SU 5402_215543-92-3_DataSheet_MedChemExpress
巴斯夫表面活性剂资料
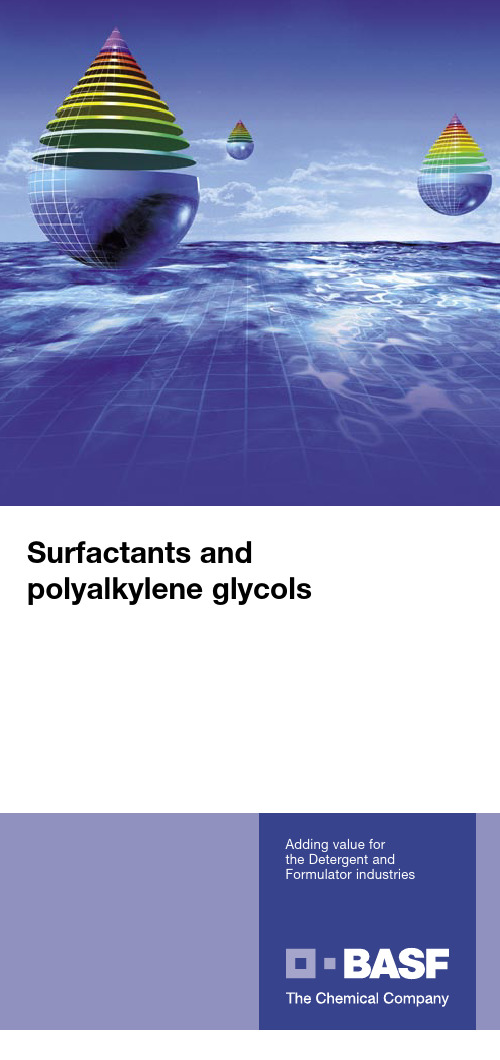
Surfactants and polyalkylene glycolsAdding value forthe Detergent andFormulator industriesNonionic surfactantsProduct Alcohol Active Cloud Physical Viscosity HLBcontent point form [mPa·s] value[%] [°C] [23 °C]Lutensol® A … N types (C12C14Fatty alcohol ethoxylates)Lutensol A 4 N + 4 EO approx. 100 approx. 62 / E Liquid approx. 50 approx. 9 Lutensol A 7 N + 7 EO approx. 100 approx. 56 / A Liquid approx. 150 approx. 12 Lutensol A 79 N + 7 EO approx. 90 approx. 56 / A Liquid approx. 120 approx. 12 Lutensol A 8 + 8 EO approx. 90 approx. 52 / A Liquid approx. 100 approx. 13Lutensol® AT types (C16C18Fatty alcohol ethoxylates)Lutensol AT 11 + 11 EO approx. 100 approx. 87 / A Solid approx. 30 (60 °C) approx. 13 Lutensol AT 18 + 18 EO approx. 100 approx. 92 / B Solid approx. 40 (60 °C) approx. 15 Lutensol AT 18 Solution + 18 EO approx. 20 approx. 92 / B Liquid approx. 30 approx. 15 Lutensol AT 25 Powder + 25 EO approx. 100 approx. 95 / B Powder approx. 70 (60 °C) approx. 16 Lutensol AT 25 E + 25 EO approx. 100 approx. 95 / B Solid approx. 70 (60 °C) approx. 16 Lutensol AT 25 Flakes + 25 EO approx. 100 approx. 95 / B Flakes approx. 70 (60 °C) approx. 16 Lutensol AT 50 Powder + 50 EO approx. 100 approx. 92 / B Powder approx. 150 (60 °C) approx. 18 Lutensol AT 50 E + 50 EO approx. 100 approx. 92 / B Solid approx. 150 (60 °C) approx. 18 Lutensol AT 50 Flakes + 50 EO approx. 100 approx. 92 / B Flakes approx. 150 (60 °C) approx. 18 Lutensol AT 80 Powder + 80 EO approx. 100 approx. 87 / B Powder approx. 400 (60 °C) approx. 18.5 Lutensol AT 80 E + 80 EO approx. 100 approx. 87 / B Solid approx. 400 (60 °C) approx. 18.5 Lutensol AT 80 Flakes + 80 EO approx. 100 approx. 87 / B Flakes approx. 400 (60 °C) approx. 18.5Lutensol® AO types (C13C15Oxo alcohol ethoxylates)Lutensol AO 3 + 3 EO approx. 100 approx. 45 / E Liquid approx. 40 approx. 8 Lutensol AO 5 + 5 EO approx. 100 approx. 62 / E Liquid approx. 80 approx. 10 Lutensol AO 7 + 7 EO approx. 100 approx. 43 / A Liquid approx. 100 approx. 12 Lutensol AO 79 + 7 EO approx. 90 approx. 43 / A Liquid approx. 100 approx. 12 Lutensol AO 8 + 8 EO approx. 100 approx. 52 / A Paste approx. 30 (60 °C) approx. 12.5 Lutensol AO 89 + 8 EO approx. 90 approx. 52 / A Liquid approx. 110 approx. 12.5 Lutensol AO 11 + 11 EO approx. 100 approx. 86 / A Paste approx. 30 (60 °C) approx. 14 Lutensol AO 30 + 30 EO approx. 100 approx. 91 / B Solid approx. 60 (60 °C) approx. 17 Lutensol AO 3109 + 3 / + 10 EO approx. 90 approx. 73 / E Liquid approx. 140 approx. 11.5Lutensol® TO types (C13 Oxo alcohol ethoxylates)Lutensol TO 2 + 2 EO approx. 100 approx. 37 / D Liquid approx. 30 approx. 7 Lutensol TO 3 + 3 EO approx. 100 approx. 40 / E Liquid approx. 50 approx. 8 Lutensol TO 5 + 5 EO approx. 100 approx. 62 / E Liquid approx. 80 approx. 10.5 Lutensol TO 6 + 6 EO approx. 100 approx. 67 / E Liquid approx. 80 approx. 11 Lutensol TO 65 + 6.5 EO approx. 100 approx. 68 / E Liquid approx. 100 approx. 11.5 Lutensol TO 7 + 7 EO approx. 100 approx. 70 / E Liquid approx. 100 approx. 12 Lutensol TO 79 + 7 EO approx. 90 approx. 70 / E Liquid approx. 110 approx. 12 Lutensol TO 8 + 8 EO approx. 100 approx. 60 / A Liquid approx. 150 approx. 13 Lutensol TO 89 + 8 EO approx. 90 approx. 60 / A Liquid approx. 120 approx. 13 Lutensol TO 10 + 10 EO approx. 100 approx. 70 / A Paste approx. 30 (60 °C) approx. 13.5 Lutensol TO 109 + 10 EO approx. 85 approx. 70 / A Liquid approx. 150 approx. 13.5 Lutensol TO 11 + 11 EO approx. 100 approx. 70 / B Paste approx. 30 (60 °C) approx. 14 Lutensol TO 12 + 12 EO approx. 100 approx. 75 / B Solid approx. 40 (60 °C) approx. 14.5 Lutensol TO 129 + 12 EO approx. 85 approx. 75 / B Liquid approx. 200 approx. 14.5 Lutensol TO 15 + 15 EO approx. 100 approx. 80 / B Solid approx. 50 (60 °C) approx. 15.5 Lutensol TO 20 + 20 EO approx. 100 approx. 86 / B Solid approx. 60 (60 °C) approx. 16.5 Lutensol TO 389 + 3 / + 8 EO approx. 90 approx. 70 / E Liquid approx. 100 approx. 12Product Alcohol Active Cloud Physical Viscosity HLBcontent point form [mPa·s] value[%] [°C] [23 °C]Lutensol® XP types (C10-Guerbet alcohol ethoxylate)Lutensol XP 30 + 3 EO approx. 100 approx. 31 / E Liquid approx. 25 approx. 9 Lutensol XP 40 + 4 EO approx. 100 approx. 44 / E Liquid approx. 90 approx. 10.5 Lutensol XP 50 + 5 EO approx. 100 approx. 56 / E Liquid approx. 90 approx. 11.5 Lutensol XP 60 + 6 EO approx. 100 approx. 62 / E Liquid approx. 140 approx. 12.5 Lutensol XP 69 + 6 EO approx. 85 approx. 62 / E Liquid approx. 70 approx. 12.5 Lutensol XP 70 + 7 EO approx. 100 approx. 68 / E Liquid approx. 290 approx. 13 Lutensol XP 79 + 7 EO approx. 85 approx. 68 / E Liquid approx. 90 approx. 13 Lutensol XP 80 + 8 EO approx. 100 approx. 56 / A Liquid approx. 300 approx. 14 Lutensol XP 89 + 8 EO approx. 85 approx. 56 / A Liquid approx. 90 approx. 14 Lutensol XP 90 + 9 EO approx. 100 approx. 69 / A Liquid approx. 1200 approx. 14.5 Lutensol XP 99 + 8 EO approx. 85 approx. 69 / A Liquid approx. 100 approx. 14.5 Lutensol XP 100 + 10 EO approx. 100 approx. 80 / A Paste approx. 30 (60 °C) approx. 15 Lutensol XP 140 + 14 EO approx. 100 approx. 78 / B Paste approx. 40 (60 °C) approx. 16Lutensol® XL types (C10-Guerbet alcohol ethoxylate)Lutensol XL 40 + 4 EO approx. 100 approx. 43 / E Liquid approx. 40 approx. 10.5 Lutensol XL 50 + 5 EO approx. 100 approx. 58 / E Liquid approx. 50 approx. 11.5 Lutensol XL 60 + 6 EO approx. 100 approx. 65 / E Liquid approx. 60 approx. 12.5 Lutensol XL 70 + 7 EO approx. 100 approx. 68 / E Liquid approx. 70 approx. 13 Lutensol XL 79 + 7 EO approx. 85 approx. 68 / E Liquid approx. 120 approx. 13 Lutensol XL 80 + 8 EO approx. 100 approx. 56 / A Liquid approx. 120 approx. 14 Lutensol XL 89 + 8 EO approx. 85 approx. 56 / A Liquid approx. 150 approx. 14 Lutensol XL 90 + 9 EO approx. 100 approx. 69 / A Liquid approx. 30 (60 °C) approx. 14.5 Lutensol XL 99 + 9 EO approx. 80 approx. 69 / A Liquid approx. 160 approx. 14.5 Lutensol XL 100 + 10 EO approx. 100 approx. 80 / A Paste approx. 30 (60 °C) approx. 15 Lutensol XL 140 + 14 EO approx. 100 approx. 78 / B Paste approx. 40 (60 °C) approx. 16 Lutensol® AP types (Alkyl phenol ethoxylates)Lutensol AP 6 + 6 EO approx. 100 approx. 61 / E Liquid approx. 350 approx. 11 Lutensol AP 7 + 7 EO approx. 100 approx. 62 / E Liquid approx. 320 approx. 11 Lutensol AP 8 + 8 EO approx. 100 approx. 34 / A Liquid approx. 320 approx. 12.5 Lutensol AP 9 + 9 EO approx. 100 approx. 51 / A Liquid approx. 300 approx. 13 Lutensol AP 10 + 10 EO approx. 100 approx. 60 / A Liquid approx. 300 approx. 13.5 Lutensol AP 14 + 14 EO approx. 100 approx. 76 / B Liquid approx. 300 approx. 14.5 Lutensol AP 20 + 20 EO approx. 100 approx. 85 / B Solid approx. 70 (60 °C) approx. 16Lutensol® ON types (C10-Oxo alcohol ethoxylates)Lutensol ON 30 + 3 EO approx. 100 approx. 53 / E Liquid approx. 30 approx. 9 Lutensol ON 50 + 5 EO approx. 100 approx. 67 / E Liquid approx. 40 approx. 11.5 Lutensol ON 60 + 6 EO approx. 100 approx. 36 / A Liquid approx. 50 approx. 12 Lutensol ON 66 + 6.5 EO approx. 100 approx. 53 / A Liquid approx. 60 approx. 12.5 Lutensol ON 70 + 7 EO approx. 100 approx. 60 / A Liquid approx. 60 approx. 13 Lutensol ON 80 + 8 EO approx. 100 approx. 80 / A Liquid approx. 100 approx. 14 Lutensol ON 110 + 11 EO approx. 100 approx. 78 / B Paste approx. 30 (60 °C) approx. 15 Lutensol® GD typesLutensol GD 70 Alkyl polyglucoside approx. 70 > 100 / B Liquid approx. 5000Lutensol® F typesLutensol FA 12 Oleyl amine + 12 EO approx. 100 approx. 86 / B Liquid approx. 150Lutensol FA 12 K Coco amine + 12 EO approx. 100 approx. 92 / B Liquid approx. 190Lutensol FA 15 T Tallow amine + 15 EO approx. 100 approx. 97 / B Liquid approx. 240Lutensol FSA 10 Oleic acid amide + 10 EO approx. 100 approx. 85 / E Liquid approx. 300Nonionic low-foam surfactantsProduct Chemical Active Cloud Physical Viscosity Wetting nature content point form [mPa·s] effect[%] [°C] [23 °C]Plurafac® LF typesPlurafac LF 120 Fatty alcohol alkoxylate approx. 100 approx. 28 / A Liquid approx. 45 approx. 25 Plurafac LF 220 Fatty alcohol alkoxylate approx. 95 approx. 42 / A Liquid approx. 90 approx. 30 Plurafac LF 221 Fatty alcohol alkoxylate approx. 95 approx. 33 / A Liquid approx. 80 approx. 30 Plurafac LF 223 Fatty alcohol alkoxylate approx. 98 approx. 33 / E Liquid approx. 60 > 300 Plurafac LF 224 Fatty alcohol alkoxylate approx. 100 approx. 27 / E Liquid approx. 45 > 300 Plurafac LF 226 Fatty alcohol alkoxylate approx. 100 approx. 28 / A Liquid approx. 100 approx. 15 Plurafac LF 300 Fatty alcohol alkoxylate approx. 100 approx. 22 / A Liquid approx. 75 approx. 15 Plurafac LF 301 Fatty alcohol alkoxylate approx. 100 approx. 32 / E Liquid approx. 130 approx. 90 Plurafac LF 303 Fatty alcohol alkoxylate approx. 100 approx. 29 / E Liquid approx. 300 approx. 130 Plurafac LF 305 Fatty alcohol alkoxylate approx. 100 approx. 38 / E Liquid approx. 100 approx. 20 Plurafac LF 400 Fatty alcohol alkoxylate approx. 100 approx. 33 / A Liquid approx. 60 approx. 25 Plurafac LF 401 Fatty alcohol alkoxylate approx. 100 approx. 74 / A Liquid approx. 135 approx. 115 Plurafac LF 403 Fatty alcohol alkoxylate approx. 100 approx. 41 / E Liquid approx. 45 > 300 Plurafac LF 404 Fatty alcohol alkoxylate approx. 100 approx. 45 / E Liquid approx. 45 approx. 70 Plurafac LF 405 Fatty alcohol alkoxylate approx. 95 approx. 55 / E Liquid approx. 70 approx. 100 Plurafac LF 500 Fatty alcohol alkoxylate approx. 100 approx. 32 / E Liquid approx. 60 approx. 60 Plurafac LF 600 Fatty alcohol alkoxylate approx. 100 approx. 55 / A Liquid approx. 90 approx. 65 Plurafac LF 711 Fatty alcohol alkoxylate approx. 100 approx. 45 / E Liquid approx. 55 approx. 25 Plurafac LF 1300 Fatty alcohol alkoxylate approx. 100 approx. 21 / E Liquid approx. 95 > 300 Plurafac LF 1430 Amine alkoxylate approx. 100 approx. 35 / A Liquid approx. 400 > 300Plurafac SLF-18B45 90 %Fatty alcohol alkoxylate approx. 90 approx. 19 / A Liquid approx. 300 approx. 70Plurafac® LF types, end-cappedPlurafac LF 131 Fatty alcohol alkoxylate approx. 100 approx. 35 / E Liquid approx. 30 approx. 30 Plurafac LF 132 Fatty alcohol alkoxylate approx. 100 approx. 30 / E Liquid approx. 20 approx. 75 Plurafac LF 231 Fatty alcohol alkoxylate approx. 100 approx. 28 / E Liquid approx. 40 approx. 50 Plurafac LF 431 Fatty alcohol alkoxylate approx. 100 approx. 39 / E Liquid approx. 40 approx. 30Product EO content Active Cloud Physical Viscosity Molar[%] content point form [mPa·s] mass[%] [°C] [23 °C] [g/mol] Pluronic® PE types (PO/EO block polymers)Pluronic PE 3100 approx. 10 approx. 100 approx. 41 / E Liquid approx. 175 approx. 1000 Pluronic PE 3500 approx. 50 approx. 100 approx. 68 / A Liquid approx. 450 approx. 1900 Pluronic PE 4300 approx. 30 approx. 100 approx. 61 / E Liquid approx. 400 approx. 1750 Pluronic PE 6100 approx. 10 approx. 100 approx. 23 / A Liquid approx. 350 approx. 2000 Pluronic PE 6120 approx. 12 approx. 100 approx. 41 / E Liquid approx. 400 approx. 2100 Pluronic PE 6200 approx. 20 approx. 100 approx. 33 / A Liquid approx. 500 approx. 2450 Pluronic PE 6400 approx. 40 approx. 100 approx. 60 / A Liquid approx. 1000 approx. 2900 Pluronic PE 6800 approx. 80 approx. 100 approx. 88 / B Powder approx. 5000 (60 °C) approx. 8000 Pluronic PE 7400 approx. 40 approx. 100 approx. 60 / A Liquid approx. 1500 approx. 3500 Pluronic PE 8100 approx. 10 approx. 100 approx. 36 / E Liquid approx. 700 approx. 2600 Pluronic PE 9200 approx. 20 approx. 100 approx. 49 / E Liquid approx. 900 approx. 3650 Pluronic PE 9400 approx. 40 approx. 100 approx. 80 / E Solid approx. 300 (60 °C) approx. 4600 Pluronic PE 10100 approx. 10 approx. 100 approx. 35 / E Liquid approx. 800 approx. 3500 Pluronic PE 10300 approx. 30 approx. 100 approx. 71 / E Paste approx. 200 (60 °C) approx. 4950 Pluronic PE 10400 approx. 40 approx. 100 approx. 81 / A Paste approx. 500 (60 °C) approx. 5900 Pluronic PE 10500 approx. 50 approx. 100 approx. 75 / B Solid approx. 500 (60 °C) approx. 6500 Pluronic PE 10500 Solution approx. 50 approx. 18 approx. 75 / B Liquid approx. 10 approx. 6500Product EO content Active Cloud Physical Viscosity Molar[%] content point form [mPa·s] mass[%] [°C] [23 °C] [g/mol] Pluronic® RPE types (EO/PO block polymers)Pluronic RPE 1720 approx. 20 approx. 100 approx. 37 / E Liquid approx. 450 approx. 2150 Pluronic RPE 1740 approx. 40 approx. 100 approx. 51 / E Liquid approx. 600 approx. 2650 Pluronic RPE 2035 approx. 35 approx. 100 approx. 41 / E Liquid approx. 690 (40 °C) approx. 4100 Pluronic RPE 2520 approx. 20 approx. 100 approx. 31 / E Liquid approx. 600 approx. 3100 Pluronic RPE 2525 approx. 25 approx. 100 approx. 38 / E Liquid approx. 400 approx. 2000 Pluronic RPE 3110 approx. 10 approx. 100 approx. 25 / E Liquid approx. 600 approx. 3500 EmulsifiersProduct Chemical Active Cloud Physical Viscosity HLB nature content [%] point [°C] form [23 °C] [mPa·s] value Emulan® typesEmulan A Oleic acid ethoxylate approx. 100 approx. 52 / E Liquid approx. 70Emulan A Oleic acid ethoxylate approx. 100 approx. 52 / E Liquid approx. 70 approx. 11 Emulan AF Fatty alcohol ethoxylate approx. 100 approx. 65 / E Solid approx. 15 (60 °C) approx. 11 Emulan AT 9 Fatty alcohol ethoxylate approx. 100 approx. 68 / A Solid approx. 20 (60 °C) approx. 13 Emulan EL Castor oil ethoxylate approx. 97 approx. 71 / B Liquid approx. 600 (40 °C) approx. 13.5 Emulan EL 40 Castor oil ethoxylate approx. 100 approx. 72 / E Liquid approx. 300 (40 °C) approx. 12 Emulan ELH 60 Castor oil ethoxylate approx. 90 approx. 85 / B Liquid approx. 2500 approx. 16 Emulan EL 200 Powder Castor oil ethoxylate approx. 100 > 100 / A Powder approx. 200 (70 °C) approx. 18 Emulan ELP Castor oil ethoxylate approx. 100 approx. 51 / E Liquid approx. 700 approx. 7 Emulan LVA Oxo alcohol ethoxylate approx. 85 approx. 56 / A Liquid approx. 90 approx. 14 Emulan NP 3070 Alkylphenol ethoxylate approx. 70 approx. 90 / B Liquid approx. 1050 approx. 17 Emulan OC Fatty alcohol ethoxylate approx. 100 approx. 90 / B Solid approx. 60 (60 °C) approx. 17 Emulan OC Solution Fatty alcohol ethoxylate approx. 30 approx. 90 / B Liquid approx. 30 approx. 17 Emulan OG Fatty alcohol ethoxylate approx. 100 approx. 92 / B Powder approx. 80 (60 °C) approx. 17 Emulan OP 25 Alkylphenol ethoxylate approx. 100 approx. 88 / B Solid approx. 100 (60 °C) approx. 17 Emulan OU Fatty alcohol ethoxylate approx. 100 approx. 90 / B Solid approx. 60 (60 °C) approx. 17 Emulan P Fatty alcohol ethoxylate approx. 100 approx. 52 / E Liquid approx. 30 approx. 11 Emulan PO Alkylphenol ethoxylate approx. 100 approx. 46 / E Liquid approx. 300 approx. 11 Emulan TO 2080 C13 Oxo alcohol ethoxylate approx. 80 approx. 93 / B Liquid approx. 400 approx. 16 Emulan TO 3070 C13 Oxo alcohol ethoxylate approx. 70 approx. 91 / B Liquid approx. 1500 approx. 17 Emulan TO 4070 C13 Oxo alcohol ethoxylate approx. 70 approx. 91 / B Liquid approx. 1400 approx. 18 Emulan XCA 23 Polyisobutene derivative approx. 70 – Liquid approx. 3600 (40 °C) –Emulphor® typesEmulphor OPS 25 Sodium octylphenol approx. 34 Liquid approx. 60polyglycol ether sulphateEmulphor NPS 25 Sodium nonylphenol approx. 31 Liquid approx. 100polyglycol ether sulphateEmulphor FAS 30 Sodium fatty alcohol approx. 30 Liquid approx. 100polyglycol ether sulphateSolubiliserProduct Chemical Active Cloud Physical Viscositynature content [%] point [°C] form [mPa·s]Emulan HE 50 Hexanol ethoxylate approx. 100 approx. 72 / B Liquid approx. 25Emulan HE S104 Alcohol alkoxylate approx. 100 approx. 56 / E Liquid approx. 45AminopolyolQuadrol L Ethylene diamine+4 PO approx. 100 LiquidIonic surfactantsProduct Concentration Physical form Chemical nature[%] [23 °C]Lutensit® typesLutensit A-BO approx. 60 Liquid Sodium dioctylsulphosuccinateLutensit A-EP approx. 100 Liquid Acid phosphoric esterLutensit A-ES approx. 40 Liquid Sodium alkylphenol ether sulphateLutensit A-FK approx. 55 Liquid Sodium fatty acid condensation productLutensit A-LBA approx. 55 Liquid Amine salt of dodecylbenzenesulphonateLutensit A-LBS approx. 98 Liquid Dodecylbenzenesulphonic acidLutensit AN 10 approx. 100 Liquid Anionic/nonionic surfactant combination based on APEO Lutensit AN 30 approx. 100 Liquid Anionic/nonionic surfactant combination based on fattyalcohol ethoxylateLutensit AN 40 approx. 70 Liquid Mixture of nonionic surfactants with alkyl carboxylic acids Lutensit AN 45 approx. 80 Liquid Mixture of nonionic surfactants with alkyl carboxylic acids Lutensit AN 50 approx. 100 Liquid Anionic/nonionic surfactant combination based on fattyalcohol ethoxylateNekal® typesNekal BX Dry approx. 68 Powder Sodium alkylnaphthalene sulphonateNekal BX Conc. Paste approx. 60 Paste Sodium alkylnaphthalene sulphonateNekal BX Conc. Paste 40 % approx. 34 Paste Sodium alkylnaphthalene sulphonateNekal BX 30 % approx. 22 Liquid Sodium alkylnaphthalene sulphonateNekal SBC approx. 72 Liquid Alkylnaphthalene sulphonic acidCorrosion inhibitorsKorantin® typesKorantin BH Solid > 98 Solid 2-Butyne-1,4-diolKorantin BH 50 approx. 50 Liquid 2-Butyne-1,4-diolKorantin LUB approx. 100 Liquid Acid phosphoric ester of a polyetherKorantin MAT approx. 100 Liquid Alkanolamine salt of a nitrogenous organic acidKorantin PAT approx. 80 Liquid Alkanolamine salt of a nitrogenous organic acidKorantin PM > 99.5 Liquid Propargyl alcohol alkoxylateKorantin PP approx. 67 Liquid Propargyl alcohol alkoxylateKorantin SMK approx. 100 Liquid Phosphoric acid monoesterFoam depressorsProduct Chemical Physical form Viscosity Concentration nature [23 °C] [m·Pas] [%] Degressal® typesDegressal SD 20 Fatty alcohol alkoxylate Liquid approx. 60 100 Degressal SD 21 Fatty alcohol alkoxylate Liquid approx. 250 100 Degressal SD 23 Alcohol alkoxylate Liquid approx. 800 100 Degressal SD 30 Carboxylic acid ester Liquid approx. 20 100 Degressal SD 40 Phosphoric acid ester Liquid approx. 20 100Polyalkylene glycolsProduct Unsaturated Physical form Viscosity at 20 °C Iodine numberalcohol [23 °C] [mm2/s]Pluriol® A … R types (Reactive polyalkylene glycols)Pluriol A 010 R Allyl alcohol ethoxylate Liquid approx. 55 approx. 50Pluriol A 11 RE Allyl alcohol alkoxylate Liquid approx. 500 approx. 12Pluriol A 13 R Allyl alcohol alkoxylate Liquid approx. 150 approx. 20Pluriol A 22 R Allyl alcohol alkoxylate Liquid approx. 300 approx. 13Pluriol A 23 R Allyl alcohol alkoxylate Liquid approx. 60 approx. 43Pluriol A 308 R Butyne diol ethoxylate Liquid approx. 175 approx. 14 Product Molar mass Physical form Viscosity at 20 °C Melting point[g/mol] [23 °C] [mm2/s] [°C]Pluriol® A … E types (Methyl polyethylene glycols)Pluriol A 350 E approx. 350 Liquid approx. 30 –Pluriol A 500 E approx. 500 Liquid approx. 60 –Pluriol A 750 E* approx. 750 Solid approx. 30 (50 °C) approx. 35Pluriol A 760 E approx. 750 Solid approx. 30 (50 °C) approx. 35Pluriol A 1000 E approx. 1000 Solid approx. 60 (50 °C) approx. 40Pluriol A 1020 E* approx. 1000 Solid approx. 60 (50 °C) approx. 40Pluriol A 2000 E approx. 2000 Solid approx. 120 (50 °C) approx. 54Pluriol A 3010 E* approx. 3000 Solid approx. 160 (70 °C) approx. 59Pluriol A 5010 E* approx. 5000 Solid approx. 200 (100 °C) approx. 62 * = not filtratedProduct Molar mass Physical form Viscosity at 20 °C Viscosity[g/mol] [23 °C] [mm2/s] [mm2/s]Pluriol® A … PE types (Alkyl polyalkylene glycol copolymers)Pluriol A 1000 PE approx. 1000 Liquid approx. 50 approx. 11 (100 °C) Pluriol A 1320 PE* approx. 1400 Liquid approx. 180 approx. 20 (100 °C) Pluriol A 2000 PE approx. 2000 Liquid approx. 250 approx. 28 (100 °C) Pluriol A 2020 PE* approx. 2000 Liquid approx. 250 approx. 28 (100 °C) * = not filtratedPluriol® A … P types (Alkyl polypropylene glycols)Pluriol A 1350 P approx. 1350 Liquid approx. 195 approx. 85 (40 °C) Pluriol A 2000 P approx. 2000 Liquid approx. 500 approx. 180 (40 °C) Pluriol® A … TE types (Polyfunctional polyalkylene glycols)Pluriol A 3 TE approx. 275 Liquid approx. 1000 approx. 230 (40 °C) Pluriol A 15 TE approx. 800 Liquid approx. 400 approx. 140 (40 °C) Pluriol A 15 TERC approx. 800 Liquid approx. 400 approx. 140 (40 °C) Pluriol A 18 TERC approx. 900 Liquid approx. 430 approx. 150 (40 °C) Reactive solventsProduct Bisphenol A Physical form Active Viscosity[23 °C] content (%) [mm2/s]Pluriol® BP …E types (Bisphenol A ethoxylates)Pluriol BP 30 E + 3 EO Liquid approx. 100 approx. 450 (60 °C) Pluriol BP 40 E + 4 EO Liquid approx. 100 approx. 580 (50 °C) Pluriol BP 60 E + 6 EO Liquid approx. 100 approx. 680 (40 °C) Pluriol BP 100 E + 10 EO Liquid approx. 100 approx. 400 (40 °C)Product Molar mass Physical form Viscosity at 75 °C Melting point [g/mol] [23 °C] [mm2/s] [°C]Pluriol® E types (Polyethylene glycols) / Technical gradePluriol E 200 approx. 200 Liquid approx. 60 (20 °C)Pluriol E 300 approx. 300 Liquid approx. 85 (20 °C)Pluriol E 400 approx. 400 Liquid approx. 110 (20 °C)Pluriol E 600 approx. 600 Liquid approx. 40 (50 °C) approx. 20 Pluriol E 1000 approx. 1000 Paste approx. 30 approx. 40 Pluriol E 1500 E approx. 1500 Solid approx. 60 approx. 45 Pluriol E 1500 Powder approx. 1500 Powder approx. 60 approx. 45 Pluriol E 1500 Flakes approx. 1500 Flakes approx. 60 approx. 45 Pluriol E 3400 E approx. 3400 Solid approx. 200 approx. 55 Pluriol E 3400 Powder approx. 3400 Powder approx. 200 approx. 55 Pluriol E 3400 Flakes approx. 3400 Flakes approx. 200 approx. 55 Pluriol E 4000 E approx. 4000 Solid approx. 260 approx. 55 Pluriol E 4000 Powder approx. 4000 Powder approx. 260 approx. 55 Pluriol E 4000 Flakes approx. 4000 Flakes approx. 260 approx. 55 Pluriol E 6000 E approx. 6000 Solid approx. 600 approx. 60 Pluriol E 6000 Powder approx. 6000 Powder approx. 600 approx. 60 Pluriol E 6000 Flakes approx. 6000 Flakes approx. 600 approx. 60 Pluriol E 8000 E approx. 8000 Solid approx. 1500 approx. 63 Pluriol E 8000 Flakes approx. 8000 Flakes approx. 1500 approx. 63 Pluriol E 9000 Powder approx. 9000 Powder approx. 2500 approx. 65 Pluriol E 9000 Flakes approx. 9000 Flakes approx. 2500 approx. 65 Product Molar mass Physical form Viscosity at 100 °C[g/mol] [23 °C] [mm2/s]Pluriol® E types (Polyethylene glycols) / CARE grade*Pluriol E 205 approx. 200 Liquid approx. 4Pluriol E 305 approx. 300 Liquid approx. 5Pluriol E 405 approx. 400 Liquid approx. 6.5Pluriol E 605 approx. 600 Liquid approx. 10Pluriol E 1505 E approx. 1500 Solid approx. 30Pluriol E 1505 Flakes approx. 1500 Flakes approx. 30Pluriol E 3405 E approx. 3400 Solid approx. 85Pluriol E 3405 Flakes approx. 3400 Flakes approx. 85Pluriol E 4005 E approx. 4000 Solid approx. 110Pluriol E 4005 Flakes approx. 4000 Flakes approx. 110Pluriol E 6005 E approx. 6000 Solid approx. 350Pluriol E 6005 Flakes approx. 6000 Flakes approx. 350Pluriol E 8005 E approx. 8000 Solid approx. 600Pluriol E 8005 Flakes approx. 8000 Flakes approx. 600* Meets the monograph requirements of the current European and American PharmacopoeiaProduct Molar mass Physical form Viscosity at 20 °C Viscosity at 40 °C [g/mol] [23 °C] [mm2/s] [mm2/s]Pluriol® P types (Polypropylene glycols)Pluriol P 400 approx. 430 Liquid approx. 95 approx. 20Pluriol P 600 approx. 600 Liquid approx. 130 approx. 40Pluriol P 900 approx. 900 Liquid approx. 180 approx. 60Pluriol P 2000 approx. 2000 Liquid approx. 440 approx. 150 Pluriol P 4000 approx. 4000 Liquid approx. 1050 approx. 350。
Gelucire-14-44-SDS-MedChemExpress

Inhibitors, Agonists, Screening LibrariesSafety Data Sheet Revision Date:Nov.-23-2018Print Date:Nov.-23-20181. PRODUCT AND COMPANY IDENTIFICATION1.1 Product identifierProduct name :Gelucire 14/44Catalog No. :HY-Y1892CAS No. :121548-04-71.2 Relevant identified uses of the substance or mixture and uses advised againstIdentified uses :Laboratory chemicals, manufacture of substances.1.3 Details of the supplier of the safety data sheetCompany:MedChemExpress USATel:609-228-6898Fax:609-228-5909E-mail:sales@1.4 Emergency telephone numberEmergency Phone #:609-228-68982. HAZARDS IDENTIFICATION2.1 Classification of the substance or mixtureNot a hazardous substance or mixture.2.2 GHS Label elements, including precautionary statementsNot a hazardous substance or mixture.2.3 Other hazardsNone.3. COMPOSITION/INFORMATION ON INGREDIENTS3.1 SubstancesSynonyms:NoneFormula:N/AMolecular Weight:N/ACAS No. :121548-04-74. FIRST AID MEASURES4.1 Description of first aid measuresEye contactRemove any contact lenses, locate eye-wash station, and flush eyes immediately with large amounts of water. Separate eyelids with fingers to ensure adequate flushing. Promptly call a physician.Skin contactRinse skin thoroughly with large amounts of water. Remove contaminated clothing and shoes and call a physician.InhalationImmediately relocate self or casualty to fresh air. If breathing is difficult, give cardiopulmonary resuscitation (CPR). Avoid mouth-to-mouth resuscitation.IngestionWash out mouth with water; Do NOT induce vomiting; call a physician.4.2 Most important symptoms and effects, both acute and delayedThe most important known symptoms and effects are described in the labelling (see section 2.2).4.3 Indication of any immediate medical attention and special treatment neededTreat symptomatically.5. FIRE FIGHTING MEASURES5.1 Extinguishing mediaSuitable extinguishing mediaUse water spray, dry chemical, foam, and carbon dioxide fire extinguisher.5.2 Special hazards arising from the substance or mixtureDuring combustion, may emit irritant fumes.5.3 Advice for firefightersWear self-contained breathing apparatus and protective clothing.6. ACCIDENTAL RELEASE MEASURES6.1 Personal precautions, protective equipment and emergency proceduresUse full personal protective equipment. Avoid breathing vapors, mist, dust or gas. Ensure adequate ventilation. Evacuate personnel to safe areas.Refer to protective measures listed in sections 8.6.2 Environmental precautionsTry to prevent further leakage or spillage. Keep the product away from drains or water courses.6.3 Methods and materials for containment and cleaning upAbsorb solutions with finely-powdered liquid-binding material (diatomite, universal binders); Decontaminate surfaces and equipment by scrubbing with alcohol; Dispose of contaminated material according to Section 13.7. HANDLING AND STORAGE7.1 Precautions for safe handlingAvoid inhalation, contact with eyes and skin. Avoid dust and aerosol formation. Use only in areas with appropriate exhaust ventilation.7.2 Conditions for safe storage, including any incompatibilitiesKeep container tightly sealed in cool, well-ventilated area. Keep away from direct sunlight and sources of ignition.Recommended storage temperature:Pure form-20°C 3 years4°C 2 yearsIn solvent-80°C 6 months-20°C 1 monthShipping at room temperature if less than 2 weeks.7.3 Specific end use(s)No data available.8. EXPOSURE CONTROLS/PERSONAL PROTECTION8.1 Control parametersComponents with workplace control parametersThis product contains no substances with occupational exposure limit values.8.2 Exposure controlsEngineering controlsEnsure adequate ventilation. Provide accessible safety shower and eye wash station.Personal protective equipmentEye protection Safety goggles with side-shields.Hand protection Protective gloves.Skin and body protection Impervious clothing.Respiratory protection Suitable respirator.Environmental exposure controls Keep the product away from drains, water courses or the soil. Cleanspillages in a safe way as soon as possible.9. PHYSICAL AND CHEMICAL PROPERTIES9.1 Information on basic physical and chemical propertiesAppearance White to off-white (Oil)Odor No data availableOdor threshold No data availablepH No data availableMelting/freezing point No data availableBoiling point/range No data availableFlash point No data availableEvaporation rate No data availableFlammability (solid, gas)No data availableUpper/lower flammability or explosive limits No data availableVapor pressure No data availableVapor density No data availableRelative density No data availableWater Solubility No data availablePartition coefficient No data availableAuto-ignition temperature No data availableDecomposition temperature No data availableViscosity No data availableExplosive properties No data availableOxidizing properties No data available9.2 Other safety informationNo data available.10. STABILITY AND REACTIVITY10.1 ReactivityNo data available.10.2 Chemical stabilityStable under recommended storage conditions.10.3 Possibility of hazardous reactionsNo data available.10.4 Conditions to avoidNo data available.10.5 Incompatible materialsStrong acids/alkalis, strong oxidising/reducing agents.10.6 Hazardous decomposition productsUnder fire conditions, may decompose and emit toxic fumes.Other decomposition products - no data available.11.TOXICOLOGICAL INFORMATION11.1 Information on toxicological effectsAcute toxicityClassified based on available data. For more details, see section 2Skin corrosion/irritationClassified based on available data. For more details, see section 2Serious eye damage/irritationClassified based on available data. For more details, see section 2Respiratory or skin sensitizationClassified based on available data. For more details, see section 2Germ cell mutagenicityClassified based on available data. For more details, see section 2CarcinogenicityIARC: No component of this product present at a level equal to or greater than 0.1% is identified as probable, possible or confirmed human carcinogen by IARC.ACGIH: No component of this product present at a level equal to or greater than 0.1% is identified as a potential or confirmed carcinogen by ACGIH.NTP: No component of this product present at a level equal to or greater than 0.1% is identified as a anticipated or confirmed carcinogen by NTP.OSHA: No component of this product present at a level equal to or greater than 0.1% is identified as a potential or confirmed carcinogen by OSHA.Reproductive toxicityClassified based on available data. For more details, see section 2Specific target organ toxicity - single exposureClassified based on available data. For more details, see section 2Specific target organ toxicity - repeated exposureClassified based on available data. For more details, see section 2Aspiration hazardClassified based on available data. For more details, see section 212. ECOLOGICAL INFORMATION12.1 ToxicityNo data available.12.2 Persistence and degradabilityNo data available.12.3 Bioaccumlative potentialNo data available.12.4 Mobility in soilNo data available.12.5 Results of PBT and vPvB assessmentPBT/vPvB assessment unavailable as chemical safety assessment not required or not conducted.12.6 Other adverse effectsNo data available.13. DISPOSAL CONSIDERATIONS13.1 Waste treatment methodsProductDispose substance in accordance with prevailing country, federal, state and local regulations.Contaminated packagingConduct recycling or disposal in accordance with prevailing country, federal, state and local regulations.14. TRANSPORT INFORMATIONDOT (US)This substance is considered to be non-hazardous for transport.IMDGThis substance is considered to be non-hazardous for transport.IATAThis substance is considered to be non-hazardous for transport.15. REGULATORY INFORMATIONSARA 302 Components:No chemicals in this material are subject to the reporting requirements of SARA Title III, Section 302.SARA 313 Components:This material does not contain any chemical components with known CAS numbers that exceed the threshold (De Minimis) reporting levels established by SARA Title III, Section 313.SARA 311/312 Hazards:No SARA Hazards.Massachusetts Right To Know Components:No components are subject to the Massachusetts Right to Know Act.Pennsylvania Right To Know Components:No components are subject to the Pennsylvania Right to Know Act.New Jersey Right To Know Components:No components are subject to the New Jersey Right to Know Act.California Prop. 65 Components:This product does not contain any chemicals known to State of California to cause cancer, birth defects, or anyother reproductive harm.16. OTHER INFORMATIONCopyright 2018 MedChemExpress. The above information is correct to the best of our present knowledge but does not purport to be all inclusive and should be used only as a guide. The product is for research use only and for experienced personnel. It must only be handled by suitably qualified experienced scientists in appropriately equipped and authorized facilities. The burden of safe use of this material rests entirely with the user. MedChemExpress disclaims all liability for any damage resulting from handling or from contact with this product.Caution: Product has not been fully validated for medical applications. For research use only.Tel: 609-228-6898 Fax: 609-228-5909 E-mail: tech@Address: 1 Deer Park Dr, Suite Q, Monmouth Junction, NJ 08852, USA。
TSKgel Butyl-NPR supplemental instructions说明书

*1 : Linear gradient 0 to 100 B% 10 min.
25 mmol/L Sodium sulfate
0.5
3 g/L Glycine 5 µL
215
11-2 Quality Specifications
Cat. No.
Types
54,HFM#VUZM/13 54,HFM#VUZM/13
.BY'MPX3BUF N-NJO
1.2
1.0
3FDPNNFOEFE 'MPX3BUF N-NJO
.BY1SFTTVSF%SP Column / In-line filter There is no guard column for TSKgel Butyl-NPR columns. Please install an in-line filter between the injection valve and the feed pump to prevent small particles and impurities in the mobile phase from entering the column. The filter will also need to be replaced if a pressure increase is observed.
Cat. No.
Types
Column Dimensions (mm ID × cm)
54,HFM#VUZM/13 4.6 × 3.5
Eluent
A) 1.8 mol/L Ammonium sulfate in 0.1 mol/L Sodium phosphate (pH 7.0)*1
Standard Specification for

Designation:F1839–08´1Standard Specification forRigid Polyurethane Foam for Use as a Standard Material for Testing Orthopaedic Devices and Instruments1This standard is issued under thefixed designation F1839;the number immediately following the designation indicates the year of original adoption or,in the case of revision,the year of last revision.A number in parentheses indicates the year of last reapproval.A superscript epsilon(´)indicates an editorial change since the last revision or reapproval.´1N OTE—Units information was editorially corrected in August2009.1.Scope1.1This specification covers rigid unicellular polyurethane foam for use as a standard material for performing mechanical tests utilizing orthopaedic devices or instruments.The specifi-cation is applicable to sheets or blocks of foam,or foam that is made by the user using a two-part liquid mixture.1.2This specification covers polyurethane foam material that is used in the laboratory for mechanical testing,as described in1.1.These materials are not intended for implan-tation into the human body.1.3The foam described herein possesses mechanical prop-erties which are on the order of those reported for human cancellous bone.See Appendix X1Rationale for further information regarding the appropriateness of using the speci-fied foam as a model for human cancellous bone.1.4This specification covers compositional requirements, physical requirements,mechanical requirements,and test methods for rigid polyurethane foam in the solidfinal form.1.5This specification provides qualification criteria for vendor or end-user processes and acceptance criteria for individual material lots.1.6This specification provides mechanical properties offive different grades of foam in the solidfinal form.A foam that does not meet the specified mechanical properties shall be identified as an ungraded foam.1.7The values stated in SI units are to be regarded as standard.No other units of measurement are included in this standard.1.8The following precautionary statement pertains to the test method portion only,Section8,of this specification:This standard does not purport to address all of the safety concerns, if any,associated with its use.It is the responsibility of the user of this standard to establish appropriate safety and health practices and determine the applicability of regulatory limita-tions prior to use.2.Referenced Documents2.1ASTM Standards:2C273Test Method for Shear Properties of Sandwich Core MaterialsD1621Test Method for Compressive Properties Of Rigid Cellular PlasticsD1622Test Method for Apparent Density of Rigid Cellular PlasticsE4Practices for Force Verification of Testing MachinesF543Specification and Test Methods for Metallic Medical Bone Screws3.Terminology3.1Definitions:3.1.1final form—the condition of the foam product when used by the end user to perform tests of orthopaedic devices or instruments.3.1.1.1Discussion—This is the condition of the foam prod-uct of which all physical and mechanical tests required by this specification are performed.3.1.1.2solid—the foam is in a uniform solid form,such asa slab,plate,or block.3.1.2foam rise direction—the nominal direction that the foam rises during the polymerization(“foaming”)process, either at the supplier’s production facilities for the solid supplied foam,or at the end-user’s facilities for foam produced from the liquid supplied form.The foam rise direction shall be marked on the foam block or indicated in the shipping documentation for foam that is supplied in the solid form. 3.1.3grades—The grade designation refers to the nominal density of the foam,in its solidfinal form,expressed in units of kg/m3.Ten grades of foam have been defined in this specification.Their nominal densities are:Grade5:80.1kg/m3Grade10:160.2kg/m3Grade12:192.2kg/m3Grade15:240.3kg/m31This specification is under the jurisdiction of ASTM Committee F04on Medical and Surgical Materials and Devices and is the direct responsibility ofSubcommittee F04.21on Osteosynthesis.Current edition approved Nov.15,2008.Published December2008.Originally approved st previous edition approved in2007as F1839–01(2007). DOI:10.1520/F1839-08E01.2For referenced ASTM standards,visit the ASTM website,,or contact ASTM Customer Service at service@.For Annual Book of ASTM Standards volume information,refer to the standard’s Document Summary page on the ASTM website.Copyright.(C)ASTM International.100Barr Harbour Dr.,PO box C-700West Conshohocken,Pennsylvania19428-2959,United StatesGrade20:320.4kg/m3Grade25:400.5kg/m3Grade30:480.5kg/m3Grade35:560.6kg/m3Grade40:640.7kg/m3Grade50:800.9kg/m3Foam that does notfit into one of these ten grades because it does not meet one or more of the physical requirements of Section4is termed ungraded.3.1.3.1Discussion—Grade5designates the nominal value of5lbm/ft3.3.1.4supplied form—the condition of the foam product when received from the supplier by the end user.3.1.4.1Discussion—The supplied form may be a solid or a liquid.The foam may be in a uniform solid form such as a slab, plate,or block or a liquid in which two liquid components (base and activator)can be mixed by the end user to producea rigid,unicellular foam slab.4.Physical and Mechanical Requirements4.1Composition—The material shall be supplied either in solid or liquid form.The solid or combined liquid parts shall produce a foam consisting of polyether polyurethane.4.2Appearance:4.2.1Solid Supplied Form—The solid foam slab shall be free of obvious extraneous matter,and appear to the unaided eye to be uniform throughout the slab in color and porosity.4.2.2Liquid Supplied Form—The two liquid components shall appear to the unaided eye throughout their volumes to be uniform and free from obvious extraneous matter or particulate debris.4.2.3Solid Final Form—The solid foam slab shall be free of obvious extraneous matter,and appear to the unaided eye to be uniform throughout the slab in color and porosity.4.3Void Content—The material in the solidfinal form shall meet the requirements of Table1for voids,cracks and nonuniform areas,when examined using the procedures de-scribed in8.1.All specimens shall meet this requirement.4.4Density—The material in the solidfinal form shall havea density within the ranges specified in Table2,according to the foam’s grade specification.The density shall be determined using the method described in8.2.All specimens shall meet this requirement.4.5Dimensional Stability—The material in the solidfinal form shall have an average percentage thickness change less than5.0%,when tested according to the method described in 8.3.4.6Compressive Strength—The material in the solidfinal form shall meet the compressive strength requirements given in Table3,when tested according to the method described in8.4. All specimens shall meet this requirement.4.7Compressive Modulus—The material in the solidfinal form shall meet the compressive modulus requirements givenin Table4,when tested according to the method described in 8.4.All specimens shall meet this requirement.4.8Shear Strength—The material in the solidfinal form shall meet the shear strength requirements given in Table5, when tested according to the method described in8.5.All specimens shall meet this requirement.4.9Shear Modulus—The material in the solidfinal form shall meet the shear modulus requirements given in Table6, when tested according to the method described in8.5.All specimens shall meet this requirement.4.10Screw Pullout—The material in the solidfinal form shall meet the screw pullout requirements given in Table7, TABLE1Requirements for Voids,Cracks,and Nonuniform Areas Defects RequirementsVoidsVoid depth(measured perpendicularto slab’s transverse plane)Void depth shall be less than50%ofthe slab thickness,and less than6.35mmVoid diameter(measured parallel toslab’s transverse plane)Larger than6.35mm None allowed in any gradeBetween3.18mmand6.35mmNo more than10allowed per230cm2surface area for Grades5and10.No more than1allowed forGrades12,15,20,25,30,and35.None allowed for Grades40and50.Between1.57mmand3.18mmNo more than20allowed per230cm2surface area for Grades5and10.No more than6allowed forGrades12,15,20,25,30,and35.No more than3allowed for Grades40and50.Cracks None allowedNon-uniform areas Concentrated areas of poorconstruction,irregular cells,and hardand soft spots shall not exceed10%of the visible surface areaTABLE2Grade Designation and DensityGradeMinimum Density,kg/m3Maximum Density,kg/m3572.1088.1010144.0176.012173.0211.515216.0264.520288.5352.525360.5440.530432.5528.535504.5617.040576.5705.050721.0881.0TABLE3Requirements for Compressive StrengthGradeMinimumCompressiveStrength,MPaMaximumCompressiveStrength,MPa50.44950.780010 1.745 2.82012 2.485 3.97015 3.820 6.05020 6.63010.452510.1516.003014.3022.703519.1530.554024.6039.555037.3561.05when tested according to the method described in8.6.All specimens shall meet this requirement.5.Significance and Use5.1This specification describes the compositional require-ments,physical requirements,mechanical requirements,and test methods for rigid unicellular polyurethane foam for use in testing orthopaedic devices or instruments.5.2This foam described in this specification is not intended to replicate the mechanical properties of human or animal bone.The requirements of this specification are intended to provide a consistent and uniform material with properties on the order of human cancellous bone to use as a test medium when testing various orthopaedic devices,such as bone screws.6.Apparatus6.1Analytical Balance or Scale—capable of weighing foam specimens to the nearest mg.6.2Micrometer Dial Gage or Caliper—capable of measur-ing dimensions of the foam specimens to60.1%.6.3Conditioning Oven—Forced-air circulating oven ca-pable of maintaining12162.8°C for24h.6.4Desiccator—containing desiccant with high affinity for water vapor(anhydrous calcium chloride or equivalent).6.5Vacuum Apparatus—capable of applying a vacuum pressure of508mm(20in.)of mercury to foam specimen for dimensional stability test.6.6Testing Machine and Load Cell—conforming to Prac-tices E4and capable of applying tensile and compressive loads at a constant displacement rate.7.Sampling and Test Specimens7.1The number of test specimens and the specimen sizes required for physical characterization and mechanical testing are described in8.1-8.6.Test specimens are required for each grade and formulation.7.2Test specimens shall be solid foam blocks.The short-transverse direction of the specimens shall coincide with the foam rise direction of the original foam bun.8.Procedure8.1Determination of Void Content:8.1.1Use the foam block specimens described and specified in8.2-8.6.8.1.2Examine all of the surfaces and edges of test speci-mens for voids and nonuniform areas with the unaided eye. Measure the dimensions of the void or nonuniform areas using an instrument capable of measuring60.025mm.8.2Determination of Foam Density:8.2.1Prepare three specimens,25.4by25.4by25.4mm from solid foam.8.2.2Determine the apparent density of the three foam specimens,in kg/m3,in accordance with Test Method D1622.8.2.3Calculate the average apparent density of the three foam specimens.8.3Determination of Dimensional Stability:TABLE4Requirements for Compressive ModulusGradeMinimumCompressiveModulus,MPaMaximumCompressiveModulus,MPa512.3020.35 1045.7571.70 1264.50100.5 1598.00151.0 20167.5257.5 25253.5390.0 30355.5548.5 35472.0732.0 40603.0941.0 50907.51435 TABLE5Requirements for Shear StrengthGradeMinimumShear Strength,MPaMaximumShear Strength,MPa50.4200.805 10 1.225 2.010 12 1.610 2.580 15 2.235 3.510 20 3.395 5.275 25 4.6657.275 30 6.0259.495 357.46011.95 408.96014.55 5012.1020.40 TABLE6Requirements for Shear ModulusGradeMinimumShear Modulus,kPaMaximumShear Modulus,kPa5 5.4609.000 1015.1522.75 1219.7029.20 1527.1039.70 2040.7559.25 2555.7081.15 3071.70105.0 3588.65131.0 40106.5159.0 50144.0220.0TABLE7Requirements for Screw Pullout GradeMinimumPullout,NMaximumPullout,N 556.00176.0 10220.0453.0 12309.5592.5 15464.5831.0 20770.01310 2511251890 3015202570 3519503355 4024004245 50338063508.3.1Prepare three specimens,25.4by25.4by12.7mm from solid foam.8.3.2Condition the specimen for24h at2162.8°C and 50610%relative humidity.Measure the specimen thickness near the center of the length to60.025mm and mark the location of the measurement.8.3.3Place the specimen on a6.35-mm thick aluminum plate and apply a minimum vacuum pressure of508mm of mercury under a vacuum bag or diaphragm.Place this assem-bly in a circulating forced-air oven for not less than2h at121 62.8°C.Remove the assembly and allow to cool to49°C or less while maintaining the vacuum.8.3.4Recondition and remeasure the thickness at the marked location in accordance with8.3.2.Calculate the per-cent thickness change.8.3.5Calculate the average percent thickness change of the three specimens.8.4Determination of Compressive Strength and Modulus: 8.4.1Preparefive specimens,50.8by50.8by25.4mm, from solid foam,with the thickness of the specimen parallel to the foam rise direction.Measure the dimensions within 60.025mm.The specimens shall be conditioned at246 2.8°C for3h prior to testing.8.4.2Test in accordance with Test Method D1621at246 2.8°C.The specimens shall be oriented such that the axis of the compressive load is applied parallel to the foam rise direction.8.4.3Determine the compressive strength using ProcedureA of Test Method D1621and the maximum compressive modulus for each specimen.8.4.4Calculate the average compressive strength and modu-lus of thefive specimens.8.5Determination of Shear Strength and Modulus:8.5.1Preparefive specimens,76.2by25.4by6.35mm, from solid foam,with the thickness of the specimen parallel to the foam rise direction.Measure the dimensions within 60.025mm.The specimens shall be conditioned at246 2.8°C for3h before testing.8.5.2Bond the edges of the foam specimen directly to the shear plates with an appropriate adhesive,such as an epoxy,so that the foam rise direction is perpendicular to the plane of maximum shear stress.8.5.3Test in accordance with Test Method C273.8.5.4Determine the shear strength and shear modulus for each specimen.8.5.5Calculate the average shear strength and modulus of thefive specimens.8.6Determination of Screw Pullout Strength8.6.1Preparefive specimens,50.8by50.8by25.4mm, from solid foam,with the thickness of the specimen parallel to the foam rise direction.8.6.2Obtainfive steel screws or threaded tools that meet the thread requirements given in Specification F543,Annex4. Grades5,10,12,15,20,and25shall use screws or threaded tools with the thread form of HB6.5screws(see Table A4.4of Specification F543,Annex4),while Grades30,35,40,and50 shall utilize screws or threaded tools with the thread form of HA4.5screws(see Table A4.2of Specification F543,Annex 4).8.6.3Drill a 3.2-mm hole in the center of each foam specimen,parallel to the thickness direction.The hole shall be positioned a minimum of10mm from any void or nonuniform area.Tap the hole to a minimum depth of25.4mm using a tap that corresponds to HB6.5or HA4.5,as appropriate.8.6.4Insert the screw or threaded tool into each foam specimen to a depth of20mm.8.6.5Test in accordance with Specification F543,Annex A3.8.6.6Determine the maximum force,in Newtons,required to remove the screw or threaded tool from the foam specimen.8.6.7Calculate the average pullout force for thefive speci-mens.9.Report9.1Include the following information in the test report of the mechanical properties of the foam:9.1.1The lot number,specified grade(if applicable),manu-facturer,and date of manufacture of the foam or two-part liquid mixture.9.1.2For foams supplied in the liquid form,the report shall include the following:9.1.2.1Mixing ratio of the two liquid parts(expressed as a ratio of the base and activator based on either weight or volume).9.1.2.2Mixing and casting technique(for example,rate of stirring,pressurization,and so forth).9.1.2.3Ambient temperature and humidity during mixing and casting.9.1.2.4Any other parameters that may affect the quality of the polyurethane foam in the solidfinal form.9.1.3Any test results that did not meet the requirements of Section4.9.1.4The average and standard deviation of the foam density as determined in8.2.9.1.5The average and standard deviation of the percent thickness change as determined in8.3.9.1.6The average and standard deviation of the compres-sive strength and modulus as determined in8.4.9.1.7The average and standard deviation of the shear strength and modulus as determined in8.5.9.1.8The average and standard deviation of the screw or threaded tool pullout force as determined in8.6.10.Qualification and Acceptance Criteria10.1Qualification Criteria:10.1.1Solid Supplied Form—A supplier of foam in the solid form shall demonstrate that its production process(for a lot of material in a particular grade)results in foam that meets all of the physical and mechanical requirements of Section4, by providing a report described in Section9.Once the supplier has demonstrated this,the supplier is qualified for that particu-lar grade.Provided there are no changes made to the produc-tion process for the qualified grade,subsequent lots of material of the qualified grade are only required to meet the acceptance criteria described in10.2.10.1.2Liquid Supplied Form—The end user of the foam supplied in the liquid form shall demonstrate that the solidfinal form produced meets all of the physical andmechanicalrequirements of Section 4,by providing a report described in Section 9.Once the end user has demonstrated this,the user is qualified for that particular grade.Provided no changes made to the production process for the qualified grade (mixing ratio,humidity,temperature,mixing and pouring technique,and so forth)subsequent lots of material of the qualified grade are only required to meet the acceptance criteria described in 10.2.10.2Acceptance Criteria —Provided the grade of foam is qualified according to the criteria described in 10.1,a lot of foam material is accepted as meeting the requirements of this standard provided the requirements of 10.2.2and 10.2.3are met,and reported in a manner consistent with 9.1.1-9.1.4and 9.1.8.10.2.1Test Specimens —Five specimens,50.8by 50.8by 25.4mm,as specified in 4.10,shall be used for the acceptance examination and testing.10.2.2Physical Requirements :10.2.2.1Composition —See 4.1,10.2.2.2Appearance —See 4.2.3,10.2.2.3Void Content —See 4.3,and 10.2.2.4Density —See 4.4.10.2.3Screw Pullout —See 4.10.11.Storage11.1The solid foam should be stored in a cool dry place between uses,and protected from exposure to light,especially direct sunlight.Exposure to ultraviolet light for an extended period of time may degrade the outer surface of the foam.11.2The supplier is responsible for storage of the solid foam until the time of delivery.Therefore,the supplier is responsible for ensuring that the requirements of this specifi-cation are met at time of delivery for any foam that had previously met the acceptance criteria of 10.2.11.3The end user is responsible for storage of the solid foam after delivery and until the time of use.Therefore,the end user is responsible for ensuring that the requirements of this specification are met at time of use for any foam which had previously met the acceptance criteria of 10.2.12.Precision and Bias12.1No information is presented about either the precision or bias of this test method for evaluating appearance or void content since these test results are nonquantitative.12.2The precision and bias of this test method for measur-ing Density are essentially as specified in Test Method D1622.12.3Data establishing the precision and accuracy to be expected from this test method for determining dimensional stability have not yet been obtained.12.4The precision and bias of this test method for measur-ing compressive strength and compressive modulus are essen-tially as specified in Test Method D1621.12.5The precision and bias of this test method for measur-ing shear strength and shear modulus are essentially as specified in Test Method C273.12.6The precision and bias of this test method for measur-ing Screw Pullout are essentially as specified in Specification F543,Annex A3.13.Keywords13.1bone;cellular plastic;medical devices;polyurethane;rigid foamAPPENDIX(Nonmandatory Information)X1.RATIONALEX1.1This specification provides compositional,physical,and mechanical requirements for rigid polyurethane foam.These requirements ensure a consistent and uniform material that may be used as a test medium when testing various medical devices.These rigid polyurethane foam materials are not intended for implantation into the human body.X1.2Researchers have found that certain densities of rigid polyurethane foam exhibit closed-cell structure similar to human cancellous bone,and possess mechanical properties that are also in the range of those of human cancellous bone (1-4)3.The uniformity and consistent properties of rigid polyurethane foam make it an ideal material for comparative testing of bone screws and other medical devices and instruments (5-7).General Plastics Manufacturing Company,4910Burlington Way,Tacoma,WA 98409,is a producer of Last-a Foampolyurethane foam that previously met the requirements of this standard.At the time of this revision,the firm could not guarantee to meet the physical requirements for any individual sample of the material.Other manufacturers of rigid polyure-thane foam that can meet the requirements of this specification may exist.X1.3The original purpose of this standard was to provide a consistent and uniform material for incorporation into the revision of Specification F543,Annex A2for use as a standard medium for testing the driving torque of medical bone screws.Future applications may include:standard material for pullout tests of medical bone screws,standard material for measuring cutting diameter of intramedullary reamers,and standard material for measuring the cutting performance of medical drills.X1.4The mechanical properties of the foam that may be important for standardization or for comparison to human cancellous bone will likely depend on the particular test3The boldface numbers given in parentheses refer to a list of references at the end of thetext.method that is being developed.It is suggested that a test method that references this specification foam material should also address the relative importance of the different mechanical properties of the foam and suggest foam grades which may provide performance similar to human cancellous bone.X1.5This specification provides ten grades(densities)of rigid polyurethane foam to provide a range of mechanical properties.It also provides that the foam may be supplied either in a solid form,or as a two-part liquid that is mixed together by the end user to produce solid foam.X1.6The values shown in Tables2-5were calculated from regression analysis of laboratory data between density and the relevant mechanical property.A confidence interval of95% was calculated for each regression and used to determine the maximum and minimum values for610%of the nominal density for each grade.X1.7During the2008review of this specification,the task force had considerable discussion of the tolerance that should be allowed on the foam density.The task force considered the historical record in the development of this specification of specifying a material suitable for the evaluation of orthopedic devices and instruments.The task force reviewed the use of wood,such as maple and pine,both raw and fresh frozen bovine and porcine bone,and other polymer-based materials. None of these materials were suitable for several reasons, including high inter-specimen variability,poor availability, high cost and dissimilar material properties to those of human bone.The difficulty of predicting and certifying the mechanical properties of foam material so that its properties would mimic the properties of bone was particularly studied.Consideration was given to specifying the tolerance on the foam density as 616.0kg/m3or as610%of the reported value.After discussion with the only known supplier of the foam(see X1.2) regarding the manufactured tolerance of the foam density,the task force adopted the tolerance as610%of the reported value.REFERENCES(1)Szivek,J.A.,Thomas,M.,and Benjamin,J.B.,“Technical Note-Characterization of a Synthetic Foam as a Model for Human Cancel-lous Bone,”Journal of Applied Biomaterials,V ol4,1993,pp.269-272.(2)Hein,T.J.,Hotchkiss,R.,Perissinotto,A.,and Chao,E.Y.S.,“Analysisof Bone Model Material for External Fracture Fixation Experiments,”Journal of Biomechanical Instrumentation,V ol22,1987,pp.43-48.(3)Thompson,J.D.,Szivek,J.A.,and Benjamin,J.B.,“Characterizationof a Series of Closed Cell Foams to Simulate Trabecular Bone from Different Patient Populations,”Presented at Society for Biomaterials 20th Annual Meeting,Boston,MA,April5-9,1994.(4)Szivek,J.A.,Thompson,J.D.,and Benjamin,J.B.,“Characterizationof Three Formulations of a Synthetic Foam as Models for a Range ofHuman Cancellous Bone Types,”Journal of Applied Biomaterials, V ol6,1995,pp.125-128.(5)Lee,R.W.,V olz,R.G.,and Sheridan,D.C.,“The Role of Fixation andBone Quality on the Stability of Tibial Knee Components,”Clinical Orthopaedics,V ol273,1991,pp.177-183.(6)Chapman,J.R.,Harrington,R.M.,Lee,K.M.,Anderson,P.A.,Tencer,A.F.,and Kowalski,D.,“Factors Affecting the Pullout Strength ofCancellous Bone Screws,”Journal of Biomechanical Engineering, V ol118,1996,pp.391-398.(7)Dawson,J.D.,McNamara,M.J.,Weld,K.J.,and Spengler, D.M.,“Effect of Crosslinking on Pedicle Screw Pull-Out Strength,”Pre-sented at American Academy of Orthopaedic Surgeons61st Annual Meeting,New Orleans,LA,February24-March1,1994.ASTM International takes no position respecting the validity of any patent rights asserted in connection with any item mentioned in this ers of this standard are expressly advised that determination of the validity of any such patent rights,and the risk of infringement of such rights,are entirely their own responsibility.This standard is subject to revision at any time by the responsible technical committee and must be reviewed everyfive years and if not revised,either reapproved or withdrawn.Your comments are invited either for revision of this standard or for additional standards and should be addressed to ASTM International Headquarters.Your comments will receive careful consideration at a meeting of the responsible technical committee,which you may attend.If you feel that your comments have not received a fair hearing you should make your views known to the ASTM Committee on Standards,at the address shown below.This standard is copyrighted by ASTM International,100Barr Harbor Drive,PO Box C700,West Conshohocken,PA19428-2959, United States.Individual reprints(single or multiple copies)of this standard may be obtained by contacting ASTM at the above address or at610-832-9585(phone),610-832-9555(fax),or service@(e-mail);or through the ASTM website().。
糖尿病患者诊断应用血清C肽及糖化血红蛋白联合检测的价值分析

DOI:10.16658/ki.1672-4062.2023.14.085糖尿病患者诊断应用血清C肽及糖化血红蛋白联合检测的价值分析倪胜南,陈少,陈一鸣泗阳康达医院检验科,江苏宿迁223700[摘要]目的探讨糖尿病患者诊断应用血清C肽联合糖化血红蛋白检测的价值。
方法将2022年1月—2023年1月泗阳康达医院收治的74例疑似糖尿病患者作为研究对象,检测入组患者糖化血红蛋白(glycosylated hemoglobin, HbA1c)以及血清C肽水平,以口服葡萄糖耐量试验(glucose tolerance test check, OGTT)为金标准,统计血清C肽联合糖化血红蛋白检测与单一项目检测的敏感性、特异度和诊断符合率。
结果74例疑似糖尿病患者根据葡萄糖耐量试验结果,确诊患者67例,确诊率为90.54%(67/74);与血清C肽、HbA1c单一检测相比,血清C肽+HbA1c联合检测敏感度更高,差异有统计学意义(P<0.05);血清C肽+HbA1c联合检测的特异度略高于血清C肽、HbA1c单一检测,但差异无统计学意义(P>0.05);联合检测诊断符合率明显高于血清C 肽、HbA1c单项检测,差异有统计学意义(P<0.05)。
结论血清C肽与糖化血红蛋白是临床诊断糖尿病的重要参考指标,二者表达水平的变化有助于检测患者胰岛素分泌功能,评估疾病严重程度,两者联合检验灵敏性与特异度良好,有助于早期明确诊断,临床参考价值较高。
[关键词] 糖尿病;血清C肽;糖化血红蛋白;诊断价值[中图分类号] R446.1 [文献标识码] A [文章编号] 1672-4062(2023)07(b)-0085-04Analysis of the Value of the Diagnostic Application of Combined Serum C-peptide and Glycosylated Hemoglobin Testing in Patients with Diabetes MellitusNI Shengnan, CHEN Shao, CHEN YimingDepartment of Laboratory Medicine, Siyang Kangda Hospital, Suqian, Jiangsu Province, 223700 China[Abstract] Objective To explore the value of applying serum C-peptide combined with glycated hemoglobin test for the diagnosis of diabetic patients. Methods A total of 74 patients with suspected diabetes admitted to Siyang Kangda Hospital from January 2022 to January 2023 were selected as the research objects. The levels of glycosylated hemoglo‐bin (HbA1c) and serum C-peptide were detected. Oral glucose tolerance test (OGTT) was used as the gold standard. The sensitivity, specificity and diagnostic coincidence rate of serum C-peptide combined with glycosylated hemoglo‐bin detection and single item detection were statistically analyzed. Results According to the results of glucose toler‐ance test, 67 patients were diagnosed in 74 patients with suspected diabetes, and the diagnosis rate was 90.54% (67/ 74). Compared with the single detection of serum C-peptide and HbA1c, the sensitivity of combined detection of se‐rum C peptide and HbA1c was higher, and the difference was statistically significant (P<0.05). The specificity of com‐bined detection of serum C-peptide and HbA1c was slightly higher than that of single detection of serum C-peptide and HbA1c, but the difference was no statistically significant (P>0.05). The diagnostic coincidence rate of combined detection was significantly higher than that of single detection of serum C-peptide and HbA1c, and the difference was statistically significant (P<0.05). Conclusion Serum C-peptide and glycosylated hemoglobin are important reference indexes for clinical diagnosis of diabetes mellitus, and changes in the expression levels of the two can help to detect the insulin secretion function of patients and assess the severity of the disease. The sensitivity and specificity of the [作者简介]倪胜南(1991-),女,本科,主管检验师,研究方向为免疫学、分子生物学检验。
LORD Corporation 产品说明书 - CHEMLOK 8560S-1

USA SAFETY DATA SHEET1. CHEMICAL PRODUCT AND COMPANY IDENTIFICATIONProduct name: CHEMLOK 8560S-1Product Use/Class: Aqueous AdhesiveLORD Corporation111 LORD DriveCary, NC 27511-7923 USATelephone: 814 868-3180Non-Transportation Emergency: 814 763-2345 Chemtrec 24 Hr Transportation Emergency No.800 424-9300 (Outside Continental U.S. 703 527-3887)EFFECTIVE DATE: 12/20/20212. HAZARDS IDENTIFICATIONGHS CLASSIFICATION:Serious eye damage/eye irritation Category 2B Skin sensitization Category 1A Carcinogenicity Category 2Specific target organ systemic toxicity (single exposure) Category 2 blood system Specific target organ systemic toxicity (repeated exposure) Category 2 blood system Hazardous to the aquatic environment - acute hazard Category 2 Hazardous to the aquatic environment - chronic hazard Category 2GHS LABEL ELEMENTS:Symbol(s)Signal WordW ARNINGHazard StatementsCauses eye irritation.May cause an allergic skin reaction. Suspected of causing cancer.May cause damage to organs.(blood system)May cause damage to organs through prolonged or repeated exposure.(blood system) Toxic to aquatic life.Toxic to aquatic life with long lasting effects.Precautionary Statements PreventionObtain special instructions before use.Do not handle until all safety precautions have been read and understood. Wear protective gloves.Use personal protective equipment as required. Do not breathe dust/fume/gas/mist/vapors/spray. Wash thoroughly after handling.Do not eat, drink or smoke when using this product.Contaminated work clothing should not be allowed out of the workplace. Avoid release to the environment.Product: CHEMLOK 8560S-1, Effective Date: 12/20/2021ResponseGet medical advice/attention if you feel unwell.Call a POISON CENTER or doctor/physician if exposed or you feel unwell.Specific treatment (see supplemental first aid instructions on this label).IF ON SKIN: Wash with plenty of soap and water.If skin irritation or rash occurs: Get medical advice/attention.IF IN EYES: Rinse cautiously with water for several minutes. Remove contact lenses, if present and easy to do.Continue rinsing.If eye irritation persists: Get medical advice/attention.Wash contaminated clothing before reuse.Collect spillage.StorageStore locked up.Disposal:Dispose of contents/container in accordance with waste/disposal laws and regulations of your country or particular locality.Other Hazards:This product contains component(s) which have the following warnings; however based on the GHS classification criteria of your country or locale, the product mixture may be outside the respective category(s).Acute: May cause mild skin irritation. In elevated-temperature applications, product may release vapors that may produce cyanosis in the absence of sufficient ventilation or adequate respiratory protection. 4,4'-Diphenylmethane bis-maleimide is harmful by inhalation. Avoid breathing sanding dust from this product. May be harmful ifswallowed. Ingestion is not an expected route of entry in industrial or commercial uses.Chronic: Prolonged or repeated contact may result in dermatitis. The nitrogen substituted aromatic in this product gave positive results for mutagenicity in an Ames Assay study while two other mutagenicity studies proved negative.IARC has designated carbon black as Group 2B - inadequate evidence for carcinogenicity in humans, but sufficient evidence in experimental animals. In 2006 IARC reaffirmed its 1995 finding that there is "inadequate evidence"from human health studies to assess whether carbon black causes cancer in humans. Further, epidemiologicalevidence from well-conducted investigations has shown no causative link between carbon black exposure and the risk of malignant or non-malignant respiratory disease in humans. IARC has identified the proprietary curative in this product as an "animal suspected" carcinogen, Group 3, which downgrades a previous NCI report of it as an "animal positive" carcinogen.3. COMPOSITION/INFORMATION ON INGREDIENTSChemical Name CAS Number RangeNitrogen substituted aromatic PROPRIETARY15 - 20%Zinc compound PROPRIETARY 5 - 10%4,4'-Diphenylmethane bis-maleimide13676-54-5 1 - 5%Carbon black1333-86-4 1 - 5%Nonylphenol ethoxylate compound PROPRIETARY0.9 - 1%Curative PROPRIETARY0.1 - 0.9%Any "PROPRIETARY" component(s) in the above table is considered trade secret, thus the specific chemical and its exact concentration is being withheld.4. FIRST AID MEASURESFIRST AID - EYE CONTACT: Flush eyes immediately with large amount of water for at least 15 minutes holding eyelids open while flushing. Get prompt medical attention.FIRST AID - SKIN CONTACT: Flush contaminated skin with large amounts of water while removing contaminated clothing. Wash affected skin areas with soap and water. Get medical attention if symptoms occur.FIRST AID - INHALATION: Move person to fresh air. Restore and support continued breathing. If breathing is difficult, give oxygen. Get immediate medical attention.Product: CHEMLOK 8560S-1, Effective Date: 12/20/2021FIRST AID - INGESTION: If swallowed, do not induce vomiting. Call a physician or poison control center immediately for further instructions. Never give anything by mouth if victim is rapidly losing consciousness, unconscious or convulsing.5. FIRE-FIGHTING MEASURESSUITABLE EXTINGUISHING MEDIA: Carbon Dioxide, Dry Chemical, Foam, Water FogUNSUITABLE EXTINGUISHING MEDIA: Not determined for this product.SPECIFIC HAZARDS POSSIBLY ARISING FROM THE CHEMICAL: Keep containers tightly closed. Closed containers may rupture when exposed to extreme heat. Use water spray to keep fire exposed containers cool. WARNING: Due to the combustible nature of the dried film of this product and the potential for smoldering or fire, the accumulation and buildup of the dried film on spray booth walls and floors, spindles, fixtures and other surfaces should be avoided, and any buildup should be removed. Keep the dried film accumulations away from sparks, friction, impact, high heat (>235 F/>112 C) or other sources of ignition. These conditions could cause the dried film to ignite very readily and quickly, and the resulting smoldering or fire may be difficult to extinguish. During removal of accumulation/buildup of this product, take precautions to avoid heat, friction and impact during the cleaning process. Use paint stripper, brass brush, or plastic scraper for cleaning. In the event of smoldering or a fire involving the dried product, Cold Fire®** fire suppressing agent is preferred as the extinguishing medium. If Cold Fire® is not available, use water spray as the extinguishing medium. Take efforts to ensure that these agents reach the base of the smoldering or fire. Parker-LORD Corporation will not be responsible for personal injuries, property damage or any other damages arising from the accumulation (buildup, cleaning/removal or any related smoldering or fire) resulting from the use of this product. Refer to the Chemlok® Safe Handling Guide for additional information. **NOTE: Parker-LORD Corporation has determined Cold Fire® fire suppressing agent to be effective in extinguishing fires involving dried Chemlok® adhesives. Parker-LORD does not recommend any particular equipment or system for use in delivering or applying Cold Fire® products. Customer is responsible for determining that Cold Fire® products and any delivery equipment or system is appropriate and effective for customer's specific needs. During a fire, irritating and/or toxic gases and particulate may be generated by thermal decomposition or combustion. SPECIAL PROTECTIVE EQUIPMENT AND PRECAUTIONS FOR FIRE-FIGHTERS: Wear full firefighting protective clothing, including self-contained breathing apparatus (SCBA). If water is used, fog nozzles are preferable.6. ACCIDENTAL RELEASE MEASURESPERSONAL PRECAUTIONS, PROTECTIVE EQUIPMENT AND EMERGENCY PROCEDURES: Avoid breathing vapors. Avoid contact. Use appropriate respiratory protection for large spills or spills in confined area. See Section 5 for cautionary information on the dried residue of this product.ENVIRONMENTAL PRECAUTIONS: Do not contaminate bodies of water, waterways, or ditches, with chemical or used container.METHODS AND MATERIALS FOR CONTAINMENT AND CLEANUP: Notify appropriate authorities if necessary. Contain and remove with inert absorbent material. Avoid contact. Keep non-essential personnel away from spill area. Before attempting cleanup, refer to hazard caution information in other sections of this Safety Data Sheet.7. HANDLING AND STORAGEHANDLING: Keep closure tight and container upright to prevent leakage. Avoid skin and eye contact. Wash thoroughly after handling. Do not handle until all safety precautions have been read and understood. Empty containers should not be re-used. Use with adequate ventilation. See Section 5 for cautionary information on handling of the dried residue of this product. Avoid breathing sanding dust from this product.STORAGE: Store only in well-ventilated areas. Keep from freezing. Keep container closed when not in use. INCOMPATIBILITY: Strong acids, bases, and strong oxidizers.8. EXPOSURE CONTROLS/PERSONAL PROTECTIONCOMPONENT EXPOSURE LIMIT Chemical Name ACGIH TLV-TWA ACGIH TLV-STELOSHA PEL-TWAOSHA PEL-CEILINGSkinProduct: CHEMLOK 8560S-1, Effective Date: 12/20/2021Nitrogen substituted aromatic N.E.N.E.N.E. N.E. N.A. Zinc compound2 mg/m3 10 mg/m3 5 mg/m3 N.E. N.A. 4,4'-Diphenylmethane bis-maleimide N.E. N.E. N.E. N.E. N.A. Carbon black3 mg/m3 N.E. 3.5 mg/m3 N.E. N.A. Nonylphenol ethoxylate compound N.E. N.E. N.E. N.E. N.A. CurativeN.E.N.E.N.E.N.E.N.A.N.A. - Not Applicable, N.E. - Not Established, S - Skin DesignationEngineering controls: Sufficient ventilation in pattern and volume should be provided in order to maintain air contaminant levels below recommended exposure limits.PERSONAL PROTECTION MEASURES/EQUIPMENT:RESPIRATORY PROTECTION: Use a NIOSH approved chemical/mechanical filter respirator designed to remove a combination of particulates and organic vapor if occupational limits are exceeded. For emergencysituations, confined space use, or other conditions where exposure limits may be greatly exceeded, use an approved air-supplied respirator. For respirator use observe OSHA regulations (29CFR 1910.134) or use in accordance with applicable laws and regulations of your country or particular locality.SKIN PROTECTION: Use neoprene, nitrile, or rubber gloves to prevent skin contact.EYE PROTECTION: Use safety eyewear including safety glasses with side shields and chemical goggles where splashing may occur.OTHER PROTECTIVE EQUIPMENT: Remove and wash contaminated clothing before reuse.HYGIENIC PRACTICES: Wash hands before eating, smoking, or using toilet facility. Do not smoke in any chemical handling or storage area. Food or beverages should not be consumed anywhere this product is handled or stored. Wash thoroughly after handling.9. PHYSICAL AND CHEMICAL PROPERTIESTypical values, not to be used for specification purposes.ODOR:Odorless VAPOR PRESSURE:N.D.APPEARANCE: Green/BlackVAPOR DENSITY:Heavier than Air PHYSICAL STATE:Thixotropic liquid LOWER EXPLOSIVE LIMIT: Not Applicable FLASH POINT: ≥ 201 °F, 93 °C Setaflash Closed Cup UPPER EXPLOSIVE LIMIT:Not Applicable BOILING RANGE:100 °CEVAPORATION RATE: Slower than n-butyl-acetateAUTOIGNITION TEMPERATURE: N.D. DENSITY:1.2 g/cm3 (10.00 lb/gal) DECOMPOSITION TEMPERATURE:N.D. VISCOSITY, DYNAMIC: ≥50 mPa.s @ 25 °C ODOR THRESHOLD: N.D.VISCOSITY, KINEMATIC: ≥42 mm2/s @ 25 °C SOLUBILITY IN H2O:Water Dispersible VOLATILE BY WEIGHT: 56.93 % pH:6.0 VOLATILE BY VOLUME:66.72 % FREEZE POINT:N.D. VOC CALCULATED: 0.02 lb/gal , 3 g/l COEFFICIENT OF WATER/OILDISTRIBUTION:N.D.LEGEND: N.A. - Not Applicable, N.E. - Not Established, N.D. - Not Determined10. STABILITY AND REACTIVITYHAZARDOUS POLYMERIZATION: Hazardous polymerization will not occur under normal conditions.STABILITY: Product is stable under normal storage conditions.Product: CHEMLOK 8560S-1, Effective Date: 12/20/2021CONDITIONS TO AVOID: High temperatures.; For dried product issues, refer to Section 5 of the (M)SDS.; DO NOT ALLOW THIS MATERIAL TO DRY OUT. As a solid, p-benzoquinone dioxime is flammable, and it may explode if exposed to shock, friction or heat.INCOMPATIBILITY: Strong acids, bases, and strong oxidizers.HAZARDOUS DECOMPOSITION PRODUCTS: Decomposition due to high temperatures or a fire causes the formation of irritating and/or toxic gases, organic vapors or fumes., May contain CO, CO2, oxides of nitrogen, oxides of sulfur, halogenated by-products, Carbon dioxide, carbon monoxide, chlorine, hydrogen chloride, Phosgene, Metal oxides11. TOXICOLOGICAL INFORMATIONEXPOSURE PATH: Refer to section 2 of this SDS.SYMPTOMS: Refer to section 2 of this SDS.TOXICITY MEASURES:Chemical NameLD50/LC50 Nitrogen substituted aromatic Oral LD50: rat 1,100 mg/kgZinc compoundOral LD50: Rat > 5,000 mg/kg Dermal LD50: Rat > 2,000 mg/kgGHS LC50 (vapour): Acute toxicity point estimate 55 mg/l Inhalation LC50: Rat > 5,700 mg/m3 /4 h 4,4'-Diphenylmethane bis-maleimide Oral LD50: Rat > 5 g/kgDermal LD50: rat > 5,400 mg/kgGHS LC50 (dust and mist): rat 0.52 mg/l Inhalation ATE: 11 mg/l Carbon blackOral LD50: Rat > 15,400 mg/kg Dermal LD50: Rabbit > 3 g/kgGHS LC50 (vapour): Acute toxicity point estimate 55 mg/l : Nonylphenol ethoxylate compound N.D.CurativeOral LD50: Rat 464 mg/kgGHS LC50 (vapour): Acute toxicity point estimate 55 mg/l Inhalation LC50: Rat > 5 mg/l /4 hGerm cell mutagenicity: No classification proposedCarcinogenicity: Category 2 - Suspected of causing cancer. Components contributing to classification: Curative.Reproductive toxicity: No classification proposed12. ECOLOGICAL INFORMATIONECOTOXICITY:Chemical NameEcotoxicityNitrogen substituted aromatic N.D. Zinc compoundN.D.4,4'-Diphenylmethane bis-maleimide Fish: Oncorhynchus mykiss (rainbow trout) > 0.145 mg/l96 hCarbon blackN.D. Nonylphenol ethoxylate compound N.D.CurativeFish: Danio rerio (zebra fish) 24 mg/l96 h Static Invertebrates: Daphnia magna (Water flea) 3.5 mg/l48 h StaticPERSISTENCE AND DEGRADABILITY: Not determined for this product.BIOACCUMULATIVE: Not determined for this product.MOBILITY IN SOIL: Not determined for this product.OTHER ADVERSE EFFECTS: Not determined for this product.13. DISPOSAL CONSIDERATIONSDISPOSAL METHOD: Disposal should be done in accordance with Federal (40CFR Part 261), state and local environmental control regulations. If waste is determined to be hazardous, use licensed hazardous waste transporter and disposal facility. Waste streams, including the dried adhesive residue, resulting from the use of this product should be tested for RCRA characteristics, including ignitability, to determine any applicable waste classifications.14. TRANSPORT INFORMATIONUS DOT RoadProper Shipping Name: Environmentally hazardous substances, liquid, n.o.s.Hazard Class: 9SECONDARY HAZARD: NoneUN/NA Number: 3082Packing Group: IIIEmergency Response Guide Number: 171For US DOT non-bulk road shipments this material may be classified as NOT REGULATED. For the mostaccurate shipping information, refer to your transportation/compliance department regarding changes inpackage size, mode of shipment or other regulatory descriptors.IATA CargoPROPER SHIPPING NAME: Environmentally hazardous substance, liquid, n.o.s.Hazard Class: 9HAZARD CLASS: NoneUN NUMBER: 3082PACKING GROUP: IIIEMS: 9LIMDGPROPER SHIPPING NAME: Environmentally hazardous substance, liquid, n.o.s.Hazard Class: 9HAZARD CLASS: NoneUN NUMBER: 3082PACKING GROUP: IIIEMS: F-AThe listed transportation classification applies to non-bulk shipments. It does not address regulatory variations due to changes in package size, mode of shipment or other regulatory descriptors. For the most accurate shipping information, refer to your transportation/compliance department.15. REGULATORY INFORMATIONU.S. FEDERAL REGULATIONS: AS FOLLOWS:SARA SECTION 313This product contains the following substances subject to the reporting requirements of Section 313 of Title III of the Superfund Amendment and Reauthorization Act of 1986 and 40 CFR part 372.:Chemical Name CAS Number Weight % Less ThanZinc compound PROPRIETARY10.0%TOXIC SUBSTANCES CONTROL ACT:INVENTORY STATUSThe chemical substances in this product are on the active TSCA Section 8 Inventory or exempt.EXPORT NOTIFICATIONThis product contains the following chemical substances subject to the reporting requirements of TSCA 12(B) if exported from the United States:None16. OTHER INFORMATIONUnder HazCom 2012 it is optional to continue using the HMIS rating system. It is important to ensure employees have been trained to recognize the different numeric ratings associated with the HazCom 2012 and HMIS schemes.HMIS RATINGS - HEALTH: 2* FLAMMABILITY: 1 PHYSICAL HAZARD: 0* - Indicates a chronic hazard; see Section 2Revision: New GHS SDS FormatEffective Date: 12/20/2021DISCLAIMERThe information contained herein is, to the best of our knowledge and belief, accurate. However, since the conditions of handling and use are beyond our control, we make no guarantee of results, and assume no liability for damages incurred by use of this material. It is the responsibility of the user to comply with all applicable federal, state and local laws and regulations.。
D5402中文版

1.1这项实践描述了一种根据在固化过程中的化学变化来评测有机涂层的耐溶剂性的溶剂摩擦技术。
这项技术可以应用在实验室,野外,或装配工厂。
D4752这个材料是乙烷基硅酸盐富锌底漆的首选。
1.2这项实践没有指定的溶剂,摩擦的次数和期望的测试结果。
1.3 这些数值是用的国际制单位来作为标准。
那些在括号里的数值仅供参考。
1.4 这个标准的主旨不是处理所有的安全隐患,如果有,结合它的用途来使用。
使用者有责任在使用前确定适合本标准的安全卫生习惯并确定监督管理的适用性。
涉及到溶剂的使用时,查阅供应商的一些特殊危险品的安全数据表。
2.参考资料2.1 ASTM 标准:D235 矿物质说明书(石油)(烃干洗溶剂)D5823 测试反射光泽的材料D740 甲基乙烷基酮的说明书D843 硝化等级的二甲苯的说明书D1186 应用于含铁的非磁性涂层中的干薄膜层的非破坏性测量材料D1400 应用于不含铁的绝缘涂层中的干薄膜层的非破坏性测量材料D3363 用铅笔测试薄层坚硬度的测试材料D4138 用破坏性方法测量保护涂层体系的测试材料D4752 用溶剂摩擦的方法来测试乙烷基硅酸盐(无机的)富锌底漆的MEK耐溶剂性的测试材料3术语3.1 这个标准具体的术语定义:3.1.1 双擦—在一个有涂层的表面用布料完成一个来回擦的动作。
4.意义和用途4.1涂料在固化过程中的化学变化,如环氧树脂,乙烯基酯,聚酯纤维,醇酸树脂和聚氨酯橡胶,能变得更加耐溶剂。
这些涂料应该能达到特定的耐溶剂级别,成为优异的面漆,且在公共机构发挥作用。
耐溶剂性级别的需求根据涂料的种类和预计的使用场所的不同而变化。
用被适合的溶剂浸湿的布料摩擦是一种能测定它是否已达到特定耐溶性的方法。
然而,耐溶剂自身的级别并不是指在它完全固化,有些涂料在他们充分的固化之前已经变成耐溶剂性了。
4.2 要达到特定级别的耐溶剂性的所需的时间受温度,薄层厚度,空气流动,水媒性或水反应的覆盖层和湿度的影响。
基于QuEChERS-液相色谱-串联质谱法测定纸制品中4种异噻唑啉酮类杀菌剂

广东化工2021年第10期· 214· 第48卷总第444期基于QuEChERS-液相色谱-串联质谱法测定纸制品中4种异噻唑啉酮类杀菌剂李柏,陈山丹,冯杰,刘萍,钱志娟(南京海关轻工产品与儿童用品检测中心,江苏扬州225009)[摘要]建立了QuEChERS结合液相色谱-串联质谱法测定纸制品中4种异噻唑啉酮杀菌剂(MI,CMI,OI和BIT)的含量。
采用多反应监测模式进行定性,外标法定量。
结果表明在5~250 μg/L(OI为0.5~25 μg/L)范围内线性关系良好(R2=0.9986~0.9999)。
方法的检出限LOD为0.044~0.571μg/L,定量限LOQ为0.146~1.91 μg/L。
4种不同的纸制品在0.2,2.5和4.0 mg/kg三个添加水平的加标回收率为84.4%~101.4%,相对标准偏差(RSD%)为2.11%~7.82%。
该方法快速,灵敏,能够满足纸制品中异噻唑啉酮杀菌剂的检测要求。
[关键词]QuEChERS;液相色谱-串联质谱,异噻唑啉酮,纸制品[中图分类号]TQ [文献标识码]A[文章编号]1007-1865(2021)10-0214-03Determination of Four Isothiazolinone Biocides in Paper Products byQuEChERS-liquid Chromatography-tandem Mass SpectrometryLi Bai, Chen Shandan,Feng Jie,Liu Ping, Qian Zhijuan(Nanjing Customs District Light Industry Products and Children’s Products Inspection Center, Yangzhou 225009, China) Abstract: A method was developed for the determination of four isothiazolinone biocides in paper products by QuEChERS with liquid chromatography-tandem mass spectrometry. The multi reaction monitoring model was used for qualitative analysis and the external standard method was used for quantitative analysis.These 4 biocides showed a good linearity in the range of 5~250 μg/L(OI in the range of 0.5~25 μg/L)(R2=0.9986~0.9999).The limit of detection (LOD) was0.044~0.571 μg/L and limit of quantitation (LOQ) was 0.146~1.91 μg/L.The average recoveries of 4 biocides were in the range of 84.4%~101.4% at the three spiked levels (0.2, 2.5 and 4.0 mg/kg) in the four different paper products and the RSD% was in the range of 2.11%~7.82%. The method is rapid, sensitive and can meet the requirements of the detection of isothiazolinone biocides in paper products.Keywords: QuEChERS;Liquid chromatography-tandem mass spectrometry;isothiazolinone;paper products在造纸工业中,造纸原料和水源中不可避免存在着大量的微生物如霉菌、细菌等,更会在各个工艺流程的环节也残留着微生物。
- 1、下载文档前请自行甄别文档内容的完整性,平台不提供额外的编辑、内容补充、找答案等附加服务。
- 2、"仅部分预览"的文档,不可在线预览部分如存在完整性等问题,可反馈申请退款(可完整预览的文档不适用该条件!)。
- 3、如文档侵犯您的权益,请联系客服反馈,我们会尽快为您处理(人工客服工作时间:9:00-18:30)。
References: [1]. Tanaka et al (2005) FGF-induced vesicular release of sonic hedgehog and retinoic acid in leftward nodal flow is critical for left-right determination. Nature 435 172. [2]. Bojesen KB, Clausen O, Rohde K, Christensen C, Zhang L, Li S, Kohler L, Nielbo S, Nielsen J, Gjorlund j MD, Poulsen FM, Bock E, Berezin V.Nectin-1 binds and signals g through g the fibroblast growth factor receptor.J Biol Chem. 2012 Sep 5. [3]. Zhu X, Li Z, Jiang D, Zhao J, Huang L, Zhang J, Huang X.Characterization and expressional analysis of Dleu7 during Xenopus tropicalis embryogenesis.Gene. 2012 Nov 1;509(1):77-84. [4]. Chen YH, Yu J.Ectopic expression of Fgf3 leads to aberrant lineage segregation in the mouse parthenote preimplantation embryos.Dev Dyn. 2012 Aug 28. [5]. Hirabayashi M, Tamura C, Sanbo M, Kato-Itoh M, Kobayashi T, Nakauchi H, Hochi S.A retrospective analysis of germ...
Caution: Not fully tested. For research purposes only Medchemexpress LLC
m o c . s s e r p x e m e h c d e m . w w w : b e AW Sm Uo ,c 0 4. 5s 8s 0e r p Jx Ne ,m n e oh t c e cd ne i rm P @ ,o y f an Wi : l ni oa sm n iE k l i W 8 1
Product Data Sheet
SU 5402 215543-92-3 HY-10407 296.32 C17H16N2O3 >98%
Product Name: CAS No.: Cat. No.: MWt: Formula: Purity :
Solubility:
DMSO
Mechanisms: Pathways:Protein Tyrosine Kinase/RTK; Target:VEGFR g y Biological Activity: SU5402(SU-5402; SU5402) is potent and selective vascular endothelial growth factor receptor (VEGFR) and fibroblast growth factor receptor (FGFR) inhibitor. (IC50 values are 0.02, 0.03, 0.51 and > 100 μM at VEGFR2, FGFR1, PDGFRβ and EGFR respectively). SU-5402 t determination and exhibits potent anticancer activity in vitro and in vivo.