[038]-电动套丝机的切削液的油路构造
电动套丝机套丝失败原因分析与处理

163前言一般现场使用较多规格为DN15,DN20和DN25的镀锌管材,主要进行的操作有切割和管外螺纹套制。
这里仅就电动套丝机在套丝过程中出现的一些常见问题,进行简要的分析。
套丝过程中,按照操作规程装好所需规格扳牙,夹持好管段,当套丝盘A线对正锁紧固定后,扳牙齿所形成的环形切削空间的大小就固定了,在电机带动管子以定速旋转时,套丝盘通过滑架手轮以一定的轴向进给,使扳牙齿对管端部进行切削,形成一段锥度为1:16的管螺纹。
在实际操作过程中,会出现一些异常情况,使套出的螺纹不合格。
一、电动套丝机 这主要表现如下:1.螺纹偏大或小,与标准件合扣,仅能进1-2两扣,或是配合过松,几乎能合到5-6扣。
形成这种现象的主要原因有:管子外径不合格,导致切削量变化,套丝后从外观上看,就表现出与正常情况下不一样的螺纹深度。
扳牙牙齿磨损,导致切削深度不够。
A线未对齐,会导致螺纹偏大或小;或套丝盘手柄螺母未锁紧,在套丝过程中因振动和受力使管径刻度移位,加工出的螺纹会偏大。
套丝盘滚轮与仿形块接触后没有锁定到位。
加工过程中,未锁定的套丝盘向上移位,切削口径扩大,也会导致螺纹偏大。
2.烂扣,断丝现象。
这会导致有密封要求的螺纹连接出现密封不严,或是连接强度变低。
按标准要求,一般出现烂扣或断丝的长度不得超过螺纹总长度的10%。
造成此种现象可能有以下原因:(1)扳牙质量差,编号混用或错装,或是牙齿有损坏。
(2)切削过程中缺少切削液循环,切削过程摩擦大,热量未及时带走,残渣在刀具处堆积阻塞,极易形成烂扣和断丝现象,管材材质较差,管材不同的屈服强度、塑性变形参数,会影响螺纹的成形质量。
(3)扳牙上有残留的铁屑,会使螺纹受到损伤,出现烂扣或断丝的现象。
二、套丝不进扣,或前端圆秃,呈和尚头状套丝不进,就是套丝盘在管子端部停留旋转,轴向进给没有跟上。
管子端口部位被 重复切屑,形成光秃状。
可能由于:1.扳牙入口端牙齿磨损,套丝时较难形成初始段螺纹。
切削液冷却结构

切削液冷却结构切削液冷却结构是一种用于机床加工过程中的冷却装置,主要用于降低切削过程中的摩擦温度,保护工件和刀具,提高加工效率和质量。
下面将从切削液冷却的原理、切削液冷却结构的种类以及其应用领域等方面进行介绍。
一、切削液冷却的原理切削液冷却是利用切削液在切削过程中吸热的特性来降低温度的一种方法。
在切削过程中,切削液通过喷射、浸润和润滑等方式,将切削区域的热量带走,起到冷却和润滑的作用。
切削液冷却可以有效降低切削过程中的摩擦温度,减少刀具磨损和工件变形,提高切削性能和加工效率。
二、切削液冷却结构的种类1. 冷却液喷射结构:冷却液通过喷嘴喷射到切削区域,形成冷却液气雾,使切削液能够充分接触工件和刀具,提供充足的冷却效果。
这种结构适用于高速切削和高温切削,可以快速散热,有效降低切削温度。
2. 冷却液浸润结构:冷却液通过管道引导到切削区域,形成冷却液薄膜,使切削液能够均匀润滑刀具和工件表面,降低摩擦系数,减少磨损和热量积累。
这种结构适用于微小切削和高精度加工,可以提高加工质量和表面粗糙度。
3. 冷却液润滑结构:冷却液通过润滑系统输送到切削区域,形成冷却液薄膜,起到润滑和冷却的作用。
这种结构适用于大型切削和重载切削,可以减少切削力和磨损,延长刀具寿命。
三、切削液冷却结构的应用领域切削液冷却结构广泛应用于各种机床和加工设备中,主要用于金属切削加工、车削加工、铣削加工、钻削加工等工艺过程。
切削液冷却结构可以提高工件表面质量,减少加工残留应力,提高切削性能和加工效率。
在高速切削、高温切削、重载切削和高精度加工等场合,切削液冷却结构更加重要,能够有效降低温度、延长刀具寿命、提高加工质量。
切削液冷却结构在机床加工中起到至关重要的作用。
通过切削液冷却结构,可以降低切削温度,减少刀具磨损和工件变形,提高加工效率和质量。
在不同的加工场合,选择合适的切削液冷却结构,可以达到最佳的加工效果。
因此,对于机床加工领域来说,切削液冷却结构是一个不可或缺的重要组成部分。
双线集中润滑系统结构组成与润滑工作原理

双线集中润滑系统结构组成与润滑工作原理
双线集中润滑系统是一种常用的润滑系统,该系统通过高压油管将润滑油分送到不同的润滑点,以保证设备在使用过程中的润滑效果和寿命。
其结构和工作原理如下:
1. 结构组成
双线集中润滑系统由润滑泵、高压油管、润滑器、加油嘴和润滑点等组成。
润滑泵是系统的核心组成部分,主要由电机、齿轮泵、压力调节器、滤芯和润滑油箱等组成。
高压油管则通过联轴器将润滑泵与润滑器相连接,润滑器则用于过滤润滑油,加油嘴则用于将润滑油输送到润滑点。
2. 工作原理
润滑泵将润滑油从油箱中吸入,并将其压缩并输送至高压油管中,高压油管再将润滑油输送至润滑器。
通过滤芯的过滤作用,润滑油的杂质将被过滤掉,将清洁的润滑油再次输送到高压油管中。
高压油管将润滑油分送到各个加油嘴处,通过加油嘴的分配,润滑点可以得到均等的润滑。
总之,双线集中润滑系统可靠且耐用,大大提高了设备的使用寿命。
切丝机原理及结构(尹文刚)

点击控制触摸屏主界面上的“设臵”按钮打开“参数 设臵”对话框,在“切丝宽度” 一栏中的输入切丝宽度(可 输入范围3~30,单位0.01mm)。当切丝宽度实际值与显示 值有误差时,可使用主界面上的“切丝宽度微调” 一栏中的 三角按钮进行修正,修正程度取值范围-400~十400
一、切丝机开机前检查工作 1.液压(气压)系统的检查 2.料仓的检查 3.刀门装置的检查 4.进刀系统的检査 5.砂轮修整器的检查 6.磨刀系统的检查
切丝机刀门装臵包括;上刀门、上刀门座、上刀门盖板、 左右侧刀门、下刀门座、下刀门及下刀门盖板等
对刀门装置的检查有以下几个方面: (1)检查各刀门是否磨损:
(2)检查上刀门升降是否顺利 (3)检査下刀门是否下沉
(1)碟型弹簧的检查。
(2)刀片寿命的检查
刀片的使用寿命取决于刀片的进给量和刀辊的转速
3.技术要点
(1)流量均匀稳定,不超过设备的工艺制造能力, 供料均衡,铺料均匀不脱节, 刀门四角勿空松。 (2)刀门应平行,并与刀片平行,刀门与刀片间的 间隙调整适当。 (3)刀片材质、硬度和尺寸规格应均匀一致,磨刀 砂轮符合质量要求。正常运行 期间刀口应锋利,不卷 刃、不缺口。 (4)刀片进给系统应保持工作正常。 (5)刀门高度适当,压力调整适宜,正常工作时应 保证稳定。 (6)调整切丝机时不合格叶丝必须剔除。 (7)切丝宽度设定应充分考虑到对叶丝物理指标和 感官质量的影响。
《培训教材》
2013版
—尹文刚
切丝机的结构
1.喂料系统 2.机架 3.送料系统 4.刀门系统 5.刀辊系统
6.磨刀系统 7.液压(气压)系统 8.电控系统
喂料系统的作用是将上道工序送来的物料均匀地送入切 丝机送料系统的料仓内,确保切丝机连续供料,同时将物料 初步压实。 切丝机喂料系统分为垂直喂料和水平喂料两种方式。
简述润滑系统的原理与组成
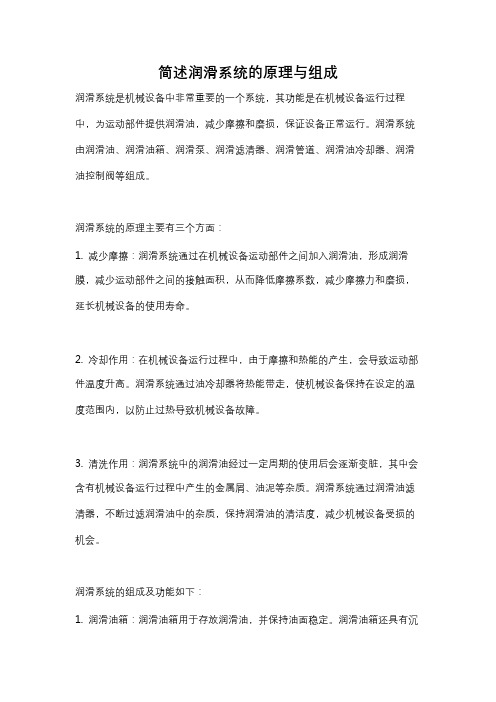
简述润滑系统的原理与组成润滑系统是机械设备中非常重要的一个系统,其功能是在机械设备运行过程中,为运动部件提供润滑油,减少摩擦和磨损,保证设备正常运行。
润滑系统由润滑油、润滑油箱、润滑泵、润滑滤清器、润滑管道、润滑油冷却器、润滑油控制阀等组成。
润滑系统的原理主要有三个方面:1. 减少摩擦:润滑系统通过在机械设备运动部件之间加入润滑油,形成润滑膜,减少运动部件之间的接触面积,从而降低摩擦系数,减少摩擦力和磨损,延长机械设备的使用寿命。
2. 冷却作用:在机械设备运行过程中,由于摩擦和热能的产生,会导致运动部件温度升高。
润滑系统通过油冷却器将热能带走,使机械设备保持在设定的温度范围内,以防止过热导致机械设备故障。
3. 清洗作用:润滑系统中的润滑油经过一定周期的使用后会逐渐变脏,其中会含有机械设备运行过程中产生的金属屑、油泥等杂质。
润滑系统通过润滑油滤清器,不断过滤润滑油中的杂质,保持润滑油的清洁度,减少机械设备受损的机会。
润滑系统的组成及功能如下:1. 润滑油箱:润滑油箱用于存放润滑油,并保持油面稳定。
润滑油箱还具有沉淀和分离润滑油中的杂质的功能。
2. 润滑泵:润滑泵是润滑系统中的核心设备,它的主要功能是将润滑油从润滑油箱中抽取,并通过压力输送到机械设备中的运动部件。
润滑泵的工作原理是利用压力差将润滑油抽出并输送。
3. 润滑滤清器:润滑滤清器用于过滤润滑油中的杂质,以保持润滑油的清洁度。
润滑滤清器通常采用网式过滤或滤芯式过滤。
网式过滤器通过网孔的大小来过滤杂质,而滤芯式过滤器则利用滤芯来捕捉杂质。
4. 润滑管道:润滑管道是将润滑油从润滑泵输送到机械设备中的运动部件的管道系统。
润滑管道需要保持畅通,以确保润滑油能够顺利地达到运动部件。
5. 润滑油冷却器:润滑油冷却器用于降低润滑油的温度,防止润滑油因温度过高而失去润滑效果,保持润滑油在适宜的温度范围内工作。
润滑油冷却器可以采用空气冷却或水冷却的方式。
6. 润滑油控制阀:润滑油控制阀用于控制润滑油的流量和压力。
切削液闭循环系统_解释说明以及概述
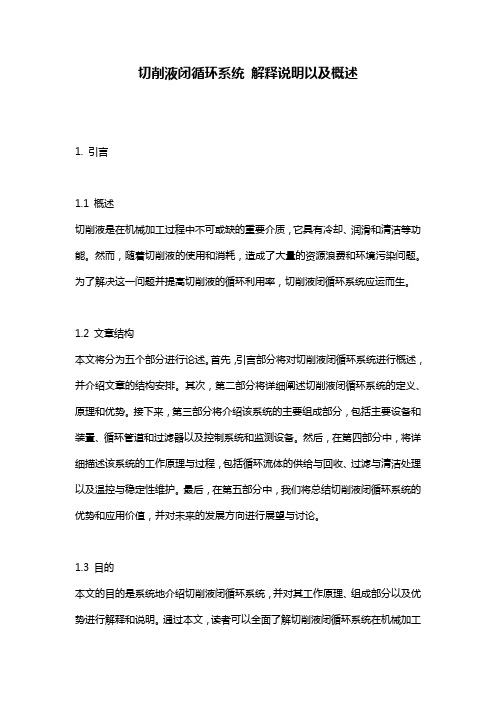
切削液闭循环系统解释说明以及概述1. 引言1.1 概述切削液是在机械加工过程中不可或缺的重要介质,它具有冷却、润滑和清洁等功能。
然而,随着切削液的使用和消耗,造成了大量的资源浪费和环境污染问题。
为了解决这一问题并提高切削液的循环利用率,切削液闭循环系统应运而生。
1.2 文章结构本文将分为五个部分进行论述。
首先,引言部分将对切削液闭循环系统进行概述,并介绍文章的结构安排。
其次,第二部分将详细阐述切削液闭循环系统的定义、原理和优势。
接下来,第三部分将介绍该系统的主要组成部分,包括主要设备和装置、循环管道和过滤器以及控制系统和监测设备。
然后,在第四部分中,将详细描述该系统的工作原理与过程,包括循环流体的供给与回收、过滤与清洁处理以及温控与稳定性维护。
最后,在第五部分中,我们将总结切削液闭循环系统的优势和应用价值,并对未来的发展方向进行展望与讨论。
1.3 目的本文的目的是系统地介绍切削液闭循环系统,并对其工作原理、组成部分以及优势进行解释和说明。
通过本文,读者可以全面了解切削液闭循环系统在机械加工中的作用,以及其对资源节约和环境保护所带来的积极影响。
此外,本文还将为未来该技术的进一步发展提供一定的参考和展望。
2. 切削液闭循环系统2.1 切削液闭循环系统的定义切削液闭循环系统是一种用于金属加工过程中的切削液管理系统。
它通过将切削液回收、再利用,并进行适当的处理与控制,来提高生产效率、降低生产成本以及减少对环境的污染。
2.2 切削液闭循环系统的原理切削液闭循环系统基于封闭回路的原理,主要包括供给和回收两个主要过程。
在供给过程中,新鲜的切削液被输送到加工设备中,用于冷却和润滑加工表面。
在加工过程中,切削液会受到污染和氧化等因素影响而变质。
因此,在回收过程中,经过过滤和清洁处理后,被回收的切削液将继续被使用。
2.3 切削液闭循环系统的优势- 资源节约:通过回收和再利用切削液,可以大大减少对资源(如水、冷却油等)的消耗。
电动套丝机的工作原理
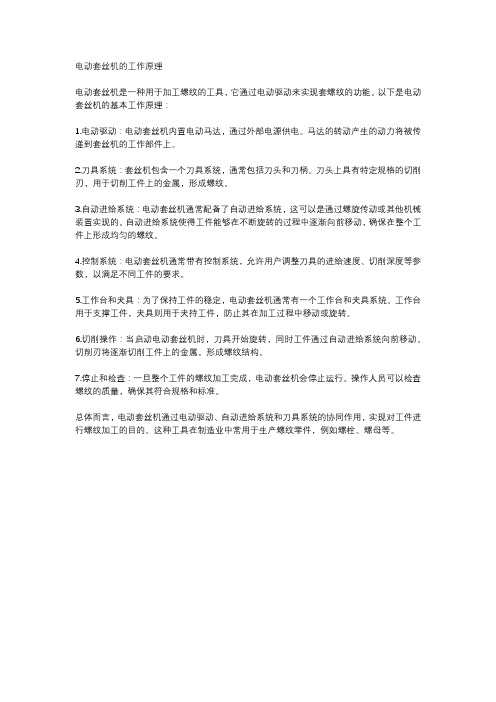
电动套丝机的工作原理
电动套丝机是一种用于加工螺纹的工具,它通过电动驱动来实现套螺纹的功能。
以下是电动套丝机的基本工作原理:
1.电动驱动:电动套丝机内置电动马达,通过外部电源供电。
马达的转动产生的动力将被传递到套丝机的工作部件上。
2.刀具系统:套丝机包含一个刀具系统,通常包括刀头和刀柄。
刀头上具有特定规格的切削刃,用于切削工件上的金属,形成螺纹。
3.自动进给系统:电动套丝机通常配备了自动进给系统,这可以是通过螺旋传动或其他机械装置实现的。
自动进给系统使得工件能够在不断旋转的过程中逐渐向前移动,确保在整个工件上形成均匀的螺纹。
4.控制系统:电动套丝机通常带有控制系统,允许用户调整刀具的进给速度、切削深度等参数,以满足不同工件的要求。
5.工作台和夹具:为了保持工件的稳定,电动套丝机通常有一个工作台和夹具系统。
工作台用于支撑工件,夹具则用于夹持工件,防止其在加工过程中移动或旋转。
6.切削操作:当启动电动套丝机时,刀具开始旋转,同时工件通过自动进给系统向前移动。
切削刃将逐渐切削工件上的金属,形成螺纹结构。
7.停止和检查:一旦整个工件的螺纹加工完成,电动套丝机会停止运行。
操作人员可以检查螺纹的质量,确保其符合规格和标准。
总体而言,电动套丝机通过电动驱动、自动进给系统和刀具系统的协同作用,实现对工件进行螺纹加工的目的。
这种工具在制造业中常用于生产螺纹零件,例如螺栓、螺母等。
车床主轴电动机润滑油泵电动机控制电路

摘要机床电气控制线路设计是高职机械专业学生学完大学的课程后进行的,学生已经掌握了机械制造、机械加工的一些基本技能,从事机床电气控制线路的设计是对以前所学电气知识的综合回顾和复习,以后对各种机床控制电路都可触类旁通,能自己动手设计和改进相应电路,也能排除相关电气故障。
主轴机必须在油泵开动后才能开动。
主轴机实现正反转,并采用定子绕组串电阻降压起动,由速度继电器完成起动到运行的过渡。
停车时,必须主轴机先停机,然后油泵机才能停机。
可以两台电动机同时停机。
任何一台过载,两台电动机均停车。
有电路,零压,过载保护。
有照明及必要的灯光显示。
关键词CA6140 机床控制线路前言CA6140型普通车床目前多用于现代化大中型制造业的成批生产车间,更多应用于生产线上。
其有较好的生产率和一定的使用性能,可很方便地车削常用的公制螺纹。
此外,其比万能型车床有较好的刚度和抗振性,能适应现代刀具发展的高速切削和强力切削。
同时,该机床还结构简单,便于工人操作,另外又可在其上方便地安装附件或自动化装置,从而实现自动或半自动车削。
普通车床靠齿轮和普通丝杠螺母传动。
由于各运动副间存在间隙,加上手工操作不准确因此重复精度较低。
普通车床测量时需停车后手工测量,测量误差较大,而且效率低下,。
适合批量较小,精度要求不高,零活类零件。
它投资较数控低,但对工人的操作技能要求较高,因此工资水平高。
低水平工人的废品率和生产率会让你头疼。
数控车床靠步进电机带动滚珠丝杠传动,由于滚珠丝杠可以有过盈量,传动无间隙,精度主要靠机床本身和程序保证。
在加工过程中可以自动测量,并能自动补偿刀具磨损及其他原因产生的误差。
所以加工质量好,精度稳定。
还可以用编程的方法车出形状复杂,普通车床难以加工的零件。
适合精度高,批量大,形状复杂的零件。
但小批量生产也很好用。
它的维修费用较普通车床高。
立车主要用于大件,它的主轴是垂直的。
立车也有数控的。
由于高技术水平的人才越来越缺,现在新上的企业多采用数控,以提高生产率和产品质量,降低废品率和成本。