锂离子电池设计总结
锂离子电池管理系统设计与实现

锂离子电池管理系统设计与实现锂离子电池是一种高性能、高效率的电池类型,在现代电子设备和交通工具的应用中得到了广泛使用。
为了更好地管理和控制锂离子电池的充放电过程,提高其使用寿命和安全性能,锂离子电池管理系统(Battery Management System, BMS)的设计与实现变得至关重要。
本文将介绍锂离子电池管理系统的设计原理和实施步骤。
一、锂离子电池管理系统的设计原理锂离子电池管理系统的设计原理主要涉及以下几个方面:电池状态监测、电池均衡控制、温度管理、电池保护和故障诊断。
1. 电池状态监测电池状态监测是指对电池电压、电流、容量等参数进行实时监测和记录。
通过采集电池的电池电压和电流等数据,可以实时了解电池的工作状态,并根据需要作出相应的充放电控制。
2. 电池均衡控制由于锂离子电池组中的每个电池单体在使用过程中容量衰减的不一致性,容易导致电池组的性能下降,甚至引发安全隐患。
因此,电池均衡控制是锂离子电池管理系统中非常重要的一部分。
通过对电池组中电池单体进行均衡充放电控制,可以减少电池单体之间的容量差异,提高整个电池组的使用寿命和性能稳定性。
3. 温度管理锂离子电池的工作性能与温度密切相关,过高或过低的温度会影响电池的寿命和性能。
因此,在锂离子电池管理系统中,需要实时监测电池组的温度,并根据需要进行温度的控制和保护。
4. 电池保护电池保护是指对电池组进行保护,避免电池因过充、过放、过流、短路等原因造成损坏或安全事故。
电池保护主要包括电池过充保护、电池过放保护、电池过流保护等。
5. 故障诊断故障诊断是锂离子电池管理系统的重要功能之一。
通过对电池组的工作参数进行实时监测和分析,可以及时发现故障原因并作出相应处理,提高电池组的可靠性和安全性。
二、锂离子电池管理系统的实现步骤锂离子电池管理系统的实施包括硬件设计和软件编程两个方面。
1. 硬件设计硬件设计主要包括电路板的设计和电路元件的选择。
在电路板的设计中,需要考虑电池状态监测、电池均衡控制、温度管理和电池保护等功能的实现,以及各个功能模块之间的连接。
新型锂离子电池的设计与优化

新型锂离子电池的设计与优化一、引言锂离子电池是目前电子设备和新能源车辆等领域广泛使用的电池类型之一。
然而,随着市场需求的不断增加和技术的不断进步,传统锂离子电池存在其不足之处,如储能量和充放电速度等问题。
因此,开发一种新型锂离子电池,在其设计和优化过程中,可以有效提高其性能和应用价值。
本文旨在介绍新型锂离子电池的设计与优化。
二、设计新型锂离子电池的目标在设计新型锂离子电池时,需要先确定其目标。
新型锂离子电池需要具有以下特点:1. 高能量密度:能够提供更多的能量,以满足用户的需求;2. 高功率密度:能够快速充放电,以适应用户的要求;3. 长寿命:电池使用寿命长,减少维护和更换成本;4. 安全性高:小概率发生事故,不会对用户或周围环境造成危害。
三、优化锂离子电池设计的几个关键点在开发新型锂离子电池时,需要考虑以下几个关键点以进行优化。
1. 正、负极材料的开发新型锂离子电池需要使用更好的正、负极材料以提高其性能。
通常情况下,锂离子电池正极材料采用的是氧化物或磷酸盐等化合物,但是这些材料存在很多问题,如容量不足、电化学稳定性差、成本高等。
因此,需要开发一种更优的正极材料。
负极材料通常采用石墨或硅基材料,然而这些材料也存在一些问题,如容量有限、容易损坏等。
因此,需要开发一种容量更大、稳定性更好的负极材料。
2. 电解液的优化电解液选择不仅关系到电池的性能和安全性,还关系到整个生产成本。
优化电解液需要从以下几个方面入手。
首先,需要选择高离子传导性、稳定性好的电解液。
其次,应使用低毒、低燃点、无污染、易于处理的电解液。
最后要保证电解液的成本可控。
3. 温控技术的发展锂离子电池的性能与工作温度密切相关。
因此,在设计和优化新型锂离子电池时,需要考虑温控技术的发展,以保证电池在各种温度下都能够正常工作。
新型温控技术的发展,如热敏电阻法、仿生温控技术等,将有助于提高锂离子电池的性能和寿命。
4. 循环寿命的改善随着锂离子电池的使用,电极材料往往会出现失效、结构变化等问题,导致电池容量和性能下降。
锂离子电池的材料与结构设计
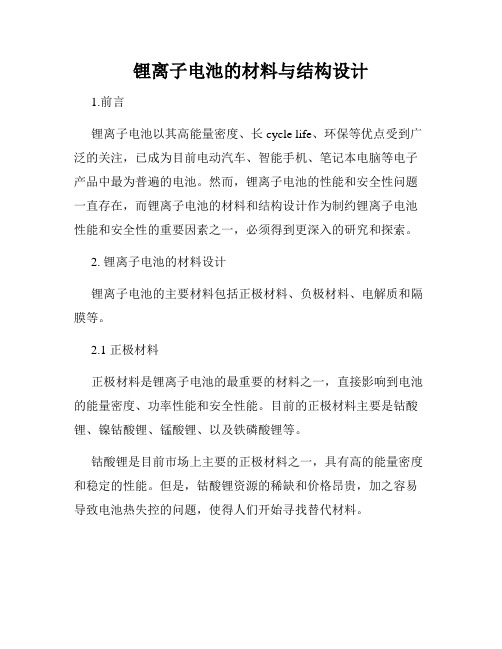
锂离子电池的材料与结构设计1.前言锂离子电池以其高能量密度、长 cycle life、环保等优点受到广泛的关注,已成为目前电动汽车、智能手机、笔记本电脑等电子产品中最为普遍的电池。
然而,锂离子电池的性能和安全性问题一直存在,而锂离子电池的材料和结构设计作为制约锂离子电池性能和安全性的重要因素之一,必须得到更深入的研究和探索。
2. 锂离子电池的材料设计锂离子电池的主要材料包括正极材料、负极材料、电解质和隔膜等。
2.1 正极材料正极材料是锂离子电池的最重要的材料之一,直接影响到电池的能量密度、功率性能和安全性能。
目前的正极材料主要是钴酸锂、镍钴酸锂、锰酸锂、以及铁磷酸锂等。
钴酸锂是目前市场上主要的正极材料之一,具有高的能量密度和稳定的性能。
但是,钴酸锂资源的稀缺和价格昂贵,加之容易导致电池热失控的问题,使得人们开始寻找替代材料。
镍钴酸锂是一种新型的高能量密度正极材料,与钴酸锂相比,镍钴酸锂具有更高的能量密度,但是在高温环境下会发生崩解反应,导致电池容易受损。
锰酸锂和铁磷酸锂等材料也开始逐渐展现出其在锂离子电池中的应用潜力。
2.2 负极材料负极材料是锂离子电池中另一个重要的材料,对电池性能具有重要影响。
主要有石墨、硅等。
石墨在目前的锂离子电池中是最常用的负极材料,但是石墨材料具有较低的储锂能力,难以满足高能量密度和高功率性能的需求。
硅是一种有着很高储锂量的负极材料,具有很大的发展前景。
但是,硅材料具有较大的膨胀率和缩胀率,这使得硅材料的稳定性和循环性能需要进一步的优化。
2.3 电解质电解质是锂离子电池中的另一个关键材料,它是连接正极和负极的桥梁,直接影响到电池的功率性能和安全性能。
目前主要采用液态电解质和固态电解质两种。
液态电解质通常采用有机溶剂电解质,其中最常用的电解质是碳酸锂。
固态电解质则相比液态电解质有更高的热稳定性和低的凝胶化温度,能有效提高电池的安全性能和循环寿命。
2.4 隔膜隔膜是分离正负极材料的一种薄膜材料,主要作用是保持正负极之间的距离,使得锂离子能在电解液中移动而不直接接触。
锂离子电池电解液功能性添加剂的设计及应用
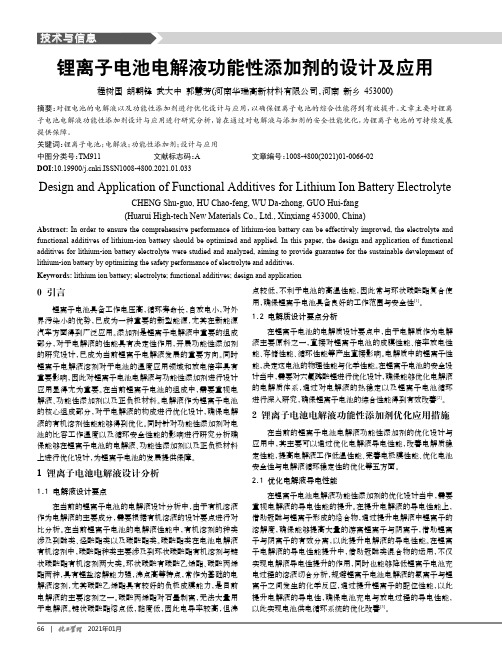
点较低,不利于电池的高温性能,因此常与环状碳酸酯复合使用,确保锂离子电池具备良好的工作范围与安全性[1]。
1.2 电解质设计要点分析在锂离子电池的电解质设计要点中,由于电解质作为电解液主要原料之一,直接对锂离子电池的成膜性能、倍率放电性能、存储性能、循环性能等产生直接影响。
电解质中的锂离子性能,决定这电池的物理性能与化学性能。
在锂离子电池的安全设计当中,需要对六氟磷酸锂进行优化设计,确保能够优化电解液的电解质体系,通过对电解液的热稳定以及锂离子电池循环进行深入研究,确保锂离子电池的综合性能得到有效改善[2]。
2 锂离子电池电解液功能性添加剂优化应用措施在当前的锂离子电池电解液功能性添加剂的优化设计与应用中,其主要可以通过优化电解液导电性能,改善电解质稳定性能,提高电解液工作低温性能、完善电极膜性能、优化电池安全性与电解液循环稳定性的优化等五方面。
2.1 优化电解液导电性能在锂离子电池电解液功能性添加剂的优化设计当中,需要重视电解液的导电性能的提升。
在提升电解液的导电性能上,借助冠醚与锂离子形成的络合物,通过提升电解液中锂离子的溶解度,确保能够提高大量的游离锂离子与阴离子,借助锂离子与阴离子的有效分离,以此提升电解液的导电性能。
在锂离子电解液的导电性能提升中,借助冠醚类混合物的运用,不仅实现电解液导电性提升的作用,同时也能够降低锂离子电池充电过程的溶液切合分析,规避锂离子电池电解液的氨离子与锂离子之间发生的化学反应,通过提升锂离子的配位性能,以此提升电解液的导电性,确保电池充电与放电过程的导电性能,以此实现电池供电循环系统的优化改善[3]。
0 引言锂离子电池具备工作电压高,循环寿命长,自放电小,对外界污染小的优势,已成为一种重要的新型能源,尤其在新能源汽车方面得到广泛应用。
添加剂是锂离子电解液中重要的组成部分,对于电解液的性能具有决定性作用,开展功能性添加剂的研究设计,已成为当前锂离子电解液发展的重要方向。
锂离子电池管理系统的设计
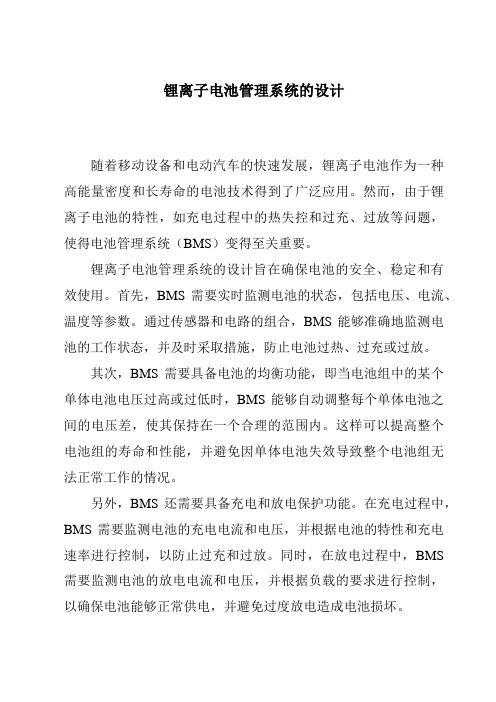
锂离子电池管理系统的设计
随着移动设备和电动汽车的快速发展,锂离子电池作为一种高能量密度和长寿命的电池技术得到了广泛应用。
然而,由于锂离子电池的特性,如充电过程中的热失控和过充、过放等问题,使得电池管理系统(BMS)变得至关重要。
锂离子电池管理系统的设计旨在确保电池的安全、稳定和有效使用。
首先,BMS需要实时监测电池的状态,包括电压、电流、温度等参数。
通过传感器和电路的组合,BMS能够准确地监测电池的工作状态,并及时采取措施,防止电池过热、过充或过放。
其次,BMS需要具备电池的均衡功能,即当电池组中的某个单体电池电压过高或过低时,BMS能够自动调整每个单体电池之间的电压差,使其保持在一个合理的范围内。
这样可以提高整个电池组的寿命和性能,并避免因单体电池失效导致整个电池组无法正常工作的情况。
另外,BMS还需要具备充电和放电保护功能。
在充电过程中,BMS需要监测电池的充电电流和电压,并根据电池的特性和充电速率进行控制,以防止过充和过放。
同时,在放电过程中,BMS 需要监测电池的放电电流和电压,并根据负载的要求进行控制,以确保电池能够正常供电,并避免过度放电造成电池损坏。
最后,BMS还需要具备故障诊断和报警功能。
当电池组中的某个单体电池出现故障或异常时,BMS能够及时发出警报并提供相应的故障诊断信息,以便维修人员及时排查和修复问题,确保电池组的正常运行。
综上所述,锂离子电池管理系统的设计是一个复杂而重要的工程。
通过实时监测电池状态、均衡电池、充放电保护以及故障诊断和报警功能的实现,BMS能够确保电池的安全、稳定和有效使用,提高电池组的性能和寿命,为移动设备和电动汽车的发展提供可靠的能源支持。
锂电池原理及充电正确方法归纳总结

一、锂电池原理锂离子电池的正极材料通常有锂的活性化合物组成,负极则是特殊分子结构的碳.常见的正极材料主要成分为LiCoO2 ,充电时,加在电池两极的电势迫使正极的化合物释出锂离子,嵌入负极分子排列呈片层结构的碳中.放电时,锂离子则从片层结构的碳中析出,重新和正极的化合物结合.锂离子的移动产生了电流.化学反应原理虽然很简单,然而在实际的工业生产中,需要考虑的实际问题要多得多:正极的材料需要添加剂来保持多次充放的活性,负极的材料需要在分子结构级去设计以容纳更多的锂离子;填充在正负极之间的电解液,除了保持稳定,还需要具有良好导电性,减小电池内阻.虽然锂离子电池很少有镍镉电池的记忆效应,记忆效应的原理是结晶化,在锂电池中几乎不会产生这种反应.但是,锂离子电池在多次充放后容量仍然会下降,其原因是复杂而多样的.主要是正负极材料本身的变化,从分子层面来看,正负极上容纳锂离子的空穴结构会逐渐塌陷、堵塞;从化学角度来看,是正负极材料活性钝化,出现副反应生成稳定的其他化合物.物理上还会出现正极材料逐渐剥落等情况,总之最终降低了电池中可以自由在充放电过程中移动的锂离子数目.过度充电和过度放电,将对锂离子电池的正负极造成永久的损坏,从分子层面看,可以直观的理解,过度放电将导致负极碳过度释出锂离子而使得其片层结构出现塌陷,过度充电将把太多的锂离子硬塞进负极碳结构里去,而使得其中一些锂离子再也无法释放出来.这也是锂离子电池为什么通常配有充放电的控制电路的原因.不适合的温度,将引发锂离子电池内部其他化学反应生成我们不希望看到的化合物,所以在不少的锂离子电池正负极之间设有保护性的温控隔膜或电解质添加剂.在电池升温到一定的情况下,复合膜膜孔闭合或电解质变性,电池内阻增大直到断路,电池不再升温,确保电池充电温度正常.而深充放能提升锂离子电池的实际容量吗?专家明确地告诉我,这是没有意义的.他们甚至说,所谓使用前三次全充放的“激活”也同样没有什么必要.然而为什么很多人深充放以后Battery Information 里标示容量会发生改变呢? 后面将会提到.锂离子电池一般都带有管理芯片和充电控制芯片.其中管理芯片中有一系列的寄存器,存有容量、温度、ID 、充电状态、放电次数等数值.这些数值在使用中会逐渐变化.我个人认为,使用说明中的“使用一个月左右应该全充放一次”的做法主要的作用应该就是修正这些寄存器里不当的值,使得电池的充电控制和标称容量吻合电池的实际情况.充电控制芯片主要控制电池的充电过程.锂离子电池的充电过程分为两个阶段,恒流快充阶段(电池指示灯呈黄色时)和恒压电流递减阶段( 电池指示灯呈绿色闪烁.恒流快充阶段,电池电压逐步升高到电池的标准电压,随后在控制芯片下转入恒压阶段,电压不再升高以确保不会过充,电流则随着电池电量的上升逐步减弱到0 ,而最终完成充电.电量统计芯片通过记录放电曲线(电压,电流,时间)可以抽样计算出电池的电量,这就是我们在Battery Information 里读到的wh. 值.而锂离子电池在多次使用后,放电曲线是会改变的,如果芯片一直没有机会再次读出完整的一个放电曲线,其计算出来的电量也就是不准确的.所以我们需要深充放来校准电池的芯片.二、手机锂电池工作原理手机锂电池的标称电压都是3.6V,充满后电压是4.2V,其实标准速率放电(0.2C,C是锂电池的容量)锂电池的放电平台一般是在3.7V,在锂电池包中其实还包括有一块保护板,保护板的主要作用是防止锂电池的过充过放及短路,所以虽然说在电池上标明了不能用金属物体短路电池的正负极,但其实你短路也没有关系的,保护板会动作切断放电回路。
聚合物锂离子电池 设计规范
一、叠片式聚合物锂离子电池设计规范1.设计容量为保证电池设计的可靠性和使用寿命,根据客户需要的最小容量来确定设计容量。
设计容量(mAh)= 要求的最小容量×设计系数(1)设计系数一般取1.03~1.10。
2.极片尺寸设计根据所要设计电池的尺寸,确定单个极片的长度、宽度。
极片长度Lp:Lp = 电池长度-A-B (2)极片宽度Wp:Wp = 电池宽度-C (3)包尾极片的长度Lp′:Lp′= 2Lp+ T'-1.0 (4)包尾极片的宽度Wp′:Wp′= Wp-0.5 (5)其中:A —系数,取值由电池的厚度T决定,当(1)T≤3mm时,对于常规电芯A一般取值4.5mm,大电芯一般取值4.8mm;(2)3mm<T≤4mm时,对于常规电芯A一般取值4.8mm,大电芯一般取值5.0mm;(3)4mm<T≤5mm时,对于常规电芯A一般取值5.0mm,大电芯一般取值5.2~6.0mm;(4)5mm<T≤6mm时,对于常规电芯A一般取值5.2mm, 大电芯一般取值5.4~6.0mm。
B —间隙系数,一般取值范围为3.6~4.0mm;C —取值范围一般为2.5~2.6mm(适用于双折边);T'—电芯的理论叠片厚度,T'的确定见6.1节.图1.双面极片、单面正极包尾极片示意图3. 极片数、面密度的确定:确定极片的数量N,并根据电池的设计容量来确定电极的面密度,电池的设计容量一般由正极容量决定,负极容量过剩。
在进行理论计算时,一般正极活性物质的质量比容量取140mAh/g,负极活性物质的质量比容量取300mAh/g。
N =(T-0.2)/0.35±1 (6)注:计算时N取整,并根据面密度的值来调整N。
S极片= Lp×Wp (7)C设= C正比×S极片×N×ρ正×η正(8)C负= C设×υ(9)= C负比×S极片×N×ρ负×η负(10)其中:S极片—单个极片的面积;C正比—正极活性物质的质量比容量,一般取值140mAh/g;η正—正极活性物质的百分含量;ρ正—正极极片的双面面密度(g/m2);C负—负极的设计容量;υ—负极容量过剩系数,一般常规电池取值1.00~1.06;DVD电池以及容量大于2000mAh的取值1.05~1.12;C负比—负极活性物质的质量比容量,一般取值300mAh/g;η负—负极活性物质的百分含量;ρ负—负极极片的双面面密度(g/m2);4. 极片厚度的确定:为保证极片中活性物质的性能发挥,涂布后的极片要进行适当轧片,一般根据材料的压实密度来确定不同面密度的极片的轧片厚度。
锂离子电池设计公式
锂离子电池设计公式
1.电池容量(C)
电池容量是电池存储和释放能量的能力。
单位通常为安时(Ah)。
电池容量可以通过公式C=Ixt计算,其中I是电流,t是电池的放电时间。
通常情况下,电池的容量指定为标称容量,即在特定条件下电池能够储存的电荷量。
2.循环寿命(CYCLE)
循环寿命是指电池能够进行多少次完全充放电循环,通常以CYCLE数目来表示。
循环寿命可以通过样品测试来确定,并用于评估电池的寿命和稳定性。
3.充电速率(CR)
充电速率是指电池接受充电电流的速度。
通常用C倍数来表示,其中C倍数为充电电流相对于电池容量的比例。
4.放电速率(DR)
放电速率是指电池输出电流相对于电池容量的比例。
放电速率可以通过C倍数来表示,其中C倍数为输出电流相对于电池容量的比例。
5.内阻(IR)
内阻是电池内部的电阻,它能够限制电池放电和充电的速度。
内阻通常用欧姆(Ω)来表示,并通过内阻测试方法进行测量。
以上是一些基本的设计公式,但实际上,在设计锂离子电池时,还有许多其他因素需要考虑,如温度特性、电池内部反应速率等。
所以以上公式只是设计中的一部分,实际设计中还需要综合考虑其他因素。
为了得到更好的锂离子电池设计结果,需要进行详细的实验和计算。
设计者需要根据电池的具体应用和要求,通过试验确定电池的各种参数,并根据实验结果进行调整和优化,以获得更好的性能和稳定性。
总结起来,锂离子电池的设计公式通常包括电池容量、循环寿命、充电速率、放电速率和内阻等参数,然而,实际设计中还需要综合考虑其他因素,并通过详细的实验和计算来优化电池的性能和稳定性。
锂离子电池设计总结
锂离子电池设计总结(一)液锂电池设计(1)根据壳子推算卷芯1、核算容量:(设计最低容量= average * )2、极片宽度:隔膜宽度= 壳子高- - 2 - -图纸高壳子底厚盖板厚绝缘垫厚余量负极片宽度= 隔膜纸宽度- 2mm正极片宽度= 负极片宽度- (1~2mm)注:核算后正负极片宽度要去查找分切刀,最好有对应分切刀;箔材的选择也要依分切刀而定。
比如:40mm的分切刀,可以一次分裁8片,则箔材尺寸应该为40*8+(10~15余量)=330~335mm,若没有合适的也可以选择40*7+(10~15mm)的箔材。
3、卷芯宽度:卷芯设计宽度= 壳子宽度- -(~)图纸宽度两层壳壁厚余量4、卷芯厚度:(1)卷芯设计厚度= 壳子厚度- -图纸厚度两层壳壁厚余量(2)卷芯设计厚度= (规格厚度––)/规格书厚度max 余量两层壳壁厚膨胀系数5、卷尺宽度:卷尺= 卷芯宽–卷芯厚–卷尺厚()–(~)余量6、最后根据(2、3、4)进行调整、确认。
7、估算卷芯/电芯最终尺寸卷芯厚度= 正极片厚+ 负极片厚+ (隔膜厚*2)卷芯宽度= 卷尺宽+ 卷尺厚+ 卷芯厚+(1~)余量最终电芯厚度= 卷芯厚度* + 壳子厚度+(~)层数单层厚度卷芯厚卷芯厚* +(~)≤规格要求(二)电池设计注意事项:1、极耳距极片底部≤极片宽度*1/42、极耳外露≥12mm~15mm 负极耳外露:6~10mm3、小隔膜= 加垫隔膜处光泊区尺寸+(2~3mm)4、壳子底部铝镍复合带尺寸:4mm * 13mm * (当壳子底部宽w ≥7mm时)3mm * 13mm * (当壳子底部宽w <7mm时)5、极片称重按涂布时箔材和敷料计算极片称重(正负极片相同)敷料量:M1 铝箔重:M2重片:M1 + M2 + ~ M1 * + M2轻片:M1 * + M2 ~ M1 + M26、胶纸贴法:负极耳上高温胶纸应超出负极片4 ~ 6 mm正极耳上透明胶纸应超出负极片2 ~ 4 mm7、面密度精确度:Eg:m±n 其中:n为m 的4% 。
铝壳锂离子电池设计
铝壳锂离子电池设计一、铝壳锂离子电池设计的内容铝壳锂离子电池设计包括:1、五金设计2、电芯设计五金设计包括:1、铝壳尺寸设计2、盖帽尺寸设计电芯设计包括:1卷针尺寸设计2、极片尺寸设计3、隔膜尺寸设计4、正负极负料设计5、刮粉位、留粉位尺寸确定6、极耳尺寸设计7、注液量设计8、其他辅助设计:胶纸尺寸等。
二、五金件设计1、电池尺寸参数厚度Hο、宽度Wο\高度Lο2、铝壳尺寸设计1.1铝壳尺寸参数:外厚H外、外宽W外、外高L外、正壁厚、侧壁厚、底厚、内厚H内、内宽W内、内高L内1.2铝壳尺寸参数设计:H外=H0-(0.2~0.4)mm;W外=W0-(0.2~0.3)mm;L外=L0-(1.0~1.5)mm;正壁厚=(0.2~0.4)mm;侧壁厚=(0.3~0.4)mm;底厚=(0.5~0.6)mm。
H内=H外-2*正壁厚;W内=W外-2*侧壁厚;L内=L外-底厚1.3盖帽尺寸参数:长度、宽度、厚度、铆钉位置、铆钉尺寸、边缘、连接片宽度、连接片长度、密封圈尺寸等。
1.4盖帽尺寸参数设计(主要由结构工程师根据铝壳尺寸完成)三、电芯参数设计1、卷针设计1.1方卷针厚度=(1.5~2.0)mm;1.2方卷针宽度≈壳内宽-壳内厚-卷针厚度-C(经验系数,C>0);1.3壳内厚≈卷芯、厚度1.4圆卷针与方卷针换算:方卷针宽度=(圆卷针直径*π-2*方卷针厚度)/2+C(经验系数)2、隔膜纸尺寸设计2.1 隔膜纸宽度=壳内高-(2~2.5)mm=电池高度-(3.5~4)2.2 隔膜纸长度=2*负极片长度+(16~25)mm(使用圆卷针时此值要大于使用方卷针)2.3 隔膜纸厚度(根据实际情况要求决定)3、极片尺寸设计3.1 负极片宽度=隔膜纸宽度-2mm正极片宽度=负极片宽度-(1~2)mm3.2 正极片长度=正极片折数*正极片平均折长(试卷,可建公式近似计算)负极片长度=负极片折数*负极片平均折长(试卷,可建公式近似计算)3.3正极片折数≈壳内厚/(0.33~0.35)负极片折数=正极片折数-13.4正极片厚度=铝箔厚度+附料厚度=铝箔厚度+(面密度/压实密度)负极片厚度=铜箔厚度+附料厚度=铜箔厚度+(面密度/压实密度)4、面密度设计正极面密度=(正极附料量-(0.05~0.1)g/【正极片长度-1/2*(刮粉位之和)】≈(41~46)mg/cm²负极面密度=正极面密度*正极克容量*正极活性物含量*(1.025~1.045)/(负极克容量*负极活性物含量)≈﹙18~21﹚mg/cm²5、附料量设计正极附料量=标称容量*(1.035~1.065)/正极克容量/正极活性物含量6、极耳尺寸设计极耳宽度=(3~5)mm;正极耳长度≈负极片宽度+电池厚度-C1(经验系数,可建公式近似计算)负极耳长度≈负极片宽度+电池厚度-C2(经验系数,可建公式近似计算)7、刮粉位、留粉位尺寸确定正极:A=正极耳宽度+(0~0.5)B≈方卷针宽度-A-1/2*CC=2*F(负极)+(6~10)mm负极:E=负极耳宽度F=E+2mm8、注液量设计注液量=电池设计容量/(310~320)四、电芯设计需要注意的几个问题1、电芯厚度1.1套壳时电芯厚度=(正极厚度+负极厚度+隔膜厚度)*空隙率系数+0.1mm正极厚度=正极片辊压厚度+烘烤反弹厚度)*(正极片折数-1)+铝箔厚度隔膜厚度=隔膜规格厚度*负极片折数*21.2正面套壳空间正面套壳空间=铝壳内厚-套壳时电芯厚度≥01.3侧面套壳空间侧面套壳空间=壳内宽—卷针宽度—卷针厚度—套壳时电芯厚度=(0~1)mm2、电池厚度2.1 设计电池厚度=(正极厚度+负极厚度+隔膜厚度)*空隙率系数+2*壳正壁厚正极厚度=(正极片辊压厚度+分容后反弹厚度)*(正极片折数-1)+铝箔厚度负极厚度=(负极片面密度/分容后压实密度)*负极片折数+铜箔厚度隔膜厚度=隔膜规格厚度*负极片折数*22.2 电池厚度空间电池厚度空间=电池厚度规格上限-设计电池厚度=(0.2~0.5)mm3、电池空隙率3.1 电池空隙率=(铝壳内部空间-正极所占空间-负极所占空间-铜箔铝箔所占空间-隔膜纸所占空间)/铝壳内部空间铝壳内部空间=壳内高*壳内宽*壳内厚正极所占空间=正极附料量/正极真实密度负极所占空间=负极料量/负极实密度铜箔所占空间=铜箔长度*铜箔宽度*铜箔厚度铝箔所占空间=铝箔长度*铝箔宽度*铝箔厚度隔膜纸所占空间=隔膜纸长度*隔膜纸宽度*隔膜纸厚度3.2 注液系数注液系数=注液量/电解液密度/(铝壳内部空间*电池空隙率)≈(0.7~0.9)。
- 1、下载文档前请自行甄别文档内容的完整性,平台不提供额外的编辑、内容补充、找答案等附加服务。
- 2、"仅部分预览"的文档,不可在线预览部分如存在完整性等问题,可反馈申请退款(可完整预览的文档不适用该条件!)。
- 3、如文档侵犯您的权益,请联系客服反馈,我们会尽快为您处理(人工客服工作时间:9:00-18:30)。
锂离子电池设计总结
(一)液锂电池设计
(1)根据壳子推算卷芯
1、核算容量:(设计最低容量= average * 0.935)
2、极片宽度:
隔膜宽度= 壳子高- 0.6 - 2 - 0.3 - 0.5
图纸高壳子底厚盖板厚绝缘垫厚余量
负极片宽度= 隔膜纸宽度- 2mm
正极片宽度= 负极片宽度- (1~2mm)
注:核算后正负极片宽度要去查找分切刀,最好有对应分切刀;箔材的选择也要依分切刀而定。
比如:40mm的分切刀,可以一次分裁8片,则箔材尺寸应该为40*8+(10~15余量)=330~335mm,若没有合适的也可以选择40*7+(10~15mm)的箔材。
3、卷芯宽度:
卷芯设计宽度= 壳子宽度- 0.6 -(0.5~1.5)
图纸宽度两层壳壁厚余量
4、卷芯厚度:
(1)卷芯设计厚度= 壳子厚度- 0.6 - 0.6
图纸厚度两层壳壁厚余量
(2)卷芯设计厚度= (规格厚度–0.2 –0.6)/ 1.08
规格书厚度max 余量两层壳壁厚膨胀系数
5、卷尺宽度:
卷尺= 卷芯宽–卷芯厚–卷尺厚(0.5mm)–(1.5~2.5)余量
6、最后根据(2、3、4)进行调整、确认。
7、估算卷芯/电芯最终尺寸
卷芯厚度= 正极片厚+ 负极片厚+ (隔膜厚*2)
卷芯宽度= 卷尺宽+ 卷尺厚+ 卷芯厚+(1~2.5)余量
最终电芯厚度= 卷芯厚度* 1.08 + 壳子厚度+(0.2~0.5)
层数单层厚度卷芯厚卷芯厚* 1.08 +(0.3~0.4)≤规格要求
(二)电池设计注意事项:
1、极耳距极片底部≤极片宽度*1/4
2、极耳外露≥12mm~15mm 负极耳外露:6~10mm
3、小隔膜= 加垫隔膜处光泊区尺寸+(2~3mm)
4、壳子底部铝镍复合带尺寸:
4mm * 13mm * 0.1mm (当壳子底部宽w ≥7mm时)
3mm * 13mm * 0.1mm (当壳子底部宽w <7mm时)
5、极片称重按涂布时箔材和敷料计算
极片称重(正负极片相同)敷料量:M1 铝箔重:M2
重片:M1 + M2 + 0.01 ~ M1 * 1.04 + M2
轻片:M1 * 0.96 + M2 ~ M1 + M2
6、胶纸贴法:
负极耳上高温胶纸应超出负极片4 ~ 6 mm
正极耳上透明胶纸应超出负极片2 ~ 4 mm
7、面密度精确度:
Eg:m±n 其中:n为m 的4% 。
即ρ= m ±4% * m
8、滚压前后极片延伸问题:
正极片滚压后极片延伸量为总长度的5% 即总长度L * 1.005为压片后长度
负极片滚压前比滚压后多给出 3 mm 铜箔,要切掉。
9、隔膜纸长度:
隔膜纸长度= 负极片长度* 2 + (30~35mm)
10、注液量:
注液量= 设计容量* (0.0030~0.0033)
11、压片厚度:
正极= 面密度(eg:22.1)/正极压实(eg:纯钴3.75)* 20 + 铝箔厚(eg:16μm或20μm)
= 22.1 / 3.75 * 20 + 16
负极= 面密度/ 负极压实* 20 + 铜箔厚
(三)设计常识:
1、固含量:固含量应该设计在65% 左右。
-------------------------------------------
正极的敷料量=标称容量/可比容量
正极面密度=正极的敷料量/正极敷料量面积
负极面密度=正极面密度*正极纯克比*正极活性物质含量*1.1/负极纯克比/负极活性物质含量
正极厚度=正极面密度/压实密度*20+箔材厚度(负极相同)
卷芯入壳松紧比=(正极长*厚+负极长*厚+隔膜长*厚)/壳子的横截面积
2、压实密度:
正极材料:LC:3.75;LNCM:3.3;LM:2.8
负极材料:SAG-23:1.4;K31、AMG-18、KMD、SKG-2:1.55;
BTR918反弹率为1.4%
其他压实可以配比计算eg:
LC (3) + LM (7) :则压实为0.3 * 3.75 + 2.8 * 0.7 (克比也这样计算)
3、克比:
正极材料:纯CO:142;三元:143;纯Mn:105;
负极材料:KMD、SKG-1:360;SAG-2:320;AMG-18、K31:340
另外:高压实密度锂钴BM-470 :克比142 ;压实3.95 。
4、配方:
正极:除LC;LC/LM=9:1;LNCM三个活性物质配方为93.8%+2%super-P+ 1.2%S-0+3%PVDF;其余配方都是93.5% LOADING,只是再PVDF上多加0.3% 。
负极:除KMD 需要多加一个点super-P为94.2 LOADING(94.2%+1.3%CMC+ 2.5%SBR+2%super-P);其余都为95.2% LOADING(95.2%+1.3%CMC+2.5%SBR+1%super-P)
注:(1)各物质配比都是干粉的百分比,不计算NMP。
(eg:LC=干粉*93.8%)(2)固含量=LC/93.8%/(1-NMP%)* NMP%。