Fibre-Bragg-gratings-in-structural-health-monitoring—Present-status-and-applications_Sensors-and-
蛋白质二级结构预测软件
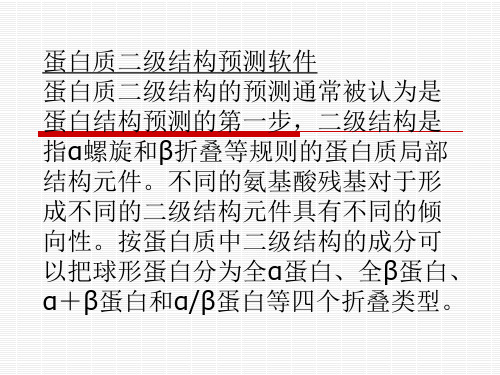
通过EMAIL进行序列检索 当网络不是很畅通时或并不急于得到较多数量的蛋白质序列时, 可采用EMAIL方式进行序列检索。 蛋白质基本性质分析 蛋白质序列的基本性质分析是蛋白质序列分析的基本方面,一 般包括蛋白质的氨基酸组成,分子质量,等电点,亲水性,和 疏水性、信号肽,跨膜区及结构功能域的分析等到。蛋白质的 很多功能特征可直接由分析其序列而获得。例如,疏水性图谱 可通知来预测跨膜螺旋。同时,也有很多短片段被细胞用来将 目的蛋白质向特定细胞器进行转移的靶标(其中最典型的例子 是在羧基端含有KDEL序列特征的蛋白质将被引向内质网。 WEB中有很多此类资源用于帮助预测蛋白质的功能。
特殊结构或结构预测 COILS http://ulrec3.unil.ch/software/COILS_ form.html MacStripe /matsudaira/m acstripe.html
与核酸序列一样,蛋白质序列的检索往往是进行相 关分析的第一步,由于数据库和网络技校术的发展, 蛋白序列的检索是十分方便,将蛋白质序列数据库 下载到本地检索和通过国际互联网进行检索均是可 行的。 由NCBI检索蛋白质序列 可联网到: “:80/entrz/qu ery.fcgi?db=protein”进行检索。 利用SRS系统从EMBL检索蛋白质序列 联网到:/”,可利用EMBL 的SRS系统进行蛋白质序列的检索。
跨膜区域 TMpred: /software/TMPRED_form.ht ml 预测蛋白质的跨膜区段和在膜上的取向,它根据来自SWISSPROT的跨膜蛋白数据库Tmbase,利用跨膜结构区段的数量、 位置以及侧翼信息,通过加权打分进行预测。Tmpred的Web 界面十分简明。用户将单字符序列输入查询序列文本框,并可 以指定预测时采用的跨膜螺旋疏水区的最小长度和最大长度。 输出结果包含四个部分:可能的跨膜螺旋区、相关性列表、建 议的跨膜拓扑模型以及代表相同结果的图。
多器官纤维化 英语

多器官纤维化英语Fibrosis is a pathological condition characterized by the deposition of excess fibrous collagen in various tissues, leading to organ dysfunction and failure. Multi-organfibrosis refers to the simultaneous or sequential development of fibrosis in different organs, such as liver, lung, heart, kidney, and skin, among others. In this article, we will discuss the causes, symptoms, diagnosis, treatment, and prevention of multi-organ fibrosis.Step 1: Causes of Multi-organ FibrosisThe exact cause of multi-organ fibrosis is not well understood. However, it is believed to be a complex, multi-factorial disease that involves genetic, environmental, and lifestyle factors. Genetic factors can play a role in the susceptibility and severity of fibrosis, while environmental factors such as exposure to toxins, infections, and chronic inflammation can trigger and perpetuate the fibrotic process. Lifestyle factors, such as smoking, alcohol consumption, and poor diet, can also contribute to the development of multi-organ fibrosis.Step 2: Symptoms of Multi-organ FibrosisThe symptoms of multi-organ fibrosis vary depending on the affected organs. In general, patients may experience fatigue, shortness of breath, swelling, pain, and loss of function in different organs. For example, patients with lung fibrosis may have persistent cough, difficulty breathing, and chest discomfort, while those with liver fibrosis may have abdominal pain, jaundice, and digestive problems. Patientswith multi-organ fibrosis may also have co-existing conditions, such as hypertension, diabetes, and autoimmune disorders.Step 3: Diagnosis of Multi-organ FibrosisDiagnosis of multi-organ fibrosis often requires a comprehensive evaluation of the patient's medical history, physical examination, and laboratory tests. Imaging studies, such as chest X-ray, CT scan, or MRI, can reveal the extent and location of fibrosis in different organs. Blood tests can also detect abnormal liver, kidney, or heart function, aswell as markers of inflammation and fibrosis. In some cases,a biopsy of the affected organ may be necessary to confirmthe diagnosis and determine the severity of fibrosis.Step 4: Treatment of Multi-organ FibrosisThe treatment of multi-organ fibrosis involves a multidisciplinary approach that addresses the underlying causes, complications, and symptoms of the disease. There is currently no cure for fibrosis, and the goal of treatment isto slow down or prevent the progression of fibrosis, improve organ function, and enhance the quality of life of the patient. Treatment options may include medications, such as immunosuppressants, anti-fibrotic agents, and antioxidants,as well as lifestyle modifications, such as smoking cessation, weight loss, and exercise. Patients with advanced fibrosismay require organ transplantation or other surgicalprocedures to replace or repair the damaged organs.Step 5: Prevention of Multi-organ FibrosisPrevention of multi-organ fibrosis involves minimizingthe risk factors and promoting healthy lifestyle habits. This includes avoiding exposure to toxins, infections, and chronic inflammation, as well as maintaining a balanced diet, regularexercise, and stress management. It is also important to undergo regular health screenings and follow-up appointments with healthcare professionals to detect and treat the early signs of fibrosis before they become irreversible.In conclusion, multi-organ fibrosis is a complex and debilitating disease that affects multiple organ systems and can be caused by a variety of genetic, environmental, and lifestyle factors. Timely diagnosis, appropriate treatment, and prevention measures are essential to reduce the burden of fibrosis on individuals and society as a whole. With ongoing research and innovation, we may one day discover a cure for multi-organ fibrosis and improve the lives of millions of people worldwide.。
大应变光纤Bragg光栅传感器的研究

大应变光纤Bragg光栅传感器的研究吴垄;李川;李英娜;许晓平;许江淳;陈焰【摘要】在通信光纤的长期允许应变为3000 με的基础上,研制了一种测量应变范围为0~6000 με的大应变光纤Bragg光栅传感器.在外加应力的作用下,固定支点的相对位置发生变化,从而带动应变管发生轴向形变,导致了粘贴在调节管两端的光纤Bragg光栅按比例产生了Bragg波长移位.通过荷载,对大应变光纤Bragg光栅传感器进行拉伸,实验表明,该传感器的载荷响应灵敏度为1.783 pm/kg,应变灵敏度为0.685 pm/με,最大应变可达5 250με.%The fiber Bragggrating(FBG)sensor with the stain of 0 ~6 000 (xe is developed based on the long-term stain in fiber which is less than 3 000 με. By the external forces, the relative position of the fixed pivots are changed,which causes the axial deformation of the strain tube leading to the Bragg wavelengths shift in proportion of FBG attached at two ends of the adjusting tubes. Through loading, the sensor is stretched. The experimental results show that the response sensitivity of the sensor is 1. 783 pm / kg, the stain sensitivity is 0. 685 pm/με, and the maximum stain range could be 5 250με.【期刊名称】《传感技术学报》【年(卷),期】2011(027)008【总页数】5页(P1141-1145)【关键词】应变传感器;光纤Bragg光栅;应变减敏;Bragg波长;调节管;紧固管【作者】吴垄;李川;李英娜;许晓平;许江淳;陈焰【作者单位】昆明理工大学信息工程与自动化学院,昆明650500;昆明理工大学信息工程与自动化学院,昆明650500;昆明理工大学信息工程与自动化学院,昆明650500;昆明理工大学信息工程与自动化学院,昆明650500;昆明理工大学信息工程与自动化学院,昆明650500;昆明理工大学信息工程与自动化学院,昆明650500【正文语种】中文【中图分类】TP212.1;TN253目前,通信光纤在1%的筛选应变作用下,制作光纤Bragg光栅的标准通信光纤的短期允许应变可达到10 000 με,而长期允许应变为3 000 με[1-2]。
CFTR与囊性纤维化

第26卷第2期2006年4月国际病理科学与临床杂志I nternati onal Journal of Pathol ogy and ClinicalMedicineVol.26 No.2Ap r. 2006 CFT R与囊性纤维化王 瑞,李学军(北京大学基础医学院药理系,北京100083)[摘要] 囊性纤维化跨膜传导调节因子(CFTR)是一种c AMP激活的ATP门控性氯离子通道,表达于气道,消化道和生殖道上皮细胞的顶部质膜中。
囊性纤维化(CF)是白人中最常见的遗传性疾病之一,由CFT R基因突变造成。
对CFTR基因的破译使人们进一步了解CF的发病机制,并为该疾病的诊断提供了新的线索。
[关键词] 囊性纤维化; 囊性纤维跨膜电导调节因子; ATP结合盒; △F508; 基因疗法; 药物治疗[中图分类号] Q71 [文献标识码] A [文章编号] 167322588(2006)022*******CFTR and cysti c f i brosisWANG Rui,L I Xue2jun(D epart m ent of Phar m acology,School of B asic M edical Sciences,Peking U niversity,B eijing100083,China)[Abstract] The cystic fibr osis trans me mbrane conductance regulat or(CFT R)is a c AMP2activa2 ted and ATP2gated Cl-channel exp ressed in the ap ical p las ma me mbrane of ep ithelial cells in the air2 ways,digestive and rep r oductive tracts.Cystic Fibr osis(CF),caused by mutati ons in the CFT R gene,is one of the most common inherited dis orders of white populati ons.The identificati on of the CF gene led us t o a further understanding of the CFT R structure and functi on,the mutati onal basis as well as the com2 p lexity of the disease.[Key words] cystic fibr osis(CF); cystic fibr osis trans me mbrane conductance regulat or (CFTR); ATP binding cassette(ABC); deltaF508; gene therapy; drug treat m ent[In t J Pa thol C lin M ed,2006,26(2):0142204] 囊性纤维化(cystic fibr osis,CF)是一种致命的常染色体隐性疾病,主要临床症状为慢性梗阻性肺部病变,是白人中最常见的遗传性疾病之一。
弹性纤维性假黄瘤病证

病情ห้องสมุดไป่ตู้制定个体化治疗方案。
PART 03
病理学特征与鉴别诊断
病理学改变及分子机制
病理学改变
弹性纤维性假黄瘤的病理学改变主要为弹性纤维的变性和断裂,导致皮肤、血管 壁等组织器官的结构和功能异常。
分子机制
该病的发生与ABCC6基因突变有关,该基因编码一种跨膜转运蛋白,参与细胞内 外的物质转运和信号传导。基因突变导致转运蛋白功能丧失,进而引发弹性纤维 的代谢异常。
诊断方法
根据皮肤病变特点,结合组 织病理学检查,如皮肤活检 发现弹力纤维变性、断裂等 特征性改变,可明确诊断。
视网膜病变特点与检查手段
视网膜病变特点
早期可出现视网膜血管迂曲、扩张, 随病情进展可出现视网膜出血、渗出 、水肿等改变,严重时可导致视网膜 脱离、视力丧失。
检查手段
眼科常规检查如视力、眼压、裂隙灯 检查等,结合眼底镜检查、荧光素眼 底血管造影等影像学检查,有助于发 现视网膜病变并评估病情严重程度。
别名
该病也被称为Gronblad-Strandberg综合征,弹性假黄瘤等。
发病原因及机制
遗传因素
弹性纤维性假黄瘤主要由基因突变引起,相关基因包括 ABCC6等。这些基因突变导致弹性纤维的代谢异常,使其在 组织中沉积并引发疾病。
发病机制
弹性纤维是维持组织弹性和结构的重要成分。在弹性纤维性 假黄瘤患者中,异常的弹性纤维沉积在皮肤、眼睛、血管等 组织器官中,导致这些部位的结构和功能受损。
PART 04
治疗方案与药物选择
药物治疗策略及注意事项
药物治疗策略
针对患者的具体症状,采用相应 的药物进行对症治疗,如使用止 痛药、抗炎药等缓解症状。
注意事项
(整理)英语翻译MicrosoftWord文档

限制性核酸内切酶微生物能够在获得的其他来源的DNA中识别自己的DNA。
这种体系已经发展到识别自我和非自我,依靠细胞内部的两种酶:修饰性甲基化酶和限制性核酸内切酶。
这种甲基化酶在新生的双链DNA链上以特定的方式对各种核苷酸残基增加甲基集团。
这种识别序列在长度上通常有4到7个碱基对并且是回文序列,这就是说,这种序列在DNA一条链上与它互补链是相同的。
大多数生物体具有许多不同的修饰性甲基化酶。
限制性核酸内切酶作为修饰性酶识别相同的序列,但是代替甲基化,在序列上切割DNA。
然而,核酸内切酶不会切割自身序列但是会降解外援DNA。
这种识别和切开双链DNA特殊序列的特性已经成为从许多类型的微生物中切除DNA片段的基础。
不同种类的限制性内切酶被发现,被称为1,2,3,和4类型。
只有2类型对新的DNA 技术是重要的。
2类型限制性内切酶有特殊的重要性因为他们的特殊序列并且可以在精确的位置使双链DNA断裂。
用这种方式切开长的外源DNA分子成为短的片段也可以在质粒载体做一个单一缺口,在这位置上DNA片段可以被插入。
在一些酶的作用下,切口产生单一链末端并且对于一个给定的限制性核苷酸得到的所有片段的目的序列是相同的。
用这种方法,任一片段通过一种特殊的退火增殖可以与其他通过相同核酸内切酶切割的片段进行配对,因此创造出一个杂交分子。
自从来自大量细菌的限制性核酸内切酶发现以后,命名细菌的一套专业术语就被采用了。
宿主微生物的属名和种名由类型的首字母确定,并且种名的前两个字母用斜体字形成三个字母的缩写。
例如,E。
coli,Eco.菌株和类型用无下滑线记号鉴定并且核酸内切酶的号码用罗马数字—EcoRⅡ.不同的核算内切酶可以用于产生不同尺寸的DNA片段使不同的3‘或5’单链延长。
这种DNA片段可以用电泳纯化。
通过EcoR1水解PBR322的单一目的位点或者通过限制性核酸内切酶因为有一个单一的目标位点,改变环状制粒成为线状DNA分子。
这个位点可以通过有两个折叠对称轴的2型限制性核酸内切酶识别:它们可以是4,5,或6核苷酸序列。
mdm核酸结构

是以核苷酸为基本组成单位的生物大分 子,携带和传递遗传信息
Friedrich Miescher (1844~1895)
米歇尔Friedrich Miescher(1844-1895) 瑞士生物学家,生前工作于巴塞尔大学的生理 学研究室。以发现核酸而闻名世界
米歇尔小时候有严重的听力障碍,因此在童 年时代,尽管他非常聪明,但总是害羞并很内向。 他酷爱音乐,与其父亲一样是一个天才歌手,在 学校的学习成绩很好。1865年米歇尔成为一 名医学生,1868年获医学博士学位。但听力 问题是他成为临床医生的障碍
二、核酸完全水解的产物 (分子组成) NH2
嘌呤(purine)
N 7
8 9 NH
5 6 1N
43 2 N
N N
NH
N
腺嘌呤(adenine, A)
O
N NH
NH
N
NH2
鸟嘌呤(guanine, G)
二、核酸完全水解的产物 (分子组成)
O
嘧啶(pyrimidine)
5 4 3N 612
NH
NH2
四、RNA的分子结
构(一)RNA的分
类
分子量
含量
空间结构
信使
RNA:
400-4000 2% -5% 一条线型
(mRNA) 转移RNA:
73-93
10%-25% 三叶草型
(tRNA) 大小不一定 80%
磷酸酯键
糖
苷
键
腺苷酸(AMP)
三、组成核酸的基本单位—核苷酸
磷酸酯键
糖 苷 键
戊糖 (脱氧核糖)
脱氧腺苷酸(dAMP)
三、组成核酸的基本单位—核苷酸
核酸结构Watson Crick-1953Natue论文英汉对照

Nature VOL 171, page737. 2 April 1953A Structure for Deoxyribose Nucleic Acid脱氧核糖核苷酸的结构We wish to suggest a structure for the salt of deoxyribose nucleic acid (D.N.A.). This structure has novel features which are of considerable biological interest.A structure for nucleic acid has already been proposed by Pauling and Corey (1). They kindly made their manuscript available to us in advance of publication.Their model consists of three intertwined chains, with the phosphates near the fibre axis, and the bases on the outside.我们想推测出DNA 结晶的结构。
这些结构有许多新的为很多生物学家所吸引的特点.Pauling and Corey 已经提出过核苷酸的一个结构.他们在出版以前慷慨的把他们的手稿给我们看过。
他们的模型由三条相互缠绕的链组成,磷酸基团靠近中心轴,而碱基在外面。
In our opinion, this structure is unsatisfactory for two reasons:我们认为,这个模型有以下两个方面的不足(1) We believe that the material which gives the X-ray diagrams is the salt, not the free acid. Without the acidic hydrogen atoms it is not clear what forces would hold the structure together, especially as the negatively charged phosphates near the axis will repel each other. (2) Some of the van der Waals distances appear to be too small.我们相信 ,产生 X 射线衍射图的是盐 , 而不是自由核酸 . 在没有呈酸性的氢原子 、尤其是在相互排斥的 、带负电荷的磷酸基团都位于 DNA 长链中心轴附近的情况下 , 究竟靠什么力量将这种结构保持在一起呢 ?( 2)该模型中某些范德华键的距离似乎太小.Another three-chain structure has also been suggested by Fraser (in the press). In his model the phosphates are on the outside and the bases on the inside, linked together by hydrogen bonds. This structure as described is rather ill-defined, and for this reason we shall not comment on it.Fraser (在出版社里)曾提出过另一个三链的结构模型。
- 1、下载文档前请自行甄别文档内容的完整性,平台不提供额外的编辑、内容补充、找答案等附加服务。
- 2、"仅部分预览"的文档,不可在线预览部分如存在完整性等问题,可反馈申请退款(可完整预览的文档不适用该条件!)。
- 3、如文档侵犯您的权益,请联系客服反馈,我们会尽快为您处理(人工客服工作时间:9:00-18:30)。
Sensors and Actuators A 147(2008)150–164Contents lists available at ScienceDirectSensors and Actuators A:Physicalj o u r n a l h o m e p a g e :w w w.e l s e v i e r.c o m /l o c a t e /s naReviewFibre Bragg gratings in structural health monitoring—Present status and applicationsMousumi Majumder ∗,Tarun Kumar Gangopadhyay,Ashim Kumar Chakraborty,Kamal Dasgupta,D.K.BhattacharyaCentral Glass &Ceramic Research Institute (CSIR),196Raja S.C.Mullick Road,PO:Jadavpur University,Kolkata 700032,Indiaa r t i c l e i n f o Article history:Received 23August 2007Received in revised form 15April 2008Accepted 15April 2008Available online 22April 2008Keywords:Fibre-optic sensor Fibre Bragg gratings FBG strain sensorSensor for structural monitoring Sensor for compositea b s t r a c tIn-service structural health monitoring (SHM)of engineering structures has assumed a significant role in assessing their safety and integrity.Fibre Bragg grating (FBG)sensors have emerged as a reliable,in situ,non-destructive tool for monitoring,diagnostics and control in civil structures.The versatility of FBG sensors represents a key advantage over other technologies in the structural sensing field.In this article,the recent research and development activities in structural health monitoring using FBG sensors have been critically reviewed,highlighting the areas where further work is needed.A few packaging schemes for FBG strain sensors are also discussed.Finally a few limitations and market barriers associated with the use of these sensors have been addressed.©2008Elsevier B.V.All rights reserved.Contents 1.Introduction .........................................................................................................................................1512.Principle of operation of FBG sensors...............................................................................................................1512.1.Strain measurement using FBG sensors .....................................................................................................1512.2.Strain–temperature cross-sensitivity .......................................................................................................1523.FBG interrogation techniques.......................................................................................................................1524.FBG encapsulation techniques......................................................................................................................1525.Applications of FBG strain sensors in structural sensing...........................................................................................1545.1.Strain monitoring in civil infrastructure.....................................................................................................1545.1.1.Strain monitoring in reinforced concrete beams...................................................................................1555.1.2.Strain monitoring in smart beams.................................................................................................1565.1.3.Pile load monitoring ...............................................................................................................1565.1.4.Early-age cement shrinkage........................................................................................................1575.1.5.Moisture/humidity measurement in civil applications............................................................................1585.1.6.FBGs in geodynamic studies .......................................................................................................1595.1.7.Ultrasonic non-destructive testing of structural health using FBG................................................................1606.Conclusion...........................................................................................................................................161Acknowledgements.................................................................................................................................161References...........................................................................................................................................161∗Corresponding author.Fax:+913324730957.E-mail address:mousumi@cgcri.res.in (M.Majumder).0924-4247/$–see front matter ©2008Elsevier B.V.All rights reserved.doi:10.1016/j.sna.2008.04.008M.Majumder et al./Sensors and Actuators A147(2008)150–1641511.IntroductionStructural integration offibre-optic sensing systems represents a new interdisciplinary branch of engineering which involves the unique combination of laser-optics,fibre-optics,optoelectronics, microelectronics,artificial intelligence,composite material science and structural engineering.Fibre-optic sensors have a number of advantages over their electrical counterparts and are the primary candidates for complete sensing systems.Fibre Bragg grating(FBG)sensors have undergone a rapid development in the recent years following the observation of very-narrow-band reflection in the photosensitive core-region of Ge-doped silica opticalfibres[1]and itsfirst successful fabrication onfibre-core by exposure of a coherent two-beam UV interference pattern in1989[2].FBGs are immune to electromagnetic inter-ference(EMI)and ground loops.They are lightweight and have small physical dimensions,suitable for being embedded into,or attached to a structure.No wires are required to connect sensors to the control system as thefibres themselves act as both the sensing elements and the signal propagation conduit.FBG sensors offer a unique advantage of single ended connection to control systems because only reflected signals from the FBGs are important for demodulation.FBGs possess excellent resolution and range,water and corrosion resistance,ability to be multiplexed,immunity to harsh weather conditions,compact sensor and harness size,and reasonable cost per channel.Besides,wavelength encoded infor-mation is given by FBGs.Since wavelength is an absolute parameter, signal from FBG may be processed such that its information remains immune to powerfluctuations along the optical path.Thus,they offer a self-referencing,absolute measurement scheme.The FBG sensing technology shows great potential for applications within a variety of industries[3].FBG sensors have attracted interest from the civil structure communities over the past decade for structural health,vibration and seismic response monitoring.FBG sensors have been embedded in concrete for deformation monitoring and traffic load assessment in bridges and buildings.FBG sensors have been established as a major leading technology as compared to other competingfibre-optic sensor technologies.A major share of the papers presented at the17th Optical Fibre Sensors Conference(OFS-18)held at Cancun,Mexico in2006were onfibre Bragg gratings.The main advantages of FBGs over other fibre sensor schemes are its low cost,good linearity,wavelength multiplexing capacity,resistance to harsh environments and the transduction mechanism,which eliminates the need for referenc-ing as in interferometric sensors.FBG sensor technology is now on the verge of maturity after almost two decades of active research and development in thisfield.Efforts are now concentrating on delivering complete FBG sensor systems including front-end elec-tronics.Strain studies in civil structures are pivotal in avoiding unex-pected catastrophic failures.Long-term strain study of structures also helps in freezing the design limits of similar structures.Con-ventionally,most structures rely on maintenance schedules,visual inspection and a few conventional sensors for the purpose of dam-age monitoring.But the high cost of maintenance,lack of precision in visual inspection and susceptibility of sensors to harsh environ-mental conditions has made structural health monitoring(SHM) a necessity.Over the past few decades,Fibre Bragg grating sen-sors have emerged as a suitable,accurate and cost-effective tool in SHM of civil structures like high-rise buildings,bridges,tunnels and dams.For existing structures,FBG sensors can be attached onto the structure surface,whereas for new structures,these sensors can be embedded into the structure during the construction phase with-out any serious effect on the structural integrity.The information from such SHM systems can provide early warning forcompro-Fig.1.Transmission and reflection spectra from an FBG.mised integrity of structures and thus help avoid severe losses.Such information is also helpful to adapt and update newer designs of similar structures.Several review papers on applications of FBGs have been published[4–11].Strain and temperature have so far been the dominating measurands of interest.These reviews have primarily focused on the various usages of the FBG sensors in different sens-ing areas.This paper aims to provide an overview of the application of FBG sensors for strain measurement,particularly in thefield of structural sensing.Various applications as in structural health mon-itoring for bridges and concrete structures,moisture sensing,strain sensing of smart structures using FBG–FRP bars and ultrasonic non-destructive testing using FBG sensors have been discussed.Practical aspects like packaging of the sensors and demodulation techniques suitable for the use of FBG sensors in structural health monitoring have been discussed in detail.This review is expected to provide useful insight to researchers in thefield of structural sensing usinga reliable and effective strain sensing platform.2.Principle of operation of FBG sensorsFBGs are obtained by creating periodic variations in the refrac-tive index of the core of an opticalfibre[2].Fig.1shows the internal structure of an opticalfibre with an FBG written in it.When light is made to pass through the grating,at a particular wavelength,called the Bragg wavelength,the light reflected by the varying zones of refractive indices will be in phase and amplified. The Bragg wavelength is expressed asB=2n eff (1) where B is the Bragg wavelength,n eff is the effective refractive index of the FBG and is the grating period.2.1.Strain measurement using FBG sensorsWhen strain is induced in an FBG,the relative change in Bragg wavelength is expressed asBB=(1− e)ε(2) whereεis the longitudinal strain on the FBG and e is the effective photo-elastic constant of thefibre core material.e=n2eff2[p12−v(p11+p12)](3) where p ij are the silica photo-elastic tensor components and is the Poisson’s ratio.For an FBG of central wavelength of1550nm, typical strain sensitivity is approximately1.2pm/microstrain[9].152M.Majumder et al./Sensors and Actuators A147(2008)150–164Table1Temperature compensation techniques in FBG interrogationSchemes of temperature compensation RemarksTwo separate FBGs(one for strain measurement and the other for temperature measurement) [12,13]The most simple and straightforward technique for temperature compensation.However,resolution of the technique is low and interrogation of twofibres is cumbersomeTwo closely spaced gratings of differentwavelengths inscribed in the samefibre[14]Interrogation is easier.In a measurement range of0–900microstrain and25–120◦C,error reported is5%One LPG and two FBG scheme[15]This technique relies on the fact that LPGs have a much higher temperature response but lower strain responsecompared to short period FBGs.Resolution reported is±9microstrain and±1.5◦CTwo FBGs with entirely different wavelengths [16]In a measurement range of600microstrain and50◦C,error reported is10microstrain and±5◦C.However,this technique requires two light sources and two interrogation units,thereby increasing the overall cost of the systemTwo FBGs of varying diameter spliced together [17,18]System is illuminated from a single broadband source and interrogated using a single interrogator.In a measurement range of2500microstrain and120◦C,maximum error reported is17microstrain and1◦CSingle FBG with an EDFA[19]The amplified spontaneous emission power of the EDFA source has a linear relation with temperature and is used tomeasure temperature.This reading is subtracted from the combined strain temperature response of the Braggwavelength to get pure strain readings.Experimental r.m.s.deviation values of strain and temperature reported were18.2microstrain and0.7◦C,respectivelySingle FBG inscribed in erbium–ytterbiumfibre[20]In a measurement range of1100microstrain and50–180◦C,error reported is55.8microstrain and3◦CFBG embedded in composite material[21,22]This technique utilizes the birefringence property of the gratings when embedded.Wavelength separation of the twopeaks provides an estimate of temperature,whereas average wavelength between such separations provide the strainvalueAthermal packaging of thefibre using metal coating of the FBG[23]By controlling the thickness of the metal coating,the effective thermal expansion coefficient and the Young’s Modulus are controlled.For a temperature change30–80◦C,Bragg wavelength shifts by about50pmFBG glued to a bimetal alloy strip used as acantilever beam[24]In a temperature range of−20to60◦C,thermo-opto coefficient reported is−0.4pm/◦C2.2.Strain–temperature cross-sensitivityThe Bragg wavelength B is also affected by temperature changes.The relative change in the Bragg wavelength due to tem-perature change is expressed asBB=(˛+ ) T(4)where T is the change in temperature experienced at the FBG location,˛is the thermal expansion and is the thermo-optic coefficient.For an FBG of central wavelength of1550nm,typical temperature sensitivity is approximately13pm/◦C[9].Combining Eqs.(2)and(4),we get the effective Bragg wavelength shift due to strain and temperature and are expressed asBB=(˛+ ) T+(1− e)ε(5)For pure strain measurements,effects of temperature change on the Bragg wavelength has to be suitably compensated.Several techniques to offset this behavior are available in literature.Table1 shows a few competing techniques to achieve the purpose of tem-perature compensation of FBGs.3.FBG interrogation techniquesVarious interrogation techniques of FBGs have been proposed in literatures[25–60].The interrogation units are responsible for reading the Bragg wavelength shift of the FBGs induced by various physical parameters like strain,temperature,etc.Optical spectrum analyzers are unsuitable for this purpose due to their high cost and low scanning speed.The choice of the interrogation method depends upon several factors like type and range of strain being measured,accuracy and sensitivity required,number of sensors being interrogated and cost of the instrumentation.The FBG interrogation schemes commonly used are tabulated (Table2).4.FBG encapsulation techniquesOwing to the large span and long service period of civil structures,the durability,reliability and robustness of its health monitoring system is a key issue.Bare FBGs being very fragile in nature,require suitable encapsulation before being put into regular monitoring service.Various encapsulation techniques for FBG strain sensors have been proposed in literatures[61–67]. Fig.2(a)–(e)shows some of the encapsulated FBGs from literature as referenced and used for strain measurement on concrete surfaces and mental surfaces,respectively.Fig.2(a)shows a capillary encapsulated FBG sensor for use in concrete structures.The mental holder ring is attached on the surface of the concrete structure and it faithfully transmits the deformation of the structure to the FBG sensor.Fig.2(b)shows an FBG sensor encapsulated in slice base by gluing.This type of encap-sulated FBG sensors can be very well used in mental and concrete structures.Fig.2(c)shows smart FRP–FBG sensors.The FRP bars are embedded with FBG sensors thus utilizing the dual properties of FRP’s mechanical strength and the FBG’s sensing ability.Fig.2(d) shows another encapsulated FBG for use in cement structures.The fibre is placed inside a steel tube,which is further enclosed in a concrete-proof plastic hose.This protects thefibre from strong alkaline environment of the cement as well is effective in faith-ful transmission of strain to the sensor.Fig.2(e)shows a packaged Table2FBG interrogation schemesTypes Technologies ReferencePassivedetec-tionschemeLinearly wavelength-dependent device[25–29]CCD spectrometer[30–33]Power detection[34–37]Identical chirped-grating pair[38] Activedetec-tionschemeFabry-perotfilter[39–41]Unbalanced Mach-Zehnder interferometer[42–49]Fibre Fourier transform spectrometer[50,51]Acoustic-optic tunablefilter[52–54]Matched FBG pair[55–58]Michelson interferometer[59]LPG pair interferometer[60]M.Majumder et al./Sensors and Actuators A147(2008)150–164153Fig.2.(a)Mental capillary encapsulated FBG sensor[62].(b)Mental slice encapsulated FBG sensor[62].(c)FRP–FBG sensors[62].(d)FBG encapsulated in a steel tube[92].(e)Long-gage FBG sensor with surface mounting facility[61].(f)Schematic of FBG embedded coaxially in a cylindrical polymer package[63].(g)Athermally packaged FBG strain sensor.FBG for civil structure applications where we require to monitor a considerably macrostrain value.The FBG is encapsulated in a tube where the distance between the tie points define its effective gage. Optional brackets are also provided to enable surface mounting of the sensors.This technique thus,is effective in increasing the overall gage of the sensor.Another packaging technique proposed by Ngoi et al.[63]is to embed the FBG coaxially in a cylindrical silicone rubber tubing as shown in Fig.2(f).This packaging is specifically useful for sensing lateral loading.FBGs have been known to suffer from a phenomenon called peak splitting under the influence of a lateral load.Peak splitting occurs due to the effect of birefringence of the FBGs when subjected to lateral loading,i.e.unequal load-ing along the two perpendicular axes of thefibre.This issue has been taken care of by packaging the FBG in silicone rubber which is known to have a low elastic modulus and high Poisson’s ratio. It is also thermally stable in the temperature range from−100to 320◦C.Experimental data obtained from FBG sensors reveal agree-ment with thefinite element simulation results.This packaging has served to increase the lateral pressure sensitivity of the FBG sensor without inducing birefringence.However,the system suffers from an inherent time lag due to the typical viscoelastic nature of silicone rubber.Upon applying a load,the packaged FBG sensor shows an abrupt rise in wavelength,which gradually settles down to a stable, lower value within a few seconds.Authors propose readings to be taken once this spurious response settles down,approximately5s after the application of the load.Leng et al.in2005have proposed various designs of FBG sensor protection depending upon the usage area.These include sensors154M.Majumder et al./Sensors and Actuators A147(2008)150–164for metallic surfaces,CFRP composites and concrete structures[64]. Designs include FBGs embedded inside steel tubes,steel rebars, CFRP prepegs,etc.The packaged sensors have been evaluated for optimum strain transfer between the sensor and test specimen by using non-linearfinite element analysis.Concrete cylinders instru-mented with FBG sensors and electrical resistance strain gauges have been subjected to compressive loading and the results found from both type of sensors to be in proper agreement.Authors also claim that due to higher resolution,FBG strain sensors would be able to detect the initiation of failure of structures earlier than the strain gauges.Dawood et al.have described in detail a procedure to embed FBG sensors between the foam core and cross-ply laminate of GFRP sandwich material using vacuum infusion technique[65]. The sandwich structure consisted of a single layer of polymer foam sandwiched between two layers of GFRP skins.An array of six mul-tiplexed FBG sensors was used.The area of the gratings was left uncoated to provide better mechanical coupling to the GFRP.The FBGs were to be embedded between the core and the skin of the sandwich.The opticalfibre was then aligned and laid up along the center line of the foam core.The prepared sandwich specimen was then placed in a vacuum bag and resin/hardener mixture infused inside.The specimen was cured for15h at room temperature.This type of packaging is useful in sensing microscopic localized defects like debonding of the GFRP material.The FBG being fully embedded in the test specimen is able to detect the internal defects of the spec-imen at an early stage.However,the embedding process is involved and requires a greater degree of precision and care.Accuracy and repeatability have been found to be satisfactory under static and dynamic loading conditions.Lu and Xia have used FBG sensors directly embedded into CFRP sheets for real-time monitoring of RC beams[66].The authors claim that in this case there is no need of a protective coating or adhe-sive layer between the bare FBG and the CFRP sheets.Thus,the measured strain from the FBG–CFRP composite provides the actual strain measured without incurring any dampening effect.This is a distinct advantage over other encapsulation technique.RCC beams instrumented with FBG-embedded CFRP sheets were subjected to compressive load.A theoretical calculation of strain at different loading conditions using the dimensional values and Young’s Mod-ulus of the RCC beams was done.The measured values were in good agreement with the theoretical strain values.Another very commonly used and simple packaging technique of FBGs for strain monitoring in concrete structures is to install the sensors in a steel rebar and then use the rebar at the site of measurement.Chung and Kang[67]have used such a technique where they have placed a six-FBG multiplexedfibre in a groove cut in a steel rebar and used a fast curing adhesive to bond thefibre to the rebar. This FBG embedded rebar has been used at the site of strain mon-itoring.However,before using this type of packaging it is essential to study the strain transfer characteristics of the adhesive and the rebar material for accurate strain measurement.Two major issues associated with the use of FBG sensors as health monitoring tool in civil structures are their high fragility and cross-sensitivity to more than one measurand.Special ather-mal encapsulated FBGs that take care of the strain–temperature cross-sensitivity are available[23,68,69].Lo and Kuo have proposed athermal packaging of FBGs using a metal coating that serves as thermal compensator[23].An FBG1cm in length is written using a phase mask.It has a central wavelength of1532.93nm at30◦C.The fibre substrate is quartz and a copper coating of5-m thickness is deposited onto the substrate using electroless plating technique. Quartz having a much lower thermal expansion coefficient than copper,any rise in ambient temperature results in a greater expan-sion of the copper than that of the FBG.This compresses the FBG and creates a negative strain on it,thereby compensating for the temperature-induced wavelength shift of the FBG.This proposed technique of temperature compensation thus involves a simple bi-material that is reliable and feasible for mass production.Moyo et al.have reported a packaged FBG that is suitable for use in the harsh conditions of the construction industry and also takes care of the temperature compensation of the sensors[69].The pack-aged sensor is dumb-bell shaped and consists of two FBGs placed closely.One FBG,sandwiched between two layers of carbon com-posite material,is epoxied on the dumb-bell surface and is prone to both strain and temperature changes.Another FBG,encased in a metal tube is prone only to temperature perturbations.Several tests were performed on these packaged FBG sensors and the data compared against conventional foil strain gauges.Tensile tests were reported on steel rebars and the sensor response was found to be linear and closely correlated to those of foil gauges.Static test on simply supported reinforced concrete beams instrumented with the sensors also showed approximately linear response,thus jus-tifying the packaging and installation procedures of the sensors. Dynamic tests on the beam were carried out using an impulse hammer and the maximum strain thus recorded by the FBG and foil gauges were respectively55and58microstrain.The packaged sensor was also embedded inside a concrete cylinder,which was subjected to compressive load.Only the strain sensor showed a high sensitivity whereas the temperature-monitoring sensor was almost unaffected.It may be noted that in most cases,the strain sensitivity of an encapsulated FBG is significantly different from that of the bare FBG. Hence calibration of the encapsulated FBG sensor must be carried out before it is put into real-world application.5.Applications of FBG strain sensors in structural sensing5.1.Strain monitoring in civil infrastructureA major application of FBG strain sensors is in thefield of real-time online health monitoring of bridges and civil structures [70–73].FBG sensors have a major advantage over conventional non-destructive techniques in that they are capable of remotely monitoring the condition of the test structure.The interrogating instrumentation being located off-site results in higher efficiency of the system and better safety of the personnel.Twenty-six FBG strain sensors have been reported to be moni-toring the Horsetail Falls Bridge in Oregom successfully for2years [74].The bridge was originally built in1914and in1998it was strengthened by placing composite wraps over the concrete beams. Long-gage FBG strain sensors are placed in grooves cut into the con-crete and in the wraps as well.This is done with a view to assess the actual strengthening provided by the wraps to the bridge.The long-gage sensors provide a relatively macroscopic strain value that can measure several kHz of dynamic strain with a resolution as low as0.1microstrain and hence are very useful in structural monitor-ing.A similar test is reported on the Sylvan Bridge with fourteen long-gage sensors.Saouma et al.[75]have used FBG sensors on aluminum as well as concrete specimens to monitor the strain and have validated the results against electrical strain gauges.They have extended the laboratory work by instrumenting six beams and six columns of a newly constructed building with FBG sensors that can be used to monitor the strain of the beams and columns online.Monitoring of the prestressing tendons of the Beddington Trail Bridge,Canada using Bragg grating strain sensor array has been done by Maaskant et al.[76].Three types of prestressing tendons have been used in this bridge,namely steel strand,carbonfibreM.Majumder et al./Sensors and Actuators A147(2008)150–164155Fig.3.Packaged FBG-based strain sensor used in the health monitoring of West Mill Bridge[78].composite cable and leadline rod.The main objective behind this work was to study the long-term losses in the tendons due to stress relaxation and creep.FBG sensors were bonded to each type of ten-don and then embedded in concrete girders.A total of18sensors were placed strategically on the girder in order to monitor the point of maximum strain generation.Proper cabling of the sensors min-imizes the effect of moisture and alkalinity of the medium on the sensors and also reduces pinching and microbending phenomena of thefibre.Static strain measurements of the girders with a precision of±40microstrain have been done.A comparison of data collected over19months reveal that the loss of prestress in CFRP tendons is almost25%lesser compared to that in steel tendons thereby jus-tifying some merit in the use of CFRP material in bridges.Besides, dynamic strain monitoring on various positions of the girder were studied by passing vehicles with known loads.Strain resolution of 1microstrain over a range of10,000microstrain had been achieved. This information can be useful from the end of traffic monitoring, bridge designing and its maintenance.FBGs have been used in the structural health monitoring of the Tsing Ma Bridge in China[77].At1377m,this is the longest sus-pension bridge in the world.It has a double deck configuration,one for highway traffic and the other for railway.The deck is of hybrid arrangement using both truss and box forms.This bridge is in ser-vice from1997and a structural health monitoring system,wind and structural health monitoring(WASHM)has been monitoring its health from inception.In this report,the response of FBG sensors has been checked against the WASHM system under specific load-ing conditions.FBGs were fabricated in-house,suitably packaged and installed on the bridge.Tests were carried out at three specific locations viz.,hanger cables,rocker bearing and supporting struc-ture on a section of the lower deck using21FBG sensors.Separate FBGs were used to monitor the instantaneous temperature of the structure and compensate accordingly in strain readings.When-ever a heavy traffic load was subjected on the bridge,the response of the FBG monitoring system peaked which was in close agree-ment to the response of the resistive strain gauge sensors of the WASHM system.Gebremichael et al.in2005have reported the use of40FBG sensors to remotely monitor the real-time strain on Europe’sfirst all-fibre reinforced composite bridge,The West Mill Bridge[78]. Fig.3shows the packaged FBG sensor used in the structural health monitoring of this bridge.The main objective behind this study was to collect real-time,in situ strain data from the bridge and to analyze this data for assessment of its structural integrity,main-tenance scheduling and validation of design codes.The authors have developed a dedicated FBG interrogation system based on the WDM technique for use in this work.Cost per channel of the instru-mentation is reported to be comparable to those of conventional strain sensors,if used in multiplexed sensor scheme.The moni-toring system wasfirst tested inside the laboratory on structural test elements instrumented with FBG and strain gauge sensors. The structural elements were subjected to both quasi-static and dynamic loading.The tests reveal that response of the FBG sen-sors was linear,repeatable and without any significant hysteresis. Finally the two-lane bridge,which is fully made of glass and carbon fibre reinforced polymer,is carefully and strategically instrumented with40FBG and11strain gauge sensors.The FBG sensors were coated with moisture-proofing silicon compound and consecu-tively with composite stripes that minimize birefringence effect in fibres due to transverse loading.On-site testing was done with a 30-ton lorry positioned at different points on the bridge.The strain monitored in the different channels conforms to the relative posi-tioning between the sensors and the loading point.The strain data obtained from FBGs and resistive gauges were found to be closely correlated and the technique has been established as a long-term condition monitoring of the all-fibre composite bridge.As a very significant continuation of this work,Kister et al.have evaluated the performance of the adhesive and protection system used with the FBG sensors installed on the West Mill Bridge[79]. Unpackaged FBG sensors were installed on the bridge structure using cynoacrylate glue,which is the primary adhesive.Beads of epoxy adhesive were also deposited on top of thefibres to ensure added anchorage.Strips of glassfibre composite material were bonded on both sides of thefibres using the two adhesives.Silicone sealant was then applied from top to seal the package from posite covers were then used to envelope the complete sensor package.The dimensions of thefinal packaged sensor were 1.8mm in thickness and maximum1m in length.The interfacial bond strength developed between the adhesive layers and the opti-calfibre were evaluated by the modifiedfibre pull-out test[80].It was reported that whereas unstrippedfibres failed due to debond-ing and sliding of cladding,strippedfibres failed due to fracture of the cladding close to the glue edge or due to rupture of the glue length.It was also observed that cynoacrylate-gluedfibres could withstand a higher failure load than the epoxy-gluedfibres.Hence cynoacrylate had been chosen as the primary adhesive for bond-ing the optical sensors on to the bridge structure.The durability of the sensor protection system was assessed by immersing coupons embedded with packaged sensors in water for a duration of90days. Results show negligible influence of water absorption on the sen-sors.Sensor survival rate while bonding on the bridge structure has been reported as100%.Integrity of adhesives and durability of the sensors has been assured and the sensors on the West Mill Bridge have been providing continuous satisfactory performance over the last3years.5.1.1.Strain monitoring in reinforced concrete beamsNumber of strain studies of reinforced concrete beams instrumented with FBG sensors have been reported in liter-atures[81–83,64,67].Maher and Nawy[82]have compared the response of FBG strain sensors and conventional resistive strain gauges on reinforcing bars.The bars having dimension of 305cm×25.4cm×30.5cm were subjected to three-point bending tests.Few FBG sensors were carefully embedded into V-grooves cut into the reinforcing bars and a few others were simply epox-ied on the back surface of the bars alongside the conventional strain gauges.For test duration of7days,the nominal compressive strength of the concrete was found to be76MPa and data collected from FBG sensors and strain gauges were in agreement.Davis et al.have reported the use of embedded wavelength divi-sion multiplexed FBG sensors in monitoring the strain on reinforced concrete beams and decks till their failure[83].An8-ft long beam was instrumented with the Bragg sensors at different strategic loca-tions and subjected to four-point bending.Thefibre sensors were bonded to rebars using ordinary foil gauge adhesives and coated。