数控机床传动系统设计介绍
数控机床的进给传动系统文档资料

图7-39滚珠丝杠螺母副
3
1-反向器 2-螺母 3-丝杠 4-滚珠
(2)滚珠丝杆螺母副的工作原理与特点 • 滚珠丝杠螺母副的结构形式
a)滚珠丝杠副轴向剖面图 滚珠丝杠螺母副
b)滚珠丝杠副法向剖面图
4
• (3)滚珠丝杠副的结构和轴向间隙的调整方法
•
1)螺纹滚道型面的形状及其主要尺寸。
21
(3) ①密封圈。密封圈装在滚珠螺母的两端。接触式的弹性密
封圈是用耐油橡皮或尼龙等材料制成的,其内孔制成与丝杠 螺纹滚道相配合的形状。接触式密封圈的防尘效果好,但因
非接触式的密封圈是用聚氯乙烯等材料制成的,其内孔形 状与丝杠螺纹滚道相反,并略有间隙。非接触式密封圈又称 为迷宫式密封圈。
②防护罩。对于暴露在外面的丝杠,一般采用螺旋钢带、伸缩 套筒以及折叠式塑料或人造革等形式的防护罩,以防止尘埃 和磨粒粘附到丝杠表面。这几种防护罩与导轨的防护罩有相 似之处,其一端连接在滚珠螺母的端面上,另一端固定在滚 珠丝杠的支撑座上。
3.齿差调隙式 在两个螺母1、5的端面法兰上分别加工出外齿Z1和Z2,并各自装入
对应的内齿圈6中。内齿圈通过螺钉固定在螺母外的套筒3端面。通常两个外齿 轮相差1齿(如Z1=100,Z2=99)。当调整间隙时,将两个外齿轮从内齿圈中抽出 并相对内齿圈分别同向转动一个齿,然后插回原内齿圈中。此时,两个螺母间产 生的相对位移为:
滚珠丝杠制动示意图
19
• 3)滚珠丝杆的防护 • 一般采用螺纹钢带、伸缩套筒、锥形套
筒以及折叠式塑料或人造革等形式的防护 罩。
20
滚珠丝杠的防护
(1)支撑轴承的定期检查。应定期检查丝杠与床 身的连接是否有松动以及支撑轴承是否损坏 等。如有以上问题,要及时紧固松动部位并
数控机床进给传动系统
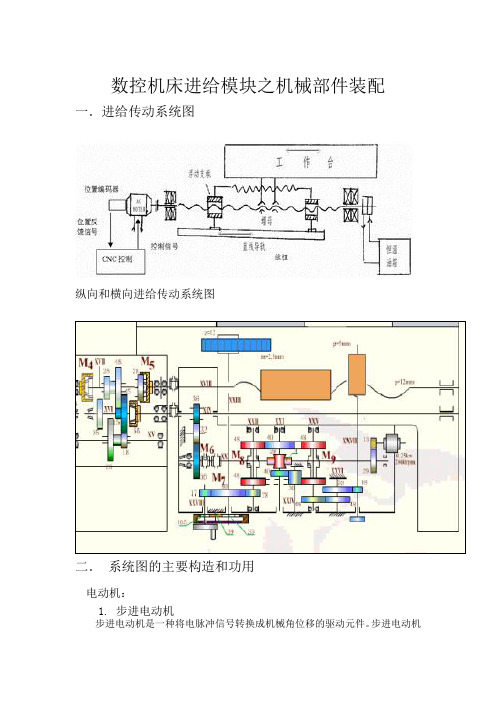
数控机床进给模块之机械部件装配一.进给传动系统图纵向和横向进给传动系统图二.系统图的主要构造和功用电动机:1. 步进电动机步进电动机是一种将电脉冲信号转换成机械角位移的驱动元件。
步进电动机是一种特殊的电动机,一般电动机通电后都是连续转动的,而步进电动机则有定位与运转两种状态。
当有一个电脉冲输入时,步进电动机就回转一个固定的角度,这角度称为步距角,一个步距角就是一步,所以这种电动机称为步进电动机。
又由于它输入的是脉冲电流,也称作脉冲电动机。
当电脉冲连续不断地输入,步进电动机便跟随脉冲一步一步地转动,步进电动机的角位移量和输入的脉冲个数严格成正比例,在时间上与输入脉冲同步。
因此,只需控制输入脉冲的数量、频率及电动机绕组的通电顺序,便可获得所需转角、转速和方向。
在无脉冲输入时,步进电动机的转子保持原有位置,处于定位状态。
步进电动机的调速范围广、惯量小、灵敏度高、输出转角能够控制,而且有一定的精度,常用作开环进给伺服系统的驱动元件。
与闭坏系统相比,它没有位置速度反馈回路,控制系统简单,成本大大降低,与机床配接容易,使用方便,因而在对精度、速度要求不十分高的中小型数控机床上得到了广泛地应用。
2. 直流伺服电动机由于数控机床对进给伺服驱动装置的要求较高,而直流电动机具有良好的调速特性,因此在半闭坏、闭坏伺服控制系统中,得到较广泛地使用。
直流进给伺服电动机就其工作原理来说,虽然与普通直流电动机相同。
然而,由于机械加工的特殊要求,一般的直流电动机是不能满足需要的。
首先,一般直流电动机转子的转动惯量过大,而其输出转矩则相对较小。
这样,它的动态特性就比较差,尤其在低速运转条件下,这个缺点就更突出。
在进给伺服机构中使用的是经过改进结构,提高其特性的大功率直流伺服电动机,主要有以下两种类型:(1)小惯量直流电动机。
主要结构特点是其转子的转动惯量尽可能小,因此在结构上与普通电动机的最大不同是转子做成细长形且光滑无槽。
以此表现为转子的转动惯量小,仅为普通直流电动机的1/10左右。
CK6140数控车床主传动系统设计

CK6140数控车床主传动系统设计数控车床的主传动系统是整个机床的核心组成部分,它主要由主轴、主轴驱动装置和主动工具头等组成。
设计一个稳定可靠的数控车床主传动系统,需要考虑诸多因素,如主轴精度、刚度、转速范围、加工能力等。
首先,主轴是数控车床主传动系统的核心部件,其精度和刚度直接影响到整个机床的加工质量。
主轴通常由高强度、高刚性的合金钢材料制成,并通过精密加工和热处理工艺提高其表面质量和硬度。
主轴的设计应考虑转动稳定性、轴向和径向刚度等因素,以确保在高速运转和大负载下能保持较小的振动和变形。
其次,主轴驱动装置主要是通过电机将动力传递给主轴,实现车床的加工运行。
常见的主轴驱动装置包括皮带传动、齿轮传动、液压传动等。
不同的传动方式具有不同的特点,需要根据数控车床的具体要求进行选择。
同时,主轴驱动装置还需要考虑电机的功率、转速调节范围、动态响应性能等因素,以满足不同加工工艺和加工材料的需求。
另外,主动工具头也是数控车床主传动系统的重要组成部分。
主动工具头一般由进给系统和切削工具组成,其主要功能是控制刀具的进给速度和刀具路径,实现工件的加工。
进给系统通常由伺服电机、滚珠丝杠等组成,将电机的旋转运动转化为刀具的直线运动。
切削工具的选择要根据不同的加工工件和加工要求进行,可以是转动刀具、切削刀具或磨削工具等。
除了上述部件,数控车床主传动系统的设计还需要考虑其控制方式和辅助装置。
传统的数控车床主传动系统采用闭环控制,通过编码器和反馈系统实现对主轴和主动工具头运动的精确控制。
辅助装置如冷却系统、润滑系统、自动换刀系统等,可以提高加工效率和工作环境的安全性。
总的来说,设计一个稳定可靠的数控车床主传动系统需要充分考虑主轴精度、刚度,主轴驱动装置的选择,主动工具头的设计以及控制方式和辅助装置的配置等因素。
只有在满足加工要求的前提下,才能实现高效、精确和安全的数控车床加工操作。
数控车床的主传动系统设计PPT

在进行动态特性分析时,需要考虑主轴的转速、转矩和刚度等参数,以及传动系统的固有频率和阻尼比等特性。 通过分析这些参数,可以评估主传动系统在加工过程中的稳定性,预测可能出现的振动和噪声问题,并采取相应 的措施进行优化设计。
强度与刚度分析
总结词
强度与刚度分析是评估主传动系统在承受外力和变形时的性能表现,以确保系统的可靠性和稳定性。
总结词:传统设计
详细描述:该实例介绍了一种传统的数控车床主传动系统设计,主要采用齿轮传 动和链传动组合的方式,具有结构简单、可靠性高的优点,但效率较低,适用于 一般加工需求。
实例二:主传动系统的改进设计
总结词:优化设计
详细描述:该实例针对传统主传动系统的不足,进行了优化改进。采用新型轴承和材料,提高了传动效率和稳定性,减少了 维护成本,适用于高精度、高效率的加工需求。
设计目的和意义
设计目的
设计出高效、稳定、可靠的数控车床主传动系统,满足加工精度和效率的要求, 提高生产效率和产品质量。
意义
主传动系统设计的优劣直接影响到数控车床的性能和加工精度,进而影响到整个 机械制造行业的生产水平和产品质量。因此,对数控车床主传动系统进行合理设 计,对于提高机械制造行业的整体水平具有重要意义。
要点二
详细描述
在进行热特性分析时,需要考虑主轴的转速、切削力和材 料导热系数等参数。通过建立热传导模型,可以预测主传 动系统在不同工况下的温度变化和热变形情况。根据分析 结果,可以采取相应的散热措施和热补偿技术,提高系统 的热稳定性和加工精度。
06 主传动系统实例分析
实例一:某型号数控车床主传动系统设计
高耐磨材料
选用高耐磨材料,如陶瓷和硬质 合金,以提高主传动系统的使用 寿命和可靠性,减少维护成本。
CK6136数控机床主传动系统设计

CK6136数控机床主传动系统设计摘要本⽂主要是数控车床主传动系统,主驱动系统,这样的设计可以⽤于普通车床修改,以适应中国的机床⼯具⾏业的发展及⽬前的状态,具有⼀定的经济效益和社会效益。
这个完整的设计包括原始数据,根据⼀些(包括机器类型,⼤⼩等),结合实际条件和情况制定⼀些参数上的车床,根据建议的参数⽐较,以确定传输⽅案,传输⽅案。
然后传输和副齿轮齿的传动⽐的计算,然后估计弹性模量和齿轮轴轴,齿轮和轴的强度和刚度,以进⾏检查。
此外,还橱柜的主要结构设计,零部件的数量的选择,从⽽完成整个主驱动系统的设计。
关键词:数控车床;主传动系统;设计AbstractThis article is mainly CNC lathe main drive, the main drive system, this design can be used for ordinary lathe modified to adapt to China's machine tool industry development and current status, with certain economic and social benefits.The complete design, including raw data, according to some (including machine type, size, etc.), combined with the actual conditions and circumstances to develop some of the parameters on the lathe, according to the recommended parameters compared to determine the transmission scheme, transmission scheme. Then the pinion gear transmission and the transmission ratio calculation, and then estimate the elastic modulus and the gear shaft axes, gears and shaft strength and rigidity to be checked. In addition, the design of the main structure of the cabinet, the choice of the number of parts, thereby completing the main drive system design.Keywords:NC machine tool;main driving system;design⽬录引⾔ (4)第1章总体设计⽅案拟定 (6)1.1拟定主运动参数 (6)1.2运动设计 (6)1.3动⼒计算和结构草图设计 (6)1.4轴和齿轮的验算 (6)1.5主轴变速箱装配设计 (6)第2章参数拟定 (7)2.1车床主参数(规格尺⼨)和基本参数 (7)2.2各级转速的确定 (7)第3章运动设计 (8)3.1主拟定传动⽅案 (8)3.2传动⽅案的⽐较 (8)3.3各级传动⽐的计算 (9)3.4各轴转速的确定⽅法 (11)3.5转速图拟定 (12)第4章动⼒计算 (13)4.1齿轮的计算 (13)4.2电磁离合器的选择和使⽤ (19)第5章轴的设计和验算 (21)5.1轴的结构设计 (21)5.2轴的强度校核(以I轴为例) (21)5.3轴的刚度校核(以I轴为例) (25)第6章主轴变速箱的装配设计 (28)6.1箱体内结构设计的特点 (28)6.2设计的⽅法(以轴的布置为例) (28)第7章结论 (31)致谢 (32)参考⽂献 (33)引⾔这次毕业设计中,我所从事设计的课题是CK6136型数控车床主传动机构设计。
第二节数控机床主传动系统
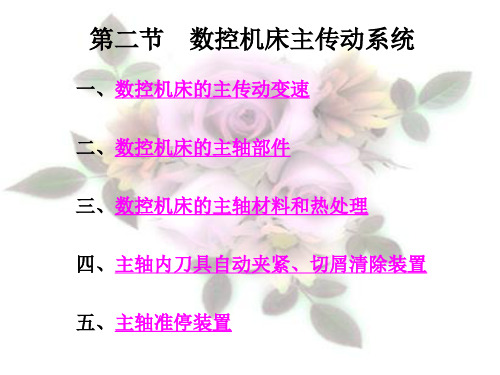
电磁离合器—— 应用电磁效应接通或切断运动的元件,便于实现 自动操作,已成为自动装置中常用的执行元件。
电磁离合器用于数控机床的主传动时,能简化变 速机构,通过若干安装在各传动轴上的离合器的吸合 和分离的不同组合来改变齿轮的传动路线,实现主轴 的变速。
例子: 1、数控镗床主轴箱中使用的无滑片式电磁离合器。 2、啮合式电磁离合器(亦称为牙嵌入电磁离合器)。
第二节 数控机床主传动系统
一、数控机床的主传动变速 二、数控机床的主轴部件 三、数控机床的主轴材料和热处理 四、主轴内刀具自动夹紧、切屑清除装置 五、主轴准停装置
一、数控机床的主传动变速
一)数控机床变速方式 二) 数控机床主传动系统的三种配置方式
1、带变速齿轮的主传动 液压拨叉变速 电磁离合器
2、通过皮带传动的主传动 3、由调速电机直接驱动的主传动 三)数控机床主传动装置的特点 四)主传动变速设计
结构特点:是在摩擦面上做成一 定的齿形,以提高所能传递的力 矩。当线圈1通电后,带有端面齿 的衔铁2被引吸和磁轭8的端面齿 互相啮合。衔铁2又通过渐开线齿 形花键与定位环5联接,再通过螺 钉7传递给齿轮(图中未示出)。 其中,隔离环6是为了防止磁力线 从传动轴通过构成回路,而削弱 电磁吸力。衔铁2和定位环5采用 渐开线花键联结,保证了衔铁与 传动轴的同轴度,使端面齿能更 可靠地啮合。采用螺钉3和压力弹 簧4的结构能使离合器的安装方式 不受限制,不管衔铁使水平还是 垂直、向上还是向下,安装都能 保证合理的齿面间隙。
无滑片式电磁离合器:
优点:省去了电刷,避免了磨损和接触不良所带来的故障, 因比较适用于高速运转的主运动系统。由于采用摩 擦片来传递扭矩,所以允许不停车变速。
缺点: 变速时产生大量的摩擦热;且由于线圈和铁芯是静止 不动的,因此必须在旋转的套筒上安装滚动轴承7, 这样加大了离合器的的径向尺寸。此外,这种摩擦离 合器的磁力线(图中的虚拟)通过钢质的摩擦片,在 线圈断电之后会有剩磁,增加了离合器的分离时间。
第3章数控机床主传动系统设计
3.3无级变速传动链的设计
数控机床的主运动广泛采用无级变速 。 无级变速优势: 在一定范围内,转速(或速度)能连续地变 换,从而获取最有利的切削速度。 数控机床一般都采用由直流或调速电动 机作为驱动源的电气无级调速。
(2)主要设计内容:
拟定结构式或结构网; 拟定转速图, 拟定各传动副的传动比; 确定带轮直径、齿轮齿数; 布置、排列齿轮,绘制传动系统图。
3. 2 分级变速主传动系统设计
3. 2. 1转速图的概念
转速图由“三线一点”组成,即传动轴线、转速 线、传动线和转速点。
3. 2 分级变速主传动系统设计
由Z, φ, n1可知主轴的各级转速应为: 31.5, 45, 63, 90, 125, 180, 250,500、710、 1000、1400。
2)变速组和传动副数的确定 :
变速组和传动副数可能的方案有: 12=4×3 12=3×4 12=3×2×2 12=2×3×2 12=2×2×3
3. 2 分级变速主传动系统设计
②绘制转速图: A、 本例所选定的结构式共有三个变速 组,变速机构共需4根轴,加上电动机轴 共5根轴,(电动机到I轴为定比带传动)故 转速图需5条竖线。主轴共12级转速,电 动机轴转速与主轴最高转速相近,故需 12条横线。然后,标注主轴的各级转速 及电动机轴的转速。
3. 1 主传动系统设计概述
(2)按传动装置类型 可分为机械传动装置 液压传动装置 电气传动装置 以及它们的组合
3. 1 主传动系统设计概述
(3)按变速的连续性 可以分为分级变速传动和无级变速传动。 分级变速传动是在一定的变速范围内均 匀、离散地分布着有限级数的转速,变 速级数一般不超过20~30级。 分级变速传动方式有滑移齿轮变速、交 换齿轮变速和离合器(如摩擦片式、牙嵌 式、齿轮式离合器)变速。
数控机床的进给传动系统
图5-30 直线电动机进给驱动系统 1-位置检测器 2-转子 3-定子 4-床身 5、8-辅助导轨 7、14-冷却板
流电,次级就在电磁 力的作用下沿初级作
6、13-次级 9、10-测量系统 11-拖链 12、17-导轨 15-工作台 16-防护 直线运动。
尽管直线电动机有很多优点,但在选用时应注意以下不足之处: 1)与同容量旋转电动机相比,直线电动机的效率和功率因数要低, 特别在低速时更明显。 2)直线电动机,特别是直线感应电动机的起动推力受电源电压的影 响较大,故对驱动器的要求较高,应采取措施保证或改变电动机的有 关特性来减少或消除这种影响。 3)在金属加工机床上,由于电动机直接和导轨、工作台做成一体, 必须采取措施以防止磁力和热变形对加工的影响。
5) 滚珠丝杠螺母副制造工艺复杂,滚珠丝杠和螺母的材料,热处理 和加工要求相当于滚动轴承。螺旋滚道必须磨削,制造成本高。
2. 静压丝杠螺母副 静压丝杠螺母副是通过油压在丝杠和螺母的接触面之间,产生一
层保持一定厚度,且具有一定刚度的压力油膜,使丝杠和螺母之间由 边界摩擦变为液体摩擦。当丝杠转动时通过油膜推动螺母直线移动, 反之,螺母转动也可使丝杠直线移动。静压丝杠螺母的特点是:
2. 减少各运动零件的惯量
传动件的惯量对进给系统的启动和制动特性都有影响,尤其是高速运转的零件,其惯量的 影响更大。在满足传动强度和刚度的前提下,尽可能减小执行部件的质量,减小旋转零件的 直径和质量,以减少运动部件的惯量。
3. 减少运动件的摩擦阻力
机械传动结构的摩擦阻力,主要来自丝杠螺母副和导轨。在数控机床进给系统中,为了减 小摩擦阻力,消除低速进给爬行现象,提高整个伺服进给系统稳定性,广泛采用滚珠丝杠和 滚动导轨以及塑料导轨和静压导轨等。
数控机床的主传动系统
高速加工、精密定位
主轴驱动系统的设计与选择
设计原则
高可靠性 良好的动态响应 经济性考虑
选择因素
机床类型 加工要求 成本预算
常见类型
交流伺服驱动系统 直流传动系统 混合驱动系统
● 03
第3章 数控机床的进给传动 系统
进给传动系统的组成与作 用
进给传动系统主要包括进给驱动装置、进给传动 机构和进给系统的控制与调节三个部分。进给驱 动装置负责提供动力,进给传动机构负责传递动 力并实现所需的运动轨迹,进给系统的控制与调 节负责对整个系统的运行进行精确控制。
主传动系统是数控机床的核心部件之一,它主要 由主轴装置、传动装置、主轴驱动系统等组成, 负责传递动力并确保机床加工的精度和速度。
主轴的类型与特性
电主轴
高速、高精度
复合主轴
结合电主轴与机 械主轴特点
机械主轴
结构简单、成本 低
主轴定向控制
01 控制意义
保证加工精度
02 控制方法
光电编码器、霍尔效应
部分控制信号依赖于反馈信号
电气控制系统的故障诊断与维 护
故障诊断方法包括观察法、信号分析法、模拟法 等;故障诊断的步骤包括故障现象的观察、故障 原因的分析、故障诊断的结果等;电气控制系统 的维护措施包括定期检查、及时维修、更换故障 部件等。
● 06
第6章 总结
数控机床主传动系统的重要性和 影响因素
夹具系统的性能评价
夹具的刚度 与稳定性
夹具的刚度与稳 定性直接影响到
加工精度
夹具的重复 定位精度
夹具的重复定位 精度直接影响到
加工效率
夹具的装夹 误差
夹具的装夹误差 会导致工件加工
误差
数控机床技术(第六章数控机床的进给传动系统)
第六章 数控机床的进给传动系统
(2)滚珠丝杠副的特点 1)传动效率高。滚珠丝杠副的传动效率高达92 %-96%,是普通梯形丝杠的3-4倍,功率消耗减少 2/3-3/4。 2)灵敏度高、传动平稳。 3)定位精度高、传动刚度高。 4)不能自锁、有可逆性。 5)制造成本高。
第六章 数控机床的进给传动系统
第六章 数控机床的进给传动系统
下图所示是静压丝杠副的结构图。
第六章 数控机床的进给传动系统
螺纹面上油腔的连 接形式与节流控制方 式有两种,如图所示。 图 a 中每扣螺纹每侧 中径上开 3-4 个油腔, 每个油腔用一个节流 器控制,称为分散阻 尼节流。图 b 是将分 布于同侧、同方位上 的 3-4 个油腔用一个 节流器控制,称为集 中 阻 尼 节 流 。
第六章 数控机床的进给传动系统
一、滚珠丝杠副
中小型数控机床中,滚珠丝杠副是减少运动部件摩擦 阻力和动静摩擦力之差最普遍采用的结构。
1.滚珠丝杠副工作原理及特点 (1)滚珠丝杠副的工 作原理
滚珠丝杠副是回转 运动与直线运动相互转 换的新型传动装置,是 在丝杠和螺母之间以滚 珠为滚动体的螺旋传动 元件。
在开环、半闭环进给系统中,传动部件的间隙直接影 响进给系统的定位精度,在闭环系统中,它是系统的主要 非线性环节,影响系统的稳定性。常用的消除传动部件间 隙的措施是对齿轮副、丝杠副、联轴器、蜗轮蜗杆副以及 支承部件进行预紧或消除间隙。但是,值得注意的是,采 取这些措施后可能会增加摩擦阻力及降低机械部件的使用 寿命,因此必须综合考虑各种因统
四、双齿轮—齿条副 在大型数控机床(如大型数控龙门铣床)的直 线进给运动中,可采用的另一种传动方式是齿轮— 齿条结构,它的效率高,结构简单,从动件易于获 得高的移动速度和长行程,适合在工作台行程长的 大型机床上用作直线运动机构。但机构的位移精度 和运动平稳性较差。 当负载小时,可采用双片薄齿轮错齿调整法, 分别与齿条齿槽左、右两侧贴紧,从而消除齿侧间 隙。当负载大时,采用顶加负载双齿轮—齿条无间 隙传动机构能较好地解决这个问题。
- 1、下载文档前请自行甄别文档内容的完整性,平台不提供额外的编辑、内容补充、找答案等附加服务。
- 2、"仅部分预览"的文档,不可在线预览部分如存在完整性等问题,可反馈申请退款(可完整预览的文档不适用该条件!)。
- 3、如文档侵犯您的权益,请联系客服反馈,我们会尽快为您处理(人工客服工作时间:9:00-18:30)。
1. 开发XXX型号数控车床的目的和理由国内数控车床经过十几年的发展,已形成较为完整的系列产品,但用户要求越来越高,对价格性能比更为看重,尤其对某些小型零件的加工,其所需负荷较小,调速范围不宽,加工工序少,效率高,但目前国内数控车床功能多,价格高,造成很大浪费,而我厂现有的数控车床,虽然在这方面做得较好,其加工范围的覆盖面也较宽,但针对上述零件加工的机床还是空白,对用户无法做到“量体裁衣”。
随着市场经济的发展和产品升级换代,上述零件加工越来越多,市场对其具有较高效率,价格较低的排刀式数控车床的要求量越来越大,综上所述,为适应市场要求,扩大我厂数控车床在国内机床市场上的占有量,特进行N-089型数控车床的开发。
2 机床概况、用途和使用范围2.1 概述:XXX型号是结合我厂数控机床和普通机床的生产经验,为满足高速、高效和高精度生产而设计成铸造底座、平床身、滚动导轨,可根据加工零件的要求自由排刀的全封闭式小规格数控车床。
本机床采用SIEMENS 802S系统,主电机为YD132S-2/4双速电机。
主传动采用富士FRN5.5G9S-4型变频器进行变频调速,进给采用德国SIEMENS公司生产的110BYG-550A 和110BYG-550B步进电机驱动的半闭环系统,两轴联动。
2.2 用途:XXX型号型数控车床可以完成直线、圆锥、锥面、螺纹及其它各种回转体曲面的车削加工,适合小轴类、小盘类零件的单件和批量生产,特别适合于工序少,调速范围窄,生产节拍快的小轴类零件的批量生产。
2.3 使用范围:本机床是一种小规格,排刀式数控车床,广泛用于汽车、摩托车、纺织、仪器、仪表、航空航天、油泵油嘴等各种机械行业。
3 XXX型号型数控车床的主要技术参数:3.1 切削区域:a. 拖板上最大回转直径75mmb. 最大切削长度180mmc. 纵拖板的最大行程250mmd. 横拖板的最大行程300mm3.2 主轴:a. 主轴头部GB59001-86-A24b. 主轴前轴承内径70mmc. 主轴通孔直径42mmd. 最大通过棒料直径25mm3.3 主传动:a. 主电机功率 4.5/5.5kwb. 主轴转速3200(4000)r/minc. 主轴最大扭矩32N⋅m3.4 进给运动:a. 快进速度:X向3m/minZ向6m/minb. 最小进给单位:X向0.0025mmZ向0.005mmc. 进给力(额定):X轴13000NZ轴10000N3.5 排刀:a. 根据特定零件安排相应刀具b. 刀具安装尺寸:外圆刀具16⨯16内孔刀具∅163.6 机床重量:约1800kg3.7 机床外形尺寸(长×宽×高):1700⨯1140⨯1550(mm)4 传动系统的确定和分析4.1 主传动方案的拟定:本机床采用YD型双速电机+变频调速,为提高扭矩,降速比为1:1.2。
4.1.1 主轴最高和最低转速的确定:该机床主要用于加工小轴类零件和有色金属件,这样就有较高的速度要求。
根据市场调研和分析:转速n max=3300~3400r/minn min=190r/min4.1.2 主电机功率的确定主电机主要满足负荷切削的要求,现假设如下切削条件:试件:材料:45钢;热处理:正火;工件直径:∅65mm切削速度:V=150m/min切削用量:ap=1.5mm;f=0.3mm/n;P=200kg⋅f/mma. 主切削力Fz=P⋅f⋅ap=200⨯0.3⨯1.5=90kg⋅f=900Nb. 切削扭矩M切=Fz⋅R==29.25N⋅mc. 切削功率M切=Fz⋅V==2.25kw该主传动效率为η=0.8则N主 N切==2.8125kwd. 根据材料考虑本机床现有一定的转速要求,又有较高的扭矩要求,而该机床定位较低,故选用普通YDS132S-2/4双速电机额定输出功率4.5/5.5kw,额定转速1440/2900r/min 采用1:1.2降速提高扭矩,并用交流变频器进行8~75HZ的低速档变频和8~66HZ的高速档变频,变速比为1:1.2时,主轴转速和输出扭矩:低速档:n额==1200r/minn低==192r/minn高==1800r/min额定扭矩M==32.23N⋅m高速档:n额==241.6r/minn低==386r/minn高==3190r/min额定扭矩M==19.56N⋅m其主轴输出功率、扭矩见图1。
对于那些对主轴转速要求较高的用户,我们在设计中考虑采用调整其变速比的方法来满足,即将原降速比1:1.2改为1:1。
实际调整就是将主传动中皮带轮的尺寸由∅120mm调整为∅150mm,仍用交流变速器进行8HZ~75HZ的低速档变频和8HZ~70HZ高速档变频,额定输出功率为4.5/5.5kw,额定转速1440/2900r/min。
这样在1:1传动时主轴低速档及额定输出扭矩:n额=1440r/minn低==230r/minn高==1440⨯1.5=2160r/minM额==26.86N⋅m主轴高速档及额定输出扭矩:n额=2900r/minn低==464r/minn高==4060r/minM额==16.3N⋅m其主轴输出功率、扭矩见图2。
4.1.3 三角皮带轮的校核根据设计结构要求,选d1=125mm,考虑皮带的滑动率ε,则大轮直径d2=ε——皮带滑动率I ——传动比 取:ε=1%;I=1.2计算得:d 2=148.5,取d 2=150mm a. 中心距确定: Dm==137.5mm ∆==12.5mm假定:a=660mm 带长:L=π⋅Dm+2a+=3.14⨯137.5+2⨯660+=1752mm按标准取:L 0=1800mm 则:a==225.128)5.13714.31800(4145.13714.31800⨯-⨯-+⨯⨯=683.9mm ,取a=684mmb. 小轮包角: α1==-a θ2180180︒>120︒ c. 带速: ν==26.5m/s>25m/sn 1:小轮最高转速n=4060r/min由计算所提,机床最高转速时,带速略超许用带速,考虑综合因素,仍选用A 型带, d 1=125mmd. 单根V 型带的基本额定功率根据d 1=125mm 、n 1=1440r/min ,由《机械设计手册》第3册中的表22.1-13d 查得(A 型带):N 1=1.93kw考虑到传动比的影响i ≠1,额定功率的增量∆N 1由表22.1-13d 查得: ∆N=0.13kw e. 带的根数: Z=Nc——计算功率:Nc=K A⋅N=1.1⨯5.5=6.05N——机床传递功率K A——工作情况系数,考虑到本机床直接传动运转平稳,无冲击,故取K A=1.1∆N1——功率增量Kα——包角系数,由表22.1-10查得Kα=0.99486K L——带长系数,由表22.1-11查得K L=0.99Z==2.9取三根A型带Z=3f. 张紧力:F=q:V型带每米长质量查表q=0.1kg/mF==188.42Ng. 径向载荷:Q=2⋅Z⋅F0⋅Sin=1130.53Sin=1112.8(N)4.1.4 主轴直径的选择:a. 由于本机床采用的A24主轴,根据经验取前支承直径∅70mm,因为考虑到最大棒料(通过)为∅25,取后轴径∅65mm。
b. 求支承的径向刚度:主轴的输出扭矩:由扭矩转速图1可查得:在n min=192r/minMmax=35.8N⋅m若取Dmax=70mm则Fz==1022.85NFy=0.5Fz=511.4N则F==1143.58N受力情况如图3。
图 3图 4支承情况如图4,设计中根据需要a=68.5,取a l=3,则l=3a=3⨯68.5=205.5由前面计算的切削力,根据力和力矩的平衡,F α=l l )(a F +=1524.8NF β=5.2055.6858.1143⨯=⋅l a F =381.2N在实际设计中,根据经验,前后轴承分别选取哈轴的46114、36114二个自成组轴承和36113二个自成组轴承,这样前轴既有较高的承载力和能满足较高的转速要求。
因此,向心推力球轴承间隙为零时的径向弹性位移量: δo=Qr ——滚动体上的径向载荷 Qr=Fr ——轴承径向载荷,此处为支反力 i ——滚动体列数 Z ——每列滚动体数 Qr α==217.2NQr β==51.6Nα:向心推力轴承推力角;36接触角15︒;46接触角25︒ d Q :滚动体直径 则:δo α==7.4μmδo β==2.79μm设:46114轴承的预紧量为18μm(由工艺推荐)也可以通过相关样本查的63113轴承的预紧量为22μm相对位移量:=2.43=7.89从图3-5查得:βα=0.24,β=0.2由式3-2:δ1=βδo得δα1=0.25δoα=0.24⨯7.4=1.7μmδβ1=0.2δoβ=0.2⨯2.79=0.558μm支承的弹性位移即包括轴承的位移,同时也包括了轴承外径与箱体孔的接触变形和轴承内径和轴的接触变形。
查哈轴样本:C46114、D36113轴承与箱体孔的装配过盈量:∆α1=0μm,∆β1=0μm由公式从图3-6查得:Kα1=0.2,Kβ1=0.2代入式:δ=F——外载荷(N)K——系数,由过盈量查图3-6得b——轴承宽度(mm)d——轴承外径δα2==1.387μmδβ2==0.415μm轴承C46114、D36113与轴的装配过盈量:∆α2=4.5μm,∆β2=0μm由公式从图3-6查得:Kα2=0.17,Kβ1=0.2δα3==1.179μmδβ3==0.415μm由以上计算可以得出本主轴组前支承、后支承的综合径向刚度:Kα==357.4N/cmKβ=N/cmc. 求最佳跨距=1.29,≈1当主轴当量外径D当==67.5mm,当量内径d当=48时,惯量矩I=0.05⨯η=≈1.2查图3-32,η-曲线可查得:=3.3则:Lo=3.3a=3.3⨯68.5=22.605本设计取a=67,跨距210mm由以上计算可以看出选a=67,跨距210mm,能够满足主轴的最佳跨距和刚度的要求。
以上计算公式均取自大连工学院戴曙主编的《金属切削机床计算》。
4.1.5 轴承寿命的计算主轴受力分析如下图5。
图 5a. 假设切削零件:试件尺寸:∅25⨯100mm夹头体重量:G=γ⋅V=7.8⨯3.14⨯=1.3kgb. 设计使用时间th设机床每天工作15h,每年使用300天,使用年限8年,在全部使用期间内切削时间占70%,则:th=15⨯300⨯8⨯70%=25200小时c. 计算平均转速n e由于本机床是190~4000r/min范围内调速,因此需要计算平均转速,设机床的总运转时间为1,则在各种转速下所占机床的总运动时间列表如表1。