CRH2型动车组车轮踏面镟修用刀片的经济性选择共5页word资料
动车组不落轮车床暂行技术条件

TJ/CL ***-2016动车组不落轮车床暂行技术条件1范围适用于CRH系列各型动车组,在车辆轮对不解体的条件下,对车轮轮缘踏面的镟修,并且也适用于单个轮对轮缘踏面镟修。
单轴不落轮车床满足同时对同一轮对的两个车轮轮缘踏面的镟修。
双轴不落轮车床满足同时对同一转向架两个轮对的四个轮缘踏面的镟修。
2规范性引用文件下列文件对于本技术条件的应用是必不可少的。
凡是注日期的引用文件,仅注日期的版本适用于本技术条件。
凡是不注日期的引用文件,其最新版本(包括所有的修改单)适用于本技术条件。
GB/T9061-2006《金属切削机床通用技术条件》;GB/T5226.1-1996《工业机械电气设备第1部分通用技术条件》;GB/T7935-2005《液压元件通用技术条件》;GB/T6576-2002《机床润滑系统》;GB/T 15760-2004《金属切削机床安全防护通用技术条件》;GB/T 1182-1996 《形状和位置公差通则、定义、符号和图样表示法》GB/T 1184-1996《形状和位置公差未注公差的规定》;GB/T4064-1983 《电气设备安全设计导则》;GB/T16769-2008《金属切削机床噪声声压级测量方法》;GB/T3766-2001《液压系统通用技术条件》;TB/T449-2003《机车车辆车轮轮缘踏面外形》;UIC519-2004《Method to determining the equivalent conicity》(等效锥度的测定方法)3术语和定义3.1踏面径向跳动径向跳动是指被测回转表面在同一横剖面内实际表面上各点到基准轴线间距离的最大径向变动量,本技术条件中的踏面径向跳动特指踏面滚动圆位置对应的径向跳动。
参见GB/T 1182-1996、TB/T449-2003。
3.2车轮多边形车轮多边形是指车轮相对回转中心的规律性偏离,本技术条件中的车轮多边形由踏面滚动圆位置对应的径向变动量随相位的函数(简称“径跳函数”)及其傅里叶变换参数来评价,1-9阶称为低阶多边形,10阶及以上称为高阶多边形,具体见附件1。
CRH2型动车组一二级检修简介

4M4T 8M8T
6M2T 8M8T
☆CRH2A型动车组定编及主要车内设备情况
车号 形式
1
T1
2
M1
3
M2
4
T2
5
T3
6
M3
7
M4
8
T2
合计
座席
主要设备
55 二等车、驾驶室、坐式厕所、盥洗室、小便间
100 二等车、饮水器
85 二等车、备品室、坐式厕所、盥洗室、小便间
100 二等车、饮水器
55 二等车、酒巴餐饮区、坐式厕所、盥洗室、小便间
受电弓
(二)①、②号上部设备检查作业
成员分工:
1.①、②号联合检查作业:(1)-(2)项 2.①号独立检查作业:(1)-(5)项 3.②号司机室独立检查作业:(1)-(8)项
1、①②号人员联合检查
(1)标志灯 ①号作业人员在车上进行车灯减光操作, ②号下车确认标志灯光颜色转换状态良好。
CRH2A动车组标志灯(前进)
(一)①、②号车顶设备检查作业
• 注意事项: 接触网供断电时应穿戴绝缘鞋、绝缘
手套和防护帽;作业前确认接触网断电,防护号志和接 地杆可靠插设;作业时注意脚下,在车顶防滑部分行走, 防止跌倒滑落
• 使用工具:手电筒、对讲机、钢板尺、棉布、清洁
剂等
检查路线
• ①、②号作业人员通过领取登顶卡进行登顶作业
3、②号作业人员独立检查
(1)空气管开闭器 检查空气管开闭器及配气管路,开闭器处于关闭位,气
路无漏泄。(重联动车组重联端开闭器处于开启位)
空气开闭器
(2)分并装置
并装置处于分割位, 气路无漏泄,气路截断 塞门处于开启位, 电线插头无松动。 (重联动车组重联端
轮对故障检修论文-CRH2型车辆轮轴部分的故障与检修浅谈
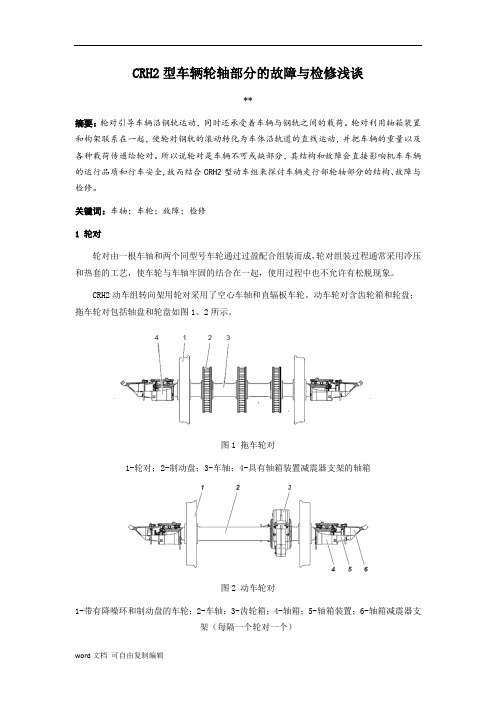
CRH2型车辆轮轴部分的故障与检修浅谈**摘要:轮对引导车辆沿钢轨运动,同时还承受着车辆与钢轨之间的载荷。
轮对利用轴箱装置和构架联系在一起,使轮对钢轨的滚动转化为车体沿轨道的直线运动,并把车辆的重量以及各种载荷传递给轮对。
所以说轮对是车辆不可或缺部分,其结构和故障会直接影响机车车辆的运行品质和行车安全,故而结合CRH2型动车组来探讨车辆走行部轮轴部分的结构、故障与检修。
关键词:车轴;车轮;故障;检修1 轮对轮对由一根车轴和两个同型号车轮通过过盈配合组装而成,轮对组装过程通常采用冷压和热套的工艺,使车轮与车轴牢固的结合在一起,使用过程中也不允许有松脱现象。
CRH2动车组转向架用轮对采用了空心车轴和直辐板车轮。
动车轮对含齿轮箱和轮盘;拖车轮对包括轴盘和轮盘如图1、2所示。
图1 拖车轮对1-轮对;2-制动盘;3-车轴;4-具有轴箱装置减震器支架的轴箱图2 动车轮对1-带有降噪环和制动盘的车轮;2-车轴;3-齿轮箱;4-轴箱;5-轴箱装置;6-轴箱减震器支架(每隔一个轮对一个)轮对的作用是引导车辆沿钢轨运动,同时还承受着车辆与钢轨之间的载荷。
因此,轮对应具有足够的强度,以保证车辆的安全运行。
在保证强度和使用寿命的前提下,应减轻轮对的重量,并使其有一定的弹性,以减少车轮与钢轨之间的动作力和磨耗。
轮对的内测距是保证车辆运行的一个重要参数。
我国铁路采用1435mm的标准轨距,轮对在钢轨上滚动时,轮对内侧距应该保证在最不利的条件下,车轮踏面在钢轨上仍有足够的安全搭接量,不造成掉道,同时还应该保证车辆在线路上运行时轮缘与钢轨之间有一定的游隙。
轮缘与钢轨之间的游隙太小,可能造成轮缘与钢轨之间的严重磨耗;轮缘与钢轨之间的游隙太大,会使轮对蛇形运动的振幅增大,影响车辆运行的品质。
CRH2型动车组轮对的内测距为1353+2mm。
-1轮对的结构还应有利于车辆顺利通过曲线和安全岔道。
1.1 车轴绝大多数的车轴为圆截面实心轴,采用优质碳素钢加热锻压成型,再经热处理(正火或正火后回火)和机械加工制成。
踏面加工刀片优化与应用

踏面加工刀片优化与应用发布时间:2021-07-02T10:36:30.693Z 来源:《工程管理前沿》2021年第7卷7期作者:马筱雅[导读] 通过对踏面加工刀片的优化选择,马筱雅中车贵阳车辆有限公司贵州省贵阳市 550017摘要:通过对踏面加工刀片的优化选择,制定有效的控制措施,在保证轮对踏面加工质量的前提下,有效地控制了踏面加工使用刀片的成本。
关键词:轮对、检修、踏面加工、刀片轮对踏面加工是轮对检修的重要工序,由于踏面外形结构较为复杂,对加工使用的刀片有非常大考验。
在加工过程中,踏面的磨耗深浅、进给量的大小等因素都会影响刀片的使用率。
为了解决刀片成本控制问题,本文对踏面加工刀片进行优化并应用。
1、现状分析目前踏面加工使用的是型号为TT8115涂层硬质合金刀片。
加工用车床倍率调节的主轴转速分别为15r/min、20r/min、30r/min。
刀片参数如表1所示。
根据表1及现场使用情况可以看出,考虑到车床的生产效率、轮对加工质量、加工表面粗糙度、刀片的排屑槽样式等方面,选择型号为TT8115合金刀片还是比较合理的。
在使用过程中,此刀片排屑情况良好,铁屑不容易刮伤加工表面。
韧性较好,不容易断裂且不会崩碎,加工的轮对质量较为稳定。
但刀片强度较低,损耗较大。
仅2019年,平均每片刀片加工的轮对数为4条(1辆=4条轮对),长期使用不利于生产成本控制。
因此,在保证质量的前提下,控制生产成本首先要控制刀片损耗。
2、优化方案2.1刀片优化2.1.1刀片选择刀片的损耗,即刀片的耐用度,与刀片的切削速度密切相关。
目前现场使用的原刀片切削速度为Vc=170~220m/min。
加工时平均1片刀片加4条车轮,耐用度略低,可以考虑选择切削速度相对较低的刀片。
在轮对踏面加工过程中,除刀片本身,待加工轮对的状态也会影响刀片使用寿命。
车轮踏面裂纹较大或踏面擦伤严重,刀片容易崩碎。
踏面磨耗较大,需要连续加工多次才能消除缺陷,使刀片损耗在一条轮对上,缩短刀片的使用寿命,即加工工件数。
CRH2动车组轮对检修流程及改进设计

摘要 (I)第1章绪论 (1)1.1研究背景 (1)1.2研究思路 (1)第2章轮对的组成 (2)2.1轮对组成的内容 (2)2.2车轴 (4)2.3轮箍 (5)2.4轮心 (5)2.5车轮 (6)2.6制动盘(车轮制动盘和车轴制动盘) (7)2.7齿轮装置 (8)第3章轮对的故障 (9)3.1轮对故障产生的原因 (9)3.2车轴故障 (9)3.3车轮故障 (10)第4章轮对的检修流程 (14)4.1轮对检修流程的内容 (14)4.2轮对修程分类 (14)4.3轮对的无损探伤 (15)4.4轮对的维修 (19)4.5轮对的组装 (19)第5章轮对检修流程的改进设计 (21)5.1原厂修轮对检修流程 (21)5.2改进后的厂修轮对检修流程 (21)5.3改进厂修轮对检修流程的优点 (21)参考文献 (22)致谢 (23)轮对即动车组与钢轨相接触的部分,由左右两个车轮牢固的压装在同一根车轴上所组成,轮对也是保证动车组在钢轨上的运行和转向,承受来自动车组的全部静、动载荷,把它传递给钢轨,并因线路不平顺产生的载荷传递给动车组各零部件。
轮对的作用是沿着钢轨滚动,将轮对的滚动转化为车体的平移;除了传递车辆重量外,还传递轮轨之间的各种作用力,包括牵引力和制动力。
其结构和故障会直接影响动车组的运行品质和行车安全,因此结合CRH2型动车组来探讨轮对的组成结构、故障、检修流程及改进设计。
关键词:轮对组成;故障;检修流程;改进设计CRH2动车组轮对检修流程及改进设计第1章绪论1.1研究背景近几年,随着高速动车组的迅速发展,高铁已经我国大多数人出行选择的交通方式,而轮对是高速动车在轨道上运行必不可少的元件之一。
动车的全部重量通过轮对支撑在钢轨上;通过轮对与钢轨的黏着产生牵引力或制动力;通过轮对滚动使动车前进。
另外,轮对在动车运行中的承载情况比较繁重,当车轮经钢轨接头、道岔等线路不平顺处时,轮对直接承受全部垂向和侧向的冲击。
CRH2动车组轮对与轴箱弹簧

CRH2动车组轮对与轴箱弹簧CRH2动车组轮对与轴箱弹簧CAD/CAE设计一、轴箱弹簧的CAD/CAE设计(一)问题描述1.CRH2轴箱弹簧组组成参数:图1.1 轴箱弹簧组组成及参数1—外圈弹簧;1—内圈弹簧;3—防雪罩(二)轴箱弹簧组的CAD设计1.轴箱内弹簧的CAD设计采用三段直线扫描法:绘制三条首尾相连的直线→绘制簧条圆→利用扫描特征中的沿路径扭转命令依次创建弹簧基体→利用拉伸切除特征创建支撑圈。
完成如下图所示的零件造型:图1.2 内弹簧图1.3 外弹簧(三)轴箱弹簧组的CAE设计1.轴箱外弹簧的CAE设计1.1刚度计算1.1.1受力分析弹簧下端受到轴箱支撑面的支持力,上端施加1mm的位移,计算支撑反力即可得到弹簧刚度的大小。
1.1.2应力计算(1)前处理:基本思想:弹簧一端固定,另外一端施加单位位移,所得固定端支反力即为弹簧刚度。
定类型:CRH2轴箱外弹簧属于静态分析画模型:调用之前建立好的轴箱外弹簧模型设属性:设弹簧材料为碳钢板分网格:共13137个节点,6999个单元。
如下图所示:图1.4 网格划分(2)求解:添约束:在弹簧下端加固定几何体约束;加载荷:在弹簧上端施加1mm的位移;图1.5 施加约束与载荷查错误:载荷列表后进行检查;求结果:进行有限元分析。
(3)后处理:列结果:列举约束反力下结论:轴箱外弹簧的刚度为652N/mm。
1.2强度计算1.2.1应力计算(1)前处理:定类型:CRH2轴箱外弹簧属于静态分析;画模型:调用之前建立好的轴箱外弹簧模型设属性:设弹簧材料为碳钢板分网格:共19508个节点,10940个单元。
如下图所示:图1.7 网格划分(2)求解:添约束:在弹簧下端加固定几何体约束;加载荷:在弹簧上端施加47.2mm的位移载荷;查错误:载荷列表后进行检查;求结果:进行有限元分析。
(3)后处理:绘图形:加载后的应力图、位移图如下所示:由上可知,外弹簧的刚度为363N/mm,弹簧所受载荷最大为28700.84N.所以弹簧上端所发生的最大位移为28700.84/363mm=79.066mm,分析时可简化为一端固定,另一端发生79.066mm的位移。
CRH2型动车组车轮滚动接触疲劳问题分析
87中国设备工程Engineer ing hina C P l ant中国设备工程 2018.02 (下)1 问题的提出随着铁路高速重载技术的快速发展,轮轨滚动接触疲劳现象越来越严重,这不但会造成运营和维修成本的大幅增加,同时也直接影响列车运营安全。
CRH2型动车组车轮采用ER8材质的车轮,近年来发生了多起车轮滚动接触疲劳故障,其中头尾车导向轮发生车轮滚动接触疲劳概率相对较高。
2 原因分析材料在循环应力作用下,产生局部永久性积累损伤,经过一定的循环次数后,接触表面产生麻点、浅层或深层剥落的过程称为接触疲劳。
车轮载荷通过一个相对很小的接触区域传递给了钢轨,通常会使局部载荷超过车轮和钢轨材料的弹性极限,这就会导致滚动接触疲劳裂纹的萌生。
CRH2型动车组车轮滚动接触疲劳主要为两类,第一类主要由横向力和纵向力引起,一般发生在车轮滚动圆外侧15~30mm 范围内,裂纹与踏面间倾斜约45°,车轮周圈均存在;第二类主要由车轮硌伤引起,发生在名义滚动圆至外侧15mm 范围内,一般发生在个别点,表现为镟轮后内部出现月牙形缺陷。
滚动接触疲劳如不及时进行镟修,均会导致剥离。
2.1 由横向力和纵向力引起的滚动接触疲劳动车组运行过程中,车轮承受纵向力、横向力和垂向力,其中纵向力主要由牵引、制动产生,横向力主要由车辆过曲线和蛇形运动产生,垂向力主要由车辆自身重量及垂向冲击产生。
车轮表面材料反复承受上述疲劳载荷作用,踏面材料发生塑性变形,此类滚动接触疲劳主要由横向力和纵向力引起,在应力超过剪切强度的条件下(主要在过曲线时),塑性应变累积而形成微裂纹,最终导致滚动接触疲劳,并在上述应力作用下裂纹沿45°方向向内部扩展,最终形成剥离。
此类缺陷起源于踏面表面,由于表面裂纹萌生阶段尺寸很小,肉眼看不到缺陷。
动车组的头尾车在进入弯道时导向轮对首先进入弯道,此时导向轮对车轮受到的横向力及纵向力较中间车更大且更为复杂,因此动车组的头车位置轮对更易发生滚动接触疲劳现象。
CRH2动车组动力学性能分析
表 3 抗蛇行减振器阻尼系数值对临界速度的影响
阻尼系数值 / kN·s·m-1
550 600 650 700 750 800 850 900 950
2. 株洲时代新材料科技股份有限公司 弹性元件事业部,湖南 株洲 412007)
作者简介:程 迪(1963-), 摘 要 :以 CRH2 动车组车辆为分析对象,利用 NUCARS 软件对动车组车辆的临界速度、各主 男,硕士,教授,现从事机 要悬挂参数对临界速度的影响趋势、车辆的直线运行响应以及车辆的曲线通过响应进行了分析。结果 车 车 辆 教 学 和 科 研 工 作 。
动车组车辆具有两系悬挂,单车模型中共有 7 个刚 体,即1 个车体、2 个构架、4 个轮对,车体与转向架之间
— 13 —
机 车 电 传 动
2010 年
的连接弹簧和阻尼器等看作是无质量的连接单元,单 元的刚度和阻尼值与实际参数相同。为精确模拟系统 的动力特性,计算中考虑横向和垂向运动相耦合的力 学模型[2]。转向架上的悬挂部件重量转化到构架上。车 体和转向架构架均为 6 个自由度,轮对具有 4 个自由度, 故单车系统共有34 个自由度。 2.1.2 系统中的非线性环节
系统运动微分方程的求解由车辆动力学分析软件 NUCARS2.3 完成,在时域内求解临界速度、动力学响 应和曲线通过性能。 2.1.4 线路条件
表1 为200 km/h速度级线路区段轨道不平顺动态管 理标准(半峰值),响应分析时,以此为依据,设计 2 级 线路不平顺。
第2章 CRH2型动车组转向架
CRH
第一节 转向架结构概要及主要参数
HTY
BOGIE
动 力 转 向 架
13
CRH 第一节 转向架结构概要及主要参数 HTY
BOGIE
横向液压减震器
驱动装置
高度调整阀
牵引电机
构架
盘型制动装置 (基础制动装置)
驱动轮对
一系悬挂装置 轴箱
二系悬挂装置
抗蛇形减震器
动力转向架总图
14
CRH
HTY
第一节 转向架结构概要及主要参数
设计)进行设计,按JIS E 4502标准进行生产。为提高车 轴的疲劳安全性,采用高频淬火热处理和滚压工艺。 为了在保证强度的同时减轻质量,轮对的车轴采用空心车 轴,镗孔径60mm,材料为S38C,轴颈直径φ130 mm, 超声波探伤检测。
26
CRH 第二节转向架主要部件组成及性能
HTY
BOGIE
31
CRH HT第Y 二节 转向架主要部件组成及性能
BOGIE
1.轴箱体结构 轴箱体为钢结构,材质采用铸钢SC450(JIS G 5101)
32
CRH HT第Y 二节 转向架主要部件组成及性能
BOGIE
2.前盖与橡胶盖 轴箱前盖采用铝合金铸件AC4CH-T6(JIS H 5202) 在前盖的前端开口部分装有橡胶盖,防止水、灰尘
2024/8/7
5
CRH
编组改进
HTY
BOGIE
E2-1000动车组采用了8动2拖的列车编组,设计速度
315km/h,列车总功率9600kW;
CRH2型动车组运营速度200km/h,列车编组改为4动4 拖,列车总功率仅为4800kW;
动车组可以采用2列(16辆)联挂运行,能够适合我国长 距离大运输量的运输模式;
CRH2型动车组总体技术
CRH2型动车组总体技术2.1动车组总体技术CRH2型动车组为动力分散、交流传动电动车组。
动车组具有“先进、成熟、经济、适用、可靠”的技术特点。
先进:动车组采用铝合金空心型材车体,采用了先进的IGBT功率元件以及VVVF牵引控制方式。
成熟:动车组的原型车为日本新干线动车组,其主要系统和部件均有长时间的运营业绩。
经济:动车组采用了流线型设计,各车辆的最大轴重仅14t,牵引和制动能耗低。
另外,列车采用再生制动方式,在节能、环保以及减少机械损耗等方面具有独特的优越性。
适用:动车组具有速度提升能力,通过调整动车、拖车的比例,动车组能够灵活适应200~300km/h各速度等级的运行。
另外,动车组还可以通过两列联挂来满足大运量的需求。
可靠:动车组采用了先进的防滑、防空转控制系统和自动列车保护系统,为列车在各种运行环境下的准时性提供了可靠的保障。
2.1.1列车组成和主要参数2.1.1.1编组CRH2型动车组最高运营速度为250km/h,可在中国铁路既有线路(指定区间)和客运专线上运行。
动车组采用8辆编组,4动4拖,由两个动力单元组成,每个动力单元由2个动车和2个拖车(T-M-M-T)组成。
CRH2型动车组编组见图2.1,动车组编组代号意义参见表2.1。
动车组前后两端均设驾驶室,列车通常运行时在前端的驾驶室内进行操作。
受电弓设在4号和6号车上,动车组运行时采用单弓受流,另一受电弓处于折叠状态。
两列动车组可联挂运行,联挂时受电弓采取双弓受流。
表2.1动车组编组代号含义表注:数字1,2表示不同型号。
2.1.1.2轴重配置动车组各车的质量如表2.2所示,列车定员610人,最大轴重为14t,最小轴重11.7t。
表2.2CRH2型动车组各车辆的质量2.1.1.3车辆定位车辆的定位、转向架、车轴及车轮的编号按图2.2进行定义。
2.1.1.4车内主要设备配置CRH2型动车组具体编组结构参见图2.3,各车辆的车内主要设备如表2.3所示。
- 1、下载文档前请自行甄别文档内容的完整性,平台不提供额外的编辑、内容补充、找答案等附加服务。
- 2、"仅部分预览"的文档,不可在线预览部分如存在完整性等问题,可反馈申请退款(可完整预览的文档不适用该条件!)。
- 3、如文档侵犯您的权益,请联系客服反馈,我们会尽快为您处理(人工客服工作时间:9:00-18:30)。
CRH2型动车组车轮踏面镟修用刀片的经济性选择
轮对主要由车轮、车轴、制动盘、齿轮箱及轴箱轴承等部分组成,它直接向钢轨传递重量,通过轮轨间的黏着产生牵引力或制动力,承担着动车行驶、制动等功能。
车轮踏面作为动车组与铁路轨道的直接接触单元,一旦出现异常磨耗及其他缺陷,动车组振动性能下降,构架将会出现横向失稳及蛇行失稳迹象,所以车轮踏面的检修质量直接关系到动车组的安全性及舒适性。
动车组在高级检修时,需在数控车轮车床上对车轮踏面进行镟修加工;在运用检修时,只需对车轮踏面表面质量进行常规检查,一旦发现裂纹、缺损等缺陷时,也需对车轮踏面进行镟修加工。
1车轮踏面镟修要求
CRH2型动车组车轮踏面形式为LMA型(见图1),车轮踏面镟修加工后,需满足以下要求:(1)踏面及轮缘不得存在裂纹、缺损、剥离、擦伤等缺陷;(2)轮缘厚度应符合28~33mm,车轮直径不得小于800mm;(3)同一车轮轮径差不大于0.2mm;(4)表面粗糙度应不大于Ra6.3等。
2车轮踏面镟修分析
CRH2型动车组车轮材料选用具有高硬度的ER8模具钢,车轮踏面镟修过程中刀片极易磨损与刃崩,所以刀片的选择直接关系到镟修质量、人工费用及制造费用。
车轮踏面镟修在数控车轮车床上进行,该车床配备有双工位车刀,刀杆上有主车刀刀片及副车刀刀片安装位,主车刀刀片对轮廓A(见图1)进行镟修,副车刀对轮廓B(见图1)进行镟修。
由图可见,双工位车刀对轮缘曲面部分加工极为方便,而且车床无需配备换刀库,加
工过程中只需准备对应刀片即可。
为便于计算成本,车轮踏面镟修实验中将主车刀刀片与副车刀刀片的寿命累计为单片刀片的寿命。
图1 ;LMA型踏面轮缘轮廓
3实验分析
3.1实验目的
选取不同类型的刀片对车轮踏面进行镟修加工,通过对比各刀片的切削情况,分析并计算车轮踏面镟修过程中产生的刀具成本、人工费用、制造费用等,以便选择较为经济的踏面镟修用刀片。
3.2实验描述
(1)刀片选择。
刀片类型有普通硬质合金刀片、硬质合金涂层刀片、金属陶瓷涂层刀片、非金属陶瓷涂层刀片、聚晶氮化硼刀片、聚晶金刚石刀片等,因车轮材料为ER8新型模具钢,具有良好的热强性、红硬性、耐磨性,硬度约为240~260HBS,所以要求刀片具备高强度、高耐磨性、高红硬性、耐冲击等性能,满足以上特性的常用刀片有普通硬质合金刀片、硬质合金涂层刀片、金属陶瓷涂层刀片,下面就某一刀具品牌的上述三种刀片进行实验与分析。
(2)切削用量的确定。
切削用量包括背吃刀量ap、主轴转速n或切削速度Vc、进给量f或进给速度Vf,根据厂家刀具切削手册查询,普通硬质合金刀片、硬质合金涂层刀片、金属陶瓷涂层刀片的切削速度Vc依次为120m/min、160m/min、180m/min,进给量f依次为0.18mm/r、0.25mm/r、0.18mm/r;根据主轴转速n=1000Vc/(π×D)、进给速度Vf=n×f可以计算出相关参数(注:式中D为车轮直径,在此取860mm,踏面镟修一般情
况下加工余量较小,背吃刀量ap可不考虑),具体数值如下表1:表1
刀片类型
切削用量普通硬质合金刀片硬质合金涂层刀片金属陶瓷涂层刀片主轴转速n(r/min) 45 60 105
进给速度Vf(mm/min) 8 15 19
(3)刀片成本。
以上表切削用量为依据,对普通硬质合金刀片、硬质合金涂层刀片、金属陶瓷涂层刀片进行轮对踏面镟修实验,其寿命依次为3条/片、5条/片、9条/片;根据此品牌刀具供应商提供的价格,单价依次为95元/片、175元/片、480元/片;经计算,三种类型的刀片成本依次为31.70元/条、35.00元/条、47.30元/条(注:单位中的条指一条轮对)。
(4)直接人工费用及制造费用。
直接人工费用指直接从事产品生产的工人薪酬,约为22元/小时;制造费用指车间管理人员工资、水电费、修理费、折旧费、递延资产摊销、运输费用等,约为65元/小时。
以上述切削用量表为依据,根据车削工时T=(L+L1)/Vf(其中L为踏面镟修长度,L1为导入导出量,在踏面镟修时,L约为160mm,L1约为5mm)计算,三种类型的刀片镟修工时依次为41分钟/条、22分钟/条、17分钟/条;经计算,对应的直接人工费用依次为15.00元/条、8.10元/条、6.20元/条;制造费用依次为44.40元/条、23.80元/条、18.40元/条。
(5)费用汇总。
轮对镟修中的各项成本及费用汇总如下表2(注:表中的总费用只含轮对踏面镟修过程中的刀具成本、直接人工费用、制造费
用,不包含辅助作业时间内发生的各项费用):
表2
刀片类型
成本及费用普通硬质合金刀片硬质合金涂层刀片金属陶瓷涂层刀片
刀具成本(元/条) 31.70 35.00 47.30
直接人工费用
(元/条) 15.00 8.10 6.20
制造费用(元/条) 44.40 23.80 18.40
总费用(元/条) 91.20 66.90 78.00
4结语
从上述实验结果可以看出,车轮踏面镟修时,刀片类型直接关系到加工成本,价格昂贵的高档刀片加工成本不一定很高,价格较低的普通刀片加工成本也不一定很低,刀片选择的关键在于,要根据被加工材料选取合适类型的刀片经济性才较好。
动车组车轮踏面镟修时,在常用的普通硬质合金刀片、硬质合金涂层刀片及金属陶瓷涂层刀片三种类型的刀片中,选用硬质合金涂层刀片较为经济。
另外,现在的刀片品牌较多,同种类型而品牌不同的刀片制造工艺不同,质量及价格也不同,后续可以继续研究。
希望以上资料对你有所帮助,附励志名言3条:
1、生命对某些人来说是美丽的,这些人的一生都为某个目标而奋斗。
2、推销产品要针对顾客的心,不要针对顾客的头。
3、不同的信念,决定不同的命运。