电厂脱硫炉内喷钙方案比较
炉内喷钙脱硫反应方程式

炉内喷钙脱硫反应方程式
摘要:
一、引言
二、炉内喷钙脱硫反应的化学方程式
三、炉内喷钙脱硫技术的优势
四、炉内喷钙脱硫技术在我国的应用
五、结论
正文:
炉内喷钙脱硫技术是一种广泛应用于燃煤电厂、钢铁厂等工业领域的脱硫技术。
该技术通过向锅炉燃烧室内喷射适量的钙基脱硫剂,使得燃烧产生的二氧化硫与钙基脱硫剂发生反应,生成硫酸钙等物质,从而达到脱硫的目的。
炉内喷钙脱硫反应的化学方程式如下:
1.燃烧产生的二氧化硫(SO2)与钙基脱硫剂(CaO)反应,生成硫酸钙(CaSO3):
SO2 + CaO → CaSO3
2.硫酸钙进一步与氧气(O2)反应,生成硫酸钙(CaSO4):
2CaSO3 + O2 → 2CaSO4
炉内喷钙脱硫技术具有以下优势:
1.脱硫效果好:钙基脱硫剂与二氧化硫反应的化学方程式具有较高的反应转化率,能有效降低排放的二氧化硫浓度。
2.适应性广:炉内喷钙脱硫技术适用于各种类型的燃烧设备,对煤种、负
荷变化等的适应性强。
3.占地面积小:与传统的脱硫设备相比,炉内喷钙脱硫技术所需的设备体积较小,节省了空间和投资成本。
4.运行成本低:钙基脱硫剂价格相对较低,且在反应过程中不易磨损,降低了运行维护成本。
炉内喷钙脱硫技术在我国的应用取得了显著成果。
自2000 年代开始,我国在燃煤电厂、钢铁厂等领域大力推广炉内喷钙脱硫技术,有效降低了二氧化硫排放,改善了空气质量。
此外,我国还积极参与国际技术交流与合作,为全球环境保护作出了贡献。
总之,炉内喷钙脱硫技术是一种高效、经济、环保的脱硫技术,具有广泛的应用前景。
炉内喷钙脱硫工艺

炉内喷钙脱硫工艺
炉内喷钙脱硫工艺是一种常用的烟气脱硫方法,主要适用于燃煤炉发电厂锅炉脱硫用。
该系统主要任务是完成物料输送、计量、送粉量调节、炉内喷射,从而使石灰石粉在炉内锻烧分解,利用生成的CaO与炉内烟气中的SO2进行反应实现炉内脱硫。
炉内喷钙脱硫石灰石粉喷射输送系统以罗茨风机为动力源,采用输粉机(料封泵,也叫低压连续气力输送泵)气源射流原理,利用高速气流的引射作用来输送粉状物料。
炉内喷钙脱硫工艺具有以下优点:
1.工艺简单,设备可靠,脱硫效率高,运行稳定;
2.无需建设烟气再热系统,投资和运行费用较低;
3.脱硫剂选择范围广,可根据当地资源选择合适的吸收剂;
4.脱硫产物为硫酸钙,可资源化利用或直接排放;
5.可与其他脱硫技术结合使用,提高整体脱硫效率。
需要注意的是,炉内喷钙脱硫工艺对吸收剂的粒度和反应活性要求较高,需要经过专门的加工和处理。
同时,该工艺对炉内温度和反应条件要求较高,需要严格控制反应条件,以保证脱硫效率和设备安全。
府谷方正电厂锅炉炉内喷钙脱硫情况
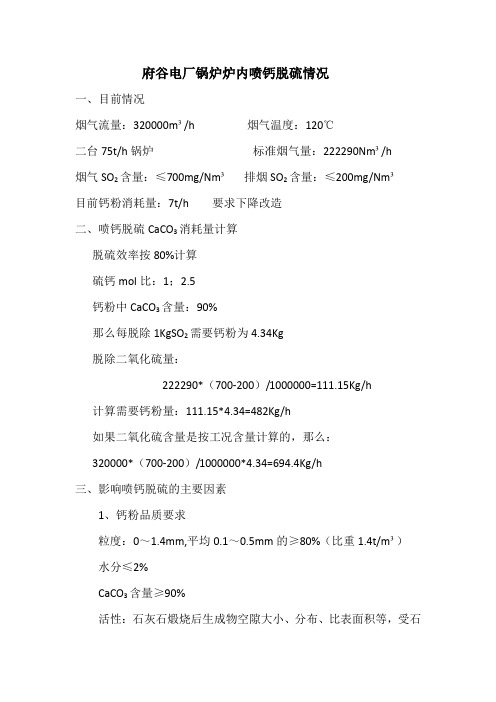
府谷电厂锅炉炉内喷钙脱硫情况
一、目前情况
烟气流量:320000m³/h 烟气温度:120℃
二台75t/h锅炉标准烟气量:222290Nm³/h
烟气SO2含量:≤700mg/Nm³排烟SO2含量:≤200mg/Nm³
目前钙粉消耗量:7t/h 要求下降改造
二、喷钙脱硫CaCO3消耗量计算
脱硫效率按80%计算
硫钙mol比:1;2.5
钙粉中CaCO3含量:90%
那么每脱除1KgSO2需要钙粉为4.34Kg
脱除二氧化硫量:
222290*(700-200)/1000000=111.15Kg/h 计算需要钙粉量:111.15*4.34=482Kg/h
如果二氧化硫含量是按工况含量计算的,那么:
320000*(700-200)/1000000*4.34=694.4Kg/h
三、影响喷钙脱硫的主要因素
1、钙粉品质要求
粒度:0~1.4mm,平均0.1~0.5mm的≥80%(比重1.4t/m³)
水分≤2%
CaCO3含量≥90%
活性:石灰石煅烧后生成物空隙大小、分布、比表面积等,受石
灰石晶体发育程度、杂质、煅烧温度的影响;
2、喷入点
温度800 ~900℃,位置,喷入形式,速度,风量
3、钙粉输送系统
均匀性
4、气源品质
压力,水分
5、锅炉燃烧环境等。
3×75t炉内喷钙方案
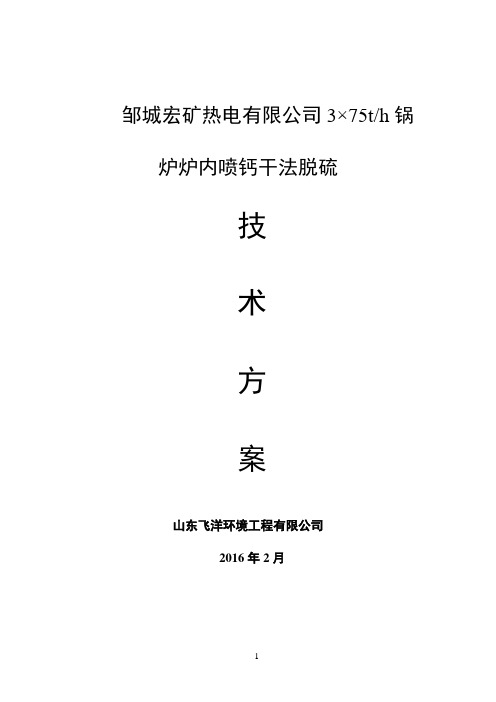
邹城宏矿热电有限公司3×75t/h锅炉炉内喷钙干法脱硫技术方案山东飞洋环境工程有限公司2016年2月目录1.概况 (3)2.厂区条件 (3)2.1厂址. (3)2.2环境条件 (3)3.燃煤资料 (3)4.脱硫剂 (4)5.设计依据 (4)6.主要技术参数 (4)7.干法脱硫系统简介 (5)(1)反应原理 (5)(2)工艺流程 (5)(3)主要性能保证 (7)(4)主要技术指标 (7)8.设备清单 (8)1.概况邹城宏矿热电有限公司(以下简称公司)位于邹城经济开发区三兴路东段,已有三台75t/h循环流化床锅炉并配套建设氨法烟气脱硫装置。
为达到环保要求的超低排放标准,拟建设炉内喷钙干法烟气脱硫系统。
2.厂区条件2.1 厂址邹城经济开发区三兴路东段2.2 环境条件年平均气压:101.53kPa年平均汽温:12.3℃极端最高汽温:41.9℃极端最低汽温:-23.3℃平均年降雨量:594.4mm最大年降雨量:1442mm瞬时最大风速(地面上10m):40m/s最大积雪深度:150mm最大冻土深度:600mm常年风向:SSE最大冻土深度-0.5m抗震设防烈度为7度。
根据国标《建筑抗震设计规范》和《火力发电厂土建专业技术设计规定》的规定,脱硫装置按7度进行抗震构造措施设防。
3.燃煤资料锅炉型号:型号:3台1.锅炉蒸发量75t/h2.风量(工况)170000m³/h4.脱硫剂石灰石目数在250以上,活性达到我方工艺设计要求。
纯度在90%以上。
5.设计依据本方案保证对系统功能设计、结构、性能、制造、建筑、供货、安装、调试、试运行等符合相关的中国法律、法规、规范、以及最新版的ISO和IEC标准。
对于标准的采用按下述原则执行:首先应符合中国国家标准、部颁标准及行业规程规定;上述标准中不包含的部分,采用技术来源国标准或国际通用标准。
标准由本方案提供,业主确认;如上述标准均不适用,由业主和本方案讨论并确定;上述标准有矛盾时,按较高标准执行。
锅炉炉内喷钙脱硫施工方案

锅炉炉内喷钙脱硫施工方案1. 引言锅炉炉内喷钙脱硫是一种常见的脱硫方法,通过在锅炉燃烧区域喷射钙基脱硫剂,可以有效去除燃烧产生的硫氧化物,减少对大气环境的污染。
本文将介绍锅炉炉内喷钙脱硫的施工方案,包括工艺流程、施工步骤、注意事项等内容。
2. 工艺流程锅炉炉内喷钙脱硫的工艺流程主要包括下面几个步骤:1.准备工作:确认锅炉停机,确保锅炉内无火焰和高温状态,清理炉内杂物,确保施工安全。
2.脱硫剂配制:按照厂家提供的配方,将钙基脱硫剂与稀释剂按照一定比例混合,制备喷钙脱硫液。
3.喷射施工:使用专用设备将喷钙脱硫液喷射到炉内燃烧区域,覆盖硫氧化物生成区域,促使其与钙基脱硫剂发生反应形成水溶性化合物。
4.喷射结束后,停留一段时间,让脱硫剂充分反应。
5.清理工作:将喷射过程中产生的积灰、残留物清理干净,恢复锅炉正常运行状态。
3. 施工步骤具体的施工步骤如下:1.停机检查:确认锅炉已经停机,并检查锅炉内部是否有残留的高温物质。
2.清理炉内:清理炉内的杂物、积灰等,确保施工环境干净整洁。
3.配制脱硫剂:按照厂家提供的配方,将钙基脱硫剂与稀释剂按照一定比例混合,充分搅拌均匀。
4.喷射施工:使用专用设备将喷钙脱硫液喷射到锅炉燃烧区域,均匀喷射覆盖整个区域。
5.喷射结束后,停留时间:根据工艺要求和脱硫剂反应时间,使脱硫剂充分反应。
6.清理工作:将喷射过程中产生的积灰、残留物清理干净,以免影响锅炉的正常运行。
4. 注意事项在进行锅炉炉内喷钙脱硫施工时,需要注意以下几点:•安全第一:施工前需要检查锅炉的停机情况,确保锅炉内无火焰和高温物质,避免施工过程中发生意外事故。
•施工环境清洁:清理锅炉炉内的杂物和积灰,确保施工环境干净整洁。
•配制脱硫液:按照厂家提供的配方,准确计量脱硫剂和稀释剂,充分搅拌均匀。
•喷射均匀:使用专用设备进行喷射,保证喷钙脱硫液均匀喷射到燃烧区域,覆盖面积广,确保脱硫效果。
•停留时间:根据工艺要求和脱硫剂反应时间,合理控制喷射后的停留时间,使脱硫剂充分反应。
炉内喷钙脱硫技术方案

炉内喷钙脱硫技术方案1. 引言在煤炭、电力、冶金等工业领域中,烟气中的二氧化硫(SO2)是一种常见的大气污染物。
高浓度的二氧化硫排放不仅对环境造成严重影响,也对人体健康构成威胁。
因此,发展高效、低成本的脱硫技术对于减少二氧化硫排放和保护环境具有重要意义。
炉内喷钙脱硫技术利用炉内的高温和燃烧炉的炉排气温度来进行脱硫。
本文将介绍炉内喷钙脱硫技术的原理、工艺流程以及该技术的优点和应用前景。
2. 原理炉内喷钙脱硫技术利用炉内高温下,钙的氧化物与燃烧产生的二氧化硫进行反应,生成硫酸钙,并最终形成石膏。
该反应可以在较低温度下进行,从而减少了能耗和设备成本。
喷钙脱硫的关键是选择适当的喷钙方式和喷钙剂。
常用的喷钙方式包括干式喷钙和湿式喷钙,喷钙剂则可选择氧化钙、氢氧化钙等。
3. 工艺流程炉内喷钙脱硫技术主要由以下几个步骤组成:3.1 炉内喷钙设备安装首先,需要在燃烧炉的炉腔内设置喷钙设备。
喷钙设备通常由喷钙器、输送管道和喷钙气流控制装置组成。
喷钙器的位置要使其能够充分覆盖燃烧产生的烟气,确保喷钙效果。
3.2 炉内喷钙过程在燃烧过程中,喷钙剂通过喷钙器喷入炉腔内,并与烟气中的二氧化硫发生反应。
喷钙剂与二氧化硫反应生成的硫酸钙会在炉腔内冷却下来,并形成石膏。
3.3 石膏收集与处理石膏是炉内喷钙脱硫技术中的副产物,需要进行收集和处理。
一种常见的处理方法是将石膏进行脱水和干燥,然后用作建材工业的原料。
4. 优点炉内喷钙脱硫技术相比其他脱硫技术具有以下优点:•节能高效:利用炉内高温进行脱硫,减少了能耗和设备成本。
•低成本:喷钙剂的成本相对较低,且喷钙剂可以选择多种低成本材料。
•适应性强:炉内喷钙脱硫技术适用于各种类型的燃烧炉,包括煤炭燃烧炉和重油燃烧炉等。
•副产物可利用:石膏是炉内喷钙脱硫的副产物,可用作建材工业的原料,具有较高的价值。
5. 应用前景炉内喷钙脱硫技术在煤炭、电力、冶金等工业领域广泛应用,对减少二氧化硫排放和保护环境具有重要意义。
炉内喷钙脱硫工艺石灰石粉输送系统技术方案剖析

炉内喷钙脱硫工艺石灰石粉输送系统技术方案剖析当前,石灰石脱硫工艺成为了烟气脱硫技术中的主流技术之一,并广泛应用于烟气脱硫的领域中。
炉内喷钙脱硫工艺是一种采用熔融钙作为脱硫剂,将其喷入燃烧器中,通过化学反应吸收燃烧过程中产生的氧化硫和氮氧化物的技术。
与传统湿法脱硫工艺相比,炉内喷钙脱硫工艺具有成本低、节能环保等优点,并且可以一次性完成脱硫,适用于高温、高氧化性的燃烧工艺。
本文将从石灰石粉输送系统技术方案剖析炉内喷钙脱硫工艺。
一、石灰石粉的性质和要求在炉内喷钙脱硫工艺中,石灰石粉扮演着重要的角色。
因此,选择合适的石灰石粉对于脱硫效果和设备使用寿命具有至关重要的意义。
首先,石灰石粉应具有足够的反应能力和活性,才能发挥最佳的脱硫效果。
其次,石灰石粉应尽可能地满足以下要求:1、粒度要求:在炉内喷钙脱硫过程中,石灰石粉的粒径大小对于反应速率和反应效果具有重要的影响。
一般来说,石灰石粉的粒径应控制在5-25μm之间。
2、密度要求:石灰石粉的密度决定了其在输送过程中的运动状态和流量,而流量又决定了脱硫效果和设备选择。
一般来说,密度在2-3g/cm³之间。
3、水分要求:石灰石粉中包含的水分和其他杂质都会影响到其反应效率,因此,在选择石灰石粉时,应选择低水分、高纯度的石灰石粉。
二、石灰石粉输送系统方案设计在炉内喷钙脱硫工艺中,石灰石粉输送系统既要满足石灰石粉输送的要求,又要避免对石灰石粉质量产生不利影响。
1、输送方式选择:石灰石粉输送系统的方式有很多种,包括气力输送、螺旋输送、斗式输送、磁力输送等。
在炉内喷钙脱硫过程中,由于石灰石粉具有一定的脆性,因此,应尽量避免采用高速气力输送或高速机械输送,以保证石灰石粉的完整性。
2、输送管道设计:石灰石粉在输送过程中容易产生积垢、积灰、积水等问题,因此,输送管道的设计应尽可能避免长时间的倾斜或水平的输送,防止石灰石粉的堆积和结块。
3、附属设备的选择:在石灰石粉输送系统中,附属设备包括阀门、布袋过滤器、灰斗、卸料装置等。
炉内喷钙脱硫工艺

炉内喷钙脱硫工艺炉内喷钙脱硫工艺是一种常用的烟气脱硫方法。
它通过在锅炉烟道内喷射钙质吸收剂,将烟气中的二氧化硫转化为硫酸钙并固定下来,从而达到减少二氧化硫排放的目的。
炉内喷钙脱硫工艺主要包括喷钙系统和脱硫反应过程两个部分。
喷钙系统是炉内喷钙脱硫的关键。
它由喷钙设备、输送系统和控制系统组成。
喷钙设备一般采用高压喷嘴,通过压缩空气将钙质吸收剂喷射到烟气通道中。
输送系统一般采用螺旋输送机或气力输送系统,将钙质吸收剂从储存仓库中输送到喷钙设备。
控制系统则负责控制喷钙设备的喷射量和频率,以满足不同工况下的脱硫要求。
脱硫反应过程是炉内喷钙脱硫的核心。
当烟气中的二氧化硫与喷射的钙质吸收剂接触时,会发生化学反应。
二氧化硫与钙质吸收剂中的氧化钙反应生成硫酸钙。
硫酸钙会与烟气中的水蒸气和氧反应生成硫酸和水。
硫酸是一种易溶于水的物质,可以被烟气带走并固定下来。
脱硫反应过程中,钙质吸收剂会逐渐被转化为石膏,因此需要定期补充新的钙质吸收剂。
炉内喷钙脱硫工艺具有以下优点:炉内喷钙脱硫工艺适用范围广。
不论是燃煤锅炉还是燃气锅炉,都可以采用此工艺进行脱硫处理。
无论是新建的锅炉还是改造的锅炉,都可以方便地引入喷钙系统。
炉内喷钙脱硫工艺具有高效的脱硫效果。
钙质吸收剂喷射到烟气中后,能够迅速与二氧化硫发生反应,并将其转化为硫酸钙,从而达到脱硫的效果。
实际应用中,炉内喷钙脱硫工艺可以将二氧化硫的排放浓度降低到国家排放标准以下。
炉内喷钙脱硫工艺具有运行成本低的优点。
钙质吸收剂价格低廉,且易于获取。
喷钙设备的投资和运行成本相对较低。
此外,炉内喷钙脱硫工艺不需要额外的吸收塔和循环泵等设备,节省了工程投资和运行维护成本。
炉内喷钙脱硫工艺对烟气系统影响小。
喷钙系统可以方便地安装在锅炉烟道上,不需要额外的烟气处理设备。
此外,炉内喷钙脱硫工艺对烟气阻力影响小,不会对锅炉的正常运行产生明显的影响。
炉内喷钙脱硫工艺是一种经济、高效的烟气脱硫方法。
它通过喷钙系统将钙质吸收剂喷射到烟气通道中,将二氧化硫转化为硫酸钙并固定下来。
- 1、下载文档前请自行甄别文档内容的完整性,平台不提供额外的编辑、内容补充、找答案等附加服务。
- 2、"仅部分预览"的文档,不可在线预览部分如存在完整性等问题,可反馈申请退款(可完整预览的文档不适用该条件!)。
- 3、如文档侵犯您的权益,请联系客服反馈,我们会尽快为您处理(人工客服工作时间:9:00-18:30)。
炉内喷钙方案比较
1.概述
热电厂规模为3×35t/h循环流化床锅炉,建厂时未考虑脱硫系统,现为响应国家环保政策,达到锅炉烟气排放标准,拟增加脱硫系统,工艺采用炉内喷钙系统。
2.设计依据
2.1 3×35t/h设计煤种的煤质分析资料如下:
煤质分析表
2.2锅炉: 3×35t/h
本工程吸收剂按炉内喷钙粉设计:
(1)、炉内喷钙粉(粒径≤0.6mm,纯度:95%,堆积重度1.4t/m3)进行炉内脱硫,炉内喷钙Ca/S=3,设计脱硫效率≥90%,炉内喷钙粉由需方采购。
(由于业主未提供,炉内喷钙粉化学分析用如下表中数据进行参考设计):
炉内喷钙粉耗用量如下表:
注:日运行24小时。
(2)1×35t/h脱硫效果:
3.炉内喷钙方案描述
3.1方案一:采用无锡市华星电力环保修造厂的技术,属于浓相输送。
其具体工艺为:石灰石粉仓(70m3)→手动插板阀(300×300)→注料泵(LXLD-0.6)→连续输送泵(LDL1.0m3)→旋转供料器(MGR-50)→喷射器(HHQ80-00)→输送管(DN80)→分配器→炉膛
输送气源:压缩空气
3.2方案二:采用我公司的稀相输送技术。
其具体工艺为:石灰石粉仓(70m3)→手动插板阀(300×300)→螺旋给料机→喷射器(HHQ80-00)→输送管(DN80)→分配器→炉膛输送气源:罗茨风机
3.3浓、稀相输送的比较
现在国内电厂炉内喷钙脱硫一般有二种方式,即浓相输送与稀相输送。
浓相输送与稀相输送相比有以下几个缺点:
A、石灰石粉流化状态不好,入炉速度大,对管路与锅炉磨损较大,特别是石灰石粉中有大的颗粒时更为严重。
B、入炉后粉气动量大,对锅炉的燃烧状况有影响。
C、耗能量大,由于所用气源为空压机提供,每10标准立方米增加的电功率为55~66KW。
因此,国外引进的炉内喷钙技术都是采用稀相输送技术。
3.4目前国内炉内喷钙现状
国内已投运的炉内喷钙脱硫系统的实际运行状况并不是连续运行的,大部分设备是长时间不运行,但是当要进行环保测试时又必须要测试合格,现在已安装投运的脱硫设备基本上不能适应这种运行状况,系统长时间不用,启动时,不能及时启动;另一方面,随着国内环保要求标准的不断提高,大部分技术是一次性的,如果提高环保要求,就要重新选用新的脱硫方法。
具体有以下几个方面的问题:
A. 长时间停用后,石灰石粉仓内石灰石粉会受潮板结,时间过长后会成为一个整体,使整个料仓固结,如要再运行清理难度很大,甚至导致料仓上的附件损坏。
B. 石灰石炉内喷钙系统管路中,由于设计、运行控制等方面的原因,在个别部位易形成料粉残留,长时间停用后可形成硬块,多次启停后会造成局部阻力过大,甚至堵塞管路。
C. 很多技术没有脱硫效率的前瞻性,而我公司引进的技术可以根据国家环保标准的要求。
通过逐步投资,不断完善跟踪并达到环保要求。
D. 电动与气动等部件比较复杂,维护难度大,不易于检修,不利于自由启停。
3.5引进脱硫技术:
我公司在芬兰LIFAC(炉内喷钙及未反应氧化钙活化)这种先进的烟气脱硫工艺的基础上,结合我国的国情和实际应用水平,开发出了模块式炉内喷钙全自动脱硫系统。
目前,中济能源环保通过烟气脱硫
工程运行,在多年独立研究开发的基础,已经形成了成熟的适合中小型机组实施喷钙脱硫成套技术。
3.6自主技术
3.6.1 粉仓防板结装置
我公司所提供的防板结措施是在石灰石中转仓内部安装Φ150的粉仓防板结装置,首先,采用PLC时间控制技术,定期搅拌石灰石粉仓内的粉料,防止其整体板结。
其次,采用逆向双螺旋机械技术,可以粉碎已板结的石灰石粉块,第三,可以使石灰石粉比较均匀的分布于仓内,保护粉仓附件。
3.6.2 粉仓气化装置
在日用石灰石仓下部安装Φ100的粉仓气化装置,通过导入的检修压缩空气气流使石灰石粉气化。
压缩空气进口配手动球阀、电磁阀、过滤器、逆止阀各一支,与上部进料装置联锁。
3.6.3 管路防堵技术
在设计石灰石粉炉内喷钙系统时,根据各系统的特殊情况,对管路的布置采用流体输送精确计算,特别是局部阻力大、易存粉的部位,采用较大的裕度系数,可以从硬件上解决问题;第二,在程序控制上,设置停机后自动吹扫功能,自动检测管内风压,进行逻辑计算来测定管内是否被吹净,如干净,则按程序停机,不净则采用脉动风压执行再吹扫程序。
3.6.4 流化床锅炉尾部增湿活化技术
在国内的不同的地区不同的锅炉执行着不同的排放标准,有的地方只采用炉内喷钙就可以达到,而有的地方达不到,我公司在消化国外技术的基础上,开发了在尾部旋风分离器增湿活化提高脱硫效率的第二步技术,可以在炉内喷钙的基础上提高10%的效率。
该技术投资省,效果好。
3.7系统主要特点
3.7.1 模块化设计,可以单个模块运行也可以多个组合运行,通过不同模块组合可以方便的达到不同脱硫效率的要求。
3.7.2运行管理方便,整个系统的启动、运行与停止可以自由切换,操作方便,脱硫效果明显,对锅炉运行工况无影响。
3.7.3具有较高的脱硫效率,合理的钙硫比,较低的运行费用,适应范围宽,锅炉可以用不同含硫量的煤做燃料。
3.7.4 投资省,占地小,维修费用低,系统运行安全可靠。
3.7.5 整个系统从进料到出料,封闭运行,清洁卫生。
4. 两方案经济比较
4.1方案一流程繁琐,操作控制要求严格,运行、维护费用高,投资较大。
设备明细见下表
4.2方案二流程简单,操作控制方便,运行、维护费用低,投资少。
设备明细见下表
5. 结论:
技术方面:方案一属浓相输送技术,较方案二的稀相输送技术有着诸多缺点;经济方面:方案二比方案一投资节省39.24万元。
而且长远来看,方案二运行、维护方便,费用低,所以我们推荐贵电厂采用方案二。
(注:文档可能无法思考全面,请浏览后下载,供参考。
可复制、编制,期待你的好评与关注)。