煤矸石智能分选系统
煤矸石智能分选设备原理

煤矸石智能分选设备原理
煤矸石智能分选设备是一种新型的煤矸石分选设备,它采用先进的智能技术,可以有效地实现煤矸石的分选。
它的原理是:首先,将煤矸石放入设备中,然后,设备会根据煤矸石的形状、大小、重量等特征,运用智能算法,将煤矸石分类,最后,将分类后的煤矸石放入不同的容器中。
煤矸石智能分选设备的优势在于,它可以有效地提高煤矸石的分选效率,减少人工分选的时间和劳动强度,提高分选的准确性,减少分选过程中的污染,从而节省大量的人力物力。
此外,煤矸石智能分选设备还可以根据客户的需求,自动调整分选参数,从而更好地满足客户的需求。
煤矸石智能分选设备的应用非常广泛,它可以用于煤矸石的分选,也可以用于其他物料的分选,如矿石、砂石、煤粉等。
它的应用不仅可以提高分选效率,而且还可以提高分选质量,从而节省大量的人力物力。
煤矸石智能分选设备的出现,为煤矸石分选提供了一种新的选择,它不仅可以提高分选效率,而且还可以提高分选质量,减少分选过程中的污染,从而节省大量的人力物力。
它的出现,为煤矸石分选带来了极大的便利,也为煤矸石行业的发展带来了新的机遇。
TDS智能干选系统的技术分析与应用研究

1 TDS智能干选系统工作原理分析与传统的利用密度分选煤矸的原理不同,TDS 智能干选机是基于朗伯比尔定律,根据性质不同的物质对光的吸收系数不同,利用煤和矸石对X射线的吸收、反射、散射程度的不同,把煤块和矸石作为一个个独立的个体进行智能分选的,分选精度高;通过合理的设置分选值X,可以调整分选密度,能很好的适应不同含矸量的原煤。
TDS智能干选技术是建立在伪双能X射线透射系统的基础上的。
根据射线源能量的大小不同,X射线透射系统可以分为单能和双能两种,前者是从宏观角度识别物体的不同形状进行分辨的,后者可以从微观的角度分辨物体,双能可以准确的排列出物质的原子序数及其他相关信息。
根据射线源的不同,双能系统又可以分为真双能系统和伪双能系统,前者采用的X射线源能够形成两种分别被探测器检测到的大小不同的能量。
而伪双能系统则是采用单一射线源和两组探测器来获得双能量值,与真双能系统不同,这两个能量值的大小基本相同。
如公式I=Ie-μhp,其中:I0为入射前的X射线强度;I为穿透原煤后的X射线强度;μ为质量吸收系数;h为被测物体厚度;ρ为被测物体密度;e为自然常数,值约为2.71828。
根据朗伯比尔定律公式:A=log(1/T)=Kbc,式中:A为吸光度;T为透光度;K为摩尔吸光系数;c为吸光物质的浓度,mol/L;b为吸收层厚度,cm。
摩尔吸光系数K的计算方法为:将TDS智能干选系统内探测器检测到的X射线在未透射物体之前的高能X射线强度I0高与低能X射线强度I0低,以及X射线在透射物体后的高能X射线强度I高与低能X射线强度I低,分别代入朗伯比尔定律公式:将以经测得的I0高、I0低、I高、I低带入上式可以得到TDS智能干选技术的关键是设置合理的X值,通过计算得到不同每种吸收X射线的K值,当K >X时,判定被测物体为矸石;当K<X时,判定被测物体为煤,根据选煤要求的不同,适当调整X值,可以得到不同含矸量的煤。
2 TDS智能干选系统结构TDS智能干选系统主要装置有:给料装置、布料装置、识别装置、X射线线阵探测、智能阵列式空气喷嘴、供风系统、精煤收集溜槽、矸石TDS智能干选系统的技术分析与应用研究□ 张晓东 太原煤气化(集团)有限责任公司生产技术部 山西太原 030032我国传统的煤矸分选采用的是重介质浅槽分选机和动筛跳汰机。
井下矸石智能分选系统方案设计

井下矸石智能分选系统方案设计摘要:随着煤矿绿色开的推广,国内已有多个井工煤矿实现了井下矸石分选及不可利用矸石返井充填开采。
本文结合矿井实际,针对生产矿井原煤开采情况,在矿井原有生产系统基础上,经过分析、比选,设计出煤矸分选方案。
设计提出的智能分选系统具有布置简单、灵活、宜复制的特点,可在同类矿井中推广应用。
系统选出的矸石进入充填运输系统,用于井下各地点充填使用。
本文对充填部分不作论述,仅提出智能分选系统设备、硐室布置等设计内容。
关键词:绿色开采井下智能选矸煤矸分选分选硐室1 矿井现状及井下分选的必要性1.1基本情况该矿生产能力为2.40Mt/a,矿井采用主斜、副立的开拓方式。
全矿井设置主辅两个水平,在10号煤层布置主水平,在5号煤层布置辅助水平,两水平的主运输大巷直接与主斜井相连,且分别布置一个10号煤层、5号煤层回采工作面。
矿井井下主运输方式采用带式输送机运输,井下辅助运输方式采用无极绳连续牵引车运输为主,部分斜巷采用绞车提升矿车及架空乘人装置等运输方式。
井下煤炭运输路径为:工作面落煤通过刮板输送机、转载机、顺槽带式输送机→南翼集中皮带大巷→主斜井→地面,进入地面生产系统及选煤厂。
掘进工作面出煤(矸)经带式输送机汇入主煤流运输系统。
1.2井下分选的必要性该矿10号煤层为厚煤层,开采的原煤中含矸量较少;5号煤层为薄煤层,开采的原煤中含矸量大。
回采时,实际割顶、破底的情况较多,一般割顶板和破底板各约200mm。
经估算仅5煤层回采工作面顶底板割落矸石量约40-56万t/a。
此外,5号煤层中的巷道均为半煤岩巷,其掘进出料含矸石量比例更高,经估算该部分掘进矸石量约10-13万t/a。
这些矸石均汇入原煤运输系统,如果不在井下分选出来则全部升井,不但造成环境污染,而且增加堆存土地占用。
同时,增加无效提升,增加能耗,降低矿井的经济效益。
基于环境保护和绿色开采的理念,将原煤中的矸石在升井之前进行分选,将其作为井下充填材料。
TDS智能分矸系统在煤矿井下的应用研究

TDS智能分矸系统在煤矿井下的应用研究作者:刘太岭郑玉鹏来源:《机电信息》2020年第02期摘要:介绍了单县能源有限责任公司(陈蛮庄煤矿)井下TDS智能分矸系统干选机的工作原理及工艺流程,阐述了该系统的创新性和实用性,分析了应用该系统后产生的经济效益,并对其市场应用前景进行了展望。
关键词:TDS智能分矸系统;煤矿;提升量1 TDS智能分矸系统概述根据山东省冲击地压煤矿“三限三强”的工作要求,陈蛮庄煤矿在井下应用了TDS智能分矸系统,即在矿井主煤流系统(西翼强力皮带)中增加TDS智能分矸机,在井下直接处理或者利用矸石,分选出质量更高的块精煤,保证了矿井的有效提升量,提高了主井提升能力。
TDS智能干选机的基本原理:TDS智能干选机通过X射线和图像识别技术,运用深度学习算法,对煤和矸进行识别,实现对块煤的精准识别和分选。
系统工艺流程:在西翼强力皮带上将原煤截留出来,经过滚轴筛进行25/50 mm筛分,滚轴筛上50 mm以上的毛煤直接作为矸石转载至回矸皮带进入分煤仓,滚轴筛下0~25 mm原煤经过沫煤转载皮带回到西翼强力皮带上,25~50 mm的原煤进入TDS智能干选机分选,执行“打矸”操作,分选出的矸石通过回矸皮带进入分煤仓,分选出的块精煤通过回煤皮带返回西翼强力皮带,最终进入井底煤仓。
井下块煤TDS智能干选系统设备具体流程如图1所示。
2 TDS智能分矸系统创新性和实用性分析(1)TDS智能干选机采用X射线透射智能识别方法,针对不同的煤质特征建立与之相适应的分析模型,通过大数据分析,对煤与矸石进行数字化识别,最终通过智能排矸系统(用阵列式气枪)将矸石排出。
(2)该分选系统工艺与传统浅槽、动筛等块煤水洗工艺相比,TDS智能干选机运行无需水、无需介质、无煤泥水处理和介质系统,系统设备数量少,生产成本低,主运系统或采区可灵活布置,适合井下运行。
(3)TDS智能分矸系统发展成熟,在井上已得到广泛应用,本项目创新点之一就是将井上TDS排矸技术应用于井下。
选煤厂重介质分选智能控制系统研究

选煤厂重介质分选智能控制系统研究一、选煤厂重介质分选智能控制系统研究的背景与意义2、选煤厂智能控制系统的组成与功能3、选煤厂重介质分选智能控制系统的实现方式与技术平台4、选煤厂重介质分选智能控制系统的应用价值和市场前景5、选煤厂重介质分选智能控制系统的发展趋势和技术创新点一、选煤厂重介质分选智能控制系统研究的背景与意义选煤厂作为煤炭行业中的重要环节,其重介质分选技术的应用已经得到广泛的推广和应用。
重介质分选技术通过在水介质中利用煤和矸石的密度差异来进行分选,以达到提高煤的品位和减少资源浪费的目的。
然而,重介质分选存在人工操作难度大、效率低下、煤质控制精度不高等缺点。
为解决这些问题,选煤厂重介质分选智能控制系统应运而生。
该系统通过引入各种先进技术和设备,以实现对重介质分选过程的自动化和智能化,从而提高生产效率和品位精度。
因此,研究选煤厂重介质分选智能控制系统具有重要的现实意义和科技价值。
二、选煤厂智能控制系统的组成与功能选煤厂重介质分选智能控制系统通常包括硬件和软件两大部分。
硬件方面,选煤厂智能控制系统通常由以下设备组成:PLC控制器、人机界面、数据采集设备、传感器、执行器等。
其中,PLC控制器是控制系统的核心,通过控制各个执行器来调控水介质、振动台、磁选机等设备的运行状态;人机界面则是用户与系统交互的窗口,可以通过显示屏幕对设备的运行状态、参数设置和历史数据等进行查看、修改和处理;数据采集设备则主要用于采集各个环节的数据、信号等信息,以进行分析和处理;传感器一般用于检测水介质、磁场强度、振动幅度等指标,以反馈给PLC控制器进行调整和控制;执行器则是系统中必不可少的控制输出设备,用于调节水介质量、振动幅度、磁场强度等参数,以保证分选效果和精度。
软件方面,选煤厂智能控制系统通常包括监控软件、控制软件和算法优化软件。
监控软件主要用于实时监测分选过程中各个环节的运行状态和数据信息,以及进行一些视觉显示;控制软件则是控制系统的核心,主要实现各种控制逻辑和功能实现,包括启停、速度控制、质量控制等多种功能;算法优化软件主要负责对分选过程进行优化处理,将各种传感器采集到的数据和信息结合起来做出更加准确和精细的控制决策。
煤矸石智能分选系统
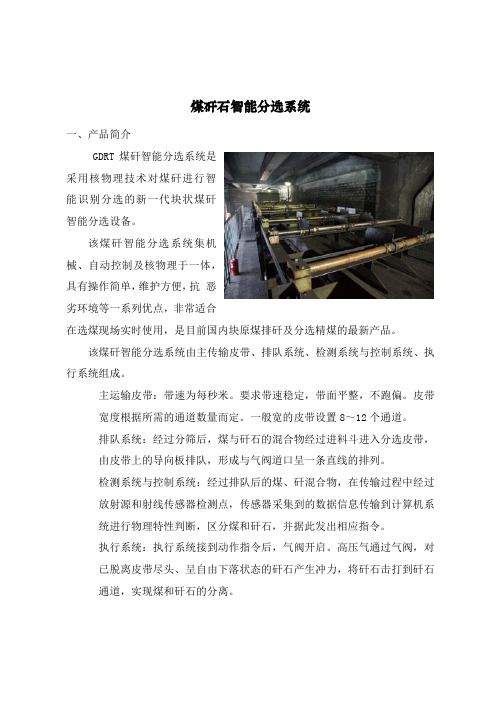
煤矸石智能分选系统一、产品简介GDRT煤矸智能分选系统是采用核物理技术对煤矸进行智能识别分选的新一代块状煤矸智能分选设备。
该煤矸智能分选系统集机械、自动控制及核物理于一体,具有操作简单,维护方便,抗恶劣环境等一系列优点,非常适合在选煤现场实时使用,是目前国内块原煤排矸及分选精煤的最新产品。
该煤矸智能分选系统由主传输皮带、排队系统、检测系统与控制系统、执行系统组成。
主运输皮带:带速为每秒米。
要求带速稳定,带面平整,不跑偏。
皮带宽度根据所需的通道数量而定。
一般宽的皮带设置8~12个通道。
排队系统:经过分筛后,煤与矸石的混合物经过进料斗进入分选皮带,由皮带上的导向板排队,形成与气阀道口呈一条直线的排列。
检测系统与控制系统:经过排队后的煤、矸混合物,在传输过程中经过放射源和射线传感器检测点,传感器采集到的数据信息传输到计算机系统进行物理特性判断,区分煤和矸石,并据此发出相应指令。
执行系统:执行系统接到动作指令后,气阀开启。
高压气通过气阀,对已脱离皮带尽头、呈自由下落状态的矸石产生冲力,将矸石击打到矸石通道,实现煤和矸石的分离。
排队系统检测系统控制系统执行系统该煤矸智能分选系统每通道的处理能力约为每小时15吨左右(根据不同的煤质、含矸量、粒度而不同),可依据具体需求在系统中设计配置相应的通道数量。
二、设备特点三、产品系列本公司根据客户要求分选物料粒级研发有如下四个产品系列:产品型号适用分选物料粒度单通道处理量(吨/小时)实际处理量跟该粒级大小物料的各自比重相关GDRT40-9040mm-190mm4 GDRT90-20090mm-200mm20 GDRT200-300200mm-300mm50四、经济及社会效益分析(一)经济效益1、经过分选,提高煤炭质量某矿选煤车间测试记录测试时间煤种测试数量矸石总量(kg)含矸量(%)发热量(Kcal/kg)早班5#混煤20吨945500445441350572、减少人工,节约费用每套系统每班仅需要系统操作人员一名,辅助人员2名。
煤矸石智能分选系统

煤矸石智能分选系统一、产品简介GDRT煤矸智能分选系统是采用核物理技术对煤矸进行智能识别分选的新一代块状煤矸智能分选设备。
该煤矸智能分选系统集机械、自动控制及核物理于一体,具有操作简单,维护方便,抗恶劣环境等一系列优点,非常适合在选煤现场实时使用,是目前国内块原煤排矸及分选精煤的最新产品。
该煤矸智能分选系统由主传输皮带、排队系统、检测系统与控制系统、执行系统组成。
●主运输皮带:带速为每秒0.8--1米。
要求带速稳定,带面平整,不跑偏。
皮带宽度根据所需的通道数量而定。
一般1.4M宽的皮带设置8~12个通道。
●排队系统:经过分筛后,煤与矸石的混合物经过进料斗进入分选皮带,由皮带上的导向板排队,形成与气阀道口呈一条直线的排列。
●检测系统与控制系统:经过排队后的煤、矸混合物,在传输过程中经过放射源和射线传感器检测点,传感器采集到的数据信息传输到计算机系统进行物理特性判断,区分煤和矸石,并据此发出相应指令。
●执行系统:执行系统接到动作指令后,气阀开启。
高压气通过气阀,对已脱离皮带尽头、呈自由下落状态的矸石产生冲力,将矸石击打到矸石通道,实现煤和矸石的分离。
排队系统检测系统控制系统执行系统该煤矸智能分选系统每通道的处理能力约为每小时15吨左右(根据不同的煤质、含矸量、粒度而不同),可依据具体需求在系统中设计配置相应的通道数量。
二、设备特点三、产品系列本公司根据客户要求分选物料粒级研发有如下四个产品系列:产品型号适用分选物料粒度单通道处理量(吨/小时)实际处理量跟该粒级大小物料的各自比重相关GDRT40-90 40mm -190mm 4 GDRT90-200 90mm -200mm 20 GDRT200-300200mm -300mm50四、经济及社会效益分析(一)经济效益1、经过分选,提高煤炭质量 某矿选煤车间测试记录测试时间 煤种测试数量矸石总量(kg)含矸量(%)发热量(Kcal/kg )6.18早班 5#混煤 20吨 9455004454.72.52.244135057 2、减少人工,节约费用每套系统每班仅需要系统操作人员一名,辅助人员2名。
煤矸石智能分选系统
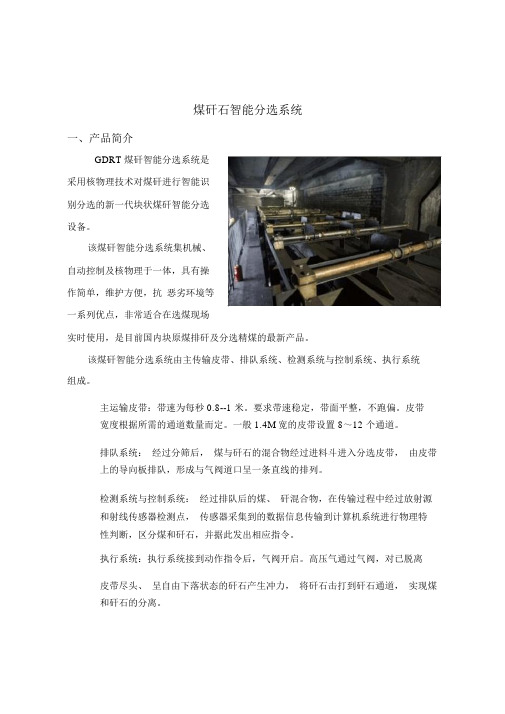
煤矸石智能分选系统一、产品简介GDRT 煤矸智能分选系统是采用核物理技术对煤矸进行智能识别分选的新一代块状煤矸智能分选设备。
该煤矸智能分选系统集机械、自动控制及核物理于一体,具有操作简单,维护方便,抗恶劣环境等一系列优点,非常适合在选煤现场实时使用,是目前国内块原煤排矸及分选精煤的最新产品。
该煤矸智能分选系统由主传输皮带、排队系统、检测系统与控制系统、执行系统组成。
主运输皮带:带速为每秒 0.8--1 米。
要求带速稳定,带面平整,不跑偏。
皮带宽度根据所需的通道数量而定。
一般 1.4M 宽的皮带设置 8~12 个通道。
排队系统:经过分筛后,煤与矸石的混合物经过进料斗进入分选皮带,由皮带上的导向板排队,形成与气阀道口呈一条直线的排列。
检测系统与控制系统:经过排队后的煤、矸混合物,在传输过程中经过放射源和射线传感器检测点,传感器采集到的数据信息传输到计算机系统进行物理特性判断,区分煤和矸石,并据此发出相应指令。
执行系统:执行系统接到动作指令后,气阀开启。
高压气通过气阀,对已脱离皮带尽头、呈自由下落状态的矸石产生冲力,将矸石击打到矸石通道,实现煤和矸石的分离。
排队系统检测系统控制系统执行系统该煤矸智能分选系统每通道的处理能力约为每小时15 吨左右(根据不同的煤质、含矸量、粒度而不同),可依据具体需求在系统中设计配置相应的通道数量。
二、设备特点三、产品系列本公司根据客户要求分选物料粒级研发有如下四个产品系列:单通道处理量产品型号适用分选物料粒度(吨 /小时)实际处理量跟该粒级GDRT30-8030mm-80mm3大小物料的各自比重GDRT40-9040mm-190mm4相关GDRT90-20090mm-200mm20GDRT200-300200mm-300mm50四、经济及社会效益分析(一)经济效益1、经过分选,提高煤炭质量某矿选煤车间测试记录矸石总量 (kg)含矸量( % )发热量( Kcal/kg )测试测试煤种>15050-150M>15050-150M时间数量总量全部拣矸前拣矸后MM M MM M6.185#50520 吨945500445 4.7 2.5 2.24413早班混煤76.182#50210 吨7904353557.9 4.4 3.54560中班混煤42、减少人工,节约费用每套系统每班仅需要系统操作人员一名,辅助人员 2 名。
- 1、下载文档前请自行甄别文档内容的完整性,平台不提供额外的编辑、内容补充、找答案等附加服务。
- 2、"仅部分预览"的文档,不可在线预览部分如存在完整性等问题,可反馈申请退款(可完整预览的文档不适用该条件!)。
- 3、如文档侵犯您的权益,请联系客服反馈,我们会尽快为您处理(人工客服工作时间:9:00-18:30)。
煤矸石智能分选系统
一、产品简介
GDRT煤矸智能分选系统是采
用核物理技术对煤矸进行智能识别
分选的新一代块状煤矸智能分选设
备。
该煤矸智能分选系统集机械、
自动控制及核物理于一体,具有操
作简单,维护方便,抗恶劣环境等
一系列优点,非常适合在选煤现场
实时使用,是目前国内块原煤排矸及分选精煤的最新产品。
该煤矸智能分选系统由主传输皮带、排队系统、检测系统与控制系统、执行系统组成。
主运输皮带:带速为每秒米。
要求带速稳定,带面平整,不跑偏。
皮带宽度根据所需的通道数量而定。
一般宽的皮带设置8~12个通道。
排队系统:经过分筛后,煤与矸石的混合物经过进料斗进入分选皮带,由皮带上的导向板排队,形成与气阀道口呈一条直线的排列。
检测系统与控制系统:经过排队后的煤、矸混合物,在传输过程中经过放射源和射线传感器检测点,传感器采集到的数据信息传输到计算机系统进
行物理特性判断,区分煤和矸石,并据此发出相应指令。
执行系统:执行系统接到动作指令后,气阀开启。
高压气通过气阀,对已脱离皮带尽头、呈自由下落状态的矸石产生冲力,将矸石击打到矸石通道,实现煤和矸石的分离。
排队系统检测系统
控制系统执行系统
该煤矸智能分选系统每通道的处理能力约为每小时15吨左右(根据不同的煤质、含矸量、粒度而不同),可依据具体需求在系统中设计配置相应的通道数量。
二、设备特点
三、产品系列
本公司根据客户要求分选物料粒级研发有如下四个产品系列:
产品型号
适用分选物料粒
度单通道处理量
(吨/小时)
实际处理量跟该
粒级大小物料的各自
比重相关
GDRT40-9040mm-190mm4 GDRT90-20090mm-200mm20 GDRT200-300200mm-300mm50四、经济及社会效益分析
(一)经济效益
1、经过分选,提高煤炭质量
某矿选煤车间测试记录
测
试时间
煤
种
测
试数
量
矸石总量(kg)含矸量(%)
发热量
(Kcal/kg)
早班
5
#
混
煤
2
0吨
9
45
50
445
441
3
50
5
7
2、减少人工,节约费用
每套系统每班仅需要系统操作人员一名,辅助人员2名。
对于年产150万吨的矿,12人四班三运转,加上其他替补人员,约48名左右的拣矸工人。
如果把工资、补贴、福利、餐费、工装以及劳保等等加在一起,平均按照25000元年/人计算,可节约费用1,200,000元。
3、减少误拣,杜绝故意误拣
人工拣矸往往有误把煤炭当矸石,拣率一般约为矸量的8%
以150万吨煤矿为例,假设含矸率20%,其中20-300mm的块煤率30%,那么因为误拣造成的损失为:
150*30%*20%*8%=万吨
假设单价800元/吨,则减少损失800*=576万元。
这还不包括因种种原因,故意误拣煤带来的损失
(二)社会效果
1、可自主确定夹矸去向
可根据需要调整煤矸识别的参数值,对于其中的“夹矸”可根据需要及煤质要求来确定“夹矸”的去向。
既可以选择将其当作矸石拣出去,也可以将其当作煤留下。
2、不用水,节约电,节能减排
该系统运用计算机、通信、自动控制以及机械等技术于一体,无需借助其他介质,这给目前水资源匮乏的中国来说,无疑带来极大的福音。
该系统除了皮带机及空压机本身需要动力电以外,其他的计算机控制系统、检测识别系统等等都是弱电,相比较其他现有洗选设备将大大减少企业的用电负荷。
3、减少矸石无效运输,节约社会资源
选矸后不但能降低原煤的灰分、含硫量,提高发热量而且还能为整个社会节约宝贵的运输资源。
以90万吨煤矿为例,按含矸20%的原煤在产地排除其中80%矸石计算,就可以为社会节约煤炭运输总量16%的运力资源。
按年均输送1000万吨、运距
平均600公里计算,其节约的运力可达60亿*=亿吨/公里。
五、该设备主要用途
在线式GDRT煤矸智能分选系统的主要用途是:
适用于原煤准备车间的排矸
适用于煤炭集运站预先排矸
适用于洗煤厂的物料前期预处理,提高生产效率、降低设备损耗、减少用水量
适用于干旱地区和严寒地区的煤矸分选
适用于老矿煤楼改造排矸
六、服务
提供现场改造的技术设计方案;
设备到货后,工程技术人员到现场指导安装、调试;
免费对操作人员进行技术培训;
定期回访用户,解决使用过程中的实际问题;
半年内实行三包,终年维修。