金属切削的变形过程
金属切削与刀具3个变形区

第二变形区主要对刀具产生(粘结)摩 擦阻力以及造成前刀面磨损;
第三变形区主要对工件已加工表面质量 产生重大影响。
编辑ห้องสมุดไป่ตู้pt
9
二、变形程度的表示方法
1. 剪切角Φ :剪切面与切削速度方向之间的夹角。
2. 相对滑移ε:滑移距离Δs与单元厚度Δy之比。
ε=Δs/ Δy =NP/MK =(NK+KP)/MK =ctan Φ+ tan(Φ -γ0)
14
积屑瘤的利弊
积屑瘤对切削加工的影响:
H ac ac
编辑ppt
结积瘤屑瘤屑
15
消除积屑瘤的措施
• 采用高速切削或低速切削,避免中低速切削; • 增大刀具前角,降低切削力; • 采用切削液。
编辑ppt
16
刀-工接触区的变形与加工质量
刀刃钝圆半径 rn 后刀面磨损带VB 弹性恢复区CD
变形特征:
切塑性金属时前刀面上应力 分布情况→刀-屑接触区可分两部分: 粘接区lf1: 剪切滑移,内摩擦 滑动区lf2: 滑动摩擦,外摩擦 一般内摩擦力约占总摩擦力的85%
编辑ppt
12
积屑瘤的生成机理
在中低速切削塑性金属材料时, 常在刀具前面刃口处粘结一 些工件材料, 形成一块硬度很高的楔块,称之为积屑瘤。
编辑ppt
13
积屑瘤的利弊
积屑瘤粘结在前刀面上,减少了刀具的磨损; 积屑瘤使刀具的实际工作前角增大,有利于减小
切削力; 积屑瘤伸出刀刃之外,使切削厚度增加,降低了
工件的加工精度; 积屑瘤使工件已加工表面变得较为粗糙。
由此可见:积屑瘤对粗加工有利,生产中应加 以利用;而对精加工不利,应以避免。
编辑ppt
宽度为0.02~0.2mm,
4技能训练应知篇之金属切削过程及其基本规律

(3)影响积屑瘤形成的因素 1)工件材料塑性大,加工时产生积屑瘤的可能 性大,加工脆性材料时,一般不产生积屑瘤; 2)切削速度过高或过低都不会产生积屑瘤,中 等速度范围内最易产生,如图4-9所示;切削速 度是通过切削热变化来体现 出对积屑瘤形成的影响的; 3)刀具前角大,能减小切 屑变形和切削力,降低切削 温度,能抑制积屑瘤产生或 减小积屑瘤的高度; 4)切削液可减少切削热和 图4-9 切削速度对 改善摩擦,抑制积屑瘤产生。 积屑瘤的影响
四、切削变形程度的衡量
衡量切削变形常用切削变形系数Λh、剪切应变ε 和剪切角 作为衡量切削变形程度的指标。 1.切应变ε(也称剪应变或相对滑移) 它是反映切削变形中金属滑 移本质的系数,切削层中m'n' 线滑移至m"n" 位置时的瞬时 位移为Δy,实际上Δy的值 很小,滑移量为Δs。滑移量 Δs越大,说明变形越严重。 由右图所示几何关系可得出 以下相对滑移关系表达式:
在整个刀-屑接触区内的正应力 分布情况是, 在刀刃处最大,离切削刃越远,前刀面上的 正应力越小,并逐渐减小到零。在前刀面刀 -屑接触区内,各点的正应力和切应力是不 相等的,所以,前刀面上各点的摩擦状态是 不同的,刀-屑摩擦系数也是变化的。且内 摩擦系数远远大于外摩擦系数的值。 一般切削条件下,来自粘结区的摩擦力约占 切削过程中总摩擦力的85%,可见,内摩擦 在刀-屑接触摩擦中起了主要作用,所以, 研究前刀面摩擦时应以内摩擦为主,这也是 切削摩擦不服从古典滑动摩擦法则的原因。
(2)第二变形区(也写成第II变形区) 是指刀-屑接触区域II。切屑沿前刀面流出 时进一步受到前刀面的挤压和摩擦,切屑 卷曲,使朝向前刀面的切屑底层金属呈纤 维化,流线方向基本上和前刀面平行。 (3)第三变形区(也写成第III变形区) 指刀-工接触区域III。已加工表面受到切削 刃钝圆部分与后刀面的挤压和摩擦,产生 径向和切向弹性与塑性变形,造成工件已 加工表层晶粒纤维化与加工硬化。 三个变形区里的切削变形互相牵连,切削变 形是整体行为,是在极短时间内完成的。
第二章第1节-金属切削过程及切屑类型分析

lfi
lfo
切屑与前刀面的摩擦
第一节 金属切削过程及切屑类型
积屑瘤
在切削速度不高而又能形成连续切屑的情况下,加工一般钢
料或其它塑性材料时,常常在前刀面处粘着一块剖面呈三角
状的硬块,称为积屑瘤。
它的硬度很高,通常是
工件材料的2—3倍,在
切屑
处于比较稳定的状态时,
能够代替刀刃进行切削。
积屑瘤
刀具
积屑瘤
切屑的种类
名称
带状切屑
切屑类型及形成条件
挤裂切屑
单元切屑
崩碎切屑
简图
形态 变形
形成 条件
影响
带状,底面光滑 ,背面呈毛茸状
剪切滑移尚未达 到断裂程度
加工塑性材料, 切削速度较高, 进给量较小, 刀具前角较大
切削过程平稳, 表面粗糙度小, 妨碍切削工作, 应设法断屑
节状,底面光滑有裂 纹,背面呈锯齿状
变形程度表示方法
变形系数
切削层经塑性变形后,厚度增加,长度缩小,宽度基本 不变。可用其表示切削层的变形程度。
◆ 厚度变形系数
h
hch hD
◆ 长度变形系数
L
LD Lch
Lch LD
切屑与切削层尺寸
第一节 金属切削过程及切屑类型
根据体积不变原理,则
h
lc lch
hch hDOMຫໍສະໝຸດ sin(90 OM sin
第二章 金属切削基本理论及应用
第一节 金属切削过程及切屑类型
金属切削过程是指在刀具和切削力的作用下形成切屑的过 程,在这一过程中,始终存在着刀具切削工件和工件材料抵抗切 削的矛盾,产生许多物理现象,如切削力、切削热、积屑瘤、刀 具磨损和加工硬化等。
机械制造工程原理第二章
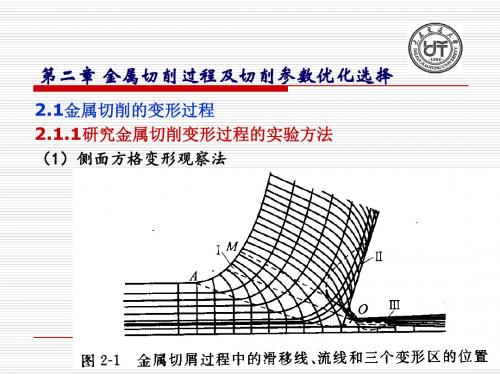
vc
Cv T ma p p f
m m n
kv
2.7 刀具的失效和切削用量的优化选择
2.7.5 切削用量的优化选择
(4)切削速度的选定
2.7 刀具的失效和切削用量的优化选择
2.7.5 切削用量的优化选择
(4)切削速度的选定
2.7 刀具的失效和切削用量的优化选择
2.7.6 刀具合理使用寿命的选择
2.5 切削力
2.5.3切削力的理论公式
Fc
s hDbD cos( o ) sin cos( o )
Fc C Fc a p Fc f Fp C F p a p p f
xF
x
y Fc y Fp yFf
2.5.4 切削力的经验公式(指数形式)F f
CFf a p f f
xF
2.5 切削力
2.5.4 切削力的经验公式(指数形式)
2.5 切削力
2.5.4 切削力的经验公式(单位切削力)
p CFc f 0.16
2.5 切削力
2.5.5 影响切削力的因素
(1) 工件材料的影响(强度、硬度、塑性) (2)切削用量的影响
1)切深和进给量 2)切削速度
2.5 切削力
tw tm tc tot (1)保证加工生产率最高的刀具使用寿命 t t C t m M tct m M m Ct tot M (2)保证加工成本最低的刀具使用寿命
T T
工序成本 切削成本 换刀成本刃磨 刀具消耗费用 辅助时间消耗费用
(3)保证加工利润率最大的刀具使用寿命 Pr
2.1.5剪切角 (1)作用在切屑上的力 (2)剪切角的计算
2.2 切屑的种类及卷屑、断屑机理
切削过程

图1-35 卷屑槽的卷屑机理
15
图1-36
卷屑槽的截面结构
16
图1-37 卷屑槽方向
图1-38 刃倾角对排屑方向的影响
17
图1-39
C形屑折断形式
18
图1-40 精车时的长螺卷屑
19
图1-41 发条状切屑碰到工件切削表面上折断
20
图1-42 C形切屑撞在工件上折断
21
图1-43 切屑碰在后刀面上折断
①脆性刀具材料破损 刀具破损前,刀具切削部分无明显的塑性变形,称为脆性破 损。硬质合金、陶瓷、立方氮化硼和金刚石刀具材料的硬度 高、脆性大常发生脆性破损,一般表现分为以下几种形式: 崩刃、 碎裂、 剥落、热裂。
②塑性刀具材料破损 由于高温高压的作用,刀具会因切削部分发生塑性流动而迅 速失效,称为塑性破损。形式:卷刃(塑性变形使刀具几何 角度)变化)、烧刃(刀具材料金相组织变化)。
22
1.2.3 切削力
(1)切削力的来源
图1-44 切削力的来源
23
(2)切削合力和分力
切削力分解为三个互相垂直的分力: 切削力Fcc——切削合力在主运动方向上的分力, 或称切向分力。 背向力Fp—— 切削合力在垂直于工作平面上的分力, 或称径向力。 进给力Ff—— 切削合力在进给方向上的分力, 或称轴向力。
6
(4)剪切滑移变形的度量 一般采用剪切角φ 、变形系数∧h和剪应变ε 三个参 数来衡量。
图1-22 金属切削层滑移过程示意图
7
变形系数定义为切屑厚度hch与切削层厚度hD之比, 或用切削层长度lc与切屑长度lch之比。
图1-23 变形系数Λ h的计算参数
8
剪应变也称相对滑移,ε =NP/MK 。
第2章 金属切削过程
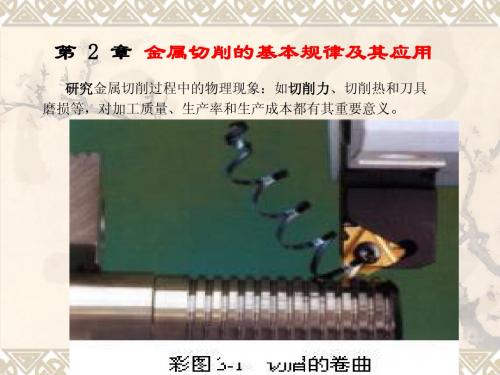
⑶主偏角 主偏角κ r 对主切削力影响不大,对吃刀抗力和进给抗 力影响显著( κr ↑—— Fp↓,Ff↑)
切削力/ N
2200
1800
1400 1000
κr - Fc
κr – Ff κr – Fp
FC—— 切削力(Fz) Ff—— 进给力(Fx) FP—— 背向力(Fy)
600 200 30 45 60
进给力Fx (Ff)
也称轴向分力,用Fx表示—总切削力在进给方 向的分力,是设计机床进给机构不可缺少的参数。 背向力 Fy(Fp) 也称径向分力,用Fy表示 —总切削力在垂直于
工作平面方向的分力,是进行加工精度分析、计算
系统刚度,分析工艺系统振动所必须的参数。
三个分力FC、Ff、FP与合力F 合力F =
2、切削温度的分布
★ 切削塑性材料 :
前刀面靠近刀尖处温度最高。
★ 切削脆性材料: 后刀面靠近刀尖处温度最高
750 ℃
刀 具
2.3.3 影响切削温度的主要因素
1.切削用量对刀具温度的影响
切削温度与切削用量的关系式为:
θ = Cθ VcZθ fyθ apxθ 三个影响指数 zθ >yθ >xθ ,说明切削速度对切削 温度的影响最大,背吃刀量对切削温度的影响最小。
C区是刀尖区,由于散热差,强度低,磨损 严重,磨损带最大宽度用VC表示 B区处于磨损带中间,磨损均匀,最大磨损 量VBmax;
3.边界磨损
N区处于切削刃与待加工表面的相交处,磨 损严重,磨损量以VN表示,此区域的 磨损也叫边界磨损
2.4.2 刀具磨损的主要原因
1. 硬质点磨损
工件材料中含有硬质点杂质,在加工过程中会将刀具表面划伤, 造成机械磨损。低速刀具磨损的主要原因是硬质点磨损。
第3章金属切削的变形过程

R2 R1
ac =
max
l
f
45° M
45° 45° 45°
4
A P
B 1
3 4' 2 3'
c
= 2' s
O
位置 应力状态 流动方向
区域
P < s 切削速度v
切削合力Fr与剪切力Fs之夹角为 (+-0),由材力知
(-0) 为切削合力Fr 与切削速度方向的夹角,称作用角, 以表示。
• 可得如下结论: • 前角 o 增大时, 增大,变形减小。故在保证刀刃
强度条件下增大前角可以改善切削过程(降低切削 力、温度、提高表面质量等); • 摩擦角 增大时, 减小,变形增大。故提高刀具 刃磨质量、使用切削液可减小前刀面上的摩擦,对 切削过程有利。
第三节 前刀面的挤压与磨擦及其对切屑变形的影响
根据前述,切屑沿前刀面流出时受到挤压和摩擦,靠近 前刀面的切屑底层进一步变成第二变形区。 特征: ➢切屑底层晶粒纤维化,流速减慢甚至会停滞在前刀面上 ➢切屑发生弯曲; ➢刀—屑接触区温度升高; ➢第二变形区的挤压和摩擦影响切屑的流出,从而影响第一 变形区金属的变形,影响剪切角的大小。
• 从前面第一和第二变形区的分析可知,变形和摩擦是 影响切削过程的关键。影响切屑变形的主要因素可从 以下四方面分析:工件材料、刀具参数、切削速度和 切削厚度
1、工件材料方面
• 工件材料强度愈高,切屑变形愈小。 • 原因:工件材料强度愈高, 减小,增大,变形系数减小。
工件材料强度对变形系数的影响
2、刀具方面
金属切削过程的基本理论和规律
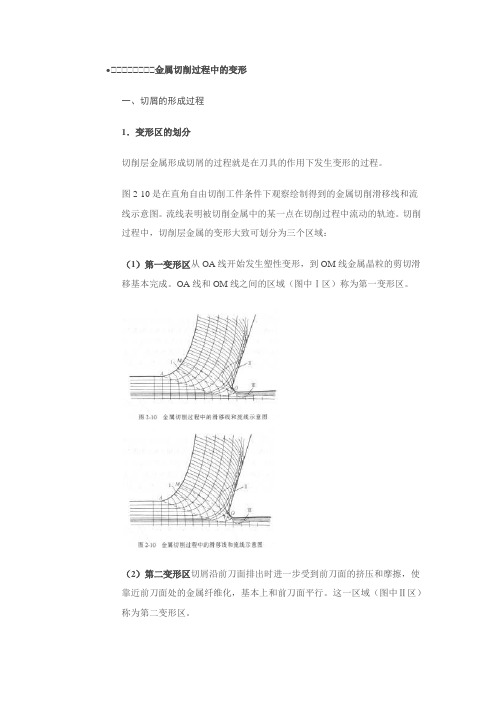
• 金属切削过程中的变形一、切屑的形成过程1.变形区的划分切削层金属形成切屑的过程就是在刀具的作用下发生变形的过程。
图2-10是在直角自由切削工件条件下观察绘制得到的金属切削滑移线和流线示意图。
流线表明被切削金属中的某一点在切削过程中流动的轨迹。
切削过程中,切削层金属的变形大致可划分为三个区域:(1)第一变形区从OA线开始发生塑性变形,到OM线金属晶粒的剪切滑移基本完成。
OA线和OM线之间的区域(图中Ⅰ区)称为第一变形区。
(2)第二变形区切屑沿前刀面排出时进一步受到前刀面的挤压和摩擦,使靠近前刀面处的金属纤维化,基本上和前刀面平行。
这一区域(图中Ⅱ区)称为第二变形区。
(3)第三变形区已加工表面受到切削刃钝圆部分和后刀面的挤压和摩擦,造成表层金属纤维化与加工硬化。
这一区(图中Ⅲ区)称为第三变形区。
在第一变形区内,变形的主要特征就是沿滑移线的剪切变形,以与随之产生的加工硬化。
OA称作始滑移线,OM称作终滑移线。
当金属沿滑移线发生剪切变形时,晶粒会伸长。
晶粒伸长的方向与滑移方向(即剪切面方向)是不重合的,它们成一夹角ψ。
在一般切削速度X围内,第一变形区的宽度仅为0.02-0.2mm,所以可以用一剪切面来表示(图2-12)。
剪切面与切削速度方向的夹角称作剪切角,以φ表示。
2.切屑的受力分析在直角自由切削的情况下,作用在切屑上的力有:前刀面上的法向力Fn和摩擦力Ff;剪切面上的正压力Fns和剪切力Fs;这两对力的合力互相平衡,如图2-14所示。
如用测力仪直接测得作用在刀具上的切削分力F c和F p,在忽略被切材料对刀具后刀面作用力的条件下,即可求得前刀面对切屑作用的摩擦角β,进而可近似求得前刀面与切屑间的摩擦系数μ。
二、切削变形程度切削变形程度有三种不同的表示方法,分述如下。
1.变形系数在切削过程中,刀具切下的切屑厚度h ch通常都大于工件切削层厚度h D,而切屑长度l ch却小于切削层长度l c。
切屑厚度h ch与切削层厚度h D之比称为厚度变形系数;而切削层长度与切屑长度之比称为长度变形系数。
- 1、下载文档前请自行甄别文档内容的完整性,平台不提供额外的编辑、内容补充、找答案等附加服务。
- 2、"仅部分预览"的文档,不可在线预览部分如存在完整性等问题,可反馈申请退款(可完整预览的文档不适用该条件!)。
- 3、如文档侵犯您的权益,请联系客服反馈,我们会尽快为您处理(人工客服工作时间:9:00-18:30)。
BO
b)偏挤压
M O
F
c)切削
金属挤压与切削比较
§ 3.2 金属切削层的变形
三个变形区分析
第Ⅰ变形区:即剪切变形区 ,金属剪切滑移,成为切屑。 金属切削过程的塑性变形主要 集中于此区域。
Ⅱ Ⅰ
Ⅲ
第Ⅱ变形区:靠近前刀面处 ,切屑排出时受前刀面挤压与
切削部位三个变形区
摩擦。此变形区的变形是造成前刀面磨损和产生积屑瘤的
§3.3 前刀面的挤压与摩擦及其 对切削变形的影响
剪切角与前刀面摩擦角 的关系
根据材料力学结论:主应力方向与最大剪应力方
向的夹角为 4 。
o 4
Lee and Shaffer公式:
4
(
o)
4
由Lee and Shaffer公式知:
o↑→ ↑→切削变形↓——应尽量增大 o
积屑瘤高度 h(μm) 变形系数
第三章 金属切削的变形过程
主要内容
研究切削变形的意义和方法 切削层的变形 前刀面的挤压和摩擦 积屑瘤 切屑变形规律 切屑的类型、卷曲和折断
§ 3.1 研究金属切削变形过程的 意义和方法
研究金属切削变形过程的意义
认识和掌握金属切削的规律,用以提高切削效 率、降低成本、保证质量。 19世纪以来,大批学者从不同方面进行研究, 科学地揭示和解释了金属切削过程的种种现象和 规律。 各行业对机械产品的需求促使人们不断地探索 和研究新问题。
由摩擦而产生的热量使接触区域温度升高
本变形区的变形也影响第一区变形
§3.3 前刀面的挤压与摩擦 及其对切削变形的影响
作用在切屑上的力
取 切 屑 为 隔 离 体 , 作 用 在 剪切面和底面的力平衡 直 角 自 由 切 削 时 各 力 的 作 用角度如图 切削层面积:
Ac ac aw
研究过程采用了多种方法
侧面变形观察法、高速摄影法 快速落刀法、扫描电镜显微观察法等
切削变形实验设备与录像装置
§ 3.2 金属切削层的变形
挤压与切削
切屑的形成与切离过程,是切削 层受到刀具前刀面的挤压而产生以 滑移为主的塑性变形过程。
正挤压:金属材料受挤压时,最大 剪应力方向与作用力方向约成45°
L
LD Lch
◆ 自由切削宽度变形可忽略
L h
Lch LD
切屑与切削层尺寸
§ 3.2 金属切削层的变形
剪切角与变形系数的关系
ach OM sin(90 o ) cos( o )
ac
OM sin
sin
相对滑移与变形系数的关系
γ0
2 2sin o 1 cos o
主要原因。
第Ⅲ变形区:已加工面受到后刀面挤压与摩擦,产生变 形。此区变形是造成已加工面加工硬化和残余应力的主要 原因。
§ 3.2 金属切削层的变形
第一变形区的剪切变形
M A
终滑移线
切屑
Φ剪切角
始滑移线:τ=τs
刀具 O
切屑根部金相照片
§ 3.2 金属切削层的变形
第Ⅰ变形区的剪切变形程度分析
剪切角 φ :
切屑
形成连续切屑
一定的切削速度
积屑瘤特点
属 于 强 烈 塑 性 变 形的工件材料 内 摩 擦 、 粘 接 、 高硬度
积屑瘤
刀具
切屑的分离和积屑瘤
积屑瘤的影响
实际前角增大 增大切削厚度 粗糙度值增大 影响耐用度
抑制积屑瘤的办法
§3.4 积屑瘤的形成及其对切削的影响
切削速度与积屑瘤和变形系数的关系
属之间产生相对滑移,其间的 摩擦属于内摩擦。
滑动区:切屑在脱离前刀面之 前,与前刀面只在一些突出点 接触,切屑与前刀面之间的摩 擦属于外摩擦。
lfi
lfo
切屑与前刀面的摩擦
§3.3 前刀面的挤压与摩擦 及其对切削变形的影响
前刀面的摩擦 外摩擦特性
外摩擦力与摩擦系数和正压力有关与接触面积无关。
摩擦系数为定值。
剪切必需的力:
Fs Ac sin
作用在切屑上的力
§3.3 前刀面的挤压与摩擦 及其对切削变形的影响
作用在切屑上的力
两处作用力平衡,汇集于 刀刃前方如图 由几何关系得:
Fs Fr cos( o )
理论切削力(合力):
理论切削力计算
Fr Fs cos( o ) Ac sin cos( o )
偏挤压:金属材料一部分受挤压时 ,OB线以下金属由于母体阻碍,不 能沿AB线滑移,而只能沿OM线滑移
切削:与偏挤压情况类似。弹性变 形→剪切应力增大,达到屈服点→产 生塑性变形,沿OM线滑移→剪切应 力与滑移量继续增大,达到断裂强度 →切屑与母体脱离。
45° M A F
B
O
a)正挤压
45° M A F
内摩擦特性
内摩擦系数为变值。
Ff s Af 1 s Fn av Af 1 av
s
切屑与前刀面的摩擦
影响前刀面摩擦系数的主要因素
工件材料、切削厚度ac、切削速度v、刀具前角 o
§3.4 积屑瘤的形成及其对切削的影响
积屑瘤形成
加工塑性材料
↑→ ↓→切削变形↑——应尽量减小
该公式仅是理论分析。只能定性地解释问题, 定量上有出入
前刀面的摩擦
特点
在高温高压作用下,切屑底层与前刀面发生粘接,切屑 与前刀面之间既有外摩擦,也有内摩擦。
两个摩擦区
粘结区:高温高压使切屑底层
软化,粘嵌在前刀面高低不平 的凹坑中,形成长度为lfi的粘 接区。切屑的粘接层与上层金
γ0
剪切面与切削速度之间的夹角。
相对滑移系数
S0 )
M
φ
O
相对滑移系数
§ 3.2 金属切削层的变形
变形系数
切削层经塑性变形后,厚度增加,长度缩小,宽度 基本不变。可用其表示切削层变的变形程度。
◆ 厚度变形系数
h
ach ac
◆ 长度变形系数
当 o= 0~30°, ≥1.5时, 与ε相近。
ε主要反映第Ⅰ变形区的变形,
还包含了第Ⅱ变形区的影响。
φ
变形系数求法
§3.3 前刀面的挤压与摩擦 及其对切削变形的影响
第二变形区特点
强 烈 的 挤 压 与
摩擦
切 屑 底 层 纤 维
化,流动缓慢甚
至停滞
切屑弯曲
切削部位三个变形区