中、高碳钢丝的高速拉拔
拉拔方式对高碳钢丝组织性能的影响
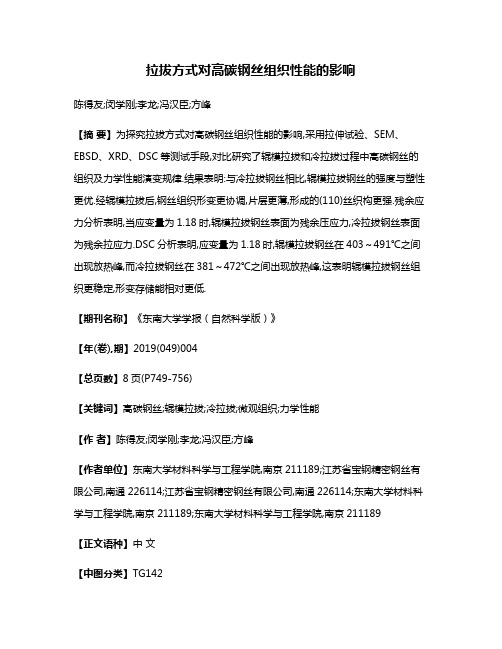
拉拔方式对高碳钢丝组织性能的影响陈得友;闵学刚;李龙;冯汉臣;方峰【摘要】为探究拉拔方式对高碳钢丝组织性能的影响,采用拉伸试验、SEM、EBSD、XRD、DSC等测试手段,对比研究了辊模拉拔和冷拉拔过程中高碳钢丝的组织及力学性能演变规律.结果表明:与冷拉拔钢丝相比,辊模拉拔钢丝的强度与塑性更优.经辊模拉拔后,钢丝组织形变更协调,片层更薄,形成的(110)丝织构更强.残余应力分析表明,当应变量为1.18时,辊模拉拔钢丝表面为残余压应力,冷拉拔钢丝表面为残余拉应力.DSC分析表明,应变量为1.18时,辊模拉拔钢丝在403~491℃之间出现放热峰,而冷拉拔钢丝在381~472℃之间出现放热峰,这表明辊模拉拔钢丝组织更稳定,形变存储能相对更低.【期刊名称】《东南大学学报(自然科学版)》【年(卷),期】2019(049)004【总页数】8页(P749-756)【关键词】高碳钢丝;辊模拉拔;冷拉拔;微观组织;力学性能【作者】陈得友;闵学刚;李龙;冯汉臣;方峰【作者单位】东南大学材料科学与工程学院,南京211189;江苏省宝钢精密钢丝有限公司,南通226114;江苏省宝钢精密钢丝有限公司,南通226114;东南大学材料科学与工程学院,南京211189;东南大学材料科学与工程学院,南京211189【正文语种】中文【中图分类】TG142大应变珠光体钢丝通常是高碳钢盘条经冷拉拔形变制得,因其兼具高强度和良好的韧性而被广泛应用于汽车轮胎钢帘线、大跨度桥梁斜拉索以及高层建筑等重要领域[1-3].冷拉拔是制备高强度钢丝的主要技术,但其存在表面摩擦阻力及剪切变形较大等不足,这些因素不仅会造成模具磨损,影响表面质量,甚至还会影响钢丝使用性能.辊模拉拔因其具有低摩擦、高速减径以及低能耗等优势,在低碳钢中已得到广泛应用[4-7],随着辊模材料及模具制备技术的突破,该技术有可能成为高强度钢丝制备技术的有益补充.与传统冷拉拔相比,辊模拉拔所需拉拔力较小,能耗更低,组织变形更均匀,在避免出现中心裂纹的情况下,具有较大的道次压缩率[5].形变后,低碳钢丝的强塑性均提升,表面性能得到改善[6-7];高碳钢丝的表面残余拉应力减小,横截面应变分布更均匀,钢丝表面温升低,表面质量更高[8-9].目前针对多道次辊模拉拔高碳钢丝的力学性能以及组织变形机理缺乏系统的研究.因此,本文通过拉伸试验、SEM、EBSD、XRD、DSC等测试手段,对比研究了多道次辊模拉拔和冷拉拔过程中高碳钢丝的力学性能及组织变形特征,进一步探讨了辊模拉拔技术在制备高强度钢丝方面的可行性,以期为辊模拉拔技术在高强度钢丝制备中的应用奠定基础.1 实验材料与方法实验材料为宝钢提供的SWRS72A高碳钢盘条(直径Φ=5.5 mm),其化学成分如表1所示.图1为辊模拉拔和冷拉拔工艺示意图.将盘条酸洗硼化后,再分别进行辊模拉拔(设备型号CL30 C1 33)和冷拉拔(设备型号LW1/600H76/600)处理,经多道次拉拔至3.05 mm,总应变量ε为1.18.表1 盘条的化学成分 %w(C)w(Mn)w(Si)w(Cr)w(Ni)w(S)w(P)w(Fe)0.7040.5010.1970.0140.012 90.004 60.005 9Bal.(a) 辊模拉拔 (b) 冷拉拔图1 2种拉拔工艺示意图采用CMT5105微机控制电子万能试验机测试钢丝样品的抗拉强度(拉伸温度25 ℃,拉伸速率2 mm/min).在Sirion-400场发射扫描电子显微镜(SEM)下观察钢丝纵截面的显微组织,并使用Nano Measurer统计片层间距.通过电子背散射衍射技术(EBSD)采集钢丝纵截面中心区域的晶体学取向信息,测试设定参数为:步长1.5 μm,区域宽度500 μm×400 μm,放大倍数500倍,经OIM analysis 处理分析织构演变规律.采用线切割在离钢丝(ε=1.18)表面0.2 mm处沿纵向切取厚1 mm、长8 mm的样品,经机械抛光及二氧化硅抛光液抛光后,使用智能X 射线衍射仪(Smartlab 3)测试其残余应力.测试设定参数:衍射源为CuKα,电压40 kV,电流30 mA,扫描范围80°~84°,扫描速度0.001 2°/s.选取试样表面法线与(211)晶面法线的夹角Ψ为0°、15°、30°、45°,测试不同Ψ下的(211)晶面衍射峰.由布拉格方程2dsinθ=nλ(其中,d为晶面间距;θ为布拉格角;n为衍射指数;λ为入射线波长)可知[10],当入射线波长一定时,应力在引起晶面间距变化时,衍射角也会随之改变,根据XRD的sin2Ψ法则[10-11],利用Jade 6计算残余应力.对钢丝样品(ε=1.18)进行差热扫描分析(STA449 F3),测试温度范围为25~550 ℃,升温速率为20 ℃/min,保护气体为氩气.采用透射电子显微镜(JEM2000EX)分析不同拉拔方式下钢丝纵向组织形貌演变.2 试验结果与分析2.1 宏观力学性能图2(a)为辊模拉拔和冷拉拔钢丝的抗拉强度随应变量变化曲线.可以看到,不同拉拔方式下钢丝的抗拉强度均随应变量的增加而增加,同一应变量下,辊模拉拔钢丝的抗拉强度均高于冷拉拔;当应变量为1.18时,辊模拉拔钢丝的强度为1 583 MPa,冷拉拔钢丝的强度为1 493 MPa,辊模拉拔钢丝的强度较冷拉拔提升约6%.图2(b)为辊模拉拔和冷拉拔钢丝的断面收缩率与应变量关系曲线.可以看到,冷拉拔钢丝的断面收缩率随应变量的增加而下降,而辊模拉拔钢丝的断面收缩率变化不大.综合可知,经辊模拉拔形变后,钢丝的强度与塑性均优于冷拉拔钢丝.2.2 珠光体组织形貌图3为不同应变量下的组织形貌照片.可以看到,未经形变的盘条组织呈等轴状,层片平直排列,方向随机分布.经辊模拉拔后,当应变量为0.23时,层片呈2种典型的形态:与拉拔轴向夹角较小的层片被均匀拉长、减薄,而与拉拔轴向夹角较大的层片发生剪切、弯折变形[12],如图3(b)中A、B区域所示.当应变量增加到0.74时,珠光体层片逐步平行于拉拔轴向排列,且进一步减薄.应变量为1.18时,层片变得更加细长,珠光体组织整体保持较好的层片结构.经冷拉拔后,当应变量为0.23时,图3(e)中A区域层片发生剪切变形,且剪切方向与拉拔方向夹角较大,B区域与拉拔轴向夹角较大的层片发生弯折变形,弯折方向朝向拉拔轴向.当应变量增加到0.74时,因较大剪切应力的存在,渗碳体片在剪切位置产生应力集中而发生断裂[13-14],如图3(f)中C区域所示.应变量为1.18时,珠光体层片基本平行于拉拔方向,局部观察到断裂、碎化的渗碳体颗粒,如图3(g)中D区域所示.(a) 抗拉强度(b) 断面收缩率图2 不同拉拔方式下钢丝力学性能比较(a) 原始盘条(ε=0)(b) 辊模拉拔(ε=0.23)(c) 辊模拉拔(ε=0.74)(d) 辊模拉拔(ε=1.18)(e) 冷拉拔(ε=0.23)(f) 冷拉拔(ε=0.74)(g) 冷拉拔(ε=1.18)图3 不同应变量下钢丝组织形貌图(纵截面)由不同拉拔方式下的组织形貌可知,两者在直观上无明显差异,为进一步分析组织形变特征,采用Nano Measurer统计了不同拉拔方式下钢丝组织中的珠光体片层间距(相邻铁素体片层中心的距离).图4为钢丝心部与边缘处片层间距随应变量变化曲线.可以看到,各应变量下,辊模拉拔钢丝心部与边缘的片层间距相近,而冷拉拔钢丝心部与边缘的片层间距则相差较大,表明其组织变形不均匀.图5为平均片层间距与应变量关系曲线.可以看到,辊模拉拔和冷拉拔钢丝的平均片层间距均随应变量的增加而不断减小,经辊模拉拔后,同一应变量下,钢丝的平均片层间距小于冷拉拔状态.此外,观察误差棒可知,冷拉拔钢丝的平均片层间距波动较大,辊模拉拔钢丝的平均片层间距波动较小.这表明,辊模拉拔方式更有利于钢丝片层组织的协调变形.(a) 辊模拉拔(b) 冷拉拔图4 钢丝心部与边缘处片层间距随应变量变化曲线图5 平均片层间距随应变量变化曲线综合比较2种拉拔变形过程可知,随着应变量的增加,钢丝的片层组织均沿拉拔方向逐渐减薄,区别在于,辊模拉拔钢丝片层组织形变更协调,促进了片层的减薄.2.3 EBSD织构演变图6为不同拉拔方式下钢丝纵截面取向成像图.可以看到,原始盘条组织呈等轴状,不同颜色的晶粒代表不同的取向,未形变盘条晶粒取向随机分布,呈各向异性;形变后,组织沿拉拔方向拉长,晶粒尺寸得到细化,产生择优取向.经OIM analysis 处理后,得到不同拉拔方式下不同应变量钢丝沿拉拔方向的反极图,如图7所示.可以看到,原始盘条中存在较弱的〈110〉丝织构,在2种拉拔变形方式下,随着应变量的增加,〈110〉丝织构均在逐渐增强.根据图7作出不同拉拔方式下〈110〉丝织构强度与应变量关系曲线,如图8所示.可以看到,形变后,〈110〉丝织构强度均随应变量的增加而增加;两者相比,同一应变量下,辊模拉拔钢丝产生的〈110〉丝织构强度高于冷拉拔状态,且织构强度差值随应变量的增加呈增大趋势.(a) 原始盘条(ε=0)(b) 辊模拉拔(ε=1.18)(c) 冷拉拔(ε=1.18)图6 不同拉拔方式下钢丝取向成像图(纵截面)(a) 原始盘条(ε=0)(b) 辊模拉拔(ε=0.49)(c) 辊模拉拔(ε=0.74)(d) 辊模拉拔(ε=1.18)(e) 冷拉拔(ε=0.49)(f) 冷拉拔(ε=0.74)(g) 冷拉拔(ε=1.18)图7 不同应变量下的织构反极图(纵截面)图8 〈110〉丝织构强度随应变量变化曲线2.4 残余应力分析采用XRD测试了不同拉拔形变钢丝(ε=1.18)在不同Ψ角下铁素体(211)晶面对应衍射峰的变化,如图9所示.可以看到,随Ψ角的增大,辊模拉拔钢丝中铁素体(211)晶面的衍射峰逐渐向右偏移,对应的衍射角逐渐增大,如图9(a)所示.冷拉拔钢丝中铁素体(211)晶面的衍射峰逐渐向左偏移,对应的衍射角逐渐减小,如图9(b)所示.(a) 辊模拉拔(b) 冷拉拔图9 应变量为1.18时铁素体(211)晶面不同Ψ角的XRD图根据半高宽法确定不同拉拔方式下不同Ψ角的铁素体(211)晶面衍射角,计算对应的晶面间距,作出(211)晶面间距d与sin2Ψ的关系曲线,如图10所示.可以看到,辊模拉拔钢丝中铁素体(211)晶面间距与sin2Ψ成负线性关系,而冷拉拔钢丝中铁素体(211)晶面间距与sin2Ψ成正线性关系.残余应力计算公式如下:(1)σ=KM(2)(4)(4)式中,εΨ为与表面成任意Ψ角的(211)晶面的应变;dΨ为不同Ψ角上的(211)晶面间距;d0为试样表面法线与(211)晶面法线平行时的晶面间距;K为常数;M为因变量;E为弹性模量;υ为泊松比.图10 铁素体(211)晶面间距与sin2Ψ关系曲线结合图10结果,由式(1)~(4)可知[10-11,15]:残余应力σ正比于M,当M<0时,表现为残余压应力;当M>0时,表现为残余拉应力.因此,经辊模拉拔后,M<0,钢丝表面为残余压应力;而对于冷拉拔钢丝,M>0,钢丝表面为残余拉应力.利用Jade软件计算表面残余应力大小.结果表明:经辊模拉拔后,钢丝表面残余压应力约为(146±20) MPa;而经冷拉拔后,钢丝表面残余拉应力约为(154±18) MPa.2.5 DSC分析图11给出了辊模拉拔和冷拉拔钢丝(ε=1.18)的DSC曲线.可以看到,辊模拉拔钢丝在403~491 ℃之间出现放热峰,峰值温度为446 ℃;冷拉拔钢丝在381~472 ℃之间出现放热峰,峰值温度为408 ℃.在放热温度区间内,放热峰的产生主要与渗碳体发生球化现象[16-18]有关.辊模拉拔钢丝中渗碳体发生球化的温度更高,这表明辊模拉拔方式下渗碳体片具有更好的热稳定性,形变存储能相对更低.比较峰值温度后半段曲线可知,冷拉拔钢丝DSC曲线的斜率高于辊模拉拔,表明冷拉拔钢丝组织放热效应更明显.图11 不同拉拔方式下应变量为1.18时钢丝的DSC曲线3 讨论不同拉拔方式下,应力的不同是导致钢丝显微组织变化的主要因素.在一个道次的辊模拉拔变形过程中,钢丝横截面形状变化以及受力分析如图12所示.图中,T为拉应力,C为压应力.可以看到,与冷拉拔相比,一个道次的辊模拉拔过程可分为2个阶段:首先钢丝横截面由初始的圆形变化为椭三角形,然后又变化为圆形.钢丝在一个道次经历的2次变形中,表面各部分受力状态不同,前后两个阶段相同位置处的钢丝表面受力状态相反,这充分促进了钢丝组织的塑性流动.此外,在拉拔过程中,钢丝轴向拉应力较小,径向压应力较大,这种倾向于轧制的应力状态,显著改善了难变形金属制品高碳钢丝的塑性.研究表明[13-14,19],当初始片层方向平行于拉拔轴向时,拉拔阻力最小,片层组织沿拉拔方向拉长、减薄;当初始片层方向与拉拔方向夹角小于30°时,珠光体片层将发生转动,并沿拉拔轴向减薄;当初始片层方向与拉拔轴向夹角大于30°时,拉拔阻力最大,片层组织以剪切变形方式发生断裂、破碎.结合2.2节的组织形貌及2.5节的DSC曲线特征可知,辊模拉拔产生的较软应力状态,使得钢丝片层间距较小,这表明,辊模拉拔形变方式下,更多渗碳体片的排列位向处于有利取向,片层形变阻力小,主要表现为拉长、减薄特征.冷拉拔钢丝片层间距较大,这表明,冷拉拔形变方式下,较多渗碳体片的排列位向处于不利取向,片层形变阻力大,主要表现为扭折、剪切至断裂.DSC结果显示,冷拉拔钢丝片层组织形变存储能更高,这表明,冷拉拔钢丝产生的变形程度较大,致使较多的渗碳体片发生破碎.因此,相较于冷拉拔,辊模拉拔钢丝组织形变更协调.(a) 钢丝横截面形状变化(b) 受力示意图图12 辊模拉拔一个道次形变过程在拉拔形变过程中,通常形成铁素体〈110〉丝织构有2种途径:一种是铁素体位错滑移,另一种是片层的转动使铁素体〈110〉取向接近拉拔轴向.辊模拉拔钢丝片层间距更小,更多渗碳体片的排列位向平行或者接近平行拉拔轴向,从而使得更多铁素体〈110〉取向转到拉拔方向,形成较强的〈110〉丝织构.冷拉拔钢丝片层间距较大,渗碳体片的排列位向不利,主要以剪切方式变形,因应力集中而导致断裂、破碎,破碎的渗碳体易造成位错堆积、缠结,使得铁素体位错滑移受阻,片层组织后续形变变得困难,从而难以形成〈110〉丝织构.因此,辊模拉拔方式更有利于〈110〉丝织构的形成,减小了沿拉拔方向上的形变阻力,有助于提高钢丝的轴向力学性能[20].不同拉拔方式下钢丝在应变量0.23、1.18时的透射照片如图13所示.可以看到,形变后,当应变量为0.23时,在辊模拉拔过程中,渗碳体片主要以缓慢弯曲方式协调变形;在冷拉拔过程中,渗碳体片主要发生剪切变形,剪切位置易产生大量缠结的位错,因应力集中而造成渗碳体片发生断裂、破碎.当应变量增加到1.18时,位错密度进一步增加,位错运动以多系滑移为主,〈110〉丝织构的形成促使片层方向转向拉拔轴向,钢丝组织形变阻力减小,片层得到进一步细化.统计应变量为1.18时的片层间距分布比例,如表2所示.可以看到,辊模拉拔钢丝的片层间距集中分布在80~100 nm,平均片层间距约为94 nm.冷拉拔钢丝的片层间距集中分布在100~130 nm,平均片层间距约为125 nm.辊模拉拔方式产生的较强〈110〉丝织构,使得钢丝形变阻力更小,从而促进了片层间距的减小.(a) 辊模拉拔(ε=0.23)(b) 冷拉拔(ε=0.23)(c) 辊模拉拔(ε=1.18)(d) 冷拉拔(ε=1.18)图13 不同拉拔方式下钢丝组织的透射照片(纵截面)表2 应变量为1.18时片层间距分布比例 %片层间距/nm[60,80)[80,100)[100,130)[130,150)[150,∞)辊模拉拔21.646.428.73.3冷拉拔7.524.526.021.720.3图14为不同拉拔方式下平均片层间距与应变量关系曲线,钢丝片层间距S与应变量ε的关系一般满足S=S0exp(-ε/2)[21](式中,S0为未变形盘条的片层间距).可以看到,冷拉拔状态的片层间距变化和理论值基本一致,辊模拉拔状态的片层间距变化则位于理论曲线下方.通常,较小的片层间距会增加位错滑移的障碍,使得钢丝变形抗力增大,进而提高钢丝强度.因此,辊模拉拔方式下,片层产生的强化作用高于冷拉拔状态.此外,相界面的增多能有效阻止裂纹的扩展,从而提升了钢丝塑性.另一方面,不同拉拔方式形变后,应变量为1.18时,冷拉拔钢丝表面为残余拉应力,辊模拉拔钢丝表面为残余压应力.研究表明[22-24],表面残余压应力的存在可提高钢丝在拉拔过程中的形变速率,改善钢丝表面质量,降低钢丝环境促进断裂及疲劳失效的倾向,延长钢丝在复杂环境条件下的使用寿命.图14 不同拉拔方式下平均片层间距随应变量变化曲线综上可知,经辊模拉拔后,钢丝形变更协调,形成的〈110〉丝织构更强,片层更薄,力学性能得以提升;然而,与冷拉拔技术相比,辊模拉拔尺寸精度较低,更高强度钢丝的生产难以实现;并且经多道次减径后,钢丝易产生侧向宽展[8-9],不利于织构的形成,会对钢丝性能造成影响.已有研究指出[25-26],为减小细丝在辊模拉拔过程中的变形不均匀性,单道次减径大小应控制在4%~8%,此方法将大大降低生产效率,增加成本.若结合2种技术的优点,在起始时采用辊模进行拉拔,得到组织性能较好的高强度钢丝,最终再通过冷拉拔进行精整加工,将可以获得综合性能良好、尺寸精度较高的产品.因此,辊模拉拔与冷拉拔的联合使用有望在弹簧钢丝、冷镦钢丝等领域得到广泛应用.4 结论1) 不同拉拔方式下高碳钢丝的抗拉强度均随应变量的增加而增加,同一应变量下,辊模拉拔钢丝的强度与塑性均优于冷拉拔钢丝.2) 与冷拉拔钢丝相比,辊模拉拔钢丝组织形变更协调,片层更薄,产生的〈110〉丝织构更强.3) 残余应力分析表明,当应变量为1.18时,辊模拉拔钢丝表面为残余压应力,冷拉拔钢丝表面为残余拉应力.4) DSC结果表明,应变量为1.18时,辊模拉拔钢丝在403~491 ℃之间出现放热峰,峰值温度为446 ℃;冷拉拔钢丝在381~472 ℃之间出现放热峰,峰值温度为408 ℃.经辊模拉拔形变后,高碳钢丝片层组织具有更好的热稳定性.参考文献【相关文献】[1] Borchers C, Kirchheim R. Cold-drawn pearlitic steel wires [J]. Progress in Materials Science, 2016, 82: 405-444.DOI: 10.1016/j.pmatsci.2016.06.001.[2] Zhang X D, Godfrey A, Huang X X, et al. Microstructure and strengthening mechanisms in cold-drawn pearlitic steel wire [J]. Acta Materialia, 2011, 59(9): 3422-3430.DOI:10.1016/j.actamat.2011.02.017.[3] Li Y J, Choi P, Goto S, et al. Evolution of strength and microstructure during annealing of heavily cold-drawn 6.3 GPa hypereutectoid pearlitic steel wire [J]. Acta Materialia, 2012, 60(9): 4005-4016.DOI: 10.1016/j.actamat.2012.03.006.[4] Gokyu I, Saito Y. Studies on the roller-die [J]. Tetsu-to-Hagane Overseas, 1964, 4: 44-52.[5] Bitkov V. Expediency of roller dies application in wire drawing—part 2 [J]. Wire Cable Technology International, 2008, 36(3): 112-113.[6] El Amine K, Larsson J, Pejryd L. Experimental comparison of roller die and conventional wire drawing [J]. Journal of Materials Processing Technology, 2018, 257: 7-14.DOI:10.1016/j.jmatprotec.2018.02.012.[7] Lee J W, Baek H M, Hwang S K, et al. The effect of the multi-pass non-circular drawing sequence on mechanical properties and microstructure evolution of low-carbon steel [J]. Materials & Design, 2014, 55: 898-904.DOI: 10.1016/j.matdes.2013.10.068.[8] Pilarczyk J W, van Houtte P, Aernoudt E. Effect of hydrodynamic and roller die drawing on the texture of high carbon steel wires [J]. Materials Science and Engineering: A, 1995, 197(1): 97-101.DOI: 10.1016/0921-5093(94)09756-9.[9] Pilarczyk J W, Dyja H, Golis B, et al. Effect of roller die drawing on structure, texture and other properties of high carbon steel wires [J]. Metals and Materials, 1998, 4(4): 727-731.DOI: 10.1007/bf03026388.[10] Yang F, Jiang J Q, Wang Y, et al. Residual stress in pearlitic steel rods during progressively cold drawing measured by X-ray diffraction [J]. Materials Letters, 2008,62(15): 2219-2221.DOI: 10.1016/j.matlet.2007.11.054.[11] Yang F, Wang Y, Jiang J Q, et al. Stress evolution of cold-drawn pearlitic steel wire subjected to uniaxial tension [J]. Materials Science and Engineering: A, 2008, 487(1/2): 468-472.DOI: 10.1016/j.msea.2007.10.061.[12] 张晓丹, Godfrey A, 刘伟,等. 珠光体钢丝冷拉拔过程中微观组织及铁素体微区取向与织构演变[J]. 金属学报, 2010, 46(2): 141-146.DOI: 10.3724/sp.j.1037.2009.00247.Zhang X D, Godfrey A, Liu W, et al. Evolutions of microstructure and ferritic micro-orientation and texture in a pearlitic steel wire during cold drawing [J]. Acta Metallurgica Sinica, 2010, 46(2): 141-146.DOI: 10.3724/sp.j.1037.2009.00247. (in Chinese)[13] 周立初, 胡显军, 马驰,等. 珠光体层片取向对冷拔珠光体钢丝形变的影响 [J]. 金属学报, 2015, 51(8): 897-903.Zhou L C, Hu X J, Ma C, et al. Effect of pearlitic lamella orientation on deformation of pearlite steel wire during cold drawing [J]. Acta Metallurgica Sinica, 2015, 51(8): 897-903. (in Chinese)[14] Zhao T Z, Zhang G L, Zhang S H, et al. Influence of lamellar direction in pearlitic steel wire on mechanical properties and microstructure evolution [J]. Journal of Iron and Steel Research International, 2016, 23(12): 1290-1296.DOI:10.1016/S1006-706X(16)30190-X. [15] 周玉, 武高辉. 材料分析测试技术 [M]. 哈尔滨:哈尔滨工业大学出版社, 2007: 97-100. Zhou Y, Wu G H. Analysis methods in materials science [M]. Harbin:Harbin Institute of Technology Press, 2007: 97-100. (in Chinese)[16] Fang F, Hu X J, Chen S H, et al. Revealing microstructural and mechanical characteristics of cold-drawn pearlitic steel wires undergoing simulated galvanization treatment [J]. Materials Science and Engineering: A, 2012, 547: 51-54.DOI:10.1016/j.msea.2012.03.075.[17] Fang F, Zhou L C, Hu X J, et al. Microstructure and mechanical properties of cold-drawn pearlitic wires affect by inherited texture [J]. Materials & Design, 2015, 79: 60-67.DOI: 10.1016/j.matdes.2015.04.036.[18] 熊毅, 陈正阁, 厉勇,等. 温压缩变形过程中渗碳体的球化行为 [J]. 材料热处理学报, 2008,29(1): 42-46.Xiong Y, Chen Z G, Li Y, et al. Spheroidization behavior of cementite during warm compression deformation [J]. Transactions of Materials and Heat Treatment, 2008, 29(1): 42-46. (in Chinese)[19] Zhang X D, Godfrey A, Hansen N, et al. Evolution of cementite morphology in pearlitic steel wire during wet wire drawing [J]. Materials Characterization, 2010, 61(1): 65-72.DOI: 10.1016/j.matchar.2009.10.007.[20] 赵天章, 宋鸿武, 张光亮,等. 拉拔过程中珠光体钢丝心部的织构演化规律及其对力学性能的影响 [J]. 金属学报, 2014, 50(6): 667-673.DOI: 10.3724/sp.j.1037.2013.00799.Zhao T Z, Song H W, Zhang G L, et al. The texture evolution at the center of pearlitic steelwire during drawing and its influence on the mechanical properties [J]. Acta Metallurgica Sinica, 2014, 50(6): 667-673.DOI: 10.3724/sp.j.1037.2013.00799. (in Chinese)[21] Embury J D, Fisher R M. The structure and properties of drawn pearlite [J]. Acta Metallurgica, 1966, 14(2): 147-159.DOI: 10.1016/0001-6160(66)90296-3.[22] Elices M. Influence of residual stresses in the performance of cold-drawn pearlitic wires [J]. Journal of Materials Science, 2004, 39(12): 3889-3899.DOI:10.1023/B:JMSC.0000031470.31354.b5.[23] Elices M, Ruiz J, Atienza J M. Influence of residual stresses on hydrogen embrittlement of cold drawn wires [J]. Materials and Structures, 2004, 37(5): 305-310.DOI: 10.1007/BF02481676.[24] Atienza J M, Elices M. Influence of residual stresses in the stress relaxation of cold drawn wires [J]. Materials and Structures, 2004, 37(5): 301-304.DOI: 10.1007/BF02481675.[25] Lambiase F, di Ilio A. Deformation inhomogeneity in roll drawing process [J]. Journal of Manufacturing Processes, 2012, 14(3): 208-215.DOI: 10.1016/j.jmapro.2011.12.005. [26] Asakawa M, Shigeta H, Shimizu A, et al. Experiments on and finite element analyses of the tilting of fine steel wire in roller die drawing [J]. ISIJ International, 2013, 53(10): 1850-1857.DOI: 10.2355/isijinternational.53.1850.。
高碳硬线拉拔脆断原因分析

追 求 高 的 线 材 加 工 性 能 , 取 得 了 不 少 成 果 , 线 材 并 使 的 拉 拔 性 能 得 到 了 很 大 提 高 , 目前 优 硬 线 仍 存 在 但
一
些 问题 , 响 了制 品 厂 的 使 用 ; 外 , 些 制 品厂 影 另 有
常 出 现 杯 锥 状 脆 断 , 口形 态 如 图 1 示 。 断 所
出 现 马 氏体 ; 对 钢 的 热 裂 纹 敏 感 性 有 突 出 的 影 响 , 硫 当 它 大 于 0 0 5 时 , 的 延 性 有 明 显 下 降 ; 会 使 . 2 钢 磷 钢 的 晶 界 脆 性 增 加 , 纹 敏 感 性 增 强 。 2 6 钢 盘 裂 图 为
1 前 言
高 碳 硬 线 盘 条 作 为 金 属 制 品 的 原 料 , 过 深 加 通 工 用 于 制 造 钢 丝 绳 、 应 力 钢 丝 及 钢 绞 线 、 力 用 镀 预 电 锌 铝 包 ) 丝 及 钢 绞 线 、 胎 钢 丝 、 簧 钢 丝 等 , 钢 轮 弹 其
拉 拔 性 能 好 坏 直 接 影 响 着 制 品 厂 的 使 用 和 产 品 的 性
维普资讯
20 0 2年 第 3期
安 徽 冶 金
・
试验研 究 ・
高碳 硬 线拉 拔脆 断原 因分析
于 同仁 刘 开 升 张 步 海
( 鞍 山钢 铁 股 份 有 限公 司 ) 马
摘 要 高 碳 硬 线 盘 条 作 为 金 属 制 品 的原 料 , 深 加 工 过 程 中 容 易 出现 脆 断 现 象 . 原 因 一 是 盘 条 本 身存 在 在 其
拉丝缺陷

拉丝缺陷原因分析在拉丝生产中,由于原料、设备、工艺条件、操作等因素,会造成种种钢丝缺陷,使产品质量不合格。
拉丝中比较常见的缺陷及其原因,有以下几个方面:(一)成品钢丝尺寸不合格1.成品钢丝直径超差(1)新换上的拉丝模,点动开车后测量线径,若超差,则属于模子制造误差或模子“错号”,应更换拉丝膜。
(2)生产过程中成品钢丝直径超出正的允差,主要是因为操作者未做到勤检查所致,若超出负的允差,通常称之为“缩丝”,其主要原因是润滑不良。
这种现象多发生在高速拉拨的情况下,尤其在湿拉中较为常见。
或者是由于润滑剂不能适应高速拉拔,或者是由于涂层不佳不能将润滑剂有效载入模孔或者润滑剂堵塞模孔(往往是由于拉丝模入口锥角度太小或定径带过长引起)造成润滑不良。
部分压缩率过大,也有可能“缩丝”。
有时拉拔条件有所改善,“缩丝”现象消失,造成整盘钢丝两头直径合格中间不合格,检验不易发现,影响钢丝的通条性能。
2.钢丝椭圆度超差,产生原因是:一方面由于拉丝模本身制造误差,这种情况下在开车前检查便可发现;另一方面是由于钢丝拉拔前处理不好(酸洗不净,涂层不良)或者拉丝模材质不好,导致模子磨损不均,钢丝变形不均。
(二)成品钢丝表面缺陷1.表面刮伤,或叫“拉毛”,产生原因是拉丝模加工不良,光洁度差;原料去锈不彻底,或者润滑不良,造成模子开裂,而在钢丝表面形成线条状划痕,使钢丝力学性能尤其是韧性下降,钢丝变脆,甚至断丝。
遇到此种情况必须及时更换模子,改善润滑。
2.钢丝表面有锈皮、锈斑和锈蚀,产生原因是:原料锈蚀严重,拉拔前预处理不好,拉拔后仍有部分氧化铁皮残留在钢丝表面;或者由于钢丝置于潮湿气氛或腐蚀性气氛(如酸雾)中,使钢丝生锈。
3.钢丝表面结疤,如氧化疤、右灰疤。
是由于钢丝表面吸附有未洗净的氧化铁皮或涂层里有坚硬颗粒,在拉拔时被压在钢丝表层所引起;还有一种呈“舌状”、“指甲状”而与钢基体相连的生根结疤,则是由于原料有结疤或翘皮而引起的。
钢丝拉拔中缩径跑号原因分析

使拉 丝模定径 带快速磨 损 、 内径增大 , 主要影 响 因素
包括 以下几个 方面 。
5m 生产 (. 00 ) m钢 丝 时 , 品卷筒 m 18± .3 m 成
速度 为 1 . n s 数 分 钟 后 测 量 , 丝 直 径 已达 5 5r , f 钢
() 1 拉丝 模 硬 质合 金 的硬 度 、 作 锥 面 及定 径 工 带 的粗糙度 均会影 响 模具 的使 用寿命 , 定径 带 的长 度 对拉丝模 具使用 寿命 有 致关 重要 的影 响 : 短 则 过 使 用寿命短 ; 长增 加拉 拔 阻力 和能耗 。为磨 模 工 过 作 人员配备 测量拉 丝 模 内部 结 构 的孔 径仪 , 以便 准
第3 卷 3
Vo . 3 13
第5 期
No 5 .
金
Sel t e
属
Wie r
制
品
20 0 7年 1 月 0
Oco e 2 (7 tb r o)
Pout r d cs
钢 丝 拉 拔 中 缩 径 跑 号 原 因 分 析
崔 影
( 布顿 ( 天津 )钢丝绳有限公司 30 2 ) 0 20
能中的任何一项性能不佳 , 在钢丝拉拔中的润滑载体 作用都会 大幅度 降低。 由于水箱 和直进 式拉 丝机可 以采用 9 % 以上 的总压 缩率 进行 生 产 , 丝表 面积 0 钢
增加较大 , 磷化质量作用尤其 明显 。如果磷化膜厚度 过薄, 经前几道 次拉拔 后遭 到破 坏 , 么在无 磷化 膜 那 的后几道 拉拔 中则钢丝与模 壁间摩 擦力会异 常增大 , 极 易跑号 。磷化 液的配方种类 较多 , 选择符合企业 自 身拉拔质量要求且价格适 中的产品非常重要。 () 5 钢丝磷 化 后 必 须 经 过 烘 干 , 未烘 干 的钢 丝
高碳热镀锌钢丝干式拉拔生产工艺探讨
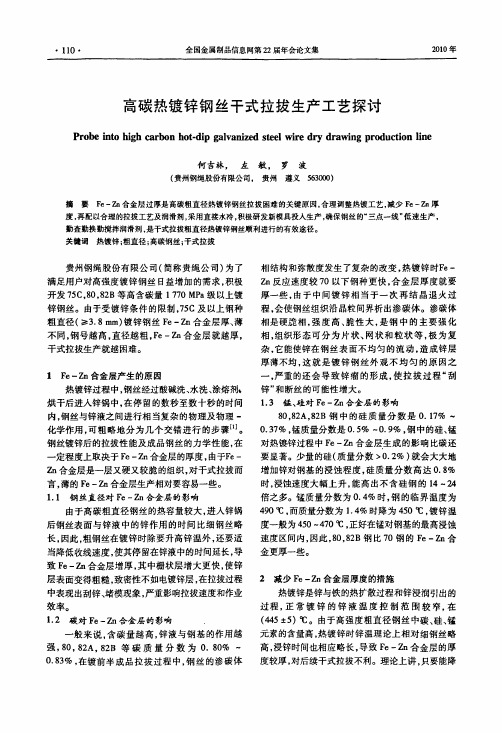
摘要Fe—ZII合金层过厚是高碳粗直径热镀锌钢丝拉拔困难的关键原因,合理调整热镀工艺,减少Fe—Zn厚 度,再配以合理的拉拔工艺及润滑剂,采用直接水冷,积极研发新模具投入生产,确保钢丝的“三点一线”低速生产, 勤查勤换勤搅拌润滑剂,是干式拉拔粗直径热镀锌钢丝顺利进行的有效途径。 关键词热镀锌;粗直径;高碳钢丝;干式拉拔
mm_+1.70
时效处理 设法进行人工时效或自然时效,即将粗直径高
强度热镀锌钢丝放置一段时间后,拉拔性能有明显 的改善。 3热镀锌钢丝在干式拉拔过程中问题 80及以上钢种经热镀锌后,拉拔至成品钢丝。 热镀锌后钢丝的力学性能有所下降,其中抗拉强度
表1
nxlli热镀锌钢丝进行干式和湿式拉拔的
试验。热镀锌钢丝在干式拉拔过程中,由于润滑效 果差,拉拔道次少(8—9道次),使得平均部分压缩 率q。大(约20%),最终导致变形热积累快,局部升 温快,镀锌钢丝力学性能和润滑效果恶化,与湿式拉 拔的对比见表1和表2。
2.3
ห้องสมุดไป่ตู้
下降3%一5%,为了确保钢丝的最终力学性能对强 度的特殊要求和弥补损失的强度,采用干式拉拔是 理想的拉拔方式。但在实际拉拔过程中,干式拉拔 较湿式拉拔要困难许多,主要表现为润滑效果差,模 具更换频繁,变形热积累快,操作难度大,生产效率 低,成品表面易出现锌层横裂等。
3.1
润滑荆的影响 贵绳公司使用的干式拉拔润滑剂有4’,AT2和
由表1、表2可知,若不采取强化水冷方式,拉 拔后钢丝的最终性能是没有保障的。 通过分析得出:干式拉拔冷却能力及润滑效果 差,加工热量的产生与积累快,在钢丝内产生的热应 力影响钢丝的韧性,使钢丝表面产生横向裂纹,降低 了钢丝的扭转值。 3.3模具的影响 干式拉拔过程中若使用光面钢丝的拉丝模进行 生产,钢丝经过4—5道次卷筒拉拔后,基本不能继 续拉拔。若使用镀锌模进行生产,能最终通过成品
细规格高碳钢丝拉拔断裂原因分析

平齐 状 断 口 的 宏 观 形 貌 特 征 是 断 面 平 齐"断 口 处几乎无变形"如 图 8 所 示( 形 成 平 齐 状 断 口 的 主
图 # 笔 尖 状 断 口
要原因包括非金 属 夹 杂 物%粗 大 晶 粒%异 常 组 织 等( 平齐状断口一般为 脆 性 断 裂"微 观 形 貌 具 有 解 理 特 征 "如 图 ! 所 示 (
第 !" 卷 第 # 期 $%#& 年 $ 月
现代冶金
'()*+, '*-.//0+12
3(/4!"5(4# 6*74$%#&
细规格高碳钢丝拉拔断裂原因分析
孙 文#$卫 健$8孙 杰#$朱 维 军#8
!#4国家金属线材制品工程技术研究中心"江苏 江阴$#!!!9# $4江苏法尔胜材料分析测试有限公司"江苏 江阴$#!!!9#84法尔胜集团有限公司"江苏 江阴$#!!8!$
图 9 斜 茬 状 断 口 的 表 面 缺 陷
4 笔 尖 状 断 口 笔 尖 状 断 裂 样 品 的 断 口 形 貌 如 图 " 所 示 断 口
4 平 齐 状 断 口
平齐 状 断 裂 样 品 的 断 口 形 貌 如 图 ? 所 示断 口 基 本 呈 平 齐 状 断 裂 面 的 大 部 分 区 域 为 韧 窝 局 部 可 见二次裂纹而断 面 的 边 缘 存 在 异 常 组 织 和 二 次 裂 纹块状异常 组 织 的 尺 寸 约 为 #%A 当 钢 丝 与 拉 丝模的润滑条件变 差 时摩 擦 热 可 使 钢 丝 表 面 薄 层 在千 分 之 几 秒 内 迅 速 升 温 到 "%% C 或 更 高#$当 钢 丝 离 开 拉 丝 模 与 润 滑 液 接 触 时 温 度 急 剧 下 降 形 成晶粒较大的异常 组 织从 而 导 致 钢 丝 的 实 际 承 载 面积降低因此边缘异常组织是该样品呈平齐状断 裂的主要原因
中高碳钢盘条拉拔断裂原因分析

新疆 钢 铁
总 14 0 期
中高碳 钢 盘条 拉拔 断 裂原 因分析
杨 朝 东 胡 波 王 卫 东
( 宝钢 集 团 八钢 金 属 制 品公 司 ) 摘 要 : 针 对 中高 碳 钢 盘 条在 拉 拔 过程 中断 线频 繁 的 问题 , 从原 材 料 质 量 、 条 预处 理 、 拔 工 艺 、 盘 拉 焊接 工 艺 的 各
表 2 金 相 组 织检 验 结 果
从金相组 织看 , 口处 组织 正常 。 断 () 3 扫描 电镜 断 口分 析 , 裂起 源 于钢 丝表 面 。 断
裂纹 附近有 夹杂 , 夹杂成 分为 : a Mg S 、 、 、 e C 、 、 iS A1F ,
钢丝 时表现更 为 突出 。 由于 脆性 夹杂 的变形 能 力差 , 丝 在拉 拔过 程 钢
2 盘 条预 处 理 情 况
由于 环保 的要 求 , 生产 中采 用 的是 无 酸洗 拉拔 技术 。 盘条 的前期 处理还 存在 一些 问题 : 主要 是盘条 表 面 的氧 化铁 皮 去除 不 干净 , 拉 拔 时会 造成 氧化 在 铁被 压 入 钢丝 基体 产 生 钢丝 表 面缺 陷 , 成润 滑效 造 果 下降 、 耗 大 , 模 易造 成 钢丝 的 “ 脆 ” 传 统 的高碳 蓝 。
表 1 盘 条 的 力学 性能 检 验 数据
八钢金属 制 品公 司生 产 中碳 网 围栏 用镀锌 钢丝 和 高碳 镀锌 钢绞 线 用 热镀 锌 钢丝 , 用的是 八钢 自 采
盘 条 钢 号 抗拉 强 度 , a延 伸 率 , 面 缩 率 , MP
样量 , 个
产 的 中高碳 钢盘 条 。 由于在 生 产过 程 中断线频 次 较
高碳钢丝拉拔过程分层现象研究

· 132 ·
内燃机与配件
HZ20-THA 型焊接转向架研制
张锐曰祝笈
(中车眉山车辆有限公司产品开发部,眉山 620032)
摘要院介绍了出口泰国 HZ20-THA 型焊接转向架的主要技术参数、结构特点以及有关计算和试验情况。 关键词院货车转向架;技术参数;结构特点;试验情况
0 引言 近年来,随着泰国社会经济发展,泰国铁路装备迎来 了更新换代期,新购车辆的速度和轴重都有了更高的要 求。2015 年,泰国某公司与中车眉山车辆有限公司签订了 集装箱平车销售合同。根据合同及技术规范要求,中车眉 山公司设计制造了适用于泰国 1000mm 轨距线路,轴重 20t,最高运行速度 100km/h 的 HZ20-THA 型焊接转向架。 1 技术参数渊见表 1冤
屈服点强度
2058 2064 1955 1991 1988 2028
屈服点扭角
1630 1573 1417 1200 1733 1662
综上,对于四种试验方式中的钢丝扭转次数进行了对 比分析,如图 1 所示,方式一、二中的扭转次数要明显比三 和四的大,这就表明多道次以及小压缩率的拉拔技术对于 钢丝性能的提高有明显的作用。
Internal Combustion Engine & Parts
· 131 ·
高碳钢丝拉拔过程分层现象研究
王思伟
(江阴希格装备科技有限公司,江阴 214400)
摘要院本文首先进行了高弹钢丝拉拔过程试验,并对其在拉拔过程中的分层现象进行了结果分析工作,进而对其出现的分层现象 提出了改进措施。在高碳钢丝拉拔过程试验中,其采用了 84C 铅溶钢丝进行拉拔试验,其制定了四种方案对高碳钢丝进行了拉拔,结 果表明拉丝模棱角以及道次压缩率都对高碳钢丝的分层现象产生作用。
- 1、下载文档前请自行甄别文档内容的完整性,平台不提供额外的编辑、内容补充、找答案等附加服务。
- 2、"仅部分预览"的文档,不可在线预览部分如存在完整性等问题,可反馈申请退款(可完整预览的文档不适用该条件!)。
- 3、如文档侵犯您的权益,请联系客服反馈,我们会尽快为您处理(人工客服工作时间:9:00-18:30)。
中、高碳钢丝的高速拉拔
中碳钢丝制品,大都仅要求中等强度,如线材塑性好,一般可以实现较高的拉拔速度。
一因此,这里主要探讨高碳钢丝的高速拉拔问题。
目前中租规格的高强度和较高强度成品钢丝的拉拔速度,是受到一定限制的。
因为线速偏高会给钢丝带来高热,影响其性能。
因此,要提高高碳钢丝的拉拔速度,除上述拉拔要求之外,关键还在于有效地降低拉拔时的温度。
国内现有的冷却方法大部分是模子与卷筒的直接水冷,此种方法在车速较低时效果尚佳,如果速度较高就不能满足要求了,估计模子温度会超过250°以上。
拉拔温度与设备种类有一定关系。
活套式拉丝机和直线式拉丝机都具有反拉力,能减少对模子的压力,因此能降低温度,提高拉拔速度。
直线式拉丝机还具有对卷筒强制风冷的效果,对降低钢丝温度有一定作用。
如果用大水箱拉拔中粗规格高强度钢丝,不但可以较大幅度地提高车速,而且仍能得到良好的机械性能。
据了解,使用大水箱车,以250米/分的速度拉拔1.8~2.8毫米的65锰钢丝时,钢丝的抗拉强度偏于下限(这是降低硬化的结果),而扭转次数(下限)却提高将近一倍或一倍以上。
这说明低温拉拔与钢丝的扭转性能关系很大。
国外发展的流体动力润滑模盒,由于改善了边界润滑状态,故有效地降低了模子的温度,同时拉拔力下降,扭转次数提高。
这说明采用流体动力润滑方法,能有效地提高拉拔速度。
国外还试制成功一种对出模钢丝进行直接水冷的新型冷却装置。
冷却水由模盒下部的入口道进入,经过模子,然后进入冷却管,最后冷却水由出口排出。
冷却水管用压缩空气密封,钢丝上的水滴同时被压缩空气吹除。
直接水冷与传统冷却方法在冷却效果和对钢丝性能的影响上,对比如下:
表不同冷却方法的比较
┏━━━━━━━━━━━━┳━━━━━━━━━┳━━━━━━━━━━┓
┃比较┃传统的冷却方法┃出模钢丝直接水冷┃
┣━━━━━━━━━━━━╋━━━━━━━━━╋━━━━━━━━━━┫
┃钢丝含碳量(C%) ┃0.63 ┃0.63 ┃
┃钢丝直径(毫米) ┃ 1.8 ┃ 1.8 ┃
┃钢丝出模口温度(℃) ┃210—260 ┃ 135—150 ┃
┃抗拉强度(公斤/毫米2) ┃ 188 ┃ 173 ┃
┃扭转次数┃ 32 ┃42 ┃
┃弯曲次数┃ 7 ┃ 8 ┃
┗━━━━━━━━━━━━┻━━━━━━━━━┻━━━━━━━━━━┛
从表中可以看到,出模钢丝直接水冷后,温度比传统的冷却方法下降38%,抗拉强度仅下降8%,这说明金属硬化速度放慢了,但是扭转次数却提高30%以上。
据有关资料介绍,直接水冷的方法,将拉拔速度由300米/分提高到500米/分时,成品质量虽有所下降,但仍比传统的冷却方法略有提高。
以上表说明,大幅度降低拉拔时钢丝的温度,是提高高碳钢丝拉拔速度的关键。