金属切削过程及控制
第一章 金属切削过程及其控制(第一节)

轨迹法:利用切削运动中刀尖的运动轨迹形成被加工表面的形状。
轨迹法形成发生线需要一个独立的成形运动。
第一章 金属切削过程及其控制
第一节 金属切削过程的基本知识 发生线的形成方法——轨迹法
轨迹法:利用切削运动中刀尖的运动轨迹形成被加工表面的形状。
刀具切削刃与工件表面之间为点接触,通过刀具与工件之 间的相对运动,由刀具刀尖的运动轨迹来实现表面的成形。 被加工表面的形状精度主要取决于机床切削运动的精度。 刀尖轨迹法是利用非成形刀具,在一定的切削运动下,由刀尖 轨迹获得零件所需表面的方法。
第一章 金属切削过程及其控制
1.2 加工表面和切削用量三要素 一、基本概念
(二)切削层及切削用量三要素——切削层 切削层是指在切削过程中,刀具的切削刃一次走刀所切
除的工件材料层。切削层的截面尺寸参数称为切削层参数。
切削层形状、尺寸直接影响着切削过程的变形、刀具承 受的负荷以及刀具的磨损。
第一章 金属切削过程及其控制
为:简单成形运动和复合成形运动。
简单成形运动:如果一个独立的成形运动,是由单独的旋转运
动或直线运动构成的,则此成形运动称为简单成形运动。
一般以主轴的旋转,刀架或工作台的直线运动的形式出现,
用A表示直线运动,用B表示旋转运动。
第一章 金属切削过程及其控制
第一节 金属切削过程的基本知识 表面成形运动
的,也可以是断续进行的,可以由工件完成,也可以由刀具完成,可
以是简单运动,也可以是复合运动。
第一章 金属切削过程及其控制 (一)切削成形运动与加工表面 按作用来分,切削运动可分为主运动和进给运动。 主运动:提供切削可能性的运 动。(速度最高,动力消耗最 大,有且只有一个) 进给运动:提供继续切削可能 性的运动。(速度低,有一个 或几个)
机械制造技术 切削过程及其控制
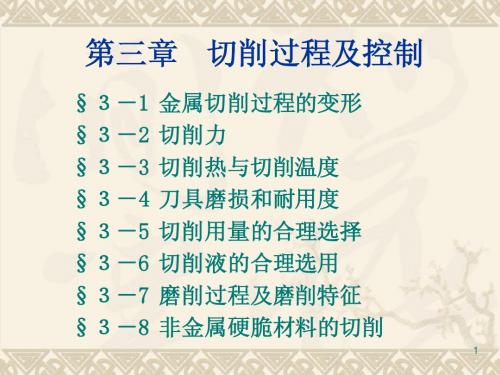
1.对刀具材料的影响
三、切削温度的测定方法
自然热电偶法:利用工件和刀具材料的不同形成 产生温差电动势的条件,工件~刀具热电偶事先 标定,切削时根据测得的电动势的值来查出对应 的温度。 人工热电偶法:组成热电偶的材料事先经过标定, 热电偶的热端焊在测点上,可测得测点的温度。 优点:测量不同材料的切削温度只需事先一次标 定,可得到测点的温度。
56
四、影响切削温度的因素
1、切削用量
切削速度 进给量 切削深度
2、刀具几何参数
前角 主偏角 负倒棱 刀尖圆弧半径
3、工件材料
4、刀具磨损
5、切削液
57
1、切削用量
切削温度与切削用量的关系式为:
c a p
x
f
y
vc
z
三个影响指数 z y x ,说明切削速 度对切削温度的影响最大,背吃刀量对切削 温度的影响最小。
11
2.
剪切角与前刀面摩擦角的关系
+ - 0 =/4 或 = /4 -(- 0 ) (1) 0 对切削有利 (2) 对切削有利
12
直角自由切削 (1)自由切削与非自由切削 只有一条直线切削刃参加 切削工作,这种情况称之为自 由切削。切金属的变形基本上 发生在二维平面内。切削刃为 曲线,或有几条切削刃(包括 副切削刃)都参加了切削,金 属变形更为复杂,且发生在三 维空间内。 (2)直角切削与斜角切削 直角切削是指刀具主切削 刃的刃倾角λ s=0的切削,此时, 主切削刃与切削速度向量成直 角,故又称它为正交切削。斜 角切削是指刀具主切削刃的刃 倾角λ s≠0的切削.
58
2、刀具几何参数 刀尖圆弧半径
刀尖圆弧半径在0~1.5mm范围内变化 基本不影响平均切削温度。因为随着刀尖 圆弧半径的增大,切削区的塑性变形增大, 切削热随之增多;但刀尖圆弧半径的增大 又使刀具的散热条件有所改善,二者综合 作用的结果使平均切削温度基本不变。
4技能训练应知篇之金属切削过程及其基本规律

(3)影响积屑瘤形成的因素 1)工件材料塑性大,加工时产生积屑瘤的可能 性大,加工脆性材料时,一般不产生积屑瘤; 2)切削速度过高或过低都不会产生积屑瘤,中 等速度范围内最易产生,如图4-9所示;切削速 度是通过切削热变化来体现 出对积屑瘤形成的影响的; 3)刀具前角大,能减小切 屑变形和切削力,降低切削 温度,能抑制积屑瘤产生或 减小积屑瘤的高度; 4)切削液可减少切削热和 图4-9 切削速度对 改善摩擦,抑制积屑瘤产生。 积屑瘤的影响
四、切削变形程度的衡量
衡量切削变形常用切削变形系数Λh、剪切应变ε 和剪切角 作为衡量切削变形程度的指标。 1.切应变ε(也称剪应变或相对滑移) 它是反映切削变形中金属滑 移本质的系数,切削层中m'n' 线滑移至m"n" 位置时的瞬时 位移为Δy,实际上Δy的值 很小,滑移量为Δs。滑移量 Δs越大,说明变形越严重。 由右图所示几何关系可得出 以下相对滑移关系表达式:
在整个刀-屑接触区内的正应力 分布情况是, 在刀刃处最大,离切削刃越远,前刀面上的 正应力越小,并逐渐减小到零。在前刀面刀 -屑接触区内,各点的正应力和切应力是不 相等的,所以,前刀面上各点的摩擦状态是 不同的,刀-屑摩擦系数也是变化的。且内 摩擦系数远远大于外摩擦系数的值。 一般切削条件下,来自粘结区的摩擦力约占 切削过程中总摩擦力的85%,可见,内摩擦 在刀-屑接触摩擦中起了主要作用,所以, 研究前刀面摩擦时应以内摩擦为主,这也是 切削摩擦不服从古典滑动摩擦法则的原因。
(2)第二变形区(也写成第II变形区) 是指刀-屑接触区域II。切屑沿前刀面流出 时进一步受到前刀面的挤压和摩擦,切屑 卷曲,使朝向前刀面的切屑底层金属呈纤 维化,流线方向基本上和前刀面平行。 (3)第三变形区(也写成第III变形区) 指刀-工接触区域III。已加工表面受到切削 刃钝圆部分与后刀面的挤压和摩擦,产生 径向和切向弹性与塑性变形,造成工件已 加工表层晶粒纤维化与加工硬化。 三个变形区里的切削变形互相牵连,切削变 形是整体行为,是在极短时间内完成的。
金属切削过程及其基本规律
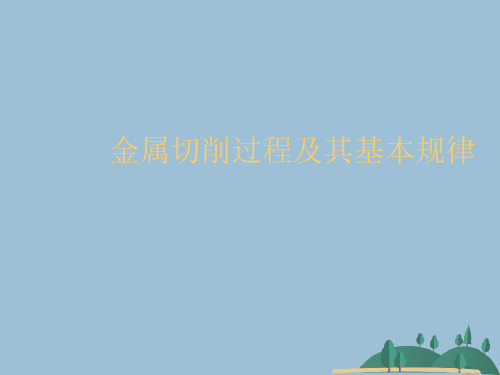
3.快速落刀法
利用一种特殊的刀架,叫做“快速落刀 装置”,在一瞬间使刀具以很快的速度 脱离工件,可获得一个在一定切削条件 下的切屑根部标本。这个标本可供研究 在该切削条件金属切削层的变形情况。
常用结构:手锤敲打,爆炸式落刀装置 (速度更快)
Hale Waihona Puke 4.扫描电镜显微观察法:用扫描电子 显微镜观察切屑的变形情况。
金属切削过程及其基本规律
研究金属切削过程的方法
(1)侧面方格变形观察法 将工件侧面抛光,画出细小的方格,在
低速切削时观察直角自由切削工件材料 的变形过程。
(2)高速摄影法:利用高速摄影机拍摄 被切削试件的侧面,可以得到一个完整 的切屑形成过程的真实图像。常用的高 速摄影机每秒可拍几百幅到一万幅以上 。
采用润滑性能好的切削液,减小摩擦; 前角的变化对塑性材料影响比较大,对脆性材料影响较小。
第二变形区:切屑底层金属晶粒纤维化 (3)内斜式:内斜式卷屑槽形成长紧卷屑的切削用量范围相当窄,因此它的应用范围不如前两种广泛。
(2)高速摄影法:利用高速摄影机拍摄被切削试件的侧面,可以得到一个完整的切屑形成过程的真实图像。 扫描电镜显微观察法:用扫描电子显微镜观察切屑的变形情况。
第一变形区:沿滑移线的剪切变形以及 (2)平行式:平行式卷屑槽的变形不如外斜式的大,切屑大多是碰在工件加工表面上折断。
刀具磨损对切削温度的影响 后刀面磨损分三个区,由刀尖向刀身方向分别为C、B、N,相应的磨损量为VC、VB、VN,其中VC 、VN较大,VB较小,原因是:
随之产生的加工硬化 故仔细研磨刀面、加切削液以减小前刀面的摩擦对改善切削过程是有利的。
前刀面上的平均摩擦系数参见公式
2.积屑瘤
(1)积屑瘤现象:在加工塑性金属材料 时,在某一切削速度范围内,在前刀面 靠近切削刃处会粘结一小块工件材料, 硬度比工件材料高,这个金属硬块称为 积屑瘤。
认识金属切削过程
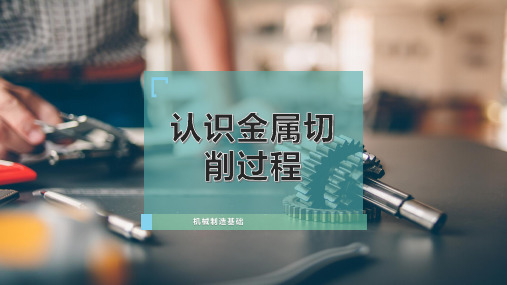
二、切削过程中工件的表面及其形成方法
(1)轨迹法
轨迹法是指利用刀具做一定规律的轨迹运动对工件进行
加工的方法。利用轨迹法加工工件时,刀具切削刃与工件表 面之间为点接触,通过刀具与工件之间的相对运动,由刀具 刀尖的运动轨迹来实现表面成形。
如图所示,刀尖的曲线运动和工件的回转运动相结合,形成了 回转双曲面。
每齿进给量:是指多齿刀具(如铣刀、铰刀等)每转过或移动一个齿相对工件在进给运动方向上的位
移,单位是mm/齿。 进给速度 vf 、进给量 f 和每齿进给量 fc 之间的关系如下:
vf nf nfz z
(2-2)
式中:n ——主运动的转速,r/s或r/min;
z ——刀具的齿数,齿/r。
15
三、切削用量
(a)平面的形成
(b)圆柱面的形成 (c)圆锥面的形成
7
二、切削过程中工件的表面及其形成方法
普通螺纹的螺旋面可以看作是由“八”形线(母线)沿螺旋线(导线)运动而
形成的,如图d所示;
直齿圆柱齿轮的渐开线齿廓表面可以看作是由渐开线(母线)沿直线(导
线)运动而形成的,如图e所示。
形成表面的母线和导线统称为发生线。
移量。已知:工件转速n为220 r/min,刀具每秒沿工件轴向移动1.6 mm,可得
(3)背吃刀量
f 60l 60 1.6 0.44 mm/r。 n 220
由于车外圆的主运动是工件的回转运动,因此根据式(2-3)和已知条件可得
ap
dw
dm 2
75 66 2
4.5 mm。
18
机械制造基础
11
二、切削过程中工件的表面及其形成方法
(3)展成法
展成法是指利用刀具和工件作展成切削运动进行加工的
金属切削过程及控制

图3-12 积屑瘤高度与切削速度关系示意图
4)积屑瘤对起削过程的影响
实际前角增大(图3-13); 增大切削厚度(图3-13) ; 使加工表面粗糙度增大; 对刀具寿命的影响。
一般积屑瘤对切削加工过程的影响是不利 的,在精加工时应尽可能避免积屑瘤的产生, 但在粗加工时,有时可充分利用积屑瘤。
图3-10
切屑和前面摩擦情况示意图
六、积屑瘤的形成及其对切削过程的影响
1)什么是积屑瘤
在中低速切削塑性金属材料时, 常在刀具前面刃口处粘 结一些工件材料, 形成一块硬度很高的楔块,称之为积屑瘤。
2)积屑瘤的形成原因
产生这种现象,是滞流层金属不断堆积的结果。
3)影响积屑瘤的因素
积屑瘤的产生以及它的积聚高度与金属材料的硬化程度 有关,也与刀刃前区的温度和压力状况有关。
三、影响切削力的因素
1. 工件材料
•影响较大的因素主要是工件材料 的强度、硬度和塑性。 •材料的强度、硬度越高,则屈服 强度越高,切削力越大。 •在强度、硬度相近的情况下,材 料的塑性、韧性越大,则刀具前面 上的平均摩擦系数越大,切削力也 就越大。
2. 切削用量
进给量f和背吃刀量ap
进给量f和背吃刀量ap增加,使切 削力Fc增加,但影响程度不同。 进给量f 增大时,切削力有所增 加;而背吃刀量ap增大时,切削 刃上的切削负荷也随之增大,即 切削变形抗力和刀具前面上的摩 擦力均成正比的增加。
第一节 金属切削过程及切屑类型 一、切屑的形成过程
1.切削变形的力学本质
切削金属形成切屑的 过程是一个类似于金属材 料受挤压作用,产生塑性 变形进而产生剪切滑移的 变形过程 (图)。
2.切屑形成过程模型
图3-1
图
金属切削过程与刀具的基本知识

金属切削过程与刀具的基本知识金属切削是一种将金属材料通过切削刀具的作用使其达到需要形状和尺寸的工艺。
金属切削工艺是机械加工的主要方法之一,广泛应用于制造业的各个领域。
本文将详细介绍金属切削过程与刀具的基本知识。
一、金属切削过程启动阶段是切削过程开始时,切削速度较低,金属会发生初步塑性变形。
切削力和切削温度相对较低。
稳定阶段是切削速度逐渐增加,形成连续的切屑,金属在切削面产生变形,切削力和切削温度达到稳定状态。
断裂阶段是切削过程接近结束时,切削力和切削温度急剧增大,金属开始断裂,切削面出现划痕。
切削过程中,切削力对刀具与工件的影响很大。
切削力的大小与切削速度、前进速度、切削深度等因素有关。
合理控制切削力可以延长刀具的使用寿命,提高切削效率。
切削温度是切削过程中的另一个重要参数。
切削温度的高低对刀具寿命和加工精度有很大影响。
高温会使刀具磨损加剧,降低其硬度和强度,导致切削质量下降。
切削速度是切削过程中的重要参数之一,它直接影响到切削效率和切削质量。
切削速度越高,切削效率越高,但也会引起刀具温度升高,容易引发刀具的磨损和断裂。
切削速度的选择要根据工件材料的硬度、刀具材料的性能及切削条件等因素进行合理搭配。
刀具是进行金属切削的工具,它的质量和性能直接影响到切削过程的效果。
下面介绍几个关于刀具的基本知识。
1.刀具的结构:刀具通常由刀柄、刀片和刀片夹持装置组成。
刀柄是刀具的主体部分,可以用来固定和传递力量。
刀片是刀具的工作部分,负责进行金属切削。
夹持装置用来固定刀片在刀柄上。
2.刀具材料:刀具材料通常需要具备高硬度、高强度、耐磨性、耐高温性、抗断裂性等特性。
常见的刀具材料有硬质合金、高速钢、陶瓷、CBN、PCD等。
3.刀片的形状:刀片的形状多样,常见的有直刃刀片、弧形刀片、切槽刀片、钻孔刀片等。
刀片的形状要根据具体的切削任务选择,以提高切削效果。
4.刀具寿命:刀具寿命是指刀具从开始使用到不能继续使用的总时间。
切削过程

图1-35 卷屑槽的卷屑机理
15
图1-36
卷屑槽的截面结构
16
图1-37 卷屑槽方向
图1-38 刃倾角对排屑方向的影响
17
图1-39
C形屑折断形式
18
图1-40 精车时的长螺卷屑
19
图1-41 发条状切屑碰到工件切削表面上折断
20
图1-42 C形切屑撞在工件上折断
21
图1-43 切屑碰在后刀面上折断
①脆性刀具材料破损 刀具破损前,刀具切削部分无明显的塑性变形,称为脆性破 损。硬质合金、陶瓷、立方氮化硼和金刚石刀具材料的硬度 高、脆性大常发生脆性破损,一般表现分为以下几种形式: 崩刃、 碎裂、 剥落、热裂。
②塑性刀具材料破损 由于高温高压的作用,刀具会因切削部分发生塑性流动而迅 速失效,称为塑性破损。形式:卷刃(塑性变形使刀具几何 角度)变化)、烧刃(刀具材料金相组织变化)。
22
1.2.3 切削力
(1)切削力的来源
图1-44 切削力的来源
23
(2)切削合力和分力
切削力分解为三个互相垂直的分力: 切削力Fcc——切削合力在主运动方向上的分力, 或称切向分力。 背向力Fp—— 切削合力在垂直于工作平面上的分力, 或称径向力。 进给力Ff—— 切削合力在进给方向上的分力, 或称轴向力。
6
(4)剪切滑移变形的度量 一般采用剪切角φ 、变形系数∧h和剪应变ε 三个参 数来衡量。
图1-22 金属切削层滑移过程示意图
7
变形系数定义为切屑厚度hch与切削层厚度hD之比, 或用切削层长度lc与切屑长度lch之比。
图1-23 变形系数Λ h的计算参数
8
剪应变也称相对滑移,ε =NP/MK 。
- 1、下载文档前请自行甄别文档内容的完整性,平台不提供额外的编辑、内容补充、找答案等附加服务。
- 2、"仅部分预览"的文档,不可在线预览部分如存在完整性等问题,可反馈申请退款(可完整预览的文档不适用该条件!)。
- 3、如文档侵犯您的权益,请联系客服反馈,我们会尽快为您处理(人工客服工作时间:9:00-18:30)。
? 滑动区: 切屑在脱离前刀面之
前,与前刀面只在一些突出点接触 ,切屑与前刀面之间的摩擦属于外 摩擦。
lfi
lfo
图 切屑与前刀面的摩擦
机械与汽车工程学院
已加工表面的变形
?刀刃钝圆半径rn :
前后刀面过渡圆弧半径。
?后刀面磨损带VB :
后刀面实际后角为零的棱带。
?弹性恢复区CD:
已加工面受到后刀面挤压 与摩擦产生塑性变形,是 造成已加工面加工硬化和 残余应力的主要原因。
Ⅲ
三个变形区
机械与汽车工程学院
切屑与前刀面的摩擦变形
?特点
在高温高压作用下,切屑底层与前刀面发生粘结,切屑 与前刀面之间既有外摩擦,也有内摩擦。
?两个摩擦区
? 粘结区: 高温高压使切屑底层
软化,粘嵌在前刀面高低不平的凹
坑中,形成长度为 lfi的粘接区。切
屑的粘接层与上层金属之间产生相 对滑移,其间的摩擦属于内摩擦。
?0
?
?
4
?
?
?
4
?
?
?
?0
前角越大,摩擦系数越小,切削变形越小。
切削材料的强度、硬度越高,进给量越大,切削厚度越大,摩擦系数减 小,变形减小
机械与汽车工程学院
影响切屑变形的主要因素:
1、工件材料:强度、硬度越大,切屑变形越小; 2、刀具前角:前角越大,切削刃越锋利,剪切角越大,切屑变 形越小; 3、切削速度:通过积屑瘤和切削温度使剪切角变化而影响切屑 变形的波动;
?使得积屑瘤增大的切削速度范围,随着 vc 实际前角 变形 ?使得积屑瘤减少的切削速度范围,随着 vc 实际前角 变形 ?在无积屑瘤的切削速度范围,随着 vc 变形
4、切削厚度:切削厚度增加,摩擦系数减少,剪切角增大,变 形系数减少。在无积屑瘤的情况下,进给量越大,变形越小。
机械与汽车工程学院
教案十
机械与汽车工程学院
3.1 切削过程与切屑类型
变形区的划分
? 第Ⅰ变形区:即剪切滑移区金属剪
切滑移,成为切屑。
始滑面OA与终滑面OM 之间的区域 ,塑性变形主要集中于此区域。
Ⅰ
三个变形区
机械与汽车工程学院
3.1 切削过程与切屑类型
变形区的划分
? 第Ⅱ变形区:纤维化区。
切屑沿前刀面流动,受挤压与摩擦,切屑底
? 偏挤压:金属材料一部分受挤压时,OB线以 下金属由于母体阻碍,不能沿 AB线滑移,而只 能沿OM线滑移。
B
O
a )正挤压
45° M A F
BO
b)偏挤压
? 切削: 与偏挤压类似。 弹性变形 →剪应力
M
增大,达屈服点→ 塑性变形,沿OM线滑移→剪
O
应力与滑移量继续增大,达 断裂强度→切屑与 F
母体分离。
hD ΔhD
机械与汽车工程学院
教案九
3.1 切削过程与切屑类型
晶粒滑移示意图
机械与汽车工程学院
教案九
3.1 切削过程与切屑类型
变形系数
切削层经塑性变形后,厚度增加,长度缩小。 假设:宽度不变,体积不变。
◆ 厚度变形系数
? ha
?
hch hD
?
OM ?sin(90? ? ? ? ? 0 ) OM ?sin ?
机械与汽车工程学院
教案九
3.1 切削过程与切屑类型
金属切削过程中,刀具与工件相互作用,产生 切 削变形、形成切屑、产生切削力 、切削热与切削温度 、 刀具磨损 等现象。为了保证产品加工质量、减少能耗、 提高生产率、必须合理使用与设计刀具、夹具和机床、 选择最合理的切削用量,必须研究切削过程,分析金 属切削变形及其规律。
3.1 切削过程与切屑类型
第3章 金属切削过程与控制
3.1 切削过程和切屑类型 3.2 切削力 3.3 切削热、切削温度和切削液 3.4 刀具的磨损和刀具耐用度 3.6 切削用量的合理选择 教学目的:掌握切削的三个变形区;了解切屑的基本类型; 掌握切削力的组成及计算方法;掌握切削热的产生以及对刀 具寿命的影响。 教学重点:1.金属切削过程中所产生的物理现象及其 内在规律及应用;2.刀具耐用度和刀具总寿命;3.合理 选择切削用量的原则和方法;
部晶粒纤维化,其方向基本与前刀面平行。
Байду номын сангаас
Ⅱ
造成前刀面的磨损和积屑瘤的形成。
三个变形区
机械与汽车工程学院
3.1 切削过程与切屑类型
变形区的划分
? 第Ⅲ变形区:纤维化与加工硬化区
工件基体留下的表层(已加工面)经 过刀具钝圆切削刃和后刀面挤压摩擦 ,产生塑性变形,刀具前移时,工件 表面回弹。
造成已加工面塑性变形、晶粒纤维化 、加工硬化和残余应力。
机械与汽车工程学院
3.1 切削过程与切屑类型
切削模型
切削方式:直角自由切削方式
特点:
?一条切削刃参与切削 过程 ?切削刃与切削速度垂 直 ?切削刃长度超过切削 层宽度
机械与汽车工程学院
教案九
3.1 切削过程与切屑类型
挤压与切削
45° M A F
? 正挤压: 金属材料受挤压时,最大剪应力 方向与作用力方向约成45°。
c)切削
金属挤压与切削比较
机械与汽车工程学院
教案九
3.1 切削过程与切屑类型
一、切屑成形过程及切削变形区的划分
切屑
金
M
属
终滑移线
切 削A
变
形
Φ 剪切角
刀具
过
程 始滑移线:τ=τs
O
切屑根部金相照片(直角自由切削)
机械与汽车工程学院
切屑的形成过程
1. 刀具挤压工件,产生弹 性变形:切削层的金属 受到刀具前刀面的推挤 后产生弹性变形;
? ε主要反映第Ⅰ变形区 的变形, Λh还包含了第 Ⅱ变形区的影响。
机械与汽车工程学院
?剪切角
对于同一材料,用相同的刀具,切削同样大小的切削层 ,当切削速度较高时,剪切角越大,剪切面积越小,即 变形程度越小。
根据材料力学平面应力
状态理论,主应力方向
与最大剪应力方向的夹
角为45o,可以推出:
?
?
?
?
?
cos(? ? ? 0 ) sin ?
◆ 长度变形系数
?
hl
?
lc l ch
由截面积相等可推出两变形系数相等
Lch Lc
切屑与切削层尺寸
剪切角越大,切削变形越小。
机械与汽车工程学院
?相对滑移系数
? ? ?S ?
cos ? 0
? y sin ? cos( ? ? ? 0 )
? 当γ0 = 0~30°,Λh ≥1.5时, Λh与ε相近
2. 塑形变形:随着切应力, 切应变逐渐增大,达到 其屈服强度时,产生塑 性变形而滑移;
3. 挤裂:刀具继续切入, 材料内部的应力、应变 继续增大,当切应力达 到其断裂强度时,金属 材料被挤断;
4. 切离:切屑沿刀具前刀 面流出。
机械与汽车工程学院
教案九
3.1 切削过程与切屑类型
金属切削过程中的滑移线和流线示意图