机械制造质量分析与控制.pptx
合集下载
机械制造质量分析与控制概述课件
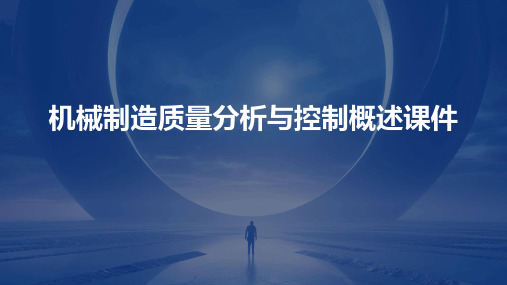
基于数据挖掘的质量管理;
当前研究与发展趋势
人工智能在机械制造 质量分析与控制中的 应用等。
从传统的单一过程控 制向集成化、智能化 、自动化方向发展;
发展趋势主要表现为
当前研究与发展趋势
数据分析方法的应用将更加广泛,如机器学习、深度学习等;
结合互联网技术,实现远程监控和实时预警。
未来在制造业的应用前景
制造过程的稳定性与可靠性控制
总结词
保证产品质量和生产效率
详细描述
通过采用先进的生产设备和技术,加强制造过程的稳定 性和可靠性控制,可以保证产品质量和生产效率。
总结词
预防故障,减少停机时间
详细描述
加强制造过程的可靠性控制,可以预防设备故障和生产 事故的发生,减少停机时间和生产损失。
总结词
提高生产效率和产品质量一致性
02
制造过程质量分析
制造过程质量的主要因素
工艺流程
工艺流程的合理性、稳定性和可维护性对制 造质量有重要影响。
制造方法
先进的制造方法可以提高制造效率和质量。
制造设备
设备的精度、运行稳定性和维护状况直接关 系到制造质量。
人员素质
操作人员的技能水平、工作态度和责任心对 制造质量有很大影响。
制造过程的质量数据采集
06
总结与展望
机械制造质量分析与控制的重要性
产品质量直接影响到企业的生存和发展,而机械制造质量分析与控制是保障产品 质量的关键环节。
通过有效的机械制造质量分析与控制,可以减少产品缺陷率,提高产品可靠性和 稳定性,增强企业的市场竞争力。
当前研究与发展趋势
当前,机械制造质量分析与控制领域的研究正在不断深入,涉及的方面包括 制造过程的在线监测与控制技术;
当前研究与发展趋势
人工智能在机械制造 质量分析与控制中的 应用等。
从传统的单一过程控 制向集成化、智能化 、自动化方向发展;
发展趋势主要表现为
当前研究与发展趋势
数据分析方法的应用将更加广泛,如机器学习、深度学习等;
结合互联网技术,实现远程监控和实时预警。
未来在制造业的应用前景
制造过程的稳定性与可靠性控制
总结词
保证产品质量和生产效率
详细描述
通过采用先进的生产设备和技术,加强制造过程的稳定 性和可靠性控制,可以保证产品质量和生产效率。
总结词
预防故障,减少停机时间
详细描述
加强制造过程的可靠性控制,可以预防设备故障和生产 事故的发生,减少停机时间和生产损失。
总结词
提高生产效率和产品质量一致性
02
制造过程质量分析
制造过程质量的主要因素
工艺流程
工艺流程的合理性、稳定性和可维护性对制 造质量有重要影响。
制造方法
先进的制造方法可以提高制造效率和质量。
制造设备
设备的精度、运行稳定性和维护状况直接关 系到制造质量。
人员素质
操作人员的技能水平、工作态度和责任心对 制造质量有很大影响。
制造过程的质量数据采集
06
总结与展望
机械制造质量分析与控制的重要性
产品质量直接影响到企业的生存和发展,而机械制造质量分析与控制是保障产品 质量的关键环节。
通过有效的机械制造质量分析与控制,可以减少产品缺陷率,提高产品可靠性和 稳定性,增强企业的市场竞争力。
当前研究与发展趋势
当前,机械制造质量分析与控制领域的研究正在不断深入,涉及的方面包括 制造过程的在线监测与控制技术;
机械制造质量分析与控制.ppt
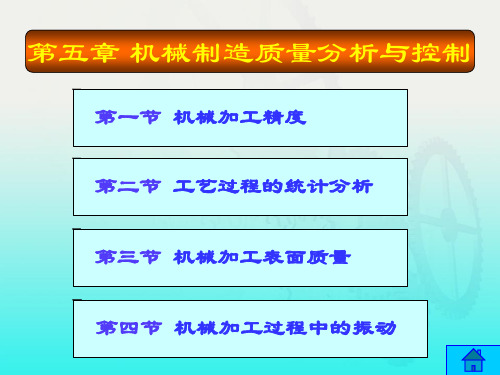
(2)成形刀具 (如成形车刀、成形铣刀、模数 铣刀等)的形状误差
(3)展成刀具 (如齿轮滚动、插齿刀、花键滚 刀等)切削刃的形状及有关尺寸,以及其安装、调 整不正确
(4)一般刀具 (如普通车刀、单刃镗刀、面铣 刀、刨刀等)的制造误差
3.夹具
夹具的作用是使工件相 对于刀具和机床具有正确的 位置,因此夹具的制造误差 对工件的加工精度 (特别是 位置精度) 有很大影响。
5. (1)由于工艺系统刚度变化引起的误差
图5-18 车削外圆时工艺 系统受力变形对加工精度 的影响
5. (2)由于切削力变化引起的误差
在加工过程中,由于工件的加工余量发生变 化、工件材质不均等因素引起的切削力变化,使 工艺系统变形发生变化,从而产生加工误差。
图5-19 毛坯形状误差的复映
5. (3)由于夹紧变形引起的误差
实际加工不可能把零件做得与理想零件完全 一致,总会有大小不同的偏差,零件加工后的实 际几何参数对理想几何参数的偏离程度,称为加 工误差。
2.加工经济精度
图5-2 加工成本与加工误差之间的关系
3.原始误差
由机床、夹具、刀具和工件组成的机械加工工艺 系统 (简称工艺系统) 会有各种各样的误差产生,这 些误差在各种不同的具体工作条件下都会以各种不同 的方式 (或扩大、或缩小) 反映为工件的加工误差。 工艺系统的误差是“因”,是根源;工件的加工误差 是 “果”,是表现;因此,我们把工艺系统的误差 称为原始误差。
1.机床的几何误差
加工中刀具相对于工件的成形运动一般 都是通过机床完成的,因此,工件的加工精 度在很大程度上取决于机床的精度。机床制 造误差对工件加工精度影响较大的有:主轴 回转误差、导轨误差和传动链误差。机床的 磨损将使机床工作精度下降。
(3)展成刀具 (如齿轮滚动、插齿刀、花键滚 刀等)切削刃的形状及有关尺寸,以及其安装、调 整不正确
(4)一般刀具 (如普通车刀、单刃镗刀、面铣 刀、刨刀等)的制造误差
3.夹具
夹具的作用是使工件相 对于刀具和机床具有正确的 位置,因此夹具的制造误差 对工件的加工精度 (特别是 位置精度) 有很大影响。
5. (1)由于工艺系统刚度变化引起的误差
图5-18 车削外圆时工艺 系统受力变形对加工精度 的影响
5. (2)由于切削力变化引起的误差
在加工过程中,由于工件的加工余量发生变 化、工件材质不均等因素引起的切削力变化,使 工艺系统变形发生变化,从而产生加工误差。
图5-19 毛坯形状误差的复映
5. (3)由于夹紧变形引起的误差
实际加工不可能把零件做得与理想零件完全 一致,总会有大小不同的偏差,零件加工后的实 际几何参数对理想几何参数的偏离程度,称为加 工误差。
2.加工经济精度
图5-2 加工成本与加工误差之间的关系
3.原始误差
由机床、夹具、刀具和工件组成的机械加工工艺 系统 (简称工艺系统) 会有各种各样的误差产生,这 些误差在各种不同的具体工作条件下都会以各种不同 的方式 (或扩大、或缩小) 反映为工件的加工误差。 工艺系统的误差是“因”,是根源;工件的加工误差 是 “果”,是表现;因此,我们把工艺系统的误差 称为原始误差。
1.机床的几何误差
加工中刀具相对于工件的成形运动一般 都是通过机床完成的,因此,工件的加工精 度在很大程度上取决于机床的精度。机床制 造误差对工件加工精度影响较大的有:主轴 回转误差、导轨误差和传动链误差。机床的 磨损将使机床工作精度下降。
同济 机械制造 制造技术基础 PPT 第五章 机械制造质量分析与控制2007A
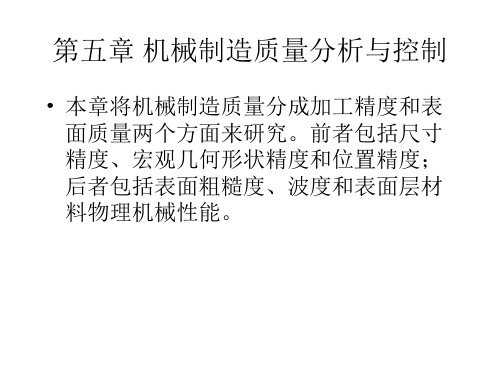
0
K (l l 0 ) 1000
0
K l 1000
(三) 夹具误差 • 精加工用夹具一般取工件上相应尺寸公 差的1/2~1/3;粗加工用夹具一般取工件 上相应尺寸公差的1/5~1/10。
四、工艺系统受力变形引起的误差 (一)基本概念 • 由机床、夹具、刀具、工件组成的工艺 系统,在切削力、传动力、惯性力、夹 紧力以及重力等的作用下,会产生相应 的变形(弹性变形及塑性变形)。这种 变形将破坏工艺系统间已调整好的正确 位置关系,从而产生加工误差。
5、研究机械加工精度的方法 • 研究机械加工精度的方法主要有分析计 算法和统计分析法。 • 分析计算法主要是对单项原始误差进行 分析计算的基础上进行的。 • 统计分析法则是对有关的原始误差进行 综合分析的基础上进行的。
二、 工艺系统的几何误差 1、机床的几何误差 机床制造误差对工件加工精度影响较大的 有:主轴的回转运动误差、导轨误差和传 动链误差。
车削细长轴时,工件在切削力作用下的弯曲变形, 加工后会形成腰鼓形的圆柱度误差。
在内圆磨床上用横向切入磨孔时,由于磨头主轴 弯曲变形,使磨出的孔会带有锥度的圆柱度误差。
垂直作用于工件加工表面(加工误差敏感方向) 的径向切削分力Fy与工艺系统在该方向上的变 形y之间的比值,称为工艺系统刚度k系
k系 Fy y
(四)减少或消除内应力的措施 1、合理设计零件结构 • 在零件结构设计中,应尽量缩小零件各部分厚 度尺寸的差异,以减少铸、锻毛坯在制造中产 生的内应力。 2、采取时效处理 (1)自然时效。在毛坯制造之后,或粗、精加 工之间,让工件停留一段时间,利用温度的自 然变化,经过多次热胀冷缩,使工件的内应力 逐渐消除。这种方法效果好,但需要时间长 (一般要半年至五年)。 (2)人工时效。在进行机械加工之前,应进行 退火、回火等热处理,这种方法对大型零件需 要一套很大的设备,其投资和能源消耗较大。
机械制造质量分析及控制共54页文档

机械制造质量分析及控制
51、没有哪个社会可以制订一部永远 适用的 宪法, 甚至一 条永远 适用的 法律。 ——杰 斐逊 52、法律源于人的自卫本能。——英 格索尔
53、人们通常会发现,法律就是这样 一种的 网,触 犯法律 的人, 小的可 以穿网 而过, 大的可 以破网 而出, 只有中 等的才 会坠入 网中。 ——申 斯通 54、法律就是法律它是一座雄伟的大 夏,庇 护着我 们大家 ;它的 每一块 砖石都 垒在另 一块砖 石上。 ——高 尔斯华 绥 55、今天的法律未必明天仍是法律。 ——罗·伯顿
ห้องสมุดไป่ตู้
31、只有永远躺在泥坑里的人,才不会再掉进坑里。——黑格尔 32、希望的灯一旦熄灭,生活刹那间变成了一片黑暗。——普列姆昌德 33、希望是人生的乳母。——科策布 34、形成天才的决定因素应该是勤奋。——郭沫若 35、学到很多东西的诀窍,就是一下子不要学很多。——洛克
51、没有哪个社会可以制订一部永远 适用的 宪法, 甚至一 条永远 适用的 法律。 ——杰 斐逊 52、法律源于人的自卫本能。——英 格索尔
53、人们通常会发现,法律就是这样 一种的 网,触 犯法律 的人, 小的可 以穿网 而过, 大的可 以破网 而出, 只有中 等的才 会坠入 网中。 ——申 斯通 54、法律就是法律它是一座雄伟的大 夏,庇 护着我 们大家 ;它的 每一块 砖石都 垒在另 一块砖 石上。 ——高 尔斯华 绥 55、今天的法律未必明天仍是法律。 ——罗·伯顿
ห้องสมุดไป่ตู้
31、只有永远躺在泥坑里的人,才不会再掉进坑里。——黑格尔 32、希望的灯一旦熄灭,生活刹那间变成了一片黑暗。——普列姆昌德 33、希望是人生的乳母。——科策布 34、形成天才的决定因素应该是勤奋。——郭沫若 35、学到很多东西的诀窍,就是一下子不要学很多。——洛克
机械制造质量分析与控制概述(PPT 71页)

图4-3 采用滑动轴承时主轴的径向圆跳动 a)工件回转型b)刀具回转型
譬如,在采用滑动轴承结构为主轴的车床上车削外圆时,切 削力F的作用方向可认为大体上时不变的,见上图,在切削力F的 作用下,主轴颈以不同的部位和轴承内径的某一固定部位相接触, 此时主轴颈的圆度误差对主轴径向回转精度影响较大,而轴承内 径的圆度误差对主轴径向回转精度的影响则不大;在镗床上镗孔 时,由于切削力F的作用方向随着主轴的回转而回转,在切削力F 的作用下,主轴总是以其轴颈某一固定部位与轴承内表面的不同 部位接触,因此,轴承内表面的圆度误差对主轴径向回转精度影 响较大,而主轴颈圆度误差的影响则不大。图中的δd表示径向 跳动量。
统计分析法:运用数理统计方法对生产中一批工件的实测结果 进行数据处理,用以控制工艺过程的正常进行。主要是研究各 项误差综合的变化规律,只适合于大批、大量的生产条件。
二、工艺系统几何误差
(一)机床的几何误差
加工中刀具相对于工件的成形运动一般都是通过机床完成的, 因此,工件的加工精度在很大程度上取决于机床的精度。机床 制造误差对工件加工精度影响较大的有:主轴回转误差、导轨 误差和传动链误差。机床的磨损将使机床工作精度下降。
图4-11 由定位副制造不准确引起的误差
如图4-11所示工件的孔装夹在水平放置的心轴上铣削平 面,要求保证尺寸h,由于定位基准与设计基准重合,故无 基准不重合误差;但由于工件的定位基面(内孔D)和夹具 定位元件(心轴d1)皆有制造误差,如果心轴制造得刚好为 d1min,而工件得内孔刚好为Dmax(如图示),当工件在水 平放置得心轴上定位时,工件内孔与心轴在P点接触,工件 实际内孔中心的最大下移量△ab=(Dmax-d1min)/2, △ab就是定位副制造不准确而引起的误差。
料的冷作硬化、金相组织的变化、残余应力等。
譬如,在采用滑动轴承结构为主轴的车床上车削外圆时,切 削力F的作用方向可认为大体上时不变的,见上图,在切削力F的 作用下,主轴颈以不同的部位和轴承内径的某一固定部位相接触, 此时主轴颈的圆度误差对主轴径向回转精度影响较大,而轴承内 径的圆度误差对主轴径向回转精度的影响则不大;在镗床上镗孔 时,由于切削力F的作用方向随着主轴的回转而回转,在切削力F 的作用下,主轴总是以其轴颈某一固定部位与轴承内表面的不同 部位接触,因此,轴承内表面的圆度误差对主轴径向回转精度影 响较大,而主轴颈圆度误差的影响则不大。图中的δd表示径向 跳动量。
统计分析法:运用数理统计方法对生产中一批工件的实测结果 进行数据处理,用以控制工艺过程的正常进行。主要是研究各 项误差综合的变化规律,只适合于大批、大量的生产条件。
二、工艺系统几何误差
(一)机床的几何误差
加工中刀具相对于工件的成形运动一般都是通过机床完成的, 因此,工件的加工精度在很大程度上取决于机床的精度。机床 制造误差对工件加工精度影响较大的有:主轴回转误差、导轨 误差和传动链误差。机床的磨损将使机床工作精度下降。
图4-11 由定位副制造不准确引起的误差
如图4-11所示工件的孔装夹在水平放置的心轴上铣削平 面,要求保证尺寸h,由于定位基准与设计基准重合,故无 基准不重合误差;但由于工件的定位基面(内孔D)和夹具 定位元件(心轴d1)皆有制造误差,如果心轴制造得刚好为 d1min,而工件得内孔刚好为Dmax(如图示),当工件在水 平放置得心轴上定位时,工件内孔与心轴在P点接触,工件 实际内孔中心的最大下移量△ab=(Dmax-d1min)/2, △ab就是定位副制造不准确而引起的误差。
料的冷作硬化、金相组织的变化、残余应力等。
机械制造质量及控制培训课件(ppt 108页)
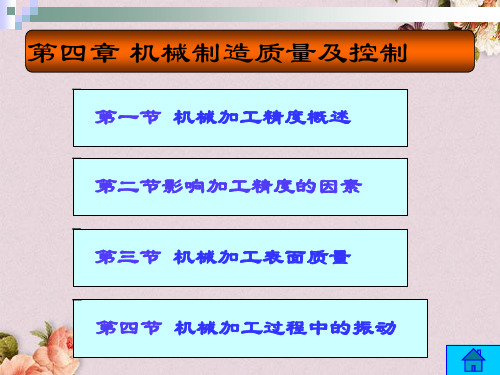
第二节 影响加工精度的因素
原始误差——由机床、夹具、刀具和工件组成的 机械加工工艺系统 (简称工艺系统) 会有各种 各样的误差产生,这些误差在各种不同的具体 工作条件下都会以各种不同的方式 (或扩大、 或缩小) 反映为工件的加工误差。
工艺系统的误差是“因”,是根源;工件 的加工误差是 “果”,是表现;因此,我们把 工艺系统的误差称为原始误差。
• 机床部件刚度的测定
1)变形与载荷 不成线性关系;
2)加载曲线和卸载 曲线不重合,卸 载曲线滞后于加 载曲线;
3)有残余变形, 反复加载卸载后 残余变形→0;
4)部件实测刚度远比按实体结构估算值小。
图中第一次加载时刀架的平均刚度值约为4.6×103 N/mm,相当于 一个 30mm×30mm×200mm 的铸铁悬臂梁的刚度,比刀架实体结构 尺寸要小的多。
4)自动控制法
一、加工精度与加工误差
获得加工精度的方法
(2)获得形状精度的方法
1)轨迹法
利用刀尖运动轨迹形成工件表面形状
2)成形刀具法 由刀刃的形状形成工件表面形状
3)展成法
由切削刃包络面形成工件表面形状
(3)获得相互位置精度的方法
1)直接找正 2)划线找正 3)夹具定位 主要由机床精度、夹具精度和工件的装夹精度来保证
(三) 工艺系统刚度对加工精度的影响
1.工件刚度低
工艺系统中如果工件刚度相对于机床、刀 具、夹具来说比较低,在切削力的作用下,工 件由于刚性不足而引起的变形对加工精度的影 响就比较大,其最大变形量可按材料力学有关 公式估算。如车削细长轴时,因工件刚度较低, 使工件产生腰鼓形的形状误差。
2.刀具刚度低
① 主轴回转误差概念 主轴回转时实际回
机械制造质量分析与控

• 波距(L2)与波高(H2)之比在50~1000范围内的 几何形状误差,称为波度。
• 波距(L1)与波高(H1)之比大于1000的几何形状 误差,称为宏观几何形状误差。
• 第五章 机械制造质量分析与控制
• 第一节 机械加工精度 • 第二节 工艺过程的统计分析 • 第三节 机械加工表面质量
第一节 机械加工精度
• (一)工艺系统的热源
内部热源切削热在工件, 刀具, 切屑, 切削液等中刀 工具 件变形
热源
摩擦热由相对运动的摩擦件产生的— 机床变形
外部热源热 环辐 境射 温度阳光气,温照和明地灯基,暧温气度设变备化,人,局体部等温 差,热风等
• (二)工件热变形对加工精度的影响 • 1. 工件均匀受热 • 车、镗、磨工件回转表面 • ΔL=αLΔθ
• (三)原始误差
• 工艺系统的误差称为原始误差
• (四)原始误差与加工误差的关系: • 工艺系统的原始误差可能原样、缩小、放大
地反映给工件。
过刀刃的加工表面法线方向的原始误差对加 工误差影响最大——误差敏感方向。 过刀刃的加工表面切线方向的原始误差对加 工误差影响最小——误差不敏感方向。一般 可以忽略不计。
• 一般用传动链末端元件的转角误差来衡 量。
• (二)刀具的几何误差
• 包括刀具的制造、安装误差及磨损。
• 采用定尺寸刀具加工时,刀具的尺寸误 差将直接影响工件尺寸精度。
• 采用成形刀具加工时,刀具的形状误差 将直接影响工件的形状精度。
• 采用展成刀具加工时,刀具切削刃的几 何形状及有关尺寸误差也会影响工件的 加工精度。
• 3. 双峰分布
• 提高机床主轴的回转精度的措施: • 适当提高主轴及箱体的制造精度;
• 选用高精度的轴承,对滚动轴承进行预 紧;
• 波距(L1)与波高(H1)之比大于1000的几何形状 误差,称为宏观几何形状误差。
• 第五章 机械制造质量分析与控制
• 第一节 机械加工精度 • 第二节 工艺过程的统计分析 • 第三节 机械加工表面质量
第一节 机械加工精度
• (一)工艺系统的热源
内部热源切削热在工件, 刀具, 切屑, 切削液等中刀 工具 件变形
热源
摩擦热由相对运动的摩擦件产生的— 机床变形
外部热源热 环辐 境射 温度阳光气,温照和明地灯基,暧温气度设变备化,人,局体部等温 差,热风等
• (二)工件热变形对加工精度的影响 • 1. 工件均匀受热 • 车、镗、磨工件回转表面 • ΔL=αLΔθ
• (三)原始误差
• 工艺系统的误差称为原始误差
• (四)原始误差与加工误差的关系: • 工艺系统的原始误差可能原样、缩小、放大
地反映给工件。
过刀刃的加工表面法线方向的原始误差对加 工误差影响最大——误差敏感方向。 过刀刃的加工表面切线方向的原始误差对加 工误差影响最小——误差不敏感方向。一般 可以忽略不计。
• 一般用传动链末端元件的转角误差来衡 量。
• (二)刀具的几何误差
• 包括刀具的制造、安装误差及磨损。
• 采用定尺寸刀具加工时,刀具的尺寸误 差将直接影响工件尺寸精度。
• 采用成形刀具加工时,刀具的形状误差 将直接影响工件的形状精度。
• 采用展成刀具加工时,刀具切削刃的几 何形状及有关尺寸误差也会影响工件的 加工精度。
• 3. 双峰分布
• 提高机床主轴的回转精度的措施: • 适当提高主轴及箱体的制造精度;
• 选用高精度的轴承,对滚动轴承进行预 紧;
第六章机械制造质量分析与控制

影响加工精度的因素及其分析
2.机床部件刚度及其特点
图6-15 车削时作用在刀具上和工件上的力
影响加工精度的因素及其分析
图6-16 在顶尖间加工棒料的变形
影响加工精度的因素及其分析
图6-17 车床刀架、头尾架静刚度测量示意图
影响加工精度的因素及其分析
图6-18 车床刀架部件的静刚度曲线
影响加工精度的因素及其分析
切削时还会超过90%,传入刀具的热量为10%~40%,传给工件的热量不到10%。但是这种数 据还不能笼统地用来估计工件的热变形大小。第一,上述这些比例关系 ,只适合于车、铣、 刨、立镗、外拉削等切屑流出较畅、切屑和刀具的摩擦也较小的情况。若是像钻孔那样, 由于横刃的挤压作用、切屑和钻头排屑沟的摩擦以及散热条件不好等原因,钻孔时所产生 的热量约有50%进入工件。又如在卧镗铸铁工件时,切屑几乎全部留在孔内,传给切屑的热 量又传给了工件。磨削时, 约有84%的磨削热传入工件 ,只有4%传入磨屑,12%传入砂轮。
研究结果,试行了按季节调温的措施(例如春、秋季取20℃,夏季取23℃,冬季取
17℃),既不影响制造质量,又可节省投资和水电消耗,还有利于工人的健康。 3)让机床在开车后空转一段时间,在到达或接近热平衡后再进行加工,在加工有
些精密零件时,尽管有不切削的间断时间,但仍让机床空转,以保持机床的热平衡。
机械加工精度的基本概念
实践表明,机床在工作中受到多种热源的影响,主要有: 1)电气热:机械动力源的能量损耗转化为热(电动机、电气箱、油泵、液压操纵箱、 活塞副、各种阀件等)。 2)传动部分将发生摩擦热(轴承副、齿轮副、离合器、导轨副等),并通过润滑油而 将热量散布开来,特别是床身内部的润滑油池,形成一个很大的热源,对床身的热变 形影响很大,会造成导轨弯曲。 3)切削热的大部分是被切屑和冷却液带走的,但是切屑和冷却液落到床身上后,其 热量也就传递给床身,使后者产生了热变形。 4)环境传来的热(室温的变化、阳光的照射、取暖装置的影响等)使机床各部分受 热不均匀而引起变形。
- 1、下载文档前请自行甄别文档内容的完整性,平台不提供额外的编辑、内容补充、找答案等附加服务。
- 2、"仅部分预览"的文档,不可在线预览部分如存在完整性等问题,可反馈申请退款(可完整预览的文档不适用该条件!)。
- 3、如文档侵犯您的权益,请联系客服反馈,我们会尽快为您处理(人工客服工作时间:9:00-18:30)。
图5-16 两零件结合面间的接触情况
4.机床部件刚度 2)摩擦力的影响
图5-17 摩擦力对机床部件刚度的影响
4.机床部件刚度
3)低刚度零件的影响 在机床部件中,个别薄弱零件对刚度 的影响很大。
4)间隙的影响 机床部件在受力作用时,首先消除零 件间在受力作用方向上的间隙,这会使机 床部件产生相应的位移。
5. (1)由于工艺系统刚度变化引起的误差
图5-18 车削外圆时工艺 系统受力变形对加工精度 的影响
5. (2)由于切削力变化引起的误差
在加工过程中,由于工件的加工余量发生变 化、工件材质不均等因素引起的切削力变化,使 工艺系统变形发生变化,从而产生加工误差。
图5-19 毛坯形状误差的复映
5. (3)由于夹紧变形引起的误差
图5-10 工件在夹具中装夹示意
三、调整误差 1.试切法调整
试切法调整广泛用在单件、小批生产中。这 种调整方式产生调整误差的来源有3
(1)度量误差 (2)加工余量的影响 (3)微进给误差
2.按定程机构调整
在大批大量生产中广泛应用行程挡 块、靠模、凸轮等机构保证加工精度。 这时候,这些机构的制造精度和调整, 以及与它们配合使用的离合器、电气开 关、控制阀等的灵敏度就成了影响误差
实际加工不可能把零件做得与理想零件完全 一致,总会有大小不同的偏差,零件加工后的实 际几何参数对理想几何参数的偏离程度,称为加 工误差。
2.加工经济精度
图5-2 加工成本与加工误差之间的关系
3.原始误差
由机床、夹具、刀具和工件组成的机械加工工艺 系统 (简称工艺系统) 会有各种各样的误差产生,这 些误差在各种不同的具体工作条件下都会以各种不同 的方式 (或扩大、或缩小) 反映为工件的加工误差。 工艺系统的误差是“因”,是根源;工件的加工误差 是 “果”,是表现;因此,我们把工艺系统的误差 称为原始误差。
4.误差敏感方向的概念
图5-3 由δz引起的加工误差
原始误差所引起的
切削刃与工件间的相对 位移,如果产生在加工 表面的法线方向,则对 加工误差有直接的影响 ;如果产生在加工表面 的切线方向上,就可以 忽略不计。我们把加工 表面的法向称之为误差 的敏感方向。
5.
分析计算法是在掌握各原始误差对加工精度影 响规律的基础上,分析工件加工中所出现的误差可 能是哪一个或哪几个主要原始误差所引起的,并找 出原始误差与加工误差之间的影响关系,进而通过 估算来确定工件的加工误差的大小,再通过试验测 试来加以验证。
第五章 机械制造质量分析与控制
第一节 机械加工精度 第二节 工艺过程的统计分析 第三节 机械加工表面质量 第四节 机械加工过程中的振动
第一节 机械加工精度
一、概 述
1.加工精度与加工误差
所谓加工精度是指零件加工后的实际几何参 数 (尺寸、形状和位置) 与理想几何参数的符合 程度。实际值愈接近理想值,加工精度就愈高。
统计分析法是对具体加工条件下加工得到的几 何参数进行实际测量,然后运用数理统计学方法对 这些测试数据进行分析处理,找出工件加工误差的 规律和性质,进而控制加工质量。分析计算法主要 是在对单项原始误差进行分析计算的基础上进行的 ,统计分析法则是对有关的原始误差进行综合分析 的基础上进行的。
二、工艺系统几何误差
五、工艺系统受热变形引起的误差
1.
(1)内部热源 内部热源来自工艺系统内部, 其热量主要是以热传导的形式传递的。
(2)成形刀具 (如成形车刀、成形铣刀、模数 铣刀等)的形状误差
(3)展成刀具 (如齿轮滚动、插齿刀、花键滚 刀等)切削刃的形状及有关尺寸,以及其安装、调 整不正确
(4)一般刀具 (如普通车刀、单刃镗刀、面铣 刀、刨刀等)的制造误差
3.夹具
夹具的作用是使工件相 对于刀具和机床具有正确的 位置,因此夹具的制造误差 对工件的加工精度 (特别是 位置精度) 有很大影响。
3.按样件或样板调整
在大批大量生产中用多刀加工时,常用专门 样件来调整切削刃间的相对位置。如活塞环槽半
当工件形状复杂,尺寸和重量都比较大的时 候,利用样件进行调整就太笨重,且不经济,这 时可以采用样板对刀。
四、工艺系统受力变形引起的误差
1.基本概念
机械加工工艺系统在切削力、夹紧力、惯性 力、重力、传动力等的作用下,会产生相应的变 形,从而破坏了刀具和工件之间的正确的相对位 置,使工件的加工精度下降。
图5-12
a)车长轴 b)磨内孔
2.工件刚度
工艺系统中如果工件刚度相对于机床、刀 具、夹具来说比较低,在切削力的作用下,工 件由于刚性不足而引起的变形对加工精度的影 响就比较大,其最大变形量可按材料力学有关
3.刀具刚度
外圆车刀在加工表面法线(y)方向上的 刚度很大,其变形可以忽略不计。镗直径较小 的内孔,刀杆刚度很差,刀杆受力变形对孔加 工精度就有很大影响。
1.机床的几何误差
加工中刀具相对于工件的成形运动一般 都是通过机床完成的,因此,工件的加工精 度在很大程度上取决于机床的精度。机床制 造误差对工件加工精度影响较大的有:主轴 回转误差、导轨误差和传动链误差。机床的 磨损将使机床工作精度下降。
2.
(1)定尺寸刀具 (如钻头、铰刀、镗刀块、孔 拉刀、丝锥、板牙、键槽铣刀等)的尺寸和形状误 差
图5-21 a)夹紧后 b)镗孔后 c)放松后 d)加过渡环后夹紧
(4)其他作用力的影响 除上述因素外,重力、惯性力、传动力等也 会使工艺系统的变形发生变化,引起加工误差。
6.
(1) 1)提高工件和刀具的刚度 2)提高机床刚度 3)采用合理的装夹方式和加工方式
(2)减小切削力及其变化 合理地选择刀具材料、增大前角和主偏角、对 工件材料进行合理的热处理以改善材料的加工性能 等,都可使切削力减小。
4.机床部件刚度 (1)机床部件刚度
图5-14 车床部件静刚度的测定 1—心轴 2、3、6—千分表 4—测力环 5—螺旋加力器
图5-15 车床刀架部件的刚度曲线 1—加ቤተ መጻሕፍቲ ባይዱ曲线 2—卸载曲线
4.机床部件刚度 (2)
1)结合面接触变形的影响 由于零件表面存在宏观几何形状误差和微观几
何形状误差,结合面的实际接触面积只是名义接触 面积的一小部分 (图所示),在外力作用下,实际 接触区的接触应力很大,产生了较大的接触变形。
4.机床部件刚度 2)摩擦力的影响
图5-17 摩擦力对机床部件刚度的影响
4.机床部件刚度
3)低刚度零件的影响 在机床部件中,个别薄弱零件对刚度 的影响很大。
4)间隙的影响 机床部件在受力作用时,首先消除零 件间在受力作用方向上的间隙,这会使机 床部件产生相应的位移。
5. (1)由于工艺系统刚度变化引起的误差
图5-18 车削外圆时工艺 系统受力变形对加工精度 的影响
5. (2)由于切削力变化引起的误差
在加工过程中,由于工件的加工余量发生变 化、工件材质不均等因素引起的切削力变化,使 工艺系统变形发生变化,从而产生加工误差。
图5-19 毛坯形状误差的复映
5. (3)由于夹紧变形引起的误差
图5-10 工件在夹具中装夹示意
三、调整误差 1.试切法调整
试切法调整广泛用在单件、小批生产中。这 种调整方式产生调整误差的来源有3
(1)度量误差 (2)加工余量的影响 (3)微进给误差
2.按定程机构调整
在大批大量生产中广泛应用行程挡 块、靠模、凸轮等机构保证加工精度。 这时候,这些机构的制造精度和调整, 以及与它们配合使用的离合器、电气开 关、控制阀等的灵敏度就成了影响误差
实际加工不可能把零件做得与理想零件完全 一致,总会有大小不同的偏差,零件加工后的实 际几何参数对理想几何参数的偏离程度,称为加 工误差。
2.加工经济精度
图5-2 加工成本与加工误差之间的关系
3.原始误差
由机床、夹具、刀具和工件组成的机械加工工艺 系统 (简称工艺系统) 会有各种各样的误差产生,这 些误差在各种不同的具体工作条件下都会以各种不同 的方式 (或扩大、或缩小) 反映为工件的加工误差。 工艺系统的误差是“因”,是根源;工件的加工误差 是 “果”,是表现;因此,我们把工艺系统的误差 称为原始误差。
4.误差敏感方向的概念
图5-3 由δz引起的加工误差
原始误差所引起的
切削刃与工件间的相对 位移,如果产生在加工 表面的法线方向,则对 加工误差有直接的影响 ;如果产生在加工表面 的切线方向上,就可以 忽略不计。我们把加工 表面的法向称之为误差 的敏感方向。
5.
分析计算法是在掌握各原始误差对加工精度影 响规律的基础上,分析工件加工中所出现的误差可 能是哪一个或哪几个主要原始误差所引起的,并找 出原始误差与加工误差之间的影响关系,进而通过 估算来确定工件的加工误差的大小,再通过试验测 试来加以验证。
第五章 机械制造质量分析与控制
第一节 机械加工精度 第二节 工艺过程的统计分析 第三节 机械加工表面质量 第四节 机械加工过程中的振动
第一节 机械加工精度
一、概 述
1.加工精度与加工误差
所谓加工精度是指零件加工后的实际几何参 数 (尺寸、形状和位置) 与理想几何参数的符合 程度。实际值愈接近理想值,加工精度就愈高。
统计分析法是对具体加工条件下加工得到的几 何参数进行实际测量,然后运用数理统计学方法对 这些测试数据进行分析处理,找出工件加工误差的 规律和性质,进而控制加工质量。分析计算法主要 是在对单项原始误差进行分析计算的基础上进行的 ,统计分析法则是对有关的原始误差进行综合分析 的基础上进行的。
二、工艺系统几何误差
五、工艺系统受热变形引起的误差
1.
(1)内部热源 内部热源来自工艺系统内部, 其热量主要是以热传导的形式传递的。
(2)成形刀具 (如成形车刀、成形铣刀、模数 铣刀等)的形状误差
(3)展成刀具 (如齿轮滚动、插齿刀、花键滚 刀等)切削刃的形状及有关尺寸,以及其安装、调 整不正确
(4)一般刀具 (如普通车刀、单刃镗刀、面铣 刀、刨刀等)的制造误差
3.夹具
夹具的作用是使工件相 对于刀具和机床具有正确的 位置,因此夹具的制造误差 对工件的加工精度 (特别是 位置精度) 有很大影响。
3.按样件或样板调整
在大批大量生产中用多刀加工时,常用专门 样件来调整切削刃间的相对位置。如活塞环槽半
当工件形状复杂,尺寸和重量都比较大的时 候,利用样件进行调整就太笨重,且不经济,这 时可以采用样板对刀。
四、工艺系统受力变形引起的误差
1.基本概念
机械加工工艺系统在切削力、夹紧力、惯性 力、重力、传动力等的作用下,会产生相应的变 形,从而破坏了刀具和工件之间的正确的相对位 置,使工件的加工精度下降。
图5-12
a)车长轴 b)磨内孔
2.工件刚度
工艺系统中如果工件刚度相对于机床、刀 具、夹具来说比较低,在切削力的作用下,工 件由于刚性不足而引起的变形对加工精度的影 响就比较大,其最大变形量可按材料力学有关
3.刀具刚度
外圆车刀在加工表面法线(y)方向上的 刚度很大,其变形可以忽略不计。镗直径较小 的内孔,刀杆刚度很差,刀杆受力变形对孔加 工精度就有很大影响。
1.机床的几何误差
加工中刀具相对于工件的成形运动一般 都是通过机床完成的,因此,工件的加工精 度在很大程度上取决于机床的精度。机床制 造误差对工件加工精度影响较大的有:主轴 回转误差、导轨误差和传动链误差。机床的 磨损将使机床工作精度下降。
2.
(1)定尺寸刀具 (如钻头、铰刀、镗刀块、孔 拉刀、丝锥、板牙、键槽铣刀等)的尺寸和形状误 差
图5-21 a)夹紧后 b)镗孔后 c)放松后 d)加过渡环后夹紧
(4)其他作用力的影响 除上述因素外,重力、惯性力、传动力等也 会使工艺系统的变形发生变化,引起加工误差。
6.
(1) 1)提高工件和刀具的刚度 2)提高机床刚度 3)采用合理的装夹方式和加工方式
(2)减小切削力及其变化 合理地选择刀具材料、增大前角和主偏角、对 工件材料进行合理的热处理以改善材料的加工性能 等,都可使切削力减小。
4.机床部件刚度 (1)机床部件刚度
图5-14 车床部件静刚度的测定 1—心轴 2、3、6—千分表 4—测力环 5—螺旋加力器
图5-15 车床刀架部件的刚度曲线 1—加ቤተ መጻሕፍቲ ባይዱ曲线 2—卸载曲线
4.机床部件刚度 (2)
1)结合面接触变形的影响 由于零件表面存在宏观几何形状误差和微观几
何形状误差,结合面的实际接触面积只是名义接触 面积的一小部分 (图所示),在外力作用下,实际 接触区的接触应力很大,产生了较大的接触变形。