Chapter 1 切削与磨削过程
磨削加工过程及典型加工工序

磨削加工过程及典型加工工序一、引言磨削加工是一种常用于金属工件加工的方法,它通过利用磨料与工件表面的相对运动,在高速旋转的磨具的作用下,将工件表面的硬度较高、粗糙度较高的层状材料切削去除,从而使工件达到精度更高、光洁度更好的目的。
本文将介绍磨削加工的原理、典型加工工序以及注意事项。
二、磨削加工的原理磨削加工是一种磨削剂与工件表面之间的相对运动产生磨削力的加工方法。
在磨削过程中,磨料与磨具之间的接触是点、线、面三种形式的交替进行,从而形成切削力。
这种切削力的作用下,磨具将工件表面的层状材料切削去除,使得工件表面达到更高的精度和光洁度。
三、典型磨削加工工序1. 平面磨削平面磨削是指对平面工件进行磨削加工的工序。
它是磨削加工中最常见的一种工序,广泛应用于各个领域的加工过程中。
平面磨削的主要步骤包括:确定磨削的位置和方向,选择合适的磨具和磨料,进行粗磨和精磨,最后进行抛光。
平面磨削的参数包括磨削速度、工件进给速度、磨削深度等。
2. 内圆磨削内圆磨削是指对内圆工件进行磨削加工的工序。
它是磨削加工中一种较为复杂的工序,需要使用专门的磨削装置和磨具。
内圆磨削的主要步骤包括:确定磨削位置、选择合适的磨具和磨料,进行粗磨和精磨,最后进行抛光。
内圆磨削的参数包括磨削速度、工件进给速度、磨削深度等。
3. 外圆磨削外圆磨削是指对外圆工件进行磨削加工的工序。
它是磨削加工中一种比较常见的工序,广泛应用于各个领域的加工过程中。
外圆磨削的主要步骤同样包括:确定磨削位置、选择合适的磨具和磨料,进行粗磨和精磨,最后进行抛光。
外圆磨削的参数也包括磨削速度、工件进给速度、磨削深度等。
4. 带状磨削带状磨削是指对宽度较大的工件进行磨削加工的工序。
它是磨削加工中一种较为特殊的工序,需要使用带状磨削装置和特殊的磨具。
带状磨削的主要步骤与其他磨削工序类似,但需要特别注意工艺参数的调整和对磨削带的管理。
四、磨削加工注意事项在进行磨削加工时,需要注意以下几点: 1. 选择合适的磨具和磨料。
第一章切削加工概论
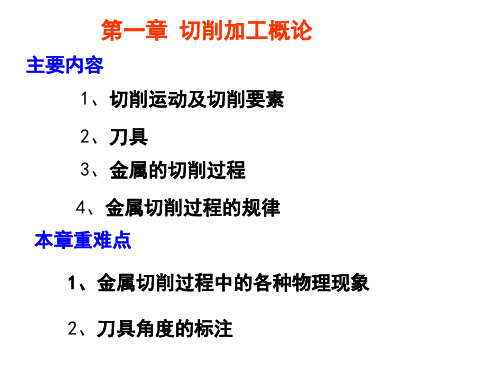
• 对于塑性较大材料,已加工表面易产生加 工硬化时,一般取较大后角。
• 后角的选择考虑因素 : • (1)切削厚度 • 当应切取削大厚 些度hD(和进给量f)较小时,后角αo • 粗荷车作时用,。切为削保厚证度刀h刃D强较度大,,取刀较具小承后受角冲,击通载
常为4 °~7°. • 精车时,为保证加工表面质量,减少后刀面
磨损,应取较大后角,取αo=8o~12o。
• (2)工件材料
- 当主运动为往复直线运动时,则进给量f的单位 是mm/str。
- af是多刃刀具的每齿进给量,单位是mm/Z。
vf f •n af •n•Z mm s
3)背吃刀量:背吃刀量ap为工件上已加工表面和 待加工表面间的垂直距离。
外圆车削时
ap
dw
dm 2
钻孔时
ap
dm 2
dw dm
2.切削层几何参数 n
耐腐蚀、承受冲击和经受高速旋转而不破 裂,主要取决于结合剂的强度。
(4)硬度
是指磨料在外力作用下脱落的难易程度, 它主要取决于结合剂的粘结力。磨料易脱 落,表示砂轮的硬度软,反之则硬。
(5)组织
表示磨料排列的疏密程度,即磨料占磨具 的容积比率。
三、刀具结构
车刀按结构分类,有整体式、焊接式、机夹式和可转位 式四种型式。
4)副偏角(kr’)
副切削刃和假定进给相反方向在基面上的投影。
5)刃倾角(S) 主切削刃与基面之间的夹角。
• 刀具角度正负的规定: • 如图所示:前刀面与基面平行时前角为零。前刀面与切
削平面间夹角小于90度时,前角为正,大于90度时,前 角为负。 • 后刀面与基面间夹角小于90度时,后角为正,大于90度 时,后角为负。 • 刃倾角是前刀面与基面在切削平面中的测量值,其正负 与前角判断类似:切削刃与基面平行时,刃倾角为零; 刀尖相对于车刀的底平面处于最高点时,刃倾角为正; 处于最低点时,刃倾角为负。
《磨削理论》PPT课件

vw dwnw /1000(m / s)
4.2.2 磨削要素
(1)金属材料切除率 a. 每秒金属切除量:
Q 1000vw fr f(a mm3 / s)
dwnw fr f(a mm3 / s)
b. 单位砂轮宽 度
切除率:
ZQ
Q B
1000vw B
fr
fa【mm3 (/ s mm)】
dwnw fr fa【mm3 (/ s mm)】
bvw
(能通量表征的是工件受热影响区域的深度。)
三、磨削温度对工件表面的影响
1. 磨削烧伤:磨削时磨削热引起工件表面温度过高,使加工表 面组织(金相组织)发生变化,从而使加工表面的硬度和塑性 发生变化,在加工表层瞬间发生的氧化变色现象。即工件表层 产生氧化膜的回火颜色。
影响磨削烧伤的因素:
不同的变质层厚度,呈现不同的烧伤颜色。
附录 接触弧长、等效直径的公式的推导
一、接触弧长
二、砂轮等效直径
三、单个磨粒的切削厚度
4.3 磨削过程
4.3.1 砂轮表面形貌图及磨粒的形状特点
一、磨粒的形状特点
磨粒的顶尖角通常为90°~120°, 磨粒以较大的负前角进行切削;磨 粒的切削刃和前刀面极不规则,磨 粒形状、大小各异,一般都有钝圆 半径;切削刃排列不规则,呈随机 分布状态。
4.2 磨削运动和磨削要素
4.2.1 磨削运动
(1) 主运动:砂轮的旋转运动,主运动速度vc——砂轮外圆 的线速度。
vc d0 n0 /1000 (m / s)
(2)径向进给运动
砂轮相对于工件径向的运动。其大小用径向进给量fr表示,
f
是
r
指工
作台每双
(单)行程
切削加工课件
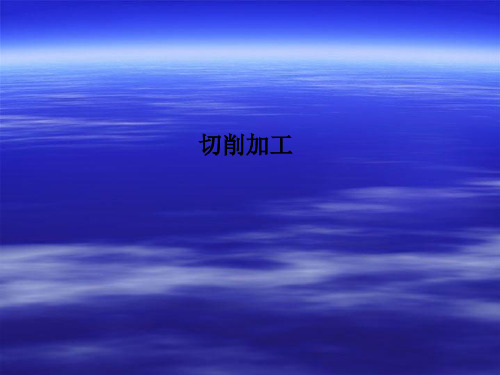
2.常用刀具材料
种
类
碳素工具钢
含碳量较高的优 质碳钢
常用牌号 T8A、T10A、T12A
主要性能
主要应用
淬火后硬度高(达63~65HRC)、价廉, 但耐热性差(200℃以下)
制造小型、手动和低速切 削工具,如手用锯条和锉 刀等
合金工具钢
碳素工具钢中加 入少量Cr、Si、 W、Mn等元素
9SiCr、CrWMn、 CrW5、GCr15
③ 主偏角 Κr――主切削刃和假定进给方向在基面(Pr)上投 影的夹角。主偏角的大小影响切屑断面形状和切削分力的大 小。有时主偏角也根据工件加工形状来定。
④ 副偏角Κ´r――副切削刃和假定进给的相反方向在基面Pr上投
影的夹角。副偏角的主要作用是减少副切削刃与工件已加工表 面的摩擦,减少刀具磨损和防止切削时产生振动。减小副偏角 可减小切削残留面积,降低己加工表面的粗糙度(如图)
1. 刀具切削部分的组成 外圆车刀由三个刀面,两条切削刃和一 个刀尖组成(图1-4)。
(1)前刀面――刀具上切屑流过的表面( )。 A r
(2)后刀面――刀具上与过渡表面相对的是主后刀面(
加工表面相对的是副后刀面( )。A 形成的交线称为主切削刃( ),
)。A 与已
三、切削层参数(如上页图) 1. 切削厚度hD――垂直与切削刃的方向上度量的切削 层截面的尺寸。(mm) 2. 切削宽度bD――沿切削刃方向度量的切削层截面的 尺寸。(mm) 3. 切削面积AD――给定瞬间,切削层在切削层尺寸平面
里的横截面积。( m m) 2
ADfapbDhD
§2 刀具材料及刀具结构
(2)车刀的主要标注角度及选择要点――在车刀设计、制造、刃 磨和测量时,必须确定的角度。
第一章 磨削加工的基本知识

第一章磨削加工的基本知识培训学习目标1.磨削用量包括那几个基本参数?如何计算砂轮圆周速度、工件圆周速度?2.试述切削液的作用、种类及特点。
3.砂轮由哪三要素构成?4.如何选择砂轮硬度?5.如何选择砂轮粒度?6.引起砂轮不平衡的原因是什么?试述平衡砂轮的目的和方法。
一、磨床的基本知识1.磨床工作在制造业中的地位磨削是一种比较精密的金属加工方法,经过磨削的零件有很高的精度和很小的表面粗糙度值。
目前用高精度外圆磨床磨削的外圆表面,其圆度公差可达到0.001mm左右,相当于一个人头发丝粗细的1/70或更小;其表面粗糙度值达到Ra0.025um,表面光滑似镜。
在现代制造业中,磨削技术占有重要的地位。
一个国家的磨削水平,在一定程度上反映了该国的机械制造工艺水平。
随着机械产品质量的不断提高,磨削工艺也不断发展和完善。
2. 普通磨床简介以常用的万能外圆磨床为例,磨床主要由床身、工作台、头架、尾座、砂轮架和内圆磨具等部件组成。
见图1。
磨床还包括液压系统。
(1)床身:磨床的支承。
(2)头架:安装与夹持工件,带动工件旋转,可在水平面内逆时针转90°;(3)内圆磨具:支承磨内孔的砂轮主轴。
(4)砂轮架:支承并传动砂轮主轴旋转,可在水平面±30°范围内转动;(5)尾坐:与头架一起支承工件;(6)滑鞍与横进给机构:通过进给机构带动滑鞍上的砂轮架实现横向进给;(7)横向进给手轮(8)工作台:a.上工作台:上面装有头架与尾坐;b.下工作台:上工作台可绕下工作台在水平面转±10°角度。
3.磨床的型号磨床的种类很多,按GB/T15375-1994磨床的类、组、系划分表,将我国的磨床品种分为三个分类。
一般磨床为第一类,用字母M表示,读作“磨”。
超精加工机床、抛光机床、砂带抛光机为第二类,用2M表示。
轴承套圈、滚球、叶片磨床为第三类,用3M表示。
齿轮磨床和螺纹磨床分别用Y和S表示,读作“牙”和“丝”。
磨削过程及磨削原理
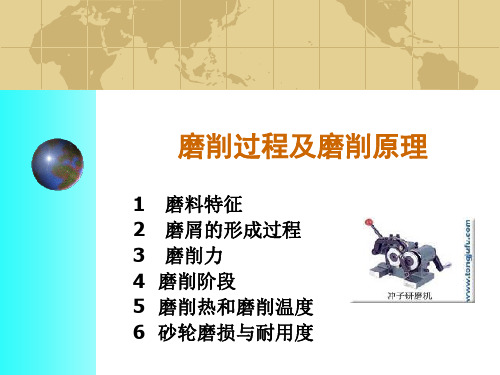
六、砂轮的磨损与耐用度
形态:磨耗磨损(A)、磨粒破碎(B-B) 和脱落磨损(C-C)。 砂轮耐用度:砂轮钝化、变形后加工 质量和效率降低。~用砂轮在两次修 整之间的实际磨削时间度时,工件将发 生颤振,表面粗糙度突然增大,或出 现表面烧伤现象。
由图可知,缩 短初磨阶段和稳定 阶段可提高生产效 率,而保持适当清 磨进给次数和清磨 时间可提高表面质 量。
五 磨削热和磨削温度
1. 磨削温度的基本概念 2. 影响磨削温度的主要因素
砂轮速度V: V ↑→θ↑ 工件速度Vw : Vw ↑→θ↓ 径向进给量fr: fr↑→θ↑ 工件材料: 导热性↓→θ↑ 砂轮硬度与粒度:硬度↓→θ↓ 磨粒大小↑→θ↓
二 磨屑的形成过程
滑擦阶段:磨粒切削厚度非常小,在 工件表面上滑擦而过,工件仅产生弹 性变形。
刻划阶段:工件材料开始产生塑性变 形,磨粒切入金属表面,磨粒的前方 及两侧出现表面隆起现象,在工件表 面刻划成沟纹。磨粒与工件间挤压摩 擦加剧,磨削热显著增加。
切削阶段:随着切削厚度的增加,在 达到临界值时,被磨粒推挤的金属明 显的滑移而形成切屑。
磨削过程及磨削原理
1 磨料特征 2 磨屑的形成过程 3 磨削力 4 磨削阶段 5 磨削热和磨削温度 6 砂轮磨损与耐用度
一 磨料特征
很不规则,大多数呈菱形八面体; 顶尖角大多数为90度~120度,以很大的负前角进行切 削; 磨粒切削刃几乎都存在切削刃钝圆半径; 在砂轮表面分布不均匀,高低也不同。
磨粒常见形状
三 磨削力
➢磨削力的的来源:工件材料产生变形时的抗力和 磨粒与工件间的摩擦力。
➢磨削力的特征: (1) 单位磨削力很大 (2) 径向分力很大---径向力虽不做工,但会使
工件产生水平方向的弯曲,直接影响加工精度。
第一章切削加工基础知识
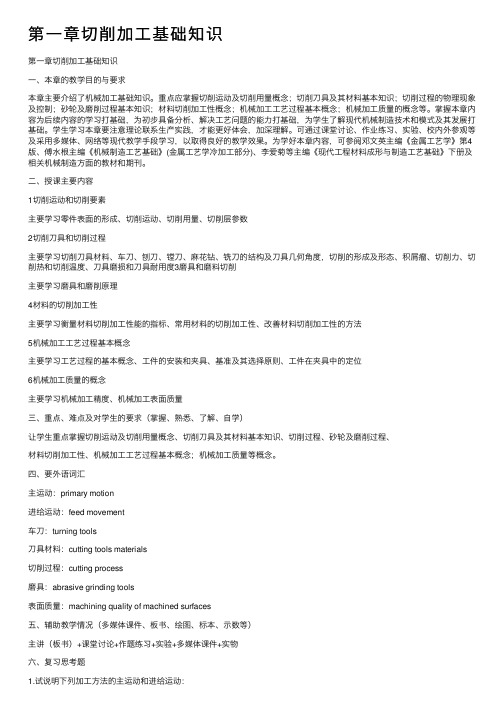
第⼀章切削加⼯基础知识第⼀章切削加⼯基础知识⼀、本章的教学⽬的与要求本章主要介绍了机械加⼯基础知识。
重点应掌握切削运动及切削⽤量概念;切削⼑具及其材料基本知识;切削过程的物理现象及控制;砂轮及磨削过程基本知识;材料切削加⼯性概念;机械加⼯⼯艺过程基本概念;机械加⼯质量的概念等。
掌握本章内容为后续内容的学习打基础,为初步具备分析、解决⼯艺问题的能⼒打基础,为学⽣了解现代机械制造技术和模式及其发展打基础。
学⽣学习本章要注意理论联系⽣产实践,才能更好体会,加深理解。
可通过课堂讨论、作业练习、实验、校内外参观等及采⽤多媒体、⽹络等现代教学⼿段学习,以取得良好的教学效果。
为学好本章内容,可参阅邓⽂英主编《⾦属⼯艺学》第4版、傅⽔根主编《机械制造⼯艺基础》(⾦属⼯艺学冷加⼯部分)、李爱菊等主编《现代⼯程材料成形与制造⼯艺基础》下册及相关机械制造⽅⾯的教材和期刊。
⼆、授课主要内容1切削运动和切削要素主要学习零件表⾯的形成、切削运动、切削⽤量、切削层参数2切削⼑具和切削过程主要学习切削⼑具材料、车⼑、刨⼑、镗⼑、⿇花钻、铣⼑的结构及⼑具⼏何⾓度,切削的形成及形态、积屑瘤、切削⼒、切削热和切削温度、⼑具磨损和⼑具耐⽤度3磨具和磨料切削主要学习磨具和磨削原理4材料的切削加⼯性主要学习衡量材料切削加⼯性能的指标、常⽤材料的切削加⼯性、改善材料切削加⼯性的⽅法5机械加⼯⼯艺过程基本概念主要学习⼯艺过程的基本概念、⼯件的安装和夹具、基准及其选择原则、⼯件在夹具中的定位6机械加⼯质量的概念主要学习机械加⼯精度、机械加⼯表⾯质量三、重点、难点及对学⽣的要求(掌握、熟悉、了解、⾃学)让学⽣重点掌握切削运动及切削⽤量概念、切削⼑具及其材料基本知识、切削过程、砂轮及磨削过程、材料切削加⼯性、机械加⼯⼯艺过程基本概念;机械加⼯质量等概念。
四、要外语词汇主运动:primary motion进给运动:feed movement车⼑:turning tools⼑具材料:cutting tools materials切削过程:cutting process磨具:abrasive grinding tools表⾯质量:machining quality of machined surfaces五、辅助教学情况(多媒体课件、板书、绘图、标本、⽰数等)主讲(板书)+课堂讨论+作题练习+实验+多媒体课件+实物六、复习思考题1.试说明下列加⼯⽅法的主运动和进给运动:a.车端⾯;b.在钻床上钻孔;c.在铣床上铣平⾯;d.在⽜头刨床上刨平⾯;e.在平⾯磨床上磨平⾯。
天津理工大学机械制造基础1.1.1 (1)

③切削层公称横截面积AD
在切削层参数平 面内度量的横截 面积。
AD=hDbD=apf
上述公式中可看出 hD、bD均与主偏角有 关,但切削层公称横截面积AD只与hD、bD 或f、ap有关。
图2-3 车削时的切削层尺寸
直角切削
三、刀具材料
金属切削过程除了要求刀具具有适当的几何 参数外,还要求刀具材料对工件要有良好的切削 性能。
在车削(切断、车螺纹、车丝杠)、镗孔、铣削等加工 中,通常因刀具工作角度的变化,对工件已加工表面质 量或切削性能造成不利影响。
1、横向进给运动对工作前、后角的影响
oe
o
oe
o
arctan v f vc arctan f d 切
2、轴向进给运动对工作前、后角的影响
轴向进给车外圆时,合成切削运动产生的加工轨迹 是阿基米德螺旋线,从而使工作前角γoe增大、工作后 角αoe 减小(图2-10) 。
切屑, 从而形成具有所需几 何特性的已加工表面。
进给运动可由刀具完
成(如车削),也可由工件完 成(如铣削),可以是间歇的 (如刨削), 也可以是连续 的(如车削)。
切削刃上选定 点相对于工件 的进给运动的 瞬时速度。
切削刃上选定 点相对于工件 的瞬时进给方 向。
(3)合成切削运动主运动和进ຫໍສະໝຸດ 运动 合成的运动称为合 成切削运动。
刀具切削性能的优劣,不仅取决于刀具切削 部分的几何参数,还取决于刀具切削部分所选配 的刀具材料。
金属切削过程中的加工质量、加工效率、加 工成本,在很大程度上取决于刀具材料的合理选 择。因此,材料、结构和几何形状是构成刀具切 削性能评估的三要素。
1. 刀具材料应具备的性能
(1)高的硬度
- 1、下载文档前请自行甄别文档内容的完整性,平台不提供额外的编辑、内容补充、找答案等附加服务。
- 2、"仅部分预览"的文档,不可在线预览部分如存在完整性等问题,可反馈申请退款(可完整预览的文档不适用该条件!)。
- 3、如文档侵犯您的权益,请联系客服反馈,我们会尽快为您处理(人工客服工作时间:9:00-18:30)。
30
一、概述
1. 研究金属切削变形的常用方法
金属切削过程是高速进行的微观变形 过程。
1) 侧面方格变形观察法
2) 快速落刀法 3) 其他方法
高速摄影法:动态观察切削过程 扫描电镜显微观察法:观察金属晶粒 内部的微观滑移情况 带显微镜头的工业电视观察法 侧面方格变形观察法 示意图
光弹性、光塑性实验法扫描电镜观察 法
32
二、切削变形
追踪切削层上任一点P,可以观察切削的变形和形成过 程。
变形特征:沿滑移线的 剪切滑移变形以及随之 产生的加工硬化。
始剪切 滑移线
终剪切 滑移线
第Ⅰ变形区的剪切变形
33
三、前刀面与切屑间的摩擦
切削过程中的许多因素,都通 过影响刀-屑之间的摩擦状况来 改变, 从而影响切屑变形。 变形特征:使切屑底层靠近前 刀面处纤维化,切屑流动速度
加工塑性材料(如钢)选较大的前角,脆性材料(如铸铁) 选较小的前角。 刀具材料韧性好(如高速钢),前角可选得大些,反之 (如硬质合金)则前角应选得小一些。
粗加工时,特别是断续切削时,应选用较小的前角;精加 工时应选用较大前角。
硬质合金车刀的前角γ 0在-5°~+20°范围内选,高速 钢刀具的前角应比硬质合金刀具大5°~10°,而陶瓷刀 具的前角一般取-5°~15。 24
3. 主偏角κr和副偏角κ´r
影响:主偏角和副偏角对刀具耐用度影响很大。减小主偏 角和副偏角
刀尖角增大,刀尖强度提高,散热条件改善,刀具耐用 度提高。 降低残留面积高度,减小加工表面的粗糙度。 主偏角和副偏角还会影响各切削分力的大小和比例。 主偏角取值:在工艺系统刚性较好时,主偏角κr宜取较小 值,如κr=30°~70°。车削细长轴时,取κr= 90°~93°, 以减小背向力Fp。 副偏角κr的大小主要根据表面粗糙度的要求选取,一般为 5°~15°,粗加工时取大值,精加工时取小值。
积屑瘤的形成及其对切削过程的影响
积屑瘤高度与切削 速度关系示意图
影响: 1)使实际前角增大 ; 2)增大切入深度; 3)使加工表面粗糙度值增大; 4)影响刀具耐用度。 39
广泛应用 硬质合金的抗弯强度低,冲击韧性
差,不锋利,较难加工,不易做成
形状复杂的整体刀具。
常用的硬质合金有钨钴类(YG类),钨钛钴类(YT类)和
通用硬质合金(YW类)3类。 19
1.1金属切削过程与刀具的基本知识
涂层刀具:耐磨性高的难熔金属化合物
钢)。加工材料的硬度愈高,效果愈好。 人造金刚石:在高温高压下由石墨转化而成 极高的硬度(显微硬度可达HV10000)和耐磨性,摩擦系 数小,切削刃非常锋利。很高的加工表面质量。 陶瓷材料:以氧化铝为主要成分,经压制而成 在1200°C时可保持HRA80的硬度,脆。 热稳定性较差(不得超过700~800℃),与铁元素的化学 亲和力很强,不宜加工钢铁件。加工硬质合金。 立方氮化硼:由六方氮化硼在高温高压下转变而成 硬度热稳定性很高(可达1300—1400°C) 。 最大的优点:在高温(1200—1300°C)时也不易与铁族 金属起反应。 20
耐用度至少可提高1—3倍(刀片),或2—10倍(高速
1.1金属切削过程与刀具的基本知识
CVD金刚石切削刀具
寿命相当于硬质合金刀具的100倍以上
加工特性:
激光焊接金刚 石圆锯片
1)刀刃强度高,能承受较单晶金刚石刀具更高的冲击载荷。 2)磨耗小,耐用度比硬质合金高100倍以上,性能优于PCD刀 具。可以多次修磨,反复使用。 3)用单晶金刚石刀具的研磨方法将刃部精细研磨抛光至 Ra≤0.05um,被加工工件表面可达到镜面光。 4)热导率>5W/cm K 。 5)热稳定性好,最高工作温度800℃。
31
2. 变形区的划分
第Ⅱ变形区: 第Ⅲ变形区: 第Ⅰ变形区: 切屑沿前刀面排出时进一步受到前刀面的挤 已加工表面受到刀刃钝圆部分和后刀面的挤压与 从OA线(称始剪切线)开始发生塑性变形, 压和摩擦,使靠近前刀面处的金属纤维化,纤维 摩擦,产生变形和回弹,造成纤维化与加工硬化。 到OM线(称终剪切线)晶粒的剪切滑移基本完成; 化方向基本上和前刀面平行;
第 1章
切削与磨削过程
1.2 切削变形、切削力与切削热
1.2.1 金属切削变形 1.2.2 切削力 1.2.3 切削热
28
1.2
切削变形、切削力与切削热
一、概述
1.2.1 金属切削变形
二、切削变形
三、切削变形程度 四、前刀面与切屑间的摩擦 五、积屑瘤的形成及其对切削过程的影响 六、影响切屑变形的主要因素
1.1.4 2. 后角αo
刀具角度的选择
后角的主要功用:减小后刀面与工件的摩擦和后刀面的 磨损,其大小对刀具耐用度和加工表面质量都有很大的 影响。
大小取决于:切削厚度(或进给量),也与工件材料,
工艺系统的刚性有关。
车削一般钢和铸铁时,车刀后角常选用4°~6°。
25
1.1.4
刀具角度的选择
18
1.1金属切削过程与刀具的基本知识
硬质合金
用高耐热性和高耐磨性的金属碳化物(碳化钨,碳化钛,碳
化钽,碳化铌等)与金属粘结剂(钴,镍,钼等)在高温下 烧结而成的粉末冶金制品。
硬度:HRA89-93,能耐850-1000º C的高温,良好的耐磨性,
切速可达100-300mБайду номын сангаасmin,可加工包括淬硬钢在内的多种材料。
影响:
切削的难易程度-很大。 ↖前角,使刀刃变得锋利,使
切削更轻快,切屑变形↘,切削力和切削功率↘
↖前角,刀刃和刀尖强度↘ ,散热体积↘ ,影响刀具
寿命。对表面粗糙度,排、断屑等有一定的影响
23
1.1.4 选择前角0
刀具角度的选择
主要取决于:工件材料、刀具材料、加工要求
工件强度、硬度较低时,取较大的前角,反之取较小的前 角;
切削速度对摩擦系数的影响
37
四、积屑瘤的形成及其对切削过程的影响
积屑瘤:在切削速度不高而又能形成连续性切屑的情况下, 加工钢料等塑性材料时,常在前刀面切削处粘着一块剖面 呈三角状的硬块。它的硬度很高(通常是工件材料的2-3 倍),在处于稳定状态时,能够代替刀刃进行切削。 积屑瘤的形成:切削加工时,切屑与前刀面发生强烈摩擦 而形成新鲜表面接触。当接触面具有适当的温度和较高的 压力时就会产生粘结(冷焊)。于是,切屑底层金属与前 刀面冷焊而滞留在前刀面上。连续流动的切屑从粘在刀面 的底层上流过时,在温度、压力适当的情况下,也会被阻 滞在底层上。使粘结层逐层在前一层上积聚,最后长成积 屑瘤。 38
35
影响前刀面摩擦系数的主要因素 工件材料:在相同切削条件下,加工几种不同工件材料,如
铜、10钢、10Cr钢、1Cr18Ni9Ti等,随着工件材料的强度
和硬度的依次增大,摩擦系数μ略有减少。 切削厚度:ac增加时,μ也略为下降,如10钢的ac从0.1mm增 大到0.18mm,μ从0.74降至0.72。因为ac增加后正应力也随之 增大。 刀具前角:在一般切削速度范围内,前角γ0愈大,则μ值愈 大。因为随着γ0增大,正应力减小,故μ增加。 切削速度:当v<30m/min时,切削速度提高,摩擦系数变大。 36
四、刀具的工作角度
横向进给运 动的影响
12
1.1金属切削过程与刀具的基本知识
轴 向 进 给 运 动 的 影 响
13
1.1金属切削过程与刀具的基本知识
安 装 高 度 的 影 响
14
1.1金属切削过程与刀具的基本知识
刀杆中心线偏斜的影响
15
1.1金属切削过程与刀具的基本知识
1.1.3 刀具的材料
2
1.1金属切削过程与刀具的基本知识
1.1.1 金属切削加工的基本概念
一、切削运动与切削用量
图1 外圆车削的切削运动 与加工表面
图2 平面刨削的切削运动 与加工表面
3
1.1金属切削过程与刀具的基本知识
切削速度Vc,进给量f(或进给速度Vf)和背吃刀量ap
4
1.1金属切削过程与刀具的基本知识
减慢,底层金属甚至会滞留在
前刀面上;由于切屑底层纤维 化晶粒被伸长,形成切屑的卷
曲;由摩擦产生的热量使切屑
底层与前刀面处温度升高。
34
前刀面与切屑间的摩擦特性-内摩擦
塑性金属在切削过程中,切屑与前刀面之间压力很大,再加上几百 度的高温,实际上切屑底层与前刀面呈粘结状态。故切屑与前刀面之间 不是一般的外摩擦,而是切屑与前刀面粘结层与其上层金属之间的内摩 擦。前刀面上的平均摩擦系数μ是一个变数。
1.1金属切削过程与刀具的基本知识
常用刀具材料
碳素工具钢; 合金工具钢; 高速钢; 硬质合金; 陶瓷; 金刚石; 立方氮化硼等。
17
1.1金属切削过程与刀具的基本知识
高速钢
含有较多钨、钼、烙、钒等元素的高合金工具钢 较高的硬度(HRC62—67)和耐热性(切削温度可达 550—600º ) 切速比碳素工具钢和合金工具钢高1—3倍(因此而得 名),刀具耐用度高10—40倍,甚至更多 加工范围:有色金属到高温合金 制造工艺简单,能锻造,容易磨出锋利的刀刃 在复杂刀具(钻头、丝锥、成形刀具、拉刀、齿轮刀具 等)的制造中占有重要地位。 分类: 通用型高速钢和高性能高速钢(按用途) 熔炼高速钢和粉末冶金高速钢(按制造工艺)
人造金刚石单晶
21
1.1金属切削过程与刀具的基本知识
1.1.4 刀具角度的选择
刀具各角度之间是相互联系,相互影响的,
孤立地选择某一角度并不能得到所希望的合理值。
1. 前角0选择