Advanced sensorless drive technique for multiphase BLDC Motors
超触觉技术系统问世 无需碰触或携带任何设备

【 4 】 李壮 云. 液压元件与系统 [ M] . 北京 : 机械 工业 出版社 ,
2 011 .
【 5 】韩桂 华. 液压 系统设计技巧 与禁忌 [ M] . 北京 : 化学工业
出版社 , 2 0 1 1 .
【 6 】王 春行. 液 压 控制 系统 [ M ] . 北京: 机 械 工业 出 版社 ,
觉 到显示 屏上 的 内容 ,而且能 在触 摸前 接收 到看不 见 的信 息 。
士 利用超声辐射力向用户发射触觉感受还是一门新技术。该研究提出了一种超触觉理论, 即一种能在空中产生触觉反馈的 士
工系 统设计 。卡 特解 释说 ,在空 中传播 的超 声波会 产 生不 同的压 力 ,如果 许 多超 声 波 同时 到达 同一 位 置 ,就 会 在该 点 产 生 明显 的压 力变 化 。超声转 换器 阵列 能对 空 中 目标施 加压 力 ,通 过屏 幕 投射 出触 觉 感受 ,直 接作 用 于用 户 手上 。一 系列 超 声转 换 器
运行 。
液压绞车的恒张力控制有 两种方 式。一种是采用 溢流 阀或减压 阀控制系统相对恒定的压力 ,而达到控
制液压 马达扭矩恒定 的 目的 ,这种方式有较大的功率 损失 ,适用 于小功率 的绞 车 ,优点是系统简单 、控制 容易 ,可以和其他液压设 备共用液压源 ,减少投资 。 第二种是采用恒压伺服变量 系统来控制定量或变 量液压 马达 ,由于采用 了压力补偿变量泵 ,使系统在 保持和释放阶段时液压泵处于恒压状态 ,保证 了马达 的恒扭矩 ,这种系统 的功率损失小 ,一般应用 于大功 率 的液压绞犁 。 本 文作 者对第 一种 系统的设计 原理进行 了详细地 分析 ,可以作为类似系统的设计 参考。 参 考文献 :
变频空调压缩机电机的参数辨识

Inductance model-based sensorless control of the switched reluctance motor drive at low speed
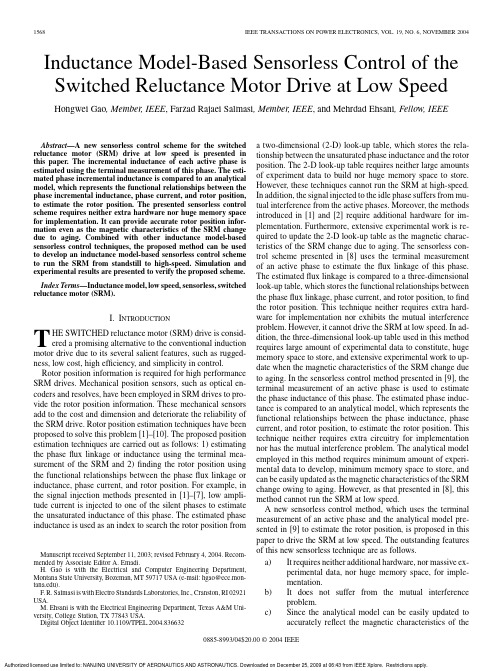
Inductance Model-Based Sensorless Control of the Switched Reluctance Motor Drive at Low Speed Hongwei Gao,Member,IEEE,Farzad Rajaei Salmasi,Member,IEEE,and Mehrdad Ehsani,Fellow,IEEEAbstract—A new sensorless control scheme for the switched reluctance motor(SRM)drive at low speed is presented in this paper.The incremental inductance of each active phase is estimated using the terminal measurement of this phase.The esti-mated phase incremental inductance is compared to an analytical model,which represents the functional relationships between the phase incremental inductance,phase current,and rotor position, to estimate the rotor position.The presented sensorless control scheme requires neither extra hardware nor huge memory space for implementation.It can provide accurate rotor position infor-mation even as the magnetic characteristics of the SRM change due to bined with other inductance model-based sensorless control techniques,the proposed method can be used to develop an inductance model-based sensorless control scheme to run the SRM from standstill to high-speed.Simulation and experimental results are presented to verify the proposed scheme. Index Terms—Inductance model,low speed,sensorless,switched reluctance motor(SRM).I.I NTRODUCTIONT HE SWITCHED reluctance motor(SRM)drive is consid-ered a promising alternative to the conventional induction motor drive due to its several salient features,such as rugged-ness,low cost,high efficiency,and simplicity in control. Rotor position information is required for high performance SRM drives.Mechanical position sensors,such as optical en-coders and resolves,have been employed in SRM drives to pro-vide the rotor position information.These mechanical sensors add to the cost and dimension and deteriorate the reliability of the SRM drive.Rotor position estimation techniques have been proposed to solve this problem[1]–[10].The proposed position estimation techniques are carried out as follows:1)estimating the phaseflux linkage or inductance using the terminal mea-surement of the SRM and2)finding the rotor position using the functional relationships between the phaseflux linkage or inductance,phase current,and rotor position.For example,in the signal injection methods presented in[1]–[7],low ampli-tude current is injected to one of the silent phases to estimate the unsaturated inductance of this phase.The estimated phase inductance is used as an index to search the rotor position fromManuscript received September11,2003;revised February4,2004.Recom-mended by Associate Editor A.Emadi.H.Gao is with the Electrical and Computer Engineering Department, Montana State University,Bozeman,MT59717USA(e-mail:hgao@).F.R.Salmasi is with Electro Standards Laboratories,Inc.,Cranston,RI02921 USA.M.Ehsani is with the Electrical Engineering Department,Texas A&M Uni-versity,College Station,TX77843USA.Digital Object Identifier10.1109/TPEL.2004.836632a two-dimensional(2-D)look-up table,which stores the rela-tionship between the unsaturated phase inductance and the rotor position.The2-D look-up table requires neither large amounts of experiment data to build nor huge memory space to store. However,these techniques cannot run the SRM at high-speed. In addition,the signal injected to the idle phase suffers from mu-tual interference from the active phases.Moreover,the methods introduced in[1]and[2]require additional hardware for im-plementation.Furthermore,extensive experimental work is re-quired to update the2-D look-up table as the magnetic charac-teristics of the SRM change due to aging.The sensorless con-trol scheme presented in[8]uses the terminal measurement of an active phase to estimate theflux linkage of this phase. The estimatedflux linkage is compared to a three-dimensional look-up table,which stores the functional relationships between the phaseflux linkage,phase current,and rotor position,tofind the rotor position.This technique neither requires extra hard-ware for implementation nor exhibits the mutual interference problem.However,it cannot drive the SRM at low speed.In ad-dition,the three-dimensional look-up table used in this method requires large amount of experimental data to constitute,huge memory space to store,and extensive experimental work to up-date when the magnetic characteristics of the SRM change due to aging.In the sensorless control method presented in[9],the terminal measurement of an active phase is used to estimate the phase inductance of this phase.The estimated phase induc-tance is compared to an analytical model,which represents the functional relationships between the phase inductance,phase current,and rotor position,to estimate the rotor position.This technique neither requires extra circuitry for implementation nor has the mutual interference problem.The analytical model employed in this method requires minimum amount of experi-mental data to develop,minimum memory space to store,and can be easily updated as the magnetic characteristics of the SRM change owing to aging.However,as that presented in[8],this method cannot run the SRM at low speed.A new sensorless control method,which uses the terminal measurement of an active phase and the analytical model pre-sented in[9]to estimate the rotor position,is proposed in this paper to drive the SRM at low speed.The outstanding features of this new sensorless technique are as follows.a)It requires neither additional hardware,nor massive ex-perimental data,nor huge memory space,for imple-mentation.b)It does not suffer from the mutual interferenceproblem.c)Since the analytical model can be easily updated toaccurately reflect the magnetic characteristics of the0885-8993/04$20.00©2004IEEESRM,the proposed sensorless control scheme can pro-vide accurate rotor position information even as themagnetic characteristics of the SRM change due toaging.d)Combined with other inductance model-based sensor-less control schemes,such as those published in[8]and[10],it can be used to develop an inductance model-based sensorless control scheme to run the SRM fromstandstill to high-speed.II.R OTOR P OSITION E STIMATION S CHEMEA.Estimation of the Phase Incremental InductanceThe phase voltage equation of the SRM is givenas(1)where,,,,and denote the phase voltage,phase current,phase resistance,phase incremental inductance,and phase self-inductance,respectively;and stand for the rotor angularposition and rotor angular speed,respectively.At low speed,the third term at the right-hand side of(1)isnegligible.Therefore,the phase voltage(1)can be simplifiedas(2)Thus,the phase incremental inductance can be givenas(3)It is evident from(3)that the phase incremental inductancecan be estimated once the phase voltage and current data areobtained.B.Development of the Phase Incremental Inductance Model1)Phase Self-Inductance Model:An analytical model,which represents the functional relationships between the phaseself-inductance,phase current,and rotor position,is presentedin[9].In this analytical model,the variation of the phaseself-inductance versus the rotor position is represented usingthe Fourier series with only thefirst three terms considered.The model for the self-inductance of phase A is givenby(4)where is the number of rotor polesand(5)(6)(7)where(8)is the aligned position inductance as a function of phasecurrent(9)is the inductance at the midway between the unaligned andaligned position as a function ofcurrent(10)is the inductance at unaligned position and is assumed to be in-dependent of the phase currentand is the degree of approxi-mation(in the presentcase yields a good accuracy).Thecoefficientsand are determined by the curvefitting methodsuch that the inductance profile obtained using(4)would exactlyfit the profile obtained from thefinite element analysis or exper-imental work.The expressions for other phase inductances are the same as(4),except with proper phase shifts.The accuracy of the above model has been verified byfiniteelement analysis and experimental work[9].Development of the above self-inductance model only re-quires measurement of the phase self-inductance at the alignedposition,unaligned position,and midway between the alignedand unaligned position.Measuring the phase inductance at thesethree rotor positions can be easily carried out.For example,foran SRM,exciting phase A,C,and B separately with suffi-cient current will move the rotor to the aligned position of phaseA,unaligned position of phase A,and the midway between thealigned and unaligned position of phase A,respectively.Afterthe rotor has been moved to each of these three positions,thephase A inductance can be measured by injecting proper currentinto phase A.The above test can be performed under the controlof the SRM drive controller when the SRM is idle.Carrying outthe test whenever the SRM is idle allows the inductance modelto be updated as the magnetic characteristics of the SRM changeowing to aging.2)Phase Incremental Inductance Model:The phase self-in-ductance model given by(4)can be used to develop a phase in-cremental inductance model,which is used for sensorless con-trol of SRM in this paper.The phase incremental inductance isderived as follows.The phaseflux linkage of the SRM is givenas(11)where stands for the phaseflux linkage of the SRM.The phaseincremental inductance,according to its definition,is givenas(12)Substituting(4)into(12)yields an analytical model rep-resenting the functional relationships between the phaseincremental inductance,phase current,and rotorposition(13)where(14)(15)(16)where(17)(18)C.Estimation of the Rotor PositionSubstituting(3)into(13)yields(19)In(19),the term can be estimate accurately according to thedc bus voltage and the gating signals of the active switches in theSRM drive inverter.The term can be calculated using thephase current data.The noisein term calculation can befiltered using the averaging method.Therefore,all the quantitiesin(19),except,can be estimated in real time once the phasecurrent is sampled.One can numerically solve(19)toestimate.In(19),the term is dominant overthe term.Therefore,the errorin estimation and sensing does not lead to a notice-able errorin estimation.From(19),one can see that estimation of the rotor positionrequires that the rotor position have one-to-one relation withthe phase incremental inductance at a given phase current.Thephase incremental inductance-phase current-rotor position char-acteristic of asample SRM is shown in Fig.1.Fig.1shows that for the sample SRM,at low current,suchasA,a unique rotor position is defined by the given phaseincremental inductance when the phase is between itsunalignedandaligned position.However,at highor medium current,suchas Aor A,the phaseexhibits the same incremental inductance at multiple rotor posi-tions,when.Therefore,at high or medium cur-rent,estimating the rotor position using the phase incrementalinductance and the current of a single phase will lead to multiplesolutions.To solve this problem,the phase incremental induc-tances of multiple active phases are estimated and used for rotorposition estimation in this work.This approach is illustrated inFig.2.The variations of the phase incremental inductance and phasecurrent of phase A(the solid curves),B(the dashed curves),C(the dotted curves),and D(the dashed-and-dotted curves)versusthe rotor position for a SRM are depicted in Fig.2,whererepresents the unaligned position of phase A.WhenFig. 1.Phase incremental inductance-phase current-rotor positioncharacteristic of a sample8=6SRM.Fig.2.Rotor position estimation using the phase incremental inductances ofmultiplephases.,phase A is active and its incremental in-ductance has one-to-one relation with the rotor position at anyphase current.Therefore,the phase incremental inductance ofphase A is estimated from its terminal measurement and used toestimate.When,though phase A is still active,the phase incremental inductance of phase A loses uniquenessversus at medium or high current,and thus,is not used to es-timate.However,when,phase B is excitedfor torque production and its phase incremental inductance hasone-to-one relation with the rotor position,and thus,is used toestimate.The phase incremental inductance of Phase C and Dare used toestimate in the same manner.The proposed rotor position estimation method requires aproper startup method such that at standstill,the phase betweenthe unaligned position and the midway between the unalignedFig.3.Simulated phase currents of the SRM.and aligned position is excitedfirst.The rotor position estima-tion scheme presented in[10]is employed to meet this require-ment.III.S IMULATION R ESULTSThe proposed senseless control scheme is studied through nu-merical simulation on asample SRM,whose rated phasevoltage,rated phase current,and rated rotor speed are100V, 6A,and1000RPM,respectively.In the simulation,each SRM phase is turned on and off at the unaligned and aligned posi-tion,respectively.The current of each SRM phase is regulated at4A,the current under which the phase incremental induc-tance has the same value at multiple rotor positions.The load of the SRM is adjusted properly so that the SRM runs at low speed (below15%of the base speed).The rotor position of the SRM is detected using the proposed position estimation scheme.The simulation results are shown in Figs.3–5.Fig.3shows the current of phase A–D.The traces in Fig.4, from the top to the bottom,depict the torque of phase A,the total torque of all the SRM phases,and the rotor speed.Fig.5 illustrates the estimated(the plus sign)and actual(the circle) commutation position of phase A.A0.65(mechanical degree) error in the rotor position estimation is observed from the quan-titative results of the simulation.Due to this error,some negative phase torque,though negligibly small,is observed in Fig.4. The simulation results presented in Figs.4and5clearly show the validity of the proposed rotor position estimation scheme.IV.E XPERIMENTAL R ESULTSThe proposed sensorless control algorithm has been imple-mented on the sample SRM mentioned in the previous section.A permanent magnet dc generator with a resistive load is used as the load of the SRM.The rotor position estimation technique,presented in[10],is used to start the SRM fromstandstill.Fig.4.Simulated torque of phase A,total torque of all the SRM phases,and rotorspeed.Fig.5.Estimated(the plus sign)and actual(the circle)commutation position of phase A.The performance of the proposed sensorless control scheme is shown in Figs.6–8.Fig.6depicts the variation of the rotor speed during the startup process.The maximum rotor speed is about130RPM in this experiment.Fig.7depicts the phase cur-rents of the SRM,which are regulated at4A in this test.In order to test the accuracy of the proposed rotor position esti-mation algorithm,an optical encoder is used to sense the actual rotor position.This sensed actual rotor position is compared to the estimated rotor position to calculate the error of the rotor position estimation.The rotor position estimation error,which is less than1mechanical degree,is depicted in Fig.8.V.C ONCLUSIONA new sensorless control scheme for the SRM drive at low speed is presented in this paper.This technique uses the terminalFig.6.Experimentally recorded rotor speed (45RPM/Div).Fig.7.Experimentally recorded current of phase A –D,from top to the bottom (1.25A/Div).Fig.8.Experimentally recorded rotor position estimation error (5/Div).measurement of the active phases and an analytical inductance model to estimate the rotor position.It neither requires addition hardware nor huge memory space for implementation.In ad-dition,this technique does not suffer from the mutual interfer-ence problem.By updating the analytical mode when the SRM is idle,the presented rotor position estimation scheme can pro-vide accurate rotor position information even as the magnetic characteristics of the SRM change due to aging.The theory ofthis sensorless control scheme is presented and veri fied by sim-ulation and experimental results.R EFERENCES[1]M.Ehsani,I.Husain,and A.B.Kulkarni,“Elimination of discrete po-sition sensor and current sensor in switched reluctance motor drives,”in Proc.IEEE Industry Applications Soc.Annu.Meeting ,vol.1,1990,pp.518–524.[2]M.Ehsani,I.Husain,S.Mahajan,and K.R.Ramani,“New modulationencoding techniques for indirect rotor position sensing in switched reluc-tance motors,”IEEE Trans.Ind.Applicat.,vol.30,pp.85–91,Jan./Feb.1994.[3]G.R.Dunlop and J.D.Marvelly,“Evaluation of a self commutedswitched reluctance motor,”in Proc.Electric Energy Conf.,1987,pp.317–320.[4]S.R.MacMinn,W.J.Rzesos,P.M.Szczensny,and T.M.Jahns,“Ap-plication of sensor integration techniques to switched reluctance motor drives,”IEEE Trans.Ind.Applicat.,vol.28,pp.1339–1344,Nov./Dec.1992.[5]S.R.MacMinn,C.M.Steplins,and P.M.Szaresny,“Switched reluc-tance motor drive system and laundering apparatus employing same,”U.S.Patent 4959596,1989.[6]W.D.Harris and ng,“A simple motion estimator for variablereluctance motors,”IEEE Trans.Ind.Applicat.,vol.IA-26,pp.237–243,Mar./Apr.1990.[7]N.H.Mvungi,houd,and J.M.Stephenson,“A new sensorlessposition detector for SR drives,”in Proc.4th Int.Conf.Power Electronics Variable Speed Drives ,1990,pp.249–252.[8]J.P.Lyons,S.R.MacMinn,and M.A.Preston,“Flux/current methodsfor SRM rotor position estimation,”in Proc.IEEE Industry Application Soc.Annu.Meeting ,vol.1,1991,pp.482–487.[9]G.Suresh,B.Fahimi,K.M.Rahman,and M.Ehsani,“Inductance basedposition encoding for sensorless SRM drives,”in Proc.IEEE Power Electronics Specialists Conf.,vol.2,1999,pp.832–837.[10]H.Gao,F.R.Salmasi,and M.Ehsani,“Sensorless control of SRM atstandstill,”in Proc.IEEE Applied Power Electronics Conf.,vol.2,2000,pp.850–856.Hongwei Gao (S ’98–M ’02)received the B.Sc.and M.Sc.degrees from Tsinghua University,Beijing,China,in 1990and 1993,respectively,and the Ph.D.degree from Texas A&M University,College Station,in 2001,all in electrical engineering.Since 2002,he has been an Assistant Professor in the Electrical and Computer Engineering De-partment,Montana State University,Bozeman.His research interests include electric machinery,motor drives,power electronics,electric and hybrid electric vehicles,renewable energy source power systems,and power quality.Dr.Gao is a member of the IEEE Power Electronics,Industry Applications,and Industrial Electronicssocieties.Farzad R.Salmasi (S ’99–M ’03)received the B.Sc.degree from Sharif University of Technology,Tehran,Iran,in 1994,the M.Sc.degree from Amir Kabir Uni-versity of Technology,Tehran,in 1997,and the Ph.D.degree from Texas A&M University,College Station,in 2002,all in electrical engineering.Currently,he is a Research Scientist with Electro Standards Laboratories,Inc.,Cranston,RI.His re-search areas include design and advanced control of electric motor drives,power electronics systems,and hybrid electric vehicles.Dr.Salmasi is a member of the IEEE Power Electronics and Industry Appli-cations Societies.Mehrdad Ehsani(S’70–M’81–SM’83–F’96)hasbeen at Texas A&M University(TAMU),CollegeStation,since1981,where he is a Professor ofelectrical engineering and Director of the AdvancedVehicle Systems Research Program.He is the authorof over300publications in pulsed-power supplies,high-voltage engineering,power electronics,andmotor drives and automotive systems.He is thecoauthor of several books on power electronics andmotor drives and a contributor to an IEEE Guide forSelf-Commutated Converters and other monographs. He is the author of over20U.S.and European Commission patents.His current research work is in power electronics,motor drives,and hybrid electric vehicles and systems.Dr.Ehsani received the Prize Paper Award in Static Power Converters and Motor Drives at the IEEE Industry Applications Society in1985,1987, and1992,the James R.Evans Avant Garde Award from the IEEE Vehicular Technology Society in2001,and the IEEE Undergraduate Teaching Award for2003.In1992,he was named the Halliburton Professor in the College of Engineering,TAMU.In1994,he was named the Dresser Industries Professor, TAMU.In2001,he was named the Dow Chemical Faculty Fellow of the College of Engineering,TAMU.He is also the Associate Editor of the IEEE T RANSACTIONS ON I NDUSTRIAL E LECTRONICS and the IEEE T RANSACTIONS ON V EHICULAR T ECHNOLOGY.He has been a member of IEEE Power Electronics Society AdCom,past Chairman of PELS Educational Affairs Committee, past Chairman of IEEE IAS Industrial Power Converter Committee,and past chairman of the IEEE Myron Zucker Student-Faculty Grant program.He was the General Chair of IEEE Power Electronics Specialist Conference for 1990.He is an IEEE Industrial Electronics Society and Vehicular Technology Society Distinguished Speaker and IEEE Industry Applications Society past Distinguished Lecturer.He is Chairman of Vehicular Technology Society Vehicle Power and Propulsion Committee,and was elected to the Board of Governors of IEEE VTS in2003.He is a Registered Professional Engineer in the State of Texas.。
Sensorless+Control+of+PMSM+Based+on+Adaptive+Sliding+Mode+Observer

ˆα + f (iα ) < 0 ΔA ⋅ iα i ˆβ + f (iβ ) < 0 ΔA ⋅ iβ i
2 MODELS AND OBSERVER
In stationary (α , β ) reference frame, the mode for PMSM is characterized by (1)
diα R 1 uα = − iα + eα + dt L L L diβ R uβ 1 = − iβ + eβ + dt L L L eα = −λ0ω e sin(θ e )
speed can be derived as
& ≈ λ B( S sin θ ˆ − S cosθ ˆ) ˆ ω e 0 1 2
And (10) can be rewritten as
(10)
− R L . Because the variation of L
& ≈ λ B ⋅ [(i ˆ − (i ˆ] ˆα − iα ) sinθ ˆβ − iβ ) cosθ ˆ ω e 0
s e e
ˆα di R 1 ˆα + 1 e ˆα + uα + f (iα ) = (− + ΔA)i dt L L L ˆβ di R 1 ˆβ + 1 e ˆβ + uβ + f (iβ ) = (− + ΔA)i dt L L L
(2) Where superscript “ ^ ” represents the estimated quantities, “—”represents the error quantities, ΔA is the variation of
新蒂纳特:一款带有先进技术和独特设计的豪华轿车说明书

SONATA2Technologyloves you.34Make a statement with Sonata’s transformational technology.Sonata’s high style not just sparks the emotions but also delivers high rewards with innovative design features like the gradient hidden light technology, a sure conversation starter that adds to Sonata’s mystique. Sonata’s high-tech image is reinforced with LED rear combination lamps and available full-LED front lighting. For a statement that expresses high performance, Hyundai offers an 18-inch alloy wheel package and premium Pirelli tires.Horizontal LED rear combination tail lights 18 inch Alloy wheelsRadiator grille/LED daytime running lights (DRL)/LED Projection headlamps/front parking sensors56A step closer to perfection.Every detail of the Sonata is truly new yet all of the key touchpoints feel so familiar and instinctive to use — for a feeling of total trust and confidence. The new Sonata has a striking presence achieved through a harmonized balance between proportion, architecture, styling and technology. Every curve and every bend add to the premium accent of the car.The all new Sonata: It really does bring you closer to driving perfection thanever before.78Rule the road.Sonata flexes its muscles on command to keep you feeling confident and in charge of all driving situations. Whether cruising along the open highway or working through stop-and-go city traffic, there’s a nimble yet dynamic quality that calms, relaxes and satisfies the driver. Steering is light yet precise and the ride is silky smooth. Premium appointments such as the head-up display and SuperVision gauge cluster further elevate driver’s awareness and safety.12.3” high resolution TFT LCD Head-up display910Sheer Rear.Smart Trunk Horizontal LED rear combination tail lightsSporty rear bumper/Rear parking sensors/Rear cameraThe design cues continue towards the rear. The connected LED Rear lamps are incorporated with rear air fins which createa unique style and enhance aerodynamic performance. The rear bumper design and extended LED lights provide a broadstance, giving Sonata its perfect blend of sporty and classy look. Rear parking sensors, smart trunk opener and rear LEDfog lamps further provide the driver convenience on journeys long and short.Sonata has a way of becoming a part of you, an extension of your body. Its seats cradle you while gauges, control knobs and pedals align perfectly with eyes, hands and feet for a sense of complete confidence and total control.The floating infotainment display offers you latest features and connectivity, whileyou nestle comfortably in the Leather upholstered luxury seats.8″ floating infotainment system display10-way powered driver seat with lumbar supportRear seat with armrest60:40 split folding seats Arrive relaxed.Sonata takes equally good care of its passengers with seats that bolster and support the spine’s natural S-curve so you can really feel the difference that good design makes. The relaxation comfort seat allows the front passenger to unwind by replicating the spinal support of a reclining chaise lounge to achieve a feeling ofnear weightlessness.12.3 inch full LCD cluster/Integrated driving mode (Comfort/Smart/Eco/Sport/Custom)The SuperVision cluster seamlessly integrates an expanded array of information presented in clear, concise and colorfulgraphics. By automatic adjustment of the transmission shift schedule, the integrated driving mode offers the driver a choiceof five types of drive settings to suit drive preference, each displayed in its own specific color.Maximum engagement.Step inside and discover an interior that engages and satisfies all the senses. The cabin is a visual feast projecting elegance and warmth while delivering a rich tactile experience. The dials of the SuperVision cluster come to life with stunning clarity and show impressive depth. Numbersand batons are crisp and clean with the gauges scoring big points for their elegance and functional simplicity.Remote engine startWireless smartphone charging systemLost or misplaced recharging cords? The cord is a thing of the past with the wireless smartphone charging system that ensures your phone will never go dead. Smart door handle with welcome lightPush start button192Maximum Torque nm/4,500 rpm232Maximum Torque nm/4,000 rpmPower with precision.Sonata dials it up with a choice of two new and improved powertrains mated to a six-speed automatic gearbox. Gear selection is controlled by a new shift-by-wire selector that makes for safer, more precise and fool-proof gear changes and its smaller footprint clears up valuable space on the center console. This same push-button convenience is brought to the electronic parking brake which comes with auto-hold that allows the driver to remove his foot from the brake pedal during stops to relax the leg muscles while maintaining brake pressure.Shift-by-wire automatic transmissionMultiple skeleton engine room structureSafety critical sub-substructures, particularly the dash crossmembers andA-pillars are made with hot-stamped steel to attain the highest possible rigidity and better withstand crash impact forces. The novel design even protects cabin occupants against the dangers of secondary impacts—the collisions that can often take place after the initial collision 6 airbag system1) Driver + passenger2) F ront Seat Side (Driver+Passenger)3) Curtain airbagsTake every precaution.Sonata leaps to the front of the race for a lighter, more rigid body structure by using more high-specification steel alloys than ever before. Not only is the body the stiffest ever, but it is 24 kg lighter and quieter than previous generation models. That ensures Sonata meets and, in many cases, even exceeds the most stringent crash safety test standards in the world.Always Safe.A road mishap may not be on your radar, but Hyundai Sonata is best-in-class when it comes to your safety. All geared up with Auto Brake Hold, Electronic Parking Brake, Electronic Stability Control, Hill-Start Assist, ISOFIX Child Seat Anchors and 6 Front and Rear Airbag System. Sonata’s top-notch safety technology loves and protects you like family.Auto brake holdAuto child lockElectronic Stability Control (ESC) and Traction ControlPanoramic sunroofFeatures.Front personal LED Lamps Rear window curtain LED headlamps (Projection type)/Daytime running light (LED)Horizontal LED Rear Tail lights with LED turn signal lampsRear AC vents Black & Chrome coating radiator grille LED high mount stop lamp Powered rear curtain18˝Alloy wheel Shift-by-wire 6-Speed automatic transmissionWireless smartphone charging system8” Floating infotainment system displayDual zone automatic climate control Arm rest (rear seats)Rear camera and concealed boot lid buttonDriver’s 10-way powered Seat + 4 way powered Passenger SeatInterior colors.Exterior colors.Polar whiteMetallic silverHampton grayOxford blueDiamond metallic blackLeatherCamel two-tone interior1,860 1,6181,625 2,8404,900Overall width (mm) Wheel tread* (mm)Wheel tread* (mm)Wheel base (mm) Overall length (mm)Overall height (mm) 1,445Specifications.Specifications.31Specifications.3233● The above values are results from internal testing and are subject to change after validation.● Some of the equipment illustrated or described in this catalog may not be supplied as standard equipment and may be available at extra cost.● Hyundai Motor Company reserves the right to change specifications and equipment without prior notice. ● The color plates shown may vary slightly from the actual colors due to the limitations of the printing process.●Please consult your dealer for full information and availability on colors and trims.3435Dealer stamp+92-42-111 111 466hyundaipakistan 1-B, Aziz Avenue, Canal Bank Road, Gulberg V, Lahore Phone +92-42-111 111 466, ***********************Hyundai Nishat Motor (Private) Limited。
伺服 驱动电机 方法
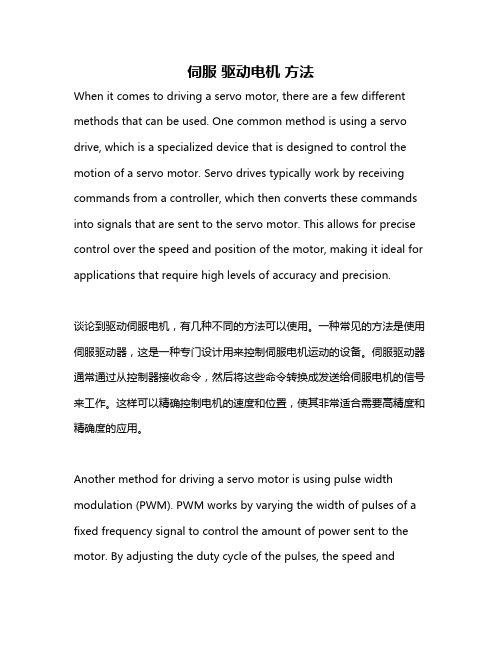
伺服驱动电机方法When it comes to driving a servo motor, there are a few different methods that can be used. One common method is using a servo drive, which is a specialized device that is designed to control the motion of a servo motor. Servo drives typically work by receiving commands from a controller, which then converts these commands into signals that are sent to the servo motor. This allows for precise control over the speed and position of the motor, making it ideal for applications that require high levels of accuracy and precision.谈论到驱动伺服电机,有几种不同的方法可以使用。
一种常见的方法是使用伺服驱动器,这是一种专门设计用来控制伺服电机运动的设备。
伺服驱动器通常通过从控制器接收命令,然后将这些命令转换成发送给伺服电机的信号来工作。
这样可以精确控制电机的速度和位置,使其非常适合需要高精度和精确度的应用。
Another method for driving a servo motor is using pulse width modulation (PWM). PWM works by varying the width of pulses of a fixed frequency signal to control the amount of power sent to the motor. By adjusting the duty cycle of the pulses, the speed andposition of the motor can be controlled. This method is often used in applications where simplicity and cost-effectiveness are important, as it does not require complex control algorithms or specialized hardware.驱动伺服电机的另一种方法是使用脉冲宽度调制(PWM)。
A High-Speed Sliding-Mode Observer for the Sensorless Speed Control of a PMSM
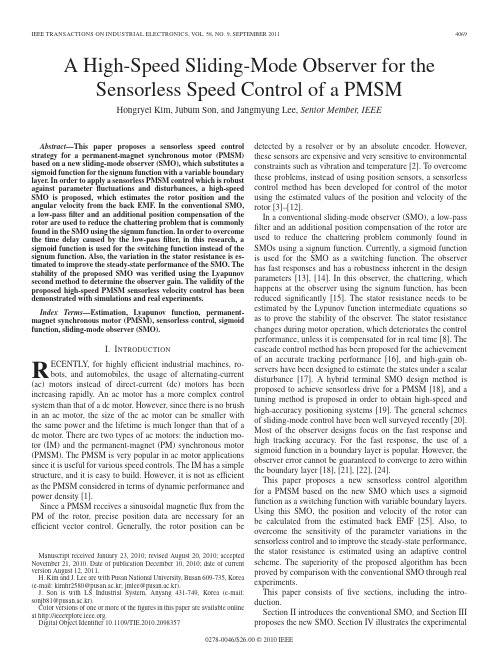
4069
A High-Speed Sliding-Mode Observer for the Sensorless Speed Control of a PMSM
detected by a resolver or by an absolute encoder. However, these sensors are expensive and very sensitive to environmental constraints such as vibration and temperature [2]. To overcome these problems, instead of using position sensors, a sensorless control method has been developed for control of the motor using the estimated values of the position and velocity of the rotor [3]–[12]. In a conventional sliding-mode observer (SMO), a low-pass filter and an additional position compensation of the rotor are used to reduce the chattering problem commonly found in SMOs using a signum function. Currently, a sigmoid function is used for the SMO as a switching function. The observer has fast responses and has a robustness inherent in the design parameters [13], [14]. In this observer, the chattering, which happens at the observer using the signum function, has been reduced significantly [15]. The stator resistance needs to be estimated by the Lypunov function intermediate equations so as to prove the stability of the observer. The stator resistance changes during motor operation, which deteriorates the control performance, unless it is compensated for in real time [8]. The cascade control method has been proposed for the achievement of an accurate tracking performance [16], and high-gain observers have been designed to estimate the states under a scalar disturbance [17]. A hybrid terminal SMO design method is proposed to achieve sensorless drive for a PMSM [18], and a tuning method is proposed in order to obtain high-speed and high-accuracy positioning systems [19]. The general schemes of sliding-mode control have been well surveyed recently [20]. Most of the observer designs focus on the fast response and high tracking accuracy. For the fast response, the use of a sigmoid function in a boundary layer is popular. However, the observer error cannot be guaranteed to converge to zero within the boundary layer [18], [21], [22], [24]. This paper proposes a new sensorless control algorithm for a PMSM based on the new SMO which uses a sigmoid function as a switching function with variable boundary layers. Using this SMO, the position and velocity of the rotor can be calculated from the estimated back EMF [25]. Also, to overcome the sensitivity of the parameter variations in the sensorless control and to improve the steady-state performance, the stator resistance is estimated using an adaptive control scheme. The superiority of the proposed algorithm has been proved by comparison with the conventional SMO through real experiments. This paper consists of five sections, including the introduction. Section II introduces the conventional SMO, and Section III proposes the new SMO. Section IV illustrates the experimental
感应电机无速度传感器直接转矩控制系统的实验研究

华中科技大学文华学院毕业设计(论文)题目:感应电机无速度传感器直接转矩控制系统的实验研究学生姓名:学号:学部(系):专业年级:指导教师:职称或学位:高级工程师2010 年 5 月 28 日目录目录........................................................................................................................... - 2 - 摘要........................................................................................................................... - 3 - 关键词................................................................................................................ - 3 - Abstract ..................................................................................................................... - 3 - Keywords ........................................................................................................... - 5 - 第1章绪论......................................................................................... - 5 -1.1选题目的及意义:...................................................................................... - 5 -1.2.课题发展现状和前景展望....................................................................... - 5 -1.3 研究内容..................................................................................................... - 6 - 第2章感应电机无速度转矩矢量控制原理......................................................... - 7 -2.1 异步电机的数学模型与坐标变换............................................................. - 7 -2.1.1异步电机的基本方程式.................................................................... - 7 -2.1.2 异步电动机的几种等效电路......................................................... - 10 -2.1.3坐标变换........................................................................................ - 13 -2.2 矢量控制变频调速系统的原理............................................................... - 17 -2.2.1 矢量控制基本方程式..................................................................... - 17 -2.2.2 转差型矢量控制............................................................................. - 19 -2.3 无速度传感器矢量控制系统的结构和速度观测原理........................... - 19 -2.3.1 无速度传感器矢量控制系统的原理............................................. - 19 -2.3.2 感应电机矢量控制系统的基本思路............................................. - 20 -2.3.3转子磁链定向的矢量控制系统...................................................... - 20 -2.4 无速度传感器矢量控制技术................................................................... - 21 - 第3章仿真设计................................................................................. - 23 -3.1 仿真平台................................................................................................... - 23 -3.2 仿真准备................................................................................................... - 24 -3.3 仿真电路................................................................................................... - 25 - 第4章仿真结果................................................................................. - 25 -4.1 仿真结果波形........................................................................................... - 25 -4.2 结果分析................................................................................................... - 26 -4.3结论............................................................................................................ - 27 - 第5章总结......................................................................................... - 27 - 参考文献................................................................................................................. - 27 - 致谢......................................................................................................................... - 29 -摘要直接转矩控制技术是继矢量控制技术之后交流传动领域中一种新兴的控制技术,它省去了复杂的矢量变换,具有动态响应快、结构简单、易于实现等优点。
- 1、下载文档前请自行甄别文档内容的完整性,平台不提供额外的编辑、内容补充、找答案等附加服务。
- 2、"仅部分预览"的文档,不可在线预览部分如存在完整性等问题,可反馈申请退款(可完整预览的文档不适用该条件!)。
- 3、如文档侵犯您的权益,请联系客服反馈,我们会尽快为您处理(人工客服工作时间:9:00-18:30)。
New advances in the development of fast semiconductor switches and cost-effective DSP processors have revolutionized the adjustable speed motor drives. These new opportunitieshave contributedto the field of motor drives by introducing novel configurations for electric machines in which the burden is shifted from complicated hardware structures onto software and control algorithms. This in turn has resulted in considerable improvement in cost while upgrading the performance of the overall drive system. The BLDC motor drive system is the most illustrative example of this trend. Very compact geometry and an impressive efficiency, along with a very simple control are among the main attractions for replacing many adjustable ih speed applications wt this emerging technology. The BLDC motor is increasingly being used in computer, aerospace, military, automotive, industrial and household products because of its high torque, compactness, and high eficiency. A BLDC motor with higher number of phases has several advantages compare to the conventional three-phase BLDC motors. It can reduce the torque ripple and increase the efficiency and iron utilization without increasing the voltage per phase. For mltr applications, the fault tolerant feature iiay is one of the most important considerations. With higher number of phases, a utilized motor can be still operated when one or more phases are failed. Based on these advantages, the multi-phase BLDC motor is considered as a good candidate for energy saving or military applications. The BLDC motor is inherently electronically controlled and requires rotor position information for proper commutation of currents. H w v r the problems of the cost and oee, reliability of rotor position sensors have motivated research in the area of psition sensorless BLDC motor drives. Solving this problem effectively will open the way for full
Tae-Hyung Kim’, Hyung-Woo Lee’, M C ~ ~ J E E E , Mehrdad Ehsani3,FCUOW,IEEE and
Department of Electrical Engineering, Texas A&M University, USA, e-mail: , ehsani@ Department oflleoretical and Applied Mechanics, Comell University, USA, e-mail : hl333@
Where, v, is the active phase voltage; R is the phase resistance; i is the phase current; B is the rotor position; , wk(@,i,) is the total flux linkage of the active phase; and ‘n’ is the number of phases. The flux linkage in the active phase includes both self and mutual flux linkages. For any multi-phase BLDC motors, the total flux linkage of a phase is:
n. MATHEhUTICAL BMlS OF THE m O W S E DSENຫໍສະໝຸດ ORLESS DRIVE METEOD
Each active phase in an AC motor is described by a first order differential equation. The general voltage equation of one of the active phases is given by,
Absfruct- The main purpose of tbls paper Is to develop a new posjtion sensorless drive method for multi-phase brushleas DC (BLDC) motors. A BLDC motor with higher number of phases has several advantages. It can reduce the Ampereturns and torque puIsalion and Increase the efficiency and h n utilization. Also, it is well used for fault tolerant motor drive systems 85 in military applications. With the developed speed-independent, new p c aiiios information that i computed i a microprocessor, highly s n accurate sensorless operation can be reabed for multLphase BLDC m t r . The operational principle of the proposed senoos sorless drive for multi-phase BLDC motors is theoretically analyzed and the performance is demonstrated by computer aimulatlons and experiments i detail. n
penetration of this motor drive into all low cost, high reliability, and large volume applications. Most popular and practical sensorless drive methods for BLDC motors rely on speed-dependent back-EMF Ill-[4]. Since the back-EMF is zero or undetectably small at standstill and low speeds, it is not possible to use the back-EMF sensing method at low speed range. Also, the estimated commutation points that are shified by 30” fiom zero crossing of back-EMFs have position error in transient state. The flux estimation method [5]-[ti] also has significant estimation error at low speed, in which the voltage equation is integrated in a relatively large period of time. In this paper, we propose a novel sensorless drive technique for multi-phase BLDC motors that covers wide speed range from near zero to high speed without additional h r w r for sensing terminal voltages. This sensorless opadae eration technique is very suitable for multi-phase BLDC motors that are gaining lots of interest for various applications. This sensorless method provides continuous rotor position informationwith good accuracy and resolution even at very IOW speed operation. This feature makes it suitabIe for high performance applications. Furthermore, the proposed sensorless algorithm is simple enough to implement in real-time using an economical, fixed-point microprocessor. The validity of the developed sensorless drive method for multi-phase BLDC motors has been verified by the computer simulationsand experiment.