CO2腐蚀预测及其在井下管柱寿命预测中的应用
CO-,2-腐蚀速率预测模型研究现状
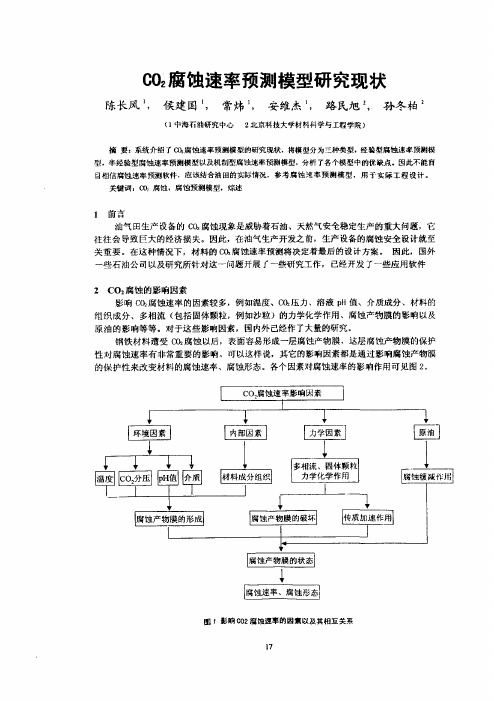
19
旷。,一[H一2CQ]! 一 i1+e一1 1—"1r+‘1 (5)
其中,巧是活化反应速率,%。是传质速率。其中 活化反应速率V,与DeWaard 91模型 相似,而传质速率可以计算为:
‰=2.45.万UO.12.PC02
(6)
其中U是流速m/s,d是水力直径m。考虑到腐蚀产物膜对腐蚀速率的影响,最后还要乘 以腐蚀产物膜因子。该模型进一步还引入了材料成分与微观组织对腐蚀速率的影响因子。 图4为利用模型计算的腐蚀速率。
(II)
腐蚀电流密度可以用两部分电流密度表示,一是活化反应电流密度“,另外一个就是
极限扩散电流密度。因此,单独求出其中各个值的大小,就可以得到腐蚀电流密度。但是, 该模型未考虑腐蚀产物膜对腐蚀速率的影响。
因此,Nasic又进一步建立了腐蚀产物膜覆盖条件下的机制模型9。该模型重点在于建 立膜的孔隙度对离子的扩散、迁移过程的影响方面,最终的目的仍然在于计算电极表面的 离子浓度,从而算出腐蚀电流密度。但Nesic建立的机制模型中未包含原油对腐蚀速率的 影响,这可能与目前大家对这方面机理的认识不足有关。另外,Nesic的机制模型只考虑一 般湍流流动对腐蚀速率的影响,不考虑流型、流态对腐蚀速率的影响。
腐蚀速率的影响,而DeWarrd模型中当含水率码o%以及流速大于lm/s时,腐蚀速率为零; 否则,原油对腐蚀速率不会产生缓蚀作用;OHIO大学的Jepson认为原油含量从o%增加到 60%时腐蚀速率逐渐下降,而ECE模型进一步给出了原油对腐蚀速率的影响因子”。但是, 总体来说,原油对腐蚀速率的影响研究还不充分,还未找到比较合适的参量来定量描述原 油对腐蚀速率的影响。
另外,OHIO大学的Jcpson针对海底管线油气水三相混输的情况,开发了多相流条件 下的CO:腐蚀预测经验模型,其腐蚀预测模型为o:
油气生产中CO2腐蚀与防腐技术

分压MPa
温度
110℃ 8.4639 8.6012 9.948 7.9002 9.948
0.5 0.75 1 1.25 1.5
在T< 70℃ 时,N80钢的腐蚀速率随温度的升高而增加 在T=70℃时达到极大值 当T> 70 时,N80 钢的腐蚀速率随温度的升高反而减小 在90℃ 附近又出现了腐蚀极小值,当温度再升高时,腐蚀速率也随着加快 当温度大于60℃ 时,随着CO2分压的增加,N80钢片的腐蚀速率出现了线性增大的 趋势
当pH 值小于4时,N80 钢在饱和CO2的3%NaCl水溶液中的腐蚀速率随 着pH 值增大而减小 当pH 值在4-9之间时,腐蚀速率为一常数值 在碱性条件下,腐蚀速率随着pH 值增大而减小
15
二氧化碳腐蚀影响因素
3、温度的影响
图6、温度对腐蚀的影响
T<60 ℃
60 ℃ <T< l00℃
T >150℃
不腐蚀 可能腐蚀 发生腐蚀
0.02MPa
0.2MPa
即当温度一定时,CO2气体的分压愈大,材料的腐蚀就愈快。
14
二氧化碳腐蚀影响因素
2、pH 值的影响
表2 不同pH 值下N80钢的腐蚀速率 pH 值 腐蚀速率mm/a pH 值 腐蚀速率mm/a 1 19.97 7 8.51 2 17.46 8 9.98 3 10.1 9 8.35 4 8.24 10 4.13 5 10.95 11 3.7
(4)
(5) (6)
析氢反应可按如下历程进行(1)(2)(3)(6)或(1)(2)(4)(5) 阴极反应:
pH<4
2H 2e H 2
H+的扩散是控制步骤
4<pH<6 H2CO3(吸附) + e- =H (吸附)+ HCO3- (吸附)
酸性气井井下管柱腐蚀预测模型及应用评价

酸性气井井下管柱腐蚀预测模型及应用评价
付 荣利 王 向 东 王 辉 胜利油田 海洋采油厂
摘 要 :在 酸 性 气 井 中 ,腐蚀 使 管 柱 的强度 大 大下 降 ,给 气 井的 开发 生产 带 来 巨大 的安 全 隐 患 。采 用 支持 向量机 方 法对 国 内某 油田的 2口生 产 气井进行 气井管 柱腐蚀 预 测 ,结果表 明 ,对 于
蚀 受 温 度 、HS含 量 、C 压 以 及 C 、 C 、 O分 l a
表 1 气井腐蚀环 境
经过计算得到两 口气井管柱的腐蚀情况 ,将预 测值 与管柱实际腐蚀 睛况进行对 比分析 ,如表 3 所示 。
表3 气井管柱腐蚀预测值与实际值对 比
C。 O分压 、气体流速 、p H值 、腐蚀产物膜 、Hs 以 1 腐蚀 影响 因素分析 及腐 蚀 介质 中其他 离子 含量 。 气井 的主要产 物是 烃类 气体 ,其 对 管柱不 会 产 ( )HS 蚀 。HS 二 元 酸 ,与 管 柱 发 生 电 2 腐 是 生 腐蚀 ,如果 气 体 中含 有腐 蚀 物质 如 C O 、HS 化学腐蚀 ,腐蚀产物一般是 FS e。当 FS e 在管柱致
多。对 气井 中存在 H s CO 两种 腐蚀介 质 的情 况 ,应重 点监 护 ,做 好 防腐措 施 并及 时更换 气井 和
管柱 。
关键词:C 。 O腐蚀 ;HS 腐蚀 ;气井管柱 ;支持向量机;腐蚀预测
d i 0 3 6 / i n 1 0 — 8 62 1 .0 0 7 o: .9 9 s .0 6 6 9 . 0 11 .4 1 .s
一
8 一 6
油 气 田地 面 工程 (tp/ w ht : ww.qd cc r) / y bmg .o n
抽油机井二氧化碳防腐技术应用

抽油机井二氧化碳防腐技术应用一、前言部分区块油井因二氧化碳腐蚀造成频繁躺井,直接影响油田的正常生产,油井二氧化碳腐蚀是制约油田生产开发的一个重要因素。
采用投放缓蚀剂、阴极保护器等措施效果不明显,通过对油井腐蚀机理的分析,提出防止油井二氧化碳腐蚀工艺措施,减少油井的腐蚀,延长了油井的检泵周期,节约了油田的检测和维修成本,提高油田的开发水平。
二、腐蚀影响因素研究1.腐蚀因素二氧化碳腐蚀钢材主要是二氧化碳溶于水生成碳酸而引起电化学腐蚀所致,主要考虑以下影响因素:1、二氧化碳分压的影响:二氧化碳分压小于0.021MPa 不产生腐蚀;在0.021~0.21MPa间为中等腐蚀;大于0.21MPa产生严重腐蚀。
2、矿化度的影响:溶液中以Cl-的影响最为突出,Cl-浓度越高,腐蚀速度越大,特别是当Cl-浓度大于3000mg/L 时腐蚀速度尤为明显。
3、流速的影响:一般认为随流速的增大,H2CO3和H+等去极化剂能更快地扩散到电极表面,使阴极去极化增强,消除扩散控制,同时使腐蚀产生的Fe2+迅速离开腐蚀金属的表面,因而腐蚀速率增大。
2.产出物分析2.1产出水在研究的过程中我们对30样本井进行了数据分析与采集,研究治理提供可靠依据。
通过对30口油井产出水的PH值、矿化度、氯离子含量和硫酸盐还原菌等指标进行分析,PH值为5.5~6.0,矿化度为44023~84040 mg/L,Cl-平均含36762mg/L ,SRB含量450~1000个/ml。
2.2伴生气将分析的伴生气中二氧化碳的含量和计算出的分压进行分析可知油井伴生气中二氧化碳的平均含量为1.78%,平均分压为0.28MPa。
油田产出水的二氧化碳含量相对较多,属于严重腐蚀等级,同时产出液的PH值较低(5.5~6.0),由此会产生严重的电化学腐蚀。
3.腐蚀影响因素认识通过腐蚀因素的实验分析,可以得出造成油井腐蚀的主要原因是:3.1油井含水率高,平均含水94.5%,介质的矿化度较高,Cl-、HCO3-等强腐蚀性离子含量高,溶液的PH值介于5.5~6.0之间,呈弱酸性,势必会造成油管、杆的电化学腐蚀。
油气井中的二氧化碳腐蚀

(4)
式中 : Ic—腐蚀速率 , mm / a; T—温度 , °K; R —气体常
数 , cal. /mole0 K。
D e W aard等认为 [ 1 ] ,在 70 ℃~80℃时 , CO2 的
腐蚀速率存在一个最大值 ,此后随温度升高 ,腐蚀速
率降低 ,这是因为生成了 FeCO3 或 Fe3 O4 膜 。这种 膜并不是在所有条件下都具有保护性 ,只有在高温
1. CO2 分压的影响 在影响 CO2 腐蚀速率的各个因素中 , CO2 分压
起着决定性作用 ,从式 ( 1)和式 ( 2)便可以看出 CO2 的腐蚀速率和 CO2 分压之间的关系 。Lohodny等 [ 8 ] 的研究表明 : 在气井中 , 当 CO2 分压大于 206. 85 kPa时将发生腐蚀 ;当 CO2 分压在 20. 685~206. 85 kPa 之 间 时 , 腐 蚀 有 可 能 发 生 ; 当 CO2 分 压 小 于
壁的剪切应力联系起来考虑的 ,因为流动直接影响
物质扩散和力矩的传递 。
当流速小于 1 m / s时 ,可以认为是静止的 ,此时
腐蚀速率较大 。因为在静止的条件下 ,没有紊流来
保证液相与保护性的烃及缓蚀成分的混合 ,加剧了
缝隙腐蚀和垢下腐蚀 。
流速在 1~3 m / s之间时 ,通常是层流 。此时 ,
膜的性质发生变化以后才具有保护性 ,这个温度被
称作成膜温度 。此时金属表面局部的 Fe2 + 浓度和
pH 值保证保护性膜的形成 ,这个温度取决于流速 、
pH值和 CO2 的分压等条件 ,当流速和 pH 值增高 、 CO2 分压降低时 ,成膜温度升高 。
成膜温度可以由式 (5)计算
log ( Fscale ) = 2400 / T - 0. 6 log ( FCO2 ) - 6. 7 ( 5) 当 log ( Fscale ) = 0时的温度即是成膜温度 。 将温度的影响用修正因子来表示 。
油气田CO2腐蚀及防控技术
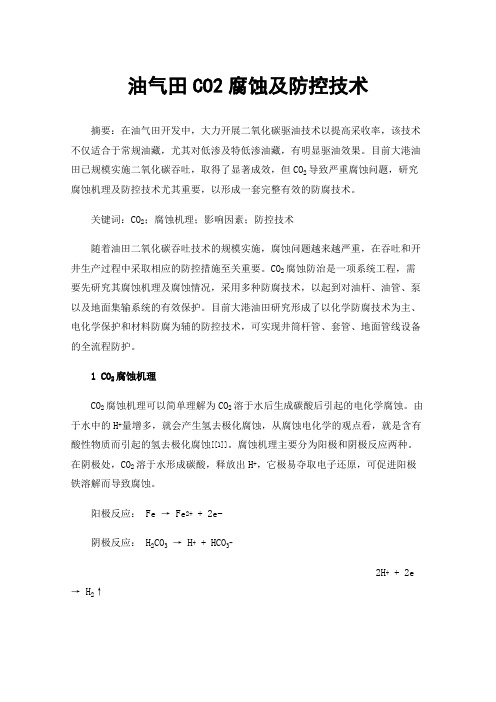
油气田CO2腐蚀及防控技术摘要:在油气田开发中,大力开展二氧化碳驱油技术以提高采收率,该技术不仅适合于常规油藏,尤其对低渗及特低渗油藏,有明显驱油效果。
目前大港油田已规模实施二氧化碳吞吐,取得了显著成效,但CO2导致严重腐蚀问题,研究腐蚀机理及防控技术尤其重要,以形成一套完整有效的防腐技术。
关键词:CO2;腐蚀机理;影响因素;防控技术随着油田二氧化碳吞吐技术的规模实施,腐蚀问题越来越严重,在吞吐和开井生产过程中采取相应的防控措施至关重要。
CO2腐蚀防治是一项系统工程,需要先研究其腐蚀机理及腐蚀情况,采用多种防腐技术,以起到对油杆、油管、泵以及地面集输系统的有效保护。
目前大港油田研究形成了以化学防腐技术为主、电化学保护和材料防腐为辅的防控技术,可实现井筒杆管、套管、地面管线设备的全流程防护。
1CO2腐蚀机理CO2腐蚀机理可以简单理解为CO2溶于水后生成碳酸后引起的电化学腐蚀。
由于水中的H+量增多,就会产生氢去极化腐蚀,从腐蚀电化学的观点看,就是含有酸性物质而引起的氢去极化腐蚀[[1]]。
腐蚀机理主要分为阳极和阴极反应两种。
在阴极处,CO2溶于水形成碳酸,释放出H+,它极易夺取电子还原,可促进阳极铁溶解而导致腐蚀。
阳极反应:Fe → Fe2+ + 2e-阴极反应: H2CO3→ H+ + HCO3-2H+ + 2e → H2↑碳酸比相同pH值下的可完全电离的酸腐蚀性更强,在腐蚀过程中,可形成全面腐蚀和局部腐蚀。
全面研究二氧化碳的腐蚀机理十分关键,2CO2腐蚀影响因素二氧化碳对金属材料的腐蚀受多种因素影响,有材质因素、压力、温度、流速、pH、介质中水和气体、有机酸、共存离子、细菌腐蚀等,本文主要介绍三种重要因素。
2.1 二氧化碳压力碳钢等金属的腐蚀速度随二氧化碳分压压力增大而加大,溶于水介质中CO2的含量增大,酸性增强,H+的还原反应就会加速,腐蚀性加大。
通过高温高压动态腐蚀评价来验证压力的影响,选取二氧化碳不同压力作为试验条件,对采出液在不同压力下评价腐蚀性。
二氧化碳驱注气井完井管柱设计

二氧化碳驱注气井完井管柱设计【摘要】co2驱是低渗透油藏补充地层能量、提高采收率的重要途径,针对co2驱注入井的特点,研究了具有锚定、反洗井、耐腐蚀和免压井作业功能的完井工艺管柱,在多口井中进行了应用,取得了较好的效果。
【关键词】二氧化碳驱注气免压井耐腐蚀完井管柱应用我国低渗透油藏资源丰富,其储量在新增探明储量中所占的比例逐渐增大,对于低渗透油藏提高采收率技术的研发和应用越来越收到重视[1]。
各油田也相继开展了co2驱油的室内研究工作,对co2的驱油机理、相态特征等取得了比较成熟的认识,但总体来说,现场应用井数还较少,在完井工艺管柱和防气窜方面还没有形成成熟的技术[3]。
1 co2驱注入井免压井作业完井管柱设计研究注入管柱是二氧化碳气进入地层的通道,是保证二氧化碳驱顺利进行的关键。
由于co2注入温度低,停注时会引起管柱蠕动,降低封隔器密封性能,同时考虑到环空保护液需要定期更换,气井压井困难等问题,设计了具有锚定、反洗井和免压井作业功能的完井管柱。
1.1 完井管柱结构及原理由于调整方案注气井转为生产井或其他原因需要更换管柱时,co2的高膨胀性使得施工过程存在较大的风险,为此设计了能够实现免压井分体丢手注气管柱。
管柱组成(从上至下):由井口悬挂器+反洗阀+安全接头+水力锚+密封插头+丢手及回接筒+蝶扳单向阀+y441封隔器+底部止回阀+筛管+丝堵等部分组成(见图1)。
丢手注气管柱中反洗阀的作用是在正常注气时油管连通,环空关闭,反洗井时与环空连通可替换保护液。
水力锚的作用是锚定管柱。
密封插头主要由插头及“o”型圈组成,主要作用就是与回接筒配套,起到连接丢手管柱与密插管柱并且密封的作用。
蝶板阀的原理是当蝶扳受到上部外力作用时,可翻转一定角度,从而实现内部的连通。
当蝶扳受到的外力消失时,蝶扳在弹簧力的作用下,可恢复原状,从而起到密封井内气体的的功能。
1.2 技术特点及技术指标a:采用锚定式管柱结构,可防止管柱蠕动,以确保注气作业正常进行,同时可保护丢手管柱上部套管。
CO2腐蚀油井水泥石的深度及其对性能的影响

CO2腐蚀油井水泥石的深度及其对性能的影响随着以石油工业为代表的工业领域的不断发展,大量的二氧化碳被排放在大气中,进一步加剧了全球气候变暖、气候灾害等问题。
同时,这些排放物也对环境产生了不可逆转的影响。
近年来,人们不断探索新的环保技术和工艺,以应对大气污染问题。
然而,除了寻求新的解决方案之外,我们也需要寻找其后果并加以控制和减少。
其中之一就是CO2对油井水泥石的腐蚀,本文旨在介绍 CO2 腐蚀油井水泥石深度及其对性能的影响的相关信息。
CO2腐蚀(carbonate corrosion)是指CO2在一定条件下与油井水泥石中的钙源反应,形成碳酸钙。
其反应具有一定的速度,在一定温度、压力、深度及CO2浓度等多重因素的共同作用下,CO2能够产生较为显著的腐蚀影响,导致水泥石的力学性能、渗透性能和耐化学性能等方面的下降。
CO2腐蚀的深度通常取决于CO2暴露的时间、CO2浓度、水泥石的质量和钙源,常常采用酸性溶液注入方法和高压瓶实验方法来模拟CO2腐蚀作用。
研究表明,CO2腐蚀深度与暴露时间和CO2浓度成正比关系,在同等环境条件下,腐蚀深度与钙源含量质量密切相关,钙源含量越高,腐蚀深度越浅。
这是因为钙源在水泥石中的存在能够与CO2形成碳酸类物质,形成一层保护膜,从而减缓或阻止CO2腐蚀水泥石的程度。
CO2腐蚀还会对水泥石的力学性能、渗透性能和耐化学性能产生重大影响。
在力学性能方面,由于CO2腐蚀加剧了水泥石内部的裂缝、孔洞和剥落等症状,导致抗压强度、抗拉强度、全弹性模量、裂缝扩展性等方面的性能均下降。
在渗透性能方面,CO2腐蚀会导致水泥石内部的孔径加大,孔洞增多,渗透性大幅度提高,从而使油井周边的水气体进入油管,降低油井的采收率。
在耐化学性能方面,CO2腐蚀也会使水泥石表面产生酸洞,并迅速降低水泥石的耐化学性能,导致水泥石更容易被化学物质侵蚀、溶解、剥落和破坏。
总的来说,CO2腐蚀是一种严重的水泥石腐蚀现象。
- 1、下载文档前请自行甄别文档内容的完整性,平台不提供额外的编辑、内容补充、找答案等附加服务。
- 2、"仅部分预览"的文档,不可在线预览部分如存在完整性等问题,可反馈申请退款(可完整预览的文档不适用该条件!)。
- 3、如文档侵犯您的权益,请联系客服反馈,我们会尽快为您处理(人工客服工作时间:9:00-18:30)。
2014年第7期内蒙古石油化工l9 C02腐蚀预测及其在井下管柱寿命预测中的应用李彦龙,董长银,陈新安,隆佳佳,许拓拓(中国石油大学(华东)石油工程学院,山东青岛266555)摘要:腐蚀是影响气井井下管柱寿命的重要因素,正确预测井下管柱的腐蚀速率是提高防腐效果的关键。
C O:腐蚀是富C O:气井管拄可靠性寿命的最关键制约因素。
笔者通过调研,对目前国内外油气田常用的腐蚀速率预测模型进行了分类和剖析,此基础上提出了气井井下管柱的可靠性使用寿命的预测方法,并建立了相应的模拟程序。
通过对比研究发现在低温低压条件下不同预测模型的预测结果相近,但是高温高压条件下的预测结果则相差较大,因此需要根据不同的矿场条件优选相应的腐蚀速率预测模型。
将腐蚀速率预测结果与井下管柱的安全使用厚度结合可以有效预测气井井下管柱的可靠性寿命。
研究结果对现场生产有一定的指导意义。
关键词:管柱寿命;C0:腐蚀;腐蚀速率;预测模型;井下管柱中图分类号:T E98文献标识码:A文章编号:1006--7981(2014)07一0019一04气井井下管柱的腐蚀损坏是困扰气田正常生产的主要制约因素之一。
针对气井井下管柱的腐蚀情况或使用寿命作出预测能有效保证气井的持续正常生产,并尽量避免意外事故的发生。
气井井下管柱的腐蚀损坏程度及使用寿命取决于气体组分,其中对管柱寿命影响最大的是C O:腐蚀。
目前关于气井井下管柱C O:腐蚀速率预测的模型较多[1’2],由于各模型所基于的机理和考虑的影响因素不同,不同预测模型的预测结果差异也因此较大。
根据建模基础的不同,C O:腐蚀速率的预测模型主要包括经验模型(含半经验模型,主要有L M D、L D L、N O R等)和机理模型(含N PO、M C3等)两类口J。
经验模型主要是基于矿场腐蚀数据或室内实验结果,机理模型则主要基于腐蚀热力学、动力学以及扩散动力学理论。
本文首先综述了矿场实际常用的几种C O:腐蚀速率预测模型及其适用条件,然后分析各模型的适应性及其对气井井下管柱使用寿命的影响。
在此基础上,编制了气井井下管柱可靠性寿命预测模型计算程序,并对模型进行了初步的验证。
1C0:腐蚀速率预测模型及其适应性分析以下仅介绍不同C O:腐蚀速率预测模型的理论计算式及理论预测结果,其具体的推导过程及分析请参考相关的参考文献。
1.1LM D模型1975年D e W aar d基于室内试验数据建立了C O:腐蚀速率预测模型,该模型仅假设腐蚀速率是温度和C O。
分压的函数。
随后该模型不断改进.L ot z 、M i l l i am s、D e W aar d于1991年引入了pH影响因子和腐蚀产物膜影响因子,并在1993年做了进一步的校正[1’5’6。
,从而形成了完整的LM D模型。
l og(C L M D)一f。
d。
[5.8一黑+0.67log(fc%]㈩式中,C。
M D为L M D模型预测得到的腐蚀速率,[m m/a];{C O表示2逸度,为腐蚀产物2C O bar f s cal e膜影响系数,无量纲。
1.2D L D模型D e W aa r d、L ot z、D ugs t a d(简称D LD模型)等人(1995)研究了流体流速对腐蚀速率的影响….提出了基于对管内C O:活化反应能及管内传质过程分析的电阻模型:上一上+上f9、C aD C A o。
C‰。
、。
’其中,C A ct表示由于C O。
活化反应导致的腐蚀速率,用下式表示:l og(cAc。
):4.93一半+o.58X109(h)(3)C一表示由于管内传质产生的腐蚀速率.用下式表示:T T0.8CM。
.=2.45X!薪x{co:(4’式中,U、d分别表示管内流体流速(m/s)和管内径(m)。
收稿日期:2014一02一06作者简介:李彦龙(1989一),男,甘肃定西人.汉族,中国石油大学在读硕士研究生.主要进行油气井防砂完井面的研究工作。
20内蒙古石油化工2014年第7期1.3N or s okM一506模型(N O R)基于对大量管流数据的分析研究,挪威国家能源科技协会(I FE)提出了N O R模型[8】,该模型已经成为挪威石油行业抗C O:腐蚀选材和腐蚀裕量设计标准比]。
,q\0146+0.3Z t l0810nv一=K。
×f…0.6,2×f杀)t-“'2×f(PH,(5)式中,K。
表示与温度和腐蚀产物膜相关的常数,无量纲;S为管壁切应力,Pa;f(PH,表示pH值影响因子。
1.4电化学模型(N PO)N es i c、Pos t l et hw ai t e、O l s en等(1995)指出,在C O:腐蚀过程中,阴极H+和H:C O。
浓度降低,阳极Fe被氧化为亚铁离子。
根据阴阳极电流密度相等可以建立C O:腐蚀速率的电化学预测模型(N P0)[9t1…。
i H+-I--i l l2C O。
+i H20+i02=i Fe(6)式中,i H+、I‘H2C O,、I’H20、i o。
分别表示H+被还原产生的电流密度、H:C0。
反应产生的电流密度、腐蚀壁面水分子的反应电流及氧在腐蚀壁面的传质过程产生的极限电流密度,A/m2。
上式中各电流密度通过电阻模型求解。
由上式可知,N PO模型能够预测不同电化学反应过程反应电流的大小,通过腐蚀电流与电极电势的关系可以求出腐蚀速率的大小,求出不同反应过程对全局腐蚀速率影响程度的大小。
1.5O hi oM uhi cor p3.0(M C3)模型该模型由俄亥俄大学多相流腐蚀研究中心的N or dsvee n、N es i c、N ybor g、St a ngel and等人提出[11,12],模型能预测水气两相流动过程中C O:腐蚀的电化学反应、化学反应、物质传递之间的耦合关系,能预测腐蚀过程中流体pH的变化规律、三相流中油水界面的高度以及段塞流条件下的全局腐蚀速率。
除以上介绍的几种油套管腐蚀速率预测模型外,还有B P公司的C a ssa ndr a模型、C or m ed模型、L i pucor模型、H ydr ocor模型、K SC模型、Sw eet Cor 模型、U L L等n],这些模型有些是做腐蚀风险的定性预测,有些由于计算程序复杂而应用较少,在此不作进一步阐述。
1.6模型适用条件分析笔者通过调研,总结了不同预测模型的适用条件,如下表1所示。
由于经验模型对现场数据或室内试验数据的依赖性很强,因此经验模型只能在模型建立时的边界条件范围内使用。
经验模型通过不同的修正因子来考虑不同的影响因素对腐蚀速率的影响,不能反映腐蚀发生的根本原因。
机理模型对腐蚀试验数据的依赖性较低,模型稍加修正便可以应用到其它方面的腐蚀预测。
但是,机理模型的建立需要对腐蚀机理、物质的扩散微观机理和关键性的控制因素有一个清晰和深入的认识,否则,模型将与实际情况偏差较大。
由以上分析可知,机理模型能够预测不同反应过程对全局腐蚀速率的贡献率,而经验模型则不能反映腐蚀过程的物理化学细节,只能输出全局腐蚀速率预测结果。
因此,为了使防腐措施更具针对性.选择机理模型显得比较合理。
但机理模型涉及物理化学方程较多,需要借助专门的计算机软件才能求解。
表1不同模型的适用条件警系譬总压c巳分压其他条件℃bar bar一 (1)L M D模型<80/<10D LD模型<901~1000<6.5撇模型20—150,Ⅷ0.1—10篙燃N PO模型20—800—1l~103<pH<6.流速O一2.5m/sM e3模型<1001—1000.1~25含水率209—l O O%.水平段塞流2气井管柱可靠性寿命预测方法图1气井井下管柱使用寿命预测思路如何根据油田生产实际选择合理的腐蚀速率预测模型是油套管寿命分析、成本控制及防腐措施实施的关键。
基于上述分析,笔者建立了气井腐蚀损坏及基于C O:腐蚀速率预测的井下管柱可靠性寿命预测的基本法,编制了应用程序。
基于C O :腐蚀速率2014年第7期李彦龙等C O z腐蚀预测及其在井下管柱寿命预测中的应用21预测的气井管柱可靠性寿命分析基本设计思路如图l所示。
应用上述方法,编制了用于气井腐蚀损坏程度预测和井下油套管使用可靠性寿命的预测计算程序,模拟计算了不同井况条件下的腐蚀速率变化情况。
当CO。
逸度为l ba r时,各模型预测的C O:腐蚀速率随温度的变化曲线如下图2所示:25r~—————1——一——一r一一————T————————r————————r——————H1l广————一——一【II…m-‘DLD『I一20}卜一’叫}“I…:…“I…一j一●一‘1,l—V-一懈l l,15}l一◆一N O R卜…÷…一j…j】f:…jI I平均值1I I,/204060温度,妒1∞120140围2当f(C02)=1bar时,不同预测模型预测的腐蚀速率随温度的变化趋势由上图可以看出,在低温条件下(t<60℃),不同模型预测的腐蚀速率均随着温度的升高而增大。
各模型的预测结果均小于l O m m/y。
当温度大于60℃时,经验模型的腐蚀速率预测结果随温度增加而有所降低,机理模型的预测结果随着温度的升高而持续增大。
造成这种现象的原因可能是机理模型没有考虑产物膜在高温条件下对腐蚀的抑制作用(N PO)或是由于模型本身的特征参数(管壁切应力)及基本假设与经验模型不同(M C3)。
N O R模型对腐蚀产物膜及pH变化的敏感性较强,因此在高温高pH条件下的腐蚀速率预测结果小于其它模型,但在低温条件下的预测结果却高于其他模型的预测结果,在100℃~150℃之间预测结果比其他模型更接近实际腐蚀速率。
图3和图4分别为60℃、120℃条件下不同模型预测的腐蚀速率随C O:逸度的变化曲线。
由图3、图4可知,在低温条件(60℃)下,不同模型的预测结果变化趋势一致,腐蚀速率随CO:逸度的增大而增大。
在高温条件(120℃)-F,机理模型预测的腐蚀速率随C O:逸度的增大而持续增大,经验模型预测的腐蚀速率随C O:逸度的增大略有降低或基本恒定。
由于经验模型考虑了腐蚀产物膜的影响,因此可以判断在高温条件下,腐蚀产物膜一旦形成,则腐蚀速率受cO:分压的影响将变小。
由以上分析可知,不同模型在不同温度和C O。
逸度条件下的腐蚀速率预测结果差异较大,其求解难易程度和适用条件都不同,因此必须在综合考虑上述因素的前提下优选出适合矿场实际的腐蚀速率预测模型。
将优选预测模型的预测结果与井下管柱的工作可靠性管壁壁厚做对比,就可以预测井下油套管的安全使用年限,即可靠性寿命。
00511522.53C02逸度』bar图3当t=60℃时,不同预测模型预测的腐蚀速率随C O:逸度的变化趋势15『i菰i.广I—]——『.—了77 110怪“1=≯pF。