10 Quality Control Guide from GE Plastics Design Guide
质量控制和保证中英版

Quality Assurance and Control质量保证和质量控制MICHAEL C. VANDERZWANPharmaceutical Technical, Roche Pharmaceuticals, Basel, SwitzerlandI. Introduction介绍. . . . . . . . . . . . . . . . . . . . . . . . . . . 235II. Defining and Assuring the Quality of the Active Pharmaceutical Ingredient 原料药质量的定义和保证. . . . . . . . . . . . . . . . . . 240III. The Regulations for Quality 质量监管. . . . . . . . . . . . . . . . . 245IV. The Quality Control and Quality Assurance Department质量控制和质量保证. . . . . . . . . . . . . . . . .273Appendix A附录. . . . . . . . . . . . . . . . . . . . . . . . . . . 280目录I. INTRODUCTION介绍 (4)A. The Product产品 (4)B. The Process工艺 (5)C. The Facilities设备 (5)D. The People人员 (6)E. The Quality Management Department质量管理部门 (6)F. The Regulatory Authorities 监管机构 (7)G. The Regulations法规 (8)II. DEFINING AND ASSURING THE QUALITY OF THE ACTIVE PHARMACEUTICAL INGREDIENT 原料药质量的定义和质量保证 (9)A. Defining the API Quality 原料药质量的界定 (10)B. Testing the API for Its Defined Attributes 原料药定义的属性测试 (11)C. Designing Quality into the Process 工艺中的质量设计 (12)D. Validation of the Process 工艺验证 (13)E. Reality实际 (15)III. THE REGULATIONS FOR QUALITY质量法规 ................ 错误!未定义书签。
质量控制中英文对照
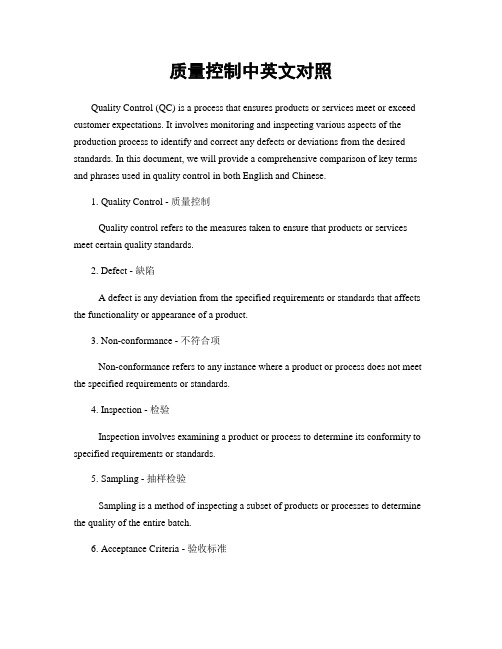
质量控制中英文对照Quality Control (QC) is a process that ensures products or services meet or exceed customer expectations. It involves monitoring and inspecting various aspects of the production process to identify and correct any defects or deviations from the desired standards. In this document, we will provide a comprehensive comparison of key terms and phrases used in quality control in both English and Chinese.1. Quality Control - 质量控制Quality control refers to the measures taken to ensure that products or services meet certain quality standards.2. Defect - 缺陷A defect is any deviation from the specified requirements or standards that affects the functionality or appearance of a product.3. Non-conformance - 不符合项Non-conformance refers to any instance where a product or process does not meet the specified requirements or standards.4. Inspection - 检验Inspection involves examining a product or process to determine its conformity to specified requirements or standards.5. Sampling - 抽样检验Sampling is a method of inspecting a subset of products or processes to determine the quality of the entire batch.6. Acceptance Criteria - 验收标准Acceptance criteria are the specified requirements or standards that a product or process must meet to be considered acceptable.7. Quality Assurance - 质量保证Quality assurance refers to the planned and systematic activities implemented in a quality system to ensure that products or services meet specified requirements.8. Statistical Process Control (SPC) - 统计过程控制SPC is a method of quality control that uses statistical techniques to monitor and control a process to ensure its stability and predictability.9. Root Cause Analysis - 根本原因分析Root cause analysis is a problem-solving technique used to identify the underlying causes of defects or non-conformances in order to prevent their recurrence.10. Corrective Action - 纠正措施Corrective action refers to the steps taken to eliminate the causes of non-conformances or defects and prevent their recurrence.11. Preventive Action - 预防措施Preventive action refers to proactive measures taken to prevent the occurrence of defects or non-conformances in the future.12. Quality Control Plan - 质量控制计划A quality control plan is a document that outlines the specific quality control activities, responsibilities, and procedures to be followed for a project or process.13. Quality Control Inspector - 质量控制检验员A quality control inspector is responsible for inspecting and testing products or processes to ensure they meet the specified requirements or standards.14. Quality Control Chart - 质量控制图A quality control chart is a graphical tool used to monitor and control a process by plotting data points over time to identify any trends or patterns.15. Quality Control Audit - 质量控制审核A quality control audit is a systematic examination of a quality control system to determine its effectiveness and compliance with specified requirements.16. Quality Control Manual - 质量控制手册A quality control manual is a document that provides guidelines and procedures for implementing and managing a quality control system.17. Quality Control Metrics - 质量控制指标Quality control metrics are measurable parameters used to assess the performance and effectiveness of a quality control system.18. Quality Control Training - 质量控制培训Quality control training refers to the process of providing employees with the necessary knowledge and skills to perform quality control activities effectively.以上是质量控制中英文对照的标准格式文本,详细介绍了与质量控制相关的关键术语和短语。
质量手册翻译中英文对照解析

质量手册翻译中英文术语表3.1.1 质量 quality3.1.2 要求 requirement3.1.3 等级 grade3.1.4 顾客满意 customer satisfaction3.1.5 能力 capability3.2.1 体系(系统) system3.2.2 管理体系 management system3.2.3 质量管理体系 quality management system 3.2.4 质量方针 quality policy3.2.5 质量目标 quality objective3.2.6 管理 management3.2.7 最高管理者 top management3.2.8 质量管理 quality management3.2.9 质量策划 quality planning3.2.10 质量控制 quality control3.2.11 质量保证 quality assurance3.2.12 质量改进 quality improvement3.2.13 持续改进 continual improvement3.2.14 有效性 effectiveness3.2.15 效率 efficiency3.3.1 组织 organization3.3.2 组织结构 organizational structure3.3.3 基础设施 infrastructure3.3.4 工作环境 '77ork environment 3.3.5 顾客 customer3.3.6 供方 supplier3.3.7 相关方 interested party3.4.1 过程 process3.4.2 产品 product3.4.3 项目 project3.4.4 设计和开发 design and development 3.4.5 程序 procedure3.5.1 特性 characteristic3.5.2 质量特性 quality characteristic 3.5.3 可信性 dependability3.5.4 可追溯性 traceability3.6.1 合格(符合) conformity3.6.2 不合格(不符合) nonconformity 3.6.3 缺陷 defect3.6.4 预防措施 preventive action3.6.5 纠正措施 corrective action3.6.6 纠正 correction3.6.7 返工 rework3.6.8 降级 regrade3.6.9 返修 repair3.6.10 报废 scrap3.6.11 让步 concession3.6.12 偏离许可 deviation permit3.6.13 放行 release3.7.1 信息 information3.7.2 文件 document3.7.3 规范 specification3.7.4 质量手册 quality manual3.7.5 质量计划 quality plan3.7.6 记录 record3.8.1 客观证据 objective evidence3.8.3 试验 test3.8.4 验证 verification3.8.5 确认 validation3.8.6 鉴定过程 qualification process3.8.7 评审 review3.9.1 审核 audit3.9.2 审核方案 audit programme3. 9.3 审核准则audit criteria3.9.4 审核证据 audit evidence3.9.5 审核发现 audit findings3.9.6 审核结论 audit conclusion3.9.7 审核委托方 audit client3. 9.8 受审核方 auditee3.9.9 审核员 auditor3.9.10 审核组 audit team3.9.11 技术专家 technical expert3.9.12 能力 competence3.10.1 测量控制体系 measurement control system 3.10.2 测量过程 measurement process3.10.3 计量确认 metrological confirmation3.10.4 测量设备 measuring equipment3.10.5 计量特性metrological characteristic 3.10.6 计量职能 metrological function Aaudit 3.9.1 审计audit client 3.9.7 客户审计audit conclusion 3.9.6 审计结论audit criteria 3.9.3 审计标准audit evidence 3.9.4 审计证据audit findings 3.9.5audit programme 3.9.2 审计大纲audit team 3.9.10 审计团队auditee 3.9.8auditor 3.9.9Ccapability 3.1.5characteristic 3.5.1concession 3.6.11conformity 3.6.1continual improvement 3.2.13 correction 3.6.6corrective action 3.6.5customer 3.3.5customer satisfaction 3.1.4 competence 3.9.12Ddefect 3.6.3dependability 3.5.3design and development 3.4.4 deviation permit 3.6.12document 3.7.2Eeffectiveness 3.2.14efficiency 3.2.15Ggrade 3.1.3Iinformation 3.7.1infrastructure 3.3.3inspection 3.8.2interested party 3.3.7Mmanagement 3.2.6management system 3.2.2 measurement control system 3.10.1 measurement process 3.10.2 measuring equipment 3.10.4 metrological characteristic 3.10.5 metrological confirmation 3.10.3 metrological function 3.10.6Nnonconformity 3.6.2Oobjective evidence 3.8.1 客观证据organization 3.3.1 organizational structure 3.3.2 Ppreventive action 3.6.4 procedure 3.4.5process 3.4.1product 3.4.2project 3.4.3Qqualification process 3.8.6 quality 3.1.1quality assurance 3.2.11quality characteristic 3.5.2 quality control 3.2.10quality improvement 3.2.12 quality management 3.2.8quality management system 3.2.3 quality manual 3.7.4quality objective 3.2.5quality plan 3.7.5quality planning 3.2.9 质量计划quality policy 3.2.4Rrecord 3.7.6 记录regrade 3.6.8release 3.6.13 放行repair 3.6.9requirement 3.1.2review 3.8.7rework 3.6.7 返工Sscrap 3.6.10specification 3.7.3supplier 3.3.6 供应商system 3.2.1 系统Ttechnical expert <audit> 3.9.11 技术出口test 3.8.3 测试top management 3.2.7 高层管理traceability 3.5.4 可塑性Vvalidation 3.8.5verification 3.8.4 验证Wwork environment 3.3.4 工作环境质量管理体系基础和术语 Quality management syst ems--Fundamentals and vocabulary质量管理和质量保证标准第2部分: GB/T 19001、GB /T 19002和GB/T 19003实施通用指南 Quality manag ement and quality assurance standards--Part 2: Generic guidelines for the application of GB /T 19001、GB/T 19002 and GB/T 19003质量管理和质量保证标准第3部分: GB/T 19001在计算机软件开发、供应、安装和维护中的使用指南 Qual ity management and quality assurance standards --Part 3: Guidelines for the application of G B/T 19001 to the development, supply, installat ion and maintenance of computer software质量管理和质量保证标准第4部分:可信性大纲管理指南 Quality management and quality assurance s tandards--Part 4: Guide to dependability prog ramme management质量管理体系要求 Quality management systems--Requirements质量管理体系业绩改进指南 Quality management sy stems--Guidelines for performance improvement s质量管理和质量体系要素第2部分: 服务指南 Quali ty management and quality system elements--Pa rt 2: Guidelines for services质量管理和质量体系要素第3部分: 流程性材料指南 Quality management and quality system elements --Guidelines for processed materials质量管理和质量体系要素第4部分: 质量改进指南 Q uality management and quality system elements--Guidelines for quality improvement质量管理质量计划指南 Quality management--Gui delines for quality plans质量管理项目管理质量指南 Quality management--Guidelines to quality in project management质量管理技术状态管理指南 Quality management--Guidelines for configuration management质量体系审核指南审核 Guidelines for auditing q uality systems--Part 1: Auditing质量体系审核指南质量体系审核员的评定准则 Guide lines for auditing quality systems--Part 2: Q ualification criteria for quality systems audit ors质量体系审核指南审核工作管理 Guidelines for au diting quality systems--Part 3: Management of audit programmes测量设备的质量保证要求第一部分: 测量设备的计量确认体系 Quality assurance requirements for mea suring equipment Part 1: Metrological confirmat ion system for measuring equipment测量设备的质量保证第2部分: 测量过程控制指南 Q uality assurance for measuring equipment--Par t 2: Guidelines for control of measurement proc esses质量手册编制指南 Guidelines for developing qual ity manuals质量经济性管理指南 Guidelines for managing the economics of quality质量管理培训指南 Quality management--Guideli nes for training English Chinesereceipt (入厂)接受,验收,进货handling 搬运packaging 包装storage 保存protection 保护comparison 比较identification 标识replacement of identification mark 标识标志更换maintenance of identification 标识的保持records of identification control 标识控制记录tender 标书normative document 标准文件supplemental 补充nonconforming product 不合格品control of nonconforming product 不合格品控制control procedure of nonconforming products 不合格品控制程序tendency of nonconformance 不合格倾向purchasing 采购verification of purchased product 采购的产品验证purchasing process 采购过程purchasing control procedure 采购控制程序purchasing information 采购信息reference standard 参照标准reference instructions 参照细则stockhouse 仓库measurement, analysis and improvement 测量,分析和改进measurement result 测量结果control procedure of monitoring and measuring d evices 测量设备控制程序planning 策划preservation of product 产品保护control procedure for maintenance, replacement and records of product identification 产品标识的保持, 更换和记录控制程序procedure for product identification and tracea bility 产品标识和可追溯性程序conformity of product 产品的符合性monitoring and measurement of product 产品的监督和测量product plan 产品方案control procedure for product preservation 产品防护控制程序method of product release 产品放行方法conformity of product, product conformity 产品符合性product realization 产品实现planning of product realization 产品实现策划product characteristics 产品特性input to product requirements 产品要求的输入product status 产品状态final acceptance of product 产品最后验收procedure 程序program documents 程序文件continual improvement 持续改进procedure for continual improvement of quality management system 持续改进质量体系程序adequacy 充分性storage location 存放地点agency personnel 代理人员submission of tenders 递交标书adjustment 调整,调节statutory and regulatory requirements 法律法规要求rework, vt 返工repair, vt 返修subcontractor 分承包方annex 附录improvement 改进improvement actions 改进措施on-the-job training 岗位技能培训responsibility of individual department and pos t 各部门, 各岗位职责change identification 更改标记change order number 更改单编号process sheets 工艺单process specification 工艺规程procedure(process card) 工艺规程(工艺卡) process characteristics 工艺特性Job Description Format 工种描述单work environment 工作环境impartiality 公正性functional requirements 功能要求supplier 供方supplier evaluation procedure 供方评价程序supplier provided special processes 供方提供的特殊过程verification at supplier's premises 供方现场验证supply chain 供应链criteria for supplier selection, evaluation and re-evaluation 供应商选择、评估和再评估准则communication 沟通customer 顾客customer property 顾客财产control procedure for customer property 顾客财产控制程序customer feedback 顾客反馈Customer Service Contact Form 顾客服务联系表customer communications 顾客沟通customer satisfaction 顾客满意statistical analysis of customer satisfaction 顾客满意度统计分析customer complaint 顾客投诉identification of customer requirements 顾客要求的识别management review 管理评审records from management review 管理评审记录management review control procedure 管理评审控制程序management representative 管理者代表management responsibility 管理职责specified limits of acceptability 规定的可接受界限specified use 规定的用途process 过程complexity of processes 过程的复杂性monitoring and measurement of processes 过程的监视和测量operation of process 过程的运行status of processes 过程的状态process approach 过程方法process controls 过程控制process control documents 过程控制文件process performance 过程业绩appropriateness 合适性changes to contractor 合同的更改contract review control procedure 合同评审控制程序internet sales 互联网销售environmental conditions 环境条件monogram pragram requirements 会标纲要要求type of activities 活动类型infrastructure 基础建设infrastructure 基础设施fundamentals and vocabulary 基础与词汇control of records 记录控制technical specificaion 技术规范process trace sheet 加工跟踪单monitoring and measurement 监视和测量monitoring and measuring device 监视和测量装置control of monitoring and measuring devices 监视和测量装置控制check method 检查方法frequency of checks 检查频次calibration status 检定状态inspection and test control procedure 检验和试验控制程序identification procedure for inspection and tes t status 检验和试验状态标识程序inspection witness point 检验见证点inspection hold point 检验停止点buildings 建筑物delivery 交付post-delivery activities 交付后的活动delivery activities 交付活动interface 接口acceptance of contract or orders 接受合同或定单type of medium 介质类型experience 经验correction action 纠正措施Corrective action response time 纠正措施答复时间,纠正措施响应时间management procedure for corrective actions 纠正措施管理程序corrective action response times 纠正措施响应时间development activity 开发活动traceability mark 可追溯性标志objectivity 客观性Customer Service Log 客户服务记录簿control feature 控制特性,控制细节control features 控制细则periodic assessment of stock 库存定期评估justification 理由routine 例程,惯例,常规质量职能分配表论证范围internal communication 内部沟通internal audit 内部审核internal audit procedure 内部审核程序internally controlled standard 内控标准internal audit 内审results of internal and external audits 内外部审核结果competence 能力training 培训training needs 培训需要evaluate 评价records of the results of the review 评审结果的记录review output 评审输出review input 评审输入Purchase Requisition 请购单authority 权限validation 确认concession 让步human resources 人力资源job training of personnel 人员岗位培训qualification of personnel 人员资格equipment control procedure 设备控制程序device type 设备类型order of design changes 设计更改通知单design and development control procedure 设计和开发控制程序design and development 设计开发design and development planning 设计开发策划control of design and development changes 设计开发更改控制design and development review 设计开发评审design and development validation 设计开发确认design and development outputs 设计开发输出design and development inputs 设计开发输入design and development verification 设计开发验证design validation 设计确认design documentation 设计文件编制design acceptance criteria 设计验收准则design verification 设计验证audit program 审核大纲conduct of audits 审核行为audit criteria 审核准则production process control 生产过程控制production process control procedure 生产过程控制程序production and service provision 生产和服务提供control of production and service provision 生产和服务提供的控制validation of processes for production and serv ice provision 生产和服务提供过程的确认production order 生产令identification and traceability 识别和可追溯性identification and traceability maintenance and replacement 识别和可追溯性维护与替换invalidate 使失效market survey 市场调研suitability 适宜性scope 适用范围controlled condition 受控状态terms and definitions 术语与定义analysis of data 数据分析sequence 顺序transfer of ownership 所有权转移system document 体系文件statistical technique 统计方法outsource(vt) a process 外包过程external source 外部来源documents of external origin 外来文件outsource, vt 外协unique identification 唯一的标识maintenance 维护Document Change Control 文件更改控制Request For Document Change (RDC) 文件更改需求单control of documents 文件控制documentation requirements 文件要求enquiry 问询,询价field nonconformity analysis 现场不符合分析relevance 相关性interaction 相互作用detail design 详细设计,详图设计,零件设计,施工设计sales department 销售部sales contract 销售合同checklist 校验表,一览表,检查一览表calibration 校准submission of action plans 行动计划的递交documented procedures 形成文件的程序documented statement 形成文件的声明performance requirements 性能要求licensee responsibilities 许可证持有者责任acceptance criteria 验收准则verification arrangement 验证安排verification results 验证结果customer focus 以客户为关注点,以客户为焦点awareness 意识introduction 引言,概述,介绍normative references 引用标准application 应用visit to user 用户访问review of requirements related to the product 有关产品的要求评审competent 有能力的effectiveness 有效性determination of requirements related to the pr oduct 与产品有关的要求的确定customer-related processes 与顾客有关的过程preventive action 预防措施management procedure for preventive actions 预防措施管理程序planned results 预期的结果intended use 预期的用途procedure for competence, knowledge and trainin g of personnel 员工能力, 知识和培训程序personnel training procedure 员工培训程序supporting services 支持性服务functions 职能部门responsibility 职责assignment of responsibility 职责分工workmanship 制造工艺manufacturing acceptance criteria 制造验收准则quality policy 质量方针quality programs 质量纲领quality management system 质量管理体系quality management system planning 质量管理体系策划performance of the quality management system 质量管理体系业绩quality plan 质量计划quality records 质量记录quality objectives 质量目标quality audit 质量审核quality manual 质量手册quality problem handling form 质量问题处理单quality requirements 质量要求allocation table of quality responsibilities 质量职能分配表availability of resources 资源的可获得性resource management 资源管理allocation of resources 资源配置provision of resources 资源提供general requirements 总要求,一般要求constituent part 组成部件organization 组织continual improvement of the organization 组织的持续改进size of organization 组织的规模Organizational Diagram 组织机构图final acceptance 最终验收work instructions 作业指导书11 / 11。
质量控制中英文对照

质量控制中英文对照Quality Control (QC) is an essential process in ensuring the consistency and excellence of products or services. It involves a series of measures and procedures to monitor and evaluate the quality of a product or service throughout its lifecycle. In this document, we will provide a comprehensive comparison of common quality control terms and phrases in both English and Chinese languages.一、质量控制 (Quality Control)Quality Control is the process of ensuring that products or services meet specified requirements and standards. It involves monitoring and inspecting various aspects of production or service delivery to identify and rectify any deviations or defects.二、质量标准 (Quality Standards)Quality Standards refer to the established criteria or specifications that products or services must meet to be considered of acceptable quality. These standards are typically defined by industry organizations, regulatory bodies, or internal company policies.三、抽样检验 (Sampling Inspection)Sampling Inspection is a statistical technique used to evaluate the quality of a batch or lot by inspecting a representative sample. This method allows for a more efficient and cost-effective assessment of quality compared to inspecting every single unit.四、充分检验 (100% Inspection)100% Inspection, as the name suggests, involves inspecting every single unit or item in a batch or lot. This method is often used when the cost of defects or failures is high, or when the consequences of non-compliance are severe.五、质量管理体系 (Quality Management System)A Quality Management System (QMS) is a set of policies, processes, and procedures implemented by an organization to ensure consistent quality performance. It encompasses activities such as quality planning, quality control, quality assurance, and continuous improvement.六、质量异常 (Quality Nonconformity)Quality Nonconformity refers to any deviation or failure to meet specified quality requirements or standards. It can include defects, deviations from specifications, or non-compliance with regulations or customer expectations.七、纠正措施 (Corrective Action)Corrective Action refers to the actions taken to eliminate the causes of quality nonconformities or prevent their recurrence. It involves identifying the root causes, implementing corrective measures, and verifying the effectiveness of the actions taken.八、预防措施 (Preventive Action)Preventive Action aims to identify and eliminate potential causes of quality nonconformities before they occur. It involves proactive measures such as risk assessments, process improvements, and employee training to prevent quality issues from arising.九、质量改进 (Quality Improvement)Quality Improvement refers to the ongoing efforts to enhance the quality of products, services, or processes. It involves analyzing data, identifying areas for improvement, implementing changes, and monitoring the results to achieve higher levels of quality and customer satisfaction.十、质量指标 (Quality Metrics)Quality Metrics are quantitative or qualitative measures used to assess the performance and effectiveness of quality control processes. Examples of quality metricsinclude defect rates, customer complaints, on-time delivery, and customer satisfaction scores.十一、质量审核 (Quality Audit)Quality Audit is a systematic and independent examination of a company's quality management system to ensure compliance with established standards and procedures. It involves assessing the effectiveness of quality control measures, identifying areas for improvement, and ensuring regulatory compliance.以上是质量控制常见术语的中英文对照,这些术语在质量管理过程中起到重要的作用。
骨灰盒产品质量控制筛查流程

骨灰盒产品质量控制筛查流程英文回答:Quality Control Screening Process for Urn Products.Inspection.Visual inspection: Check for any visible defects, such as cracks, chips, or dents.Weight and size measurement: Ensure that the urn meets the specified size and weight requirements.Material inspection: Verify that the urn is made from the correct material, such as wood, ceramic, or metal.Surface finish inspection: Examine the urn's surface for any imperfections, such as scratches or uneven paint.Testing.Durability testing: Submerge the urn in water for 24 hours to test its resistance to moisture.Corrosion testing: Expose the urn to salt spray for 24 hours to test its resistance to corrosion.Load testing: Place a weight on the urn to test its weight-bearing capacity.Fire resistance testing: Expose the urn to a flame for 30 minutes to test its fire resistance.Documentation.Inspection and test records: Maintain detailed records of all inspections and tests conducted on the urn.Warranty and certification: Provide a warranty for the urn and certify that it meets the specified quality standards.Corrective Action.Identify defects: Determine the root cause of any defects found during the screening process.Implement corrective measures: Take steps to prevent similar defects from occurring in the future.Retest and document: Retest the urn after implementing corrective measures to ensure its quality.Continuous Improvement.Regular review: Periodically review the screening process to identify areas for improvement.Customer feedback: Collect feedback from customers to identify potential issues with the urn.Industry best practices: Stay abreast of industry best practices and emerging technologies to improve the screening process.By implementing a robust quality control screening process, manufacturers can ensure that their urn products meet the highest quality standards and provide customers with peace of mind.中文回答:骨灰盒产品质量控制筛查流程。
质量控制(英文)

质量控制(英文)Quality ControlIntroduction:Quality control is a crucial aspect of any business or manufacturing process. It ensures that the products or services meet the required standards and customer expectations. This article will discuss the importance of quality control and elaborate on five key aspects of implementing an effective quality control system.1. Importance of Quality Control:1.1 Enhances customer satisfaction: Quality control ensures that products or services meet the desired level of quality, leading to customer satisfaction and loyalty.1.2 Reduces costs: Implementing quality control measures helps identify and rectify defects early in the production process, reducing costs associated with rework or product recalls.1.3 Builds reputation: Consistently delivering high-quality products or services builds a positive reputation for the business, leading to increased customer trust and market competitiveness.2. Quality Control Planning:2.1 Defining quality standards: Clearly defining quality standards is essential to ensure that all stakeholders have a common understanding of the expected level of quality.2.2 Establishing quality control processes: Developing robust quality control processes involves identifying critical control points, setting up inspection and testing procedures, and defining corrective actions for non-compliance.2.3 Training and resource allocation: Providing adequate training to employees involved in quality control and allocating necessary resources, such as testing equipment or software, is crucial for effective implementation.3. Quality Control Techniques:3.1 Statistical Process Control (SPC): SPC involves monitoring and controlling the production process using statistical methods to ensure that it remains within the desired quality limits.3.2 Six Sigma: Six Sigma is a data-driven approach that aims to minimize defects and variations in processes by identifying and eliminating root causes of errors.3.3 Failure Mode and Effects Analysis (FMEA): FMEA is a proactive technique that helps identify potential failure modes in a product or process, assess their impact, and take preventive measures.4. Quality Control Tools:4.1 Checklists: Checklists provide a systematic approach to ensure that all quality control requirements are met during the production process.4.2 Pareto Analysis: Pareto Analysis helps prioritize quality issues by identifying the most significant factors contributing to defects or non-compliance.4.3 Control Charts: Control charts visually represent process data over time, enabling the identification of trends, variations, and potential out-of-control situations.5. Continuous Improvement:5.1 Feedback and data analysis: Collecting feedback from customers and analyzing data related to defects or customer complaints helps identify areas for improvement.5.2 Root cause analysis: Conducting root cause analysis allows businesses to identify underlying causes of quality issues and implement corrective actions to prevent recurrence.5.3 Regular audits and reviews: Conducting regular audits and reviews of the quality control system ensures its effectiveness and compliance with standards, leading to continuous improvement.In conclusion, implementing a robust quality control system is essential for businesses to ensure customer satisfaction, reduce costs, and build a strong reputation. By focusing on aspects such as quality control planning, techniques, tools, and continuous improvement, organizations can achieve and maintain high-quality standards in their products or services.。
(全方位)产品质量优化措施英文版

(全方位)产品质量优化措施英文版Comprehensive Product Quality Optimization MeasuresIn order to enhance the quality of our products, we need to implement a series of measures that cover all aspects of the production process.1. Quality Control Procedures- Establish strict quality control procedures at every stage of production to ensure consistency and reliability.- Conduct regular inspections and testing to identify and address any defects or issues early on.- Implement a feedback loop system to gather insights from customers and make necessary improvements.2. Supplier Management- Select reliable and reputable suppliers who can provide high-quality raw materials and components.- Establish clear quality standards and expectations for suppliers to meet our product requirements.- Conduct regular audits and evaluations to monitor supplier performance and address any issues promptly.3. Employee Training and Development- Provide comprehensive training programs for employees to enhance their skills and knowledge in product quality management.- Encourage continuous learning and improvement to ensure that employees are equipped to maintain high quality standards.- Recognize and reward employees who demonstrate a commitment to product quality and excellence.4. Continuous Improvement Initiatives- Implement a continuous improvement culture within the organization to foster innovation and drive quality enhancements.- Encourage collaboration and cross-functional teamwork to identify opportunities for improvement and implement effective solutions.- Utilize data analytics and technology tools to monitor product quality metrics and make data-driven decisions.5. Customer Feedback and Satisfaction- Solicit feedback from customers through surveys, reviews, and direct communication channels to gauge satisfaction levels.- Use customer feedback to identify areas for improvement and prioritize enhancements based on customer preferences.- Develop a customer-centric approach to product development and quality assurance to meet and exceed customer expectations.By implementing these comprehensive product quality optimization measures, we can enhance the overall quality of our products and maintain a competitive edge in the market.。
Quality control

• Corrective Action System (ECAR System)
• Voice Of Customer (VOC) • Customer Returns Metric (RMA) • Monthly Quality Review
Incoming Quality Assurance Process Quality Assurance
20
Quality Control Introduction
什么是 “SPEARS” ?
SPEARS Solectron Process Excellence And Response System.
Design. Build. Ship. Service.
21
Quality Control Introduction
Compliance; Date Code, Packaging)
Supplier Quality Assurance
• Part Verification (PVTS; Auto LCR) • First Article Inspection • Online QC • SPC Control / SPC System • SPEARS / STARS System • 5DX; ICT; FT • Final QA • Post Package Audit • Process Audit • Roving Audits • Preventive Maintenance & Calibration • ESD Controls • Weekly Quality Review
Quality Control Introduction
Design. Build. Ship. Service.
- 1、下载文档前请自行甄别文档内容的完整性,平台不提供额外的编辑、内容补充、找答案等附加服务。
- 2、"仅部分预览"的文档,不可在线预览部分如存在完整性等问题,可反馈申请退款(可完整预览的文档不适用该条件!)。
- 3、如文档侵犯您的权益,请联系客服反馈,我们会尽快为您处理(人工客服工作时间:9:00-18:30)。
Quality Control GuideThe global marketplace demands highspeed to market, low cost and world classquality. GE Plastics is committed toproviding customers with the highest qualityproducts and services. Our Six Sigmaquality initiative results in the virtualelimination of defects from every product,process and transaction. This effort willpresent opportunities to reduce cost,expand and improve customer serviceQuality Control GuideContentsFailure AnalysisDegradationDegradationDegradation TestingDegradation Test ResultsChemical AttackStressStressDesign StressProcessing StressAssembly StressEnd-Use StressStress Concentration FactorsTroubleshooting GuideTroubleshooting GuideHistoryHypothesis of FailureTestingSourceFormulate SolutionCommunicateFeedbackInjection Molding Troubleshooting ConsiderationsFailure AnalysisWhen trying to determine the cause or causes of a part’s failure, it is good to maintain an open mind, best expressed by the phrase, "The Most Obvious Cause Isn’t." This reminds you to not assume anything during the analysis – to look for secondary or tertiary factors which may also be significant contributors to the part’s failure. The failure of a part molded from a thermoplastic resin can be caused by a number of factors during the life history of the part. Errors in design, processing, secondary operations, assembly and the end use environment can lessen the expected performance. Often two, three, or more factors can be found which may contribute to less than satisfactory performance of the part. However, of all the possibilities, by far the three most common problems are polymer degradation during processing, chemical attack and unexpected stress concentrations or accumulations.DegradationPolymer degradation is almost always associated with the processing of a material. If the degradation is a sudden or new occurrence, it is probably a result of changes in drying, processing parameters or the material. If the degradation is ongoing, (i.e., it cannot be resolved by standard troubleshooting), then it is more likely caused by part design, tool design or the molding machine.Degradation TestingFor most unreinforced thermoplastics, the test used to determine the level of degradation is the melt flow, or melt viscosity test. If the material is glass reinforced, a more accurate measurement can often be obtained from an intrinsic viscosity test. For a few resins, neither of these tests are accurate, and an alternative test must be used, such as the thermal gravimetric analysis – TGA.Degradation Test ResultsThe results of any analytical degradation test must be compared to some base value and reported as a percent change. The most accurate results are obtained by testing parts and pellets from the same lot of resin, in the same test equipment. The next best control value would be QC data from the manufacturer for the same lot of resin.There is always a small amount of degradation incurred in the molding process, due to the heat and shear that the material is subjected to in the mold. What percentage change is the dividing line between acceptable and unacceptable processing? General guidelines exist for most resins and processes. However, physical properties react differently to a particular level of degradation, and the needs of a specific part vary as well. Thus, the amount of acceptable degradation should be considered application dependent, and is determined either by the performance or failure of the part, or by thorough end use testing.9-1Degradation Testing GuidelinesChemical AttackExposure of a thermoplastic part to an incompatible solvent, solution or chemical may result in a variety of effects, ranging from surface melting, cracking and crazing, to degradation of properties such as elongation with little apparent evidence.When searching for a potentially incompatible material, it should be remembered that the attack may come from a minor component in almost any carrier – lubricants, cleaners, gaskets, adhesives, even mating plastic components! When in doubt, check it!Chemical compatibility – or the resistance of a material to a specific agent – depends upon a number of factors. The contact time may be critical; a cleaning agent which evaporates quickly may be acceptable for a part in its intended use, but if a molded plastic is immersed for extended periods of time, the part may be severely attacked. Similarly, elevated temperatures or stress levels may initiate or accelerate an attack. Remember that stresses are cumulative – a part may pass a compatibility test as molded, but with externally applied stresses, induced by an assembly operation for example, the part may be more susceptible to attack.StressA common factor in most part failures is stress. Compensating for all possible situations and their effects is virtually impossible. Even if all stresses are accurately evaluated, failure can still occur from some other unanticipated factor(s).Design StressHand calculations are typically used as a first approximation in the basic design of a part - and sometimes as the final analysis. Thus, it is important to understand their limitations:Most conventional hand calculations are only valid for simple geometries such as beams and plates.Hand calculations assume a linear relationship between stress and strain. The nature of plastic materials is that most exhibit a non-linear relationship, beginning at relatively low stress levels.Most hand calculations assume that displacements are relatively small so that changes in geometry do not significantly affect the stiffness of the part. Due to their relatively low stiffness and high deflections, this assumption is rarely valid for plastic parts. Thus, larger factors of safety are needed to compensate for the inaccuracies of hand calculations.Finite Element Analysis (FEA) utilizes the capability of a computer and specialized software to reduce a design to elements, each of which can be studied alone or as part of a system (or part).The most difficult area to analyze for both hand and FEA calculations is Stress Concentrations. Often, the best approach is simply to test actual parts and then modify the design accordingly.Processing StressResidual or molded-in stresses are inherent in all processing methods, but are most significant in injection molding. As the material is injected, the layer in contact with the mold quickly freezes. As the material filling the area between these frozen layers cools, it shrinks – pulling against the outside layers. This results in a slight compressive stress on the outside surface of a molded part and a slight tensile stress internally. The magnitudes of these stresses can be significantly affected by processing parameters and the cooling rate of the part. Warping of the part could indicate significant molded-in stresses.The most critical areas for molded-in stresses are the gate area, the farthest end of the flow, and any areas of sudden change in the flow, such as sharp corners and wall thickness transitions. In these areas, the level of molded-in stress is particularly high, and they should be evaluated carefully before being subjected to additional stresses.Assembly StressAdditional stresses are encountered when the part is joined as an element into an assembly. Mechanical fasteners are an obvious source of stress concentrations, but welding processes also induce residual stresses. Variations in tolerances and accumulations of tolerances can result in mismatched parts and cause sporadic high assembly stresses. Dissimilar materials will also cause additional stresses, if reactions to the assembly environment result in unequal size changes.End-Use StressAll possible end-use conditions and loadings must be anticipated in part design. Environmental changes can be significant – for example, large temperature excursions in combination with differences in coefficient-of-thermal-expansion (CTE) between components can result in high induced stresses. Some end-use loadings, such as impact, can be difficult to analyze before parts are available for testing. The most impossible task of all is to envision abuses that the part was not meant to experience.Stress Concentration FactorsStress Concentration Factors are a standard tool for design engineers. Developed from empirical data, they are used to approximate stress levels in areas that hand calculations cannot evaluate. Stress Concentration Factors are dependent upon the design only – they are the same regardless of the material. Since thermoplastic resins in general have relatively low stress limits compared to metals, consideration of Stress Concentration Factors is an important step in the design of thermoplastic parts.9-2Stress Concentration FactorsTroubleshooting GuideFailure of molded plastic parts can occur in several ways: mechanical failure, fatigue, thermal troubleshoot, chemical attack, improper processing, design and tooling, material inconsistencies, etc. The following is an operational outline for troubleshooting and correcting failures of molded plastic parts.1. Identify and Define Problem2. Research Failure History3. Hypothesis of Failure4. Testing5. Determine Source of Failure6. Formulate Solution7. Communicate Findings8. FeedbackThe first step is to identify exactly what the problem is, and define what would constitute an acceptable solution. Then characterize as completely as possible the failure:TYPE - brittle, ductile, single or multiple locations, etc.HOW - minor, catastrophic, slow, fast, etc.MODE - flexure, tensile, vibration, impact, creep, heat, etc.LOCATION - crack origin, thin wall, corner, gate, hole, boss, etc.SYMPTOMS - surface appearance, fracture surface, strength or properties reduction, snap, tear, etc. HistoryThe next step of information gathering is the history of the application, as well as the specific failed parts: FUNCTION - – what exactly is the part expected to doPERFORMANCE - – specifications, requirements, etc.MATERIAL - – resin, grade, color, lot, QC specificationsHISTORY - – has it ever worked, where did it happen, failure at inspection, percentage of failures, repeatability, etc.PROCESSING - – set-up, regrind, drying, gate and sprue, mold release, machine size and type, etc. DESIGN - – prints, analyses, testing, changes, etc.SECONDARY OPERATIONS - – fastening, bonding, welding, coating, painting, printing, etc. ENVIRONMENT - chemicals, weathering, UV, loading, temperature, time, etc. Hypothesis of Failure Use the accumulated information to determine the most likely contributing factor(s) to the failure. Decide if sufficient information is present to determine corrective measures or if there is a need for further information.With justifiable hypotheses, testing may be instituted to provide verification of the cause(s) of failure. Such testing might include:DEGRADATION - – melt flow, melt viscosity, intrinsic viscosity, or TGASTRESS - – print review, finite element analysis, physical testingCOMPATIBILITY - – data survey, chemical testing, chemical wash, microscopy, etc.FTIR - – composition, contaminationASH - – level of reinforcement, possibility and condition of regrind SourceUsing the test data, visual inspections, design and processing information, and the general background information, a "supported" conclusion of the source(s) of the part failure may be drawn. In many cases, the "cause" of failure may include multiple sources.Formulate SolutionAfter having identified and rated the most likely cause(s) of failure, it is necessary to isolate the optimum solution. The solution should be feasible, adequate and economical. This is often difficult and may involve a series of compromises. If possible, alternative measures should always be provided so that improvements, cost and timeliness can be evaluated for the best solution.CommunicateProper communication of findings is an integral step in the solution process. The findings must be forwarded in a concise, clear and timely manner or they are of little use. Verbal communication is the quickest method, and is often used to speed results. However, formal reports are beneficial in documenting the activity for immediate and future reference.Feedback is critical in that it reflects the effectiveness of the analysis. If the corrective measures did not resolve the problem, an alternative approach may be necessary. Even invalid conclusions provide important information, and can be used as the basis of a more focused, in-depth evaluation.This chart lists some of the factors that are considered in the design, development, manufacture and use of a part. When the part’s performance does not meet expected levels, it may be helpful to recreate and question the thought process behind some of these decisions.Injection Molding Troubleshooting ConsiderationsFeedback is critical in that it reflects the effectiveness of the analysis. If the corrective measures did not resolve the problem, an alternative approach may be necessary. Even invalid conclusions provide important information, and can be used as the basis of a more focused, in-depth evaluation.Page 11 of 11。