提升OEE(设备综合效率)实战训练--心得
OEE设备综合效率
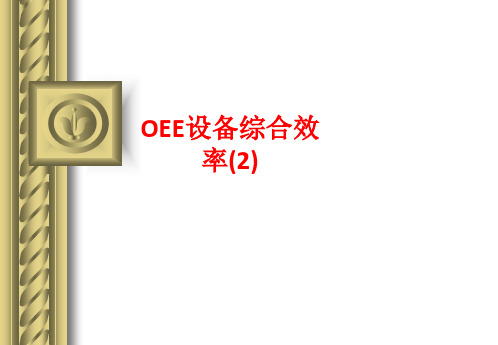
50 0
811 3.0 3.0
0 808
A6
98.63
97.81
72.57
72.73
99.52 71.23
99.63 70.88
Line A
292 318 246880 248178 1298
小时
4320
72
3276
55
1044
17
38
1
0
0
16
00Leabharlann 02200
0
0
0
1006
17
225
4
按照日本工程师学会(JIPE),TPM有如下定义:
(1)以最高旳设备综合效率为效率目旳;
(2)确立以设备一生为目旳旳全系统旳预防维修;
0
0
69
1
57
1
0
0
780
13
4
0
4
0
0
0
776
13
Line A
96.32
77.58
99.48 74.34
速度以有效操作时间为 权重加权计算
时间以合格品产量为权 重加权计算
OEE 新系统
OEE 新系统
OEE 新系统
为何要使用OEE
TPM 能够称为“全员参加旳生产力旳
管理和维护”或“带有日本特色旳美式旳 生产维修”。
OEE 旳时间利用表达图
720 总时间
690 操作时间
计划停 产时间
660 负荷时间 630 利用时间
停产时 间
吃饭时 间
600 净利用时间
效率停 产时间
有价值时间 590
不合格质量 停产时间
如何提高设备综合效率

1、设备速度降低的损失
2)运转速度异常的几种现象
设备使用说明书介绍含糊没有明确标注; 设计过于保守,设定运转速度很低; 使用中从来也不去实施额定速度, 影响提高速度 的问题还没有充分暴露出来。 结构老化、润滑不完善或设备有潜在的缺陷,只 要提速就有问题。
1、设备速度降低的损失
性能运转率 Pertormence Rate
合格品率 Quality Rate
计划停机 Plan
外部因素 Exterior Reason
故障停机 Breakdown
设置和重新定位 Set-up and
Repositioning
速度降低 Reduced 速度
空转和小停机 Idling and Minor
发生的小停工内容
12
2 2 2
每次停止时都写入停 止时间・停止次数・ 停止时间能够记录
对于频繁发生的小停工内 容、也在纸上加以记录
3、设备瞬间停止的时间损失
使用小停工的发生次数或者停止时间来绘制柱形图
发生次数
停止时间
从次数和停止时间多 的部分开始改善!
材启次主切卡
次材 主切启卡
料动工轴屑盘
工料 轴屑动盘
主要作用
① MTTR (Mean Time To Repair ): 平均修理时间 掌握修理难度
停止时间的合计
t a + t b + t c +……………. tx
= 停止回数 (件数) =
N
分析间接修理的 损失
维修工技能水平
ta
tb
tc
t
tx故障发生后的反
d
t1
t2
t3
t4
设备综合效率OEE的分析与改善!太实用了!
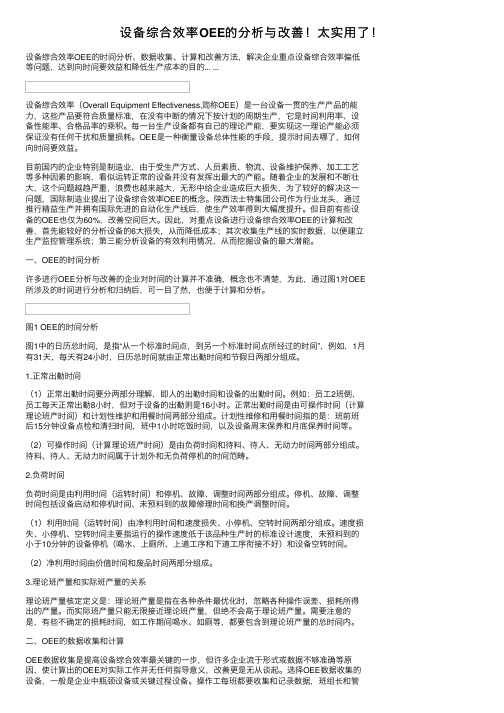
设备综合效率OEE的分析与改善!太实⽤了!设备综合效率OEE的时间分析、数据收集、计算和改善⽅法,解决企业重点设备综合效率偏低等问题,达到向时间要效益和降低⽣产成本的⽬的... ...设备综合效率(Overall Equipment Effectiveness,简称OEE)是⼀台设备⼀贯的⽣产产品的能⼒,这些产品要符合质量标准,在没有中断的情况下按计划的周期⽣产,它是时间利⽤率、设备性能率、合格品率的乘积。
每⼀台⽣产设备都有⾃⼰的理论产能,要实现这⼀理论产能必须保证没有任何⼲扰和质量损耗。
OEE是⼀种衡量设备总体性能的⼿段,提⽰时间去哪了,如何向时间要效益。
⽬前国内的企业特别是制造业,由于受⽣产⽅式、⼈员素质、物流、设备维护保养、加⼯⼯艺等多种因素的影响,看似运转正常的设备并没有发挥出最⼤的产能。
随着企业的发展和不断壮⼤,这个问题越趋严重,浪费也越来越⼤,⽆形中给企业造成巨⼤损失,为了较好的解决这⼀问题,国际制造业提出了设备综合效率OEE的概念。
陕西法⼠特集团公司作为⾏业龙头,通过推⾏精益⽣产并拥有国际先进的⾃动化⽣产线后,使⽣产效率得到⼤幅度提升。
但⽬前有些设备的OEE也仅为60%,改善空间巨⼤。
因此,对重点设备进⾏设备综合效率OEE的计算和改善,⾸先能较好的分析设备的6⼤损失,从⽽降低成本;其次收集⽣产线的实时数据,以便建⽴⽣产监控管理系统;第三能分析设备的有效利⽤情况,从⽽挖掘设备的最⼤潜能。
⼀、OEE的时间分析许多进⾏OEE分析与改善的企业对时间的计算并不准确,概念也不清楚,为此,通过图1对OEE所涉及的时间进⾏分析和归纳后,可⼀⽬了然,也便于计算和分析。
图1 OEE的时间分析图1中的⽇历总时间,是指“从⼀个标准时间点,到另⼀个标准时间点所经过的时间”,例如,1⽉有31天,每天有24⼩时,⽇历总时间就由正常出勤时间和节假⽇两部分组成。
1.正常出勤时间(1)正常出勤时间要分两部分理解,即⼈的出勤时间和设备的出勤时间。
利用ope快速提升效率心得体会

利用ope快速提升效率心得体会转职做生产管理后,第一感觉就是忙,不断地赶订单,第二感觉是累,更多的是心累,会议多了很多,尤其是公司高层的会议,几乎每隔一段时间,都会有一些降低成本的新方向出来,然后各工厂就要执行下去!那时,我满脑子都是“费用”和“成本”。
公司每天喊着的都是“Efficiency Up(效率提升)”和“Cost Down (降低成本)”。
尤其是08年之后,广东的最低工资标准飞涨,人工成本上涨,5月份又张了一次,具体张多少我忘记了。
但是,对于企业来讲,这些都是血淋淋的成本。
在销售额不能扩大的情况下,人工成本涨对企业的打击,无疑是致命的。
我所了解的很多企业,目标不是要利润提升多少,而是维持,压力确实蜜大的。
在经济危机笼罩的大背果下,维持已经殊为不易,更不要谈扩大销售。
在内部成本不断上涨的情况下,能够维持利润,简直类似于神话。
人工成本上涨,老板就盯着人工成本。
顾有几分“哪里上张压哪里,Soeasy!”的架势,为了应对人工成本上涨张,日本总郎给出的每年的生产力(Productivity)提升目标也在不断上张。
“提升效率”,曾经做愿梦的时候,是被这四个字吓醒的!从生产的角度讲,不管是降低人工成本,还是提高效,很大程度上都是要减少实际生产工时(AT,Actual time),就是用更少的时间生产出更多的订单。
这是一个“整体效率”的概念,对于企业而言,老板关心的一定不是某个工位的效率提升或者某个工段的效率提升,所关心的一定是工厂整体的效率提升,简单一点说,就是整个工厂以更少的投入获得更大的产出。
这是很多企业投入自动化的动机所在,自动化设备投入了,人就少了,所以,效率也就跟着提开了。
但这个逻辑并不全对。
工厂的效率高低与自动化水平并没有直接关系。
在我转职做生产管理之后,我所关注的重点就发生了转变,不仅关注ST(标准工时),但是更多的是关注AT(实际生产工时),主要是因为:AT(实际生产工时)在财务里就是直接生产人员出勤工时,财务部门要依据出勤工时给每个员工核算工资的,这在财务上是会构成实实在在的成本的:因为负麦一个工厂,我最关心的问题也随之变化。
oee设备综合效率

OEE设备综合效率
生产效率在制造业中起着至关重要的作用,而OEE(Overall Equipment Effectiveness)设备综合效率是一个关键的评估指标。
本文将探讨OEE设备综合效率的定义、计算方法、影响因素以及提高OEE的策略。
1. OEE设备综合效率的定义
OEE是一个综合性指标,用于衡量设备在生产过程中的综合表现。
它综合考虑了设备的开动率、性能率和质量率,反映出设备的整体运行效率。
2. OEE的计算方法
OEE的计算方法为:OEE = 开动率 x 性能率 x 质量率。
其中,开动率指的是设备实际运行时间占总时间的比例,性能率表示设备运行速度与设计速度之比,质量率表示合格品数量与总产量之比。
3. OEE设备综合效率的影响因素
影响OEE设备综合效率的因素多种多样,包括设备故障率、设备维护计划、操作人员技能等。
有效管理这些因素对提高OEE至关重要。
4. 提高OEE的策略
4.1 定期维护
定期维护设备可以减少故障率,提高设备的可靠性和稳定性,进而提升OEE。
4.2 持续改善
不断优化生产流程和设备设置,引入先进技术和管理方法,可以提高设备的性能率和质量率。
4.3 操作人员培训
提高操作人员的技能和知识水平,可以减少操作失误,提高设备的开动率和生产质量。
结语
OEE设备综合效率是一个关键的生产效率指标,通过科学的管理和技术手段提高设备的OEE,可以提升生产效率、降低生产成本,实现制造业的可持续发展。
有效管理OEE,是企业迈向产业4.0的重要一步。
以上内容仅为理论探讨,实践中具体落地还需根据不同企业的实际情况和需求来进行调整和优化。
经典OEE提升报告

为什么对以手工作业为主体的装配线
参考
应用OEE是不合适的呢?
设备的节拍成为瓶颈的生产线
人的作业成为瓶颈的生产线
「生产线的综合效率 」是指「设备在多大 「生产线的综合效率」是指「人在多大
程度上能够避免浪费而生产呢 」
程度上能够避免浪费而生产呢 」
OP5 OP4 OP3 OP2 OP1
O P3
所有设备的加工没有完成、
O P2
零件不会移动到下一个设备
瓶颈工序决定节拍
O P1
例)把多台机械加工设备用传送带来连接的生产线
加工時間 待ち 搬送
OP3
OP2
OP1
更换零件 加工时间 计划节拍 停工待料
B
A
OP1
14秒
120秒
134秒
OP2
14秒
89秒
103秒
*开动时间=负荷时间-停止时间
*良品率=
产量-不良数 产量
如果不良数知道 的话就能够计算
负荷时间・停止时间・计划节拍・产量・不良数等知道的话就能够计算
OEE是什么?(来看看损失的构成!)
上班时间
生产时间
生产外时间(教育、会议・・・)
负荷时间 开动时间
计划停止(计划保全・生产停止・
早晚会・・)
停止损失
OP5 OP4 OP3 OP2 OP1
如果某一工序停止 生产线全体也停止
假设各工序的OEE
是这样的・・・。
那么线整体的
OP1
85% OEE是多少呢?
OP2 OP3 OP4 OP5
80% 90% 75% 80%
85%×80%×90%×75%×80%=
OEE设备综合效率改善(2+1模式)2

5、确定设备问题的要因:确定各项原因的判别标准,现场分析确认各项原因是否达到标准,以此判定是否是主要原因
6、制定改善对策方案:针对要因制定改善对策方案和改善计划
7、对策实施方案:能马上落实的改善对策现场实施,其它方案根据改善计划实施并及时跟进实施状况
9、设备故障树分析法(FTA)
10、检修管理作业标准
11、建立完善的检修管理标准化流程
案例:滚动轴承功能故障前的不同潜在故障点分析
案例:汽机检修作业标准案例分析
案例:双螺杆常见故障分析
五、提高设备利用率改善OEE
1、人机配合效率改善
2、设备切换效率改善
3、作业切换时间的形态
4、快速切换改善着眼点
5、快速切换的实施法则
1、掌握设备综合效率的计算方法
2、通过建立设备点检标准改善OEE
3、通过建立设备保养标准改善OEE
4、通过建立设备检修标准改善OEE
5、提高设备利用率改善OEE
6、设备故障问题分析解决改善OEE
7、减少设备准备时间,实现快速换型
8、降低加工不良,学习防错技术
9、提升维修技术,减少故障时间
培训对象
维修部门的工程师、经理、主管,中高层管理者和生产(制造)部门经理、主管、现场班组长。
(1)设备点检表项目---点检部位
(2)设备点检表项目---点检内容
(3)设备点检表项目---点检方法
(4)设备点检表项目---点检标准
(5)设备点检表项目---点检周期
10、精密点检与设备劣化倾向管理
(1)精密点检内容
(2)精密点检的主要检测方法
(3)设备劣化管理
OEE(设备综合效率)分析与管理

OEE(设备综合效率)分析与管理嘿,伙计们!今天我们要聊聊一个非常有趣的话题:OEE(设备综合效率)分析与管理。
你知道吗,这个话题可是关乎到咱们工厂的生产效率呢!所以,我们可得认真对待,不能马虎。
让我们来简单了解一下OEE是什么吧。
OEE是设备的运转率、可用率和性能指标的综合体现,它可以帮助我们了解设备的运行状况,从而提高生产效率。
好了,现在我们已经知道了OEE的重要性,那么接下来就要看看如何进行OEE分析和管理了。
我们要做的是收集数据。
这可是个技术活儿,可不是随便拍几张照片就能搞定的。
我们需要定期对设备进行检查,记录下设备的运行时间、故障时间等信息。
这些数据可是OEE分析的基础哦!接下来,我们要对这些数据进行整理。
把相同类型的设备放在一起,把相同的时间段也放在一起。
这样一来,我们就可以更清楚地看到设备的运行状况了。
如果有数据缺失或者不准确的地方,我们要及时进行调整和补充。
整理好数据后,我们就可以开始进行OEE分析了。
这里有几个关键指标:运转率、可用率和性能指标。
运转率是指设备实际运行时间与计划运行时间的比值;可用率是指设备在规定时间内正常运行的时间占总时间的比例;性能指标则是根据设备的性能要求制定的一些标准,比如设备的输出功率、产量等。
通过这三个指标,我们可以得出设备的综合效率。
我们还可以进一步分析设备的瓶颈在哪里,从而找到提高生产效率的方法。
比如,如果发现设备的某个部件经常故障,那我们就需要及时更换或者维修这个部件,以保证设备的正常运行。
在进行OEE分析的过程中,我们还要注意数据的准确性和可靠性。
毕竟,这些数据关系到我们的生产效率,可不能马虎大意。
所以,我们在收集数据、整理数据的过程中,一定要细心、耐心地去做。
我们要把OEE分析的结果运用到实际生产中去。
比如,我们可以根据OEE分析的结果,调整生产线的布局,优化设备的使用方式等。
这样一来,我们的生产效率就会得到显著提高啦!OEE分析和管理是一个系统性的工作,需要我们从多个方面入手。
- 1、下载文档前请自行甄别文档内容的完整性,平台不提供额外的编辑、内容补充、找答案等附加服务。
- 2、"仅部分预览"的文档,不可在线预览部分如存在完整性等问题,可反馈申请退款(可完整预览的文档不适用该条件!)。
- 3、如文档侵犯您的权益,请联系客服反馈,我们会尽快为您处理(人工客服工作时间:9:00-18:30)。
提升OEE(设备综合效率)实战训练
---心得
一、 简述
1、培训时间:
***年*月*日
2、地 点:
*******
3、学员
***
3、主办单位:
北京冠卓企业管理顾问有限公司
4、培训目的:
保证设备的良好运转,为生产提供助力、提升企业竞争力。
5、培训内容:
·认识设备综合效率(OEE)
·如何计算设备的综合效率{OEE0}
·降低设备停机损失的分析和改善
·缩短生产准备时间的分析和改善
·设备性能降低的分析与改善
·设备加工不良的分析与改善
·设备综合效率的现场应用
·设备OEE提升的改善活动
6、培训方式
讲授法模式进行培训
二、培训心得体会
两天的培训学习提升OEE的应用,我个人的认识和感想与大家一起分享,希望能有所
帮助。
1、OEE含义
OEE是一个独立测量设备效率的工具,也是展示TPM活动成果的指标,它表示了设备实际
的产出对于理论产能的比率。
2、(OEE)理论计算
OEE = 时间运转率 * 性能运转率 * 良品率
其中:
时间运转率 = 运转时间 / 负荷时间 * 100%
性能运转率 =(单件产品的理论生产时间 * 总生产数量)/ 运转时间 * 100%
良品率 =(总生产数量 — 不良数量)/ 总生产数量 * 100%
通过这样统计计算的目的,就是让我们有数据可分析,而后才能准确的得以改善,控制
我们的工作流程,以求达到改进工作的目的。
3、设备OEE低下的分析和改善
分析方法:
当我们的设备OEE低下时,我们需要选择一种符合生产现场的分析方法,将设备OEE
低下的问题分析出来,从而才能浮现出改善方法,在培训学习提升OEE中,有一个分析工具
叫“PM分析法”,PM分析法:将现象(Phenomena)作物理(Physical)解析,并从结构上
(Mechanism)作分解,导出所有与人、机、物、料、环、及工艺相关的原因,逐项排查,进
而找到问题发生的根本原因排除设备故障。
运用PM分析法的7个步骤:①查明现象→②物理分析→③成立条件→④逐一排查→⑤
找出异常→⑥制定方案→⑦改善设施。
改善方法:
①对生产设备准备时间的损失的改善,我们可以用“快速换型”,也就是单分钟模具转换
(﹤10分钟),换型时间的定义是,从上个产品的作业结束,到下一产品开始出现良品时所
需的时间。将这种方法用来减少换模时间的浪费,但是我要注重的是将所有换型时间控制在
10分钟以下,才能达到我们预期改善的目的。
②生产设备性能低下的改善:设备速度低下、空转瞬间停止是主要影响设备性能低下的
原因。设备设计时要达到额定速度,赋予固有可靠性,设备使用和保养时要赋予使用可靠性。
可靠性既是指系统、设备或零部件,在规定的条件和时间内,完成规定功能的能力。
三、改善计划
目前我公司未进行OEE计算,我个人认为可不进行计算,因为OEE是展示TPM活动
成果的指标,我们需要将TPM预防维修推行成功后才能实施OEE计算。
对生产设备准备时间的损失的改善:
①针对生产设备日常更换刀模具停机损失进行分析,预计2012年12月15日前完成。
②前期阶段以11#机生产设备为示范,制定成切刀、棉切刀总成更换改善方案,预计2012
年12月30日前完成。
③2013年元月30日完成11#机1台设备作示范,如试用可行,便对其他设备逐一进行改善。
四、总结
对于系统实施提升OEE,后续TPM预防维修逐步完善后才能推行,这样才能保证设备的良
好运转,为生产提供助力、提升企业竞争力。
设备科