物料需求计划表
物料需求计划(MRP)

即使在产品需求量是均衡的情况下,考虑到 零部件的生产批量以及一种零部件可能用于生 产不同的最终成品,也会使得对零部件的需求 是波动的。波动需求现象意味着订购点法不宜 用于制造业中零部件的库存控制。
计算机提供的数据处理能力,可以迅速地完 成对零部件需求的计算。
MRP的主要思想:
把所有物料分成独立需求和相关需求两种 类型
需求无关的某一物料的需求。 这种独立需求大多是最终产品或维修件 这类需求受市场因素的影响,需求多为随机波动。 独立需求一般根据订单与市场预测来确定---订货点法+预测;
相关需求( Dependent Demand )是指与另一物料或产品需求直
接相关的某一物料的需求。
(2) 如果用订货点法控制零部件和原料库存,会形成“块 状”需求
假设产成品的需求率是均匀的,如果采用订货点方法,使 零件和原材料的需求呈“块状”。 “块状”需求与均匀需求相比,平均库存水平几乎提高一 倍,占用更多的资金。
块状需求示意图
产品 零部件 原材料
解决“块装”问题的办法
相关需求可以从最终 产品的需求量中推算 出来的。 相关需求不是随机的, 其数量和时间是由上 一级物料需求确定的--MRP;
低层代码概念:当一个零件或部件出现在多种产品结构的不同层 次,或者出现在一个产品结构的不同层次上时,该零(部)件就具有 不同的层次码。以它的数字最大的代码为其低层代码。
(3) 库存状态文件
库存状态文件保存了每一种物料的有关数据,产品结 构文件是相对稳定的,而库存状态文件却处于不断变 动之中。
零部件 抽屉
制造业生产中的零部件、原材料的库存管理,与 产品或用于维修服务的零部件库存不同,不能当作
独立项目看待。它们的需求是根据由它们装配而成 的最终成品的需求所决定的,属称相关需求。
物料需求计划

3、现有库存量(POH)
其概念与MPS中的概念相同,指每周需求被满足之后手头仍有的库存量。该记录随着每周 进货或出货的情况而更新,未来各周的POH则可计算的出
4、计划订货入库量 (PR)
含义是,计划订货或生产、但订单尚未发出的订货量。这个量的意义是要保持POH的量不 低于安全库存(在MPS中未考虑安全库存,保持POH非负即可)。对于某些不需要安全库
某办公家具公司,其两种主要产品(即企业要出厂的最终产品)是办公用椅A和B,其需 求大致稳定:产品A每周需30个,产品B每周需20个。这两种产品都需要用到一种支架部
件C。因此,对C的平均需求量是每周50个。A和B的装配期是1周
如右图示,在这种格式中,左上方通常要标出产品名称及其性质(如右图中,表明C是支 架部件),右上方表示计划因子,通常包括三项:生产批量、生产周期和安全库存量。 在本例中,C的批量是230个,生产周期为2周,安全库存量为50个。这些计划因子的量都 需要预先选定。当这些值发生变化以后,管理人员必须及时更新库存记录。下面首先来
存的中间物料,则如同MPS,其意义是要保持POH非负
在库存记录中所表示的PR量应包括这两种情况: 1)在POH出现短缺(或为负值或小于安全库存量)的当周制订一个PR量,其值的大小应是POH大于等于安全库存 2)继续计算其后各周的POH,当又出现短缺时,制订下一个PR量
5、计划发出订货量 (plannedorderreleas
基本计算模式
物料需求计划(MRP)的制定需要三个关键信息:MPS、BOM、库存记录
MPS
主生产计划
BOM
物料清单
库存记录
在MRP的制定过程中,库存记录的计算方法构成了MRP的基本计算模型
计划bom表

计划bom表在制造业中,BOM表(Bill of Materials)是非常重要的一项文档,它记录了产品所需的各种原材料、零部件和组件的清单。
BOM表不仅是生产计划和生产过程中的重要参考依据,也是产品设计、采购和库存管理的基础。
因此,编制一份准确、完整的BOM表对于企业的生产运营至关重要。
首先,BOM表的编制需要明确产品的设计要求和规格参数。
在设计阶段,工程师需要详细了解产品的功能特性,确定各个零部件之间的关联关系,以及各个零部件的规格、尺寸、材料等信息。
这些信息将直接影响到BOM表的编制,因此设计人员需要与BOM表编制人员密切合作,确保BOM表的准确性和完整性。
其次,BOM表的编制还需要考虑到产品的生命周期管理。
随着产品的不断更新换代和改进,BOM表也需要不断进行修订和更新。
因此,在编制BOM表时,需要考虑到产品的版本管理和变更控制,确保BOM表与实际生产的一致性。
同时,还需要与产品设计、工艺工程、采购和供应链等部门进行有效的沟通和协调,及时获取最新的产品信息,以便及时更新BOM表。
另外,BOM表的编制还需要考虑到供应链管理和采购计划。
在编制BOM表时,需要充分考虑到各种原材料、零部件和组件的采购渠道、供应商信息、价格和交货周期等因素,以便为采购部门提供参考依据,帮助其制定合理的采购计划和库存管理策略。
同时,还需要与供应商保持密切的合作关系,及时了解市场变化和供应商的动态,以便调整BOM表和采购计划。
最后,BOM表的编制还需要考虑到生产计划和物料需求计划。
在编制BOM表时,需要充分考虑到生产工艺流程、生产能力和物料需求计划等因素,以便为生产计划部门提供参考依据,帮助其合理安排生产计划和物料供应。
同时,还需要与生产计划部门保持密切的沟通和协调,及时了解生产进度和物料需求情况,以便调整BOM表和生产计划。
综上所述,BOM表的编制是一个复杂而又重要的工作,它需要各个部门之间的密切合作和协调。
只有通过有效的沟通和协作,才能编制出准确、完整的BOM 表,为企业的生产运营提供有力的支持。
第九讲物料需求计划
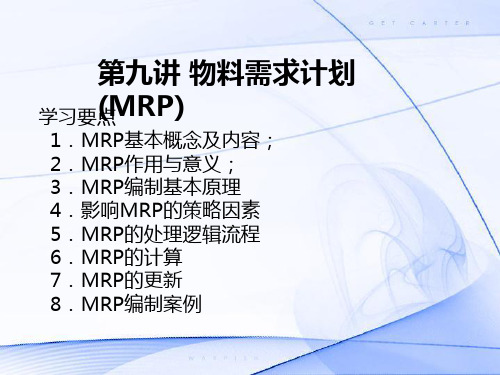
MRP项目
计划周期
1 2 3 4 5 6 25 7 8 30 40 25 40 15 15 30 15 15 30 9 10 11 15 15 30 12 13
X(LT=4) Y(LT=6) 相关需求X-A 相关需求Y-A 独立需求A
A的毛需求
15
40
40
30
15
45
【例题9.3:应用低位码 计算物料的净需求】 已知:MPS为在第8个 计划周期时产出200件A 产品;各物料的计划接 收量和已分配量为0; 物料ABCD期初库存分别 为0、120、60、70件, 安全库存量为0;物料 ABCD批量规则为直接批 量法。求物料ABCD的净 需求。
毛需求计算考虑因素
• • • • •
是否存在独立需求 是否共用物料 是否低位码 是否是计划BOM 是否存在替代
如果存在替代,要不要替代则考虑: • 是否可以降低工作量 • 是否可以降低成本 • 客户是否满意 • 近期是否短缺
(3)计算净需求量。 考虑安全库存推算特定时段的净需求量。 当PAB初值≥安全库存时,净需求=0 当PAB初值<安全库存时,净需求=安全库存- PAB初值
生产什么? MPS
主生产计划
2
(物料清单) 用到什么?
产品信息
4 物料需求计划 MRP
已有什么? (物料可用量)
3 库存信息
买什么?
采购计划
做什么?
生产计划
MRP 回答了
问
4 个制造业的主要问题
答
(生产什么 1 生产什么?
2 用到什么? 3 已有什么?
+
用到什么) - 已有什么 1 主生产计划( MPS) = 还缺什么
(二)MRP中的输出数据项 1.采购订单 采购什么? 采购多少? 何时开始采购? 何时完成采购? 2.制造订单 制造什么? 制造多少? 何时开始制造? 何时完成制造?
第十一章ERP之物料需求计划
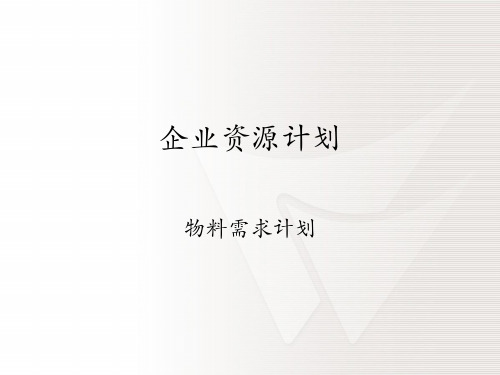
X(LT=4)
Y(LT=6)
A(1)
B(1)
A(1)
产品X、Y的BOM图(物料X的需求关系〕
C(1)
物料A的毛需求计算表
周
1 2 3 4 5 6 7 8 9 10 11 12 13
2.独立需求
当一个项目的需求不能直接从另一个项目的需求计划得到时 ,这种需求称为独立需求;否则,为相关需求。 ➢ 独立需求与相关需求的概念是相对的。例如,若生产园
珠笔,则笔的需求是独立需求,其需求数量是由预测 得 到的,而对构成笔的笔芯和弹簧之类的项目而言便是相 关需求。其需求数量是通过计划 得到的。但是,若想单 独销售笔芯,则笔芯又是独立需求。 ➢ 在编制物料需求计划时,必须认真地分析与收集独立需 求与相关需求。
5.其它因素
(1)低阶码(low level code,LLC)
➢ 低阶码,又称层次码或低层码,是系统分配给物料清单 上的每个物品一个从0至N的数字码。在产品BOM结构 中,最上层的层级码为0,下一层部件的层级码则为l, 依此类推。
➢ 一个物品只能有一个MRP低阶码,当一个物品在多个产 品中所处的产品结构层次不同或即使处于同一产品结构 中但却处于不同产品结构层次时,则取处在最低层的层 级码作为该物品的低阶码,也即取层次最低的、数字最 大的层级码。
• MRP的概念 • MRP的工作原理 • MRP处理过程 • MRP的编制案例 • MRP的更新方法 • 能力需求计划 • MRP和LRP
MRP的编制案例
例1 求毛需求及发出订货计划
• 例1 求毛需求及发出订货计划:已知MPS为在第8个计划周 期时产出100件A产品,其中A产品的BOM图见下图。
即一个项目是采购件还是制造件的标识码。采购或制造标识 码通常用一个字母(P或M)表示。当MRP运行时,该码决定 做采购订单或制造订单计划。
BOM表制作

一、BOM表的定义 二、BOM表的作用 三、BOM表的相关流程图 1、BOM发布流程 2、BOM禁用流程 四、BOM表包含哪些物料 五、BOM表出错导致哪些后果
一、BOM表的定义
BOM是Bill of Materials(物料清单)的缩写,是指产 品所需零部件明细表及其结构,在MRP2中,物料一词有着广 泛的含义,它是所有产品、半成品、在制品、原材料、配套 件、协作件、易耗品等等与生产有关的物料的统称。 ,如 工时、材料、设备、工装、车间等。用以描述产品零件、半 成品和成品之间的关系。在某些工业领域,可能称为“配 方”、“要素表”或其他名称。从概念上来理解BOM有以下 的含义: 1.狭义的BOM一般说来,我们对BOM最初的理解就 是顾名思义,材料清单,也就是通常所说的产品结构,这是 BOM狭义理解。业界先驱,著名ERP专家陈启申先生,在它的 著作《MRPII制造资源计划基础》中,有详细的介绍和论述。 2.广义的BOM对于某一物料的产品结构,每个人都有不同的 理解,那么就会有不同的产品结构树定义;同时,同一个物 料,可以有多种产品结构,这样,在BOM定义过程中,容易 出现偏差。
打开产品文件夹 找到要放的位置
找到放置的位置后新建产品BOM,如下:
点击单一BOM
出现以下画面
输入编码和名称,如下:
点击组成如下:
点击引用物料出现在以下页面:
输入需要的 物料编码
点击查询出现所需物料点击确定出现以下页面:
输入需要的数量和装配位置,其它所需要物料都以此方 法输入
BOM建好后,启动流程,点中一般BOM归档/升级 流程
常用封装
目前我们公司 有几款封装为: 0805封装、0603 封装、1206封装、 2010封装、1210 封装、1812封装、 2512封装,最为 常用的有0805、 1206、0603三类。
物料需求

例: X对A的需求
周
1 2 3 45
毛需求 10 量
20 15
Y对A的需求
6 71 2 3 4
25
30 40
独立A需求
5612 20 10 15 15
30 40
10
20 15
25
15
20 10
2020/8/11
2. 物料统管: 库存控制、物料搬运、厂内外运输、外协外包
、利废利材、采购供应、厂内仓库等由一个物料经理统一领 导。
3. 物料编码:唯一性:同一零件不同加工阶段、不同颜色就
是不同零件。编码最大可达15位。6位编码可编号为: 000,000——999,999 , 100万种。
4. 项目主文件: 2020/8/11
1U的数目=1 200 +2V的数目=2 300
=800
2U的数目=2 200=400
2V的数目=2 300=600
一个简单的MRP例子
现在考虑获得上述物料项的时间
假设:T需要1周;U需要2周;V需要2周;W需要3周; X需要1周;Y需要1周。
所有物料何时订货?何时到货?才能满足生 产产品T的需要。
1 主生产计划(MPS):
各种型号产品时段计划 展开的零件时段计划
主生产计划
2. 物料清单(BOM): 根据产品结构而定
BOM
物物料料需需求求计计划划
库存信息
的零件 3。库存信息
结果如何?
N CP
看能力平衡(CP)
Y
2020/8/11
生产计划
采购计划
§10-2 MRP的运算依据(续)
MRP运行所需的信息
2020/8/11
一个简单的MRP例子
七、物料需求计划

第七讲物料需求计划1、物料需求计划的基本原理用料预算方法□用料预算第一条常备材料:由生产管理单位依生产及保养计划定期编制"材料预算及存量基准明细表"拟订用料预算。
第二条预备材料:由生产管理单位依生产及保养计划的材料耗用基准,按科别(产品表)定期编制"材料预算及存量基准明细表"拟订用料预算,其杂务用品直接依过去实际领用数量,并考虑库存情况,拟订次月用料预算。
第三条非常备材料:订货生产的用料,由生产管理单位依生产用料基准,逐批拟订产品用料预算,其他材料直接由使用单位定期拟订用料预算。
□存量管理第四条常备材料:物料管理单位依材料预算用量,交货所需时间、需用资金、仓储容量、变质速率及危险性等因素,选用适当管理方法以"材料预算及存量基准明细表"列示各项材料的管理点,连同设定资料呈主管核准后,作为存量管理的基准,并拟"常备材料控制表"进行存量管理作业,但材料存量基准设定因素变动足以影响管理点时,物料管理单位应即修正存量管理基准。
第五条预备材料:物料管理单位应考虑材料预算用量,在精简采购、仓储成本的原则下,酌情以"材料预算及存量基准明细表"设定存量管理基准加以管理,但材料存量基准设定因素变动时,物料管理单位必须修正其存量管理基准。
第六条非常备材料:由物料管理单位依据预算用量及库存情况实施管理(管理方法由各公司自订)。
□用料差异分析第七条材料预算用量与实际用量差异超过管理基准时,依下列规定办理:(一)常备材料:物料管理单位应于每月10日前就上月实际用量与预算用量比较(内购材料用)或前三个月累计实际用量与累计预算用量比较(外购材料用)其差异率在管理基准(各公司自订)以上者,需填制"材料使用量差异分析月报表"送生产管理单位分析原因,并提出改善对策。
(二)预备材料:物料管理单位以每月或每三个月一期,于次月10日前就最近一个月或三个月累计实际用量与累计预算用量比较,其差异率在管理基准(各公司自订)以上者按科别填制"材料使用量差异分析月报表",送生产管理单位分析原因,并提出改善对策。