SMC简介
SMC(中国)有限公司
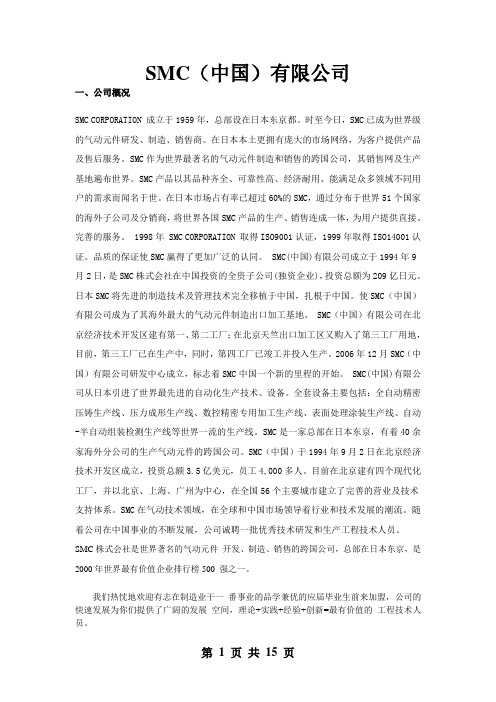
SMC(中国)有限公司一、公司概况SMC CORPORATION 成立于1959年,总部设在日本东京都。
时至今日,SMC已成为世界级的气动元件研发、制造、销售商。
在日本本土更拥有庞大的市场网络,为客户提供产品及售后服务。
SMC作为世界最著名的气动元件制造和销售的跨国公司,其销售网及生产基地遍布世界。
SMC产品以其品种齐全、可靠性高、经济耐用、能满足众多领域不同用户的需求而闻名于世。
在日本市场占有率已超过60%的SMC,通过分布于世界51个国家的海外子公司及分销商,将世界各国SMC产品的生产、销售连成一体,为用户提供直接、完善的服务。
1998年 SMC CORPORATION 取得ISO9001认证,1999年取得ISO14001认证。
品质的保证使SMC赢得了更加广泛的认同。
SMC(中国)有限公司成立于1994年9月2日,是SMC株式会社在中国投资的全资子公司(独资企业),投资总额为209亿日元。
日本SMC将先进的制造技术及管理技术完全移植于中国,扎根于中国。
使SMC(中国)有限公司成为了其海外最大的气动元件制造出口加工基地。
SMC(中国)有限公司在北京经济技术开发区建有第一、第二工厂;在北京天竺出口加工区又购入了第三工厂用地,目前,第三工厂已在生产中,同时,第四工厂已竣工并投入生产。
2006年12月SMC(中国)有限公司研发中心成立,标志着SMC中国一个新的里程的开始。
SMC(中国)有限公司从日本引进了世界最先进的自动化生产技术、设备。
全套设备主要包括:全自动精密压铸生产线、压力成形生产线、数控精密专用加工生产线、表面处理涂装生产线、自动-半自动组装检测生产线等世界一流的生产线。
SMC是一家总部在日本东京,有着40余家海外分公司的生产气动元件的跨国公司。
SMC(中国)于1994年9月2日在北京经济技术开发区成立,投资总额3.5亿美元,员工4,000多人。
目前在北京建有四个现代化工厂,并以北京、上海、广州为中心,在全国56个主要城市建立了完善的营业及技术支持体系。
SMC简介

SMC复合材料性能简介
SMC复合材料是英文Sheet moulding compound的缩写,即片状模塑料。
主要原料由GF(专用纱)、UP(不饱和树脂)、低收缩添加剂,MD(填料)及各种助剂组成。
SMC复合材料具有优越的耐腐蚀性能,质轻及工程设计容易、灵活等优点,其机械性能可以与部分金属材料相媲美,其制造的产品具有良好的刚性,耐变形,使用温度范围大的优点.SMC复合材料是20世纪80年代发展起来的,主要有长纤维增强粒料(LFP)、连续纤维增强预浸带(MITT)和玻璃纤维毡增强型热塑性复合材料(GMT)。
根据使用要求不同要求,产品设计、模具制造、成品制造。
能够根据用户要求设计模具及制造,并将高科技配方融入其中,从而使我们的产品更加合理耐用。
本公司生产的SMC复合材料箱等产品,具有质量好、重量轻、抗冲击、耐老化、阻燃性、密封性能、绝缘性能好,防盗性好(复合材料箱不会偷窃)产品无须油饰保养等优点。
本公司一贯以“质量第一、用户至上”为宗旨,“以质量求生存,以信誉求发展”为目标。
公司里有完善的质量管理体系及专业的售后服务班子。
“对用户在使用过程中反映的问题和建议能及时赶赴现场采纳及解决。
保证能让用户在使用我们的产品时做到“满意、放心、称心”。
SMC、BMC原材料生产简介

SMC、BMC原材料生产简介一项目背景 1.1 SMC BMC简介SMC(Sheet Molding Compound—片状模塑料)和BMC(Bulk Molding Compound-团状模塑料)两种工艺方法原材料基本相同,均系将树脂、玻纤、填料等原辅料预先制得的模塑料,然后将其模压或者注射成型制品。
这两种制造工艺上世纪60年代原发于德国,美国、西欧、日本发展成为规模化、机械化生产热固性玻璃钢制品的主要方法。
发达国家SMC、BMC制品的生产量已经占到热固性玻璃钢产量的30%左右。
我国(大陆)已经引进日本、德国、美国SMC生产线21条(含安装中的3条)、BMC生产线3条,2006年我国SMC、BMC产量达22.5万吨,占到全国热固性玻璃钢产量的16%。
主要产品有汽车零部件、卫星天线反射面、建筑用吊顶、门、绝缘子、接线端子、电表箱、断路器外壳、咪表壳、音响设备壳体、水箱、浴具、桌椅、低压电器、高速公路防眩板、沼气池壳等。
我国大陆SMC模塑料已出口到台湾省、越南、欧洲;模压制品已出口日本、法国、德国。
1.2 SMC、BMC的特点:(1)成本低,密度大:配方中加入大量的填料,如碳酸钙和(或)氢氧化铝等,成本大幅度降低,比一般玻璃钢成型的原材料成本低;(2)生产效率较高,如模压一张SMC椅子面,连辅助时间加模压时间不过7分钟;压一张标准门面,需时3分钟;BMC注射汽车前灯反射面半分钟生产2只;SMC模压直径1.8米(36公斤重)需时6分钟;(3)可生产高品质的制品,可达到A级表面;(4)复杂制品可整体成型,嵌件、孔、台、筋、凹槽等均可同时成型;(5)与通常的热塑性塑料相比,制品耐热性、绝缘性、弹性模量等性能要高一些;(6)闭模成型,生产环境好;(7)原材料利用率高;(8)成型工艺脉络清晰简明,易实现机械化以至半自动化,对工人熟练程度要求不高;(9)可方便地调节玻璃纤维长度和配方,适应不同尺寸、不同复杂程度要求的产品。
SMC培训资料

05
smc培训课程与资源推荐
smc基础培训课程推荐
课程名称:SMC基础教程
推荐理由:该课程详细介绍了SMC的基本概念、原理和方法,帮助学员了解SMC 在制造业中的重要性和应用场景。
该课程包括SMC的基本概念、特点、组成要素、实施步骤等方面的内容,同时结 合实际案例进行讲解,帮助学员更好地掌握SMC的应用。
公司规模与业绩
smc在全球拥有多个分支机构和子公司,主要分布在亚洲、 欧洲和北美。公司的年销售额和利润持续增长,是机械和气 动元件行业的领导者。
smc产品与服务
产品范围
smc提供广泛的气动和机械元件,包括气缸、阀、空气马达、各种传感器和 控制器等。此外,smc还提供各种定制化的解决方案,以满足不同客户的需 求。
SMC材料
SMC材料是一种玻璃纤维增强复合材料,具有轻质、高强度、耐腐蚀等特点。SMC材料 在制造过程中,经过高温高压成型,具有较高的尺寸稳定性和机械强度。
SMC工艺
SMC工艺是一种先进的复合材料制造技术,通过将SMC材料、树脂、填料等原材料混合 ,经过高温高压成型,最终得到高性能的复合材料制品。
SMC材料与工艺的应用
smc专业技能培训课程推荐
课程名称:SMC专业技能提升
推荐理由:该课程针对已经了解SMC基础知识的学员,深入讲解SMC 的专业技能和应用,包括流程优化、生产计划制定、库存管理等方面的
内容。
该课程包括流程优化、生产计划制定、库存管理等方面的内容,同时结 合实际案例进行讲解,帮助学员更好地掌握SMC的专业技能和应用。
VS
影响力
smc对行业的影响力表现在多个方面。首 先,smc通过不断研发和创新,推动气动 和机械元件行业的发展。其次,smc通过 提供优质的产品和服务,帮助客户提高生 产效率和降低成本。最后,smc通过参与 国际标准和行业组织的制定,对行业的发 展方向产生积极影响。
smc是什么材料
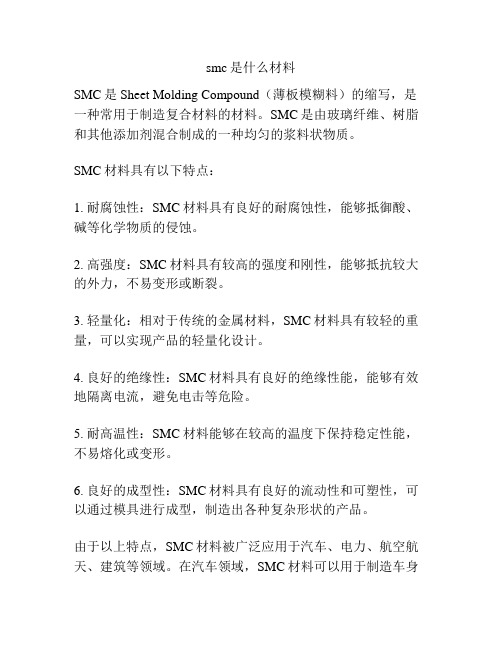
smc是什么材料
SMC是Sheet Molding Compound(薄板模糊料)的缩写,是一种常用于制造复合材料的材料。
SMC是由玻璃纤维、树脂和其他添加剂混合制成的一种均匀的浆料状物质。
SMC材料具有以下特点:
1. 耐腐蚀性:SMC材料具有良好的耐腐蚀性,能够抵御酸、碱等化学物质的侵蚀。
2. 高强度:SMC材料具有较高的强度和刚性,能够抵抗较大的外力,不易变形或断裂。
3. 轻量化:相对于传统的金属材料,SMC材料具有较轻的重量,可以实现产品的轻量化设计。
4. 良好的绝缘性:SMC材料具有良好的绝缘性能,能够有效地隔离电流,避免电击等危险。
5. 耐高温性:SMC材料能够在较高的温度下保持稳定性能,不易熔化或变形。
6. 良好的成型性:SMC材料具有良好的流动性和可塑性,可以通过模具进行成型,制造出各种复杂形状的产品。
由于以上特点,SMC材料被广泛应用于汽车、电力、航空航天、建筑等领域。
在汽车领域,SMC材料可以用于制造车身
外壳、车门、引擎罩等部件,以减轻整车重量,提高燃油经济性。
在电力领域,SMC材料可以用于制造电力设备的外壳、绝缘子等部件,以提供良好的绝缘性能和耐腐蚀性。
在航空航天领域,SMC材料可以用于制造飞机的内饰、座椅等部件,以满足轻量化和耐高温的需求。
在建筑领域,SMC材料可以用于制造建筑材料、装饰板等产品,以提供耐候性和美观性。
综上所述,SMC是一种具有耐腐蚀性、高强度、轻量化、良好的绝缘性、耐高温性和良好的成型性的材料,被广泛应用于各个领域。
SMC复合材料

SMC复合材料SMC(Sheet Molding Compound)复合材料是一种由玻璃纤维、环氧树脂、填料和添加剂等原材料制成的热固性复合材料。
它具有优异的机械性能、耐腐蚀性能和成型性能,被广泛应用于汽车、电力、建筑等领域。
本文将从材料特性、制造工艺、应用领域等方面对SMC复合材料进行介绍。
首先,SMC复合材料具有高强度、高刚度和优异的耐热性能。
由于其含有玻璃纤维等增强材料,使得其在拉伸、弯曲等方面具有出色的性能表现,同时还具有较好的耐热性能,适用于高温环境下的使用。
此外,SMC复合材料还具有良好的耐腐蚀性能,能够抵御化学腐蚀、水腐蚀等,因此在户外环境或者化工领域中有着广泛的应用前景。
其次,SMC复合材料的制造工艺相对简单,生产效率较高。
制造SMC复合材料的工艺流程包括原材料预混、模压成型、固化等步骤,整个生产过程可实现自动化操作,大大提高了生产效率。
同时,由于SMC复合材料的成型性能较好,可以通过模具成型制作出各种形状的构件,满足不同领域的需求。
此外,SMC复合材料在汽车、电力、建筑等领域有着广泛的应用。
在汽车领域,SMC复合材料被用于制造车身外板、车身内饰等部件,其轻质、高强度的特性能够降低汽车整车质量,提高燃油经济性。
在电力领域,SMC复合材料被用于制造变压器壳体、绝缘子等,具有优异的绝缘性能和耐候性,能够保障电力设备的安全稳定运行。
在建筑领域,SMC复合材料被用于制造装饰板、管道等,其耐候性和耐腐蚀性能能够满足建筑材料的长期使用需求。
综上所述,SMC复合材料具有优异的机械性能、耐腐蚀性能和成型性能,制造工艺简单高效,应用领域广泛。
随着材料科学技术的不断发展,相信SMC复合材料在未来会有更广阔的应用前景。
SMC培训资料

案例介绍
该食品公司采用SMC的真空吸盘 和气缸等产品,实现了生产线的 自动化控制,提高了生产效率和 产品质量。
技术特点
真空吸盘具有高精度、高吸附力、 易于更换等优点;气缸具有高可靠 性、低能耗、易于维护等优点。
06
smc未来发展与趋势
smc技术发展方向
持续优化现有技术
防尘型气缸
耐高温型气缸
采用全封闭结构,适用于尘埃较多的工作环 境,具有较好的防尘性能。
适用于高温环境,具有较好的耐高温性能和 稳定性。
smc组件及功能
缓冲件
减少活塞运动过程中的冲击和振动。
活塞
气缸的主要执行部件,可实现往复直线运 动。
缸筒
提供气缸的行程和容纳活塞运动的空间。
密封件
防止气缸内的气体泄漏和外界杂质进入。
smc发展历程
1960年代初期,smc在日本成 立。
1980年代,smc进入中国市场 ,并在北京设立了中国第一家
代表处。
2000年代,smc在中国建立了 多个生产基地,并不断完善研
发和销售网络。
smc产品与服务
气缸
包括普通气缸、无杆气缸、双作用 气缸等,适用于各种自动化设备。
气动阀
包括电磁阀、气控阀、手控阀等, 可实现不同流体介质的控制。
05
smc应用案例与析
汽车行业应用案例
案例名称
XX汽车公司生产线自动化控 制系统
案例介绍
该汽车公司采用SMC的紧凑型气 缸和真空发生器等产品,实现了 生产线的自动化控制,提高了生 产效率和产品质量。
技术特点
SMC的紧凑型气缸具有体积小、速 度快、节能环保等优点;真空发生 器具有高性能、高效率、易于维护 等优点。
片状模塑料(SMC)
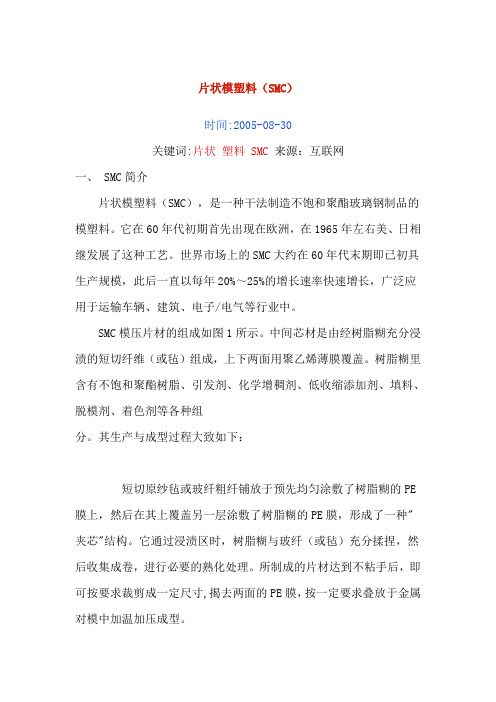
片状模塑料(SMC)时间:2005-08-30关键词:片状塑料SMC来源:互联网一、 SMC简介片状模塑料(SMC),是一种干法制造不饱和聚酯玻璃钢制品的模塑料。
它在60年代初期首先出现在欧洲,在1965年左右美、日相继发展了这种工艺。
世界市场上的SMC大约在60年代末期即已初具生产规模,此后一直以每年20%~25%的增长速率快速增长,广泛应用于运输车辆、建筑、电子/电气等行业中。
SMC模压片材的组成如图1所示。
中间芯材是由经树脂糊充分浸渍的短切纤维(或毡)组成,上下两面用聚乙烯薄膜覆盖。
树脂糊里含有不饱和聚酯树脂、引发剂、化学增稠剂、低收缩添加剂、填料、脱模剂、着色剂等各种组分。
其生产与成型过程大致如下:短切原纱毡或玻纤粗纤铺放于预先均匀涂敷了树脂糊的PE 膜上,然后在其上覆盖另一层涂敷了树脂糊的PE膜,形成了一种"夹芯"结构。
它通过浸渍区时,树脂糊与玻纤(或毡)充分揉捏,然后收集成卷,进行必要的熟化处理。
所制成的片材达到不粘手后,即可按要求裁剪成一定尺寸,揭去两面的PE膜,按一定要求叠放于金属对模中加温加压成型。
二、 SMC应用领域:1、在汽车工业中的应用欧、美、日等发达国家已在汽车制造中大量采用SMC材料,涉及到轿车、客车、火车、拖拉机、摩托车,以及运动车、农用车等所有车种,主要应用部件包括以下几类:1)悬架零件前后保险杠,仪表板等。
2)车身及车身部件车身壳体、硬壳车顶、地板、车门、散热气护栅板、前端板、阻流板、行李舱盖板、遮阳罩、翼子板、发动机罩、大灯反光镜。
3)发动机盖下部件如空调器外壳、导风罩、进气管盖、风扇导片圈、加热器盖板、水箱部件、制动系统部件,以及电瓶托架,发动机隔音板等。
4)车内装饰部件门内饰板、车门把手、仪表盘、转向杆部件、镜子边框、座椅等。
5)其他如泵盖等电气部件,以及齿轮隔音板等驱动系统零件。
其中,尤以保险杠、车顶、前脸部件、发动机罩、发动机隔音板、前后翼子板等部件最重要,产量最大。
- 1、下载文档前请自行甄别文档内容的完整性,平台不提供额外的编辑、内容补充、找答案等附加服务。
- 2、"仅部分预览"的文档,不可在线预览部分如存在完整性等问题,可反馈申请退款(可完整预览的文档不适用该条件!)。
- 3、如文档侵犯您的权益,请联系客服反馈,我们会尽快为您处理(人工客服工作时间:9:00-18:30)。
SMC简介片状模塑料(sheet molding Compound),是一种干法制造不饱和聚脂玻璃钢制品的模塑料。
SMC模压片材的组成:中间芯材是由经树脂糊充分浸渍的短切纤维(或毡)组成,上下两面用薄膜覆盖。
树脂糊里含有不饱和聚脂树脂、引发剂、化学增稠剂、低收缩添加剂、填料、脱模剂、着色剂等各种组份。
其生产与成型过程大致如下:短切原纱毡或玻纤粗纤铺放于预先均匀涂敷了树脂的薄膜上,然后在其上覆盖另一层涂敷了树脂糊的薄膜,形成了一种“夹芯”结构。
它通过浸渍区时树脂糊与玻璃纤维(或毡)充分揉捏,然后集成收卷,进行必要的熟化处理。
SMC具有良好的机械性能与简易加工性,使其成为众所瞩目的材料。
SMC成型一般只需3~6min,具有节省人力与能源,便于大量生产,提高产品质量等优点。
在与各种材料进行对比中,SMC不仅优于钢铁、铝等传统金属材料,而且可与一般热塑性塑料及其它增强材料一争高低。
(1)与金属材料相比,SMC具有优越的电气性能,耐腐蚀性能、质轻以及工程设计容易、灵活等特点;(2)与增强热塑性塑料相比,SMC的成型周期短,成型设备投资低,SMC制品不易变形,机械性能与热变形温度较高,耐化学药品性优,且价格较低;(3)与一般热塑性塑料相比,SMC的物理性能是后者不可比拟的。
SMC特点1、质轻高强:可实现轻量化目标,且具有良好的抗冲吸能性;2、产品设计自由度大:实现产品的流线型设计,通过后粘接技术实现中空结构的成型,减轻产品重量;3、材料流动性好,可实现复杂结构的成型:筋、台结构的一次成型,预埋件的成型,抽芯结构的实现;4、可实现轿车级表面质量水平,可实现SMC部件之间或SMC部件和金属件之间的粘接,可实现随车身进行高温烤漆,线胀系数非常低。
5、低的热导率和良好耐腐性:隔热-隔音-减震-耐腐蚀SMC的基本组成1、树脂不饱和聚酯树脂(UP)是SMC的最基本配方材料。
它通常由不饱和二元羧酸(或酸酐)、饱和二元羧酸(或酸酐)与多元醇缩聚而成,并在缩聚结束后加入一定量的乙烯基体(如苯乙烯)配成粘稠状液态树脂。
根据其化学结构上的差异通常可分为通用型(邻苯型)、间苯型、双酚A型三大类。
最常用的是通用型和间苯型(较贵,具有良好的机械性能)不饱和聚酯树脂。
SMC专用树脂提出如下要求:①低粘度,有利于玻纤的浸渍;②增稠快,以满足增稠的要求;③活性高,能快速固化,以提高生产效率;④热性能好,保证制品的热强度;⑤耐水性好,以提高制品的防潮性;⑥在加入引发剂后的几个月存放期内,必须稳定,而在高温下能快速固化,以确保短的模塑周期。
2、引发剂在SMC树脂糊系统中,不饱和聚酯树脂需加入引发剂,活化树脂与交联单体(如苯乙烯)中的双键发生共聚反应,从而使SMC在模腔内固化成型。
对引发剂的基本要求:贮存稳定性好,反应速度高,操作方便且安全。
引发剂的种类及其使用浓度的选择,主要取决于制品性能的要求和成型温度,以及SMC生产工艺过程,贮存稳定性要求等。
具体地说,应考虑到以下因素:①适用期;②树脂混合物在模具内的流动性;③反应性;④制品的外观与光泽;⑤单体残留量;⑥制品的物理机械性能。
常用于SMC的引发剂以过氧化物为主。
(引发剂浓度越高,制品固化越快,制品表面质量越好)随着引发剂浓度和成型温度的提高,制品固化时间缩短。
当固化温度足够高,时间足够长,制品的最终固化与引发剂浓度(0.2%~1.0%)无关。
但是,引发剂浓度越高,制品固化越快,表面质量越好。
制品的表面质量正比于固化时所达到的放热峰值。
模具温度与放热峰值间温差越大,制品表面质量越好。
而峰值大小与引发剂类型和用量有关。
3、填料(1)碳酸钙(CaCO3)它是一种最基本的填料,其吸油值很低,在配方中易加入。
对促进SMC成型过程及提高制品表面质量最为有效,它具有良好遮盖特性,制品表面着色性好,纤维显露少。
其来源丰富,价格低廉。
但是,碳酸钙填料在模压过程中有优先流动倾向。
(2)水合氧化铝它是SMC常用阻燃型填料,亦可改善制品的耐水性和电绝缘性。
(3)高岭土也是一种理想的填料,在模压过程中其优先流动倾向弱,它不仅有足够的阻力使增强材料相互交合,且能充满模腔内狭小死角等部位。
流动性是它的主要特点。
但其制品的模后收缩率稍大,着色纯度稍差。
另外吸油值高,填料加入量低。
(4)滑石粉流动性良好,能提高制品耐水性,制品易于机械加工,但其吸油值高,加入量低。
4、低收缩添加剂控制收缩率是SMC发展过程中的一项重要课题。
目前通用的方法是在不饱和聚酯树脂中加入一定量的热塑性聚合物来实现。
SMC常用的热塑性添加剂有如下几种:PE粉、PS及其共聚物、PVC及其共聚物、乙酸纤维素和丁酸纤维素、热塑性聚酯、PVAC、PMMA等。
根据其作用机理的不同,大致可分为二类:一类是与不饱和聚酯树脂不相溶的添加剂,如PE和PVC,其加入量为树脂的5~10%;另一类是在树脂固化前彼此相溶,而固化后添加剂又以小颗粒球状从树脂析出形成第二相,如PVAC、PS等。
由于热塑性塑料在树脂中分散性差,一般要求先将其溶于苯乙烯中。
由于苯乙烯会引起SMC表面发粘,因而限制了添加剂的加入量,为此,国外已开发出羧基化热塑性添加剂,其自身参与增稠反应,很好地解决了上述问题。
(PS和HDPE粉是用于SMC低收缩体系的主要添加剂,其收缩效果通常为0.1~0.3%,它们不能获得精密控制的尺寸公差,因而不能用于低轮廓体系,但其着色接受性好,能在几乎所有颜料体系中获得良好的着色深度。
PVAC、PMMA常用于生产收缩率相当低的制品,在某些场合可实现零收缩,其收缩效果为0~0.05%,加入量为树脂的10~20%,但其着色接受性差,不适于着色体系)。
5、化学增稠剂在SMC生产中增稠剂是必需的,通过增稠作用使SMC从利于玻纤浸渍的低粘度转化为不粘手的高粘度。
在浸渍阶段,树脂增稠要足够缓慢,保证玻纤的良好浸渍;浸渍后后树脂浸渍要足够快,使SMC尽快进入模压阶段和尽量减少存货量;当SMC粘度达到可成型和模压粘度后,增稠过程要立即停止,稳定,以获得尽可能长的贮存寿命。
常用的增稠体系包括3类:①Ca、Mg的氧化物和氢氧化物系统;②MgO和环状酸,酐的组合系统;③LiCl和MgO的组合系统。
以第一类的应用最为普遍,也最为重要,它们主要尖型有CaO/Ca(OH)2、CaO/Mg(OH)2、MgO、Mg(OH)2等。
在CaO/Ca(OH)2系统中,一般来说,Ca(OH)2决定系统的起始增稠特性,而CaO决定系统所能达到的最高粘度水平。
CaO与MgO 并用时也能加快增稠。
MgO是应用最广泛且最具代表性的化学增稠剂,其特点是增稠速度快。
其增稠特性与活性有关。
随着MgO加入量增加,增稠也越迅速。
Mg(OH)2与MgO相比,其前期增稠速度缓慢,更利于浸渍作业,而最终粘度两者相当,但Mg(OH)2的用量较多,其制品效果更好。
6、内脱模剂对于SMC,粘模是一个严重的问题,因些须在配方中加入内脱模具剂。
它们通常为长链脂肪酸及其盐类,受热熔化并作为第二相流到模具表面,从而阻止了不饱和聚酯树脂与金属模具表面发生亲合作用。
所选用脱模剂的熔点低于固化温度,以保证其在树脂固化前已熔化。
其加入量一般为0.5%~2.0%。
脱模剂是引起增稠行为变化的重要因素。
硬脂酸金属盐引起的粘度变化直接与颗粒尺寸与形状有关。
当以MgO或Mg(OH)2作增稠剂时,发现加Znst的粘度比加Cast 的低,当用Ca(OH)2作增稠剂时,增稠行为则相反。
研究表明,Znst的灰分含量能改变增稠速度,因此,必须对脱模剂的颗粒尺寸和灰分含量进行精确控制,以保证生产稳定性。
7、着色剂 SMC的着色分为内着色与外着色两种。
内着色通过在树脂糊配方中加入着色剂,外着色则通过对成型制品进行表面涂装而实现,后着属于二次加工范畴。
SMC常用的着色剂为无机和有机颜料,一般加入量为树脂的0.5~5%。
8、增强材料对SMC专用玻纤的一般要求是:切割性好,浸润性佳,流动性好,制品强度高,外观良好等。
其常用类型不外乎短切原纱毡和无捻粗纱两种。
无捻粗纱是用多股原纱平行卷绕制成的圆筒状纱团,它是SMC主要使用的增强材料。
一般来说,硬质粗纱的成型流动性好,软质粗纱成型流动阻力大,易开纤,但不易产生纤维显露。
在SMC中,无捻粗纱切割长度可以是6、12、25、50mm,但以25 mm居多。
增加纤维长度可改进模压效率,提高制品强度,但纤维长度增加到一定程度,便还会有更大的收益。
SMC一般适用的玻纤含量为20~40%,玻纤含量高低取决于对制品强度要求。
但玻纤含量过高或过低都会增加制片工艺的困难,玻纤含量过高还会造成成型困难。
9、其他助剂 SMC的贮存期有限是一大缺点,因为它会由于苯乙烯单体的损失产生流动性变差,或由于引发剂慢速分解引起树脂的聚合。
在SMC配方中加入自由基捕捉剂(阻聚剂),则可以调节其贮存期,在一定时期内阻止聚合反应的发生。
也可以加入链转移剂(缓聚剂),降低放热峰温度来减缓聚合反应的速度。
SMC模压成型工艺过程SMC模压成型工艺过程,主要有以下几个工序1.压制前准备(1)SMC的质量检查SMC片材的质量对成型工艺过程及制品质量有很大的影响。
因此,压制前必须了解料的质量,如树脂糊配方、树脂糊的增稠曲线、玻纤含量、玻纤浸润剂类型、单重、薄膜剥离性,硬度及质量均匀性等。
(2)剪裁按制品的结构形状,加料位置,流程决定片材剪裁的形状与尺寸,制作样板裁料。
剪裁的形状多为方形或圆形,尺寸多按制品表面投影面积的40%-80%。
为防止外界杂质的污染,上下薄膜在装料前才揭去。
(3)设备的准备①熟悉压机的各项操作参数,尤其要调整好工作压力和压机运行速度及台面平行度等。
②模具安装一定要水平,并确保安装位置在压机台面的中心,压制前要先彻底清理模具,并涂脱模剂。
加料前要用干净纱布将脱模剂擦均,以免影响制品外观质量。
对于新模具,用前必须去油。
2、加料(1)加料量的确定每个制品的加料量在首次压制时可按下式计算:加料量=制品体积×1.8 (2)加料面积的确定加料面积的大小,直接影响到制品的密度程度料的流动距离和制品表面质量.它与SMC的流动与固化特性、制品性能要求、模具结构等有关。
一般加料面积为40%-80%。
过小会因流程过长而导致玻纤取向,降低强度,增加波纹度,甚至不能充满模腔;过大,不利于排气,易产生制品内裂纹。
(3)加料位置与方式加料位置与方式直接影响到制品的外观,强度与方向性。
通常情况下,料的加料位置应在模腔的中部。
对于非对称复杂制品,加料位置必须确保成型时料流同时达到模具成型内腔各端部。
加料方式必须有利于排气。
多层片材叠合时,最好将料块按上小下大呈宝塔形叠置。
另外,料块尽量不要分开加,否则会产生空气裹集和熔接区,导致制品强度下降。