器的工作效率,减少能量损失,降低材料消耗,保证机器工作的可靠性。
二、摩擦的分类及评价方法在机器工作时,零件之间不但相互接触,而且接触的表面之间还存在着相对运动。
从摩擦学的角度看,这种存在相互运动的接触面可以看作为摩擦副。
有四种摩擦分类方式:按照摩擦副的运动状态分类、按照摩擦副的运动形式分类、按照摩擦副表面的润滑状态分类、按照摩擦副所处的工况条件分类。
这里主要以根据摩擦副之间的状态不同分类,摩擦可以分为:干摩擦、边界摩擦、流体摩擦和混合摩擦,如图2-1所示。
图2-1 摩擦状态1、干摩擦当摩擦副表面间不加任何润滑剂时,将出现固体表面直接接触的摩擦(见图2-1a),工程上称为干摩擦。
此时,两摩擦表面间的相对运动将消耗大量的能量并造成严重的表面磨损。
这种摩擦状态是失效,在机器工作时是不允许出现的。
由于任何零件的表面都会因为氧化而形成氧化膜或被润滑油所湿润,所以在工程实际中,并不存在真正的干摩擦。
2 、边界摩擦当摩擦副表面间有润滑油存在时,由于润滑油与金属表面间的物理吸附作用和化学吸附作用,润滑油会在金属表面上形成极薄的边界膜。
边界膜的厚度非常小,通常只有几个分子到十几个分子厚,不足以将微观不平的两金属表面分隔开,所以相互运动时,金属表面的微凸出部分将发生接触,这种状态称为边界摩擦(见图2-1b)。
摩擦、磨损简介

摩擦、磨损简介磨损基本概念磨损是零部件失效的一种基本类型。
通常意义上来讲,磨损是指零部件几何尺寸(体积)变小。
零部件失去原有设计所规定的功能称为失效。
失效包括完全丧失原定功能;功能降低和有严重损伤或隐患,继续使用会失去可靠性及安全性和安全性。
1、磨损的分类:按照表面破坏机理特征,磨损可以分为磨料磨损、粘着磨损、表面疲劳磨损、腐蚀磨损和微动磨损等。
前三种是磨损的基本类型,后两种只在某些特定条件下才会发生。
磨料磨损:物体表面与硬质颗粒或硬质凸出物(包括硬金属)相互摩擦引起表面材料损失。
粘着磨损:摩擦副相对运动时,由于固相焊合作用的结果,造成接触面金属损耗。
表面疲劳磨损:两接触表面在交变接触压应力的作用下,材料表面因疲劳而产生物质损失。
腐蚀磨损:零件表面在摩擦的过程中,表面金属与周围介质发生化学或电化学反应,因而出现的物质损失。
微动磨损:两接触表面间没有宏观相对运动,但在外界变动负荷影响下,有小振幅的相对振动(小于100μm),此时接触表面间产生大量的微小氧化物磨损粉末,因此造成的磨损称为微动磨损2、表征材料磨损性能的参量为了反映零件的磨损,常常需要用一些参量来表征材料的磨损性能。
常用的参量有以下几种:(1)磨损量由于磨损引起的材料损失量称为磨损量,它可通过测量长度、体积或质量的变化而得到,并相应称它们为线磨损量、体积磨损量和质量磨损量。
(2)磨损率以单位时间内材料的磨损量表示,即磨损率I=dV /dt (V为磨损量,t为时间)。
(3)磨损度以单位滑移距离内材料的磨损量来表示,即磨损度E=dV/dL (L为滑移距离)。
(4)耐磨性指材料抵抗磨损的性能,它以规定摩擦条件下的磨损率或磨损度的倒数来表示,即耐磨性=dt/dV或dL/dV。
(5)相对耐磨性指在同样条件下,两种材料(通常其中一种是Pb-Sn合金标准试样)的耐磨性之比值,即相对耐磨性εw=ε试样/ε标样。
摩擦基本概念当物体与另一物体沿接触面的切线方向运动或有相对运动的摩擦趋势时,在两物体的接触面之间有阻碍它们相对运动的作用力,这种力叫摩擦力。
摩擦、磨损和润滑
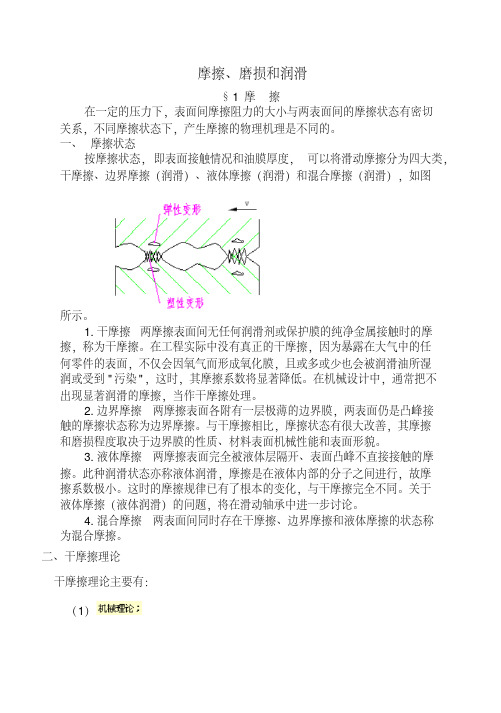
摩擦、磨损和润滑
§1 摩擦
在一定的压力下,表面间摩擦阻力的大小与两表面间的摩擦状态有密切关系,不同摩擦状态下,产生摩擦的物理机理是不同的。
一、摩擦状态
按摩擦状态,即表面接触情况和油膜厚度,可以将滑动摩擦分为四大类,干摩擦、边界摩擦(润滑)、液体摩擦(润滑)和混合摩擦(润滑),如图
所示。
1.干摩擦两摩擦表面间无任何润滑剂或保护膜的纯净金属接触时的摩
擦,称为干摩擦。
在工程实际中没有真正的干摩擦,因为暴露在大气中的任何零件的表面,不仅会因氧气而形成氧化膜,且或多或少也会被润滑油所湿润或受到"污染",这时,其摩擦系数将显著降低。
在机械设计中,通常把不出现显著润滑的摩擦,当作干摩擦处理。
2.边界摩擦两摩擦表面各附有一层极薄的边界膜,两表面仍是凸峰接
触的摩擦状态称为边界摩擦。
与干摩擦相比,摩擦状态有很大改善,其摩擦和磨损程度取决于边界膜的性质、材料表面机械性能和表面形貌。
3.液体摩擦两摩擦表面完全被液体层隔开、表面凸峰不直接接触的摩
擦。
此种润滑状态亦称液体润滑,摩擦是在液体内部的分子之间进行,故摩擦系数极小。
这时的摩擦规律已有了根本的变化,与干摩擦完全不同。
关于液体摩擦(液体润滑)的问题,将在滑动轴承中进一步讨论。
4.混合摩擦两表面间同时存在干摩擦、边界摩擦和液体摩擦的状态称
为混合摩擦。
二、干摩擦理论
干摩擦理论主要有:
(1)。
摩擦和磨损的联系

摩擦和磨损的联系一、摩擦和磨损的基本概念及关系摩擦力是指两个接触物体相对运动时出现的阻力,而磨损是指固体表面在相对运动或接触过程中,由于摩擦力所引起的物质的消耗和形貌的变化。
摩擦和磨损密切相关,两者之间存在着紧密的联系。
本文将对摩擦和磨损的关系进行全面深入的探讨。
二、摩擦对磨损的影响1. 摩擦对磨损程度的影响摩擦力的大小直接决定了磨损的程度。
当两个物体之间的摩擦力增大时,磨损程度也会相应增加。
摩擦力的大小与物体间的相互作用力、表面粗糙度以及润滑情况等因素密切相关。
2. 摩擦对磨损方式的影响摩擦力的作用下,可以产生不同的磨损方式。
当两个物体间的摩擦力较小时,可能会出现微小的磨粒,造成表面磨损;当摩擦力增大时,可能会出现表面剥蚀、刮伤等更为明显的磨损方式。
3. 摩擦对磨损速率的影响摩擦力的大小还会直接影响磨损速率。
摩擦力越大,物体表面的材料消耗速度越快,磨损速率也会相应增加。
因此,在工程设计中需要合理控制摩擦力的大小,以减缓磨损速率,延长材料的使用寿命。
三、磨损对摩擦的影响1. 磨损对摩擦力的影响磨损会造成物体表面的不平整,增加了摩擦力的大小。
磨损表面的粗糙度会显著影响摩擦力的大小。
当物体表面经过长时间的磨损后,摩擦力可能会大幅增加,从而对摩擦产生重大影响。
2. 磨损对摩擦过程的影响磨损会改变物体表面的形貌和材料特性,从而对摩擦过程产生影响。
磨损会使物体表面变得粗糙,增加了接触面积,改变了摩擦系数。
此外,磨损还会引起表面的氧化、硬质颗粒剥离等现象,进一步改变了摩擦过程的特性。
3. 磨损对摩擦耐磨性能的影响磨损会降低物体的摩擦耐磨性能。
物体经过长时间的磨损后,表面会变得疲劳、龟裂、掉屑等,从而降低了摩擦耐磨性能。
因此,在工程设计中需要充分考虑材料的磨损特性,选择具有较高耐磨性的材料,以提高摩擦耐磨性能。
四、如何减少摩擦和磨损1. 合理润滑润滑是减少摩擦和磨损的重要手段之一。
润滑可以在物体表面形成一层保护膜,减少摩擦力的大小,降低磨损程度。
第四章 摩擦、磨损及润滑概述
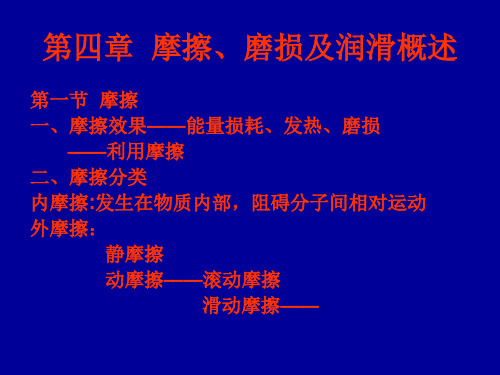
第四章 摩擦、磨损及润滑概述
第一节 摩擦 一、摩擦效果——能量损耗、发热、磨损
——利用摩擦 二、摩擦分类 内摩擦:发生在物质内部,阻碍分子间相对运动 外摩擦:
静摩擦 动摩擦——滚动摩擦
滑动摩擦——
1.干摩擦 机械传动中不允许
2.边界摩擦 边界油膜(十层分子厚度仅 为0.02μm),金属突峰接触,摩擦系数0.1 左右
油温 3.疲劳磨损(点蚀) 提高表面硬度、减小粗糙度值和控制接触应
力
4.流体体磨粒磨损、流体侵蚀磨损
流动所夹带的硬物质引起的机械磨损,管道 磨损
流体冲蚀作用引起的机械磨损,燃汽轮机叶 片、火箭发动机尾喷管的磨损。
5.腐蚀磨损
机械化学磨损是指由机械作用及材料与环境 的化学作用或电化学作用共同引起的磨损
2.流体静力润滑 3.弹性流体动力润滑 λ>3~4 4.边界润滑 5.混合润滑
1.如图所示,在 情况下,两相对运动的平 板间粘性流体不能形成油膜压力。
2.摩擦副接触面间的润滑状态判据参数膜厚 比值λ为 时,为混合润滑状态,值λ为 时,可达到流体润滑状态。
A.6.25; B. 1.0;C. 5.2; D. 0.35。
λ≤1——边界摩擦
λ>3——流体摩擦
1≤λ≤3——混合摩擦
第二节 磨损 一、磨损过程 ——磨合、 稳定磨损、 剧烈磨损。 二、磨损分类 1.磨粒磨损 开式齿轮传动 合理选择材料,提高表面硬度
2.粘着磨损 ——轻微磨损、胶合、咬死
齿轮传动、蜗杆传动滑动轴承等 合理选择摩擦副材料、润滑剂,限制压力和
3.各种油杯中, 可用于脂润滑。
A.针阀式油杯;B.油绳式油杯;C.旋盖式油杯。
4.为了减轻摩擦副的表面疲劳磨损,下列措施中, 是不合理的
摩擦与磨损

咬死
粘着强度高,粘着面积大,剪切应力小,粘接点焊合 而使相对运动受阻。
• 1、摩擦:摩擦是机器运转过程中不可避免的物理现象。
•
世界上1/3~1/2的能源消耗在摩擦上。
• 力求维持液体润滑;
• 最低要维持边界润滑和混合润滑;
• 避免出,现干摩擦。
• 2、磨损:各种机械零件因磨损失效的占全部失效零件的一半
1 什么叫摩 擦副
2 按接触状 态,摩擦 分为几类?
3 机件磨损 的三个阶 段
4 磨损的机 理
摩擦
一、摩擦 1.定义:两物体接触区产生阻碍运动并消耗能量的现象,称 为摩擦。有些情况下却要利用摩擦工作,如车辆行驶,带 传动,摩擦制动器等。 2.摩擦副:相互摩擦的两个物体。
二、摩擦表面 相互运动零件配合表面的摩擦、磨损与摩擦表面的形貌、
摩擦和磨损状况优于固体 摩擦,但比液气体摩擦差。
磨损 一、磨损的概念
• 定义:摩擦副的表面物质,在摩擦的过程中逐渐损失, 使其尺寸、形状和位置精度及表面层性质发生改变的 现象,称为磨损。
• 形成:摩擦导致机件表面材料逐渐损耗,形成磨损。 • 磨损会影响机器的精度,降低工作的可靠性,甚至促
使机器提前报废。 • 但是有时也会利用磨损有利的一面,比如精加工中的
• 实现良好磨合的措施: • A、能很好地保证润滑油的品质和润滑油连续 充足地供给。 • B、有合适的负荷与运转时间分配。一般原则
是:转速、负荷由小到大,先升速后加负荷。
• C、摩擦表面的加工粗糙度应适当。
磨损的类型
按磨损的机理分类
粘着磨损 磨料(粒)磨损 疲劳磨损 冲蚀磨损 腐蚀磨损
定义
特征 影响因素
表面层的结构和性能有关。
摩擦和磨损

(1)力学性能的影响 陶瓷材料所固有的脆性是导致其磨损的主要原因。
20世纪80年代Evans公式,与陶瓷材料的硬度、断裂 韧性和弹性模量等力学性能与其磨损特性联系起来:
H式为中硬,度V;为磨α损为体与材积料;无W关为的载常荷数;;KIEC为为断弹裂性韧模性量;; L为滑行距离。
响,对于脆性较大的材料如工具钢、白口铁、
陶瓷等必须考虑裂纹在犁沟和材料磨损中的
作用。
图1-32a表示断裂韧性对各种材料耐磨 性的影响。图1-32 b表示当考虑材料硬度和 载荷强度影响时断裂韧性与耐磨性之间的关 系。当硬度逐渐下降而断裂韧性逐渐增加 时,耐磨性也逐渐增加,到极大值后,随着 硬度的下降和断裂韧性的增加,耐磨性反而 逐渐下降。峰值的右边材料其耐磨性与断裂 韧性无关,而左边的材料在磨损时必须考虑 到断裂韧性的影响。
摩擦表面热诱导相变密切相关,这种相变是 表面温度的函数,而摩擦表面温度又受环境 温度、滑行速度及摩擦系数的影响。在不同 条件下可能诱发T M相变或T C相变,这两 种相变的影响截然不同。
b.热致化学反应。在摩擦过程中,摩擦升温 和滑行速度的变化可能导致陶瓷表面发生化 学反应,从而影响其摩擦学性能。研究表 明,热致化学反应对陶瓷摩擦磨损性能的影 响主要取决于不同表面膜的生成。这种化学 反应同时依赖于温度和滑行速度等。
(a).
(b) .
图1-32 各种材料的断裂韧性与耐磨性的关系
(a). 断裂韧性对各种材料耐磨性的影响;
(b). 考虑材料硬度和载荷强度影响时断裂
韧性与耐磨性之间的关系
3)基体显微组织
在磨粒磨损时多相材料和磨粒的接触有
重要影响。多相组织中弥散相的体积百分
数,分布特点,弥散相和基体的结合性质,
摩擦和磨损

固体摩擦
• 分为干摩擦和边界摩擦 • 摩擦副在直接接触时产生的摩擦称为干摩 擦。 • 在摩擦副间施加润滑剂后,摩擦副的表面 吸附一层极薄的润滑膜,这种摩擦状态称 为边界摩擦。
液(气)体摩擦
• 在摩擦副间施加润滑剂后,摩擦副的表面 被一层具有一定压力和厚度的流体润滑膜 完全隔开时的摩擦,称为液(气)体摩擦。 • 说明:这种摩擦理论上不产生磨损,是一 种理想的摩擦状态。
混合摩擦
• 兼有固体摩擦和液(气)体摩擦中两种摩 擦状态以上的一种摩擦状态。
作业
• • • • 1、摩擦定义。 2、摩擦是如何分类的? 3、什么是干摩擦? 4、什么是混合摩擦?
一、摩擦定义
• 1、摩擦是指两物体的接触表面阻碍它们相对运动 的机械阻力。 • 2、摩擦副: • 相互摩擦的两个物体称为摩擦副。 • 3、分类: • 根据摩擦副的运动状态分为静态、临界、动态、 惯性摩擦。 • 根据摩擦副的运动形式分为滑动和滚动摩擦。 • 根据摩擦副的摩擦状态分为固体摩擦、液(气) 体摩擦、混合摩擦。
摩擦和磨损
1、熟记摩擦和磨损定义 2、理解摩擦和磨损分类 3、掌握摩擦和磨损应用与危害。 4• • • • 1、人们行走时,在光滑的 地面上行走十分困难,这是 因为接触面摩擦太小的缘故; 2、汽车上坡打滑时,在路面 上撒些粗石子或垫上稻草, 汽车就能顺利前进,这是 靠增大粗糙程度而增大摩 擦力。