数控机床主旋转运动无级调速传动设计
数控铣床主传动系统设计
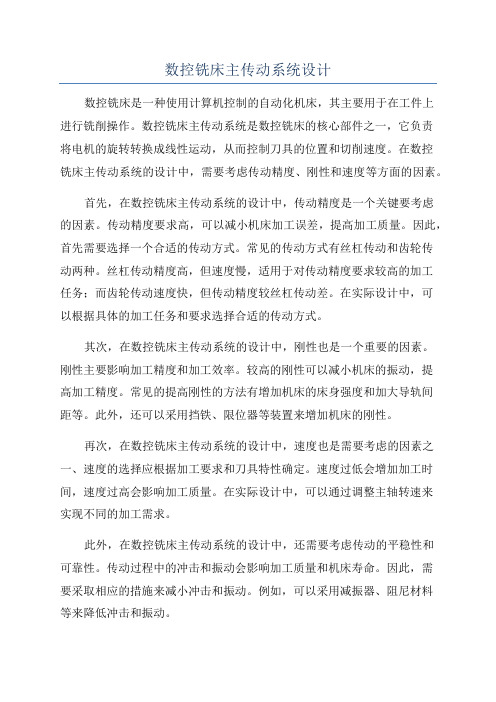
数控铣床主传动系统设计数控铣床是一种使用计算机控制的自动化机床,其主要用于在工件上进行铣削操作。
数控铣床主传动系统是数控铣床的核心部件之一,它负责将电机的旋转转换成线性运动,从而控制刀具的位置和切削速度。
在数控铣床主传动系统的设计中,需要考虑传动精度、刚性和速度等方面的因素。
首先,在数控铣床主传动系统的设计中,传动精度是一个关键要考虑的因素。
传动精度要求高,可以减小机床加工误差,提高加工质量。
因此,首先需要选择一个合适的传动方式。
常见的传动方式有丝杠传动和齿轮传动两种。
丝杠传动精度高,但速度慢,适用于对传动精度要求较高的加工任务;而齿轮传动速度快,但传动精度较丝杠传动差。
在实际设计中,可以根据具体的加工任务和要求选择合适的传动方式。
其次,在数控铣床主传动系统的设计中,刚性也是一个重要的因素。
刚性主要影响加工精度和加工效率。
较高的刚性可以减小机床的振动,提高加工精度。
常见的提高刚性的方法有增加机床的床身强度和加大导轨间距等。
此外,还可以采用挡铁、限位器等装置来增加机床的刚性。
再次,在数控铣床主传动系统的设计中,速度也是需要考虑的因素之一、速度的选择应根据加工要求和刀具特性确定。
速度过低会增加加工时间,速度过高会影响加工质量。
在实际设计中,可以通过调整主轴转速来实现不同的加工需求。
此外,在数控铣床主传动系统的设计中,还需要考虑传动的平稳性和可靠性。
传动过程中的冲击和振动会影响加工质量和机床寿命。
因此,需要采取相应的措施来减小冲击和振动。
例如,可以采用减振器、阻尼材料等来降低冲击和振动。
在数控铣床主传动系统的设计中,需要综合考虑传动精度、刚性、速度、平稳性和可靠性等方面的因素。
根据具体的加工要求和刀具特性,选择合适的传动方式和速度,同时采取一些措施来提高刚性和减小冲击和振动,从而实现高精度、高效率的加工。
数控铣床主传动系统的设计对于提高数控铣床的加工能力和精度至关重要,我们需要不断的优化和改进主传动系统的设计,以满足不断增长的市场需求。
数控车床主传动机构设计方案(doc 22页)

数控车床主传动机构设计方案(doc 22页)0 引言这次毕业设计中,我所从事设计的课题是经济型数控车床主传动机构设计。
此类数控车床属于经济型中档精度机床,这类机床的传动要求采用手动与电控双操纵方式,在一定范围内实现电控变速。
总体的设计方案就是对传动方案进行比较,绘出转速图,对箱体及内部结构进行设计,包括轴和齿轮的设计、校核等。
为什么要设计此类数控车床呢?因为随着我国国民经济的不断发展,我国制造业领域涌现出了许多私营企业,这些企业的规模普遍不大,没有太多的资本。
一些全功能数控系统,其功能虽然丰富,但成本高,对于这些中小型企业来说购置困难,但是中小型企业为了发展生产,希望对原有机床进行改造,进行数控化、自动化,以提高生产效率。
我国机床工业的发展现状是机床拥有量大、工业生产规模小,突出的任务就是用较少的资金迅速改变机械工业落后的生产面貌,使之尽可能提高自动化程度,保证加工质量,减轻劳动强度,提高经济效益。
我国是拥有300多万台机床的国家,而这些机床又大量是多年累积生产的通用机床,自动化程度低,要想在近几年内用自动和精密设备更新现有机床,不论是资金还是我国机床厂的能力都是办不到的。
因此,普通机床的数控改造,大有可为。
它适合我国的经济水平、教育水平和生产水平,已成为我国设备技术改造主要方法之一。
目前,我国经济型数控系统发展迅速,研制了几十种简易数控系统,有力地促进了我国数控事业的发展。
经济型数控机床系统就是结合现实的生产实际,我国的国情,在满足系统基本功能的前提下,尽可能地降低价格。
经济型数控车床有许多优点。
1)其降格便宜,且性能价格比适中,与进口标准数控车床相比,前者只需一万元左右,后者则需十万甚至几十万元。
因此,它特别适合于改造在设备中占有较大比重的普通车床,适合在生产第一线大面积推广。
从提高资本效率出发,改造闲置设备,能发挥机床的原有功能和改造后的新增功能,提高机床的使用价值。
2)适用于多品种、中小批量产品的适应性强。
机床主传动设计
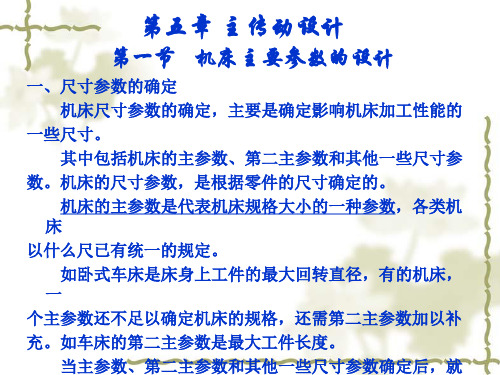
通用机床是为适应多种零件加工而设计制造的,主轴需 要变速。因此需确定它的变速范围,即最低与最高转速。
1).主轴最低(nmin)和最高转速(nmax)的确定
根据公式有:
nm in
1000 vm in
d m ax
nm ax
1000 vmax
2 、主电动机和传动机构须能供给和传递足够的功率和扭 矩,并具有较高的传动效率。
3、执行件(如主轴组件)须有足够的精度、刚度、抗振 性和小于许可限度的热变形和温升。
4 、噪声应在允许的范围内。 5、 操纵要轻便灵活、迅速、安全可靠,并须便于调整和 维修。 6 、结构简单、润滑与密封良好,便于加工和装配,成本 低。
此表不仅可用于转速、双行程数和进给量数列,而且也可用于机床 尺寸和功率参数等数列。表中的数列应优先选用。
图 7 1
3、公比的选用 a.对于通用机床,为使转速损失不过大,机床结构又不过于
复杂,一般取Ф=1.26或1.41。
b.对于大批量生产用的专用机床,自动化机床公比应取小些, 这些机床的生产率高,转速损失的影响显著,一般取 Ф=1.12或1.26
dm in
nmax和nmin的比值是变速范围Rn:
Rn nm ax nm in
注意:dmax和dmin不是机床上可能加工的最大和最小直径, 而是经济加工的最大和最小直径 (即不是理论上的最大和 最小直径),通常可取dmax= KD ; dmin=Rd dmax
最大加工直径dmax =( 0.5-0.6)D 最小加工直径dmin=(0.2-0.25)dmax
例:
以Ø 400mm普通车床为例,计算其主轴的极限转速。 (1)计算主轴最高转速nmax:
数控车床主传动系统的设计资料

数控车床主传动系统的设计资料1.传动方式:数控车床的主传动系统主要采用齿轮传动、皮带传动或蜗杆传动等方式实现。
齿轮传动具有传动效率高、传动比稳定等特点,适合数控车床的高精度加工。
皮带传动具有传动平稳、减震降噪等特点,适合一些对噪音要求较高的场合。
蜗杆传动则适用于需要大扭矩输出和自锁性能的情况。
2.主轴转速范围:数控车床的主传动系统需要设计具有较宽的主轴转速范围,以满足不同加工需求。
主轴转速范围的设计取决于工件材料的加工硬度、所需表面光洁度和所使用的刀具类型等因素。
通常情况下,数控车床的主轴转速范围可以从几十转/分钟到上万转/分钟。
3.主轴扭矩输出:数控车床主传动系统需要设计具有较大的主轴扭矩输出,以满足加工过程中的切削力需求。
主轴扭矩输出的设计取决于工件材料的加工硬度、切削类型和所使用的刀具等因素。
通常情况下,数控车床主轴扭矩输出可以达到几百牛·米以上。
4.切削力平衡:数控车床主传动系统需要设计具有良好的切削力平衡性能,以保证加工过程中的稳定性和精度。
切削力平衡的设计需要考虑主轴和工件的质量平衡、刀具的质量和刀具夹持方式等因素。
同时,还需要考虑冷却液的引入和排出,以保证加工过程中的冷却和润滑效果。
5.变速机构:6.轴向和径向刚度:数控车床主传动系统需要设计具有良好的轴向和径向刚度,以保证加工过程中的稳定性和精度。
轴向刚度的设计需要考虑主轴和工件的支撑形式和支撑点,径向刚度的设计需要考虑主轴轴承的选择和安装方式等因素。
同时,还需要考虑刀具切削力对主传动系统的影响。
7.自动换刀装置:总之,数控车床主传动系统的设计需要考虑传动方式、主轴转速范围、主轴扭矩输出、切削力平衡、变速机构、轴向和径向刚度以及自动换刀装置等因素,以实现高精度、高效率和可靠性的加工过程。
同时,还需要根据具体的加工需求和预算限制,选择合适的设计方案和关键部件。
数控机床主传动系统

伺服驱动系统的性能决定了数控机床的动态特性和加工精度。
主轴与卡盘
主轴是数控机床主传动系统的输 出部件,它能够带动刀具或工件
旋转。
主轴通常采用高精度轴承和刀具 夹紧装置,以确保加工过程中的
稳定性和精度。
类型与分类
类型
数控机床主传动系统根据其结构和工作原理的不同,可以分为多种类型,如机械主传动系统、液压主 传动系统、电气主传动系统等。
分类
数控机床主传动系统还可以根据其传动方式的不同进行分类,如带传动、链传动、齿轮传动等。不同 类型的数控机床主传动系统具有不同的特点和应用范围,需要根据具体的加工需求和加工条件进行选 择。
主轴定位精度与重复定位精度
主轴定位精度
主轴在特定位置的准确度,决定了加 工零件的尺寸精度。定位精度越高, 加工精度越好。
重复定位精度
主轴在相同位置的重复精度,反映了 主轴运动的稳定性。重复定位精度越 高,主轴运动越稳定。
热稳定性与动态特性
热稳定性
主轴在切削过程中抵抗温度变化的能力,热稳定性越高,加工过程中主轴的性能越稳定。
动态特性
主轴在动态切削过程中的表现,包括振动、噪声等。动态特性越好,切削过程越平稳,加工表面质量越高。
04
主传动系统的控制技术
数控编程与加工技术
数控编程
根据加工需求,使用数控编程语言(如G代码)对机床进行编程,以控制主轴的运动轨 迹和加工过程。
加工工艺
根据工件材料、加工要求和刀具特性,选择合适的加工工艺,如粗加工、半精加工和精 加工等,以确保加工质量和效率。
特点
数控机床主传动系统具有高精度、高 效率、高稳定性等特点,能够满足复 杂、高效、高ห้องสมุดไป่ตู้度的加工需求。
普通数控车床主传动系统设计

普通数控车床主传动系统设计1. 引言普通数控车床主传动系统是数控车床中的核心部件之一,主要负责提供动力和转速控制,以实现对工件的加工操作。
本文将详细介绍普通数控车床主传动系统的设计原理和关键要素。
2. 设计原理普通数控车床主传动系统的设计原理基于数控技术和机械传动原理。
其根本原理如下:•主电机提供动力:普通数控车床主传动系统的第一要素是主电机。
主电机通过机械传动装置将动力传递给主轴,驱开工件的旋转运动。
•变速装置实现转速控制:为了满足不同加工需求,普通数控车床主传动系统通常配备了变速装置。
变速装置可以改变主轴的转速,使其适应不同工件加工的要求。
•控制系统实现精确控制:普通数控车床主传动系统的另一重要元素是控制系统。
控制系统通过编程控制,实现对主电机和变速装置的精确控制,确保工件加工的精度和稳定性。
3. 设计要素3.1 主电机选择主电机是普通数控车床主传动系统的关键组成局部。
在选择主电机时,需要考虑以下因素:•功率:根据加工要求和工件材料的硬度,选择适当的主电机功率,以确保足够的动力输出。
•转速范围:根据加工要求和工件材料的特性,选择主电机的转速范围,以满足不同加工情况下的转速要求。
•耐久性:主电机应具有较高的耐久性和可靠性,以适应长时间运行和重复工作的需求。
3.2 变速装置设计变速装置的设计对普通数控车床主传动系统的性能和灵巧性有重要影响。
在设计变速装置时,需要考虑以下因素:•传动比:根据不同的加工要求,设计适宜的传动比,以实现主轴转速的调整。
•换挡操作:如果变速装置采用机械换挡方式,需要考虑换挡操作的平稳性和可靠性。
如果采用电子控制方式,那么需要确保换挡速度和精确性。
•维护和保养:变速装置应设计成易于维护和保养,以提高系统的可靠性和使用寿命。
3.3 控制系统设计控制系统是普通数控车床主传动系统的智能化局部。
在设计控制系统时,需要考虑以下要素:•控制精度:控制系统应具有较高的精度,以满足工件加工的精度要求。
数控机床一般都是无极调速ppt课件

精选编辑ppt
20
伺服变压器
就是将380V变成 220v, 三相交流伺服每相输 入是380V,输出为 220V。因为系统和伺 服驱动都需要用到 220V的电压。
精选编辑ppt
21
刀架电机
刀架电机
发信盘
精选编辑ppt
22
思考
• 同学们,在进行数控机床电气线路安装时, 能否分的清它们之间接线联系?
精选编辑ppt
5
屌丝逆袭记
因为在数控机床中,存在中数控系统、伺服驱 动器、变频器、伺服电机,使得数控机床能够 实现自动化、高精度和高效率。
屌丝想要逆袭,成为高富帅,就得购买数 控系统、伺服驱动器、变频器、伺服电机 等,可以让普通机床改造成数控机床。
精选编辑ppt
6
从电气原理图上进行比较
精选编辑ppt
17
编码器的作用
• 它是一种将旋转位移转换成一串数字脉冲 信号的旋转式传感器,这些脉冲能用来控 制角位移,如果编码器与齿轮条或螺旋丝 杠结合在一起,也可用于测量直线位移。
• 编码器产生电信号后由数控制置CNC、可 编程逻辑控制器PLC、控制系统等来处理。
• 可以将进给轴的位置移动反馈给系统,而 且使得机床的加工精度更高。
• 能进行华中系统的整机电气线路安装与参 数调试。
• 能FANUC数控系统机床的电气线路安装与 参数调试
• 能进行系统信号线的焊线工作。
精选编辑ppt
11
介绍数控机床各套装
• 数控系统 • 伺服驱动器 • 伺服电机 • 变频器 • 伺服变压器
精选编辑ppt
12
日本FANUC数控系统;
数控系统
广数系统
•
2、采用自动排屑装置 数控车床大都采用斜床身结构布局,排屑方
经济型数控机床主传动系统的运动设计

第5卷 第2期集美大学学报(自然科学版)Vol.5 No.2 2000年6月Journal of Ji mei University(Natural Science)Jun.2000 [文章编号]1007-7405(2000)02-0044-04经济型数控机床主传动系统的运动设计孙长久(集美大学机械与电子工程系,福建厦门361021)[摘要]分析了变频调速交流电机的功率特性和转矩特性以及主运动为回转运动数控机床的功率特性和扭矩特性,提出经济型数控机床主传动系统分段无级变速传动的运动设计原则,并就几种设计情况进行了分析.[关键词]数控机床;主传动系统;变频调速交流电机;功率特性;转矩特性;功率匹配[中图分类号]TH132;TM344.4[文献标识码]A0 引言数控机床应该随工件或刀具直径的变化,以及不同的加工材料的要求,提供最适应的切削速度,常采用主轴伺服单元和交流主轴电机构成主传动调速系统.经济型数控机床限于制造成本,多采用交流异步电机串接齿轮构成有级变速,虽然能够满足加工要求,但是缺点也很明显,例如要改变切削速度,需停车手动变速.若用交流异步电机配置变频调速器直接拖动主轴,虽能无级变速,但电机低速输出功率小,不能满足强力切削要求.由于轴承极限转速和额定频率影响,电机转数不能太高,恒功率范围受到限制.经济型数控机床主传动系统一直难于平衡系统性能和制造成本的矛盾.目前国内研制的YP系列主轴变频调速交流电机,采用特殊电磁设计,低速性能好,恒功率范围宽,如果和磁通矢量控制变频调速器配合构成主传动调速系统,性能接近主轴伺服单元和交流主轴电机构成的调速系统,价格却低许多,为经济型数控机床主传动系统高性能低成本设计提供了解决方案.1 变频调速交流电机的功率特性和转矩特性变频调速交流电机的功率特性和转矩特性见图1.50Hz额定频率转速为n d,200Hz对应的最高转速为n dmax,2Hz对应的最低转速为n dmin,n d到最高转速n dmax的区域 为恒功率区,电机输出全部功率,恒功率调速范围R dp=n dmax/n d=4,输出转矩随转速的增加而减少.最低转速n dmin到n d的区域 为恒转矩区,电机输出最大转矩,恒转矩调速范围R dt= n d/n dmin=25,输出功率随转速的下降而下降.全部工作频率内电机的调速范围R nd=R dt R dp=25 4=100.[收稿日期]1999-10-21[作者简介]孙长久(1954-),男,讲师,从事机械制造和机电传动控制方向研究.图1 调速电机的功率和转矩特性2 数控机床主轴的功率特性和扭矩特性回转运动数控机床主轴的功率特性和扭矩特性见图2,n j 是机床主轴传递全部功率的最低转速,称为计算转速.n j 到最高转速n max 的区域 为恒功率区,应能传递全部功率,恒功率变速范围R np =n max /n j ,一般为20左右,切削扭矩随转速的降低而增大.n j 以下到n min 的区域 为恒扭矩区,应能输出最大切削扭矩,恒扭矩变速范围R nt =n j /n min 较小,一般为5~8,传递功率则随转速的降低而降低.数控机床主传动系统设计,应能满足主轴的功率特性和扭矩特性要求.图2 机床主轴的功率和扭矩特性3 主传动系统分段无级变速传动方案的确定和分析3.1 传动方案的确定调速电机恒功率范围小于机床主轴恒功率范围,恒转矩范围又大于机床主轴恒扭矩范围,两者机械特性不相匹配,直接驱动主轴使低速段最大切削扭矩降低,需在调速电机和机床主轴之间串接一个机械分段变速装置扩大调速电机的恒功率范围,使两者机械特性相匹配.一般按类比法确定调速电机功率P 、典型加工条件最大切削扭矩T ma x 、主轴最高转速n ma x 和最低转速n min ,算出主轴的计算转速n jn j =9550P /T maxn j 是同时满足调速电机全部功率和主轴最大切削扭矩的最低转速,根据n j 和n ma x 可求出主轴恒功率范围为R np =n ma x /n j .若调速电机恒功率范围为R dp ,串接的机械分段变速装置的调速范围R 分为R 分=R np /R dp = (Z-1)F (1)其中 F 和Z 分别为分段变速装置的公比和级数由式(1)得: Z =(lg R np -lg R dp )/lg F + 1.其中Z 应为整数,一般取Z =2、3、4等.若取Z =3,主轴配置的三个传动副使支承长度增加,刚度下降,不宜采用.取Z =4,主轴箱需增加两对传动副和一根传动轴,对制造成本和系统可靠性不合适,也不宜采用.经济型数控机床主传动系统多取Z =2构成两级传动:低速级和高速级.低速级计算转速n 1j 也是主轴的计算转速n j ,相对应的是调速电机的额定转速n d .这样低速级传动比便可确定为i 1=n j /n d低速级最低转速n 1min 和最高转速n 1ma x 也随之确定,即n 1mi n =i 1 n dm i n ,n 1max =i 1 n dmax45 第2期孙长久:经济型数控机床主传动系统的运动设计低速级传动比i 1,对于齿轮传动,受径向结构尺寸限制,i 1 1/4.对带传动,受安装位置和传动效率限制,i 1 1/3.若i 1不满足要求,可在调速电机与分段变速装置之间增加一定比减速传动副使i 1满足上述要求.高速级传动比为i 2=i 1 FF 一般按调速电机恒功率范围R dp 取,即 F =R dp .则高速级的计算转速n 2j 和最高转速n 2max 为 n 2j =i 2 n d =n 1max ,n 2m ax =i 2 n dmax即高速级的计算转速n 2j 和低速级的最高转速n 1ma x 相等,高低两级功率特性曲线见图3.3.2 传动方案的分析由图3看出:高低两级功率曲线重合,全部转速范围的功率得到充分利用,是较理想的方案.若高速级最高转速低于机床主轴最高转速,即n 2max <n max 时,要求 F >R dp ,使n 2max 和n max 相等.由功率特性图4上看出n 1max 和n 2j 不相衔接,造成间断,间断区转速范围为n 2j -n 1ma x =i 2 n d -n d R dp =n d ( F -R dp ).这一范围通过调速电机恒转矩区变速得到,电机输出功率小于额定输出功率,造成功率损失.设 = F /R dp , 为 F >R dp 时的功率损失系数,则功率降低区的最低输出功率为P 0=P / =P R dp / F若 1.1,则P 0 90%P ,对切削加工影响不大,可不作考虑.但当功率损失过多时,为使主轴在功率降低区仍能得到所需的功率,需增大电机的功率到P 1 P ,电机功率比 F =R dp 时的功率大 倍.当电机转速处在恒功率区时又增加了电力消耗,经济性受到一定影响.为避免电机功率过大, 1.41,即不要超过调速电机功率等级的级比.当 F <R dp 时,功率特性见图5.高低两级部分转速重合,其范围为n 1max -n 2j ,重合度 =R dp / F . <1.2,以免主传动恒功率范围太窄.部分转速重合设计方式适合机床主轴转速跨于两级之间又能实现不停车连续变速的场合,数控车床主传动多采用这种设计方式.以上设计过程没有考虑系统内传动元件造成的功率损失.图3高低速二级功率曲线衔接图4高低速二级功率曲线分开图5 高低速二级功率曲线重叠4 结论1)主轴变频调速交流电机串接两级机械变速装置,可以最少的传动元件构成经济型数 46 集美大学学报(自然科学版)第5卷控机床主传动系统.如取两级变速装置级比 F 等于调速电机恒功率范围R dp ,可使调速电机的恒功率范围扩大为R 2dp ,基本满足机床主轴的机械特性和调速范围要求.2)可使主传动系统具有硬机械特性.如构成主轴转速反馈,可在整个切削负荷范围内使主轴转数波动率不超过 0.2%.利用变频调速器的低频转矩提升功能和外接制动电阻,使系统低速转矩提高30%并能满足电磁制动要求,进一步简化了主传动系统的结构,提高了可靠性.3)性价比高.性能接近主轴伺服单元和交流主轴电机调速系统,而价格仅为其三分之一.可应用于经济型数控机床和低价位加工中心,具有广泛的推广应用前景.[参考文献][1]戴 曙.数控机床设计讲座[J].制造技术与机床,1994,(9):49-52.[2]廖效果.数字控制机床[M ].武汉:华中理工大学出版社,1992.183-184.[3]崔永平.关于两档无级变速主传动系统初步设计的分析[J].制造技术与机床,1995,(12):28-29.The Movement Design of the Main Transmission Systemfor Economic Numerical Control Machine ToolSUN Chang -jiu(Dept.of Mechanical and Electronic Engineer i ng ,Ji mei Uni versity,Xiamen 361021,China)Abstract:This paper analyzes the power character and torque character for frequency conversion timing AC motor,and the po wer character and torque character for the spiddle of machine tool whose main movement is rotation.Some designing principles are brought forward on the subsection stepless variable drive for main transmission syste m of economic numerical machine tool,and the analyse are carried out on the designs and calculations in different cases.Key w ords:numerical contral machine tool;main transmission system;frequency conversion timing AC motor;power character;torque character;matching 47 第2期孙长久:经济型数控机床主传动系统的运动设计。
- 1、下载文档前请自行甄别文档内容的完整性,平台不提供额外的编辑、内容补充、找答案等附加服务。
- 2、"仅部分预览"的文档,不可在线预览部分如存在完整性等问题,可反馈申请退款(可完整预览的文档不适用该条件!)。
- 3、如文档侵犯您的权益,请联系客服反馈,我们会尽快为您处理(人工客服工作时间:9:00-18:30)。
-- -- 数控机床主旋转运动无级调速传动设计
摘 要:对主旋转运动无级调速设计类型、方案作了分析,并对带有分级变速机构的无级
调速主传动设计,从理论上分析论证了主轴转速连续的条件。 下面给出了一个具体的设计举例。 关键词:无级调速;主旋转运动;分级变速 --
-- 1 概述 随着近代电机控制技术的不断发展,交流变频无级调速主轴电机使数控机床主传动实现无级调速,解决了直流电机长期运转产生整流火花和电刷磨损的难题,同时也省掉了一些不必要的浪费,节省了资源。曾为主要动力源的直流调速电机,在多数数控机床主旋转运动中逐渐被一些交流调速主轴电机所取代。 无级调速主传动系统按品种和工艺范围的不同,分为两类,一类是高速专能化数控机床,一类是通用化数控机床。这两类机床的主传动系统的设计有较大差别,传动方案也大不相同。 下面就是我对上述两类机床进行的分析,给出设计方案及相关参数,对串联分级变速机构的主传动无级调速系统的设计方法,从理论上加以分析论述。最后给出一个设计示例。希望通过我的介绍以后大家对无级调速主传动系统有更加进一步的了解。 --
-- 2 高速专能化数控机床主传动无级调速 通过一些相关的资料我了解到:对要求主轴转速高,变速范围和恒功率区变速范围都较小的数控磨床、高精密数控车床等,工作时除了高速外,切削深度和进给量相对都小,而切削功率和转矩也小,通常不必选用大功率的交流无级调速主轴电机,也不需要串联分级变速机构和增大恒转矩区的转矩。只要根据具体设计要求,选用合适的交流无级调速的主轴电机,任意的采用下列传动方案之一,都可以实现对高速专能化数控机床主传动实现无级调速的功能,下面我们分别来介绍这两种方案。 2.1 选用内装式主轴电机(即电主轴)
所谓内装式主轴电机,就是主轴箱和电机融为一体,电机转子就是主轴,主轴是中空的,头部是标准结构,便于安装卡盘和刀具,电机座就是主轴箱体,可安装在床身上。除此外,无任何中间传动件,结构简单,传动精度和机械效率都很高。主轴的实际工作转速高于电机的基本转速nd,nd=1500 r/min,小功率的nd=2000 r/min,这类机床的恒功率区变速范围小,通常都在3-5,内装式主轴电机完全能满足要求。目前国外这类数控机床和加工中心主轴最高转速可达到几万转,一般都在5000-6000 r/min,我国因刀具技术水平限制,最高转速5000 r/min,一般都在3500 r/min左右,已有成套设备生产供应。 2.2 选用输出转换型主轴电机
这种电机既能变频调速,又能切换绕组(即变级)分档变速,使电机本身的调速范围和恒功率区调速范围增大,以满足机床主轴较大变速范围的要求。若电机输出轴与机床主轴之间采用多联V型带或齿型带降速传动,可实现低速增转矩功能。目前,皮带传动的小型机床转矩可达到245 N·m,中型机床转矩大于490 N·m,大型机床达到785-1177 N·m。主轴系统和进给系统有很大的差别。根据机床主传动的工作特点,早期的机床主轴传动全部采用三相异步电动机加上多级变速箱的结构。随着技术的不断发展,机床结构有了很大的改进,从而对主轴系统提出了新的要求,而且因用途而异。在数控机床中,数控车床占42%,数控机床的钻镗铣床占33%,数控磨床、冲床占23%,其他只占2%。为了满足量大面广的前两类数控机床的需要,对主轴传动提出了下述要求:主传动电动机应有2.2~250kW的功率范围;要有大的无级调速范围,如能在1:100~1000范围内进行恒转矩调速和1:10的恒功率调速;要求主传动有四象限的驱动能力;为了满足螺纹车削,要求主轴能与进给实行同步控制;在加工中心上为了自动换刀,要求主轴能进行高精度定向停位控制,甚至要求主轴具有角度分度控制功能等等。 主轴传动和进给传动一样,经历了从普通三相异步电动机传动到直流主轴传动,而随着微处理器技术和大功率晶体管技术的进展,现在又进入了交流主轴伺服系统的时代,目前已很少见到在数控机床上有使用直流主轴伺服系统了。但是国内生产的交流主轴伺服系统的产品尚很少见,说明我们在这个领域的知识水平还很欠缺,大多采用进口产品,因此我们在这方面的发展潜能还是很大的,还有待我们去进一步完善和发展。 正如19.3.1节所述,交流伺服电动机有永磁式同步电动机和笼型异步电动机两种结构形式,而且绝大多数采用永磁式同步电动机的结构形式。而交流主轴电动机的情况则不同,交流主轴电动机均采用异步电动机的结构形式,这是因为,一方面受永磁体的限制,当电动机容量做得很大时,电动机成本会很高,对数控机床来讲无法接受采用;另一方面,数控机床的主轴传动系统不必像进给伺服系统那样要求如此高的性能,采用成本低的异步电动机进行矢量闭环控制,完全可满足数控机床主轴的要求。但对交流主轴电动机性能要求又与普通异步电动机不同,要求交流主轴电动机的输出特性曲线(输出功率与转速关系)是在基本速度以下时为恒转矩区域,而在基本速度以上时为恒功率区域。交流主轴控制单元与进给系统一样,也有模拟式和数字式两种,现在所见到的国外交流主轴控制单元大多-- -- 都是数字式的。下图 示出了交流主轴控制单元的框图。 伺服电动机的传递函数为:G﹙s﹚=K/S﹙Tm+1﹚ ⑴积分控制电路及输入输出波形 其传递函数为:G﹙s﹚=1/s
图2-1 图2-2 ⑵微分控制电路及输入输出波形 其传递函数为:G﹙s﹚=s
(a) 输入波形;(b)输出波形 --
-- 图2-3 ⑶ PWM控制电路的基本构成及工作原理: 开关电源一般都采用脉冲宽度调制(PWM)技术,其特点是频率高,效率高,功率密度高,可靠性高。然而,由于其开关器件工作在高频通断状态,高频的快速瞬变过程本身就是一电磁骚扰(EMD)源,它产生的EMI信号有很宽的频率范围,又有一定的幅度。若把这种电源直接用于数字设备,则设备产生的EMI信号会变得更加强烈和复杂. 由于各个变换通道交叉开闭,电流相互叠加,大大减少了输入、输出电流纹波,减小了电磁干扰EMI。电流纹波的减少,使传统的昂贵的、不易安装的电解电容器可以采用小型的贴片陶瓷电容来代替。参看图2-4 中输出电流纹波的示意图,2个通道的IL纹波电流相互叠加,结果使输出电容上承受的纹波电流减小。
图2-4 它们的工作过程简述如下:由数控系统来的速度指令(如10V时相当于6000r/min或4500r/min)在比较器中与检测器的信号相与之后,经比例积分回路3将速度误差信号放大作为转矩指令电压输出,再经绝对值回路4使转矩指令电压永远为正。然后经函数发生器6(它的作用是当电动机低速时提高转矩指令电压),送到V/F变换器7,变成误差脉冲(如10V相当于200kHz)。该误差脉冲送到微处理器8并与四倍回路17送来的速度反馈脉冲进行运算。在此同时,交预先写在微处理器部件中的ROM中的信息读出,分别送出振幅和相位信号,送到DA强励磁9和DA振幅器10。DA强励磁回路用于控制增加定子电流的振幅,而DA振幅器用于产生与转矩指令相对应的电动机定子电流的振幅。它们的输出值经乘法器11之后形成定子电流的振幅,送给U相和V相的电流指令回路12。另一方面,从微处理器输出的U、V两相的相位(即sinθ和sin(θ-120°))也被送到U相和V相的电流指令回路12,它实际上也是一个乘法器,通过它形成了U相和V相的电流指令。-- -- 这个指令与电机电流反馈信号相与之后的误差,经放大后送至PWM控制回路14,变成频率为3kHz的脉宽信号。而W相信号则由Iu、Iv两信号合成产生。上述脉冲信号经PWM变换器15控制电动机的三相交流电流。脉冲发生器16是一个速度检测器,用来产生每转256个脉冲的正、余弦波形,然后经四倍回路17变成1024脉冲/r。它一方面送微处理器,另一方面经F/V变换器19作为速度反馈送到比较器2,并与速度指令进行比较。但在低速时,由于F/V变换器的线性度较差,所以此时的速度反馈信号由微分电路18和同步 整流电路20产生。
--
-- 3 串联分级变速机构的主传动系统 对于通用型数控机床,如数控车床、铣床、镗床及加工中心,要求主轴变速范围Rn≥100-200,恒功率区的变速范围尽量大,当主轴最低转速拟定后,主轴的计算转速应较低,主轴的恒转矩区增转矩作用较大,满足低速大转矩的切削加工要求。实现这些功能应在交流无级调速主轴电机后串联分级变速机构,这种交流变频主轴电机,最高转速为4500r/min,基本转速nd为1500 r/min,最低转速为45 r/min,显然电机的恒功率区不能满足机床要求。应串联分级变速机构,扩大电机恒功率区变速范围。另外,电机的额定功率比同类型的通用机床要选得高些,若传动系统设计得好,主轴恒动功率区无功率缺口或缺口很小,也可能不需要选大功率的电机。 选用较大功率的原因有二,一是电机在恒转矩区运行时,应保证主轴在最低转速切削时有足够大的功率;二是因主轴在恒功率区工作时,有些系统会出现功率缺口,为在缺口低谷处功率应保证传递全部功率,只有选择额定功率较大的电机给予补偿。 我国引进并国产化的BESK系列的交流主轴电机适用于这类机床,连续运转额定功率分别为7.5、11、15、18.5、22 kW五种规格,电机的最高转速ndmax=4500 r/min,基本转速nd=1500 r/min,最低转速nmind=45 r/min。其功率转矩特性曲线如图3-1所示。
图3-1电机功率转矩特性图 由图2看出,电机在恒转矩区功率随转速降低而减小,当电机转速低于300 r/min时因功率的减小而不能利用,实际可用的电机最低转速取决于机床所要求的最小切削功率和电机的额定输出功率。
3.1 确定初选电机功率
根据机床要求,初选电机功率,并考虑主传动®机械总效率系数约为η=09;电机功率选得适当主轴恒功率区无缺口或有微小缺口,电机功率选得较大 主轴恒功率区允许有略大的缺口。
3.2 确定最小输出功率