缩釉地成因及解决方法
瓷器形成缩釉的主要原因

瓷器形成缩釉的主要原因
在陶瓷生产过程中,由于多种原因,往往在烧成后有釉的产品表面上会出现局部无釉缺陷,即缩釉。
那么形成缩釉的主要原因是什么呢?
形成缩釉主要原因有两个:
其一是釉料中的灰尘和釉料本身的收缩。
有些釉,特别是那些含氧化锡的釉,如果釉施得过稠,或施在一个脏的表面上,将会缩起,变成较大的结块。
在高温胎体涂上了粘度较高的釉料时,会产生针眼状的露胎缩釉点,其原理如下:当窑温升至1300°C左右时,胎体中部分原料进行化学反应,并逐步完成烧结。
反应中产生较多的气体,主要是氧气、二氧化碳和少量二氧化硫。
在胎体加温至1300°C的同时,胎表面的釉料同时在1300°C的温度下,并进入熔融状态,熔融状态的釉料呈液膜,紧贴在烧结状的胎体表面。
当胎体内释放出的气体逸出釉面时,即在釉里产生大量气泡。
如果气泡聚集较大,釉的粘度又较高,逸出的地方就产生露胎的缩釉点。
有的呈针眼状,在瓷器的转角处积釉很厚,缩釉面会较大。
第二个主要原因是釉料中塑性成分含量太多了,以至在干燥期间,釉层收缩过于严重,产生微细裂纹,使釉面开裂。
在烧成过程中,易形成釉堆,结成块状,而不能均匀地熔融覆盖坯体。
这种缺陷经常出在素烧过的坯件上。
探秘:汝瓷中的棕眼和缩釉斑

探秘:汝瓷中的棕眼和缩釉斑各位藏友大家好,今天我们来聊一聊汝瓷中的棕眼和缩釉斑,什么是汝瓷的棕眼和缩釉斑呢?其实就是汝瓷釉面上的一种缺陷、瑕疵。
什么叫棕眼呢?就是汝瓷釉面上塌陷的小坑,这种小坑只能用马的棕毛穿进去,故此得名棕眼。
缩釉斑就是汝瓷釉面上露胎缩釉的地方。
这两个瑕疵是胎里带,棕眼和缩釉斑的形成是汝瓷与生俱来的,出窑就有的。
它们是怎么形成的呢,棕眼的形成是汝瓷胚胎有空隙,空隙里有水分,在汝窑里烧制过程中,水分蒸发不断向釉面膨胀,冲破釉面而形成的。
缩釉斑的形成有多种说法,我感觉比较可信的说法,就是釉水调稀了,胚胎湿过釉料后,放入窑炉开始烧造,随着温度的升高,釉料开始收缩,由于釉料过稀,有一部分胎挂不上釉料,也有一部分釉面气泡破裂造成釉料回缩,从而造成了缩釉斑和缩釉点。
尤其是瓷器的边沿和棱角部分,挂釉比较困难,所以这一部分露胎缩釉比较严重,如果露胎的部位大了,我们一般称之为缩釉斑,如果露胎的部位小了,我们称之为缩釉点。
全世界存放汝瓷比较多的地方就是台北故宫博物馆和北京故宫博物院,台北故宫博物院的二十一件汝瓷大部分都有棕眼和缩釉斑。
北京故宫博物院馆藏的汝瓷大部分也有这种情况。
图一是北京故宫博物院馆藏的汝瓷天青釉盘,可以清楚的看到这个盘子口沿处有两处缩釉斑,这个缩釉斑是铁褐色,因为它的泥土可能含铁比较多一点,再经过近一千年的氧化,它就呈现一种铁褐色。
还有一种缩釉斑呈现一种铜黄色,有人说这叫铜骨。
这个盘子中间也有缩釉点。
图一图二是北京故宫博物院馆藏的汝瓷天青釉盘,底足稍微外撇,满釉支烧,三个芝麻支钉痕,呈黄白色,刻乙字款,肉眼可见,足心有明显的棕眼,圈足边缘处釉薄也呈黄褐色。
图二图三是北京故宫博物院馆藏的汝瓷天青釉,满釉支烧,圈足稍微外撇,五个支钉痕呈黄白色,刻有乾隆皇帝的御题诗,也可以清晰的看到有棕眼和缩釉斑。
图三宋代汝瓷上的棕眼和缩釉斑是那个时代特有的瑕疵,由于当时生产技术和工艺流程的局限,做不到尽善尽美,留下了缩釉斑和棕眼等特征。
缩釉与爆釉

会会长汪庆正先生认为:瓷器鉴定是一门边缘科学,它同化学、物理、人文科学关系十分密切,古陶瓷的鉴定要知道器物的产生年代,产地在哪里,当时采用什么原材料和用什么工艺……所以,我们在鉴定一件瓷器时,除了常说的器型、纹饰、款识等因素外,多研究一些原材料和加工工艺相关的胎釉知识很有必要。
古瓷涩胎之上火石红现象的类别。
一、顺火石红;由瓷器的足部,顺着胎釉的结合处向足端产生浓淡过渡的火石红。有人称此种浓淡过渡现象为散场现象。产生原因是晾坯时日短、胎釉中所含的水份未及干透。
瓷器的胎体主要是经过瓷土(或瓷石)与高岭土粉碎、漂洗、沉淀加工而成。瓷土的主要成分为二氧化硅、氧化铝、氧化钙,高岭土的成分中氧化铝的含量稍高一些。瓷釉由石英、云母、钠长石等物质组成,自然界里称作釉果,其化学成分主要为硅酸盐,但瓷釉中还加一些碱性助熔剂。除此之外,明清瓷器中一般都加入了由草木灰和氧化钙加工而成的釉灰。
六、由底足察看各个时期其胎釉的结合情况,尤其是明以前,一般都有护胎土,或化状土、或子金土呈现,而仿品则要不涂点朱砂红,要不涂点浆水,要不没有;
七、观察
其粘沙现象,如明之以前的器物多有不同程度的粘沙现象,清官民之窑足内积釉处也有粘沙,而仿品这一点却极少做到(伪品也有少数粘沙,然不像真品那样显得老化干燥),因其烧造工艺高于古时,釉也施得不是那么厚,不会造成积釉,再加多为模注而过于规整等原因,使之极少有粘沙;
道光以后的瓷器烧结的温度也不太高。主要是康乾盛世后,经济的发展使瓷器民用普遍化。乾隆后期已有五件套作为姑娘的嫁妆,嘉道后盛行。所以瓷土的需求量很大,精细的原料仅能用于官窑。道光以后瓷土质量欠佳,主要是精品高岭土减少,胎中氧化钙的成分增加,降低了瓷胎的烧结温度,一般在1200°C-1250°C烧结固化。嘉道以后在烧制陶瓷用的釉料中增加了碱性助熔剂,在温度近1300°C时釉料熔融,但较前期的粘度低,较稀薄。但这种较稀薄的釉料均匀地渗入烧结的瓷胎中,所烧制的瓷器也很漂亮。此种瓷器胎釉结合尚可,釉面较薄,有的可见胎痕。釉内气泡较小,少有层次感。
陶瓷缩釉原因及解决方法

陶瓷缩釉原因及解决方法
陶瓷缩釉是在陶瓷制作过程中常见的问题,主要原因是由于陶瓷
制作过程中温度控制不当或釉料配方不合理所导致的。
它会严重影响
陶瓷的美观和使用寿命,因此我们需要了解缩釉的原因,并采取相应
的解决方法来避免这个问题的发生。
首先,导致陶瓷缩釉的一个主要原因是在烧制过程中温度控制不当。
如果温度过高或过低,都会导致釉料无法充分熔化,从而引起缩釉。
解决这个问题的方法是通过调整烧制的温度和时间来达到适当的
烧制条件。
这需要根据不同的釉料和陶瓷材质进行实验和调整,以确
定最佳的烧制参数。
其次,釉料配方不合理也会导致缩釉的问题。
釉料中的成分比例
不正确或配方中含有不稳定的化合物,都会导致釉料熔化不均匀,从
而引起缩釉现象。
解决这个问题的方法是对釉料配方进行优化和改进。
使用稳定的化合物替代不稳定的化合物,并精确调整各组成分的比例,以确保釉料在烧制过程中能够均匀熔化,避免缩釉的发生。
此外,制作过程中的其他因素也可能导致缩釉问题。
例如,陶瓷
成型时制作的过于粗糙或薄弱的样品可能无法承受烧制的过程,从而
导致缩釉现象。
因此,需要确保陶瓷的成型过程细致且合理,并且选
择合适的釉料以确保质量。
在解决陶瓷缩釉问题时,我们应该结合具体情况采取针对性的解
决方法。
从控制温度、调整釉料配方到优化成型方法,都需要综合考
虑。
同时,定期进行质量检查和改进也是避免缩釉问题的重要手段。
只有不断改进和提升制作工艺,才能在陶瓷制作中避免缩釉问题的发生,保证产品的质量和美观。
缩釉的成因及解决方法

缩釉的成因及解决方法对有釉陶瓷产品如日用陶瓷、卫生陶瓷、有釉墙地砖等来说,胎体表面上的一层釉起着极为重要的作用。
一是可以遮盖胎体的不良色泽,起装饰美化作用;二是可以提高产品的抗污、去污能力;三是提高陶瓷产品的强度与整体使用功能。
但是在生产中,由于多种原因,往往在烧成后有釉的产品表面上会出现局部无釉缺陷,即缩釉。
缩釉不但影响产品外观,而且一旦出现会导致整体产品的报废。
一般来说,在陶瓷釉面上所显示的缩釉缺陷可在烧成前或烧成中引起。
当釉溶化后,陶瓷的某些部位没被釉料覆盖导致了在烧成后的产品某些无釉部位。
如果釉特别稠(粘度大),在烧成中它就不能平滑地在产品表面流动。
在某些地方,釉料就会聚集成堆或有时会在釉面出现大量裂纹。
实际上,这些并不是裂纹,只是釉料没有流动。
通常,在烧结温度时,釉料应该完全液化并流动均匀地覆盖表面。
当釉料由于表面张力的不能很好地流动,釉料不能流动到的部位便显露出坯体,这就叫"缩釉"。
有时当釉表面趋向于聚集或卷缩时,整个釉面层会裂成釉珠状。
以下几个方面的原因可能导致缩釉。
(1)釉料干燥时收缩过大;(2)釉料颗粒过细;(3)釉层过厚;1 缩釉原因的讨论1.1 收缩坯料与釉料在烧成和干燥过程中会发生收缩,二者的收缩不相同。
如果坯料与釉料的收缩相差过大,便会发生釉料开裂。
如果釉料球磨过细,则易形成裂纹,这是由于釉料被过度球磨后,在干燥过程中引起的过度收缩。
当过度球磨釉料时,虽然釉料的悬浮性能增强,烧成后釉面的质量会得以较大提高。
如釉面光泽增面,釉面针孔减少等,但施釉后釉料在干燥过程中釉面会趋于粉末化,并且很易被磕碰掉。
不但过度球磨能导致过度收缩。
另外,如果釉浆中塑性粘土含量太高,干燥时釉料的收缩大,则会在釉面产生裂纹。
此外坯体表面凹凸不平,如存有大颗粒的泥块等,也会产生小范围内的不均匀收缩。
在使用熔块釉时,过度球磨极易产生施釉釉面开裂,这是因为熔块釉在存放期间更易于沉淀,经搅拌后再使用时,由于搅拌不匀造成釉面收缩不一致,在釉料干燥过程中易产生釉面开裂,烧成后会明显出现裂纹;另一个原因就是通常被过度球磨后的釉由于其颗粒细而具有更大的表面积,在高温时易发生化学反应和固相反应,并且具有熔解坯体中氧化硅和氧化铝的倾向。
缩点釉在陶瓷艺术品上的应用研究

228缩点釉在陶瓷艺术品上的应用研究★ 程法伟缩点釉是一种能形成斑点图案的釉料,本文探讨了缩点釉的形成机理,重点介绍了缩点釉的研制过程和具体应用,讨论了影响收缩效果的关键问题,收缩釉,俗称缩点釉,是一种能在陶瓷表面膨胀过程中形成圆形斑点的特殊釉料,这种现象是利用陶瓷制造过程中的收缩膨胀原理。
收缩膨胀如果温度掌握错误就会釉面开裂,要不断调整瓷器配方,改变操作方式,工艺制作,才能使收缩后的釉面彩绘均匀,美观大方,缩点釉用于陶瓷的外表,能起到很好的装饰效果。
一、釉面产生缩釉现象的原因该釉料采用物理活性高、粒度细、多孔晶体形态的结构性原料,并施涂于陶瓷器皿表面,但出现釉面稍干就会造成小裂缝,所以在煅烧过程中要注意温度大小,太高则会导致釉料熔化。
复合釉熔体具有很高的表面张力、高温高粘度、釉料对坯料的润湿性大等特点。
造成釉面收缩的原因有很多,一是因为瓷器表面玻璃上釉时,釉面很薄,坯体与釉之间的有机结合力差,导致釉面显示空白,会形成斑点。
二是釉浆过细,颗粒过分散,烧成过程中釉面膨胀过大,造成釉面收缩;三是坯体潮湿闷热,窑内水汽过多,这样削弱了釉面的附着力,会使釉面层部分脱落。
四是釉料熔体张力高、粘度低,这种现象本质上是由于釉料熔体对坯体润湿性差,釉液的外表面充满张力,在高温影响下釉的流动性越差,釉液就不能铺展和润湿,从而造成收缩。
二.缩点釉在陶瓷艺术品上的具体应用大部分基础釉专用配方包含松散粉末,如氧化钛和硫酸钡,他们颗粒细小,表面积大,且吸水能力强,这有利于收缩点的形成,能很好的达到收缩的良好效果。
适当添加用量为11%的添加剂时,能让收缩点更均匀、明显。
加漆是收缩点的点睛之处,在工艺基础釉料专用配方中加入各种添加剂,并加入5%的金属镁,在高温作用下金属镁晶体呈现多孔结构,施加在物体上的收缩点会明显且混合均匀。
(一)施釉厚度的应用制作收缩釉的釉浆比一般的釉厚,釉浆的主要含水量为45%-55%,釉面厚度为1-2毫米,釉层非常厚,这样表面开裂程度比较强,点的整边较大,烧成后收缩点均匀美观,釉面厚度一般都要大于0.8毫米,如果太小会使釉面形成的裂纹就不均匀,烧成后收缩点大小没有变化,收缩点不光滑,且鼓包不是很明显,但釉面整体厚度过大,远大于2毫米,就会出现釉面起皮的现象,并影响釉面上形成的小裂纹美观的程度,会破坏釉面的形状。
釉料的缺陷
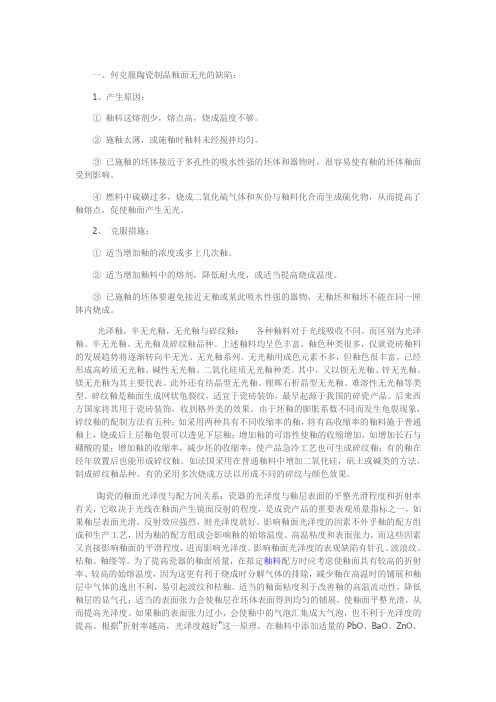
一、何克服陶瓷制品釉面无光的缺陷:1、产生原因:①釉料这熔剂少,熔点高,烧成温度不够。
②施釉太薄,或施釉时釉料未经搅拌均匀。
③已施釉的坯体接近于多孔性的吸水性强的坯体和器物时,很容易使有釉的坯体釉面受到影响。
④燃料中硫磺过多,烧成二氧化硫气体和灰份与釉料化合而生成硫化物,从而提高了釉熔点,促使釉面产生无光。
2、克服措施:①适当增加釉的浓度或多上几次釉。
②适当增加釉料中的熔剂,降低耐火度,或适当提高烧成温度。
③已施釉的坯体要避免接近无釉或某此吸水性强的器物,无釉坯和釉坯不能在同一匣钵内烧成。
光泽釉,半无光釉,无光釉与碎纹釉:各种釉料对于光线吸收不同,而区别为光泽釉、半无光釉、无光釉及碎纹釉品种。
上述釉料均呈色丰富,釉色种类很多,仅就瓷砖釉料的发展趋势将逐渐转向半无光、无光釉系列。
无光釉用成色元素不多,但釉色很丰富,已经形成高岭质无光釉、碱性无光釉、二氧化硅质无光釉种类。
其中,又以钡无光釉、锌无光釉、镁无光釉为其主要代表。
此外还有结晶型无光釉、锂辉石析晶型无光釉、难溶性无光釉等类型。
碎纹釉是釉面生成网状龟裂纹,适宜于瓷砖装饰,最早起源于我国的碎瓷产品。
后来西方国家将其用于瓷砖装饰,收到格外美的效果。
由于坯釉的膨胀系数不同而发生龟裂现象,碎纹釉的配制方法有五种:如采用两种具有不同收缩率的釉,将有高收缩率的釉料施于普通釉上,烧成后上层釉龟裂可以透见下层釉;增加釉的可溶性使釉的收缩增加,如增加长石与硼酸的量;增加釉的收缩率,减少坯的收缩率;使产品急冷工艺也可生成碎纹釉;有的釉在经年放置后也能形成碎纹釉。
如法国采用在普通釉料中增加二氧化硅,矾土或碱类的方法,制成碎纹釉品种。
有的采用多次烧成方法以形成不同的碎纹与颜色效果。
陶瓷的釉面光泽度与配方间关系:瓷器的光泽度与釉层表面的平整光滑程度和折射率有关,它取决于光线在釉面产生镜面反射的程度,是成瓷产品的重要表观质量指标之一,如果釉层表面光滑,反射效应强烈,则光泽度就好。
景德镇高温颜色釉陶瓷缩釉现象分析

过程中最大的敌人 ,油污 的憎水性 ,会使得釉层不能和 坯体完全结合 ,必然会产 生缩 釉。
旦坯体与釉体存在较大的收缩差 ,高温 中熔 融状态就会 产生相对滑动和移位 ,在坯体 和釉体接触界面上产 生剪 切应力 ,减弱坯体 与釉体 结合力 ,最终导致坯 与釉的分 离 ,导致缩釉。
缩釉源 :
定要较粗 ,而对于 吹釉 等其他 方式 ,粗细 问题都不是很
大。
创作过程中 ,我发现缩 釉存在季节性现 象,另 外 ,缩釉 可在 成品 的任 何 部位 产生 ,例如 钵 类缩釉 ,内面 、外
面 、 底 部 、 口沿 均 可 能 出现 ,但 多数 是 内面 不 缩 则 外 面
( )施釉前生坯存放 时间和 方式 二
K oi f r m / 岭 坛/ a l Ou n 高 论
景德镇 高温颜色釉 陶瓷缩釉 现象分析
An lzn n ter d c o lz h n me o fh tmp rtr oo lz d c rmisi ig eh n ay ig o e u t n ga ep e o n n o i e eau ec lr ae e a c nJn d z e h i g
正 常 情 况 下 ,生 坯 放 置 2 天 以 上 也 会 产 生 积 灰 , 放 置 半 个 月 以上 则 会 出现 黄 色 的碱 皮 ,这 种 浮 灰 和 碱 皮
缩釉 ,反之亦然 ,但是 内面 ,外面 同时缩 釉的情况比较 罕见。在这几年的高温颜 色釉陶瓷 的创作过程 中 ,统计
发 现 外 面 缩 釉 比内 面 的 多 ,手 工 胎 缩 釉 比注 浆和 机 压 的
( )施釉在生坯过程 中方式 三
在 釉 体 施 釉 到 坯 体 的过 程 中 ,一 定 要均 匀 ,力 度 巧
- 1、下载文档前请自行甄别文档内容的完整性,平台不提供额外的编辑、内容补充、找答案等附加服务。
- 2、"仅部分预览"的文档,不可在线预览部分如存在完整性等问题,可反馈申请退款(可完整预览的文档不适用该条件!)。
- 3、如文档侵犯您的权益,请联系客服反馈,我们会尽快为您处理(人工客服工作时间:9:00-18:30)。
缩釉的成因及解决方法对有釉瓷产品如日用瓷、卫生瓷、有釉墙地砖等来说,胎体表面上的一层釉起着极为重要的作用。
一是可以遮盖胎体的不良色泽,起装饰美化作用;二是可以提高产品的抗污、去污能力;三是提高瓷产品的强度与整体使用功能。
但是在生产中,由于多种原因,往往在烧成后有釉的产品表面上会出现局部无釉缺陷,即缩釉。
缩釉不但影响产品外观,而且一旦出现会导致整体产品的报废。
一般来说,在瓷釉面上所显示的缩釉缺陷可在烧成前或烧成中引起。
当釉溶化后,瓷的某些部位没被釉料覆盖导致了在烧成后的产品某些无釉部位。
如果釉特别稠(粘度大),在烧成中它就不能平滑地在产品表面流动。
在某些地方,釉料就会聚集成堆或有时会在釉面出现大量裂纹。
实际上,这些并不是裂纹,只是釉料没有流动。
通常,在烧结温度时,釉料应该完全液化并流动均匀地覆盖表面。
当釉料由于表面力的不能很好地流动,釉料不能流动到的部位便显露出坯体,这就叫"缩釉"。
有时当釉表面趋向于聚集或卷缩时,整个釉面层会裂成釉珠状。
以下几个方面的原因可能导致缩釉。
(1)釉料干燥时收缩过大;(2)釉料颗粒过细;(3)釉层过厚;(4)釉料熔融时的粘度和表面力(5)釉料对坯体表面较弱的附着力;(6)不正确地使用釉料;(7)坯体方面的原因;(8)烧成温度、烧成条件以及窑炉的气氛;(9)釉料中所加入的色料的影响;(10)釉料的化学组成;(11)坯釉之间的结合力;(12)ZnO的影响。
为了研究几个突出的缩釉因素,特别进行了一系列实验。
在本论文的实验中选择了一种特定的釉料配方:锆乳浊釉。
表1是该配方所用原料及其百分含量,表3是其化学成分分析结果。
釉料施于常规的坯体上,其配方与化学组成如表2、表4所示。
表1 研究用釉料配方(%)表2 研究用坯体配方(%)表3 研究用釉料的化学成分(%)表4 研究用坯体的化学成分(%)1 缩釉原因的讨论1.1 收缩坯料与釉料在烧成和干燥过程中会发生收缩,二者的收缩不相同。
如果坯料与釉料的收缩相差过大,便会发生釉料开裂。
如果釉料球磨过细,则易形成裂纹,这是由于釉料被过度球磨后,在干燥过程中引起的过度收缩。
当过度球磨釉料时,虽然釉料的悬浮性能增强,烧成后釉面的质量会得以较大提高。
如釉面光泽增面,釉面针孔减少等,但施釉后釉料在干燥过程中釉面会趋于粉末化,并且很易被磕碰掉。
不但过度球磨能导致过度收缩。
另外,如果釉浆中塑性粘土含量太高,干燥时釉料的收缩大,则会在釉面产生裂纹。
此外坯体表面凹凸不平,如存有大颗粒的泥块等,也会产生小围的不均匀收缩。
在使用熔块釉时,过度球磨极易产生施釉釉面开裂,这是因为熔块釉在存放期间更易于沉淀,经搅拌后再使用时,由于搅拌不匀造成釉面收缩不一致,在釉料干燥过程中易产生釉面开裂,烧成后会明显出现裂纹;另一个原因就是通常被过度球磨后的釉由于其颗粒细而具有更大的表面积,在高温时易发生化学反应和固相反应,并且具有熔解坯体中氧化硅和氧化铝的倾向。
这样会导致釉粘度增加,变得更加粘稠,引起缩釉缺陷的发生。
因此在釉料制备过程中,应避免过度球磨釉炎,保持一定的釉料颗粒级配,以减少减釉缺陷的发生。
在釉料长时间存放后,应充分搅拌均匀。
1.2 研磨因子为了研究过度研磨釉料所造成的缩釉的影响,特别做了一系列试验。
试验是将已过200目筛的配釉用各种原料配制好,分别球磨6h、12h、24h、36h、48h。
检测其结果。
表5列出了经上述不同时间球磨后所测试出的釉料的颗粒尺寸分布。
图1显示釉料经不同球磨时间球磨后的颗粒尺寸大小与百分数。
为了确定缩釉的本质,我们将已球磨好的釉通过多次浸釉法施在瓷坯体表面,以获得不同的釉层厚度。
干燥后所观察到的釉面结果如表6所示。
表5 釉料经不同时间下球磨后颗粒尺寸表6 不同研磨时间、多次浸釉形成多层釉层的釉面结果从表5-6可以看出,随着研磨时间及施釉厚度的增加,缩釉逐渐增加,有时甚至在干燥后就可观察到釉面开裂。
虽然在干燥期间裂纹并不可见,但,在烧成后裂纹却出现了。
球磨时间越长,釉料颗粒越细,则收缩越大,缩釉也越明显。
如果生坯中包含有较高的粗颗粒原料或含有较高的非可塑性原料,便会由于不规则的收缩而很难获得合适的光滑釉面。
在干燥期间只有在釉料过度收缩时,可观察到裂纹。
干燥期间所产生的细小裂纹。
在烧成后便会显现出来,形成缩釉。
图2显示过度球磨所出现的缩釉缺陷。
1.3 釉层厚度同一种颗粒细度的釉料。
施釉时因其施釉厚度的不同,会出现不同的结果。
釉层越厚,则越容易产生缩釉,如表6所示。
这是因为釉层越厚,收缩越大。
在生产中,应控制好釉层厚度,对于卫生瓷来说,釉层厚度一般控制在0.6mm左右。
1.4 釉的粘度釉料在其熔化时粘度太大便会引起缩釉。
因为釉料的表面力已克服了釉料与坯体的粘着力,釉料就会在瓷的角位或其它部位聚集成堆。
图3表示瓷表面釉料聚集成堆的形成过程。
较厚釉层更易开裂和缩釉。
硫酸盐会影响釉料的熔融,特别是在釉料中长石含量高的情况下,影响釉料的熔融。
粘度是一种控制熟釉均匀性的参数。
一般来讲,粘度可通过添加盐溶液如CaCl2,或者是ZnO、石灰等来控制。
在生产中应避免使用高粘度的釉料,否则便会导致不合适的釉面覆盖层。
图4显示因不合适的釉料粘度所导致的缩釉缺陷。
1.5 熟釉的表面力在高温下,当釉料与坯体一起烧成时,由于二者之间发生了化学反应,便会在二者之间形式中间过渡层而产生相互结合力。
结合力大小由釉--空气、坯体-空气以及固体-液体之间的表面力所决定。
可溶性盐类在坯体表面的聚集会削弱坯釉之间的这种结合力而易引起缩釉;具有高表面力的釉收缩大,易导致釉面缩釉。
如果熔融的釉料对坯体表面的润湿性差,则烧成后的秋面易产生缩釉。
在釉料中加入较少的氧化物添加剂如V2O5、MnO2、Sb2O3等,可降低釉料的表面力,因而可减少缩釉的发生。
另外可以将防发酵盐如苯钠或者是磺酸蓖麻油加入釉浆中来保持釉的表面力。
在烧成中釉料高温时具有较低的表面力,这样有利于气体的排除。
但是如果釉料的表面力太低,则高温烧成时釉的流动太大,会导致跑釉现象,造成烧成后的产品漏边角和漏棱角。
在生产中可以通过调整釉料配方来控制釉的表面力。
合适的釉料,其表面力应在满足不漏边角和不漏棱角的前提下,尽可能低一些。
1.6 釉浆与坯体的粘着力差粘着力即釉与坯体表面的结合力。
如果过度研磨釉料或者釉料中含有太多可塑性原料,釉料便不能与坯体表面很好地粘接在一起。
有些有机物添加剂如醋酸纤维素铵对提高釉料粘度非常有用。
在生料釉中,粘土本身能作粘接剂。
熔块釉有时不能很好地附着在坯体上,特别是不能很好地附着在完全瓷化的瓷上,在这种情况下易产生缩釉。
添加有机粘接剂如骨胶有助于增强釉料的粘接力。
另外将坯体在干燥器中保持干燥大约1小时后进行施釉,使釉料施在热坯上,有助于增强釉料的粘接力,减少缩釉的发生。
1.7 釉的施用在坯体上施加过厚的釉层有时会造成如图5所示的缩釉。
这是因为釉层很厚,会产生不同的收缩而减弱釉对坯体的粘接力,烧成后引起产品缩釉。
连接施釉时如果间隔时间太长,会导致的施釉层不均匀而引起缩釉。
特别是对不合适的素坯上釉时,素坯会很快吸收釉浆而形成较厚的釉覆盖层,导致缩釉。
因此施釉前首先将素坯用海绵沾水搽抹弄湿,使其吸收釉浆速度减慢并均匀吸收釉浆,减少缩釉的发生。
施釉时应用足够的高度或压力以便能使釉平滑地流动到坯体表面各处。
通过较好地控制釉的流动性与触变性,可以有效地防止缩釉:在生产和实验中我们发现多孔的瓷坯体在浸釉时,如果浸釉时间过长,会由于形成不均匀的釉层而产生少量的釉面裂纹。
施釉时坯体气孔处与坯体表面会产生不同的釉层厚度。
为了使釉均匀平滑地覆盖住平面的坯体表面,应该使釉料具有足够的流动性。
当使用喷釉法时,要处理好喷枪、气压以及喷枪与被喷釉坯体之间的距离等因素,控制好上述关系便能获得平滑均匀的釉层,防止缩釉。
1.8 坯体的物理条件瓷的物理条件取决于它的质地、瓷化特征以及收缩性质。
在平滑表面的坯体上,釉料的流动速度均匀一致。
坯体的质地取决于用于坯体的原料的制备与研磨。
研磨细,则坯体质地平滑。
粗糙的坯体表面有时施釉后在干燥时产生不规则的收缩使釉层与坯体剥离,入窑烧成,当温度升高时,釉表面力的作用会将釉从坯釉剥离处拉开而产生缩釉。
完全瓷化后,瓷坯体很难喷上釉或浸上釉。
这是因为其吸水率太低而不能快速吸收釉料且釉料对坯体的粘接力低,在这种情况下,缩釉的可能性很高,如果被施釉的坯体形状复杂且不规则,那么产生缩釉的可能性更大,这是因为施釉时釉料在坯体表面各部门的流动不一致,从而形成了不同厚度的球状釉层。
所施釉的坯体太湿也会导致缩釉,原因是太湿的坯体对釉的吸附力弱。
1.9 烧成温度及烧成条件与气氛烧成时在坯体排除气体期间,应该控制好烧成制度,否则会在较低温度下出现釉面缩釉或裂纹。
如已上釉的坯体在搬运或装车过程受到碰撞,会破坏釉料与坯体之间的正常粘接。
当冲击过度时,可能使已干燥的部分釉面从坯体表面剥离而最终产生缩釉。
在烧成早期出现过多的气泡或者是在坯体量气体逸出之间,釉已经熔融,最终导致产品的缩釉。
过烧也会引起缩釉。
1.10 色料的影响一些釉下色料像粉红、绿色、无光钴蓝等,因不容易被熔融的釉润湿,造成色料与釉分离而可能产生缩釉。
解决方法是加入适量的助熔剂。
1.11 釉的化学组成有时釉料的组成也能导致缩釉。
因为不合适的釉料在特定的烧成条件与熔融点下不能恰当地流动。
釉料中添加乳浊剂如硅酸锆、氧化锡等,能引起缩釉。
这是因为它们影响了釉的粘度与表面力,特别是现时所用的硅酸锆,一般为几个微米、颗粒细,比表面积大,更易引起缩釉。
在生产中应合理地设计釉料配方,并保持恰当的颗粒级配以防止缩釉的发生。
在熔块中有过多的B2O3熔剂会导致缩釉。
釉料配方中存在过多比例的生粘土,在烧成时因为其大的收缩能产生缩釉,有时在干燥期间本身出现裂纹,一般釉料中较为理想的生粘土的加入量在10%左右。
如果配方中需要加入较多的粘土时,可通过将其中一部分粘土先进行高温预烧后再加入,以减少过大的收缩。
通过添加碳酸钡,能减少粘土坯体中可溶性盐的作用,阻止缩釉的发生。
1.12 釉与坯之间的结合力有时在釉料与坯体之间不理想的粘接会产生缩釉,如图6所示。
原因可能如下:(1)有釉素坯吸收了更多的釉料,结果形成太厚的釉层,导致在干燥时产生裂纹。
另一方面,瓷化的素坯不能牢固地吸附均匀一致的釉层而使釉与坯之间粘接力较弱,导致烧后产品缩釉。
(2)如果上釉坯体放置很长一段时间后才入窑烧成,会因放置期间发生某些化学反应和细菌作用,导致烧成后产品缩釉。
如果已准备好的釉料存放了很长时间而未使用,那么该釉料的性能可能已经改变,施用这样的釉极易产生缩釉缺陷。
因为有些粘接剂如CMC等在长时间存放后会因化学和细菌的作用而失效。
为了克服这种问题,建议添加醋酸或者是盐酸以及其他防腐剂。