机械专业考评检查表
机械检查表
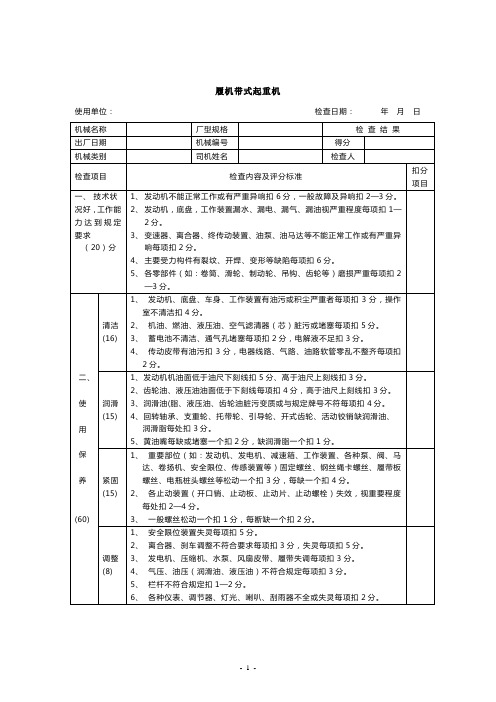
履机带式起重机使用单位:检查日期:年月日说明:本表各项扣分扣至零分为止,不计负分。
汽车式、轮胎式、叉式起重机使用单位:检查日期:年月日说明:本表各项扣分扣至零分为止,不计负分。
塔式、龙门式、门座式、桥式起重机使用单位:检查日期:年月日说明:本表各项扣分扣至零分为止,不计负分。
推土机、装载机、挖掘机、压路机及内燃土方机械使用单位:检查日期:年月日说明:本表各项扣分扣至零分为止,不计负分。
载重汽车、拖拉机、混凝土翻斗车、自卸车、交通车辆、低架平板车及其他特种车使用单位:检查日期:年月日说明:本表各项扣分扣至零分为止,不计负分。
混凝土泵车、混凝土搅拌车使用单位:检查日期:年月日说明:本表各项扣分扣至零分为止,不计负分。
混凝土搅拌楼、混凝土搅拌站使用单位:检查日期:年月日说明:本表各项扣分扣至零分为止,不计负分。
混凝土搅拌机、沙浆搅拌机、麻刀机等混凝土机械设备使用单位:检查日期:年月日说明:本表各项扣分扣至零分为止,不计负分。
钢筋弯曲机、切断机U型卡机等钢筋机械使用单位:检查日期:年月日说明:本表各项扣分扣至零分为止,不计负分。
车床、刨床、铣床、镗床、破口机、剪板机、联合冲剪机、弯管机等金属加工设备使用单位:检查日期:年月日说明:本表各项扣分扣至零分为止,不计负分。
焊接设备使用单位:检查日期:年月日说明:本表各项扣分扣至零分为止,不计负分。
柴油发电机组、空压机、柴油机等动力设备使用单位:检查日期:年月日说明:本表各项扣分扣至零分为止,不计负分。
施工升降机、高空作业吊篮使用单位:检查日期:年月日说明:本表各项扣分扣至零分为止,不计负分。
牵张设备使用单位:检查日期:年月日说明:本表各项扣分扣至零分为止,不计负分。
其它机械使用单位:检查日期:年月日说明:本表各项扣分扣至零分为止,不计负分。
机械考核表

外租机械月度考评表
考核对象: 考评内容
机械性能
2.燃料消耗情况 1.出工是否积极、是否按0 10 10 10 10 20 10 5 10 5 30
机 械 管 理 小 组 审 核 意 见
项 目 管 理 委 员 会 审 批 意 见
注:本表每月20日由项目设备管理小组和现场负责人、工区长等相关人员进行共同考核后报项目管理委员会审批存档。
考核得分
备注
1.根据机械本月度设备自身的完好率和故障率
工作态度
2.是否服从现场技术员的管理 3.是否消极怠工、是否有脱岗窜岗现象 1.是否熟练操作流程
操作员技能
2.是否达到现场施工技术要求 1.能否预防安全隐患,并排除
安全意识
2.机械启动前的检查工作是否到位
考核得分合计 考 核 人 签 认
现场技术员: 工区长: 拌合楼负责人:
起重机械考评检查表No.233

起重机械考评检查表
No.233
序号考评内容考评说明应得分实得分备注
1钢丝绳的断丝数、腐蚀(磨损)
量、变形量、使用长度和固定
状态符合国标规定
除“△”项目外,凡不符合
考评内容任一条款要求
时,该台设备为不合格。
注“△”项目不规范或不够
完善,每台(处)从总
分扣0.5分,最多不超过
总分的20%。
实得分=
0.78×100 —(各台、处
因不规范的扣分之和)
32
△2 滑轮的护罩完好,转动灵活
3吊钩等取物装置无裂纹、明显变形或磨损超标等缺陷,紧固装置完好
4制动器工作可靠,连接件无超标使用,安装与制动力矩符合要求
5
各类行程限位、限量开关与联
锁保护装置完好可靠
6
紧停开关、缓冲器和终端止挡
器等停车保护装置使用有效
△7
各种信号装置与照明设施符合
规定
△8
PE连接可靠,电气设备完好有
效。
机械设计结果检查表(更新)

机械设计结果检查表(更新)机械设计结果检查表一、规划1.是否真的有制作意义,目标是否切实可行2.技术规格(性能、大小、重量等)是否满足要求3.制作费用、制作期限是否合适二、功能1.是否可实现目标所设定的功能2.必要的功能是否都考虑到了3.是否考虑了机械要求的动力源、信息源、信号线和控机器等装配问题三、机构、结构1.机构与结构是否满足功能要求2.是否采用了最合适的机构3.是否采用了最简单的机构和结构4.力的作用线是否形成封闭回路5.平衡性是否良好,结构是否美观6.力线作用回路上,结构尺寸是否与作用力大小成比例7.轴的回转方向以及手柄、衬套的动作及方向是否正确,是否明确做了图示8.空气、油液的流动方向是否正确,是否做了图示标注9.是否考虑了振动的问题(是否避开了共振店,对振动系统相应的部分是否已加以固定)10.对高速回转部分的考虑是否周到全面(因噪声、离心应力、油的搅拌等产生的损耗和发热)11.对于平面度的不良部位的安装,是否讨论采用3点式安装法12.对负荷问题是否不仅从驱动侧方面做了考虑,而且也对零件的重力及惯性力方面的影响做了研究、考虑13.对装配、配管是否采用了合适的固定四、与外部环境的关系1.能否抵抗外部条件的影响2.是否对高温、低温、沙尘、腐蚀性、振动等做了考虑3.是否考虑了伴随温度的变化而产生长度变化和间隙减少4.对大气条件下的滑动部、调整螺旋部等的生锈问题是否有所考虑5.是否有因积水而产生冻结破裂的危险性6.对周围的影响是否允许(振动、噪音、发热)7.是否安置在能够利用的空间之内8.移动及动作时,与周围是否有干涉现象9.所利用的设备(水、空气、电力)是否可及时满足要求10.对安全、防灾等是否做了周密的考虑五、形状1.形状是否满足功能要求2.是否采用了最简单的形状3.其形状是否具有加工的可能性4.其形状是否便于组装及拆卸5.零件的形状、孔形状、凹部形状是否合乎规范6.是否为适应操作的最佳形状六、强度1.是否保证了静力学强度和疲劳强度2.弯曲变形是否没有问题3.带有电动机等强制振动要素的机械,其机械的固有振动频率是否高于强制振动频率4.力线作用回路上,结构尺寸是否与作用力大小成比例七、尺寸1.尺寸有否遗漏2.是否有重复的尺寸3.其尺寸是否可行(要考虑到加工性)4.对倒角C及圆弧过渡R是否做了指定5.是否检查了C、R处的配合零件的相应尺寸6.是否尽可能采用整数尺寸7.配合的指定是否合适8.(与相关零件的)关联尺寸对否合适9.是否已采用制图法对关联零部件的相互关系进行了检查(间隙、关涉、机罩的开闭、检查,加润滑油、调整等)10.是否正确计入了用于固定、搬运时的尺寸11.是否计入了可动部分的行程(动作范围)12.锐角、棱边、形状复杂、厚度变化大的零件,由于淬火等易产生局部应力集中及裂痕,为了防止出现这种现象是否对过渡圆弧的大小做了考虑13.尺寸的计入方法是否合适(考虑累计误差)14.累计尺寸是否无误15.是否标出了整体尺寸16.是否正确表示了占用空间的大小17.是否考虑了公差(尺寸的允许误差)18.是否有不必要过严公差要求(并包含配合公差)19.对表面粗糙度是否做了指定20.表面粗糙度是否合适,是否有要求过严现象21.是否考虑了形位公差(平行度、垂直度、圆柱度等)22.公差是否合乎制作误差及组装误差要求23.是否考虑了加工基准面八、重量1.重量是否满足基本性能要求2.零件的重量是否限制在适合搬运的20kg以下3.20kg以上的零件是否配置了吊装结构九、材料1.机械性质(拉伸强度、刚性、硬度、比重)是否合适2.温度变化时,是否也能充分满足强度要求3.是否不至于因温度变化而产生热膨胀4.加工性能(切削性、焊接性、延伸性)是否没问题5.对有导电性、导热性要求的场合,是否给予了考虑6.有否足够的耐腐蚀性,不够时,是否指定了表面处理7.对钢铁材料是否考虑了热处理问题8.是否考虑了尽可能从库存品种选择材料9.没有库存品的场合,所选择的材料是否能采购到10.是否无意中指定了特殊材料(高价、无库存、加工性差)十、加工方法(一)钣金、焊接1.是否可以弯曲2.能否焊接3.焊接指定有否遗漏4.焊缝处是否对联结螺母等有干涉现象5.是否考虑了焊接变形6.是否考虑了钣金公差7.是否考虑了防止应力集中问题8.是否没超出钢板的规格范围9.是否考虑了钢板厚度的统一性,以及使用扁钢及型钢(二)切削加工1.机械加工是否可能2.是否考虑了用什么样的机械加工问题(用现有设备加工是否可能)(是否有未经验过的机械加工之处)3.是否考虑了刀具的形状及尺寸4.是否考虑了在凹处设置圆弧R的问题5.是否在凸处要设置倒角C6.精加工符号是否合适,记入有否遗漏7.精加工要求是否过于严格8.尺寸公差能否降低9.形位公差能否降低10.对滑动面、油密封及垫圈等部位是否采用了合适的表面粗糙度11.是否考虑了加工顺序12.加工是否可从同一方向进行13.尺寸的指示方法从加工方法、加工顺序的角度看是否合适14.有否夹紧余量15.是否考虑了加工基准面的问题(三)热处理1.材质是否合适2.对淬火的深度、硬度等是否做了指示3.是否指定了淬火范围(四)表面处理1.是否有必要进行电镀或涂漆2.对电镀,涂漆部位的指定是否合适3.是否注意到了生锈的问题4.采取了那些防锈措施十一、装配、拆卸1.是否能组装2.是否留有工具作业空间3.是否考虑工具作业范围4.拆卸是否可能(对静配合部分是否能拆卸)5.拆卸时,必须要更换的部件是否做了考虑6.油密封、防尘密封、O型圈等在组装与拆卸时,是否不至于损伤7.是否能从部件单元进行组装拆卸(对部件更换时的作业顺序、拆卸余量、拆卸空间是否做了考虑)8.是否考虑了组装调整的问题9.是否妥善处理了由于加工、组装等造成的累计误差问题10.是否可按零件号码的顺序进行组装11.是否能减少维修保养时的工具种类12.对维修作业上必要的仪器能否连接得上13.是否已用图示法对维修作业时的人体动作姿势进行了确认检查14.维修性是否良好十二、检查1.对指定的精度能否进行检查确认2.是否研究了使用什么样的检查器具的问题十三、搬运、安装1.是否考虑了放置场所2.是否考虑了怎样搬运3.是否考虑了门的宽度、通道、吊车、天棚的高度以及可用手拿起的重量等问题4.是否考虑了拆卸输送的场合下,对所有零件的搬运问题5.是否检查了产品和零件的包装及放置形式的问题6.重心的位置是否合适7.是否考虑了现场安装8.地面是否足以承受载荷十四、机械要素1.使用的机械要素是否满足设计性能要求2.是否考虑了机械要素的通用性问题(特别是弹簧、齿轮等)3.对购入零件的库存品有无及交货问题是否做了确认4.没有库存品的场合,实际上是否能够买到十五、电气要素1.电机的动力是否充分2.是否留有配线空间3.是否采取了对噪声、干扰等的处理措施4.接地是否良好十六、操作性1.是否考虑了人的体格和作业空间、移动空间的问题2.是否考虑了最大操作力、最合适操作力的问题3.手柄等的操作方向与人的习惯是否和谐一致4.是否考虑了视觉角度等问题5.对明亮度、温度、音响等方面的舒适性是否做了考虑十七、安全性1.是否考虑了棱角割手以及碰伤、掉落、爆炸、开裂、火灾、人体卷入等问题2.是否考虑了避免操作员与高温部接触的危险性,以及具备了紧急脱离性能、升降性和安全闸等措施3.是否存在由于燃料配管及油压配管的松动、损伤而产生的泄露,或者由于电线短路而发生火灾的危险性4.有否安装作业时的照明装置5.带轮、传动带等可动部件是否设置了防护罩6.为了防止组装差错、调整差错、操作失误等问题是否设定了相应的防止措施7.是否设置了误操作、不良情况发生时,机械可自动停止于安全部位的自我保险装置8.绝缘零部件是否绝缘可靠9.非绝缘零部件(需要导电)是否导电良好十八、制图法(一)投影法1.投影法:第一视角法2.视图安排的位置是否容易看清楚3.视图的表示是否正确(尽可能按可视部位方向描绘)4.视图的粗细线是否正确,粗细线是否可以区别5.对实线、虚线、点划线是否区别画出6.向视图的指示是否妥当7.剖视图的位置和方向是否妥当8.剖视图的表示方法是否妥当(尽可能采用全剖视)9.是否使用了国标规定的文字、数字10.尺寸的比例是否采用了标准规定的比例11.不易看清楚的部位是否画了详细的放大图(二)标题栏1.是否标记出第一视角2.比例是否无误3.是否有设计者、制图者的签字,联系地址明确记载了吗4.是否写入了实验名及装置名5.零件的名称是否贴切并已记入6.是否已记入零件号,图号7.是否已记入材质、热处理及其他特殊事项及重量8.是否指定了一般加工误差。
机械制造企业安全质量标准化考评检查表(1)

机械制造企业安全质量标准化考评检查表一、基础管理考评检查表安全生产责任制考评检查表职业安全健康规章制度考评检查表规划与年度计划考评检查表机构与人员考评检查表职业安全健康教育考评检查表事故管理考评检查表“三同时”管理考评检查表班组安全管理考评检查表序号考评内容考评说明应得分实得分备注1建立健全了岗位安全操作规程应有班长、安全员、生产工人安全职责文本,少一种扣8分;一人不熟悉职责扣8分;一人不执行扣12分。
242安全技术操作规程有所有工种的安全技术操作规程文本,少一种扣10分,有一人不熟悉扣10分,发现一人违章不得评为合格班组。
223安全检查与隐患整改有每周一次的检查与整改记录,少一次扣5分;发现一项隐患未整改扣10分;应报上级整改的隐患未上报且没有临时安全措施,每一项扣15分。
244安全活动每月两次安全活动,少一次安全活动扣10分。
15安全5安全教育三级安全教育少一人扣全分,变换工种教育少一人扣2分,复工教育少一人扣2分。
15合计100注:累计少于80分为不合格班组,发生轻伤以上事故扣全分。
计分方法:实得分=安全操作规程考评检查表序号考评内容考评说明应得分实得分备注1建立健全了岗位安全操作规程1.查岗位安全操作规程,无遗漏岗位,每缺少一种扣0.5分。
2.岗位安全操作规程符合安全技术标准,一项不合格扣0.2分。
62严格执行岗位安全操作规程现场抽查岗位安全操作规程的执行情况,出现一人次违章行为扣0.5分。
7合计13特种设备及人员安全管理考评检查表相关方安全管理考评检查表现场监督检查考评检查表2序号考评内容考评说明应得分实得分备注1现场操作依据安全操作规程和操作现场违章表现范围中第三方面的内容,现场抽查,一处不合格扣3分。
32现场作业依据安全生产规章制度和操作现场违章表现范围中第二方面的内容,现场抽查,一处不合格扣2分。
23防护用品穿戴依据操作现场违章表现范围中第一方面的内容,现场抽查,一处不合格扣0.3分。
机械制造企业安全质量标准化考评检查表(全)
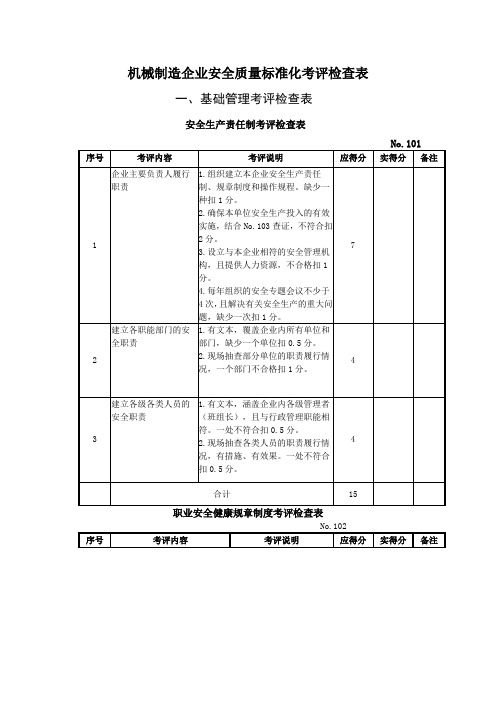
机械制造企业安全质量标准化考评检查表一、基础管理考评检查表安全生产责任制考评检查表No.102No.103No.104No.105No.106No.107班组安全管理考评检查表 No.108计分方法:实得分=安全操作规程考评检查表No.110相关方安全管理考评检查表No.111现场监督检查考评检查表No.112No.113No.115二、设备设施安全考评检查表工业气瓶考评检查表No.202No.203No.204No.205①连接部位无裂纹、变形、过热泄漏等缺陷; 任意一条不合格,则判该台为不合格。
实得分=×0.5×100 在检验周期内使③爆破片的工作压力、温度与工作参数相符,④液位计指示准确、有最高、最低液位标记,沉降、疏水器、排污(水)阀及其管道无泄漏,布局No.209空压机考评检查表No.211No.213No.214锻造机械考评检查表No.216No.217No.218No.219-1No.219-2No.219-3No.220No.221No.222No.224-1防雷接地装置考评检查表No.228No.229No.230No.231探伤设备(磁粉探伤)考评检查表No.232-1No.232-2No.232-3No.232-4No.233No.235No.237No.238电梯考评检查表No.240No.242三、作业环境与职业健康考评检查表厂区环境考评检查表No.301No.304No.305。
机械制造企业安全质量标准化考评检查表

机械制造企业安全质量标准化考评检查表一、基础管理考评检查表安全生产责任制考评检查表No.101职业安全健康规章制度考评检查表No.102No.103No.104职业安全健康教育考评检查表No.105事故管理考评检查表No.106No.107No.108计分方法:实得分=安全操作规程考评检查表No.109特种设备及人员安全管理考评检查表No.110相关方安全管理考评检查表No.111现场监督检查考评检查表No.112的内容,现场抽查,一处不合格应急救援预案考评检查表No.113危险源管理考评检查表No.114安全健康档案考评检查表No.115二、设备设施安全考评检查表工业气瓶考评检查表No.201No.202油库、油罐考评检查表No.203液化气站考评检查表No.204No.205No.206No.207No.2080.6×100锅炉与辅机考评检查表No.209No.210工业管道考评检查表No.211No.212工厂建筑考评检查表No.213涂装作业场所考评检查表No.214No.215铸造机械考评检查表No.216No.217酸碱油槽考评检查表No.218工业梯台(直梯)考评检查表No.219-1实得分=工业梯台(斜梯)考评检查表工业梯台(活动轻金属梯)考评检查表No.219-3工业梯台(轮式移动平台)考评检查表No.219-4工业梯台(走台、平台)考评检查表No.219-5工业炉窑考评检查表No.220厂内机动车辆考评检查表No.221运输(输送)机械考评检查表No.222变配电系统考评检查表低压电气线路(固定线路)考评检查表No.224-1得分=低压电气线路(临时线路)考评检查表No.224-2得分=动力(照明)配电箱(柜、板)考评检查表No.225电网接地系统考评检查表No.226防雷接地装置考评检查表No.227实得分=12-独立避雷针系统与其它系统隔离,间距合格电焊机考评检查表No.228手持电动工具考评检查表No.229移动电气装备考评检查表No.230电气试验站(台、室)考评检查表No.231探伤设备(磁粉探伤)考评检查表No.232-1实得分=探伤设备(射线探伤)考评检查表No.232-2实得分=探伤设备(着色探伤)考评检查表No.232-3探伤设备(超声波探伤)考评检查表No.232-4实得分=起重机械考评检查表No.233No.234No.235木工机械考评检查表No.2360.3分,最多不超过总分的砂轮机考评检查表No.237风动工具考评检查表No.238,凡不符合考评内容任一条款要求时,电梯考评检查表No.239注塑机考评检查表No.240%。
起重机械考评检查表

4
9
#
(1)主要受力构件没有严重塑性变形等明显可见的缺陷;
(2)重要金属结构的连接焊缝无明显可见的焊接缺陷,螺栓或铆钉联接不得有松动等明显缺陷。
外观检查。一项不符合扣4分
4
10
#
轨道固定牢固,轨道端部止挡可靠。流动式支腿可靠地固定或支承
4
23
#
(1)门座起重机的象鼻架或臂架顶端、岸桥的梯形架和外臂架顶端应安装红色(航空红色)障碍灯;
(2)门座起重机的象鼻架高端或臂架顶端 、岸桥的梯形架和外臂架顶端应设避雷针;
(3)门座起重机、岸桥、起升高度大于50m的桁架臂式汽车、轮胎起重机和起升高度大于55m的履带起重机,在起重机较高处不受遮挡的地方设置有风速仪(使用单位总调度台有气象预报职能时可不设)
外观检查。查最近的自行检查记录等
5
14
#
液压油箱应有过滤装置。液压管路、接头、阀组等元件不得漏油。液压系统有相对运动部位的软管,应避免相互刮擦
外观检查
2
15
*
(1)制动器的零部件不应有裂纹、过度磨损、塑性变形、缺件等缺陷;
(2)制动器调整适宜,制动平稳可靠
外观检查。查最近的自检查记录等。必要时制试验。每条1.5分
检查开关。有一项不符扣3分
3
18
**
(1)起重机必须设置紧急断电开关。
(2)该开关在紧急情况下应方便切断起重机总电源
检查开关。有一项不符扣3分
3
19
**
起升机构高度限位器有效
查验最近的自行检查记等。必要时操作试验。不符合扣5分
5
20
- 1、下载文档前请自行甄别文档内容的完整性,平台不提供额外的编辑、内容补充、找答案等附加服务。
- 2、"仅部分预览"的文档,不可在线预览部分如存在完整性等问题,可反馈申请退款(可完整预览的文档不适用该条件!)。
- 3、如文档侵犯您的权益,请联系客服反馈,我们会尽快为您处理(人工客服工作时间:9:00-18:30)。
检验
电梯按检查周期由法定检查机构进行了检验。
3
安全装置
限速器、安全钳、缓冲器、限位器、报警装置以及门的安全装置完整,且灵敏可靠。
4
钢丝绳
曳引绳与与补偿绳断丝数、腐蚀磨损量、变形量、使用长度和固定状态符合国家标准规定。
5
轿厢
轿厢结构牢固可靠,轿厢门开启灵敏。
6
电气
电气部分灵敏可靠。
计分方法及结果
合计
2)标有△的条款不规范、不完善时每处从总分扣分。但最多不超过应得分的20%。
不合格台数
3)实得分=5— 24×—————— - (各台处扣分之和)
评价台数
应得分
5
实得分
检查人:检查时间:
电梯考评检查表
单位:
序
号
评价内容
查证要求与方法
编号及检查记录(符合造、维修应由具备资料的单位承担,产品有合格证书、自检报告。
7
旋转部位的楔、销、键
不加罩的楔、销、键不许突出旋转杆平面,有突出部位应≤3mm,距操作者站立地面≥1.8M,以人不能触及为准。
△8
清铁屑用工具
金切机床配有专用接屑钩,夹屑钳、扒屑铲、毛刷等。
9
磨床砂轮机
砂轮外观、内孔、表面安装软垫,摩损极限达到“砂轮机”条款要求,运转无明显跳动,整机无振动。
加工长零件、防护装置
△6
防护栏
跑车等设备两端应设防护栏,且保持完好,固定牢靠。
7
安全装置
安全装置应齐全、完好、可靠
△8
平刨开
口度
平刨台面应平滑、光洁,台面开口度应≤55mm+最大刨削厚度。
评分方法与得分计算
1)本项评分应每台逐条检查,并抽样开机校验,除标有“△”条款外,有一条不符合要求,即判该台设备不合格;标“△”的项号虽有但不完善,每台(处)从总分扣分,最多不超过2分;
计分方法:1)凡不符合评价内容任一条款要求时,该台设备为不合格。
不合格台数
2)实得分=16———————××100
评价台数
应得分
16
实得分
检查人:检查时间:
风动工具考评检查表
单位:
序
号
评价内容
查证要求与方法
编号及检查记录(符合√,不符合×)
1
夹紧装置
1)风动砂轮的夹紧装置必须可靠,砂轮不应有松动现象,砂轮挡(紧)板与砂轮之间垫1-2mm厚的软衬垫。
△6
设备电器箱、柜线路接地
不许用设备本身载流导电,电气箱柜门关闭严密,门前0.8M内无杂物无工件,箱内布线整齐合理,编号清晰正确,要清洁干燥无积水、尘、油、杂物备件,防短路过载、失压、空压、自锁上锁、过流及信号齐全完好有效,各元件合格,各开关手柄、指示灯、仪表、按钮完好齐全对应,箱柜门上有电器应接地,各线路无老化、破损,无脱落。
△2
操作平台
操作平台结构合理,不得有严重脱焊、变形、腐蚀和断开、裂纹等缺陷。
3
电气
电器箱、柜与线路符合要求,控制台各参数显示完好,功能指标清楚,按急动灵敏可靠。
4
控制系统
液压管路连接可靠,油箱及管路无漏油,控制系统开关齐全,动作可靠。
△5
模具
模具各紧固螺栓齐全,无松动、变形、裂纹。
6
自动进料
自动取料装置标识清楚、动作灵敏,所控制的工伤部件动作准确,机械手的活动区域应有护栏。
3)凡需设有联锁装置的操作门(窗、栏、杆)的联锁装置和需限制运动件范围的行程限位均应固定且灵敏可靠;
4)紧急停车装置可靠且与其它开关明显区别。
△3
局部照明
电压为安全电压,电源线不许接一根相线后利用床身载流导电。
△4
PE线
PE线可靠,有足够强度。
△5
梯台
符合“登高梯台”项目相关条款的要求。
计分
方法
及结
2)实得分=10-不合格率×0.54×100-(各台各项扣分总和)
应得分
10
实得分
检查人:检查时间:
其它机械考评检查表
单位:
序号
评价内容
查证要求与方法
设备编号及检查记录(符合√不符合×)
△1
防护罩、盖、栏
防护罩、盖、栏等应齐全、完好、可靠.。
2
安全装置
1)警示信号与其它信号有明显差别;
2)有惯性冲撞的运动部件,采取可靠的缓冲措施;
1)PE线有足够的强度和截面、固定牢靠,有每年一次的检测记录;
2)负荷匹配线路规范;
7
安全防护装置
安全防护装置完好、可靠(人手不进入危险区的可不装),装有灵敏可靠的安全控制装置,以保证人体误入危险区时能立即停机;剪切厚度>6.3mm的剪切机压料防护装置,必须可以调整,底面与工作台间隙应不大于钢板厚度+8mm。
计分方法及结果
合计
8
计分方法:1)单机评价累计得分<6分者为不合格。
不合格台数
2)实得分=8———————××100
评价台数
应得分
8
实得分
检查人:检查时间:
注塑机考评检查表
单位:
序
号
评价内容
查证要求与方法
编号及检查记录(符合√,不符合×)
1
罩、盖、栏
防护罩、盖、栏的安装应牢固,无明显的锈蚀或变形,且与电气联锁。
设备编号及记录(符合√不符合×不规范)
△1
防护罩、盖、栏
防护罩、盖、栏等应齐全、完好、可靠,无损坏、无松动,栏、梯台应符合GB4053-83标准
2
防止夹、卡具松脱装置
连接完好,易松脱位置应有防松脱措施,锁紧手柄齐全有效,夹卡刀具螺钉齐全,无滑扣、拧不紧现象。
3
限位、联锁、手柄
各种手柄、按钮、制动、保险、联锁、限位等装置应齐全完好,灵敏可靠,标志正确清晰,运动行程在规定范围内应互不干扰,快速手轮在自动进给时及时脱开,卡爪灵活。
△4
设备PE线
机床PE线不许搭接或串接,接线规范可靠,不涂漆,不加绝缘垫。明设的沿床身,不许用铝芯线;暗设的应有接地标志,可用>4mm2铝线。
△5
设备照明
采用36V或24V安全电压,变压器外壳PE可靠,次级线不接零,行灯应用胶皮耐油缆线,无老化,无接头,无破损,无扭结。220V照明高度应≥1.8M,线路可靠,灯泡上有灯罩。
单位:
序
号
评价
内容
查证要求与方法
编号及评价结果(是√、否×)
1
限位及联锁装置
1)限位装置齐全完好,灵敏可靠,能切实起到限位保安作用;
2)吊截、横截锯锯片移动距离限制在锯割木料宽度内。
△2
防护装置
各旋转部位的防护装置应齐全完好,作用可靠。
3
夹紧和锁紧装置
1)夹紧装置完好,装夹方便,作用可靠,运行中不得有松脱现象;
2)装夹的砂轮无裂纹,缺损,受潮。
3)砂轮的装夹牢靠,无松动,压紧螺母或螺栓无滑扣,有防松措施。
2
防护罩
1)防护罩应安装牢固无损坏,其厚度应能挡住砂轮破碎时飞出的碎片。
2)防护罩与砂轮的间隙应适中,不与转动件相摩擦。
△3
气阀、开关
1)气阀(开关)应密封良好,关闭后不漏风。
2)开关应转动(调节)灵活,控制准确。
8
压料脚
平整,有飞溅伤人可能区域装防护挡板或网。
评分方法与结果
1)本项评分应每台逐条检查,除标有“△”条款外,有一条不符合要求,即判整机不合格;标“△”的条款具备但不规范,每台(处)从总分扣分,最多不超过分;
2)实得分=26-不合格率×0.64×100-(各台处因不规范的扣分总和)
应
得
分
26
实
得
分
检查人:检查时间:
PE连接可靠,电源引线应穿管敷设,受条件限制,若采用橡胶电缆线时应沿墙壁面敷设,线路不允许有接头、破损、老化或过载。
4
控制开关
1)开关应单机单设;
2)设备上有尘、水进入可能的,按钮开关应有防护装置,且不妨碍操作。
5
防护
凡有碾、绞、压、挤、切伤可能的部位均应有可靠防护。
评分方法与结果
计分方法:1)除标有△的条款外,其余任一条款不符合要求,则该台为不合格;
1.除△号项外,凡不符合评价内容条款任一要求时,该台设备为不合格。
2.注△项目设置时,单台不合格,但不规范、不完善时每台(处)从总分扣分,最多不超过总分的30%。
3.计分公式:实得分=26—54×不合格台数÷评价台数-(各台各处扣分总和)
总台数
合格数
应得分
实得分
26
检查人:检查时间:
木工机械考评检查表
4
工作部件及防松脱锁卡
1)各工作部件应完好无损,且与工具相匹配,砂轮应无破损、受潮湿、受冻和裂纹;钻头无裂损现象;主轴无明显变形,各连接、紧固件齐全有效。
2)砂轮防护罩卡子,风铲定位销等防松脱的装置完好有效。
△5
气路、气管
1)气管应采用耐压>1Mpa的橡胶管、其长度<12米,无老化、腐蚀现象。
2)气路密封无泄漏。
3
挡屑屏板
1)应完好有足够强度,便于调整,能挡住碎块飞出。
2)挡屑板的宽度应大于防护罩外圆部分宽度,并能随砂轮的磨损而调节与砂轮圆周表面间隙,间隙≤6mm。
4
砂轮
应无裂损、受潮,受冻现象,检查时可用目测或敲击方法检验。
5
托架
1)托架完整无损,调整灵活,固定牢靠,有足够面积和强度。
2)托架与砂轮之间的间隙最大不得超过3mm。
计分方法及结果
计分方法:
1)除“△”项目外,凡不符合考评内容任一条款要求时,该台设备为不合格。
2)注“△”项目不规范或不够完善,每台(处)从总分扣分,最多不超过总分的20%。