第四章金属材料及热处理
金属材料及热处理第四单元 铁碳合金相图
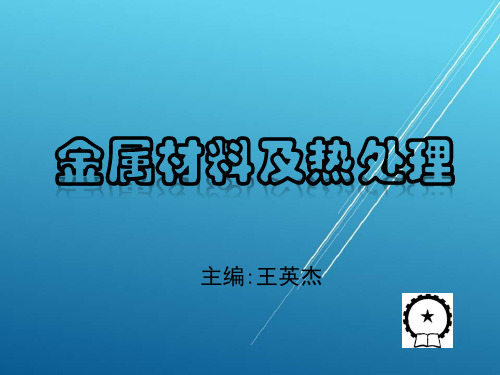
第四单元 铁碳合金相图
铁碳合金的平衡组织是由铁 素体和渗碳体两相所构成的。当碳 的质量分数w(C)<0.9%时,随着碳 的质量分数的增加,钢的强度和硬 度提高,而塑性和韧性降低;当碳 的质量分数w(C)>0.9%时,由于Fe3 CⅡ的数量随着碳的质量分数的增 加而急剧增多,并明显地呈网状分 布于奥氏体晶界上,这样不仅降低 了钢的塑性和韧性,而且也降低了 钢的强度,如图4-9所示。
心立方的固溶体,常用符号A(或γ)表示。奥氏体仍保持γ-Fe的面心立方 晶格,碳在γ-Fe中的位置如图4-3所示。
在金相显微镜下观察,奥氏体的显微组织呈多边形晶粒状态,但晶界 比铁素体的晶界平直些,并且晶粒内常出现孪晶组织(图中晶粒内的平行 线),如图4-4所示。
第四单元 铁碳合金相图
图4-3 奥氏体的晶胞示意图
特征为铁素体薄层和渗碳体薄层交替重叠的层状复相组织。由于珠光体的 显微组织形态酷似珍珠贝母外壳形纹,故称之为珠光体组织,如图4-6所示。
图4-6 共析钢中珠光体的金相显微组织
第四单元 铁碳合金相图
能力知识点五 莱氏体(Ld) 莱氏体是指高碳的铁基合金在凝固过程中发生共晶转变时所形成
的奥氏体和渗碳体所组成的共晶体,莱氏体碳的质量分数为4.3%。 莱氏体的性能与渗碳体相似,硬度高,塑性很差,脆性大。莱氏
图4-7 简化后的Fe-F3C相图
第四单元 铁碳合金相图
一、铁碳合金相图中的特性点 铁碳合金相图中的主要特性点的温度、碳的质量分数及其含义见
表4-1。
表4-1 铁碳合金相图中的特性点
第四单元 铁碳合金相图
二、铁碳合金相图中的主要特性线 1.液相线ACD 2.固相线AECF 3.共晶线ECF 4.共析线PSK 5.GS线 6.ES线 7.GP线 8.PQ线
《金属材料与热处理》第四章铁碳合金
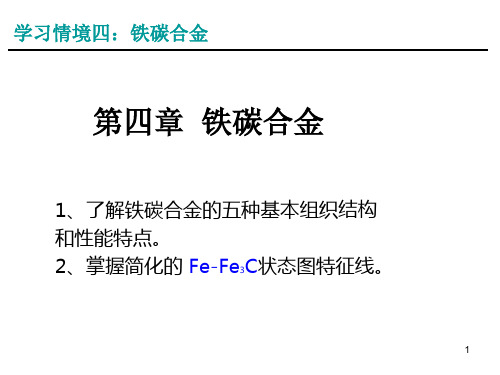
学习情境四:铁碳合金 4.3
4、在焊接方面的应用 焊接时由焊缝到母材各区域的温度是不同的,根据Fe-Fe3C 相图可知,受到不同加热温度的各区域在随后的冷却中可能 会出现不同的组织和性能。这需要在焊接之后采用相应的热 处理方法加以改善。 5、在热处理方面的应用
Fe-Fe3C相图是制订热处理工艺的依据。应用Fe-Fe3C相 图可以正确选择各种碳钢的退火、正火、淬火等热处理的 加热温度范围。由于含碳量的不同,各种碳钢热处理的加 热温度和组织转变也各不相同,都可从状态图中求得。
31
学习情境四:铁碳合金 4.4
1、在钢铁材料选用方面的应用
Fe-Fe3C相图反映了铁碳合金的组织、性能随成分的变化 规律,为钢铁材料的选用提供了依据。如各种型钢及桥梁、船 舶、各种建筑结构等,都需要强度较高、塑性及韧性好、焊接 性能好的材料,故一般选用含碳量较低(WC<0.25%)的钢材; 各种机械零件要求强度、塑性、韧性等综合性能较好的材料, 一般选用碳含量适中(WC=0.30%~0.55%)的钢;各类工具、 刃具、量具、模具要求硬度高,耐磨性好的材料,则可选用含 碳量较高(WC=0.70%~1.2%)的钢。纯铁的强度低,不宜 用作工程材料。白口铸铁硬度高、脆性大,不能锻造和切削加 工,但铸造性能好,耐磨性高,适于制造不受冲击、要求耐磨、 形状复杂的工件,如冷轧辊、球磨机的铁球等。
29
学习情境四:铁碳合金 4.4
低碳钢:Wc=0.1-0.25% 中碳钢:Wc=0.25-0.6% 高碳钢:Wc=0.6-1.4% 随着Wc的增加,硬度、强度都增加。
30
学习情境四:铁碳合金 4.3
三、铁碳合金状态图的应用
1、在钢铁材料选用方面 2、在铸造生产上的应用 3、在锻造方面的应用 4、在焊接方面的应用 5、在热处理方面的应用
金属材料及热处理(最新版)

8、屈氏体:同上是珠光体的一种,更细片状铁素体+更细片状渗碳体叫之为屈氏体, 形成温度 600-550oC。HB330-400(HRC32-38)。
6
生产中防止回火脆性的方法主要有: z 回火后进行快速冷却(油或水冷)为消除重新产生的热应力,则在回火后可再进行
Ms, γ Fe转变为α Fe,碳原子全部被保留在α Fe中,形成一种过饱和的固溶体组织,这就
是马氏体。这种转变也称非扩散形转变。马氏体金相显微组织呈针状,黑色针状物为马氏 体,白色基体称为残余奥氏体。性能十分脆硬。HB可达 600-700(HRC60-65)。淬火即可 获得这种组织。硬度取决于C含量,低C钢淬不硬,含C量高于 0.8%,硬度几乎不再增加了。 马氏体的转变随C含量增高而降低含碳量 0.5%时Mz约 0oC,Ms290oC随着含C增Ms下降,C量 小于 0.8%时Mz也随C ↑ 而下降,0.9 以上时Mz在-100oC附近下降不大。奥氏体向马氏体的转 变有一个很大的特点:奥氏体不能百分之百转化为马氏体总有较少的奥氏保留下来,称保 留下来的为残氏奥氏体。因奥氏体为γ Fe面心产方晶格,比容(单位重量的体积)较小,约 只有 0.122—0.125,而马氏体为α Fe过饱和固溶体,比容较大,约有 0.127-0.130,可见, 在转变过程中,在马氏体形成的同时还伴随着体积的膨胀,从而会对尚未转变的奥氏体造 成一内压力,合使其不易发生向马氏体的转变而被保留下来。Ms Mz点越低剩余奥氏体量也 就越多。
金属材料与热处理
一、金属材料及热处理
金属材料和热处理基本概念及基础知识-热处理工艺

淬透性一般可用淬火临界直径、截面硬度分布曲 线和端淬硬度分布曲线等表示。由于钢中化学成分的 波动,表示钢淬透性硬度曲线有一个波动范围,被称 为淬透性带。 钢材的淬透性与淬硬性是两个完全不同的概念。 淬火硬度高的不一定淬透性好,而硬度低的钢材也可 能具有高的淬透性。 一般机械制造行业大多以心部获得50% 马氏体为 淬火临界直径标准,对于重要机加及军工行业则以心 部获得90 %马氏体作为临界直径标准,以保证零件整 个截面都获得较高力学性能。
2.加热与保温时间
五、钢的回火与回火工艺
将淬火钢重新加热到A1以下某一温度,保温后冷 却到室温的热处理工艺称回火。
1、回火的目的
• ⑴ 降低淬火钢的脆性,消除或减少淬火钢的内应力。 • ⑵ 提高钢的塑性和韧性,获得所要求的性能。
• ⑶ 稳定工件尺寸,降低硬度,便于切削加工。
第四节 钢的表面淬火
将钢加热到临界点以上(某些退火也可在临界点以下) 保温一定时间,随炉缓慢冷却,以获得接近平衡状态组织的 热处理工艺。主要用于铸、锻、焊件毛坯的热处理。
• 1、退火的目的 • 1)降低钢件硬度,便于切削加工。 • 2)消除工件内应力,稳定尺寸。
• 3)细化晶粒,改善组织,提高钢的机械性能。 • 4)为最终热处理做好组织准备。
一、钢的渗碳 渗碳是将钢件加热到奥氏体状态下,于富碳介质 中长时间加热,使碳原子渗入表层,增加钢件表层的 含碳量,然后通过淬火获得高硬度的马氏体组织,达 到提高强度、耐磨性及疲劳强度的目的。 渗碳一般用含碳0.1~0.25%的低碳钢。 渗碳—淬火+低温回火
1、渗碳方法
⑴ 气体渗碳(煤油、苯、甲醇+丙酮) 渗碳介质的分解—吸收—扩散三个基本过程。 主要应控制好加热温度(930 º C)和保温时间。 温度越高,渗速越大,扩散层越厚,但晶粒越大,使 钢变脆。保温时间取决于渗层厚度,但时间越长,扩 散速度减慢。钢件渗碳几小时到几十小时,可得到 0.5~2mm的渗碳层深度。 ⑵ 固体渗碳 ⑶ 液体渗碳
金属材料及热处理知识(整理版)

硬度金属抵抗更硬物体压入表面的能力,称为硬度。
硬度是反映金属材料局部塑性变形的抵抗能力。
根据试验方法和测量范围的不同,硬度可分为布氏、洛氏、维氏等几种。
1、布氏硬度(HB)布氏硬度是用淬火硬化后的钢球(直径有:2.5、5、10毫米三种)作为压印器,以一定的压力P压入被测金属材料表面,这时在被测金属材料表面留下压坑。
根据压坑面积的大小,可用下式计算出布氏硬度值,用符号HB表示为HB=P/F(公斤/毫米2)式中P——钢球所加的负荷(公斤);F——压坑面积(毫米2)。
布氏硬度是用单位压坑面积所受负荷的大小来表示的。
一般硬度值都不需要经过计算,在生产中用放大镜测出压坑直径,再根据压印器钢球直径D和压力负荷P直接查表,便可得出HB的值。
布氏硬度在标注时不写单位,如HB=212。
测量不同金属材料时所用的压印器和负荷等标准,也可以查表。
用布氏硬度法测得的硬度值准确,因为压坑大,不会由于表面不平或组织不均匀而引起误差。
但压坑太大有损表面,所以布氏硬度一般不宜作成品检验,只适合测量硬度不高的原材料,如毛坯、铸件、锻件、有色金属及合金等。
2、洛氏硬度(HR)洛氏硬度法是用金刚石做的呈120°的圆锥体,或直径为1.58毫米的淬火钢球,作为压印器,在一定的负荷下压入金属表面,根据压坑的深浅来测量金属材料的硬度,(根据压坑深度)可把硬度数值从表盘上直接读出来。
根据测量硬度范围不同,洛氏硬度可分为HRA、HRB、HRC三种。
它们的适用范围与压印器、负荷的选定可根据下表查出,洛氏硬度的选用标准洛氏硬度没有单位,测量方法简单,压坑小,不影响零件表面质量,测量硬度范围广,但不如布氏硬度精确度高。
HRA适宜测量高硬度材料;HRB适宜测量有色金属及硬度低的材料;HRC适宜测量淬火、回火后的金属材料。
3、维氏硬度(HV)维氏硬度试验的原理与布氏硬度法相似,只不过它的压印器是136°的四棱锥金刚石,以一定的负荷压入平整的试样表面,然后测出四棱锥压坑的对角线长度d,算出压坑面积F,用单位面积所受负荷的大小来表示维氏硬度值,即HV= P/F(公斤/厘米2)维氏硬度测量精确、硬度测量范围大,尤其能很好地测量薄试样的硬度。
第四章 非合金钢-《金属材料与热处理》中职通用第七版
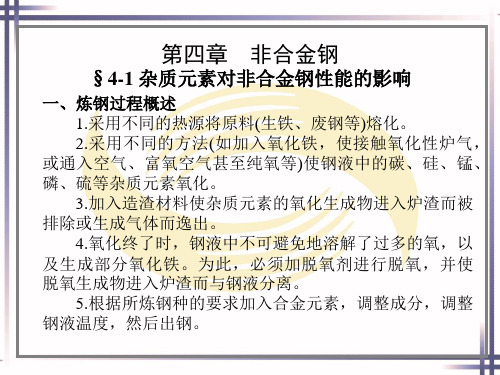
3.加入造渣材料使杂质元素的氧化生成物进入炉渣而被 排除或生成气体而逸出。
4.氧化终了时,钢液中不可避免地溶解了过多的氧,以 及生成部分氧化铁。为此,必须加脱氧剂进行脱氧,并使 脱氧生成物进入炉渣而与钢液分离。
5.根据所炼钢种的要求加入合金元素,调整成分,调整 钢液温度,然后出钢。
析出,而将在长期搁置时以细小分散的氮化物析出,从而使
钢的韧性显著下降,导致工件易于脆性破坏,这种现象称为 时效。
7.氢 尽管氢在钢中含量不多,但即使是微量氢的存在也会造
成氢脆等缺陷,因而是有害元素。
§4-2 非合金钢的分类
一、按非合金钢的含碳量分类
1.低碳钢 含碳量≤0.25%。
2.中碳钢 含碳量为0.25%~0.6%。
§4-3 非合金钢的牌号与用途
一、非合金钢的牌号表示方法
二、常用非合金钢的性能和用途
1.碳素结构钢
2.优质碳素结构钢
3.碳素工具钢
4.铸造碳钢
§4-4 低碳钢与高碳钢的冲击试验
氮在高温下能溶于fe或fe中急速冷却后并不立即析出而将在长期搁置时以细小分散的氮化物析出从而使钢的韧性显著下降导致工件易于脆性破坏这种现象称为时效
第四章 非合金钢
§4-1 杂质元素对非合金钢性能的影响
一、炼钢过程概述 1.采用不同的热源将原料(生铁、废钢等)熔化。 2.采用不同的方法(如加入氧化铁,使接触氧化性炉气,
3.高碳钢 含碳量≥0.60%。
二、按非合金钢的质量等级分类
1.普通碳素钢 2.特殊质量碳素钢 3.优质碳素钢
三、按非合金钢的用途分类
1.碳素结构钢 2.碳素工具钢
金属材料及热处理 04 淬火与时效
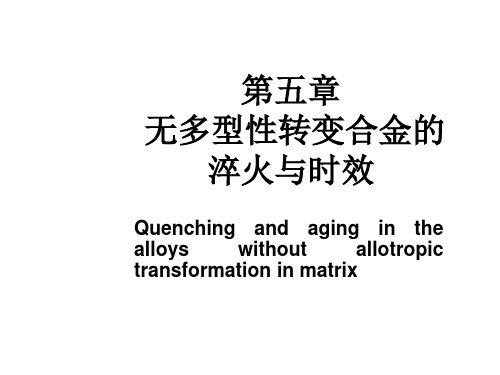
定发展。
浓度起伏生成CIII, ΔGVIII 为负,晶核也 可稳定发展。 不论β相开始成分如何,最终发展的Cb。
形核---长大分解机制
L T0 A C0 + B A
T
G
GV G G
C1
C0
C2
B
沉淀粒子形核驱动力计算(经典形核理论)
G G
G GV
G D GV / n2 G
时效(回火)——亚稳过饱和固溶体分解, 时效与回火区别在于 基体转变与否?铝、 铜、钛和钢铁 。
2、工艺形式:
大多数情况下淬火+ 时效,但是也存在仅有 淬火(自然时效)和仅有时效(挤后冷即
淬)的情况
淬火
时效
3、目的与应用:
淬火(固溶处理)——获得过饱和固溶体:i、时效前的预处理;ii、冷加工前的中 间处理,消除加工硬化,消除脆硬相的有害影响;iii、最终热处理(固溶处理); 时效——使过饱和固溶体分解(脱溶、沉淀),用作最终热处理,调整组织性能。
(C1)——以形核长大过程的分解 A
2、脱溶过程的相变驱动力及其在自由能-成分曲线上的表征
相变驱动力是脱溶过程发生前后的体系自由能变化(差)
在温度T下,C0合金单相固溶体α摩尔自由 能为G0,析出少量成分C2脱溶晶核, α相成 分降至C1,二者摩尔自由能分别为G2 、 G1 。 若脱溶相摩尔数n1而脱溶后α基体的为n2, ΔG=G(析出后)-G(析出前) =(n1G1+n2G2)-( n1+n 2)G0
T1
+
T2
低;但有些合金相反,也有些合金的性
A
C2
C0
C1
B
能变化不大。
基体无多型性转变的合金固溶处理后急
金属材料与热处理

1.退火 退火是将钢加热到工艺预定的某一温度, 经保温后缓慢冷却下来的热处理方法。 常用的退火方法有完全退火、球化退火 和去应力退火等。
2.正火 正火是将钢加热到工艺规定的某一温度, 使钢的组织完全转变为奥氏体,经保温 一段时间后,在空气中冷却到室温的工 艺方法。正火的冷却速度比退火稍快, 过冷度稍大。因此,正火后所获得的组 织较细,强度、硬度较高。
10、15、20等钢属于低碳钢,具有良 好的冷冲压性能及可焊性,常用来制造 用力不大、韧性要求较高的机械零件, 如螺钉、螺帽、法兰盘、拉杆及化工机 械中的焊接容器等。经过渗碳淬火处理 后,其表面硬而耐磨,心部保持高的塑 性和韧性,常用于制造承受冲击载荷的 耐磨零件,如凸轮、摩擦片等。
30、45、50等钢属于中碳钢,经调质 处理(即淬火后高温回火)后,有良好的 综合力学性能,是受力较大的机器零件 理想的原材料。主要用来制造截面尺寸 不大的齿轮、连杆及轴类零件。 60以上的钢属于高碳钢,经热处理后, 有高强度和良好的弹性,适于制造弹簧、 钢绳、轧辊等弹性零件及耐磨零件。
易切削钢也是结构钢的一种。其特 点是易于切削加工。这种材料适用于自 动机床上加工。它是向钢中加入一种或 几种易生成脆性夹杂物的元素(硫和磷 等),使钢中形成有利于断屑的夹杂物, 从而改善了钢的切削加工性能。
3.碳素工具钢 碳素工具钢的牌号以 “碳”字汉语拼音字首 “T”与其后面 的一组数字组成,数字表示钢中平均碳 的质量分数为千分之几。含锰较高的在 数字后标注“Mn”,高级优质钢在钢号 后标注“A”。如T10A表示平均碳的质 量分数为1.0%的高级优质碳素工具 钢。
(2)合金渗碳钢 常用的渗碳钢有20Cr、20Mn2B、20CrMnTi、 20MnVB。 适于制造易磨损而又承受较大冲击载荷的零件, 如汽车、拖拉机的齿轮、凸轮轴、气门顶杆等。 (3)合金调质钢 常用的合金调质钢有40Cr、40Mn2、 35CrMnSi和40MnB等。 适用于制造性能要求高及截面尺寸较大的重要零 件,如承受交变载荷、中等转速、中等载荷的轴 类、杆类、齿轮等零件。
- 1、下载文档前请自行甄别文档内容的完整性,平台不提供额外的编辑、内容补充、找答案等附加服务。
- 2、"仅部分预览"的文档,不可在线预览部分如存在完整性等问题,可反馈申请退款(可完整预览的文档不适用该条件!)。
- 3、如文档侵犯您的权益,请联系客服反馈,我们会尽快为您处理(人工客服工作时间:9:00-18:30)。
第四章答案
1.解释名词:①滑移、②加工硬化、③回复、④再结晶
答:①滑移:晶体的一部分沿着一定的晶面(滑移面)和晶向(滑
移方向)相对于另一部分产生相对滑动的过程。
滑移变形有如下特点: 滑移只能在切应力作用下发生。
滑移常沿晶体中原予密度最大的晶面和晶向发生。
②加工硬化:随着塑性变形量的增加,金属的强度、硬度升高,
塑性、韧性下降这种现象称为加工硬化。
③回复:回复是指当加热温度较低时,仅使金属的点缺陷和位错
近距离运动(如大量的空位移动到表面或与间隙原于合并;异号位错在同一滑移面上合并消失)而使晶格畸变减少,内应力显著降低的过程。
④再结晶:金属的组织和性能又重新恢复到冷性变形前的状态。
而且结晶出的晶格与变形前完金一样,所以称为再结晶过程
2.用手来回弯折一根铁丝时,开始感觉省劲,后来逐渐感到有些费劲,最后铁丝被弯断。
试解释过程演变的原因?
答:铁丝在塑性变形前的塑性、韧性好,容易变形;用手来回弯
折铁丝时感觉省劲;随着变形量的增加,金属的强度、硬度升高,塑性、韧性下降产生了加工硬化。
所以后来逐渐感到有些费劲了。
3.当金属继续冷冲压有困难时,通常需要进行什么热处理?为什么? 答:金属的塑性变形,不仅会使金属的晶粒破碎拉长,而且还会
使位错等晶格缺陷大量增加,从而使金属产生加工硬化和残余内应
力,这些不仅会造成金属进一步加工的困难,而且还会引起一系列的性能变化。
所以,金属在塑性变形之后或在其加工变形的过程中,需要进行的热处理是退火,即对金属进行一定温度的加热,便其组织从不稳定的状态趋于稳定的状态,性能得以恢复。
退火的目的是①为了消除加工硬化,以便进一步加工,②为了保留其加工硬化性能,仅只减小其残余内应力,或改善某些理化性能。
4.热加工对金属组织和性能有什么影响?钢材在热加工(如锻造)时,为什么不产生加工硬化现象?
答:热加工能消除铸态金属与合金的某些缺陷,如使气孔焊合,
使粗大的树枝晶和柱状晶破碎,从而使材料组织致密,晶粒细化,成分均匀,力学性能提高。
热加工使铸态金属中的夹杂物及枝晶偏析沿变形方向拉长,便枝
晶间富集的杂质及夹杂物的分布逐渐与变形方向一致,形成彼此一致的宏观条纹,称为流线,由这种流线所体现的组织称为纤维组织。
纤维组织使钢产生各向异性,与流线平行的方向强度高,而垂直方向上强度低,在制订加工工艺时,应使流线分布合理,尽量便流线与工件工作时所受到的最大拉应力方向一致,与剪切或冲击应力方向相垂直。
在热加工亚共析钢时,常发现钢中的铁素体与珠光体呈带状或层
状分布,这种组织称为带状组织。
带状组织是由于枝晶偏析或夹杂物在压力加工过程中被拉长所造成的。
带状组织不仅降低钢的强度,而且还降低塑性和冲击韧度。
轻微的带状组织可通过多次正火或高温扩
散退火加正火来消除。
热加工时也会产生的加工硬化,但能很快以再结晶方式自动消
除,因而热加工不会带来加工硬化。
5.金属塑性变形造成哪几种残余应力?它们对机械零件可能产生
哪些影响?
答:塑性变形是外界对金属做功产生的,其所做的功大部分在变
形过程中以热的方式消耗掉,还有一小部分转化为内应力而残留于金属中。
这类在塑性变形后残留在内部的应力称为残余内应力。
残余内应力是一种弹性应力,在金属中处于自相平衡状态。
根据残余内应力平衡范围的大小不同,残余内应力可分为宏观残余内应力、微观残余内应力和晶格畸变内应力三种。
宏观残余内应力是由工件不同部分(如表面与心部)的宏观变形
不均匀性引起的,故其应力平衡范围包括整个工件,称之为第一类内应力。
微观残余内应力是由晶粒或亚晶粒内部的不均匀变形引起的,其作用范围与晶粒尺寸相当,即在晶粒或亚晶粒之间保持平衡,称之为第二类内应力。
晶格畸变内应力由金属变形时产生的大量位错、空位等缺陷所引起,即由晶格畸变产生,其作用范围更小,称之为第三类内应力。
这三种内应力对工件的影响是不同的:第一类内应力主要使工件产生变形;第二类内应力会使工件内部产生微裂纹;第三类内应力则使工件强度、硬度升高,塑性和耐蚀性下降。
6.产生加工硬化的原因?它在工程上带来哪些利弊?
答:金属经冷塑性变形后产生加工硬化的原因如下:
(1)位错密度随变形量增加而增加,从而使变形抗力增大。
(2)随变形量增加,亚结构细化,亚晶界对位错运动有阻碍作用。
(3)随变形量增加,空位密度增加。
(4)几何硬化。
由于塑性变形时晶粒方位的转动,使各晶粒由有
利位向墙到不利位札因而变形抗力增大。
由于加工硬化的存在,使金属已变形部分产生加工硬化后停止
变形,而未变形部分则开始发生变形,因此,没有加工硬化,金属就不会发生均匀塑性变形。
加工硬化是工业上用以提高金属强度、硬度和耐磨性的重要手段
之一。
特别是对那些不能以热处理强化的金属和合金尤为重要。
塑性变形还使金属的电阻增大,耐蚀性下降。
7.锡在300C 和钨在11000C 时的塑性变形加工各属于哪种加工?为什么? (锡的熔点为2320C,钨的熔点为33800C)
答:热加工与冷加工的区别是以金属材料的再结晶温度为分界。
凡是在材料再结晶温度以上所进行的塑性变形加工称为热加工,而在材料再结晶温度以下所进行的塑性变形加工称为冷加工。
各种纯金属的再结晶温度θ再与其熔点θ熔之间按绝对温度计算其关系可用下式表示:
θ再 = 0.4θ溶
所以它们都属于冷加工。