金属材料及热处理 04 淬火与时效
淬火时效及其材料的意义
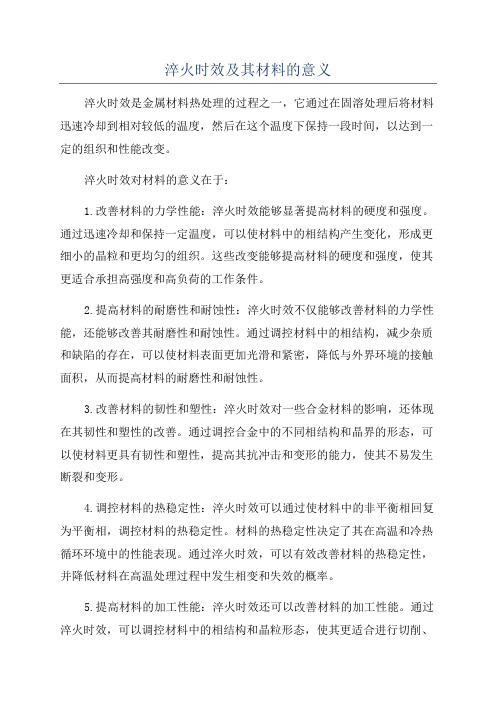
淬火时效及其材料的意义淬火时效是金属材料热处理的过程之一,它通过在固溶处理后将材料迅速冷却到相对较低的温度,然后在这个温度下保持一段时间,以达到一定的组织和性能改变。
淬火时效对材料的意义在于:1.改善材料的力学性能:淬火时效能够显著提高材料的硬度和强度。
通过迅速冷却和保持一定温度,可以使材料中的相结构产生变化,形成更细小的晶粒和更均匀的组织。
这些改变能够提高材料的硬度和强度,使其更适合承担高强度和高负荷的工作条件。
2.提高材料的耐磨性和耐蚀性:淬火时效不仅能够改善材料的力学性能,还能够改善其耐磨性和耐蚀性。
通过调控材料中的相结构,减少杂质和缺陷的存在,可以使材料表面更加光滑和紧密,降低与外界环境的接触面积,从而提高材料的耐磨性和耐蚀性。
3.改善材料的韧性和塑性:淬火时效对一些合金材料的影响,还体现在其韧性和塑性的改善。
通过调控合金中的不同相结构和晶界的形态,可以使材料更具有韧性和塑性,提高其抗冲击和变形的能力,使其不易发生断裂和变形。
4.调控材料的热稳定性:淬火时效可以通过使材料中的非平衡相回复为平衡相,调控材料的热稳定性。
材料的热稳定性决定了其在高温和冷热循环环境中的性能表现。
通过淬火时效,可以有效改善材料的热稳定性,并降低材料在高温处理过程中发生相变和失效的概率。
5.提高材料的加工性能:淬火时效还可以改善材料的加工性能。
通过淬火时效,可以调控材料中的相结构和晶粒形态,使其更适合进行切削、冷加工和热加工等工艺过程。
改善材料的加工性能,可以提高生产效率和降低生产成本。
总而言之,淬火时效在金属材料热处理中具有重要意义,能够显著改善材料的力学性能、耐磨性和耐蚀性、韧性和塑性、热稳定性以及加工性能。
这些改变使材料更适合承担各种工作条件和环境要求,从而提高产品的质量和可靠性。
第六章 淬火与时效(1)
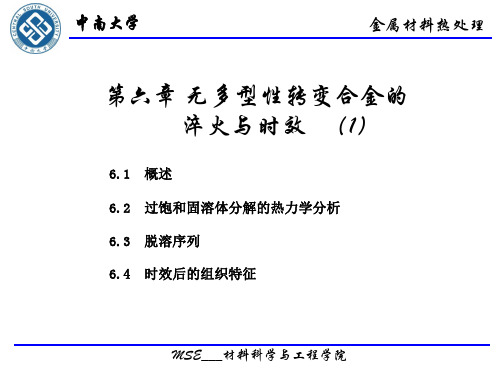
为塑性提高,虽然强度有下降)。
3. 与铸造态合金比较:塑性提高。铸态组织(第二相)
MSE___材料科学与工程学院
中南大学
c. 固溶处理的应用
金属材料热处理
1.目的:获得过饱和固溶体(尽可能使基体成分均匀)。
热处理强化铝合金中常用
2.在某些合金如QBe 、Cr18Ni9钢等可作为冷变形前的软化处 理(中间退火)。
中南大学
金属材料热处理
Note:
At the early stage of formation of G.P zone, the clustering sequence is changeable, e.g. in the Al-Mg-Si alloys. The general sequence is as follows: Through Atomic Probe Field Ion Microscopy-(APFIM) Clusters of Si atoms Clusters of Mg atoms
金属材料热处理
列
G.P(spheric)→’(flake) →(Ag2Al) G.P(pole) → ’’→ → ’→ (Mg2Si) G.P(plate)→’’(plate)→ ’ → (CuAl2)
Cu
Fe Ni
Cu-Be
Fe-C (pure Fe) Ni-Cr-Al-Ti
G.P(plate)→’ →(2)(CuBe)
分解驱动力:体积Gibbs能之差。
分解阻力: 梯度能:化学键失去平衡导致能量增加。浓度梯度 应变能:成分分离必然引起晶格常数变化从而导致共格应变能。
MSE___材料科学与工程学院
中南大学 G T
2’
2
金属材料的热处理

金属材料的热处理金属材料的热处理是指通过加热、保温和冷却等一系列工艺,改变金属材料的组织结构和性能的方法。
热处理可以使金属材料获得理想的组织和性能,从而满足不同工程需求。
在工程实践中,热处理是非常重要的一环,下面我们来详细了解一下金属材料的热处理过程。
首先,我们来谈谈金属材料的热处理工艺。
热处理工艺包括退火、正火、淬火、回火等几种主要方法。
其中,退火是指将金属材料加热到一定温度,然后通过控制冷却速度,使其组织发生改变,消除应力和提高塑性。
正火是指将金属材料加热到一定温度,然后保温一段时间,再进行适当冷却,以改善其硬度和强度。
淬火是指将金属材料加热到临界温度以上,然后迅速冷却,使其获得高硬度和高强度。
回火是指在淬火后,将金属材料重新加热到一定温度,然后进行适当冷却,以减轻淬火所产生的脆性。
其次,我们来讨论金属材料热处理的影响因素。
热处理的效果受到许多因素的影响,如加热温度、保温时间、冷却速度等。
加热温度是影响热处理效果的关键因素之一,不同金属材料对应的加热温度也不同。
保温时间是指金属材料在一定温度下的停留时间,它决定了金属材料的组织结构和性能。
冷却速度也是影响热处理效果的重要因素,不同冷却速度会导致金属材料组织结构和性能的差异。
最后,我们来总结一下金属材料热处理的应用。
金属材料的热处理广泛应用于航空航天、汽车制造、机械制造等领域。
通过热处理,可以改善金属材料的力学性能、耐磨性能、耐蚀性能等,提高其使用寿命和可靠性。
因此,热处理在工程实践中具有非常重要的意义。
综上所述,金属材料的热处理是一项非常重要的工艺,通过合理的热处理工艺,可以使金属材料获得理想的组织和性能。
在实际应用中,我们需要根据不同金属材料的特点和工程需求,选择合适的热处理工艺,以获得最佳的效果。
希望本文能够对大家了解金属材料的热处理有所帮助。
淬火时效及其材料的意义

淬火时效及其材料的意义淬火是把合金加热到固溶体溶解曲线上,保温一段时间,然后以大于临界冷却速度急速冷却,从而得到过饱和固溶体的热处理方法。
淬火的目的:强化钢件,充分发挥钢材性能的潜力.如:提高钢件的机械性能,诸如硬度、耐磨性、弹性极限、疲劳强度等,改善某些特殊钢的物理或者化学性能,如增强磁钢的铁磁性, 提高不锈钢的耐蚀性等。
淬火后对不同合金的性能也有所不同:对铝合金及大多数有色金属合金而言,经过淬火,不同合金也有不同①。
增加,6或W减少②。
减少,3或W增加③。
增加,6或W增加④。
、6、ψ基本不变淬火后性能出现差异的原因:固溶强化与第二相(或称过剩相,表示与固溶体平衡的其他相)强化之间的差异造成的。
若淬火前第二相的强化效果<淬火后固溶强化效果,则淬火后合金强度增加;反之淬火前第二相的强化效果>淬火后固溶强化效果,则淬火后合金强度减少。
钢的淬火:将钢件加热到AC3或ACl相变点以上的某一温度,保持一段时间,然后以大于Vk的速度冷却,获得马氏体或下贝式体组织的热处理工艺。
淬火后必须进行回火处理。
回火的目的是:⑴降低脆性,消除应力,防止钢件变形甚至开裂。
⑵获得工件所需要的力学性能,调整硬度,减小脆性,得到韧性和塑性。
⑶稳定工件尺寸,因为马氏体是不稳定组织。
淬火是提高材料的强度和硬度,就是材料抗弯曲扭曲变形的能力和抗划痕的能力,可淬火后材料内部有很高的内应力,容易降低材料的疲劳强度(就是材料抵抗中高频率轻微震动产生裂纹的能力),回火可以有效的去处材料的内应力一般根据具体应用不同可以分为淬火 +高温回火(就是调质处理),淬火+中温回火和淬火+低温回火,淬火的目的是使材料内部形成马氏体组织,不同材料的结晶温度也不一样,要使此种材料在何种温度下及在某一温度段保温时间都很有讲究,是非常专业的一门学科,所以选用的淬火介质和多少材料使用多少淬火介质溶液都有相当高的要求。
表面淬火钢的表面淬火有些零件在工件时在受扭转和弯曲等交变负荷、冲击负荷的作用下,它的表面层承受着比心部更高的应力。
重庆大学硕士研究生考试试题金属学与热处理((含金属材料))04版
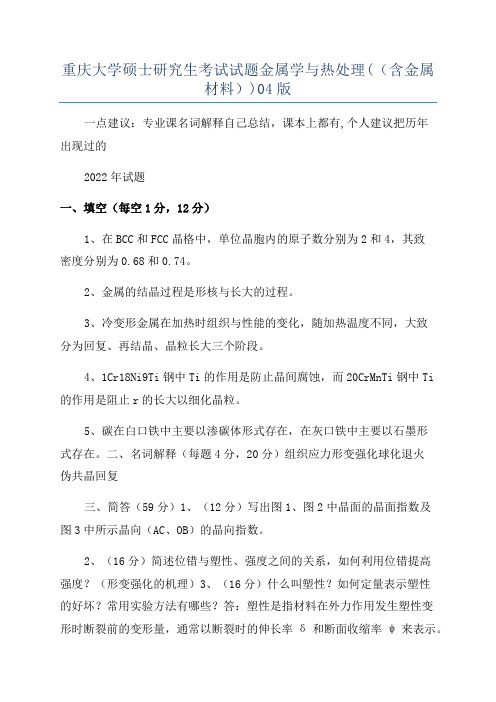
重庆大学硕士研究生考试试题金属学与热处理((含金属材料))04版一点建议:专业课名词解释自己总结,课本上都有,个人建议把历年出现过的2022年试题一、填空(每空1分,12分)1、在BCC和FCC晶格中,单位晶胞内的原子数分别为2和4,其致密度分别为0.68和0.74。
2、金属的结晶过程是形核与长大的过程。
3、冷变形金属在加热时组织与性能的变化,随加热温度不同,大致分为回复、再结晶、晶粒长大三个阶段。
4、1Cr18Ni9Ti钢中Ti的作用是防止晶间腐蚀,而20CrMnTi钢中Ti的作用是阻止r的长大以细化晶粒。
5、碳在白口铁中主要以渗碳体形式存在,在灰口铁中主要以石墨形式存在。
二、名词解释(每题4分,20分)组织应力形变强化球化退火伪共晶回复三、简答(59分)1、(12分)写出图1、图2中晶面的晶面指数及图3中所示晶向(AC、OB)的晶向指数。
2、(16分)简述位错与塑性、强度之间的关系,如何利用位错提高强度?(形变强化的机理)3、(16分)什么叫塑性?如何定量表示塑性的好坏?常用实验方法有哪些?答:塑性是指材料在外力作用发生塑性变形时断裂前的变形量,通常以断裂时的伸长率δ和断面收缩率ψ来表示。
常用方法:单向静拉伸实验法,压痕法,记忆材料法。
4、(15分)比较下贝氏体与高碳马氏体的主要不同点答:①从组成上看,马氏体是C在α—Fe中过饱和的间隙固溶体,下贝氏体是由含碳过饱和的片状α和其内部析出的ε—C化物组成②下贝氏体中无孪晶亚结构存在,高碳马氏体含有大量孪晶③下贝氏体比高碳马氏体具有更高的韧性,较低的缺口敏感性和裂纹敏感性。
2022年试题:一、名词解释(每题4分,20分)金属键刃型位错结晶潜热缩松真实应力二、简答(60分)1、(12分)某晶体的原子位于正方晶格的节点上,其晶格常数a=b≠c,c=(2/3)a,今有一晶面在某YZ坐标轴上的截距分别为5个原子间距,2个原子间距和3个原子间距,求该晶面的晶面指数。
常用金属材料及热处理

常用金属材料及热处理金属是人类社会重要的材料之一,广泛应用于各行各业。
常见的金属材料包括铁、铝、铜、钢等。
在使用金属材料的过程中,为了改善其性能,常常需要对其进行热处理。
下面将介绍一些常用的金属材料和其热处理方法。
1.铁:铁是一种性能优良的金属材料,常用于制作建筑结构、机械零件等。
铁的热处理方法有退火、正火、淬火和回火等。
退火可以降低材料的硬度,提高其塑性和延展性;正火可以提高材料的韧性和强度;淬火可以使材料获得高硬度和耐磨性;回火可以降低材料的脆性,并改善其强度和韧性。
2.铝:铝是一种轻质金属,常用于制造飞机、汽车等产品。
铝的热处理方法有固溶处理、时效硬化等。
固溶处理可以改善铝的强度和塑性;时效硬化可以在固溶处理基础上,进一步提高铝的强度和硬度。
3.铜:铜是一种导电性能优良的金属材料,常用于制造导线、电路板等。
铜的热处理方法有退火、退火软化等。
退火可以消除铜材料中的应力,改善其韧性和延展性;退火软化可以使铜材料变得更加易加工。
4.钢:钢是一种优质的金属材料,常用于制造建筑结构、机械零件等。
钢的热处理方法有退火、正火、淬火和回火等。
不同的钢材在热处理时的温度和时间以及冷却速度等参数都有所差异,可以根据具体需要来选择合适的热处理方法,以获得理想的性能。
此外,还有许多其他金属材料也需要经过热处理来改善其性能,比如镍、锌、锡等。
热处理方法的选择应根据具体的金属材料以及使用要求来确定。
综上所述,金属材料在使用过程中,经常需要进行热处理来改善其性能。
不同的金属材料有不同的热处理方法,通常包括退火、正火、淬火和回火等。
通过热处理可以改变金属材料的组织结构和性能,使其达到更加理想的状态。
热处理技术在金属材料的应用中起着重要的作用,对于提高产品质量和使用寿命具有重要意义。
金属材料热处理
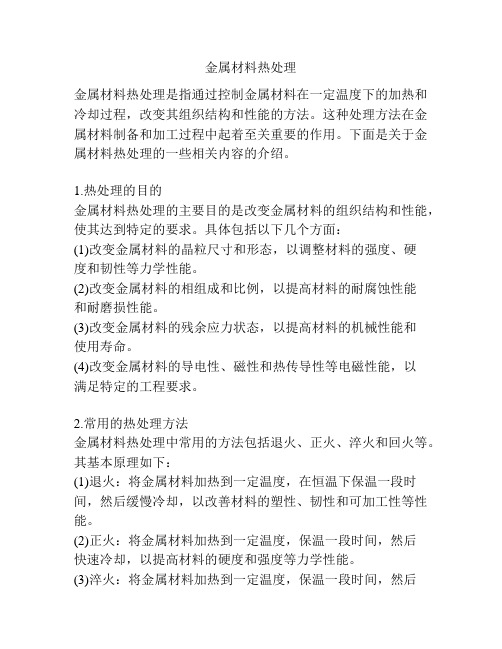
金属材料热处理金属材料热处理是指通过控制金属材料在一定温度下的加热和冷却过程,改变其组织结构和性能的方法。
这种处理方法在金属材料制备和加工过程中起着至关重要的作用。
下面是关于金属材料热处理的一些相关内容的介绍。
1.热处理的目的金属材料热处理的主要目的是改变金属材料的组织结构和性能,使其达到特定的要求。
具体包括以下几个方面:(1)改变金属材料的晶粒尺寸和形态,以调整材料的强度、硬度和韧性等力学性能。
(2)改变金属材料的相组成和比例,以提高材料的耐腐蚀性能和耐磨损性能。
(3)改变金属材料的残余应力状态,以提高材料的机械性能和使用寿命。
(4)改变金属材料的导电性、磁性和热传导性等电磁性能,以满足特定的工程要求。
2.常用的热处理方法金属材料热处理中常用的方法包括退火、正火、淬火和回火等。
其基本原理如下:(1)退火:将金属材料加热到一定温度,在恒温下保温一段时间,然后缓慢冷却,以改善材料的塑性、韧性和可加工性等性能。
(2)正火:将金属材料加热到一定温度,保温一段时间,然后快速冷却,以提高材料的硬度和强度等力学性能。
(3)淬火:将金属材料加热到一定温度,保温一段时间,然后快速冷却,以在材料中形成淬火组织,提高材料的硬度和耐磨性能等。
(4)回火:将淬火后的金属材料再次加热到一定温度,保温一段时间,然后冷却,以消除淬火过程中的残余应力和脆性,并调整材料的力学性能。
3.常见的金属材料与热处理方法的应用各种金属材料的组织结构和性能特点不同,因此在热处理过程中需要选择不同的方法和参数。
以下是一些常见金属材料的热处理方法及其应用:(1)碳钢:通过正火和淬火处理,可以提高碳钢的硬度、强度和耐磨性能,广泛应用于机械加工和制造业。
(2)不锈钢:通过固溶和沉淀硬化处理,可以改善不锈钢的耐腐蚀性能和耐磨损性能,常见于化工和海洋工程。
(3)铝合金:通过固溶处理和时效处理,可以改善铝合金的强度、韧性和耐腐蚀性能,常用于航空和汽车制造业。
金属材料的热处理工艺及性能改善技术
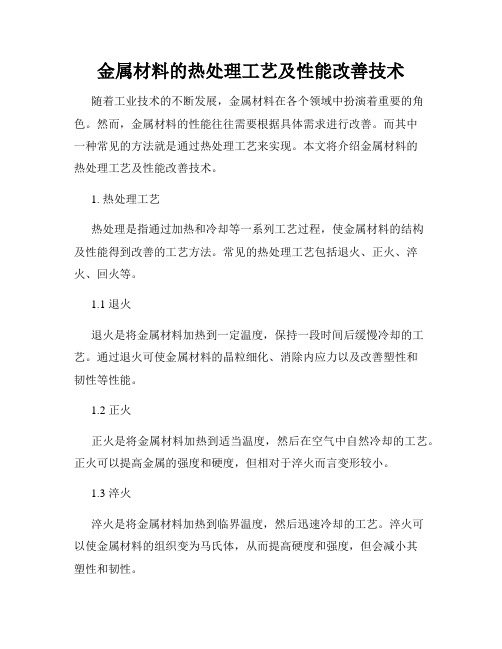
金属材料的热处理工艺及性能改善技术随着工业技术的不断发展,金属材料在各个领域中扮演着重要的角色。
然而,金属材料的性能往往需要根据具体需求进行改善。
而其中一种常见的方法就是通过热处理工艺来实现。
本文将介绍金属材料的热处理工艺及性能改善技术。
1. 热处理工艺热处理是指通过加热和冷却等一系列工艺过程,使金属材料的结构及性能得到改善的工艺方法。
常见的热处理工艺包括退火、正火、淬火、回火等。
1.1 退火退火是将金属材料加热到一定温度,保持一段时间后缓慢冷却的工艺。
通过退火可使金属材料的晶粒细化、消除内应力以及改善塑性和韧性等性能。
1.2 正火正火是将金属材料加热到适当温度,然后在空气中自然冷却的工艺。
正火可以提高金属的强度和硬度,但相对于淬火而言变形较小。
1.3 淬火淬火是将金属材料加热到临界温度,然后迅速冷却的工艺。
淬火可以使金属材料的组织变为马氏体,从而提高硬度和强度,但会减小其塑性和韧性。
1.4 回火回火是将淬火后的金属材料再次加热到适当温度后冷却的工艺。
通过回火可以减轻淬火带来的脆性,提高金属材料的韧性和塑性。
2. 性能改善技术除了热处理工艺外,还有一些其他的技术可以用于金属材料的性能改善。
2.1 表面处理技术表面处理技术可以通过改变金属材料的表面结构和成分,来提升其耐磨性、耐腐蚀性以及表面光洁度等性能。
常见的表面处理技术包括电镀、喷涂和化学处理等。
2.2 合金化合金化是指将金属材料与其他元素进行混合,形成新的合金材料的过程。
通过合金化可以改变金属材料的组织结构和成分,从而改善其硬度、耐磨性、耐腐蚀性等性能。
2.3 疲劳寿命改善技术金属材料在长时间的使用过程中往往会出现疲劳破坏。
为了提高金属材料的疲劳寿命,可以采用表面强化、应力调控和表面涂覆等技术来改善材料的耐疲劳性能。
2.4 加工技术金属材料在加工过程中,其组织结构可能会发生变化,从而影响其性能。
因此,通过精确的加工技术可以使金属材料的性能得到改善。
- 1、下载文档前请自行甄别文档内容的完整性,平台不提供额外的编辑、内容补充、找答案等附加服务。
- 2、"仅部分预览"的文档,不可在线预览部分如存在完整性等问题,可反馈申请退款(可完整预览的文档不适用该条件!)。
- 3、如文档侵犯您的权益,请联系客服反馈,我们会尽快为您处理(人工客服工作时间:9:00-18:30)。
3、不形核自发分解(Spinodal 分解) 拐点或旋点(Spinodal point)
可能出现Spinodal分解的合金系有:Al-Zn、AuNi、Au-Pt、Nb-V、Zr-Nb、Cr-W、 Cu-Ni、CuRb、Ir-Pt等,其相图都存在 如图所示的混溶间 隙,析出相仅成分与母相存在差异,结构相同。 如图所示,自由能成分曲线必然存在其二阶导 数 d2G/dC2=0的点,即 s1 和 s2 两个点,可称之 为拐点或旋点(Spinodal point),成分在两拐 点 间 , d2G/dC2<0 , 而 在 两 拐 点 以 外 , d2G/dC2>0 。若将不同温度下的自由能成分曲 线的拐点的成分位置相应地表示在相图上,则 可得到旋点线(RKV),过冷到旋点线以下的 固溶体可能发生Spinodal 分解。
编织样花纹 周期排列的立方体
<100>晶向相互平行的杆状物三度 交织而成的调 幅组织(Cu-Ni-Fe)
<100>晶向呈周期排列分布的调幅 组织(Ni-Al)
4、按形核长大机制分解的固溶体脱溶
按形核-长大机制的分解(脱溶)的相变驱动力(1)
具有混合间隙的A-B 系(连续固溶体)
如图所示,在 s1 点左侧的 Co合金,它 的自由能G1大于平衡两相混合物自由 能 G2 ,因此, 存在分离成成分 Ca 和 Cb两相的趋势,若成分起伏造成微观 区域中的成分偏离 Cf和Cg,则因这段 自由能曲线下凹,成份分离后体系的 自由能G3较原始固溶体自由能G1高, 偏离不稳,易消失而不能继续发展。 只有产生大的浓度起伏(如 Cm 和 Cn ) 时,自由能才能下降,成分偏聚才能 稳定发展下去,直到达到平衡成分 (Ca和Cb)。 临界成分——(略)
淬火
时效
强 度 、 硬 度
温度或时间
5.2 固溶处理(只讨论基体无多型性变化的情况)
固溶过程的热力学分析
只要基体的固溶度随温度变化即可。铝、 T L
镁、铜、镍合金均可。
合金固溶处理前后性能的变化分析
不同合金性能变化会不相同,与合金成 分、原始组织、淬火工艺、淬火后组织 等有关:
一些合金处理后,其强度提高而塑性降
C0
A
C1
C0
C2
B
when C1→C0, i.e. a little amount of precipitates is form.
GV G 2 G1
n1G n 2 G n1 n 2 G (C 0 )
G (C 0 ) G n 2 G G (C 0 ) C 2 C 0 C C 0 1
Al-Cu:
α -Al ss
→ 偏聚(丛聚) →
G.P区
→
θ’’ → θ’
→
θ
产生原因: 脱溶初期界面能和弹性应变能影 响大。亚稳相多与基体共格或半
共格,降低形核功。
能量—— 成份—— 结构——
脱溶相结构简介(以Al-Cu为例)
G.P.区:起伏——偏聚——GP区
1906年首次在Al-Cu-Mg中发现。1938年A.Guinier, G.D.Preston 独立地在自然时 效的Al-Cu合金中发现。 固溶体中存在成分起伏(不稳),过冷,起伏增强,形成稳定丛聚(很小,难以 观察),一段时间后,丛聚发展成GP区,又称预脱溶期产物,或原子偏聚区。 G.P区特点:(1)与基体结构相同,但富集溶质原子,原子间距与基体不同; (2)与基体完全共格,界面能小,但应变能较高,其形状主要取决于共格应变 能,多呈盘碟状,也有球(Al-Sc)、杆的;(3) 作为G.P区的晶核微小,数量 大,形成速率快,与空位浓度有关,可以近似为均匀形核。均匀的空位和空位群 可成为G.P区的形核优先位置,增加空位浓度和寿命可获得大而多的G.P区, G.P区的形核和分布也相对均匀。(4)形成有两种机制:Spinodal分解和正常的 形核长大过程。
第五章 无多型性转变合金的 淬火与时效
Quenching and aging in the alloys without allotropic transformation in matrix
五、无多型性转变合金的淬火与时效
5. 1 概述 5. 2 固溶处理
5. 3 过饱和固溶体分解机制
1、脱溶过程的热力学基础 2、脱溶过程的相变驱动力及其在自由能-成分曲线上的表征 3、不形核自发分解(Spinodal 分解) 4、按形核长大机制分解的固溶体脱溶
TS TS* 2 2
E xB 1 xB Vm / R 1
化学Spinodal 分解
化 学 Spinodal 分 解 温 度 与 共 格 Spinodal 分解温度之差随晶格常数 变化率、杨氏模量、摩尔浓度以及 摩尔体积的变化。
共格旋点
共格Spinodal 分解
可能出现Spinodal分解的合金: Al-Zn,Al-Li合金的Fcc相的分解; Al-Cu合金中从Fcc基体析出G.P区; Fe-Cu 系中的液相凝固以及Fcc相的分解; Cu-Ag, Cu-Ni系中的Fcc相的分解等。
定发展。
浓度起伏生成 CIII , ΔGVIII 为负,晶核也 可稳定发展。 不论β相开始成分如何,最终发展的Cb。
形核---长大分解机制
L T0 A C0 + B A
T
G
GV G G
C1
C0
C2
B
沉淀粒子形核驱动力计算(经典形核理论)
G G
G GV
G D GV / n2 dG G G (C 0 ) C 2 C 0 dC
解成αa+αb两相组织。
G(T1)
B
然而,过饱和固溶体的脱溶可以以 两种不同类型的转变来完成: G (C2)——不形核自发分解 (Spinodal分解);
A
C2
( 1 ) 成 份 处 于 s1s2 之 间 的 合 金
G(T) s1 a s2 b B
( 2 ) 成 份 处 于 s1s2 之 外 的 合 金
形核阻力: 新相与母相之间的界面能; 比容积差导致的应变能。
临界晶核半径的决定因素: G GV GInter GE
按形核-长大机制的分解(脱溶)的相变驱动力 (2)
A-B共晶系
大多数合金具有共晶、包晶或其它类型的相 图,有过饱和固溶体中析出的相不仅成分与 原始固溶体不同,而且晶体结构也有区别。 如图所示,β相和α相结构各异,自由能曲线 不连续,无曲线上凸,没有Spinodal 分解的 可能性。因此,这种情形下,亚稳过饱和固 溶体分解过程是按形核长大机制进行的。 浓度起伏生成CI, ΔGVI为正,晶核不稳。 浓度起伏生成CII, ΔGVII为负,晶核可稳
弹性模量的各向异性也导致成分偏聚具有方向性。
Spinodal分解发生的实际温度
合金发生了 Spinodal 分解的可能性 应该用 Spinodal 分解的共格旋点来 估计。 化学 Spinodal 分解与共格 Spinodal 分 解(Without gradient energy)
1 T1 A 12 2’ 3’ 34 B A 混溶间隙 4 B G T 2’ 2 G(T) 3’ 3
但对于铸造合金而言,可以起到提高强
度和塑性,调节性能的作用。
5.3 过饱和固溶体分解机制
1、 脱溶过程的热力学基础
T
T1 T2 G G(T2) a b C1
这里,以一个具有混合间隙的 A-B 二元合金系为解说对象,以便我们
能较全面地了解过饱和固溶体分解 的相变驱动力和脱溶过程。
a
s1
s2
b
对于处于ab之间成分的合金,其过 饱和固溶体都会发生分解,自发分
(C1)——以形核长大过程的分解
A
2、脱溶过程的相变驱动力及其在自由能-成分曲线上的表征
相变驱动力是脱溶过程发生前后的体系自由能变化(差)
在温度T下,C0合金单相固溶体α摩尔自由 能为G0,析出少量成分C2脱溶晶核, α相成 分降至C1,二者摩尔自由能分别为G2 、 G1 。 若脱溶相摩尔数n1而脱溶后α基体的为n2, ΔG=G(析出后)-G(析出前) =(n1G1+n2G2)-( n1+n 2)G0
时效(回火)——亚稳过饱和固溶体分解, 时效与回火区别在于 基体转变与否?铝、 铜、钛和钢铁 。
2、工艺形式:
大多数情况下淬火+ 时效,但是也存在仅有 淬火(自然时效)和仅有时效(挤后冷即
淬)的情况
淬火
时效
3、目的与应用:
淬火(固溶处理)——获得过饱和固溶体: i、时效前的预处理; ii、冷加工前的中 间处理,消除加工硬化,消除脆硬相的有害影响;iii、最终热处理(固溶处理); 时效——使过饱和固溶体分解(脱溶、沉淀),用作最终热处理,调整组织性能。
5. 4 脱溶序列 5. 5 脱溶产物的组织特征 5. 6 时效前后合金性能的变化 5. 7 影响时效过程及材料性能的因素 5. 8 淬火(固溶处理)与时效的工艺规程 5. 9 小结
5. 1 概述
1、 基本概念:
淬火——高温快冷至低温,建立低温下的亚 稳态,形成过饱和固溶体的过程。 两种情
况有多型性和无多型性。
4、组织变化:
淬火(固溶处理)——可溶相溶解,形成过饱和 固溶体,基体发生回复、再结晶与晶粒长大; 时效——过饱和固溶体分解(脱溶、沉淀),粗 化,产生强化相颗粒,基体晶粒一般无明显变化。
5、性能变化:
淬火(固溶处理),分三种情况: i、若原始组织中第二相弥散且硬,固溶后强度下 降,塑性保持或提高(第二相沉淀强化大于固溶 强化); ii、若原始组织中第二相粗大、不弥散,固溶后强 度提高(第二相沉淀强化小于固溶强化) ; iii 、若原始组织中第二相脆硬,且沿晶界或网胞 呈网状分布,固溶后强度、塑性都会有明显提高 (第二相沉淀强化大于固溶强化,例如,铸造合 金的固溶处理)。 时效——如图所示。