生产线平衡(line balance)
生产线平衡LineBalance

© USI proprietary and confidential
8
二﹑生产线平衡的常见概念
USI SMT线平衡计算公式:
© USI proprietary and confidential
9
二﹑生产线平衡的常见概念
USI SZ的生产线平衡率指标:
SMT>92%; ASM&TEST&PACKYING>88%
1.各工站顺序(作业单位)填入生产流动平衡表內. 2.量测各工序作业时间记入表內. 3.清点各工序人数记入表內. 4.根据分配时间划出柱狀图或曲线图. 5.在最高时间点的工序顶点橫向划一条线. 6.计算平衡率.
SS rrS S S Srr r SrS tr ti i r t11i 0 t0i1% % 0 001% 00% 0
确定生产线平衡改善方向
1、5M方法的改善
2、作业方法的改善
© USI proprietary and confidential
18
三﹑生产线平衡的分析改善
1、5M方法的改善:
(5M:人员,机器设备,物料,作业方法,环境)
减少耗时最长工序作业时间的方法有: 人员(Man):调换作业者;增加作业者;多能工训练; 新手避免工作负荷过重,利用作业员熟练程度的 差异性,平衡作业流程.
24
Q&A
某一生产线﹐按照工程分析设计成10个作业 工序﹐每个工序的时间分別为 18﹑12﹑15﹑14﹑25﹑12﹑41﹑20﹑28﹑12. 你如何來安排生产与人力配置?
© USI proprietary and confidential
25
机器设备(Machine):利用或改良工具、机器;人机 比合理配置;人机同步作业;提高自动半自动化水平; 人机工程分析,提高机械效率.
平衡生产线
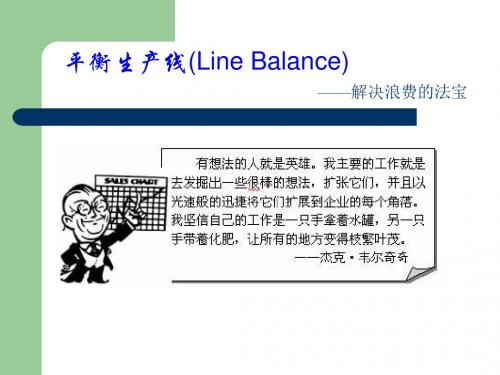
【本讲小结】
平衡生产线(LineBalancing)是把工作分配到各道工序的 决策过程,通过对人力、机械设备和工作任务的恰当分配,大大地提高生产线 的平衡率,使整个生产线达到最佳的平衡状态。生产线平衡的改善方法包括: 分担转移、作业改善压缩、加人以便直接缩短循环时间、拆解去除的方法图、 重排和作业改善后的合并等各种方法。
间较短的工序2中,从而大大提升整条生产线的平衡率。
生产线平衡的改善方法
6.作业改善后合并的方法
当用前面几种方法改善工序流程后,在重新思考新的工序之间是否还存在着合并 的空间。将可以合并的工序尽最大可能地合并和简化,这样,整条生产线的瓶颈自然
也相应地越来越少,使得平衡率和效率也能有效地得到持续的提升。如图10-6所示。
平衡生产线范例 1.改善前的工序情况
如图(a)所示,本范例包含八道工序:剪裁、除毛边、钻孔、拧螺丝、喷漆、检查、印制以及入 库前的检查,每道工序各有操作人员一名。在这个范例中,钻孔工序是出现瓶颈的工序,作业时间 长达30秒钟。 图中阴影部分代表空余的时间,在这段时间内,拧螺丝等工序的作业人员必须等待钻孔工序的作业 人员加工完毕后才能工作。不难看出,整条生产线的循环时间等于瓶颈工序的作业时间:30秒钟。
4.改善后的工序情况
如图(b)所示,生产线经过平衡改善后,总时间由原来的120分钟缩短为117分钟;八道工序合 并成为六道,操作人员总数相应地减少为六个。 此时,瓶颈工序为工序3(钻孔)和工序4(拧螺丝),整条生产线的循环时间等于瓶颈工序的作 业时间:22秒钟。
生产线平衡生产线平衡(linebalancing)
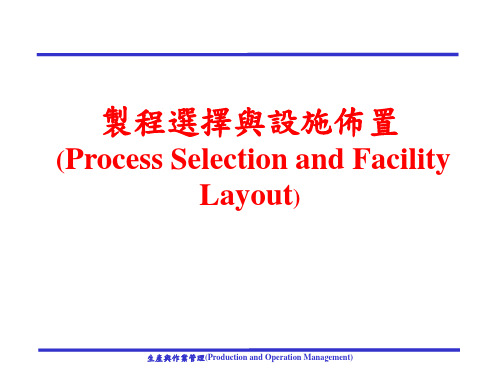
生產與作業管理(Production and Operation Management)
自動化 (automation)
• 指以機器代替人工,而此機器包括能夠 自動運作的感應器與控制裝置。 • 自動化的範圍從工廠的完全自動化到單 一自動化作業的形式。 • 服務業的自動化亦是一種選擇。
– 舉例:自動提款機 (ATM)、自動空調、自動 檢驗、自動存取系統、快遞包裹分類、郵件 處理、電子郵件、網路銀行以及電子收費器 等。
製程選擇與設施佈置
(Process Selection and Facility
Layout)
生產與作業管理(Production and Operation Management)
學習目標
解釋製程選擇策略的重要性。 2. 解釋製程選擇對一個組織的影響。 3. 描述基本製程型態。 4. 討論製程的自動化方法。 5. 解釋技術管理的必要性。 6. 列舉重新規劃設施佈置的原因。 7. 描述設施佈置的基本型態。 8. 列舉產品別佈置與製程別佈置的主要優點與缺點。 9. 解決簡單的生產線平衡問題。 10. 建立簡單的製程別佈置。
– 例如,軟磁碟、磁碟片或微處理器等
生產與作業管理(Production and Operation Management)
可程式自動化
• 機器人(robot):主要由三個部分組成:機 械手臂、動力供應及控制器。
生產與作業管理(Production and Operation Management)
– 為非例行性的工作,並在一段時間間隔內完成特定目 標。 – 設備彈性與作業人員技術的範圍也是從低至高皆有。
• 舉例:
– 從簡單到複雜都有,製作動畫、新產品或服務上市、 發行圖書、諮詢服務或興建橋梁等。
生产线平衡改善

作业技能
瓶颈
作业
改善
调整
拆解分割
作业人员
增加
作业人员
取消 不必要动作
合并 微小动作
作业方 法改善
重排 作业工序
简化 复杂动作
生产线平衡改善
生产线瓶颈改善方法示意图
1人→2人
分担转移
作业改善
增加人员
拆解去除
重新分配
改善合并
生产线平衡与瓶颈改善应在各工段之间进行,这样才能真正 提高生产能力平衡,最大限度地降低中间在库、提高效率。
生产线不平衡造成中间在库,降低整体效率
能力需求:100件/H
项目 能力 达成率
工序1 100件/H
100%
工序2 125件/H
125%
工序3 80件/H
80%
工序4 100件/H
80%
生产线平衡改善
线不平衡,造成生产时间损失,形成浪费
作业 工时 (分)
10
瓶颈(Bottleneck)
12 10
10 11
大于85%:可以认为生产线基本上实现了“一个流”生产。
一般来说,平衡损失率在5%以内是可以接受的,否则就要进行改 善。 生产线平衡率100%表示:工站之间无等待,前后产能一致;工站 节拍相同,动作量相同(动作量是指工站中各种必要动素的时间总 量);平衡损失时间为零;设计效率最大化。 生产线平衡改善
8
8
7
6
损失时间 作业时间
1 2 3 4 5 6 7 8 9 工序
生产线平衡改善
生产线平衡的目标
☆ 提高人员与设备工装的生产效率 ☆ 减少产品的工时消耗,降低成本 ☆ 减少工序的在制品,降低在线库存量 ☆ 实现单元化生产,提高生产系统的弹性
精益培训系列课件---生产线平衡 (leicaibing)
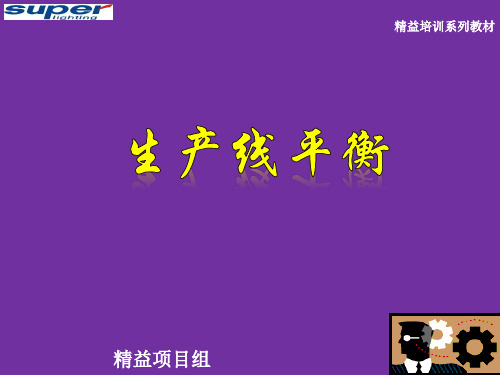
精益生产系列学为什么要做?可不可以不做?为什么要在这里做? 能不能在其他地方做?为什么要现在做?能不能以后做?为什么一定由他来做? 能不能由其他人做?他做得怎么样?有没有做得更好的?
LB生产线平衡
精益生产系列学习
基本原则和方法:ECRS法则(取消、合并、重排、简化)
LB生产线平衡
基本原则和方法:基本方法图示
精益生产系列学习
提高 设备效率
改进 工具夹具 作业 拆解分割 瓶颈 改善 增加 作业人员 提高 作业技能 调整 作业人员
取消 不必要动作
作业方 法改善
合并 微小动作
重排 作业顺序
简化 复杂动作
LB生产线平衡
基本原则和方法:5W1H
通过5W1H系统地分析工艺流程安排的合理性和必要性; 5W1H: What(什么) Why(为什么) Where(何地) When(何时) Who(谁)
30 25 20 15 10 5 0
单位:min/个
产 线 平 衡 图
10
15 30
18
灰色 — 平衡损失时间 橙色 — 员工作业时间
20
15
12
A
B
C
D
LB生产线平衡
常用术语介绍:OCT —节拍柱状图
精益生产系列学习
OCT —节拍柱状图(山积图/山积表),反映各个工序作业时间对比情况的图表, 从中可以找到影响整个工序产能的工序,发现可改善的地方。
LB生产线平衡
常用术语介绍:瓶颈工序
瓶颈的常见表现: 整体进度缓慢,生产效率下降; 出现产品零部件不能配套的现象; 一些工序加班赶货,而另一些则很轻松; 一些工序的半成品堆积过多,而另一些则很少; 个别工序在等材料、设备,其他工序进展正常;
生产线平衡LineBalance

间隔标记距离 所耗时间
3-3
平衡率计算
平衡率:用于评价流程中各工位节拍符合度的一 个综合比值。
∑ 各工序作业时间 平衡率 = ------------------------------ 100% 瓶颈时间工位数
3-4
生产线平衡图
生产线平衡图 :
表明作业的工站数以及每个工站的作业时间与节拍时间的对比。 能够明显地看出哪些存在浪费的工站,鉴别出工站与工站间的不平衡性。 优化当前的生产线平衡图,并绘制出优化后的生产线平衡图 .
电源包装 改善
后 前
7.9" 7.1" 7.8"
9.4"
S10
S11
S10
S11
18
3 - 18
3 - 13
数据整理和计算
资料分析与处理
第三步:初步制定生产线平衡图
根据各工站时间表,绘制生产线平衡图 ( 山积表),计算初始 平衡率。 识别增值动作及非增值动作,通过 ECRS 减少各工站非增值动 作时间。 通过对各分解动作单元进行分解组合排列组合,并确定每个工 站的所需的人数,尽可能地使瓶颈时间接近节拍时间。 对于瓶颈工站,重点分析动作时间,通过减小动作幅度,优化 作业工位布局等方法来降低瓶颈时间,然后重新计算平衡率。 根据确定的生产线总人数,考虑合适的生产线布局。
3 - 12
拆解动作
时间观测
时间测量流程
数据与信息记录
作业内容
➊观测中判断作业员的速度,并如实记录 ,不可修改测量数据。 ➋ 如遇特殊情况,应作标记。 ➊观测完毕后,对数据进行整理计算,补 充测量有怀疑或错漏数据。 ➋ 计算出每个工站的作业时间,并列出每 个工站所需使用的工治具、设备等。 ➊ 标记并汇总可以自由移动的工序时间, 并计算这些工序所占时间的比例。 ➋ 分析工序流程中哪些工序的作业时间 容易改善优化。
生产线平衡计算

G (2.25-1)=1.25
Idle=0.05
Idle = 0
Idle = 1.75
Idle = 1.25 Idle = 0.85
生产线平衡 - 19
5-4、排工位:
工作站1
2
A
工作站3
1
1
B
G
工作站5
1.4 H
C 3.25
工作站2
D 1.2
工作站1
E
F
.5
1
工作站4
生产线平衡 - 20
6、产线平衡率计算
瓶颈C/T=1.2s ≤T/T = 3600/3000=1.2 s
1.0
1.0
1.0
A
B
G
1.2
H
C
D
1.08
1.2
生产线平衡 - 13
E
F
0.5
1.0
3-2、拟定瓶颈CT
瓶颈C/T=2.4s ≤T/T = 3600/1500=2.4s
2.0
1.0
1.0
A
B
G
2.4
H
C
D
E
F
1.63
1.2
0.5
1.0
生产线平衡 - 2
瓶颈时间
时间
T2
瓶颈时间
T1
T3
T4
T5
S1 S2 S3
S4
S5
工站
生产线作业工时最长旳工站旳原则 工时称之为瓶颈。
产出旳速度取决于时间最长旳工站
生产线平衡 - 3
生产节拍
生产节拍 指生产线上连续出产两件相同制品旳时 间间隔。它决定了生产线旳生产能力、 生产速度和效率。 工作时间 节拍时间:Tact Time = 目的量
生产线平衡讲解与案例分析
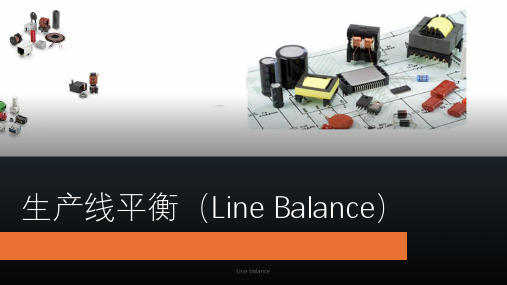
=
单件时间总和 瓶颈时间∗工站总数
*
100%
✓ 平衡损失率 = 1-平衡率。 ✓ 各工站的CT越接近,产线平衡率越高,平衡损失率越小。
Line balance
生产线平衡的常见概念
➢ UPH和UPPH
✓ UPH (Units Per Hours):指的是单位小时内的产出. UPH = 1/瓶颈时间(H)
如何确定节拍? 1.依据产能需要 2.根据实际产线考虑
Line balance
生产线平衡的常见概念
➢ 循坏时间(Cycle time)和瓶颈(Bottleneck)
✓ 循环时间(Cycle time)是指连续完成相同的两个产品之间的间隔时间。即就是完成单个产品的平均时间。它决定了生产线的产出能 力、生产速度和效率。 例:如A零件的第一档工艺, 生产设备每小时(循坏)产出为50pcs,则: 循坏时间(CT)= 1*3600s/50pcs = 72s/pc 根据以上节拍比较说明该工艺不能满足出货需求。
49
60
53
Line balance
生产线平衡的案例分析
➢ 生产A零件的线平衡分析
✓ 5. 改善后的平衡状态图
70
59
60
50
40
30
20
10
0
洗
• 改善后:
瓶颈工序
A零件改善后线平衡状态
60
47
50.5
49
25.5
#1
切
刮刀
抛光
上漆
作业循坏时间(CT)(秒/件)
节拍(秒/件)
平衡效率(LBE)= 单间时间总和/(瓶颈时间*工站总数) *100%= (59+25.5+…+23)/(60*8) *100% = 77.9% UPH = (1*3600)s/(60s/件) = 60 件/小时 UPPH = 60/11 = 5.45件 一个月产出: 60*22*8 = 10560件> 客户需求10k件.
- 1、下载文档前请自行甄别文档内容的完整性,平台不提供额外的编辑、内容补充、找答案等附加服务。
- 2、"仅部分预览"的文档,不可在线预览部分如存在完整性等问题,可反馈申请退款(可完整预览的文档不适用该条件!)。
- 3、如文档侵犯您的权益,请联系客服反馈,我们会尽快为您处理(人工客服工作时间:9:00-18:30)。
生产线平衡(line balance)
什么是生产线平衡
生产线平衡是依照流水线作业的工程顺序,以生产目标算出周期时间,将作业分割或者结合,使各个工序的负荷均匀,以提高生产效率的方法。
一个产品,少则两三个工程,多则几十个,而每个工程又是由多个作业要素所组成,在生产工场里,制造部门依物料的加工流程分为一组、二组、三组,而每组内又由许多的个别工序所组成,所以又把它联结成一条条的生产线。
生产线平衡的相关概念
流程的“节拍”(Cycle time)是指连续完成相同的两个产品(或两次服务,或两批产品)之间的间隔时间。
换句话说,即指完成一个产品所需的平均时间。
节拍通常只是用于定义一个流程中某一具体工序或环节的单位产出时间。
如果产品必须是成批制作的,则节拍指两批产品之间的间隔时间。
在流程设计中,如果预先给定了一个流程每天(或其它单位时间段)必须的产出,首先需要考虑的是流程的节拍。
而通常把一个流程中生产节拍最慢的环节叫做“瓶颈“。
流程中存在的瓶颈不仅限制了一个流程的产出速度,而且影响了其它环节生产能力的发挥。
更广义地讲,所谓瓶颈是指整个流程中制约产出的各
种因素。
例如,在有些情况下,可能利用的人力不足、原材料不能及时到位、某环节设备发生故障、信息流阻滞等,都有可能成为瓶颈。
正如“瓶颈”的字面含义,一个瓶子瓶口大小决定着液体从中流出的速度,生产运作流程中的瓶颈则制约着整个流程的产出速度。
瓶颈还有可能“漂移”,取决于在特定时间段内生产的产品或使用的人力和设备。
因此在流程设计中和日后的日常生产运作中都需要引起足够的重视。
与节拍和瓶颈相关联的另一个概念是流程中的“空闲时间”空闲时间是指工作时间内没有执行有效工作任务的那段时间,可以指设备或人的时间。
当一个流程中各个工序的节拍不一致时,瓶颈工序以外的其它工序就会产生空闲时间。
这就需要对生产工艺进行平衡。
制造业的生产线多半是在进行了细分之后的多工序流水化连续作业生产线,此时由于分工作业,简化了作业难度,使作业熟练度容易提高,从而提高了作业效率。
然而经过了这样的作业细分化之后,各工序的作业时间在理论上,现实上都不能完全相同,这就势必存在工序间节拍不一致出现瓶颈的现象。
除了造成的无谓的工时损失外,还造成大量的工序堆积即存滞品发生,严重的还会造成生产的中止。
为了解决以上问题就必须对各工序的作业时间平均化,同时对作业进行标准化,以使生产线能顺畅活动。
“生产线工艺平衡”即是对生产的全部工序进行平均化,调整各作业负荷,以使各作业时间尽可能相近。
是生产流程设计与作业标准化必须考虑的最重要的问题。
生产线工艺平衡的目的是通过平衡生
产线使用现场更加容易理解“一个流”的必要性及“小单元生产”的编制方法,它是一切新理论新方法的基础。
生产线平衡的方法研究[1]
一条均衡性很高的生产线所追求的目标包括:
减少物质、能源、时间和资金的占用与浪费;降低生产成本;降低员工的疲劳度,减少遭受损伤和工伤的概率;利用有限的资源求得最高的产出,提高生产效率.没有一个良好的运行方法,就不可能达到以上目标,也就是说均衡生产需要一个良好方法,一个好方法反过来也能带来好的均衡性。
方法研究就是对现有的或拟议的工作方法进行系统记录和严格的考察,作为开发和应用更容易、更有效的工作方法,以及降低成本的一种手段。
按照从粗到精、从宏观到微观、由概括到具体的体系,方法研究包括程序分析、操作分析和动作分析三部分。
(1)程序分析
完成任何工作所需经过的路线和手续即为程序,程序分析主要以整个生产过程为研究对象,研究分析一个完整的工艺流程,看是否有多余或重复作业、工序是否合理、搬运是否太多、等待是否太长,进一步来改善工作程序和工作方法.高平衡率的生产线离不开良好的作业程序。
(2)操作分析
所谓操作分析就是通过对以人为主工序的详细研究,使操作者、操作对象、操作工具三者科学地结合、合理地布置和安排,达到工序结构合理,减轻劳动强度,减少作业时间消耗之要求,以提高产品品质和产量为目的而进行的分析.通常,合理的人机结合,能为高平衡率的生产线提供最直接的单元保障.如果人机结合不合理、不科学,那么这种作业就是一种粗放型高消耗的作业,就没有人员之间、机器之间、人机之间的相互协调与配合,更谈不上合理,这时不免会出现人等人、人等机、机等人和机等机等一系列严重影响生产线平衡的“等待性”浪费.也就是说,人机相互之间高效合理的配合,不仅能够大大减少作业等待,更重要的是能够提高生产线的平衡率,进而提升作业效率。
(3)动作分析
动作分析是在程序决定后,研究并减少甚至消除人体各种动作的浪费,以寻求省力、省时、安全和最经济的动作。
其实质是研究分析人在进行各种操作时的细微动作,消除无效动作,使操作简便有效,提高工作效率。
动作分析能在其它方法无效时,给生产线的平衡提供一把秘密武器,它从最基本的“动素”入手,寻求改进空间,以提升生产线的平衡能力.当然,它与工业工程其它方法综合运用,会使企业收到更好的效果。
1、首先应考虑对瓶颈工序进行作业改善,作业改善的方法,可参照程序分析的改善方法及动作分析、工装自动化等IE方法与手段;
2、将瓶颈工序的作业内容分担给其它工序;
3、增加各作业员,只要平衡率提高了,人均产量就等于提高了,单位产品成本也随之下降;
4、合并相关工序,重新排布生产工序,相对来讲在作业内容较多的情况下容易拉平衡;
6、分解作业时间较短的工序,把该工序安排到其它工序当中去。
改善的注意事项
(1)生产线的管理人员,对一些改善技法缺乏了解,一旦出现不平衡的状态,习惯用人员增补来弥补,这是一个不动脑筋的做法,不足为取。
(2)除了上面介绍的技法以外,也可以对材料、零部件、设计方法进行检讨,看是否有缩短工时的可能。
(3)生产线补进新手时,因新手对工作不熟悉,熟练度不足,因此,在配置上尤其要注意,防止造成巨大的不平衡使产量大幅下降,同时对新手造成过大的工作压力。
1、提高作业员及设备工装的工作效率;
2、单件产品的工时消耗,降低成本(等同于提高人均产量);
3、减少工序的在制品,真正实现“一个流”;
4、在平衡的生产线基础上实现单元生产,提高生产应变能力,对应市场变化,实现柔性生产系统;
5、通过平衡生产线可以综合应用到程序分析、动作分析、规划分析、搬运分析、时间分析等全部IE手法,提高全员综合素质。
(1)工程名:指本工程的名称或代号;
(2)标准时间:指作业指导书上所要求的作业时间;
(3)实测时间:指作业者完成操作的实际时间;
(4)节拍:根据生产计划量所得出的一个工程所需时间;
(5)不平衡率:是指生产线各工程工作分割的不均衡度。
生产线平衡与目视管理[1]
目视管理是利用形象直观、色彩适宜的各种视觉感知信息来组织生产现场活动,它是一种以公开化和视觉显示为特征的管理方式.由于目视管理主要依靠形象直观的视觉感知信息,能引起人们的注意,让人一看就懂,知道自己作业或工作的缺陷和不足之处,所以它是一
种效率高、不易错、以人为本的工作方法,很受现场管理人员的欢迎[2][3]。
常用的与生产线平衡联系密切的目视管理手段有下面两种。
(1)生产任务及完成情况的看板和公开图表管理.看板管理是可
视化的一种表现形式,即对数据、情报等状况一目了然地表现,主要是对管理项目,特别是情报进行的透明化管理活动,它通过各种形式如
标识、现状板、图表、电子屏等把文件上、脑子里或现场等隐藏的情报揭示出来,便于快速发现、快速应对.在现场,工作人员通过这种图表特别是能实时自动跟踪统计生产线状况的电子图表,使操作人员可以时时刻刻知道自己工位的现状,即工位能力是否充足、瓶颈或接下来的瓶颈是否将要在此出现.这就相当于一个在线反馈,对生产线的
走向实时监测,一旦生产线将要异常或正在异常时能及时报警,使生
产线现场相关人员能未雨绸缪,及时解决问题,确保生产线处于稳定、均衡、高效率的运作之中。
(2)标准作业指导书(Standard Operation Proce-dure,简称SOP).具有防错功能,也就是说在操作标准化的前提下,不管是谁,只要按照标准作业指导书进行作业,即使你原来从未操作过这个机器或进行过这种作业,一样能够合格地完成.它的最大优点就是能够使生产线的
均衡性在有新手作业时不会遭到破坏;进一步而言,企业能够弹性配
置作业人数,降低因市场需求多变而频繁转产所造成的人员招募和储备成本,提升企业的应变能力,实现柔性生产。
1.↑ 1.0 1.1孙建华,高广章,蒋志强.生产线平衡的手段与方法研
究[J].成组技术与生产现代化,2004,21(4)
2.↑肖智军.现场管理三大工具——标准化·目视管理·管理看
板[J].企业管理,2003,(11):64-70
3.↑张喜征.目视管理的现场动作[J].管理,2001,(3):28-30。