经济型数控车床自动对刀的设计与实现
数控车床对刀的原理及方法

数控车床对刀的原理及方法一、数控车床对刀的原理:对刀是数控加工中的主要操作和重要技能。
在一定条件下,对刀的精度可以决定零件的加工精度。
同时,对刀效事还直接影响数控加工效丰。
仅仅知道对刀方法是不够的。
还要知道数控系统的各种对刀设置方式,。
以及这些方式在加工程序中的调用方法,同时要知道各种对刀方式的优缺点。
使用条件等。
一股来说,数控加工零件的编程和加工是分开进行的。
数控编程员根据零件的设计图纸,速定一个方便编程的工件坐标系,工件坐标系-般与零件的工艺基准或设计基准重合。
在工件坐标系下进行零件加工程序的编制,对刀时,应使指刀位点与对刀点重合,所谓刀位点是指刀具的定位基准点,对于车刀来说,其刀位点是刀失。
对刀的目的是确定对刀点。
在机床坐标系中的绝对坐标值,测量刀具的刀位偏基值。
对刀点找正的准确度直接影响加工精度。
在实际加工工件时。
使用一把刀具一般不能满足工件的加工要求,通常要使用多把刀具进行加工。
在使用多把车刀加工时,在换刀位置不变的情况下,换刀后刀失点的几何位置将出现差异,这就要求不同的刀具在不同的起始位置开始加工时。
都能保证程序正常运行。
为了解决这个问题。
机床数控系統配备了刀具几何位置补能的功能,利用刀其几何位置补偿功能,只要事先把每把刀相对于某一预先选定的基准刀的位置偏差测量出来,输入到数控系统的刀具梦数补正栏指定组号里,在加工程序中利用T指令,即可在刀具轨述中自动补偿刀具位置偏差。
刀具位置值差的利量同样也需通过对刀操作来实现。
生产厂家在制造数控车床,必须建立位置测量,控制、显示的统基准点。
该基准点就是机床坐标系原点,也就是机床机械目零后所处的位置。
操作方法01数控车床对刀是车床加工技术中比较复杂的工艺之一,它的精度将会直接影响到所加工零部件的精度,所以不能马虎。
02数控车床对刀的基本原理就是将零件的坐标系与数控机床的坐标系整合起来,然后依据这个坐标系来确定对刀位置。
03目前数控车床大部分采用的是对刀器主动对刀,对刀器会自动向零件确定一个原点位置,这是十分方便快捷的对刀方法。
经济型数控车床的对刀及刀偏的计算方法探讨

设 2号 刀 为外 螺 纹车 刀 , 先手 动 后点 动 的方 式下 , 刀尖 移 至 其 刚接 触 外 圆 , 最 终 移 至如 图 1所 在 将 并 示 0点。 时, 此 显示 器 上 的坐 标 ( 为 X 、 d) 设 c Z 就是 2 刀 的刀 偏 , r= 3 号 若 ,d =一4则 “= r=3 训 = d ,
・
收 稿 日期 :02 4—1 20 —0 6
作者简介 : 洪均(92 , 重庆市江津人 , 夏 17 一) 男, 重庆工商大学 助理实验师 。
维普资讯
第 2期
夏 洪 均 : 济 型 数 控 车 床 的对 刀及 刀 偏 的计 算 方 法 探 讨 经
维普资讯
第1 9卷 第 2期
Vl . 9 N 2 0 1 o. 1
渝 州大学学报( 自然 科 学版 )
J OUR LO NA FYL I U UN V S I Na.ce . dt ) r- AI C I ER rY( tS in E i.
20 0 2年 6月
8 1
2 1 常 用 的 刀偏 调试 方 法 . 多 刀 车 削时 , 常 以第 一 把进 行 车 削的 刀具 为基 准 刀 , 通 一般 是 外 圆车 刀 , 为 1 刀 。 设 号 同对 刀 时 的方 法 样, 用该 刀 偏端 面 车外 圆 , 如 图 1 示 0 点位 置 时将 显 示器 上 的x、 坐标 都 清零 。 时 1 刀 刀尖 的 在 所 z 此 号 坐 标为 XO ZO 其成 为 真正 意 义 上 的基 准刀 。 T 1 U ) 将该 刀 退 至安 全换 刀位 置后 , 2 刀。 、 , 即 O ( O WO 。 换 号
所谓 对 刀 , 是 将 刀具 的刀位 点 调整 到与 数 控程 序 中 G 2 或 其 它 建 立 工 件 坐 标 系 指 令 ) 指 定 的坐 就 9( 所 标位 置 。即 在工 件 坐标 系中使 刀 具 的 刀 位 点位 于 起 刀 点 ( 刀 点 ) , 其 在 数 控 程 序 的控 制 下 , 对 上 使 由此 刀 具 所切削 出的加 工 表 面相 对于 定 位基 准 有正 确 的尺寸 关 系, 从而 保 证 零 件 的加 工 精 度 要 求 。 经 济型 数 控 车 床一般 采 用 手工 编 程 , 为编 程 方便 , 序 原 点通 常 设在 车 床 主轴 中心 线与 工 件 端 面 的交 点 处 。 在此 , 程 设 编程 原 点在 主 轴 中心线 与 工 件左 端 面 的交点 处 , 外 圆车 刀来 对刀 。 以 在 手 动方 式 下 , 将外 圆车 刀随 意在 工 件毛 坯右 端 以从 中心 向外 圆进 给 的方 式偏 端 面, 到适 合 于车 削外 圆时停 止 x 向退 刀, 将 显示 器上 x、 并 Z坐 标都 清零 。 后 向 Z的 负 向进 刀 车一 段 外 圆, 时如 图 1 然 此 所示 O点 就 是坐 标 零点 。 刀 停 车后 , 外 圆直 径 D。 建 立 工 件 坐 标 系指 令 为 G 2 退 测 若 9 Z , 件 总长 为 L( 6工 一般 L约 小于 b 。 么, 刀 点 Q 的位 置 关 系 ( )那 对 图 1 其坐 标就 可用 如下 公式 求 得 : = a—D, ) z= b—L。 中, 为x 向坐 其 标值( 本文 均取 直 径 值 ) z为 Z 向坐 标值 。 ,
简述数控车床的对刀步骤
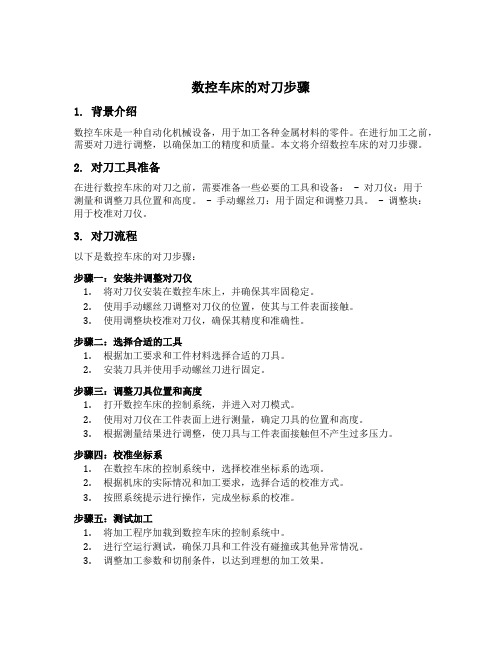
数控车床的对刀步骤1. 背景介绍数控车床是一种自动化机械设备,用于加工各种金属材料的零件。
在进行加工之前,需要对刀进行调整,以确保加工的精度和质量。
本文将介绍数控车床的对刀步骤。
2. 对刀工具准备在进行数控车床的对刀之前,需要准备一些必要的工具和设备: - 对刀仪:用于测量和调整刀具位置和高度。
- 手动螺丝刀:用于固定和调整刀具。
- 调整块:用于校准对刀仪。
3. 对刀流程以下是数控车床的对刀步骤:步骤一:安装并调整对刀仪1.将对刀仪安装在数控车床上,并确保其牢固稳定。
2.使用手动螺丝刀调整对刀仪的位置,使其与工件表面接触。
3.使用调整块校准对刀仪,确保其精度和准确性。
步骤二:选择合适的工具1.根据加工要求和工件材料选择合适的刀具。
2.安装刀具并使用手动螺丝刀进行固定。
步骤三:调整刀具位置和高度1.打开数控车床的控制系统,并进入对刀模式。
2.使用对刀仪在工件表面上进行测量,确定刀具的位置和高度。
3.根据测量结果进行调整,使刀具与工件表面接触但不产生过多压力。
步骤四:校准坐标系1.在数控车床的控制系统中,选择校准坐标系的选项。
2.根据机床的实际情况和加工要求,选择合适的校准方式。
3.按照系统提示进行操作,完成坐标系的校准。
步骤五:测试加工1.将加工程序加载到数控车床的控制系统中。
2.进行空运行测试,确保刀具和工件没有碰撞或其他异常情况。
3.调整加工参数和切削条件,以达到理想的加工效果。
步骤六:完成对刀1.确认对刀完成后,关闭对刀模式并保存相关设置。
2.将工件固定在数控车床上,并开始正式的加工过程。
4. 注意事项在进行数控车床的对刀过程中,需要注意以下事项:•安全第一:在操作过程中要注意保护自己和他人的安全,避免发生意外事故。
•仔细测量:对刀仪的测量结果将直接影响加工的精度和质量,因此要仔细进行测量。
•切勿强力碰撞:刀具和工件之间不应产生过大的压力,以免损坏刀具或工件。
•校准坐标系:正确校准坐标系可以确保加工程序的准确性和一致性。
数控机床对刀

(7)将光标移动至欲设定的偏置号处。
(8)输入Zβ(或0)。
(9)按软键[MESURE]。
(10)在手动方式中用一把实际刀具切削外圆。
(11)仅仅在Z方向上退刀,不要移动X,停止主轴。
(12)测量被车削部分的直径D。
(13)按功能键OFFSET/SETING。
(14)按软键[OFFSET]。
实习总结:
用试切法确定起刀点的位置对刀的步骤:
(1)在MDI或手动方式下,用基准刀切削工件端面;
(2)用点动移动X轴使刀具试切该端面,然后刀具沿X轴方向退出,停主轴。
记录该Z轴坐标值并输入系统。
(3)用基准刀切量工件外径。
(4)用点动移动Z轴使刀具切该工件的外圆表面,然后刀具沿Z方向退出,停主轴。用游表卡尺测量工件的直径,记录该X坐标值并输入系统。
(3)对刀点与对刀:对刀点是用来确定刀具与工件的相对位置关系的点,是确定工件坐标系与机床坐标系的关系的点。
对刀就是将刀具的刀位点置于对刀点上,以便建立工件坐标系。
(4)对刀基准(点):对刀时为确定对刀点的位置所依据的基准,该基可以是点、线、面,它可以设在工件上或夹具上或机床上。
(5)对刀参考点:是用来代表刀架、刀台或刀盘在机床坐标系内的位置的参考点,也称刀架中心或刀具参考点。
(5)对第二把刀,让刀架退离工件足够的地方,选择刀具号,重复(1)—(4)步骤。
法拉克车床对刀:
基准刀的对法:
(1)在手动方式中用一把实际刀具切削端面。
(2)仅仅在X轴方向上退刀,不要移动Z轴,停止主轴。
(3)测量工件坐标系的零点至端面的距离β(或0)。
(4)按功能键OFFSET/SETING。
(5)按软键[OFFSET]。
数控车床对刀的原理与方法

数控车床对刀的原理与方法数控车床的刀具对刀是确保机床工作精度的关键步骤之一、对刀准确度影响着工件的加工精度和质量。
数控车床的对刀一般采用刀具测量、感应式对刀、比较式对刀等方式。
下面将介绍数控车床对刀的原理和方法。
1.刀具测量:数控车床通常提供一个专门的测量装置,用来测量刀具的长度和半径。
通过刀具测量装置的读数,可以计算出刀具的几何参数,以便在数控系统中设置正确的刀具补偿值。
2.感应式对刀:数控车床使用感应式传感器,通过与刀具接触或靠近刀具来感应刀具的位置信息。
传感器可以测量到刀具的长度和半径,并将这些信息传递给数控系统。
3.比较式对刀:比较式对刀是通过测量工件上已加工的特征来确定刀具的位置。
例如,在数控车床上面加工一个规定尺寸的槽后,可以使用传感器测量槽的尺寸,然后根据预定的槽尺寸,调整刀具的位置。
根据数控车床对刀的原理,可以采用以下方法进行对刀:1.感应式对刀:数控车床上通常有一个专用的感应式对刀装置。
在对刀过程中,需要选取一把已知长度的刀具,并使用感应式传感器测量其长度。
将测量到的刀具长度输入数控系统,系统会自动计算并设置刀具长度补偿值。
然后,将正确长度的刀具安装到车刀刀架上,依次对各个刀具进行对刀。
2.刀具测量:刀具测量是比较常见的对刀方式。
使用专用的刀具测量设备可以测量刀具的长度和半径。
在对刀过程中,首先选取一把已知长度和半径的刀具,将其放入测量设备中测量。
然后,将测量到的数值输入数控系统,系统会自动计算出刀具的补偿值。
最后,将已校准好的刀具安装到车刀刀架上。
3.比较式对刀:在比较式对刀中,首先需要加工一个已知尺寸的特征,例如一条槽或一组孔。
然后,使用专用的测量仪器测量加工后的特征尺寸。
将测量到的尺寸和预定的尺寸进行比较,计算出相应的补偿值。
最后,根据计算结果调整刀具的位置。
除了上述方法外,还可以使用图形化的数控系统来辅助进行对刀。
通过在数控系统中显示工件轮廓的模拟图像,可以直观地观察刀具的位置与工件轮廓之间的关系,从而调整刀具的位置。
数控车床自动对刀装置系统设计

整个装置安装在一个 T型支撑架上 , 支撑架 固定在主轴
箱体上。
2 对刀 装置测 头 部分
本装置的检测部分 主要 包括 测头结 构 和对刀 程序 两个
图 3 对 刀路 线
方面。测头方面主要 是在 Y轴 传感 器 上 , 使其 和 X轴有 一
定夹角 , 而不 是与 x轴垂直 , 使得 对刀 仪具有更 好 的适 用
联接传感器I
联 接传 感器2 联接传感器3
Z 1 0 0
Z1 0 o
N 0 0 0 4
N o o O 5
Z 1 0 0 Z1
U1
N 0 o O 6 N0 o O 7
N 0 o O 8 NO 0 O 9 N 0 0l 0
服电机从 而达 到预定方案 , 进而提高 了定位精 度。考 虑到刀
架 的控 制要求达到 需运动路线 即可 , 其运动精 度对 数控对 刀的总体 精度影 响不 高 , 所 以本 部分 采用 数控 机 床的 C N C 系统控制 刀架 的对刀路线 ( 如图 3 ) 。
圈 1 对 刀装 置 示 意 图
传感器使用开关信号 , 让控制 电路 简单 便维护 。对刀 程
序完全调用系统的函数 和指令 , 让对 刀程序 更加 灵 活 , 可 经
过简单修改而适应 不同系统的车床 。
3 对 刀装 置控 制 系统 部 分
控制系统包括 对刀架在 对刀过 程 中的运 动路线 控制及
来进行 中间传 动使 装置传动平稳 , 放大转矩 使电机的结构 更 小, 具体尺寸见整个装 置的尺 寸 , 并 且选 用带 自锁 的蜗轮 蜗
No o1 1
Z 3 0
X8 9 X1 0 0 MO 6 X1 0 o
数控车床的几种精确对刀方法
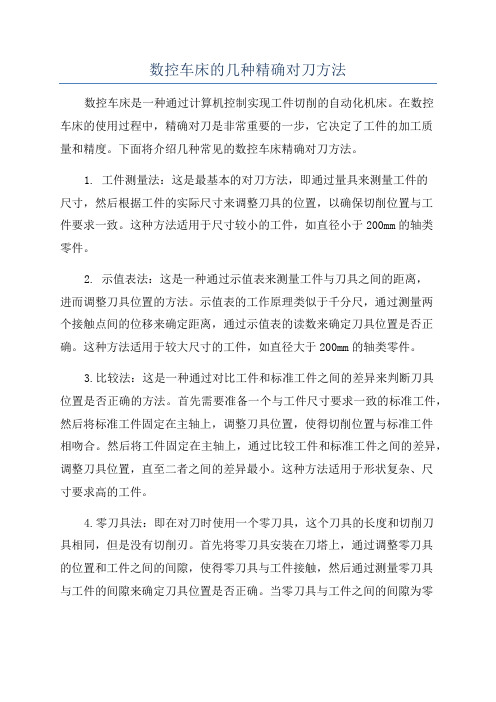
数控车床的几种精确对刀方法数控车床是一种通过计算机控制实现工件切削的自动化机床。
在数控车床的使用过程中,精确对刀是非常重要的一步,它决定了工件的加工质量和精度。
下面将介绍几种常见的数控车床精确对刀方法。
1. 工件测量法:这是最基本的对刀方法,即通过量具来测量工件的尺寸,然后根据工件的实际尺寸来调整刀具的位置,以确保切削位置与工件要求一致。
这种方法适用于尺寸较小的工件,如直径小于200mm的轴类零件。
2. 示值表法:这是一种通过示值表来测量工件与刀具之间的距离,进而调整刀具位置的方法。
示值表的工作原理类似于千分尺,通过测量两个接触点间的位移来确定距离,通过示值表的读数来确定刀具位置是否正确。
这种方法适用于较大尺寸的工件,如直径大于200mm的轴类零件。
3.比较法:这是一种通过对比工件和标准工件之间的差异来判断刀具位置是否正确的方法。
首先需要准备一个与工件尺寸要求一致的标准工件,然后将标准工件固定在主轴上,调整刀具位置,使得切削位置与标准工件相吻合。
然后将工件固定在主轴上,通过比较工件和标准工件之间的差异,调整刀具位置,直至二者之间的差异最小。
这种方法适用于形状复杂、尺寸要求高的工件。
4.零刀具法:即在对刀时使用一个零刀具,这个刀具的长度和切削刀具相同,但是没有切削刃。
首先将零刀具安装在刀塔上,通过调整零刀具的位置和工件之间的间隙,使得零刀具与工件接触,然后通过测量零刀具与工件的间隙来确定刀具位置是否正确。
当零刀具与工件之间的间隙为零时,即可确定刀具位置正确。
这种方法适用于切削刀具无法直接测量的情况下,如刀具形状复杂或刀具长度超过测量仪器范围的情况。
需要注意的是,对于数控车床的精确对刀方法,不同的机床可能会有不同的要求和适用范围,具体的对刀方法应根据机床的实际情况和工件要求来选择。
在对刀过程中,还需要注意对刀时机床的静止状态、对刀速度和对刀力度的控制,以确保对刀的准确性和稳定性。
此外,对于精度要求较高的工件,还可以采用自动对刀装置、光学对刀仪等专用设备来实现更精确的对刀。
经济型数控车床的快速对刀

对 刀结 束。
一 对刀时应注意问题
① 安 装 刀 具 时 . 若 有 空 刀 位 . 则 此 刀 位 之 前
或 之 后 那 把 刀 需 连 续 对 两 次 . 因 为 对 刀 软 件 是 按
大 缩 短 了 对 刀 时 问 。 由 于 采 用 了 电 信 号 位 置 检 测
法 . 使 对 刀 误 差 控 制 在 一 步 之 内 ,从 而 提 高 了 对 刀精 度 。
把 刀 的 刀 补 值 , 并 将 该 差 值 进 往 引 导 程 序 %0 . 中
以 便 加 工 时 使 用 。 刀 补 值 的 计 算 是 以 第 一 把 刀 对
刀 后 返 回 的 位 置 作 为 基 本 设 定 点 , 其 他 刀 具 均 以
第 一 把 刀 具 的 刀 尖 为 基 准 .对 刀 后 得 到 各 刀 具 与 第 一 把 刀 之 间 的 相 对 偏 差 。 在 执 行 零 件 加 工 程 序
机 ( 2 图 ), 计 算 机 立 即 控 制 刀 具 后 退 至 一 固 定 位
置 . 该 位 置 印 刀 尖 位 置 一 般 不 同 于 第 一 把 刀 具 , 对 刀 后 , 刀
尖 返 回 到 出 发 点 , 这 时 计 算 机 自动 计 算 出 该 刀 具
皿
对刀原理
回 ∞/ 22 3
维普资讯
时 . 如 果 遇 到 换 刀 命 令 , 在 换 刀 后 , 系 统 会 自 动 取 出 相 应 刀 具 的 偏 差 进 行 补 偿 。 选 样 编 制 加 工 程 序时 , 一 个 出 发 点 进 行 缩 程 , 而 不 需 考 虑 几 把 刀 有 不 同 的 起 始 点 , 从 而 简 化 了 编 程 工 作 . 并 大
- 1、下载文档前请自行甄别文档内容的完整性,平台不提供额外的编辑、内容补充、找答案等附加服务。
- 2、"仅部分预览"的文档,不可在线预览部分如存在完整性等问题,可反馈申请退款(可完整预览的文档不适用该条件!)。
- 3、如文档侵犯您的权益,请联系客服反馈,我们会尽快为您处理(人工客服工作时间:9:00-18:30)。
经济型数控车床自动对刀的设计与实现摘要:为了解决经济型数控车床存在的对刀问题,本文借助于一对刀模块,设计了一种自动对刀方法。
理论和实验结果表明,该对刀方法,不仅提高了对刀精度和效率,而且具有快速、准确、一致性好和使用方便等优点。
关键词:对刀模块自动对刀精度效率一致性
中图分类号:tg5 文献标识码:a 文章编号:1672-3791(2012)11(a)-0067-01
目前经济型数控车床对刀一般大都采用机械对刀仪、光学对刀仪、试切法等机械方法对刀,普遍存在以下缺点:一是要依靠人工来测定刀尖的位置,工作可靠性不高,效率低;二是由于操作者技术水平不同,对刀精度一致性差。
为此本文设计了一种新型的自动对刀方法,较好地解决了上述问题。
1 自动对刀的设计与实现
1.1 自动对刀的工作原理
自动对刀是借助于一对刀模块,在相应的对刀程序控制下自动实现对刀。
1.2 自动对刀的程序设计(如图1)
在设计对刀程序时,首先设定了第一把刀的刀尖基准位置点t1。
对刀时,首先通过点动按钮把第一把刀移到对刀模块的附近,假定为图中的a点。
程序控制工作过程有以下几点。
(1)从a点开始,x向步进电机动作,刀架沿一x向进给,同
时步进电机每进给一步,对刀程序不断检测有无“基准位置”信号。
若无,继续上述动作。
若有,立即停止刀架运动,假设此时的刀具与对刀模块的接触点为图中的b点。
在此运动过程中,由于刀架的进给速度较慢,惯量小,因此能立即停止刀架的运动,而不损坏刀具。
(2)从对刀模块接触点b开始,让刀架快速沿十x向退回一设定的距离x0,此时刀尖到达图中的c点,即bc=x0,停止刀架的运动。
(3)从c点开始,z向电机动作,刀架沿一z向运动,同时电机每进给一步,对刀程序不断检测有无“基准位置”信号。
若无,继续上述动作。
若有立即停止刀架运动,假定此时刀具与对刀模块的接触点为图中的d点。
(4)从d点开始,让刀架沿+z向快速退回一设定的距离z0,此时到达图1中的t1点,即dt1=z0。
综上所示,对刀程序自动设定了第一把刀的刀尖基准位置点t1。
由于各把刀是装在同一刀架上,其拖板的运动是一致的,若将第一把刀的工作过程来定第二把刀,势必导致破坏第一把刀的基准位置。
为了解决此问题,采用了下述的工作过程,既能保持第一把刀的基准位置,又能检测它们之间的相对位置差值。
这里以第二把刀为例来说明其工作过程。
首先通过调用自动回转刀架子程序,把第二把刀换到前面来,假定此时的第二把刀的刀尖位置点为图1中的t2点。
只要能够测
出t2点的坐标值,就可得到第二把刀与第一把刀的相对位置的偏差δx和δz的大小与方向。
程序控制的工作过程如下。
(1)从t2点开始,让刀架沿—x向运动,步进电机每进给一步,计数器计数一次,同对刀程序不断检测有无“基准位置”信号。
若无,继续上述动作。
若有,立即停止刀架的运动,同时计数器的计数工作停止。
假设此时的刀具与对刀模块的接触点为图示的e点,此时的计数器内容即为t2e这段距离。
(2)从e点开始,刀架沿+x向快速退回ft2这段距离,即ft2=x0,到达图中的f 点。
接着把第一把刀的基准位置x向坐标值x0与计数器记录的距离t2e相减,则得到第二把刀相对于第一把刀的相对位置偏差δx的大小与方向,并存贮在相应的刀具补偿存贮单元中。
(3)从f点开始,z向电机动作,刀架沿—z向运动,电机每进给一步,计数器计数一次,同时对刀程序不断检测有无“基准位置”信号。
若无,继续上述动作。
若有立即停止刀架运动,同时计数器的计数工作停止。
假定此时的刀具与模块的接触点为图示的d 点,计数器的内容即为fd这段距离。
(4)从d点开始,让刀架沿+z向快速退回计数器记录的距离fd,刀尖重新回到f点。
接着把第一把刀的基准位置z向坐标值z0与第二把刀的计数器记录的距离fd相减,则得到第二把刀相对于第一把刀的相对位置偏差δz的大小与方向,并存贮在相应的刀具补偿存贮单元中。
(5)从f点开始,刀架沿+x向快速退回ft2这段距离,即ft2=
δx,到达图中的t2 点,使刀架重新回到原位。
综上所述,对刀程序自动测出了第二把刀相对于第一把刀的相对位置偏差δx和δz的大小和方向,并存放于相应地刀具补偿单元中。
2 对刀精度及其实验分析
从上述的对刀控制程序可知,首先设定了第一把刀的基准位置,其它各把刀采用“步进计数”的方法即步进电机每进给一步,计数器计数一次,同时对刀程序不断检测有无“基准位置”信号,一旦检测到此信号,立即停止刀架的运动,同时计数器的计数工作也停止,此时的计数器记录的距离与第一把刀设定的距离相差,则可求出其偏差的大小和方向。
因此从理论上说,电接触法自动对刀的对刀精度应该不大于1个脉冲当量,为了验证理论的正确性,作了如下的实验,并进行了分析。
对自动对刀方法的重复测量次数和偏差值。
以x向步进计数来说明,其电机的脉冲当量为0.005 mm/步。
对z向步进计数与此相同,在此省略。
从中可知,重复测量时,数值变化不大,只有1个脉冲差值(0.005 mm),符合理论要求,而且一致性较好。
最后我们再用试切工件的方法测得第二把刀相对第一把刀的横向偏差δx 为2.99 mm,而用自动对刀方法测出的偏差也为2.99 mm,由此可知,自动对刀方法是可行的,符合实际情况。
此外,自动对刀方法测出四把刀的偏差只要3 min时间,而普通的试切工件的方法大约要30 min时间。
综上所述,本文设计的自动对刀方法,较好地解决了对刀精度和效率问题,具有快速、准确、一致性好和使用方便等优点,可适用于切削机床的各种刀具,如右偏刀、切槽刀、切断刀、内孔车刀、螺纹刀等,对装刀时各把刀的相对位置无要求,具有广泛的适用性。
参考文献
[1] 罗敏.双刀架曲轴数控车床自动对刀程序设计[j].制造
技术与机床,2010(5):27-30.
[2] 黄炳辉.浅析普通车床中自动对刀仪相关技术问题[j].
中国现代教育装备,2010(9):69-71.。