An Integrated Simulation System for Human Factors Study
外文文献文献列表
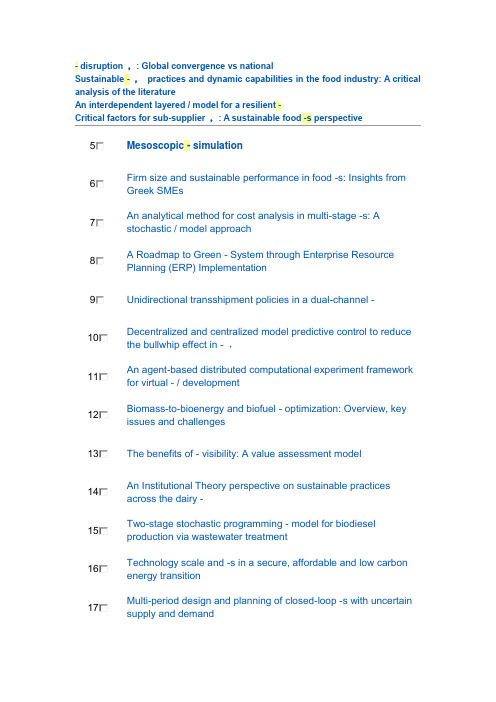
- disruption ,: Global convergence vs nationalSustainable - ,practices and dynamic capabilities in the food industry: A critical analysis of the literature5 Mesoscopic - simulation6 Firm size and sustainable performance in food -s: Insights from Greek SMEs7 An analytical method for cost analysis in multi-stage -s: A stochastic / model approach8 A Roadmap to Green - System through Enterprise Resource Planning (ERP) Implementation9 Unidirectional transshipment policies in a dual-channel -10 Decentralized and centralized model predictive control to reduce the bullwhip effect in - ,11 An agent-based distributed computational experiment framework for virtual - / development12 Biomass-to-bioenergy and biofuel - optimization: Overview, key issues and challenges13 The benefits of - visibility: A value assessment model14 An Institutional Theory perspective on sustainable practices across the dairy -15 Two-stage stochastic programming - model for biodiesel production via wastewater treatment16 Technology scale and -s in a secure, affordable and low carbon energy transition17 Multi-period design and planning of closed-loop -s with uncertain supply and demand18 Quality control in food - ,: An analytical model and case study of the adulterated milk incident in China19 - information capabilities and performance outcomes: An empirical study of Korean steel suppliers20 A game-based approach towards facilitating decision making for perishable products: An example of blood -21 - design under quality disruptions and tainted materials delivery22 A two-level replenishment frequency model for TOC - replenishment systems under capacity constraint23 - dynamics and the ―cross-border effect‖: The U.S.–Mexican border’s case24 Designing a new - for competition against an existing -25 Universal supplier selection via multi-dimensional auction mechanisms for two-way competition in oligopoly market of -26 Using TODIM to evaluate green - practices under uncertainty27 - downsizing under bankruptcy: A robust optimization approach28 Coordination mechanism for a deteriorating item in a two-level - system29 An accelerated Benders decomposition algorithm for sustainable - / design under uncertainty: A case study of medical needle and syringe -30 Bullwhip Effect Study in a Constrained -31 Two-echelon multiple-vehicle location–routing problem with time windows for optimization of sustainable - / of perishable food32 Research on pricing and coordination strategy of green - under hybrid production mode33 Agent-system co-development in - research: Propositions and demonstrative findings34 Tactical ,for coordinated -s35 Photovoltaic - coordination with strategic consumers in China36 Coordinating supplier׳s reorder point: A coordination mechanism for -s with long supplier lead time37 Assessment and optimization of forest biomass -s from economic, social and environmental perspectives – A review of literature38 The effects of a trust mechanism on a dynamic - /39 Economic and environmental assessment of reusable plastic containers: A food catering - case study40 Competitive pricing and ordering decisions in a multiple-channel -41 Pricing in a - for auction bidding under information asymmetry42 Dynamic analysis of feasibility in ethanol - for biofuel production in Mexico43 The impact of partial information sharing in a two-echelon -44 Choice of - governance: Self-managing or outsourcing?45 Joint production and delivery lot sizing for a make-to-order producer–buyer - with transportation cost46 Hybrid algorithm for a vendor managed inventory system in a two-echelon -47 Traceability in a food -: Safety and quality perspectives48 Transferring and sharing exchange-rate risk in a risk-averse - of a multinational firm49 Analyzing the impacts of carbon regulatory mechanisms on supplier and mode selection decisions: An application to a biofuel -50 Product quality and return policy in a - under risk aversion of a supplier51 Mining logistics data to assure the quality in a sustainable food -: A case in the red wine industry52 Biomass - optimisation for Organosolv-based biorefineries53 Exact solutions to the - equations for arbitrary, time-dependent demands54 Designing a sustainable closed-loop - / based on triple bottom line approach: A comparison of metaheuristics hybridization techniques55 A study of the LCA based biofuel - multi-objective optimization model with multi-conversion paths in China56 A hybrid two-stock inventory control model for a reverse -57 Dynamics of judicial service -s58 Optimizing an integrated vendor-managed inventory system for a single-vendor two-buyer - with determining weighting factor for vendor׳s ordering59 Measuring - Resilience Using a Deterministic Modeling Approach60 A LCA Based Biofuel - Analysis Framework61 A neo-institutional perspective of -s and energy security: Bioenergy in the UK62 Modified penalty function method for optimal social welfare of electric power - with transmission constraints63 Optimization of blood - with shortened shelf lives and ABO compatibility64 Diversified firms on dynamical - cope with financial crisis better65 Securitization of energy -s in China66 Optimal design of the auto parts - for JIT operations: Sequential bifurcation factor screening and multi-response surface methodology67 Achieving sustainable -s through energy justice68 - agility: Securing performance for Chinese manufacturers69 Energy price risk and the sustainability of demand side -s70 Strategic and tactical mathematical programming models within the crude oil - context - A review71 An analysis of the structural complexity of - /s72 Business process re-design methodology to support - integration73 Could - technology improve food operators’ innovativeness? A developing country’s perspective74 RFID-enabled process reengineering of closed-loop -s in the healthcare industry of Singapore75 Order-Up-To policies in Information Exchange -s76 Robust design and operations of hydrocarbon biofuel - integrating with existing petroleum refineries considering unit cost objective77 Trade-offs in - transparency: the case of Nudie Jeans78 Healthcare - operations: Why are doctors reluctant to consolidate?79 Impact on the optimal design of bioethanol -s by a new European Commission proposal80 Managerial research on the pharmaceutical - – A critical review and some insights for future directions81 - performance evaluation with data envelopment analysis and balanced scorecard approach82 Integrated - design for commodity chemicals production via woody biomass fast pyrolysis and upgrading83 Governance of sustainable -s in the fast fashion industry84 Temperature ,for the quality assurance of a perishable food -85 Modeling of biomass-to-energy - operations: Applications, challenges and research directions86 Assessing Risk Factors in Collaborative - with the Analytic Hierarchy Process (AHP)87 Random / models and sensitivity algorithms for the analysis of ordering time and inventory state in multi-stage -s88 Information sharing and collaborative behaviors in enabling - performance: A social exchange perspective89 The coordinating contracts for a fuzzy - with effort and price dependent demand90 Criticality analysis and the -: Leveraging representational assurance91 Economic model predictive control for inventory ,in -s92 - ,ontology from an ontology engineering perspective93 Surplus division and investment incentives in -s: A biform-game analysis94 Biofuels for road transport: Analysing evolving -s in Sweden from an energy security perspective95 - ,executives in corporate upper echelons Original Research Article96 Sustainable - ,in the fast fashion industry: An analysis of corporate reports97 An improved method for managing catastrophic - disruptions98 The equilibrium of closed-loop - super/ with time-dependent parameters99 A bi-objective stochastic programming model for a centralized green - with deteriorating products100 Simultaneous control of vehicle routing and inventory for dynamic inbound -101 Environmental impacts of roundwood - options in Michigan: life-cycle assessment of harvest and transport stages102 A recovery mechanism for a two echelon - system under supply disruption103 Challenges and Competitiveness Indicators for the Sustainable Development of the - in Food Industry104 Is doing more doing better? The relationship between responsible - ,and corporate reputation105 Connecting product design, process and - decisions to strengthen global - capabilities106 A computational study for common / design in multi-commodity -s107 Optimal production and procurement decisions in a - with an option contract and partial backordering under uncertainties108 Methods to optimise the design and ,of biomass-for-bioenergy -s: A review109 Reverse - coordination by revenue sharing contract: A case for the personal computers industry110 SCOlog: A logic-based approach to analysing - operation dynamics111 Removing the blinders: A literature review on the potential of nanoscale technologies for the ,of -s112 Transition inertia due to competition in -s with remanufacturing and recycling: A systems dynamics mode113 Optimal design of advanced drop-in hydrocarbon biofuel - integrating with existing petroleum refineries under uncertainty114 Revenue-sharing contracts across an extended -115 An integrated revenue sharing and quantity discounts contract for coordinating a - dealing with short life-cycle products116 Total JIT (T-JIT) and its impact on - competency and organizational performance117 Logistical - design for bioeconomy applications118 A note on ―Quality investment and inspection policy in a supplier-manufacturer -‖119 Developing a Resilient -120 Cyber - risk ,: Revolutionizing the strategic control of critical IT systems121 Defining value chain architectures: Linking strategic value creation to operational - design122 Aligning the sustainable - to green marketing needs: A case study123 Decision support and intelligent systems in the textile and apparel -: An academic review of research articles124 - ,capability of small and medium sized family businesses in India: A multiple case study approach125 - collaboration: Impact of success in long-term partnerships126 Collaboration capacity for sustainable - ,: small and medium-sized enterprises in Mexico127 Advanced traceability system in aquaculture -128 - information systems strategy: Impacts on - performance and firm performance129 Performance of - collaboration – A simulation study130 Coordinating a three-level - with delay in payments and a discounted interest rate131 An integrated framework for agent basedinventory–production–transportation modeling and distributed simulation of -s132 Optimal - design and ,over a multi-period horizon under demand uncertainty. Part I: MINLP and MILP models133 The impact of knowledge transfer and complexity on - flexibility: A knowledge-based view134 An innovative - performance measurement system incorporating Research and Development (R&D) and marketing policy135 Robust decision making for hybrid process - systems via model predictive control136 Combined pricing and - operations under price-dependent stochastic demand137 Balancing - competitiveness and robustness through ―virtual dual sourcing‖: Lessons from the Great East Japan Earthquake138 Solving a tri-objective - problem with modified NSGA-II algorithm 139 Sustaining long-term - partnerships using price-only contracts 140 On the impact of advertising initiatives in -s141 A typology of the situations of cooperation in -s142 A structured analysis of operations and - ,research in healthcare (1982–2011143 - practice and information quality: A - strategy study144 Manufacturer's pricing strategy in a two-level - with competing retailers and advertising cost dependent demand145 Closed-loop - / design under a fuzzy environment146 Timing and eco(nomic) efficiency of climate-friendly investments in -s147 Post-seismic - risk ,: A system dynamics disruption analysis approach for inventory and logistics planning148 The relationship between legitimacy, reputation, sustainability and branding for companies and their -s149 Linking - configuration to - perfrmance: A discrete event simulation model150 An integrated multi-objective model for allocating the limited sources in a multiple multi-stage lean -151 Price and leadtime competition, and coordination for make-to-order -s152 A model of resilient - / design: A two-stage programming with fuzzy shortest path153 Lead time variation control using reliable shipment equipment: An incentive scheme for - coordination154 Interpreting - dynamics: A quasi-chaos perspective155 A production-inventory model for a two-echelon - when demand is dependent on sales teams׳ initiatives156 Coordinating a dual-channel - with risk-averse under a two-way revenue sharing contract157 Energy supply planning and - optimization under uncertainty158 A hierarchical model of the impact of RFID practices on retail - performance159 An optimal solution to a three echelon - / with multi-product and multi-period160 A multi-echelon - model for municipal solid waste ,system 161 A multi-objective approach to - visibility and risk162 An integrated - model with errors in quality inspection and learning in production163 A fuzzy AHP-TOPSIS framework for ranking the solutions of Knowledge ,adoption in - to overcome its barriers164 A relational study of - agility, competitiveness and business performance in the oil and gas industry165 Cyber - security practices DNA – Filling in the puzzle using a diverse set of disciplines166 A three layer - model with multiple suppliers, manufacturers and retailers for multiple items167 Innovations in low input and organic dairy -s—What is acceptable in Europe168 Risk Variables in Wind Power -169 An analysis of - strategies in the regenerative medicine industry—Implications for future development170 A note on - coordination for joint determination of order quantity and reorder point using a credit option171 Implementation of a responsive - strategy in global complexity: The case of manufacturing firms172 - scheduling at the manufacturer to minimize inventory holding and delivery costs173 GBOM-oriented ,of production disruption risk and optimization of - construction175 Alliance or no alliance—Bargaining power in competing reverse -s174 Climate change risks and adaptation options across Australian seafood -s – A preliminary assessment176 Designing contracts for a closed-loop - under information asymmetry 177 Chemical - modeling for analysis of homeland security178 Chain liability in multitier -s? Responsibility attributions for unsustainable supplier behavior179 Quantifying the efficiency of price-only contracts in push -s over demand distributions of known supports180 Closed-loop - / design: A financial approach181 An integrated - / design problem for bidirectional flows182 Integrating multimodal transport into cellulosic biofuel - design under feedstock seasonality with a case study based on California183 - dynamic configuration as a result of new product development184 A genetic algorithm for optimizing defective goods - costs using JIT logistics and each-cycle lengths185 A - / design model for biomass co-firing in coal-fired power plants 186 Finance sourcing in a -187 Data quality for data science, predictive analytics, and big data in - ,: An introduction to the problem and suggestions for research and applications188 Consumer returns in a decentralized -189 Cost-based pricing model with value-added tax and corporate income tax for a - /190 A hard nut to crack! Implementing - sustainability in an emerging economy191 Optimal location of spelling yards for the northern Australian beef -192 Coordination of a socially responsible - using revenue sharing contract193 Multi-criteria decision making based on trust and reputation in -194 Hydrogen - architecture for bottom-up energy systems models. Part 1: Developing pathways195 Financialization across the Pacific: Manufacturing cost ratios, -s and power196 Integrating deterioration and lifetime constraints in production and - planning: A survey197 Joint economic lot sizing problem for a three—Layer - with stochastic demand198 Mean-risk analysis of radio frequency identification technology in - with inventory misplacement: Risk-sharing and coordination199 Dynamic impact on global -s performance of disruptions propagation produced by terrorist acts。
国际自动化与计算杂志.英文版.
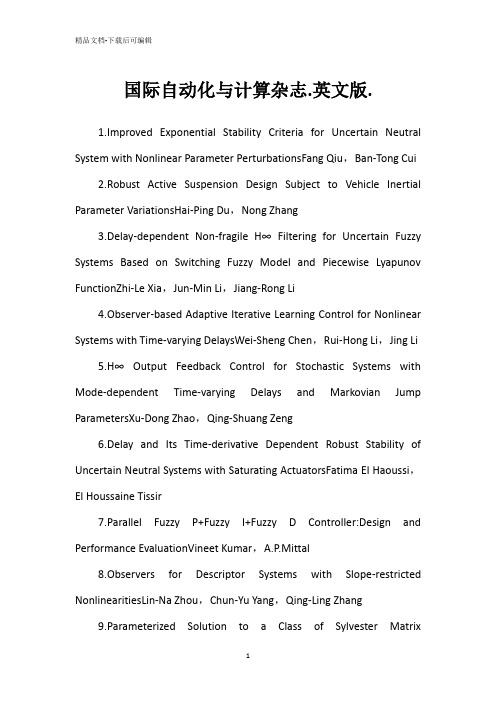
国际自动化与计算杂志.英文版.1.Improved Exponential Stability Criteria for Uncertain Neutral System with Nonlinear Parameter PerturbationsFang Qiu,Ban-Tong Cui2.Robust Active Suspension Design Subject to Vehicle Inertial Parameter VariationsHai-Ping Du,Nong Zhang3.Delay-dependent Non-fragile H∞ Filtering for Uncertain Fuzzy Systems Based on Switching Fuzzy Model and Piecewise Lyapunov FunctionZhi-Le Xia,Jun-Min Li,Jiang-Rong Li4.Observer-based Adaptive Iterative Learning Control for Nonlinear Systems with Time-varying DelaysWei-Sheng Chen,Rui-Hong Li,Jing Li5.H∞ Output Feedback Control for Stochastic Systems with Mode-dependent Time-varying Delays and Markovian Jump ParametersXu-Dong Zhao,Qing-Shuang Zeng6.Delay and Its Time-derivative Dependent Robust Stability of Uncertain Neutral Systems with Saturating ActuatorsFatima El Haoussi,El Houssaine Tissir7.Parallel Fuzzy P+Fuzzy I+Fuzzy D Controller:Design and Performance EvaluationVineet Kumar,A.P.Mittal8.Observers for Descriptor Systems with Slope-restricted NonlinearitiesLin-Na Zhou,Chun-Yu Yang,Qing-Ling Zhang9.Parameterized Solution to a Class of Sylvester MatrixEquationsYu-Peng Qiao,Hong-Sheng Qi,Dai-Zhan Cheng10.Indirect Adaptive Fuzzy and Impulsive Control of Nonlinear SystemsHai-Bo Jiang11.Robust Fuzzy Tracking Control for Nonlinear Networked Control Systems with Integral Quadratic ConstraintsZhi-Sheng Chen,Yong He,Min Wu12.A Power-and Coverage-aware Clustering Scheme for Wireless Sensor NetworksLiang Xue,Xin-Ping Guan,Zhi-Xin Liu,Qing-Chao Zheng13.Guaranteed Cost Active Fault-tolerant Control of Networked Control System with Packet Dropout and Transmission DelayXiao-Yuan Luo,Mei-Jie Shang,Cai-Lian Chen,Xin-Ping Guanparison of Two Novel MRAS Based Strategies for Identifying Parameters in Permanent Magnet Synchronous MotorsKan Liu,Qiao Zhang,Zi-Qiang Zhu,Jing Zhang,An-Wen Shen,Paul Stewart15.Modeling and Analysis of Scheduling for Distributed Real-time Embedded SystemsHai-Tao Zhang,Gui-Fang Wu16.Passive Steganalysis Based on Higher Order Image Statistics of Curvelet TransformS.Geetha,Siva S.Sivatha Sindhu,N.Kamaraj17.Movement Invariants-based Algorithm for Medical Image Tilt CorrectionMei-Sen Pan,Jing-Tian Tang,Xiao-Li Yang18.Target Tracking and Obstacle Avoidance for Multi-agent SystemsJing Yan,Xin-Ping Guan,Fu-Xiao Tan19.Automatic Generation of Optimally Rigid Formations Using Decentralized MethodsRui Ren,Yu-Yan Zhang,Xiao-Yuan Luo,Shao-Bao Li20.Semi-blind Adaptive Beamforming for High-throughput Quadrature Amplitude Modulation SystemsSheng Chen,Wang Yao,Lajos Hanzo21.Throughput Analysis of IEEE 802.11 Multirate WLANs with Collision Aware Rate Adaptation AlgorithmDhanasekaran Senthilkumar,A. Krishnan22.Innovative Product Design Based on Customer Requirement Weight Calculation ModelChen-Guang Guo,Yong-Xian Liu,Shou-Ming Hou,Wei Wang23.A Service Composition Approach Based on Sequence Mining for Migrating E-learning Legacy System to SOAZhuo Zhang,Dong-Dai Zhou,Hong-Ji Yang,Shao-Chun Zhong24.Modeling of Agile Intelligent Manufacturing-oriented Production Scheduling SystemZhong-Qi Sheng,Chang-Ping Tang,Ci-Xing Lv25.Estimation of Reliability and Cost Relationship for Architecture-based SoftwareHui Guan,Wei-Ru Chen,Ning Huang,Hong-Ji Yang1.A Computer-aided Design System for Framed-mould in Autoclave ProcessingTian-Guo Jin,Feng-Yang Bi2.Wear State Recognition of Drills Based on K-means Cluster and Radial Basis Function Neural NetworkXu Yang3.The Knee Joint Design and Control of Above-knee Intelligent Bionic Leg Based on Magneto-rheological DamperHua-Long Xie,Ze-Zhong Liang,Fei Li,Li-Xin Guo4.Modeling of Pneumatic Muscle with Shape Memory Alloy and Braided SleeveBin-Rui Wang,Ying-Lian Jin,Dong Wei5.Extended Object Model for Product Configuration DesignZhi-Wei Xu,Ze-Zhong Liang,Zhong-Qi Sheng6.Analysis of Sheet Metal Extrusion Process Using Finite Element MethodXin-Cun Zhuang,Hua Xiang,Zhen Zhao7.Implementation of Enterprises' Interoperation Based on OntologyXiao-Feng Di,Yu-Shun Fan8.Path Planning Approach in Unknown EnvironmentTing-Kai Wang,Quan Dang,Pei-Yuan Pan9.Sliding Mode Variable Structure Control for Visual Servoing SystemFei Li,Hua-Long Xie10.Correlation of Direct Piezoelectric Effect on EAPap under Ambient FactorsLi-Jie Zhao,Chang-Ping Tang,Peng Gong11.XML-based Data Processing in Network Supported Collaborative DesignQi Wang,Zhong-Wei Ren,Zhong-Feng Guo12.Production Management Modelling Based on MASLi He,Zheng-Hao Wang,Ke-Long Zhang13.Experimental Tests of Autonomous Ground Vehicles with PreviewCunjia Liu,Wen-Hua Chen,John Andrews14.Modelling and Remote Control of an ExcavatorYang Liu,Mohammad Shahidul Hasan,Hong-Nian Yu15.TOPSIS with Belief Structure for Group Belief Multiple Criteria Decision MakingJiang Jiang,Ying-Wu Chen,Da-Wei Tang,Yu-Wang Chen16.Video Analysis Based on Volumetric Event DetectionJing Wang,Zhi-Jie Xu17.Improving Decision Tree Performance by Exception HandlingAppavu Alias Balamurugan Subramanian,S.Pramala,B.Rajalakshmi,Ramasamy Rajaram18.Robustness Analysis of Discrete-time Indirect Model Reference Adaptive Control with Normalized Adaptive LawsQing-Zheng Gao,Xue-Jun Xie19.A Novel Lifecycle Model for Web-based Application Development in Small and Medium EnterprisesWei Huang,Ru Li,Carsten Maple,Hong-Ji Yang,David Foskett,Vince Cleaver20.Design of a Two-dimensional Recursive Filter Using the Bees AlgorithmD. T. Pham,Ebubekir Ko(c)21.Designing Genetic Regulatory Networks Using Fuzzy Petri Nets ApproachRaed I. Hamed,Syed I. Ahson,Rafat Parveen1.State of the Art and Emerging Trends in Operations and Maintenance of Offshore Oil and Gas Production Facilities: Some Experiences and ObservationsJayantha P.Liyanage2.Statistical Safety Analysis of Maintenance Management Process of Excavator UnitsLjubisa Papic,Milorad Pantelic,Joseph Aronov,Ajit Kumar Verma3.Improving Energy and Power Efficiency Using NComputing and Approaches for Predicting Reliability of Complex Computing SystemsHoang Pham,Hoang Pham Jr.4.Running Temperature and Mechanical Stability of Grease as Maintenance Parameters of Railway BearingsJan Lundberg,Aditya Parida,Peter S(o)derholm5.Subsea Maintenance Service Delivery: Mapping Factors Influencing Scheduled Service DurationEfosa Emmanuel Uyiomendo,Tore Markeset6.A Systemic Approach to Integrated E-maintenance of Large Engineering PlantsAjit Kumar Verma,A.Srividya,P.G.Ramesh7.Authentication and Access Control in RFID Based Logistics-customs Clearance Service PlatformHui-Fang Deng,Wen Deng,Han Li,Hong-Ji Yang8.Evolutionary Trajectory Planning for an Industrial RobotR.Saravanan,S.Ramabalan,C.Balamurugan,A.Subash9.Improved Exponential Stability Criteria for Recurrent Neural Networks with Time-varying Discrete and Distributed DelaysYuan-Yuan Wu,Tao Li,Yu-Qiang Wu10.An Improved Approach to Delay-dependent Robust Stabilization for Uncertain Singular Time-delay SystemsXin Sun,Qing-Ling Zhang,Chun-Yu Yang,Zhan Su,Yong-Yun Shao11.Robust Stability of Nonlinear Plants with a Non-symmetric Prandtl-Ishlinskii Hysteresis ModelChang-An Jiang,Ming-Cong Deng,Akira Inoue12.Stability Analysis of Discrete-time Systems with Additive Time-varying DelaysXian-Ming Tang,Jin-Shou Yu13.Delay-dependent Stability Analysis for Markovian Jump Systems with Interval Time-varying-delaysXu-Dong Zhao,Qing-Shuang Zeng14.H∞ Synchronization of Chaotic Systems via Delayed Feedback ControlLi Sheng,Hui-Zhong Yang15.Adaptive Fuzzy Observer Backstepping Control for a Class of Uncertain Nonlinear Systems with Unknown Time-delayShao-Cheng Tong,Ning Sheng16.Simulation-based Optimal Design of α-β-γ-δ FilterChun-Mu Wu,Paul P.Lin,Zhen-Yu Han,Shu-Rong Li17.Independent Cycle Time Assignment for Min-max SystemsWen-De Chen,Yue-Gang Tao,Hong-Nian Yu1.An Assessment Tool for Land Reuse with Artificial Intelligence MethodDieter D. Genske,Dongbin Huang,Ariane Ruff2.Interpolation of Images Using Discrete Wavelet Transform to Simulate Image Resizing as in Human VisionRohini S. Asamwar,Kishor M. Bhurchandi,Abhay S. Gandhi3.Watermarking of Digital Images in Frequency DomainSami E. I. Baba,Lala Z. Krikor,Thawar Arif,Zyad Shaaban4.An Effective Image Retrieval Mechanism Using Family-based Spatial Consistency Filtration with Object RegionJing Sun,Ying-Jie Xing5.Robust Object Tracking under Appearance Change ConditionsQi-Cong Wang,Yuan-Hao Gong,Chen-Hui Yang,Cui-Hua Li6.A Visual Attention Model for Robot Object TrackingJin-Kui Chu,Rong-Hua Li,Qing-Ying Li,Hong-Qing Wang7.SVM-based Identification and Un-calibrated Visual Servoing for Micro-manipulationXin-Han Huang,Xiang-Jin Zeng,Min Wang8.Action Control of Soccer Robots Based on Simulated Human IntelligenceTie-Jun Li,Gui-Qiang Chen,Gui-Fang Shao9.Emotional Gait Generation for a Humanoid RobotLun Xie,Zhi-Liang Wang,Wei Wang,Guo-Chen Yu10.Cultural Algorithm for Minimization of Binary Decision Diagram and Its Application in Crosstalk Fault DetectionZhong-Liang Pan,Ling Chen,Guang-Zhao Zhang11.A Novel Fuzzy Direct Torque Control System for Three-level Inverter-fed Induction MachineShu-Xi Liu,Ming-Yu Wang,Yu-Guang Chen,Shan Li12.Statistic Learning-based Defect Detection for Twill FabricsLi-Wei Han,De Xu13.Nonsaturation Throughput Enhancement of IEEE 802.11b Distributed Coordination Function for Heterogeneous Traffic under Noisy EnvironmentDhanasekaran Senthilkumar,A. Krishnan14.Structure and Dynamics of Artificial Regulatory Networks Evolved by Segmental Duplication and Divergence ModelXiang-Hong Lin,Tian-Wen Zhang15.Random Fuzzy Chance-constrained Programming Based on Adaptive Chaos Quantum Honey Bee Algorithm and Robustness AnalysisHan Xue,Xun Li,Hong-Xu Ma16.A Bit-level Text Compression Scheme Based on the ACW AlgorithmHussein A1-Bahadili,Shakir M. Hussain17.A Note on an Economic Lot-sizing Problem with Perishable Inventory and Economies of Scale Costs:Approximation Solutions and Worst Case AnalysisQing-Guo Bai,Yu-Zhong Zhang,Guang-Long Dong1.Virtual Reality: A State-of-the-Art SurveyNing-Ning Zhou,Yu-Long Deng2.Real-time Virtual Environment Signal Extraction and DenoisingUsing Programmable Graphics HardwareYang Su,Zhi-Jie Xu,Xiang-Qian Jiang3.Effective Virtual Reality Based Building Navigation Using Dynamic Loading and Path OptimizationQing-Jin Peng,Xiu-Mei Kang,Ting-Ting Zhao4.The Skin Deformation of a 3D Virtual HumanXiao-Jing Zhou,Zheng-Xu Zhao5.Technology for Simulating Crowd Evacuation BehaviorsWen-Hu Qin,Guo-Hui Su,Xiao-Na Li6.Research on Modelling Digital Paper-cut PreservationXiao-Fen Wang,Ying-Rui Liu,Wen-Sheng Zhang7.On Problems of Multicomponent System Maintenance ModellingTomasz Nowakowski,Sylwia Werbinka8.Soft Sensing Modelling Based on Optimal Selection of Secondary Variables and Its ApplicationQi Li,Cheng Shao9.Adaptive Fuzzy Dynamic Surface Control for Uncertain Nonlinear SystemsXiao-Yuan Luo,Zhi-Hao Zhu,Xin-Ping Guan10.Output Feedback for Stochastic Nonlinear Systems with Unmeasurable Inverse DynamicsXin Yu,Na Duan11.Kalman Filtering with Partial Markovian Packet LossesBao-Feng Wang,Ge Guo12.A Modified Projection Method for Linear FeasibilityProblemsYi-Ju Wang,Hong-Yu Zhang13.A Neuro-genetic Based Short-term Forecasting Framework for Network Intrusion Prediction SystemSiva S. Sivatha Sindhu,S. Geetha,M. Marikannan,A. Kannan14.New Delay-dependent Global Asymptotic Stability Condition for Hopfield Neural Networks with Time-varying DelaysGuang-Deng Zong,Jia Liu hHTTp://15.Crosscumulants Based Approaches for the Structure Identification of Volterra ModelsHouda Mathlouthi,Kamel Abederrahim,Faouzi Msahli,Gerard Favier1.Coalition Formation in Weighted Simple-majority Games under Proportional Payoff Allocation RulesZhi-Gang Cao,Xiao-Guang Yang2.Stability Analysis for Recurrent Neural Networks with Time-varying DelayYuan-Yuan Wu,Yu-Qiang Wu3.A New Type of Solution Method for the Generalized Linear Complementarity Problem over a Polyhedral ConeHong-Chun Sun,Yan-Liang Dong4.An Improved Control Algorithm for High-order Nonlinear Systems with Unmodelled DynamicsNa Duan,Fu-Nian Hu,Xin Yu5.Controller Design of High Order Nonholonomic System with Nonlinear DriftsXiu-Yun Zheng,Yu-Qiang Wu6.Directional Filter for SAR Images Based on NonsubsampledContourlet Transform and Immune Clonal SelectionXiao-Hui Yang,Li-Cheng Jiao,Deng-Feng Li7.Text Extraction and Enhancement of Binary Images Using Cellular AutomataG. Sahoo,Tapas Kumar,B.L. Rains,C.M. Bhatia8.GH2 Control for Uncertain Discrete-time-delay Fuzzy Systems Based on a Switching Fuzzy Model and Piecewise Lyapunov FunctionZhi-Le Xia,Jun-Min Li9.A New Energy Optimal Control Scheme for a Separately Excited DC Motor Based Incremental Motion DriveMilan A.Sheta,Vivek Agarwal,Paluri S.V.Nataraj10.Nonlinear Backstepping Ship Course ControllerAnna Witkowska,Roman Smierzchalski11.A New Method of Embedded Fourth Order with Four Stages to Study Raster CNN SimulationR. Ponalagusamy,S. Senthilkumar12.A Minimum-energy Path-preserving Topology Control Algorithm for Wireless Sensor NetworksJin-Zhao Lin,Xian Zhou,Yun Li13.Synchronization and Exponential Estimates of Complex Networks with Mixed Time-varying Coupling DelaysYang Dai,YunZe Cai,Xiao-Ming Xu14.Step-coordination Algorithm of Traffic Control Based on Multi-agent SystemHai-Tao Zhang,Fang Yu,Wen Li15.A Research of the Employment Problem on Common Job-seekersand GraduatesBai-Da Qu。
注塑模具工艺立体光照成型毕业论文中英文对照资料外文翻译文献

注塑模具工艺中英文对照资料外文翻译文献附录2Integrated simulation of the injection molding process withstereolithography moldsAbstract Functional parts are needed for design verification testing, field trials, customer evaluation, and production planning. By eliminating multiple steps, the creation of the injection mold directly by a rapid prototyping (RP) process holds the best promise of reducing the time and cost needed to mold low-volume quantities of parts. The potential of this integration of injection molding with RP has been demonstrated many times. What is missing is the fundamental understanding of how the modifications to the mold material and RP manufacturing process impact both the mold design and the injection molding process. In addition, numerical simulation techniques have now become helpful tools of mold designers and process engineers for traditional injection molding. But all current simulation packages for conventional injection molding are no longer applicable to this new type of injection molds, mainly because the property of the mold material changes greatly. In this paper, an integrated approach to accomplish a numerical simulation of injection molding into rapid-prototyped molds is established and a corresponding simulation system is developed. Comparisons with experimental results are employed for verification, which show that the present scheme is well suited to handle RP fabricated stereolithography (SL) molds.Keywords Injection molding Numerical simulation Rapid prototyping1 IntroductionIn injection molding, the polymer melt at high temperature is injected into the mold under high pressure [1]. Thus, the mold material needs to have thermal and mechanical properties capable of withstanding the temperatures and pressures of the molding cycle. The focus of many studies has been to create theinjection mold directly by a rapid prototyping (RP) process. By eliminating multiple steps, this method of tooling holds the best promise of reducing the time and cost needed to createlow-volume quantities of parts in a production material. The potential of integrating injection molding with RP technologies has been demonstrated many times. The properties of RP molds are very different from those of traditional metal molds. The key differences are the properties of thermal conductivity and elastic modulus (rigidity). For example, the polymers used in RP-fabricated stereolithography (SL) molds have a thermal conductivity that is less than one thousandth that of an aluminum tool. In using RP technologies to create molds, the entire mold design and injection-molding process parameters need to be modified and optimized from traditional methodologies due to the completely different tool material. However, there is still not a fundamental understanding of h ow the modifications to the mold tooling method and material impact both the mold design and the injection molding process parameters. One cannot obtain reasonable results by simply changing a few material properties in current models. Also, using traditional approaches when making actual parts may be generating sub-optimal results. So there is a dire need to study the interaction between the rapid tooling (RT) process and material and injection molding, so as to establish the mold design criteria and techniques for an RT-oriented injection molding process.In addition, computer simulation is an effective approach for predicting the quality of molded parts. Commercially available simulation packages of the traditional injection molding process have now become routine tools of the mold designer and process engineer [2]. Unfortunately, current simulation programs for conventional injection molding are no longer applicable to RP molds, because of the dramatically dissimilar tool material. For instance, in using the existing simulation software with aluminum and SL molds and comparing with experimental results, though the simulation values of part distortion are reasonable for the aluminum mold, results are unacceptable, with the error exceeding 50%. The distortion during injection molding is due to shrinkage and warpage of the plastic part, as well as the mold. For ordinarily molds, the main factor is the shrinkage and warpage of the plastic part, which is modeled accurately in current simulations. But for RP molds, the distortion of the mold has potentially more influence, which have been neglected in current models. For instance, [3] used a simple three-step simulation process to consider the mold distortion, which had too much deviation.In this paper, based on the above analysis, a new simulation system for RP molds is developed. The proposed system focuses on predicting part distortion, which is dominating defect in RP-molded parts. The developed simulation can be applied as an evaluation tool for RP mold design and process opti mization. Our simulation system is verified by an experimental example.Although many materials are available for use in RP technologies, we concentrate on usingstereolithography (SL), the original RP technology, to create polymer molds. The SL process uses photopolymer and laser energy to build a part layer by layer. Using SL takes advantage of both the commercial dominance of SL in the RP industry and the subsequent expertise base that has been developed for creating accurate, high-quality parts. Until recently, SL was primarily used to create physical models for visual inspection and form-fit studies with very limited func-tional applications. However, the newer generation stereolithographic photopolymers have improved dimensional, mechanical and thermal properties making it possible to use them for actual functional molds.2 Integrated simulation of the molding process2.1 MethodologyIn order to simulate the use of an SL mold in the injection molding process, an iterative method is proposed. Different software modules have been developed and used to accomplish this task. The main assumption is that temperature and load boundary conditions cause significant distortions in the SL mold. The simulation steps are as follows:1T he part geometry is modeled as a solid model, which is translated to a file readable by the flow analysis package.2Simulate the mold-filling process of the melt into a pho topolymer mold, which will output the resulting temperature and pressure profiles.3Structural analysis is then performed on the photopolymer mold model using the thermal and load boundary conditions obtained from the previous step, which calculates the distortion that the mold undergo during the injection process.4If the distortion of the mold converges, move to the next step. Otherwise, the distorted mold cavity is then modeled (changes in the dimensions of the cavity after distortion), and returns to the second step to simulate the melt injection into the distorted mold.5The shrinkage and warpage simulation of the injection molded part is then applied, which calculates the final distor tions of the molded part.In above simulation flow, there are three basic simulation mod ules.2. 2 Filling simulation of the melt2.2.1 Mathematical modelingIn order to simulate the use of an SL mold in the injection molding process, an iterativemethod is proposed. Different software modules have been developed and used to accomplish this task. The main assumption is that temperature and load boundary conditions cause significant distortions in the SL mold. The simulation steps are as follows:1. The part geometry is modeled as a solid model, which is translated to a file readable by the flow analysis package.2. Simulate the mold-filling process of the melt into a photopolymer mold, which will output the resulting temperature and pressure profiles.3. Structural analysis is then performed on the photopolymer mold model using the thermal and load boundary conditions obtained from the previous step, which calculates the distortion that the mold undergo during the injection process.4. If the distortion of the mold converges, move to the next step. Otherwise, the distorted mold cavity is then modeled (changes in the dimensions of the cavity after distortion), and returns to the second step to simulate the melt injection into the distorted mold.5. The shrinkage and warpage simulation of the injection molded part is then applied, which calculates the final distortions of the molded part.In above simulation flow, there are three basic simulation modules.2.2 Filling simulation of the melt2.2.1 Mathematical modelingComputer simulation techniques have had success in predicting filling behavior in extremely complicated geometries. However, most of the current numerical implementation is based on a hybrid finite-element/finite-difference solution with the middleplane model. The application process of simulation packages based on this model is illustrated in Fig. 2-1. However, unlike the surface/solid model in mold-design CAD systems, the so-called middle-plane (as shown in Fig. 2-1b) is an imaginary arbitrary planar geometry at the middle of the cavity in the gap-wise direction, which should bring about great inconvenience in applications. For example, surface models are commonly used in current RP systems (generally STL file format), so secondary modeling is unavoidable when using simulation packages because the models in the RP and simulation systems are different. Considering these defects, the surface model of the cavity is introduced as datum planes in the simulation, instead of the middle-plane.According to the previous investigations [4–6], fillinggoverning equations for the flow and temperature field can be written as:where x, y are the planar coordinates in the middle-plane, and z is the gap-wise coordinate; u, v,w are the velocity components in the x, y, z directions; u, v are the average whole-gap thicknesses; and η, ρ,CP (T), K(T) represent viscosity, density, specific heat and thermal conductivity of polymer melt, respectively.Fig.2-1 a–d. Schematic procedure of the simulation with middle-plane model. a The 3-D surface model b The middle-plane model c The meshed middle-plane model d The display of the simulation result In addition, boundary conditions in the gap-wise direction can be defined as:where TW is the constant wall temperature (shown in Fig. 2a).Combining Eqs. 1–4 with Eqs. 5–6, it follows that the distributions of the u, v, T, P at z coordinates should be symmetrical, with the mirror axis being z = 0, and consequently the u, v averaged in half-gap thickness is equal to that averaged in wholegap thickness. Based on this characteristic, we can divide the whole cavity into two equal parts in the gap-wise direction, as described by Part I and Part II in Fig. 2b. At the same time, triangular finite elements are generated in the surface(s) of the cavity (at z = 0 in Fig. 2b), instead of the middle-plane (at z = 0 in Fig. 2a). Accordingly, finite-difference increments in the gapwise direction are employed only in the inside of the surface(s) (wall to middle/center-line), which, in Fig. 2b, means from z = 0 to z = b. This is single-sided instead of two-sided with respect to the middle-plane (i.e. from the middle-line to two walls). In addition, the coordinate system is changed from Fig. 2a to Fig. 2b to alter the finite-element/finite-difference scheme, as shown in Fig. 2b. With the above adjustment, governing equations are still Eqs. 1–4. However, the original boundary conditions inthe gapwise direction are rewritten as:Meanwhile, additional boundary conditions must be employed at z = b in order to keep the flows at the juncture of the two parts at the same section coordinate [7]:where subscripts I, II represent the parameters of Part I and Part II, respectively, and Cm-I and Cm-II indicate the moving free melt-fronts of the surfaces of the divided two parts in the filling stage.It should be noted that, unlike conditions Eqs. 7 and 8, ensuring conditions Eqs. 9 and 10 are upheld in numerical implementations becomes more difficult due to the following reasons:1. The surfaces at the same section have been meshed respectively, which leads to a distinctive pattern of finite elements at the same section. Thus, an interpolation operation should be employed for u, v, T, P during the comparison between the two parts at the juncture.2. Because the two parts have respective flow fields with respect to the nodes at point A and point C (as shown in Fig. 2b) at the same section, it is possible to have either both filled or one filled (and one empty). These two cases should be handled separately, averaging the operation for the former, whereas assigning operation for the latter.3. It follows that a small difference between the melt-fronts is permissible. That allowance can be implemented by time allowance control or preferable location allowance control of the melt-front nodes.4. The boundaries of the flow field expand by each melt-front advancement, so it is necessary to check the condition Eq. 10 after each change in the melt-front.5. In view of above-mentioned analysis, the physical parameters at the nodes of the same section should be compared and adjusted, so the information describing finite elements of the same section should be prepared before simulation, that is, the matching operation among the elements should be preformed.Fig. 2a,b. Illustrative of boundary conditions in the gap-wise direction a of the middle-plane model b of thesurface model2.2.2 Numerical implementationPressure field. In modeling viscosity η, which is a function of shear rate, temperature and pressure of melt, the shear-thinning behavior can be well represented by a cross-type model such as:where n corresponds to the power-law index, and τ∗ characterizes the shear stress level of the transition region between the Newtonian and power-law asymptotic limits. In terms of an Arrhenius-type temperature sensitivity and exponential pressure dependence, η0(T, P) can be represented with reasonable accuracy as follows:Equations 11 and 12 constitute a five-constant (n, τ∗, B, Tb, β) representation for viscosity. The shear rate for viscosity calculation is obtained by:Based on the above, we can infer the following filling pressure equation from the governing Eqs. 1–4:where S is calculated by S = b0/(b−z)2η d z. Applying the Galerkin method, the pressure finite-element equation is deduced as:where l_ traverses all elements, including node N, and where I and j represent the local node number in element l_ corresponding to the node number N and N_ in the whole, respectively. The D(l_) ij is calculated as follows:where A(l_) represents triangular finite elements, and L(l_) i is the pressure trial function in finite elements.Temperature field. To determine the temperature profile across the gap, each triangular finite element at the surface is further divided into NZ layers for the finite-difference grid.The left item of the energy equation (Eq. 4) can be expressed as:where TN, j,t represents the temperature of the j layer of node N at time t.The heat conduction item is calculated by:where l traverses all elements, including node N, and i and j represent the local node number in element l corresponding to the node number N and N_ in the whole, respectively.The heat convection item is calculated by:For viscous heat, it follows that:Substituting Eqs. 17–20 into the energy equation (Eq. 4), the temperature equation becomes:2.3 Structural analysis of the moldThe purpose of structural analysis is to predict the deformation occurring in the photopolymer mold due to the thermal and mechanical loads of the filling process. This model is based on a three-dimensional thermoelastic boundary element method (BEM). The BEM is ideally suited for this application because only the deformation of the mold surfaces is of interest. Moreover, the BEM has an advantage over other techniques in that computing effort is not wasted on calculating deformation within the mold.The stresses resulting from the process loads are well within the elastic range of the mold material. Therefore, the mold deformation model is based on a thermoelastic formulation. The thermal and mechanical properties of the mold are assumed to be isotropic and temperature independent.Although the process is cyclic, time-averaged values of temperature and heat flux are used for calculating the mold deformation. Typically, transient temperature variations within a mold have been restricted to regions local to the cavity surface and the nozzle tip [8]. The transients decay sharply with distance from the cavity surface and generally little variation is observed beyond distances as small as 2.5 mm. This suggests that the contribution from the transients to the deformation at the mold block interface is small, and therefore it is reasonable to neglect the transient effects. The steady state temperature field satisfies Laplace’s equation 2T = 0 and the time-averaged boundary conditions. The boundary conditions on the mold surfaces are described in detail by Tang et al. [9]. As for the mechanical boundary conditions, the cavity surface is subjected to the melt pressure, the surfaces of the mold connected to the worktable are fixed in space, and other external surfaces are assumed to be stress free.The derivation of the thermoelastic boundary integral formulation is well known [10]. It is given by:where uk, pk and T are the displacement, traction and temperature,α, ν represent the thermal expansion coefficient and Poisson’s ratio of the material, and r = |y−x|. clk(x) is the surfacecoefficient which depends on the local geometry at x, the orientation of the coordinate frame and Poisson’s ratio for the domain [11]. The fundamental displacement ˜ulk at a point y in the xk direction, in a three-dimensional infinite isotropic elastic domain, results from a unit load concentrated at a point x acting in the xl direction and is of the form:where δlk is the Kronecker delta function and μ is the shear modulus of the mold material.The fundamental traction ˜plk , measured at the point y on a surface with unit normal n, is:Discretizing the surface of the mold into a total of N elements transforms Eq. 22 to:where Γn refers to the n th surface element on the domain.Substituting the appropriate linear shape functions into Eq. 25, the linear boundary element formulation for the mold deformation model is obtained. The equation is applied at each node on the discretized mold surface, thus giving a system of 3N linear equations, where N is the total number of nodes. Each node has eight associated quantities: three components of displacement, three components of traction, a temperature and a heat flux. The steady state thermal model supplies temperature and flux values as known quantities for each node, and of the remaining six quantities, three must be specified. Moreover, the displacement values specified at a certain number of nodes must eliminate the possibility of a rigid-body motion or rigid-body rotation to ensure a non-singular system of equations. The resulting system of equations is assembled into a integrated matrix, which is solved with an iterative solver.2.4 Shrinkage and warpage simulation of the molded partInternal stresses in injection-molded components are the principal cause of shrinkage and warpage. These residual stresses are mainly frozen-in thermal stresses due to inhomogeneous cooling, when surface layers stiffen sooner than the core region, as in free quenching. Based onthe assumption of the linear thermo-elastic and linear thermo-viscoelastic compressible behavior of the polymeric materials, shrinkage and warpage are obtained implicitly using displacement formulations, and the governing equations can be solved numerically using a finite element method.With the basic assumptions of injection molding [12], the components of stress and strain are given by:The deviatoric components of stress and strain, respectively, are given byUsing a similar approach developed by Lee and Rogers [13] for predicting the residual stresses in the tempering of glass, an integral form of the viscoelastic constitutive relationships is used, and the in-plane stresses can be related to the strains by the following equation:Where G1 is the relaxation shear modulus of the material. The dilatational stresses can be related to the strain as follows:Where K is the relaxation bulk modulus of the material, and the definition of α and Θ is:If α(t) = α0, applying Eq. 27 to Eq. 29 results in:Similarly, applying Eq. 31 to Eq. 28 and eliminating strain εxx(z, t) results in:Employing a Laplace transform to Eq. 32, the auxiliary modulus R(ξ) is given by:Using the above constitutive equation (Eq. 33) and simplified forms of the stresses and strains in the mold, the formulation of the residual stress of the injection molded part during the cooling stage is obtain by:Equation 34 can be solved through the application of trapezoidal quadrature. Due to the rapid initial change in the material time, a quasi-numerical procedure is employed for evaluating the integral item. The auxiliary modulus is evaluated numerically by the trapezoidal rule.For warpage analysis, nodal displacements and curvatures for shell elements are expressed as:where [k] is the element stiffness matrix, [Be] is the derivative operator matrix, {d} is the displacements, and {re} is the element load vector which can be evaluated by:The use of a full three-dimensional FEM analysis can achieve accurate warpage results, however, it is cumbersome when the shape of the part is very complicated. In this paper, a twodimensional FEM method, based on shell theory, was used because most injection-molded parts have a sheet-like geometry in which the thickness is much smaller than the other dimensions of the part. Therefore, the part can be regarded as an assembly of flat elements to predict warpage. Each three-node shell element is a combination of a constant strain triangular element (CST) and a discrete Kirchhoff triangular element (DKT), as shown in Fig. 3. Thus, the warpage can be separated into plane-stretching deformation of the CST and plate-bending deformation of the DKT, and correspondingly, the element stiffness matrix to describe warpage can also be divided into the stretching-stiffness matrix and bending-stiffness matrix.Fig. 3a–c. Deformation decomposition of shell element in the local coordinate system. a In-plane stretchingelement b Plate-bending element c Shell element3 Experimental validationTo assess the usefulness of the proposed model and developed program, verification is important. The distortions obtained from the simulation model are compared to the ones from SL injection molding experiments whose data is presented in the literature [8]. A common injection molded part with the dimensions of 36×36×6 mm is considered in the experiment, as shown in Fig. 4. The thickness dimensions of the thin walls and rib are both 1.5 mm; and polypropylene was used as the injection material. The injection machine was a production level ARGURY Hydronica 320-210-750 with the following process parameters: a melt temperature of 250 ◦C; an ambient temperature of 30 ◦C; an injection pressure of 13.79 MPa; an injection time of 3 s; and a cooling time of 48 s. The SL material used, Dupont SOMOSTM 6110 resin, has the ability to resist temperatures of up to 300 ◦C temperatures. As mentioned above, thermal conductivity of the mold is a major factor that differentiates between an SL and a traditional mold. Poor heat transfer in the mold would produce a non-uniform temperature distribution, thus causing warpage that distorts the completed parts. For an SL mold, a longer cycle time would be expected. The method of using a thin shell SL mold backed with a higher thermal conductivity metal (aluminum) was selected to increase thermal conductivity of the SL mold.Fig. 4. Experimental cavity modelFig. 5. A comparison of the distortion variation in the X direction for different thermal conductivity; where “Experimental”, “present”, “three-step”, and “conventional” mean the results of the experimental, the presented simulation, the three-step simulation process and the conventional injection molding simulation, respectively.Fig. 6. Comparison of the distortion variation in the Y direction for different thermal conductivitiesFig. 7. Comparison of the distortion variation in the Z direction for different thermal conductivitiesFig. 8. Comparison of the twist variation for different thermal conductivities For this part, distortion includes the displacements in three directions and the twist (the difference in angle between two initially parallel edges). The validation results are shown in Fig.5 to Fig. 8. These figures also include the distortion values predicted by conventional injection molding simulation and the three-step model reported in [3].4 ConclusionsIn this paper, an integrated model to accomplish the numerical simulation of injection molding into rapid-prototyped molds is established and a corresponding simulation system is developed. For verification, an experiment is also carried out with an RPfabricated SL mold.It is seen that a conventional simulation using current injection molding software breaks down for a photopolymer mold. It is assumed that this is due to the distortion in the mold caused by the temperature and load conditions of injection. The three-step approach also has much deviation. The developed model gives results closer to experimental.Improvement in thermal conductivity of the photopolymer significantly increases part quality. Since the effect of temperature seems to be more dominant than that of pressure (load), an improvement in the thermal conductivity of the photopolymer can improve the part quality significantly.Rapid Prototyping (RP) is a technology makes it possible to manufacture prototypes quickly and inexpensively, regardless of their comp lexity. Rapid Tooling (RT) is the next step in RP’s steady progress and much work is being done to obtain more accurate tools to define the parameters of the process. Existing simulation tools can not provide the researcher with a useful means of studying relative changes. An integrated model, such as the one presented in this paper, is necessary to obtain accurate predictions of the actual quality of final parts. In the future, we expect to see this work expanded to develop simulations program for injection into RP molds manufactured by other RT processes.References1. Wang KK (1980) System approach to injection molding process. Polym-Plast Technol Eng 14(1):75–93.2. Shelesh-Nezhad K, Siores E (1997) Intelligent system for plastic injection molding process design. J Mater Process Technol 63(1–3):458–462.3. Aluru R, Keefe M, Advani S (2001) Simulation of injection molding into rapid-prototyped molds. Rapid Prototyping J 7(1):42–51.4. Shen SF (1984) Simulation of polymeric flows in the injection molding process. Int J Numer Methods Fluids 4(2):171–184.5. Agassant JF, Alles H, Philipon S, Vincent M (1988) Experimental and theoretical study of the injection molding of thermoplastic materials. Polym Eng Sci 28(7):460–468.6. Chiang HH, Hieber CA, Wang KK (1991) A unified simulation of the filling and post-filling stages in injection molding. Part I: formulation. Polym Eng Sci 31(2):116–124.7. Zhou H, Li D (2001) A numerical simulation of the filling stage in injection molding based on a surface model. Adv Polym Technol 20(2):125–131.8. Himasekhar K, Lottey J, Wang KK (1992) CAE of mold cooling in injection molding using a three-dimensional numerical simulation. J EngInd Trans ASME 114(2):213–221.9. Tang LQ, Pochiraju K, Chassapis C, Manoochehri S (1998) Computeraided optimization approach for the design of injection mold cooling systems. J Mech Des, Trans ASME 120(2):165–174.10. Rizzo FJ, Shippy DJ (1977) An advanced boundary integral equation method for three-dimensional thermoelasticity. Int J Numer Methods Eng 11:1753–1768.11. Hartmann F (1980) Computing the C-matrix in non-smooth boundary points. In: New developments in boundary element methods, CML Publications, Southampton, pp 367–379.12. Chen X, Lama YC, Li DQ (2000) Analysis of thermal residual stress in plastic injection molding. J Mater Process Technol 101(1):275–280.13. Lee EH, Rogers TG (1960) Solution of viscoelastic stress analysis problems using measured creep or relaxation function. J Appl Mech 30(1):127–134.14. Li Y (1997) Studies in direct tooling using stereolithography. Dissertation, University of Delaware, Newark, DE..。
电子科学与技术专业介绍(2016中英文)

电子科学与技术专业介绍本专业培养具备微电子和应用电子领域宽厚理论基础、专业知识和实践能力,能从事半导体分立器件、集成电路和电路板级应用电路的设计、制造、生产管理和教学工作的复合型人才。
毕业生掌握半导体物理和微电子器件基本理论,设计C语言和硬件描述语言程序,能够采用正向和逆向方法设计集成电路,具备集成电路工艺和器件仿真设计和实践能力;掌握电路板设计方法,具备开发单片机应用电路能力。
主要课程:电路与电子技术理论与应用系列课程、计算机基础技术系列课程、电子线路CAD、单片机原理及应用、微控制器系统及接口技术、数字系统与逻辑设计、半导体物理学、微电子器件基础、微电子工艺原理、集成电路原理与设计。
主要实践教学环节:计算机应用基础训练、电子工艺实习、模拟电子课程设计、数字电子课程设计、电子线路自动化技术设计实践、计算机网络课程设计、智能电子系统设计实践、集成电路版图课程设计、集成电路解析实践、微电子电路实训综合实践和生产实习等。
就业方向:学生毕业后可以报考本专业或相关专业研究生。
在微电子和应用电子等相关领域,在科研院所和学校从事研究和教学工作,在企业从事集成电路设计、电子元器件研制、应用电子产品软硬件设计和生产技术管理等工作。
The major introduction of electronics science and technologyThe major is to cultivate the interdisciplinary talents who have broad theoretical basis, professional knowledge and practical ability in microelectronics and electronic application fields, can engage in design, manufacturing, management and teaching for discrete semiconductor devices, integrated circuits , circuit board and other electric products.The graduates master the basic theory of semiconductor physics and microelectronic devices, design programs by C language and hardware description language, can design integrated circuits with the forward and inverse method, have the abilities of integrated circuit process and device simulation design and practical. they master circuit board design, have the ability of design SCM application circuits.Main courses: the series courses of electronic technology theory and application, basic computer technology series courses, electronic circuit CAD. Principle and application of single chip microcomputer, micro controller system and interface technology, digital system and logical design, semiconductor physics, microelectronics device, principles of microelectronics process, integrated circuit principle and design.Main practice courses: practice on computer application basic training, electronic technology, course design of analog electronics, course design of digital electronic, practice on electronic circuit automation technology design, course design of computer network, practice on intelligent electronic systems design, practice on integrated circuit layout design, practice on integrated circuit analytic, practice on microelectronic circuit.Employment direction: the graduates can pursue the master degree of related majors. In microelectronics and electronic application fields, they also engage in research and teaching in scientific research institutes and universities, engaged in integrated circuit design, development of electronic devices, software and hardware design for electric products and management inenterprises.。
吉林体育学院研究生导师介绍

吉林体育学院研究生导师介绍姓名:满江虹Array性别:女出生年月:1971年9月职务/职称:教授所在系/部:体育产业研究基地导师:博士生导师电话:电子邮件:manjh@■学科(专业):体育人文社会学■主要研究方向:体育量化研究,体育产业管理■教育经历(1)1994年毕业于曲阜师范大学数学系,获理学学士学位(2)1997年毕业于曲阜师范大学自动化研究所,获理学硕士学位(3)2005年毕业于东南大学经济管理学院,获管理学博士学位(4)2009年山东大学管理学院,工商管理博士后(5)2010年美国贝勒大学商学院,访问学者一年■课题研究(1)我国运动休闲特色小镇产业链构建的机理及实现路径研究,国家社科基金一般项目,主持人,2018年(2)大众冰雪运动风险评估体系构建与实证研究,吉林省社会科学基金项目,2017(3)基于自组织的我国学校“阳光体育运动”可持续发展长效机制研究,吉林省教育科学规划重点项目,主持人,2015(4)体育用品制造企业配送管理的决策方法体系研究,吉林省社会科学基金项目,2014(5)基于参数调节与智能计算的电子类产品回收与再制造策略的建模、仿真与实证研究,中国博士后科学基金面上资助项目,2010(6)配送管理中的软决策方法研究,山东省软科学研究计划一般项目,2009■核心刊物论文发表(1)基于DEA的体育事业协同路径优化系统动力学仿真研究,西安体育学院学报,2018,1,CSSCI,第一作者(2)基于社会网络分析的体育事业发展研究热点分析及聚类研究,南京体育学院学报(社会科学版),2017,6,核心期刊,第一作者(3)体育企业参与政府购买公共服务的模式,上海体育学院学报,2017,9,CSSCI,第一作者(4)中国居民社会认知与自感健康关系研究——体育参与的中介效应,武汉体育学院学报,2017,9,核心期刊,CSSCI,第一作者(5)阶层认同对城镇居民体育参与的影响研究——基于结构方程模型的分析,天津体育学院学报,2016,3,CSSCI,第一作者(6)山东省竞技体育可持续发展模式的系统动力学建模与仿真研究,山东体育学院学报,2013,6,核心期刊,第一作者(7)基于转运协调机制的救灾物资库存控制策略与仿真.,软科学,2012,8,CSSCI,第一作者(8)An Integrated Supply Chain Modeling and Simulation Based on System Dynamics,The 2010 International Conference on Management and Service Science,2010,8,EI收录,第一作者(9)Research on the Collection Policy of Integrated Supply Chain Based on Remanufacture,2010 International Conference on Intelligent Computation Technology and Automation,2010,5,EI收录,第一作者(10)A Knowledge Discovery Way for Reverse Logistics Center Location,The 6th International Conference on Fuzzy Systems and Knowledge Discovery,2009,8,EI收录,第一作者(11)An improved way Based on Rough SET for multi-stage reverse Logistics processing Center Location,Proceedings of International Conference on Machine Learning and Cybernetics,2009,7,EI收录,第一作者(12)A Rough Way for Logistics Center Location Based on Information Entropy,Proceedings of the IEEE International Conference on Automation and Logistics,2008,9,EI收录,第一作者(13)An improved fuzzy discretization way for decision tables with continuous attributes,Proceedings of 2007 International Conference on Machine Learning and Cybernetics,2007,11,EI收录,第一作者(14)An immune solution for attributes reduction in decision table,Proceedings of 2005 International Conference on Machine Learning and Cybernetics,2005,8,EI收录,第一作者(15)基于信息熵的粗约简及其Bayes解释的供应链需求集成分析,东南大学学报(自然科学版),2004,3,EI收录,第一作者(16)基于知识发现的商品住宅有效需求趋势预测方法,系统工程理论与实践,2004,10,,CSSCI、EI收录,第一作者(17)A CBR model for knowledge sharing in supply chain based on generalized Rough Set,Proceedings of 2003 International Conference on Machine Learning and Cybernetics,2003,11,EI收录,第一作者■主要著作绿色供应链系统分析,独著,吉林科学技术出版社,2013年12月出版■培养研究生情况(1)指导学术型硕士研究生13名,在读5名;指导体育专业硕士10名,在读6名。
System Modeling and Simulation
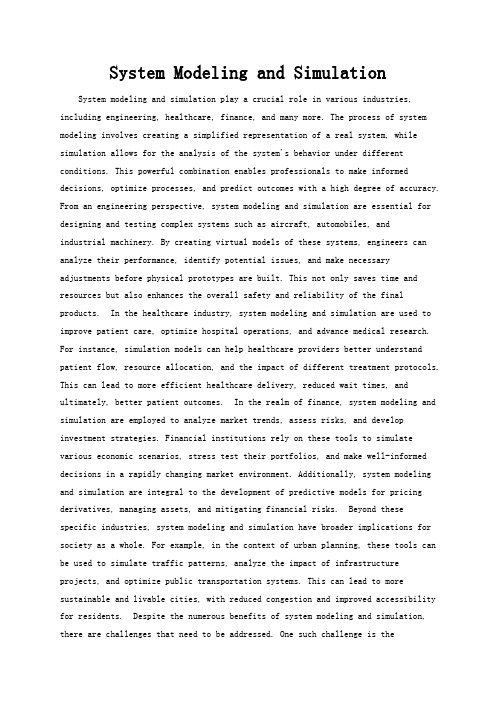
System Modeling and Simulation System modeling and simulation play a crucial role in various industries, including engineering, healthcare, finance, and many more. The process of system modeling involves creating a simplified representation of a real system, while simulation allows for the analysis of the system's behavior under different conditions. This powerful combination enables professionals to make informed decisions, optimize processes, and predict outcomes with a high degree of accuracy. From an engineering perspective, system modeling and simulation are essential for designing and testing complex systems such as aircraft, automobiles, andindustrial machinery. By creating virtual models of these systems, engineers can analyze their performance, identify potential issues, and make necessary adjustments before physical prototypes are built. This not only saves time and resources but also enhances the overall safety and reliability of the final products. In the healthcare industry, system modeling and simulation are used to improve patient care, optimize hospital operations, and advance medical research. For instance, simulation models can help healthcare providers better understand patient flow, resource allocation, and the impact of different treatment protocols. This can lead to more efficient healthcare delivery, reduced wait times, and ultimately, better patient outcomes. In the realm of finance, system modeling and simulation are employed to analyze market trends, assess risks, and develop investment strategies. Financial institutions rely on these tools to simulate various economic scenarios, stress test their portfolios, and make well-informed decisions in a rapidly changing market environment. Additionally, system modeling and simulation are integral to the development of predictive models for pricing derivatives, managing assets, and mitigating financial risks. Beyond thesespecific industries, system modeling and simulation have broader implications for society as a whole. For example, in the context of urban planning, these tools can be used to simulate traffic patterns, analyze the impact of infrastructureprojects, and optimize public transportation systems. This can lead to more sustainable and livable cities, with reduced congestion and improved accessibility for residents. Despite the numerous benefits of system modeling and simulation, there are challenges that need to be addressed. One such challenge is thecomplexity of creating accurate models that capture all relevant aspects of a system. This requires a deep understanding of the system's behavior, as well as the availability of reliable data for validation and calibration. Additionally, the computational resources required for running simulations of large-scale systems can be substantial, necessitating efficient algorithms and high-performance computing infrastructure. Furthermore, the interpretation of simulation results and the translation of findings into actionable insights can be a daunting task. It requires interdisciplinary collaboration between domain experts, data scientists, and simulation specialists to ensure that the outcomes are meaningful and applicable in real-world scenarios. Moreover, there is a need for continuous refinement and validation of simulation models to keep them relevant and accurate in dynamic environments. From a human perspective, the use of system modeling and simulation can evoke a sense of empowerment and confidence in decision-making. Professionals who leverage these tools are better equipped to anticipate challenges, explore innovative solutions, and make evidence-based choices. This can lead to a greater sense of control over complex systems and a reduced fear of the unknown, ultimately fostering a culture of continuous improvement and resilience. In conclusion, system modeling and simulation are indispensable tools that have far-reaching implications across various industries and societal domains. While they offer tremendous potential for innovation and progress, it is essential to acknowledge the challenges associated with their application and to work towards overcoming them through collaboration, innovation, and a commitment to excellence. As technology continues to advance, the future of system modeling and simulation holds great promise for shaping a more efficient, sustainable, and prosperous world.。
《锦绣金华》八年级教案
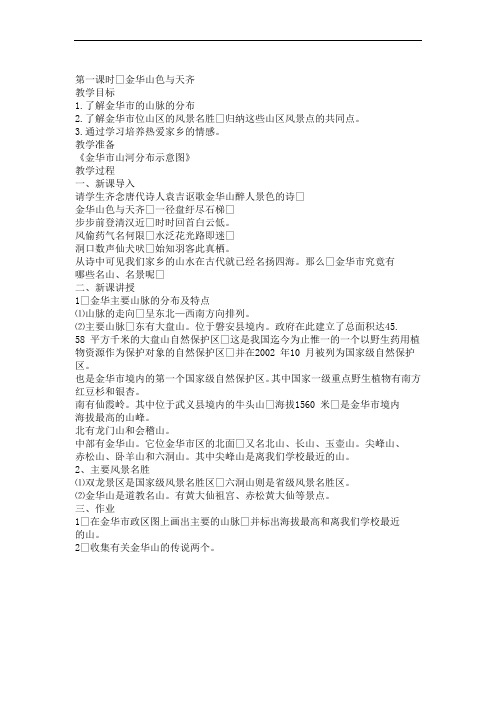
第一课时���金华山色与天齐 教学目标 1.了解金华市的山脉的分布 2.了解金华市位山区的风景名胜���归纳这些山区风景点的共同点。 3.通过学习培养热爱家乡的情感。 教学准备 《金华市山河分布示意图》 教学过程 一、新课导入 请学生齐念唐代诗人袁吉讴歌金华山醉人景色的诗��� 金华山色与天齐���一径盘纡尽石梯��� 步步前登清汉近���时时回首白云低。 风偷药气名何限���水泛花光路即迷��� 洞口数声仙犬吠���始知羽客此真栖。 从诗中可见我们家乡的山水在古代就已经名扬四海。那么���金华市究竟有 哪些名山、名景呢��� 二、新课讲授 1���金华主要山脉的分布及特点 ⑴山脉的走向���呈东北—西南方向排列。 ⑵主要山脉���东有大盘山。位于磐安县境内。政府在此建立了总面积达45. 58 平方千米的大盘山自然保护区���这是我国迄今为止惟一的一个以野生药用植 物资源作为保护对象的自然保护区���并在2002 年10 月被列为国家级自然保护 区。 也是金华市境内的第一个国家级自然保护区。 其中国家一级重点野生植物有南方 红豆杉和银杏。 南有仙霞岭。其中位于武义县境内的牛头山���海拔1560 米���是金华市境内 海拔最高的山峰。 北有龙门山和会稽山。 中部有金华山。它位金华市区的北面���又名北山、长山、玉壶山。尖峰山、 赤松山、卧羊山和六洞山。其中尖峰山是离我们学校最近的山。 2、主要风景名胜 ⑴双龙景区是国家级风景名胜区���六洞山则是省级风景名胜区。 ⑵金华山是道教名山。有黄大仙祖宫、赤松黄大仙等景点。 三、作业 1���在金华市政区图上画出主要的山脉���并标出海拔最高和离我们学校最近 的山。 2���收集有关金华山的传说两个。
Complete supercriti cal 630 MW on-line simulation system devel opme nt and applicati on of cir culati ng water MCC standby power transformation, t he transformation of de sulfuri zation w aste water, the unit water supply system of compre hensive treatment and dis charge valve modification of c oal mill 5 key technologi cal transformation projects , group healt h is improve d. --S cience and technology i nnovati on is furt her
集成电路设计与集成系统专业完全解析

集成电路设计与集成系统专业(本科、学制四年)Integrated Circuit Design & Integrated System一、专业简介集成电路设计和应用是多学科交叉高技术密集的学科,是现代电子信息科技的核心技术,是国家综合实力的重要标志。
“集成电路设计和集成系统”是国家教育部2003年最新设立的本科专业之一。
目前国内外对集成电路设计人才需求旺盛。
本专业主要以培养高层次、应用型、复合型的芯片设计工程人才为目标,为计算机、通信、家电和其它电子信息领域培养既具有系统知识又具有集成电路设计基本知识,同时具有现代集成电路设计理念的新型研究人才和工程技术人员。
二、培养目标和培养范围培养目标:本专业以集成电路设计能力为目标,培养掌握微电子和集成电路基本理论、现代集成电路设计专业基础知识和基本技能,掌握集成电路设计的EDA工具,熟悉电路、计算机、信号处理、通信等相关系统知识,能够满足集成电路设计领域及相关行业工作需求,从事集成电路设计和集成系统的研究、开发和应用。
具有一定创新能力的适应现代化建设和当前急需的高级技术人才。
培养范围:本专业学生将具有以下方面的知识与能力:1、扎实的数理基础和外语能力;2、充实的社会科学知识,在文、史、哲、法、社会和政经等领域有一定的修养;3、模拟、数字电路基本原理与设计的硬件应用能力;4、信息系统的基本理论、原理与设计应用能力;5、计算机和网络的基本原理及软硬件应用能力;6、微电子及半导体器件基本理论知识;7、集成电路基本理论与原理以及集成电路设计与制造基本知识;8、集成电路设计、制造和EDA技术的基本知识与应用能力。
三、就业方向集成电路以及电子整机设计及制造等领域从事科研、教学、科技开发、生产管理和行政管理等工作;继续深造攻读电子信息类学科的硕士学位。
四、主干课程电路分析基础、信号课组、电子线路课组、计算机课组、微电子课组、电磁场与电磁波、电子设计自动化、集成电路分析与设计、集成电路工艺和版图设计、超大规模集成电路设计、VLSI测试技术、数字系统组成原理和设计技术、嵌入式系统设计、VLSI信号处理等。
- 1、下载文档前请自行甄别文档内容的完整性,平台不提供额外的编辑、内容补充、找答案等附加服务。
- 2、"仅部分预览"的文档,不可在线预览部分如存在完整性等问题,可反馈申请退款(可完整预览的文档不适用该条件!)。
- 3、如文档侵犯您的权益,请联系客服反馈,我们会尽快为您处理(人工客服工作时间:9:00-18:30)。
An Integrated Simulation System for Human Factors StudyYing Wang, Wei ZhangDepartment of Industrial Engineering, Tsinghua University, Beijing 100084, ChinaFouad Bennis, Damien ChablatIRCCyN, Ecole Centrale de Nantes, F44321 Nantes Cedex 3, FranceAbstractIt has been reported that virtual reality can be a useful tool for ergonomics study. The proposed integrated simulation system aims at measuring operator’s performance in an interactive way for 2D control panel design. By incorporating some sophisticated virtual reality hardware/software, the system allows natural human-system and/or human-human interaction in a simulated virtual environment; enables dynamic objective measurement of human performance; and evaluates the quality of the system design in human factors perspective based on the measurement. It can also be for operation training for some 2D control panels.Keywords: virtual reality, human factors, ergonomics, simulation, manikin1.IntroductionHuman factors engineering requires that the design of a system should consider the human’s aspects. In other word, any designed system should be user-friendly. However, in many cases, it is not easy to satisfy this requirement because it is difficult to quantify the human’s requirement or the human’s performance. Sometimes, iterative design at the cost of time and money is necessary. In order to reduce the iterations for time and cost concern, designers may use one of the following three approaches, or a combination of them.The first approach is that the designers have the required quantitative data or enough clear understanding about the users. The data may include the anthropometrical data about the users, the capability of the users, and the specific scenarios of the system use. For example, by having the anthropometrical data and the scenario of use, one can design a chair that is suitable for a specific percentage users and the specific use scenario. However, in many situations, especially for new applications, having these data is not possible.As an alternative approach, one can use physical prototypes to test the design. Now with rapid prototyping technology, one can obtain a physical prototype directly from its CAD model within one day or only hours. By testing the interaction with the user, the designer can easily find the problems and then quickly modify the design and test again. Many applications have shown that the use of rapid prototyping technology can effectively reduce the iteration time and improve the design quality [1]. However, in some cases, the designed system can be so complicated that having its prototype can be time consuming and costly. In some cases, it is even impossible.The third approach is using a virtual prototype instead of a physical one. Arthur et al. have demonstrated that theperception, and spatial knowledge acquisition in the virtual world was indistinguishable from that of the actual physical representation of the real-world layout for certain tasks [2]. According to Buck (1998), ergonomics studies in virtual prototypes allow in early design stages to verify whether the “user interface” of a product is user friendly or not. The typical operations and procedures can be carried out in a way, which is close to reality. The design of the virtual environment and the provided virtual reality interaction tools should allow the user to make all the necessary movements. In this way, ergonomic flaws are very probable to be detected in an immersive virtual environment, and can be corrected at an early design stage, which saves a lot of effort [3]. Wilson (1999) has demonstrated that virtual reality can be a potential tool to support many types of ergonomics contribution, including assessments of office and workplace layouts, testing consequences for reach and access, reconfiguring and evaluation of alternative interface designs, checking operating or emergency procedures, and training for industrial and commercial tasks [4]. Sonoda et al. have developed a power plant training simulator based on virtual reality. The developed training simulator can realize field space as virtual space and can have a fast display of large-scale 3D models, 3D user-interfaces, and the stereoscopic vision and sound effects. The trainee can train in field operations similar to the real world [5].The objective of our research is to develop an integrated system that incorporates virtual reality techniques for human factors study. More specifically at present, this system is for 2D control panel design evaluation and improvement, and for training. However, by having stereo projection, it is potentially possible for 3D system simulations.2.System StructureFor human factors study, the developed simulation system should be able to capture the user’s operation, such as the operator’s hand position, gesture, and be able to recognize the specific operations (e.g. pushing a button, tuning a knob, or turning on a switch etc.). On the other hand, in order to simulate 2D control panels of different size in an actual scale, the system is required to have a screen with enough size for most applications. For accurate measurement of user’s operation, the system should have quick responding features.The main components of our hardware system are shown in Figure 1. There are four CCD cameras to detect the operator’s hand position. A pair of 5DT Data Gloves is used to capture the operator’s finger gesture. By combining the hand position and gesture information, the detection computer can recognize the operator’s operation, such as pushing a button or tuning a knob, etc. The recognized operation is then sent to the simulation computers via LAN network. The simulation computers, depending on the screen size (width: height), may be any number. In our system, the screen size is 7.6 meters wide and 2 meters high. So we used three synchronized channels, which means there are three simulation computers and three projectors. The simulations computers work together, run the simulation scenario and the logic and displays the virtual panel to the wide screen through three 3600 lumens projectors. Then the operator can realtimely interact with the virtual control panel, such a turning on a light by pushing a certain button, or changing a quantity value by tuning a certain knob.For simulation purpose, it is needed to have a designed control panel model. The model includes the geometric model and the control logic model. The geometric model defines the geometry of the panel as well as the textures to make it intuitive. It may be designed using any modeling software packages, such as Multigen Creator TM, 3D MAX, etc. Figure 2 shows one simplified geometric model of a control panel, with six meters, six lights, six buttons, andtwo display screens. The logic model defines the control logics, for example, in order to turn on a certain light, which button or buttons should be pushed. Table 1 lists part of the logics using a relation matrix. According to Table 1, when the operator pushes the “Red” button, the control logics will make “R-1” and “R-2” lights on. At the same time, he/she will hear an audio feedback, which is an alarming audio. The logics will be reflected in the developed program.Figure 1. Hardware components of the simulation systemFigure 2. Geometric model of a simplified control panel3.Motion Tracking and Recognition3.1 Finger Position TrackingFinger position tracking is realized by four CCD cameras. A small active light, as the position marker, is mounted onthe operator’s index finger. CCD apertures are reduced such that only the active lights are visible in the image, allthe other objects in the environment, including the screen with projection, are not visible. This can insure enough contrast between the marker and the other objects. Before simulation, the screen area must be calibrated in order to establish the mapping relationship between the global coordinate system and the pixel coordinate system in the four CCD camera images. In other words, the marker in each specific position in the global coordinate system has a corresponding pixel coordinates in the four CCD images. In this way, during simulation, the detection computer acquires the CCD images every 40 milliseconds and computes the marker’s position according to the calibrated relationship. This can be expressed as follows:⎥⎦⎤⎢⎣⎡⎥⎥⎥⎦⎤⎢⎢⎢⎣⎡=⎥⎥⎥⎦⎤⎢⎢⎢⎣⎡j i a a a a a a z y x 323122211211 (1) where x , y , z are marker’s global coordinates, a 11, a 12, …, a 32 are transformation matrix which is obtained by calibration, i and j are marker’s pixel coordinates in each CCD image [6].Table 1. Part of the control logicsButton AudioEffectLights Screens Meters R-1 R-2 R-3 Y-1 Y-2 Y-3 G-1 G-2 Left Right RedAlarm On On YellowCaution On On WhiteAudio A file On On On On On BlackAudio B file Off Off Off Off Off Off Off Off Off LeftAudio C file On Next Slide RightAudio D file On Next Slide DefaultEnv Flk Flk * R: Red Light Y: Yellow Lights G: Green Lights Env: Environment sound Flk: Flicker3.2 Finger Gesture TrackingFinger gesture information is provided by the data glove. The glove detects each finger’s gesture and expresses the gesture using a number between 0 and 255. By reading the number for each finger, the detection computer can obtain the gesture of each finger.3.3 Operation RecognitionCurrently, we defined three kinds of operations: pushing a button, tuning a knob, and turning on a switch. All these three operations can be recognized by analyzing the finger’s position change and the gesture. They are defined as follows:Pushing a button is TRUE when:1)Index finger (with marker) is in a valid button zone, and2)Index finger is open (gesture value over a certain threshold), and3)The finger acceleration and deceleration are over a certain threshold (i.e. “pushing”).Tuning a knob is TRUE when:1)Index finger (with marker) is in a valid knob zone, and2)Thumb finger and the other four fingers form a “hold” gesture, and3)The relative gesture change of the fingers forms a clockwise or counterclockwise tuningTurning a switch is TRUE when:1)Index finger (with marker) is in a valid switch zone, and2)Thumb finger and the other four fingers form a “hold” gesture, and3)The finger acceleration and deceleration are over a certain threshold (i.e. “push” or “pull”).3.4 Operation AcquiringThe recognized operations above are acquired in a rate of 25 times per second. The acquired data is saved both in the detection computer and in the simulation computer (server computer only, salve computers don’t save). After testing, the researchers can retrieve the data and analyze. For example, how many errors did the operator make, in what kind circumstances did the operator make the errors, what is the shortest, average, and longest response time between certain events (e.g. when an alarm signal is given by a light, how long did it take for the operator to respond to the alarm).4.Multi-Channel SynchronizationThe simulation software is developed on the platform of Multigen Vega TM. Vega has a module of Distributed Vega, which enables multi-computer synchronization [7]. The synchronized computers will not compute and update the next frame if any synchronized computer has not finished the current frame. In our system, we used three simulation computers. One of the computers is defined as server, the other two as slaves. The server computer reads data transmitted from the detection computer via the network, and then distributes the data to the salves through Distributed Vega module.Each of the three computers drives one projector for one display channel on the wide screen. Besides synchronization, it is also needed to overcome the channel overlap problem. Otherwise, the overlapped zone will have a higher brightness than the other areas. This problem is solved by channel overlap blending techniques. By applying a series of continuously changing gray bars in the overlap zone, continuous brightness is achieved along the three channels. Figure 3 shows the blended result of the simulation system. In this simulation, we used the geometric model shown in Figure 2 and the logics listed in Table 1. Due to the CCD specifications (25Hz, 768*576 pixels), currently, this system has a time resolution of 40 milliseconds (25Hz), and a spatial resolution of 0.5-2 cm on the screen, depending on the location of the screen. This performance can be further improved if high-speed CCD cameras with higher image resolutions are used. However, it is also possible to use more CCDs to increase the spatial resolutions. Time resolution seems enough for most testing applications.Figure 3. Multi-channel blending and simulation results5.ConclusionsIn this research, a wide-screen simulation system was developed. It is especially suitable for 2D control panel testing and training. Optical motion tracking and wireless data gloves eliminate the requirement of cables between the operator and computer. Distributed Vega allows synchronization of multi-computers, which enables virtually unlimited number of computers, as well as unlimited number of projectors for large screen simulation. The current stage of this research has demonstrated the feasibility of using virtual reality for human factors study. In the future, practical control panel design evaluation and training application will be tested on this system. More markers will be tracked in order to obtain more information about the whole body movement.AcknowledgementsThe authors would like to acknowledge the financial support from the National Natural Science Foundation of China under grant number 50205014. We would also like to acknowledge the researcher exchange program in Ecole Centrale de Nantes, France, for making the collaborated study possible.References[1]Dai, F. (ed.), 1998, Virtual Reality for Industrial Applications, Springer, Berlin, 2-3.[2]Arthur, E., Hancock, P. A., Chrysler, S. T., 1997, “The Perception of Spatial Layout in Real and VirtualWorlds,” Ergonomics, 40 (1), 69-77.[3]Buck, M., 1998, “Chapter 2: Immersive User Interaction within Industrial Virtual Environment,” appears inVirtual Reality for Industrial Applications, Dan, F. (ed.), Springer, Berlin, 39-60.[4]Wilson, J.R., 1999, “Virtual Environments Applications and Applied Ergonomics,” Applied Ergonomics, 30(1), 3-9.[5]Sonoda, Y., Yoshimoto, N., Morimura, K., Nakatani, T., Matsuzaki, S., 2000, “Development of Plant TrainingSimulator based on Virtual Reality,” Technical Review - Mitsubishi Heavy Industry, 37(1), 19-23.[6]Banerjee, P., Zetu, D., Virtual Manufacturing, John Wiley & Sons, 2001.[7]。