V8发动机曲轴有限元分析
基于ANSYS Workbench的V8发动机曲轴有限元模态分析

【 摘
要】 曲轴是发动机最重要的部件之一 , 其强度 、 刚度 可以决定发动机的性能, 只有强度、 刚度
合格 的曲轴才 能保 障发 动机 的正常运行 。 利用 Sl Wok 建 立 了一 个高速 赛车 V 发 动机 的曲轴模型 , oi rs d 8 并将 曲轴模 型保存 为 I E G S格 式导入 到有 限元 分析软 件 A S SWokec N Y rbnh中, 最后 对 曲轴模 型进行 了 有 限元模 态分析 , 获取 了曲轴 的前 1 固有频 率和相 应振型 。模 态分析a kh. sa l t aodtersnn e q e c g n w i i e oip oete z i h r s be o v i eo a c u nyr i h hw l hl t m r h ao f n a l  ̄i h eo, c l p v
L u nZ N o gj n Y i - a gZ A G L n - ig V D a ,E G D n-i , U Xa yn ,H N o g pn a o ( c ol f rnp r t na dA t t eE gn eig Xh aU iesy C eg u6 0 3 , hn ) S h o o a sot i n uo i n ie r , iu nvri , h n d 10 9 C ia T ao mo v n t
d . dar eec aao ep r na m d ayi i o ti d w ih rv e ert a bs r e An frn ed x ei t a a l s s ban . hc o i sat oe c aif e t f e m lo ln s e p d h il so
r i it ad i - a t akh . ea ly n esn o h c sa lbi Z p f e r f n t f
MSC柴油发动机曲轴疲劳分析示例
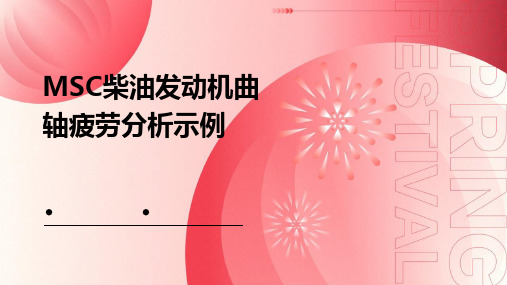
曲轴疲劳寿命预测
01
应力-寿命法(S-N法)
通过测试不同应力和循环次数下材料的断裂寿命,建立应力与寿命的关
系曲线,用于预测曲轴的疲劳寿命。
02
局部应变法(ε-N法)
通过测量曲轴局部区域的应变和循环次数,计算材料的疲劳寿命。该方
法考虑了应力集中的影响,更适用于预测曲轴的疲劳寿命。
03
有限元分析(FEA)
曲轴疲劳损伤机制
弯曲疲劳
由于周期性的弯矩作用,曲轴在 应力集中的位置(如轴颈和曲拐 的过渡区域)容易发生弯曲疲劳
断裂。
扭转疲劳
周期性的扭矩作用使曲轴在轴颈和 曲拐的过渡区域产生剪切应力,可 能导致扭转疲劳断裂。
热疲劳
由于温度变化引起的热应力,可能 导致曲轴材料内部产生微裂纹,进 而扩展形成疲劳裂纹。
详细描述
该案例针对曲轴的结构和工艺参数进行了优化设计,如改变曲轴的形状、增加 加强筋等。通过有限元分析和疲劳试验验证了优化设计的有效性,发现这些改 进能够显著提高曲轴的抗疲劳性能和疲劳寿命。
05
结论与展望
疲劳分析在MSC柴油发动机曲轴设计中的重要性
疲劳分析是评估曲轴结构强度和寿命 的关键手段,通过分析可以预测曲轴 在不同工况下的疲劳损伤和断裂风险。
在船舶领域,柴油发动机曲轴作为船 舶推进系统的关键部件,需承受高负 荷和极端环境条件下的运转。
在发电机组领域,柴油发动机曲轴用 于驱动发电机,要求具有高效率和可 靠性。
02
疲劳分析基本原理
疲劳定义与分类
疲劳定义
疲劳是由于材料或结构在循环应力或 应变下逐渐损伤和失效的现象。
疲劳分类
根据应力类型和循环特性,疲劳可分 为高周疲劳和低周疲劳,其中高周疲 劳是指循环次数大于10^4的疲劳,低 周疲劳是指循环次数小于10^4的疲劳 。
通过FEA、MBS 和 FEMFAT 对曲轴进行疲劳强度分析

内部节点
接口节点
Author: Robert Wahlmüller
Date: July 2007
7
Component Mode Synthesis 部件模态合成 (Craig Bampton Method)
假定: 柔体具有小的变形 => 部件模态的线性叠加
u
physical coordinates 物理坐标 Modal (Generalized) Coordinates 模态坐标 变换矩阵,包含部件模态
Author: Robert Wahlmüller
Date: July 2007
10
Component Mode Synthesis 部件模态合成 部件模态合成的主要优点:
大大降低了柔体的自由度数量
eg.: dof 100.000
MKK MKI MIK MII
. .K u . .I u
+
. .C q . .N q .. qC .. N q
16
Two Mass Flywheel 双质量飞轮
弹簧和质量系统 (刚性部件) 主要质量通过约束或是刚度进行操纵
齿轮箱 / 试验台轴的影响是主要的
主和次质量的连接通过应用径向约束 (inline) 或是刚度 扭曲和倾斜连接通过应用非线性弹簧(从供应商得到)
M
φ
range 1 range 2 limit stop
= u =
q
C 约束模态Constraint Modes矩阵
q
N 固有模态Normal Modes矩阵
uK
uI
=
I
C
0
N
qC (=uK)
*
qN
毕业设计(论文)-发动机曲轴连杆机构仿真及有限元分析设计-adams

全套图纸加扣 3012250582曲轴连杆活塞组件虚拟样机的建立学院名称:机械工程学院专业班级:机械设计制造及其自动化0501 班学生姓名:号:学指导教师:2009 年6 月摘要柴油机的气缸、活塞、连杆、曲轴以及主轴承组成一个曲柄连杆机构。
柴油机通过曲柄连杆机构,将活塞的往复运动转换为曲轴的回转运动,使气缸内燃油燃烧所产生的热能转变为曲轴输出的机械功。
可见,曲柄连杆机构是柴油机重要的传力机构。
对其运动和受力情况进行分析和研究,是十分必要的。
这种分析研究既是解决柴油机的平衡、振动和总体设计等课题的基础,也是对其主要零部件在强度、刚度、磨损等方面进行计算和校验时的依据。
本文在曲柄连杆机构理论分析的基础上,利用多体动力学理论,三维造型软件Pro/E 及动力学分析软件ADAMS对内燃机曲柄连杆机构的动力学问题进行了虚拟样机仿真分析。
并以CT484Q柴油机为研究对象,在Pro/E中建立CT484柴油机曲柄连杆机构的虚拟样机模型,导入ADAMS中进行动力学分析,绘制出虚拟样机模型中各连接位置处受力仿真结果曲线。
通过本文的研究,展示了一种简捷、高效的机械设计分析手段,对今后同类型的研究乃至更大规模的仿真分析积累了一些经验。
本文的研究也可以为今后内燃机机构的造型、优化设计提供参考依据。
关键词:内燃机,曲柄连杆机构,ADAMS,虚拟样机,仿真AbstractThe Cylinder, piston, connecting rod, crankshaft and main bearings of diesel engine Compose of a crank-connecting rod mechanism. Through the crank-connecting rod mechanism, Diesel engine convert the piston reciprocating motion to the rotary movement of the crankshaft, and make the cylinder generated by fuel combustion energy into mechanical work output of the crankshaft. This shows that diesel engine crank linkage is an important body for transmission force. It is necessary to analysis and research its movement and force. This analysis is the foundation to solve the balance of diesel engine, vibration and overall design, It is the basis for validate and calculate the strength, stiffness, wear, etc.In this paper, based on the theoretical analysis of crank-connecting rod mechanism, use of multi-body dynamics theory, and use the three-dimensional modeling software, Pro/ E and the dynamic analysis software ADAMS to carry out crank and connecting rod for internal combustion engine body dynamics simulation of a virtual prototype simulation. And study CT484Q Diesel Engine, established linkage of the virtual prototype of diesel engine model In Pro/ E, then do dynamic analysis in ADAMS and draw the connection position of the power curve for the simulation result.Through this paper, the study demonstrated a simple and efficient means of mechanical design and analysis for future research as well as the same type of simulation analysis and accumulate some experience. The study of this paper can provide reference for the modeling and optimal design.Key words: Internal Combustion Engine, Crank-connecting rod mechanism, ADAMS, Virtual Prototyping目录第一章绪论··················································1.1 研究的意义···············································1.2 内燃机曲柄连杆机构的工作特点以及难点·····························1.3 国内外研究及手段···········································1.3.1计算机辅助设计(CAD)·····································1.3.2 多体动力学分析(MBS)···································1.3.3 有限元分析···········································1.3.4优化设计理论··········································1.4 主要研究内容和方法··········································第二章曲柄连杆机构的动力学理论分析·······························2.1 内燃机工作过程分析··········································2.1.1压缩始点气体状态·········································2.1.2压缩终点气体状态········································2.1.3燃烧过程及燃烧终点气体状态·································2.1.4膨胀终点气体状态········································2.2 曲柄连杆机构的运动分析·······································2.3曲柄连杆机构的动力学分析······································2.3.1曲柄连杆机构的质量换算····································2.3.2曲柄连杆机构的惯性力和惯性力矩······························2.3.3曲柄连杆机构的动力学分析··································2.4 内燃机工作过程计算··········································第三章曲轴连杆活塞组件的虚拟样机································3.1Pro/E 系统的建模原理及其特点····································3.1.1参数化设计············································3.1.2 特征建模的基本思想······································3.1.3全相关的单一数据库······································3.2 曲柄、连杆、活塞组件几何模型的建立以及装配··························3.2.1活塞组件的建模·········································3.2.2 连杆组建的建模········································3.2.3曲轴组件的建模·········································3.2.4曲轴连杆活塞组件的总装配···································第四章曲柄连杆机构的运动学和动力学分析·····························4.1ADAMS简介及其基本原理·······································4.1.1 运动学和动力学基本概念···································4.1.2 ADAMS中多刚体动力写方程的建立······························4.2ADAMS 中的运动学和动力学分析···································4.2.1 曲柄连杆机构刚体模型的转化和输入·····························4.2.2 曲轴轴系多刚体动力学仿真分析·······························第五章结论与展望·············································5.1 总结····················································5.2 展望····················································致谢························································参考文献·····················································附录·························································第一章绪论1.1研究的意义内燃机是目前世界上应用最广泛的热动力装置,自1860年法国人设计出第一台煤气发动机以来,内燃机无论是在结构上还是在性能上都较以前有了很大的进步。
某V8发动机曲轴三维设计及有限元分析
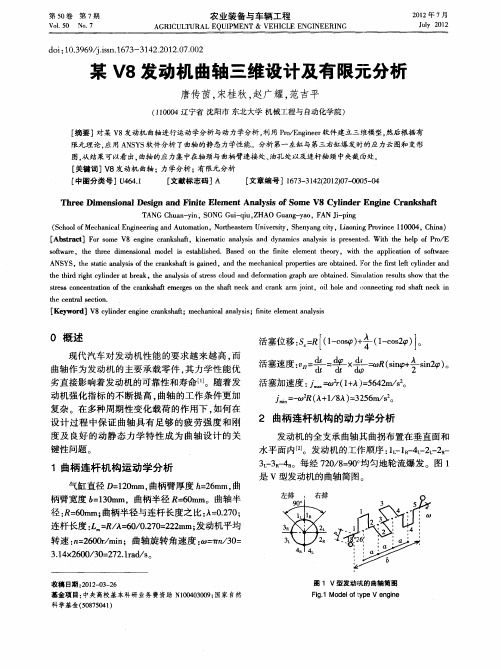
Vo . 0 I 5 No 7 .
农 业装 备与 车辆 工程
A RC L U A Q IME T&V H C EE G N E I G G IU T R LE U P N E IL N IE R N
21 0 2年 7月
J l 2 1 uy 0 2
d i1 . 6 /.s.63 3 4 . 1 . . 2 o:03 9js 17 — 1 2 0 20 0 9 in 2 7 0
0 概 述
现代 汽 车 对 发动 机 性 能 的要 求越 来 越 高 , 而 曲轴 作 为 发 动机 的主要 承 载 零件 . 力 学性 能优 其
活塞位移: = 1c ̄q 1c 2)。 S R ( o )A(-o t f x f- s - sp
活 速 := × Ri 争i ) 塞 度Ⅱ 誓= 罟 (p s 。 s+ n m
sescnet t no ecakhfe re ntesa ekadca ka l o t ihl adcn et gr h t eki t s o cnr i f rnsat megs h t c n rn r i ,o oe n o nc n dsa c r ao h t o h f n n jn l i o f n n
T ANG h a - i ,S C u n yn ONG G iqu, HAO a g y o,F u— i Z Gu n - a AN ipn J- ig
(c olf c aia E gne n dA t t n N r es r nvrt, h nagc y Lann rv c 10 4 C i ) Sh o o hncl nier g n u ma o , ot at nU iesy S eyn i , i ig oi e10 0 , hn Me i a o i h e i t o P n a
基于有限元法的某柴油机曲轴的模态分析

从上面抽样点 图可知 8 号为工业 区 , 问题( 1 ) 分析得 出工业 区污染 广泛 、 集 中。工业污染 物有废 水 、 废气、 废渣, 可 以很好 的解释上 图走 势 。2 2号为主干道 区 , 分析可 知 , 主干 道区除 As 、 M轻 度污染外 , 其余 均为 中强级 别污染 。整合 模型 ( 一) 和模型 ( 二) 均得出同一结果 , 且都 经过严格的科学论证 , 则可以认定 : 8 、 2 2 和3 1 0 号点或者其周围为污染源。 参考文献 [ 1 ] 柴 立元等. 环境影响评价 学. 长沙: 中南大学出版社 , 2 0 0 6 [ 2 ] 祁轶 宏等. 基于 GI S的铜陵地 区土壤 重金 属元素的 空间分 布. 安 徽: 合肥 工业 大学学报 , 2 0 0 6 . [ 3 ] 韩 中庚. 数 学建模竞赛 北京 : 科 学出版社 , 2 0 0 7 . [ 4 ] 赵剑 强. 城 市地表径 流污染与控制 北京 : 中国环境科 学出版社 ,
量 的三维 曲面 图的对 比分析 , 确定 污染 源的代表点( 可能不止一个 ) , 从 而找 出第一组污染源。 模型求解 :
抽 样 点 厨, 般 色越 睚 高度 越 高
1 4 . 5 0 6 3 6 6 3 1 . 9 1 7
1 9 8 2 8 7 8 8 6 5 2 7 1 9 2 2 4 . 5 6 8 7 8 4 . 0 7 1 5 1 4 2 9 6 9 8 2 4 9 . 4 6 6 6
2 0 0 2
基 于有限元 法的 票柴 油机 曲轴的模态分析
张连 钵 苏铁 熊 王 军 马 电虎 ( 1 . 中北 大 学机 电工程 学院 2 . 山 西天地 煤机装 备有 限公 司)
[ 摘 要] 本 文应 用有限元理论 , 对某柴油机 的曲轴进行 了动态特 性研 究。首先 , 在P RO/ E中建立 了柴油机 曲轴 的三维实体模 型 , 利 用A N S Y S 对其进行 自由模 态分析 , 得到 了前 1 0 阶的 固有频率和振型 ; 其 次, 利 用计 算结果, 对振动 危险区域进行 了分析 , 并研究 了曲 轴模 态的规律 , 为曲轴的结构优 化设 计方法提供 了一定的参考依据 。 [ 关键词] 曲轴 有 限元 法 模 态分析 曲轴是发动 机 中最为 重要 、 承受载 荷最为复 杂的零件之一 。曲轴 在工作过程 中, 要承受多种载荷共 同作用 , 且 随着发动机工作条件的复 杂化 , 要求 曲轴在满足静态 刚强度要求 的基 础上 , 还必须要满足动态特 性的要求 I 。对发动机 的曲轴进行模 态分析 , 可在设 计过程 中比较准确 地得到 曲轴 的固有频率和振型, 有助 于获取 曲轴 的动态特性 , 所得到 的 相关数据对于曲轴设计的优化和改进具有重要意义。
有限元分析实例.

板端接触法
共同曲率法
精益设计 国 外 强调考虑结构的大变形 准确模拟片间的接触状态
钢板弹簧的设计参数
普通多片式钢板弹簧
:主要用于货车和大客车上
模型分析云图
安装孔处应力
最大应力都 在盘安装孔 外侧,并且 应力相对集 中,除了安 装孔外侧, 其他位置所 受的应力都 较小
盘周应力
盘周摩擦表面 上的机械应力 并不明显,与 帽盘接连孔外 侧的应力相比 非常小。只有 机械应力作用 于盘周不致出 现破坏
连接位置处应力
可以看出连接 处应力并不大, 有应力位置只 在刹车盘受摩 擦力和夹紧力 一侧,应力大 小也随周期变 化。机械应力 对连接处没有 过多要求
分析结果
2、Equivalent (von-Mises) Stress(等效应力)
根据分析报告,等效应力最大 值为65.418MPa,且等效应力在整 个运动行程中呈周期性变化。在等 效应力云图中,等效应力主要分布 在活塞杆上。因此,曲柄连杆在工 作时,其主要承受的应力在与活塞 直接相连的杆上。
分析结果
5、施加载荷 根据曲柄连杆工 作情况,综合第一类 自由约束和第三类表 面载荷对有限元模型 进行载荷定义。载荷 施加具体如图4,大 小为0.3MPa。 6、运动参数设定 曲柄转速设置 为2.09 rad/s
三、分析结果
1、Total Deformation(总变形 )
根据分析报告,总变形的最大 值为1.9232mm,在整个运动过程 中其分布呈抛物线状,变形最大 且对结构有危险的是曲柄与连杆、 连杆与活塞杆连接处。这也是设 计中需要校核和加强的地方。
Workbench是ANSYS公司提出的协同仿 真环境,解决企业产品研发过程中CAE软件 的异构问题。提供了全新的“项目视图 (Project Schematic View)”功能,将整个 仿真流程更加紧密的组合在一起,通过简单 的拖拽操作即可完成复杂的多物理场分析流 程。Workbench 所提供的CAD双向参数链接 互动、项目数据自动更新机制、全面的参数 管理、无缝集成的优化设计工具等,是 ANSYS 在“仿真驱动产品设计”方面达到前 所未有的高度。
基于有限元法的某柴油机曲轴的模态分析
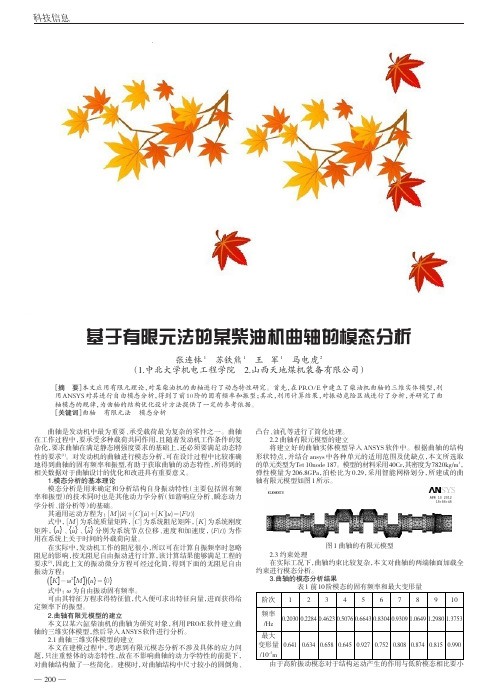
As
Cd
Cr
CuBiblioteka HgNiPb
Zn
功能 区
14.09979 1204.475 707.4908 309.2679 674.7762 37.13 474.2679 2909.131 一
11.66978 946.5542 218.9285 2310.813 12578.69 28.07566 364.8962 1637.318 二
基于有限元法的某柴油机曲轴的模态分析
张连钵 1 苏铁熊 1 王 军 1 马电虎 2 (1.中北大学机电工程学院 2.山西天地煤机装备有限公司)
[摘 要]本文应用有限元理论,对某柴油机的曲轴进行了动态特性研究。首先,在 PRO/E 中建立了柴油机曲轴的三维实体模型,利 用 ANSYS 对其进行自由模态分析,得到了前 10 阶的固有频率和振型;其次,利用计算结果,对振动危险区域进行了分析,并研究了曲 轴模态的规律,为曲轴的结构优化设计方法提供了一定的参考依据。 [关键词]曲轴 有限元法 模态分析
— 200 —
凸台、油孔等进行了简化处理。 2.2 曲轴有限元模型的建立 将建立好的曲轴实体模型导入 ANSYS 软件中。根据曲轴的结构
形状特点,并结合 ansys 中各种单元的适用范围及优缺点,本文所选取 的单元类型为Tet 10node 187。模型的材料采用40Cr,其密度为7820kg/m3, 弹性模量为 206.8GPa,泊松比为 0.29,采用智能网格划分,所建成的曲 轴有限元模型如图 1 所示。
曲轴是发动机中最为重要、承受载荷最为复杂的零件之一。曲轴 在工作过程中,要承受多种载荷共同作用,且随着发动机工作条件的复 杂化,要求曲轴在满足静态刚强度要求的基础上,还必须要满足动态特 性的要求[1]。对发动机的曲轴进行模态分析,可在设计过程中比较准确 地得到曲轴的固有频率和振型,有助于获取曲轴的动态特性,所得到的 相关数据对于曲轴设计的优化和改进具有重要意义。
- 1、下载文档前请自行甄别文档内容的完整性,平台不提供额外的编辑、内容补充、找答案等附加服务。
- 2、"仅部分预览"的文档,不可在线预览部分如存在完整性等问题,可反馈申请退款(可完整预览的文档不适用该条件!)。
- 3、如文档侵犯您的权益,请联系客服反馈,我们会尽快为您处理(人工客服工作时间:9:00-18:30)。
V8发动机曲轴有限元分析唐传茵1,马岩2,朱博1,胡作健1(1.东北大学机械工程与自动化学院,辽宁沈阳110819;2.沈阳仪表科学研究院,辽宁沈阳110004)来稿日期:2012-03-10基金项目:中央高校基本科研业务费资助(N100403009);国家自然科学基金(50875041);沈阳市科学计划项目(F10205175)作者简介:唐传茵,(1979-),女,辽宁海城人,博士,讲师,主要从事车辆动力学及控制技术,系统仿真技术及应用研究1引言现代汽车对发动机性能的要求越来越高,而曲轴作为发动机的主要承载零件,其力学性能优劣直接影响着发动机的可靠性和寿命。
随着发动机强化指标的不断提高,曲轴的工作条件更加复杂。
在多种周期性变化载荷的作用下,如何在设计过程中保证曲轴具有足够的疲劳强度和刚度及良好的动静态力学特性成为曲轴设计的关键性问题。
2曲柄连杆机构设计气缸直径D =120mm ,曲柄臂厚度h =26mm ,曲柄臂宽度b =130mm ,曲柄半径R =60mm 。
曲轴半径:R =60mm ;曲柄半径与连杆长度之比:λ=0.270;连杆长度:L m =R /λ=60/0.270=222mm ;发动机平均转速:n =2600r/min 。
发动机的全支承曲轴其曲拐布置在垂直面和水平面内。
发动机的工作顺序:1L-1R-4L-2L-2R-3L-3R-4R 。
每径720/8=90°均匀地轮流爆发。
应用Pro/Engineer 软件,形成完整的曲轴模型,如图1所示。
图1曲轴的完整三维模型Fig.1The complete three dimensional model of the crankshaft3曲轴的有限元静力分析选取第一左缸爆发时和第三右缸爆发时,这两个状态作为计算工况来进行曲轴的静态分析。
每个气缸的一个工作循环有四个行程:进气-压缩-做功-排气。
此发动机的工作顺序:1L-1R-4L-2L-2R-3L-3R-4R 。
3.1第一左缸爆发时第一左缸爆发时曲轴的变形,发图2所示。
由图2可见,曲轴的位移值在靠近第一连杆轴颈中央截面处最大,最大值达到了(1.28×10-6)mm ,如图3所示。
而曲轴其他处的位移都小于此值。
摘要:对某V8发动机曲轴进行运动学分析与动力学分析,利用Pro/Engineer 软件建立三维模型,然后根据有限元理论,应用ANSYS 软件分析了曲轴的静态力学性能。
分析第一左缸与第三右缸爆发时的应力云图和变形图,从结果可以看出,曲轴的应力集中在轴颈与曲柄臂连接处、油孔处以及连杆轴颈中央截面处。
进行模态分析,曲柄臂和主轴颈、曲柄臂和连杆颈相连处是曲轴振动中危险的区域,由振型图可以发现它们是曲轴振动中变形最大的区域。
关键词:V8发动机曲轴;力学分析;有限元分析;模态分析中图分类号:TH16;U464.1文献标识码:A文章编号:1001-3997(2013)01-0211-03Finite Element Analysis of Some V8Cylinder Engine CrankshaftTANG Chuan-yin 1,MA Yan 2,ZHU Bo 1,HU Zuo-jian 1(School of Mechanical Engineering and Automation ,Northeastern University ,Liaoning Shenyang 110004,China ;School of Mechanical Engineering and Automation ,Northeastern University ,Liaoning Shenyang 110004,China )Abstract :For some V8engine crankshaft ,kinematic analysis and dynamics analysis is presented ,with the help of Pro/e software ,and the three dimensional model is established ,based on the finite element theory ,with the application of software ANSYS ,and then the static analysis of the crankshaft is gained ,and the mechanical properties are obtained.For the left with the first cylinder and the right with the third cylinder at break ,the analysis of stress cloud and deformation graph are obtained.Simulation results show that ,the stress concentration of the crankshaft emerges on the shaft neck and crank arm joint ,oil hole and connecting rod shaft neck in the central section.And the mode frequency analysis is obtained ,the mode of vibration diagram indicates that the shaft neck and crank arm joint ,crank pin and crank arm joint constitute the dangerous region of the crank vibration.Key Words :V8Cylinder Engine Crankshaft ;Mechanical Analysis ;Finite Element Analysis ;Mode Frequency AnalysisMachinery Design &Manufacture机械设计与制造第1期2013年1月211图2第一左缸爆发时曲轴的节点位移Fig.2The Displacement of the Crankshaft Nodewith the Outbreak of the First Left Cylinder图3第一左缸爆发时曲轴的节点位移最大处Fig.3The Maximum Displacement of the Crankshaft Nodewith the Outbreak of the First left Cylinder3.2第三右缸爆发时第三右缸爆发时曲轴的变形,如图4所示。
曲轴的位移值在靠近第三连杆轴颈中央截面处最大,最大值达到了(1.21×10-6)mm,如图5所示。
而曲轴其他处的位移都小于此值。
图4第三右缸爆发时曲轴的变形Fig.4The Deformation of the Crankshaftwith the Outbreak of the Third Right Cylinder图5第三右缸爆发时曲轴的节点位移最大处Fig.5The Maximum Displacement of the CrankshaftNode with the Outbreak of the Third right Cylinder 有限元分析得到的曲轴的应力集中在油孔、轴颈与曲柄臂连接处以及连杆轴颈的中央截面等处,最大值为:第一左缸爆发时:σmax=59.426MPa第三右缸爆发时:σmax=58.646MPa曲轴的材料为碳素钢50Mn:强度极限:σB=800MPa屈服极限:σT=370MPa及τT=250MPa弯曲疲劳极限(耐久性):σ-1=340MPa拉伸—压缩的疲劳极限:σ-1p=0.75σ-1=0.75×340=255MPa扭转疲劳极限:τ-1=0.53σ-1=0.53×340=180MPa有限元分析所得的最大应力远小极限应力,曲轴强度符合要求。
4曲轴模态有限元分析4.1发动机曲轴的模态原理文采用Lanczo法进行模态提取(1)给定向量xi;(2)生成向量xi(i=1,2,3,…,:)。
求解:Kx軃i=Mxi-1正交化x軃i=xi-αi-1xi-1-βi-2xi-2,其中,αi-1=x軃iMxi-1正则化xi=xii,其中,βi=x赞iTMx赞i軃軃1/2(3)将广义特征值问题Kφr=MφΩr转化为Lanczos向量类对三角矩阵T标准特征值问题:A=K-1MAxi-1=βixi+αi-1xi-1+βi-1xi-2,其中(i二2,3,…,r),且x={0}将上式写成矩阵的形式:AX=XT,其中:T=α1β2β2α2β3β3α33333333333333333333333,X=x1x2 (x)i33,引人原特征矩阵和Lanczos向量间的变换:准r=XZ其中,准r=φ1φ2……φi33得:TZ=Zλ(4)求解标准特征值问题的部分特征解:Z=z1z2……z i33,λ=dingλii i,原问题的部分特征解:准r=XZ,Ωr=λ-1;即:W2i=1λi(i=1,2……r)设定计算十阶固有频率,频率范围设置为(0~10000)Hz。
4.2模态计算结果与分析由于发动机曲轴体积大,求解过程中将产生上万个方程,因此不可能计算全部的解,但系统较低阶的若干阶固有频率及相应的振型对系统的动力响应影响最大,仅列出对曲轴贡献较大的前10阶模态,第1-10阶频率(Hz)。
如图6~图8所示。
曲轴模态分析结果,如表1所示。
第1期唐传茵等:V8发动机曲轴有限元分析212表1曲轴模态分析表Tab.1TheAnalysisTableoftheVibrationModeoftheCrankshaftSet Frequency Load stepsubstep cumula10.000011120.000012230.000013340.000014450.000015560.00001667246.791778288.071889558.8619910654.8611010NODALSOLUTIONSTEP=1SUB=7FREQ=246.793USUM(AVG)RSYS=0DMX=.374619SMN=.449E-03SMX=.374619.449E-03.08359E.166747.249896.333045.042024.125172.208321.29147.374619图6第七阶振型Fig.6The Seventh Order of the Vibration Mode of the Crankshaft.014793.102096.189397.276699.364.058444.145746.233048.32032.407651NODALSOLUTIONSTEP=1SUB=8FREQ=288.071USUM(AVG)RSYS=0DMX=.407651SMN=.014793SMX=.407651图7第八阶振型Fig.7The Eighth Order of the Vibration Mode of the Crankshaft.00773508473.161724.238719.315714.046232.123227.200222.277217.354212NODALSOLUTIONSTEP=1SUB=9FREQ=558.859USUM(AVG)RSYS=0DMX=.354212SMN=.007735SMX=.354212图8第九阶振型Fig.8The Ninth Order of the Vibration Mode of the Crankshaft通过分析知道:其中,前六阶频率对应振型为刚体自由振动振型,而高阶频率对应的振型为弯曲振型和扭曲振型,因此曲轴的前几阶的频率远小后面的固有频率的值.通过曲轴的振型的数据及动态显示可以发现,曲轴的前六阶固有频率对应为曲轴的刚体自由振动,7,8固有频率对应为曲轴的弯曲变形,第9,10阶频率则对应为曲轴的扭曲变形.在曲轴的振动过程中,弯曲、扭曲是曲轴的主要的变形形式,随着频率的增高,危险振型便有可能发生,这些振型是弯曲和扭转的叠加,在一定的频率范围内甚至成波形扭曲,曲轴的两端的承载部件将承受很大的交变载荷,所以应该加强两端轴承的刚度和强度。