数控铣床控制系统设计
FANUC0imateC数控铣床电气控制系统及PLC控制设计基础

FANUC 0i mate C 数控铣床电气控制系统及PLC控制设计基础
FANUC-Oi Mate MC系统 配置图
welcome to use these PowerPoint templates, New Content design, 10 years experience
FANUC 0i mate C 数控铣床电气控制系统及PLC控制设计基础
FANUC 0i mate C 数控铣床电气控制系统及PLC控制设计基础
FANUC 0i mate C 系统的配置
➢Text ➢Text ➢Text
FANUC-Oi Mate MC系统配置 系统功能选择:系统功能包括B包功能,具备3个CNC轴控制功能和3轴联 动。系统只有基本单元无扩展功能。 伺服放大器和电动机:系统伺服为βi伺服单元(电源模块、主轴模块和进 给模块为一体)驱动βi系列主轴电动机和βi 进给伺 服电动机 示装置和MDI键盘:系统显示装置为7.2 in黑白LCD,MDI键盘标准配 置为小键盘 I/O装置:根据机床特点和要求选择I/O装置 机床操作面板:可以选择系统标准操作面板或机床厂家的操作面板 附加伺服轴:只能选择一个附加伺服轴
FANUC 0i mate C 系统的 功能连接图
welcome to use these PowerPoint templates, New Content design, 10 years experience
FANUC 0i mate C 数控铣床电气控制系统及PLC控制设计基础
1、主轴电系机的统选硬型件配置
显卡:视频信号和图形/文字显示信号。 轴卡:电动机标准参数和伺服轴的控制信息等。 下层功能板
闪存FROM:FROM中装载了系统各种管理和控制软件及机床厂家 的PMC程序和宏管理文件
数控铣床的控制系统设计与分析

数 控 系统 的 的任 务 是 对 刀 具 和 工 件 之 间 的 相 对 运 动 进 行 控 制 ,数 控 装 置 中 的 P C1F 7 I 687
上文所 述 的软、 硬
件 合 成 为 数 控 装
置, 此装置 是数控 系统 的核心 , 能 功 有 正 确 识 别 和 解
精度 非常精 确 ,将 电压信 号转 换为 转矩和 转速来
中所 设 计 的 铣床 控 制 系 统所 采 用 的是 Mi oot c sf r
公司生产 P C1F 7 单片机 ,最主 要 的特 点是 除 I 6 8X
手 动控 制垂直 升 降进给 伺服 电动 机外 ,在键 盘输
入 方式 下 ,通 过 单片机 内部程序 的运 行 ,闭环控 制 横 向进给 伺服 电动机 和 纵 向进 给伺 服 电动机 的 二 坐标 进给 方 向不断变 换 , 自动 在平 面 内铣 出所 设 计 的形状 。这 一设计 针对 性强 、成本 低 、效率
驱动 控制 对象 的伺服 电机 。为 了便 于操作 和观 察
工作 状态 ,电源 、键 盘 、显示 器 、单片机 等都 安 排在控 制 台 的面 板上 。该 设计 的硬件 系统 框 图如
图 2 示。 所
高,具有 很强 的推广 使用 价值 。
1 控制系统
PC1F 7 I 6 8 7单 片机具 有哈 佛总线 结构 、R S IC 技 术 、功耗 低 、驱 动 能力强 、应 用平 台界面 友好 、 开发方 便 、一次 性编程 、体 积小 等特 点 ,因此 以 PC1 F 7 单片机 为主 开发 的控制 系统 ,在软 、 I 6 8X 硬 件 的设计 上有 其独特 优 势 ,在 铣床 的控 制系统
数控铣床设计说明书

1.1数控机床的产生和发展历程1.1.1数控机床的发展简史1946年世界上诞生了第一台电子计算机,同期美国北密执安的小型飞机承包商帕尔森斯公司(Parsosncoproraitno)为了制造飞机机翼轮廓的板状样板,提出了采用数字控制技术进行机械加工的思想,1949年由帕尔森斯公司与美国麻省理工学院伺服机构研究所合作开始从事数控机床的研制工作,1952年,研制出第一台实验性数控系统,并把它装在一台立式铣床上,成为世界上第一台数控机床,成功实现了同时控制三轴的运动。
1954年11月,在帕尔森斯专利基础上,第一台工业用的数控机床由美国本迪克斯公司(Bendixocproratjno)生产出来,从此,传统机床产生了质的变化。
50多年过去了,数控系统由当时的电子管起步,经历了两个阶段六代的发展,即:硬件逻辑数控,简称为数控(NC)阶段经历了三代,即1952年第一代—电子管;1995年第二代—晶体管和印刷电路板;1965年第三代—小规模集成电路,由于它体积小,功耗低,使数控系统的可靠性得以进一步提高,数控系统发展到第三代。
计算机数控(计算机数字的控制,简写为CNC)阶段也经历了三代,即1970年第四代—小型计算机,1974年第五代—微处理器(MNC)和1990年第六代—基于Pc的阶段。
数控系统发展到了第五代以后,从根本上解决了可靠性低、价格昂贵、应用不方便等极为关键的问题,并在上世纪七十年代末八十年代初以后首先在美国、日本、欧洲等工业发达国家得到大规模普及应用。
1.1.2 我国数控技术的发展1.1.2.1我国数控技术经过了研制开发、引进技术、消化吸收、科技攻关和产业攻关几个过程,并得到了飞速发展。
从1958年起,由一些科研院所、高等学校和少数机床厂起步进行数控系统的研制和开发,由于受到当时国产电子元器件水平低、部门经济等因素的制约,未能取得较大的进展。
在改革开放以后,经过“六五”(1981一1985年)的引进国外技术,“七五”(1986一1990年)的消化吸收和“八五”(1991一1995)国家组织的科技攻关和“九五”(1996一2000年)国家组织的产业化攻关,才使得我国数控技术逐步取得实质性的进展,一些较高档次的数控系统(五轴联动),分辨率为0.002 m的高精度数控系统、数字仿形数控系统、为柔性单元配套的数控系统都开发出来,并造出样机,开始了专业化生产和使用。
立式数控铣床X-Y工作台
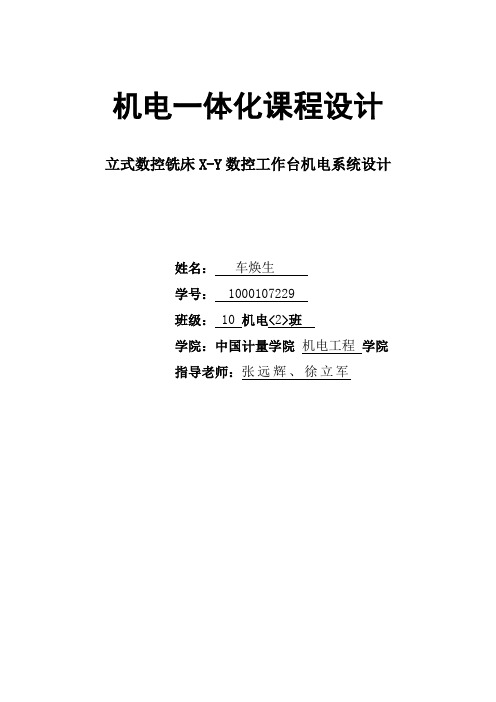
机电一体化课程设计立式数控铣床X-Y数控工作台机电系统设计姓名:***学号: **********班级:10机电<2>班学院:中国计量学院机电工程学院指导老师:张远辉、徐立军目录前言................................................................................................ 错误!未定义书签。
一、设计任务 (2)1.1课程设计时间 (2)1.2课程设计题目 (2)1.3课程设计任务 (2)1.4课程设计内容 (2)1.5课程设计要求 (2)二、总体方案的确定 (3)2.1机械传动部件的选择 (3)2.2控制系统的设计 (4)三、机械传动部件的计算与选型 (4)3.1导轨上移动部件的重量估计 (4)3.2铣削力的计算 (5)3.3导轨副计算和选型 (6)3.4滚珠丝杠螺母副的计算和选型 (7)3.5步进电机减速箱的选用 (9)3.6步进电机的计算与选型 (9)3.7编码器(反馈电路)选型 (13)四、工作台机械装配图的绘制 (14)4.1可参考课本图6-23 XY数控工作台装配图 (14)五、工作台控制系统的设计 (14)5.1电源电路 (14)5.2存储器扩展电路 (15)5.3键盘电路 (17)5.4显示电路 (18)5.5传感器电路 (19)六、步进电机驱动电路设计 (20)6.1驱动电路 (20)6.2光电隔离 (20)七、程序设计 (21)7.1功能 (21)7.2框图 (22)7.3代码 (23)八、总结 (24)参考文献 (24)答辩记录 (25)前言X-Y数控工作台是许多机电一体化设备的基本部件,如数控车床的纵-横向进刀机构、数控铣床和数控钻床的X-Y工作台、激光加工设备的工作台、电子元件表面贴装设备等。
因此,选择X-Y数控工作台作为机电综合课程设计的内容,对于机电一体化专业的教学具有普遍意义。
深圳市众为兴数控技术 ADT-CNC4840 铣床控制系统 说明书

ADT-CNC4840 铣床控制系统 用 户 手 册深圳市众为兴数控技术有限公司 地址:深圳市南山区马家垅工业区36栋5楼 邮编:518052 目录第一篇:编程.......................................41. 综述 (4)1.1 可编程功能 (4)1.2 准备功能 (9)1.3 辅助功能 (11)2. 插补功能 (11)2.1 快速定位(G00) (11)2.2 直线插补(G01) (12)2.3 圆弧插补(G02/G03) (12)3. 进给功能 (14)3.1 进给速度 (14)3.2 自动加减速控制 (14)3.3 暂停( G04 ) (15)4. 参考点和坐标系 (15)4.1 机床坐标系 (15)4.2 关于参考点的指令( G27、G28、G29 ) (15)4.3 工件坐标系 (17)4.4 平面选择 (19)5. 坐标值和尺寸单位 (19)5.1 绝对值和增量值编程(G90和G91) (19)6. 辅助功能 (20)6.1 M代码 (20)6.2T代码 (21)6.3 主轴转速指令(S代码) (21)7. 程序结构 (21)7.2 程序正文结构 (21)7.2.5文件结束 (23)8. 简化编程功能 (23)8.1 孔加工固定循环(G73,G74,G76,G80 ̄G89) (23)9.刀具补偿功能 (35)9.1 刀具长度补偿(G43,G44,G49) (35)9.2 刀具半径补偿B (37)第二篇 操 作 篇...................................751.概要 (75)1.1手动操作 (75)1.2刀具按程序移动─自动运转 (76)1.3自动运转的操作 (76)1.4程序调试 (77)1.5程序的编辑 (78)1.6数据的显示及设定 (78)1.7显示 (79)2.操作面板说明 (79)2.1LCD面板 (79)2.2显示页面选择 (81)2.3操作方式选择 (81)2.4键盘的说明 (81)3.手动操作 (84)3.1手动返回参考点 (84)3.2手动连续进给 (85)3.3单步进给 (85)3.4手轮进给 (85)3.5手动辅助机能操作 (86)4.自动运行 (87)4.1自动运转 (87)4.2自动运转的停止 (87)4.3进给倍率 (88)5.调试 (88)5.1单程序段 (88)5.2跳过任选程序段(或机床软操作面板) (88)5.3输入信号检测输出信号测试 (88)6.安全操作 (88)6.1急停 (88)6.2超程 (89)7.报警处理 (89)8.程序存储、编辑、下载、显示 (89)8.1程序存储、编辑操作前的准备 (89)8.2把程序存入存储器中 (89)8.3程序检索 (89)8.4程序的删除 (90)8.5删除全部程序 (90)8.6字的插入、修改、删除 (90)8.7存储程序的个数 (91)8.8存储容量 (91)8.9程序下载 (91)8.10程序显示编辑界面 (93)9.数据的显示、设定 (93)9.1系统参数 (93)9.2刀补参数设定显示 (93)9.3工件坐标系设定 (93)9.4参数的显示 (96)9.5参数的设定和查询 (96)9.6机床软操作面板的显示及设置 (97)9.7设置参数设定 (97)9.8诊断显示设定 (98)10.显示 (99)10.1状态显示 (99)10.2程序显示 (100)10.3位置显示及清零 (101)第三篇 连 接 篇..................................1031、系统结构 (103)1.1CNC4840数控系统的组成 (103)2、外部连接 (104)2.1外部接口图 (104)2.2电机驱动器控制接口 (106)对应外壳定义:机床输出扩展接口 (119)附录1规格一览表 (122)附录2参数一览表 (125)附录4错误代码一览表 (132)附录5G功能一览表 (133)附录6工件坐标系设定及对刀 (135)第一篇:编程 1. 综述 1.1 可编程功能 通过编程并运行这些程序而使数控机床能够实现的功能我们称之为可编程功能。
数控铣床电主轴系统设计说明书
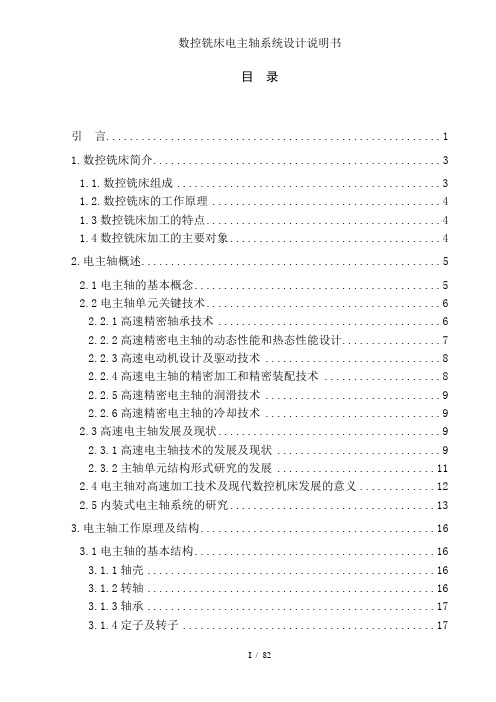
目录引言 (1)1.数控铣床简介 (3)1.1.数控铣床组成 (3)1.2.数控铣床的工作原理 (4)1.3数控铣床加工的特点 (4)1.4数控铣床加工的主要对象 (4)2.电主轴概述 (5)2.1电主轴的基本概念 (5)2.2电主轴单元关键技术 (6)2.2.1高速精密轴承技术 (6)2.2.2高速精密电主轴的动态性能和热态性能设计 (7)2.2.3高速电动机设计及驱动技术 (8)2.2.4高速电主轴的精密加工和精密装配技术 (8)2.2.5高速精密电主轴的润滑技术 (9)2.2.6高速精密电主轴的冷却技术 (9)2.3高速电主轴发展及现状 (9)2.3.1高速电主轴技术的发展及现状 (9)2.3.2主轴单元结构形式研究的发展 (11)2.4电主轴对高速加工技术及现代数控机床发展的意义 (12)2.5内装式电主轴系统的研究 (13)3.电主轴工作原理及结构 (16)3.1电主轴的基本结构 (16)3.1.1轴壳 (16)3.1.2转轴 (16)3.1.3轴承 (17)3.1.4定子及转子 (17)3.2电主轴的工作原理 (17)3.3电主轴的基本参数 (19)3.3.1电主轴的型号 (19)3.3.2转速 (19)3.3.3输出功率 (19)3.3.4 输出转矩 (19)3.3.5电主轴转矩和转速、功率的关系 (20)3.3.6 恒转速调速 (20)3.3.7 恒功率调速 (20)3.3.8 轴承中径 (20)3.4自动换刀装置 (21)4. 电主轴结构设计 (22)4.1主轴的设计 (22)4.1.1.铣削力的计算 (22)4.1.2 主轴当量直径的计算 (23)4.2高速电主轴单元结构参数静态估算 (23)4.2.1 高速电主轴单元结构静态估算的内容及目的 (23)4.2.2轴承的选择和基本参数 (23)4.3轴承的预紧 (24)4.4主轴轴承静刚度的计算 (24)4.4.1 主轴单元主要结构参数确定及刚度验算 (26)4.4.2主轴单元主要结构参数确定 (27)4.4.3主轴强度的校核 (32)4.4.4主轴刚度的校核 (34)4.4.5主轴的精密制造 (35)4.5主轴电机 (36)4.5.1电机选型 (36)4.6主轴轴承 (37)4.6.1轴承简介 (37)4.6.2陶瓷球轴承 (38)4.6.3陶瓷球轴承的典型结构 (40)4.7主轴轴承精度对主轴前端精度影响 (40)4.8拉刀机构设计 (41)4.8.1刀具接口 (41)4.8.2拉刀杆尺寸设计 (42)4.8.3夹具体结构尺寸设计 (43)4.8.4 松、拉刀位移的确定 (45)4.8.5碟型弹簧的设计及计算 (46)4.9HSK工具系统结构特点分析 (48)4.10HSK工具系统的静态刚度 (52)4.10.1 HSK工具系统的变形转角及极限弯矩 (52)5.电主轴的润滑及冷却 (55)5.1润滑介绍 (55)5.1.1润滑的作用和目的 (55)5.1.2 电主轴润滑的主要类型 (55)5.1.3 油气润滑的原理和优点 (57)5.2电主轴的冷却 (58)5.2.1电主轴的热源分析 (58)5.2.2电主轴的冷却方法 (59)5.3电主轴的防尘和密封 (60)6.电主轴的驱动和控制 (61)6.1恒转矩变频驱动和参数设置 (61)6.2恒功率变频驱动和参数设置 (62)6.3矢量控制驱动器的驱动和控制 (64)6.4普通变频器原理 (65)6.5本设计采用的变频器原理 (67)6.6主轴准停 (69)6.6.1主轴的准停功能 (69)6.6.2主轴准停的工作原理 (69)6.6.3主轴准停控制方法 (70)7.主轴动平衡 (72)7.1动平衡介绍 (72)7.2动平衡设计 (73)总结 (75)致谢 (76)参考文献 (77)引言高速机床是实现高速切削加工的前提和条件。
课程设计数控立式铣床XY工作台机电系统设计说明书
《机电一体化》课程设计数控立式铳床XY工作台机电系统设计院系:汽车学院专业:机械设计制造及其自动化班级:机电一班组长:雷博文组员:金亮、黄明亮、夏佳、熊秀成指导教师:蒋强目录一、设计目的 (3)二、设计任务 (3)三.总体方案的确定 (4)1、机械传动部件的选择..................................... ••:•. (3)(1) 导轨副的选用 (4)(2) 伺服电动机的选用 (4)(3) 工作台的选用 (4)2、................................................................. 控制系统的设计.. (4)3、................................................................. 绘制总体方案图.. (5)四、.......................................... 直线伺服电机的计算与选型51、.............................................. 导轨上移动部件的重量42、...................................................... 铣削力的计算43、........................................................ 载荷的计算74、............................................................ 初选型号75、............................................ 直线伺服电机可用性验算8五、........................................... 直线滚动导轨副的计算与选型81、直线滚动导轨选择理由 (8)2、直线导轨额定寿命L 的计算和选型 (10)3、光栅尺的选择 (11)4、工作台的选型 (12)六、PLC选型 (13)七、....................................................... 伺服放大器选型18八、控制系统硬件电路设计 (20)结束语 (21)参考文献 (22)一、设计目的课程设计是一个很重要的实践性教学环节,要求学生综合运用所学的理论知识,独立进行设计训练,主要目的:1) 通过本设计,使学生全面地,系统地了解和掌握数控机床得基本组成及其相关基本知识,学习总体方案拟定、分析与比较的方法。
立式铣床使用的X-Y两轴控制的数控平台--课程设计
攀枝花学院Panzhihua University课程设计(说明书)立式铣床使用的X-Y两轴控制的数控平台院(系):机械学院专业:机械设计制造及其自动化班级:二班学生姓名:学号:指导老师:职称:教授2016 年12月18 日攀枝花学院课程设计(说明书)课程设计任务书攀枝花学院本科学生课程设计任务书摘要X-Y数控工作台是是指能分别沿着X 向和Y向移动的工作台,是许多机电一体化设备的基本部件,如数控车床的纵—横向进刀机构、数控铣床和数控钻床的X-Y工作台、激光加工设备的工作台、电子元件表面贴装设备等。
模块化的X-Y 数控工作台,通常由导轨座、移动滑块、工作、滚珠丝杠螺母副,以及伺服电动机等部件构成。
其中伺服电动机做执行元件用来驱动滚珠丝杠,滚珠丝杠螺母带动滑块和工作平台在导轨上运动,完成工作台在X、Y方向的直线移动。
导轨副、滚珠丝杠螺母副和伺服电动机等均以标准化,由专门厂家生产,设计时只需根据工作载荷选取即可。
控制系统根据需要,可以选取用标准的工作控制计算机,也可以设计专用的微机控制系统。
载实1}通过该实验使同学们深刻了解所使用的可逆寄存器微分@SFTR指令和可逆寄存器SFTR指令的共同点都是具有控制数据左、右移动功能;而其不同处是应该注意到使用可逆寄存器SFTR指令时,要加前沿微分DIFU( 013)指令而可逆寄存器微分@SFTR是不需要的。
实验所用的电动机容量为0. 25kW,采用直接启矶3台电动机每台可逆顺序启动的时间间隔为2秋3台电动机首先正转顺序启动,启动结束转为正常运布录正常运行的时间定为10秒,停止时间定为5秋3台电动机再反转顺序启动,启动结束转为正常运布录正常运行的时间定为10秒,停止时间定为5秋实验要求按照上述顺序反复运标实验所使用的PLC为OMRON- CPM2A-CDR- A型机关键词X-Y数控工作台,数控铣床AbstractCNC XY table are mean to each along X and Y to move to the table, electromechanical integration equipment, many basic components, such as vertical CNC lathe - lateral feed body,CNC milling and CNC drilling machine XY work Taiwan, laser processing equipment, workstations, electronic components surface mount equipment. Modular CNC XY table, usually by rail seat, move the slider, work, ball screw pair, and the servo motor and other component parts. One servo motor to drive the ball screw actuator to do, the ball screw drive and work platform slide rail movement, complete table in the X, Y direction of the straight line movement. Guideways, ball screw pair and servo motors etc., shall be standardized by the specialized manufacturers, design can be selected only according to work load. Control system as needed, you can select a computer using a standard job control, you can design a dedicated computer control system.Keywords XY table ,CNC milling tools目录摘要 (I)Abstract (II)1 设计任务 (1)2 设计主要步骤 (2)2.1 确定设计总方案 (2)2.1.1 机械传动部件的选择 (2)2.2.2 控制系统的设计 (3)3 机械传动部件的计算与选型 (4)3.1工作台外形尺寸及重量初步估算 (4)3..2 计算切削力 (5)3.3 直线滚动导轨副的计算与选型 (6)3.4 滚珠丝杠螺母副的计算与选型 (6)4 步进电动机的计算与选型 (9)4.1步进电机的相关计算及校核 (9)4.1.1计算加在步进电动机转轴上的总转动惯量 (9)4.1.2计算加在步进电动机转轴上的等效负载转矩 (10)4.1.3最大工作负载状态下电动机转轴所承受的负载转矩 (11)4.1.4步进电动机最大静转矩的选定 (11)4.1.5步进电动机的性能校核 (11)4.2步进电动机驱动电源的选用 (13)4.3确定联轴器的型号 (14)4.4增量式旋转编码器的选用 (14)5 电气原理图设计 (15)5.1典型数控工作台电气原理 (15)5.2单片机的选择 (15)5.3外部程序存储器的扩展 (16)5.4外部数据存储器的扩展 (16)5.5 I/O口扩展电路 (16)5.6 显示器接口设计 (16)5.7 键盘接口电路设计 (17)5.8 步进电机的接口电路设计 (17)6 工作台控制系统的设计 (18)6.1 进给控制原理框图 (18)6.2驱动系统 (18)6.3 步进电机驱动电路和工作原理 (18)6.4 驱动电路的时间常数 (19)6.5 电源电路的确定 (20)6.6 元器件的确定 (20)7 机械部分装配图的绘制 (22)总结 (23)参考文献 (24)1 设计任务题目:立式铣床使用的X-Y两轴控制的数控平台设计任务:设计一种供立式铣床使用的X-Y两轴控制的数控平台,平台的主要参数如下:1 最大铣削宽度13mm2最大背吃刀量7mm3工作台进给最大移动速度V xf=V yf=550mm/min4工作台空载最大移动速度V x0=V y0=3500mm/min5加工范围300mmX330mm6工作台面尺寸280mmX320mm7定位精度取±0.012 设计主要步骤2.1 确定设计总方案2.1.1 机械传动部件的选择(1)导轨副的选用要设计的数控铣床X-Y工作台,是轻型立式数控铣床的,需要承受的载荷不大,而且脉冲当量小,定位精度高,因此选用直线滚动导轨副,它具有摩擦系数小,不易爬行,传动效率高,结构紧,安装预紧方便等优点。
MasterCAM数控铣床的加工毕业设计含示意图
摘要数控铣床是在普通铣床上集成了数字控制系统,可以在程序代码的控制下较精确地进行铣削加工的机床。
数控铣床一般由数控系统、主传动系统、进给伺服系统、冷却润滑系统等几大部分组成。
数控铣床是目前功能强大、简便、高效的加工机床,只需输入加工程序便可自动加工的自动化程度很高的数控加工中心之一。
MasterCAM软件是美国的CNCSoftware公司开发的基于PC平台的CAD/CAM 系统,现已广泛应用于机械加工、模具制造、汽车工业和航天工业等领域。
采用MasterCAM软件能方便的建立零件的几何模型,迅速自动生成数控代码,缩短编程人员的编程时间,特别对复杂零件的数控程序编制,可大大提高程序的正确性和安全性,降低生产成本,提高工作效率。
烟灰缸是日常用途广泛的环保工具,为了彰显烟灰缸的个性化和功能性,因此希望利用现有知识和能力,制造一个外观美丽并且实用的烟灰缸。
为此,用PROE 做出烟灰缸零件图,将其导入MasterCAM软件中进行模拟仿真加工,利用MasterCAM自动编程功能,导出烟灰缸数控加工程序,并在FANUC仿真软件中仿真模拟加工,最后将导出的数控加工程序输入数控铣床中,加工出我们需要的烟灰缸凸模实体模型。
关键词:数控铣床,MasterCAM,烟灰缸,仿真,加工AbstractCNC milling machine is in the common milling machine with integrated digital control system in the program code, can control accurately for milling machine. CNC milling machine by the general NC system, main transmission system, feed servo system, cooling and lubrication system of several major components. CNC milling machine is the most powerful, simple, efficient processing machine, only need to input the processing program can automatically processing, high degree of automation of CNC machining centers.MasterCAM software is belong to the United States of America CNCSoftware company,which developed the PC platform based on CAD / CAM system,now it has been widely used in machining, mold manufacturing, automobile industry and the aerospace industry and other fields。
数控铣床教案
数控铣床资源补充:(1.教学设计2.教学课件3.视频资源4.技术资源5.学习工作6.考试题库7.维修案例8.加工案例)第一章数控铣床(加工中心)概述一、数控铣床(加工中心)的结构二、数控铣床(加工中心)的组成三、数控铣床(加工中心)的特点四、数控铣床(加工中心)的刀具第二章数控编程基础知识第一节数控编程的内容和方法一、数控编程的内容二、数控编程的方法第二节程序的结构与格式一、程序的结构二、程序字三、指令类型(代码类型)第三节数控机床的三大机能(F、S、M)一、进给机能(F)二、主轴机能(S)三、辅助机能(M)第四节数控铣床(加工中心)的坐标系一、坐标系的确定原则二、坐标轴的确定方法三、数控铣床的坐标系第五节工件坐标系和工作平面的设定一、工件坐标系的设定(零点偏置)二、工作平面的设定第六节程序编制中的工艺分析一、数控加工工艺的主要内容二、工序划分原则三、零件装夹四、加工路线的确定五、选择刀具和切削用量六、工艺文件编制第三章FANUC铣床、加工中心程序编制第一节辅助功能M代码和准备功能G代码第二节快速定位G00第三节直线 G01第四节圆弧G02、G03第五节刀具补偿第六节程序暂停 G04第七节增量(相对)坐标系第八节主程序、子程序第九节极坐标编程(G15、G16)第十节镜像加工指令(G24、G25)第十一节图形旋转指令(G68、G69)第十二节比例缩放指令(G50、G51)第十三节孔加工固定循环简述第十四节孔加工固定循环编程第四章华中程序编制第一节华中系统概述快速定位G0直线G1圆弧插补G2、G3暂停指令 G4主轴运动指令螺纹加工指令刀具与刀具补偿刀具半径补偿指令简化编程指令镜像功能G24、G25缩放功能G50、G51旋转变换G68、G69固定循环G73高速深孔加工循环G74反攻螺纹循环G76精镗循环G81钻孔循环(中心钻)G82带停顿的钻孔循环G83深孔加工循环G84攻螺纹循环G85镗孔循环G86镗孔循环G87反镗循环G88镗孔循环G89镗孔循环G80取消固定循环宏指令编程宏变量及常量运算符与表达式赋值语句条件判别语句IF ELSE ENDIF循环语句WHILE ENDW宏程序编程格式和调用宏程序调用的参数传递第五章典型零件加工中心加工工艺分析及编程操作一、基本零件的加工与工艺分析1二、基本零件的加工与工艺分析2三、基本零件的加工与工艺分析3四、阶台零件的加工与工艺分析五、倒角零件的加工与工艺分析六、圆角零件的加工与工艺分析七、模块零件的加工与工艺分析八、压板零件的加工与工艺分析九、箱体零件的加工与工艺分析十、折板零件的加工与工艺分析第六章数控系统操作第一节 FANUC i 系列标准数控系统一、操作界面简介二、FANUC i 标准系统的操作第二节华中系列标准数控系统一、操作界面简介二、华中标准系统的操作第七章自动编程6.1 CAXA 2008制造工程师自动编程概述6.1.1 CAXA制造工程师自动编程软件简介6.1.2 CAXA制造工程师2008用户操作界面6.1.3 应用CAXA制造工程师软件自动编程的操作步骤6.2 CAXA制造工程师2008加工设置管理6.2.1 毛坯定义6.2.2 起始点6.2.3 刀具库6.2.4 加工操作管理6.2.5 后置处理6.2.6 工艺清单简介6.3 CAXA制造工程师2008加工共同参数6.3.1 切入切出6.3.2 切削用量6.3.3 下刀方式6.3.4 公共参数6.3.5 加工边界6.3.6 刀具参数6.4 CAXA自动编程数控加工典型实例6.4.1 高效率切除加工余量方法——插铣式粗加工6.4.2 等高线粗加工方式6.4.3 扫描线粗加工6.4.4 扫描线精加工6.4.5 参数线精加工方式6.4.6 三维偏置精加工职业技能鉴定(初级工、中级工、高级工)试题精选及解答数控技能大赛试题及解答数控铣加工中心操作入门任务1 加工中心操作基本步骤任务2 加工中心机床面板任务3 加工中心工件的定位与安装任务4 加工中心对刀情境2 加工中心加工工艺分析任务1 加工中心刀具选择任务2 制定平面凸轮零件的数控铣削加工工序任务3 制定端盖零件的加工中心加工工艺任务4 制定柱面凸轮零件数控综合加工工艺情境3 加工中心编程入门任务1 直线沟槽铣削任务2 加工中心多刀加工程序情境4 平面铣削编程与加工任务1 平面铣削加工任务2 台阶面铣削加工情境5 圆弧零件程序编制与加工任务1 圆弧沟槽加工任务2 祥云图案加工情境6 零件轮廓铣削编程与加工任务1 外轮廓编程与加工任务2 内轮廓编程与加工情境7 模具型腔零件编程与加工任务1 凸模零件加工任务2 凹模零件加工情境8 槽类零件编程与加工任务1 封闭槽与开放槽加工任务2 燕尾槽加工情境9 孔类零件编程与加工任务1 钻孔任务2 孔系零件的加工任务3 镗孔任务4 螺纹孔加工情境10 变量编程与零件加工任务1 相邻面加工R角类零件程序编制任务2 椭圆凹腔曲面加工任务3 空间波浪曲面的加工情境11 计算机辅助编程任务1 转盘编程与加工任务2 螺旋桨皮带轮编程与加工现代制造技术技能竞赛加工案例集锦——数控铣工赛项试题一轮廓加工1试题二型腔加工15试题三齿形轮廓加工28试题四轮廓与型腔加工55试题五具有腰形槽轮廓加工65试题六封闭槽加工75试题七型腔与孔加工81试题八内外轮廓加工(一)90试题九“U”形槽与外轮廓加工101试题十封闭槽与外轮廓加工108试题十一含岛屿型腔加工115试题十二耳形轮廓加工125试题十三含岛屿型腔与轮廓加工131试题十四封闭槽与外轮廓加工143试题十五平面与轮廓加工152试题十六内外轮廓加工(二)159试题十七平面与外轮廓加工165试题十八型腔与外轮廓加工172试题十九轮廓与异形腔加工180试题二十跑道形轮廓加工189试题二十一孔与封闭槽加工198试题二十二端盖加工206试题二十三凸轮槽加工217章数控机床的基础知识节认识数控机床一、基本概念二、数控机床的产生三、数控机床的分类四、数控机床的发展五、加工中心的选型第二节数控机床的组成第三节先进制造系统简介一、计算机直接数控系统(DNC)二、柔性制造单元FMC三、柔性制造系统FMS四、计算机集成制造系统CIMS五、数控机床的网络技术第二章数控铣床/加工中心的应用节数控铣床/加工中心一、数控铣削加工的主要对象二、数控机床坐标系第二节数控铣削加工的组织与质量管理一、成组技术在数控加工中的应用二、“5S”管理三、文明生产四、数控机床安全生产规程五、ISO 9000族标准第三节数控铣床/加工中心的安装与精度检验一、数控铣床的安装二、数控铣床/加工中心几何精度三、数控铣床/加工中心定位精度四、数控铣床/加工中心加工精度五、机床空运转试验六、机床连续空运转试验七、机床负荷试验八、最小设定单位试验九、原点返回试验第四节数控铣床/加工中心的维护保养一、保养的内容和要求二、加工中心保养的操作第二篇FANUC系统数控铣床/加工中心第三章数控机床的操作与仿真节数控铣床/加工中心的手动操作一、操作面板简介二、数控铣床/加工中心的手工操作三、与参考点有关的指令第二节对刀与参数设置一、对刀二、工件坐标系的设定三、PMC的参数设置第三节程序编辑与自动加工一、程序编辑二、程序的输入与输出三、自动加工四、镜像功能五、程序的再启动六、程序的复制七、移动部分程序八、合并程序第四章平面与外轮廓加工节平面加工一、数控铣床/加工中心用铣平面夹具二、在数控铣床/加工中心上加工平面常用刀具三、平面铣削工艺四、数控程序编制的基础五、平面度误差的检测六、平面加工中常见误差第二节外轮廓的加工一、数控铣削加工工序的划分二、铣削内外轮廓的进给路线三、数控加工工艺文件四、指令介绍五、刀具半径补偿第五章孔系加工与箱体类零件加工节孔系加工一、孔加工用刀具二、孔加工的进给路线三、孔加工的固定循环功能四、孔加工常见误差及修正第二节箱体零件的加工第六章槽与复合轮廓加工节槽类零件的加工一、槽的加工工艺二、子程序三、导致键槽产生加工误差的原因第二节复合轮廓的加工一、机夹可转位刀片及代码二、坐标变换三、极坐标编程第七章曲面加工节圆曲线轮廓与固定斜角平面铣削一、加工原理二、用户宏程序三、B类宏程序编程四、用户宏程序的调用五、圆曲线轮廓铣削六、固定斜角平面铣削七、通用宏程序的编写第二节曲面的加工一、刀具二、曲面轮廓加工工艺第八章特殊零件加工节螺旋件的加工一、夹具二、铣削螺纹三、螺旋线加工四、柱面坐标编程[G071(G107)]五、螺旋面和槽(凸轮)的误差分析第二节型腔加工第三节特殊零件加工一、G10/G11的应用二、托盘的应用三、动力头编程第四节配合件的加工第三篇SIEMENS(802D)系统数控铣床/加工中心第九章SIEMENS(802D)数控铣床/加工中心的操作与仿真节数控铣床/加工中心的程序编辑一、系统控制面板二、SIEMENS 802D机床控制面板三、程序编辑四、通过RS232接口进行数据传送五、插入固定循环第二节对刀与参数的设定一、输入刀具参数及刀具补偿参数二、输入/修改零点偏置值三、设定编程数据四、设定R参数值五、PLC参数的设置第三节数控铣床/加工中心的操作与仿真一、开机与关机二、刀具装夹三、回参考点四、手动控制进给运动五、MDA运行方式(手动输入)六、自动加工七、程序段搜索八、执行外部程序(由RS232接口输入)九、坐标系切换第十章轮廓加工节外轮廓的加工一、基本知识二、基本准备功能介绍三、其他指令四、循环第二节内轮廓的加工一、子程序二、极坐标与柱面坐标三、坐标变换第十一章孔系与型腔加工节孔系零件的加工一、孔加工固定循环简介二、加工实例第二节槽类零件与型腔加工一、铣槽循环二、型腔铣削三、加工实例。
- 1、下载文档前请自行甄别文档内容的完整性,平台不提供额外的编辑、内容补充、找答案等附加服务。
- 2、"仅部分预览"的文档,不可在线预览部分如存在完整性等问题,可反馈申请退款(可完整预览的文档不适用该条件!)。
- 3、如文档侵犯您的权益,请联系客服反馈,我们会尽快为您处理(人工客服工作时间:9:00-18:30)。
控制系统课程项目设计说明书项目名称:数控铣床控制系统设计系别:机械电子工程系专业:机械设计制造及其自动化姓名:city 学号:09128888 组员:学号:学号:指导教师:陈少波完成时间:2012 年 6 月8 日至2012 年 6 月22 日目录1 概述 (3)1.1 设计目的 (3)1.2使用设备 (3)1.3设计内容及要求 (4)2 NUM1020控制系统设计 (4)2.1 功能概述 (4)2.2 主要元器件选型 (5)2.2.1电机选型 (5)2.2.2 伺服驱动器与变频器选型 (8)2.3 电路原理设计 (9)2.3.1 电源供电设计 (9)2.3.2 驱动电路设计 (10)2.3.3 电机编码器与伺服驱动器连接设计 (10)2.3.4 手轮与轴卡连接设计 (11)2.3.5铣床控制电路设计 (12)2.4 控制系统设计 (13)2.4.1控制系统功能设计 (13)2.4.2 参数设置 (14)2.4.3 程序设计 (16)3 总结 (20)1 概述1.1 设计目的1)、掌握简单数控铣床控制系统的设计过程2)、掌握常用数控系统(NUM1020)的操作过程3)、掌握交流伺服电机的工作方式及应用过程4)、了解数控系统内置式PLC 的实现原理及编程方式5)、掌握数控系统自动控制功能程序的设计及开发过程1.2使用设备1)、NUM1020数控系统一套2)、安川交流伺服电机3套3)、计算机及梯形图编辑软件一套1.3设计内容及要求1)、以实验室现有的设备(NUM1020数控系统)作为控制器,参照实验室现有的数控铣床的功能,完成一台具有3轴联动功能的数控铣床的电气系统设计过程。
2)、移动轴(3轴)采用实验室现有的交流伺服电机进行驱动,采用半闭环位置控制模式。
3)、主轴采用实验室现有的变频调速器进行设计驱动,系统不要求具备自动换刀功能。
4)、完成PLC输入输出点的分配。
5)、具有行程及其他基本的保护功能。
6)、设计相关功能的梯形图控制程序(要求具有:手动进给功能、手轮进给功能、MDI功能、自动控制功能及各种基本的逻辑保护功能)7)、完成设计报告。
2 NUM1020控制系统设计2.1 功能概述此三轴联动数控铣床由X、Y、Z轴三轴及主轴组成,X、Y、Z轴采用伺服电机传动,由伺服驱动器驱动。
主轴采用普通三相异步电机,由变频器驱动。
数控系统采用NUM1020数控系统。
由NUM1020数控系统作为控制核心,三台伺服驱动器通过NUM1020系统的轴卡地址编码控制,主轴变频器由数控系统的PLC输出模拟量控制,同时变频器反馈速度模拟量输入到PLC。
系统框图如图1所示。
图1 功能概述图2.2 主要元器件选型2.2.1电机选型性能参数设计指标:(1)工作台质量m=510kg(所受的重力W=5000N);(2)主轴部分工作部件质量m=510kg(所受的重力W=5000N);(3)工作台的最大行程L p=600mm;(4)工作台X轴和Y轴最大移动速度V max=9000mm/min;(5)z轴最大移动速度为3000mm/min;(6)主轴最大转速n=2000n/min;(7)最大切削力F=1000N;(8)铣刀最大直径d=20mm;(9)工作台采用贴塑导轨,导轨的动摩擦系数μ=0.15。
(10)位置控制精度0.01mm。
2.2.1.1 X轴和Y轴驱动电机选型:X、Y轴为平动,电机驱动力仅需要克服平动所受到的导轨的摩擦力,因此电机所需功能较小。
所需驱动功率假设电机传动效率为η=0.9,则电机最小功率为P_1=P/η=0.13kW2.2.1.2 Z轴驱动电机选型:Z轴电机驱动主轴部件移动时,需要克服工作部件的重力,所需要电机功能较大。
所需驱动功率假设电机传动效率为η=0.9,则电机最小功率为P_2=P/η=0.28kW2.2.1.3 主轴轴驱动电机选型:依据性能参数设计指示,最大切削力F=1000N,铣刀最大直径d=20mm 所需电机最大转矩T由公式得所需驱动功率查电机型号选型手册,低功率交流电机的转速较大,没有2840 n/min及以下的,因此,此处电机扭矩计算按电机转速3000 n/min计算:假设电机传动效率为η=0.9,则电机最小功率为P_2=P/η=3.5Kw根据以上计算,X、Y、Z轴的伺服电机选用日本安川品牌的交流伺服电机,主轴选用西门子品牌的三相异步电机。
电机型号如下表所示:2.2.1.4 控制精度验算:设齿轮传动比,丝杆导程为t=6mm,则控制精度为符合设计精度指示要求。
2.2.2 伺服驱动器与变频器选型因驱动电机选取的是安川品牌的伺服电机,为了使系统性能更优,方便维护,选取安川品牌的伺服驱动器,型号与伺服电机对应。
变频器选型台达品牌的通用型号。
如下表所示:伺服器与变频器型号2.3 电路原理设计2.3.1 电源供电设计图2所示是铣床数控系统输入电源电路部分。
其中L1、L2、L3为火线,构成三相交流380V供电线;N为零线;PE为地线。
一台伺服电机额定电流8A,整个系统估计30A,初定40A,选用14平方铜线。
电源总开关采用断路器,对电路过载及过流保护。
通过三相隔离变压器,将三相交流380V电压转换成三相交流220V电压对伺服电机的供电,三台伺服电机的总功率是2.9KW,变压器功率选4.5KW。
加入220VAC-24VDC电源模块,将两相220V交流电压转换成24V直流电压,对NUM系统及其PLC输入输出部分供电。
图2 电源供电设计图3 驱动电路设计2.3.2 驱动电路设计如图3所示,X、Y、Z轴伺服电机连接伺服驱动器,主轴电机连接变频器,变频器的电路接通及正反转控制由NUM系统的PLC输出电路控制。
主轴电机由接入变频器,由AC380V供电。
冷却液泵采用三相AC380V的电机驱动,功率为40W。
电路中采用断路器对电路进行过载及短路保护。
2.3.3 电机编码器与伺服驱动器连接设计如图4所示,为电机编码器与伺服驱动器连接,采用速度控制模式。
X、Y、Z轴的接线方式相同。
图4电机编码器与伺服驱动器连接电路2.3.4 手轮与轴卡连接设计图5 手轮与轴卡连接电路2.3.5铣床控制电路设计图6 铣床控制电路如图6所示,继电器部分KA1~KA10为直流24V中间继电器,由输出开关量控制,主要控制主轴正反转、冷却电动机及伺服控制等。
图中S1、S3分别为X轴的正、反超程限位开关的常闭触点;S3、S4分别为Y轴的正、反超程限位开关的常闭触点;S5、S6分别为Z轴的正、反超程限位开关的常闭触点,它们结合伺服系统的运行标志位来控制系统的运行允许继电器。
伺服ON是来自伺服电源模块与伺服驱动模块的故障连锁。
2.4 控制系统设计图7 PLC接口如图7所示,根据系统控制对PLC的输入输出端口进行分配,输入开关量主要有进给装置、主轴装置、冷却液等的状态信息,输出开关量控制是相应的继电器工作。
2.4.1控制系统功能设计字段值定义2.4.2 参数设置数控机床存在很多的参数,不同的参数起到不同的控制作用,系统庞大,故在此只设置一些参数起到我们想要的参数,下面是NUM1020典型参数设置表:详细说明:(1)P2的意思是测量轴X、Y、Z轴,三个轴分别占有从低位到高位的三个位置。
系统设置为07时,在X、Y、Z所占的位子上显示的数都为1,所以三轴都测量。
当改成05时在Z的位置上显示的为0,所以只有X、Y轴测量(2)P0是指在显示屏中显示的轴。
同理当三轴都显示的时候系统设置为07。
当改为03时,Z轴不显示。
(3)P10是指轴的测量方向,当系统设置为04时,Z轴是1、X、Y轴是0。
应该X、Y轴的转动方向一致。
但由于决定电机转动方向的还有电机的三根线的接线方式。
所以会导致在观察的时候X、Z轴的转动方向一致。
(4)P11轴的测量单位转换系数、俗称电子齿轮。
通过改变其的设置值可以改变电机的转速。
(5)P12是手轮的测量方向,在系统中给首轮分配了两个位。
当设置值为00时,顺时针转动手轮时显示轴转动方向的值为正值。
当设置值为01时,顺时针转动手轮时显示轴转动方向的值为负值。
(6)P23是参数的设置可改变最大跟随误差,当超过跟随误差时,屏幕出现报警。
2.4.3 程序设计程序初始化:%w5.7为屏幕保护功能选择,设定其为0即禁止屏幕保护。
%w4.0当其为1时允许所有轴进给,不为1时所有轴都不能进给。
%w100.0为控制轴组1(X、Y、Z)的进给,%w100.1复位时,处于MDI模式或自动模型,其运行后其他指令不再运行,直接回到原来程序继续运行。
其中%w4.0、%w4.3、%w100.5、%100.2、%100.1等均为无条件执行,梯形图:MDI手轮和手动选择程序采用%M10.w作为分支条件,根据其等于1或者2转到相关的子程序执行。
图中%16.B代表手动方式和回零方式。
%15.B代表手动增量类型和手轮进给。
手轮控制%I100.0手动进给轴选择x,%I101.0代表手动正向进给,%I501.0代表正向行程开关限制,%w9.0代表手动正向进给(电机正转);%I101.0代表手动负向进给,%I501.1代表负向行程开关限制,%w9d.0代表手动负向进给(电机反转)。
Y、Z轴的方向控制同X轴。
此外,为了解决正转和反转同时转动的问题,用了互锁原理,当%101.0作用时,只有正转;当%101.1作用时,只有反转,当两个同时按下时两个都不转,控制X、Y、Z方向梯形图如下:主轴控制①%R122.0、%R122.1、%R122.2分别代表主轴的顺时、逆时转动和主轴停;%Q501.0代表主轴顺时转动的灯亮,%Q501.1逆时针转动的灯亮;%I503.6代表出故障,%w100.5代表系统至于等待状态,不处理正在执行的程序段中的下一个功能。
自动加工循环程序%I103.1循环启动按钮输入,当输入为1时,循环启动模型开启;%W3.2动作向NC系统提出循环加工请求;%R3.2为PLC检测到NC系统响应了循环加工请求后就动作,梯形图:电机报警要%R5.0显示息,%Q500.3才有效。
且%500.2、%500.3 %500.4都不工作,%M700.1运行。
3 总结这个课程设计项目综合了《数控技术》和《机电传动控制》两门课和内容,是一个综合的应用。
通过本次课程设计,使我了解熟悉了简单的数控铣床控制系统的设计过程和常用数控系统(NUM1020)的设计过程。
由于临近期末考试,时间紧迫,设计的准备工作内容量较大,因此这个课程设计由我和另两位同学组队完成。
项目中,我负责电机的选型及电气原理图设计。
这次课程项目设计,极大的提高了我能力。
因为时间问题,这个项目在两天时间内基本完成了,组员分工明确,及时交流查找到的信息,互相帮助解决各自遇到的问题,有效的提高了项目进程。
项目设计中,核心部件选用的是外国的产品,因国产的伺服电机运行不稳定,可靠性远比不上外国的产品,数控系统可靠性较差等等这些原因使我们放弃选用国产的产品。