产品包装验证流程
生产车间包装检验流程

生产车间包装检验流程
生产车间包装检验流程:
①核对订单:确认产品型号、数量与订单一致,确保包装的产品正确无误。
②清洁工作台:保持工作台干净整洁,避免异物污染产品。
③检查包装材料:确认包装盒、说明书、标签等材料齐全且无破损、脏污。
④产品外观检查:目视检查产品表面是否有划痕、凹陷、色差等问题。
⑤功能测试:随机抽样进行功能测试,确保产品质量符合标准。
⑥包装操作:按照规定的方法和顺序将产品放入包装盒内,添加填充物固定。
⑦标签粘贴:准确粘贴产品标签,包括产品信息、批次号、生产日期等。
⑧密封包装:使用胶带或其他密封方式确保包装盒封闭严密。
⑨二次检验:对已包装的产品进行再次检查,确认无漏装、错装、标签错误等情况。
⑩打包加固:对于外包装,使用打包带或胶带加固,确保运输过程中的安全。
⑪批量抽检:对整批包装完成的产品进行随机抽检,验证包装质量和产品一致性。
⑫记录归档:记录检验结果,包括检验日期、检验人、产品批次和检验结论,以便追溯。
⑬异常处理:对检验中发现的问题产品进行标记隔离,分析原因,采取纠正措施。
⑭入库准备:将检验合格的包装产品搬运至指定区域,等待入库或发货。
医疗器械包装完整性试验验证方案
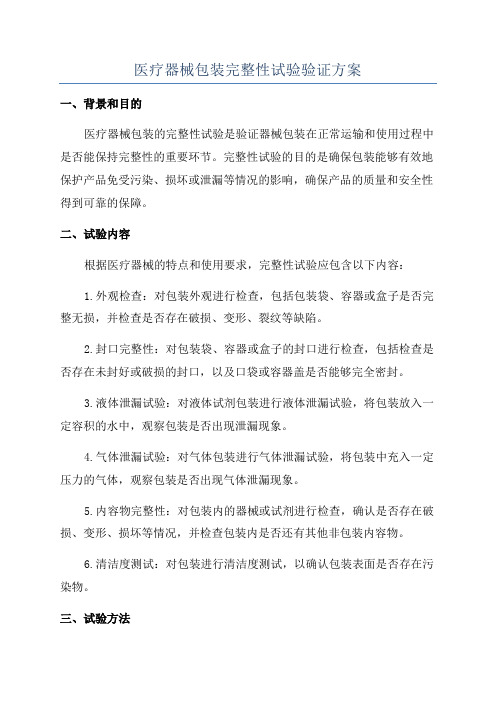
医疗器械包装完整性试验验证方案一、背景和目的医疗器械包装的完整性试验是验证器械包装在正常运输和使用过程中是否能保持完整性的重要环节。
完整性试验的目的是确保包装能够有效地保护产品免受污染、损坏或泄漏等情况的影响,确保产品的质量和安全性得到可靠的保障。
二、试验内容根据医疗器械的特点和使用要求,完整性试验应包含以下内容:1.外观检查:对包装外观进行检查,包括包装袋、容器或盒子是否完整无损,并检查是否存在破损、变形、裂纹等缺陷。
2.封口完整性:对包装袋、容器或盒子的封口进行检查,包括检查是否存在未封好或破损的封口,以及口袋或容器盖是否能够完全密封。
3.液体泄漏试验:对液体试剂包装进行液体泄漏试验,将包装放入一定容积的水中,观察包装是否出现泄漏现象。
4.气体泄漏试验:对气体包装进行气体泄漏试验,将包装中充入一定压力的气体,观察包装是否出现气体泄漏现象。
5.内容物完整性:对包装内的器械或试剂进行检查,确认是否存在破损、变形、损坏等情况,并检查包装内是否还有其他非包装内容物。
6.清洁度测试:对包装进行清洁度测试,以确认包装表面是否存在污染物。
三、试验方法1.外观检查和封口完整性:视情况采用目视检查或使用放大镜等辅助工具进行检查。
2.液体泄漏试验:将包装放入一定容积的水中,通过观察是否有气泡或水分进入包装内部来判断是否有泄漏。
3.气体泄漏试验:使用气密性测试装置,将包装封口处连接到装置上,通过观察气密性测试装置上的压力变化来判断是否有气体泄漏。
4.内容物完整性:视情况采用目视检查、重量测量等方法进行检查。
5.清洁度测试:使用适当的检测方法,如抽取法、粘贴法或压棉法等,测试包装表面的污染物残留情况。
四、试验评价根据试验结果评价包装完整性。
对于无明显缺陷、漏液、漏气以及清洁度符合要求的包装,评价为合格;对于存在缺陷、漏液、漏气以及清洁度不达标的包装,评价为不合格。
五、试验数据和记录试验过程中应完整记录所有试验数据,包括试验项目、试验方法、试验结果等。
包装测试方案
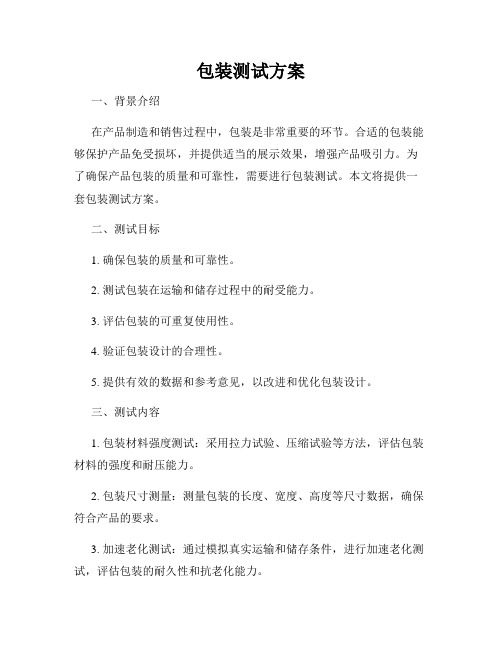
包装测试方案一、背景介绍在产品制造和销售过程中,包装是非常重要的环节。
合适的包装能够保护产品免受损坏,并提供适当的展示效果,增强产品吸引力。
为了确保产品包装的质量和可靠性,需要进行包装测试。
本文将提供一套包装测试方案。
二、测试目标1. 确保包装的质量和可靠性。
2. 测试包装在运输和储存过程中的耐受能力。
3. 评估包装的可重复使用性。
4. 验证包装设计的合理性。
5. 提供有效的数据和参考意见,以改进和优化包装设计。
三、测试内容1. 包装材料强度测试:采用拉力试验、压缩试验等方法,评估包装材料的强度和耐压能力。
2. 包装尺寸测量:测量包装的长度、宽度、高度等尺寸数据,确保符合产品的要求。
3. 加速老化测试:通过模拟真实运输和储存条件,进行加速老化测试,评估包装的耐久性和抗老化能力。
4. 包装堆放试验:将多个包装堆叠在一起,模拟储存和运输过程中可能出现的堆放情况,评估包装的稳定性和抗压能力。
5. 防水性能测试:使用水柱测试方法,评估包装的防水性能,确保产品在潮湿环境中不受损。
6. 包装开启力测试:测试包装的开启力,确保消费者能够轻松打开包装。
7. 包装外观检查:检查包装的印刷质量、装饰图案等外观细节,确保符合产品的品牌形象和标准。
8. 包装承载能力测试:测试包装的最大承载重量,评估包装的安全性能。
四、测试方法1. 采用专业的测试设备和仪器,确保测试数据的准确性和可靠性。
2. 根据产品特性和包装要求,设计相应的测试方案和流程。
3. 对于不同类型的包装,采用不同的测试方法和标准。
4. 按照标准操作要求进行测试,记录测试数据和观察结果。
5. 对于不符合要求的包装,提出改进建议,并进行进一步的测试和优化。
五、测试报告测试报告应包括以下内容:1. 测试目标和测试方法的简要描述。
2. 测试过程和操作记录。
3. 测试数据和观察结果的详细说明。
4. 对于不合格的包装进行原因分析和改进建议。
5. 结论和建议,以便优化和改进包装设计。
包装审核流程
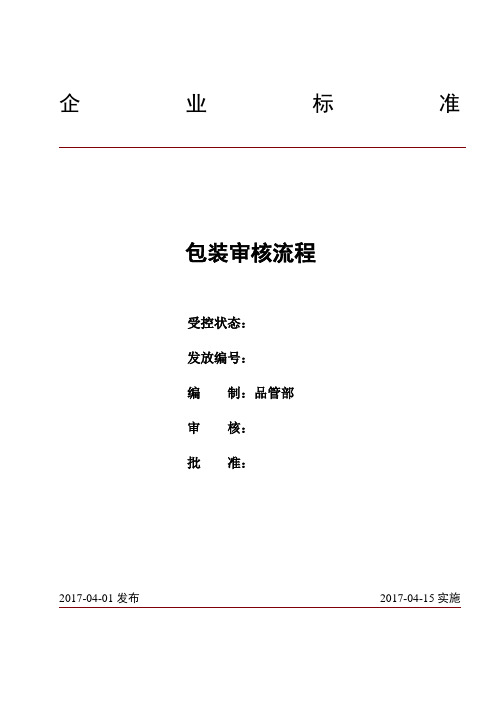
包装审核流程受控状态:发放编号:编制:品管部审核:批准:包装审核流程1 目的为使包装审核的工作能够在各部门的相互配合下有效快速的完成,同时使我公司包装更加规范化,特制定此流程。
2 适用范围本流程适用于集团公司负责包装的设计审核、制版、印刷等流程的相关部门。
3 职责3.1 研发部负责产品配方中使用的各种原辅料、添加剂的食品安全相关法律法规符合性的审查,并为包装配料标签的设计提供产品的真实配方。
3.2 品管部负责产品名称、包装设计等相关法律、法规符合性的审核。
3.3 品管部负责根据研发部提供的配方表编制包装袋的配料表,同时负责协调各产品相应的生产厂区品控化验室对我公司尚不具备检测能力的其他营养成分外检。
3.4 检验中心负责产品营养标签中能量、蛋白质、脂肪、碳水化合物、钠等五项强制标示项目的检测,做出判定并出具营养成分表。
3.5 市场部负责产品的名称、包装设计、条形码相关法规符合性的审核。
3.6 采购部负责分配新包装的供应商,协调由供应商制版。
3.7 各厂区负责包装与真实配料符合性的监督、审核。
4 工作程序4.1 产品包装设计、印刷的通知4.1.1 新产品通过品尝后,由研发部下发品尝通过通知,由市场部组织研发部、品管部沟通确定新产品的命名,市场部订出推广计划(包括要求提供配料、产品规格、样品数量等)。
4.1.2 常规产品因配方调整需改变配料标签的,由研发部24h之内向市场部、品管部提出纸版更改包装的设计、印刷通知,并将配方提供给品管部,双方填写《配方工艺收到、发放、回收记录表》,同时将样品送检测中心进行营养标签的检测。
4.1.3 因包装相关法律法规的新发布实施、调整等需改变包装标示标签的,由品管部24h之内提出更改包装的设计印刷通知。
需跟客户确定产品标签的包装更改前,相关人员及时与客户沟通包装变更情况,变更后的新包装找客户确认。
(如餐饮客户)各相关部门共同签字确认。
4.1.4 因营销策划需求需更改产品包装的,由市场部24h之内负责向品管部提出包装更改的通知,如果包装更改涉及产品的配方及保质期及贮存方法的更改,要一并通知研发部。
产品包装流程及检验管控
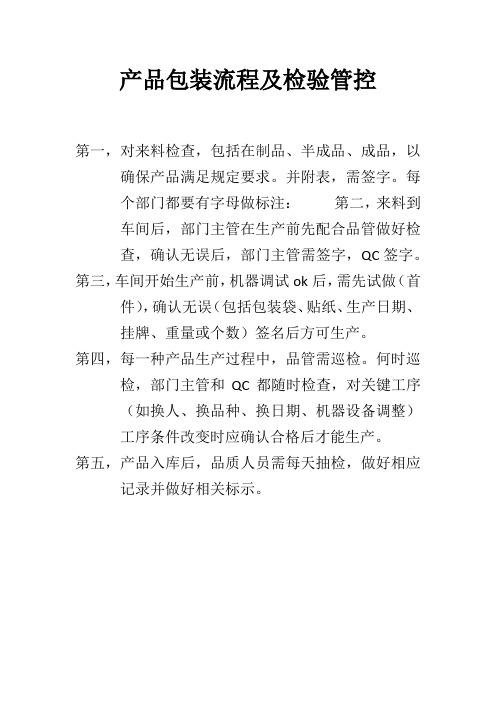
产品包装流程及检验管控
第一,对来料检查,包括在制品、半成品、成品,以确保产品满足规定要求。
并附表,需签字。
每
个部门都要有字母做标注:第二,来料到
车间后,部门主管在生产前先配合品管做好检
查,确认无误后,部门主管需签字,QC签字。
第三,车间开始生产前,机器调试ok后,需先试做(首件),确认无误(包括包装袋、贴纸、生产日期、
挂牌、重量或个数)签名后方可生产。
第四,每一种产品生产过程中,品管需巡检。
何时巡检,部门主管和QC都随时检查,对关键工序
(如换人、换品种、换日期、机器设备调整)
工序条件改变时应确认合格后才能生产。
第五,产品入库后,品质人员需每天抽检,做好相应记录并做好相关标示。
产品质量检验流程(顺序)
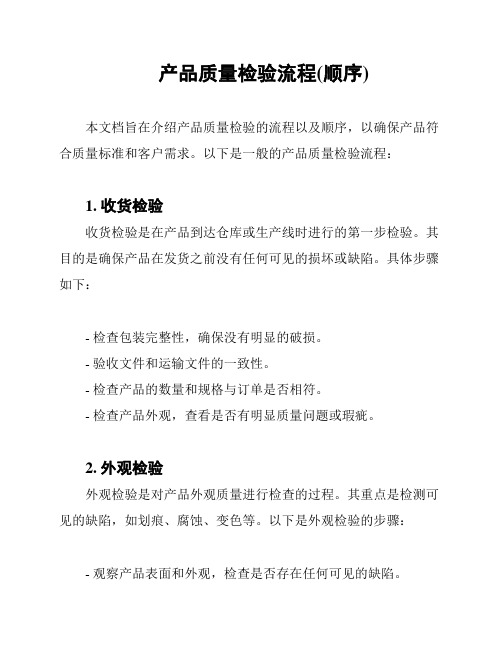
产品质量检验流程(顺序)本文档旨在介绍产品质量检验的流程以及顺序,以确保产品符合质量标准和客户需求。
以下是一般的产品质量检验流程:1. 收货检验收货检验是在产品到达仓库或生产线时进行的第一步检验。
其目的是确保产品在发货之前没有任何可见的损坏或缺陷。
具体步骤如下:- 检查包装完整性,确保没有明显的破损。
- 验收文件和运输文件的一致性。
- 检查产品的数量和规格与订单是否相符。
- 检查产品外观,查看是否有明显质量问题或瑕疵。
2. 外观检验外观检验是对产品外观质量进行检查的过程。
其重点是检测可见的缺陷,如划痕、腐蚀、变色等。
以下是外观检验的步骤:- 观察产品表面和外观,检查是否存在任何可见的缺陷。
- 检查产品的颜色、光泽度和纹理是否符合要求。
- 如果适用,进行产品尺寸和形状的测量,确保符合规格。
3. 功能性检验功能性检验是对产品功能的验证和测试。
其目的是确保产品能够按照预期的方式正常工作。
以下是功能性检验的步骤:- 根据产品说明书或技术规格书,检查产品的功能参数和性能标准。
- 进行适当的测试,以验证产品的功能是否符合要求。
- 如适用,进行必要的操作和操作步骤测试,以确保产品可以正常使用。
4. 可靠性检验可靠性检验是对产品在一定条件下持续运行的能力进行测试。
其目的是评估产品的可靠性和耐久性。
以下是可靠性检验的步骤:- 根据产品的设计寿命和使用环境,制定相应的可靠性测试方案。
- 进行负载、温度、湿度和振动等相关测试。
- 持续观察产品在测试期间的性能表现,并记录测试结果。
5. 批量抽检批量抽检是对大批量产品进行采样检验,以评估产品质量的过程。
其目的是通过对样本的检验,推断整个批次产品的质量水平。
以下是批量抽检的步骤:- 根据相关采样标准和检验水平,确定抽样方法和抽样数量。
- 针对样本进行外观、功能和可靠性等检验。
- 根据样本的检验结果,评估整个批次产品的质量合格率。
6. 最终检验最终检验是产品生产过程中的最后一步检验,其目的是确保产品符合质量标准和客户要求。
新产品包装检验流程
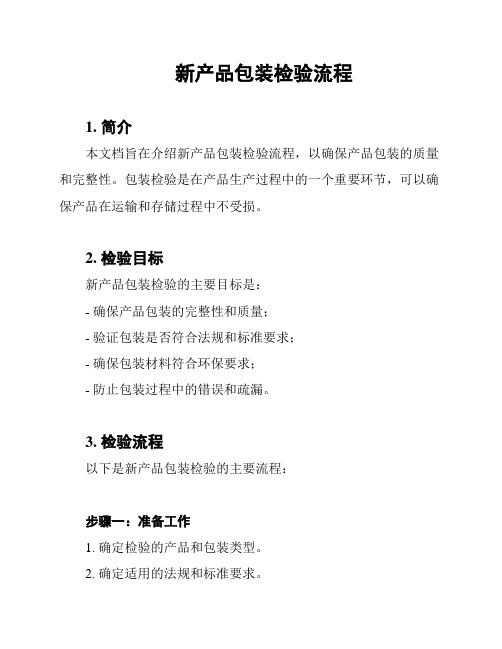
新产品包装检验流程1. 简介本文档旨在介绍新产品包装检验流程,以确保产品包装的质量和完整性。
包装检验是在产品生产过程中的一个重要环节,可以确保产品在运输和存储过程中不受损。
2. 检验目标新产品包装检验的主要目标是:- 确保产品包装的完整性和质量;- 验证包装是否符合法规和标准要求;- 确保包装材料符合环保要求;- 防止包装过程中的错误和疏漏。
3. 检验流程以下是新产品包装检验的主要流程:步骤一:准备工作1. 确定检验的产品和包装类型。
2. 确定适用的法规和标准要求。
3. 准备检验所需的设备和工具。
步骤二:外观检验1. 检查产品包装的外观是否完整,包括包装箱、保护材料和标签等。
2. 验证包装箱的尺寸和质量是否符合要求。
3. 检查标签上的信息是否准确、清晰可读。
步骤三:功能性检验1. 验证包装是否能够保护产品免受运输和存储过程中的损坏。
2. 检查包装材料的耐久性和防水性能等功能性要求。
步骤四:环境检验1. 检查包装材料是否符合环保要求,如是否采用可回收材料。
2. 验证包装材料是否符合相关环保标准和法规要求。
步骤五:记录和报告1. 记录检验结果和发现的问题。
2. 编写检验报告,包括产品包装的评估和建议改进措施。
4. 质量控制措施为确保检验过程的准确性和可靠性,需要采取以下质量控制措施:- 培训检验人员,使其熟悉检验流程和标准要求。
- 使用标准化的检验方法和工具。
- 定期校准和维护检验设备。
5. 结论通过遵循新产品包装检验流程,可以确保产品包装的质量和完整性,提高产品在运输和存储过程中的安全性和可靠性。
检验结果和报告将提供改进产品包装的指导和建议。
产品包装设计、核审及签样流程

7
包装样版
工程签样版
采购
工程部
半个工作日
1、采购对供应商提供的样版进行首次审核,符合后提交工程审核;2、工程对供应商制作的样版再次进行审核,并在样版上签字确认;3、工程将签字确认后的样版提交给业务确认;4、所有审核结果必须及时向PMC进行反馈。
《客户确认函》
业务部
1个工作日
1、业务将《包装材质、结构及尺寸说明书》《包装唛头说明书》提交给客户确认;2、客户确认后,须签署书面的《客户确认函》给业务部;3、业务将《客户确认函》反馈给PMC部;4、PMC根据客户确认结构及尺寸说明书》《包装唛头说明书》
《包装打样计划》
PMC部
半个工作日
1、PMC将经客户确认的《包装材质、结构及尺寸说明书》《包装唛头说明书》等相关资料提交给采购;2、采购根据采购周期及装配生产计划制定《包装打样计划》,并同供应商进行沟通。
6
《包装打样计划》《包装材质、结构及尺寸说明书》《包装唛头说明书》
包装样版(2-3个)
采购
1-2个工作日
8
工程签样版
客户签样版
业务
0.5-1个工作日
1、业务将工程签样版提供给客户进行确认;2、客户确认后须在样版上签字并将样版返回业务;3、业务将客户签样版回交给工程部;4、工程部将客户审核结果通知采购;5、客户签样版作为品管验货依据。
9
客户签样版
《采购计划》《采购合同》《采购进度跟进表》
采购
半个工作日
1、采购制定采购计划,制定《采购进度跟进表》;2、采购向供应商下单,制定《采购合同》;3、采购跟进供应商生产进度,并及时反馈供应商供货异常。