关于二级液压节流锥阀的低汽蚀研究论文外文翻译-中英文文献对照翻译
200t液压机液压系统设计英文文献

HydraulicHydraulic systemA complete hydraulic system consists of five parts, namely, power components, the implementation of components, control components, auxiliary parts and hydraulic oil.The role of dynamic components of the original motive fluid into mechanical energy to the pressure that the hydraulic system of pumps, it is to power the entire hydraulic system. The structure of the form of hydraulic pump gears are generally pump, vane pump and piston pump.Implementation of components (such as hydraulic cylinders and hydraulic motors) which is the pressure of the liquid can be converted to mechanical energy to drive the load for a straight line reciprocating movement or rotational movement.Control components (that is,the various hydraulic valves) in the hydraulic system to control and regulate the pressure of liquid,flow rate and direction. According to the different control functions, hydraulic valves can be divided into the village of force control valve, flow control valves and directional control valve. Pressure control valves are divided into benefits flow valve (safety valve), pressure relief valve, sequence valve, pressure relays, etc.; flow control valves including throttle, adjusting the valves, flow diversion valve sets, etc.; directional control valve includes a one-way valve, one-way fluid control valve, shuttle valve, valve and so on. Under the control of different ways, can be divided into the hydraulic valve control switch valve, control valve and set the value of the ratio control valve.Auxiliary components, including fuel tanks, oil filters, tubing and pipe joints, seals, pressure gauge, oil level, such as oil dollars.Hydraulic oil in the hydraulic system is the work of the energy transfer medium, there are a variety of mineral oil, emulsion oil hydraulic molding Hop categories.Hydraulic principleIt consists of two cylinders of different sizes and composition of fluid in the fluid full of water or oil. Water is called"hydraulic press"; the said oil-filled"hydraulic machine."Each of the two liquid a sliding piston, if the increase in the small piston on the pressure of a certain value, according to Pascal's law, small piston to the pressure of the pressure through the liquid passed to the large piston, piston top will go a long way to go. Based cross-sectional area of the small piston is S1, plus a small piston in the downward pressure on the F1. Thus, a small piston on the liquid pressure to P=F1/SI, Can be the same size in all directions to the transmission of liquid." By the large piston is also equivalent to the inevitable pressure the large piston is the cross-sectional area S2, the pressure P on the piston in the upward pressure generated F2=P×S2 Cross-sectional area is a small multiple of the piston cross-sectional area. From the type known to add in a small piston of a smaller force, the piston will be in great force, for which the hydraulic machine used to suppress plywood, oil, extract heavy objects, such as forging steel.History of the development of hydraulicHydraulic and air pressure drive hydraulic fluid as the transmission is made according to the 17th century, Pascal's principle of hydrostatic pressure to drive the development of an emerging technology, the United Kingdom in 1795 Joseph (Joseph Braman,1749-1814), in London wateras a medium to form hydraulic press used in industry, the birth of the world's first hydraulic press. Media work in 1905 will be replaced by oil-water and further improved.World War I (1914-1918) after the extensive application of hydraulic transmission, especially after 1920, more rapid development. Hydraulic components in the late 19th century about the early 20th century, 20 years, only started to enter the formal phase of industrial production. 1925 Vickers (F·Vikers) the invention of the pressure balanced vane pump, hydraulic components for the modern industrial or hydraulic transmission of the gradual establishment of the foundation. The early 20th century Constantine (G·Constantimsco) fluctuations of the energy carried out by passing theoretical and practical research;in 1910 on the hydraulic transmission (hydraulic coupling, hydraulic torque converter, etc.) contributions, so that these two areas of development.The Second World War (1941-1945) period, in the United States 30% of machine tool applications in the hydraulic transmission. It should be noted that the development of hydraulic transmission in Japan than Europe and the United States and other countries for nearly 20 years later. Before and after in 1955, the rapid development of Japan's hydraulic drive, set up in 1956, "Hydraulic Industry." Nearly 20 to 30 years, the development of Japan's fast hydraulic transmission, a world leader.Hydraulic transmission applicationThere are many outstanding advantages, it is widely used, such as general workers. Plastic processing industry, machinery, pressure machinery, machine tools, etc.; operating machinery engineering machinery, construction machinery, agricultural machinery, automobiles, etc.; iron and steel industry metallurgical machinery, lifting equipment,such as roller adjustment device; civil water projects with flood control the dam gates and devices, bed lifts installations, bridges and other manipulation of institutions; speed turbine power plant installations, nuclear power plants, etc.; ship deck crane (winch), the bow doors, bulkhead valves, such as the stern thruster; special antenna technology giant with control devices, measurement buoys, movements such as rotating stage; military-industrial control devices used in artillery, ship anti-rolling devices, aircraft simulation, aircraft retractable landing gear and rudder control devices and other devices.液压液压系统一个完整的液压系统由五个部分组成,即动力元件、执行元件、控制元件、辅助元件和液压油。
液压动力系统中英文对照外文翻译文献

中英文对照外文翻译文献(文档含英文原文和中文翻译)原文:FEATURE-BASED COMPONENT MODELS FOR VIRTUALPROTOTYPING OF HYDRAULIC SYSTERMAbstract:This paper proposes a feature-based approach for the virtual prototyping of hydraulic systems. It presents a framework which allows the designer to develop a virtual hydraulic system prototype in a more intuitive manner, i.e. through assembly of virtual components with engineering data. The approach is based on identifying the data required for the development of the virtual prototypes, and separating the information into behaviour, structural, and product attributes. Suitable representations of these attributes are presented, and the framework for the feature-based virtual prototyping approach is established,based on the hierarchical structure of components in a hydraulic system. The proposed framework not only provides a precise model of the hydraulic prototype but also offers the possibility of designing variation classes of prototypes whose members are derived by changing certain virtual components with different features.Key words: Computer-aided engineering; Fluid power systems;Virtualprototyping1.IntroductionHydraulic system design can be viewed as a function-to-form transformation process that maps an explicit set of requirements into a physical realisable fluid power system. The process involves three main stages: the functional specification stage,the configuration design stage, and the prototyping stage.The format for the description of the design in each stage is different.The functional specification stage constitutes the initial design work. The objective is to map the design requirements. To achieve this, the design problems are specified Correspondence and offprint requests to: Dr S. C. Fok, Schoool of Mechanical and Production Engineering, Nanyang Technological University, Nanyang Avenue, Singapore 639798. The designer must identify the performance attributes, which can include pressure, force, speed, and flowrate, with the required properties such as size, cost, safety and operating sequence. performance requirements for each attribute. In this stage, the design is abstracted in terms of the performance attributes with associated values.The objective of the configuration design stage is to synthesise a hydraulic circuit that performs the required functions conforming to the performance standards within defined constraints. A typical hydraulic system is made up of many subsystems. The smallest building block in a subsystem is the standard hydraulic component (such as valves, cylinders,pumps, etc.). Each type of standard component serves a specific elemental function. The design effort in the configuration design stage is fundamentally a search for a set of optimal arrangements of standard components (i.e. hydraulic circuit) to fulfil the functional requirements of the system. Based on this framework, the designers would normally decompose the overall system functions in terms of subfunctions. This will partition the search space and confine the search for smaller hydraulic subcircuits to perform the subfunctions.Computers are often used to support the configuration design process. For example, Kota and Lee devised a graph-based strategy to automate the configuration of hydraulic circuits. After the development of the hydraulic circuits, digital simulation tools are often used to study and evaluate these configurations. With these tools, designers can compare the behaviour of different circuits and also analyse the effects when subcircuits are combined. In the configuration design stage, the design is traditionally represented as a circuit drawing using standard icons to symbolise the type of standard component. This is a form of directed graph S(C,E) where the circuit S contains components C in the form of nodes with relations between components denoted by edges E.The prototyping stage is the verification phase of the system design process where the proposed hydraulic circuit from the configuration design stage isdeveloped and evaluated. Physical prototyping aims to build a physical prototype of the hydraulic system 666 S. C. Fok et al. using industrial available components. The process of physical prototyping involves the following: Search for appropriate standard components from different manufacturers. Pre-evaluation and selection of components based on individual component cost, size, and specification, and compatibility factors between components. Procurement and assembly of the selected components.Test and evaluate the physical prototype based on the overall system requirements. Use other components or redesign the circuit (or subcircuits)if necessary.Besides dynamics, the development of the physical prototype must take into consideration other factors including structure,cost, and weight. The dynamics data are used to confirm the fluid power system behaviour whereas the geometric information is used to examine the assembly properties. The development of the physical prototype will provide the actual performance,structure, and cost of the design.The main disadvantage of physical prototyping is that it is very tedious and time consuming to look for a set of suitable combinations of standard components from among so many manufacturers. Although the basic functions of the same types of standard component from different manufacturers do not differ, their dynamics, structural and cost characteristics may not be similar, because of design variation. Hence, for a given hydraulic circuit, different combinations of parts from differentmanufacturers can have implications on the resulting system,in terms of dynamics, structure, and cost. Value engineering can be used at this stage to improve the system design by improving the attributes at the component level. This includes maximizing the performance-to-cost ratio and minimising the size-to-performance ratio. Virtual prototyping can be viewed as a computer-aided design process, which employs modelling and simulating tools to address the broad issues of physical layout, operationalconcept, functional specifications, and dynamics analysis under various operating environments. The main advantage of virtual prototyping is that a hydraulic system prototype can be assembled, analysed, and modified using digital computers without the need for physical components, thus saving lead time and cost.The main requirement of a virtual hydraulic system prototype is to provide the same information as a physical prototype for the designer to make decisions.To achieve this, the virtual prototype must provide suitable and comprehensive representations of different data. Furthermore, transformation from one representation to another should proceed formally. Xiang et al. have reviewed the past and current computer-aided design and prototyping tools for fluid power systems. The work revealed that the current tools could not provide a completerepresentation of the design abstractions at the prototyping stage for design judgement. Most of the tools concentrate on the dynamics behaviour. Vital geometrical and product information that relates to the system prototype consideration and evaluation is frequently missing.To advance the development of computer-aided virtual prototyping tools for fluid power systems, there is a need to address the formal representations of different abstractions of behaviour,structural, and product data along with their integration. This paper focuses on these issues and proposes the formalism of a unified component model and the taxonomy based on the feature-based approach. In Section 2, we discuss the feature- based approach focusing on the key information and their representations required for hydraulic system prototyping. Section 3 presents a formalism of the feature-based model and structure for the development of virtual hydraulic system prototypes.The structure is illustrated with an example. Future work and conclusions are given in Section 4.2. Feature-Based ApproachFeatures can be defined as information sets that refer to aspects of attributes that can be used in reasoning about the design, engineering or manufacturing processes. The concept of using features to integrate CAD/CAPP/CAM is not new and there are many papers on the application of this approach in CIM. In all these applications, the feature model is regarded as the basis whereas design by features is the key for the integration. To develop a feature model, the relevant information concerning the design must be identified and grouped into sets based on the nature of the information. The relevant information should contain sufficient knowledge for activities such as design, analysis, test, documentation, inspection, and assembly, as well as support various administrative and logistic functions. Design by features is the process of building a model of the design using features as primitive entities. The feature model provides the standardisation of relevant data. Through the design by features approach, vital knowledge of the design will be generated and stored. Together, the feature model and the design by features approach will provide the essential information, which can be used, not only for the simultaneous consideration of many different concerns with the design, but also to interface the many activities in the design realisation process, including the life cycle support operations. The main drawback of the feature-based design approach is that the feature model should be properly defined . This can be difficult, as features are sets of knowledge that are application dependent. The organisation of the features can also be application specific. Non-trivial data-management problems could arise if the feature model is not properly defined. To avoid these problems, the type,representation and structure of the features should be resolved prior to using the feature-based design methodology. The main concern when developing afeature model is that it is application-specific. In the domain of virtual prototyping of hydraulic systems, the details of the constituent standard components must be able to be used to describe the overall system. The component features are bearers of knowledge about that part. To create a suitable feature model for hydraulic system design based on the assembly of standard components, the relevant information associated with various standard components must be identified and classified. This definition Feature-Based Component Models 667 of the component feature set can then be extended to encompass the subsystem feature set based on the hierarchical structure between the components in the subsystem. In the same manner, a hierarchical structure for the hydraulic system feature representation would evolve by considering the system as a hierarchy of subsystems.The necessary information required for a proper description of the virtual prototype must be no less than that derived by the designer from a physical prototype for decision making. These data should generally include the shape, weight, performance properties, cost, dimensions, functionality data, etc. Comparison with the physical prototyping process, the information required for each standard component could be separated into three distinct groups: behaviour attributes, structural attributes, and product attributes.2.1 Behaviour AttributesThe behaviour of a hydraulic component can be defined in terms of the dynamics characteristics used to satisfy the functional requirements. Consider a hydraulic cylinder connected to a load. Its function is to transmit a force from the stroke of the piston to the load. The maximum force it can transmit can be used to define the functionality and the behaviour requirements can be specified in terms of the desired load acceleration characteristics. Hence for a hydraulic component, behaviour attributes express functionality and can be reflected in the dynamics characteristics. The designer is responsible for the proper definition of the overall system behaviour characteristics in terms of the desired dynamics. A standard component will have its own behaviour and provide a specific plex functions that cannot be achieved by a single standard component are derived using a combination of components. Hence, the behaviour of the standard component will play an important role as the individual behaviours of components together with their arrangement can alter the overall system function .The behaviour of a standard component can be nonlinear and can be dependent on the operating conditions. When two components are combined, it is possible that their behaviours can interact and produce undesired or unintended characteristics. These unwanted behaviours are assumed to have been resolved during the configuration design stage. The hydraulic circuit used in theprototyping stage is assumed to be realisable and without any undesirable interacting behaviours. This means that the output behaviour of a component will provide the input to the subsequent component.The representation of behaviours for hydraulic systems has been widely investigated. These representations include transfer functions, state-space and bond graphs. Transfer functions (for single-input–single-output systems) and state-space equations (for multiple-input–multiple-output systems) are based on the approximation of the dynamics about a nominal operating condition. The power bond graph model is based on the causal effects that describe the energy transformations in the hydraulic system. This approach is appealing for hydraulic system analysis. The main disadvantage is that the derivation of the dynamics equation in a bond graph of a complicated fluid power system can become very tedious. As a result, recent work has concentrated on the used of artificial intelligence to represent the nonlinear mapping between the input and output data, which can be obtained via experimental work. These nonlinear mappings can be accomplished using artificial neural networks .It is quite natural for a hydraulic system designer to use input–output data to describe the behaviour of a hydraulic component. The configuration design of a hydraulic system is often achieved through steps of function decomposition. To design a hydraulic system, the designer often tries to decompose the functions and their requirements down to the component level.译文:基于原型液压系统特征的机构模型摘要:本文为原型液压系统的设计提出了一种基于特征的方法。
液压机外文翻译文献

液压机外文翻译文献(文档含中英文对照即英文原文和中文翻译)原文:The Analysis of Cavitation Problems in the Axial Piston Pumpshu WangEaton Corporation,14615 Lone Oak Road,Eden Prairie, MN 55344This paper discusses and analyzes the control volume of a piston bore constrained by the valve plate in axial piston pumps. The vacuum within the piston bore caused by the rise volume needs to be compensated by the flow; otherwise, the low pressure may cause the cavitations and aerations. In the research, the valve plate geometry can be optimized by some analytical limitations to prevent the piston pressure below the vapor pressure. The limitations provide the design guide of the timings andoverlap areas between valve plate ports and barrel kidneys to consider the cavitations and aerations. _DOI: 10.1115/1.4002058_ Keywords: cavitation , optimization, valve plate, pressure undershoots1 IntroductionIn hydrostatic machines, cavitations mean that cavities or bubbles form in the hydraulic liquid at the low pressure and collapse at the high pressure region, which causes noise, vibration, and less efficiency.Cavitations are undesirable in the pump since the shock waves formed by collapsed may be strong enough to damage components. The hydraulic fluid will vaporize when its pressure becomes too low or when the temperature is too high. In practice, a number of approaches are mostly used to deal with the problems: (1) raise the liquid level in the tank, (2) pressurize the tank, (3) booster the inlet pressure of the pump,(4) lower the pumping fluid temperature, and (5) design deliberately the pump itself.Many research efforts have been made on cavitation phenomena in hydraulic machine designs. The cavitation is classified into two types in piston pumps: trapping phenomenon related one (which can be prevented by the proper design of the valve plate)and the one observed on the layers after the contraction or enlargement of flow passages (caused by rotating group designs) in Ref. (1). The relationship between the cavitation and the measured cylinder pressure is addressed in this study. Edge and Darling (2) reported an experimental study of the cylinder pressure within an axial piston pump. The inclusion of fluid momentum effects and cavitations within the cylinder bore are predicted at both highspeed and high load conditions. Another study in Ref. (3) provides an overview of hydraulic fluid impacting on the inlet condition and cavitation potential. It indicates thatphysical properties (such as vapor pressure, viscosity, density, and bulk modulus) are vital to properly evaluate the effects on lubrication and cavitation. A homogeneous cavitation model based on the thermodynamic properties of the liquid and steam is used to understand the basic physical phenomena of mass flow reduction and wave motion influences in the hydraulic tools and injection systems (4). Dular et al. (5, 6) developed an expert system for monitoring and control of cavitations in hydraulic machines and investigated the possibility of cavitation erosion by using the computational fluid dynamics (CFD) tools. The erosion effects of cavitations have been measured and validated by a simple single hydrofoil configuration in a cavitation tunnel. It is assumed that the severe erosion is often due to the repeated collapse of the traveling vortex generated by a leading edge cavity in Ref. (7). Then, the cavitation erosion intensity may be scaled by a simple set of flow parameters: theupstream velocity, the Strouhal number, the cavity length, and the pressure. A new cavitation erosion device, called vortex cavitation generator, is introduced to comparatively study various erosion situations (8).More previous research has been concentrated on the valve plate designs, piston, and pump pressure dynamics that can be associated with cavitations in axial piston pumps. The control volume approach and instantaneous flows (leakage) are profoundly studied in Ref. [9]. Berta et al. [10] used the finite volume concept to develop a mathematical model in which the effects of port plate relief grooves have been modeled and the gaseous cavitation is considered in a simplified manner. An improved model is proposed in Ref.[11] and validated by experimental results. The model may analyze the cylinder pressure and flow ripples influenced by port plate and relief groove design. Manring comparedprincipal advantages of various valve plate slots (i.e., theslots with constant, linearly varying, and quadratic varyingareas) in axial piston pumps [12]. Four different numericalmodels are focused on the characteristics of hydraulic fluid,and cavitations are taken into account in different ways toassist the reduction in flow oscillations [13].The experiences of piston pump developments show thatthe optimization of the cavitations/aerations shall includethe following issues: occurring cavitation and air release,pump acoustics caused by the induced noises, maximal amplitudes of pressure fluctuations, rotational torque progression, etc. However, the aim of this study is to modifythe valve plate design to prevent cavitation erosions causedby collapsing steam or air bubbles on the walls of axial pump components. In contrast to literature studies, the researchfocuses on the development of analytical relationshipbetween the valve plate geometrics and cavitations. The optimization method is applied to analyze the pressure undershoots compared with the saturated vapor pressurewithin the piston bore.The appropriate design of instantaneous flow areas betweenthe valve plate and barrel kidney can be decided consequently.2 The Axial Piston Pump and Valve PlateThe typical schematic of the design of the axis piston pumpis shown in Fig. 1. The shaft offset e is designed in this caseto generate stroking containment moments for reducingcost purposes.The variation between the pivot center of the slipper andswash rotating center is shown as a. The swash angle αis the variable that determines the amount of fluid pumped pershaft revolution. In Fig. 1, the n th piston-slipper assembly is located at the angle of nθ. The displacement of the n thpiston-slipper assembly along the x-axis can be written asx n = R tan (α)sin (n θ)+ a sec (α) + e tan (α) (1) where R is the pitch radius of the rotating group. Then, the instantaneous velocity of the n th piston is x˙n = R 2sec ()αsin (n θ)α+ R tan (α)cos (n θ)ω+ R 2sec ()αsin (α)α + e 2sec ()αα (2) where the shaft rotating speed of the pump is ω=d n θ / dt .The valve plate is the most significant device to constraint flow in piston pumps. The geometry of intake/discharge ports on the valve plate and its instantaneous relative positions with respect to barrel kidneys are usually referred to the valve plate timing. The ports of the valve plate overlap with each barrel kidneys to construct a flow area or passage, which confines the fluid dynamics of the pump. In Fig. 2, the timing angles of the discharge and intake ports on the valve plate are listed as (,)T i d δ and (,)B i d δ. The opening angle of the barrel kidney is referred to as ϕ. In some designs, there exists asimultaneous overlap between the barrel kidney and intake/discharge slots at the locations of the top deadcenter (TDC) or bottom dead center (BDC) on the valve plate on which the overlap area appears together referred to as “cross-porting” in the pump design engineering. The cross-porting communicates the discharge and intake ports, which may usually lower the volumetric efficiency. The trapped-volume design is compared with the design of the cross-porting, and it can achieve better efficiency 14]. However, the cross-porting isFig. 1 The typical axis piston pump commonly used to benefit the noise issue and pump stability in practice.3 The Control Volume of a Piston BoreIn the piston pump, the fluid within one piston is embraced by the piston bore, cylinder barrel, slipper,valve plate, and swash plate shown in Fig. 3. There exist some types of slip flow by virtue of relative Fig. 2 Timing of the valve plate motions and clearances between thos e components. Within the control volume of each piston bore, the instantaneous mass is calculated asn M = ρn V (3) where ρ and n V are the instantaneous density and volume such that themass time rate of change can be given asFig. 3 The control volume of the piston boren n n dM dV d V dt dt dtρρ=+ (4)where d n V is the varying of the volume.Based on the conservation equation, the mass rate in the control volume isn n dM q dtρ= (5) where n q is the instantaneous flow rate in and out of onepiston. From the definition of the bulk modulus,n dP d dt dtρρβ= (6) where Pn is the instantaneous pressure within the piston bore. Substituting Eqs. (5) and (6) into Eq. (4) yields(?)n n n n n ndP q dV d V w d βθθ=- (7) where the shaft speed of the pump is n d dt θω=. The instantaneous volume of one piston bore can be calculated by using Eq. (1) asn V = 0V + P A [R tan (α)sin (n θ)+ a sec (α) + e tan (α) ](8) where P A is the piston sectional area and 0V is the volume of each piston, which has zero displacement along the x-axis (when n θ=0, π).The volume rate of change can be calculated at thecertain swash angle, i.e., α =0, such thattan cos n p n ndV A R d αθθ=()() (9) in which it is noted that the piston bore volume increases or decreases with respect to the rotating angle of n θ. Substituting Eqs. (8) and (9) into Eq. (7) yields0[tan()cos()] [tan sin sec tan() ]n P n n n p n q A R dP d V A R a e βαθωθαθαα-=-++()()()(10)4 Optimal DesignsTo find the extrema of pressure overshoots and undershoots in the control volume of piston bores, the optimization method can be used in Eq. (10). In a nonlinear function, reaching global maxima and minima is usually the goal of optimization. If the function is continuous on a closed interval, global maxima and minima exist. Furthermore, the global maximum (or minimum) either must be a local maximum (or minimum) in the interior of the domain or must lie on the boundary of the domain. So, the method of finding a global maximum (or minimum) is to detect all the local maxima (or minima) in the interior, evaluate themaxima (or minima) points on the boundary, and select the biggest (or smallest) one. Local maximum or local minimum can be searched by using the first derivative test that the potential extrema of a function f( · ), with derivative ()f ', can solve the equation at the critical points of ()f '=0 [15]. The pressure of control volumes in the piston bore may be found as either a minimum or maximum value as dP/ dt=0. Thus, letting the left side of Eq. (10) be equal to zero yields tan()cos()0n p n q A R ωαθ-= (11) In a piston bore, the quantity of n q offsets the volume varying and then decreases the overshoots and undershoots of the piston pressure. In this study, the most interesting are undershoots of the pressure, which may fall below the vapor pressure or gas desorption pressure to cause cavitations. The term oftan()cos()p n A R ωαθ in Eq. (11) has the positive value in the range of intake ports (22ππθ-≤≤), shown in Fig. 2, which means that the piston volume arises. Therefore, the piston needs the sufficient flow in; otherwise, the pressure may drop.In the piston, the flow of n q may get through in a few scenarios shown in Fig. 3: (I) the clearance between the valve plate and cylinder barrel, (II) the clearance between the cylinder bore and piston, (III) theclearance between the piston and slipper, (IV) the clearance between the slipper and swash plate, and (V) theoverlapping area between the barrel kidney and valve plate ports. As pumps operate stably, the flows in the as laminar flows, which can be calculated as [16]312IV k k Ln i I k h q p L ωμ==∑ (12)where k h is the height of the clearance, k L is the passagelength,scenarios I –IV mostly have low Reynolds numbers and can be regardedk ω is the width of the clearance (note that in the scenario II,k ω =2π· r, in which r is the piston radius), and p is the pressure drop defined in the intake ports as p =c p -n p (13) where c p is the case pressure of the pump. The fluid films through the above clearances were extensively investigated in previous research. The effects of the main related dimensions of pump and the operating conditions on the film are numerically clarified in Refs. [17,18]. The dynamic behavior of slipper pads and the clearance between the slipper and swash plate can be referred to Refs. [19,20]. Manring et al. [21,22]investigated the flow rate and load carrying capacity of the slipper bearing in theoretical and experimental methods under different deformation conditions. A simulation tool called CASPAR is used to estimate the nonisothermal gap flow between the cylinder barrel and the valve plate by Huang and Ivantysynova [23]. The simulation program also considers the surface deformations to predict gap heights, frictions, etc., between the piston and barrel and between the swash plate and slipper. All these clearance geometrics in Eq. (12) are nonlinear and operation based, which is a complicated issue. In this study, the experimental measurements of the gap flows are preferred. If it is not possible, the worst cases of the geometrics or tolerances with empirical adjustments may be used to consider the cavitation issue, i.e., minimum gap flows.For scenario V, the flow is mostly in high velocity and can be described by using the turbulent orifice equation as((Tn d i d d q c A c A θθ= (14) where Pi and Pd are the intake and discharge pressure of the pump and ()i A θ and ()d A θ are the instantaneousoverlap area between barrel kidneys and inlet/discharge ports of the valve plate individually.The areas are nonlinear functions of the rotating angle, which is defined by the geometrics of the barrel kidney, valve plate ports, silencing grooves, decompression holes, and so forth. Combining Eqs. (11) –(14), the area can beobtained as3()K IV A θ==(15)where ()A θ is the total overlap area of ()A θ=()()i d A A θλθ+, andλis defined as=In the piston bore, the pressure variesfrom low to high while passing over the intake and discharge ports of the valve plates. It is possible that the instantaneous pressure achieves extremely low values during the intakearea( 22ππθ-≤≤ shown in Fig. 2) that may be located below the vapor pressure vp p , i.e., n vp p p ≤;then cavitations canhappen. To prevent the phenomena, the total overlap area of ()A θmight be designed to be satisfied with30()K IV A θ=≥(16)where 0()A θ is the minimum area of 0()A θ=0()()i d A A θλθ+and0λis a constant that is0λ=evaporates into a gaseous form. The vapor pressure of any substance increases nonlinearly with temperature according to the Clausius –Clapeyron relation. With the incremental increase in temperature, the vapor pressure becomes sufficient to overcome particle attraction and make the liquid form bubbles inside the substance. For pure components, the vapor pressure can be determined by the temperature using the Antoine equation as /()10A B C T --, where T is the temperature, and A, B, and C are constants [24]. As a piston traverse the intake port, the pressure varies dependent on the cosine function in Eq. (10). It is noted that there are some typical positions of the piston with respect tothe intake port, the beginning and ending of overlap, i.e., TDC and BDC (/2,/2θππ=- ) and the zero displacement position (θ =0). The two situations will be discussed as follows: (1) When /2,/2θππ=-, it is not always necessary to maintain the overlap area of 0()A θ because slip flows may provide filling up for the vacuum. From Eq. (16), letting 0()A θ=0,the timing angles at the TDC and BDC may be designed as31cos ()tan()122IV c vpk k i I P k p p h A r L ωϕδωαμ--≤+∑ (17) in which the open angle of the barrel kidney is . There is no cross-porting flow with the timing in the intake port.(2) When θ =0, the function of cos θ has the maximum value, which can provide another limitation of the overlap area to prevent the low pressure undershoots suchthat 30(0)K IV A =≥ (18)where 0(0)A is the minimum overlap area of 0(0)(0)i A A .To prevent the low piston pressure building bubbles, the vapor pressure is considered as the lower limitation for the pressure settings in Eq. (16). The overall of overlap areas then can be derived to have a design limitation. The limitation is determined by the leakage conditions, vapor pressure, rotating speed, etc. It indicates that the higher the pumping speed, the more severe cavitation may happen, and then the designs need more overlap area to let flow in the piston bore. On the other side, the low vapor pressure of the hydraulic fluid is preferred to reduce the opportunities to reach the cavitation conditions. As a result, only the vapor pressure of the pure fluid is considered in Eqs. (16)–(18). In fact, air release starts in the higher pressure than the pure cavitation process mainly in turbulent shear layers, which occur in scenario V. Therefore, the vapor pressure might be adjusted to design the overlap area by Eq. (16) if there exists substantial trapped and dissolved air in the fluid. The laminar leakages through the clearances aforementioned are a tradeoff in the design. It is demonstrated that the more leakage from the pump case to piston may relieve cavitation problems.However, the more leakage may degrade the pump efficiency in the discharge ports. In some design cases, the maximum timing angles can be determined by Eq. (17)to not have both simultaneous overlapping and highly low pressure at the TDC and BDC. While the piston rotates to have the zero displacement, the minimum overlap area can be determined by Eq. 18 , which may assist the piston not to have the large pressure undershoots during flow intake.6 Conclusions The valve plate design is a critical issue in addressing thecavitation or aeration phenomena in the piston pump. This study uses the control volume method to analyze the flow, pressure, and leakages within one piston bore related to the valve plate timings. If the overlap area developed by barrel kidneys and valve plate ports is not properly designed, no sufficient flow replenishes the rise volume by the rotating movement. Therefore, the piston pressure may drop below the saturated vapor pressure of the liquid and air ingress to form the vapor bubbles. To control the damaging cavitations, the optimization approach is used to detect the lowest pressure constricted by valve plate timings. The analytical limitation of the overlap area needs to be satisfied to remain the pressure to not have large undershoots so that the system can be largely enhanced on cavitation/aeration issues. In this study, the dynamics of the piston control volume is developed by using several assumptions such as constant discharge coefficients and laminar leakages. The discharge coefficient is practically nonlinear based on the geometrics, flow number, etc. Leakage clearances of the control volume may not keep the constant height and width as well in practice due to vibrations and dynamical ripples. All these issues are complicated and very empirical and need further consideration in the future. The results presented in this paper can be more accurate in estimating the cavitations with these extensive studies. Nomenclature0(),()A A θθ= the total overlap area between valve plate ports and barrel kidneys 2()mm Ap = piston section area 2()mm A, B, C= constants A= offset between the piston-slipper joint and surface of the swash plate 2()mmd C = orifice discharge coefficiente= offset between the swash plate pivot and the shaft centerline of the pump 2()mmk h = the height of the clearance 2()mmk L = the passage length of the clearance 2()mm M= mass of the fluid within a single piston (kg) N= number of pistons n = piston and slipper counter,p p = fluid pressure and pressure drop (bar) Pc= the case pressure of the pump (bar) Pd= pump discharge pressure (bar) Pi = pump intake pressure (bar) Pn = fluid pressure within the nth piston bore (bar) Pvp = the vapor pressure of the hydraulic fluid(bar) qn, qLn, qTn = the instantaneous flow rate of each piston (l/min) R = piston pitch radius 2()mmr = piston radius (mm )t =time (s )V = volume 3()mmwk = the width of the clearance (mm )x ,x˙= piston displacement and velocity along the shaft axis (m, m/s )x y z --=Cartesian coordinates with an origin on the shaft centerlinex y z '''--= Cartesian coordinates with an origin on swash plate pivot,αα=swash plate angle and velocity (rad, rad/s )β= fluid bulk modulus (bar ),B T δδ= timing angle of valve plates at the BDC and TDC (rad ) ϕ = the open angle of the barrel kidney (rad )ρ= fluid density (kg /m3),θω = angular position and velocity of the rotating kit (rad, rad/s )μ =absolute viscosity (Cp ),λλ=coefficients related to the pressure drop翻译:在轴向柱塞泵气蚀问题的分析本论文讨论和分析了一个柱塞孔与配流盘限制在轴向柱塞泵的控制量设计。
液压专业毕业设计科技文献外文翻译--阻尼式溢流阀的建模与动态响应(英语)
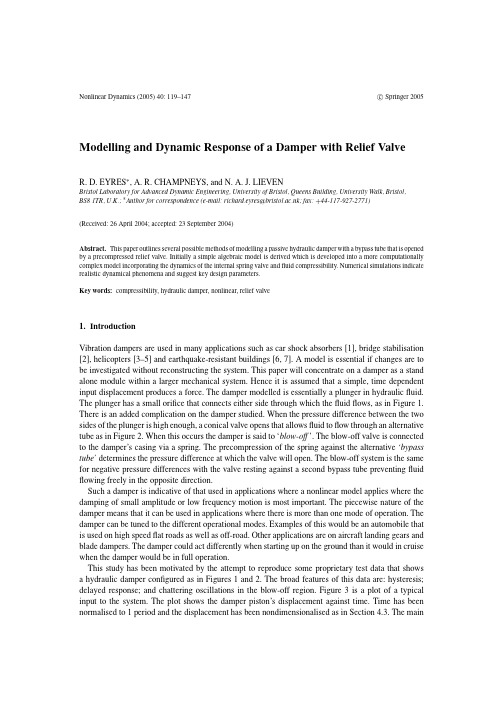
Abstract. This paper outlines several possible methods of modelling a passive hydraulic damper with a bypass tube that is opened by a precompressed relief valve. Initially a simple algebraic model is derived which is developed into a more computationally complex model incorporating the dynamics of the internal spring valve and fluid compressibility. Numerical simulations indicate realistic dynamical phenomena and suggest key design parameters. Key words: compressibility, hydraulic damper, nonlinear, relief valve
Figure 4. The required normalised force output against normalised time and velocity for one cycle.
[8–11], to our knowledge the effects of the passive blow-off valve have not been treated in the literature (although relief valves treated on their own have been shown to lead to nonlinear [12, 13] and chaotic dynamics [14].) The resulting model can be used to predict the effect of changing the properties of the damper on the dynamic response. The key features investigated are the sizes of the orifice and bypass tube along with the stiffness and discharge characteristics of the spring and valve respectively. In this paper a simple lumped mass parametric model is derived that incorporates all these effects. The rest of this paper is outlined as follows. Section 2 describes the modelling process used by previous researchers to model Figure 1 as a simplification of an automobile shock absorber. Sections 3 and 4 investigate several possible extensions to the model in Section 2 to take into account the blow-off. First an explicit model is derived to give the force for a given displacement input. The relief valve and compressibility of the fluid are then considered separately. A model for the whole system is then derived. Section 5 gives some results using the different models. There is also a discussion in Section
附录二外文文献翻译

附录二:外文文献翻译水轮机转轮叶片的简化模型赛义德,加里斌威塞克斯技术学院,艾舍斯特,英国南安普敦SO407AA摘要:混流式水轮机叶片是以曲梁的压力均匀分布为模型的。
这种简化允许最大应力的分析计算随后用有限元分析比较相同的水轮机。
有两种曲梁的模型已经被提出,其中一个在不同的工况下都显示出了与有限元良好的相关性。
该模型已应用于德本迪汗水水电站2号机组的整个操作过程中记录的数据进行分析。
结果表明使水轮机叶片上出现裂缝的最大拉应力的形成不能被单独以高应力水平来解释,而应该用不同因素的组合来解释。
2009爱思唯尔有限公司保留所有权利。
关键词:混流式水轮机转轮、曲梁、应力分析1.介绍混流式水轮机是一种复杂的力学结构,它的力学性能只能用数值法来模拟。
有限元法(FEM)经常被用来进行混流式水轮机转轮的应力分析,这就需要压力分布的知识。
这些可从测量学[3,7,9]或从计算流体力学(CFD)模拟[6,14,18]。
费尔哈特演示了在数值模拟和和所有的混流式水轮机实测数据之间有很好的吻合。
流体结构相互作用分析法经常被用来计算混流式水轮机转轮中的压力[21]。
用有限元方法计算转轮叶片的应力是由Angehrn引入的。
混流式水轮机的有限元计算结果和实验测量的比较也被报道过,并且揭示了不同的方式达成了令人满意的结果。
整个水轮机转轮的数值分析,对计算机的内存和计算时长有很高的要求。
为了减少计算时间,以及减少对内存的需求,已经提出来转轮简化模型来计算在整个运行期间转轮叶片上的压力。
例如,叶片与上冠或下环之间的焊接头被简化为一个简单的T形焊接头。
单一使用一个简化模型计算所需的时间比整个水轮机转轮的有限元分析所需的时间少得多。
这项研究提出了一个将转轮叶片简化为曲线梁的简化方法。
结果与赛义德等人用有限元法获得的结果进行了比较[20]。
用于应力分析的数据是从从德本迪汗水电站2号机组所收集的(在伊拉克北部库尔德发电的主要供应商之一从1997年到2002年)。
液压英文文献及翻译
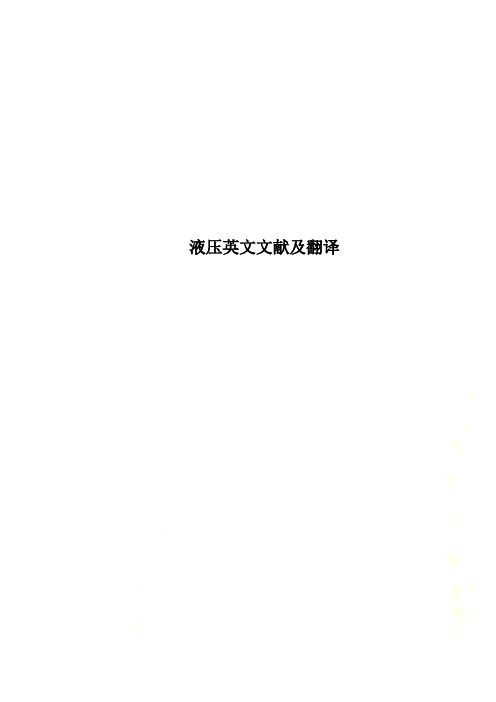
液压英文文献及翻译液压系统1.绪论液压站称液压泵站,是独立的液压装置。
它是按逐级要求供油。
并控制液压油流方向、压力和流量,适用在主机与液压装置可分离的各种液压机械上面。
用户在购后只要将液压站与主机上执行机构(油缸或油马达)用不同的油管相连,液压机械即实现各种规定的动作与工作循环。
液压站是由集成块、泵装置或阀组合、电气盒、油箱电气盒组合而成。
各个部件功能为:泵装置——上装有电机和油泵,其是液压站的动力源,能将机械能转化为液压油压力能。
阀组合--其板式阀装在立板上,板后管连接,与集成块的功能相同。
油集成块--是由液压阀及通道体组装而成。
其对液压油实行压力、方向和流量调节。
箱--是板焊的半封闭容器,上面还装有滤油网、空气滤清器等,是用来储油与油的冷却及过滤。
电气盒--分两种型式:一种是设置外接引线的端子板;一种是配置了全套控制电器。
液压站工作原理:电机带动油泵转动,然后泵从油箱中吸油并供油,将机械能转化为液压站压力能,液压油通过集成块(或阀组合)实现方向、压力、流量调节后经过外接管路并至液压机械里的油缸或油马达中,从而控制液动机方向变换、力量的大小及速度的快慢,来推动各种液压机械做功。
(1)液压的发展历程在我国液压(含液力,下同)、气动和密封件工业的发展历程,大致可分成三个阶段,即:在20世纪50年代初到60年代初是起步阶段;60-70年代为专业化生产体系的成长阶段;80-90年代为快速发展阶段。
在其中,液压工业始于50年代初从机床行业生产的仿苏的磨床、拉床、仿形车床等液压传动来起步,液压元件由机床厂里的液压车间生产,自产自用。
在进入60年代后,液压技术应用从机床逐渐推广到农业机械与工程机械等领域,原来附属于主机厂里的液压车间有些独立出来,成为液压件的专业生产厂。
在60年代末、70年代初,随着生产机械化的不断发展,特别是在为第二汽车制造厂等提供了高效、自动化设备的带动下,液压元件制造业出现了不断迅速发展的局面,一批中小企业也开始成为液压件专业制造厂。
毕业设计——阀门 外文文献翻译 中英文

第一章阀门的基础知识第一节概述阀门是流体管路的控制装置,其基本功能是接通或切断管路介质的流通,改变介质的流通,改变介质的流动方向,调节介质的压力和流量,保护管路的设备的正常运行。
工业用的阀门的大量应用是在瓦特发明蒸汽机之后,近二三十年来,由于石油、化工、电站、冶金、船舶、核能、宇航等方面的需要,对阀门提出更高的要求,促使人们研究和生产高参数的阀门,其工作温度从超低温-269℃到高温1200℃,甚至高达3430℃,工作压力从超真空1.33x10-8Mpa(1x10-1 ㎜Hg)到超高压1460MPa,阀门通径从1mm 到600mm,甚至达到9750mm,阀门的材料从铸铁,碳素钢发展到钛及钛合金,高强度耐腐蚀钢等,阀门的驱动方式从手动发展到电动、气动、液动、程控、数控、遥控等。
随着现代工业的不断发展,阀门需求量不断增长,一个现代化的石油化工装置就需要上万只各式各样的阀门,阀门使用量大。
开闭频繁,但往往由于制造、使用选型、维修不当,发生跑、冒、滴、漏现象,由此引起火焰、爆炸、中毒、烫伤事故,或者造成产品质量低劣,能耗提高,设备腐蚀,物耗提高,环境污染,甚至造成停产等事故,已屡见不鲜,因此人们希望获得高质量的阀门,同时也要求提高阀门的使用,维修水平,这时对从事阀门操作人员,维修人员以及工程技术人员,提出新的要求,除了要精心设计、合理选用、正确操作阀门之外,还要及时维护、修理阀门,使阀门的“跑、冒、滴、漏”及各类事故降到最低限度。
第二节阀门的分类阀门的用途广泛,种类繁多,分类方法也比较多。
总的可分两大类:第一类自动阀门:依靠介质(液体、气体)本身的能力而自行动作的阀门。
如止回阀、安全阀、调节阀、疏水阀、减压阀等。
第二类驱动阀门:借助手动、电动、液动、气动来操纵动作的阀门。
如闸阀,截止阀、节流阀、蝶阀、球阀、旋塞阀等。
此外,阀门的分类还有以下几种方法:一、按结构特征,根据关闭件相对于阀座移动的方向可分:1.截门形:关闭件沿着阀座中心移动。
毕业设计论文外文文献翻译泄压阀的最低要求中英文对照
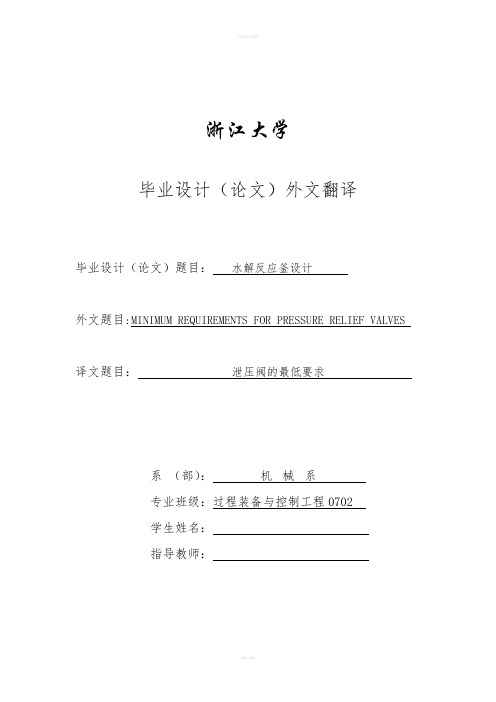
浙江大学毕业设计(论文)外文翻译毕业设计(论文)题目:水解反应釜设计外文题目:MINIMUM REQUIREMENTS FOR PRESSURE RELIEF VALVES 译文题目:泄压阀的最低要求系(部):机械系专业班级:过程装备与控制工程0702学生姓名:指导教师:指导教师评阅意见MINIMUM REQUIREMENTS FORPRESSURE RELIEF VALVESUG-136(a) Mechanical RequirementsUG-136(a) (1) the design shall incorporate guiding arrangements necessary to ensure consistent operation and tightness.UG-136(a) (2) The spring shall be designed so that the full lift spring compression shall be no greater than 80% of the nominal solid defection. The permanent set of the spring (defined as the difference between the freeheight and height measured 10 min after the spring has been compressed solid three additional times after presetting at room temperature) shall not exceed 0.5% of the free height.UG-136(a)(3) Each pressure relief valve on air, water over 140°F (60°C), or steam service shall have a substantial lifting device, which when activated will release the seating force on the disk when the pressure Relief valve is subjected to a pressure of at least 75% of the set pressure of the valve. Pilot operated pressure relief valves used on these services shall be provided with either a lifting device as described above or means for connecting and applying pressure to the pilot adequate to verify that the moving parts critical to proper operation are free to move.UG-136(a) (4) the seat of a pressure relief valve shall be fastened to the body of the pressure relief valve in such a way that there is no possibility of the seat lifting.UG-136(a) (5) in the design of the body of the pressure relief valve, consideration shall be given to minimizing the effects of deposits.UG-136(a) (6) Pressure relief valves having screwed inlet or outlet connections shall be provided with wrenching surfaces to allow for normal installation without damaging operating parts.UG-136(a) (7) Means shall be provided in the design of all pressure relief valves for use under this Division for sealing all initial adjustments which can be made without disassembly of the valve. Seals shall be installed by the Manufacturer or Assembler at the time of initial adjustment. Seals shall be installed in a manner to prevent changing the adjustment without breaking the seal. For pressure relief valves largerThan NPS 1|2 (DN 15), the seal shall serve as a means of identifying the Manufacturer Or Assembler making the initial adjustment.UG-136(a) (8) If the design of a pressure relief valve is such that liquid can collect on the discharge side of the disk, except as permitted in (a)(9) below, the valve shall be equipped with a drain at the lowest point where liquid can collect (for installation, see UG-135).UG-136(a) (9) Pressure relief valves that cannot be equipped with a drain as required in (a) (8) above because of design or application may be used provided:(a) The pressure relief valves are used only on gas service where there is neither liquid discharged from the valve nor liquid formed by condensation on the discharge side of the valve; and(b) the pressure relief valves are provided with a cover or discharge piping per UG-135(f) to prevent liquid or other contaminant from entering the discharge side of the valve; and(c) The pressure relief valve is marked FOR GAS SERVICE ONLY in addition to the requirements of UG-129.UG-136(a) (10) for pressure relief valves of the diaphragm type, the space above the diaphragm shall be vented to prevent a buildup of pressure above the diaphragm. Pressure relief valves of the diaphragm type shall be designed so that failure or deterioration of the diaphragm material will not impair the ability of the valve to relieve at the rated capacity. UG-136(b) Material SelectionsUG-136(b) (1) Cast iron seats and disks are not permitted.UG-136(b) (2) Adjacent sliding surfaces such as guides and disks or disk holders shall both be of corrosion resistant material. Springs of corrosion resistant material or having a corrosion resistant coating are required. The seats and disks of pressure relief valves shall be of suitable material to resist corrosion by the fluid to be contained. NOTE: The degree of corrosion resistance, appropriate to the intended service, shall be a matter of agreement between the manufacturer andThe purchaser.UG-136(b)(3) Materials used in bodies and bonnets or yokes shall be listed in Section II and this Division.Carbon and low alloy steel bodies, bonnets, yokes and bolting (UG-20) subject to in-service temperatures colder than −20°F(−30°C) shall meet the requirements of UCS-66, unless exempted by the following.(a) The coincident ratio defined in Fig. UCS-66.1 is 0.35 or less.(b) The material(s) is exempted from impact testing per Fig. UCS-66. UG-136(b) (4) Materials used in nozzles, disks, and other parts contained within the external structure of the pressure relief valves shall be one of the following categories:(a) Listed in Section II;(b) listed in ASTM specifications;(c) Controlled by the Manufacturer of the pressure relief valve by a specification ensuring control of chemical and physical properties and quality at least equivalent to ASTM standards.UG-136(c) Inspection of Manufacturing and/or Assembly of Pressure Relief ValvesUG-136(c)(1) A Manufacturer or Assembler shall demonstrate to the satisfaction of a representative from an ASME designated organization that his manufacturing, production, and testing facilities and quality control procedures will insure close agreement between the performance of random production samples and the performance of those valves submitted for Capacity Certification.UG-136(c) (2) Manufacturing, assembly, inspection, and test operations including capacity are subject to inspections at any time by a representative from an ASME designated organization.UG-136(c) (3) A Manufacturer or Assembler may be granted permission to apply the UV Code Symbol to production pressure relief valves capacity certified in accordance with UG-131 provided the following tests are Successfully completed. This permission shall expire on the fifth anniversary of the date it is initially granted. The permission may be extended for 5 year periods if the following tests are successfully repeated within the 6-month period before expiration.(a) Two sample production pressure relief valves of a size and capacity within the capability of an ASME accepted laboratory shall be selected by a representative from an ASME designated organization.(b) Operational and capacity tests shall be conducted in the presence of a representative from an ASME designated organization at an ASME accepted laboratory. The pressure relief valve Manufacturer or Assembler shall be noticed of the time of the test and may have representatives present to witness the test. Pressure relief valves having an adjustable blow down construction shall be adjusted by the Manufacturer or Assembler following successful testing for operation but prior to flow testing so that the blow down does not exceed 7% of the set pressure or 3 psi (20 kPa), whichever is greater. This adjustment may be made on the flow test facility.(c) Should any pressure relief valve fail to relieve at or above its certified capacity or should it fail to meet performance requirements of this Division, the test shall be repeated at the rate of two replacement pressure relief valves, selected in accordance with (c)(3)(a) above, for Each pressure relief valve that failed.(d) Failure of any of the replacement pressure relief valves to meet the capacity or the performance requirements of this Division shall be cause for revocation within 60 days of the authorization to use the Code Symbol on that particular type of pressure relief valve. During this period, the Manufacturer or Assembler shall demonstrate the cause of such decadency and the action taken to guard against future occurrence, and the requirements of (c) (3) above shall apply.UG-136(c) (4) Use of the Code Symbol Stamp by an Assembler indicates the use of original, unnoticed parts in strict accordance with the instructions of the Manufacturer of the pressure relief valve.(a) An assembler may transfer original and unnoticed pressure relief parts produced by the Manufacturer to other Assemblers provided the following conditions are met:(1) Both Assemblers have been granted permission to apply the V or UV Code Symbol to the specifi c valve type in which the parts are to be used;(2) The Quality Control System of the Assembler receiving the pressure relief valve parts shall define the controls for the procurement and acceptance of those parts; and(3) The pressure relief valve parts are appropriately packaged, marked, or sealed by the Manufacturer to ensure that the parts are:(a) Produced by the Manufacturer; and(b) The parts are original and unnoticed. However, an Assembler may convert original finished parts by machining to another finished part fora specifi c application under the following conditions:(1) Conversions shall be specified by the Manufacturer. Drawings and/or written instructions used for part conversion shall be obtained from the Manufacturer and shall include a drawing or description of the converted Part before and after machining.(2) The Assembler’s quality control system, as accepted by a representative from an ASME designated organization, must describe in detail the conversion of original parts, provisions for inspection and acceptance, personnel training, and control of current Manufacturer’s Drawings and/or written instructions.(3) The Assembler must document each use of a converted part and that the part was used in strict accordance with the instructions of the Manufacturer.(4) The Assembler must demonstrate to the Manufacturer the ability to perform each type of conversion. The Manufacturer shall document all authorizations granted to perform part conversions. The Manufacturer And Assembler shall maintain a file of such authorizations.(5) At least annually a review shall be performed by the Manufacturer of an Assembler’s system and machining capabilities. The Manufacturer shall document the results of these reviews. A copy of this documentation shall be kept onfile by the Assembler. The review results shall be made available to a representative from an ASME designated organization.UG-136(c) (5) In addition to the requirements of UG-129, the marking shall include the name of the Manufacturer and the finalAssembler. The Code Symbol Stamp shall be that of the final Assembler.NOTE: Within the requirements of UG-136(c) and (d): A Manufacturer is defined as a person or organization who is completely responsible for design, material selection, capacity cortication, manufacture of all component parts, assembly, testing, sealing, and shipping of pressure relief valves credited under this Division. An Assembler is defined as a person or organization who purchases or receives from a Manufacturer or another Assembler the necessary component parts or pressure relief valves and assembles, adjusts, tests, seals, and ships pressure relief valves credited under this Division, at a geographical location other than and using facilities other than those used by the Manufacturer. An Assembler may be organizationally independent of a Manufacturer or may be wholly or partly owned by a Manufacturer.UG-136(d) Production Testing by Manufacturers and Assemblers UG-136(d) (1) each pressure relief valve to which the Code Symbol Stamp is to be applied shall be subjected to the following tests by the Manufacturer or Assembler. A Manufacturer or Assembler shall have a documented program for the application, calibration, and maintenance Of gages and instruments used during these tests.UG-136(d)(2) The primary pressure parts of each pressure relief valve exceeding NPS 1 (DN 25) inlet size or 300 psi (2100 MPa) set pressure where the materials used are either cast or welded shall be tested at a pressure Of at least 1.5 times the design pressure of the parts. These tests shall be conducted after all machining operations on the parts have been completed. There shall be no visible sign of leakage.UG-136(d) (3) the secondary pressure zone of each closed bonnet pressure relief valve exceeding NPS 1 (DN 25) inlet size when such pressure relief valves are designed for discharge to a closed system shall be tested With air or other gas at a pressure of at least 30 psi (200 kPa). There shall be no visible sign of leakage.UG-136(d) (4) each pressure relief valve shall be tested to demonstrate its popping or set pressure. Pressure relief valves marked for steam service or having special internal parts for steam service shall be tested with steam, except that pressure relief valves beyond the capability Of the production steam test facility either because of size or set pressure may be tested on air. Necessary corrections for differentials in popping pressure between steam and air shall be established by the Manufacturer and applied to the popping point on air. Pressure relief valves marked for gas or vapor may be tested with air. Pressure relief Valves marked for liquid service shall be tested with water or other suitable liquid. When a valve is adjusted to correct for service conditions of superimposed back pressure, temperature, or the differential in popping pressure between steam and air, the actual test pressure (cold differential test pressure) shall be marked on the valve perUG-129. Test fixtures and test drums where applicable shall be of adequate size and capacity to ensure that pressure relief valve action is consistent with the stamped set pressure within the tolerances required by UG-134(d).UG-136(d) (5) after completion of the tests required by (d) (4) above, a seat tightness test shall be conducted. Unless otherwise designated by a Manufacturer’s published pressure relief valve specification or another specification agreed to by the user, the seat tightness test and acceptance criteria shall be in accordance with API 527.UG-136(d) (6) Testing time on steam pressure relief valves shall be sufficient, depending on size and design, to insure that test results are repeatable and representative of held performance.UG-136(e) Design Requirements.At the time of the submission of pressure relief valves for capacity cortication, or testing in accordance with (c) (3) above, the ASME designated organization has the authority to Review the design for conformity with the requirements of UG-136(a) and UG-136(b) and to reject or require medication of designs which do not conform, prior to capacity testing.UG-136(f) Welding and Other Requirements.All welding, brazing, heat treatment, and nondestructive examination used in the construction of bodies, bonnets, and yokes shall be performed in accordance with the Applicable requirements of this Division. Selections from:ASME BOILER AND PRESSURE VESSEL CODE AN INTERNATIONAL CODE泄压阀的最低要求UG(a)136机械需求UG 136(a)(1)设计应纳入指导和进行必要安排以确保一致的行动和密封性。
- 1、下载文档前请自行甄别文档内容的完整性,平台不提供额外的编辑、内容补充、找答案等附加服务。
- 2、"仅部分预览"的文档,不可在线预览部分如存在完整性等问题,可反馈申请退款(可完整预览的文档不适用该条件!)。
- 3、如文档侵犯您的权益,请联系客服反馈,我们会尽快为您处理(人工客服工作时间:9:00-18:30)。
中文共4400字第一部位外文原文标题:关于二级液压节流锥阀的低汽蚀研究Research on low cavitation in water hydraulic two-stagethrottle poppet valveAbstract: Cavitation has important effects on the performances and lifespan of water hydraulic control valve, such as degradingefficiency, intense noise, and severe vibration. Two-stage throttle valve is a practicable configuration to mitigate cavitation, which is extensively used in water hydraulic pressurerelief valves and throttle valves. The pressure distribution inside a medium chamber located between two throttles of a two-stage throttle valve is investigated through numerical simulations. The effects of the passage area ratio of the two throttles and the inlet and outlet pressures on the pressure inside the medium chamber are examined. The simulation results indicate that (a) the pressureinside the medium chamber is not constant, (b) the locations ofmaximum and minimum pressures inside the medium chamber are both fixed, which will not vary with the passage area ratio or the inlet and outlet pressures, and (c) the ratio of the pressure drop acrossthe front throttle to the total pressure drop across the two-stage throttle valve is nearly constant. The critical cavitation indexof the two-stage throttle valve is then established. A semiempirical design criterion is obtained for the water hydraulic two-stage throttle valve. The correlation between the critical cavitation index and the passage area ratio of the two throttlesis investigated. Relevant validation experiments are conducted ata custom-manufactured testing apparatus. The experimental results are consistent with the simulated ones. Further analyses indicatethat (a) the large backpressure can improve not only the anti-cavitation capability but also the total load rigidity of the water hydraulic two-stage throttle valve, (b) an appropriate passage area ratio will be beneficial for improving the anti-cavitation capability of the water hydraulic two-stage throttle valve, and (c) the water hydraulic two-stage throttlevalve with a passage area ratio of 0.6 would have the best anti-cavitation performance with the lowest risk of cavitation.Keywords: computational fluid dynamics simulation cavitation load rigidity passage area ratio two-stage throttle valve water hydraulics1 INTRODUCTIONWater hydraulic systems are operated with raw water (pure tapwater) substituting for mineral oil. They have advantages in terms of durability, reliability, safety, and cleanness. Such systems are becoming more and more popular, especially in fields of steel andglass production, coal and gold mining, food and medicine processing, nuclear power generation, ocean exploration, and underwater robotics [1–5].Because the opening of a water hydraulic control valve is very small compared with that of oil valve, the water flow velocitythrough the water hydraulic control valve is larger under the same pressure condition; thus cavitation erosion may occur due to thehigh vapour pressure of water. Cavitation has an important effecton the performance and lifespan of water hydraulic control valve,such as degrading efficiency, intense noise, and severe vibration. Previously, a number of studies on the relationships between cavitation and discharge coefficient, thrust force and pressuredistributions in the valves, and mitigation of cavitation damagewere carried out through increasing outlet pressure of valves,modifying shapes of throttles, adding stages of valves, selectinganti-corrosion materials for parts, and controlling maximum fluid temperature and flow velocity. Tsukiji et al. [6] investigatedcavitation by flow visualization in hydraulic poppet-type holdingvalves to reduce cavitation. Some measures were employed to diminish noise and cavitation through controlling flowrate, upstream pressure, downstream pressure, and valve lift in case ofconverging flow.Aoyama et al. [7] studied experimentally the unsteady cavitation performance in an oil hydraulic poppet valve. It wasfound that, as absolute values of the variation rates of inlet and outlet pressure increased, the incipient cavitation index exhibited a tendency to decrease, whereas the final cavitationindex a tendency to increase under all geometrical parameters. Asthe absolute values of the variation rates of inlet and outletpressure further increased, the hysteresis between the incipientand final cavitation indices would become larger than ever for each combination of the valve and valve seat.Ishihara et al. [8] studied oil flow unsteadiness effect oncavitation phenomena a t sharp-edged orifices. The rate of pressure drop across the orifice was kept constant, and cavitation incipience and finale were recorded by using scattered laser beams showing that (a) there existed two types of cavitation, namely,gaseous cavitation and vapourous cavitation, and (b) cavitationincipience and finale varied with the initial condition, the temperature of hydraulic oil, and the rate of pressure drop.Johnston et al. [9] carried out an experimental investigationof flow and force characteristics of hydraulic poppet and discvalves using water as the working fluid. The axisymmetric valvehousing was constructed from clear perspex to facilitate flow visualization; tests were performed on a range of different poppet and disc valves operating under steady and non-cavitating conditions, for Reynolds numbers greater than 2500. Measured flow coefficients and force characteristics showed obvious differences depending on valve geometry and opening.Vaughan et al. [10] conducted computational fluid dynamics (CFD) analysis on flow through poppet valves. Simulations were comparedwith experimental measurements and visualized flow patterns. Aqualitative agreement between simulated and visualized flow patterns was identified. However, errors in the prediction of jetseparation and reattachment resulted in quantitative inaccuracies. These errors were due to the limitations of the upwind differencing scheme employed and the representation of turbulence by the k –1 model, which was known to be inaccurate when applied to recirculating flow.Ueno et al. [11] investigated experimentally and numericallythe oil flow in a pressure control valve under an assumption ofnon-cavitating conditions for various configurations of the valveson the basics of a finite difference method. They concluded thatthe main noise of the testing valves was generated from cavitation, and the noise was affected by the valve configuration. Pressure measurements and flow visualization at two locations in a valvechamber were also performed on the basis of two-dimensional models. Through comparisons of the measured and calculated results, several design criteria were set up for low-noise valves.Martin et al. [12] investigated cavitation in spool valves inorder to identify damage mechanisms of the related components.Tests were conducted in a representative metal spool valve as well as a model being three times larger. Data taken under non-cavitating conditions with both of these valves showed that the orientationof high-velocity angular jets would be shifted due to variationsin valve opening and Reynolds number. By means of high-frequency response pressure transducers strategically placed in the valvechamber, the cavitation could be sensed through the correlation of noise with a cavitation index. The onset of cavitation could bedetected by comparing energy spectra for a fixed valve opening with a constant discharge. The incipient cavitation index, as definedin this investigation, was correlated with the Reynolds number for both valves.Gao et al. [13] performed a simulation of cavitating flows inhydraulic poppet valves by means of an renormalization group (RNG) k –1 turbulence model, which was derived from the nstantaneousNavier–Stokes equations based on the RNG theory. Experiments were conducted to catch cavitation images around the seat of a poppetvalve from perpendicular directions, using a pair of industrialfibre scopes and a high-speed visualization system. The binarycavitating flowfield distributions obtained through digital processing of the original cavitation image showed satisfactoryagreement with numerical results; the vibrations of valve body and poppet induced by the cavitating flow were detected using a vortex displacement transducer, a laser displacement metre and a digitalstrain device. It was concluded that the opening and cone of aconical valve had significant effects on the intensity of cavitation. However, in this study, only downstream cavitationinception volume was analysed in estimating the anti-cavitationcapability, whereas the effects of outlet pressure were not considered.Oshima et al. [14] experimentally investigated the influencesof (a) chamfer length in the valve seat, (b) the poppet angle, and(c) the oil temperature on the flow characteristics and the cavitation phenomena, using water instead of oil as the workingmedium in water poppet throttles. The cavitation phenomena weredirectly observed and the pressure distribution between the valveseat and poppet surface was measured in water poppet throttles. Comparison analyses on the condition of critical cavitation wereconducted between oil and water. It was found that the dischargecoefficient and the critical cavitation number for water poppetthrottles were considerably different from those of oil ones, dueto the high density and low viscosity of water. Recently, Liu etal. [15, 16] investigated experimentally the flow and cavitationcharacteristics of a two-stage throttle in water hydraulic system; they concluded that the two-stage throttle had stronger anti-cavitation capability than the single-stage one, and that the shape of seats also affected the anti-cavitation capability of the throttles. The cavitation choking appeared only when cavitationindex was less than 0.4. They also conducted several studies on the relationships between the cavitation and the configuration of control valve, and between the cavitation and the passage area ratio of two throttles. However, the pressure between two throttles wasassumed to be constant, which may not be applicable for the two-stage throttle with a medium chamber.As an extension of Liu et al. [15, 16], this research will focus on the investigation of cavitation characteristics in the waterhydraulic two-stage throttle poppet valve. This objective entailsthe following research tasks: (a) on the basis of the RNG k – 1 turbulent model, numerical simulations will be conducted to investigate the pressure distribution inside the medium chamberlocated between the two throttles, (b) the effect of the passagearea ratio of the two throttles and pressure between the two throttles on the anti-cavitation capability will be studied, (c)the design criteria of the two-stage throttle valve will be established for low-cavitation and noise, and (d) experimentalvalidation will be performed through a custom-manufactured testing apparatus, to demonstrate applicability of the developed simulation approach and design criteria.2SIMULATION OF PRESSURE BETWEEN TWO THROTTLES2.1Statement of problemsIf water pressure decreases below the saturationvapour pressure pv (absolute pressure) of water under a given temperature, the vapour or gas will spill out of the water, and then cavitation will occur. For water, pv . 0.023 MPa when the temperature is 20 8C. Generally, the likelihood of the cavitationfor the throttle valve can be measured by a cavitation index (K ),which can be expressed as followsThe critical cavitation index (Kc) is the minimum cavitationindex for the throttle under non-cavitating flow in throttle valve. For a single-stage throttle valve, Ksc . 0.4 [14, 17–20]. It denotes that, if the cavitation index K is less than 0.4, thecavitation will occur. Therefore, the cavitation index (K ) should be larger than 0.4 so as to avoid cavitation in the throttle valve.The larger the pressure drop across the throttle valve, thesmaller the cavitation index (and thus greater probability of cavitation for the throttle valve). The two-stage throttle valveis a practicable configuration to mitigate cavitation, being extensively used in water hydraulic pressure relief valves andthrottle valves. Figure 1(a) is a scheme of water hydraulic two-stage throttle valve, which consists of a poppet and a seat with a step shape bore. There are two tandem throttles to take the total pressure drop (pin -pout). Therefore, the pressure drop across each stage throttle is less than the total drop of the valve, which isdiffered from a single-stage throttle. Hence, the cavitation index of each stage throttle should be larger than that of thesingle-stage throttle valve, leading to a reduced possibility ofcavitation and erosion.For the two-stage throttle valve, the definition of cavitation index Kt can be analogously expressed as followsActually, for each stage throttle, the critical conditions foravoiding cavitation in a single-stage throttle should be satisfied. ThenThe pressure distribution inside the medium chamber locatedbetween the two throttles should be obtained to calculate cavitation indices for both stages. CFD simulation will be undertaken to explore the pressure distribution of the medium chamber.2.2Mathematical modelIn view of the axisymmetric structure of the two-stage throttle valve, the computational domain is simplified to a two-dimensionalaxisymmetric geometrical model (ABCDE), as shown in Fig. 1(a); its grids are generated (Fig. 1(b)) through an advanced grid preprocessor (Gambit of software package FLUENT) [21, 22]. In Fig. 1(a), AB a nd BC d enote fixed wall of seat, ED i s fixed wall of poppet, CD the inlet, and AE the outlet. The water is assumed to be incompressible viscous fluid with ρ= 998.2 kg/m3, and μ=1.007×10-6m2/s; the effects of pressure and temperature on the density and viscidity of water are neglectable; all of the wallsare assumed adiabatic with a zero slip velocity. The inlet andoutlet boundaries can be specified as pressure levels.The RNG k –1 equation model (turbulence kinetic energy equation k and dissipation equation 1) and the multiphase model are used in this research. The Boussinesq hypothesis is employed torelateReynolds stresses to the mean v elocity gradients The turbulence kinetic energy (k) and its rate of dissipation (1) are obtained from transport equations (6) and (7), respectivelyIn this research, the multiphase model involves liquid and gas phases that are considered as interpenetrating continua. The lawof conservation of mass and momentum is satisfied in each phase.The derivation of the conservation equations can be done by ensembling the local instantaneous balances for all of the phases.Volume fractions (ap) represent the space occupied by gas phase.The continuity equation for gas phase can yieldIn these equations, Gk represents the generation of turbulence kinetic energy due to the mean v elocity gradient; sk and s1 are the inverse effective turbulent Prandtl numbers for k and 1, respectively.2.3Simulation results Sensitivity analyses of the variations ofpressures inside the medium chamber along with the changing passage area ratio of the two throttles and the inlet and outlet pressures were performed. As a large number of numerical simulations were conducted, it is impossible to include all of the results here.Instead, representative outcomes are explicated to demonstrate important findings. The simulated contours of the volume fractionof water vapour are shown in Fig. 2. The passage area ratio (r) could significantly affect the cavitation occurrence and intensity under conditions of pin . 10 MPa and pout . 1 MPa. There are several key transferring points for passage area ratio including r . 0.2, 0.5, and 2.0. When r was less than 0.2, water vapour would be formedinside the medium chamber of the two-stage throttle valve, and the corresponding maximum volume fraction of water vapour would increase up to 85.3 per cent as shown in Fig. 2(a). This was ascribedto the high fluid velocity and the intense recirculation inside the medium chamber. The recirculation would cause the formation of alow-pressure zone and thus potential cavitation. With an increasingr level, the volume fraction of water vapour would be reduced. When r ranged from 0.5 to 0.8, the maximum volume fraction of water vapour would fall (to 0.162 per cent or below) and, consequently, thepossibility of cavitation would decrease. However, with furtherincrease of the passage area ratio (e.g. when r . 2.0), the maximum volume fraction of water vapour would increase up to 5.15–26.7 per cent as shown in Figs 2(c) and (d); thus, cavitation would occuragain.The simulated contours of pressure inside the medium chambersare presented in Fig. 3 when the passage area ratio varied from 0.1 to 6.0 under conditions of pin . 10 MPa and pout . 1 MPa. It canbe seen from Fig. 3 that, when r was less than 0.2 or larger than2.0, the pressure drop would be solely taken by the front or rearthrottle of the two-stage throttle valve. This looked like a single-stage throttle valve, with its anti-cavitation capabilitybeing similar to that of single-stage throttle valve. When r wasbetween 0.2 and 2.0, the total pressure drop would be shared by the two tandem throttles. Obviously, a sound r level would help suppresscavitation inception in the water hydraulic two-stage throttlepoppet valve.In order to clarify the correlations among pressure levelsinside the medium chamber and the related impact factors (r, pin,and pout), a virtual line (l ) was employed to locate the pressurelevels inside the medium chamber. They ranged from the midpoint of line AE to the midpoint of line CD. The virtual line was dividedinto eight parts, and the corresponding nodes were marked by ordinal numbers (from 0 to 8); the pressure levels on the virtual line were denoted as pl.The effects of the passage area ratio (r) on the pressure (pl) under condition of pin . 10 MPa and pout . 4 MPa are illustratedin Fig. 4. The pressure level would vary with the passage area ratio. The larger the passage area ratio r, the higher the pressure level on the virtual line. However, when r is less than 0.2, the pressures inside the medium chamber would become low. This was attributed to the small front throttle, which could be considered as a jet nozzle. The fluid would have less direction variations and jet contraction when passing through the front throttle. A high flow velocity through the front throttle would be generated, and thus the pressure would decrease rapidly. In such a case, the flow pattern would belike that of a single-stage throttle. From Fig. 4, the pressurelevels on the virtual line (l) would vary at different space positions, confirming that the pressure levels inside the mediumchamber were not constants. It was also very interesting that thelocations of the maximum and minimum pressures were fixed on thevirtual line, being indifferent of the variations of the passagearea ratio.第二部位中文翻译关于二级液压节流锥阀的低汽蚀研究摘要:汽蚀对于液压控制阀的性能和寿命有重要影响,如引起效率的降低,产生强烈的噪音和振动。