复合材料界面1
金属基复合材料界面

金属基复合材料界面金属基复合材料界面是指由金属基体和其他材料相互作用形成的界面。
金属基复合材料是一种重要的结构材料,在航天、航空、汽车制造等领域发挥着重要作用。
而界面则是金属基复合材料性能的关键因素之一,影响着材料的力学性能、热学性能、电学性能等。
金属基复合材料界面的特点主要包括界面强度、界面形态以及界面反应等。
首先,界面强度是指金属基复合材料界面的抗剪强度,决定了材料的强度和韧性。
界面形态则是指金属基复合材料界面的结构形貌,包括界面的平整度、均匀度等。
最后,界面反应是指金属基复合材料界面处发生的化学反应,影响着材料的稳定性和使用寿命。
金属基复合材料界面的研究主要包括界面强度的测试方法以及界面的表征技术。
一般来说,界面强度可以通过剪切测试、拉伸测试等方法进行测量。
剪切测试是将金属基复合材料的界面置于剪切载荷下,通过测量界面之间的滑动距离和加载力来计算界面的剪切强度。
拉伸测试则是将金属基复合材料的界面置于拉伸载荷下,通过测量界面的断裂强度和断裂面积来计算界面的拉伸强度。
界面的表征技术主要包括电子显微镜观察和X射线衍射分析等。
电子显微镜观察可用于观察金属基复合材料界面的形貌和结构特征,如界面的平整度、均匀度以及异质相等。
X射线衍射分析则可以用于分析界面处的晶体结构和相变行为,从而揭示界面反应的机制和影响因素。
金属基复合材料界面的性能调控主要包括三个方面,即界面结构调控、界面化学调控以及界面力学调控。
界面结构调控主要是通过改变复合材料的结构和工艺参数来调控界面的形貌和结构特征,从而改善界面的强度和稳定性。
界面化学调控则是通过引入中间相或质量扩散来调控界面的化学反应,从而提高界面的稳定性和抗氧化性能。
界面力学调控主要是通过改变金属基复合材料的力学性能来调控界面的剪切强度和散射行为,从而提高界面的强度和韧性。
总之,金属基复合材料界面是一种关键的材料界面,影响着金属基复合材料的力学和热学性能。
了解金属基复合材料界面的特点和性能调控方法,对于开发高性能金属基复合材料具有重要意义。
复合材料的界面工程与性能优化
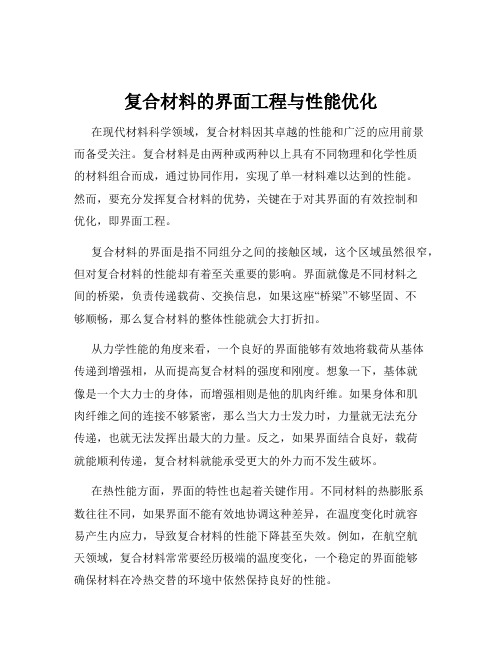
复合材料的界面工程与性能优化在现代材料科学领域,复合材料因其卓越的性能和广泛的应用前景而备受关注。
复合材料是由两种或两种以上具有不同物理和化学性质的材料组合而成,通过协同作用,实现了单一材料难以达到的性能。
然而,要充分发挥复合材料的优势,关键在于对其界面的有效控制和优化,即界面工程。
复合材料的界面是指不同组分之间的接触区域,这个区域虽然很窄,但对复合材料的性能却有着至关重要的影响。
界面就像是不同材料之间的桥梁,负责传递载荷、交换信息,如果这座“桥梁”不够坚固、不够顺畅,那么复合材料的整体性能就会大打折扣。
从力学性能的角度来看,一个良好的界面能够有效地将载荷从基体传递到增强相,从而提高复合材料的强度和刚度。
想象一下,基体就像是一个大力士的身体,而增强相则是他的肌肉纤维。
如果身体和肌肉纤维之间的连接不够紧密,那么当大力士发力时,力量就无法充分传递,也就无法发挥出最大的力量。
反之,如果界面结合良好,载荷就能顺利传递,复合材料就能承受更大的外力而不发生破坏。
在热性能方面,界面的特性也起着关键作用。
不同材料的热膨胀系数往往不同,如果界面不能有效地协调这种差异,在温度变化时就容易产生内应力,导致复合材料的性能下降甚至失效。
例如,在航空航天领域,复合材料常常要经历极端的温度变化,一个稳定的界面能够确保材料在冷热交替的环境中依然保持良好的性能。
除了力学和热性能,界面还对复合材料的电学、光学等性能产生影响。
比如在电子封装材料中,界面的电学特性直接关系到信号的传输速度和稳定性;在光学材料中,界面的平整度和折射率匹配程度决定了光线的透过率和反射率。
那么,如何进行复合材料的界面工程来优化其性能呢?这涉及到多个方面的策略和技术。
首先是对界面的物理和化学改性。
通过物理方法,如表面打磨、等离子体处理等,可以增加界面的粗糙度和活性,从而提高界面的结合强度。
化学改性则包括对基体和增强相表面进行化学处理,引入官能团,以增强它们之间的化学键合。
复合材料的界面

复合材料的界面复合材料是由两种或两种以上不同的材料组成的材料,通过各自的特性相互作用形成的一种新型材料。
界面是不同材料之间的接触面,是复合材料性能的决定因素之一。
下面将从界面的作用、界面的特性和界面的调控三个方面对复合材料的界面进行详细介绍。
界面在复合材料中起着连接、传递和分散应力的作用。
首先,界面连接了不同材料一起,使其形成整体性能优于单个材料的复合材料。
其次,界面能够传递应力,使复合材料整体受力均匀、分散应力集中,提高材料的强度和韧性。
最后,界面还能够分散应力,减少裂纹扩展和断裂的可能性,延长复合材料的使用寿命。
界面的特性主要包括接触角度、界面能、亲水性或疏水性等。
首先,接触角度反映了界面的亲水性或疏水性,即其与液体接触时的表面张力。
亲水性的界面会使液体在复合材料中能够更好地湿润、浸润,提高复合材料的粘合度和界面传递性。
其次,界面能是指界面上分子之间相互作用的能量。
界面能越小,表示复合材料中不同材料之间的相容性越好,界面强度越高。
最后,亲水性界面和疏水性界面对复合材料的性能也会产生不同的影响。
如亲水性界面可增加复合材料的应力强度、韧性和热稳定性,而疏水性界面可减少复合材料的吸湿性和电导性。
界面的调控主要通过界面改性和表面处理两个途径实现。
首先,通过界面改性可以改变界面的性质,提高其性能,例如通过添加界面活性剂进行处理,使界面能更好地吸附和传递应力;通过聚合物接枝物改性,增加界面粘合力等。
其次,通过表面处理可以对界面进行改善,例如通过物理或化学方法处理材料表面,使其表面特性更加适合复合材料的应用。
常用的表面处理方法有溶剂清洗、电子束辐照、化学氧化等。
综上所述,界面是影响复合材料性能的重要因素,通过界面的调控可以改善复合材料的性能。
理解和研究界面的特性和调控方法对于开发出更加优异的复合材料具有重要意义。
复合材料的界面特性与力学性能
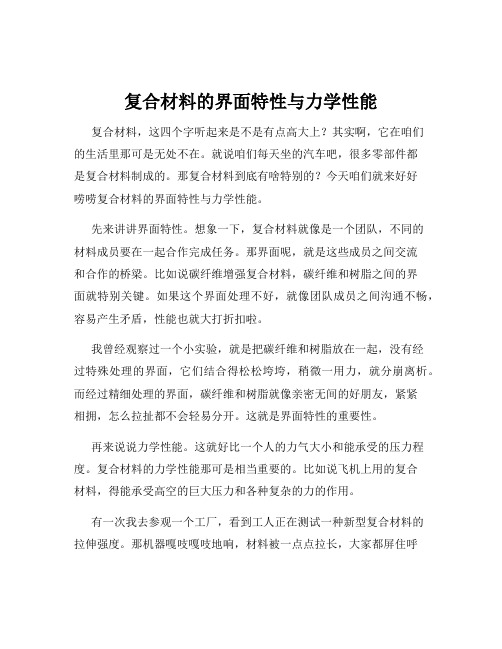
复合材料的界面特性与力学性能复合材料,这四个字听起来是不是有点高大上?其实啊,它在咱们的生活里那可是无处不在。
就说咱们每天坐的汽车吧,很多零部件都是复合材料制成的。
那复合材料到底有啥特别的?今天咱们就来好好唠唠复合材料的界面特性与力学性能。
先来讲讲界面特性。
想象一下,复合材料就像是一个团队,不同的材料成员要在一起合作完成任务。
那界面呢,就是这些成员之间交流和合作的桥梁。
比如说碳纤维增强复合材料,碳纤维和树脂之间的界面就特别关键。
如果这个界面处理不好,就像团队成员之间沟通不畅,容易产生矛盾,性能也就大打折扣啦。
我曾经观察过一个小实验,就是把碳纤维和树脂放在一起,没有经过特殊处理的界面,它们结合得松松垮垮,稍微一用力,就分崩离析。
而经过精细处理的界面,碳纤维和树脂就像亲密无间的好朋友,紧紧相拥,怎么拉扯都不会轻易分开。
这就是界面特性的重要性。
再来说说力学性能。
这就好比一个人的力气大小和能承受的压力程度。
复合材料的力学性能那可是相当重要的。
比如说飞机上用的复合材料,得能承受高空的巨大压力和各种复杂的力的作用。
有一次我去参观一个工厂,看到工人正在测试一种新型复合材料的拉伸强度。
那机器嘎吱嘎吱地响,材料被一点点拉长,大家都屏住呼吸,眼睛紧紧盯着仪表上的数据。
最后结果出来,那种满足的神情,就好像是看到自己精心培养的孩子考了个好成绩一样。
复合材料的界面特性和力学性能是相互关联的。
一个好的界面特性能够让力学性能得到充分发挥,就像一个配合默契的团队,能够高效地完成任务。
而如果界面特性不好,力学性能再好也白搭,就像一群有本事的人,却因为互相不配合而干不成大事。
在实际应用中,为了获得理想的复合材料性能,科学家和工程师们可是绞尽脑汁。
他们不断地研究新的材料组合,改进界面处理技术。
有时候,为了找到最合适的配方和工艺,得进行无数次的试验和失败。
比如说,在研发一种用于体育器材的复合材料时,研发人员得考虑材料的强度、韧性、重量等各种因素。
复合材料的界面

改变强化材料表面的性质
• 对SiC晶须表面采用化学方法处理后XPS(X-ray Photoelectron Spectroscopy)分析的结 果。由C(1s)和Si(2p)的波谱可以看出,有的地方存在SiO2,有的地方不存在SiO2。 利用这样的表面状态的差来增强界面的结合力。
6.6.2 向基体添加特定的元素
• 在用烧结法制造复合材料的过程中,为了有助于 烧结,往往向基体添加一些元素。有时为了使纤 维与基体发生适度的反应以控制界面,也可以添 加一些元素。在SiCPCS纤维强化玻璃陶瓷(LAS) 中,如果采用通常的LAS成分的基体,在晶化处 理时会在界面产生裂纹。而添加百分之几的Nb时, 热处理过程中会发生反应,在界面形成数微米的 NbC相,获得最佳界面,从而达到高韧化的目的。
5.5 界面行为
5.5.1 界面的脱粘与剥离(Debonding)
研究界面的脱粘与剥离的意义
研究思路 ➢ 考虑基体中仅有一根纤维,受到拉伸载荷为Pf的情
况 ➢ 分析复合材料中强化材料与基体间应力传递的方
式 解析法: ➢ 应用最大剪切应力理论 ➢ 应用断裂力学理论
脱粘、剥离与滑动的关系为一旦发生脱粘与剥离,剥离部分就产生滑 动。解析法可以应用最大剪切应力理论,也可以应用断裂力学理论。
临界值
• 断裂的机制 张开型裂纹 φ=0
剪切型裂纹 φ=90 φ=tan-1(KⅡ/KⅠ)
界面对复合材料性能的影响
• 界面特性
复合材料性能
界面黏结强度下降复合材料弹性模量下降
• 但界面特性与复合材料性能的定量关系少
• 界面参数 (强度,韧性)
• 脆性组元的界面区域,尺寸与厚度相当的缺 陷 断裂力学模型
5.2.1 界面应力与非弹性过程
复合材料的界面理论

复合材料的界面理论1、界面形成及其形成1.1界面的定义复合材料的界面是指基体与增强相之间化学成分有显著变化的、构成彼此结合的、能起载荷传递作用的微小区域。
复合材料的界面是一个多层结构的过渡区域,约几个纳米到几个微米。
此区域的结构与性质都不同于两相中的任何一相。
这一界面区由五个亚层组成,每一亚层的性能都与基体和增强相的性质、复合材料成型方法有关。
界面区域如图1-1所示。
1.2界面的形成复合材料体系对界面要求各不相同,它们的成形加工方法与工艺差别很大,各有特点,使复合材料界面形成过程十分复杂,理论上可分为两个阶段: 第一阶段:增强体与基体在一组份为液态(或粘流态)时的接触与浸润过程。
在复合材料的制备过程中,要求组份间能牢固的结合,并有足够的强度。
要实现这一点,必须要使材料在界面上形成能量最低结合,通常都存在一个液态对固体的相互浸润。
所谓浸润,即把不同的液滴放到不同的液态表面上,有时液滴会立即铺展开来,遮盖固体的表面,这一现象称为“浸润”。
第二阶段:液态(或粘流态)组份的固化过程,即凝固或化学反应。
固化阶段受第一阶段的影响,同时它也直接决定着所形成的界面层的结构。
以固热性树脂的固化过程为例,固化剂所在位置是固化反应的中心,固化反应从中心以辐射状向四周扩展,最后形成中心密度大、边缘密度小的非均匀固化结构,密度大的部分称为胶束或胶粒,密度小的称胶絮。
2、界面对复合材料性能的影响及影响界面结合强度的因素 2.1界面对复合材料性能的影响复合材料内界面结合强度是影响复合效果的最主要因素。
界面的结合强度主要取决于界面的结构、物理与化学性能。
具有良好结合强度的界面,可以产生如下强化效应:(1)阻止裂纹的扩散,提高材料的韧性;(2)通过应力传递,使强化相承受较大的外载荷,提高复合材料的承载能力;(3)分散和吸收各种机械冲击和热冲击的能量,提高抗外加冲击的能力;(4)使强化相与基体产生既相互独立又相互协调的作用,弥补各自的缺点,获得新的材料使用性能。
复合材料的界面(1)
缺点:难以同时满足拉丝、退并、纺织与树脂浸 湿和粘结。
玻纤的表面处理
五.玻纤表面处理工艺
·迁移法
将化学处理剂直接加入树脂胶液中进行整体 掺和,在浸润的同时将处理剂施予GF上,借 处理剂从树脂胶液致纤维表面的“迁移”作 用而与纤维表面发生作用,从而在树脂固化 过程中产生偶联作用。
玻纤的表面处理
玻纤的表面处理
·钛酸酯偶联剂
亲有机部分通常为长链烃基(C12~C18),长力的 缠绕可以转移应力应变,提高冲击强度,断裂伸 长率与剪切长度。此外长链烃基还可以改变无机 物界面处的表面能使粘度下降,显示良好的熔融 流动性。
玻纤的表面处理
·其他偶联剂
锆类偶联剂是含铝酸锆的低分子量的无机聚合物。 它不仅可以促进不同物质之间的粘合,而且可以 改善复合材料体系的性能,特别是流变性能。该 类偶联剂既适用于多种热固性树脂,也适用于多 种热塑性树脂。 Байду номын сангаас 此外还有镁类偶联剂和锡类偶联剂。
步骤:首先出去玻璃纤维表面的纺织型浸润剂,然后经过 处理剂溶液浸渍、水洗、烘干等工艺,使GF表面被附着上 一层处理剂。 特点:处理的各道工序都需要专门的设备,初投资较大 , 玻璃纤维强度损失大,但处理效果好稳定,是国内常用的 处理方法。
玻纤的表面处理
五.玻纤表面处理工艺
·前处理法
适当改变浸润剂的配方,既能满足拉丝、退并、 纺织各道工序的要求,又不妨碍树脂对玻璃纤维 的浸湿和粘结。将化学处理剂加入到浸润剂中。 与后处理法相比省去复杂的工艺设备,使用简便。 避免热处理造成GF强度的损失。
复合材料的界面性质及其影响因素研究
复合材料的界面性质及其影响因素研究复合材料是由两种或多种不同类型的材料组合而成的材料。
当前,复合材料已经成为了制造轻、高强度、高性能结构的关键材料。
然而,复合材料不同于单一材料。
它的内部结构是非均匀的。
它由多种不同的物理和化学材料和界面组成。
这些界面对于决定材料的性能和可靠性非常重要。
因此,深入研究复合材料的界面性质及其影响因素是十分必要的。
界面性质是由所制备的复合材料的成分和结构决定的。
界面包含了粘合剂、封闭剂、填充剂等物质。
界面的主要作用是调节复合材料的微观结构和基本物理性质。
因此,界面的稳定性和耐久性非常重要。
同时,在研究界面的影响因素时,也要考虑到其所面临的环境。
在研究复合材料界面性质的时候,最简单的方式是通过表面官能基的化学反应。
表面官能基是复合材料基材与填充剂之间的接触面上能够吸附住附加分子的位点。
改变表面官能基的产生和附加分子的种类和数量将导致复合材料的界面性质的变化。
此外,调节表面粗糙度、温度、湿度等因素也可以影响到复合材料的界面性质。
表面官能基种类和数量是影响界面性质的最重要因素之一。
表面官能基可以用于调节填充物和基材界面的粘合能力。
例如,氢键作用是一种重要的表面官能基之一,它可以稳定共价键。
低反式构象的分子通常易于通过氢键作用而形成稳定的晶体和膜表面。
通过调节复合材料中官能基种类和数量,可以控制复合材料的界面化学反应。
根据目标,可以使该反应同时导致优越的耐久性、粘附力和光学性质。
此外,使用界面活性剂等表面活性剂可以影响复合材料界面性质。
表面活性剂可以通过三种方式作用于界面。
它们可以影响表面粗糙度,提高表面能量,以及增加材料和附加分子之间的化学反应。
对于复合材料的生产,涂覆基材可以利用表面活性剂来加强涂层和基材之间的粘合力。
另一个影响复合材料界面性质的重要因素是填料种类和形状。
填料种类和形状决定了复合材料的宏观和微观结构,以及界面交互作用的方式。
粒子形状的变化可以通过影响界面张力和力学适应性来影响复合材料的性能。
复合材料的界面相互作用与性能
复合材料的界面相互作用与性能在现代材料科学的广阔领域中,复合材料以其独特的性能和广泛的应用成为了研究的焦点。
复合材料并非简单地将不同材料混合在一起,其性能的优劣在很大程度上取决于材料之间的界面相互作用。
复合材料通常由两种或两种以上具有不同物理和化学性质的组分材料组成。
这些组分可以是金属、陶瓷、聚合物等。
而它们之间的界面,就像是不同国家之间的边界,看似狭窄,却对整个“领土”(复合材料)的稳定和发展起着至关重要的作用。
界面的相互作用首先体现在物理结合方面。
这包括表面的粗糙度、微观的几何形状匹配等因素。
一个粗糙的界面可以提供更多的接触面积,增强材料之间的机械嵌合作用,就如同拼图的碎片相互嵌合得越紧密,整体就越牢固。
而良好的几何形状匹配则能减少应力集中,使载荷更均匀地分布在整个复合材料中。
化学相互作用在复合材料的界面中同样不可或缺。
在某些情况下,不同组分材料在界面处会发生化学反应,形成新的化合物。
这种化学反应可以增强界面的结合强度,提高复合材料的整体性能。
例如,在碳纤维增强聚合物复合材料中,碳纤维表面的官能团与聚合物基体之间可能发生化学反应,从而改善纤维与基体之间的载荷传递。
界面的相互作用还对复合材料的性能产生了深远的影响。
从力学性能来看,一个良好的界面能够有效地传递应力,避免在界面处出现应力集中和过早的失效。
这意味着复合材料在承受外力时,能够充分发挥各组分材料的优势,展现出比单一材料更出色的强度和韧性。
热性能也是一个重要方面。
不同材料的热膨胀系数往往不同,如果界面结合不好,在温度变化时就容易产生热应力,导致材料性能下降甚至失效。
而通过优化界面相互作用,可以降低热应力,提高复合材料在不同温度环境下的稳定性。
电性能方面,界面的存在可能会影响电子的传输和电导性能。
在一些导电复合材料中,界面的特性对于控制电阻、电容等电学参数起着关键作用。
此外,界面相互作用还影响着复合材料的耐腐蚀性和耐磨性等性能。
一个稳定且结合良好的界面可以有效地阻止腐蚀介质的侵入,延长材料的使用寿命;在摩擦磨损的过程中,界面的特性也决定了材料的耐磨表现。
复合材料的界面定义
复合材料的界面定义
复合材料是由两种或两种以上的材料组合而成的新材料,具有优异的性能和特点。
在复合材料中,界面是指不同组分之间的交界面,是复合材料中最重要的部分之一。
界面的性质和特点直接影响着复合材料的整体性能和应用范围。
因此,对复合材料的界面进行准确的定义是非常重要的。
首先,复合材料的界面可以被定义为不同组分之间的交界面,包括纤维和基体
之间的界面、不同填料之间的界面等。
这些界面通常是由于材料的不同成分或性质所导致的,因此界面的性质往往会对整体材料的性能产生显著的影响。
其次,复合材料的界面还可以被定义为材料的微观结构和相互作用的区域。
在
这些区域中,不同组分之间的相互作用会产生一系列的界面效应,如界面扩散、界面结合、界面应力传递等。
这些效应会直接影响着复合材料的力学性能、热学性能、耐久性等方面。
另外,复合材料的界面还可以被定义为材料的表面区域,包括纤维表面、填料
表面、基体表面等。
这些表面区域往往是复合材料与外界环境或其他材料之间的直接接触区域,因此界面的性质会直接影响着复合材料的耐腐蚀性、黏附性、润湿性等方面。
综上所述,复合材料的界面可以被定义为不同组分之间的交界面、材料的微观
结构和相互作用区域,以及材料的表面区域。
界面的性质和特点直接影响着复合材料的整体性能,因此对复合材料的界面进行准确的定义是非常重要的。
在未来的研究中,我们需要进一步深入理解复合材料的界面定义,探索界面效应对复合材料性能的影响机制,为复合材料的设计、制备和应用提供更加科学、准确的理论基础。
- 1、下载文档前请自行甄别文档内容的完整性,平台不提供额外的编辑、内容补充、找答案等附加服务。
- 2、"仅部分预览"的文档,不可在线预览部分如存在完整性等问题,可反馈申请退款(可完整预览的文档不适用该条件!)。
- 3、如文档侵犯您的权益,请联系客服反馈,我们会尽快为您处理(人工客服工作时间:9:00-18:30)。
反应原理:第一步甲醛与苯酚加成生成羟甲基苯酚
OH + C2H O
OH
OH
CH 2OH CH2O HOH2C
CH 2OH
OH
OH
CH2 O
CH 2OH
CH 2OH
CH2 OH
OH
HOH 2C
CH 2OH
CH 2OH
第二步羟甲基与苯酚邻对位氢脱水缩合
OH
CH 2OH +
OH
OH
CH 2
OH
或羟甲基与羟甲基缩合成醚键,再在加热下脱去甲醛成次甲基
轻质高强 电性能好 耐腐蚀性能好 热性能好 性能的可设计性及材料与结构的一致性 如:不同方向力学性能的调整(纤维的排列方向,铺层的次序,铺层的层数变
化),材料热膨胀系数的调整(碳纤维在平行纤维方向的热膨胀系数为负 值),制品不同部位力学性能的调整。 在制造复合材料的同时,也直接得到制品,材料和制品可一次获得。 界面结合性差,层间剪切强度低
H2N(CH2CH2NH)nCH2CH2NH2 多乙烯多胺
8.2.3 酚醛树脂
由酚类和酚醛树脂:以碱为催化剂,甲醛/苯酚摩尔 比大于1,反应到一定阶段停止,加热固化。
热塑性酚醛树脂:以酸为催化剂,甲醛/苯酚摩尔 比小于1,加入六次甲基四胺等固化剂才能固化。
酚醛树脂固化反应有小分子放出,所以固化在 加热、加压下进行。
8.3 增强材料
凡能提高基体材料机械强度、弹性模量等力学性能的材 料称为增强材料。
复合材料的界面
8.1 复合材料概述
复合材料是由两种或两种以上的不同材料通过一定工艺 制成的多相材料,并具有与原组成材料不同的新的性能。
包括三层意义: 它是一种多相材料,包含两种或两种以上物理上不同并可(机械)
分离的材料。 它可以在人为控制下以某种工艺将几种分离的不同材料混合在一起,
形成复合材料。 它的性能应优于各单独的组分材料,在某些方面可能具有组分材料
O CO
HC=CH
O CO
HC=CH
在引发剂的存在下,不饱和聚酯中的双键与苯乙烯发生 自由基共聚反应,交联成三元网状结构
O CO
O CO
O
HC-CH
CO
CH-Ph
CH
n
O
HC-CH
CO
HC-CH
CH-Ph CH
n HC-CH
过氧化物引发剂: BPO 过氧化甲乙酮 过氧化环己酮
氧化-还原引发体系: BPO-N,N-二甲基苯胺 过氧化甲乙酮-环烷酸钴 过氧化环己酮-环烷酸钴
R-O-CH2-CH-CH2 O
R-NH-CH2-CH-CH2 O
R-COO-CH2-CH-CH2 O
另一种引入环氧基的方法是用过醋酸或过 氧化氢对带双键的化合物进行环氧化:
R-CH=CH-R'-CH=CH-R"
R-CH-CH-R'-CH-CH-R"
O
O
线型脂肪族类环氧树脂
环氧树脂的固化
反应性固化剂: 脂肪族多元胺、芳香胺、 多元酸等
缩水甘油醚型环氧树脂
R-OH+CH2-CH-CH2Cl O
R-O-CH2-CH-CH2Cl OH
缩水甘油胺型环氧树脂
R-NH2+CH2-CH-CH2Cl O
R-NH-CH2-CH-CH2Cl OH
缩水甘油酯型环氧树脂
R-COOH+CH2-CH-CH2Cl O
R-COO-CH2-CH-CH2Cl OH
一些常用材料及纤维复合材料的比强度和比模量
材料
密度 (g/cm3)
钢
7.8
铝合金
2.8
钛合金
4.5
玻璃纤维复合 材料
2.0
碳纤维I/环氧 复合材料
1.6
碳纤维II/环氧 1.45 复合材料
有机纤维/环 氧复合材料
1.4
硼纤维/环氧 复合材料
2.1
拉伸强度 (GPa) 1.03 0.47 0.96 1.06
1.07
1.50
1.40
1.38
弹性模量 比强度
比模量
(102GPa) (106cm) (108cm)
2.1
1.3
2.7
0.75
1.7
2.6
1.14
2.1
2.5
0.4
5.3
2.0
2.4
6.7
15
1.4
10.3
9.7
0.8
10.0
5.7
2.1
6.6
10
8.2 聚合物基复合材料
8.2.1 不饱和聚酯 不饱和聚酯树脂是由饱和二元酸(或酸酐),不
没有的独特性能。
复合材料的结构:
基体相 增强剂相 相与相之间存在界面。
复合材料按基体分类 聚合物基复合材料
热塑性聚合物基:PP、PE、尼龙、PVC 热固性聚合物基:不饱和聚酯、环氧树脂、酚醛树脂等 金属基复合材料 无机非金属基复合材料: 陶瓷基、水泥基、玻璃基
复合材料的特性
OH
OH
CH 2OH + HOH2C
-H2 O
OH
OH
OH
OH
CH 2OH2C
- CH2O
CH 2
碱催化下第二步羟甲基缩合反应较慢,羟甲基 可稳定存在,因此在以后加热时,羟甲基可继 续反应,固化成网络结构。
酸催化下,羟甲基的缩合反应迅速,生成的羟 甲基立即缩合,但因苯酚过量,甲醛消耗完反 应终止。以后再加入甲醛或固化剂,反应继续, 固化成网络结构。
饱和二元酸(或酸酐)与多元醇缩聚而成的聚 酯在乙烯基单体(如苯乙烯)中的溶液。
饱和二元酸或酸酐:
O
COOH
C CO
O
COOH
不饱和二元酸或酸酐
O HC C HC C O
O
HC COOH HOOC CH
多元醇
CH 3CH-CH 2 OH OH
交联剂
CH=CH2
HOCH2CH2OH
多元酸(酸酐)与多元醇缩聚,形成主链含有双键的 聚酯:
实际应用例子:大型储槽,容器,卫生洁具,冷却塔,雷达 罩,人造大理石,人造玛瑙,舰船方面的应用,等等。
8.2.2 环氧树脂
环氧树脂是指分子结构中含有2个或2个以上环氧基 的化合物。环氧基可在分子链末端,也可在分子链 的中间。
分子链中引入环氧基一般有两种方法,一种是由含 活泼氢的化合物如酚类、有机酸类、胺类与环氧氯 丙烷发生开环反应,然后在碱的作用下闭环,引入 环氧基:
催化性固化剂: 叔胺、三氟化硼等
脂肪族多元胺固化原理
R-NH2+CH2-CH----O
OH
CH2-CHR-N CH2-CH-
OH
常用的脂肪胺固化剂
H2NCH2CH2NHCH2CH2NH2 二乙烯三胺
H2NCH2CH2NHCH2CH2NHCH2CH2NH2 三乙烯四胺
H2NCH2CH2NHCH2CH2NHCH2CH2NHCH2CH2NH2 四乙烯五胺