A catastrophic aluminium-alloy dust explosion
ASTM有色金属标准.B94
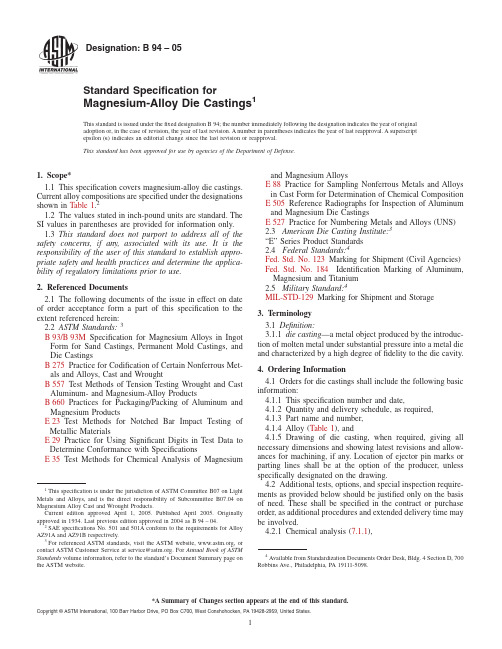
3 For referenced ASTM standards, visit the ASTM website, , or contact ASTM Customer Service at service@. For Annual Book of ASTM Standards volume information, refer to the standard’s Document Summary page on the ASTM website.
4 Available from Standardization Documents Order Desk, Bldg. 4 Section D, 700 Robbins Ave., Philadelphia, PA 19111-5098.
*A Summary of Changes section appears at the end of this standard.
2.2 ASTM Standards: 3 B 93/B 93M Specification for Magnesium Alloys in Ingot
冶金词汇英语翻译
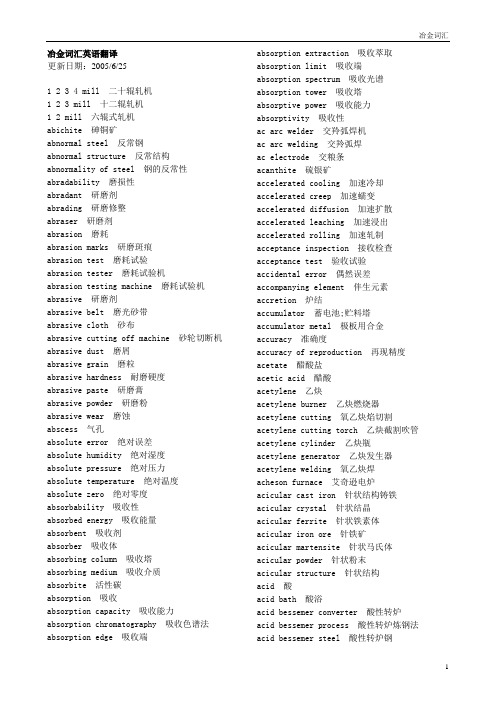
冶金词汇冶金词汇英语翻译更新日期:2005/6/251 2 3 4 mill 二十辊轧机1 2 3 mill 十二辊轧机1 2 mill 六辊式轧机abichite 砷铜矿abnormal steel 反常钢abnormal structure 反常结构abnormality of steel 钢的反常性abradability 磨损性abradant 研磨剂abrading 研磨修整abraser 研磨剂abrasion 磨耗abrasion marks 研磨斑痕abrasion test 磨耗试验abrasion tester 磨耗试验机abrasion testing machine 磨耗试验机abrasive 研磨剂abrasive belt 磨光砂带abrasive cloth 砂布abrasive cutting off machine 砂轮切断机abrasive dust 磨屑abrasive grain 磨粒abrasive hardness 耐磨硬度abrasive paste 研磨膏abrasive powder 研磨粉abrasive wear 磨蚀abscess 气孔absolute error 绝对误差absolute humidity 绝对湿度absolute pressure 绝对压力absolute temperature 绝对温度absolute zero 绝对零度absorbability 吸收性absorbed energy 吸收能量absorbent 吸收剂absorber 吸收体absorbing column 吸收塔absorbing medium 吸收介质absorbite 活性碳absorption 吸收absorption capacity 吸收能力absorption chromatography 吸收色谱法absorption edge 吸收端absorption extraction 吸收萃取absorption limit 吸收端absorption spectrum 吸收光谱absorption tower 吸收塔absorptive power 吸收能力absorptivity 吸收性ac arc welder 交羚弧焊机ac arc welding 交羚弧焊ac electrode 交粮条acanthite 硫银矿accelerated cooling 加速冷却accelerated creep 加速蠕变accelerated diffusion 加速扩散accelerated leaching 加速浸出accelerated rolling 加速轧制acceptance inspection 接收检查acceptance test 验收试验accidental error 偶然误差accompanying element 伴生元素accretion 炉结accumulator 蓄电池;贮料塔accumulator metal 极板用合金accuracy 准确度accuracy of reproduction 再现精度acetate 醋酸盐acetic acid 醋酸acetylene 乙炔acetylene burner 乙炔燃烧器acetylene cutting 氧乙炔焰切割acetylene cutting torch 乙炔截割吹管acetylene cylinder 乙炔瓶acetylene generator 乙炔发生器acetylene welding 氧乙炔焊acheson furnace 艾奇逊电炉acicular cast iron 针状结构铸铁acicular crystal 针状结晶acicular ferrite 针状铁素体acicular iron ore 针铁矿acicular martensite 针状马氏体acicular powder 针状粉末acicular structure 针状结构acid 酸acid bath 酸浴acid bessemer converter 酸性转炉acid bessemer process 酸性转炉炼钢法acid bessemer steel 酸性转炉钢冶金词汇acid bottom 酸性炉底acid brick 酸性砖acid brittleness 酸洗脆性acid bronze 耐酸青铜acid corrosion 酸腐蚀acid electric furnace 酸性电炉acid electrolyte 酸性电解液acid embrittlement 酸洗脆性acid extraction 酸性萃取acid furnace 酸性炉acid hearth 酸性炉底acid leaching 酸性浸出acid lined furnace 酸性炉acid lining 酸性内衬acid medium 酸性介质acid open hearth furnace 酸性平炉acid open hearth process 酸性平炉法acid open hearth steel 酸性平炉钢acid oxide 酸性氧化物acid process 酸性法acid pump 酸泵acid refractory 酸性耐火材料acid resistance 耐酸性acid resistant steel 耐酸钢acid resisting cast iron 耐酸铸铁acid resisting casting 耐酸铸件acid resisting steel 耐酸钢acid slag 酸性渣acid solution 酸性溶液acid steel 酸性钢acid tank 酸性槽acidity 酸度acidproof alloy 耐酸合金acidproof brick 耐酸砖acidproof cast iron 耐酸铸铁acidproof casting 耐酸铸件acidulated bath 酸性化槽acierage 表面钢化acoustic absorbing material 吸音材料acoustic diagnosis 音响诊断acoustic emission 声发射acoustic fatigue 声波振动疲劳acoustic inspection 音响检查actinium 锕actinouranium 锕铀activated alumina 活性氧化铝activated carbon 活性碳activated chlorine 活性氯activated sintering 活化烧结activation 活化activation analysis 活化分析activation energy 活化能activation volume 活化容积activator 活化剂active material 放射性物质active mixer 预炼混铁炉active power 有效功率active solvent 活性溶剂active surface 活性表面activity 活度activity coefficient 活度系数activity factor 活度系数activity probe 活度探示器actual load 有效负载actual solution 实际溶液actual stress 实际应力actual throat 实际角焊缝厚度adamite 水砷锌矿adamite roll 阿达迈特高碳铬镍耐磨铸铁轧辊adaptive mill control 轧机自适应控制addition 添加addition agent 添加剂addition compound 加成化合物addition element 加合金元素addition reaction 加成反应additive 添加剂additive deformation 附加变形additive efficient deformation rate 有效附加变形率additive property 加和性additivity rule 加成定则adherence 附着adherent slag 附着渣adhesion 附着adhesion force 附着力adhesion heat 粘附热adhesion test 附着力试验adhesive capacity 粘着能力adhesive force 附着力adiabatic calorimeter 绝热量热器adiabatic compression 绝热压缩adiabatic demagnetization 断热去磁冶金词汇adiabatic equilibrium 绝热平衡adiabatic exponent 绝热指数adiabatic process 绝热过程adjustable end stop 升降挡板adjustable mold 可担adjusting 蝶adjusting screw 第螺钉adjustment 蝶admiralty brass 海军黄铜admiralty gun metal 海军炮铜admissible concentration 容许浓度admissible error 容许误差admissible stress 容许应力admixture heat 混合热adobe 风干砖adsorbability 可吸附性adsorbate 吸附物adsorbent 吸附剂adsorbing power 吸附能力adsorption 吸附adsorption chromatography 吸附色层法adsorption isotherm 吸附等温线adsorption overvoltage 吸附过电压adsorption surface area 吸附表面积adular 冰长石advance 艾德万斯康铜aeration 充气aeration corrosion 充气腐蚀aeration tank 充气槽aerosol 气溶胶aerospace material 宇航材料aerospace structural metal 宇航结构金属affinage 精炼affinity 亲和力afterblow 后吹aftercontraction 附加收缩aftercooler 后冷却器aftereffect 后效afterflow 残余塑性变形aftertreatment 后处理agate 玛瑙agc 自动厚度控制age hardening 时效硬化age hardening alloy 时效硬化合金aged steel 时效钢agent 试剂agglomerant 粘结剂agglomerate 烧结矿agglomerated cake 烧结块agglomerated charge 烧结料agglomerating machine 烧结机agglomerating plant 烧结装置agglomeration 烧结agglomeration roasting 烧结焙烧agglutination 凝集aggregate 集合体aggregation 聚集aggression 侵蚀aggressiveness 侵蚀性aging 时效aging crack 时效裂纹aging oven 时效炉aging resistance 抗时效性aging stability 时效稳定性aging steel 时效钢agitating vane 搅拌叶片agitation 搅拌agitation leach 搅拌浸出agitator 搅拌机agitator tank 搅拌槽air acetylene welding 空气乙炔焊接air arc cutting 电弧气割air bath 空气浴air blast quenching 气零火air blast temperature 鼓风温度air box 风箱air brick 不烧砖air bubble 空气泡air chamber 空气室air classification 风选air cleaner 空气净化器air compressor 空气压缩机air conditioning 空气第air conduit 空气导管air conveying 气龄送air cooled condenser 空气冷凝器air cooler 空气冷却器air cooling 空气冷却air damper 风挡air distillation 常压蒸馏air exhauster 排气机air filter 空气过滤器冶金词汇air fuel mixture 空气燃料混合物air furnace 反射炉air gate 出气口air hammer 空气锤air hardening 空气淬火air hardening steel 空气硬化钢air hose 通风软管air inlet 进气口air jacket 空气套air manometer 空气压力计air mortar 气硬砂浆air oxidation 空气氧化air patenting 空气铅淬火air permeability 透气性air pipe 风管air port 空气喷口air preheater 空气预热器air pressure 空气压力air pump 空气泵;活塞泵air purification 空气净化air quenching 空气淬火air rammer 风动掉棒air regenerator 空气蓄热室air reservoir 储气罐air separation 气力分离air separator 气力分离器air test 气密试验air uptake 空气上升道air valve 空气阀airbond 自硬粘结剂airing 空气干燥;通风airtight joint 气密接头aisle 工段ajax northrup furnace 阿杰克斯诺斯拉普炉albion metal 阿尔比饵锡铅箔albite 钠长石albronze 铝青铜alchemy 炼金术alclad 阿尔克拉德包铝硬铝板;高强度铝合金alcohol 醇aldrey 阿尔德雷导线用铝合金alfenide 阿里费尼德锌白铜aligned composite material 取向复合材料aligned eutectic 取向共晶aligned structure 取向结构alignment 定心aliquation 偏析;层化alitizing 渗铝alkali 碱alkali battery 碱性蓄电池alkali metal 碱金属alkali reaction 碱性反应alkali resistance 耐碱性alkali salt 碱金属盐alkali solution 碱性液alkaline bath 碱浴alkaline earth metal 碱土金属alkaline electrolyte 碱性电解液alkaline fusion 碱熔alkaline leaching 碱性浸出alkalinity 碱度allemontite 砷锑矿alligator effect 鳄皮效应alligator shears 杠杆式剪断机alligatoring 鳄嘴裂口allomerism 异质同晶allomorphism 同质异晶allomorphy 同质异晶allopalladium 硒钯矿allotropic modification 同素变态allotropic transformation 同素异形变态allotropy 同素异形体allowable error 容许误差allowable load 容许负荷allowable pressure 容许压力allowable stress 容许应力allowable variation 容许偏差alloy 合金alloy addition 合金添加alloy hardening 合金硬化alloy pig iron 合金生铁alloy plating 合金镀覆alloy steel 合金钢alloy steel castings 合金钢铸件alloy system 合金系alloy tool steel 合金工具钢alloyage 合金化alloyed iron 合金铸铁alloyed scrap 合金废料alloying 合金化alloying constituent 合金成分alloying element 合金元素冶金词汇alloying metal 合金金属alloying power 合金化能力alluvial gold 砂金alni 阿尔尼alnico 阿尔尼科合金alpaca 阿尔帕克锌白铜alpakka 阿尔帕克锌白铜alpax 阿尔帕克斯铝硅合金alpha brass 黄铜alpha bronze 青铜alpha decay 衰变alpha disintegration 衰变alpha iron 铁alpha particle 粒子alpha rays 射线alpha region 相区域alpha solid solution 固溶体alphatizing 气化渗铬法alsifer 阿尔违尔硅铝铁合金altaite 碲铅矿alternate lay wire rope 混合捻钢丝绳alternate steel 代用钢alternate stress 交变应力alternating bending test 反复弯曲试验alternating current arc welder 交羚弧焊机alternating current arc welding 交羚弧焊alternating current arc welding machine 交羚弧焊机alternating load 应变载荷alternating stress amplitude 交变应力振幅aludel 梨坛aludur 阿鲁杜合金alum 茂alumel 阿卢梅镍铝合金alumina 氧化铝alumina brick 高铝砖aluminate 铝酸盐aluminate inclusion 铝酸盐夹杂物aluminic acid 铝酸aluminium castings 铝铸件aluminized coat 铝镀覆层aluminized screen 铝化荧光屏aluminizing 渗铝aluminosilicate 铝硅酸盐aluminosilicate refractory 硅酸铝耐火材料aluminothermic process 铝热法aluminothermic reduction 铝热还原aluminothermic welding 铝热焊aluminothermics 铝热法aluminothermy 铝热法aluminum 铝aluminum alloy 铝合金aluminum base alloy 铝基合金aluminum brass 铝黄铜aluminum bronze 铝青铜aluminum chloride 氯化铝aluminum copper alloy 铝铜合金aluminum fluoride 氟化铝aluminum foil 铝箔aluminum hydroxide 氢氧化铝aluminum iron alloy 铝铁合金aluminum leaf 铝箔aluminum magnesium alloy 铝镁合金aluminum nickel alloy 铝镍合金aluminum nitrate 硝酸铝aluminum nitride 氮化铝aluminum ore 铝矿aluminum oxide 氧化铝aluminum plating 镀铝aluminum powder 铝粉aluminum silicate 硅酸铝aluminum silicon alloy 铝硅合金aluminum solder 铝焊料aluminum wire 铝线alundum 人造刚玉alunite 茂石alunogen 毛矾石amalgam 汞齐amalgam process 混汞法amalgam test 汞齐试验amalgamated metal 混汞金属amalgamating bath 混汞化槽amalgamation 混汞amalgamator 混汞器ambient air 周围空气ambient temperature 周围温度amblygonite 磷铝石americium 镅amianthus 白丝状石棉ammonia 氨ammonia alum 铵铝矾ammonia leaching 氨浸出冶金词汇ammonia nitriding 氨氮化ammonia water 氨水ammonium 铵ammonium alum 铵铝矾ammonium chloride 氯化铵ammonium fluoride 氟化铵ammonium molybdate 钼酸铵ammonium nitrate 硝酸铵ammonium oxalate 草酸铵ammonium phosphate 磷酸铵ammonium sulfate 硫酸铵amorphism 非晶性amorphous alloy 非晶质合金amorphous body 非晶体amorphous carbon 无定形碳amorphous film 非晶体膜amorphous metal 非晶体金属amorphous phase 非晶形相amorphous state 非晶质状态amorphous substance 无定形物质amount of contraction 收缩量amount of shrinkage 收缩量ampangabeite 铌钛铁铀矿amperometric titration 电廖定amperometry 电廖定amphion 两性离子ampholyte 两性电解质amphoteric compound 两性化合物amphoteric electrolyte 两性电解质amphoteric element 两性元素amphoteric ion 两性离子amphoteric oxide 两性氧化物amphoterism 两性amplitude 振幅amplitude of oscillation 振荡振幅anaconda process 安那康达法analog computer 模拟计算机analysis 分析analytical balance 分析天平analytical chemistry 分析化学analytical sample 分析试样analyzer 分析器anatase 锐钛矿anatomical alloy 骨科用易熔合金anelastic behavior 滞弹行为anelasticity 滞弹性angle 角钢angle butt weld 斜口对接焊缝angle of bite 轧入角angle of lag 滞后角angle of lead 超前角angle of neutral plane 中性角angle of nip 咬入角angle of nonslip point 中性角angle of repose 休止角angle of rest 休止角angle pass 角钢孔型angle section 角钢angle steel 角钢anglesite 硫酸铅矿angular carbide 角形碳化物angular powder 角状粉angular velocity 角速度anhydride 酐anhydrite 硬石膏animal charcoal 动物煤anion 阴离子anion catalyst 阴离子催化剂anion exchange 阴离子交换anion exchange resin 阴离子交换尸anion exchanger 阴离子交换剂anionite 阴离子交换剂anionite membrane 阴离子交换膜anisotropic material 蛤异性材料anisotropy 蛤异性annabergite 镍华annealed powder 退火粉annealed steel 退火钢annealing 退火annealing box 退火箱annealing cycle 退火周期annealing furnace 退火炉annealing of defects 缺陷退火annealing oven 退火炉annealing pot 退火箱annealing temperature 退火温度annealing twin 退火孪晶annerodite 铌钇铀矿annular furnace 环式窑annular kiln 环式窑anode 阳极anode alloy 阳极合金冶金词汇anode casting 阳极铸造anode chamber 阳极室anode compartment 阳极室anode copper 阳极铜anode drop 阳极降anode effect 阳极效应anode efficiency 阳极电璃率anode fall 阳极降anode furnace 阳极炉anode mud 阳极泥anode nickel 阳极镍anode pickling 阳极酸洗anode process 阳极法anode rays 阳极射线anode remnants 残阳极anode scrap 残阳极anode slime 阳极泥anode sludge 阳极泥anode voltage 阳极电压anodic brightening 阳极抛光anodic coating 阳极镀层anodic corrosion 阳极腐蚀anodic current 阳极电流anodic current density 阳极电淋度anodic current efficiency 阳极电璃率anodic dissolution 阳极溶解anodic overvoltage 阳极过电压anodic oxidation 阳极氧化anodic polarization 阳极极化anodic process 阳极法anodic protection 阳极保护anodic reaction 阳极反应anodic treatment 阳极处理anodizing 阳极处理anolyte 阳极电解液anomalous slip 反常滑移anorthic system 三斜晶系anorthite 钙长石anorthoclase 钠斜微长石anthracite 无烟煤anthracitic coal 无烟煤anticarburizer 渗碳防止剂anticathode 反阴极anticorodal 耐蚀铝合金anticorrodant 防腐剂anticorrosive agent 防腐剂anticorrosive paint 防腐涂料antiferromagnetism 反铁磁性antifoaming agent 防沫剂antifriction alloy 减磨合金antifriction bearing 抗摩轴承antifriction material 减摩材料antifriction metal 减磨合金antimonate 锑酸盐antimonial lead 锑铅antimonic acid 锑酸antimonic anhydride 锑酸酐antimonide 锑化物antimonite 辉锑矿antimonous acid 亚锑酸antimony 锑antimony bronze 锑青铜antimony glance 辉锑矿antimony sulfide 硫化锑antimony white 锑白antioxidant 反氧化剂antiphase domain 反相畴antiphase domain boundary 反相畴界antipiping compound 冒口保温剂anvil 铁砧anvil block 砧座aod 氩氧脱碳aod converter aod转炉aod process 氩氧脱碳法apatite 磷灰石aperture 口径apochromat 复消色差透镜apochromatic lens 复消色差透镜apparatus 仪器装置apparent density 表观密度apparent modulus of elasticity 表观弹性系数apparent particle density 颗粒表观密度apparent power 表观功率apparent specific gravity 表观比重apparent viscosity 表观粘度apparent volume 表观体积approach angle 拉模变形锥approach table 输入辊道approximate analysis 近似分析apron conveyor 板式运输机apron feeder 裙板加料机aqua regia 王水冶金词汇aquadag 胶体石墨润滑剂aqueous electrolysis 水溶液电解aqueous leach 水溶液浸出aqueous medium 水介质aqueous solution 水溶液aqueous vapour 水蒸汽ar transformation ar 转变arbitrary analysis 仲裁分析arbor 轴arborescent powder 师状粉arborescent structure 枝晶组织arc 弧arc air gouging 电弧空气气削arc blow 电弧磁偏吹arc blowout 熄弧arc brazing 电弧钎焊arc cutting 电弧切割arc discharge 电弧放电arc drop 电弧压降arc force 电弧力arc furnace 电弧炉arc furnace electrode 电弧炉电极arc gouging 电弧刨削arc heating 电弧加热arc image furnace 反射电弧炉arc length 弧长arc spraying 电弧喷镀arc stabilizer 电弧稳定装置arc start 起弧arc strike 起弧arc welding 电弧焊接arc welding alternator 电弧焊用交立电机arc welding electrode 电弧焊条arc welding generator 弧焊发电机arc welding machine 电弧焊接机arc welding set 电弧焊机组arc welding transformer 电焊变压器arch 拱arch brick 拱砖arcogen 气电焊arcos arc process 阿考斯二氧化碳保护弧焊法ardometer 光测高温计area reduction 断面收缩areometer 比重计argental mercury 银汞argentan 锌白铜argentiferous lead 含银铅argentite 辉银矿argentum 银argon 氩argon arc 氩气保护电弧argon arc welding 氩弧焊argon blowing in ladle 桶吹氩argon oxygen decarburization 氩氧脱碳argon oxygen decarburization converter aod转炉argon oxygen decarburization process 氩氧脱碳法argon rinsing treatment 氩清洗处理argon stirring 吹氩搅拌argyrodite 硫银锗矿arizonite 红钛铁矿arm mixer 桨叶式搅拌机armature wire 钢筋线材armco iron 阿姆克铁armor 装甲钢板armor plate 装甲板armor plate mill 装甲板轧机armor steel 装甲钢armored cast iron 钢筋铸铁arrangement 装置;配置array of dislocations 位错排列arrest point 临界点arsenate 砷酸盐arsenic 砷arsenic acid 砷酸arsenic anhydride 砷酸酐arsenic poisoning 砷中毒arsenical copper 砷铜arsenical nickel 红砷镍arsenical pyrite 砷黄铁矿arsenide 砷化物arsenite 亚砷酸盐arsenolite 砷华arsenopyrite 砷黄铁矿arsenous acid 亚砷酸arsenous anhydride 亚砷酸酐art bronze 艺术青铜art castings 艺术铸件artificial aging 人工时效artificial draught 人工通风artificial gas 人造气体冶金词汇as cast condition 铸态as cast metal 铸态金属as cast structure 铸造组织as rolled state 轧制状态asbestos 石棉asbestos packing 石棉垫料asbestos paper 石棉纸asbestos plate 石棉板asbestos wool 石棉绒asbolane 钴土矿asbolite 钴土矿ascending tube 上升管ascension pipe 上升管asea skf process asea skf 法ash cellar 灰坑ash content 含灰量ash cooling 灰中冷却ash pan 灰盘asparagolite 黄绿磷灰石asparagus stone 黄绿磷灰石asperity 不平度aspirator 吸气器assay 试金;试料assay balance 试金天平assay furnace 试金炉assel elongator 阿塞尔三辊式轧管机assel mill 阿塞尔三辊式轧管机assemblage 装配assembling 装配astatine 砹asterism 星芒atacamite 氯铜矿athermal growth 绝热生长athermal nucleation 非热成核athermal solution 非热溶液athermal transformation 非热转变atmophile element 亲气元素atmosphere 大气atmospheric corrosion 大气腐蚀atmospheric pressure 大气压力atmospheric rusting 大气锈蚀atom 原子atom fraction 原子分数atom magnetic moment 原子磁矩atomic absorption spectrometry 原子吸收光谱学atomic arrangement 原子排列atomic binding 原子键atomic bond 原子键atomic crystal 原子结晶atomic diameter 原子直径atomic displacement 原子位移atomic energy 原子能atomic group 原子团atomic heat 原子热atomic heat capacity 原子热容量atomic hydrogen 原子氢atomic lattice 原子晶格atomic mass 原子质量atomic model 原子模型atomic nucleus 原子核atomic number 原子序数atomic oxygen 原子氧atomic percent 原子百分比atomic pile 原子反应堆atomic plane 原子面atomic power 原子力atomic radius 原子半径atomic ratio 原子比atomic reactor 原子反应堆atomic size 原子大小atomic spectrum 原子光谱atomic structure 原子结构atomic volume 原子体积atomic weight 原子量atomic welding 氢原子焊atomization 喷雾atomized powder 喷雾粉atomizer 喷雾器atomizing 喷雾attached test coupon 附铸试棒attack 侵蚀attenuation 衰减attraction 吸引attractive force 引力attrition 磨损attritor grinding 磨碎机粉碎auric chloride 氯化金auric compound 正金化合物auric cyanide 氰化金aurous chloride 氯化亚金aurous compound 亚金化合物冶金词汇aurous cyanide 氰化亚金ausaging 沉淀硬化ausannealing 等温退火ausforming 过冷奥氏体形变热处理ausrolling 过冷奥氏体轧制形变热处理austempering 奥氏体等温淬火austenite 奥氏体austenite former 奥氏体形成元素austenite region 奥氏体区域austenite stabilization 奥氏体稳定化处理austenite structure 奥氏体组织austenitic electrode 奥氏体钢焊条austenitic grain size 奥氏体粒度austenitic iron 奥氏体铸铁austenitic stainless steel 奥氏体不锈钢austenitic steel 奥氏体钢austenitic transformation 奥氏体转变austenitization 奥氏体化austenitizing 奥氏体化austenitizing temperature 奥氏体化温度austenoferritic steel 奥氏体铁素体钢austenomartensitic steel 奥氏体马氏体钢austrian test 焊缝抗弯试验autocatalysis 自动催化酌autoclave 高压釜autoclave leaching 加压浸出autocrucible melting 自成坩埚熔炼autodiffusion 自扩散autodiffusion coefficient 自扩散系数autogenous ignition 自发着火autoignition 自发着火automatic arc welding 自动电弧焊automatic arc welding machine 自动电焊机automatic control 自动控制automatic gage control 自动厚度控制automatic mill 自动轧机automatic size control 自动尺寸控制automatic spot welding 自动点焊automatic steel 易切钢automatic welding 自动焊接automatic welding machine 自动电焊机automobile body sheet 汽车车身钢板automobile steel 汽车钢automolite 铁锌尖晶石autoradiography 自射线照相法autunite 钙铀云毋auxiliaries 辅助设备auxiliary air 二次空气auxiliary anode 辅助阳极auxiliary electrode 辅助电极auxiliary pump 辅助泵average roll pressure 平均轧制压力average sample 平均试样avional 阿维奥纳尔铝合金avogadrite 氟硼砷石avogadro's number 阿弗加德罗数axial force 轴向力axial porosity 轴芯气孔率axial pressure 轴向压力axial ratio 轴比axial slip 轴向滑移axial stress 轴向应力axial vector 轴矢量axis 轴azeotrope 共沸混合物azeotropic distillation 共沸蒸馏azeotropic mixture 共沸混合物azeotropic solution 共沸溶液azeotropy 共沸azimuthal quantum number 方位量子数azotization 氮化azotizing 氮化azurite 蓝铜矿b h curve 磁化曲线babbit 巴比合金back electromotive force 反电动势back extraction 反萃取back lining 安全衬砖层back pressure 反压力back pull 后拉力back pull drawing 后张力拉伸back pull stress 逆应力back reaction 逆反应back reflection method 背反射法back tension 后拉力back tension drawing 后张力拉伸back titration 回滴定back wall 后壁backfin 压折backfire 回火backflash 回火backhand welding 右焊backing 垫板;轴衬backing sand 填充砂backing strip 衬背带材backpad 挤压垫backstep welding 逐步退焊法backstepping 逐步退焊法backup roll 支承辊backup roll bending 支承辊弯曲backup strip 衬背带材backward extrusion 反挤压backward pass 偶数道次backward slip 后滑backward slip zone 后滑区backward welding 右焊bacterial leaching 细菌浸出bacteriosmelt 细菌冶金baddeleyite 斜锆石baffle plate 挡板bag filter 袋滤器bag filtration 袋过滤baghouse 袋滤室bahnmetal 巴鼎基轴承合金bainite 贝氏体bainite quenching 贝氏体淬火bainite range 贝氏体区域bainite structure 贝氏体组织bainite transformation 贝氏体转变bainitic hardening 贝氏体淬火bainitic steel 贝氏体钢baked anode 焙烧阳极baked core 干燥型心baked permeability 干透气性baked strength 干强度baking 烘干;烧成baking coal 炼焦煤balance 天平balanced housing 平衡装置的机架balanced steel 半脱氧钢balancer 平衡装置balancing device 平衡装置balbach thum process 巴尔巴赫卧式电极银电解精炼法bale 打包baled scrap 打包废金属baling press 打包机baling strip 打包带钢baling wire 打包钢丝ball burnishing 钢球抛光ball clay 黏土ball hardness testing machine 布氏硬度计ball mill 球磨机ball milled powder 球磨粉ball rolling mill 钢球轧机baller 切边卷取机balling machine 切边卷取机ballistic galvanometer 冲混疗band 带band arc welding 带极电弧焊band conveyor 带式运输机band electrode 板状电极band filter 带式过滤器band saw 带锯band spectrum 带光谱band theory 能带理论bandage 带banded structure 条状组织bander 打包机banding 铁条打捆banding machine 打包机bank 堤;冷床banking 封炉bar 棒bar brass 黄铜棒bar drawbench 拔棒机bar drawing 长芯棒拔制bar graph 直方图bar mill 小型轧机bar pointer 压尖机bar section 形材bar steel 条钢bar straightener 型钢矫直机bar strip 薄板坯板料barbed wire 刺钢丝barbotage 起泡barbotage leach 鼓泡浸出bare electrode 裸焊条bare wire welding 裸线弧焊barff process 蒸气发蓝处理barffing 蒸气发蓝处理barite 重晶石barium 钡barium carbonate 碳酸钡barium chloride 氯化钡barium chromate 铬酸钡barium hydroxide 氢氧化钡barium oxide 氧化钡barium sulfate 硫酸钡bark 薄脱碳层barkhausen effect 巴克豪生效应barometric pressure 大气压barrel 辊身barrel converter 卧式吹炉barrel diameter 辊身直径barrel mixer 圆筒混合机barrel plating 转筒滚镀barrel roll 桶形辊barrel type roll piercing mill 带桶形轧辊的穿孔机barren solution 贫液barrier 势垒barrier height 势垒高度baryte 重晶石basal plane 基面basal slip 基面滑移basal tuyere 炉底风嘴base 基;碱;基础;炉底;贫矿base metal 基底金属;贱金属base plate 底板basic bessemer conveter 托马斯转炉basic bessemer process 碱性转炉炼钢法basic bessemer slag 碱性转炉炉渣basic bessemer steel 碱性转炉钢basic bottom 碱性炉底basic brick 碱性砖basic carbonate 碱式碳酸盐basic coating 碱性药皮basic covering 碱性药皮basic electrode 碱性被覆焊条basic flux 碱性熔剂basic furnace 碱性炉basic hearth 碱性炉床basic lead carbonate 碱式碳酸铅basic lining 碱性内补basic open hearth furnace 碱性平炉basic open hearth process 碱性平炉炼钢法basic open hearth steel 碱性平炉钢basic oxide 碱性氧化物basic oxygen furnace 碱性氧气转炉basic oxygen furnace slag 氧气转炉渣basic oxygen process 顶吹氧转炉法basic oxygen steel 氧气吹炼钢basic pig iron 托马斯生铁basic process 碱性法basic refractory 碱性耐火材料basic salt 碱式盐basic slag 碱性渣basic steel 碱性钢basicity 碱度basicity of slag 炉渣碱度basket charging 吊篮装料batch 批batch annealing 分批退火batch distillation 分批蒸馏batch furnace 分批装料炉batch method 分批法batch patenting 分批铅处理batch process 分批法batch sintering 间歇烧结batcher 称量配料器bath 浴bath carburizing 液体渗碳bath cooling 浴冷bath furnace 浴炉bath level 熔池水平bath nitriding 液体氮化bath patenting 铅浴淬火bath sample 浴池试样bath voltage 槽电压baumann printing 包曼试验baumann test 包曼试验bauschinger effect 巴斯青格效应bauxite 铝土矿bauxite brick 铝矾土砖bay 跨间bayer process 拜耳法bayleyite 菱镁铀矿beach marks 贝壳状纹理bead 焊蚕bead bend test 焊缝抗弯试验bead forming 卷边bead trimmer 焊瘤除器beading 成球beaker 烧杯beam 梁beam blank 轧制工字梁用的异形坯beam flange 梁的凸缘beam mill 钢梁轧机beam pass 梁孔型bean ore 豆状铁矿bear punch 手动穿孔机bearing 轴承bearing alloy 轴承合金bearing brass 轴承黄铜bearing bronze 轴承青铜bearing bush 轴承瓦bearing cast iron 减摩轴承铸铁bearing metal 轴承合金bearing modulus 轴承模数bearing steel 轴承钢bearing tube 轴承管becking bar 扩孔锻造用心轴beckmann thermometer 贝克曼温度计bed charge 底料bed coke 底焦bed plate 地脚板beehive oven 蜂房式炼焦炉behavior 行为beilby layer 贝尔倍层bell 料钟;罩bell and hopper arrangement 钟斗装料装置bell bronze 钟用青铜bell furnace 罩式炉bell less top 无种炉顶bell less top charger 无钟装料机bell less type system 无钟装料机bell metal 钟用青铜bell type annealing furnace 钟形退火炉bell type top charger 钟罩式装料机bellows 风箱belly 炉腰belly pipe 直吹管belt conveyor 带式运输机belt drive 皮带传动belt drop hammer 皮带式落锤belt feeder 带式给料机belt furnace 带式炉belt transmission 皮带传动bementite 蜡硅锰矿benardos system 贝纳尔德斯法bench 拉伸机;工专bend 弯曲bend over test 弯曲试验bend test 弯曲试验bending 弯曲bending and unbending test 反复弯曲试验bending jaw 弯曲钳口bending load 弯曲负荷bending machine 弯曲机bending moment 弯曲力矩bending press 压弯机bending radius 弯曲半径bending rigidity 抗弯刚度bending roll 弯曲辊bending rolls 弯板机bending strain 弯曲应变bending strength 抗弯强度bending stress 弯曲应力bending test 弯曲试验beneficiated ore 精矿beneficiation 选矿benitoite 蓝锥矿bentonite 膨润土berthierite 辉铁锑矿beryl 绿柱石beryllate&np;铍酸盐beryllia 氧化铍beryllite 水硅铍石beryllium 铍beryllium bronze 铍青铜beryllium chloride 氯化铍beryllium copper 铍铜合金beryllium oxide 氧化铍beryllonite 磷钠铍石berzelianite 硒铜矿bessemer copper 转炉铜bessemer pig iron 酸性转炉生铁bessemer process 酸性转炉炼钢法bessemer steel 酸性转炉钢bessemerizing 贝氏炼钢法best process 锭头电渣补注法beta decay 衰变beta disintegration 衰变beta iron 铁beta region 相区域betafite 钛铌铀矿bethanizing 钢丝电镀锌betts process 贝茨粗铅电解精炼法bevel 斜面bevel angle 边缘斜截角bevel cutting 开坡口beveled edge 斜切的边缘beveling 开坡口bewel 浇包柄biaxial crystal 双轴晶体bichromate 重铬酸盐bichromate treatment 重铬酸盐表面处理bichromic acid 重铬酸bicrystal 双晶体bifurcated runner 分叉鳞big end down mold 上小下大锭模big end up mold 上大下小锭模big mill 开毗机billet 薄板坯板料billet centering press 定心压力机billet mill 钩毗机billet scalping unit 畔剥皮装置billet shears 畔剪断机billet storage 畔仓库billet yard 畔仓库billon 毕隆铸币金合金bimetal 双金属bimetal blank 双金属坯bimetal sheet 双金属板bimetal tube 双金属管bimetal wire 双金属线bimetallic fuse 双金属保险丝bimetallic strip 双金属片bimetallic temperature regulator 双金属温度第器bimetallic thermostat 双金属温度第器bin 料箱bin feeder 漏斗给料机binary alloy 二元合金binary compound 二元化合物binary constitutional diagram 二元系状态图binary electrolyte 二元电解质binary eutectic 二元共晶binary system 二元系binder 粘结剂binder metal 粘结金属binder pool 粘结金属池binding agent 粘结剂binding band 捆轧用钢带binding energy 结合能binding enthalpy 键焓binding machine 打包机binding wire 扎线bingham's etching solution 宾厄姆电解腐蚀液binnite 淡铜矿binocular microscope 双目显微镜biological metal 生物金属bipolar system 双极式bisilicate 二硅酸盐bismite 铋华bismuth 铋bismuth chloride 氯化铋bismuth glance 辉铋矿bismuth ocher 铋华bismuthate 铋酸盐bismuthine 辉铋矿bismuthinite 辉铋矿bismutosmaltite 钴砷铋矿石biting 轧辊咬入轧件bitumen 沥青bituminous coal 沥青煤bivariant system 双变系black annealing 黑退火black ash 黑灰black cinder 黑炉渣black copper 黑色铜black fracture 黑色断口black heart malleable iron 黑心可锻铸铁black iron ore 磁铁矿black nickel 黑色镍black oxide finish 氧化发黑处理black plate 黑钢板black sand 旧砂black thermit 黑色铝热剂blackband 菱铁矿blackbody 黑体blackbody radiation 黑体辐射blackbody temperature 黑体温度blacking scab 涂料起皮blacklead 石墨blacksmith 锻工blacksmith tongs 锻工钳blacksmith's anvil 锻砧blackwash 铸模涂料。
Aluminium-铝-英文版
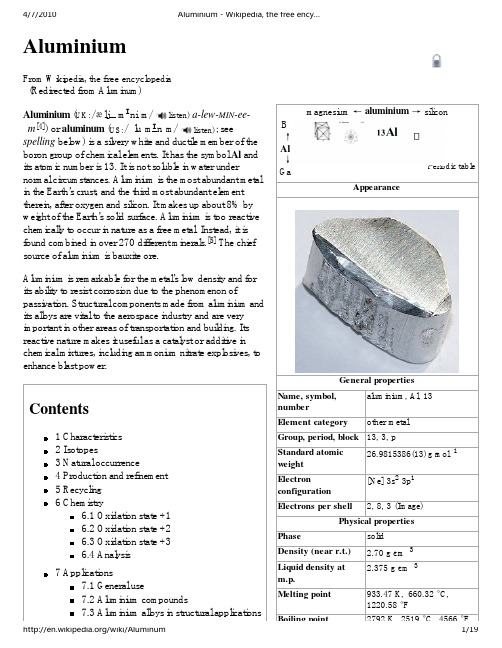
Aluminium magnesium ←aluminium→silicon B ↑Al ↓Ga Appearance General properties Name,symbol,number aluminium, Al, 13Element category other metal Group,period,block 13,3,p Standard atomic weight 26.9815386(13) g·mol −1Electron configuration [Ne] 3s 2 3p 1Electrons per shell 2, 8, 3 (Image)Physical properties Phase solid Density (near r.t.) 2.70g·cm −3Liquid density at m.p. 2.375 g·cm −3Melting point 933.47K, 660.32 °C, 1220.58 °F From Wikipedia, the free encyclopedia(Redirected from Aluminum)Aluminium (UK:/ˌælj ʊˈm ɪniəm/(listen)a-lew-MIN -ee-əm [4]) or aluminum (US:/əˈlu ːm ɪnəm/(listen); seespelling below) is a silvery white and ductile member of theboron group of chemical elements. It has the symbol Al andits atomic number is 13. It is not soluble in water undernormal circumstances. Aluminium is the most abundant metalin the Earth's crust, and the third most abundant elementtherein, after oxygen and silicon. It makes up about 8% byweight of the Earth's solid surface. Aluminium is too reactivechemically to occur in nature as a free metal. Instead, it isfound combined in over 270 different minerals.[5] The chiefsource of aluminium is bauxite ore.Aluminium is remarkable for the metal's low density and forits ability to resist corrosion due to the phenomenon ofpassivation. Structural components made from aluminium andits alloys are vital to the aerospace industry and are veryimportant in other areas of transportation and building. Itsreactive nature makes it useful as a catalyst or additive inchemical mixtures, including ammonium nitrate explosives, toenhance blast power.Contents1Characteristics2Isotopes3Natural occurrence4Production and refinement5Recycling6Chemistry6.1Oxidation state +16.2Oxidation state +26.3Oxidation state +36.4Analysis7Applications7.1General use7.2Aluminium compounds7.3Aluminium alloys in structural applicationsPeriodic table 13Al 4/7/2010Aluminium - Wikipedia, the free ency…Boiling point2792K, 2519 °C, 4566 °FHeat of fusion10.71kJ·mol−1Heat of vaporization294.0kJ·mol−1Specific heat capacity(25 °C) 24.200 J·mol−1·K−1Vapor pressureP/Pa110100 1 k10 k100 kat T/K148216321817205423642790Atomic propertiesOxidation states3, 2[1], 1[2](amphoteric oxide)Electronegativity 1.61 (Pauling scale)Ionization energies(more)1st: 577.5kJ·mol−12nd: 1816.7 kJ·mol−13rd: 2744.8 kJ·mol−1Atomic radius143pmCovalent radius121±4 pmVan der Waalsradius184 pmMiscellaneaCrystal structure face-centered cubicMagnetic ordering paramagnetic[3]Electrical resistivity(20 °C) 28.2 nΩ·mThermal conductivity(300 K) 237 W·m−1·K−1Thermal expansion(25 °C) 23.1 µm·m−1·K−1Speed of sound (thinrod)(r.t.) (rolled) 5,000m·s−1Young's modulus70 GPaShear modulus26 GPaBulk modulus76 GPaPoisson ratio0.35Mohs hardness 2.75Vickers hardness167 MPaBrinell hardness245 MPaCAS registrynumber7429-90-5Most stable isotopesMain article:Isotopes of aluminiumiso NA half-life DM DE(MeV)DP265+26 Etched surface from a high purity(99.9998%) aluminium bar, size55×37 mm7.4Household wiring8History9Etymology9.1Nomenclature history9.2Present-day spelling10Health concerns11Effect on plants12See also13References14External linksCharacteristicsAluminium is a soft,durable,lightweight,malleable metalwith appearanceranging from silveryto dull grey,depending on thesurface roughness.Aluminium isnonmagnetic andnonsparking. It isalso insoluble inalcohol, though it can be soluble in water in certain forms. Theyield strength of pure aluminium is 7–11MPa, whilealuminium alloys have yield strengths ranging from 200 MPato 600 MPa.[6] Aluminium has about one-third the densityand stiffness of steel. It is ductile, and easily machined,cast,drawn and extruded.Corrosion resistance can be excellent due to a thin surfacelayer of aluminium oxide that forms when the metal is exposedto air, effectively preventing further oxidation. The strongestaluminium alloys are less corrosion resistant due to galvanicreactions with alloyed copper.[6] This corrosion resistance isalso often greatly reduced when many aqueous salts arepresent, particularly in the presence of dissimilar metals.Aluminium atoms are arranged in a face-centred cubic (fcc)structure. Aluminium has a stacking-fault energy ofapproximately 200 mJ/m2.[7]4/7/2010Aluminium - Wikipedia, the free ency…26Al trace 7.17×105y β+1.1726Mg ε-26Mg γ 1.8086-27Al 100%27Al is stable with 14neutronsAluminium is one of the few metals that retain full silvery reflectance in finely powdered form, making it an important component of silver paints. Aluminium mirror finish has thehighest reflectance of any metal in the 200–400 nm (UV) andthe 3,000–10,000 nm (far IR) regions; in the 400–700 nmvisible range it is slightly outperformed by tin and silver and inthe 700–3000 (near IR) by silver,gold, and copper.[8]Aluminium is a good thermal and electrical conductor, having 62% the conductivity of copper. Aluminium is capable of being a superconductor, with a superconducting critical temperature of 1.2kelvins and a critical magnetic field of about 100gauss (10milliteslas).[9]IsotopesMain article:isotopes of aluminiumAluminium has nine isotopes, whose mass numbers range from 23 to 30. Only 27Al (stable isotope) and 26Al (radioactive isotope,t 1/2 = 7.2×105y) occur naturally; however,27Al has a natural abundance above 99.9%.26Al is produced from argon in the atmosphere by spallation caused by cosmic-ray protons. Aluminium isotopes have found practical application in dating marine sediments, manganese nodules, glacial ice,quartz in rock exposures,and meteorites. The ratio of 26Al to 10Be has been used to study the role of transport, deposition,sediment storage,burial times, and erosion on 105 to 106 year time scales.[10]Cosmogenic 26Al was first applied in studies of the Moon and meteorites. Meteoroid fragments, after departure from their parent bodies, are exposed to intense cosmic-ray bombardment during their travel through space, causing substantial 26Al production. After falling to Earth, atmospheric shielding protects the meteorite fragments from further 26Al production, and its decay can then be used to determine the meteorite's terrestrial age. Meteorite research has also shown that 26Al was relativelyabundant at the time of formation of our planetary system. Most meteorite scientists believe that the energy released by the decay of 26Al was responsible for the melting and differentiation of some asteroids after their formation 4.55billion years ago.[11]Natural occurrenceSee also:Aluminium in AfricaIn the Earth's crust, aluminium is the most abundant (8.3% by weight) metallic element and the third most abundant of all elements (after oxygen and silicon).[12] Because of its strong affinity to oxygen, however, it is almost never found in the elemental state; instead it is found in oxides or silicates.Feldspars, the most common group of minerals in the Earth's crust, are aluminosilicates. Native aluminium metal can be found as a minor phase in low oxygen fugacity environments, such as the interiors of certain volcanoes.[13] It also occurs in the minerals beryl,cryolite,garnet,spinel and turquoise.[12] Impurities in Al 2O 3, such as chromium or cobalt yield the gemstones ruby and sapphire, respectively. Pure Al 2O 3, known as corundum, is one of the hardest materials known.[12]Although aluminium is an extremely common and widespread element, the common aluminium minerals are not economic sources of the metal. Almost all metallic aluminium is produced from the ore bauxite (AlO x (OH)3-2x ).Bauxite occurs as a weathering product of low iron and silica bedrock in tropical climatic conditions.[14] Large deposits of bauxite occur in Australia,Brazil,Guinea and Jamaica but the primary mining areas for the ore are in4/7/2010Aluminium - Wikipedia, the free ency…Bauxitedeposits of bauxite occur in Australia,Brazil,Guinea and Jamaica but the primary mining areas for the ore are in Ghana,Indonesia, Jamaica, Russia and Surinam.[15]Smelting of the ore mainly occurs in Australia, Brazil, Canada,Norway, Russia and the United States. Because smelting is an energy-intensive process, regions with excess natural gas supplies (such as the United Arab Emirates) are becoming aluminium refiners.Production and refinementAlthough aluminium is the most abundant metallic element in the Earth's crust, it is never found in free, metallic form,and it was once considered a precious metal more valuable than gold.Napoleon III, Emperor of France, is reputed to have given a banquet where the most honoured guests were given aluminium utensils, while the others had to make do with gold.[16][17] The Washington Monument was completed, with the 100 ounce (2.8 kg) aluminium capstone being put in place on December 6, 1884, in an elaborate dedication ceremony. It was the largest single piece of aluminium cast at the time, when aluminium was as expensive as silver.[18] Aluminium has been produced in commercial quantities for just over 100 years.Aluminium is a strongly reactive metal that forms a high-energy chemicalbond with oxygen. Compared to most other metals, it is difficult to extractfrom ore, such as bauxite, due to the energy required to reduce aluminiumoxide (Al 2O 3). For example, direct reduction with carbon, as is used toproduce iron, is not chemically possible, since aluminium is a strongerreducing agent than carbon. However there is an indirect carbothermicreduction possible by using carbon and Al 2O 3 which forms anintermediate Al 4C 3 and this can further yield aluminium metal at atemperature of 1900–2000°C. This process is still under development.This process costs less energy and yields less CO 2 than the Hall-Héroult process.[19] Aluminium oxide has a melting point of about 2,000 °C(3,600 °F). Therefore, it must be extracted by electrolysis. In this process, the aluminium oxide is dissolved inmolten cryolite and then reduced to the pure metal. The operational temperature of the reduction cells is around 950to 980 °C (1,740 to 1,800 °F). Cryolite is found as a mineral in Greenland, but in industrial use it has been replaced by a synthetic substance. Cryolite is a chemical compound of aluminium,sodium, and calcium fluorides: (Na 3AlF 6).The aluminium oxide (a white powder) is obtained by refining bauxite in the Bayer process of Karl Bayer.(Previously, the Deville process was the predominant refining technology.)The electrolytic process replaced the Wöhler process, which involved the reduction of anhydrous aluminium chloride with potassium. Both of the electrodes used in the electrolysis of aluminium oxide are carbon. Once the refined alumina is dissolved in the electrolyte, its ions are free to move around. The reaction at the cathode is:Al 3+ + 3 e − → AlHere the aluminium ion is being reduced. The aluminium metal then sinks to the bottom and is tapped off, usually cast into large blocks called aluminium billets for further processing.At the anode, oxygen is formed:2 O 2− → O 2 + 4 e −This carbon anode is then oxidized by the oxygen, releasing carbon dioxide:4/7/2010Aluminium - Wikipedia, the free ency…World production trend of aluminiumAluminium output in 2005O 2 + C → CO 2The anodes in a reduction cell must therefore be replaced regularly, since they are consumed in the process.Unlike the anodes, the cathodes are not oxidized because there is no oxygen present, as the carbon cathodes are protected by the liquid aluminium inside the cells. Nevertheless, cathodes do erode, mainly due to electrochemical processes and metal movement. After five to ten years, depending on the current used in the electrolysis, a cell has to be rebuilt because of cathode wear.Aluminium electrolysis with the Hall-Héroult process consumes a lot ofenergy, but alternative processes were always found to be less viableeconomically and/or ecologically. The worldwide average specific energyconsumption is approximately 15±0.5kilowatt-hours per kilogram ofaluminium produced (52 to 56MJ/kg). The most modern smeltersachieve approximately 12.8 kW·h/kg (46.1 MJ/kg). (Compare this to theheat of reaction, 31 MJ/kg, and the Gibbs free energy of reaction, 29MJ/kg.) Reduction line currents for older technologies are typically 100to 200kiloamperes; state-of-the-art smelters [20] operate at about 350kA. Trials have been reported with 500 kA cells.Electric power represents about 20% to 40% of the cost of producing aluminium, depending on the location of the smelter. Smelters tend to be situated where electric power is both plentiful and inexpensive, such as South Africa,Ghana, the South Island of New Zealand, Australia, the People's Republic of China, the Middle East,Russia,Quebec and British Columbia in Canada, and Iceland.[21]In 2005, the People's Republic of China was the top producer ofaluminium with almost a one-fifth world share, followed by Russia,Canada, and the USA, reports the British Geological Survey.Over the last 50 years, Australia has become a major producer of bauxiteore and a major producer and exporter of alumina.[22] Australiaproduced 62 million tonnes of bauxite in 2005. The Australian depositshave some refining problems, some being high in silica but have theadvantage of being shallow and relatively easy to mine.[23]See also:Category:Aluminium minerals RecyclingMain article:Aluminium recyclingAluminium is 100% recyclable without any loss of its natural qualities. Recovery ofthe metal via recycling has become an important facet of the aluminium industry.Recycling involves melting the scrap, a process that requires only five percent of theenergy used to produce aluminium from ore. However, a significant part (up to 15%of the input material) is lost as dross (ash-like oxide).[24] The dross can undergo afurther process to extract aluminium.4/7/2010Aluminium - Wikipedia, the free ency…Aluminium recycling codefurther process to extract aluminium.Recycling was a low-profile activity until the late 1960s, when the growing use ofaluminium beverage cans brought it to the public awareness.In Europe aluminium experiences high rates of recycling, ranging from 42% of beverage cans, 85% of construction materials and 95% of transport vehicles.[25]Recycled aluminium is known as secondary aluminium, but maintains the same physical properties as primary aluminium. Secondary aluminium is produced in a wide range of formats and is employed in 80% of the alloy injections. Another important use is for extrusion.White dross from primary aluminium production and from secondary recycling operations still contains usefulquantities of aluminium which can be extracted industrially.[26] The process produces aluminium billets, together with a highly complex waste material. This waste is difficult to manage. It reacts with water, releasing a mixture of gases (including, among others,hydrogen,acetylene, and ammonia) which spontaneously ignites on contact with air;[27]contact with damp air results in the release of copious quantities of ammonia gas. Despite these difficulties,however, the waste has found use as a filler in asphalt and concrete.[28]ChemistryOxidation state +1AlH is produced when aluminium is heated in an atmosphere of hydrogen. Al 2O is made by heating the normal oxide, Al 2O 3, with silicon at 1,800 °C (3,272 °F) in a vacuum.[29]Al 2S can be made by heating Al 2S 3 with aluminium shavings at 1,300 °C (2,372 °F) in a vacuum.[29] It quickly disproportionates to the starting materials. The selenide is made in a parallel manner.AlF, AlCl and AlBr exist in the gaseous phase when the tri-halide is heated with aluminium. Aluminium halides usually exist in the form AlX 3, where X is F, Cl, Br, or I.[29]Oxidation state +2Aluminium monoxide, AlO, has been detected in the gas phase after explosion [30] and in stellar absorptionspectra.[31]Oxidation state +3Fajans' rules show that the simple trivalent cation Al 3+ is not expected to be found in anhydrous salts or binary compounds such as Al 2O 3. The hydroxide is a weak base and aluminium salts of weak acids, such as carbonate,cannot be prepared. The salts of strong acids, such as nitrate, are stable and soluble in water, forming hydrates with at least six molecules of water of crystallization.Aluminium hydride, (AlH 3)n , can be produced from trimethylaluminium and an excess of hydrogen. It burnsexplosively in air. It can also be prepared by the action of aluminium chloride on lithium hydride in ether solution, but cannot be isolated free from the solvent. Alumino-hydrides of the most electropositive elements are known, the4/7/2010Aluminium - Wikipedia, the free ency…most useful being lithium aluminium hydride, Li[AlH4]. It decomposes into lithium hydride, aluminium and hydrogen when heated, and is hydrolysed by water. It has many uses in organic chemistry, particularly as a reducing agent. The aluminohalides have a similar structure.Aluminium hydroxide may be prepared as a gelatinous precipitate by adding ammonia to an aqueous solution of an aluminium salt. It is amphoteric, being both a very weak acid, and forming aluminates with alkalis. It exists in various crystalline forms.Aluminium carbide, Al4C3 is made by heating a mixture of the elements above 1,000 °C (1,832 °F). The pale yellow crystals have a complex lattice structure, and react with water or dilute acids to give methane. The acetylide, Al2(C2)3, is made by passing acetylene over heated aluminium.Aluminium nitride, AlN, can be made from the elements at 800 °C (1,472 °F). It is hydrolysed by water to form ammonia and aluminium hydroxide.Aluminium phosphide, AlP, is made similarly, and hydrolyses to give phosphine.Aluminium oxide, Al2O3, occurs naturally as corundum, and can be made by burning aluminium in oxygen or by heating the hydroxide, nitrate or sulfate. As a gemstone, its hardness is only exceeded by diamond,boron nitride, and carborundum. It is almost insoluble in water.Aluminium sulfide, Al2S3, may be prepared by passing hydrogen sulfide over aluminium powder. It is polymorphic.Aluminium iodide, AlI3, is a dimer with applications in organic synthesis.Aluminium fluoride, AlF3, is made by treating the hydroxide with HF, or can be made from the elements. It consists of a giant molecule which sublimes without melting at 1,291 °C (2,356 °F). It is very inert. The other trihalides are dimeric, having a bridge-like structure.When aluminium and fluoride are together in aqueous solution, they readily form complex ions such as[AlF(H2O)5]2+,AlF3(H2O)3, and[AlF6]3−. Of these,[AlF6]3− is the most stable. This is explained by the fact that aluminium and fluoride, which are both very compact ions, fit together just right to form the octahedral aluminium hexafluoride complex. When aluminium and fluoride are together in water in a 1:6 molar ratio,[AlF6]3− is the most common form, even in rather low concentrations.Organometallic compounds of empirical formula AlR3 exist and, if not also polymers, are at least dimers or trimers. They have some uses in organic synthesis, for instance trimethylaluminium.AnalysisThe presence of aluminium can be detected in qualitative analysis using aluminon.ApplicationsGeneral useAluminium is the most widely used non-ferrous metal.[32] Global production of aluminium in 2005 was 31.9 million tonnes. It exceeded that of any other metal except iron (837.5 million tonnes).[33] Forecast for 2012 is 42–45 million tons, driven by rising Chinese output.[34] Relatively pure aluminium is encountered only when corrosion resistance and/or workability is more important than strength or hardness. A thin layer of aluminium can be deposited onto a flat surface by physical vapour deposition or (very infrequently)chemical vapour deposition orHousehold aluminium foil Aluminium-bodied Austin "A40Sports" (circa 1951)Aluminium slabs being transported from the smelters other chemical means to form optical coatings and mirrors. When so deposited, a fresh, pure aluminium film serves as a good reflector (approximately 92%) of visible light and an excellent reflector (as much as 98%) of medium and far infrared radiation.Pure aluminium has a low tensile strength, but when combined with thermo-mechanical processing, aluminium alloys display a marked improvement in mechanical properties, especially when tempered. Aluminium alloys form vital components of aircraft and rockets as a result of their high strength-to-weight ratio. Aluminium readily forms alloys with many elements such as copper,zinc,magnesium,manganese and silicon (e.g.,duralumin). Today, almost all bulk metal materials that are referred to loosely as "aluminium", are actually alloys. For example, the common aluminium foils are alloys of 92% to 99% aluminium.[35]Some of the many uses for aluminium metal are in:Transportation (automobiles, aircraft,trucks,railway cars, marinevessels,bicycles etc.) as sheet, tube, castings etc.Packaging (cans, foil, etc.)Construction (windows,doors,siding, building wire, etc.)A wide range of household items, from cooking utensils to baseballbats, watches.[36]Street lighting poles, sailing ship masts,walking poles etc.Outer shells of consumer electronics, also cases for equipment e.g.photographic equipment.Electrical transmission lines for power distributionMKM steel and Alnico magnetsSuper purity aluminium (SPA, 99.980% to 99.999% Al), used inelectronics and CDs.Heat sinks for electronic appliances such as transistors and CPUs.Substrate material of metal-core copper clad laminates used in highbrightness LED lighting.Powdered aluminium is used in paint, and in pyrotechnics such assolid rocket fuels and thermite.Aluminium can be reacted with hydrochloric acid to form hydrogengas.Aluminium compoundsAluminium ammonium sulfate ([Al(NH 4)](SO 4)2),ammonium alumis used as a mordant, in water purification and sewage treatment, inpaper production, as a food additive, and in leather tanning.Aluminium acetate is a salt used in solution as an astringent.Aluminium borate (Al 2O 3 B 2O 3) is used in the production of glassand ceramic.Aluminium borohydride (Al(BH 4)3) is used as an additive to jetfuel.Aluminium foamAluminium bronze (CuAl 5)Aluminium chloride (AlCl 3) is used: in paint manufacturing, in antiperspirants, in petroleum refining and in the production of synthetic rubber.Aluminium chlorohydrate is used as an antiperspirant and in the treatment of hyperhidrosis.Aluminium fluorosilicate (Al 2(SiF 6)3) is used in the production of synthetic gemstones, glass and ceramic.Aluminium hydroxide (Al(OH)3) is used: as an antacid, as a mordant, in water purification, in the manufacture of glass and ceramic and in the waterproofing of fabrics.Aluminium oxide (Al 2O 3), alumina, is found naturally as corundum (rubies and sapphires),emery, and is used in glass making. Synthetic ruby and sapphire are used in lasers for the production of coherent light. Used as a refractory, essential for the production of high pressure sodium lamps.Aluminium phosphate (AlPO 4) is used in the manufacture: of glass and ceramic,pulp and paper products,cosmetics, paints and varnishes and in making dental cement.Aluminium sulfate (Al 2(SO 4)3) is used: in the manufacture of paper, as a mordant, in a fire extinguisher, inwater purification and sewage treatment, as a food additive, in fireproofing, and in leather tanning.Aqueous Aluminium ions (such as found in aqueous Aluminium Sulfate) are used to treat against fish parasites such as Gyrodactylus salaris .In many vaccines, certain aluminium salts serve as an immune adjuvant (immune response booster) to allow the protein in the vaccine to achieve sufficient potency as an immune stimulant.Aluminium alloys in structural applicationsMain article:Aluminium alloyAluminium alloys with a wide range of properties are used in engineeringstructures. Alloy systems are classified by a number system (ANSI) or bynames indicating their main alloying constituents (DIN and ISO).The strength and durability of aluminium alloys vary widely, not only as aresult of the components of the specific alloy, but also as a result of heattreatments and manufacturing processes. A lack of knowledge of theseaspects has from time to time led to improperly designed structures andgained aluminium a bad reputation.One important structural limitation of aluminium alloys is their fatiguestrength. Unlike steels, aluminium alloys have no well-defined fatigue limit,meaning that fatigue failure will eventually occur under even very smallcyclic loadings. This implies that engineers must assess these loads anddesign for a fixed life rather than an infinite life.Another important property of aluminium alloys is their sensitivity to heat.Workshop procedures involving heating are complicated by the fact that aluminium, unlike steel, will melt withoutfirst glowing red. Forming operations where a blow torch is used therefore requires some expertise, since no visual signs reveal how close the material is to melting. Aluminium alloys, like all structural alloys, also are subject to internal stresses following heating operations such as welding and casting. The problem with aluminium alloys in this regard is their low melting point, which make them more susceptible to distortions from thermally induced stress relief. Controlled stress relief can be done during manufacturing by heat-treating the parts in an oven, followed by gradual cooling—in effect annealing the stresses.The low melting point of aluminium alloys has not precluded their use in rocketry; even for use in constructing combustion chambers where gases can reach 3500 K. The Agena upper stage engine used a regeneratively cooled aluminium design for some parts of the nozzle, including the thermally critical throat region.Household wiringSee also:Aluminium wireCompared to copper, aluminium has about 65% of the electrical conductivity by volume, although 200% by weight. Traditionally copper is used as household wiring material. In the 1960s aluminium was considerably cheaper than copper, and so was introduced for household electrical wiring in the United States, even though many fixtures had not been designed to accept aluminium wire. In some cases the greater coefficient of thermal expansion of aluminium causes the wire to expand and contract relative to the dissimilar metal screw connection, eventually loosening the connection. Also, pure aluminium has a tendency to creep under steady sustained pressure (to a greater degree as the temperature rises), again loosening the connection. Finally,Galvanic corrosion from the dissimilar metals increased the electrical resistance of the connection.All of this resulted in overheated and loose connections, and this in turn resulted in fires. Builders then became wary of using the wire, and many jurisdictions outlawed its use in very small sizes in new construction. Eventually, newer fixtures were introduced with connections designed to avoid loosening and overheating. The first generation fixtures were marked "Al/Cu" and were ultimately found suitable only for copper-clad aluminium wire, but the second generation fixtures, which bear a "CO/ALR" coding, are rated for unclad aluminium wire. To adapt older assemblies, workers forestall the heating problem using a properly-done crimp of the aluminium wire to a short "pigtail" of copper wire. Today, new alloys, designs, and methods are used for aluminium wiring in combination with aluminium termination.HistoryAncient Greeks and Romans used aluminium salts as dyeing mordantsand as astringents for dressing wounds;alum is still used as a styptic. In1761Guyton de Morveau suggested calling the base alum alumine. In1808,Humphry Davy identified the existence of a metal base of alum,which he at first termed alumium and later aluminum (see Etymologysection, below).The metal was first produced in 1825 (in an impure form) by Danishphysicist and chemist Hans Christian Ørsted. He reacted anhydrousaluminium chloride with potassium amalgam and yielded a lump of metallooking similar to tin.[37]Friedrich Wöhler was aware of theseexperiments and cited them, but after redoing the experiments of Ørstedhe concluded that this metal was pure potassium. He conducted a similar。
铝箔英文版的MSDS
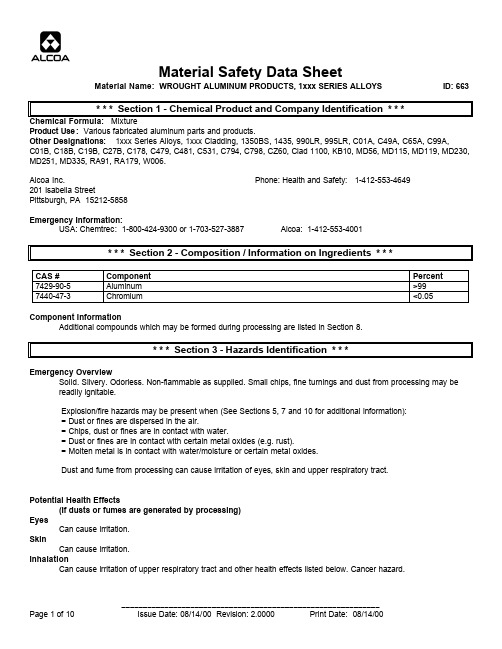
Material Safety Data SheetMaterial Name: WROUGHT ALUMINUM PRODUCTS, 1xxx SERIES ALLOYS ID: 663* * * Section 1 - Chemical Product and Company Identification * * *Chemical Formula: MixtureProduct Use: Various fabricated aluminum parts and products.Other Designations: 1xxx Series Alloys, 1xxx Cladding, 1350BS, 1435, 990LR, 995LR, C01A, C49A, C65A, C99A,C01B, C18B, C19B, C27B, C178, C479, C481, C531, C794, C798, CZ60, Clad 1100, KB10, MD56, MD115, MD119, MD230, MD251, MD335, RA91, RA179, W006.Alcoa Inc.Phone: Health and Safety: 1-412-553-4649201 Isabella StreetPittsburgh, PA 15212-5858Emergency Information:USA: Chemtrec: 1-800-424-9300 or 1-703-527-3887 Alcoa: 1-412-553-4001* * * Section 2 - Composition / Information on Ingredients * * *CAS #Component Percent7429-90-5Aluminum>997440-47-3Chromium<0.05 Component InformationAdditional compounds which may be formed during processing are listed in Section 8.* * * Section 3 - Hazards Identification * * *Emergency OverviewSolid. Silvery. Odorless. Non-flammable as supplied. Small chips, fine turnings and dust from processing may be readily ignitable.Explosion/fire hazards may be present when (See Sections 5, 7 and 10 for additional information):= Dust or fines are dispersed in the air.= Chips, dust or fines are in contact with water.= Dust or fines are in contact with certain metal oxides (e.g. rust).= Molten metal is in contact with water/moisture or certain metal oxides.Dust and fume from processing can cause irritation of eyes, skin and upper respiratory tract.Potential Health Effects(If dusts or fumes are generated by processing)EyesCan cause irritation.SkinCan cause irritation.InhalationCan cause irritation of upper respiratory tract and other health effects listed below. Cancer hazard.Health Effects of IngredientsChromium dust Can cause irritation of eyes, skin and respiratory tract. Chromium and trivalent chromiumIARC/NTP: Not classified by IARC.Aluminum dust, fines and fumes Low health risk by inhalation. ACGIH: Listed as nuisance dust (milling,cutting, grinding).Some products are supplied with a lubricant/oil coating or have residual oil from the manufacturing process. OilCan cause irritation of skin. Skin contact (prolonged or repeated): Can cause dermatitis. Mineral oils, untreated or mildly refined Studies with experimental animals by skin contact have found skin tumors. IARC/NTP: Listed as "known to be a human carcinogen" by the NTP. Listed as carcinogenic to humans by IARC (Group 1)*.Health Effects Of Additional Compounds Which May Be Formed During ProcessingHexavalent chromium (Chrome VI) Can cause irritation of eyes, skin and respiratory tract. Skin contact: Can cause irritant dermatitis, allergic reactions and skin ulcers. Chronic overexposures: Can cause perforation of the nasal septum, respiratory sensitization, asthma, fluid in the lungs (pulmonary edema), lung damage, kidneydamage, lung cancer, nasal cancer and cancer of the gastrointestinal tract. IARC/NTP: Listed as "known to be a human carcinogen" by the NTP. Listed as carcinogenic to humans by IARC (Group 1)*.Alumina Low health risk by inhalation. ACGIH: Listed as nuisance dust.If the product is heated well above ambient temperatures or machined, oil vapor or mist may be generated. Oilvapor and mist Can cause irritation of respiratory tract. Acute overexposures: Can cause bronchitis, asthma,headache, central nervous system effects (nausea, dizziness and loss of coordination) and drowsiness (narcosis).Welding, plasma arc cutting, and arc spray metalizing can generate ozone. Ozone Can cause irritation of eyes, nose and upper respiratory tract. Acute overexposures: Can cause shortness of breath, tightness of chest,headache, cough, nausea and narrowing of airways. Effects are reversible on cessation of exposure. Acuteoverexposures (high concentrations): Can cause respiratory distress, respiratory tract damage, bleeding and fluid in the lungs (pulmonary edema). Effects can be delayed up to 1-2 hours. Additional information: Studies withexperimental animals by inhalation have found genetic damage, reproductive harm, blood cell damage, lung damage and death.Welding fumes IARC/NTP: Listed as possibly carcinogenic to humans by IARC (Group 2B)*. AdditionalInformation: In one study, occupational asthma was associated with exposures to fumes from aluminum welding.Plasma arc cutting can generate oxides of nitrogen. Oxides of nitrogen (NO and NO2) Can cause irritation ofeyes, skin and respiratory tract. Acute overexposures: Can cause reduced ability of the blood to carry oxygen(methemaglobin). Can cause cough, shortness of breath, fluid in the lungs (pulmonary edema) and death. Effects may be delayed up to 2-3 weeks. Nitrogen dioxide (NO2) Chronic overexposures: Can cause scarring of the lungs (pulmonary fibrosis).*IARC ClassificationsGroup 1: The agent is carcinogenic to humans. There is sufficient evidence that a causal relationship existedbetween exposure to the agent and human cancer.Group 2B: The agent is possibly carcinogenic to humans. Generally includes agents for which there is limitedevidence in the absence of sufficient evidence in experimental animals.Medical Conditions Aggravated By Exposure to the ProductAsthma, chronic lung disease, and skin rashes.* * * Section 4 - First Aid Measures * * *First Aid: EyesFlush eyes with plenty of water or saline for at least 15 minutes. Consult a physician.First Aid: SkinWash skin with soap and water for at least 15 minutes. Consult a physician if irritation persists.First Aid: InhalationRemove to fresh air. If unconscious or severely injured, check for clear airway, breathing and presence of pulse.Perform CPR if there is no pulse or respiration. Consult a physician.* * * Section 5 - Fire Fighting Measures * * *Flammable PropertiesThis product does not present fire or explosion hazards as shipped. Small chips, turnings, dust and fines fromprocessing may be readily ignitable.Fire/ExplosionMay be a potential hazard under the following conditions:= Dust or fines dispersed in the air can be explosive. Even a minor dust cloud can explode violently.= Chips, dust or fines in contact with water can generate flammable/explosive hydrogen gas. Hydrogen gas could present an explosion hazard in confined or poorly ventilated spaces.= Fines and dust in contact with certain metal oxides (e.g., rust). A thermite reaction, with considerable heatgeneration, can be initiated by a weak ignition source.= Molten metal in contact with water/moisture or other metal oxides (e.g., rust). Moisture entrapped by moltenmetal can be explosive. Contact of molten aluminum with other metal oxides can initiate a thermite reaction. Extinguishing MediaUse Class D extinguishing agents on dusts, fines or molten metal. Use coarse water spray on chips and turnings.DO NOT USE: Halogenated agents on small chips, dusts or fines. Water around molten metal.Fire Fighting Equipment/InstructionsFire fighters should wear NIOSH approved, positive pressure, self-contained breathing apparatus and full protective clothing when appropriate.* * * Section 6 - Accidental Release Measures * * *Small/Large SpillIf molten: Contain the flow using dry sand or salt flux as a dam. Do not use shovels or hand tools to halt the flow of molten aluminum. Allow the spill to cool before remelting as scrap.* * * Section 7 - Handling and Storage * * *Handling/StorageProduct should be kept dry. Avoid generating dust. Avoid contact with sharp edges or heated metal. Hot and cold aluminum are not visually different.Requirements for Processes Which Generate Dusts or FumesIf processing of these products includes operations where dust or extremely fine particulate is generated, obtain and follow the safety procedures and equipment guides contained in Aluminum Association Bulletin F-1 and National Fire Protection Association (NFPA) brochures listed in Section 16. Cover and reseal partially empty containers. Use non-sparking handling equipment. Provide grounding and bonding where necessary to prevent accumulation of staticcharges during dust handling and transfer operations. (See Section 15).Local ventilation and vacuum systems must be designed to handle explosive dusts. Dry vacuums and electrostatic precipitators must not be used. Dust collection systems must be dedicated to aluminum dust only and should be clearly labeled as such. Do not co-mingle fines of aluminum with fines of iron, iron oxide (rust) or other metal oxides.Do not allow chips, fines or dust to contact water, particularly in enclosed areas.Avoid all ignition sources. Good housekeeping practices must be maintained.Requirements for Remelting of Scrap Material and/or IngotMolten metal and water can be an explosive combination. The risk is greatest when there is sufficient molten metal to entrap or seal off the water. Water and other forms of contamination on or contained in scrap or remelt ingot are known to have caused explosions in melting operations. While the products may have minimal surface roughness and internal voids, there remains the possibility of moisture contamination or entrapment. If confined, even a fewdrops of water can lead to violent explosions.All tooling and containers which come in contact with molten metal must be preheated or specially coated and rust free. Molds and ladles must be preheated or oiled prior to casting. Any surfaces that may contact molten metal(e.g., concrete) should be specially coated.Drops of molten metal in water (e.g. from plasma arc cutting), while not normally an explosion hazard, can generate enough flammable hydrogen gas to present an explosion hazard. Vigorous circulation of the water and removal of the particles minimize the hazards.During melting operations, the following minimum guidelines should be observed:= Inspect all materials prior to furnace charging and completely remove surface contamination such as water, ice, snow, deposits of grease and oil or other surface contamination resulting from weather exposure, shipment, orstorage.= Store materials in dry, heated areas with any cracks or cavities pointed downwards.= Preheat and dry large or heavy items such as ingot adequately before charging into a furnace containing molten metal. This is typically done by use of a drying oven or homogenizing furnace. The drying cycle should bring theinternal metal temperature of the coldest item of the batch to 400°F and then hold at that temperature for 6 hours.* * * Section 8 - Exposure Controls / Personal Protection * * *Engineering ControlsUse with adequate explosion-proof ventilation to meet the limits listed in Section 8.Personal Protective EquipmentRespiratory ProtectionUse NIOSH-approved respiratory protection as specified by an Industrial Hygienist or other qualified professional if concentrations exceed the limits listed in Section 8. Suggested respiratory protection: P95Eye ProtectionWear safety glasses/goggles to avoid eye contact.Skin ProtectionWear impervious gloves to avoid repeated or prolonged skin contact with residual oils and to avoid any skin injury. GeneralPersonnel who handle and work with molten metal should utilize primary protective clothing like face shields, fire resistant tapper's jackets, leggings, spats and similar equipment to prevent burn injuries. In addition to primaryprotection, secondary or day-to-day work clothing that is fire resistant and sheds metal splash is recommended for use with molten metal.Minimize breathing oil vapors and mist. Remove oil contaminated clothing; launder or dry-clean before reuse.Remove oil contaminated shoes and thoroughly clean and dry before reuse. Cleanse skin thoroughly after contact, before breaks and meals, and at the end of the work period. Oil coating is readily removed from skin with waterless hand cleaners followed by a thorough washing with soap and water.Exposure GuidelinesA: General Product InformationAlcoa recommends an Occupational Exposure Limit for Oil Mist of 0.5 mg/m3 TWA.B: Component Exposure LimitsAluminum (7429-90-5)ACGIH10 mg/m3 TWA (metal dust)OSHA15 mg/m3 TWA (total dust); 5 mg/m3 TWA (respirable fraction)Chromium (7440-47-3)ACGIH0.5 mg/m3 TWAOSHA 1 mg/m3 TWAC: Additional Compounds Which May be Formed During ProcessingAlumina (non-fibrous) (1344-28-1)ACGIH as Al: 10 mg/m3 TWA (The value is for total dust containing no asbestos and < 1%crystalline silica)OSHA15 mg/m3 TWA (total dust); 5 mg/m3 TWA (respirable fraction)Chromium (II) compounds (Not Available)OSHA0.5 mg/m3 TWA (as Cr)Chromium (III) compounds (as Cr) (Not Available)ACGIH as Cr: 0.5 mg/m3 TWAChromium (VI) compounds- water soluble (Not Available)ACGIH0.05 mg/m3 TWAChromium (VI) compounds (certain water insoluble forms) (Not Available)ACGIH0.01 mg/m3 TWAChromic acid and chromates (7738-94-5)OSHA and chromates: C 1 mg/10m3Welding fumes (NOC) (Not Available)ACGIH 5 mg/m3 TWAOzone (10028-15-6)ACGIH Heavy work: 0.05 ppm TWA; Moderate work: 0.08 ppm TWA; Light work: 0.1 ppm TWA;heavy, moderate or light work, <= 2Hrs: 0.20 ppmOSHA0.1 ppm TWA; 0.2 mg/m3 TWANitrogen dioxide (10102-44-0)ACGIH 3 ppm TWAACGIH 5 ppm STELOSHA C 5 ppm; C 9 mg/m3Nitric oxide (10102-43-9)ACGIH25 ppm TWAOSHA25 ppm TWA; 30 mg/m3 TWA* * * Section 9 - Physical & Chemical Properties * * *Appearance:SilveryPhysical State:Solid: sheet, plate, wire, rod,bar, extrusion, forgings, etc.Boiling Point:Not applicable Melting Point:Range: generally 1190-1215 ºF(643-657 ºC)Vapor Pressure:Not applicable Vapor Density:Not applicableSolubility Water:None Specific Gravity:See DensitypH Level:Not applicableDensity:Range: generally 2.70-2.71g/cm³ (0.097-0.098 lb/in³)Odor:None Odor Threshold:Not applicableOctanol-Water Coefficient:Not applicable* * * Section 10 - Chemical Stability & Reactivity Information * * *StabilityStable under normal conditions of use, storage, and transportation as shipped.Conditions to AvoidChips, fines, dust and molten metal are considerably more reactive with the following:= Water: Slowly generates flammable/explosive hydrogen gas and heat. Generation rate is greatly increased with smaller particles (e.g., fines and dusts). Molten metal can react violently/explosively with water or moisture,particularly when the water is entrapped.= Heat: Oxidizes at a rate dependent upon temperature and particle size.= Strong oxidizers: Violent reaction with considerable heat generation. Can react explosively with nitrates (e.g., ammonium nitrate and fertilizers containing nitrate) particularly when heated or molten.= Acids and alkalis: Reacts to generate flammable/explosive hydrogen gas. Generation rate is greatly increased with smaller particles (e.g., fines and dusts).= Halogenated compounds: Many halogenated hydrocarbons, including halogenated fire extinguishing agents, can react violently with finely divided aluminum.= Iron oxide (rust) and other metal oxides (e.g., copper and lead oxides): A violent thermite reactiongenerating considerable heat can occur. Reaction with aluminum fines and dusts requires only very weak ignition sources for initiation. Molten aluminum can react violently with iron oxide without external ignition source.= Iron powder and water: An explosive reaction forming hydrogen gas occurs when heated above 1470°F(800°C).* * * Section 11 - Toxicological Information * * *Health Effects of IngredientsA: General Product InformationNo information available for product.B: Component Analysis - LD50/LC50No LD50/LC50's are available for this product's components.CarcinogenicityA: General Product InformationNo information available for product.B: Component CarcinogenicityChromium (7440-47-3)ACGIH A4 - not classifiable as a human carcinogenIARC Monograph 49; 1990* * * Section 12 - Ecological Information * * *EcotoxicityA: General Product InformationNo information available for product.B: Component Analysis - Ecotoxicity - Aquatic ToxicityNo ecotoxicity data was found for this product's components.Environmental FateNo information available for product.* * * Section 13 - Disposal Considerations * * *Disposal InstructionsReuse or recycle material whenever possible. Material may be disposed of at an industrial landfill.US EPA Waste Number & DescriptionsA: General Product InformationRCRA Status: Must be determined at time material is disposed. If material is disposed as waste, it must becharacterized under RCRA according to 40 CFR, Part 261, or state equivalent in the U.S.B: Component Waste NumbersRCRA waste codes other than described under Section A may apply depending on use of product. Refer to 40 CFR 261 or state equivalent in the U.S.* * * Section 14 - Transportation Information * * *Special TransportationPSN #1PSN #2PSN #3PSN #4Notes:(1)Proper Shipping Name:Not RegulatedHazard Class:-UN NA Number:-Packing Group:-RQ:-Other - Tech Name:-Other - Marine Pollutant:-Notes:(1)When "Not regulated," enter the proper freight classification, "MSDS Number," and "Product Name" on theshipping paperwork.Canadian TDG Hazard Class & PIN:Not regulated* * * Section 15 - Regulatory Information * * *US Federal RegulationsA: General Product InformationAll electrical equipment must be suitable for use in hazardous atmospheres involving aluminum powder inaccordance with 29 CFR 1910.307. The National Electrical Code, NFPA 70, contains guidelines for determining the type and design of equipment and installation which will meet this requirement.B: Component AnalysisThis material contains one or more of the following chemicals required to be identified under SARA Section 302 (40 CFR 355 Appendix A), SARA Section 313 (40 CFR 372.65) and/or CERCLA (40 CFR 302.4).Aluminum (7429-90-5)SARA 313:form R reporting required for 1.0% de minimis concentration (fume or dust only) Chromium (7440-47-3)SARA 313:form R reporting required for 1.0% de minimis concentrationCERCLA:final RQ = 5000 pounds (2270 kg) (no reporting of releases of this hazardous material isrequired if the diameter of the pieces of the solid metal released is equal to or exceeds0.004 inches)SARA 311/312 Physical and Health Hazard Categories:Immediate (acute) Health Hazard:Yes, if particulates/fumes generated during processing.Delayed (chronic) Health Hazard:Yes, if particulates/fumes generated during processing.Fire Hazard:NoSudden Release of Pressure:NoReactive:Yes, if moltenState RegulationsA: General Product InformationPENNSYLVANIA "Special Hazardous Substance": Chromium compounds, hexavalentChemical(s) known to the State of California to cause cancer: Hexavalent chromiumB: Component Analysis - StateThe following components appear on one or more of the following state hazardous substances lists: Component CAS #CA FL MA MN NJ PAAluminum7429-90-5Yes Yes Yes Yes Yes Yes Chromium7440-47-3Yes Yes Yes Yes Yes Yes Other RegulationsA: General Product InformationIn reference to Title VI of the Clean Air Act of 1990, this material does not contain nor was it manufactured using ozone-depleting chemicals.B: Component Analysis - WHMIS IDLThe following components are identified under the Canadian Hazardous Products Act Ingredient Disclosure List:Component CAS #Minimum ConcentrationAluminum7429-90-51% item 47 (197)C: Component Analysis - InventoryComponent CAS #TSCA DSL EINECS AUST.MITIAluminum7429-90-5Yes Yes Yes Yes NoChromium7440-47-3Yes Yes Yes Yes NoNote: Pure metals are not specifically listed by CAS or MITI number. The class of compounds for each of these metals is listed on the MITI inventory.* * * Section 16 - Other Information * * *MSDS HistoryOriginal: March 16, 1990Supersedes: March 4, 1999Revised: August 14, 2000MSDS StatusChanges in Sections 1 and 2.Prepared ByHazardous Materials Control Committee.MSDS System Number115949Other Information= Aluminum Association’s Bulletin F-1, "Guidelines for Handling Aluminum Fines Generated During VariousAluminum Fabricating Operations." The Aluminum Association, 900 19th Street, N.W., Washington, DC 20006.= Aluminum Association, "Guidelines for Handling Molten Aluminum, The Aluminum Association, 900 19th Street, N.W., Washington, DC 20006.= NFPA 65, Standard for Processing and Finishing of Aluminum (NFPA phone: 800-344-3555)= NFPA 651, Standard for Manufacture of Aluminum and Magnesium Powder= NFPA 70, Standard for National Electrical Code (Electrical Equipment, Grounding and Bonding)= NFPA 77, Standard for Static Electricity= Guide to Occupational Exposure Values-1999, Compiled by the American Conference of Governmental Industrial Hygienists (ACGIH).= Documentation of the Threshold Limit Values and Biological Exposure Indices, Sixth Edition, 1991, Compiled by the American Conference of Governmental Industrial Hygienists, Inc. (ACGIH).= NIOSH Pocket Guide to Chemical Hazards, U.S. Department of Health and Human Services, June 1994.= Dangerous Properties of Industrial Materials, Sax, N. Irving, Van Nostrand Reinhold Co., Inc., 1984.= Patty’s Industrial Hygiene and Toxicology: Volume II: Toxicology, 4th ed., 1994, Patty, F. A.; edited by Clayton,G. D. and Clayton, F. E.: New York: John Wiley & Sons, Inc.= TOMES CPS(TM), MICROMEDEX, Inc., 1999Key-Legend:ACGIH American Conference of Governmental Industrial HygienistsAICS Australian Inventory of Chemical SubstancesCAS Chemical Abstract ServiceCERCLA Comprehensive Environmental Response, Compensation, and Liability ActCFR Code of Federal RegulationsCPR Cardio-pulmonary ResuscitationDOT Department of TransportationDSL Domestic Substances List (Canada)ECOIN European Core InventoryE P A Environmental Protection ActIARC International Agency for Research on CancerLC50Lethal concentration (50 percent kill)LC Lo Lowest published lethal concentrationLD50Lethal dose (50 percent kill)LD Lo Lowest published lethal doseNFPA National Fire Protection AssociationNIOSH National Institute for Occupational Safety and HealthNTP National Toxicology ProgramOEL Occupational Exposure LimitOSHA Occupational Safety and Health AdministrationPEL Permissible Exposure LimitPIN Product Identification NumberRCRA Resource Conservation and Recovery ActSARA Superfund Amendments and Reauthorization ActSTEL Short Term Exposure LimitTCLP Toxic Chemicals Leachate ProgramTDG Transportation of Dangerous GoodsTLV Threshold Limit ValueTSCA Toxic Substance Control ActTWA Time Weighted Averageatm atmospherecm centimeterg, gm gramin inchkg kilogramlb poundm metermg milligramml, ML millilitermm millimetern.o.s.not otherwise specifiedppb parts per billionppm parts per millionpsia pounds per square inch absoluteu micronug microgramINFORMATION HEREIN IS GIVEN IN GOOD FAITH AS AUTHORITATIVE AND VALID; HOWEVER, NO WARRANTY, EXPRESS OR IMPLIED, CAN BE MADE.This is the end of MSDS # 663。
铝合金熔铸过滤工艺流程英语

铝合金熔铸过滤工艺流程英语Aluminum Alloy Melt Filtration Process.Molten aluminum filtration is a critical process in the production of high-quality aluminum castings. It removes impurities and inclusions from the molten metal, resulting in improved casting quality, reduced scrap rates, and increased productivity. There are various melt filtration techniques available, each with its own advantages and disadvantages. The choice of filtration method depends on the specific application and the desired results.Types of Melt Filtration Techniques.Ceramic Foam Filters (CFFs): CFFs are made of porous ceramic materials and are placed in the melt stream to trap impurities. They are highly effective in removing large particles and inclusions, but they can be expensive and require careful handling.Depth Filters: Depth filters are made of a variety of materials, such as fiberglass, cellulose, or metal fibers. They are designed to trap particles throughout their depth, providing a high level of filtration efficiency. However, they can be more restrictive to flow and may require frequent replacement.Screen Filters: Screen filters are made of perforated metal or wire mesh and are placed in the melt stream to remove larger particles. They are less efficient than CFFs or depth filters but are less expensive and more durable.Flux Filters: Flux filters are made of a mixture of fluxes and ceramic materials. They are used to remove oxides, dross, and other impurities from the melt. Flux filters can be effective in improving the melt quality, but they can also introduce additional impurities into the metal.Process Steps of Melt Filtration.The melt filtration process typically involves thefollowing steps:1. Preheat the filter: The filter is preheated to the desired temperature to prevent thermal shock when it is immersed in the molten metal.2. Immerse the filter in the melt: The filter is carefully immersed in the molten metal stream. It is important to ensure that the filter is fully submerged and that there are no air pockets trapped inside.3. Filtration: The molten metal flows through the filter, leaving behind impurities and inclusions. The filtration efficiency depends on the type of filter used and the operating conditions.4. Remove the filter: Once the filtration process is complete, the filter is carefully removed from the melt stream. It is important to avoid introducing any impurities into the melt during this step.5. Clean the filter: The filter is cleaned to removeany remaining impurities. The cleaning method depends on the type of filter used.Advantages of Melt Filtration.Improved casting quality: Melt filtration removes impurities and inclusions, resulting in castings with a smoother surface finish, reduced porosity, and enhanced mechanical properties.Reduced scrap rates: By removing impurities, melt filtration helps to prevent casting defects that can lead to scrap.Increased productivity: Melt filtration can improve the efficiency of the casting process by reducing the need for remelting and recasting.Reduced energy consumption: Melt filtration can reduce energy consumption by preventing the formation of dross and other impurities that can reduce the thermal efficiency of the casting process.Factors to Consider When Selecting a Melt Filtration Technique.When selecting a melt filtration technique, the following factors should be considered:Type of aluminum alloy: Different aluminum alloys have different solidification characteristics and impurity levels, which can affect the choice of filtration method.Casting size and complexity: Larger and more complex castings require a higher level of filtration efficiency to achieve the desired quality.Filtration efficiency: The filtration efficiency of a particular method determines its ability to remove impurities and inclusions.Flow rate: The flow rate of the molten metal through the filter is an important consideration, as it can affect the overall productivity of the casting process.Cost: The cost of the filtration method, including the initial investment and ongoing maintenance, should be taken into account.Conclusion.Melt filtration is an essential process in the production of high-quality aluminum castings. By removing impurities and inclusions from the molten metal, melt filtration helps to improve casting quality, reduce scrap rates, increase productivity, and reduce energy consumption. The choice of filtration method depends on the specific application and the desired results. Careful considerationof the factors discussed in this article will helpfoundries select the most appropriate melt filtration technique for their needs.。
陶瓷坩埚灼烧氧化铝

陶瓷坩埚灼烧氧化铝英文回答:Ceramic crucibles are commonly used for firing alumina, a process known as calcination. Calcination is the process of heating a substance to a high temperature to bring about a chemical reaction, such as the conversion of aluminum hydroxide to aluminum oxide. The crucible provides a controlled environment for the calcination process, allowing for precise temperature control and preventing contamination of the alumina.One of the main advantages of using a ceramic crucible for firing alumina is its high temperature resistance. Ceramic materials, such as porcelain or alumina-based ceramics, can withstand extremely high temperatures without melting or deforming. This is crucial for the calcination process, which typically requires temperatures above 1000 degrees Celsius. The ceramic crucible acts as a protective container, ensuring that the alumina remains intact duringthe firing process.Another advantage of using a ceramic crucible is its chemical inertness. Ceramic materials are non-reactive and do not interact with the substances being heated. This is important for calcining alumina, as any reaction between the crucible and the alumina could result in impurities or unwanted by-products. The inertness of the ceramic crucible ensures that the calcination process remains pure and uncontaminated.Furthermore, ceramic crucibles are durable and long-lasting. They can be reused multiple times without losing their integrity or performance. This is cost-effective and environmentally friendly, as it reduces the need for frequent replacement of crucibles. Additionally, ceramic crucibles are easy to clean and maintain, requiring minimal effort to remove any residue or impurities after each use.In terms of drawbacks, ceramic crucibles can be brittle and prone to cracking or breaking under certain conditions. Extreme temperature changes or physical impact can causethe crucible to fracture, rendering it unusable. However, with proper handling and care, this risk can be minimized.Overall, ceramic crucibles are an excellent choice for firing alumina due to their high temperature resistance, chemical inertness, and durability. They provide a reliable and controlled environment for the calcination process, ensuring the production of high-quality alumina.中文回答:陶瓷坩埚是常用于灼烧氧化铝的一种容器。
Dust Explosion training
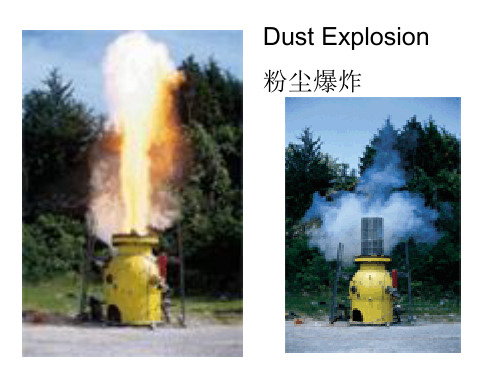
MIE
Minimum Ignition energy 最小点燃能量
MEC
Minimum explosible concentration 最低可 爆炸浓度
LOC
Limiting oxygen concentration 最低氧指数
Determines the least amount of oxygen required for explosion propagation through the dust cloud.决定通过粉尘云传播爆炸所需要的最低氧气数量。
Fuel 燃料
Ignition 点燃源
Oxygen 氧气
Dust Explosion Pentagon 粉尘爆炸五边形
Fuel 燃料
Ignition 点燃源
Dispersion 传播 Oxygen 氧气
Confinement 禁闭
Dust explosibility: pressure-time chart 粉尘爆炸性:压力-时间表
Used to design enclosures and predict the severity of the consequence.通常用 于设计围栏并预测结果严重性
(dp/dt)max
Maximum rate of pressure rise压力上升 的最大速度
Predicts the violence of an explosion. Used to calculate KSt. 预测爆炸的威力。 用于计算KSt. Predicts the ease and likelihood of ignition of a dispersed dust cloud.预测散布的 粉尘云的易燃性和可然性 Measures the minimum amount of dust, dispersed in air, required to spread an explosion. Analogous to the lower flammability limit (LFL) for gas/air mixtures. 测量传播爆炸而需要的散布在空气中的最小粉尘数量。与气体/空气混合物的较 低可燃极限类似。
美国钢铁产品的标准比较多
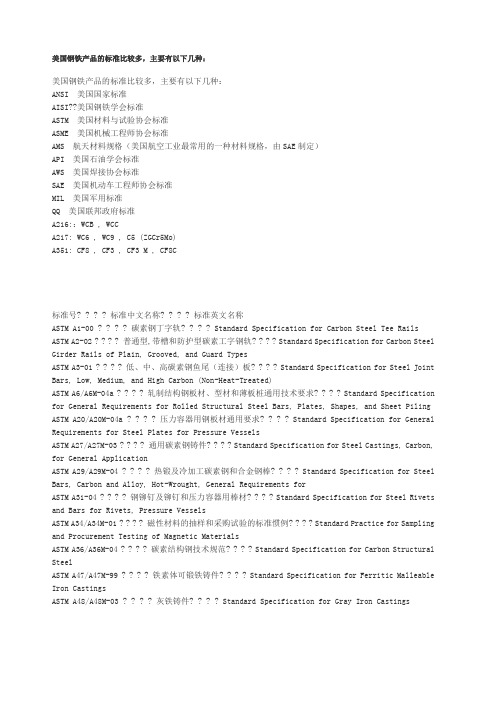
美国钢铁产品的标准比较多,主要有以下几种:美国钢铁产品的标准比较多,主要有以下几种:ANSI 美国国家标准AISI??美国钢铁学会标准ASTM 美国材料与试验协会标准ASME 美国机械工程师协会标准AMS 航天材料规格(美国航空工业最常用的一种材料规格,由SAE制定)API 美国石油学会标准AWS 美国焊接协会标准SAE 美国机动车工程师协会标准MIL 美国军用标准QQ 美国联邦政府标准A216::WCB , WCCA217: WC6 , WC9 , C5 (ZGCr5Mo)A351: CF8 , CF3 , CF3 M , CF8C标准号? ? ? ? 标准中文名称? ? ? ? 标准英文名称ASTM A1-00 ? ? ? ? 碳素钢丁字轨? ? ? ? Standard Specification for Carbon Steel Tee Rails ASTM A2-02 ? ? ? ? 普通型,带槽和防护型碳素工字钢轨? ? ? ? Standard Specification for Carbon Steel Girder Rails of Plain, Grooved, and Guard TypesASTM A3-01 ? ? ? ? 低、中、高碳素钢鱼尾(连接)板? ? ? ? Standard Specification for Steel Joint Bars, Low, Medium, and High Carbon (Non-Heat-Treated)ASTM A6/A6M-04a ? ? ? ? 轧制结构钢板材、型材和薄板桩通用技术要求? ? ? ? Standard Specification for General Requirements for Rolled Structural Steel Bars, Plates, Shapes, and Sheet Piling ASTM A20/A20M-04a ? ? ? ? 压力容器用钢板材通用要求? ? ? ? Standard Specification for General Requirements for Steel Plates for Pressure VesselsASTM A27/A27M-03 ? ? ? ? 通用碳素钢铸件? ? ? ? Standard Specification for Steel Castings, Carbon, for General ApplicationASTM A29/A29M-04 ? ? ? ? 热锻及冷加工碳素钢和合金钢棒? ? ? ? Standard Specification for Steel Bars, Carbon and Alloy, Hot-Wrought, General Requirements forASTM A31-04 ? ? ? ? 钢铆钉及铆钉和压力容器用棒材? ? ? ? Standard Specification for Steel Rivets and Bars for Rivets, Pressure VesselsASTM A34/A34M-01 ? ? ? ? 磁性材料的抽样和采购试验的标准惯例? ? ? ? Standard Practice for Sampling and Procurement Testing of Magnetic MaterialsASTM A36/A36M-04 ? ? ? ? 碳素结构钢技术规范? ? ? ? Standard Specification for Carbon Structural SteelASTM A47/A47M-99 ? ? ? ? 铁素体可锻铁铸件? ? ? ? Standard Specification for Ferritic Malleable Iron CastingsASTM A48/A48M-03 ? ? ? ? 灰铁铸件? ? ? ? Standard Specification for Gray Iron CastingsASTM A49-01 ? ? ? ? 经热处理的碳素钢鱼尾(连接)板,微合金鱼尾板及锻制碳素钢异型鱼尾板? ? ? ? Standard Specification for Heat-Treated Carbon Steel Joint Bars, Microalloyed Joint Bars, and Forged Carbon Steel Compromise Joint BarsASTM A53/A53M-04 ? ? ? ? 无镀层热浸的、镀锌的、焊接的及无缝钢管的技术规范? ? ? ? Standard Specification for Pipe, Steel, Black and Hot-Dipped, Zinc-Coated, Welded and SeamlessASTM A65-01 ? ? ? ? 钢轨道钉? ? ? ? Standard Specification for Steel Track SpikesASTM A66-01 ? ? ? ? 钢质螺旋道钉? ? ? ? Standard Specification for Steel Screw SpikesASTM A67-00 ? ? ? ? 热加工低碳钢和高碳钢垫板技术规范? ? ? ? Standard Specification for Steel Tie Plates, Low-Carbon and High-Carbon Hot-WorkedASTM A74-04 ? ? ? ? 铸铁污水管及配件的技术规范? ? ? ? Standard Specification for Cast Iron Soil Pipe and FittingsASTM A82-02 ? ? ? ? 钢筋混凝土用无节钢丝? ? ? ? Standard Specification for Steel Wire, Plain, for Concrete ReinforcementASTM A90/A90M-01 ? ? ? ? 镀锌和镀锌合金钢铁制品镀层重量的试验方法? ? ? ? Standard Test Method for Weight [Mass] of Coating on Iron and Steel Articles with Zinc or Zinc-Alloy Coatings ASTM A99-03 ? ? ? ? 锰铁合金? ? ? ? Standard Specification for FerromanganeseASTM A100-04 ? ? ? ? 硅铁? ? ? ? Standard Specification for FerrosiliconASTM A101-04 ? ? ? ? 铬铁? ? ? ? Standard Specification for FerrochromiumASTM A102-04 ? ? ? ? 钒铁合金? ? ? ? Standard Specification for FerrovanadiumASTM A105/A105M-03 ? ? ? ? 管系部件用碳素钢锻件? ? ? ? Standard Specification for Carbon Steel Forgings for Piping ApplicationsASTM A106/A106M-04a ? ? ? ? 高温用无缝碳素钢管? ? ? ? Standard Specification for Seamless Carbon Steel Pipe for High-Temperature ServiceASTM A108-03 ? ? ? ? 优质冷加工碳素钢棒材技术规范? ? ? ? Standard Specification for Steel Bar, Carbon and Alloy, Cold-FinishedASTM A109/A109M-03 ? ? ? ? 冷轧碳素钢带技术规范? ? ? ? Standard Specification for Steel, Strip, Carbon (0.25 Maximum Percent), Cold-RolledASTM A111-99a(2004)e1 ? ? ? ? 电话和电报线路用镀锌"铁"丝规格? ? ? ? Standard Specification for Zinc-Coated (Galvanized) Iron Telephone and Telegraph Line WireASTM A116-00 ? ? ? ? 镀锌钢丝编织栏栅网? ? ? ? Standard Specification for Metallic-Coated, Steel Woven Wire Fence FabricASTM A121-99(2004) ? ? ? ? 镀锌刺钢丝? ? ? ? Standard Specification for Mettalic-Coated Carbon Steel Barbed WireASTM A123/A123M-02 ? ? ? ? 钢铁产品的锌镀层(热浸镀锌)技术规范? ? ? ? Standard Specification for Zinc (Hot-Dip Galvanized) Coatings on Iron and Steel ProductsASTM A125-96(2001) ? ? ? ? 热处理螺旋形钢弹簧? ? ? ? Standard Specification for Steel Springs, Helical, Heat-TreatedASTM A126-04 ? ? ? ? 阀门、法兰和管配件用灰铁铸件? ? ? ? Standard Specification for Gray Iron Castings for Valves, Flanges, and Pipe FittingsASTM A128/A128M-93(2003) ? ? ? ? 钢铸件,奥氏体锰? ? ? ? Standard Specification for Steel Castings, Austenitic ManganeseASTM A131/A131M-04 ? ? ? ? 海船用结构钢? ? ? ? Standard Specification for Structural Steel for ShipsASTM A132-04 ? ? ? ? 钼铁合金? ? ? ? Standard Specification for FerromolybdenumASTM A134-96(2001) ? ? ? ? 电熔(电弧)焊钢管(NPS为16英寸和16英寸以上)? ? ? ? Standard Specification for Pipe, Steel, Electric-Fusion (Arc)-Welded (Sizes NPS 16 and Over)ASTM A135-01 ? ? ? ? 电阻焊钢管? ? ? ? Standard Specification for Electric-Resistance-Welded Steel PipeASTM A139/A139M-04 ? ? ? ? 电熔(电弧)焊钢管(4英寸以上的)? ? ? ? Standard Specification for Electric-Fusion (Arc)-Welded Steel Pipe (NPS 4 and Over)ASTM A143/A143M-03 ? ? ? ? 热浸镀锌结构钢制品防脆裂措施和探测脆裂的程序? ? ? ? Standard Practice for Safeguarding Against Embrittlement of Hot-Dip Galvanized Structural Steel Products and Procedure for Detecting EmbrittlementASTM A144-02 ? ? ? ? 铁钨合金规范? ? ? ? Specification for FerrotungstenASTM A146-04 ? ? ? ? 氧化钼制品? ? ? ? Standard Specification for Molybdenum Oxide Products ASTM A148/A148M-03 ? ? ? ? 结构用高强度钢铸件? ? ? ? Standard Specification for Steel Castings, High Strength, for Structural PurposesASTM A153/A153M-04 ? ? ? ? 钢铁制金属构件上镀锌层(热浸)? ? ? ? Standard Specification for Zinc Coating (Hot-Dip) on Iron and Steel HardwareASTM A159-83(2001) ? ? ? ? 汽车用灰铁铸件? ? ? ? Standard Specification for Automotive Gray Iron CastingsASTM A167-99 ? ? ? ? 不锈钢和耐热铬镍钢板、薄板及带材? ? ? ? Standard Specification for Stainless and Heat-Resisting Chromium-Nickel Steel Plate, Sheet, and StripASTM A176-99 ? ? ? ? 不锈钢和耐热铬钢板、薄板及带材? ? ? ? Standard Specification for Stainless and Heat-Resisting Chromium Steel Plate, Sheet, and StripASTM A178/A178M-02 ? ? ? ? 电阻焊接碳素钢钢管及碳锰钢锅炉和过热器管的技术规范? ? ? ? Standard Specification for Electric-Resistance-Welded Carbon Steel and Carbon-Manganese Steel Boiler and Superheater TubesASTM A179/A179M-90a(2001) ? ? ? ? 热交换器和冷凝器用无缝冷拉低碳钢管? ? ? ? Standard Specification for Seamless Cold-Drawn Low-Carbon Steel Heat-Exchanger and Condenser Tubes ASTM A181/A181M-01 ? ? ? ? 普通锻制碳素钢管的规格? ? ? ? Standard Specification for Carbon Steel Forgings, for General-Purpose PipingASTM A182/A182M-02 ? ? ? ? 高温设备用锻制或轧制的合金钢管法兰、锻制管件、阀门及零件? ? ? ? Standard Specification for Forged or Rolled Alloy-Steel Pipe Flanges, Forged Fittings, and Valves and Parts for High-Temperature ServiceASTM A183-03 ? ? ? ? 钢轨用碳素钢螺栓和螺母? ? ? ? Standard Specification for Carbon Steel Track Bolts and NutsASTM A184/A184M-01 ? ? ? ? 混凝土加筋用变形钢筋编织网? ? ? ? Standard Specification for Fabricated Deformed Steel Bar Mats for Concrete ReinforcementASTM A185-02 ? ? ? ? 钢筋混凝土用焊接钢丝结构? ? ? ? Standard Specification for Steel Welded Wire Reinforcement, Plain, for ConcreteASTM A192/A192M-02 ? ? ? ? 高压用无缝碳素钢锅炉管? ? ? ? Standard Specification for Seamless Carbon Steel Boiler Tubes for High-Pressure ServiceASTM A193/A193M-04b ? ? ? ? 高温设备用合金钢和不锈钢螺栓材料? ? ? ? Standard Specification for Alloy-Steel and Stainless Steel Bolting Materials for High-Temperature ServiceASTM A194/A194M-04a ? ? ? ? 高温和高压设备用碳素钢与合金钢螺栓和螺母的规格? ? ? ? Standard Specification for Carbon and Alloy Steel Nuts for Bolts for High Pressure or High Temperature Service, or BothASTM A197/A197M-00 ? ? ? ? 化铁炉用可锻铸铁? ? ? ? Standard Specification for Cupola Malleable IronASTM A202/A202M-03 ? ? ? ? 压力容器用铬锰硅合金钢板? ? ? ? Standard Specification for Pressure Vessel Plates, Alloy Steel, Chromium-Manganese-SiliconASTM A203/A203M-97(2003) ? ? ? ? 压力容器用镍合金钢板? ? ? ? Standard Specification for Pressure Vessel Plates, Alloy Steel, NickelASTM A204/A204M-03 ? ? ? ? 压力容器用钼合金钢板? ? ? ? Standard Specification for Pressure Vessel Plates, Alloy Steel, MolybdenumASTM A209/A209M-03 ? ? ? ? 锅炉和过热器用无缝碳钼合金钢管? ? ? ? Standard Specification for Seamless Carbon-Molybdenum Alloy-Steel Boiler and Superheater TubesASTM A210/A210M-02 ? ? ? ? 锅炉和过热器用无缝中碳素管? ? ? ? Standard Specification for Seamless Medium-Carbon Steel Boiler and Superheater TubesASTM A213/A213M-04 ? ? ? ? 无缝铁素体和奥氏体合金钢锅炉、过热器和换热器管? ? ? ? Standard Specification for Seamless Ferritic and Austenitic Alloy-Steel Boiler, Superheater, andHeat-Exchanger TubesASTM A214/A214M-96(2001) ? ? ? ? 热交换器与冷凝器用电阻焊接碳素钢管? ? ? ? Standard Specification for Electric-Resistance-Welded Carbon Steel Heat-Exchanger and Condenser Tubes ASTM A216/A216M-93(2003) ? ? ? ? 高温下使用的适合于熔焊的碳素钢铸件规格? ? ? ? Standard Specification for Steel Castings, Carbon, Suitable for Fusion Welding, for High- Temperature ServiceASTM A217/A217M-02 ? ? ? ? 适合高温受压零件用合金钢和马氏体不锈钢铸件? ? ? ? Standard Specification for Steel Castings, Martensitic Stainless and Alloy, for Pressure-Containing Parts, Suitable for High-Temperature ServiceASTM A220/A220M-99 ? ? ? ? 珠光体可锻铁? ? ? ? Standard Specification for Pearlitic Malleable IronASTM A225/A225M-03 ? ? ? ? 压力容器用锰矾镍合金钢板? ? ? ? Standard Specification for Pressure Vessel Plates, Alloy Steel, Manganese-Vanadium-NickelASTM A227/A227M-99 ? ? ? ? 机械弹簧用冷拉钢丝? ? ? ? Standard Specification for Steel Wire, Cold-Drawn for Mechanical SpringsASTM A228/A228M-02 ? ? ? ? 乐器用优质弹簧钢丝? ? ? ? Standard Specification for Steel Wire, Music Spring QualityASTM A229/A229M-99 ? ? ? ? 机械弹簧用油回火的钢丝? ? ? ? Standard Specification for Steel Wire, Oil-Tempered for Mechanical SpringsASTM A230/A230M-99 ? ? ? ? 阀门用油回火优质碳素钢弹簧丝? ? ? ? Standard Specification for Steel Wire, Oil-Tempered Carbon Valve Spring QualityASTM A231/A231M-96(2002) ? ? ? ? 铬钒合金钢弹簧丝? ? ? ? Standard Specification for Chromium-Vanadium Alloy Steel Spring WireASTM A232/A232M-99 ? ? ? ? 阀门用优质铬钒合金钢弹簧丝? ? ? ? Standard Specification for Chromium-Vanadium Alloy Steel Valve Spring Quality WireASTM A234/A234M-04 ? ? ? ? 中温与高温下使用的锻制碳素钢及合金钢管配件? ? ? ? Standard Specification for Piping Fittings of Wrought Carbon Steel and Alloy Steel for Moderate and High Temperature ServiceASTM A239-95(2004) ? ? ? ? 用普力斯试验法(硫酸铜浸蚀)确定铁或钢制品上镀锌层最薄点的测试方法? ? ? ? Standard Practice for Locating the Thinnest Spot in a Zinc (Galvanized) Coating on Iron or Steel ArticlesASTM A240/A240M-04ae1 ? ? ? ? 压力容器用耐热铬及铬镍不锈钢板、薄板及带材? ? ? ? Standard Specification for Chromium and Chromium-Nickel Stainless Steel Plate, Sheet, and Strip for Pressure Vessels and for General ApplicationsASTM A242/A242M-04 ? ? ? ? 高强度低合金结构钢? ? ? ? Standard Specification for High-Strength Low-Alloy Structural SteelASTM A247-67(1998) ? ? ? ? 铁铸件中石墨显微结构评定试验方法? ? ? ? Standard Test Method for Evaluating the Microstructure of Graphite in Iron CastingsASTM A249/A249M-04 ? ? ? ? 锅炉、过热器、换热器和冷凝器用焊接奥氏体钢管? ? ? ? Standard Specification for Welded Austenitic Steel Boiler, Superheater, Heat-Exchanger, and Condenser TubesASTM A250/A250M-04 ? ? ? ? 锅炉和过热器用电阻焊铁素体合金钢管? ? ? ? Standard Specification for Electric-Resistance-Welded Ferritic Alloy-Steel Boiler and Superheater TubesASTM A252-98(2002) ? ? ? ? 焊接钢和无缝钢管桩? ? ? ? Standard Specification for Welded and Seamless Steel Pipe PilesASTM A254-97(2002) ? ? ? ? 铜焊钢管规格? ? ? ? Standard Specification for Copper-Brazed Steel TubingASTM A255-02 ? ? ? ? 测定钢淬透性用末端淬火试验的标准试验方法? ? ? ? Standard Test Method for Determining Hardenability of SteelASTM A262-03 ? ? ? ? 奥氏体不锈钢晶间浸蚀敏感性的检测? ? ? ? Standard Practices for Detecting Susceptibility to Intergranular Attack in Austenitic Stainless SteelsASTM A263-03 ? ? ? ? 耐腐蚀铬钢包覆板材,薄板材及带材技术规范? ? ? ? Standard Specification for Stainless Chromium Steel-Clad PlateASTM A264-03 ? ? ? ? 包覆的不锈铬镍钢板,薄板及带材规格? ? ? ? Specification for Stainless Chromium-Nickel Steel-Clad PlateASTM A265-03 ? ? ? ? 镍和镍基合金包覆钢板规格? ? ? ? Standard Specification for Nickel and Nickel-Base Alloy-Clad Steel PlateASTM A266/A266M-03a ? ? ? ? 压力容器部件用碳素钢锻件规格? ? ? ? Standard Specification for Carbon Steel Forgings for Pressure Vessel ComponentsASTM A268/A268M-04 ? ? ? ? 一般设备用无缝和焊接铁素体与马氏体不锈钢管? ? ? ? Standard Specification for Seamless and Welded Ferritic and Martensitic Stainless Steel Tubing for General ServiceASTM A269-04 ? ? ? ? 一般设备用无缝和焊接奥氏体不锈钢管? ? ? ? Standard Specification for Seamless and Welded Austenitic Stainless Steel Tubing for General ServiceASTM A270-03a ? ? ? ? 卫生设施用无缝钢和焊接奥氏体不锈钢管? ? ? ? Standard Specification for Seamless and Welded Austenitic Stainless Steel Sanitary TubingASTM A275/A275M-98(2003) ? ? ? ? 钢锻件的磁粉检查试验方法? ? ? ? Standard Test Method for Magnetic Particle Examination of Steel ForgingsASTM A276-04 ? ? ? ? 不锈钢棒材和型材? ? ? ? Standard Specification for Stainless Steel Bars and ShapesASTM A278/A278M-01 ? ? ? ? 适用于650F容压部件用灰铸铁件的技术规范? ? ? ? Standard Specification for Gray Iron Castings for Pressure-Containing Parts for Temperatures Up to 650°F (350°C) ASTM A283/A283M-03 ? ? ? ? 低和中等抗拉强度碳素钢板? ? ? ? Standard Specification for Low and Intermediate Tensile Strength Carbon Steel PlatesASTM A285/A285M-03 ? ? ? ? 压力容器用低和中等抗拉强度的碳素钢板? ? ? ? Standard Specification for Pressure Vessel Plates, Carbon Steel, Low- and Intermediate-Tensile StrengthASTM A288-91(2003) ? ? ? ? 涡轮发电机磁性定位环用碳素钢和合金钢锻件? ? ? ? Standard Specification for Carbon and Alloy Steel Forgings for Magnetic Retaining Rings for Turbine Generators标准号? ? ? ? 标准中文名称? ? ? ? 标准英文名称ASTM A289/A289M-97(2003) ? ? ? ? 发电机非磁性定位环用合金钢锻件的技术规范? ? ? ? Standard Specification for Alloy Steel Forgings for Nonmagnetic Retaining Rings for GeneratorsASTM A290-02 ? ? ? ? 减速器环用碳素钢和合金钢锻件? ? ? ? Standard Specification for Carbon and Alloy Steel Forgings for Rings for Reduction GearsASTM A291-03 ? ? ? ? 减速器小齿轮、齿轮和心轴用碳素钢和合金钢锻件? ? ? ? Standard Specification for Steel Forgings, Carbon and Alloy, for Pinions, Gears and Shafts for Reduction Gears ASTM A295-98 ? ? ? ? 高碳耐磨轴承钢技术规范? ? ? ? Standard Specification for High-Carbon Anti-Friction Bearing SteelASTM A297/A297M-97(2003) ? ? ? ? 一般用耐热铬铁与镍铬铁合金钢铸件规格? ? ? ? Standard Specification for Steel Castings, Iron-Chromium and Iron-Chromium-Nickel, Heat Resistant, for General ApplicationASTM A299/A299M-04 ? ? ? ? 压力容器用锰硅碳钢板? ? ? ? Standard Specification for Pressure Vessel Plates, Carbon Steel, Manganese-SiliconASTM A302/A302M-03 ? ? ? ? 压力容器用锰钼和锰钼镍合金钢板? ? ? ? Standard Specification for Pressure Vessel Plates, Alloy Steel, Manganese-Molybdenum and Manganese-Molybdenum-Nickel ASTM A304-04 ? ? ? ? 有末端淬火淬透性要求的合金钢棒材的技术规范? ? ? ? Standard Specification for Carbon and Alloy Steel Bars Subject to End-Quench Hardenability RequirementsASTM A307-04 ? ? ? ? 抗拉强度为60000psi的碳素钢螺栓和螺柱的技术规范? ? ? ? Standard Specification for Carbon Steel Bolts and Studs, 60 000 PSI Tensile StrengthASTM A308/A308M-03 ? ? ? ? 经热浸处理镀有铅锡合金的薄板材的技术规范? ? ? ? Standard Specification for Steel Sheet, Terne (Lead-Tin Alloy) Coated by the Hot-Dip ProcessASTM A309-01 ? ? ? ? 用三点试验法测定长镀锌薄钢板镀层的重量成分的试验方法? ? ? ? Standard Test Method for Weight and Composition of Coating on Terne Sheet by the Triple-Spot TestASTM A311/A311M-04 ? ? ? ? 有机械性能要求的消除应力的冷拉碳素钢棒? ? ? ? Standard Specification for Cold-Drawn, Stress-Relieved Carbon Steel Bars Subject to Mechanical Property Requirements ASTM A312/A312M-04a ? ? ? ? 无缝和焊接奥氏体不锈钢管? ? ? ? Standard Specification for Seamless, Welded, and Heavily Cold Worked Austenitic Stainless Steel PipesASTM A313/A313M-03 ? ? ? ? 不锈钢弹簧丝技术规范? ? ? ? Standard Specification for Stainless Steel Spring WireASTM A314-97(2002) ? ? ? ? 锻造用不锈及耐热钢坯及钢棒规格? ? ? ? Standard Specification for Stainless Steel Billets and Bars for ForgingASTM A319-71(2001) ? ? ? ? 高温无压部件用灰铁铸件? ? ? ? Standard Specification for Gray Iron Castings for Elevated Temperatures for Non-Pressure Containing PartsASTM A320/A320M-04 ? ? ? ? 低温用合金钢螺栓材料规格? ? ? ? Standard Specification for Alloy-Steel and Stainless Steel Bolting Materials for Low-Temperature ServiceASTM A321-90(2001) ? ? ? ? 经淬火和回火的碳素钢棒? ? ? ? Standard Specification for Steel Bars, Carbon, Quenched and TemperedASTM A322-91(2001)e1 ? ? ? ? 合金钢棒材.级别? ? ? ? Standard Specification for Steel Bars, Alloy, Standard GradesASTM A323-93(2000) ? ? ? ? 硼铁规格? ? ? ? Standard Specification for FerroboronASTM A324-73(2000) ? ? ? ? 钛铁合金? ? ? ? Standard Specification for FerrotitaniumASTM A325-04a ? ? ? ? 经热处理最小抗拉强度为120/105ksi的热处理钢结构螺栓? ? ? ? Standard Specification for Structural Bolts, Steel, Heat Treated, 120/105 ksi Minimum Tensile Strength ASTM A325M-04a ? ? ? ? 经热处理最小抗拉强度为830Mpa的热处理钢结构螺栓? ? ? ? Standard Specification for Structural Bolts, Steel, Heat Treated 830 Mpa Minimum Tensile Strength [Metric] ASTM A327-91(1997) ? ? ? ? 铸铁冲击试验方法? ? ? ? Standard Test Methods for Impact Testing of Cast IronsASTM A327M-91(1997) ? ? ? ? 铸铁冲击试验方法(米制)? ? ? ? Standard Test Methods for Impact Testing of Cast Irons (Metric)ASTM A328/A328M-03 ? ? ? ? 薄钢板桩? ? ? ? Standard Specification for Steel Sheet Piling ASTM A333/A333M-04a ? ? ? ? 低温用无缝与焊接钢管规格? ? ? ? Standard Specification for Seamless and Welded Steel Pipe for Low-Temperature ServiceASTM A334/A334M-04a ? ? ? ? 低温设备用无缝与焊接碳素和合金钢管? ? ? ? Standard Specification for Seamless and Welded Carbon and Alloy-Steel Tubes for Low-Temperature ServiceASTM A335/A335M-03 ? ? ? ? 高温用无缝铁素体合金钢管? ? ? ? Standard Specification for Seamless Ferritic Alloy-Steel Pipe for High-Temperature ServiceASTM A336/A336M-03a ? ? ? ? 压力与高温部件用合金钢锻件规格? ? ? ? Standard Specification for Alloy Steel Forgings for Pressure and High-Temperature PartsASTM A338-84(2004) ? ? ? ? 铁路,船舶和其他重型装备在温度达到650华氏度(345摄氏度)时使用的可锻铸铁法兰,管件和阀门零件? ? ? ? Standard Specification for Malleable Iron Flanges, Pipe Fittings, and Valve Parts for Railroad, Marine, and Other Heavy Duty Service at Temperatures Up to 650°F (345°C)ASTM A340-03a ? ? ? ? 有关磁性试验用符号和定义的术语? ? ? ? Standard Terminology of Symbols and Definitions Relating to Magnetic TestingASTM A341/A341M-00 ? ? ? ? 用直流磁导计和冲击试验法测定材料的直流磁性能的试验方法? ? ? ? Standard Test Method for Direct Current Magnetic Properties of Materials Using D-C Permeameters and the Ballistic Test MethodsASTM A342/A342M-99 ? ? ? ? 磁铁材料导磁率的试验方法? ? ? ? Standard Test Methods for Permeability of Feebly Magnetic MaterialsASTM A343/A343M-03 ? ? ? ? 在电力频率下用瓦特计-安培计-伏特计法(100-1000赫兹)和25 厘米艾普斯亭(EPSTEIN) 机架测定材料的交流电磁性能的试验方法? ? ? ? Standard Test Method forAlternating-Current Magnetic Properties of Materials at Power Frequencies UsingWattmeter-Ammeter-Voltmeter Method and 25-cm Epstein Test FrameASTM A345-98 ? ? ? ? 磁设备用平轧电炉钢? ? ? ? Standard Specification for Flat-Rolled Electrical Steels for Magnetic ApplicationsASTM A348/A348M-00 ? ? ? ? 用瓦特计--安培计--伏特计法(100-10000赫兹)和25厘米艾普斯亭框测定材料的交流磁性能的试验方法? ? ? ? Standard Test Method for Alternating Current Magnetic Properties of Materials Using the Wattmeter-Ammeter-Voltmeter Method, 100 to 10 000 Hz and 25-cm Epstein FrameASTM A350/A350M-04 ? ? ? ? 要求进行缺口韧性试验的管道部件用碳素钢与低合金钢锻件技术规范? ? ? ? Standard Specification for Carbon and Low-Alloy Steel Forgings, Requiring Notch Toughness Testing for Piping ComponentsASTM A351/A351M-03 ? ? ? ? 容压零件用奥氏体及奥氏体铁素体铸铁的技术规范? ? ? ? Standard Specification for Castings, Austenitic, Austenitic-Ferritic (Duplex), for Pressure-Containing PartsASTM A352/A352M-03 ? ? ? ? 低温受压零件用铁素体和马氏体钢铸件规格? ? ? ? Standard Specification for Steel Castings, Ferritic and Martensitic, for Pressure-Containing Parts, Suitable for Low-Temperature ServiceASTM A353/A353M-93(1999) ? ? ? ? 压力容器用经二次正火及回火处理的含9%镍的合金钢板? ? ? ? Standard Specification for Pressure Vessel Plates, Alloy Steel, 9 Percent Nickel,Double-Normalized and TemperedASTM A354-04 ? ? ? ? 淬火与回火合金钢螺栓,双头螺栓及其他外螺纹紧固件规格? ? ? ? Standard Specification for Quenched and Tempered Alloy Steel Bolts, Studs, and Other Externally Threaded FastenersASTM A355-89(2000) ? ? ? ? 渗氮用合金钢棒? ? ? ? Standard Specification for Steel Bars, Alloys, for NitridingASTM A356/A356M-98(2003) ? ? ? ? 蒸汽轮机用厚壁碳素钢、低合金钢和不锈钢铸件? ? ? ? Standard Specification for Steel Castings, Carbon, Low Alloy, and Stainless Steel, Heavy-Walled for Steam TurbinesASTM A358/A358M-04 ? ? ? ? 高温用电熔焊奥氏体铬镍合金钢管? ? ? ? Standard Specification for Electric-Fusion-Welded Austenitic Chromium-Nickel Stainless Steel Pipe for High-Temperature Service and General ApplicationsASTM A363-03 ? ? ? ? 地面架空线用镀锌钢丝绳? ? ? ? Standard Specification for Zinc-Coated (Galvanized) Steel Overhead Ground Wire StrandASTM A367-60(1999) ? ? ? ? 铸铁的激冷试验方法? ? ? ? Standard Test Methods of Chill Testing of Cast IronASTM A368-95a(2000) ? ? ? ? 不锈钢和耐热钢丝绳的标准? ? ? ? Standard Specification for Stainless Steel Wire StrandASTM A369/A369M-02 ? ? ? ? 高温用锻制和镗孔碳素钢管和铁素体合金钢管? ? ? ? Standard Specification for Carbon and Ferritic Alloy Steel Forged and Bored Pipe for High-Temperature ServiceASTM A370-03a ? ? ? ? 钢制品机械测试的标准试验方法和定义? ? ? ? Standard Test Methods and Definitions for Mechanical Testing of Steel Products标准号? ? ? ? 标准中文名称? ? ? ? 标准英文名称ASTM A372/A372M-03 ? ? ? ? 薄壁压力容器用碳素钢及合金钢锻件? ? ? ? Standard Specification for Carbon and Alloy Steel Forgings for Thin-Walled Pressure VesselsASTM A376/A376M-02a ? ? ? ? 高温中心站用无缝奥氏钢管? ? ? ? Standard Specification for Seamless Austenitic Steel Pipe for High-Temperature Central-Station ServiceASTM A377-03 ? ? ? ? 球墨铸铁压力管规范索引? ? ? ? Standard Index of Specifications for Ductile-Iron Pressure PipeASTM A380-99e1 ? ? ? ? 不锈钢零件、设备和系统的清洗和除垢? ? ? ? Standard Practice for Cleaning, Descaling, and Passivation of Stainless Steel Parts, Equipment, and SystemsASTM A381-96(2001) ? ? ? ? 高压输送用金属弧焊钢管? ? ? ? Standard Specification forMetal-Arc-Welded Steel Pipe for Use With High-Pressure Transmission SystemsASTM A384/A384M-02 ? ? ? ? 防止钢组件热浸镀锌时翘曲和扭曲用安全保护? ? ? ? Standard Practice for Safeguarding Against Warpage and Distortion During Hot-Dip Galvanizing of Steel Assemblies ASTM A385-03 ? ? ? ? 提供高质量镀锌覆层(热浸)? ? ? ? Standard Practice for Providing High-Quality Zinc Coatings (Hot-Dip)ASTM A387/A387M-03 ? ? ? ? 压力容器用铬钼合金钢板? ? ? ? Standard Specification for Pressure Vessel Plates, Alloy Steel, Chromium-MolybdenumASTM A388/A388M-03 ? ? ? ? 重型钢锻件超声波检测? ? ? ? Standard Practice for Ultrasonic Examination of Heavy Steel ForgingsASTM A389/A389M-03 ? ? ? ? 适合高温受压部件用经特殊热处理的合金钢铸件规格? ? ? ? Standard Specification for Steel Castings, Alloy, Specially Heat-Treated, for Pressure-Containing Parts, Suitable for High-Temperature ServiceASTM A390-95(2001) ? ? ? ? 饲养家禽用镀锌钢丝栏栅网(六角形和直线形)? ? ? ? Standard Specification for Zinc-Coated (Galvanized) Steel Poultry Fence Fabric (Hexagonal and Straight Line)ASTM A391/A391M-01 ? ? ? ? 80号合金钢链条? ? ? ? Standard Specification for Grade 80 Alloy Steel ChainASTM A392-03 ? ? ? ? 镀锌钢丝链环栏栅网? ? ? ? Standard Specification for Zinc-Coated Steel Chain-Link Fence FabricASTM A394-04 ? ? ? ? 传动塔架用镀锌和裸露钢螺栓? ? ? ? Standard Specification for Steel Transmission Tower Bolts, Zinc-Coated and BareASTM A395/A395M-99e1 ? ? ? ? 高温用铁素体球墨铸铁受压铸件? ? ? ? Standard Specification for Ferritic Ductile Iron Pressure-Retaining Castings for Use at Elevated TemperaturesASTM A400-69(2000) ? ? ? ? 钢棒的成分及机械性能选择指南? ? ? ? Standard Practice for Steel Bars, Selection Guide, Composition, and Mechanical PropertiesASTM A401/A401M-03 ? ? ? ? 铬硅合金钢丝? ? ? ? Standard Specification for Steel Wire, Chromium-Silicon AlloyASTM A403/A403M-04 ? ? ? ? 锻制奥氏体不锈钢管配件? ? ? ? Standard Specification for Wrought Austenitic Stainless Steel Piping FittingsASTM A407-93(2004) ? ? ? ? 盘簧用冷拉钢丝? ? ? ? Standard Specification for Steel Wire, Cold-Drawn, for Coiled-Type SpringsASTM A409/A409M-01 ? ? ? ? 腐蚀场所或高温下使用的焊接大口径奥氏体钢管? ? ? ? Standard Specification for Welded Large Diameter Austenitic Steel Pipe for Corrosive or High-Temperature ServiceASTM A411-03 ? ? ? ? 镀锌低碳钢铠装线? ? ? ? Standard Specification for Zinc-Coated (Galvanized) Low-Carbon Steel Armor WireASTM A413/A413M-01 ? ? ? ? 碳素钢链? ? ? ? Standard Specification for Carbon Steel Chain ASTM A414/A414M-04 ? ? ? ? 压力容器用碳素薄钢板? ? ? ? Standard Specification for Steel, Sheet, Carbon, for Pressure VesselsASTM A416/A416M-02 ? ? ? ? 预应力混凝土用无涂层七股钢铰线? ? ? ? Standard Specification for Steel Strand, Uncoated Seven-Wire for Prestressed ConcreteASTM A417-93(2004) ? ? ? ? 之字形、方形、正弦形家具用弹簧元件用冷拔钢丝? ? ? ? Standard Specification for Steel Wire, Cold-Drawn, for Zig-Zag, Square-Formed, and Sinuous-Type Upholstery Spring UnitsASTM A418-99(2003) ? ? ? ? 涡轮机及发电机钢转子锻件的超声波检查方法? ? ? ? Standard Test Method for Ultrasonic Examination of Turbine and Generator Steel Rotor ForgingsASTM A420/A420M-04 ? ? ? ? 低温下用锻制碳素钢和合金钢管配件? ? ? ? Standard Specification for Piping Fittings of Wrought Carbon Steel and Alloy Steel for Low-Temperature ServiceASTM A421/A421M-02 ? ? ? ? 预应力混凝土用无涂层消除应力钢丝的技术规范? ? ? ? Standard Specification for Uncoated Stress-Relieved Steel Wire for Prestressed ConcreteASTM A423/A423M-95(2000) ? ? ? ? 无缝和电焊低合金钢管? ? ? ? Standard Specification for Seamless and Electric-Welded Low-Alloy Steel TubesASTM A424-00 ? ? ? ? 搪瓷用钢薄板? ? ? ? Standard Specification for Steel, Sheet, for Porcelain EnamelingASTM A426/A426M-02 ? ? ? ? 高温用离心铸造的铁素体合金钢管? ? ? ? Standard Specification for Centrifugally Cast Ferritic Alloy Steel Pipe for High-Temperature ServiceASTM A427-02 ? ? ? ? 冷轧和热轧用锻制合金钢辊? ? ? ? Standard Specification for Wrought Alloy Steel Rolls for Cold and Hot ReductionASTM A428/A428M-01 ? ? ? ? 钢铁制品上铝覆层重量的测试方法? ? ? ? Standard Test Method for Weight [Mass] of Coating on Aluminum-Coated Iron or Steel ArticlesASTM A434-04 ? ? ? ? 热轧与冷精轧经回火及淬火的合金钢棒? ? ? ? Standard Specification for Steel Bars, Alloy, Hot-Wrought or Cold-Finished, Quenched and TemperedASTM A435/A435M-90(2001) ? ? ? ? 钢板的直射束纵向超声波检验? ? ? ? Standard Specification for Straight-Beam Ultrasonic Examination of Steel PlatesASTM A436-84(2001) ? ? ? ? 奥氏体灰口铁铸件? ? ? ? Standard Specification for Austenitic Gray Iron CastingsASTM A437/A437M-01a ? ? ? ? 高温用经特殊处理的涡轮型合金钢螺栓材料? ? ? ? Standard Specification for Alloy-Steel Turbine-Type Bolting Material Specially Heat Treated for High-Temperature ServiceASTM A439-83(1999) ? ? ? ? 奥氏体可锻铸铁铸件? ? ? ? Standard Specification for Austenitic Ductile Iron CastingsASTM A447/A447M-93(2003) ? ? ? ? 高温用镍铬铁合金钢铸件(25-12级)? ? ? ? Standard Specification for Steel Castings, Chromium-Nickel-Iron Alloy (25-12 Class), for High-Temperature Service ASTM A449-04a ? ? ? ? 经淬火和回火的钢螺栓和螺柱? ? ? ? Standard Specification for Quenched and Tempered Steel Bolts and StudsASTM A450/A450M-04 ? ? ? ? 碳素钢管、铁素体合金钢管及奥氏体合金钢管? ? ? ? Standard Specification for General Requirements for Carbon, Ferritic Alloy, and Austenitic Alloy Steel TubesASTM A451/A451M-02 ? ? ? ? 高温用离心铸造的奥氏体钢管? ? ? ? Standard Specification for Centrifugally Cast Austenitic Steel Pipe for High-Temperature ServiceASTM A453/A453M-03 ? ? ? ? 具有同奥氏体钢相类似的膨胀系数、屈服强度为50-120Ksi(345-827MPa)的耐高温螺栓材料? ? ? ? Standard Specification for High-Temperature Bolting Materials, with Expansion Coefficients Comparable to Austenitic Stainless SteelsASTM A455/A455M-03 ? ? ? ? 压力容器用高强度碳锰钢板? ? ? ? Standard Specification for Pressure Vessel Plates, Carbon Steel, High-Strength ManganeseASTM A456/A456M-99(2003) ? ? ? ? 大型曲轴锻件的磁粉检查? ? ? ? Standard Specification for Magnetic Particle Examination of Large Crankshaft ForgingsASTM A459-97(2003) ? ? ? ? 镀锌平轧扁钢铠装带? ? ? ? Standard Specification for Zinc-Coated Flat Steel Armoring TapeASTM A460-94(2004)e1 ? ? ? ? 包铜钢丝绳标准? ? ? ? Standard Specification for Copper-Clad Steel Wire StrandASTM A463/A463M-02a ? ? ? ? 热浸镀铝薄钢板? ? ? ? Standard Specification for Steel Sheet, Aluminum-Coated, by the Hot-Dip ProcessASTM A466/A466M-01 ? ? ? ? 非焊接碳素钢链? ? ? ? Standard Specification for Weldless Chain ASTM A467/A467M-01 ? ? ? ? 机器链和盘旋链? ? ? ? Standard Specification for Machine and Coil Chain标准号? ? ? ? 标准中文名称? ? ? ? 标准英文名称。
- 1、下载文档前请自行甄别文档内容的完整性,平台不提供额外的编辑、内容补充、找答案等附加服务。
- 2、"仅部分预览"的文档,不可在线预览部分如存在完整性等问题,可反馈申请退款(可完整预览的文档不适用该条件!)。
- 3、如文档侵犯您的权益,请联系客服反馈,我们会尽快为您处理(人工客服工作时间:9:00-18:30)。
A catastrophic aluminium-alloy dust explosion in China G.Li a,*,H.-X.Yang a,C.-M.Yuan a,R.K.Eckhoff a,ba Fire&Explosion Protection Laboratory,Northeastern University,Shenyang,Chinab Dept.Physics and Technology,University of Bergen,Bergen,Norwaya r t i c l e i n f oArticle history:Received1July2015Received in revised form11November2015Accepted15November2015 Available online2December2015Keywords:Accidental dust explosions Secondary dust explosions Aluminium product polishing Waste metal dustsDustfilters a b s t r a c tOn August2,2014a catastrophic dust explosion occurred in a large industrial plant for polishing various aluminium-alloy parts in Kunshan,China.The explosion occurred during manual polishing of the sur-faces of aluminium-alloy wheel hubs for the car industry.75people lost their lives immediately and another185were injured.Subsequently,71of the seriously injured also died,which increased the total loss of lives to146.The direct economic loss of was351million yuan.This is probably one of the most serious dust explosion catastrophes known apart from some very major coal dust explosion disasters in coal mines.Based on measurements of explosion parameters of dust samples collected on the explosion site and on-site investigations and interviews,it was concluded that a series of consecutive explosions was initiated in one of the external dustfilters.Then it propagated into the main building via the dust extraction ducting and further onto the secondfloor.At the same time the propagating in-house dust flame was sucked into the ducts leading to seven other external dustfilters,which also exploded.On the basis of investigations on site after the explosion and subsequent laboratory experiments and data analyses it was concluded that the explosion was most probably initiated by self-ignition of contaminated aluminium-alloy dust in the dust collecting barrel below the external bagfilter unit in which the initial primary explosion took place.General ignorance of the potential risk of dust explosions in industries producingfine metal dusts as a low-mass waste by-product is the most probable basic root cause of this catastrophic accident.Therefore, avoiding accumulation of deposits of such dusts indoors by good regular housekeeping and other means is regarded the most effective and practical way of loss prevention due to metal dust explosions in such plants.In addition,explosion isolation between dust collecting systems and workshops appears to be another important measure towards minimizing the consequences of such explosions.©2015Elsevier Ltd.All rights reserved.1.IntroductionAs pointed out by Eckhoff(2005)the threat of accidental dust explosions remains a persistent hazard in the process industries.Abbasi and Abbasi(2007)reviewed the main dust explosions that have occurred world-wide during the period1911e2004.It may appear that during the last decade only two other major catastrophic dust explosions have occurred worldwide,which are comparable to the one discussed in the present paper as regards losses of lives.Thefirst occurred in USA on February6,2008.A catastrophic dust explosion andfire devastated the Imperial Sugar refinery plant in USA,causing14deaths and38injuries(CSB,2009).The other occurred in China on Feb.24,2010in the maize starch production plant of Qianhuangdao Lihua Starch.According to State Administration of Work Safety(2014)21employees lost their lives and47others were injured in this disaster.The catastrophic dust explosion accident to be discussed in the present paper is probably one of the most serious industrial dust explosions in modern history apart from some very major coal dust explosion disasters in coal mines.The site of the explosion was a plant named Zhong Rong Metal Products Co(ZRMP),located in Kunshan,China.The plant was mainly polishing surfaces of various metal parts.In the morning of August2,2014a catastrophic aluminium-alloy dust explosion swept through a factory building where aluminium-alloy wheel-hubs for the car industry were polished manually.75people lost their lives more or less imme-diately and another185were injured.Subsequently,71of the seriously injured also lost their lives,which increased the total loss*Corresponding author.E-mail address:ligang@(G.Li).Contents lists available at ScienceDirectJournal of Loss Prevention in the Process Industries jo urnal homepag e:/locate/jlp/10.1016/j.jlp.2015.11.0130950-4230/©2015Elsevier Ltd.All rights reserved.Journal of Loss Prevention in the Process Industries39(2016)121e130of lives to 146.The direct economic loss of was 351million yuan.This accident once again has reminded the world of the importance of acknowledging the hazard of industrial dust explo-sions,and also to acknowledge the need for continually updating the knowledge and awareness required for preventing such catas-trophes in the future.2.The plant that was struck by the explosion 2.1.Sketch of the workshop buildingThe explosion occurred in a two-storey reinforced concrete-frame-structure work-shop building of length 44m (from north to south)and width 24m (from east to west).The two storeys comprised a basement with concrete floor and a first floor above it.The height between floor and ceiling was 4.5m in both storeys.The total floor area was 2112m 2.The roof of the building (and hence also of the first floor)was a light steel beam structure covered by coloured steel panels.The external and internal walls of the building were of brick.The two floors were connected by open stair cases at each end (north and south)of the building.On both sides of the eastern wall there was a 4m by 4m steel-panel sliding door leading to the outside.The floor of the first storey (i.e.the basement of the building)was of concrete.2.2.Process equipment layoutThe 32polishing production lines (16lines on the basement and 16lines on the first floor)were arranged in parallel in the south-north direction.Along each line there were 12working stations,as indicated in Fig.1.On the day before the accident,a total of 29production lines were in operation,13on the basement and 16in the first floor.348workers were on duty.Polishing operations were conducted manually as shown in Fig.2.Electric grinding guns were the main tools.According to the finish smoothness required different grades of grinding heads and/or emery papers were used.2.3.Dust collection system and processing equipmentAccording to the documents investigated,8sets of dust collec-tion systems were installed in March 2006outside the main factory building to serve the polishing processes on the two floors.Therefore,every two production lines shared a set of de-dusting system.Every two pieces of dust extraction ducts were merged by a T-joint into one main 450mm F main duct leading to the bagfilter.At each work location along a production line there was a 500mm Â200mm,which meant that each dust extraction system collected the dust from the 48work locations.According to the design of the bag filters in the dust collectors the bags were supposed to be cleaned by mechanical shaking at intervals.However,after the explosion accident survivors told that,due to breakdown of the electric motor,the automatic shaking systems had been out of operation for a long time.Instead workers had to shake the bags manually every morning before commencing work.This process was called “shaking ash ”.The air flow for each of the 8main dust extraction lines was produced by a suction fan mounted on the clean side of the bag filter unit,and all the 8air flows were joined in a main discharge duct to the atmosphere.No special requirements addressing a possible dust explosion hazard had been enforced on selection and installation of all the electrical equipment used in the plant.Neither the dust collectors or the dust extraction ducting,nor all electrical sockets and power distribution cabinets had been adequately earthed.3.The explosion catastrophe 3.1.ExtentIn the morning of August 2,2014,at about 7:34a.m.,when normal polishing activity has been going on for half an hour,a strong explosion occurred.A survivor stated that he was polishing his second hub at the moment of the first explosion.A video camera located outside another factory building about 500m away from the building that was stuck by the explosion revealed a sequence of several explosions lasting for about 5e 7s,including a distinct series of 8successive explosions.These 8explosions were identi fied on the video recording as violent “mushroom-shaped ”dust/smoke clouds being blown up from each of the 8dust collectors.All the windows in the first floor of the building that exploded were shattered and blown to the outside,and the window frames were completely deformed.Two thirds of the southern wall of the building collapsed,as illustrated in Fig.3.Window frames were blown out of the eastern wall,and two air conditioners located at this wall got partly detached from the wall,as shown in Fig.4.The blasts also lifted some of the light steel-panel roof of the second floor,and broke all the windows.Surprisingly,the glass was found scattered on the ground floor inside the building.Almost all process equipment in the workshop was destroyed as shown in Fig.5.Fig.1.Production lines with workstations.Fig.2.Workers on duty at the work stations.G.Li et al./Journal of Loss Prevention in the Process Industries 39(2016)121e 130122The dust extraction ducts inside the building were basically intact,but the duct connected to the 1#filter suffered serious damage and got detached from the T-joint.As Fig.6shows,a duct branch within the workshop was broke into three parts with the middle part of it having been torn apart.All the dust filters (1#,3#,5#and 7#)collecting dust from the first floor were more severely damaged than those (2#,4#,6#and 8#)collecting dust from the second floor.In particular dust filter #1was blown entirely apart.A signi ficant detail is that the dust col-lecting barrel of this filter had its bottom completely blown out,as shown in Fig.7.The blue arrow shows the corroded hole in the barrel to be discussed later in this paper.3.2.Loss of life,injuries,and financial lossesOn the first day of the catastrophic explosion 75workers lost their lives,whereas 185were injured.Most of the dead corpses carbonized,and all the injured persons had symptoms of respira-tory tract burns.During the days and weeks after the catastrophe another 71workers died,which means that finally the total loss of lives amounted to 146,whereas the total number of injured workers was 114.The direct financial losses caused by this explo-sion disaster amounted to 351million yuan.4.Analysis of the explosion development 4.1.Identi fication of the exploding materialThe investigation revealed that the aluminium dust generated during polishing of aluminium alloy hubs was the onlypossibleFig.3.Collapsed and destroyed part of southernwall.Fig.4.Destroyed eastern wall and airconditioners.Fig.5.Destroyed process lines on the second floor.Fig.6.Detailed view of damagedducts.Fig.7.Dust collecting barrel of 1#filter with its bottom blown off.G.Li et al./Journal of Loss Prevention in the Process Industries 39(2016)121e 130123material that could have caused the explosion accident.The explosive properties of clouds in air of aluminium dust have been investigated by many authors,e.g.Nifuku and Katoh(2001) and Marmo et al.,(2004).In NFPA(2008)aluminium dust is ranked among the most explosible metal dusts.Some data collected by CSB(2003)indicates that nearly25%of all dust explosions in the United States between1980and2005involved metal dusts,and that aluminium dusts accounted for the majority of these events. Metal dusts account for about19%of all dust explosions worldwide.4.2.Identification of the site of explosion initiationExamination of the explosion site revealed that the wall next to the southern-side stairwell leading to the secondfloor(close to the #1dust collector)showed clear traces of a large number of particles having been ejected upwards from the bottom,as shown in Fig.8.This would indicate that the blast wave swept from thefirst floor to the secondfloor along this wall.The fact that the northern side stair railing collapsed from south to north proved that the blast wavefirst propagated from the south to north along thefirstfloor. This agrees with the assumption that the starting point of the in-door propagation from south to north was the production line corresponding to the#1filter,because the dust extraction duct of filter#3close to the#1filter duct suffered a shift from south to north,as shown in Fig.9.Also,several of the“spiro”ducts in the dust extraction and ventilation systems on thefirstfloor showed signs of having been moved from south to north.The closer an item was to the#1filter ducts,the more obvious was this northwards displacement.As already said above,the indoor dust extraction duct connected to the #1dust collector was broken into3separate sections at theflanges, as indicated in Fig.6.The end of the pipeline suffered the most serious damage away from the dust collector to east,as shown in Fig.10.This kind of displacement was not found for the other dust extraction ducts.It was concluded,therefore that the explosion originated in the#1 dust collector outside the western wall of the building,and spread from there to the interior of the1stfloor of the workshop,causing eastward displacement of dust extraction ducts.The1#dustfilter suffered the most serious damage among the8 dust collectors.The cubicalfilter enclosure was completely torn open,and the conical hopper was partly damaged.Theflange connecting the hopper to the dust collecting barrel below was torn apart,and the barrel was separated from the hopper,as shown in Figs.11and12.4.3.Analysis of path of blast wave propagationAs already said above,an external video monitor revealedaFig.8.Vertical upwards traces of aluminium dust particles ejected along the southernwall of thebuilding.Fig.9.#3duct moved to thenorth.Fig.10.End of#1duct moved to theeast.Fig.11.Totally damaged#1dustfilter.G.Li et al./Journal of Loss Prevention in the Process Industries39(2016)121e130124series of successive explosions extending over about 6s,from the appearance of the first “mushroom ”-shaped cloud at dust filter #1till the appearance of the last cloud at one of the other filters.According to the evidence found on site the blast wave that was initiated in filter #1propagated,followed by the propagating dust flame,upstream inside the dust extraction duct and entered the first floor working lines,from where it exited into the workrooms via the dust extraction hoods above the working tables,and eventually ignited the dispersed deposited dust on the floor near both the #1and #2production lines,causing major escalating secondary explosions.Then these explosions and associated dust flames propagated the entire length from north to south along the first floor and got sucked into the dust extraction ducts leading to the 3#,5#,and 7#dust filters,triggering 3further major filter explosions.The most probable blast wave propagation path on the first floor is indicated in Fig.13.While sweeping through the first floor,the blast wave,driven by the secondary explosions had also propagated through the south-ern and northern stairs upwards to the second floor.There it destroyed part of the second floor roof and dispersed the dust deposited on the production lines,the floor etc.causing another extensive secondary dust explosion sweeping through the entire secondary floor.Finally the flame was sucked into 2#,4#,6#and 8#dust filters via the second floor production lines,which caused the four further major filter explosions with the “mushroom ”shaped dust clouds being blown to the outside from the filter enclosures.It should be noted that the dust extraction ducts connected to the 1#dust collector were torn into three parts at the connecting flanges.Each of the three ducts has 8sucking holes located sym-metrically along both sides of the duct.The layout of the ducting system connected to the 1#bag filter unit is shown in Fig.14.The thickness of all duct walls was about 1mm.The venting was provided by two opposite 100mm F openings for every 1m duct length.This would give quite generous venting,although the vent area was somewhat less than that required by NFPA (2008a).In the actual explosion only the middle section of the duct was torn apart by the explosion overpressure in the duct,as shown in Fig.6.A likely reason for the maximum pressure occurring in the middle section could be acceleration of the de flagrating flame in the duct due to flow-induced turbulence,causing pressure piling and enhanced explosion pressure.Under given circumstanced such de flagrations can transit to detonation-like explosions,and this possibly occurred midway along the duct.5.Further analysis5.1.Conditions for dust explosion occurrenceAs pointed out by Amyotte (2013)it is well known that 5basic conditions have to be ful filled simultaneously for a dust explosion to occur:presence of a combustible dust in a finely divided form as a cloudpresence of an oxidant atmosphere presence of an ignition sourceconcentration of dust in the cloud within the explosive range (between the minimumexplosive and maximum explosive concentration)some degree of con finement of the dustcloudFig.12.Torn receiving hopper of #1dust filter.Fig.13.Most probable course of blast wave propagation on the first floor.yout with dimensions of the dust extraction ducting connected to the 1#bag filter unit.G.Li et al./Journal of Loss Prevention in the Process Industries 39(2016)121e 1301255.2.Characteristics of aluminium-alloy dust from hub finishing processThe particle diameter distribution of a sample of aluminium-alloy dust collected from the explosion site was measured using a laser-based particle size analyser.The results are given in Table 1.According to the documents from the Zhong Rong Metal Prod-ucts Co.the chemical composition of the wheel hubs that were finished in the plant on the day of the explosion was as shown in Table 2.This table also shows the chemical composition of the metals in the collected dust sample (Table 1).The collected dust also contained some other components (e.g.polishing paste and sandpaper fragments)but these are not included in Table 2.As can be seen,the percentages by mass of Si and Fe in the collected dust were signi ficantly higher than in the hubs.Explosion parameters for the collected dust samples were determined in the Fire &explosion protection laboratory at Northeastern University,Shenyang,China.Before determining the explosion parameters of the dust the impurities (traces of polishing paste and sandpaper fragments)were removed.The results ob-tained are shown in Table 3.The three first parameters were determined in a 20L closed standard explosion bomb,the other two in other standardized tests.5.3.Formation of the initial explosive dust cloudThe total amount of dust generated per day during the hub polishing was rather small.According to survivors the dust barrels at the bottom of the dust collectors were normally emptied twice a week,and the mass of dust collected in one barrel would then not be more than about 30kg.The volume of the dust fan that operated 12h a day for one filter was about 22,300standard m 3per hour.Therefore the average dust concentration in the clouds entering the filters was about 0.1g/m 3.As shown in Table 3this is less than one percent of the minimum explosive concentration (MEC)of the sample of the collected dust.Consequently,even if there has been an ignition source in the dust cloud flowing through the dust extraction system,a dust explosion could not have been initiated inside the flowing cloud.The dust concentration in the bag filter would have a pro-nounced maximum during the regular bag cleaning sequences of the mechanical vibrating system.But as mentioned before,the vibrating system of the filter close to which the explosion most probably started was out of operation at the time of the explosion because of breakdown of an electric motor.Therefore the workers had to clean the bags by shaking the bag holder every morning before commencing work.The explosion occurred about 30min after the production had started.Fig.15indicates the zone in the “dirty ”side of the filter enclosure,where excessive,explosive dust concentrations would occur during the falling down of the sticked dusts from the filter-bag.5.4.Identi fication of a likely ignition sourceAt the outset one has to consider several possible sources for ignition of the dust cloud on the “dirty ”side in the dust filter enclosure,including:Friction sparkElectrostatic discharge Electrical fault Thermite reactionSelf-heating in deposit of aluminium-alloy dust from hub polishing5.4.1.Friction sparkWhen using an emery wheel rotating at high speed to polish hard metals of metal alloys a beam of bright visible friction sparks is normally generated.Such sparks are burning particles of highTable 1Particle diameter distribution of sample of aluminium-alloy dust.Cumulative volume %of particles smaller than D D3a D10D50D90D97Dav Particle diameter (m m)5.27.619455923aD3¼5.2means that the volume of particles in the dust having particle diameters smaller than 5.2m m was 3%of the total volume.Table 2Chemical composition (%by mass)of metals in a raw hub and in dust sample.ElementAl Si Mg Fe Ti Raw hub 91.2e 92.3 6.5e 7.50.20e 0.40&0.20&0.20Dust sample88.410.20.110.550.0Table 3Explosion parameters for the dust sample.Parameters MEC (g/m 3)P max (bar,g)K St(bar $m $s À1)MIE (mJ)MITC ( C)Results40112507e 11540MEC is the minimum explosive dust concentration.P max is the maximum explosion pressure (closed explosion bomb of 20L).K St is the maximum rate of rise of explosion pressure.MIE is the minimum ignition energy of the dust cloud (electric spark).MITC is the minimum ignition temperature of clouds of thedust.Fig.15.Possible zone for formation of explosive dust clouds in the filter enclosure during manual bag cleaning.G.Li et al./Journal of Loss Prevention in the Process Industries 39(2016)121e 130126temperatures.Li et al.,(2013)found that such sparks from friction between Ti and an emery wheel can easily ignite a methane/air mixture.However,when using an aluminium alloy instead of ti-tanium no ignition was observed.Eckhoff(2003)describes dust cloud ignition experiments by metal particle sparks from short single impacts and pointed out that ignition by such impacts may seem less likely than believed by many in the past,unless the sparking metal is titanium or zirconium.When an aluminium-alloy wheel hub from the explosion site was polished in the laboratory by using a hand held electric grinder, no sparks could be seen by the naked eye against a black back-ground.The temperatures of both the friction spot and hot particles were recorded by a VH-420Thermal Imager(low band LW, 7.5e14m m)produced by Infratec in Germany.The friction spot was found to be the hottest area where the highest temperature value was133.5 C,as indicated in Fig.16.Even if the temperature of the hot particles produced by this polishing process had been consid-erably higher than maximum temperature found in this test,it is difficult to envisage that the particle would be an ignition source when they eventually,after a long period of travel and cooling, reached the explosive dust cloud in the dustfilter.5.4.2.Electrostatic dischargeThe phenomenon of electrostatic charge accumulation on pro-cess plant,powders and dust particles is well documented in the literature.The amount of charge generated depends on many things,including the relative humidity of the air within the process equipment,the particle size,chemical composition of the particles, and the nature of contacting surfaces.There are several types of electrostatic discharges,viz.corona discharges,brush discharges, propagating brush discharges,bulk surface discharges and spark discharges.Apart from corona and brush discharges,all the elec-trostatic discharges mentioned can in principle give rise to dust explosions in air.The minimum ignition energy of the dust sample collected on site,as determined in a standard laboratory test,was7e11mJ as shown in Table3.This is a comparatively low value,and at the outset one cannot neglect the possibility of an electrostatic spark discharge being the ignition source in the present case.However, due to the high electric conductivity of the wheel hub dust it would probably be difficult to accumulate enough electrostatic charge by tribo electric processes to produce even a spark discharge of only about10mJ.Moreover,it had been raining continuously for several days before the explosion accident,and light rain persisted even right up to the moment of the explosion.The relative humidity of the air was97%at the average ambient temperature of29 C.Considering these factors,an electrostatic discharge is unlikely to have been the ignition source of the present explosion disaster.5.4.3.Electrical faultA faulty electrical circuit,a damaged electrical wire or another electrical component can cause sparking or arcing that can defi-nitely ignite explosive dust clouds.However,in the dustfilter in which the explosion most probably started there were no other electrical components than the defect and out-of-operation electric motor intended for automatic periodic shaking of thefilter bags. Furthermore,this motor was on the“clean”side of thefilter.Therefore,an electrical fault is not considered a likely ignition source in the present case.5.4.4.Thermite reactionWhen aluminium or aluminium alloys gets in contact with iron oxide at a high temperature,a strong exothermal reaction can result,releasing sufficient energy to ignite mostflammable mix-tures.This exothermal reaction is called a“thermite reaction”and the reaction equation is:Fe2O3þ2Al/Al2O3þ2Feþheat(1) Survivors of the explosion catastrophe discussed in the present paper said that they usually polished their blunt iron scissors at the same work table as they normally polished the wheel hubs.As seen in Table2,the element analysis of a sample of the dust from the actual hub polishing operation showed an iron content of0.55%by weight.However,nearly2/3of this was from other sources than the aluminium-alloy hubs.In the case of the temperature rise caused by self-heating re-action,small amount of ferric oxide and aluminium in the polished aluminium dust could in principle give rise to a thermite reaction that would liberate some heat and increase the likelihood of self-ignition in the dust deposit.5.4.5.Self-heating/self-ignition in the deposit of aluminium-alloy dust in the dust-collecting barrel below the dustfilterAs shown in Table1the particles produced by polishing the aluminium-alloy hubs were relatively small,with the median (volume based)diameter being only19m m.Due to some organic material added in the polishing process the deposited dust became quitefluffy,as indicated by Fig.17.Tests showed that the poured bulk density of thisfluffy dust was only about520kg/m3.This would indicate that the heat conductivity of deposits of this dust would also be considerably lower than that of deposits of pure aluminium-alloy dust.Many metals can react exothermally with water.Inside a deposit of metal dust/powder the initial reaction rate may be very slow,but if the heat dissipation into the surrounding parts of the dust deposit is sufficiently low,the self-heating reaction can accelerate right up to self-sustained exothermal combustion.Birks and Alabi(1986) investigated the special problem of self-ignition in piles of direct-reduced iron when the piles were exposed to water.They found that auto-ignition starts with aqueous“corrosion”reactions and becomes completely developed when stable high temperature oxidation isestablished.Fig.16.Thermal image of hand hold grinder polishing an aluminium wheel hub.G.Li et al./Journal of Loss Prevention in the Process Industries39(2016)121e130127。