划线与钻孔
【钳工基本操作2】划线与冲眼
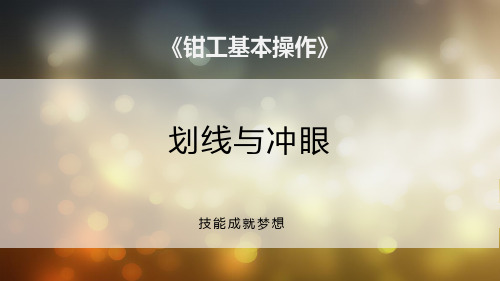
2.选择划线基准 划线时选择一个或几个平面(或线) 作为划线的根据,划其余的尺寸线都从这 些线或面开始,这样的线或面就是划线基 准。选定划线基准应尽量与图纸上的设计 基准一致。
钳工
01 划线工具 02 划线方法 03 冲眼
3.划线 (1)平行线的划法 1)用靠边角尺推平行线。将角尺紧靠 工件基准边,并沿基准边移动,用钢尺度 量尺寸后,沿角尺划出。
二、划线方法
基本操作步骤:划线前的准备→选择划线基准 →划线。 1.划线前的准备
划线前,在工件划线部位的表面涂上一层薄而 均匀的涂料,从而使划出的线条清晰。涂料与其 表面要有一定的附着力。
常用的涂料有石灰水,适用于铸、锻件的毛坯 表面;蓝油,适用于已加工的表面。
钳工
01 划线工具 02 划线方法 03 冲眼
正确
错误
钳工
01 划线工具 02 划线方法 03 冲眼
3.样冲
它一般用工具钢制成,尖端磨成45º~60º并淬硬 (可用废丝锥或废立铣刀代用),也称中心冲,用 于在工件所划加工线条上冲小眼。冲眼的作用是固 定已划好的线条或为作直线、作圆、作圆弧或钻孔 定中心。
外形
样冲角度
钳工
01 划线工具 02 划线方法 03 冲眼
3)正多边形的划法。在已知圆内划正方形;在已 知圆内划正六方形,用几何作图法或用按等弦长 作图法划出。
在圆内划正方形
在圆内划正六方形
钳工
01 划线工具 02 划线方法 03 冲眼
三、冲眼
1.冲眼方法 冲眼时要看准位置,先将样冲外倾,使尖端对正 视的正中。然后再将样冲直立冲眼,同时手要搁实。
外倾对线
直立冲眼
钳工
01 划线工具 02 划线方法 03 冲眼
钻孔规范要求
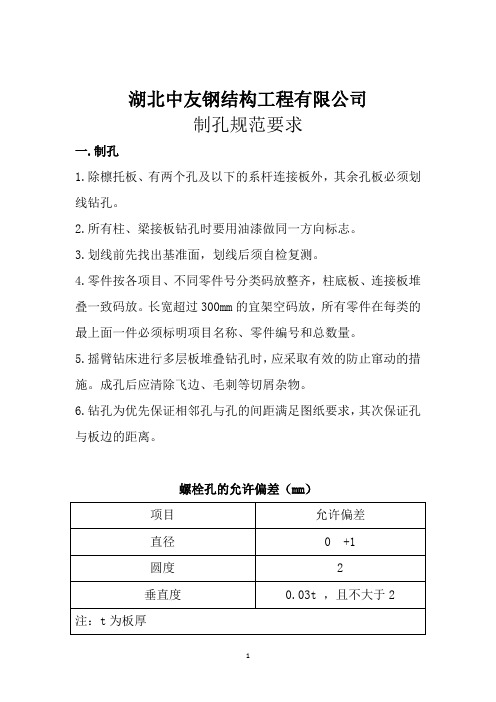
湖北中友钢结构工程有限公司
制孔规范要求
一.制孔
1.除檩托板、有两个孔及以下的系杆连接板外,其余孔板必须划线钻孔。
2.所有柱、梁接板钻孔时要用油漆做同一方向标志。
3.划线前先找出基准面,划线后须自检复测。
4.零件按各项目、不同零件号分类码放整齐,柱底板、连接板堆叠一致码放。
长宽超过300mm的宜架空码放,所有零件在每类的最上面一件必须标明项目名称、零件编号和总数量。
5.摇臂钻床进行多层板堆叠钻孔时,应采取有效的防止窜动的措施。
成孔后应清除飞边、毛刺等切屑杂物。
6.钻孔为优先保证相邻孔与孔的间距满足图纸要求,其次保证孔与板边的距离。
螺栓孔的允许偏差(mm)
螺栓孔孔间距的允许偏差(mm)。
7实习教案(划线、钻孔——在台式钻床上钻孔)
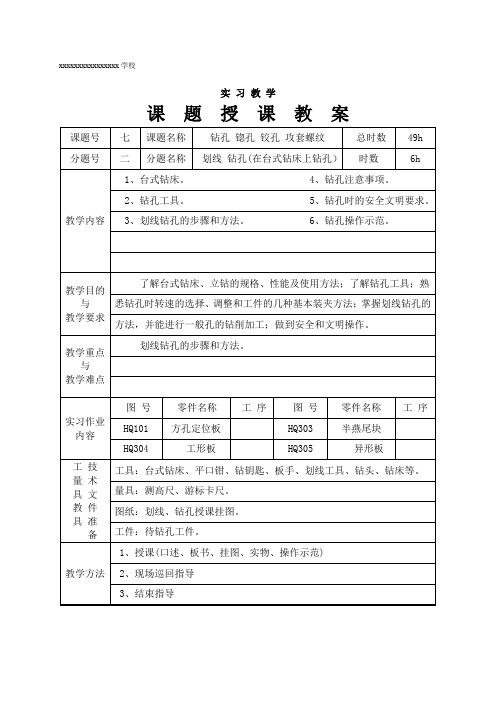
xxxxxxxxxxxxxxxx学校实习教学课题授课教案组织教学集合、点名、检查学生着装、安定学生情绪。
导入新课授课钻孔钻孔:用钻头在实心材料上加工孔的方法,称为钻孔。
钻孔是工业生产中一项很重要的工作,因为钻头的刚性和精度都较差,所以,钻孔后的公差等级一般为IT10~IT9,表面粗糙度值大于或等于Ra12.5μm。
故钻孔操作主要加工精度要求不高的孔或作为孔的粗加工。
一、台式钻床(对照挂图或实物重点讲解结构及功能)——了解台式钻床简称台钻。
是一种小型钻床,主要用来加工直径小于或等于12毫米的小孔。
它结构简单,操作方便,灵活性较大,常用于零件的加工、装配、和修理工作中,在工厂很受欢迎。
钻孔时,工件装夹在钻床的工作台上固定不动,钻头装在钻床主轴上(或装在与主轴连接的钻夹头上),一面旋转作切削运动(主运动),一面沿钻头轴线向下作直线进给运动(进给运动)。
二、钻孔工具(对照实物讲解)——了解1、钻头:钻头在钻孔中主要起切削作用。
它的材料主要是高速钢和硬质合金。
种类有麻花钻和扁钻。
其中麻花钻是使用最多最普遍的钻孔工具。
根据麻花钻柄部的形状不同有直柄和锥柄之分(关于钻头的几何形状和切削角度将在下堂钻头刃磨中讲解)。
2、辅助工具:辅助工具主要是装夹工件和退卸钻头的定位装夹工具。
台钻上常用的辅助工具主要有钻夹头和钻钥匙、平口钳和板手,另外还有V型铁、压板、垫铁和螺栓、手虎钳及软钳口等。
三、划线钻孔的步骤和方法(对照实物以操作示范为主)——重点掌握1、钻孔前工件的划线:(1)、按孔的位置尺寸要求划出孔的十字中心线,并打上中心冲眼(冲眼要小,位置要准)。
(2)、按孔径的大小划出孔的圆周线。
对直径较大的孔,应划出几个大小不等的校正园或以孔中心为对称的几个校正方格(见下图),以方便钻孔时检查。
(3)、将冲眼加大,以方便正确落钻定心。
检查圆检查方框孔位检查线形状2、钻孔前的准备:(1)、根据工件材料及工艺要求,刃磨好钻头,并检查刃磨质量。
第一章钳工操作基础1-pdf
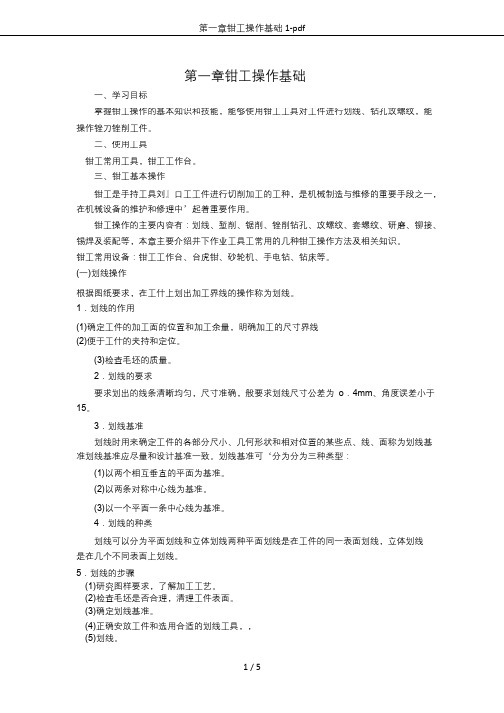
第一章钳工操作基础一、学习目标掌握钳工操作的基本知识和技能,能够使用钳工工具对工件进行划线、钻孔攻螺纹,能操作锉刀锉削工件。
二、使用工具钳工常用工具,钳工工作台。
三、钳工基本操作钳工是手持工具刘』口工工件进行切削加工的工种,是机械制造与维修的重要手段之一,在机械设备的维护和修理中’起着重要作用。
钳工操作的主要内容有:划线、堑削、锯削、锉削钻孔、攻螺纹、套螺纹、研磨、铆接、锡焊及装配等,本章主要介绍井下作业工具工常用的几种钳工操作方法及相关知识。
钳工常用设备:钳工工作台、台虎钳、砂轮机、手电钻、钻床等。
(一)划线操作根据图纸要求,在工什上划出加工界线的操作称为划线。
1.划线的作用(1)确定工件的加工面的位置和加工余量,明确加工的尺寸界线(2)便于工什的夹持和定位。
(3)检查毛坯的质量。
2.划线的要求要求划出的线条清晰均匀,尺寸准确,般要求划线尺寸公差为 o.4mm、角度误差小于15。
3.划线基准划线时用来确定工件的各部分尺小、几何形状和相对位置的某些点、线、面称为划线基准划线基准应尽量和设计基准一致。
划线基准可‘分为分为三种类型:(1)以两个相互垂直的平面为基准。
(2)以两条对称中心线为基准。
(3)以一个平面一条中心线为基准。
4.划线的种类划线可以分为平面划线和立体划线两种平面划线是在工件的同一表面划线,立体划线是在几个不同表面上划线。
5.划线的步骤(1)研究图样要求,了解加工工艺。
(2)检查毛坯是否合理,清理工件表面。
(3)确定划线基准。
(4)正确安放工件和选用合适的划线工具,,(5)划线。
(6)检查划线的正确性及是否有线条漏划。
(7)在线条卜打样冲眼。
6.划线工具(1)划线平板:划线平板面是划线的基准面,用来支撑工件持光洁。
平板安放应保持水平,板面保(2)划针:划针是用来在工件上划线条,尖端成 15°—20°夹角。
划线时,针尖紧靠导向工具的边缘,上部向外侧倾斜 20°‘左右,向划线方向倾斜 60°左右。
(整理)模具钳工操作规范
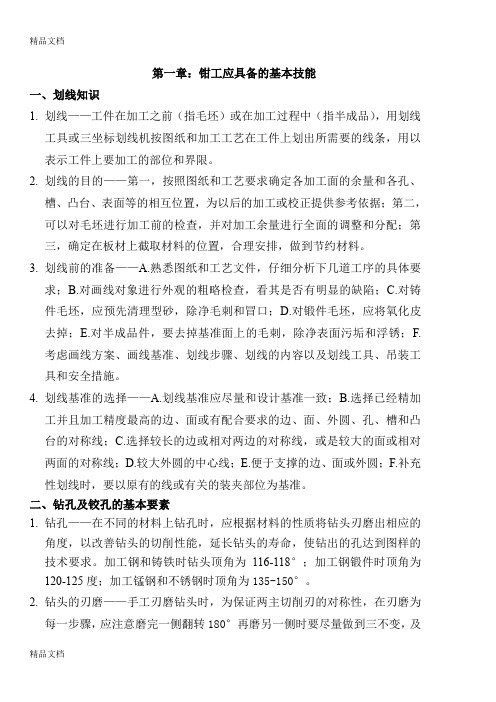
第一章:钳工应具备的基本技能一、划线知识1.划线——工件在加工之前(指毛坯)或在加工过程中(指半成品),用划线工具或三坐标划线机按图纸和加工工艺在工件上划出所需要的线条,用以表示工件上要加工的部位和界限。
2.划线的目的——第一,按照图纸和工艺要求确定各加工面的余量和各孔、槽、凸台、表面等的相互位置,为以后的加工或校正提供参考依据;第二,可以对毛坯进行加工前的检查,并对加工余量进行全面的调整和分配;第三,确定在板材上截取材料的位置,合理安排,做到节约材料。
3.划线前的准备——A.熟悉图纸和工艺文件,仔细分析下几道工序的具体要求;B.对画线对象进行外观的粗略检查,看其是否有明显的缺陷;C.对铸件毛坯,应预先清理型砂,除净毛刺和冒口;D.对锻件毛坯,应将氧化皮去掉;E.对半成品件,要去掉基准面上的毛刺,除净表面污垢和浮锈;F.考虑画线方案、画线基准、划线步骤、划线的内容以及划线工具、吊装工具和安全措施。
4.划线基准的选择——A.划线基准应尽量和设计基准一致;B.选择已经精加工并且加工精度最高的边、面或有配合要求的边、面、外圆、孔、槽和凸台的对称线;C.选择较长的边或相对两边的对称线,或是较大的面或相对两面的对称线;D.较大外圆的中心线;E.便于支撑的边、面或外圆;F.补充性划线时,要以原有的线或有关的装夹部位为基准。
二、钻孔及铰孔的基本要素1.钻孔——在不同的材料上钻孔时,应根据材料的性质将钻头刃磨出相应的角度,以改善钻头的切削性能,延长钻头的寿命,使钻出的孔达到图样的技术要求。
加工钢和铸铁时钻头顶角为116-118°;加工钢锻件时顶角为120-125度;加工锰钢和不锈钢时顶角为135-150°。
2.钻头的刃磨——手工刃磨钻头时,为保证两主切削刃的对称性,在刃磨为每一步骤,应注意磨完一侧翻转180°再磨另一侧时要尽量做到三不变,及手持钻头的部位不变,手的姿势不变,刃磨吃刀情况不变。
2022届浙江选考高中通用技术考点专练 考点17 金工工艺流程
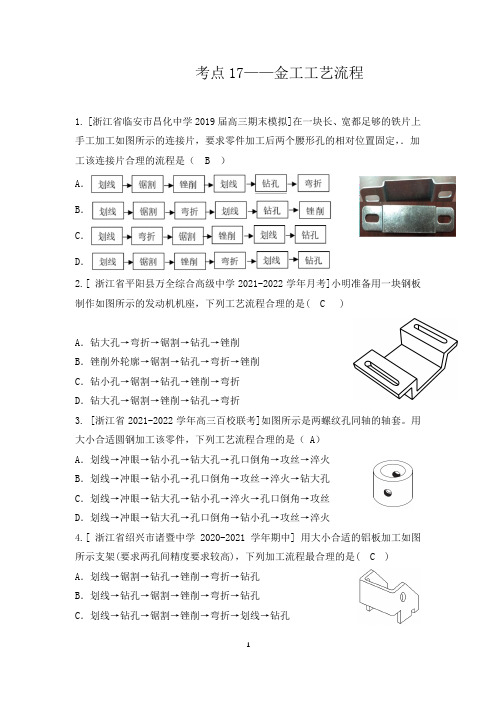
考点17——金工工艺流程1. [浙江省临安市昌化中学2019届高三期末模拟]在一块长、宽都足够的铁片上手工加工如图所示的连接片,要求零件加工后两个腰形孔的相对位置固定,.加工该连接片合理的流程是( B )A.B.C.D.2.[ 浙江省平阳县万全综合高级中学2021-2022学年月考]小明准备用一块钢板制作如图所示的发动机机座,下列工艺流程合理的是( C )A.钻大孔→弯折→锯割→钻孔→锉削B.锉削外轮廓→锯割→钻孔→弯折→锉削C.钻小孔→锯割→钻孔→锉削→弯折D.钻大孔→锯割→锉削→钻孔→弯折3. [浙江省2021-2022学年高三百校联考]如图所示是两螺纹孔同轴的轴套。
用大小合适圆钢加工该零件,下列工艺流程合理的是( A)A.划线→冲眼→钻小孔→钻大孔→孔口倒角→攻丝→淬火B.划线→冲眼→钻小孔→孔口倒角→攻丝→淬火→钻大孔C.划线→冲眼→钻大孔→钻小孔→淬火→孔口倒角→攻丝D.划线→冲眼→钻大孔→孔口倒角→钻小孔→攻丝→淬火4.[ 浙江省绍兴市诸暨中学2020-2021学年期中] 用大小合适的铝板加工如图所示支架(要求两孔间精度要求较高),下列加工流程最合理的是( C ) A.划线→锯割→钻孔→锉削→弯折→钻孔B.划线→钻孔→锯割→锉削→弯折→钻孔C.划线→钻孔→锯割→锉削→弯折→划线→钻孔D.划线→钻孔→锯割→弯折→锉削→划线→钻孔5.[ 浙江省湖州市德清县第三中学2020-2021学年返校考试] 小明用一块大小合适的矩形钢加工成如图所示的零件,下列加工“形状I”步骤合理的是( A)A.划线→钻孔→锯割→锉削B.划线→锯割→钻孔→锉削C.划线→锯割→锉削→钻孔D.划线→钻孔→锉削→锯割6. [浙江省绍兴市上虞区2020-2021学年期末教学质量调测]将一块厚度为 2mm,大小合适的钢板加工成如图所示的工件。
以下加工流程中合理的是( C )A.划线→锯割→弯折→钻孔→锉削B.划线→钻孔→锯割→锉削→弯折C.划线→钻孔→锯割→弯折→锉削D.划线→锯割→钻孔→锉削→弯折7. [浙江省名校协作体2020-2021学年联考]如图所示是小明用30mm×30mm长度合适的方钢加工的连接件。
钻孔时注意事项
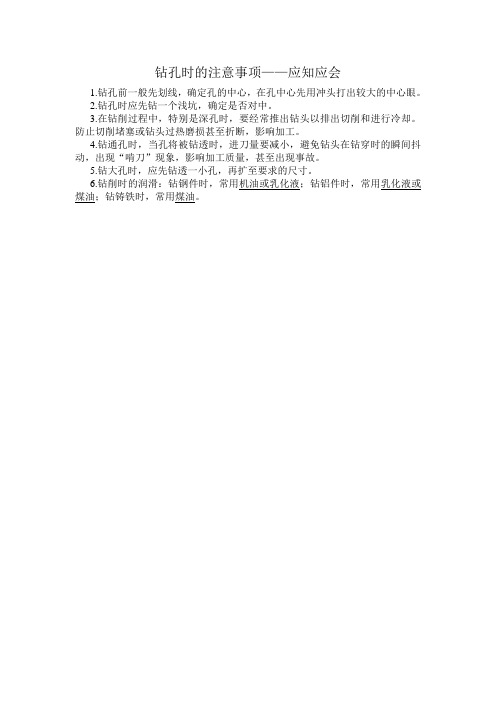
钻孔时的注意事项——应知应会
1.钻孔前一般先划线,确定孔的中心,在孔中心先用冲头打出较大的中心眼。
2.钻孔时应先钻一个浅坑,确定是否对中。
3.在钻削过程中,特别是深孔时,要经常推出钻头以排出切削和进行冷却。
防止切削堵塞或钻头过热磨损甚至折断,影响加工。
4.钻通孔时,当孔将被钻透时,进刀量要减小,避免钻头在钻穿时的瞬间抖动,出现“啃刀”现象,影响加工质量,甚至出现事故。
5.钻大孔时,应先钻透一小孔,再扩至要求的尺寸。
6.钻削时的润滑:钻钢件时,常用机油或乳化液;钻铝件时,常用乳化液或煤油;钻铸铁时,常用煤油。
钳工技能划线

划线划线是利用划线工具,按图样要求,在毛坯或半成品上划出加工界线,称为划线。
(毛坯 -- 已具有所要求的形体,需要加工才能制成零件的半成品,通常指铸件或锻件。
)划线是钳工的先行工序,是钳工操作的第一个步骤,工件在加工的过程中,划线起着重要的指导作用。
如;在工件上钻孔,要通过划线确定孔的位置。
加工锤头(实习考核件)也要先划出锤头形状,然后再进行加工,不能拿着一块料盲目的琢磨着去干。
一、划线简介1)划线的种类划线分为平面划线和立体划线两种。
平面划线:是在工件或毛坯的一个平面上划线。
立体划线:是平面划线的复合,是在工件或毛坯的几个表面上划线即在工件的长、宽、高三个方向划线。
2)划线的基本要求1.线条清晰均匀、定形、定位尺寸准确。
2.划线精度一般为0.25~0.5mm。
3.工件的加工精度不能完全由划线确定,而应在加工过程中通过测量来保证。
3)划线的主要作用(1)确定加工面的加工位置和加工余量,使加工有明显的界限。
(2)便于复杂工件在机床上的装夹,可按划线找正定位。
(3)还可以及时发现不合格的毛胚从而及时处理,以避免不必要的浪费。
(4)还可以通过借料划线使误差较大的毛胚得到补救,提高毛坯的利用率。
二、主要划线工具划线的工具很多,按用途分有以下几类:基准工具、量具、直接划线工具以及夹持工具等。
1)基准工具划线平台是划线的主要基准工具。
其安放时要平稳牢固,上平面要保持水平。
平面的各处要均匀使用,不许碰撞或敲击其表面,要注意其表面的清洁。
长期不用时,应涂防锈油防锈,并盖保护罩。
划线平板的使用方法1、钢制平板一般用于冷作放样或样板修整;铸铁平板除具有钢制平板用途外,经压砂后可作研磨工具;大理石平板不须涂防锈油脂,且受温度影响较小,但湿度高时易变形。
2、0、1、2级平板一般作检验用,3级平板一般作划线用。
3、平板安放平稳,一般用三个支承点调整水平面。
大平板增加的支承点须垫平垫稳,但不可破坏水平,且受力须均匀,以减少自重受形。
- 1、下载文档前请自行甄别文档内容的完整性,平台不提供额外的编辑、内容补充、找答案等附加服务。
- 2、"仅部分预览"的文档,不可在线预览部分如存在完整性等问题,可反馈申请退款(可完整预览的文档不适用该条件!)。
- 3、如文档侵犯您的权益,请联系客服反馈,我们会尽快为您处理(人工客服工作时间:9:00-18:30)。
操作方法⒈准确划线钻孔前,首先应熟悉图样要求,加工好工件的基准;一般基准的平面度≤0.04mm,相邻基准的垂直度≤0.04mm。
按钻孔的位置尺寸要求,使用高度尺划出孔位置的十字中心线,要求线条清晰准确;线条越细,精度越高。
由于划线的线条总有一定的宽度,而且划线的一般精度可达到0.25~0.5mm,所以划完线以后要使用游标卡尺或钢板尺进行检验;若对于划线后检验做的不够,经常拿着划错线的工件进行钻孔,根本保证不了孔的位置精度;特别是在等级鉴定的考场上,由于学生们心理紧张担心工件不能按时完成,往往划完线后不进行检验急于钻孔,等到发现孔的位置精度超差较大时已经晚了。
因此,要养成划完线后进行检验的好习惯。
⒉划检验方格或检验圆划完线并检验合格后,还应划出以孔中心线为对称中心的检验方格或检验圆,作为试钻孔时的检查线,以便钻孔时检查和借正钻孔位置,一般可以划出几个大小不一的检验方格或检验圆,小检验方格或检验圆略大于钻头横刃,大的检验方格或检验圆略大于钻头直径。
⒊打样冲眼划出相应的检验方格或检验圆后应认真打样冲眼。
先打一小点,在十字中心线的不同方向仔细观察,样冲眼是否打在十字中心线的交叉点上,最后把样冲眼用力打正打圆打大,以便准确落钻定心。
这是提高钻孔位置精度的重要环节,样冲眼打正了,就可使钻心的位置正确,钻孔一次成功;打偏了,则钻孔也会偏,所以必须借正补救,经检查孔样冲眼的位置准确无误后方可钻孔。
钻孔加工,钻孔加工厂打样冲眼有一小窍门:将样冲倾斜着样冲尖放在十字中心线上的一侧向另一侧缓慢移动,移动时,当感觉到某一点有阻塞的感觉时,停止移动直立样冲,就会发现这一点就是十字中心线的中心;此时在这一点打出的样冲眼就是十字中心线的中心,也可以多试几次,你就会发现样冲总会在十字中心线的中心处有阻塞的感觉。
⒋装夹擦拭干净机床台面、夹具表表面、工件基准面,将工件夹紧,要求装夹平整、牢靠,便于观察和测量。
应注意工件的装夹方式,以防工件因装夹而变形。
⒌试钻钻孔前必须先试钻:使钻头横刃对准孔中心样冲眼钻出一浅坑,然后目测该浅坑位置是否正确,并要不断纠偏,使浅坑与检验圆同轴。
如果偏离较小,可在起钻的同时用力将工件向偏离的反方向推移,达到逐步校正。
如果偏离过多,可以在偏离的反方向打几个样冲眼或用錾子錾出几条槽,这样做的目的是减少该部位切削阻力,从而在切削过程中使钻头产生偏离,调整钻头中心和孔中心的位置。
试钻切去錾出的槽,再加深浅坑,直至浅坑和检验方格或检验圆重合后,达到修正的目的再将孔钻出。
注意:无论采用什么方法修正偏离,都必须在锥坑外圆小于钻头直径之前完成。
如果不能完成,在条件允许的情况下,还可以在背面重新划线重复上述操作。
⒍钻孔钳工钻孔一般以手动进给操作为主,当试钻达到钻孔位置精度要求后,即可进行钻孔。
受动进给时,进给力量不应使钻头产生弯曲现象,以免孔轴线歪斜。
钻小直径孔或深孔时,要经常退钻排屑,以免切屑阻塞而扭断钻头,一般在钻孔深度打直径的3倍时,一定要退钻排屑。
此后,每钻进一些就应退屑,并注意冷却润滑,钻孔的表面粗糙度值要求很小时,还可以选用3%~5%乳化液、7%硫化乳化液等起润滑作用的冷却润滑液.钻孔将钻透时,手动进给用力必须减小,以防进给量突然过大、增大切削抗力,造成钻头折断、或使工件随着钻头转动造成事故。
钻孔位置控制钻孔的位置精度的控制,实质上是钻削过程中钻头与工件的相互正确位置控制过程。
为了考核操作者的操作技能,要求钻孔时孔的位置调整只能是手工、动态控制过程,不允许使用钻模以及其他夹具,因此孔的位置精度受到划线、机床精度、工件和钻头的装夹、钻头刃磨质量、工件位置及机床切削用量的调整等一些不确定因素的影响,再加上要有一定的加工技巧和必要的保证措施,所以,当孔的位置精度要求较高时,就会导致出现严重超差现象。
如何有效地避免和消除孔的位置超差现象,是控制钻孔时孔的质量关键。
在钻孔操作时,除了划线正确之外,钻正底孔、及时准确纠偏、修锉底孔的位置,是保证孔的位置精度的基础。
⒈划线由于开始钻孔时的位置精度基本上取决于样冲眼的位置,这样就把动态控制孔的位置精度在一定程度上转化为样冲眼位置的冲制精度上来。
考虑到打样冲眼在控制孔的位置精度时所起的重要的作用,所以,在具体操作时应注意:①选取刀头锋利的高度尺,以便在加工表面上划出孔中心线的沟痕较深,利用样冲移动时孔中心线沟痕对它的阻力作用,来确定样冲眼打制的正确位置。
②为了减少目测孔中心与理想位置的尺寸偏差,应划出各尺寸孔的控制圆或控制方框(由于划线精度的原因,建议采用划控制方框的方法),并在钻削过程中目测的同时,利用卡尺测量的方法,保证其位置精度。
③由于把修锉、钻扩底孔进行纠偏方式转移到样冲眼位置偏差的纠正上来,可更有效地减少扩孔纠偏底孔的位置的次数,缩短操作加工时间,所以,打完样冲眼后要仔细检查其位置精度并作必要的纠偏。
⒉工件及钻头的装夹由于在钻孔过程中,如只采用目测的方法很难保证其位置精度,必须采用游标卡尺等量具进行测量,为了方便测量,在工件安装时要使工件高出机用虎钳钳口一定尺寸。
钻头的装夹要尽可能短,以提高其刚性和强度,从而更有利于其位置精度的保证。
⒊钻底孔底孔的位置正确或者超差较小,可有效地减少扩孔纠偏底孔的位置的次数,缩短操作加工时间,对提高加工精度及加工效率具有特别重要的作用。
第一步:钻头直径的选择,钻头直径太小,强度弱,加工过程中易折断;钻扩纠偏时,钻头弯曲、偏斜,导致向欲纠偏的相反方向加工,加大了原有的孔的位置误差。
钻头直径太大,横刃长,定心性能差,修锉、钻扩纠偏孔的位置的次数相对减少。
如果底孔孔径相对图纸规定的孔径较大,有可能对超差的底孔不能消除。
故应根据实际情况选择合适的钻头,因为中心钻既能很好定位又能保证足够的刚度和强度,所以在钻底孔时选用中心钻为宜。
第二步:对正样冲眼,中心钻与样冲眼的对正有两种方法,一是用手转动钻夹头,并移动平口钳或转动台钻的工作台,使中心钻与样冲眼对正。
二是比较规整的工件尽可能处于浮动状态,依靠钻削力的拉动使工件位置产生微量的移动,让钻头与样冲眼自动对中。
第三步:检测,为了提高孔的位置的检测精度,应对检测结果进行必要的修正:一是测量两孔壁的最近点和最远点,取平均值。
二是采取钻孔后插入相应的量棒再进行测量,以减小游标卡尺测量爪非线型因素对测量结果的影响。
⒋扩孔的位置控制底孔的位置经检测确定位置正确,应采取有效措施,防止在扩孔过程中孔的位置产生新的位置偏差。
首先扩孔所用的钻头顶角要小,以减小钻削时的径向偏心力及振动,增大自动定心的作用和效果。
然后用手转动钻夹头,并移动平口钳或转动台钻的工作台,使钻头的两主切削刃同时与原底孔的钻头进入端端口孔壁接触后,再开动钻床进行钻孔,这样操作基本上能保证原底孔的位置不变。
⒌扩孔纠偏对于孔的位置超差在0.20mm以内的底孔,可采取向纠偏方向推动工件,逐步加大钻头直径进行扩孔方式加以解决。
(注意:为了削弱钻头自动定心作用,应适当加大钻头顶角角度)⒍修锉纠偏对于孔的位置超差大于0.20mm的底孔,若仍然采取上述方法,势必会增加扩孔的次数和不同规格尺寸的钻头占有量,延长纠偏的时间。
可采取圆锉修锉技术去除多余的偏移余量后,再配以钻扩方式加以解决。
第一步:相关测量计算,先测量出底孔的尺寸误差、形位误差,如超差,相对理想位置,通过计算分析出孔的位置误差值。
然后,确定修锉底孔的方向(修锉底孔的方向,为实际孔的位置中心到理想位置中心的连线方向)和修锉孔的形状(修锉孔的形状应接近椭圆状,椭圆的几何中心与理想位置中心重合,椭圆的短轴为原底孔直径,消除孔的位置误差的最小底孔直径,即为椭圆的长轴)。
第二步:选择锉刀和修锉方法,所选的修锉圆锉直径略小于原底孔直径。
直径过大或等于底孔直径,圆锉插不进底孔内或修锉时锉削困难。
过小易修锉成梨状,使钻头不对称受力,钻孔时产生新的孔的位置偏移误差。
修锉时可在台虎钳上用手工修锉,也可借助于钻床主轴的旋转运动,把圆锉夹于钻夹头内,上下移动,推动工件进行加工。
薄板件从底孔一端修锉即可;当工件较厚时,对于通孔来讲,应从底孔两端进行修锉,以减少锉内圆弧面与孔口端面的不垂直误差。
第三步:扩孔,所选扩孔钻头的直径应大于工件厚度中间平面的椭圆长轴的尺寸。
扩孔应尽量选用短钻头,小的顶角、后角,低速切削。
#p#分页标题#e#第四步:检测,检测孔的尺寸精度、形位精度是否合格。
如不合格,则重复上述过程,直至符合图纸规定的技术要求为止。
在钻孔过程中要按照先基准后一般、先高精度后一般的原则,即优先加工或保证基准位置上的孔,或尺寸精度、形位精度要求相对较高的孔。
如何有效地避免和消除孔的位置超差现象,是控制钻孔时孔的质量关键,但是由于影响因素较多,所以需要反复的强化训练,以达到完全控制孔的位置精度的目的。
这是一个循序渐进、精度逐步提高的漫长的过程。
钻孔的位置精度的控制,实质上是钻削过程中钻头与工件的相互正确位置控制过程。
为了考核操作者的操作技能,要求钻孔时孔的位置调整只能是手工、动态控制过程,不允许使用钻模以及其他夹具,因此孔的位置精度受到划线、机床精度、工件和钻头的装夹、钻头刃磨质量、工件位置及机床切削用量的调整等一些不确定因素的影响,再加上要有一定的加工技巧和必要的保证措施,所以,当孔的位置精度要求较高时,就会导致出现严重超差现象。
如何有效地避免和消除孔的位置超差现象,是控制钻孔时孔的质量关键。
在钻孔操作时,除了划线正确之外,钻正底孔、及时准确纠偏、修锉底孔的位置,是保证孔的位置精度的基础。
1、划线由于开始钻孔时的位置精度基本上取决于样冲眼的位置,这样就把动态控制孔的位置精度在一定程度上转化为样冲眼位置的冲制精度上来。
考虑到打样冲眼在控制孔的位置精度时所起的重要的作用,所以,在具体操作时应注意:①选取刀头锋利的高度尺,以便在加工表面上划出孔中心线的沟痕较深,利用样冲移动时孔中心线沟痕对它的阻力作用,来确定样冲眼打制的正确位置。
②为了减少目测孔中心与理想位置的尺寸偏差,应划出各尺寸孔的控制圆或控制方框(由于划线精度的原因,建议采用划控制方框的方法),并在钻削过程中目测的同时,利用卡尺测量的方法,保证其位置精度。
③由于把修锉、钻扩底孔进行纠偏方式转移到样冲眼位置偏差的纠正上来,可更有效地减少扩孔纠偏底孔的位置的次数,缩短操作加工时间,所以,打完样冲眼后要仔细检查其位置精度并作必要的纠偏。
2、工件及钻头的装夹由于在钻孔过程中,如只采用目测的方法很难保证其位置精度,必须采用游标卡尺等量具进行测量,为了方便测量,在工件安装时要使工件高出机用虎钳钳口一定尺寸。
钻头的装夹要尽可能短,以提高其刚性和强度,从而更有利于其位置精度的保证。
3、钻底孔底孔的位置正确或者超差较小,可有效地减少扩孔纠偏底孔的位置的次数,缩短操作加工时间,对提高加工精度及加工效率具有特别重要的作用。