汽车内高压成形技术1
常见内高压成形工艺过程及特点
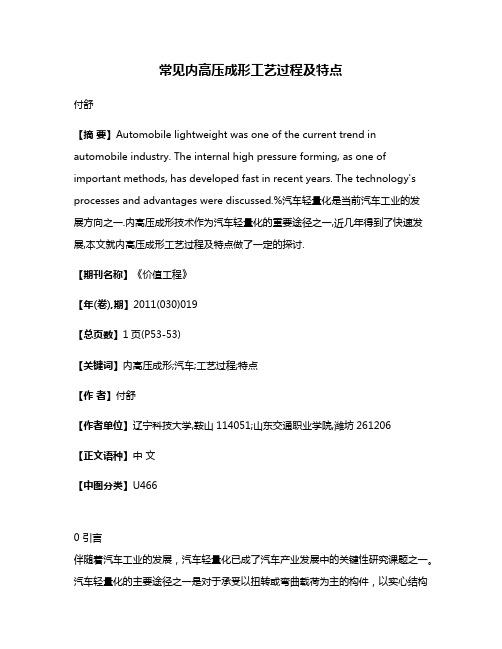
常见内高压成形工艺过程及特点付舒【摘要】Automobile lightweight was one of the current trend in automobile industry. The internal high pressure forming, as one of important methods, has developed fast in recent years. The technology's processes and advantages were discussed.%汽车轻量化是当前汽车工业的发展方向之一.内高压成形技术作为汽车轻量化的重要途径之一,近几年得到了快速发展,本文就内高压成形工艺过程及特点做了一定的探讨.【期刊名称】《价值工程》【年(卷),期】2011(030)019【总页数】1页(P53-53)【关键词】内高压成形;汽车;工艺过程;特点【作者】付舒【作者单位】辽宁科技大学,鞍山114051;山东交通职业学院,潍坊261206【正文语种】中文【中图分类】U4660 引言伴随着汽车工业的发展,汽车轻量化已成了汽车产业发展中的关键性研究课题之一。
汽车轻量化的主要途径之一是对于承受以扭转或弯曲载荷为主的构件,以实心结构代替空心结构。
内高压成形技术就是一种加工空心构件的先进工艺方法,适合制造空心变截面轻量化构件,既可以减轻重量节约材料又可以充分利用材料的强度和刚度,在汽车工业中的应用日益广泛。
1 内高压成形原理及工艺过程1.1 内高压成形原理以管材作为坯料,通过管材内部施加超高压液体和轴向加力补料把管坯压入到模具型腔使其成形为所需零件。
以金属管材为毛坯,在专用模具与设备上利用液体介质在管坯内部产生超高压,成形工作压力通常为200~400MPa,最高1000MPa。
在施加高内压的同时,轴向活塞对管坯的两端施加轴向推力,进行补料。
在两种外力的共同作用下,管坯材料发生塑性变形,并最终与模具型腔内壁贴合,得到形状与精度均符合技术要求的中空零件[1]。
高压氧舱技术参数

高压氧舱技术参数(一)舱体部分1.结构形式:双舱四门舱体。
平底、平封头圆形高压氧舱。
★2.氧舱规格要求:舱体直径23400mm,长度W1oIOomn1。
3.最高工作压力0.2MPa.4.治疗人数:20人,其中主舱16人,过渡舱4人。
人均舱容23疗。
5.舱体设计使用年限220年。
6.舱门形式:一次冲压成型高强度薄壳门。
锁紧方式:低压自动锁紧。
★7.舱门透光尺寸及数量:(高X宽)>1900×1200mm o采用平移门技术。
两端开门。
数量4套。
8.照明方式及数量:冷光源外照明,采用球面照明窗,数量16个。
采用氧舱凸型照明装置。
9.观察窗尺寸及数量:透光直径30Omnb数量8只。
10.摄像窗数量(利用观察窗):8个,主舱6个、过渡舱2个。
I1递物筒数量:2套,透光直径300mm,主舱、过渡舱各1套。
12.舱内座椅及数量:高压氧舱专用活动座椅(外罩:阻燃等级2B1级),共20个。
13.吸氧装具布局方式及数量:采用新式吸氧装置。
主舱16个,过渡舱4个。
14.舱内装饰的设计采用手术室理念,两侧内壁无夹层,减少细菌残留。
金属材料选用1.5mm 镀锌冷轧钢板,表层静电喷塑,高强度,抗磨,抗撞,阻燃等级为A级。
15.舱内地板采用高档地板革铺面。
16.舱内配设吸痰装置3套:主舱2套、过渡舱1套。
17.舱内配设急救供氧装置3套:主舱2套、过渡舱1套。
18.舱内配呼吸机气源接口装置6套:主舱4套、过渡舱2套。
19.配设生物电无损导联装置接口3套:主舱2套、过渡舱1套。
20.舱内配全方位拾音对讲装置5套:主舱3套、过渡舱2套。
21.舱内配无触点感应式应急呼叫报警装置20套:每人位1套。
22.每舱室均设置自动泄压安全阀2套,并配手动紧急卸压装置。
23.其他配置:23.1每舱室均配设药品柜1套。
(二)操作控制台★设备操作控制方式:采用机械手动+电动遥控+计算机自动化操作三种形式;采用集中控制台。
1.计算机控制系统1套。
内高压成形

a
6
2. 成形分类
③变径管内高压成形:非对称大截面
差管件成形困难,通过轴向进给和内压匹配 ,以及贴模顺序控制,实现截面差120%构 件内高压成形,突破100%膨胀率的极限值 。
内高压成形概述
图3 排气系统三元催化内高压管
极限膨胀率:零件某一个截面周长相对 于初始周长的变化率。
是标志变径管内高压成形技术水平的 一个重要指标
避免屈曲的方法:合理选择管材长度、增加预成形工序、控制 工艺参数。
a
15
4. 缺陷形式
起皱:轴向力过大,将产生压缩失稳,即起皱。
皱纹
有益皱纹:可以展平的皱纹
有益皱纹不是缺陷,反而可以作为 一种预成形的 手段。
死皱:加压整形无法展平的皱纹
死皱是一种缺陷,可以通过调节加载路径防止 。
变径管内高压成形技术
a
22
2. 发展趋势
内高压成形特点及发展趋势
①超高压成形 复杂的结构形式和精度、大的壁厚和高强度材料,需要更高的内压,将 发展到600MPa,甚至1000MPa。
② 新的成形工艺 拼焊管内高压成形、双层管内高压成形、内高压成形与连接工艺复合。
③ 超高强度钢成形 随强度增加,塑性降低,将会导致管件开裂,成形难度增大。
a
18
5. 成形区间及加载路线
C起皱区
变径管内高压成形技术
D成形区
A弹性区
图4 轴向应力和内压之间关系示意图
a
B开裂区
19
5. 成形区间及加载路线
σz:轴向应力; σθ:环向应力; λ= σz/ σθ :加载比例参数 η:缺陷因子; Fcr:临界屈曲轴向压应力
变径管内高压成形技术
0 < λ < 1: λ ↑, Fcr ↑ λ >1 : λ ↑, Fcr ↓ 这说明λ= 1.0是一个分水岭值,即无 论缺陷因子如何影响,按照λ = 1.0这 个比例加载关系进行加载是最理想的 加载路径。
汽车后桥壳内高压成形工艺及胀型模具设计

汽车后桥壳内高压成形工艺及胀型模具设计汽车后桥壳是几何形状较为复杂的零件,目前汽车桥壳的主要生产方式是铸造和冲压焊接。
铸造工艺对材料和能源太过浪费,零件的力学性能较差;冲压焊接工艺的焊缝质量难保证,材料利用率较低。
利用液压胀形工艺成形整体桥壳能克服以上缺陷,节约材料和能源,同时工序少、材料利用率高。
本文研究汽车后桥壳鼓包部分的液压胀型工艺。
針对汽车后桥壳特点,采用半滑动式液压胀形工艺,能够有效降低合模压力的整体式的滑动模块,同时固定模块可防止飞边的出现,也考虑了取件问题。
本设计的亮点是整体式的滑动模块具备分担大部分的管坯胀形力,降低设备吨位的作用;设计的预胀形模具和终胀形模具滑动模块部分能够共用,减少模具开发制造费用。
标签:汽车桥壳;半滑动式;液压胀形;模具设计汽车桥壳属于大型复杂异型截面零件,它保护着内部的主减速器,差速器,半轴等零件,并承受着车身重量与车轮传来的力矩。
其作用及性能,要求既有足够的强度和刚度,又要尽量减轻质量;而且在保证桥壳使用要求的前提下,力求结构简单,制造方便,以利于降低成本。
车桥主要有两种生产方式:铸造和冲压焊接。
铸造可以制造出形状较为复杂的车桥,但铸造件重量大,消耗材料和能源多,较为浪费。
冲压-焊接成形工艺较好,废品率低,重量轻,强度高,并且成本较低[1]。
但冲压焊接工艺工序多,费材耗能,焊缝长,对焊缝质量要求较高。
而利用液压胀形工艺生产桥壳则材料利用率高,节省能源和材料,加工工序较少,且加工效率高,易实现机械化、自动化[2]。
壁厚合理,应力分布较好,刚度高,重量轻。
本设计就是要依据图1-1所给的后桥壳相关尺寸,材料为20号碳钢无缝管。
图1-1为设计中桥壳为轻型车后桥壳,鼓包部分的最大直径为440mm,最小直径68mm,长度为1953mm,桥壳壁厚为10mm,均匀管径为127mm。
为了减少变形过程中变形量过大导致径缩胀形失败,选取了直径为127mm,厚度为10mm的管胚,这样可以保证大部分材料不流动就可以满足桥壳设计要求。
管材内高压成形技术

目录第一章绪论 (1)1.1研究背景 (1)1.2管材内高压成形基本原理 (1)1.3管材内高压成形的适用领域 (3)第二章管材内高压成形的影响因素 (4)2.1轴向应力的影响 (4)2.2内压力大小的影响 (4)2.3摩擦系数的影响 (5)2.4起皱的影响 (6)第三章管材内高压成形的设备关键技术 (7)第五章管材内高压成形的工程研发案例 (9)第六章管材内高压成形的展望 (11)第一章绪论1.1研究背景近年来,汽车轻量化是汽车制造业的重要发展趋势。
由于世界能源的紧张和环保问题的日趋严重,汽车工业面临着严峻的挑战:减轻汽车自身重量,提高行驶速度,降低能耗。
除了采用轻体材料以外,汽车轻量化的另一个主要途径是以“空代实”。
这就求促使人们不得不改进传统工艺,创造出适应新经济时代要求的新工艺。
通过合理的结构设计,许多零部件都能采用标准的管材,通过液压成形技术成形结构很复杂的单一整体结构件,代替承受弯曲和扭转载荷的构件,既节省了材料,又发挥了材料的最大效能。
在汽车工业中管材液压成形作为一个非常重要的成形技术已得到了广泛应用,主要用于生产汽车动力系统、排气系统、汽车底盘以及一些结构件。
汽车用排气管件大多为形状比较复杂、轴线有很大变化的零件。
传统成形工艺除铸造成形外,主要采用冲压两个半壳而后组焊成形,或采用管坯进行数控弯曲、扩管、缩管加工而后组焊成形。
这样制造的零件模具费用高、生产周期长、成本高,不适应当前汽车行业在减轻自重、降低成本、提高市场竞争力等方面的要求。
而采用内高压技术制造排气管件可以较精确地控制零件的尺寸精度,便于在后续工序中与其他零件进行装配,且能够进一步减轻系统重量,减少焊缝数量,内表面光滑,排气阻力小,使成形后的产品质量和寿命得到进一步提高。
1.2管材内高压成形基本原理内高压成形(Internal High Pressure Forming)是以管材作坯料,通过管材内部施加超高压液体和轴向进给补料把管坯压入到模具型腔使其成形为所需工件。
内高压成形技术在汽车配气凸轮轴加工中的应用研究

( fc f eerho h arcu m n & Of eo R sac nU rpei ahnn eh o g , hn c u q i e t i s o p
能更 好 的合金材 料 , 以使 润 滑 油路 更 加 简捷 、 可 紧凑 , 提 高配气 凸轮 轴 的耐磨 性能 。发 动机空 心凸轮轴 传统 制 造工艺 是采用 圆钢棒 料 、 造 毛坯或铸 造毛坯 , 锻 其加
De st n iy
发动机 功率 密度 的 提 高 , 求 配 气 凸轮 轴 的转 速 要 也要 相应提 高 , 就要 求配气 凸轮轴 不仅要 质量 轻 、 这 润
流畅、 高效 。
滑 良好 , 而且耐磨性要好。因此, 配气 凸轮轴的结构有 所 改进 , 用耐磨 金属 和加工性 能 良好 的金 属组 合 、 采 中
I 罚 : 辜 铷稳 籀 毫
I ocAo aftn Th ly ps u nau geno T i: tM uc i cog r
内高压 成形 技 术 在 汽车 配 气 凸轮 轴 加 工 中 的应用 研究
刘劲松 聂凤 明 康 战 张广平
( 长春 设备 工艺研 究所超 精 密加 工技 术研 究室 , 吉林 长 春 10 1 ) 302 摘 要: 针对汽 车发动 机的 配气 凸轮轴 , 行高压 胀 紧组装成 型技术 研 究 , 进 突破 组装 凸轮轴抗 扭性能提 高 、 相 位角控 制和 高压 密 封及压 力控制等 关键 技术 , 决新 一 代发 动机 凸轮轴 润 滑和 耐磨 问题 , 解 为发 动机 更加趋 于紧凑 化 、 量化 , 轻 以及功 率密度 的进 一步提 高 。 提供 工艺 技术 支撑 。 关键词 : 内高压成 形 配气 凸轮轴 高压 胀紧 功率 密度
金属材料成型_3.5_内高压成型技术
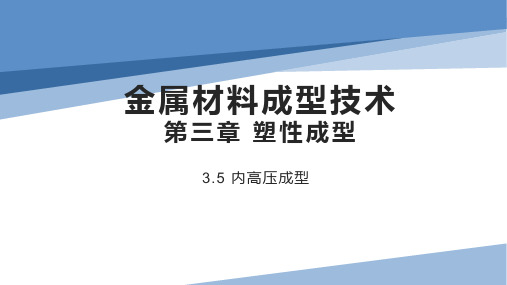
图3-28 内高压成型原理
ON形有下料、弯管、预成型、液压成型、切割等五道主 要工序组成,根据零件结构要素和精度的不同,工序会有增减。
下料,采用切管机按工艺要求切去要求的长度,同时在管端去 除毛刺,避免影响后工序密封。
采用3轴数控预成型机,预成型是内高压成型工序中比较关键的 工序,它的作用是提前对胚件材料进行材料分配和阻尼设置,使内 高压成形工序顺利得到满足液压成形工序需要的胚件。
7)创新性∶克服传统制程限制,应用于新产品设计开发。。
图3-30 变截面高强度管
THREE
3
内高压成型典型应用
内高压成形适用于制造航空、航天、汽车行业的沿构件轴线变化的圆形、 矩形截面或异型截面空心构件。
图3-31 内高压成型在汽车轻量化应用
FOUR
4
内高压成型重点企业
近年来保隆科技通过学习国内外内高压设备成熟技术,并结合长期从事内 高压成形生产经验,自主开发了具有独特创新亮点的3000吨双工位双增压内 高压成形机,已经投入批量生产使用效果达到设计预期。
THANKS
图3-32 中国内高压成型产线增长情况
兴迪源机械自2010年开始组建超高压液力成形技术团队,突破了成形 压力100MPa-250MPa的技术难关,研发出“内高压成型设备”并投入用户 生产现场。至今,公司已是创立超过10年的实力企业,已掌握了成形压 力为500MPa的技术,并吨、成形压力达500MPa以内的各种规格的内高 压成型液压设备数十台套,技术研发成果在国内同行的民营企业中达到优 异水平。
5)提高强度、刚性及疲劳强度∶成形过程中液体具冷却作用,使工件 被"冷作强化",获得比一般冲压加工更高的工件强度。以散热器支架为例, 垂直方向提高39%∶水平方向提高50%。
内高压成型工艺

内高压成型工艺内高压成型工艺是一种常见的塑料成型工艺,通过将高温高压的流体塑料注入模具中,使其在模具内形成所需的形状,然后冷却固化,最后取出成品。
内高压成型工艺具有成型速度快、成型精度高、产品表面光滑等优点,被广泛应用于汽车、家电、电子、建筑等领域。
内高压成型工艺的核心是模具的设计和制造。
模具是内高压成型的关键工具,在成型过程中起到承载和塑形的作用。
模具的设计需要考虑产品的形状、尺寸、材料特性等因素,以确保成型后的产品符合要求。
同时,模具的制造需要采用高精度加工设备和工艺,以保证模具的精度和寿命。
在内高压成型过程中,首先需要将塑料料粒加热至熔融状态,形成熔体。
然后,将熔体注入模具中,通过模具的形状和结构使熔体充满整个模腔。
在注入过程中,需要控制注射速度和压力,以确保熔体填充充分且均匀。
注入完成后,需要保持一定的压力,使熔体在模具内冷却和固化。
最后,打开模具,取出成品。
内高压成型工艺可以实现复杂形状和细节的成型,因此被广泛应用于汽车行业。
例如,汽车车身的内饰件、仪表盘、门板等都可以通过内高压成型工艺来制造。
内高压成型可以保证产品的精度和强度,同时具有良好的外观质量,满足汽车对外观和功能的要求。
除了汽车行业,内高压成型工艺还在其他领域有着广泛的应用。
在家电行业,空调壳体、洗衣机外壳等产品都可以使用内高压成型工艺来制造。
在电子领域,电视机外壳、电脑外壳等产品也可以通过内高压成型来实现。
在建筑领域,一些装饰材料、管道等也可以采用内高压成型工艺来生产。
内高压成型工艺相对于其他成型工艺具有一定的优势。
首先,成型速度快,可以大大提高生产效率。
其次,成型精度高,可以生产出尺寸精确的产品。
此外,内高压成型工艺还可以生产出表面光滑、质量稳定的产品,满足市场对产品质量的要求。
内高压成型工艺是一种重要的塑料成型工艺,具有广泛的应用前景。
通过不断改进工艺和技术,可以进一步提高成型效率和产品质量,满足市场对高品质产品的需求。
- 1、下载文档前请自行甄别文档内容的完整性,平台不提供额外的编辑、内容补充、找答案等附加服务。
- 2、"仅部分预览"的文档,不可在线预览部分如存在完整性等问题,可反馈申请退款(可完整预览的文档不适用该条件!)。
- 3、如文档侵犯您的权益,请联系客服反馈,我们会尽快为您处理(人工客服工作时间:9:00-18:30)。
一、内高压成形技术分类和特点按工艺过程的不同,我们将内高压成型件分为3类:
1 变径管
2 弯曲轴线异型截面管
3 多通管
变径管的工艺过程
n1填充阶段:管材放入下模,闭合上模,充满液体,排除气体,重头密封。
n2成形阶段:管内液体加压胀形,两端冲头推进补料,除过渡圆角管材基本贴靠模具。
n3整形阶段:提高内压,使管材完全贴靠模具,基本无补料。
缺陷类型及解决方案
n屈曲:成形初期没有建立足够的内压,施加了过大的轴向力造成。
n起皱:成形中后期,内压足够足够的情况下也可造成起皱。
n开裂:轴向压力及补料量不足的情况下,在内压连续作用下管材过渡膨胀超过其极限膨胀率而导致。
n解决:均可通过改变加载曲线解决。
曲线零件的工艺过程
n弯曲:保证管材轴线与产品保持一致,为预成型和内高压成型做好准备,数控弯管机,先进绕弯工艺,要注意控制壁厚变化。
n预成型:通过预成型使截面变化较大部位得到充分补料。
n内高压成型及液压冲孔:
缺陷类型
n开裂
弯曲段外侧:管材弯曲过程造成
多边形截面过渡区:加载曲线的影响
焊缝热影响区:焊接条件
n死皱:管材直径过大、分模面形式,尤其是预成型分模面。
n飞边:零件某处截面特殊,预成型截面和内高压分模面设计不合理导致,模具闭合时造成。
后续工序
n液压冲孔:在液体压力的支撑作用下,利用冲头将管材分离的一种冲孔方法。
一般采用冲孔弯曲。
种类:由内向外冲孔、由外向内冲孔。
n管端切割:使用激光切割机。
内高压成型管材
原材料
n低碳钢
n低合金高强钢
n不锈钢:奥氏体不锈钢304和1Cr18Ni9Ti,耐热抗氧化铁素体不锈钢429和309(发动机歧管)
n铝合金:5000系(飞机火箭管件)、6000系(汽车及自行车)、7000系
n铜合金
n钛合金:纯钛和TC4
n镍基合金
管材种类和规格
n无缝管:无焊缝,力学性能一致性好,由于加工偏心,周向壁厚分布不均。
n电阻焊管(ERW):有加工硬化现象,导致不同部位屈服应力不同,焊缝隆起应用刀具刮除,有时可保留内部隆起,但有高度限制,焊缝和热影响区容易开裂。
n拉拔管(DOM)
n激光焊管:
内高压成形件优势(与冲压焊接件相比)
(1)减轻质量,节约材料
Ø结构件:20%-30%;轴类件:30%-50%50%
1.36
2.72仪表盘支梁34%7.912
副车架24%11.516.5
散热器支架减重内高压成形件(kg )冲压件
(kg )
名称(2)可减少零件数量、后续机械加工和组装焊接量:副车架(6-1)、仪表盘支架(17-10)
(3)提高强度与刚度,尤其疲劳强度:冷作硬化、无焊点连接点
(4)材料利用率高。
内高压件材料利用率:95%-98%,冲压件:60-70%
(5)降低生产成本,降低15~20%,模具费用降低20~30%。
三、国外内高压成形技术在汽车上应用现状和范围
四、内高压成形设备与模具
内高压设备组成
n合模压力机
n高压源
n水平缸
n液压泵站
n水压系统
n计算机控制系统
我公司的优势
n技术成熟:依托哈工大技术优势,有成熟产品。
n价格低廉:相对国外,技术、设备、成品件。
n前期试制:产品前期开发数据阶段,可提供样件试制。
n政策优势:首次合作,价格优惠。
谢谢!敬请指正!。