李岩
中国历史故事-李岩身世解析 李岩为何投了李自成?

中国历史故事-李岩身世解析李岩为何投了李自成?李岩这个名字不特别,双字名又简单,中国历史上叫“李岩”的不知道有多少。
不过今天给大家说的,却是李自成麾下大将李岩。
没错,就是那个被牛金星谗言杀害的大将。
李岩原名李信,河南开封府杞县人,父亲李精白是山东巡抚加兵部尚书衔。
天启年间,因为与奸宦魏忠贤有关系,所以在崇祯初年之时,被打为阉党,给予“交结近侍,又次等论,徒三年,输赎为民”。
也就是说李精白被削职为民了,不过虽然没了官位,却并不代表李家日子难过。
他在家乡名声不坏,家底殷实,所以成了当地有名的乡绅财主。
李岩出生在这样的家庭,少什么也少不了教育,后来又中了举人。
如此一来,李岩和李自成麾下其他大将不同,可谓是文武双全了。
年长之后,李岩遵循父母之命,与杞县豪门之家汤家的女儿成了亲。
两人门当户对,汤氏也是贤良的大家闺秀,婚后生活还是挺美满的。
出身富贵,家有贤妻,身负功名,李岩为何最后抛弃了安逸的生活,选择加入农民军,在战场上拼命呢?崇祯末年,不知道是不是老天爷也知道大明帝国已经快要灭亡,所以也要来插一脚。
人祸不断,天灾也是频发。
杞县百姓,就因为天灾而饱受痛苦,许多人因为灾祸而死。
当然这灾难对富户没影响,受难的都是穷苦人家。
李岩虽然出身富户,但自幼慷慨侠义,常常周济穷人,为他们打抱不平、伸张正义。
眼见着百姓因为灾祸活不下去,县令宋某却仍然稳坐不动,于是前往请命,希望官府能赈济灾民。
谁知道宋某身为父母官,却并不在乎百姓的死活。
对于李岩的劝谏丝毫不放在心上,好似并不知道外面饿殍遍地似的。
李岩虽说有功名在身,但是却也不能强逼宋某赈灾。
所以回到家中,将家里的余粮都拿来救济灾民。
他一个人的力量始终杯水车薪,于是写《劝赈歌》,劝勉各大富户都出一份力,救救百姓。
人都是自私的,如李岩这般仁慈侠义之人毕竟是少数。
所以不管李岩如何呼吁,响应的人仍然少之又少。
朝政的黑暗,官员的腐败冷漠,以及周遭人的事不关己高高挂起,这些都促使了李岩选择了投靠李自成。
唐山青年书法家李岩

唐山青年书法家李岩简介李岩,河北唐山人,出生于1982年2月,法名:奥赛多杰。
青年书法家,青年企业家,自幼爱好书画,师从韩新生老师,是刘海大师再传弟子。
多年从事国画书法的创作、研究,作品曾得到了中央美院朱军山老师、方胜老师的高度好评。
作品以弘扬仁义道德为主要内容,以倡导德善为艺术追求。
现为中国书法家协会会员、中国青年书法家协会会员、唐山市书法家协会会员。
他多次受邀在国内举办联合书展,多次参加全国各类书法赛事并获奖项,部分作品被国内外多家艺术机构及个人收藏。
唐山青年书法家李岩幼承家学,书法功底深厚,其创作奔放自由,法度严谨,厚重而不失飘逸,灵动而不失庄严。
他注重吸收历代各家各派之所长,无论是作品的题材、构想、章法意境等诸方面,均能多方接纳,为我所用。
近些年,他将书法意境的延伸和深层次的文化挖掘作为自己创作的方向,赋予以历史内涵和时代感,由此开拓了一种书法新气象。
唐山青年书法家李岩性格平易近人,为人淳朴友善。
他生性好学,仰慕书法。
喜欢直抒胸臆的创作,无论何时何地,素纸铺展开来,浓蘸笔墨,下笔如行云流水,神采飞扬,笔锋上下游动,左右擒纵,点画无一处含糊懈怠,法度尽在他的指腕之间。
那流畅的线条,清秀美观的墨迹氤氲满纸,散发出一阵阵沁人心脾的芳香,书法艺术的魅力、神韵展示的酣畅淋漓、熠熠有神。
他说:“书法的写与法、笔与墨将中国文化内涵表达的淋漓尽致。
它的种种笔法如人的坐卧、行立、揖让、颠伏,各尽意态,但它们既相互矛盾又彼此映衬协调。
”通过这种不同节奏感的书写表达,作品生动、自然,让人回味无穷。
中国的书法是中华文明历史发展的一个载体,与中国人的思想观念有着密切的联系。
书法几千年来一直在见证着是文化的发展传承。
从历代的名爵公卿到如今的学者文人,都将其看作是一种至高的艺术追求,他们用各自的点、画书写经营来阐述对书法艺术和历史人生的理解。
历史趣谈李自成为什么杀李岩 为什么李自成要起义
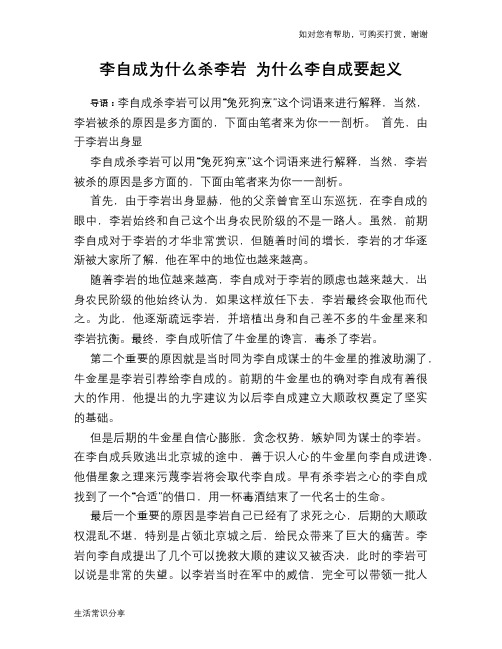
如对您有帮助,可购买打赏,谢谢李自成为什么杀李岩为什么李自成要起义
导语:李自成杀李岩可以用“兔死狗烹”这个词语来进行解释,当然,李岩被杀的原因是多方面的,下面由笔者来为你一一剖析。
首先,由于李岩出身显
李自成杀李岩可以用“兔死狗烹”这个词语来进行解释,当然,李岩被杀的原因是多方面的,下面由笔者来为你一一剖析。
首先,由于李岩出身显赫,他的父亲曾官至山东巡抚,在李自成的眼中,李岩始终和自己这个出身农民阶级的不是一路人。
虽然,前期李自成对于李岩的才华非常赏识,但随着时间的增长,李岩的才华逐渐被大家所了解,他在军中的地位也越来越高。
随着李岩的地位越来越高,李自成对于李岩的顾虑也越来越大,出身农民阶级的他始终认为,如果这样放任下去,李岩最终会取他而代之。
为此,他逐渐疏远李岩,并培植出身和自己差不多的牛金星来和李岩抗衡。
最终,李自成听信了牛金星的谗言,毒杀了李岩。
第二个重要的原因就是当时同为李自成谋士的牛金星的推波助澜了,牛金星是李岩引荐给李自成的。
前期的牛金星也的确对李自成有着很大的作用,他提出的九字建议为以后李自成建立大顺政权奠定了坚实的基础。
但是后期的牛金星自信心膨胀,贪念权势,嫉妒同为谋士的李岩。
在李自成兵败逃出北京城的途中,善于识人心的牛金星向李自成进谗,他借星象之理来污蔑李岩将会取代李自成。
早有杀李岩之心的李自成找到了一个“合适”的借口,用一杯毒酒结束了一代名士的生命。
最后一个重要的原因是李岩自己已经有了求死之心,后期的大顺政权混乱不堪,特别是占领北京城之后,给民众带来了巨大的痛苦。
李岩向李自成提出了几个可以挽救大顺的建议又被否决,此时的李岩可
生活常识分享。
青春在爱与责任中绽放——记长春市二道区东站十委社区党委副书记李岩

2015年第1期她,曾经是长春市一〇八中学小学部的一名优秀青年教师,在三尺讲台上教书育人,以其优异的工作成绩获得吉林省十佳教学优秀教师、长春市十佳教师、长春市骨干教师等称号。
她,曾作为谭竹青事迹报告团中的一员,足迹遍及北京、上海、武汉、西安,在祖国的大江南北、长城内外宣传谭竹青事迹,洒播时代先锋精神。
她,以亲人谭竹青为榜样,为传承谭竹青精神,放弃教师的岗位来到社区,成为一名普通的社区工作者。
从此,社区建设多了一个推动人,社区居民多了一个贴心人,贫困群体多了一个主心骨。
她,就是长春市二道区东站十委社区党委副书记、居委会主任,年轻的社区工作者——李岩。
如今,她用青春、理想、智慧和汗水传承发扬谭竹青精神,继续在东站十委这块土地上砥砺前行、默默耕耘。
用青春与理想完成人生事业的华丽转身李岩是长春市二道区东站十委社区党委副书记,她还有个特殊的身份,就是优秀共产党员的典范、社区工作者的楷模谭竹青的外孙女。
1997年李岩进入长春市一〇八中学小学部做了一名普通教师,上班后从小在姥姥身边长大的李岩总是抽空就去看姥姥,可经常会“扑个空”,在她眼里,姥姥总有忙不完的事儿,常常是下班回家还没来得及歇口气就有人找她解决困难。
那时候的李岩,心中总有些不解,姥姥也是人,姥姥也需要休息,姥姥也得回家啊。
2005年,谭竹青病重,弥留之际还在惦记着社区工作:“居民议事会安排好了没有?明天的会议我怕是去不了了,给我请个假吧。
”那一刻,李岩瞬间彻悟了,眼泪不停地往下流,她终于理解谭竹青老人为何牵挂着她深爱的社会事业,牵挂着东站十委的居民。
姥姥没有留下什么,但却留下了最宝贵的精神财富。
姥姥去世后,李岩多次参加谭竹青事迹报告团汇报,每次汇报结束后,她总思考着这样一个问题,人生的意义是什么?姥姥为什么能够得到那么多人的尊敬和爱戴?后来她得到了答案,根本原因在于姥姥把一生都献给了她钟爱的社区事业。
姥姥不仅是李岩可亲可敬的长辈,更是她人生与事业的领路人。
关于李岩和红娘子的上下五千年故事

关于李岩和红娘子的上下五千年故事在明末的历史上,李岩是一个重要人物。
李自成以饥民造反起家,所过残破,实为流寇,李自成用李岩之策而收拾民心,得以建号大顺,挺进京师。
除此之外,当时李岩还发生过什么事情呢?下面我们一起来看看吧。
李岩和红娘子李自成离开商洛,到河南的时候,河南正发生一场大旱灾,成千上万饥民到处流亡。
李自成一到河南,饥民听到李闯王出山的消息,纷纷前来投奔。
有一天,一群饥民拥着一个读书人模样的青年来找闯王。
李自成询问来历,知道那青年名叫李岩(又名李信),刚被大家从河南杞县牢里救出来。
李岩本来是杞县地方一户富户人家的儿子。
前几年,当地灾荒闹得凶,好多农民断了粮。
李岩拿出家里的一些粮食,接济断粮的穷人。
对于一个富户子弟来说,这样做是少见的。
所以,穷人们觉得李岩为人不错,称呼他“李公子”。
杞县连年灾荒,穷人已经苦得过不了日子。
但是,县官照样派差役向穷人逼税逼债。
李岩怕逼出事来,去见姓宋的县官,劝他暂时停止征税,还希望他拨出一部分官粮借给饥民。
县官对李岩说:“上司向地方派军饷,催得紧。
我不问他们要税要租,拿什么交帐。
再说,官仓里的粮食早就空了,拿什么借给饥民。
要借,只有请你们几家富户人家出粮了。
”李岩见县官不答应,回到家,打开自家的粮仓,把二百多石粮食拿出来让饥民分了。
闹饥荒的百姓见李公子肯捐粮,很高兴。
但是受灾的百姓多,光李家捐粮也不顶事。
有人想个主意,聚集几十个人到别的富户人家去请愿,要他们学李家的样儿。
那些富户人家不但不同意,反而向上门的饥民瞪白眼,说家里根本没粮。
饥民一气之下,闹了起来,冲进一个富户的粮仓,把他家的粮食分了。
富户们发了慌,纷纷向县官哭诉。
县官说:“这不是反了吗?”立刻派了几名差役拿着他的令牌前去制止,还扬言说,如果再聚众要挟,一定要重办。
饥民们正在气头上,哪怕你县官硬压。
他们揪住差役,把令牌扔在地上,砸得粉碎,还拥到县衙门前,嚷嚷说:“我们没有粮,早晚得饿死,不如跟你们拼了吧。
李岩同志简历doc

李岩同志简历
李岩,男,生于1970年1月,博士,天津
市公安医院针灸理疗科主任,主任医师,天津中
医药大学硕士研究生导师,中国当代国医大师贺
普仁教授入室弟子,学术继承人。
中国针灸学会
会员,中国针灸学会刺络与拔罐学会常务理事,
天津针灸学会理事、副秘书长,天津针灸学会针药委员会副主任委员。
国家自然基金委项目评审专家,中国针灸学会针灸临床方案咨询专家。
天津市医学教育专家,天津市科学技术奖评审、科技计划验收和科技成果评价专家,天津市药监局医疗器械评审专家。
参加卫生部中医药管理局《三棱针操作国家标准》、《火针操作国家标准》的制定工作,天津市131人才工程人选。
2000 年荣获第二届天津优秀青年人才奖,获公安局三等功2次,获公安局嘉奖2次。
国内外发表期刊论文60 余篇,主持国家自然基金项目1项,参与2项,主持市科委重点项目2项,参与市科委面上项目2项、主持局级科研课题4项,科研成果获天津市公安局科技成果二等奖2项,三等奖3项,填补天津市火针疗法的研究空白,参编著作4 部。
带教硕士硕士研究生18名。
在天津科教频道《百医百顺》主讲医学健康讲座14讲,天津人民广播电台生活频道进行健康讲座5讲。
在临床工作中,主张针药并用,年门诊量超过10000人次。
1、火针疗法治疗:痤疮、斑秃、扁平疣、带状疱疹、脾胃病、类风湿性关节炎、丹毒、急性扭伤、面瘫、急慢性盆腔炎、乳腺炎、不孕症、痛经及各种疑难痛证。
2、刺血疗法治疗:湿疹、痛风、荨麻疹、黄褐斑、偏头痛、脑血管病后遗症、三叉神经痛等。
3、中药结合穴位贴敷治疗:过敏性鼻炎、哮喘、咳嗽等。
榆林诗人 李岩简介

榆林诗人李岩简介李岩,字子石,号临川,唐代诗人,榆林人。
他的诗歌风格高峰奇绝,以其诗歌超然脱俗的风格和深刻的思想内涵而著称于世。
李岩出生于唐朝贞观年间(627年-649年),祖籍榆林。
他自幼聪慧,喜爱读书,十五岁时便考中进士。
后来他曾在唐太宗的宫廷任职,但很快就离开了宫廷,回到榆林老家,开始了他的诗歌创作。
李岩的诗歌风格独特,充满哲理思考,常常表现出对人生、自然、社会等方面的深刻思考和洞察。
他的诗作不仅表现出对大自然的感受,还表达了对人生的思考和对社会现实的关注。
他的诗歌充满了对人生哲理和人生意义的探索,对于那个时代的人们来说,李岩的诗歌是一种启迪和鼓舞。
李岩的代表作品有《临川集》、《苦寒行》、《榆林诗稿》等。
其中,他的《临川集》是他的代表作之一,这部诗集包括了他一生中的所有诗歌。
这部诗集共有诗歌近千首,内容丰富,涉及了人生、自然、社会等各个方面,是中国古代诗歌史上的一部杰作。
李岩的诗歌作品,不仅在当时就受到了广泛的赞誉,而且在后世也一直被人们所推崇。
他的诗歌风格独特,充满哲理思考,表现出对人生、自然、社会等方面的深刻思考和洞察。
他的诗歌充满了对人生哲理和人生意义的探索,对于那个时代的人们来说,李岩的诗歌是一种启迪和鼓舞。
李岩的诗歌不仅在中国古代文学史上有重要的地位,在世界文学史上也有着不可忽视的地位。
他的诗歌作品被翻译成多种语言,在国际上也获得了广泛的赞誉。
他的诗歌作品不仅对中国古代文学的发展有着深远的影响,而且对世界文学的发展也产生了重要的影响。
总之,李岩是一位伟大的诗人,他的诗歌作品不仅在中国古代文学史上有着重要的地位,而且在世界文学史上也有着不可忽视的地位。
他的诗歌风格独特,充满哲理思考,表现出对人生、自然、社会等方面的深刻思考和洞察。
他的诗歌充满了对人生哲理和人生意义的探索,对于那个时代的人们来说,李岩的诗歌是一种启迪和鼓舞。
历史趣谈李岩哪里得罪了李自成?从来没有得罪过他?
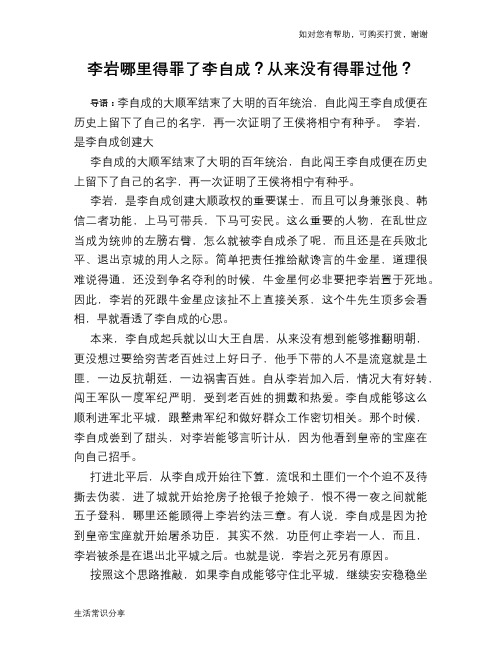
如对您有帮助,可购买打赏,谢谢李岩哪里得罪了李自成?从来没有得罪过他?
导语:李自成的大顺军结束了大明的百年统治,自此闯王李自成便在历史上留下了自己的名字,再一次证明了王侯将相宁有种乎。
李岩,是李自成创建大
李自成的大顺军结束了大明的百年统治,自此闯王李自成便在历史上留下了自己的名字,再一次证明了王侯将相宁有种乎。
李岩,是李自成创建大顺政权的重要谋士,而且可以身兼张良、韩信二者功能,上马可带兵,下马可安民。
这么重要的人物,在乱世应当成为统帅的左膀右臂,怎么就被李自成杀了呢,而且还是在兵败北平、退出京城的用人之际。
简单把责任推给献谗言的牛金星,道理很难说得通,还没到争名夺利的时候,牛金星何必非要把李岩置于死地。
因此,李岩的死跟牛金星应该扯不上直接关系,这个牛先生顶多会看相,早就看透了李自成的心思。
本来,李自成起兵就以山大王自居,从来没有想到能够推翻明朝,更没想过要给穷苦老百姓过上好日子,他手下带的人不是流寇就是土匪,一边反抗朝廷,一边祸害百姓。
自从李岩加入后,情况大有好转,闯王军队一度军纪严明,受到老百姓的拥戴和热爱。
李自成能够这么顺利进军北平城,跟整肃军纪和做好群众工作密切相关。
那个时候,李自成尝到了甜头,对李岩能够言听计从,因为他看到皇帝的宝座在向自己招手。
打进北平后,从李自成开始往下算,流氓和土匪们一个个迫不及待撕去伪装,进了城就开始抢房子抢银子抢娘子,恨不得一夜之间就能五子登科,哪里还能顾得上李岩约法三章。
有人说,李自成是因为抢到皇帝宝座就开始屠杀功臣,其实不然,功臣何止李岩一人,而且,李岩被杀是在退出北平城之后。
也就是说,李岩之死另有原因。
生活常识分享。
- 1、下载文档前请自行甄别文档内容的完整性,平台不提供额外的编辑、内容补充、找答案等附加服务。
- 2、"仅部分预览"的文档,不可在线预览部分如存在完整性等问题,可反馈申请退款(可完整预览的文档不适用该条件!)。
- 3、如文档侵犯您的权益,请联系客服反馈,我们会尽快为您处理(人工客服工作时间:9:00-18:30)。
Biomass and BioenergyVolume 26, Issue 4, April 2004, Pages 377-388--------------------------------------------------------------------------------doi:10.1016/j.biombioe.2003.08.003 | How to Cite or Link Using DOIPublished by Elsevier Science Ltd.Permissions & ReprintsHigh-pressure co-gasification of coal and biomass in a fluidized bedT. R. McLendon, , a, A. P. Luib, R. L. Pineaulta, S. K. Beera and S. W. Richardsonaa National Energy Technology Laboratory, 3610 Collins Ferry Road, Morgantown WV 26507, USAb Parsons Infrastructure and Technology Group, 3610 Collins Ferry Road, Morgantown WV 26507, USAReceived 14 May 2003; revised 29 July 2003; accepted 5 August 2003. ; Available online 25 September 2003.AbstractMixtures of coal and biomass were co-gasified in a jetting, ash-agglomerating, fluidized-bed, pilot scale-sized gasifier to provide steady-state operating data for numerical simulation verification. Biomass used was sanding waste from furniture manufacture. Powder River Basin subbituminous and Pittsburgh No. 8 bituminous coals (screened from −1.2 to +0.25 mm) were mixed with sawdust (screened to −1.2 mm) and pneumatically conveyed into the gasifier at an operating pressure of 3.03 MPa. Feed mixtures ranged up to 35% by weight biomass. The results of gasification tests of subbituminous coal/sawdust mixtures showed few differences in operations compared to subbituminous coal only tests. The bituminous coal mixture had marked differences. Transport properties of coal/biomass mixtures were greatly improved compared to coal only.Author Keywords: Biomass gasification; Co-gasification; Coal and biomass gasification; Biomass solids fluidization; Jetting fluidized bed gasificationArticle Outline1. Introduction2. Experimental3. Results/discussion4. ConclusionsAcknowledgementsReferences1. IntroductionDisposal costs of waste biomass and increasing environmental penalties of mining coal have suggested to many that trying to utilize waste biomass as a partial fuel substitute for coal was potentially beneficial. Also, the possibility of using less desirable or waste coals in conjunction with biomass to explore whether synergies would exist is appealing. Considerable excellent work in co-gasification from bench scale to large pilot scale has been undertaken during the last decade [1, 2, 3, 4, 5, 6, 7, 8, 9, 10, 11, 12 and 13]. Davidson [14] provides a very good summary of pertinent efforts prior to 1997. The first step is simply to determine whether it is realistic (or even possible) to use the intended resource(s) in whichever of the many gasifier types are available. Whether synergies occur is dependent upon the test conditions such as: feedstock type, direct particle contact, pressure, reactor type, temperature, etc. Tars are a significant problem for some of the systems reported and some researchers report that biomass with coal reduces them. The salient issue for consideration is that there are numerous varieties of both gasifiers and feedstocks and the possible permutations of gasifiers with feedstocks are considerable. Only actual tests can determine if synergies or insurmountable obstacles will occur. Numerical simulation is most valid for screening studies, extrapolation of experimentally determined data, and evaluation of the possible applications.Madsen and Christensen [1] report on a series of air-blown fluidized bed and entrained bed co-gasification tests with coal and straw. Pressures in the larger unit (based on U-Gas design) were up to 14.2 bar and feed rates of the feedstock were a maximum of 720 kg/h. Feeding presented problems, but some synergies were noted. Sjostrom et al. [2 and 3] also report synergies in fluidized bed co-gasification of wood and coal mixtures at small particle sizes with maximum feed rates of 5.2 kg/h and maximum pressures of 15 bar. Reinoso et al. [4] report on a comprehensive experimental program including a series of tests in larger pilot scale air-blown circulating fluid bed gasifiers at near atmospheric pressures. Feedstocks were waste coal, lignite, and pine chips at solids feed rates up to 800 kg/h. Results indicated that using waste coals in circulating fluid beds of the type tested would not be viable because of economic, operational and design constraints. Modeling comparisons indicated synergies existed between coal and biomass. Kurkela et al. [5] describe evaluations of a variety of biomasses and coals (and mixtures) in a fluidized bed gasifier with maximum feed rates of 80 kg/h at pressures up to 5 bar. de Jong et al. [6] report synergies with co-gasification of coal, miscanthus and straw in an air-blown fluidized bed gasifier operating at up to 5 bar. Pan et al. [7] co-gasified coals with pine chips at atmospheric pressure in an air-blown, bench scale fluidized bed gasifier. Some synergies were noted.2. ExperimentalThe purpose of the experimental program was to provide highly instrumented, steady-state operating data for numerical simulation matching and verification. The gasifier used was the National Energy Technology Laboratory's (NETL) pilot scale-sized Fluidized Bed Gasifier (FBG) located in Morgantown WV. Since many of the operational and technical details of the present system have never been described completely in the open literature [15] key specific information will be given here. With a good understanding of the phenomena occurring within the gasifier results are better understood. A simplified picture of the FBG is shown in Fig. 1 with reactor dimensions. The reactor is dense-refractory lined and has no internal heat-loss compensation mechanism. The coal for these tests was screened from −1.2 to +0.25 mm, and the sawdust(sanding waste from furniture manufacture) was screened to −1.2 mm. Solid feed was premixed and conveyed to the Batch Hopper from the Silo with N2. The Batch Hopper pressure was lowered to receive the feed and raised to match system pressure when dumping to the Feed Hopper directly below. For coal only feed, the Feed Hopper is constantly fluidized to prevent bridging and rat-holing. The feeder is directly below the Feed Hopper and the solids fall into one of the “pockets” in a rotating shaft where it is expelled by air pressure at the upside down position. The feed is then pneumatically conveyed with cool air into the jet in the axial center of the FBG bottom.Full-size image (33K)Fig. 1.Fluidized bed gasifier.View Within ArticleThe FBG in the jetting mode is a dry-bottom, ash-agglomerating gasifier with the solids/air mixture being surrounded by an annular stream of heated air and steam. In order to prevent excessive agglomeration of the char particles during the rapid pyrolysis conditions just above the jet, particle velocities are kept high. The minimum desirable velocity is 15 m/s. The jet area is where the free radical oxidation reactions occur and it is the hottest place in the gasifier. Once through the initial pass inside the jet, the coal particles (thus the biomass also) are assumed to be essentially completely pyrolyzed. Analyses of solids removed from the reactor verify this. Considerable problems with clinkering have been experienced with this type of gasifier [16]. A delicate balance must be maintained where some ash agglomeration occurs, but at a slow controlled rate, if possible. This is not easy. Regardless of the issues associated with this type of gasifier, it has many positive features leading to its use in the Pinon Pine IGCC demonstration project [17].The pyrolyzed char particles are jetted upward into the upper parts of the gasifier where circulation patterns develop. The general direction of the particles in the center is upward and along the walls it is down. Reentrainment of the particles occurs at the jet, aided by auxiliary jets inside the refractory insert at the main jet level. Modeling videos and analysis of conditions have indicated that the most significant particle mixing occurs at the level of the jets. More detail is provided in an unpublished report [18]. At nominal conditions, average coal char particle residence times are on the order of 1.5–2 h, and gas residence times are less than 1 min. At the gas flow rates in these tests, the fine particles are entrained in the gas flows and probably have residence times inside the gasifier on the order of a few minutes. Therefore, any catalytic effect of wood ash may not be as pronounced in the FBG as in other gasifier types. Differential pressure gauges are used to determine particulate densities in the FBG. Solids are removed in three places: heavier agglomerated particles come out the very bottom (underflow); medium particles comeout at the level of the first freeboard junction (overflow); and fly ash is removed in the Cyclone.The reactor is provided with numerous internal thermocouples as per Fig. 1 locations. Key process gas flows are very accurately measured to within 2% on a cold flow comparison to traceable standards. Process control is by both traditional PID controllers and a redundant distributed control system (APACS/Process Suite) provided by Moore products. The data are captured by APACS on a continuous basis, on about a 1-s interval depending on conditions. Gases for analysis are cleaned up downstream of the cyclone. The primary gas analyzer is a Perkin-Elmer magnetic sector mass spectrometer (MS), with continuous backup by an Ametekquadrupole MS and periodic sampling by a gas chromatograph. Gas analyses are reported on a dry basis. It should be noted that for feeds normally used in the FBG, tar production is not a problem. This gasifier has sufficient high-temperature gas residence time and enough char suspended throughout the reactor to provide ample opportunity for tar degradation. Downstream equipment is not designed for tars and problems with tars do not occur.Reactor temperature is not controlled. The modeling effort is stand-alone work and each steady-state operational period can be used as is, but for the series of tests reported here, only one parameter at a time was varied (where possible) to prevent second order interactions. However, when changing coal feed rate, there is an associated effect of changing char particle buildup in the gasifier. This is significant because the suspended char reacts with gases to gasify the char. The diffusion control constraint is lessened by having more char as reactant. More char particles suspended gives more surface area.The issue of when steady state has been achieved is not a trivial consideration. There are considerable fluctuations in gas analyses, bed temperatures, and reactor internal differential pressures even when the system has been operating with no set point changes for many hours. Of course, a constant set point does not preclude movement within an instrument's dead-band range. There are short-term changes, intermediate-term changes and long-term drifts. Feedstocks vary slightly from drum to drum. In addition, when the Feed Hopper is fluidized the feed particles segregate as per density and size; so the feed at the bottom will be different from the feed at the top. Therefore, for the biomass tests the fluidization feature was turned off. In addition, the issue of reactor temperature is important. It is significant that any thermocouple inside the gasifier reads the local temperature and there is considerable variation between the readings from the bed thermocouples. Reporting one temperature as the temperature of gasification is problematic. We simply report temperature at location as per time. To avoid the oxymoron condition of transient steady state, considerable judgement must be used.The strategy of the experimental effort was to establish a base case of operation about which one variable at a time could be changed. The base case was Powder River Basin subbituminous coal at a feed rate of 31.8 kg/h, with a reactor internal pressure of 3.03 MPa. The bituminous coal was Pittsburgh No. 8. Feedstock analyses are given in Table 1. The coal/biomass mixtures were as given in Table 2. For all tests: reactor pressure was 3.03 MPa, convey air was 42.9 m3/h at standard conditions, reactor air was 27.5 m3/h at standard conditions and steam was 27.2 kg/h. It should be noted that the coal feed rate was not constant for all tests. This introduced morethan one variable change for each test.--------------------------------------------------------------------------------Table 1. Analyses of feeds used in biomass testingFull-size table (<1K)View Within Article--------------------------------------------------------------------------------Table 2. Steady-state operating conditionsFull-size table (<1K)View Within Article3. Results/discussionFig. 2 shows the comparison of CO for all coal/biomass tests reported compared to the base case. It should be noted that the time period shown for the bituminous coal mixture includes an earlier part of the test when steady state had not yet been reached. This unsteady-state operation was included because the run was terminated early due to a malfunction. At the beginning of the bituminous/biomass run, the bed was mostly subbituminous coal char but the feed had been bituminous coal for at least 30 min. The CO level at time zero is nearly the same for all tests, but CO begins to drift down for the bituminous coal as the bed eventually fills with its char. Of significance is that the CO for the subbituminous coals, regardless of addition of biomass, is nearly the same. Fig. 2 shows another consistent feature of results from this gasifier. There is considerable fluctuation of readings from the gas analyzers with time. This is typical and is not an artifact of the instruments. The thermocouples and the differential pressure instruments show the same transient behavior. In fact, all figures presented in this paper are time averaged because all data points plotted show a wide band. Since the system is so well controlled, the fluctuations are obviously the result of feed differences with time. However, in the case of the bituminous coal mixture, adjustments of some control features were causing additional variations. We were trying to lower temperatures in the jet area (to prevent clinkering) without compromising the test.--------------------------------------------------------------------------------Full-size image (17K)Fig. 2.CO comparison.View Within ArticleFig. 3 shows that CO2 production is slightly higher for all biomass tests compared to the base case. Fig. 4 shows that the H2 production was within a range of 2 or 3% for most of the test periods. The bituminous mixture H2 could have been lower during the latter part of its run because of the efforts to lower temperatures. Regardless of the causes, the inherent characteristic of fluctuations must be taken into account by persons using such data for evaluation and design. From the perspective of considerable operational experience, it could not be concluded that there is a significant difference in H2 or CO production from any of the runs using subbituminous coal, with or without biomass included.--------------------------------------------------------------------------------Full-size image (15K)Fig. 3.CO2 comparison.View Within Article--------------------------------------------------------------------------------Full-size image (15K)Fig. 4.H2 comparison.View Within ArticleFig. 5 shows the comparison of readings for all runs from TE-733 (just above the jet less than 1 cm inside the bed). TE 733 is not in a thermowell, therefore, it is more sensitive than some of the others. But because it is near the wall it will normally read lower than a thermocouple sticking out further. Anything sticking out into the bed near the jet must be in a thermowell in order to survive for any significant time. All biomass tests show higher temperatures than the base case and the bituminous test shows about twice the temperature reading of the subbituminous tests. Because of its location near the wall, TE-733 is within the zone of descending char particles. Note that when the bituminous test began, TE-733 read about the same as it did for the other runs. As the bed began to contain more bituminous char, TE-733 began to show increased temperatures. Fig. 6 shows temperatures from TE-700 (inside a thermowell nearly 4 cm inside the bed at the same elevation as TE-733). Fig. 7 shows temperatures from TE-701 (inside a thermowell about 7.6 cm inside the bed, same elevation). The further inside the bed, the closer the temperatures become (differences are less). This is because the char from the bituminous coal is nearly absent from the lower part of the bed when the bed becomes nearly all bituminous in origin (to be discussed later). At the temperatures near the jet, heat transfer is predominantly by radiation. The bituminous coal has so little char that TE-733 can see the heat source from the jet. With the subbituminous coal char present, radiant energy from the jet must be absorbed and re-radiated to get to the wall. The further up the reactor, the closer all temperatures get and at the top they are essentially the same for all tests. It is of interest to note that TE-701 shows temperatures that approach ash fusion temperatures for the Pittsburgh No. 8 bituminous coal we used.--------------------------------------------------------------------------------Full-size image (17K)Fig. parison of TE-733.View Within Article--------------------------------------------------------------------------------Full-size image (18K)Fig. parison of TE-700.View Within Article--------------------------------------------------------------------------------Full-size image (17K)Fig. parison of TE-701.View Within ArticleThat the lower bed was nearly absent of char during the bituminous run is shown by Fig. 8. It is the differential pressure transducer located across the section just above the jet, PDT-707. Fig. 8 compares only the base case to the bituminous test but all subbituminous runs are about the same and all are several times the values recorded during the bituminous test. Fig. 9, PDT-708, the next differential pressure transducer up from PDT-707, shows that the difference is decreasing and at the top of the reactor the values are nearly the same. Fig. 10, from PDT-709 (the next pressure transducer up from PDT-708), shows another interesting feature discussed earlier. The 65/35 subbituminous test had significantly less coal feed than the base case and all other biomass tests. Note that the char particulate loading for this test decreases in the PDT-709 zone. The bed was being depleted of coal char and this behavior is consistent with other tests where th e coal feed was insufficient to “build the bed” with char. Its equilibrium value is probably about the value indicated after the 200 min interval shown in Fig. 10.--------------------------------------------------------------------------------Full-size image (12K)Fig. parison of PDT-707.View Within Article--------------------------------------------------------------------------------Full-size image (14K)Fig. parison of PDT-708.View Within Article--------------------------------------------------------------------------------Full-size image (16K)Fig. parison of PDT-709.View Within ArticleTable 4 shows the partitioning of the solids removed from the FBG for the various test periods (i.e. which of the ports from which the char is removed as shown in Fig. 1). Toward the end of the bituminous test, essentially no solids were removed from the underflow. Table 3 shows why. It is a comparison of overflow solids for the base case and the 75/25 biomass experiments. The bituminous coal char has about half the bulk density as the subbituminous char and the screen analyses show dramatic differences. This is consistent for a coal with a free swelling index of 7.5.--------------------------------------------------------------------------------Table 3. Overflow solids comparisonFull-size table (<1K)View Within Article--------------------------------------------------------------------------------Table 4. Carbon consumption/solids partitioningFull-size table (<1K)View Within ArticleThe data do not show much in the way of synergies for the subbituminous tests. One can hardly see the difference in the respective tests. However, there is one very significant synergy present for the bituminous coal/biomass mixture. Without the biomass present, it is not possible to use Pittsburgh No. 8 in the FBG [15]. It has always clinkered almost immediately when used alone. It is speculated that the presence of the biomass somehow deposits a coating on the bituminous char at the exit of the jet to prevent the typical uncontrollable agglomeration.There was no opportunity to try to optimize the operation of the FBG during the bituminous coal/biomass mixture test. Since we had never run such a coal in the gasifier before, we were trying various tweaks to keep temperatures low to keep it from clinkering. We discovered that frequent dumping of the overflow was necessary due to it filling up quickly. We had to eventually dump every 15 min in order to keep up. This precluded focusing on other issues. The run was terminated when an unscreened piece of sawdust pellet plugged the feed tube and we had to shut down to unplug the tube.Table 4 shows carbon consumption and solids partitioning for the base case and biomass tests. It should be noted that the conclusion that more biomass, hence less coal, leads to more efficient use of carbon could be misleading. The general experimental evidence is that biomass is easy to gasify. Coal char is not. With less coal char, there is more reactive gas available to consume the coal char, since the gas flow rates were unchanged. Table 5 compares carbon utilization for several fluidized bed coal/biomass operations. Care should be taken when comparing results such as these. Experiments are not necessarily designed to optimize conditions. They are conducted to evaluate whatever parameters are of most interest, while attempting to reduce experimental uncertainty.--------------------------------------------------------------------------------Table 5. Carbon conversion comparison to other research in fluidized bed coal/biomass utilization Full-size table (4K)View Within ArticleAnother unexpected synergy existed for the greatly improved transport and handling properties of the coal/biomass mixtures compared to coal alone. It was not necessary to fluidize the Feed Hopper with the biomass present. In addition, when calibrating the Feeder about 5% of the coalis lost to the dust collection system when coal alone is used. With all mixtures this was reduced to about 3%.The most significant alteration of flow properties occurred when we were calibrating the Feeder with mixtures. The Feed Hopper is normally kept at less than 20 kPa above the pressure in the reactor in order to assure no back flow of hot gas up the feed tube. During one calibration with biomass mixtures the differential pressure controller was inadvertently set at several times that value. The calibration showed an increase of several times the expected flow rate. Had that occurred with coal only, the feeder would have instantly plugged. Also, we were not fluidizing the Feed Hopper. Because of the mechanical configuration and the constant rotational speed, the only way for the coal/biomass mixture to have had such a remarkable increase in flow rate was for the feed to be undergoing dense packing in the pocket. Why this behavior occurs is not readily apparent. The speculation is that the fine biomass dust may act like miniature roller bearings or it will fill in depressions in the coal particles to make them smoother and rounder. Perhaps, the biomass affects static electric charges on the quite dry feeds. An extensive literature survey was conducted and much work has been done in the area of copier toner materials wherea few weight percent of various materials are added to significantly affect solids flow properties[19]. Considerable additional work is being done in the pharmaceutical industry with deliveries of inhalent powders [20]. However, nothing was revealed in the search that indicated anyone had published any work with materials like coal and biomass.4. Conclusions•Synergies with subbituminous coal/biomass mixtures are not readily apparent in gasification. •A most significant synergy exists with gasification of highly caking coals and biomass in the FBG since without the biomass, such coal cannot be processed at all.•The transport (rheological) properties of all the coal/biomass mixtures are greatly improved relative to coal only for our system. Plugging is greatly reduced and handling is much easier. •The particulate flow patterns in the FBG for swelling bituminous coals are greatly altered compared to particulate flow patterns for subbituminous coals.•Carbon utilization for the FBG is about the same as similar fluidized bed gasifiers using biomass.AcknowledgementsWe greatly appreciate the support of John Rockey and David Wildman of the US Dept of Energy, NETL. Their foresight and efforts made this work possible and valuable.References1. Madsen M, Christensen E. Combined gasification of coal and straw coal. In: APAS Clean Coal Technology Programme, vol. 3. 1992–1994. p. C2.2. Sjostrom K, Bjornbom E, Chen G, Brage C, Rosen C, Yu Q. Synergetic effects in co-gasification of coal and biomass. In: APAS Clean Coal Technology Programme, vol.3. 1992–1994. p. C3.3. K. Sjostrum, G. Chen, Q. Yu, C. Brage and C. Rosen, Promoted reactivity of char in co-gasification of biomass and coal: synergies in the thermochemical process. Fuel 78 (1999), pp. 1189–1194.4. Reinoso C, Cuevas A, Janssen K, Morris M, Lassing K, Nilsson T, Grimm HP, Puigjaner L, Ying Gang P, Velo E, Zaplana M, McMullan JT, Williams BC, Sloan EP, McIlveen-Wright D. Fludised bed combustion and gasification of low-grade coals and biomass in different mixtures in pilot plants aiming to high efficiency and low emission processes. In: APAS Clean Coal Technology Programme, vol. 3. 1992–1994. p. C5.5. Kurkela E, Laatikainen J, Stahlburg P. Cogasification of biomass and coal. In: APAS Clean Coal Technology Programme, vol. 3. 1992–1994. p. C9.6. de Jong W, Andries J, Hein KRG. Coal-biomass gasification in a pressurized fluidized bed gasifier. In: ASME International GT and Aerospace Congress, Stockholm, SE, June 2–5, 1998. p. 1–7.7. Y.G. Pan, E. Velo, X. Roca, J.J. Manya and L. Puigjaner, Fluidized-bed co-gasification of residual biomass/poor coal blends for fuel gas production. Fuel 79 (2000), pp. 1317–1326. Article | PDF (312 K) | View Record in Scopus | Cited By in Scopus (33)8. Keil JHA, Bos A, den Uil H, Plaum JM. The development of cogasification for coal/biomass and for other coal/waste mixtures and the reduction of emissions from the utilisation of the derived fuel gas. In: APAS Clean Coal Technology Programme, vol. 3. 1992–1994. p. C8.9. Olsen A, Rathman O, Gjernes E, Fjellerup J, Illerup JB, Hald P, Hansen LK, Kirkegard M. Combustion and gasification of coal and straw under pressurized conditions. Riso-R-808(EN).10. A. Collot, Y. Zhuo, D. Dugwell and R. Kandiyoti, Co-pyrolysis and co-gasification of coal and biomass in bench-scale fixed-bed and fluidised bed reactors. Fuel 78 (1999), pp. 667–679. Article | PDF (636 K) | View Record in Scopus | Cited By in Scopus (57)11. Z. Xie, J. Feng, W. Zhao, K.C. Xie, K.C. Pratt and C.Z. Li, Formation of NOx and SOx precursors during the pyrolysis of coal and biomass. Part IV. Pyrolysis of a set of Australian and Chinese coals. Fuel 80 (2001), pp. 2131–2138. Article | PDF (303 K) | View Record in Scopus | Cited By in Scopus (35)12. Chen G, Sjostrom K, Bjornborm E, Brage C, Rosen C, Yu QZ. Coal/wood co-gasification in a pressurized fluidized bed. Proceedings of Third International Symposium on Coal Combustion Science and Technology, Beijing, China, September 1995. p. 383–90.13. Brage C, Yu QZ, Sjostrom K. Characterisation of tars from coal-biomass gasification. Proceedings of Third International Symposium on Coal Combustion Science and Technology, Beijing, 1995. p. 45–52.。